气液分离器设计
旋流式液气分离器的设计
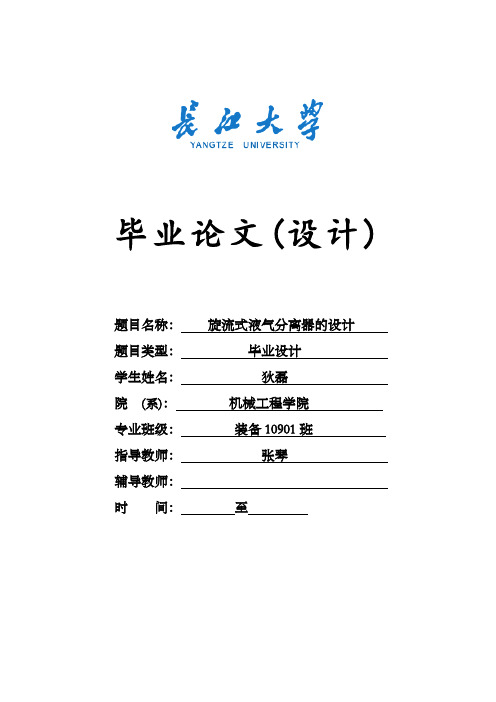
毕业论文(设计)题目名称:旋流式液气分离器的设计题目类型:毕业设计学生姓名:狄磊院(系):机械工程学院专业班级:装备10901班指导教师:张琴辅导教师:时间:至目录毕业论文(设计)任务书 (Ⅰ)开题报告 (Ⅱ)指导教师审查意见 (Ⅲ)评阅教师评语 (Ⅳ)答辩会议记录 (Ⅴ)中文摘要 (Ⅵ)外文摘要 (Ⅶ)1 绪论 (7)选择旋流式液气分离器的意义 (7)国内外现状和进展趋势 (7)国外现状和进展趋势 (7)国内现状和进展趋势 (9)2 方案论证 (9)旋流式液气分离方案的可行性 (9)旋流式分离器的结构及工作原理 (10)3 分离器的整体设计 (11)旋流器的直径和长度的计算 (11)分离器结构设计 (13)分离器整体结构设计 (13)脱气结构 (15)钻井液入口的尺寸 (15)旋流器的结构设计 (15)外筒体的设计 (17)接口管设计 (18)外部结构 (21)4、要紧零部件的设计及校核计算 (22)筒体和封头的壁厚计算 (22)外容器筒体、封头壁厚计算 (22)旋流器筒体封头壁厚计算 (24)人孔 (25)人孔选择 (25)人孔补强 (26)支座 (26)分离器的总质量 (26)支座的选用及安装要求 (28)5 分离器的安装 (28)焊接 (28)安装顺序 (29)6 壳体的有限元分析 (32)7 总结 (35)参考文献 (37)致谢 (39)附录一 (40)附录二 (43)旋流式液气分离器的设计学生:狄磊,长江大学机械工程学院指导教师:张琴,长江大学机械工程学院【摘要】旋流分离器,是一种利用离心沉降原理将非均相混合物中具有不同密度的相分离的机械分离设备。
在具有密度差的混合物以必然的方式及速度从入口进入旋流分离器后,在离心力场的作用下,密度大的相被甩向周围,并顺着壁面向下运动,作为底流排出;密度小的相向中间迁移,并向上运动,最后作为溢流排出。
如此就达到了分离的目的。
旋流分离技术可用于液液分离、气液分离、固液分离、气固分离等。
气液分离器设计论文

气液分离器设计论文一、气液分离器的设计原理气液分离器的设计原理主要基于两种物质之间的相态差异,通过利用气体和液体之间的密度和粘度等差异来实现分离。
在气液分离器中,气体通常通过进料管进入,然后通过分离介质展开,并在分离介质中与液体相互作用,从而实现气液分离。
二、气液分离器的设计流程1.确定物料特性:首先需要确定处理的气体和液体的特性,包括流量、压力、温度、组成等。
这些物料的特性将对分离器的设计和选择产生影响。
2.确定设备选型:根据物料特性和分离要求,选择适当的气液分离器类型,包括总体形式、入口位置、出口位置、流动路径等。
3.计算处理容量:根据物料特性和处理要求,计算出所需的处理容量,包括气体和液体的流量。
4.计算设计参数:根据物料特性和处理容量,计算出分离器的设计参数,包括分离介质的形状、尺寸、孔径等。
5.进行设备设计:根据计算得到的设计参数,进行气液分离器的详细设计,包括细节尺寸、结构布置等。
三、气液分离器的优化方法1.优化分离介质:分离介质的选择对分离效果有着重要影响,在设计中可以选择具有较好分离性能的材料,如网格结构、纤维材料等。
2.优化流动路径:流动路径的设计也会对分离效果产生影响,可以通过改变管道形状、加入隔板等方式来改善分离效果。
3.优化设备结构:设备结构的合理设计也能够提高气液分离器的效果,可以通过改变分离器的长度、直径等参数来改善分离效率。
4.优化操作参数:在实际操作中,还可以通过调整气体和液体的流量、压力、温度等操作参数来提高分离效果。
总结起来,气液分离器的设计是一个综合考虑物料特性、设备选型、处理容量和设计参数等多种因素的过程。
