最新橡胶工艺原理(十八)
橡胶 工艺 原理

橡胶工艺原理
橡胶是一种由橡胶树的乳液经过加工制成的具有弹性的材料。
橡胶的工艺原理主要包括以下几个方面。
1. 采集橡胶乳液:橡胶树的树干被割开后,乳液会自然流出。
采集工人使用刮刀将乳液慢慢刮下,收集到容器中。
2. 乳液稳定化:采集到的橡胶乳液中含有大量的水分和其他杂质,需要经过稳定化处理。
常用的稳定化剂包括氨水和醋酸,它们可以使乳液保持稳定状态,并防止乳液中的橡胶团聚。
3. 合成橡胶:乳液经过稳定化处理后,需要加入硫化剂、填充剂和加工助剂等多种化学物质进行合成橡胶的加工。
其中,硫化剂可以使橡胶分子之间的交联结构更加牢固,增加橡胶材料的强度和耐磨性;填充剂可以提高橡胶材料的硬度和耐磨性;加工助剂则可以调整橡胶材料的流动性和加工性能。
4. 橡胶成型:合成橡胶经过调配后,可以通过各种成型方法将其制成不同形状的橡胶制品。
常见的成型方法包括压延、压缩模压、浇注和挤出等。
5. 硫化和固化:成型后的橡胶制品需要进行硫化或固化处理,使其获得所需的弹性和耐磨性。
硫化是将成型的橡胶制品置于加热的硫化炉中,在一定温度下与硫化剂反应,形成较为稳定的交联结构;固化则是使用特定的固化剂或光线照射,使成型的橡胶制品的分子链交联,增加其硬度和强度。
通过以上的工艺原理,橡胶可以被制备成各种应用于工业、交通、建筑和日常生活中的橡胶制品,如轮胎、密封件、橡胶管、橡胶鞋等。
橡胶加工工艺
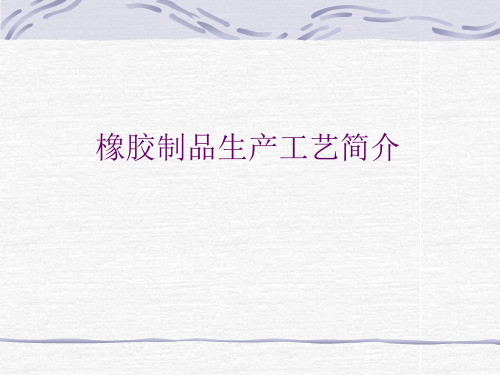
➢ 化学塑解剂:塑解剂的用量,在NR中一般为生胶重量的0.1~0.3%,合 成橡胶则应增大到2~3%。
橡胶制品生产工艺简介-塑炼工艺塑炼工艺
不同胶料开炼机混炼时辊筒温度
胶种
天然胶 丁苯胶 氯丁胶 丁基胶 丁腈胶 顺丁胶 三元乙丙胶 氯磺化聚乙烯 氟橡胶23—27 丙烯酸酯橡胶
橡胶制品生产工艺简介-塑炼工艺塑炼工艺
常用橡胶的塑炼特性
2. SBR ➢ 软SBR的初始门尼粘度一般在54~64之间,不需进行塑炼。 ➢ SBR采用机械塑炼效果不大,比较有效的方法时采用高温
塑炼法,以130~140℃温度最好,温度过高易生成凝胶。 3.BR ➢ BR一般不需要进行塑炼。 4.CR ➢ CR的初始门尼粘度都较低,一般不需要进行塑炼。但在储
➢ 物料在密炼室中主要受到几种作用: 转子间及转子与混炼室内壁间的作用;
转子棱间的搅拌作用;
转子轴向的往复切割作用。
➢ 优点:自动化程度高,生产效率高,节能,劳动强度低
➢ 缺点:温度高,冷却困难,易过炼,出料为无定形状
橡胶制品生产工艺简介-塑炼工艺塑炼工艺
密炼机
橡胶制品生产工艺简介-塑炼工艺塑炼工艺
存过程中其可塑性会下降,因此CR仍需经过塑炼加工,才 能获得所要求的可塑性。 ➢ CR宜采用开炼机进行塑炼,低温薄通塑炼效果最好。
橡胶制品生产工艺简介-塑炼工艺塑炼工艺
常用橡胶的塑炼特性
5.IIR ➢ 门尼粘度在38~75之间的品种一般不需要塑炼。 ➢ IIR采用机械塑炼效果不大,但用密炼机在120℃以上,并
且加入塑解剂进行高温塑炼则可取得较好的塑炼效果。 6.NBR ➢ NBR的塑炼应采用开炼机在低温(40℃以下)、小辊距
橡胶的压延工艺
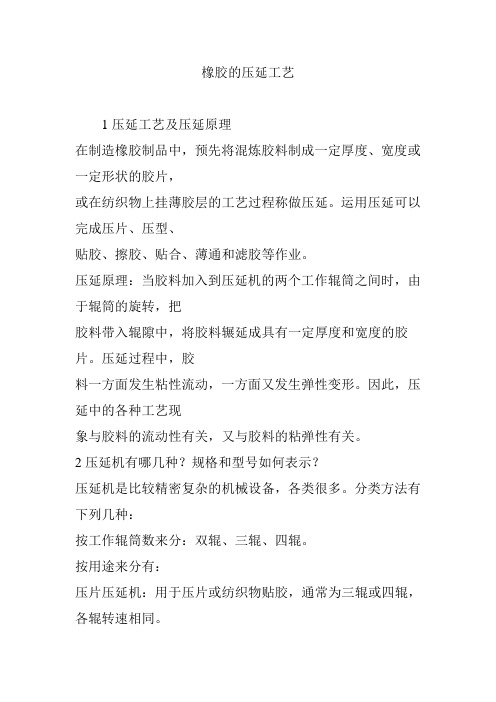
橡胶的压延工艺1压延工艺及压延原理在制造橡胶制品中,预先将混炼胶料制成一定厚度、宽度或一定形状的胶片,或在纺织物上挂薄胶层的工艺过程称做压延。
运用压延可以完成压片、压型、贴胶、擦胶、贴合、薄通和滤胶等作业。
压延原理:当胶料加入到压延机的两个工作辊筒之间时,由于辊筒的旋转,把胶料带入辊隙中,将胶料辗延成具有一定厚度和宽度的胶片。
压延过程中,胶料一方面发生粘性流动,一方面又发生弹性变形。
因此,压延中的各种工艺现象与胶料的流动性有关,又与胶料的粘弹性有关。
2压延机有哪几种?规格和型号如何表示?压延机是比较精密复杂的机械设备,各类很多。
分类方法有下列几种:按工作辊筒数来分:双辊、三辊、四辊。
按用途来分有:压片压延机:用于压片或纺织物贴胶,通常为三辊或四辊,各辊转速相同。
擦胶压延机:用于纺织物擦胶,通常为三辊,各辊之间有一定速比。
通用(万能)压延机:这种压延机兼有上述两种压延机的功能,通常为三辊或四辊,各辊的速比可借辅助齿轮调节。
压型压延机:用于制造表面带有花纹或有一定形状的胶片,其中有一个辊筒刻有花纹。
钢丝压延机:用于钢丝帘布的贴胶,由四个辊筒组成。
按辊筒的排列形式有:I型、△型、T型、L型、Z型、S型等。
压延机规格可用辊筒外直径×辊筒工作部分长度来表示,如压延机规格Φ610×1730。
我国压延机型号可表示为XY —4T—1730。
其中XY 表示橡胶胶压延机,4T表示四辊筒型排列。
1730表示辊筒工作部分的长度(mm)。
