新型高效离心式气液分离器设计与试验研究
气液分离器

气液分离器{气水分离器)翌SM^NG:鸵i气液分离器俗称油水分离器,用来分离气体中大于5微米的液体和固体颗粒。
是在气体中除油水的最简单实用的设备。
PX QF气液分离器可应用于对压缩空气、合成气、煤气、氢气、氮气、氧气、天然气、瓦斯气、沼气、氨气、硫化氢、尾气等各种气体的气液分离。
PX QF气液分离器设计制造符合国内或国外的各种标准和规范,如GB150《钢制压力容器》或ASME标准,并刻有CS及ASME钢印。
PX QF气液分离器工作原理通过五级分离—降速、离心、碰撞、变向、凝聚等原理,除去压缩空气(气体)中的液态水份和固体颗粒,达到净化的作用。
湿气在冷却过程中冷凝后,在分离器中的挡板廹使气体改变方向二次,并以设计好的速度旋转,产生离心力高效地分离出液体和颗粒,排水器应及时排放出冷凝液。
常安置在后冷却器的后面,因为要求进气温度越低越好,一般不超过60°C。
PXQF气液分离器产品特点1.除水效率高:可除去99%的液态水份,油份。
2.体积小、重量轻。
3.安装方便,管道式连接、可悬挂安装。
4.免维护、可靠性好。
5.寿命长:可使用20年。
6.按GB150压力容器标准制造,安全可靠。
PXQF气液分离器应用范围1.压缩空气冷凝水分离回收2.蒸汽管线冷凝水分离3.气液混合部位的进/出口分离4.真空系统中冷凝水分离排放5.水冷却塔后的冷凝水分离6.地热蒸汽分离器7.其他多种气液分离应用PXQF气液分离器PXQF DN65 400 600 159 360 18 自动放水阀HL10/1 PXQF DN80 510 760 219 420 42 自动放水阀HL13/1,20/1 PXQF DN100 580 850 273 480 60 自动放水阀HL40/1 PXQF DN125 580 850 273 480 60 自动放水阀HL60/1,70/1,80/1 PXQF DN150 650 990 426 630 120 自动放水阀HL100/1 PXQF DN200 630 1040 426 630 150 自动放水阀HL150/1 PXQF DN250 770 1180 478 680 200 自动放水阀325 HL200/1 PXQF DN300 840 1300 630 830 400 自动放水阀HL370/1 PXQF DN400 1180 1910 820 1090 600 自动放水阀HL370/1 PXQF DN450 2200 920 自动放水阀£气液分离器。
气液旋流器离心式分离器设计

气液旋流器离心式分离器设计介绍本文档旨在设计一种气液旋流器离心式分离器。
该分离器可用于将气体和液体分离,并具有高效率和可靠性。
设计原理气液旋流器离心式分离器基于离心力和旋流效应来实现气体和液体的分离。
当气体和液体混合进入分离器时,它们会在旋流器中形成旋转流动。
由于离心力的作用,液体会向外运动,被收集在分离器的外部。
而气体则沿着分离器的中心轴进一步向上排出。
设计要素1. 旋流器尺寸旋流器的尺寸是设计中的关键要素。
尺寸过小可能会导致分离效率降低,而尺寸过大则增加了设备的造价和能耗。
根据实际需求和操作参数,确定合适的旋流器尺寸。
2. 进出口形状和位置进出口的形状和位置会影响气体和液体在旋流器中的流动。
合理设计进出口形状和位置,可以提高分离效率和减少能耗。
需要根据具体情况选择最佳的进出口设计。
3. 分离器材料分离器的材料应具有良好的耐腐蚀性和耐压性能,以确保长期稳定运行并避免材料损坏。
根据分离介质的特性选择合适的材料,例如不锈钢、聚合物等。
4. 出口管道设计出口管道的设计对于分离效果和气体排放起着重要作用。
必须确保出口管道与旋流器的连接处无泄漏,并能够有效排出气体。
设计步骤1. 确定分离器的工作条件和需求。
2. 根据工作条件和需求,选择合适的旋流器尺寸和材料。
3. 设计进出口形状和位置,确保流动性和分离效果。
4. 设计出口管道,确保无泄漏和顺畅排出气体。
5. 检查设计是否符合安全和环保要求。
6. 制作设计图纸和说明文档,并提交给相关部门进行评审。
结论气液旋流器离心式分离器是一种高效率和可靠性的气液分离设备。
通过合理的设计和选择适当的工艺参数,可以实现高效的气液分离和能源节约。
在设计过程中,需要考虑旋流器尺寸、进出口形状、分离器材料和出口管道等要素。
最终的设计应符合安全和环保要求,并通过评审批准后开始制造。
气-液分离器设计

Re
=
Vt d * ρG µG
=
0.841× 350 ×10−6 14.6 ×10−6
×
4.9
= 98.8 由图2.5.1—1查得CW=1.25,由式(2.2.1—2)计算,得Vt=0.75,再由式(2.2.1—3)计算,得Re=88.4, 由图 2.5.1—1查得
近似估算法是根据分离器内的物料流动过程,假设Re=130,由图2.5.1—1查得相应的阻力系数CW=1, 此系数包含在Ks系数内,KS按式(2.2.1—1)选取。由式(2.2.1—1)计算出浮动(沉降)流速(Vt),再
设定一个气体流速(ue),即作为分离器内的气速,但ue值应小于Vt。
真正的物料流动状态,可能与假设值有较大的出入,会造成计算结果不准确,因此近似估算法只
4
SLDI 233A14-98
得 ALA = Ab + 2A1 = 0.107 + 2 × 0.4 = 0.289
ATOT
ATOT
3.14
查图2.5.1—5得 hLA = 0.333,从最低液位经2min后得到液面高度为 DT
hLA = 0.333 × DT = 0.333× 2000 = 666mm(hLA即是图中h)
间的时间间隔分别是2、1、1、2min。要计算对应时间间距的各液位高度。
解题:如图2.3.3所示。