通过优化设计,可以提高分离效果,实现更加高效和可靠的气液分离。
立式重力气-液分离器的工艺设计

立式重力气-液分离器的工艺设计许建华【摘要】Gravity gas-liquid separator has been widely used in the chemical industry,and the most used of which is the vertical gravity gas-liquid separator.In this paper,a brief introduction to the common gravity gas-liquid separator is introduced,and as an example,an engineering design of a gas-liquid separator is showed.The selection of equipment and the key parameters of vertical gravity gas-liquid separator are introduced in details,and several key issues which should be cared in the process design are also listed.%重力气-液分离器在化工生产中一直被广泛应用,其中以立式重力气-液分离器应用最多。
简单介绍了化工装置中常见的重力气-液分离器,并以一台气-液分离器的工程设计为例,就立式重力气-液分离器的设备选型和关键参数的工艺计算做了详细介绍,并指出了立式重力气-液分离器在工艺设计中应注意的几个问题。
【期刊名称】《化工设计通讯》【年(卷),期】2016(042)007【总页数】2页(P99-99,124)【关键词】重力气-液分离器;设备选型;工艺设计【作者】许建华【作者单位】南京扬子石油化工设计工程有限责任公司,江苏南京 210048【正文语种】中文【中图分类】TQ053.2重力气-液分离器因分离负荷范围大,在化工生产中一直被广泛应用。
气液分离器设计文档

一、浮动流速V t。
计算:由Aspen模拟得,进气液分离器前各流相参数为:流量Q=8823.86m3/h,液相体积流量为14.82m3/h,压力P=10atm,温度T=293.15K,可求的二氧化碳在此状态下密度约为13.31g/L,由经验公式:可算得浮动流速V t=0.58m/s。
二、直径D计算:式中:D——分离器直径,m;V G,maz——气体最大体积流量,m3/h;u e——容器中气体流速,m/s。
可算得直径D=2.32m。
三、高度H计算:容器高度分为气相空间高度和液相高度,此处所指的高度,是指设备的圆柱体部分,如图所示:低液位(LL)与高液位(HL)之间的距离,采用下式计算:式中:H L——液体高度,m;t——停留时间,min;D——容器直径,m;V L——液体体积流量,m3/h。
停留时间(t)以及釜底容积的确定,受许多因素影响。
这些因素包括上、下游设备的工艺要求以及停车时板上的持液量。
当液体体积较小时,规定各控制点之间的液体高度最小距离为100mm。
表示为:LL(低液位)-100mm-LA(低液位报警)-100mm-NL(正常液位)-100mm-HA (高液位报警)-100mm-HL(高液位)。
停留时间取10min,得H L=0.58m。
圆柱体高度H=1.2D+0.1D+H L+100=3696mm。
四、接管管径计算:(1)入口接管两相入口接管的直径应符合下式:式中:u p——接管内流速,m/s;ρG——接管直径,m。
可由下图快速差得接管直径:查图得:接管直径可谓200mm。