3在设计压延机时为什么需采用补偿措施在压延机加工过程中,当胶料通过辊距时,给予辊筒的横压力很高,加上辊筒自身的重量,致使辊筒会产生一定的弹性弯曲(其弯曲度称为挠度)结果使压延胶片出现中间厚两边薄的现象。
为了克服为种弊病,通常在设计压延机时,都采取一些补偿措施,以确保压延的精密度,常用的补偿方法有;凹凸系数法(中高法);轴交叉法和反弯曲法(予负荷法)等。
4什么叫压延效应,它对制品的性能有何影响?压延后的制品在纵横方向性能差异的现象叫做压延效应,即沿胶片纵方向(压延方向)的扯断强度大,伸长率小,收缩率大;而沿胶片横向的扯断强度小,伸长率大,收缩率小。
橡胶加工工艺—橡胶压出工艺(高分子成型课件)
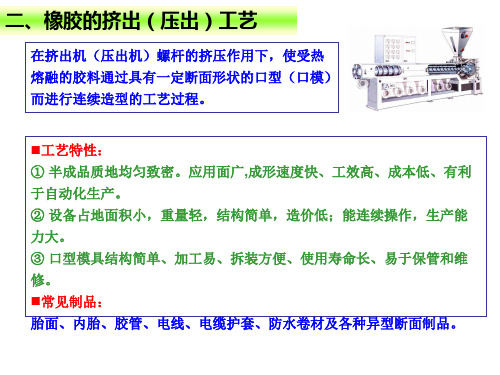
二、橡胶的挤出(压出)工艺
(一)压出机工作原理及胶料的运动状态 3 物料在口型中的流动状体和挤出变形 胶料经机头进入口型后,由于口型形状不同及内表 面对物料流动的阻碍,物料流动速度也存在有与机 头类似的速度分布。中间流速大,越接近口型壁流 速越小 。 一般粘弹性的物料,从口型挤出后就不可避免地存 在松弛现象,即:胶条的长度会沿挤出方向缩短, 厚度沿垂直挤出方向增加(离模膨胀现象或称作挤 出变形现象)。挤出后的变形(收缩和膨胀)可以控制 在一定范围,但不可能完全消除。要求收缩率为 2~5%。 物料可塑性小、含胶率大,填充剂用量小,物料挤 出快,机头和口型温度低,膨胀和收缩率就大。
二、橡胶的挤出(压出)工艺
在挤出机(压出机)螺杆的挤压作用下,使受热 熔融的胶料通过具有一定断面形状的口型(口模) 而进行连续造型的工艺过程。
工艺特性: ① 半成品质地均匀致密。应用面广,成形速度快、工效高、成本低、有利 于自动化生产。 ② 设备占地面积小,重量轻,结构简单,造价低;能连续操作,生产能 力大。 ③ 口型模具结构简单、加工易、拆装方便、使用寿命长、易于保管和维 修。 常见制品: 胎面、内胎、胶管、电线、电缆护套、防水卷材及各种异型断面制品。
二、橡胶的挤出(压出)工艺
(一)压出机工作原理及胶料的运动状态
1 胶料在挤出机中的运动状态
加料段:加入的条状胶料,受到旋转螺杆的推挤作用形成连续的胶 团,并沿着螺槽的空间一边旋转,一边不断前进。 压缩段:加料段输送过来的松散胶团在压缩段被逐渐压实、软化, 并把夹带的空气向加料段排出。同时胶团间间隙缩小,密度增高, 进而粘在一起,再加上受到剪切和搅拌作用,因而胶团逐渐被加热 塑化形成连续的粘流体。 挤出段:在挤出段,压缩段输送过来的物料进一步塑化均匀,并输 送到机头和口模处挤出成型。
HCR工艺原理及特点
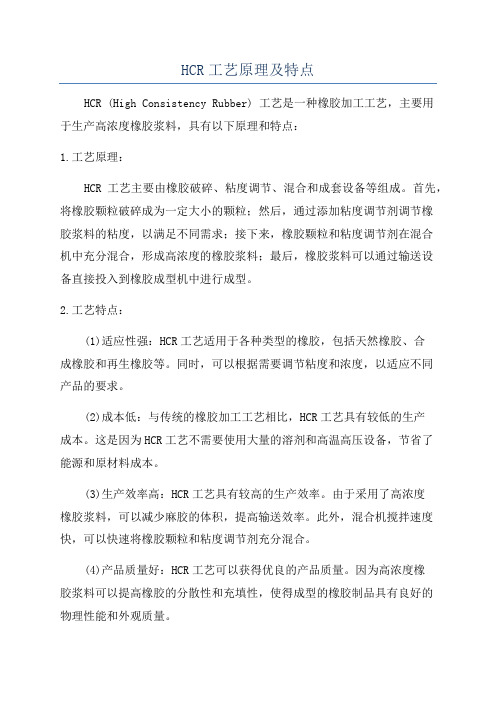
HCR工艺原理及特点HCR (High Consistency Rubber) 工艺是一种橡胶加工工艺,主要用于生产高浓度橡胶浆料,具有以下原理和特点:1.工艺原理:HCR工艺主要由橡胶破碎、粘度调节、混合和成套设备等组成。
首先,将橡胶颗粒破碎成为一定大小的颗粒;然后,通过添加粘度调节剂调节橡胶浆料的粘度,以满足不同需求;接下来,橡胶颗粒和粘度调节剂在混合机中充分混合,形成高浓度的橡胶浆料;最后,橡胶浆料可以通过输送设备直接投入到橡胶成型机中进行成型。
2.工艺特点:(1)适应性强:HCR工艺适用于各种类型的橡胶,包括天然橡胶、合成橡胶和再生橡胶等。
同时,可以根据需要调节粘度和浓度,以适应不同产品的要求。
(2)成本低:与传统的橡胶加工工艺相比,HCR工艺具有较低的生产成本。
这是因为HCR工艺不需要使用大量的溶剂和高温高压设备,节省了能源和原材料成本。
(3)生产效率高:HCR工艺具有较高的生产效率。
由于采用了高浓度橡胶浆料,可以减少麻胶的体积,提高输送效率。
此外,混合机搅拌速度快,可以快速将橡胶颗粒和粘度调节剂充分混合。
(4)产品质量好:HCR工艺可以获得优良的产品质量。
因为高浓度橡胶浆料可以提高橡胶的分散性和充填性,使得成型的橡胶制品具有良好的物理性能和外观质量。
(5)环保性好:HCR工艺对环境的影响较小。
与传统的橡胶加工工艺相比,HCR工艺不需要使用大量的溶剂和污水处理设备,减少了废物的排放和处理成本。
(6)工艺控制精度高:HCR工艺可以精确控制橡胶浆料的粘度、浓度和颗粒大小。
通过调节粘度调节剂的添加量和搅拌时间等参数,可以满足不同产品的要求。
总结起来,HCR工艺是一种适应性强、成本低、生产效率高、产品质量好、环保性好且工艺控制精度高的橡胶加工工艺。
该工艺在橡胶制品行业具有广泛应用前景。
橡胶加工工艺—橡胶压延工艺(高分子成型课件)
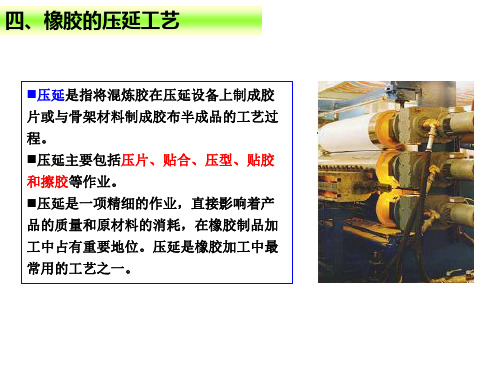
