热轧薄板带钢生产.
热轧带钢生产车间布置设计分析

热轧带钢生产车间布置设计分析热轧带钢简介以板坯或钢锭为原料用热轧方式生产各种中厚钢板、薄钢板和带钢的轧钢车间设计。
热轧板带钢车间设计范围包括中厚板车间设计、连续热轧宽带钢车间设计、施特克尔(炉卷)带钢轧钢车间设计和热轧窄带钢车间设计。
除了以上四类板带轧钢车间外,尚有叠轧薄板车间和行星轧板车间。
工艺流程热轧宽带钢主要生产工艺流程是板坯经加热后由粗轧机组及精轧机组制成带钢。
从精轧最后一架轧机出来的热钢带通过层流冷却到设定温度,由卷取机卷成钢带卷,冷却后的钢带卷,根据用户的不同需求,经过不同的精整作业线加工而成为钢板、平整卷及纵切钢带产品的过程。
设备构成主体、加热炉、推钢机、出钢机、粗轧机组(四机架)、飞剪、精轧机组(七机架连轧)、卷取机、吊车、精整机组(开卷机、矫直机、剪切机、张力卷取机等)。
在进行车间设计时主要是轧机型式和轧机组成的选择,同时从设备的可靠性、产品质量、维修方便、设备结构、外形和机组重量等因素进行比较和选择。
主要轧钢机有中厚钢板轧机、热轧宽带钢轧机、施特克尔(炉卷)带钢轧机和热轧窄带钢轧机。
(1)中厚钢板轧机。
有二辊式、三辊劳特式、四辊式。
轧机布置型式主要有单机架、双机架型式。
现代的中厚板车间设计均采用四辊式轧机,按产品和产量的不同选用单机架或双机架组成,最佳型式是粗轧机和精轧机,均为四辊轧机并顺列布置。
(2)热轧宽带钢轧机。
指辊身长度不小于1000mm的热轧带钢轧机,世界上建设最多的为1500~1800mm和2000~2300mm热轧带钢轧机,最大的达2690mm。
按粗轧机的型式和组成有半连续式、3/4连续式和连续式三种热轧宽带钢轧机。
(3)施特克尔带钢轧机。
主要用于轧制不锈钢、硅钢等难变形金属。
该轧机的特点是在轧机入口和出口设有带卷筒的加热保温炉,用以保持带钢轧制温度,因此在中国称炉卷轧机。
现代的施特克尔带钢车间,一般由一架四辊式可逆式万能粗轧机和一架四辊可逆式精轧机组成。
轧机后设有带钢冷却设备、卷取机和钢板剪切设备。
热轧薄规格带钢精轧穿带稳定性的改善

区域治理前沿理论与策略九十年代初期,热轧工艺得以在国内迅速发展,该工艺具备耗能低,便于加工,生产效率高等特点。
热轧原理具体是在钢材退火温度足够高时进行轧制,经过这足够长的时间,在材料中产生无应变能力的新晶粒,新晶粒开始产生的温度就是再结晶温度的初始温度,新晶粒占据全部材料的时的温度为再结晶温度的终了温度,再结晶温度取初始温度与终了温度的平均值,一般情况下此温度主要受到材料成分与环境温度这两个因素的影响。
这便是关于热轧的简单原理,其实在我们的实际加工薄规格产品中主要的轧制方式而言,主要分为单坯轧制、半无头轧制以及全无头轧制三种方式,以下通过简单介绍这三种方式,进一步了解如何改善相关工艺的稳定性。
一、热轧薄规格产品的轧制方式、原理以及技术特点1.单块板坯轧制技术,其原理是将钢材的首尾安置在没有张力情况下,即非稳定轧制状态下进行生产的,这样轧制的钢材精度很难控制,比较容易造成钢材之间相互重叠。
当钢材的尾部离开精轧机时容易弯曲,制造的产品公差基数大,相对应的尺寸精度与性能达不到合格标准。
因此对于规格要求较薄的热轧板采用此技术生产时难度较大,且产品达不到所要求的性能指标。
2.半无头轧制技术,该技术原理是利用薄板坯连铸连轧生产线中长于普通板坯四到六倍的板坯,来保证带钢不间断进行轧制,再由相关的机器平均裁制成相等质量的钢材。
跟上述介绍的单块板坯轧制技术不同的是,此技术虽然对相关的生产设备以及技术提出了更高的要求,但是大幅度地提高了产品的生产效率,进而增强了产品的性能指标。
3.全无头轧制技术,具体原理是通过板坯对粗轧机与精轧机之间进行连接,并且在此过程中需要进行板坯加热以及协调两台加工设备之间的工作频率,才可最终实现无头轧制。
上述可见对技术要求相当高,尤其是粗轧机与精轧机的连接技术,直至上世纪九十年代末期,在日本的川崎钢厂此项技术才得以实现。
在我国粗轧机与精轧机之间的连接方式主要分为两种,即变形链接与感应加热链接,用以保障当板坯在进入精轧机后正常的运行。
热轧带钢生产工艺及工艺要求

钢往板往表 破面坏不钢• 得板有的成气物品泡理、性:结能厚疤或、成度拉为1裂产.、生2~刮破2伤裂5、和.4折锈m叠蚀、的m裂缺缝陷宽、源度夹,杂成6和为50压应~入力2氧集1化中3铁的0m皮薄等弱m缺环陷节,。因为这些缺陷不仅影响轧件的外观形象,而且