最低液位,即液面起始高度(计算时间为0)的液位高度(hLL)为150mm。 容器横截面积(ATOT):
ATOT
= πDT2 4
=π
× 22 4
= 3.14m2
相当于液体在容器中停留时间为1min所占的横截面积为:
2.2 立式重力分离器的尺寸设计
2.2.1 分离器内的气速
气液分离器设计

文档来源为:从网络收集整理.word版本可编辑.欢迎下载支持.气—液分离器设计2005-04-15 发布2005-05-01 实施0文档来源为:从网络收集整理.word版本可编辑.欢迎下载支持.目次1 总则1.1 目的1.2 范围1.3 编制本标准的依据2 立式和卧式重力分离器设计2.1应用范围2.2 立式重力分离器的尺寸设计2.3 卧式重力分离器的尺寸设计2.4 立式分离器(重力式)计算举例2.5附图3 立式和卧式丝网分离器设计3.1 应用范围 3.2 立式丝网分离器的尺寸设计3.3 卧式丝网分离器的尺寸设计3.4 计算举例3.5 附图4 符号说明1 总则 1.1 目的本标准适用于工艺设计人员对两种类型的气—液分离器设计,即立式、卧式重力分离器设计和立式、卧式丝网分离器设计。
并在填写石油化工装置的气—液分离器数据表时使用。
1.2 范围本标准适用于国内所有化工和石油化工装置中的气-液分离器的工程设计。
1.3 编制本标准的依据:化学工程学会《工艺系统工程设计技术规定》HG/T20570.8-1995第8篇气—液分离器设计。
2 立式和卧式重力分离器设计 2.1 应用范围2.1.1 重力分离器适用于分离液滴直径大于200μm 的气液分离。
2.1.2 为提高分离效率,应尽量避免直接在重力分离器前设置阀件、加料及引起物料的转向。
2.1.3 液体量较多,在高液面和低液面间的停留时间在6~9min ,应采用卧式重力分离器。
2.1.4 液体量较少,液面高度不是由停留时间来确定,而是通过各个调节点间的最小距离100mm 来加以限制的,应采用立式重力分离器。
2.2 立式重力分离器的尺寸设计 2.2.1 分离器内的气速 2.2.1.1 近似估算法5.0⎪⎪⎭⎫ ⎝⎛-=G GL s t K V ρρρ (2.2.1—1)式中V t ——浮动(沉降)流速,m/s ;ρL 、ρG ——液体密度和气体密度,kg/m 3; K S ——系数d *=200μm 时,K S =0.0512; d *=350μm 时,K S =0.0675。
气液分离器的原理与完善(丝网式)
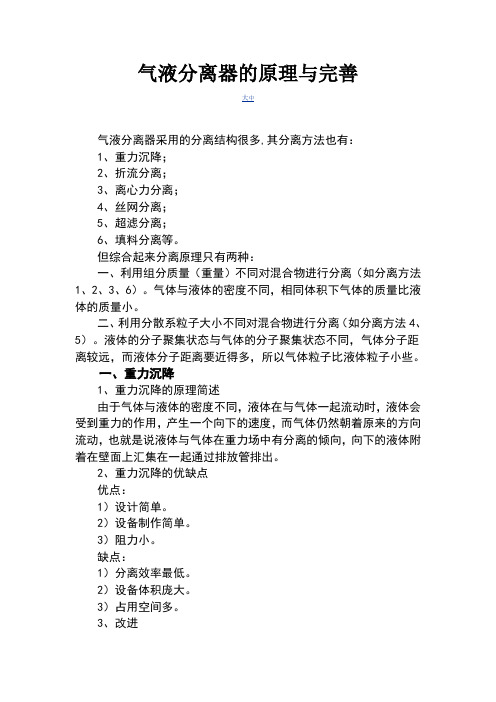
气液分离器的原理与完善大中气液分离器采用的分离结构很多,其分离方法也有:1、重力沉降;2、折流分离;3、离心力分离;4、丝网分离;5、超滤分离;6、填料分离等。
但综合起来分离原理只有两种:一、利用组分质量(重量)不同对混合物进行分离(如分离方法1、2、3、6)。
气体与液体的密度不同,相同体积下气体的质量比液体的质量小。
二、利用分散系粒子大小不同对混合物进行分离(如分离方法4、5)。
液体的分子聚集状态与气体的分子聚集状态不同,气体分子距离较远,而液体分子距离要近得多,所以气体粒子比液体粒子小些。
一、重力沉降1、重力沉降的原理简述由于气体与液体的密度不同,液体在与气体一起流动时,液体会受到重力的作用,产生一个向下的速度,而气体仍然朝着原来的方向流动,也就是说液体与气体在重力场中有分离的倾向,向下的液体附着在壁面上汇集在一起通过排放管排出。
2、重力沉降的优缺点优点:1)设计简单。
2)设备制作简单。
3)阻力小。
缺点:1)分离效率最低。
2)设备体积庞大。
3)占用空间多。
3、改进重力沉降的改进方法:1)设置内件,加入其它的分离方法。
2)扩大体积,也就是降低流速,以延长气液混合物在分离器内停留的时间。
4、由于气液混合物总是处在重力场中,所以重力沉降也广泛存在。
由于重力沉降固有的缺陷,使科研人员不得不开发更高效的气液分离器,于是折流分离与离心分离就出现了。
二、折流分离1、折流分离的原理简述由于气体与液体的密度不同,液体与气体混合一起流动时,如果遇到阻挡,气体会折流而走,而液体由于惯性,继续有一个向前的速度,向前的液体附着在阻挡壁面上由于重力的作用向下汇集到一起,通过排放管排出。
2、折流分离的优缺点优点:1)分离效率比重力沉降高。
2)体积比重力沉降减小很多,所以折流分离结构可以用在(高)压力容器内。
3)工作稳定。
缺点:1)分离负荷范围窄,超过气液混合物规定流速后,分离效率急剧下降。
2)阻力比重力沉降大。
3、改进从折流分离的原理来说,气液混合物流速越快,其惯性越大,也就是说气液分离的倾向越大,应该是分离效率越高,而实际情况却恰恰相反,为什么呢究其原因:1)在气液比一定的情况下,气液混合物流速越大,说明单位时间内分离负荷越重,混合物在分离器内停留的时间越短。
一种新型离心式气液分离器分离性能的数值模拟与试验研究
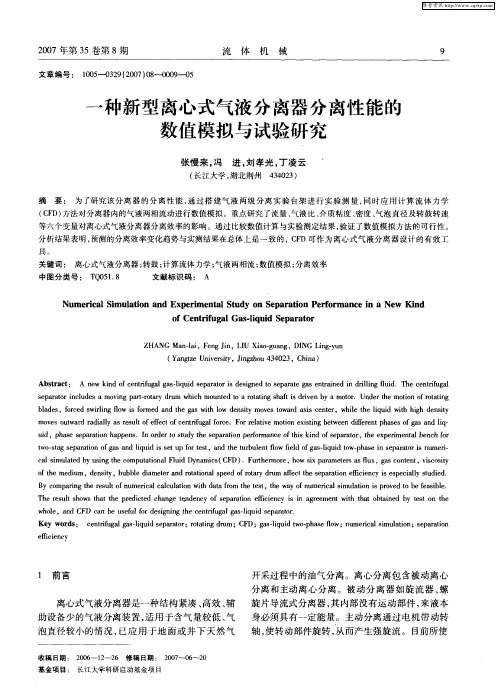
Ab t a t A n w k n f e t f g l a —iu d s p r tri d sg e o s p r t g se t ie n d l n u d sr c : e id o n r u a s l i e a ao e in d t e a ae a n r n d i r l g f i .T e c n r u a c i g q s a i i l h e t fg i l s p r tri cu e vn a t o ay d u wh c u td t ar t t g s a t sd v nb tr U d rte moin o oa ig e a ao n l d sa mo ig p r r tr r m i h mo ne o o ai h f i r e y a moo . n e t f tt - n i h o r n
