模具常见问题及解决方法
模具改善方案怎么写
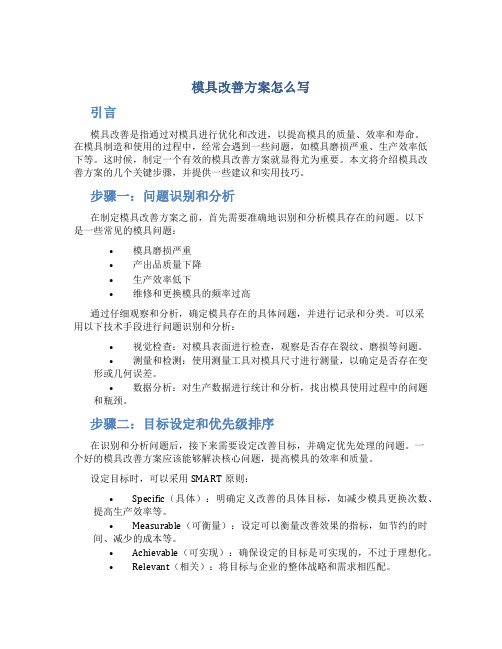
模具改善方案怎么写引言模具改善是指通过对模具进行优化和改进,以提高模具的质量、效率和寿命。
在模具制造和使用的过程中,经常会遇到一些问题,如模具磨损严重、生产效率低下等。
这时候,制定一个有效的模具改善方案就显得尤为重要。
本文将介绍模具改善方案的几个关键步骤,并提供一些建议和实用技巧。
步骤一:问题识别和分析在制定模具改善方案之前,首先需要准确地识别和分析模具存在的问题。
以下是一些常见的模具问题:•模具磨损严重•产出品质量下降•生产效率低下•维修和更换模具的频率过高通过仔细观察和分析,确定模具存在的具体问题,并进行记录和分类。
可以采用以下技术手段进行问题识别和分析:•视觉检查:对模具表面进行检查,观察是否存在裂纹、磨损等问题。
•测量和检测:使用测量工具对模具尺寸进行测量,以确定是否存在变形或几何误差。
•数据分析:对生产数据进行统计和分析,找出模具使用过程中的问题和瓶颈。
步骤二:目标设定和优先级排序在识别和分析问题后,接下来需要设定改善目标,并确定优先处理的问题。
一个好的模具改善方案应该能够解决核心问题,提高模具的效率和质量。
设定目标时,可以采用SMART原则:•Specific(具体):明确定义改善的具体目标,如减少模具更换次数、提高生产效率等。
•Measurable(可衡量):设定可以衡量改善效果的指标,如节约的时间、减少的成本等。
•Achievable(可实现):确保设定的目标是可实现的,不过于理想化。
•Relevant(相关):将目标与企业的整体战略和需求相匹配。
•Time-bound(有时间限制):设定一个明确的时间范围,使目标有明确的约束。
确定优先级时,可以根据问题的严重性、影响范围和可改善的效果等因素进行排序。
步骤三:寻找解决方案在设定目标之后,需要寻找适合的解决方案。
以下是几种常见的模具改善方案:•材料改进:选择更耐磨、耐腐蚀的材料,以延长模具的使用寿命。
•结构优化:通过对模具结构进行改进,提高模具的刚性和稳定性,减少变形和磨损。
常见模具问题改善方法

偏大1、凹凸模间隙太松加大凸模或减少凹模2、成形块直身太浅、R太大加高成形块减小R位3、压筋压太少追加压筋4、凹模顶底弹力太小加大弹力5、角度偏大研磨角度6、凸凹模未锁紧紧固螺丝或定位7、凸凹模边多边少重新调整间隙8、凸模深度不够调整凸模高度偏小1、凸凹间隙太紧加大间隙2、成形块直身太深R位太小减少成形块直身或加大R位3、压筋压得太深降低压筋4、凹模顶底力太小加大顶底顶力5、凹凸角位偏小调整角度6、凸凹模未固定固定凸凹模7、凸凹间隙边多边少重新调整间隙8、凸凹深度未到位调整深度偏高1、成形R位太小加大R位2、压筋太小加深压筋3、定位太松固定定位4、凸凹间隙太紧放松间隙5、剪口落料太多减少开料尺寸6、凸模压得太深把凸模上升7、凸凹不垂直调整凸凹垂直度偏低1、成形R位太大缩小R位2、压筋太少加大压筋3、定位太紧研磨定位4、凸凹间隙太松调整间隙5、剪口落料不够增加开料尺寸6、凸模压得不够调整凸模深度7、凸凹不垂直调整凸凹垂直度不脱料1、缺少或顶料力不够增加顶料或加大顶料力2、冲孔冲头太长缩短冲头3、外脱或内脱太紧或太低调整间隙增高内外脱4、未退磁或油类太多太浓退磁或更换油类5、冲头变形修理或更换冲头6、角度偏小或让位不够调整角度加大让位孔径不良1、冲头同镶件间隙不符调整冲头同镶件间隙2、冲孔后变形成形后冲孔3、冲头同镶件材质不够硬更换或调整冲头同镶件4、压料未到位调整压料5、烧公烧镶件省或更换公同镶件6、冲头或镶件崩角研磨或更换冲头同镶件拉料1、压料不够增加压料力或追加压筋2、余料太多减少余料3、冲头同镶件加钝研磨冲头同镶件4、间隙不符调整间隙产品擦伤1、光洁度太粗省光洁度2、间隙太紧调整间隙3、油类不够增加油类4、有异物去除异物5、凹模有印省光洁度6、米位不够省R位产品压印1、顶料销太利省顶料销光洁度2、压得太深压力太大调整压力3、顶料销孔螺丝孔销钉孔不够光滑省顶料销螺丝销钉孔4、凸凹模上有压印省平压卯5、凸凹模上有异物/产品有异物去除异物正批锋1、间隙不符调整间隙2、硬度不够更换或调整硬度3、铲模研磨刀口或更换刀口4、烧公或烧模省烧公或烧模、研磨,烧公或烧模更换公同镶件5、油类不够增加油类6、单剪口调整间隙,研磨刀口7