确定淬火工艺规范的原则3-5
淬火工艺规程

淬火工艺规程1主题内容与适用范围本标准规定阀门零件、工具、模具等金属材料的淬火工艺。
本标准的淬火,除指在通常的冷却水、油、空气中淬火之外,还包括热浴中的分级和等温淬火。
适用于阀门零件、工具、模具等金属材料在箱式电阻炉,盐浴炉中淬火。
2技术内容2.1 淬火的定义把钢加热到临界点(Ac3或Ac1)以上,使之奥氏体化,保温一定的时间,然后以大于临界冷却速度的冷却速度快速冷却,获得马氏体组织的工艺过程,称为淬火。
2.2 淬火的目的2.2.1 对于优质结构钢工件,通过淬火与适当的回火配合来满足工件性能要求,如:强度、硬度、塑性及韧性等的不同配合。
2.2.2对于各种碳钢、合金钢及表面热处理或化学热处理的工件,通过淬火得到高硬度的马氏体组织,然后低温回火,用以提高其硬度及耐磨性。
2.3 淬火前的准备2.3.1 检查工件表面有无裂纹、尖角及锈蚀等影响淬火质量的缺陷。
2.3.2 根据图纸及工艺文件,明确工件淬火的具体要求,如硬度、局部淬火范围等。
12.3.3 检查淬火工具、冷却剂是否齐全,有不需要淬硬的孔眼、尖角或厚度变化较大时,为了防止变形和开裂危险,应采用堵塞或缠绕石棉绳,使工件各部分加热和冷却均匀。
2.3.4 如果工件表面要求不允许有氧化皮和脱碳的现象时,可在盐炉或通有保护气体的炉中加热。
2.3.5 在箱式电炉中加热时,为防止氧化、脱碳现象发生,可将工件加热到200~350℃,然后撒上硼酸粉末,放入炉中加热(加热温度不得超过950℃),也可在工件表面敷以石棉板或生铁屑,使之与空气隔绝;或将工件装入盛有木碳或已用过的铸铁屑的铁箱内,加盖密封。
2.3.6 大批工件(或两件以上),应作首件或小批量试淬。
认可后方可进行批量生产,并在生产过程中经常抽检。
2.3.7 工件淬火硬度不够而返修时,可重新淬火。
重新淬火的原则如下:形状简单的工件,水淬者可不经退火而重新淬一次;油淬者可不经退火而重新淬火两次;形状复杂的工件和精度要求高的工件需进行退火、高温回火或正火处理;高速钢需经退火、消除残余应力后,方可重新淬火。
淬火工艺规程

淬火工艺规程一、淬火前得准备1、检查工件表面,不允许有碰伤、裂纹、锈斑、油垢及其她脏物存在,油垢可用碱煮洗,锈斑可用喷砂或冷酸清洗。
2、准备淬火所用得工具,检查设备就是否完好。
3、检查控温仪表指示就是否正确。
4、工件形状复杂得,其中有不需要淬硬得孔眼、尖角或厚度变化大得地方,为了防止变形与淬裂得危险均应采用堵塞或缠绕石棉得方法,使工件各部分加热及冷却温度均匀。
5、要求工件表面不允许有氧化脱碳现象,要用硼砂酒精溶液涂覆。
二、淬火规范1、加热温度(1)亚共析钢淬火加热温度为Ac3+30~50℃,一般在空气炉中加热比在盐浴中加热高10~30℃,采用油、硝盐淬火介质时,淬火加热温度应比水淬提高20℃左右。
(2)共析钢、过共析钢淬火加热温度为Ac1+30~50℃,一般合金钢淬火加热温度为Ac1或Ac3+30~50℃.(3)高速钢、高铬钢及不锈钢应根据要求合金碳化物溶入奥氏体得程度选择。
过热敏感性强及脱碳敏感性强得钢,不易取上限温度.(4)低碳马氏体钢淬透性较低,应提高淬火温度以增大淬硬性;中碳钢及中碳合金钢应适当提高淬火温度来减少淬火后片状马氏体得相对量,以提高钢得韧性;高碳钢采用低温淬火或快速加热可限制奥氏体固溶碳量,而增加淬火后板条马氏体得含量,减少淬火钢得脆性.另外,提高淬火温度还会增加淬火后得残余奥氏体量。
2、加热方法(1)模具:室温进炉或300—400℃进炉,并在550—600℃时等温一段时间。
(2)弹簧或原材料(调质处理),可在淬火温度时进炉.3、保温时间加热与保温时间由零件入炉到达指定工艺温度所需升温时间(ι1),透热时间(ι2)及组织转变所需时间(ι3)组成。
ι1+ι2由设备功率、加热介质及工件尺寸、装炉数量等因素决定,ι3则与钢材得成分、组织及热处理技术要求有关。
普通碳钢及低合金钢在透热后保温5~15min即可满足组织转变得要求,合金结构钢透热后应保温15~25min。
高合金工具钢、不锈钢等为了溶解原始组织中得碳化物,应在不使奥氏体晶粒过于粗化得前提下,适当提高奥氏体化温度,以缩短保温时间。
乙炔火焰淬火工操作规程范本

乙炔火焰淬火工操作规程范本一、安全措施1.在操作前,应仔细阅读乙炔火焰淬火操作手册,并经过必要的培训和指导。
2.操作人员应佩戴耐火防护服、安全帽、防护眼镜、防护手套等个人防护用品。
3.操作区域应有良好的通风设备,确保操作环境的安全。
4.严禁吸烟、使用明火及其他可能引发火灾的行为。
5.必须将乙炔气瓶固定在稳定的支架上,并确保接口密封良好。
6.在使用乙炔火焰淬火时,应将氧气调节阀开至合适的压力,并注意调节器的漏气情况。
7.严禁私自更改或调整设备的操作参数,如气流流速、火焰温度等。
8.操作人员需要定期检查和维护乙炔火焰淬火设备,确保其正常运行。
9.操作结束后,应将乙炔气瓶、氧气气瓶及其他操作工具妥善储存,确保其安全。
二、操作步骤1.将乙炔气瓶连接到乙炔调节器,调节气流流速和火焰温度。
2.将氧气气瓶连接到氧气调节器,调节气流流速和火焰温度。
3.将乙炔气体和氧气按照合适的比例混合,在混合室中点燃乙炔气体。