b a e ,fr e wi i g f w i fr d a d te g s w t o e st v s tw r xsc ne ,w i h iu d w t ih d n i ld s oc d s r n o s o me n h a i lw d n i mo e o a d a i e tr h l t e l i i hg e st l l h y e q h y mo e uwa d r d al sr s l o f c fc n r u a o c .F rrl t e mo in e it g b t e n d f r n h e fg sa d l — v s o t r a il a e u t f f to e t f g f r e o e ai t x si e w e i e e t a s o n i y ee i l v o n f ps a q
井下离心旋流式高效油气分离器性能模拟试验

摘要 现 有井 下油 气分 离器效 率 较低 , 已不 能 满足 高 油 气 比油 井 的生 产 需要 ,为 了解决 高含
气井 中井下 多相 混抽 泵或 电潜泵 的使 用 与效 率低 等 问题 ,开 展 了井 下离心 旋 流 式高 效 油 气分 离器
的研 究。该 分 离器采 用 2级 串联结 构 , 以水 力旋 流器 为 第 1级 ;以对 结构 进 行 了优 化 改造 的离心 旋 转式分 离器为 第 2级 。通 过试 制 样机 的 室内模 拟试 验 ,验 证 了新 设 计 的井 下 离心 旋流 式高 效油 气分 离器 的分 离效率 ,总分 离效 率可达 9 % 以上 ,其 对含 气体 积分 数 的适 应 范 围 由原分 离器 的 0 5
( 脱克 斯力 ) 的束 缚 ,气 相 形成 内旋 流 ,在 沿径 斯
向 向轴 心移 动的 同时 向上 经溢 流 口排 出 ;而液相形
成 外旋 流沿径 向 向旋 流器 壁运 动 ,同时在 重力作用 下 ,沿旋 流 器 壁 向下 做 螺 旋 移 动 ,最 后 从 底 流 口
流出。
分 离器 结 构及 工作 原 理
级 、分 选设 备 ,具 有 结 构 简 单 、成 本 低 廉 、体 积
小 、处 理 能 力 大 、分 离 粒 径 小 的 特 点 J 。水 力 旋
流 器本 身没有 运动 部件 ,但能将 不 同密度 的物质通
过离心 力和重 力 的双重作 用进 行分 离 。其 气液分 离 机 理为 :气液 混合 物 以一 定 的高速度 切 向进 入旋 流 器 内表 面 ,切 向速 度使气 相与 液相 因密度 差产生 不 同的离 心 力 ,从 而 使 气 相 与 液 相 之 问摆 脱 粘 着 力
维普资讯
气液分离器分离效果仿真研究

在一定的试验基础上采用数值模拟计算可以
收 稿 日 期 :2016-〇4-18
作者简介:孙 李 ,本 科 ,合肥通用机电产品检测院市场服务部部长_丨1的主要研究领域足制冷令调设备检测方法。
第2期
孙 李 :气液分离器分离效果仿真研究
பைடு நூலகம்
•23 •
从机理上 更 好 地 指 导 气 液 分 离 器 的 优 化 设 计 ,减 少 试 验 量 ,降 低 试 验 成 本 ,提 高 经 济 效 益 。因 此 , 本 文 基 于 计 算 流体力学基本数学模型,建立了多 联机空调系统 内 部 气 液 分 离 器 的 仿 真 模 型 ,进行 计 算 分 析 ,并 对 其 结 构 进 行 了 优 化 设 计 。
Numerical research of separating effect for gas-liquid separator
高效离心式气液分离器模拟实验
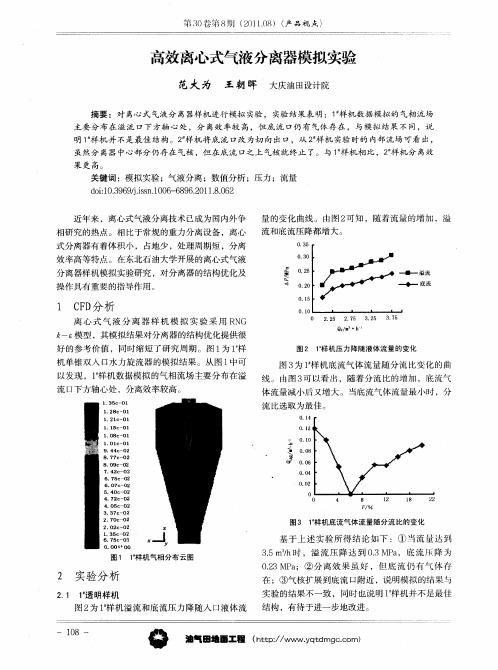
2 实验分析
2 1 1透 明样机 .
图2 1 为 样机溢流和底流压力降随人 口液体流 结构 ,有 待 于进一 步地 改进 。
— —
18— 0 —
油. 田地面工程 ( _ ‘
h t :/ c .q d n c c r ) t p/ vww y t r g .o n
3 苍 8 ( 0 1 g 产 品视 点) ( ) 期 2 1 . )( O
果 更 高。
毗 毗 毗毗 叭
乏 毗 芎∞ ; ;
关键 词 :模拟 实验 ;气 液分 离 ;数值 分析 ;压 力 ;流量
d i 0 9 9jsn1 0 — 8 62 1 ..6 o: . 6 /i . 6 6 9 . 180 2 13 .s 0 0
近年 来 ,离 心式气 液 分离 技术 已成 为 国 内外 争 量 的变 化 曲线 。 由图 2 知 ,随 着流 量 的增 加 ,溢 可 相研 究 的热点 。相 比于常 规 的重力 分离 设备 ,离心 流 和底 流压 降都增 大 。 式分 离 器有着 体 积小 ,占地少 ,处 理周 期短 ,分离 效率 高 等特 点 。在东 北石 油 大学开 展 的离 心式 气液 分离 器 样机模 拟 实验 研究 ,对 分离 器 的结 构优 化及 操作 具有 重要 的指导作 用 。
0 1 .4 0 1 .2
0 0 .1
上
0 O8 .
口
O. O6
O0 .4
0. O2 0
0
4
8
1 2
Байду номын сангаас
1 8
2 2
l % : f
图3 1样机底流气体流量随分流 比的变化
基 于上 述 实验 所 得 结 论 如下 :① 当流 量 达 到
气旋浮高效油水分离器试验研究
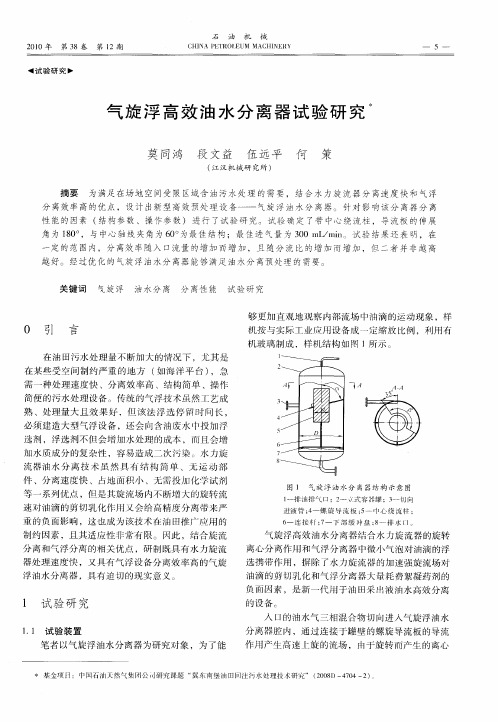
2 试 验 结 果 及 分 析
2 1 结 围的水 而结 合并上 升 ,通