a,b-两辊压型(v1=v2); c-三辊压型(v1v2=v3); d-四辊压型(v2=v3=v4v1)
三、橡胶的压延工艺
(二)压延工艺方法 3 胶片贴合
胶片贴合:通过压延机将两层或多层薄胶片贴合在一起的工艺过程。
通常用于制造较厚、质量要求较高 的胶片和两种不同胶料组成的胶片、 夹布层胶片等。 贴合方法有二辊压延机贴合法、三 辊压延机贴合法、四辊压延机贴合法。 四辊压延机可一次同时完成两个新 鲜胶片的压延与贴合。贴合效率高、 质量好、精度高,但压延效应大。
三、橡胶的压延工艺
(二)压延工艺方法 1 压片
压片:利用压延机等速辊筒将胶料制成具有规定断面厚度和宽度的表面 光滑的胶片。胶片应表面光滑,无绉缩,内部密实,无孔穴、气泡或海绵; 断面厚度均匀,精度,各部分收缩变形一致。 设备:压片压延机一般为三辊或四辊压延机,但多采用三辊压延机
压片工艺分类: ①积胶压延法片材表 面光滑,密实,减少气泡,但会增大压 延效应,适于丁苯橡胶。②普通挤胶法 适于NR。
三、橡胶的压延工艺
(三)压延制品厚度的控制
1 沿辊筒轴线方向上厚度
三高两低现象
(1)辊筒的弹性弯曲变形(横压力) 辊筒弹性弯曲变形(横压力)使压延制品中间厚两边薄 克服方法: a 中高度补偿法 ; b 轴交叉法 ; c 预应力法 (2)辊筒表面温度 轴承润滑油带走部分热量,辊筒温度中间高两边低使压延制品两边 较中间厚。 克服方法: a 中间鼓风冷却; b 两边红外加热
厚擦法:T上>T下>T中; 薄擦法: T上>T中> T下
三、橡胶的压延工艺
(二)压延工艺方法 5 纺织物挂胶的工艺影响因素
(1)胶料的可塑度 为了保证胶料对布孔的充分渗透,胶料要有较高的可塑 度(比压片胶料大)。天然橡胶的贴胶可塑度为0.4-0.5、 擦胶可塑度为0.5-0.6较为合适。 (2)辊温 辊温控制比压片时高,以增大胶料的流动性及胶料与纺织 物间的附着力。但辊温过高易产生焦烧。
青岛科技大学橡胶工艺原理讲稿

青岛科技大学橡胶工艺原理讲稿( 5)青岛科技大学 , 橡胶, 讲稿 , 工艺, 原理§3-6 炭黑对橡胶的补强机理 炭黑补强作用使橡胶的力学性能提高,同时也使橡胶在粘弹变形中由粘性作用而产生的损耗因素提高。
例如 力软化效应提高。
因应力软化效应能够比较形象地说明大分子滑动补强机理,因此将两者结合一起讨论。
一.应力软化效应一)应力软化效应的含义3-18 所示,第二次拉伸的应力 - 应变曲线在第一次的下面。
若将第二次拉伸比增大超过第一次拉伸比处急骤上撇与第一次曲线衔接。
若将第二次拉伸应力去掉,恢复。
第三次拉伸,则第三次的应力应变曲线又会在第二次曲线下面。
随次数增加,下降减少,大约 4~5 次后达到平衡。
上述现象叫应力软化效应,也称为 应力软化效应用拉伸至给定应变所造成的应变能下降百分率( 3-10 )式中 W1 —第一次拉伸至给定应变时所需要的应变能; W2 —第一次拉伸恢复后,第二次(或更多次数)再拉伸至同样应变时所需的应变能。
(二) 应力软化效应的影响因素 应力软化效应代表一种粘性的损耗因素,所以凡是影响粘弹行为的因素对它均有影响。
填料及其性质对应力软化效应有决定性作用。
1 .填充的影响2.填料品种对应力软化效应的影响3.炭黑品种对应力软化效应的影响 总的趋势是补强性高的炭黑应力软化效应比较高,反之亦然。
(三) 应力软化的恢复应力软化有恢复性,但在室温下停放几天,损失的应力恢复很少,而在 100CX 24h 真空中能恢复大部分损失的应力。
因为炭黑的吸附是 动态的,在恢复条件下,橡胶大分子会在炭黑表面重新分布,断的分子链可被新链代替。
剩下的不能恢复的部分称为永久性应力软化作 用。
二.炭黑的补强机理近半个世纪以来,人们对炭黑补强机理曾进行了广泛的探讨。
各个作者提出的机理虽然能说明一定的问题,但有局限性。
随着时间进展, 橡胶补强机理也在不断地深化和完善。
橡胶大分子滑动学说的炭黑补强机理是一个比较完善的理论。
橡胶模压成型工艺原理
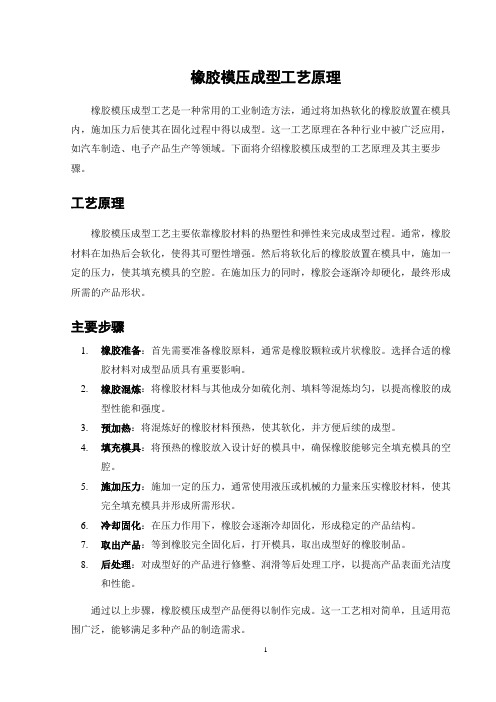
橡胶模压成型工艺原理橡胶模压成型工艺是一种常用的工业制造方法,通过将加热软化的橡胶放置在模具内,施加压力后使其在固化过程中得以成型。
这一工艺原理在各种行业中被广泛应用,如汽车制造、电子产品生产等领域。
下面将介绍橡胶模压成型的工艺原理及其主要步骤。
工艺原理橡胶模压成型工艺主要依靠橡胶材料的热塑性和弹性来完成成型过程。
通常,橡胶材料在加热后会软化,使得其可塑性增强。
然后将软化后的橡胶放置在模具中,施加一定的压力,使其填充模具的空腔。
在施加压力的同时,橡胶会逐渐冷却硬化,最终形成所需的产品形状。
主要步骤1.橡胶准备:首先需要准备橡胶原料,通常是橡胶颗粒或片状橡胶。
选择合适的橡胶材料对成型品质具有重要影响。