、崩角研磨或更换刀口8、刀口钝研磨刀口反批锋1、外脱料太高弹力太大降低外脱料减少弹力2、间隙太大调整间隙拉深起皱1、弹簧力不够增加弹簧力2、R位不够光省R位3、走料不够增加走料4、间隙不符调整间隙5、油类不当更换油类6、压力不够增加压力7、转速太快减少转速拉深破裂1、R位不够增大R位2、光滑不够抛光3、拉深行程太多减少拉深行程4、间隙不符调整间隙5、边多边少调整间隙6、拉深油不当更换拉深油7、弹簧力不够增加弹簧力8、转速太快减少转速9、材质太硬更换材质10、拉深力太小增加拉深力平面度不良1、压力不够调整压力2、脱料不均调整脱料3、材质不当更换材质V折模可能产生的不良现象1、角度偏大偏小调整角度深度2、V折边有印省V折模边3、平面度超差硬成型冲及凹模取放料物方便性探讨1、非特别材料:模具要退磁2、连续模的落料:不是直接掉料的应加吹气或磨斜度3、导柱的设计应考虑取放材料及材料宽窄4、材料卸压及顶料的平面度5、模具应有材料固定位冲头折断分析1、塞屎2、冲头直身太长3、冲头无固定4、冲头小材料厚5、间隙不符6、刀口不对7、内脱料让位不够8、冲头太脆或不够硬9、冲头变形折弯角度不良(偏大、偏小)1、成形间隙大调整成形间隙为合理状态2、成形深度不够加深成形浓度不合理状态3、顶针顶料不顺修正顶针与轧弯距离,修正弹力大小不均4、R圆角过大减小R圆角,不良结果:会有拉伤偏小原因同偏大问题点修正对策相反折弯边高度不良偏高:1、设计展开2.拉料3、折弯R过大产品不脱料1、弹力太小加大弹簧力度2、冲头太紧重新修正过紧位置3、顶针孔到轧弯边距离太大修正顶针孔到边的距离4、角度小调整气压,骨位降低5、间隙紧调整成形间隙为合理状态6、脱料力不平衡修正平衡力度孔径不良孔过大:1、拉料孔变形、变大加大弹弓力度,减小拉料,加刻印2、冲头研磨不标准、过大按标准重新研磨3、冲针不圆修正重磨孔过小:1、压线太深,孔挤小减低压线2、冲头研磨过小重新研磨拉料现象1、单边折弯有拉料做档块结构2、成形力度不够,弹力过小,成形会拉料加大上下弹力产品擦伤1、间隙不合理、偏小调整间隙2、模板硬度不够加硬3、R角不够圆滑研磨R4、板件表面光洁度达不到要求产品压印1、与产品接触面凸起位修正光滑且圆角过度批锋正批锋:1、间隙过大2、间隙过小3、刀口不利反批锋:1、内脱高模面太多2、产品分离不顺畅拉伸起皱1、凸凹模不够光滑抛光凸凹模2、上下模压力太小加大上下模弹弓、气顶力度3、凸凹模间隙配对不均匀重新调整间隙4、周边无压料筋加压筋拉深破裂1、R角不够大、光滑2、压料力太大3、R角位硬度不够平面度不良1、下模脱料,压力不够大加大脱料力为气顶,弹力胶2、上模脱料不均匀,产品变形更改上模脱料结构V曲可能产生不良现象1、角度大调整啤机上升调整V曲深度变浅2、角度偏小与上述相反3、V曲时擦伤严重加大R位不良影响角度取放料的方便性探讨1、管位直身位要高顶针面二个料厚,管位尽量不采用管轧弯边冲头折断分析1、冲孔堵屎2、冲针在孔里摩擦不顺3、冲针太小无加强4、脱料不顺操作规程1、上落模操作规程上模前:首先检查啤机闭合高度是否够,模具螺丝是否紧固下模前:详细填写好模具调试管制单。
塑料模具设计常见问题及改进方法

塑料模具设计常见问题及改进方法塑料模具是塑料制品生产的关键工具,其设计质量直接影响着产品的成型质量和生产效率。
在塑料模具设计过程中,常会遇到一些常见问题,例如设计不合理、成型不良等。
本文将介绍塑料模具设计常见问题及改进方法。
一、常见问题1.设计不合理在塑料模具设计过程中,设计不合理是最常见的问题之一。
设计不合理会导致模具结构复杂、易损件过多、成本增加等问题。
这些问题都会影响模具的使用寿命和生产效率。
2.成型不良成型不良也是常见的问题之一。
成型不良可能是由于模具设计不合理、材料选择不当、成型参数设置不正确等原因导致的。
成型不良会影响产品的质量,甚至导致生产事故。
3.模具寿命短模具寿命短是塑料模具常见问题之一。
模具寿命短可能是由于材料选择不当、表面处理不到位、使用条件不合理等原因导致的。
模具寿命短会增加生产成本,降低生产效率。
4.技术水平低一些塑料模具设计人员技术水平低也是常见问题。
技术水平低会导致设计不合理、制造精度低、模具寿命短等问题。
5.应力集中在塑料模具设计中,应力集中也是一个常见问题。
应力集中可能导致模具开裂、损坏等问题,从而影响模具的使用寿命和生产效率。