过 气泡 的一 k升对油 滴进行 浮选 ,在 罐 和中心绕 流柱 之 间 、入 口及 其上 方就形 成 了一个 旋流 、脱气 和浮
选 。 由气 泡吸 附的较 小油滴 逐渐 凝 聚 ,结合 产生 较 大 的油滴 通过顶 部 的排油 排气 口连续 不断地 被清
摘 要 为 满足 在 场地 空 间受 限 区域含 油 污水 处 理 的 需要 ,结 合 水 力旋 流 器 分 离速度 快和 气浮
分 离效 率 高 的优 点 ,设计 出新 型高效 预处 理 设 备—— 气旋 浮 油水 分 离 器 。针 对 影 响该 分 离器 分 离
性能 的 因素 ( 结构 参 数 、操 作参 数 )进 行 了试 验 研 究。试 验 确定 了带 中心 绕流 柱 ,导 流板 的伸展
基金项 目:巾圈石油灭然气集刚公 『研究课题 “ d 樊东 南堡油 田回注污水处理技术研究” (0 8 4 0 20 D一 7 4—2 )
石 油
机
械
21 00年
第3 8卷
第1 2期
力作 用 ,密 度较 大 的水将 向罐壁 移动 ,而 油滴 和气 泡等 较轻成 分将 被 压 向罐 中间 ,到 达 中心 绕 流 柱 ,
越好 。经 过优 化 的 气旋 浮油 水分 离器 能够 满足 油水分 离预 处理 的需要 。 关 键词 气旋 浮 油 水分 离 分 离性能 试 验研 究
够 更加 直 观地观 察 内部流 场 中油滴 的运动 现象 ,样
0 引 言
在 油 田污水 处理 量不 断加 大 的情 况下 ,尤其是
加水 质成分 的复杂性 ,容 易造成 二 次污染 。水 力旋 流器 油水 分 离 技 术 虽 然 具 有 结 构 简 单 、无 运 动 部
气液分离器的设计
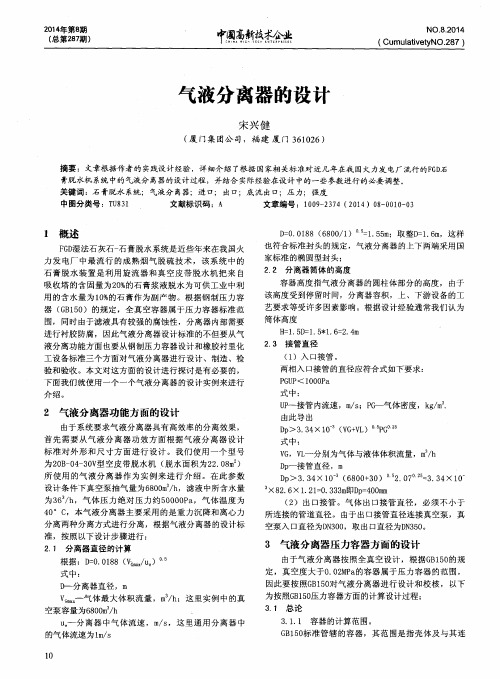
D = O . 0 1 8 8( 6 8 0 0 / 1 ) = 1 . 5 5 m ;取 整D = I . 6 m ,这 样
也 符合 标 准封 头 的规定 ,气 液分 离器 的上下 两端 采用 国
家 标准 的椭 圆型封 头 ;
2 . 2 分 离器简 体 的高度 容 器 高度 指气 液分 离器 的圆柱 体 部分 的 高度 , 由于 该 高度 受 到停 留 时间 ,分 离器容 积 ,上 、下游 设 备 的工
×8 2 . 6 ×1 . 2 1 = 0 . 3 3 3 m  ̄ g D p = 4 0 0 m m
( 2 ) 出 口接 管 。气 体 出 口接 管 直径 ,必 须 不 小 于 所连 接 的管 道直 径 。 由于 出 口接 管直 径连接 真 空泵 ,真 空泵 入 口直径 为D N 3 0 0 ,取 出 口直径 为D N 3 5 0 。
因此要按照G B 1 5 0 对气液分离器进行设计和校核,以下 为按照G B 1 5 0 压力容器方面的计算设计过程 ;
3 . 1 总 论
u 一分离器 中气体流速 ,m / s ,这里通用分离器 中 的气体 流速 为 i m / s
1 0
3 . 1 . 1 容器 的计 算范 围 。 G B I 5 0 标 准 管辖 的容 器 ,其 范 围 是指 壳 体 及 与其 连
2 气液 分离 器功 能方 面的 设计
由于 系统 要 求气 液 分离 器具 有 高效 率 的分 离效 果 ,
式 中: U P 一接 管 内流速 ,m / s ;P G 一 气体 密度 ,k g / m 。 .
由此 导 出
D p> 3 . 3 4×1 0 一 。( V G + V L)。 ・ P G 。
基于CFD的离心式气-液分离器结构设计及仿真优化
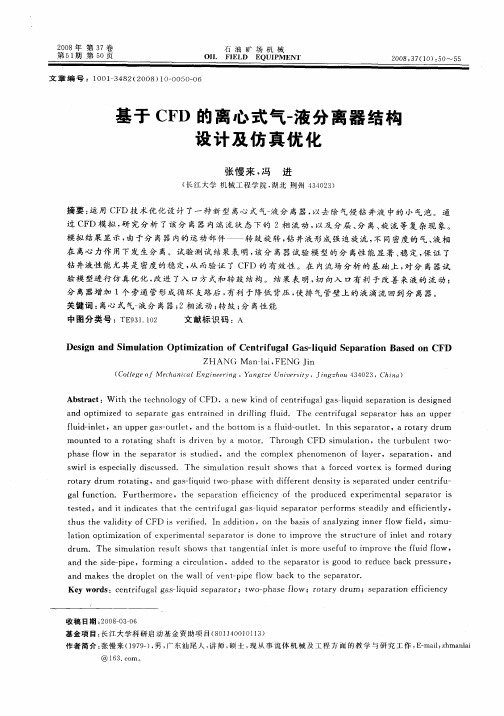
在 离心 力作 用 下发 生分 离。试验 测试 结果表 明 , 分 离 器试验 模 型 的 分 离性 能 显著 、 定 , 该 稳 保证 了
钻井液 性能 尤其是 密度 的稳 定 , 而验证 了 C D 的 有 效性 。在 内流 场 分析 的 基 础上 , 分 离器试 从 F 对
验 模 型进行 仿真 优化 , 改进 了入 口方 式和转 鼓 结构 。结 果表 明 , 向入 口有 利 于改善 来液 的 流动 ; 切
文献标 识码 : A
De i n a d S m u a i n Optm i a i n o nti u a slqu d S p r to s d o sg n i l to i z to f Ce rf g lGa —i i e a a i n Ba e n CFD
分 离 器 增 加 1个 旁 通 管 形 成 循 环 支 路 后 , 利 于 降 低 背 压 , 排 气 管 壁 上 的 液 滴 流 回 到 分 离 器 。 有 使 关 键 词 : 心 式 气一 分 离 器 ; 流 动 ; 鼓 ; 离 性 能 离 液 2相 转 分
中图分 类号 : E 3.0 T 9 112
过 C D模 拟 , 究分析 了该 分 离器 内湍 流状 态下 的 2相 流 动 , F 研 以及 分层 、 离、 流 等 复 杂现 象。 分 旋
模 拟 结 果 显 示 , 于 分 离器 内的 运 动 部 件 —— 转 鼓 旋 转 , 井 液 形 成 强 迫 旋 流 , 同 密 度 的 气 、 相 由 钻 不 液
r t r r m o a i o a y d u r t tng,a d g s lq d t o ph s t if r ntd n iy i e a a e nd rc nt iu— n a —i ui w a e wih d fe e e st ss p r t d u e e rf
气液分离器的原理与完善(丝网式)

气液分离器的原理与完善字体大小:- - 发布于2008-11-03 阅读(0)气液分离器采用的分离结构很多,其分离方法也有:1、重力沉降;2、折流分离;3、离心力分离;4、丝网分离;5、超滤分离;6、填料分离等。