4.调整火焰温度,使其适应具体的淬火工艺要求。
5.将待淬火的工件放置在火焰下,保持一定的冷却时间。
6.根据工艺要求,适时调整火焰温度和工件的加热时间。
7.淬火后,将工件迅速移出火焰,进行冷却处理。
8.在操作过程中,严格控制火焰的接触面积和温度,确保工件的淬火效果。
9.注意观察工件的表面状态,及时调整火焰的温度和加热时间,以确保淬火质量。
三、常见问题及处理1.工件表面出现裂纹:可能是火焰温度过高或加热时间过长,应适当降低火焰温度和加热时间。
2.工件淬火效果不佳:可能是火焰温度过低或加热时间不足,应适当提高火焰温度和加热时间。
3.工件加热不均匀:可能是火焰接触面积不均,应调整火焰形状和火焰接触面积。
4.操作设备漏气:应立即停止操作,检查设备密封性,修复或更换漏气部件。
5.气瓶压力异常:应立即停止操作,检查气瓶连接和调节器,调整气瓶压力。
四、紧急处理措施1.发生火灾时,应立即关闭乙炔和氧气的供气阀门,切断气源。
第3章淬火应力变形开裂

③加热介质 加热介质不同, 则加热速度不同, 因而保温时间也随之不同。
在一般生产中,以铅浴炉加热速度为最快,盐浴炉次之,空气电阻炉 为最慢. 表 保温时间的经验公式
④装炉情况
工件在炉中的放置及排列情况对其受热条件有明显 影响 , 故装炉情况不同, 其保温时间也不同。 ⑤ 炉温 提高炉温,可缩短加热保温时间。 快速加热已在生产上得到应用, 是将工件放入比正常 加热温度高出约100~200℃左右的炉中进行加热; 为防止过热,须严格控制加热保温时间。
3.4.2 淬火时工件的变形
两种 主要 形式
工件几何形状的变化 (通常称为翘曲)
引起
淬火工件中热应力 和组织应力 是组织转变时比容 变化而引起的
体积变化, (工件体积 按比例地胀大或缩小)
概念 把组织转变所引起的体积变化称为体积变形,
也叫比容差效应。
1 引起各种变形的原因及其变化规律
⑴ 淬火前后组织变化引起的体积变形 工件在淬火前组织一般为珠光体组织,而淬火后为马氏体组织。 由于组织的比容不同,引起体积变化,产生变形。一般是使工件的 体积在各个方向上作均匀的胀大或缩小,但不改变形状。
(2)双液淬火法(双淬火介质淬火法) 工艺:该种方法是把加热到淬火温度的工件,先在冷却能力强的淬 火介质中冷却至接近Ms点,然后转入慢冷的淬火介质中冷却至室 温,以达到不同淬火冷却温度区间,并有比较理想的淬火冷却速 度.这样既保证了获得较高的硬度层和淬硬层深度又可减少内应力 及防止发生淬火开裂.一般用水作快冷淬火介质,用油或空气作慢 冷淬火介质,但较少采用空气 . 盐水-冷至400℃左右-转至油中。 优点:先快冷可避免过冷奥氏体的 分解,后慢冷可有效地降低变 形和开裂倾向,第二种冷却介 质也可以是其他介质(热浴)。
淬火工艺流程
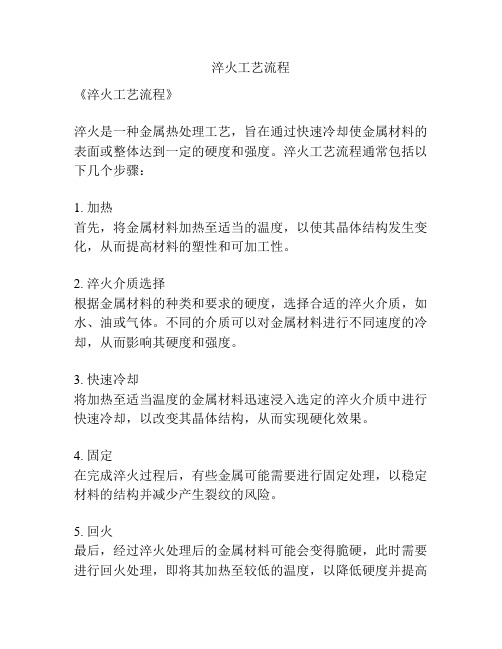
淬火工艺流程
《淬火工艺流程》
淬火是一种金属热处理工艺,旨在通过快速冷却使金属材料的表面或整体达到一定的硬度和强度。
淬火工艺流程通常包括以下几个步骤:
1. 加热
首先,将金属材料加热至适当的温度,以使其晶体结构发生变化,从而提高材料的塑性和可加工性。
2. 淬火介质选择
根据金属材料的种类和要求的硬度,选择合适的淬火介质,如水、油或气体。
不同的介质可以对金属材料进行不同速度的冷却,从而影响其硬度和强度。
3. 快速冷却
将加热至适当温度的金属材料迅速浸入选定的淬火介质中进行快速冷却,以改变其晶体结构,从而实现硬化效果。
4. 固定
在完成淬火过程后,有些金属可能需要进行固定处理,以稳定材料的结构并减少产生裂纹的风险。
5. 回火
最后,经过淬火处理后的金属材料可能会变得脆硬,此时需要进行回火处理,即将其加热至较低的温度,以降低硬度并提高
韧性。
淬火工艺流程的确切操作方式和参数需要根据具体的金属材料和要求来确定,对于不同种类的金属和不同用途的制品,淬火工艺流程也会有所差异。
同时,精准控制淬火工艺流程,能够有效提高金属材料的硬度和强度,从而满足不同场合的使用要求。
钢的淬火临界尺寸标准

钢的淬火临界尺寸标准钢的淬火临界尺寸标准是指钢材在进行淬火处理时,能够保证材料的组织结构得到充分的变质,从而达到所要求的力学性能和物理性能。
淬火临界尺寸标准是根据不同类型的钢材来设定的,下面将分别介绍碳钢、合金钢和不锈钢的淬火临界尺寸标准。
1. 碳钢的淬火临界尺寸标准碳钢是一种含有一定量碳元素的钢材,根据碳的含量不同,碳钢可以分为低碳钢、中碳钢和高碳钢。
对于碳钢的淬火临界尺寸标准,通常以钢材的截面尺寸来进行确定。
根据相关标准,对低碳钢、中碳钢和高碳钢的淬火临界尺寸标准如下:- 低碳钢:一般指碳含量小于0.25%的钢材,其淬火临界尺寸一般为截面尺寸小于30 mm;- 中碳钢:一般指碳含量在0.25%~0.60%之间的钢材,其淬火临界尺寸一般为截面尺寸小于20 mm;- 高碳钢:一般指碳含量大于0.60%的钢材,其淬火临界尺寸一般为截面尺寸小于15 mm。
2. 合金钢的淬火临界尺寸标准合金钢是一种通过在钢材中添加合金元素来改变钢材性能的钢材。
合金元素可以是铬、镍、钼、锰、硅等元素。