板坯:厚度135~180mm 宽度650~2080mm 长度6~17m
薄板坯连铸连轧热轧带钢工艺 Nhomakorabea对定于的重 化要学1用成.2途分.2的,结保设构证备钢良板好布,的置要焊求接2具性有能较、好常的温综或合低性温能冲,击即韧除性了或有一良定好的的冲工压艺性性能能,,保甚证至一除定了的有金一相定 组的织强及度各和向塑组性织以均外匀,性还等要。求保证一
薄板坯连铸连轧热轧带钢工艺 热轧带钢生产工艺及工艺要求
2、薄板坯连铸连轧工艺
薄板坯 连铸连轧 流程1
连铸
定尺坯剪切
定尺坯加热
精轧 轧后冷却
卷取
开卷检查 钢卷运输
钢卷打包 钢卷称重 钢卷打号 钢卷入库
薄板坯 连铸连轧 设备布置1 CSP
CSP连铸机
辊底式均热炉
除鳞机 事故剪
生产能力: - 单线: 150万吨/年 - 双线: 250万吨/年
铸坯厚度: 55~70 mm 成品宽度: 900.....1 680 mm
生产线:唐钢 UTSP 本钢连铸连轧线
3、中厚板坯连铸连轧热轧带钢工艺
工艺流程
连铸
定尺坯切割 定尺坯加热
热坯下线
冷坯装炉 板坯库
可逆 粗轧
热卷
精轧
轧后 冷却
卷取
开卷检查 钢卷运输
钢卷打包
钢卷称重 钢卷打号 钢卷入库
中厚板坯 连铸连轧 设备布置
除鳞 1 定宽压力机
热轧板带钢发展历史
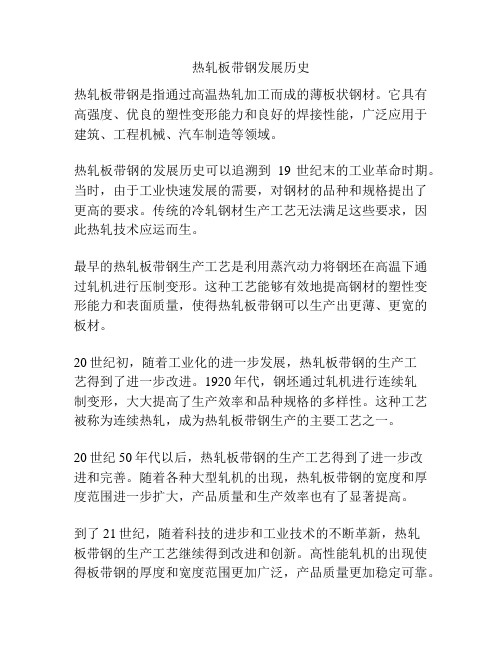
热轧板带钢发展历史
热轧板带钢是指通过高温热轧加工而成的薄板状钢材。
它具有高强度、优良的塑性变形能力和良好的焊接性能,广泛应用于建筑、工程机械、汽车制造等领域。
热轧板带钢的发展历史可以追溯到19世纪末的工业革命时期。
当时,由于工业快速发展的需要,对钢材的品种和规格提出了更高的要求。
传统的冷轧钢材生产工艺无法满足这些要求,因此热轧技术应运而生。
最早的热轧板带钢生产工艺是利用蒸汽动力将钢坯在高温下通过轧机进行压制变形。
这种工艺能够有效地提高钢材的塑性变形能力和表面质量,使得热轧板带钢可以生产出更薄、更宽的板材。
20世纪初,随着工业化的进一步发展,热轧板带钢的生产工
艺得到了进一步改进。
1920年代,钢坯通过轧机进行连续轧
制变形,大大提高了生产效率和品种规格的多样性。
这种工艺被称为连续热轧,成为热轧板带钢生产的主要工艺之一。
20世纪50年代以后,热轧板带钢的生产工艺得到了进一步改
进和完善。
随着各种大型轧机的出现,热轧板带钢的宽度和厚度范围进一步扩大,产品质量和生产效率也有了显著提高。
到了21世纪,随着科技的进步和工业技术的不断革新,热轧
板带钢的生产工艺继续得到改进和创新。
高性能轧机的出现使得板带钢的厚度和宽度范围更加广泛,产品质量更加稳定可靠。
总的来说,热轧板带钢的发展历史可以追溯到19世纪末的工业革命时期,经过多个阶段的改进和创新,技术不断进步,产品质量不断提高。
如今,热轧板带钢已成为建筑和制造业中不可或缺的重要材料之一。
板带生产工艺5(热连轧带钢生产)

调宽轧制(AWC)及自由程序轧制(SFR) 尽可能不在或少在更换产品与铸坯 原料的规格品种,更换轧辊与导卫等装 置,改变轧制工艺条件及处理事故等方 面耽误时间,以保证过程的节奏性和连 续性不受影响和破坏,这在热连轧带钢 生产中主要包括有灵活变更宽度的技术, 自由程序(或随意计划)轧制技术及缩减 自由程序(或随意计划) 换辊的次数与时间等。
调宽轧制(AWC)
现代化的板坯连铸机一般具有在线 调宽技术,但即使连铸机具有快速调宽 装置,为了稳定浇铸作业,稳定炼钢与 连铸的节奏均衡及减少锥形板坯的长度, 也应尽量减少结晶器宽度的调节变化, 亦即结晶器宽度的改变应该是越少越好, 而将调宽改变板坯规格的任务主要交给 轧钢去承担。在轧钢车间调控板坯的宽 度采用的技术主要有:
日本钢管福山厂继新日铁界厂、室兰厂等之后 于1984年9月实现了宽带钢的CC-DR工艺,其 布置如图所示。该厂将连铸机安装在距炼钢设 备630m的宽带钢轧机的头部200m处,钢水包 经铁路送来进行连铸。生产线上装有二流板坯 连铸机。连铸板坯厚220mm、宽 700~1650mm、长5900~145O0mm。采用长 32m、容量为225720×l03kJ/h 的板坯边缘部加热器及2400kW,500~1000Hz 可变频板料边部感应加热器,精轧前使板坯边 部温度由1070℃提高到1250℃~1270℃,以保 持板坯断面温度均匀。