但综合起来分离原理只有两种:一、利用组分质量(重量)不同对混合物进行分离(如分离方法1、2、3、6)。
气体与液体的密度不同,相同体积下气体的质量比液体的质量小。
二、利用分散系粒子大小不同对混合物进行分离(如分离方法4、5)。
液体的分子聚集状态与气体的分子聚集状态不同,气体分子距离较远,而液体分子距离要近得多,所以气体粒子比液体粒子小些。
一、重力沉降1、重力沉降的原理简述由于气体与液体的密度不同,液体在与气体一起流动时,液体会受到重力的作用,产生一个向下的速度,而气体仍然朝着原来的方向流动,也就是说液体与气体在重力场中有分离的倾向,向下的液体附着在壁面上汇集在一起通过排放管排出。
2、重力沉降的优缺点优点:1)设计简单。
2)设备制作简单。
3)阻力小。
缺点:1)分离效率最低。
2)设备体积庞大。
3)占用空间多。
3、改进重力沉降的改进方法:1)设置内件,加入其它的分离方法。
2)扩大体积,也就是降低流速,以延长气液混合物在分离器内停留的时间。
4、由于气液混合物总是处在重力场中,所以重力沉降也广泛存在。
由于重力沉降固有的缺陷,使科研人员不得不开发更高效的气液分离器,于是折流分离与离心分离就出现了。
二、折流分离1、折流分离的原理简述由于气体与液体的密度不同,液体与气体混合一起流动时,如果遇到阻挡,气体会折流而走,而液体由于惯性,继续有一个向前的速度,向前的液体附着在阻挡壁面上由于重力的作用向下汇集到一起,通过排放管排出。
2、折流分离的优缺点优点:1)分离效率比重力沉降高。
2)体积比重力沉降减小很多,所以折流分离结构可以用在(高)压力容器内。
3)工作稳定。
缺点:1)分离负荷范围窄,超过气液混合物规定流速后,分离效率急剧下降。
离心式气液分离器内流场的数值模拟与结构优化
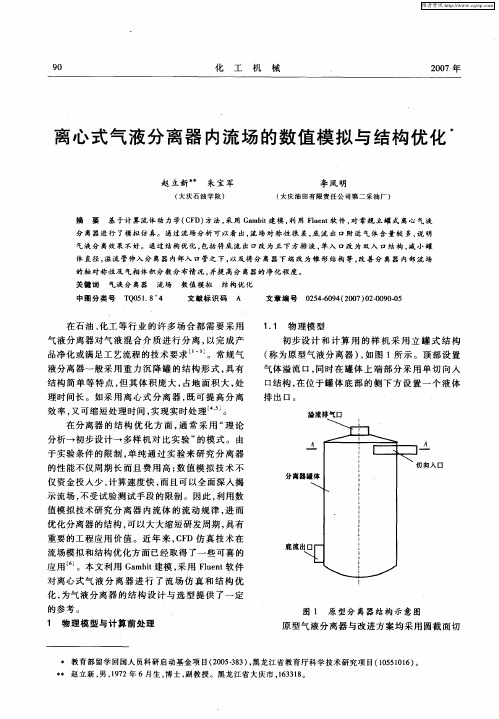
分 离
值模拟 技术 研究 分 离器 内流 体 的 流动 规 律 , 而 进 优化分 离器 的结构 , 以大大缩 短研 发周期 , 有 可 具 重要 的工程应 用 价 值 。近年 来 , F C D仿 真 技 术 在 流场模 拟 和结构 优化方 面 已经 取得 了一些 可喜 的 应 用 。本文 利用 G m i建模 , 用 Fu n 软件 a bt 采 le t 对离心 式 气 液分 离 器 进 行 了流 场 仿 真 和结 构 优 化, 为气 液分 离器 的结构 设 计 与 选 型提 供 了一定 的参考 。 图 1 原型 分 离器结构 示意 图
对较 低 。从 图 5还可 发 现 , 在入 口管 附 近还 存 在
一
个 明显 的循环 流 ( 涡流 ) 区域 , 一 方 面会 造成 这
流场紊 乱 , 另外 涡流也 会加 大 分离器 的压 力损耗 。 由此 可见 , 该结 构分 离器不 利 于气液 分离 , 需进 行
改进 和优化 设计 。
维普资讯
化
工
机
械
20 0 7焦
离 心式 气 液分 离器 内流场 的数 值 模 拟 与 结构 优 化
赵 立新 朱宝 军
李凤 明
( 庆 油 田有 限 责 任 公 司 第 二 采 油厂 ) 大
( 庆石油学院) 大
摘
要
基 于计 算 流 体 动 力 学 ( F 方 法 , 用 G mb 建模 , 用 Fun 软 件 , 常 规 立罐 式 离心 气 液 C D) 采 a i t 利 l t e 对
维普资讯
第 3 4卷
第 2期
化
工 机
气液分离器设计范文
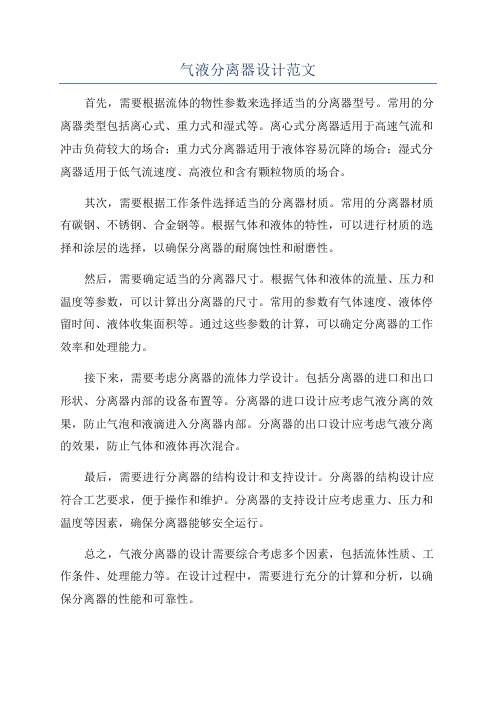
气液分离器设计范文
首先,需要根据流体的物性参数来选择适当的分离器型号。
常用的分离器类型包括离心式、重力式和湿式等。
离心式分离器适用于高速气流和冲击负荷较大的场合;重力式分离器适用于液体容易沉降的场合;湿式分离器适用于低气流速度、高液位和含有颗粒物质的场合。
其次,需要根据工作条件选择适当的分离器材质。
常用的分离器材质有碳钢、不锈钢、合金钢等。
根据气体和液体的特性,可以进行材质的选择和涂层的选择,以确保分离器的耐腐蚀性和耐磨性。
然后,需要确定适当的分离器尺寸。
根据气体和液体的流量、压力和温度等参数,可以计算出分离器的尺寸。
常用的参数有气体速度、液体停留时间、液体收集面积等。
通过这些参数的计算,可以确定分离器的工作效率和处理能力。
接下来,需要考虑分离器的流体力学设计。
包括分离器的进口和出口形状、分离器内部的设备布置等。
分离器的进口设计应考虑气液分离的效果,防止气泡和液滴进入分离器内部。
分离器的出口设计应考虑气液分离的效果,防止气体和液体再次混合。
最后,需要进行分离器的结构设计和支持设计。
分离器的结构设计应符合工艺要求,便于操作和维护。
分离器的支持设计应考虑重力、压力和温度等因素,确保分离器能够安全运行。
总之,气液分离器的设计需要综合考虑多个因素,包括流体性质、工作条件、处理能力等。
在设计过程中,需要进行充分的计算和分析,以确保分离器的性能和可靠性。
高效气液分离器效果评价_0

高效气液分离器效果评价【摘要】靖边气田开发初期,分离器是按照纯气层的地质状况设计的,主要用在脱水撬前对天然气进行分离,目的是分离出天然气中的游离水及携带的固体杂质,避免高矿化度的游离水及固体杂质进入脱水撬,影响脱水撬的正常运行。
但随着气田的不断开发,使得原有的分离器无法对气液进行有效分离,个别集气站露点不合格,脱水撬结晶盐堵塞等问题频繁发生。
本文对国内外常用分离器的分离特性及发展概况进行了调研,对强制旋流吸收吸附分离器和立式精细聚结分离器的结构原理及靖边气田现场试验应用情况进行效果评价,为靖边气田在开发中后期气液分离器的选型提供一定的参考依据。