二、改进方法为了解决设计不合理的问题,可以通过优化设计来改进。
优化设计可以减少模具结构复杂度、减少易损件、降低成本等。
优化设计可以采用CAD软件进行模拟分析,找出设计不合理的地方并进行改进。
2.增加冷却系统成型不良的问题可以通过增加冷却系统来改进。
增加冷却系统可以有效降低成型温度、缩短成型周期、提高产品质量。
合理的冷却系统设计可以通过有限元分析和实验验证。
3.优化材料选择模具寿命短的问题可以通过优化材料选择来改进。
优化材料选择可以选择抗磨损、抗腐蚀、高强度的材料,从而提高模具的使用寿命。
还可以采用表面处理技术来提高模具的使用寿命。
为了解决技术水平低的问题,可以通过提高技术水平来改进。
提高技术水平可以通过培训、学习、实践等方式来进行。
提高技术水平可以提高设计水平、精度水平、制造工艺水平等。
塑料模具设计常见问题及改进方法

塑料模具设计常见问题及改进方法塑料模具设计在实际应用中,常常会遇到一些问题,影响生产效率和产品质量。
下面将介绍一些常见的问题,并提出改进的方法。
1. 精度不够:在塑料模具的设计和制造过程中,如果精度不够,会导致产品尺寸和形状的不一致,影响产品的质量。
改进方法可以通过使用高精度加工设备和工艺,并进行严格的质量控制来提高精度。
2. 成型件表面质量不良:塑料模具中常常会出现成型件表面出现纹痕、气泡、疤痕等问题,影响产品的外观和质量。
改进方法可以选择适合的模具材料,提高模具表面光洁度,调整模具温度和冷却系统等。
3. 模具寿命短:塑料模具在长时间使用过程中容易出现磨损、疲劳断裂等问题,导致模具寿命较短。
改进方法可以选择耐磨性好的材料制作模具,增加模具的强度和硬度,正确使用和维护模具等。
4. 模具结构复杂:一些塑料模具的结构比较复杂,设计和制造难度大,容易出现问题。
改进方法可以使用先进的设计软件和CAD/CAM技术,优化模具结构,简化模具制造过程,提高生产效率和产品质量。
5. 生产周期长:一些塑料模具的设计和制造周期较长,影响生产进度和交货时间。
改进方法可以使用模具快速制造技术,如快速加工和快速制造等,缩短模具的设计和制造周期。
6. 模具排气不畅:在塑料模具制造过程中,如果模具的排气不畅,容易产生气泡等缺陷,影响产品质量。
改进方法可以优化模具的设计和加工过程,设置合适的排气口和排气系统,并通过模具试验和调整来改善排气效果。
7. 模具变形:一些大尺寸或复杂结构的塑料模具在使用中容易发生变形,影响产品的尺寸精度和外观。
改进方法可以通过增加模具的刚性和稳定性,使用优质的模具材料,控制模具温度和冷却系统等来减少模具变形。
塑料模具设计常见问题的改进方法主要包括提高精度、改善表面质量、增加模具寿命、简化结构、缩短生产周期、优化排气系统和控制模具变形等。
通过不断改进和优化,可以提高塑料模具的生产效率和产品质量。
注塑模具常见问题及解决办法【图解】

塑料模具,是塑料加工工业中和塑料成型机配套,赋予塑料制品以完整构型和精确尺寸的工具。
由于塑料品种和加工方法繁多,塑料成型机和塑料制品的结构又繁简不一,所以,塑料模具的种类和结构也是多种多样的。
注塑模具常见问题及解决办法详细介绍如下:1.浇口脱料困难在注塑过程中,浇口粘在浇口套内,不易脱出。
开模时,制品出现裂纹损伤。
此外,操作者必须用铜棒尖端从喷嘴处敲出,使之松动后方可脱模,严重影响生产效率。
这种故障主要原因是浇口锥孔光洁度差,内孔圆周方向有刀痕。
其次是材料太软,使用一段时间后锥孔小端变形或损伤,以及喷嘴球面弧度太小,致使浇口料在此处产生铆头。
浇口套的锥孔较难加工,应尽量采用标准件,如需自行加工,也应自制或购买专用铰刀。
锥孔需经过研磨至Ra0.4以上。
此外,必须设置浇口拉料杆或者浇口顶出机构。
2.导柱损伤导柱在模具中主要起导向作用,以保证型芯和型腔的成型面在任何情况下互不相碰,不能以导柱作为受力件或定位件用。
在以下几种情况下,注射时动,定模将产生巨大的侧向偏移力:(1).塑件壁厚要求不均匀时,料流通过厚壁处速率大,在此处产生较大的压力;(2).塑件侧面不对称,如阶梯形分型面的模具相对的两侧面所受的反压力不相等。
3.大型模具因各向充料速率不同,以及在装模时受模具自重的影响,产生动定模偏移。
在上述几种情况下,注射时侧向偏移力将加在导柱上,开模时导柱表面拉毛,损伤,严重时导柱弯曲或切断,甚至无法开模。