2.橡胶混炼:将橡胶材料与其他成分如硫化剂、填料等混炼均匀,以提高橡胶的成型性能和强度。
3.预加热:将混炼好的橡胶材料预热,使其软化,并方便后续的成型。
4.填充模具:将预热的橡胶放入设计好的模具中,确保橡胶能够完全填充模具的空腔。
5.施加压力:施加一定的压力,通常使用液压或机械的力量来压实橡胶材料,使其完全填充模具并形成所需形状。
6.冷却固化:在压力作用下,橡胶会逐渐冷却固化,形成稳定的产品结构。
7.取出产品:等到橡胶完全固化后,打开模具,取出成型好的橡胶制品。
8.后处理:对成型好的产品进行修整、润滑等后处理工序,以提高产品表面光洁度和性能。
通过以上步骤,橡胶模压成型产品便得以制作完成。
这一工艺相对简单,且适用范围广泛,能够满足多种产品的制造需求。
总的来说,橡胶模压成型工艺依靠橡胶材料的特性和适当施加的压力,实现了橡胶制品的高效成型。
它在现代工业生产中扮演着重要角色,为各行业提供了高品质、高性能的橡胶制品,推动了工业的发展与进步。
橡胶加工原理归纳整理(2012新)

一.名词解释∶1、冷流性:生胶或未硫化胶在停放过程中因为自身重量而产生流动的现象2、自补强性:在不加补强剂的条件下,橡胶能结晶或在拉伸过程中取向结晶,晶粒分布于无定形的橡胶中起物理交联点的作用,使本身的强度提高的性质。
如拉伸650%时,结晶度可以达到35%。
3、弹性:表示橡胶弹性变形能力的大小,受配方、硫化条件的影响,决定于交联密度。
4、回弹性: 指橡胶受到冲击后,能够从变形状态迅速恢复原状的能力。
受橡胶内耗的影响,内耗越大,回弹越小。
5.液体橡胶: 液体橡胶是一种分子量大约在2000~10000之间,在室温下为粘稠状流动液体,经过适当的化学反应可形成三维网状结构,从而获得和普通硫化胶具有类似的物理机械性能的齐聚物。
6、热塑性弹性体: 是高温下呈塑性流动状态,可以象塑料一样进行加工成型,不需要硫化,而常温下又具有橡胶的弹性。
这类材料兼有热塑性塑料的加工成型特征和硫化胶的弹性性能。
7.塑炼:为了便于对橡胶材料的加工,通常需要在一定的条件下,对其进行加工处理,使橡胶材料强韧的弹性转变为柔软而具有可塑性的状态,以获得必要的加工性能。
这种使弹性材料变为具有可塑性材料的工艺过程称为塑炼。
8.塑解剂:能提高塑炼效果,缩短塑炼时间,减小弹性复原,塑炼温度一般以70~75℃为宜。
9. 门尼粘度:一定温度100℃一定转子转速下,测未硫化胶对转子转动的阻力。
门尼粘度越小,流动性越好。
10. 混炼: 将各种配合剂混入并均匀分散在橡胶中的过程叫混炼, 混炼的实质是橡胶的改性过程,混炼不是生胶和配合剂简单的机械混合过程,混炼胶也不是生胶与配合剂的简单的机械混合物。
在混炼过程中,机械—化学反应起着重要作用,致使混炼胶由生胶和各种配合剂组成一种复合体11、半擦胶:常用三辊压延机完成,工艺与贴胶工艺基本相同,唯一差别是在纺织物引入压延机的辊隙处留有适量的积存胶料,借以增加胶料对织物的挤压和渗透.从而提高胶料对布料的附着力12、熔体破裂:高聚物熔体在挤出时,如果剪切速率过大超过一极限值时,从口型中出来的挤出物不再是光滑的,而会出现表面粗糙(鲨鱼皮现象)、波浪、竹节、螺旋型畸变,有时则会完全无规则破碎的现象。
隔震橡胶支座工艺原理
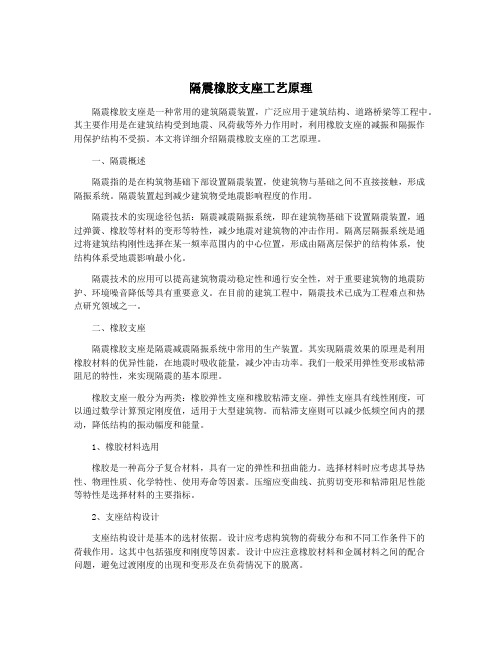
隔震橡胶支座工艺原理隔震橡胶支座是一种常用的建筑隔震装置,广泛应用于建筑结构、道路桥梁等工程中。
其主要作用是在建筑结构受到地震、风荷载等外力作用时,利用橡胶支座的减振和隔振作用保护结构不受损。
本文将详细介绍隔震橡胶支座的工艺原理。
一、隔震概述隔震指的是在构筑物基础下部设置隔震装置,使建筑物与基础之间不直接接触,形成隔振系统。
隔震装置起到减少建筑物受地震影响程度的作用。
隔震技术的实现途径包括:隔震减震隔振系统,即在建筑物基础下设置隔震装置,通过弹簧、橡胶等材料的变形等特性,减少地震对建筑物的冲击作用。
隔离层隔振系统是通过将建筑结构刚性选择在某一频率范围内的中心位置,形成由隔离层保护的结构体系,使结构体系受地震影响最小化。
隔震技术的应用可以提高建筑物震动稳定性和通行安全性,对于重要建筑物的地震防护、环境噪音降低等具有重要意义。
在目前的建筑工程中,隔震技术已成为工程难点和热点研究领域之一。
二、橡胶支座隔震橡胶支座是隔震减震隔振系统中常用的生产装置。
其实现隔震效果的原理是利用橡胶材料的优异性能,在地震时吸收能量,减少冲击功率。
我们一般采用弹性变形或粘滞阻尼的特性,来实现隔震的基本原理。
橡胶支座一般分为两类:橡胶弹性支座和橡胶粘滞支座。
弹性支座具有线性刚度,可以通过数学计算预定刚度值,适用于大型建筑物。
而粘滞支座则可以减少低频空间内的摆动,降低结构的振动幅度和能量。
1、橡胶材料选用橡胶是一种高分子复合材料,具有一定的弹性和扭曲能力。