合金钢的淬火临界尺寸标准也是根据钢材的截面尺寸来进行确定,但也会考虑合金元素的含量以及钢材的具体用途。
一般来说,合金钢的淬火临界尺寸要小于碳钢,以保证合金元素的充分固溶和弥散。
具体的淬火临界尺寸标准可按照以下原则进行确认:- 根据合金元素的种类和含量,参考相关的合金钢标准来确定淬火临界尺寸;- 考虑钢材的具体用途和力学性能要求,根据经验确定合适的淬火临界尺寸。
3. 不锈钢的淬火临界尺寸标准不锈钢含有铬等合金元素,以提高钢材的耐腐蚀性能,具有很高的抗氧化性和美观性。
不锈钢的淬火临界尺寸标准一般较高,一方面由于不锈钢的合金元素含量较高,需要较长的时间进行固溶;另一方面,不锈钢的耐腐蚀性能对淬火工艺的设计和控制要求更高。
一般来说,不锈钢的淬火临界尺寸标准较碳钢和合金钢更小,以保证合金元素充分固溶和弥散的同时,尽量减少钢材表面的氧化和腐蚀。
热处理工艺规范

热处理工艺规范一、淬火、回火工艺规范1.淬火、回火准备工作:1)检查设备,仪表是否正常;2)正确选择夹具;3)检查零件表面是否有碰伤、裂纹、锈斑等缺陷;4)确认零件要求的淬火部位硬度、变形等的技术要求,核对零件的形状、材料的加工状态是否与图样及工艺文件相符合;5)表面不允许氧化、脱碳的零件,当在空气炉加热时,应采取防氧化脱碳剂装箱保护或采用真空炉加热;6)易开裂的部位如尖角靠边的孔,应采取预防措施,如塞石棉、耐火泥等。
2.常见材料淬火、回火工艺规范1)加热温度表1 常用材料的常规淬火、回火规范注:Cr12Mo1V1 即 D2(美国)、(德国)、SLD(日立)、SKD11(日本)、K110(奥地利);9CrWMn 即 O1(美国)、(德国)、K460(奥地利);4Cr5MoSiV1 即 H13(美国)、(德国)、8407/8402(一胜百)、W302(奥地利);7Cr7Mo3V2Si 即 LD1;HS-1是高级火焰淬火,多用模具钢;除45号钢或特别说明均采用回火两次的工艺。
2)淬火保温时间t =8~10 min+kαDk——装炉系数(1~);α——保温系数(见表2);D——零件有效厚度。
表2 淬火保温系数3)回火保温时间①工件有效厚度d<=50mm,保温2小时;②工件有效厚度d>50mm,按照保温时间t=d/25(小时)计算;③每次回火后空冷至室温,再进行下次回火。
4)去应力(入炉时效)①高合金钢550~650℃,热透后,保温时间>3小时;3.淬火和回火设备1)淬火设备——真空淬火炉、中温箱式炉、高温箱式炉。
2)回火设备——真空回火炉、中温箱式炉。
3)冷却设备——水槽、油槽、风箱。
4.操作方法1)零件应均匀摆放于炉内有效加热区,在箱式炉中一般为单层排列加热,工件间适当间隙。
小件可适当堆放,但要酌情增加保温时间。
2)细长零件加热要考虑装炉方法,以减少工件变形,如垂直吊挂,侧立放平支稳等。
热处理检验方法国家标准
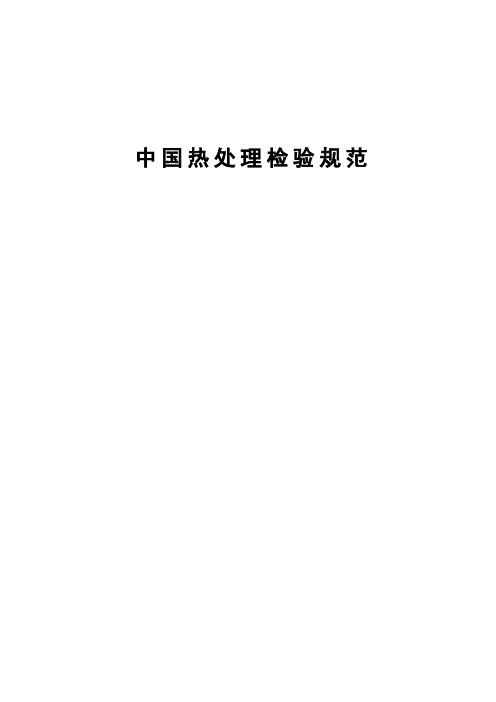
中国热处理检验规范热处理检验方法和规范金属零件的内在质量主要取决于材料和热处理。
因热处理为特种工艺所赋予产品的质量特性往往又室补直观的内在质量,属于“内科”范畴,往往需要通过特殊的仪器(如:各种硬度计、金相显微镜、各种力学性能机)进行检测。
在GB/T19000-ISO9000系列标准中,要求对机械产品零部件在整个热处理过程中一切影响因素实施全面控制,反映原材料及热处理过程控制,质量检验及热处理作业条件(包括生产与检验设备、技术、管理、操作人员素质及管理水平)等各方面均要求控制,才能确保热处理质量。
为此,为了提高我公司热处理产品质量,遵循热处理相关标准,按零件图纸要求严格执行,特制定本规范一、使用范围:本规范适用于零件加工部所有热处理加工零件。
二、硬度检验:通常是根据金属零件工作时所承受的载荷,计算出金属零件上的应力分布,考虑安全系数,提出对材料的强度要求,以强度要求,以强度与硬度的对应关系,确定零件热处理后应具有大硬度值。
为此,硬度时金属零件热处理最重要的质量检验指标,不少零件还时唯一的技术要求。
1、常用硬度检验方法的标准如下:GB230 金属洛氏硬度试验方法GB231 金属布氏硬度试验方法GB1818 金属表面洛氏硬度试验方法GB4340 金属维氏硬度试验方法GB4342 金属显微维氏硬度试验方法GB5030 金属小负荷维氏试验方法2、待检件选取与检验原则如下:为保证零件热处理后达到其图纸技术(或工艺)要求,待检件选取应有代表性,通常从热处理后的零件中选取,能反映零件的工作部位或零件的工作部位硬度的其他部位,对每一个待检件的正时试验点数一般应不少于3个点。
通常连续式加热炉(如网带炉):应在连续生产的网带淬火入回火炉前、回火后入料框前的网带上抽检3-5件/时。
且及时作检验记录。
同时,若发现硬度超差,应及时作检验记录。
同时,若发现硬度越差,应及时进行工艺参数调整,且将前1小时段的零件进行隔离处理(如返工、检)。
不锈钢淬火正确方法

不锈钢淬火正确方法不锈钢淬火是一种常见的热处理工艺,通过淬火可以提高不锈钢的硬度和强度,改善其机械性能。
正确的不锈钢淬火方法可以确保制品的质量和性能,下面将介绍不锈钢淬火的正确方法。
首先,选择合适的不锈钢材料非常重要。