为了解决以上问题在模具分型面上增设高强度的定位键四面各一个,最简便有效的是采用圆柱键。
导柱孔与分模面的垂直度至关重要.在加工时是采用动,定模对准位置夹紧后,在镗床上一次镗完,这样可保证动,定模孔的同心度,并使垂直度误差最小。
此外,导柱及导套的热处理硬度务必达到设计要求。
4.动模板弯曲模具在注射时,模腔内熔融塑料产生巨大的反压力,一般在600~1000公斤/厘米。
模具制造者有时不重视此问题,往往改变原设计尺寸,或者把动模板用低强度钢板代替,在用顶杆顶料的模具中,由于两侧座跨距大,造成注射时模板下弯。
模具工艺改进方案
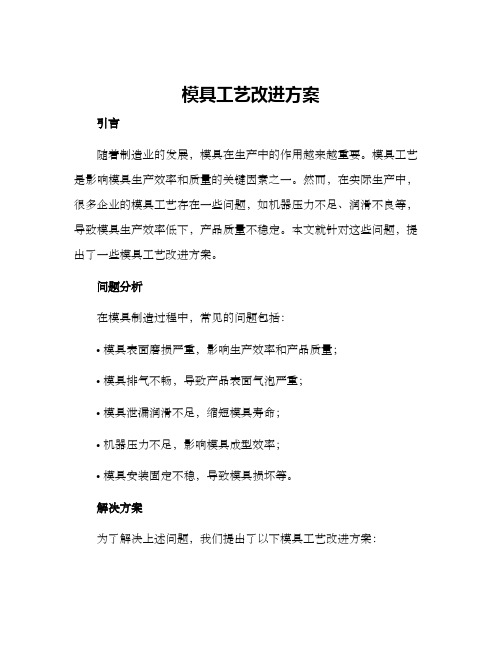
模具工艺改进方案引言随着制造业的发展,模具在生产中的作用越来越重要。
模具工艺是影响模具生产效率和质量的关键因素之一。
然而,在实际生产中,很多企业的模具工艺存在一些问题,如机器压力不足、润滑不良等,导致模具生产效率低下,产品质量不稳定。
本文就针对这些问题,提出了一些模具工艺改进方案。
问题分析在模具制造过程中,常见的问题包括:•模具表面磨损严重,影响生产效率和产品质量;•模具排气不畅,导致产品表面气泡严重;•模具泄漏润滑不足,缩短模具寿命;•机器压力不足,影响模具成型效率;•模具安装固定不稳,导致模具损坏等。
解决方案为了解决上述问题,我们提出了以下模具工艺改进方案:1. 模具表面处理一些模具表面磨损严重,导致模具生产效率低下。
因此,我们建议对模具表面进行处理。
这种处理方法可以采用电火花切割、高压水切割等方式。
经过处理后,模具表面会变得更加光滑,减少了摩擦,从而可以提高生产效率和产品质量。
2. 改善模具排气我们可以通过钻孔等方式改善模具的排气,从而减少产品表面气泡的产生。
同时,在模具设计和制造时,还应加以考虑,尽可能减少模具排气难度,以提高生产效率。
3. 加强模具润滑模具泄漏润滑不足是一个常见问题,我们可以在生产过程中加强模具润滑,特别是在模具关键部位涂抹润滑剂。
这样能够保持模具的润滑状态,延长模具寿命。
4. 调整机器压力机器压力不足是导致模具成型效率低下的一个重要原因。
我们可以通过调整机器压力,增加压力来提高成型效率,同时也可以减少因成型不牢固导致的浪费。
5. 加强模具的固定稳定性模具安装固定不稳会导致模具在生产过程中受损。
我们可以加强模具在机器上的固定稳定性,以避免不必要的损坏。
结论在模具制造过程中,模具工艺是一个非常关键的因素。
本文提出了一些模具工艺改进方案,以帮助企业改善生产效率和产品质量。
当然,不同的企业面临的问题和情况也不同,因此,我们应该根据实际情况,结合专业知识和经验,制定出更加恰当的方案,以提高生产效率和产品质量。
模具失效及解决方法实例

模具失效及解决方法实例一、引言模具是工业生产中必不可少的工具,它能够成型出各种形状和尺寸的产品。
然而,模具在使用过程中会受到各种因素的影响,导致失效。
模具失效不仅会影响生产效率,增加生产成本,还会影响产品的质量。
因此,了解模具失效的原因和解决方法非常重要。
本文将介绍模具失效的类型、原因以及一些常见的解决方法实例。
二、模具失效类型1. 磨损:模具在使用过程中,其工作表面会与材料不断接触,导致工作表面磨损。
2. 腐蚀:模具受到化学或电化学作用,导致腐蚀损坏。
3. 塑性变形:材料在模具内塑性变形,导致模具变形。
4. 热疲劳:模具在工作过程中频繁冷热交替,导致热疲劳损坏。
5. 裂纹扩展:由于制造、使用过程中产生的裂纹在交变应力作用下扩展导致破坏。
三、模具失效原因1. 操作不当:如超负荷生产、材料硬度过高、材料中有杂质等都会导致模具过早磨损或腐蚀。
2. 维护不当:润滑不足、冷却系统不良等都会导致模具过热或腐蚀。
3. 材料问题:模具材料的选择不当,如硬度、耐腐蚀性、耐磨性等都会影响模具的使用寿命。
4. 制造问题:制造过程中的缺陷,如铸造缺陷、热处理不当等都会导致模具产生裂纹或塑性变形。
四、解决方法实例1. 磨损修复:对于磨损的模具,可以采用堆焊、喷涂等方法进行修复。
例如,对于磨损的凸轮表面,可以采用堆焊的方式进行修复,选择耐磨性好、焊前流动性好的合金堆焊焊条。
在修复过程中,需要注意控制热输入,避免热影响扩大。
同时,对于一些磨损严重的模具,还可以采用喷涂的方法进行修复,选择耐磨性好、耐腐蚀的涂层材料,如金属陶瓷、镍基涂层等。
2. 腐蚀防护:对于腐蚀的模具,可以采用镀层、表面处理等方法进行防护。