为使连铸与轧机生产能力相匹配,连铸 速度必须保持在2.0~2.5m/min的范围内。 热轧成品尺寸为厚1.0~12.7mm,宽 600~1630mm,卷重30t。设有在线缺陷 600~1630mm 30t 检测器,把一部分有缺陷的板坯检出, 经清理后与一部分冷坯装入加热炉,进 行加热和轧制。该厂月产量24万t,直接 轧制量15万t,直轧率达62.5%。
薄规格热轧带钢轧制技术研究

薄规格热轧带钢轧制技术研究摘要:常规热连轧相对于薄板坯连铸连轧而言,不具有铸坯薄、轧件头尾和断面温度均匀等优点,因而在薄规格轧制方面没有优势。
但是随着各轧机设备的功能不断优化,计算机控制技术的不断提高,核心配套制造水平的不断提升,市场对钢铁材料综合性能要求的不断更新,真正实现了热轧带钢产品从规格到品种的全覆盖,因此提高热轧薄规格的稳定性是该生产线追求的新目标。
本文从温度控制、中间坯形状控制、穿带翘头、甩尾等方面对常规2250mm热连轧生产线轧制薄规格的关键技术进行了分析和总结。
关键词:薄规格热轧带钢;轧制技术前言目前受国内钢铁行业遇冷、钢材产量饱和、国内外钢铁企业盈利空间下降等影响,业内大多数企业处于微利或亏损状态。
因此,如何降低生产经营成本、提高经济效益成为钢铁厂的主要目标,其中生产薄规格产品就是有效措施之一,也是衡量一个企业生产技术水平的主要指标。
1存在的问题虽然薄规格的吨钢价格较高,但是薄规格产品轧制时,极易在带钢头部发生轧破、轧碎,在带钢尾部发生甩尾等问题,并使后续生产的带钢产生硌印、卡钢的几率大大增加。
以上轧制不稳定的情况对薄规格产品,特别是极限规格产品批量组织生产带来困难,而且对各项工艺指标(终轧温度、平直度、凸度等)的控制产生影响,使带钢内部组织产生不一致,导致产品性能和尺寸精度不合格,影响正常的交货周期。
2轧制薄带钢控制措施2.1温度控制2.1.1 中间坯长度上温差控制轧制厚度2.0mm及以下薄规格产品,中间坯长度约60m以下,而厚度仅为38mm,按精轧轧制时间2.0min计,中间坯的头尾温差达60~80℃。
为了有效减小中间坯在长度方向上的温差,采取了以下的措施:(1)提前投入中间坯保温罩;(2)提高精轧机轧制速度,适当提高终轧温度;(3)薄规格计划不安排10米以上板坯,减小中间坯长度;(4)加热炉烧钢时,坯料头部温度适当比尾部提升10~20℃。
通过以上措施,中间坯的头尾温差基本控制在50℃以内。
热轧带钢的生产工艺流程
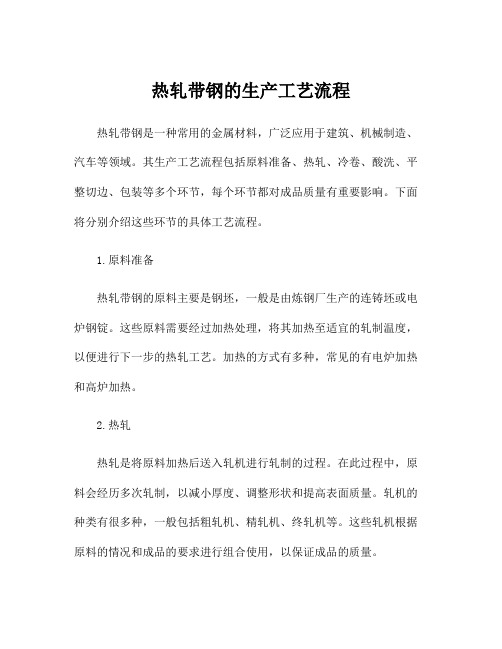
热轧带钢的生产工艺流程热轧带钢是一种常用的金属材料,广泛应用于建筑、机械制造、汽车等领域。
其生产工艺流程包括原料准备、热轧、冷卷、酸洗、平整切边、包装等多个环节,每个环节都对成品质量有重要影响。
下面将分别介绍这些环节的具体工艺流程。
1.原料准备热轧带钢的原料主要是钢坯,一般是由炼钢厂生产的连铸坯或电炉钢锭。
这些原料需要经过加热处理,将其加热至适宜的轧制温度,以便进行下一步的热轧工艺。
加热的方式有多种,常见的有电炉加热和高炉加热。
2.热轧热轧是将原料加热后送入轧机进行轧制的过程。
在此过程中,原料会经历多次轧制,以减小厚度、调整形状和提高表面质量。
轧机的种类有很多种,一般包括粗轧机、精轧机、终轧机等。
这些轧机根据原料的情况和成品的要求进行组合使用,以保证成品的质量。
3.冷卷热轧完毕后,成品还需要进行冷卷处理。
冷卷是将热轧带钢送入冷轧机进行二次轧制,以获得更高的表面质量和更好的机械性能。
冷卷后的带钢表面光滑,尺寸精确,结构紧密,力学性能良好。
4.酸洗冷卷完毕后,带钢表面会有一层氧化皮和油污,需要进行酸洗去除。
酸洗是将带钢送入酸洗槽中,在盐酸或硫酸的环境下进行酸洗处理,去除表面氧化层、油污和杂质,以提高带钢表面质量和增强附着力。
5.平整切边经过酸洗处理后的带钢需要进行平整和切边。
平整是指通过辊压机或拉伸机进行带钢的拉平处理,使其表面更加光滑平整,尺寸更加精确。
切边是指对带钢的边缘进行切割,使其边缘更加整齐,以满足不同客户的要求。
6.包装最后一道工序是将成品带钢进行包装。