(2)出口接管气体出口接管直径,必须不小于所连的管道直径液体出口管的设计,应使液体流速小于等于1m/s。
任何情况下,较小的出口气速有利于分离。
由于出口管径为80,液体流量为14.82m3/h,为了满足设计要求,可取液体出口接管直径为100,气体出口直径可取600mm。
气液分离器设计资料

气液分离器设计资料一、气液分离器的基本原理气液分离器通过利用气液流动特性和设备内部结构,使气体和液体分离,从而达到适当的处理效果。
其基本原理是根据气体与液体的密度差异、速度差异等流体特性,通过设定合适的流速、流程和建立合理的分离结构,使气体与液体在设备内部发生分离。
二、气液分离器的设计要点1.设计流程和参数:气液分离器的设计要根据具体的工艺流程和工况参数进行,包括气体流量、液体流量、流速和流程等。
根据不同的流程要求,选择合适的设计流程和参数,确保设备能够实现预期的分离效果。
2.分离结构设计:气液分离器的分离结构是实现气液分离的关键,直接影响设备的分离效果。
常见的分离结构有板式分离器、旋风分离器、网式分离器等。
根据具体的工况要求选择合适的分离结构,合理设计分离结构的尺寸和布置。
3.材料选择和防腐保温措施:由于气液分离器常用于化工、石化等领域,其内部容易受到介质的腐蚀,因此在设计时需要选择适合的材料来构建设备。
常用的材料有不锈钢、碳钢等。
另外,对于高温、低温工艺,需要对设备进行适当的保温措施,以确保设备的正常运行。
4.安全性设计:在气液分离器设计时需要充分考虑设备的安全性。
合理设置安全阀、排气装置和液位控制装置等,以防止因设备内部积存过高的压力或液位等不安全因素引发意外事故。
三、气液分离器的设计注意事项1.考虑介质特性:在气液分离器设计时需要对介质的物性、腐蚀性等进行充分的考虑。
针对不同的介质选择合适的材料和防腐措施,确保设备的稳定性和耐用性。
2.考虑流体流动特性:不同介质的流动特性不同,如气体的速度、粘度、密度等与液体的流速、液位等因素的关系,都会影响设备的分离效果。
因此在设计过程中需要考虑这些因素,并根据实际情况进行适当的调整。
3.良好的排气和排液性能:气液分离器的设计还需要考虑良好的自动排气和排液性能,以防止设备内部积聚气体或液体,影响设备的正常运行。
可以通过设置合适的排气装置、液位控制装置等来实现。
气-液分离器设计

4
SLDI 233A14-98
得 ALA = Ab + 2A1 = 0.107 + 2 × 0.4 = 0.289
ATOT
ATOT
3.14
查图2.5.1—5得 hLA = 0.333,从最低液位经2min后得到液面高度为 DT
hLA = 0.333 × DT = 0.333× 2000 = 666mm(hLA即是图中h)
2
SLDI 233A14-98
a) 入口接管
两相入口接管的直径应符合式(2.2.2—3)要求。
式中
ρG uP2 <1000Pa
(2.2.2—3)
up——接管内流速,m/s; рG——气体密度,kg/m3。
由此导出
式中
DP>3.34×10-3(VG+VL)0.5
ρ
0. 25 G
(2.2.2—4)
VG、VL——分别为气体与液体体积流量,m3/h; DP——接管直径,m。
低液位(LL)与高液位(HL)之间的距离,采用式(2.2.2—2)计算
式中
HL
=
VLt 47.1D2
(2.2.2—2)
HL——液体高度,m;
t——停留时间,min;
D——容器直径,m; VL——液体体积流量,m3/h。
气、液
图2.2.2 立式重力分离器 停留时间(t)以及釜底容积的确定,受许多因素影响。这些因素包括上、下游设备的工艺要求以及停 车时塔板上的持液量。当液体量较小时,规定各控制点之间的液体高度最小距离为100mm。表示为:LL(低 液位)-100mm-LA(低液位报警)-100mm-NL(正常液位)-100mm-HA(高液位报警)-100mm-HL(高液位)。 2.2.2.3 接管直径