【关键词】立式气液聚结分离器强制旋流吸收吸附分离器效果评价1 靖边气田气液分离器结构性能对比1.1 双筒卧式重力分离器内部构造及工作原理靖边气田气液分离器主要采用的是双筒卧式分离器,其内部设置有导流板、波纹板、丝网捕雾器等部件,各部件通过重力沉降、直接拦截、惯性碰撞,实现天然气中游离水的脱除。
可分离单井来气的气体中所携带的大于8μm固体颗粒和大于15μm的液滴及0.5μm的液雾等。
该分离器由分离立管、集液包、气进口、气出口、和排液口等组成。
流体经气液入口进入分离器内,在螺旋型通道中由下向上作强制性旋转运动,使流体产生离心力,在离心力的作用下,离心力大的液滴向吸收吸附层聚集。
吸收吸附层是具有良好弹性的孔网材料,可以有效的吸收经离心作用“甩”向外壁的液滴动能,更有利于液滴的吸附;同时可以有效地克服器壁对液滴的反作用力,降低液滴的离散作用,使旋流分离作用得到更好的发挥。
被吸附的液滴不断聚结,在重力作用下经吸收吸附层与筒体之间的间隙向下沉降流入筒体下部,从液体出口排出;而前面未被吸收吸附层吸收或被反弹回流体的液滴又在强制作用、离心力作用、吸收吸附作用下,不断重复液滴聚集、气液分离过程,从而使液滴不断地从流体中分离出来。
脱除液滴后的气体则经中心立管从气体出口流出。
完成强吸分离功能的分离立管,是由管壳体、吸收吸附层、中心立管和螺旋型隔板四部分组成。
离心式气液分离器主要结构参数分析_冯进
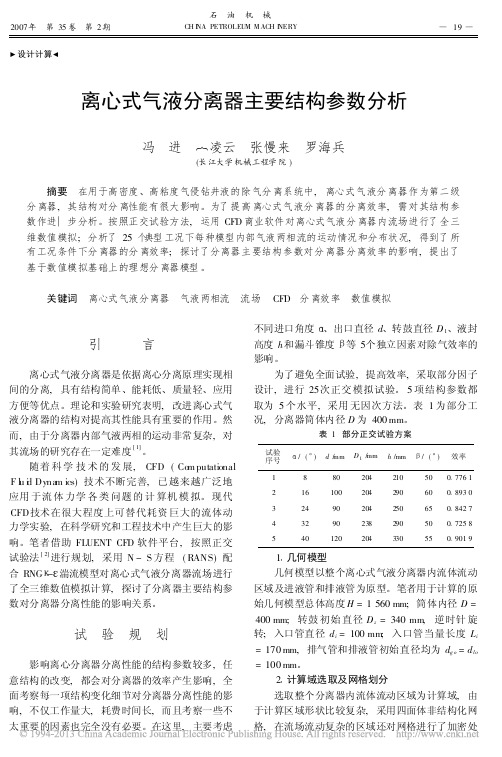
设计计算离心式气液分离器主要结构参数分析冯 进 丁凌云 张慢来 罗海兵(长江大学机械工程学院)摘要 在用于高密度、高粘度气侵钻井液的除气分离系统中,离心式气液分离器作为第二级分离器,其结构对分离性能有很大影响。
为了提高离心式气液分离器的分离效率,需对其结构参数作进一步分析。
按照正交试验方法,运用CFD商业软件对离心式气液分离器内流场进行了全三维数值模拟;分析了25个典型工况下每种模型内部气液两相流的运动情况和分布状况,得到了所有工况条件下分离器的分离效率;探讨了分离器主要结构参数对分离器分离效率的影响,提出了基于数值模拟基础上的理想分离器模型。
关键词 离心式气液分离器 气液两相流 流场 CFD 分离效率 数值模拟引 言离心式气液分离器是依据离心分离原理实现相间的分离,具有结构简单、能耗低、质量轻、应用方便等优点。
理论和实验研究表明,改进离心式气液分离器的结构对提高其性能具有重要的作用。
然而,由于分离器内部气液两相的运动非常复杂,对其流场的研究存在一定难度[1]。
随着科学技术的发展,CFD(Co m putational F l u i d Dyna m ics)技术不断完善,已越来越广泛地应用于流体力学各类问题的计算机模拟。
现代CFD技术在很大程度上可替代耗资巨大的流体动力学实验,在科学研究和工程技术中产生巨大的影响。
笔者借助FLUENT CFD软件平台,按照正交试验法[2]进行规划,采用N-S方程(RANS)配合RNG - 湍流模型对离心式气液分离器流场进行了全三维数值模拟计算,探讨了分离器主要结构参数对分离器分离性能的影响关系。
试 验 规 划影响离心分离器分离性能的结构参数较多,任意结构的改变,都会对分离器的效率产生影响,全面考察每一项结构变化细节对分离器分离性能的影响,不仅工作量大,耗费时间长,而且考察一些不太重要的因素也完全没有必要。
在这里,主要考虑不同进口角度 、出口直径d、转鼓直径D1、液封高度h和漏斗锥度 等5个独立因素对除气效率的影响。
轴流导叶式气液旋流分离器的试验研究
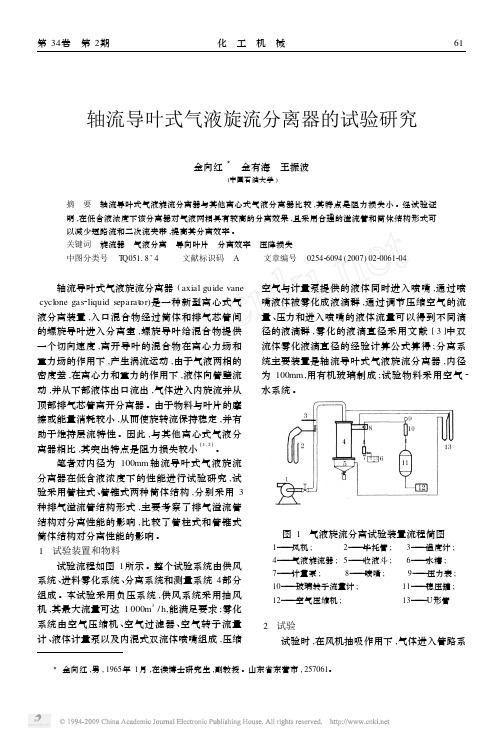
轴流导叶式气液旋流分离器的试验研究金向红3 金有海 王振波(中国石油大学)摘 要 轴流导叶式气液旋流分离器与其他离心式气液分离器比较,其特点是阻力损失小。
经试验证明,在低含液浓度下该分离器对气液两相具有较高的分离效果,且采用合理的溢流管和筒体结构形式可以减少短路流和二次流夹带,提高其分离效率。
关键词 旋流器 气液分离 导向叶片 分离效率 压降损失中图分类号 T Q05118+4 文献标识码 A 文章编号 025426094(2007)022******* 轴流导叶式气液旋流分离器(axial guide vane cycl one gas2liquid separat or)是一种新型离心式气液分离装置,入口混合物经过筒体和排气芯管间的螺旋导叶进入分离室,螺旋导叶给混合物提供一个切向速度,离开导叶的混合物在离心力场和重力场的作用下,产生涡流运动,由于气液两相的密度差,在离心力和重力的作用下,液体向管壁流动,并从下部液体出口流出,气体进入内旋流并从顶部排气芯管离开分离器。
由于物料与叶片的摩擦或能量消耗较小,从而使旋转流保持稳定,并有助于维持层流特性。
因此,与其他离心式气液分离器相比,其突出特点是阻力损失较小[1,2]。
笔者对内径为100mm轴流导叶式气液旋流分离器在低含液浓度下的性能进行试验研究,试验采用管柱式、管锥式两种筒体结构,分别采用3种排气溢流管结构形式,主要考察了排气溢流管结构对分离性能的影响,比较了管柱式和管锥式筒体结构对分离性能的影响。
1 试验装置和物料试验流程如图1所示。
整个试验系统由供风系统、进料雾化系统、分离系统和测量系统4部分组成。
本试验采用负压系统,供风系统采用抽风机,其最大流量可达1000m3/h,能满足要求;雾化系统由空气压缩机、空气过滤器、空气转子流量计、液体计量泵以及内混式双流体喷嘴组成,压缩空气与计量泵提供的液体同时进入喷嘴,通过喷嘴液体被雾化成液滴群,通过调节压缩空气的流量、压力和进入喷嘴的液体流量可以得到不同滴径的液滴群,雾化的液滴直径采用文献[3]中双流体雾化液滴直径的经验计算公式算得;分离系统主要装置是轴流导叶式气液旋流分离器,内径为100mm,用有机玻璃制成;试验物料采用空气2水系统。