例如,对于受腐蚀的模具钢表面,可以采用镀铬或镀锌等防腐方法进行防护。
此外,还可以采用表面处理的方法提高模具表面的抗腐蚀性能,如采用氧化处理、磷化处理等。
3. 温度控制:对于塑性变形的模具,可以通过调整生产工艺、选择合适的材料等方法来降低模具工作时的温度。
塑料模具设计常见问题及改进方法

塑料模具设计常见问题及改进方法塑料模具在现代工业生产中扮演着非常重要的角色,它直接影响了产品的质量和生产的效率。
塑料模具设计的质量直接影响着模具的使用寿命和产品的质量,因此塑料模具设计中常见的问题需要得到及时的解决和改进。
本文将重点介绍塑料模具设计常见问题及改进方法,希望能够帮助读者更好地理解和应对塑料模具设计中的挑战。
一、常见问题1. 设计不合理塑料模具在设计过程中,如果没有合理的考虑产品的结构特点、成型工艺和模具的工作原理,容易导致模具设计不合理。
比如模具结构设计不合理导致产品成型不良,模具寿命较短等问题。
2. 加工难度大一些塑料模具的设计结构复杂,加工难度大。
特别是一些细小、精密的塑料模具,加工难度更大。
一些特殊结构或者特殊材料的塑料模具,可能需要特殊的加工工艺,增加了加工难度和成本。
3. 寿命较短一些塑料模具因为设计不合理、材料选择不当或者加工工艺不良等原因,导致模具的寿命较短。
这不仅影响了生产的效率,还会增加生产成本。
4. 产品成型质量差塑料模具设计不合理或者模具加工精度不高可能会导致产品成型质量差。
比如产品出现毛边、气泡等缺陷,严重影响了产品的质量。
5. 不符合环保要求随着环保意识的增强,越来越多的塑料产品需要满足环保要求。
如果塑料模具的设计不符合环保要求,可能导致产品不符合标准,无法上市销售。
二、改进方法2. 提高加工精度加强塑料模具的加工工艺,提高加工精度。
选择适合的加工设备,采用适当的加工工艺,确保模具的尺寸精度和表面质量。
3. 选用高品质材料选择高品质的模具材料,确保模具的寿命和成型质量。
一些特殊材料,特别是一些特殊结构或者特殊工艺的塑料模具,还需要专门的材料选择和处理。
4. 加强模具的维护和保养对塑料模具进行定期的检查、清洁、维护和保养。
及时发现和修复模具的问题,延长模具的使用寿命。
5. 提高模具使用环境的卫生提高模具使用环境的卫生,确保模具的使用环境符合要求。
因为模具使用环境的卫生直接影响着模具的使用寿命和成型质量。
模具注塑常见问题及解决方法

模具注塑常见问题及解决方法模具注塑是一种常见的塑料加工方法,在生产过程中常常会遇到一些问题。
本文将针对模具注塑常见问题进行分析,并提出相应的解决方法,以帮助读者更好地应对这些问题。
一、模具注塑常见问题及解决方法1. 产品缺陷问题在模具注塑过程中,常常会出现产品缺陷问题,如翘曲、热缩、短射等。
这些问题的出现可能是由于模具设计不合理导致的,解决方法是对模具进行优化设计,确保模具的结构合理,避免产品缺陷的出现。
2. 模具磨损问题随着模具的使用,模具表面会出现磨损现象,这可能会导致产品的尺寸不准确或表面粗糙。
为了解决这个问题,可以采用定期维护模具的方法,及时清理模具表面的污垢,使用润滑剂减少磨损,并定期对模具进行研磨或更换磨损部位。
3. 模具温度控制问题在模具注塑过程中,温度的控制对产品质量至关重要。
如果温度控制不当,可能会导致产品尺寸不稳定、表面质量差等问题。
解决这个问题的方法是通过调节注塑机的温度控制系统,确保模具的温度在合适的范围内,并根据具体产品的要求进行调整。
4. 模具开裂问题模具在使用过程中可能会出现开裂的情况,这可能是由于模具材料强度不够或者受到过大的应力导致的。
解决这个问题的方法是选择合适的模具材料,并进行合理的模具结构设计,以增强模具的强度和稳定性。
5. 模具尺寸偏差问题在模具注塑过程中,由于材料的收缩和其他因素的影响,可能会导致产品尺寸与设计要求有偏差。
解决这个问题的方法是通过调整注塑工艺参数,如注塑温度、注塑压力等,来控制产品的尺寸,并根据实际情况进行模具结构的调整。
6. 模具堵塞问题在模具注塑过程中,有时会出现模具堵塞的情况,导致无法正常注塑。
解决这个问题的方法是通过清理模具内部的积聚物,如残留物、杂质等,并确保模具的通道畅通,以保证正常的注塑。
7. 模具寿命问题模具在长时间的使用过程中,可能会出现疲劳、损耗等问题,导致模具寿命减少。