选择材料时应考虑其导热性、物理性质、化学特性、使用寿命等因素。
压缩应变曲线、抗剪切变形和粘滞阻尼性能等特性是选择材料的主要指标。
2、支座结构设计支座结构设计是基本的选材依据。
设计应考虑构筑物的荷载分布和不同工作条件下的荷载作用。
这其中包括强度和刚度等因素。
设计中应注意橡胶材料和金属材料之间的配合问题,避免过渡刚度的出现和变形及在负荷情况下的脱离。
3、生产工艺橡胶支座生产的工艺流程包括原材料配比、橡胶混合、制模、硫化及安装等步骤。
橡胶制品的成型工艺介绍

橡胶制品的成型工艺介绍橡胶制品种类繁多,但其生产工艺过程,却基本相同。
以一般固体橡胶(生胶)为原料的制品,它的生产工艺过程主要包括:原材料准备塑炼混炼成型硫化修整检验(1)生胶的塑炼使弹性生胶转变为可埋状态的加工过程称为塑炼。
塑炼的目的是降低生胶的弹性、增加其可塑性,并且获得适当的流动性,以满足混炼,压延或压出成型、硫化以及胶浆制造、海绵胶制造等各种加工过程的要求。
塑炼有机械塑炼法和化学塑炼法。
前者通过塑炼机的机械破坏作用,降低生胶的弹性,获得一定的可塑性。
后者通过化学药品的化学作用,使生胶达到塑化的目的。
塑炼过程的实质是橡胶的大分子断裂成相对分子质量较小的分子,从而使黏度下降,可塑性增大。
(2)胶料的混炼将各种配合剂混入生胶中制成质量均匀的混炼胶的过程称为混炼。
其基本任务是制造出符合性能要求的混炼胶,使压延或压出成型、涂胶及硫化等后续工序得以正常进行。
混炼过程就是炭黑等配合剂在生胶中均匀分散的过程,配合剂每一颗粒的表面必须完全被橡胶包围和湿润。
用来制备塑炼胶、混炼胶的设备有开放式炼胶机(简称开炼机)、密闭式炼胶机(简称密炼机)。
开炼机的工作原理是两个异向向内旋转的中空辊筒以不同速度相对回转,两辊筒大小相同。
生胶或胶料随着辊筒的转动在摩擦力作用下被卷入两辊间隙。
由于两辊筒的转速不同而产生速度梯度作用,生胶或胶料受到强烈的摩擦剪切,橡胶的分子链断裂,在周围氧气或塑解剂的作用下生成相对分子质量较小的稳定分子,塑炼后橡胶的可塑性得到提高,混炼后可获得质量均匀的混炼胶。
橡胶制品的成形方法有哪些?一、模压成型常用模压方法来制造某些形状复杂如皮碗、密封圈的橡胶制品,借助成型的阴、阳模具将胶料放置在模具中加热成型。
阅读:橡胶模压制品的废次品的特征及产生原因二、挤出成型压出成型又称挤出成型,压出成型常用设备是橡胶挤出机,工作原理与塑料挤出机相似。
物料经过挤出机料斗进入料筒,通过料筒和旋转螺杆之间的作用,胶料边受热塑化,边被螺杆向前推送,连续通过机头并借助于口型模而制成各种复杂截面形状的制品或半制品,如轮胎的胎面胶、内胎胎筒、纯胶管、胶管内外层胶及电线和电缆的外皮等。
(完整版)橡胶生产工艺

橡胶制品的基本生产工艺过程4.1 基本工艺流程伴随现代工业尤其是化学工业的迅猛发展,橡胶制品种类繁多,但其生产工艺过程,却基本相同。
以一般固体橡胶(生胶)为原料的制品,它的生产工艺过程主要包括:原材料准备→塑炼→混炼→成型→硫化→休整→检验4.2 原材料准备橡胶制品的主要材料有生胶、配合剂、纤维材料和金属材料。
其中生胶为基本材料;配合剂是为了改善橡胶制品的某些性能而加入的辅助材料;纤维材料(棉、麻、毛及各种人造纤维、合成纤维)和金属材料(钢丝、铜丝)是作为橡胶制品的骨架材料,以增强机械强度、限制制品变型。
在原材料准备过程中,配料必须按照配方称量准确。
为了使生胶和配合剂能相互均匀混合,需要对某些材料进行加工:生胶要在60--70℃烘房内烘软后,再切胶、破胶成小块;块状配合剂如石蜡、硬脂酸、松香等要粉碎;粉状配合剂若含有机械杂质或粗粒时需要筛选除去;液态配合剂(松焦油、古马隆)需要加热、熔化、蒸发水分、过滤杂质;配合剂要进行干燥,不然容易结块、混炼时旧不能分散均匀,硫化时产生气泡,从而影响产品质量;4.3 塑炼生胶富有弹性,缺乏加工时的必需性能(可塑性),因此不便于加工。
为了提高其可塑性,所以要对生胶进行塑炼;这样,在混炼时配合剂就容易均匀分散在生胶中;同时,在压延、成型过程中也有助于提高胶料的渗透性(渗入纤维织品内)和成型流动性。
将生胶的长链分子降解,形成可塑性的过程叫做塑炼。
生胶塑炼的方法有机械塑炼和热塑炼两种。
机械塑炼是在不太高的温度下,通过塑炼机的机械挤压和摩擦力的作用,使长链橡胶分子降解变短,由高弹性状态转变为可塑状态。
热塑炼是向生胶中通入灼热的压缩空气,在热和氧的作用下,使长链分子降解变短,从而获得可塑性。
4.4 混炼为了适应各种不同的使用条件、获得各种不同的性能,也为了提高橡胶制品的性能和降低成本,必须在生胶中加入不同的配合剂。
混炼就是将塑炼后的生胶与配合剂混合、放在炼胶机中,通过机械拌合作用,使配合剂完全、均匀地分散在生胶中的一种过程。
橡胶(并用)共混原理,您真的了解吗?