毕业设计气液分离器
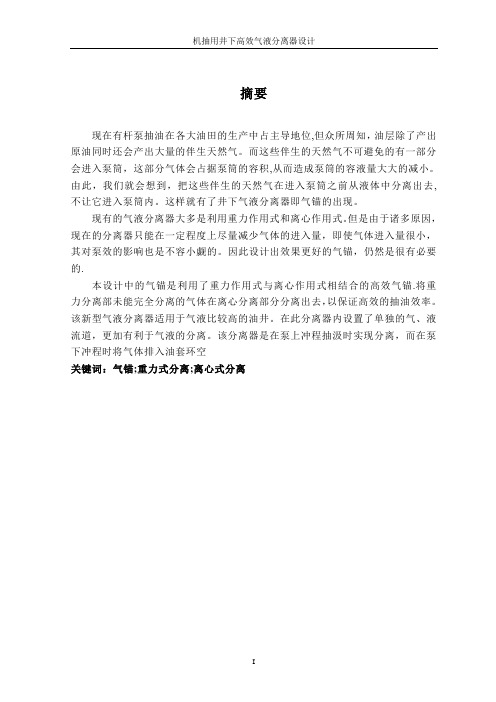
机抽用井下高效气液分离器设计摘要现在有杆泵抽油在各大油田的生产中占主导地位,但众所周知,油层除了产出原油同时还会产出大量的伴生天然气。
而这些伴生的天然气不可避免的有一部分会进入泵筒,这部分气体会占据泵筒的容积,从而造成泵筒的容液量大大的减小。
由此,我们就会想到,把这些伴生的天然气在进入泵筒之前从液体中分离出去,不让它进入泵筒内。
这样就有了井下气液分离器即气锚的出现。
现有的气液分离器大多是利用重力作用式和离心作用式。
但是由于诸多原因,现在的分离器只能在一定程度上尽量减少气体的进入量,即使气体进入量很小,其对泵效的影响也是不容小觑的。
因此设计出效果更好的气锚,仍然是很有必要的.本设计中的气锚是利用了重力作用式与离心作用式相结合的高效气锚.将重力分离部未能完全分离的气体在离心分离部分分离出去,以保证高效的抽油效率。
该新型气液分离器适用于气液比较高的油井。
在此分离器内设置了单独的气、液流道,更加有利于气液的分离。
该分离器是在泵上冲程抽汲时实现分离,而在泵下冲程时将气体排入油套环空关键词:气锚;重力式分离;离心式分离IAbstractNow the rod pumping is also the most important method of oil production。
But as we know,the reservoir yields not only oil but also a lot of gas. And inevitably, part of the gas will enter the pump and occupy its volume。
Therefore the pump’s volume for the oil will reduce seriously。
So,we will thought that, separate the gas from the oil before it entering the pump。
- 1、下载文档前请自行甄别文档内容的完整性,平台不提供额外的编辑、内容补充、找答案等附加服务。
- 2、"仅部分预览"的文档,不可在线预览部分如存在完整性等问题,可反馈申请退款(可完整预览的文档不适用该条件!)。
- 3、如文档侵犯您的权益,请联系客服反馈,我们会尽快为您处理(人工客服工作时间:9:00-18:30)。
新型高效离心式气液分离器设计与试验研究
孙福江1 ,王永伟1 ,张 扬1 ,王奎升1 ,张 建2 ,李清方2 ,张新军2
(1. 北京化工大学 机电工程学院 ,北京 100029 ;2. 胜利工程设计咨询有限责任公司 ,山东 东营 257026)
摘要 :针对常规离心式分离器进行结构改进 ,开发出新型离心式气液分离器 。通过试验证明 ,该分 离器解决了在一定压力下气液分离经常出现的气 、液夹带现象 ,改善了气液分离用离心式分离设备 气 、液 2 相流的流场 ,使分离器对于气 、液 2 相混合流中粒径在 3~8 μm 以上的液体组分分离效率 达到 90 %以上 。 关键词 :离心式分离器 ;气液分离 ;分离粒径 ;分离效率 ;结构设计 中图分类号 : TE931. 1 文献标识码 : A
由于分离介质以气体为主 ,因此计算时要考虑
在进口处的横向和纵向膨胀效应 ,即
ξin =
1-
(R-
ab
re ) ( a +πDtan γ)
(2)
式中 , a 为动力矩系数 ,其定义为入口气体动量矩与
沿壁面气体流动动量矩之比 ; b 为当量直径 ,m ; R 为
分离器旋流腔半径 ,m ; re 为溢流口直径 ,m ; D 为旋
,D
为分离器直径
,mm ,
Fi
为分离
器入口截面积 ,m2 ,V 1 为在 1/ 2 分离器入口高以下
环形空间的体积 ,m3 ,V 2 为分离器排气管下口以下
的分离空间体积减去内旋流的体积 ,m3 ; <为系数 , <
= (1 + n) S t ,其中 , St =ρP d2P V i / ( 18μD) ,ρP 为颗粒
第 38 卷 第 10 期 孙福江 ,等 :新型高效离心式气液分离器设计与试验研究
·61 ·
级效率 ,为设计和制造高效旋流分离器奠定理论基 础 。本文主要研究气液 2 相流离心式分离器的结构 设计和试验 ,并通过对试验数据的分析来验证设计 的新型高效离心式气液分离器的分离效果 。
似取 n = 0. 5 。
内涡旋动能损失为
∫∫ P′vf
=
E M
=
r0 0
12ρvθ3 d r
r0
vθd r
0
(7)
式中 , r0 为最大切向速度面半径 ,m 。
2. 1. 4 出口压力损失
出口压力损失包括局部阻力损失 Δpol 和沿程摩
擦损失 Δpof 两部分 ,即 Δpout =Δpol +Δpof 。
2009 年 第 38 卷 石 油 矿 场 机 械 第1 0 期 第 60 页 OIL FIELD EQUIPMENT 2009 ,38( 10) :60~64
·试验研究 ·
文章编号 : 100123482 (2009) 1020060205
密度 , kg/ m3 , dP 为 颗粒 粒径 , mm , 计 算中 取水 分
粒径为 3~8 μm , vi 为入口气速 , m/ s ,μ为动力粘
度 ,Pa ·s ; n 为 旋 流 指 数 , 由 试 验 确 定 , 通 常 取
0. 5~01 7 。
2. 3 结构设计[6 ]
2. 3. 1 长度尺寸
流腔直径 ,m ;γ为气流在分离器内旋转的下倾角 , (°) ,在内壁边缘处约为 13 °。
2. 1. 2 内壁摩擦压力损失
流体流经分离器内壁由于摩擦所造成的压力损 失可用下式计算
Δplo =
1 2
[1
-
(
re R