为了延长模具的寿命,可以采取以下措施:定期对模具进行维护和保养,及时更换损坏的模具零件,提高模具的使用寿命。
注塑模具常见问题解决方案
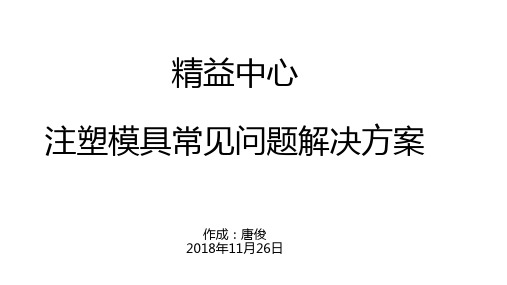
顶出机构设计不合理
圆筒、深腔类产品、深筋位、孔纹、气泡
原因分析
进浇口尺寸太小
进浇点位置设计不合理 模具困气
解决对策
大水口侧进浇厚度不能太薄,一般不小于主体壁厚1/2,潜筋位进浇口,筋位 适当加宽、浇口可做椭圆形改善进浇口表面困气不良。
进胶点的位置布置应充分考虑气体能顺利排出型腔,型腔的充填压力最小。 产品周圈分型面和熔胶未端需要加强排气、深筋、深柱超过6-8mm以上需要 做排气镶件。 PC、PMMA等透明部件防止冷料进入型腔而产生流痕必须做“S”形流道。
顶机构设计不合理 热量集中冷却不足 冷却不均
6.缩水
原因分析
产品胶位太厚 加强筋太厚 流道偏小 浇口偏小 产品走胶困难 浇口位置设计不合理 热量集中冷却不足 冷却不均
解决对策
模具设计前期应考虑产品避免局部胶位太厚,主体壁厚造型需均匀,拐角部位圆 角过渡。 加强筋厚度在模具设计时不超过主体壁厚的1/2,太厚产品表面会缩水,BOO柱根 部需做火山口减胶,深度0.3T,坡度为30º 比如PC、PC+ABS、玻纤类材料流行性不好,试模后可适当加大流道直径。 比如PC、PC+ABS、玻纤类材料流行性不好,试模后可适当加大浇口直径。 浇口数量的设计要考虑塑每种材料的流长比(L/T),产品深筋、薄避充填过程 容易产生滞留而导致缩水,产品、模具设计前期需要重点考虑。 浇口应设计在产品胶位较厚且容易走胶的部位,进胶压力损失少,利于充填。 深腔胶位、深骨类区域热量较集中,冷却缓慢,应该考虑增加水井加强冷却。 水路设计需随形产品胶位,水路直径D一般取数为6、8、10,具体根据模具规格 来调整,距离产品胶位10-20之间,水路间距等于5D,不小于30mm。
解决对策
碰穿面与插穿面,公模面负公差控制-0.015-0mm;母模面正公差控制+0.015-0
模具试模问题点和对策
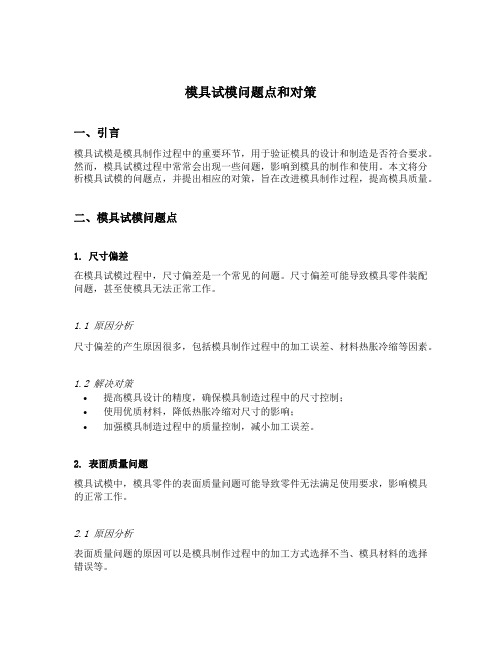
模具试模问题点和对策一、引言模具试模是模具制作过程中的重要环节,用于验证模具的设计和制造是否符合要求。
然而,模具试模过程中常常会出现一些问题,影响到模具的制作和使用。
本文将分析模具试模的问题点,并提出相应的对策,旨在改进模具制作过程,提高模具质量。
二、模具试模问题点1. 尺寸偏差在模具试模过程中,尺寸偏差是一个常见的问题。
尺寸偏差可能导致模具零件装配问题,甚至使模具无法正常工作。
1.1 原因分析尺寸偏差的产生原因很多,包括模具制作过程中的加工误差、材料热胀冷缩等因素。
1.2 解决对策•提高模具设计的精度,确保模具制造过程中的尺寸控制;•使用优质材料,降低热胀冷缩对尺寸的影响;•加强模具制造过程中的质量控制,减小加工误差。
2. 表面质量问题模具试模中,模具零件的表面质量问题可能导致零件无法满足使用要求,影响模具的正常工作。
2.1 原因分析表面质量问题的原因可以是模具制作过程中的加工方式选择不当、模具材料的选择错误等。
2.2 解决对策•合理选择加工方式,避免对零件表面造成过多的刀痕和热裂纹;•选择合适的模具材料,提高模具表面的硬度和耐磨性。
3. 压铸模具的冲击力问题压铸模具在试模过程中,往往需要经受较大的冲击力。
如果冲击力过大,可能导致模具零件断裂、变形等问题。
3.1 原因分析冲击力过大的原因可以是模具结构设计不合理、材料强度不足等。
3.2 解决对策•优化模具结构设计,增加模具零件的强度和刚度;•选择高强度的材料,提高模具的抗冲击性。
三、模具试模问题对策1. 尺寸偏差解决对策1.设计精度提升:–合理利用CAD/CAM技术进行精确绘制和加工;–增加模具试模过程中的检测频率,及时发现和修正尺寸偏差问题。
2.选材优化:–选择具有稳定性能的模具材料,如优质合金钢等;–充分考虑材料热胀冷缩特性,进行合理的尺寸设计。
2. 表面质量问题解决对策1.加工方式改进:–优化模具加工的工艺流程,减小切削力和热裂纹产生的可能性;–使用先进的电火花加工技术,提高模具表面质量。
模具常见问题及解决方法

模具常见问题及解决方法模具常见问题及解决方法1.冲头使用前应注意①用干净抹布清洁冲头。
②查看表面是否有刮、凹痕。
如有,则用油石去除。