不同种类的不锈钢材料在淬火过程中会有不同的变化,因此需要根据具体的材料类型来选择合适的淬火工艺。
通常情况下,Austenitic不锈钢适合采用水淬,Ferritic不锈钢适合采用油淬,Martensitic不锈钢适合采用空气或油淬。
其次,淬火前需要对不锈钢材料进行预热处理。
预热的目的是为了减少淬火时的变形和裂纹,提高淬火效果。
预热温度一般为850℃-900℃,时间根据材料的厚度和规格来确定,一般为1-2小时。
接着,进行淬火处理。
淬火时需要将不锈钢材料加热到适当的温度,保持一定时间后迅速冷却。
淬火温度一般为不锈钢的临界温度,具体温度根据材料的类型和要求来确定。
在加热和保温过程中,需要注意控制加热速度和保温时间,以免产生过热或过烧的情况。
最后,进行回火处理。
淬火后的不锈钢材料通常会出现过硬和脆性的情况,需要通过回火来改善其性能。
回火温度和时间根据具体材料来确定,一般为250℃-400℃,时间为1-2小时。
回火后的不锈钢材料会获得适当的硬度和韧性,提高其使用性能。
在不锈钢淬火过程中,需要严格控制各个环节,确保每一步操作都符合要求。
只有这样,才能获得优质的淬火制品。
同时,需要注意安全防护措施,避免因操作不当而造成意外事故的发生。
总之,不锈钢淬火是一项重要的热处理工艺,正确的淬火方法可以提高不锈钢材料的硬度和强度,改善其机械性能。
通过选择合适的材料、进行预热处理、严格控制淬火和回火过程,可以确保不锈钢淬火的质量和性能,满足不同工程和使用要求。
3-5 加工余量及工序尺寸、公差的确定
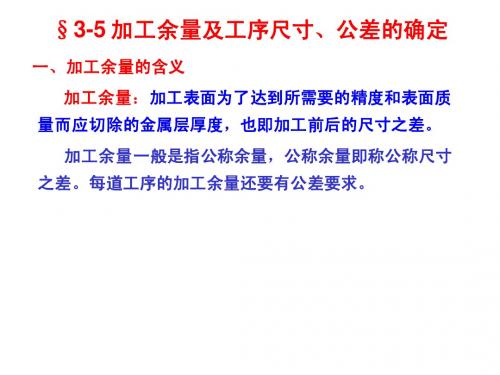
空间误差对加工余量的影响
安装误差对加工余量的影响
因为 a和
b 有方向性,为向量。故单边余量
Zb Ta Rya Ha a b
孔、外圆,则为双边
2Zb Ta 2(Rya Ha ) 2 a b
浮动镗孔、拉孔、铰孔时,不能纠正空间、位置,则:
二、加工余量对机械加工的影响 余量过大—不能保留零件最耐磨的表层,降低表层 机械物理性能,增加切削工时,增加了材料、工具、 电力的消耗,成本提高。 余量过小—不能保证去掉零件表面缺陷层,不能保 证质量,对切削刀具不利,缩短了刀具寿命,余量
不够会出废品。 三、 工序间尺寸公差对机械加工的影响 公差过大—加工余量增加,造成不必要的加工 公差过小—无形中提高了各工序的加工精度,成本提高
2
56 2
②确定各工序的加工余量
查工艺人员手册:研磨0.01,精磨0.1,粗磨0.3, 半精车1.1,粗车4.5。取4.49
③确定经济精度和表面粗糙度
④确定各工序尺寸、公差、表面粗糙度及毛坯尺寸
工序 名 研磨 精磨 粗磨
工序 间余 量 0.01 0.1 0.3
工序间 经济精度
0 h5 0.011 0 h6 0.016
四、加工余量的确定
1、前一工序的公差 T(毛坯公差的入体部分)
a
2、前一工序遗留的表面粗糙度 Rya和表面缺陷层深度 数值 H a 3、前一工序所形成的工件空间误差 尺寸公差带内的形状误差和位置误差 4、本工序的安装误差 b
a,即没有包括在
包括定位误差、夹紧误差、及夹具本身的误差
表3.13 各种加工方法的上述两项值
0 h8 0.a 0.16 Ra 1.25 50 50+0.01 =50.01 50.01+0.1 =50.11
TRIZ理论应用案例.
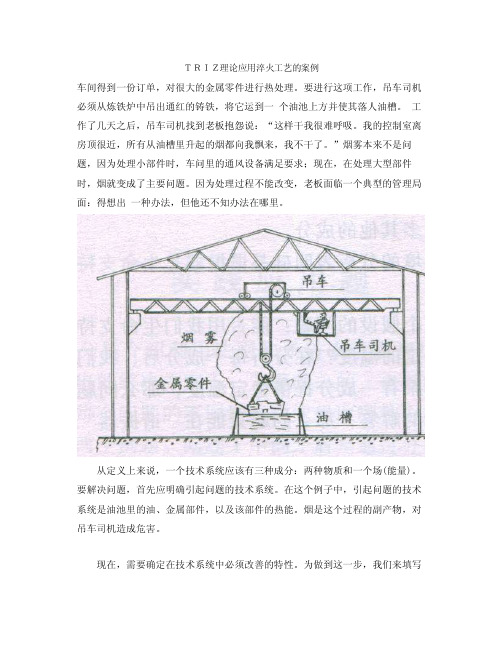
TRIZ理论应用淬火工艺的案例车间得到一份订单,对很大的金属零件进行热处理。
要进行这项工作,吊车司机必须从炼铁炉中吊出通红的铸铁,将它运到一个油池上方并使其落人油槽。
工作了几天之后,吊车司机找到老板抱怨说:“这样干我很难呼吸。
我的控制室离房顶很近,所有从油槽里升起的烟都向我飘来,我不干了。
”烟雾本来不是问题,因为处理小部件时,车问里的通风设备满足要求;现在,在处理大型部件时,烟就变成了主要问题。
因为处理过程不能改变,老板面临一个典型的管理局面:得想出一种办法,但他还不知办法在哪里。
从定义上来说,一个技术系统应该有三种成分:两种物质和一个场(能量)。
要解决问题,首先应明确引起问题的技术系统。
在这个例子中,引起问题的技术系统是油池里的油、金属部件,以及该部件的热能。
烟是这个过程的副产物,对吊车司机造成危害。
现在,需要确定在技术系统中必须改善的特性。
为做到这一步,我们来填写附表1,指出需改善的特性。
1.标明技术系统的名称金属处理过程2.指出技术系统的系统对大型金属部件进行过油处理3.列出该技术系统中的主要成分及相应作用4.描述技术系统的操作本例中,吊车司机将通红的部件放到装满油的油槽中,金属部件一接触油就会激起浓烟,污染环境。
5.表示出应该改善或取消的特性:例如通过取消烟雾或减少烟雾所造成的危害,改善吊车司机的工作条件。
利用附表2构建技术矛盾。
(填写附表2,能够有助于清楚地确定问题中的技术矛盾。
)在问题中,从1a项到1d项都与问题无关,因为不是要改善技术系统的特性。
相反,我们是想去除有害的作用。
2a.“讲明需要减掉、去除或使其中性化的负面特性”。
这个特性就是烟雾。
2b.“列出传统的减掉、去除该特性或使该特性中性化的方法”。
利用金属盖来覆盖油槽,这样可以防止油烟四散。