空调气液分离器的设计与使用

空调气液分离器的设计与使用一、工作原理二、气液分离器的作用三、气液分离器的安装位置四、气液分离器的容积设计五、气液分离器回油孔的设计六、气液分离器均压孔的设计七、气液分离器评价试验步骤和判定标准八、气液分离器的图纸九、气液分离器设计和使用的雷区十、气液分离器的选型对照表十一、气液分离器错误的安装引起的故障(案例)一、工作原理饱和气体在降温或者加压过程中,一部分可凝气体组分会形成小液滴·随气体一起流动。
气液分离器就是处理含有少量凝液的气体,实现凝液回收或者气相净化。
其结构一般就是一个压力容器,内部有相关进气构件、液滴捕集构件。
一般气体由上部出口,液相由下部收集。
气液分离罐是利用丝网除沫,或折流挡板之类的内部构件,将气体中夹带的液体进一步凝结,排放,以去除液体的效果。
基本原理是利用气液比重不同,在一个突然扩大的容器中,流速降低后,在主流体转向的过程中,气相中细微的液滴下沉而与气体分离,或利用旋风分离器,气相中细微的液滴被进口高速气流甩到器壁上,碰撞后失去动能而与转向气体分离。
下图是空调使用的气液分离器二、气液分离器的作用1.把从蒸发器返回到压缩机的冷媒分离成气体和液体,仅使气体回到压缩机,从而避免液态制冷剂进入压缩机破坏润滑或者损坏涡旋盘。
(以防止压缩机液击。
)2.使气液分离器中的润滑油回到压缩机,它可以暂时储存多余的制冷剂液体,并且也防止了多余制冷剂流到压缩机曲轴箱造成油的稀释。
因为在分离过程中,冷冻油也会被分离出来并积存在底部,所以在气液分离器出口管和底部会有一个油孔,保证冷冻油可以回到压缩,从而避免压缩机缺油。
注:①如果能保证蒸发器出口的冷媒总是气体的状态,也可以取消气液分离器。
②原则上讲,所有的热泵产品都应该增加气液分离器,单冷机型视情况决定,一般建议使用。
3.一般情况下12000W制冷量(5匹及以上的空调)需要气液分离器,而涡旋压缩机本身不带储液罐,则另外要增加气液分离器,旋转式压缩机本身就带有储液罐。
气液分离器设计

文档来源为:从网络收集整理.word版本可编辑.欢迎下载支持.气—液分离器设计2005-04-15 发布2005-05-01 实施0文档来源为:从网络收集整理.word版本可编辑.欢迎下载支持.目次1 总则1.1 目的1.2 范围1.3 编制本标准的依据2 立式和卧式重力分离器设计2.1应用范围2.2 立式重力分离器的尺寸设计2.3 卧式重力分离器的尺寸设计2.4 立式分离器(重力式)计算举例2.5附图3 立式和卧式丝网分离器设计3.1 应用范围 3.2 立式丝网分离器的尺寸设计3.3 卧式丝网分离器的尺寸设计3.4 计算举例3.5 附图4 符号说明1 总则 1.1 目的本标准适用于工艺设计人员对两种类型的气—液分离器设计,即立式、卧式重力分离器设计和立式、卧式丝网分离器设计。
并在填写石油化工装置的气—液分离器数据表时使用。
1.2 范围本标准适用于国内所有化工和石油化工装置中的气-液分离器的工程设计。
1.3 编制本标准的依据:化学工程学会《工艺系统工程设计技术规定》HG/T20570.8-1995第8篇气—液分离器设计。
2 立式和卧式重力分离器设计 2.1 应用范围2.1.1 重力分离器适用于分离液滴直径大于200μm 的气液分离。
2.1.2 为提高分离效率,应尽量避免直接在重力分离器前设置阀件、加料及引起物料的转向。
2.1.3 液体量较多,在高液面和低液面间的停留时间在6~9min ,应采用卧式重力分离器。