橡胶(并用)共混原理,您真的了解吗?概述橡胶共混的意义:改善工艺性能,使用性能和技术经济性能。
大约 70%以上的橡胶是以橡胶并用或橡塑并用的形式进行加工和使用。
橡胶共混的内容:相容性形成均相体的能力:热力学相容、工艺相容共混物形态结构:连续相、分散相、界面配合剂在共混物中分布:硫化助剂、填料的分布,共交联和物性橡胶的工艺相容性:通过机械方法或其他条件将热力学不相容体系混合,可以获得足够稳定的共混物,这种共混物在微观区域内构成多相形态,但在宏观上仍能保持其均匀性。
聚合物共混影响因素:混炼工艺条件:时间、强度、辊温、加工方法配方组成:生胶、共混比、相容剂、加工助剂共混物形态结构的影响因素一是粘度不匹配引起的不相容性,由于粘度相差太大,并用胶难以形成紧密结合的共混物;二是热力学不相容性,从而使共混物难以形成分子级共混;三是由于硫化速率不匹配引起的硫化不相容性。
(1) 聚合物共混时的分散过程分散相平均粒径的大小决定于:混炼时间、混炼强度、分散相用量。
分散相宏观破碎能↓,相容性↑,界面张力↓,分散相体积分数↓,剪切速率↑,则:平均粒径↓(2) 相容性对共混物形态结构的影响聚合物相容性两种极端:完全不相容完全相容或相容性极好。
较好的共混改性物:分散相大小适宜、需要多相结构、相之间结合力较强。
对于单纯热力学不相容性,改进的方法很多,最常见的方法是添加增容剂。
(3) 组分浓度对共混物形态的影响组分体积分数 > 74%,连续相;< 26%,分散相;26-74% ,视具体条件而定。
当二者的初始粘度和内聚能接近时,浓度大者易形成连续相。
(4) 组分粘度对共混物形态结构的影响二者粘度相差越大,分散相体积分数↑,分散相粒径↓;二者粘度接近,分散相体积分数↑,分散相粒径↑;粘度低组分,连续相;粘度相近,“海-海”结构。
对于单纯的粘度不匹配导致的不相容性,可以选择合适的牌号或通过改进共混工艺过程如加增塑剂、填料等调节各相的粘度使之匹配。
橡胶浇注工艺
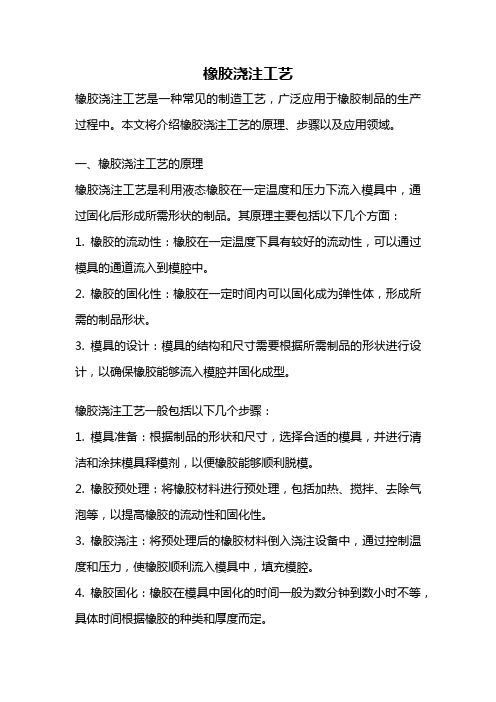
橡胶浇注工艺橡胶浇注工艺是一种常见的制造工艺,广泛应用于橡胶制品的生产过程中。
本文将介绍橡胶浇注工艺的原理、步骤以及应用领域。
一、橡胶浇注工艺的原理橡胶浇注工艺是利用液态橡胶在一定温度和压力下流入模具中,通过固化后形成所需形状的制品。
其原理主要包括以下几个方面:1. 橡胶的流动性:橡胶在一定温度下具有较好的流动性,可以通过模具的通道流入到模腔中。
2. 橡胶的固化性:橡胶在一定时间内可以固化成为弹性体,形成所需的制品形状。
3. 模具的设计:模具的结构和尺寸需要根据所需制品的形状进行设计,以确保橡胶能够流入模腔并固化成型。
橡胶浇注工艺一般包括以下几个步骤:1. 模具准备:根据制品的形状和尺寸,选择合适的模具,并进行清洁和涂抹模具释模剂,以便橡胶能够顺利脱模。
2. 橡胶预处理:将橡胶材料进行预处理,包括加热、搅拌、去除气泡等,以提高橡胶的流动性和固化性。
3. 橡胶浇注:将预处理后的橡胶材料倒入浇注设备中,通过控制温度和压力,使橡胶顺利流入模具中,填充模腔。
4. 橡胶固化:橡胶在模具中固化的时间一般为数分钟到数小时不等,具体时间根据橡胶的种类和厚度而定。
5. 脱模和后处理:橡胶固化后,将制品从模具中取出,进行脱模。
然后根据需要进行修整、清洁、检验等后处理工序。
三、橡胶浇注工艺的应用领域橡胶浇注工艺广泛应用于橡胶制品的生产中,主要包括以下几个领域:1. 汽车工业:橡胶浇注工艺可以用于汽车零部件的制造,如橡胶密封件、橡胶管件等。
2. 电子工业:橡胶浇注工艺可以用于电子产品的制造中,如橡胶按键、橡胶密封圈等。
3. 医疗器械:橡胶浇注工艺可以用于医疗器械的制造,如橡胶导管、橡胶垫片等。
4. 工程机械:橡胶浇注工艺可以用于工程机械的制造,如橡胶履带、橡胶振动器等。
5. 日用品:橡胶浇注工艺可以用于日用品的制造,如橡胶手柄、橡胶垫等。
橡胶浇注工艺是一种常见且重要的制造工艺,通过控制橡胶的流动性和固化性,以及合理设计模具,可以制造出各种形状的橡胶制品。
橡胶工艺原理-复习思考题-+答案

橡胶工艺原理-复习思考题-+答案(总12页)--本页仅作为文档封面,使用时请直接删除即可----内页可以根据需求调整合适字体及大小--《橡胶工艺原理》复习思考题名词解释碳链橡胶、硬质橡胶、杂链橡胶、混炼胶、硫化胶、冷冻结晶、拉伸结晶、极性橡胶杂链橡胶:碳-杂链橡胶: 主链由碳原子和其它原子组成全杂链橡胶:主链中完全排除了碳原子的存在,又称为“无机橡胶”,硅橡胶的主链由硅、氧原子交替构成。
混炼胶:所谓混炼胶是指将配合剂混合于块状、粒状和粉末状生胶中的未交联状态,且具有流动性的胶料硫化胶 : 配合胶料在一定条件下(如加硫化剂、一定温度和压力、辐射线照射等)经硫化所得网状结构橡胶谓硫化胶,硫化胶是具有弹性而不再具有可塑性的橡胶,这种橡胶具有一系列宝贵使用性能。
硬质橡胶:玻璃化温度在室温以上、简直不能拉伸的橡胶称为硬质橡胶一般来说,塑料、橡胶、纤维的分子结构各有什么特点影响橡胶材料性能的主要因素有哪些?橡胶性能主要取决于它的结构,此外还受到添加剂的种类和用量、外界条件的影响。
(1) 化学组成:单体,具有何种官能团(2) 分子量及分子量分布(3) 大分子聚集状况:空间结构和结晶(4) 添加剂的种类和用量(5) 外部条件:力学条件、温度条件、介质简述橡胶分子的组成和分子链结构对橡胶的物理机械性能和加工性能的影响。
答:各种生胶的MWD曲线的特征不同,如NR一般宽峰所对应的分子量值为30~40万,有较多的低分子部分。
低分子部分可以起内润滑的作用,提供较好的流动性、可塑性及加工性,具体表现为混炼速率快、收缩率小、挤出膨胀率小。
分子量高部分则有利于机械强度、耐磨、弹性等性能。
简述橡胶的分类方法。
答:按照来源用途分为天然胶和合成胶,合成胶又分为通用橡胶和特种橡胶;按照化学结构分为碳链橡胶、杂链橡胶和元素有机橡胶;按照交联方式分为传统热硫化橡胶和热塑性弹性体。