2c.“写出在2b项条件中更加恶化的特性”。
系统的复杂性和重量增加。
2d.“构建技术矛盾如下”:技术矛盾1:如果利用金属盖将(油烟雾带来的有害)特性减少(去除),则系统的复杂性增加。
热处理标准规范

热处理检验规范金属零件的内在质量主要取决于材料和热处理。
因热处理为特种工艺所赋予产品的质量特性往往又室补直观的内在质量,属于“内科”范畴,往往需要通过特殊的仪器(如:各种硬度计、金相显微镜、各种力学性能机)进行检测。
在GB/T19000-ISO9000系列标准中,要求对机械产品零部件在整个热处理过程中一切影响因素实施全面控制,反映原材料及热处理过程控制,质量检验及热处理作业条件(包括生产与检验设备、技术、管理、操作人员素质及管理水平)等各方面均要求控制,才能确保热处理质量。
为此,为了提高我公司热处理产品质量,遵循热处理相关标准,按零件图纸要求严格执行,特制定本规范一、使用范围:本规范适用于零件加工部所有热处理加工零件。
二、硬度检验:通常是根据金属零件工作时所承受的载荷,计算出金属零件上的应力分布,考虑安全系数,提出对材料的强度要求,以强度要求,以强度与硬度的对应关系,确定零件热处理后应具有大硬度值。
为此,硬度时金属零件热处理最重要的质量检验指标,不少零件还时唯一的技术要求。
1、常用硬度检验方法的标准如下:GB230 金属洛氏硬度试验方法 GB231 金属布氏硬度试验方法GB1818 金属表面洛氏硬度试验方法 GB4340 金属维氏硬度试验方法GB4342 金属显微维氏硬度试验方法 GB5030 金属小负荷维氏试验方法2、待检件选取与检验原则如下:为保证零件热处理后达到其图纸技术(或工艺)要求,待检件选取应有代表性,通常从热处理后的零件中选取,能反映零件的工作部位或零件的工作部位硬度的其他部位,对每一个待检件的正时试验点数一般应不少于3个点。
通常连续式加热炉(如网带炉):应在连续生产的网带淬火入回火炉前、回火后入料框前的网带上抽检3-5件/时。
且及时作检验记录。
同时,若发现硬度超差,应及时作检验记录。
同时,若发现硬度越差,应及时进行工艺参数调整,且将前1小时段的零件进行隔离处理(如返工、检)。
通常期式加炉(如井式炉、箱式炉):应在淬火后、回火后均从料框的上、中、下部位抽检6-9件/炉,且及时作检验记录。
淬火的方法
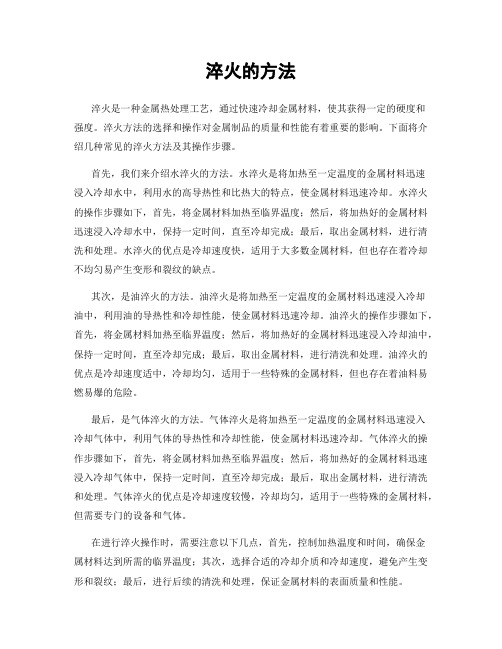
淬火的方法淬火是一种金属热处理工艺,通过快速冷却金属材料,使其获得一定的硬度和强度。
淬火方法的选择和操作对金属制品的质量和性能有着重要的影响。
下面将介绍几种常见的淬火方法及其操作步骤。
首先,我们来介绍水淬火的方法。
水淬火是将加热至一定温度的金属材料迅速浸入冷却水中,利用水的高导热性和比热大的特点,使金属材料迅速冷却。
水淬火的操作步骤如下,首先,将金属材料加热至临界温度;然后,将加热好的金属材料迅速浸入冷却水中,保持一定时间,直至冷却完成;最后,取出金属材料,进行清洗和处理。
水淬火的优点是冷却速度快,适用于大多数金属材料,但也存在着冷却不均匀易产生变形和裂纹的缺点。
其次,是油淬火的方法。
油淬火是将加热至一定温度的金属材料迅速浸入冷却油中,利用油的导热性和冷却性能,使金属材料迅速冷却。
油淬火的操作步骤如下,首先,将金属材料加热至临界温度;然后,将加热好的金属材料迅速浸入冷却油中,保持一定时间,直至冷却完成;最后,取出金属材料,进行清洗和处理。
油淬火的优点是冷却速度适中,冷却均匀,适用于一些特殊的金属材料,但也存在着油料易燃易爆的危险。
最后,是气体淬火的方法。
气体淬火是将加热至一定温度的金属材料迅速浸入冷却气体中,利用气体的导热性和冷却性能,使金属材料迅速冷却。
气体淬火的操作步骤如下,首先,将金属材料加热至临界温度;然后,将加热好的金属材料迅速浸入冷却气体中,保持一定时间,直至冷却完成;最后,取出金属材料,进行清洗和处理。
气体淬火的优点是冷却速度较慢,冷却均匀,适用于一些特殊的金属材料,但需要专门的设备和气体。
在进行淬火操作时,需要注意以下几点,首先,控制加热温度和时间,确保金属材料达到所需的临界温度;其次,选择合适的冷却介质和冷却速度,避免产生变形和裂纹;最后,进行后续的清洗和处理,保证金属材料的表面质量和性能。
综上所述,淬火是一种重要的金属热处理工艺,选择合适的淬火方法和操作步骤对金属制品的质量和性能有着重要的影响。
淬火工岗位职责(5篇)
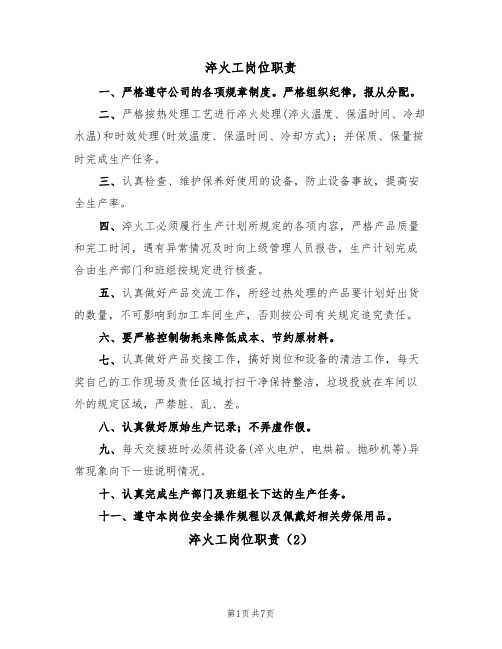
淬火工岗位职责一、严格遵守公司的各项规章制度。
严格组织纪律,报从分配。
二、严格按热处理工艺进行淬火处理(淬火温度、保温时间、冷却水温)和时效处理(时效温度、保温时间、冷却方式);并保质、保量按时完成生产任务。
三、认真检查、维护保养好使用的设备,防止设备事故,提高安全生产率。
四、淬火工必须履行生产计划所规定的各项内容,严格产品质量和完工时间,遇有异常情况及时向上级管理人员报告,生产计划完成合由生产部门和班组按规定进行核查。
五、认真做好产品交流工作,所经过热处理的产品要计划好出货的数量,不可影响到加工车间生产,否则按公司有关规定追究责任。
六、要严格控制物耗来降低成本、节约原材料。