)
2
]
(
ab/πre )
2
(
12ρvi2n )
(3)
式中 ,ρ为流体密度 ,kg/ m3 ; vin为进气口速度 ,m/ s 。
2. 3. 3 溢流管插入深度
为保证气 、液 2 相混合流进入分离器后能够按
照预期的轨迹运动 ,保护内部流场 ,避免上升流影响
进气流的流动稳定性 ,分离器溢流管插入深度应为
溢流管内径的 5. 2~5. 3 倍 。
2. 3. 4 溢流管出口结构
由于旋转所产生的强涡流场很容易使尚未凝结
成大液滴的液态组分在气流的带动下重新卷起 ,随 气流通过溢流管排出 ,形成二次混合流 ,从而降低分 离器的气液分离效率 ,因此在溢流口出口设计了专 门用来收集和分离由于气 、液夹带现象混合到已分
(1. Col le ge of Mechanical an d Elect rical En gi neeri n g , B ei j i n g U ni versit y of Chemical Technolog y , B ei j i n g 100029 , Chi na;2. S hen gli En gi neeri n g Desi g n Cons ult ation Co. , L t d. , Don g y i n g 257026 , Chi na)
Δpol
=
1 2
[1
-
(
re R
)
2
]
(
a b/πre )
2
(
12ρvi2n )
(8)
∫ Δpof
π2 =
( S +ΔS) 14πde
f
(
1 r0 vin
r0 0
vθd r)2Fra bibliotek(12ρvi2n )
(9)
式中 , S 为溢流管插入深度 ,mm ;ΔS 为分离空间高
度 ,mm ; f 为摩擦阻力系数 ; de 为溢流管直径 ,mm 。
1 常规离心式分离器结构
常规离心式分离器结构[2] 如图 1 ,2 相流混合气 体从进气管进入分离器内部 ,在筒体内按照流道形 成初旋流 ,到达锥体时由于锥体角度的变化使 2 相 旋流加速 ,2 相流不同密度的组分产生的加速度不 同形成速度差 ,重组分加速快 ,而轻组分加速慢 。由 于旋涡产生的负压效应 ,在分离器中心区域产生了 一个向上吸的负压区域 ,将 2 相混合流中密度较小 的轻组分引导向上运动 ,从排气管排出 ,密度较大的 重组分则按照螺旋轨迹向下流动 ,从下料管排出 。
Design and Test Study of Ne w High Eff iciency Centrif ugal Separator f or Gas2liquid Separation
SU N Fu2jiang1 ,WAN G Yo ng2wei1 ,ZHAN G Yang1 ,WAN G Kui2sheng1 , ZHAN G J ian2 ,L I Qing2fang2 ,ZHAN G Xin2jun2
2. 2 分离效率
按照油田天然气输送要求 ,对于 3~8 μm 的水
滴分离器的分离效率为 90 %以上 。其分离粒径计
·62 ·
石 油 矿 场 机 械 2009 年 10 月
算式为
d50 =
6. 24 abμ πρp hv0
(10)
式中 ,μ为动力粘度 , Pa ·s ;ρp 为气 、液 2 相混合流
图 1 常规离心式分离器结构
2 新型离心式气液分离器结构设计[3]
2. 1 压力损失 压力损失包括入口压力损失 、内壁摩擦损失 、旋
转动能损失 、出口压力损失等[425 ] 。
2. 1. 1 入口压力损失
入口压力损失可按下式确定 ,即
Δpin =ξin ( 12ρg vi2n )
(1)
式中 ξ, in 为阻力系数 。
收稿日期 :2009204210 基金项目 :国家高技术研究发展计划 (863 计划) 项目“高频脉冲电场与离心场联合作用下复杂乳状液处理技术研究” (2007AA06Z224) 的子课题“天然气旋流分液设备的开发研究” 作者简介 :孙福江 (19822) ,男 ,黑龙江齐齐哈尔人 ,硕士研究生 ,研究方向为流体机械及离心分离机械 , E2mail : monkey586 @163. com 。
cy ; st ruct ure desig
目前 ,对离心式旋流分离器的研究主要集中在 结构设计和流场研究 2 个方面[1] ,其中 ,结构设计主 要在于改进现有的离心式分离器进出口形状和长度 尺寸 ,通过降低流体经过分离器的压力降和阻力损
失提高分离效率 ,减少能量损失 ,使结构更加优化 ; 流场研究主要是模拟流体在旋流分离器内部的流 动 ,寻找更恰当的数值模拟函数近似地拟合流体流 动方程 ,更准确地计算离心式旋流分离器的分离分
∫R
M = vθd r r0
(6)
其中 , vθ 为气流沿竖直方向的流动速度 , m/ s , vθ =
f1
vin ( R -
b 2
)
Rn -
1
[ 1 - 0. 4 ( b ) 0. 5 ] rn
,f1
为壁面粗糙度修正系数 ,
R
取 f 1 = 0. 85~0. 95 ; n 为准自由涡速度分布指数 ,近
2. 1. 3 旋转动能损失
旋转动能损失包括外涡旋动能损失和内涡旋动
能损失 2 部分 。
外涡旋动能损失为
Pvf
=
E M
(4)
式中 , E 为单位时间内通过垂直于气流方向的单位
高度的平面动能 ,J ,为
∫ E =
R r0
12ρvθ3 d r
(5)
M 为单位时间内通过垂直于气流方向的单位高度
平面的体积流量 ,kg/ m3 ,为
旋转流 。
含液气流在筒体内作高速螺旋运动时 ,如果受 到干扰或阻碍就会引起液滴颗粒在筒体内壁反弹 , 被气流夹带着与出口气流一起排出 。所以 ,设计时 要考虑筒体内径 D0 和筒体外径 DB 的大小 ,保证含 尘气流在筒体内的旋流环行通道宽度 ≥L w ,其关系 式为