2.1.4 液体量较少,液面高度不是由停留时间来确定,而是通过各个调节点间的最小距离100mm 来加以限制的,应采用立式重力分离器。
2.2 立式重力分离器的尺寸设计 2.2.1 分离器内的气速 2.2.1.1 近似估算法5.0⎪⎪⎭⎫ ⎝⎛-=G GL s t K V ρρρ (2.2.1—1)式中V t ——浮动(沉降)流速,m/s ;ρL 、ρG ——液体密度和气体密度,kg/m 3; K S ——系数d *=200μm 时,K S =0.0512; d *=350μm 时,K S =0.0675。
- 1、下载文档前请自行甄别文档内容的完整性,平台不提供额外的编辑、内容补充、找答案等附加服务。
- 2、"仅部分预览"的文档,不可在线预览部分如存在完整性等问题,可反馈申请退款(可完整预览的文档不适用该条件!)。
- 3、如文档侵犯您的权益,请联系客服反馈,我们会尽快为您处理(人工客服工作时间:9:00-18:30)。
气—液分离器设计2005-04-15 发布2005-05-01 实施目次1 总则1.1 目的1.2 范围1.3 编制本标准的依据2 立式和卧式重力分离器设计2.1应用范围2.2 立式重力分离器的尺寸设计2.3 卧式重力分离器的尺寸设计2.4 立式分离器(重力式)计算举例2.5附图3 立式和卧式丝网分离器设计3.1 应用范围 3.2 立式丝网分离器的尺寸设计3.3 卧式丝网分离器的尺寸设计3.4 计算举例3.5 附图4 符号说明1 总则 1.1 目的本标准适用于工艺设计人员对两种类型的气—液分离器设计,即立式、卧式重力分离器设计和立式、卧式丝网分离器设计。
并在填写石油化工装置的气—液分离器数据表时使用。
1.2 范围本标准适用于国内所有化工和石油化工装置中的气-液分离器的工程设计。
1.3 编制本标准的依据:化学工程学会《工艺系统工程设计技术规定》HG/T20570.8-1995第8篇气—液分离器设计。
2 立式和卧式重力分离器设计 2.1 应用范围2.1.1 重力分离器适用于分离液滴直径大于200μm 的气液分离。
2.1.2 为提高分离效率,应尽量避免直接在重力分离器前设置阀件、加料及引起物料的转向。
2.1.3 液体量较多,在高液面和低液面间的停留时间在6~9min ,应采用卧式重力分离器。
2.1.4 液体量较少,液面高度不是由停留时间来确定,而是通过各个调节点间的最小距离100mm 来加以限制的,应采用立式重力分离器。
2.2 立式重力分离器的尺寸设计 2.2.1 分离器内的气速 2.2.1.1 近似估算法5.0⎪⎪⎭⎫ ⎝⎛-=G GL s t K V ρρρ (2.2.1—1)式中V t ——浮动(沉降)流速,m/s ;ρL 、ρG ——液体密度和气体密度,kg/m 3; K S ——系数d *=200μm 时,K S =0.0512; d *=350μm 时,K S =0.0675。
近似估算法是根据分离器内的物料流动过程,假设Re =130,由图2.5.1—1查得相应的阻力系数C W =1,此系数包含在K s 系数内,Ks 按式(2.2.1—1)选取。
由式(2.2.1—1)计算出浮动(沉降)流速(V t ),再设定一个气体流速(u e ),即作为分离器内的气速,但u e 值应小于V t 。
真正的物料流动状态,可能与假设值有较大的出入,会造成计算结果不准确,因此近似估算法只能用于初步计算。
2.2.1.2 精确算法从浮动液滴的平衡条件,可以得出:5.0G W G L t 3)(*4⎥⎦⎤⎢⎣⎡-=ρρρC gd V (2.2.1—2)式中V t ——浮动(沉降)流速,m/s ; d *——液滴直径,m ;ρL 、ρG ——液体密度和气体密度,kg/m 3; g ——重力加速度,9.81m/s 2; C w ——阻力系数。