一般来说,成品带钢会经过检验、打包、标识等环节,然后进行存储和运输。
包装的方式有多种,常见的有卷取式包装和条形包装,根据客户的需求和成品的规格进行选择。
总的来说,热轧带钢的生产工艺流程包括原料准备、热轧、冷卷、酸洗、平整切边、包装等多个环节,每个环节都对最终产品的质量有重要影响。
只有严格按照工艺流程进行操作,并且保证每个环节的质量把控,才能保证生产出优质的热轧带钢产品。
金属属性加工学--板材课后题

有不正确的大家改改一、填空:1.板带钢主要按厚度来进行分类。
2. 按厚度不同将板带钢分为薄板、厚板两大类。
3.对板带钢的技术要求有尺寸精确高、板形好、表面质量高、性能良好四方面。
4.尺寸精度主要是指厚度精度。
5.板形的好坏与厚度精度有直接关系。
6.轧钢常用的原料有连铸坯、铸锭、初轧坯三种,板带常用的是连铸坯。
7.板带钢轧制的突出特点是轧制压力大。
8.板带钢热轧时重点在降低内阻,冷轧时重点在降低外阻。
9.降低外阻的主要措施是减小工作辊直径、采用轧制润滑、采用张力轧制,其中主要是减小工作辊直径二、问答题1.连铸与轧制衔接模式有哪几种?方式1…为连续铸轧工艺,铸坯在铸造的同时进行轧制。
方式1为连铸坯直接轧制工艺(CC-DR),高温铸坯不需进加热炉加热,只略经补偿加热即可直接轧制。
方式2为连铸坯直接热装轧制工艺(CC-DHCR或HDR),也称高温热装炉轧制工艺,铸坯温度保持在A3 线以上奥氏体状态装入加热炉加热到轧制温度后进行轧方式3和4为铸坯冷却至A3甚至A1线以下温度装炉,也称低温热装工艺(CC-HCR)。
和2一样,都需加热炉加热,故可统称为连铸坯热装轧制工艺。
方式5为常规冷装炉轧制工艺。
2.什么是连铸坯直接轧制工艺,有何特点?总结:在连铸机和轧机间无正式加热炉缓冲工序的称为直接轧制工艺;只有加热炉缓冲工序且能保持连续高温装炉的称谓直接高温热装轧制工艺;连铸坯温度在A3线以上(1100℃),无正式加热工序,铸坯热轧前无相变,保留粗大奥氏体晶粒。
低温热装工艺则在加热炉前有缓冷坑或保温炉缓冲。
一般以400度作为热装、冷装的分界3.连铸坯热送热装和直接轧制的主要优点有哪些?热装和直接轧制的特点:利用冶金热能,节约能源;提高成材率,节约金属消耗;简化生产工艺流程;大大缩短生产周期;提高产品质量。
4.实现连铸连轧的主要技术环节有哪些?铸坯温度保证与输送技术;(关键技术)自由程序(灵活)轧制技术;生产计划管理技术;工艺设备的可靠性技术。
热轧薄板带钢生产-连铸连轧及连续铸轧技术教学课件46P
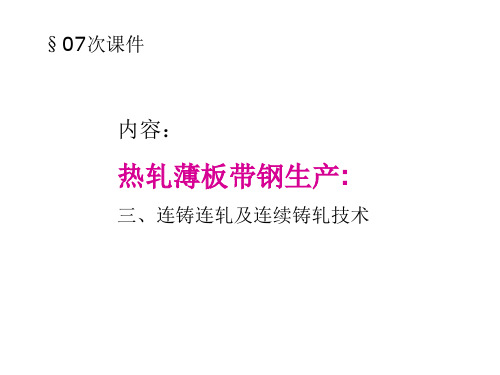
温
炉
薄
度
炼 钢 炉
外 精 炼 装
板 坯 连 铸
流 量 衔 接
热 连 轧 机
置
机
装
置
刚性工艺装置
柔性工艺装置
1.薄板坯连铸设备
2.温度、流量衔接装置:称为均热炉
形式有三种:
直通式辊底隧道炉、感应加热炉、步进炉应加热炉 1)直通式辊底隧道炉
(1) 直通式辊底隧道炉的结构、特点及参数
炉子长度:200米左右 炉子分段: 加热段、保温段、缓冲段、出料段等组成。
目的:改善轧辊磨损和轧辊辊面粗糙。
(4)润滑轧制技术
概念:在轧制过程中,向轧辊辊面喷涂一种特殊轧制 油,通过辊子的旋转,将润滑剂带入变形区,使轧辊及轧 材表面形成一层极薄的油膜。
优点:油膜改变了变形区的变形条件,降低了轧制力, 减少了轧辊的磨损,提高了产品的表面质量。
难点:如何解决轧件咬入问题,即选择最优的喷油开 闭时间
控制理论:利用液压压下的高响应性和良好的设定精度, 开发了高精度的轧机水平调整技术。它可以在极短的时 间内进行自动水平调整,使左右两侧轧制力之差恒定, 从而实现了蛇形控制。
三、典型的薄板坯连铸连轧工艺
1)CSP工艺技术 (Compact Strip Production—紧凑式带钢生产技术) (1)主要设备: 组成:CSP连铸机、辊底式加热炉、精轧机、层流冷却
C 克服在两相区轧制的危害;(因奥氏体轧制时温降 大,有时进入两相区)
D 提高轧机的生产效率;(增大压下,减小道次)
E 生产更薄规格的热轧带钢;(铁素体较软) F 为冷轧提供冲压性能更高的带钢。
(2)半无头轧制技术
概念:
铸坯长度相当于4~6块单块轧制的薄板坯,加热后进入 轧机,轧后的带钢由高速飞剪分切成所要求重量的钢卷。 优点:
热轧薄板带钢生产

(1)作业率的不匹配。 (2)生产节奏不匹配。 (3)板坯的温度场不同。 (4)对铸坯的尺寸要求不同。 (5)维修和停机的周期不同。
整理课件
薄板坯连铸连轧不能完全代替传统的热连轧工艺
原
压缩比小
因
产品表面质量差
整理课件
二、薄板坯连铸连轧生产中的主要设备及工艺
薄板坯连铸连轧工艺的组成:
炉子长度:200米左右 炉子分段: 加热段、保温段、缓冲段、出料段等组成。
作用
加热保温作用; 缓冲作用:缓冲时间10min左右。
整理课件
(2) 辊底式炉的横移方式
整理课件
(3) 直通式辊底隧道炉的工艺操作:
a. 板坯剪切后,头部翘起100mm,尾部保持平直, 避免撞击炉辊。
的压缩并流畅地结合在一起。
2.近终形连铸技术:在保证成品钢材质量的前提下,
尽量缩小铸坯的断面来取代压力加工。
3. 薄板坯连铸连轧的优点
(1)工艺简化,设备减少,生产线短。 (2)生产周期短。 (3)节约能源,提高成材率。 (4)更有利于生产薄带和超薄带钢
整理课件
4.实现薄板坯连铸连轧的主要条件
(1)具备高温无缺陷板坯的生产技术。 (2)连铸机具有板坯在线调宽技术。 (3)炼钢、连铸机、热连轧机操作高度稳定
②当卷取机咬入带钢以后,辊道速度应与轧制和 卷取速度同步进行加速,以防产生滑动擦伤。
③当带钢尾部离开轧机以后,辊道速度应比卷 取速度低,使带钢尾部“拉直”。
整理课件
6)精 整 热带钢生产精整作业线内容:平整、横切、纵
切、分卷、酸洗等 1、平整
目的:改善钢板的板形和消除局部的厚度差。
图 平整机组 1-开卷机;2-直头机;3-侧导辊;4-四辊式平整机;5-下切剪; 6-侧导辊;7-导辊;8-张力卷取机
稳定薄规格带钢生产的措施及效果

A s r c : T e e t n l s S h A v n a e n f i u t n i e f r d c s f o R l e h e btat h t x a a y i t e d a t g a d Di f c l y o L n o P o u t o H t o l d S e t
表 12 0  ̄2 0 04 0 5年主要技术经济指标 完成情况对 比
- 兰 蔓塑 ■ 圭 !
维普资讯
表 2 2 0  ̄2 0 0 4 0 5年 薄 规 格 产 品产 量 情 况 对 比
2US . T P线 生 产 薄 规 格 热 轧 带 钢 技 术 难 点
由于 市场 影 响 , 定 薄 规 格 钢 板 生产 , 高 3 Om 稳 提 .m
以下薄规格板带产量成为工作重点,因此唐钢热 轧薄 板厂 必须通 过 技术创 新 、 技术 改造 开发 新 品
要技术 经济指标完成情 况对 比。表 2 20  ̄ 为 04 20 年薄规格产 品产量情况对比。 05
C uC u — u n x e i T n x uX u Z e  ̄J a3 n Y n a iQ n  ̄Y n a — i2 h h n G a g ,G nL — a g ,D i— h n i u — a H oL — i g a gH i X a
(.o o ld S e tF co y o a g S e l . eh ia e t r o a gS e l e e , C ia 0 3 1) 1H t R l e h e a t r fT n— te :2 T c n c lC n e f T n — t e :Hb i hn 6 0 6
2 1US 线适合轧制薄规格热轧带钢的设计特点 . TP
1轧钢热轧冷轧工艺介绍

②电焊管生产 电焊管生产具有尺寸范围广、可以生产各种成分的钢管
(如难穿孔的高合金钢)、钢管尺寸精确、质量好和便于实 现机械化等优点,近来发展较快。
主要工序有: 管坯准备(拆卷、矫直、切边、表面清理、切头与端头焊 接)、管坯成型、管缝焊接、钢管精整(包括定径减径、矫 直、探伤、热处理、液压实验及其它加工部分)。
15
3)钢管:(8%~16%)
凡是全长为中空断面且长度与周长之比 较大的钢材称为钢管。
钢管规格用其外形尺寸(外径或边长) 和壁厚(或内径)表示。各种钢管的规格按 直径和壁厚的组合很多,其外径最小可达 0.1mm,大至4000mm;壁厚薄达0.01mm, 厚至100mm.