七、认真做好产品交接工作,搞好岗位和设备的清洁工作,每天奖自己的工作现场及责任区域打扫干净保持整洁,垃圾投放在车间以外的规定区域,严禁脏、乱、差。
八、认真做好原始生产记录;不弄虚作假。
九、每天交接班时必须将设备(淬火电炉、电烘箱、抛砂机等)异常现象向下一班说明情况。
十、认真完成生产部门及班组长下达的生产任务。
十一、遵守本岗位安全操作规程以及佩戴好相关劳保用品。
淬火工岗位职责(2)淬火工是一种专门负责进行金属材料淬火处理的职业。
他们的主要职责包括以下几个方面:1. 根据工程图纸和工艺要求,准备淬火设备、工具和材料。
2. 检查和调整淬火设备的工作参数,确保设备正常运行。
3. 将金属材料放入淬火设备中,并根据工艺要求控制加热温度和保温时间。
4. 根据材料的不同特性和要求,选择适当的淬火介质(如水、油或空气)进行淬火处理。
5. 监控淬火过程的温度和时间,确保淬火效果符合要求。
6. 检查淬火后的金属材料的硬度和性能,并进行必要的修整和调整。
7. 维护和保养淬火设备,及时清理和更换使用过的淬火介质。
8. 配合质检和工程师进行产品质量检验和改进工作。
9. 按照安全操作规程,确保淬火过程的安全性。
10. 参与处理非标准淬火工艺和问题的调查和解决。
淬火+回火时间确定

D有效厚度的计较原则:之五兆芳芳创作
1.圆柱体取直径
2.正方形截面取边长
3.长方形截面取短边长
4.板件取板厚
5.套筒类工件取壁厚
6.圆锥体取离小头的2/3长度处取直径
一、淬火加热时间
淬火加热时间包含升温时间和保温时间.生产中一般不降2个时间分隔,罢了总的加热时间考虑.影响因素良多:加热介质、炉温、钢的化学成分、零件尺寸形状、装炉方法和装炉量等.
淬火介质:油:适合合金钢、小尺寸碳钢
水:形状复杂和截面尺寸较大得碳钢经常使用经验公式:T=a ×K ×D
T——加热时间min
a——加热系数min/mm与工件尺寸、加热介质、钢的化学成分有关,可从资料中查得
K——装炉修正系数(取1.5-2.0)
D——零件有效厚度mm
二、回火保温时间
回火保温时间参考
经验公式的计较办法如下:Th=Kh+AhD Th:回火时间,min;
Kh:回火时间基数,min;
Ah:回火时间系数,min/mm;
D:工件有效厚度,mm.
Kh及Ah推荐表。
汽车大梁 淬火注意事项

淬火是一种金属热处理工艺,通过将金属加热到适当的温度并保持一段时间,然后快速冷却,以提高金属的硬度和耐磨性。
对于汽车大梁的淬火,有一些注意事项需要注意:
1. 淬火前的准备:在淬火前,需要仔细检查大梁的表面质量,确保表面无缺陷、无锈蚀、无油污等。
同时,需要检查淬火设备和冷却介质是否正常,并确保淬火时的温度和时间控制准确。
2. 温度控制:淬火温度是影响淬火质量的关键因素之一。
对于不同的金属材料,淬火的温度范围是不同的。
因此,需要根据大梁的材料和要求,严格控制淬火的温度范围。
3. 冷却速度:淬火的冷却速度也是影响淬火质量的重要因素。
冷却速度过快可能导致淬火不均,而冷却速度过慢则可能使金属过热,导致表面氧化或开裂。
因此,需要根据大梁的尺寸和形状,选择合适的冷却速度。
4. 介质选择:淬火介质的选择对淬火质量也有很大影响。
常用的淬火介质有水、油、盐溶液等。
对于汽车大梁的淬火,需要根据大梁的材料和要求,选择合适的淬火介质。
5. 质量检测:淬火后,需要对大梁进行质量检测,包括硬度、组织结构、力学性能等方面的检测。
如果发现质量问题,需要及时采取措施进行处理。
6. 环境保护:在淬火过程中,需要注意环境保护,控制有害物质的排放,防止对环境和人体造成危害。
总之,汽车大梁的淬火需要严格控制工艺参数和操作规程,确
保质量和安全。
同时,需要注意环境保护和安全生产,防止对环境和人体造成危害。
60号钢淬火要求

60号钢淬火要求
钢的淬火要求通常包括以下几个方面:
1. 温度要求:一般淬火温度范围为800~900℃之间,具体温度
取决于钢材的成分和淬火的目的,要求淬火时温度要控制得准确。
对于60号钢,淬火温度一般在850~900℃之间。
2. 冷却介质:淬火时需要使用适当的冷却介质来迅速冷却钢材,以使其获得所需的硬度和组织结构。
常用的淬火介质包括水、油和气体。
对于60号钢,通常选择适量的水或油来淬火。
3. 保温时间:淬火过程中,保温时间要足够,以确保钢材的温度均匀达到淬火温度。
一般情况下,保温时间为10~30分钟左右,具体时间也要根据钢材的大小和形状来确定。
4. 冷却速度:淬火的关键在于快速冷却,以避免钢材产生退火或其他有害的相变。
冷却速度的选择要根据钢材的成分和要求的硬度来确定,一般要求快速冷却以得到较高的硬度。
总结起来,60号钢的淬火要求包括温度、冷却介质、保温时
间和冷却速度等方面。
具体的淬火要求还需根据具体情况和要求来确定。
- 1、下载文档前请自行甄别文档内容的完整性,平台不提供额外的编辑、内容补充、找答案等附加服务。
- 2、"仅部分预览"的文档,不可在线预览部分如存在完整性等问题,可反馈申请退款(可完整预览的文档不适用该条件!)。
- 3、如文档侵犯您的权益,请联系客服反馈,我们会尽快为您处理(人工客服工作时间:9:00-18:30)。