首先由假设的Re 数,从图2.5.1—1查C W ,然后由所要求的浮动液滴直径(d *)以及ρL 、ρG 按式(2.2.1—2)来算出't V ,再由此't V 计算Re 。
G'*μρGt e V d R = (2.2.1—3)式中μG ——气体粘度,Pa ·S 。
其余符号意义同前。
由计算求得Re 数,查图2.5.1—1,查得新C W ,代入式(2.2.1—2),反复计算,直到前后两次迭代的Re 数相等,即t 't V V =为止。
取u e ≤V t ,即容器中的气体流速必须小于悬浮液滴的浮动(沉降)流速(V t )。
2.2.2 尺寸设计尺寸图见图2.2.2所示。
2.2.2.1 直径5.0e Gmax 0188.0⎪⎪⎭⎫ ⎝⎛=u V D (2.2.2—1) 式中D ——分离器直径,m ;V Gmax ——气体最大体积流量,m 3/h ; u e ——容器中气体流速,m/s 。
由图2.5.1—2可以快速求出直径(D )。
2.2.2.2 高度容器高度分为气相空间高度和液相高度,此处所指的高度,是指设备的圆柱体部分,见图2.2.2所示。
低液位(LL )与高液位(HL )之间的距离,采用式(2.2.2—2)计算2L L 1.47Dt V H (2.2.2—2)式中H L ——液体高度,m ; t ——停留时间,min ; D ——容器直径,m ; V L ——液体体积流量,m 3/h 。
图2.2.2 立式重力分离器停留时间(t )以及釜底容积的确定,受许多因素影响。
这些因素包括上、下游设备的工艺要求以及停车时塔板上的持液量。
当液体量较小时,规定各控制点之间的液体高度最小距离为100mm 。
表示为:LL (低液位)-100mm-LA (低液位报警)-100mm-NL (正常液位)-100mm-HA (高液位报警)-100mm-HL (高液位)。
2.2.2.3 接管直径1) 入口接管气、液两相入口接管的直径应符合式(2.2.2—3)要求。
ρG P u 2<1000Pa (2.2.2—3) 式中u p ——接管内流速,m/s ; рG ——气体密度,kg/m 3。
由此导出D P >3.34×10-3(V G +V L )0.5ρG 025. (2.2.2—4)式中V G 、V L ——分别为气体与液体体积流量,m3/h ; D P ——接管直径,m 。
由图2.5.1—3可以快速求出接管直径。
2) 出口接管气体出口接管直径,必须不小于所连接的管道直径。
液体出口接管的设计,应使液体流速小于等于1m/s 。
任何情况下,较小的出口气速有利于分离。
2.3 卧式重力分离器的尺寸设计 2.3.1 计算方法及其主要尺寸设备尺寸计算的依据是液体流量及停留时间。
按式(2.3.1)求出“试算直径”D T ,在此基础上,求得容器中液体表面上的气体空间,然后进行校核,验证是否满足液滴的分离。
卧式重力分离器的尺寸见图2.3.1所示。
试算直径 31L T 12.2⎪⎭⎫ ⎝⎛⋅=A C t V D (2.3.1) 式中C =L T /D T =2~4(推荐值是2.5);D T 、L T ——分别为圆柱部分的直径和长度,m ; V L ——液体的体积流量,m 3/h ; t ——停留时间,min ;A ——可变的液体面积(以百分率计)即 A =A TOT -(A a +A b ),均以百分率计其中 A TOT ——总横截面积,%;A a ——气体部分横截面积,%;A b ——液位最低时液体占的横截面积,%。
图2.3.1 卧式重力分离器通常开始计算时取A =80%,并假设气体空间面积A a 为14%,最小液体面积A b 为6%。
选择C 值时,须考虑容器的可焊性(壁厚)和可运输性(直径、长度)。