③及时上油防锈。
④安装冲头时小心不能有任何倾斜,可用尼龙锤之类的软材料工具把它轻轻敲正,只有在冲头正确定位后才能旋紧螺栓。
2.冲模的安装与调试安装与调校冲模必须特别细心。
因为冲模尤其大中型冲模,不仅造价高昂,而且重量大微量移动困难,人身的安全应始终放在首位。
无限位装置的冲模在上下模之间应加一块垫木板,在冲床工作台清理干净后,将合模状态的待试模具置于台面合适位置。
按工艺文件和冲模设计要求选定的压机滑块行程,在模具搬上台面前调至下死点并大于模具闭合高度10~15mm的位置,调节滑块连杆,移动模具,确保模柄对准模柄孔并达到合适的装模高度。
一般冲裁模先固定下模(不拧紧)后再固定上模(拧紧),压板T型螺栓均宜使用合适扭矩扳手拧紧(下模),确保相同螺拴具有一致而理想的预加夹紧力。
可以有效防止手动拧紧螺纹出现的因体力、性别、手感误差造成的预紧力过大或过小、相同螺纹预紧力不等,从而引起冲压过程中上下模错移、间隙改变、啃剥刃口等故障发生。
试模前对模具进行全面润滑并准备正常生产用料,在空行程启动冲模3~5次确认模具运作正常后再试冲。
调整和控制凸模进入凹模深度、检查并验证冲模导向、送料、推卸、侧压与弹压等机构与装置的性能及运作灵活性,而后进行适当调节,使之达到最佳技术状态。
对大中小型冲模分别试冲3、5、10件进行停产初检,合格后再试冲10、15、30件进行复检。
经划线检测、冲切面与毛刺检验、一切尺寸与形位精度均符合图纸要求,才能交付生产。
3.冲压毛刺①模具间隙过大或不均匀,重新调整模具间隙。
②模具材质及热处理不当,产生凹模倒锥或刃口不锋利,应合理选材、模具工作部分材料用硬质合金,热处理方式合理。
③冲压磨损,研磨冲头或镶件。
④凸模进入凹模太深,调整凸模进入凹模深度。
⑤导向结构不精密或操作不当,检修模具内导柱导套及冲床导向精度,规范冲床操作。
塑料模具设计常见问题及改进方法

塑料模具设计常见问题及改进方法塑料模具设计在产品制造领域中起着至关重要的作用,它直接影响着产品的质量、成本和生产效率。
在实际的工程实践中,常常会面临一些问题,这些问题不仅影响着模具制造的进度和成本,还可能影响产品的质量。
对塑料模具设计中常见的问题进行分析和改进至关重要。
本文将就塑料模具设计中常见的问题及改进方法进行探讨。
一、常见问题1. 设计不合理在塑料模具设计中,设计不合理是一个常见的问题。
设计不合理可能表现为模具结构复杂、零件过多、形状复杂等。
这些问题会影响模具的加工难度和加工时间,进而影响模具制造的成本和周期。
2. 塑料熔体流动不均匀塑料模具设计中,塑料熔体流动不均匀也是一个常见问题。
塑料熔体流动不均匀可能导致产品表面出现痕迹、气泡或裂痕,影响产品的外观质量。
3. 模具寿命短模具寿命短是塑料模具设计中常见的问题之一。
模具寿命短可能与模具材料选择不合适、模具表面处理不当、模具结构设计不合理等因素有关。
4. 产品流道设计不合理产品流道设计不合理也是塑料模具设计中的一个常见问题。
产品流道设计不合理可能会导致塑料熔体流动不畅、充模不足,从而影响产品的成型质量。
5. 模具开发周期长模具开发周期长是另一个常见的问题。
模具开发周期长可能与设计修改频繁、样品确认时间长、加工难度大等因素有关。
以上这些问题都会影响模具制造的进度和成本,进而影响产品的质量。
对这些常见问题进行改进是非常重要的。
二、改进方法1. 设计合理化针对设计不合理的问题,可以通过合理化设计来改进。
合理化设计包括减少零件数量、简化结构、优化形状等。
合理化设计可以降低模具制造的难度和成本,提高模具的使用寿命。
2. 流道设计优化针对塑料熔体流动不均匀的问题,可以通过流道设计的优化来改进。
流道设计优化包括优化流道尺寸、优化流道布局、增加流道翻转等。
优化流道设计可以改善塑料熔体的流动性,提高产品的成型质量。
3. 材料选择和表面处理针对模具寿命短的问题,可以通过合理选择模具材料和进行合适的表面处理来改进。
模具异常及处理方法
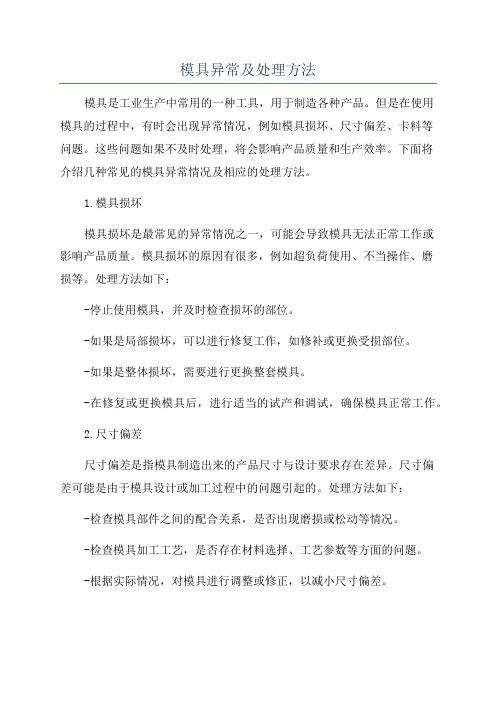
模具异常及处理方法模具是工业生产中常用的一种工具,用于制造各种产品。
但是在使用模具的过程中,有时会出现异常情况,例如模具损坏、尺寸偏差、卡料等问题。
这些问题如果不及时处理,将会影响产品质量和生产效率。
下面将介绍几种常见的模具异常情况及相应的处理方法。