3.5 确定淬火工艺规范的原则淬火工艺方法及其应用淬火工艺规范包括1)淬火加热方式、2)加热温度、3)保温时间、4)冷却介质及冷却方式等。
确定工件淬火规范的依据是工件图纸及技术要求,所用材料牌号,相变点及过冷奥氏体等温或连续冷却转变曲线,端淬曲线,加工工艺路线及淬火前的原始组织等。
只有充分掌握这些原始材料,才能正确地确定淬火工艺规范。
一、淬火加热方式及加热温度的确定原则淬火一般是最终热处理工序。
因此,应采用保护气氛加热或盐炉加热。
只有一些毛坯或棒料的调质处理(淬火、高温回火)可以在普通空气介质中加热。
因为调质处理后尚须机械切削加工,可以除去表面氧化、脱碳等加热缺陷。
但是随着少、无切削加工的发展、调质处理后仅是一些切削加工量很小的精加工,因而也要求无氧化,脱碳加热。
淬火加热一般是热炉装料。
但对工件尺寸较大,几何形状复杂的高合金钢制工件,应该根据生产批量的大小,采用预热炉(周期作业)预热,或分区(连续炉)加热等方式进行加热。
1:淬火加热温度:淬火加热温度,主要根据钢的相变点来确定。
对亚共析钢,一般选用淬火加热温度为Ac3+(30—50℃),过共析钢则为Ac1+(30—50℃)。
之所以这样确定,因为对亚共析钢来说,若加热温度低于Ac3,则加热状态为奥氏体与铁素体二相组成,淬火冷却后铁素体保存下来,使得零件淬火后硬度不均匀,强度和硬度降低。
比Ac3点高30—50℃的目的是为了使工件心部在规定加热时间内保证达到Ac3点以上的温度,铁素体能完全溶解于奥氏体中,奥氏体成分比较均匀,而奥氏体晶粒又不致于粗大。
对过共析钢来说,淬火加热温度在Ac1~Ac3之间时,加热状态为细小奥氏体晶粒和未溶解碳化物,淬火后得到隐晶马氏体和均匀分布的球状碳物。
这种组织不仅有高的强度和硬度、高的耐磨性,而且也有较好的韧性。
如果淬火加热温度过高,碳化物溶解,奥氏体晶粒长大,淬火后得到片状马氏体(孪晶马氐体),其显微裂纹增加,脆性增大,淬火开裂倾向也增大。
由于碳化物的溶解,奥氏体中含碳量增加,淬火后残余奥氏体量增多,钢的硬度和耐磨性降低。
高于Ac1点30—50℃的目的和亚共析钢类似,是为了保证工件内各部分温度均高于Ac1。
2:注意:确定淬火加热温度时,尚应考虑工件的形状、尺寸、原始组织、加热速度、冷却介质和冷却方式等因素。
在工件尺寸大、加热速度快的情况下,淬火温度可选得高一些。
因为工件大,传热慢,容易加热不足,使淬火后得不到全部马氏体或淬硬层减薄。
加热速度快,工件温差大,也容易出现加热不足。
另外,加热速度快,起始晶粒细,也允许采用较高加热温度。
在这种情况下,淬火温度可取Ac3+(50—80℃),对细晶粒钢有时取Ac3+100℃。
对于形状较复杂,容易变形开裂的工件,加热速度较慢,淬火温度取下限。
考虑原始组织时,如先共析铁素体比较大,或珠光体片间距较大,为了加速奥氏体均匀化过程,淬火温度取得高一些。
对过共析钢为了加速合金碳化物的溶解,以及合金元素的均匀化,也应采取较高的淬火温度。
例如高速钢的Ac1点为820—840℃,淬火加热温度高达1280℃。
考虑选用淬火介质和冷却方式时,在选用冷却速度较低的淬火介质和淬火方法的情况下,为了增加过冷奥氏体的稳定性,防止由于冷却速度较低而使工件在淬火时发生珠光体型转变,常取稍高的淬火加热温度。
二、淬火加热时间的确定原则淬火加热时间应包括工件整个截面加热到预定淬火温度,并使之在该温度下完成组织转变、碳化物溶解和奥氏体成分均匀化所需的时间。
因此,淬火加热时间包括升温和保温两段时间。
在实际生产中,只有大型工件或装炉量很多情况下,才把升温时间和保温时间分别进行考虑。
一般情况下把升温和保温两段时间通称为淬火加热时间。
当把升温时间和保温时间分别考虑时,由于淬火温度高于相变温度,所以升温时间包括相变重结晶时间。
保温时间实际上只要考虑碳化物溶解和奥氏体成分均匀化所需时间即可。
在具体生产条件下,淬火加热时间常用经验公式计算,通过试验最终确定。
常用经验公式是式中——加热时间,(min);a——加热系数,(min/mm);K——装炉修正系数;D——零件有效厚度(mm)。
加热系数口表示工件单位厚度需要的加热时间,其大小与工件尺寸、加热介质和钢的化学成分有关。
装炉量修正系数X是考虑装炉的多少而确定的。
装炉量大时,K值也应取得较大,一般由实验确定;工件有效厚度D的计算,可按下述原则确定:圆柱体取直径,正方形截面取边长,长方形截面取短边长,板件取板厚,套筒类工件取壁厚,圆锥体取离小头2/3长度处直径,球体取球径的0.6倍作为有效厚度D。
三、淬火介质及冷却方式的选择与确定淬火介质的选择,首先应按工件所采用的材料及其淬透层深度的要求,根据该种材料的端淬曲线,通过一定的图表来进行选择。
其选择方法已在本章淬透性一节讲述。
若仅从淬透层深度角度考虑,凡是淬火烈度大于按淬透层深度所要求的淬火烈度的淬火介质都可采用。
但是从淬火应力变形开裂的角度考虑,淬火介质的淬火烈度愈低愈好。
综合这两方面的要求,选择淬火介质的第一个原则应是在满足工件淬透层深度要求的前提下,选择淬火烈度最低的淬火介质。
四:淬火方法及其应用:目前常用主要有以下几种方法;1)单液淬火法它是最简单的淬火方法。
把已加热到淬火温度的工件淬人一种淬火介质,使其完全冷却。