简述橡胶的分子量和分子量分布对其物理机械性能和加工性能的影响。
- 1、下载文档前请自行甄别文档内容的完整性,平台不提供额外的编辑、内容补充、找答案等附加服务。
- 2、"仅部分预览"的文档,不可在线预览部分如存在完整性等问题,可反馈申请退款(可完整预览的文档不适用该条件!)。
- 3、如文档侵犯您的权益,请联系客服反馈,我们会尽快为您处理(人工客服工作时间:9:00-18:30)。
最新橡胶工艺原理(十八)王作龄 编译中图分类号:TQ 330.1 文献标识码:E 文章编号:167128232(2004)0920047207第9章 混 炼9.1 引言对物质进行搅拌的操作被用于产品制造的各个领域。
在化工厂里将原料溶于反应槽中的溶剂中制造反应溶液,然后加入催化剂边搅拌边进行反应时,该搅拌的方法一般被称为搅拌。
在这样的装置中使用着各种形状的搅拌器。
根据溶液的粘度不同,平均1m 3溶液需要施加的搅拌能(搅拌所需的动力)大约为0.1~10kJ s ・m 3。
但是,作为橡胶的混炼则是基于具有各种功能和特性的橡胶配方设计,对生胶和配合剂进行混合的操作。
此时消耗的动力因为是对与水等完全不同的固体状生胶和配合剂进行混合的,所以这个能量非常大。
根据通用橡胶混炼使用的密炼机标准推算,平均1m3混炼胶所需的混炼能为几百至几千kJ s ,为前述搅拌消耗动力的几百倍至几万倍。
图9-1 橡胶加工流程图图9-1是橡胶加工流程示意图。
在该加工流程中,若混炼不当,则配方再好也不能得到应有的性能。
如表9-1所示,根据不同的目的,橡胶使用的配合剂有很多种,而且每一种都有作用。
例如,在防振胶垫的配方中,对于天然橡胶100份,加入合计91份的12种配合剂。
在橡胶工业中不是连续进行混炼,通常每一次混炼采用分批方式。
图9-2、图9-3分别是密炼机(in ternal m ixer )和开炼机(op en ro ll m ill )的示意图,橡胶混炼多用这两种机械。
图9-2 密炼机示意图1-底座;2-下顶栓;3-夹套;4-密炼室;5-机身;6-投料门;7-进料斗;8-活塞杆;9-风筒;10-冷却水管;11-加料斗壁;12-上顶栓;13-转子;14-卸料门离合器9.2 塑炼与混炼如图9-1所示,在橡胶加工操作中,炼胶操作由塑炼和混炼组成。
9.2.1 塑炼根据日本橡胶协会出版的《橡胶用语辞典》的解释,“塑炼”在英语中用“m asticati on ”表示,其定义是“对生胶施加机械剪切力,使分子聚集体分解并切断分子链,将橡胶的可塑度调整到容易加工水平的操作,有时使用塑解剂进行”。
用密炼机和开炼机对橡胶反复加以剪切变形和拉伸变形,切断较长的分子链,而且解除橡胶分子侧链间的相互缠结,使橡胶中的局部性粘度的高低平均化,并使橡胶具有均匀的可塑性和流动性,以达到容易混炼和成型加工操作的目的。
塑炼分为低温塑炼和高温塑炼。
图9-4为温度对天然橡胶塑炼效果的影响。
纵座标表9-1 各种配合剂的用途与种类配合剂用 途种 类交联剂交联1.二烯类橡胶:硫黄、有机硫化物、有机过氧化物、烷基酚醛树脂2.EPM 和硅橡胶等:有机过氧化物3.CR 、CHR 、氟橡胶、丙烯酸酯橡胶:多元胺、金属氧化物、多元醇促进剂促进交联反应硫黄交联:胺类、秋兰姆类、噻唑类促进助剂对促进剂活化硫黄交联:金属氧化物和脂肪酸防焦剂防止早期硫化芳香族有机酸、亚硝基化合物补强性填充剂提高橡胶的强度等炭黑、白炭黑、树脂类非补强性填充剂增加体积、降低成本碳酸钙、陶土等功能性填充剂赋予磁性、导电性等金属粉末、铁素体粉软化剂、增塑剂赋予软化和耐寒性、降低成本松焦油、石油系油、DO P 、DH P (NDR )粘合剂赋予粘性烷基酚醛树脂、石油树脂、松香塑解剂塑炼(降低分子量)五氯硫酚锌盐等防老剂防止氧、臭氧、金属离子等的老化芳香族胺类、酚类着色剂着色颜料、染料硬化剂提高硬度酚醛树脂、高苯乙烯树脂等发泡剂制造海绵橡胶N ,N ′2二亚硝基五亚甲基四胺等分散剂用于分散配合剂脂肪酸脱模剂改善制品脱模性内部填充型增粘剂增强粘合力、改善耐腐蚀性有机钴盐、H issei 2间苯二酚2六亚甲基四胺图9-3 开炼机示意图1-机架;2-辊筒轴承;3-挡胶板;4-调距装置;5-紧急刹车杆;6-齿轮;7-万向联轴节;8-减速器;9-紧急停车装置;10-电机;11-托料盘;12-底座;13-加热冷却装置;D -辊筒直径;L -辊筒表面长度图9-4 温度对天然橡胶塑炼效果的影响的塑炼效果是一定体积中塑炼橡胶分子数的增加分(N M -N M 0)被塑炼开始时的分子数N M 0除得出的商。
低温塑炼是在冷却下进行,温度越低分子链越容易断裂,在60℃以下塑炼效果好。
此外,高温塑炼在密炼机中进行,是在130℃以上通过分子链断裂生成的自由基与周围的氧结合产生自动氧化进行塑炼的。
9.2.2 混炼根据《橡胶用语辞典》的解释,“混炼”用英文表示为“m ix ing ,kneading ,com pouding ”,其定义是“将生胶和配合剂进行混合,施加机械剪切力,使橡胶具有可塑性,同时将填充剂和配合剂分散于橡胶中的操作”。
亦即,混炼是将配合剂均匀而且不形成聚集体混合分散到塑炼胶中的操作。
该操作是作为配合剂的粉粒体间的混合(m ix ing )、由高粘度物质的生胶润湿粉状体的捏合(kneading )和混炼(m illing ),或者是组合了粉状体在生胶中均匀分散(disp ersi on )和粉碎(grinding )的复杂的单元操作。
用密炼机混炼可在几分钟的短时间内使炭黑、交联剂、软化剂、防老剂等各种配合剂与塑炼胶混合,因此,密炼机中也有因橡胶粘性流动的生热和伴随为排除这种热而进行冷却等的热传递现象。
表9-2为氯丁橡胶注射成型加工的能耗。
其中,混炼所需的能耗很大,占全部能耗的70%以上。
因此,仔细领会混炼工序的目的,进行高效率的工序设计对于橡胶工业来说是极为重要的课题。