16
(1)按用途分为管道用钢、锅炉用钢、地质钻探管、 化工用管、轴承用管、注射针管等; (2)按制造方法分为无缝钢管、焊接(有缝)钢管及 冷轧与冷拔管; (3)按管端形态可分为光管和车丝(带螺纹的)管; (4)按外径和壁厚之比的不同分为特厚管、厚壁管、 薄壁管和极薄壁管。
1.金属成型方法
(1)铸造: (2)切削加工:包括车、刨、铣、磨、钻等; (3)焊接: (4) 金属压力加工(轧制、锻造、冲压、拉拔、挤压)。
1
2.金属压力加工的方法
★金属压力加工:
金属在受到外力作用并不破坏自身完整性的条件下, 稳定改变其几何形状与尺寸,从而获得所需要的几何形状 与尺寸的加工方法。
17
2. 轧钢机
1)轧钢机的基本组成: 轧制钢材的设备称为轧钢机。
轧钢机由轧辊、工作机架、齿轮机座、联 接轴和联轴节、主电机等组成。
18
2) 轧钢机的分类:
(1)按轧机的用途分类
①初轧机:以轧辊直径大小命名,例如:1150初轧机; ②型钢轧机:以轧辊直径或齿轮机座中的人字齿轮的节圆直径来表示
热轧轧机——精选推荐

1综述1.1 热轧板带钢生产状况热轧带钢是重要的钢材品种,对整个钢铁工业的技术进步和经济效益有着重要影响。
发达国家热轧带钢产量约占热轧钢材的50%以上,并在国际市场竞争中居于领先地位。
我国钢铁工业近年来产量增长较快,但高附加值产品的数量和质量较低。
我国一般热轧带钢产品厚度下限是1.8mm,但实际上只生产很少厚度小于2.0mm的热轧带钢,即使窄带钢,产品厚度一般也大于2.5mm。
因此,相当一部分希望使用厚度小于2mm带钢作原料的用户,只得使用冷轧带钢。
如果能开发薄规格的热轧带钢,则可代替相当一部分的冷轧带钢使用,使生产成本大为降低[1]。
1.1.1 热轧宽带钢生产状况国外热轧宽带钢生产的技术进步表现在以下几方面:①热带钢无头轧制技术[2]。
无头轧制技术能稳定生产宽薄带钢及超薄热轧带钢,其宽厚比可由传统热连轧的800∶1提高到1 000∶1,并能应用润滑轧制及强制冷却技术生产具有新材料性能的高新技术产品②薄板坯连铸连轧技术。
它主要有紧凑式热带钢生产工艺CSP (Compact Strip Process)、在线热带钢生产工艺ISP (In-Line Strip Production)、灵活式薄板坯轧制工艺FTSR (Flexible Thin Slab Rolling)和连铸直接轧制工艺CONROLL等10余种类型。
德国SMS公司开发的CSP工艺已成功地轧制出厚度为0.8mm的薄带钢产品,并已经广泛应用在家用电器、建筑工业等领域;奥钢联(VAI)开发的CONROLL工艺也成功地生产出厚度0.9mm~1.0mm、表面质量极好的热轧薄带钢,可用作汽车的外露部件;美国至今已经投产的薄板坯连铸连轧生产线达百余条,生产能力5×107t/年[3]。
③铁素体区轧制生产工艺。
它又称相变控制轧制,是由比利时冶金研究中心于1994年开发的一项轧制新技术,当初主要目的就是用薄规格的热轧带钢取代1.0mm~2.0mm厚度范围的冷轧产品。
国丰热轧薄规格窄带钢生产实践

总第265期2018年第1期HEBEIMETALLURGYTotalNo.2652018,Number1收稿日期:2017-09-25作者简介:李海滨(1974-),男,助理工程师,2009年毕业于唐山科技职业技术学院冶金工程专业,现在唐山国丰钢铁有限公司薄板厂工作,E-mail:2286498667@qq.com国丰热轧薄规格窄带钢生产实践李海滨,陆国栋(唐山国丰钢铁有限公司薄板厂,河北唐山063300)摘要:详细介绍了唐山国丰薄板厂620窄带生产线的设备技术参数及轧制工艺。
对轧制薄规格带钢过程中的温度控制、轧制过渡、板型控制、头部温降控制、甩尾、飘钢、轧烂等问题进行了重点提示。
针对轧制薄规格带钢时容易出现的折印、中间浪、折边、混晶缺陷提出了应对措施。
实践证明:轧薄需要足够的功率和良好稳定的轧制设备;板型控制是轧薄的关键;轧薄容易出现的折印、中间浪、混晶、折边缺陷中,折印普遍存在屈服强度低的带钢表面,且热轧不能消除,中间浪、混晶、折边可以通过针对性的措施消除。
关键词:薄规格窄带钢;轧制;实践中图分类号:TG335.5 文献标识码:B文章编号:1006-5008(2018)01-0066-03doi:10.13630/j.cnki.13-1172.2018.0116PRODUCTIONPRACTICEOFHOT-ROLLEDTHINGAUGENARROWSTRIPINGUOFENGLiHaibin,LuGuodong(StripmillofTangshanGuofengironandSteelCo.,Ltd.,Tangshan,Hebei,063300)Abstract:Thetechnicalparametersandrollingprocessof620narrowstripproductionlineinTangshanGuofengstripmillareintroducedindetails.Thispaperfocusesonthetemperaturecontrol,rollingtransition,shapecontrol,headtemperaturedropcontrol,tailflick,etcSomecountermeasuresareputforwardforthedefectsofcrossbreak,middlewaves,foldingandmixed-phaseduringtherollingprocess.Itisprovedthatshapecontrolisthekeyofsheetrollingwhichneedssufficientpowerandstablerollingequipment.Asfortheabovedefects,crossbreakisgenerallyfoundonthestripsurfacewithlowyieldstrength,whichcannotbeeliminatedbyhotrolling;middlewaves,foldingandmixed-phasecanbeeliminatedthroughtargetedmeasures.KeyWords:thingaugenarrowstrip;rolling;practice0 引言中国窄带钢市场已经历了20多年的发展,市场进一步分化,以热带冷,薄规格需求增加,质量要求也进一步提高。
- 1、下载文档前请自行甄别文档内容的完整性,平台不提供额外的编辑、内容补充、找答案等附加服务。
- 2、"仅部分预览"的文档,不可在线预览部分如存在完整性等问题,可反馈申请退款(可完整预览的文档不适用该条件!)。
- 3、如文档侵犯您的权益,请联系客服反馈,我们会尽快为您处理(人工客服工作时间:9:00-18:30)。
(2)当前降低成本,提高经济效益,节 约能耗和提高成材率成为关键问题,为 此而迅速开发了一系列新工艺新技术 (3)为了提高质量而采用高度自动化和 全面计算机控制,采用各种AGC系统和 液压控制技术,开发各种控制板形的新 技术和新轧机,利用升速轧制和层流冷 却以控制钢板温度与性能。 厚度精度由过去的人工控制的±0.2mm提 高到0.05mm,终轧和卷曲温度控制在 ±15℃以内。
26
3/4连续式
• 可逆式轧机可以 放在第二架,也 可以放在第一架, 前者优点是大部 分铁皮已在前面 除去,使辊面和 板面质量好些, 但第二架四辊可 逆轧机的换辊次 数比第一架二辊 可逆式要多二倍。 一般还是倾向于 前者
27
• 优点:3/4连轧机较全连轧机所需设备 少,厂房短,总的建设投资要少5%~6%, 生产灵活性稍大些 • 缺点:可逆式机架的操作维修要复杂些, 耗电量也大些。对于年产300万t左右规 模的带钢厂,采用3/4连轧机一般较为 适宜 • 粗轧机组各机架都采用万能轧机,轧机 前都带小立辊,主要目的是用以控制板 卷的宽度,同时也起着对准轧制中心线
32
热卷取箱结构
• 主要优点: • 1)粗轧后在入精轧机 之前进行热卷取,以 保存热量,减少温降, 保温可达90%以上 • 2)首尾倒置开卷,以 尾为头喂入轧机,均 化板带的头尾温度, 可以不用升速轧制而 大大提高厚度精度
33
主要优点
3)起储料作用,这样可增大卷重,提 高产量 4)可延长事故处理时间约8~9min, 从而可减少废品及铁皮损失.提高 成材率 5)可使中间辊道缩短约30%~40%, 节省厂房和基建投资 因此在热轧带钢生产中采用热卷取 箱是发展的方向
热轧薄板带钢生产
热连轧带钢生产 中小型企业薄板带 钢生产 热连轧板带钢轧制规 程设计
2
一、热连轧带钢生产
• 1924年第一台带钢热连轧机投产, 连轧带钢生产技术得到很大的发展 • 现代热连轧机的发展趋势和特点 • 板带热连轧机生产技术(新技术)
工业发达国家中,热连轧带钢已占板带钢总产量的 工业发达国家中,热连轧带钢已占板带钢总产量的 80% 80% 左右, 左右, 占钢材总产量的 占钢材总产量的 50% 50% 以上,现代板带热连轧生产出现了很多新 以上,现代板带热连轧生产出现了很多新 技术 技术
6
热连轧带钢生产
1、原料选择与加热 2、粗轧 3、精轧 4、轧后冷却及精整 5、热带连轧机工艺流程与车间布置
7
1、原料选择与加热
• 原料:主要是初轧板坯和连铸板坯 • 由于连铸坯的优点,比初轧坯物理化学 性能均匀,且便于增大坯重,故对热带 连轧更为合适,其所占比重亦日趋增大, 很多工厂连铸坯已达100% • 板坯规格 • 厚度一般为50~300mm,多数为200~ 250mm,最厚达350mm
10
加热
• 加热设备:加热炉型式,基本上与 中厚板相类似 • 由于板坯较长,故炉子宽度一般比 中厚板要大得多,其炉膛内宽达 9.6~15.6m
11
加热
•为了适应热连 轧机产量增大的 需要,现代连续 式加热炉
• 一方面都采用多段(6~8段以上)供 热方式,以便延长炉子高温区,实 现强化操作快速烧钢,提高炉底单 位面积产量 • 另一方面尽可能加大炉宽和炉长, 扩大炉子容量。为了增加炉长,最 好采用步进式炉
15
粗轧(布置方式)
• 现代热带连轧机的精轧机组大都是 由6~8架组成,并没有什么区别, 粗轧机组的组成和布置不同是各种 形式热连轧机主要特征之所在 • 热带连轧机主要分为三大类 • 全连续式、 • 半连续式 • 3/4连续式
16
粗轧
17
粗轧(轧制方式)
• 不管是哪一类,实际上,其粗轧机 组都不是同时在几个机架上对板坯 进行连续轧制的 • 原因:粗轧阶段轧件较短,厚度较 大,温度降较慢,难以实现连轧, 也不必进行连轧
3
轧机类别 及代表轧 机 第一代热 连轧机
投产 年份 1960 年前 1958 60年 代 1964 1970 年后
最高速 度m/s 10-12 10.2
板卷单 重kg/mm 4-11 8.6
最大卷 重t -10 10.5