这种方法常用于形状简单的碳钢和合金钢工件。
对碳钢而言,直径大于3—5mm的工件应于水中淬火,更小的可在油中淬火。
对各种牌号的合金钢,则以油为常用淬火介质。
由过冷奥氏体转变(等温或连续冷却)动力学曲线看出,过冷奥氏体在且,点附近的温度区是比较稳定的。
为了减少工件与淬火介质之间的温差,减小内应力,可以把欲淬火工件,在淬入淬火介质之前,先空冷一段时间。
这种方法叫预冷淬火法。
2 中断淬火法(双淬火介质淬火法)该种方法是把加热到淬火温度的工件,先在冷却能力强的淬火介质中冷却至接近Ms点,然后转入慢冷的淬火介质中冷却至室温,以达到不同淬火冷却温度区间,并有比较理想的淬火冷却速度.这样既保证了获得较高的硬度层和淬硬层深度又可减少内应力及防止发生淬火开裂.一般用水作快冷淬火介质,用油或空气作慢冷淬火介质,但较少采用空气.这种方法的缺点是:对于各种工件很难确定其应在快冷介质中停留的时间,而对于同种工件,这时间也难控制.在水中冷却时间过长,将使工件某些部分冷到马氏体点以下,发生马氏体转变,结果可能导致变形和开裂。
反之,如果在水中停留的时间不够,工件尚未冷却到低于奥氏体最不稳定的温度,发生珠光体型转变,导致淬火硬度不足。
此外,还应考虑:当工件自水中取出后,由于心部温度总是高于表面温度,若取出过早,心部储存的热量过多,将会阻止表面冷却,使表面温度回升,致使已淬成的马氏体回火,未转变的奥氏体发生珠光体或贝氏体转变.由于迄今仍未找到兼有水、油优点的淬火介质,所以尽管这种方法在水中保持的时间较难确定和控制,但对只能在水中淬硬的碳素工具钢仍多采用此法.当然,这就要求淬火操作者有足够熟炼的技术。
在水中停留时间为每5~6mm有效厚度约1秒钟。
中断淬火法也可以另种方式进行,即把工件从奥氏体化温度直接淬入水中,保持一定时间后,取出在空气中停留,由于心部热量的外传使表面又被加热回火,同时沿工件截面温差减小,然后再将工件淬入水中保持很短时间,再取出在空气中停留,如此往复数次,最后在油中或空气中冷却。
这种方法主要用于碳钢制的大型工件,以减少在水中淬火时的内应力。
显然这种方法不能得到很高的硬度。
3.喷射淬火法这种方法就是向工件喷射水流的淬火方法.水流可大可小,枧所要求的淬火深度而定。
用这种方法淬火,不会在工件表面形成蒸汽膜,这样就能够保证得到比昔通水中淬火更深的淬硬层。
为了消除因水流之间冷却能力不同所造成的冷却不均匀现象,水流应细密,最好同时工件上下运动或旋转.这种方法主要用于局部淬火。
用于局部淬火时,因未经水冷的部分冷却较慢,为了避免已淬火部分受未淬火部分残留热量的影响,工件一旦全黑,立即将整个工件淬入水中或油中.4.分级淬火法.把工件由奥氏体化温度淬人高于该种钢马氏体开始转变温度的淬火介质中,在其中冷却直至工件各部分温度达到淬火介质的温度,然后缓冷至室温,发生马氏体转变.这种方法不仅减少丁热应力,而且由于马氏体转变前,工件各部分温度已趋于匀匀,因而马氏体转变的不同时现象也减少。
分级淬火只适用于尺寸较小的工件.对于较大的工件,由于冷却介质的温度较高,工件冷却较缓慢,因而很难达到其临界淬火速度。
某些临界淬火速度铰小的合金钢没有必要采用此法,因为在油中淬火也不致于造成很大内应力.反之,若采用分级淬火来代替油淬,其生产效串并不能显著提高.淬火介质的温度可高于或略低于马氏体点,当低于马氏体点时,由于温度比较低,冷却较剧烈,故可用于较大工件的淬火.各种碳索工具钢和合金工具钢(Ms=200—250℃)淬火时,分级温度选择在250℃附近,但更经常选用120—150℃,甚至100℃。
分级温度选在低于Ms 点,是否还谓之分级淬火,尚有待商榷.因为一般分级淬火的概念是在分级温度等温后,取出缓冷时才发生马氏体转变,但在低于Ms点以下的温度等温后已发生了大量马氏体转变.分极保持时间应短于在该分级温度下臭氏体等温分解的孕育期,但应尽量使工件内外强度均匀。
分级后处于奥氏体状态的工件,具有较大的塑性(相变超塑性),因而创造了进行工件的矫直和矫正的条件.这对工具具有特别重要的意义.因而高于Ms点分级温度的分级淬火,广泛地应用于工具制造业.对碳钢来说,这种分级淬火适用于直径8一lOmm工具.若分级淬火温度低于Ms点,因工件自淬火剂中取出时,已有一部分奥氏体转变成马氏体,上述奥氏体状态下的矫直就不能利用。
但这种方法用于尺寸较大的工件(碳钢工具可达10—15mm直径)时,不引起应力及淬火裂缝,故仍被广泛利用.5.等温淬火法工件淬火加热后,若长期保持在下贝氏体转变区的温度,使之完成奥氏体的等温转变,获得下贝氏体组织,这种淬火称为等温淬火。
等温淬火与分级淬火的区别在于前者获得下贝氏体组织.进行等温淬火的目的是为了获得变形少,硬度较高并兼有良好韧性的工件。
因为下贝氏体的硬度较高而韧性又好,在等沮淬火时冷却又较慢,贝氏体的比容也比较小,热应力,组织应力均很小,故形状变形和体积变形也较小。
等温淬火用的淬火介质与分级淬火相同。
等温温度主要由钢的C曲线及工件要求的组织性能而定。
等温温度越低,硬度越高,比容增大,体积变形也相应增加。
因此,调整等温温度可以改变淬火钢的机械性能和变形规律,一般认为在Mc~Ms点+30℃沮度区间等温可获得良好的强度和韧性.。