由D T 和A a =14%,查图2.5.1-4,得出气体空间高度(a ),a 值应不小于300mm 。
如果a <300mm ,需用A <80%的数值,再进行计算新的试算直径。
2.3.2 接管距离两相流进口接管与气体出口接管之间的距离应尽可能大,即L N ≈L T 及L T =C ·D T 。
式中L N ——两相流进口到气体出口间的距离,m; L T ——圆筒形部分的长度,m 。
根据气体空间(A a )和一个时间比值(R )(即液滴通过气体空间高度所需沉降时间与气体停留时间的比)来校核液滴的分离,计算进口和出口接管之间的距离('N L )。
RA D V a L a 5.0GG L '2T G'N )(524.0ρρρ-⋅=(2.3.2—1)式中'N L 、'T D 、a ——分别为进出口接管间距离、卧式容器直径和气体空间高度,m ;V G ——气体流量,m 3/h ;ρL 、ρG ——分别为液体密度、气体密度,kg/m 3;气、液气L T液A a ——气体部分横截面积,%; R 对于d *=350μm ,使用R =0.167 对于d *=200μm ,使用R =0.127 R =τs /τT其中 τs ——直径为d *的液滴,通过气体空间高度(a )所需要的时间,s ;τT ——气体停留时间,s 。
两相流进口到气体出口间的距离(L N )不应小于'N L 。
接管设计见2.2.2.3规定。
2.3.3 液位和液位报警点计算实例已知:V L =120m 3/h ,t =6min ,D T =2000mm ,L T =5000mm ,最低液位高度h LL =150mm 。
最低液位(LL )、低液位报警(LA )、正常液位(NL )、高液位报警(HA )、最高液位(HL )之间的时间间隔分别是2、1、1、2min 。
要计算对应时间间距的各液位高度。
解题:如图2.3.3所示。
最低液位,即液面起始高度(计算时间为0)的液位高度(h LL )为150mm 。
容器横截面积(A TOT ):22214.3424m D A T TOT =⨯==ππ相当于液体在容器中停留时间为1min 所占的横截面积为: A 1=120×1/(60×5)=0.4m 2图2.3.3 卧式重力分离器液位高度其它几个高度按下述方法求出:h LL /D T =150/2000=0.075,由图2.5.1—5查得)(034.0LL TOTb h h A A 即是图中=。
2TOT b 107.014.3034.0034.0m A A =⨯=⨯=得 289.014.34.02107.02TOT1b TOTLA =⨯+=+=A A A A A查图2.5.1—5得333.0TLA =D h ,从最低液位经2min 后得到液面高度为)(6662000333.0333.0h h mm D h LA T LA 即是图中=⨯=⨯=得416.014.34.03107.03TOT 1b TOT NL =⨯+=+=A A A A A 查图2.5.1—5得TNLD h =0.434,过1min 后,液面高度为h NL =0.434×2000=868mm (h NL 即是图中h ) 得544.014.34.04107.04TOT 1b TOT HA =⨯+=+=A A A A A 查图2.5.1—5得THAD h =0.535,再过1min 液面高度为h HA =0.535×D T =0.535×2000=1070mm (h HA 即是图中h )得798.014.34.06107.06TOT1b TOTHL =⨯+=+=A A A A A查图2.5.1—5得746.0THL =D h ,再过2min 液面高度为h HL =0.746×D T =0.746×2000=1492mm(h HL 即是图中h )。