成品厚 度mm 2-10 2-8 1.512.7 1.512.7
主电机 总容量 104kw ≤5 3.5
38
精轧机组各机架的活套支持器
• 缓冲金属流量的变化,给控制调整以时 间,并防止成叠进钢,造成事故 • 调节各架的轧制速度以保持连轧常数, 当各种工艺参数产生波动时发出信号和 命令,以便快速进行调整。 • 带钢能在一定范围内保持恒定的小张力, 防止因张力过大引起带钢拉缩,造成宽 度不均甚至拉断 • 最后几个精轧机架间的活套支持器,还 可以调节张力,以控制带钢厚度。
34
3、精轧
• 由粗轧机组轧出的带钢坯,经百多米长 的中间辊道输送到精轧机组进行精轧。 精轧机组的布置比较简单。 • 带坯在进入精轧机之前,首先要进行测 温、测厚并接着用飞剪切去头部和尾部 • 切头的目的:为了除去温度过低的头部 以免损伤辊面,并防止“舌头”、“鱼 尾”卡在机架间的导卫装置或辊道缝隙 中。
35
精轧
• 切尾: • 有时还要把轧件的后端切去,以防 后端的“鱼尾”或“舌头”给卷取 及其后的精整工序带来困难。 • 现代的切头飞剪机一般装置有两对 刀刃,一对为弧形刀,用以切头, 这有利于减小轧机咬入时的冲击负 荷,也有利于咬钢和减小剪切力; 另一对为直刀,用于切尾。
36
精轧机组
•
37
活套支持器工作状态示意图
41
精轧
(D)达到最高速度后,至带钢尾部离开减 速开始机架(F1)为止,维持最高速度 (E)带钢尾端离开最末机架后,到达卷取 机前要使带钢停住,但若减速过急,则 会使带钢在输出辊道上堆叠,因此当尾 端尚未出精轧机组之前,就应提前减速 到规定的速度 (F)带钢离开最末架(F7)以后,立即将 轧机转速回复到后续带钢的穿带速度
24
粗轧
• 空载返回连续式轧机 • 为了减少粗轧机架,有的连续式轧 机第一或第二架设计成下辊可以利 用斜楔自由升降,借以实现空载返 回再轧一道,以减少轧机的数目 • 对一般连续轧机,空载返回再轧的 操作方法只是当其他粗轧机架发生 故障或损坏时才采用
25
粗轧
全连续问题
• 全连续式轧机:粗轧机组每架只轧一道, 轧制时间往往要比精轧机组的轧制时间 少得多,即粗轧机的利用率并不很高, 或者说粗轧机生产能力与精轧机不相平 衡 • 近年来,为了充分利用粗轧机,同时也 为了减少设备和厂房面积,节约投资, 而广泛发展一种3/4连续式布置形式 • 特点:粗轧机组内设置1~2架可逆式轧 机,把粗轧机由六架缩减为四架
14
粗轧(轧机结构)
板坯厚度大,温度 高,塑性好,抗力 小,选用二辊轧机 可满足工艺要求
• 板坯除鳞以后,接着进入二辊轧机轧制 • 随着板坯厚度的减薄和温度的下降,变 形抗力增大,而板形及厚度精度要求也 逐渐提高,故须采用强大的四辊轧机进 行压下,才能保证足够的压下量和较好 的板形 • 为了使钢板的侧边平整和控制宽度精确, 在以后的每架四辊粗轧机前面,一般皆 设置有小立辊进行轧边
31
粗轧
• 优点: • 保温结构简单,成本低,效率高,采用 它以后可降低加热炉出坯温度达75℃, 从而提高成材率0.15%,节约燃耗14%, 还可提高板带末端温度约100℃ • 使板带温度更加均匀,可轧出更宽更薄 重量更大及精度性能质量更高的板卷 • 使带坯在中间辊道停留达8min而仍保持 可轧温度,便于处理事故,减少废品, 提高成材率
22
粗轧
• 为了大幅度提高产量,广泛采用全 连续式轧机 • 全连续:是指轧件自始至终没有逆 向轧制的道次 • 半连续:是指粗轧机组各机架主要 或全部为可逆式而言
23
全连续式
• 粗轧机由5~6个 机架组成,每架 轧制一道,全部 为不可逆式,大 都采用交流电机 传动 • 优点:轧机产量 可高达400~600 万t/年,适合于 大批量单一品种 生产,操作简单, 维护方便 • 缺点:设备多, 投资大,轧制流 程线或厂房长度 增大
8
原料选择
• 宽度:近代连轧机完全取消了展宽 工序,以便加大板坯长度 • 采用全纵轧制,故板坯宽度要比成 品宽度大,由立辊轧机控制带钢宽 度 • 长度:主要取决于加热炉的宽度和 所需坯重
9
原料选择
• 重量:重量增大可以提高产量和成 材率,但受到设备条件、轧件终轧 温度与前、后允许温度差,以及卷 取机所能容许的板卷最大外径等的 限制 • 目前板卷单位宽度的重量不断提高, 达到15~30kg/mm,并准备提高到 33~36kg/mmΒιβλιοθήκη 23-30 28.6 25.1
23-36 36 23.6
45 45 44.5
0.9-25
0.9-25 1.225.4
350-600 600 400
4
1969 1989
12.7 10.21
现代热连轧机的发展趋势和特点
(1)为了提高产量而不断提高速度, 加大卷重和主电机容量、增加轧机 架数和轧辊尺寸、采用快速换辊及 换剪刃装置等 • 轧制速度普遍超过15~20m/s,高 达30m/s以上,卷重达45t以上,产 品厚度扩大到0.8~25mm/s,年产 可达300~600万t。
的作用
28
现代热连轧机工作机架轧辊直径范围
29
粗轧
• 为了减少输送辊道上的温度降以节 约能耗 • 近年来很多工厂还采用在输送辊道 上安置绝热保温罩或补偿加热炉 (器) • 在轧件出粗轧机组之后采用热卷取 箱进行热卷取等新技术
30
辊道保温罩绝热块的结构
• 利用逆辐射原理, 以耐火陶瓷纤维 做成绝热毡,受 热的一面覆以金 属屏膜,受热时 金属膜(0.05~ 0.5mm厚)迅速升 至高温,然后作 为发热体将热量 逆辐射返回给钢 坯
42