表9-2 氯丁橡胶注射成型加工的能耗加工工序能耗,GJ m 3混炼(密炼机3)2.8可塑化0.5注射成型0.3硫化0.2合计3.83本伯里密炼机9.3 混合与分散如上所述,混炼是由各种单元操作组合而成,但基本上就是关于配合剂的混合与分散。
关于混合、混炼、捏合和分散,日本学者池上把这些操作作为混合的操作进行如图9-5所示的分类。
如图9-5(a )、(b )所示,混合是对材料相互的排列进行均等分散配置,使材料粒子的初期形状发生变化并不是目的。
如图9-5(c )所示,所谓分散和混合就是通过分散聚集体作接近单一粒子的混合所推进的精细分散混合。
所谓混入是指在混合的同时如图9-5(d )那样均匀混入粉体粒子表面或粒子间隙的包覆作用,称之为混炼、捏合。
橡胶材料的物理性能根据橡胶中各种配合图9-5 混合操作的分类剂在某一阶段的分散状态如何而差异很大。
因此,为制造质量稳定、性能优异的橡胶制品,设定分散度的评价指标,同时进行混炼工序管理。
9.3.1 混合度和混合曲线如上所述,用密炼机和开炼机进行混炼是混合、混入、分散的操作搀杂的非常复杂的操作。
其中关于粉粒体的混合很大程度形成了定量操作和混合评价。
混炼和捏合基本属于掺混操作,因此考虑的方法大致相同。
图9-6为对具有均匀粒径的两种成分(白色A 粒子和黑色B 粒子)仅以相同个数进行混合过程的研究。
如图9-6(a )所示,混合开始处于完全分离状态,而后受到混炼作用而进行如图9-6(b )那样的混合。
但是,即使进行混合也不会变成黑、白粒子如晶格那样整齐且相互有规律排列的状态,实际上变成如图9-6(c )所示的黑、白粒子无规分散状态。
图9-6 混炼进行过程示意图a .混合度的定义基本混合度(degree of m ix ing ,M )的评价方法是评价浓度波动,测定浓度的试样从混炼胶的几个地方采取。
双组分体系混合度的定义式如表9-3所示。
在表中的定义式中,Ρ、Ρ0、Ρr 分别表示任意混合时间的标准偏差、混合开始时的标准偏差、完全混合状态的标准偏差,其表示式分别如下:表9-3 代表性混合度表示法分类混合度M的表示分离状态M0完全混合M r混合程度的表示1(Ρ20-Ρ2) (Ρ20-Ρ2r)0121-Ρ Ρ001 (Ρ20-Ρ2r) (Ρ2-Ρ2r)1∞Ρr ΡΡr Ρ1未混合程度的表示1Ρ Ρ01ΡrΡ02(Ρ2-Ρ2r) (Ρ20-Ρ2r)10 Ρ2-Ρ2rΡ20-Ρ2r01Ρ2Ρ20Ρ2r2ΡΡ0Ρr Ρ2=(∑(x i-x c)2) n(9.1)Ρ20=x c(1-x c)(9.2)Ρ2r=[x c(1-x c)] n(9.3)式中,x c为投料比(浓度);n为试样数量。
多组分体系混合物因存在各组分间的相互干涉等因素,所以其混合情况要比上述双组分体系混合物复杂得多,但在实用性上对于构成组分的最重要组分即关键组分多数取相同的处理方式。
b.混合曲线图9-7为粉体混合机的典型混合特性曲线(或混合曲线)。
这是以混合度M对从混合开始时测定的时间即混合时间t的变化绘制的曲线。
明确混合机内的混合状态和混合机理非常重要。
图中混合过程的初期区域 主要受对流混合支配;中间区域 通过对流混合和剪切混合进行粒子分散;在最终区域 中出现扩散混合效应,进行反复混合和分散,达到动态平衡状态,此时的混合度称为最终混合度。
图9-7 混合特性曲线9.3.2 粒径分布与分散度a.粒径分布用干法和湿法分散装置分散聚集的粉体和固体粒子时,分散前后的粒径可用各种方法进行测定。
分散进展如何可以粒径分布作为如图9-8(a)所示的透地率曲线表示,多以50%粒径d50作为该分布的代表粒径进行处理。
如图9-8(b)所示,50%粒径d50的变化对于分散时间的曲线,多用于分散进行的状况与分散的评价。
但是,对于将填充剂混炼分散于熔融的塑料中以及将各种配合剂混炼于生胶中的情形而言,与一般的粉碎和分散操作相比,测定分散于塑料和橡胶基质中粉体的粒径分布要困难得多。
b.炭黑的分散度基质中粉体的分散状态非常重要,它直接影响到制品的物理性能和质量。
在将由多成分组成的配合剂分散于橡胶时,分散所需要的能量和分散状态可作为参数使用。
例如,炭黑在橡胶中的分散状态如何可用以下各种方法进行评价人。
即:(a)平均粒子径d50(b)d50 d050与分散时间t的关系(d050为未分散①的平均粒径)图9-8 ①测定力矩或耗电量;②测定门尼粘度;③测定硫化胶的物理性能及其标准偏差; ④测定体积电阻系数及其标准偏差;⑤用显微镜测定分散度及其标准偏差。
炭黑分散状态的评价以前用肉眼判断,自1969年制定了A STM D2663之后用其A法(肉眼判断法)和B法(聚集块统计法)进行评价。
表9-4为A STM D2663(B法)的分类。
其中(a)为B法的分散度分类,(b)为按聚集块大小的分类。
炭黑在胶料中的分散度可按以下方法求出。
却,首先将用超薄切片机切成的非常薄的试样用粗汽油润湿,然后将试样平摊在显微镜用玻璃载片上,用目镜上装有带格玻璃的显微镜表9-4 AST M D2663-69(B法)的分类(a)分散度的分类项 目A B C D E F G H 分散度范围,%100~98.698.6~96.096.0~91.891.8~4.484.4~71.671.6~48.448.4~0(0)平均分散度,%99.397.393.988.178.060.030.0(0)范围宽1.42.64.27.412.823.248.4(0) (b)按聚集块的大小分类项 目123456聚集块平均面积,10Λm22.88.425.376228684聚集块平均直径,Λm19335798170295范围(10Λm2的筛孔数)0.5~4.94.9~14.714.7~43.943.9~128.4128.4~395.5395.5~∞观察,对各可见区计算炭黑聚集块超过12网络所占的网络的总数,取5个可见区的平均值为U,放大倍率为75~100倍。