1.模具损坏模具损坏是最常见的异常情况之一,可能会导致模具无法正常工作或影响产品质量。
模具损坏的原因有很多,例如超负荷使用、不当操作、磨损等。
处理方法如下:-停止使用模具,并及时检查损坏的部位。
-如果是局部损坏,可以进行修复工作,如修补或更换受损部位。
-如果是整体损坏,需要进行更换整套模具。
-在修复或更换模具后,进行适当的试产和调试,确保模具正常工作。
2.尺寸偏差尺寸偏差是指模具制造出来的产品尺寸与设计要求存在差异。
尺寸偏差可能是由于模具设计或加工过程中的问题引起的。
处理方法如下:-检查模具部件之间的配合关系,是否出现磨损或松动等情况。
-检查模具加工工艺,是否存在材料选择、工艺参数等方面的问题。
-根据实际情况,对模具进行调整或修正,以减小尺寸偏差。
-做好模具使用记录,及时分析和总结问题,改善模具设计或加工工艺。
3.卡料卡料是指在模具使用过程中,被加工材料卡在模具中无法顺利移出的现象。
这可能会导致模具损坏或产品质量问题。
处理方法如下:-检查模具的流道设计是否合理,是否存在死角或过于复杂的结构。
-检查模具表面的润滑情况,是否需要增加或更换润滑剂。
-检查模具的开模间隙是否合适,是否需要调整开模力度。
-对于经常出现卡料问题的模具,可以考虑增加振动装置或改善模具结构,以提高模具使用性能。
4.模具使用寿命低模具使用寿命低可能是由于材料质量、操作不当等原因引起的。
处理方法如下:-检查模具材料是否合格,是否存在质量问题。
-培训操作人员,提高其模具操作技能和注意事项的认识。
-加强模具的日常维护和保养工作,定期清洁和润滑模具。
-在使用过程中,严格控制模具的工作负荷,避免超负荷使用。
木质模具常见问题及解决方法
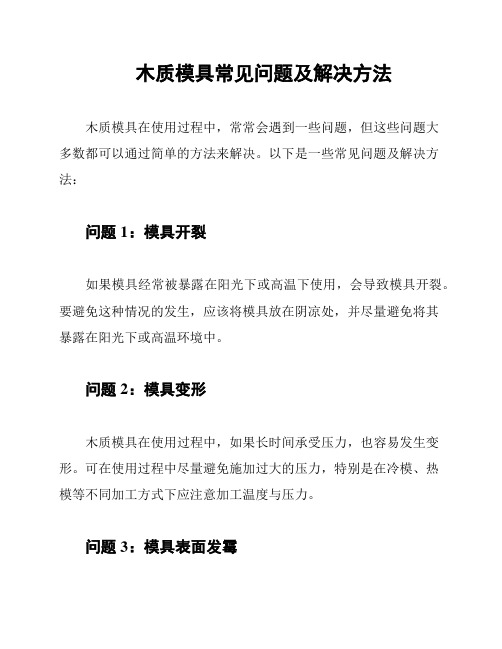
木质模具常见问题及解决方法
木质模具在使用过程中,常常会遇到一些问题,但这些问题大
多数都可以通过简单的方法来解决。
以下是一些常见问题及解决方法:
问题 1:模具开裂
如果模具经常被暴露在阳光下或高温下使用,会导致模具开裂。
要避免这种情况的发生,应该将模具放在阴凉处,并尽量避免将其
暴露在阳光下或高温环境中。
问题 2:模具变形
木质模具在使用过程中,如果长时间承受压力,也容易发生变形。
可在使用过程中尽量避免施加过大的压力,特别是在冷模、热
模等不同加工方式下应注意加工温度与压力。
问题 3:模具表面发霉
木质模具在潮湿的环境下容易发霉,导致表面失去光洁度。
如
果发现模具表面已经发霉,可以用一块湿布蘸取食盐轻擦模具表面,再用清水擦拭干净即可。
问题 4:模具不平整
如果模具的表面不平整,会导致制品表面出现小凸起或凹陷,
影响美观度。
此时可以在模具表面涂上一层薄油,再均匀地抹上一
层细沙,用细布擦拭沙子,直至模具表面平整。
问题 5:模具故障
如果在使用过程中发现模具出现故障,如断裂、变形或失效等,不应该自行修复,应该将其送到专业的维修机构进行处理。
以上是木质模具的一些常见问题以及解决方法,希望能够帮助
您更好地保养和使用模具。
冲压模具常见故障分析及解决方法

冲压模具常见故障分析及解决方法冲压模具在使用过程中,常常会出现一些故障,影响生产效率和模具寿命。
下面将介绍一些常见的冲压模具故障及解决方法。
1.模具损坏:模具在使用过程中容易出现磨损、断裂等问题。
其主要原因可能是设计不合理、材料选择不当、模具使用频繁或模具维护不当等。
解决方法包括:重新设计模具、更换高强度材料、合理安排生产计划以减少使用频率、定期维护和保养模具。
2.模具卡料:模具在冲压过程中可能会出现卡料现象,导致模具损坏和生产中断。
这通常是由于材料不适合冲压工艺或冲切刀刃不锋利引起的。
解决方法包括:调整冲压参数、更换合适的材料、定期维护冲切刀刃。
3.模具发热:冲压过程中,模具可能因为摩擦、压力等原因发热,进而影响冲压质量。
这往往是由于模具孔内润滑不良、冲压速度过快或冲压压力不稳定等原因造成的。
解决方法包括:添加润滑剂、调整冲压参数。
4.模具卡模:模具在工作过程中,可能会因为模具安装不稳固或模具部件变形等原因导致卡模。
解决方法包括:重新固定模具、更换变形的模具部件。
5.模具冷却不良:冲压过程中,模具需要通过冷却来保持合适的工作温度。
如果模具冷却不良,可能会导致模具变形、模具表面质量下降等问题。
解决方法包括:优化冷却水路径、增加冷却装置。
6.模具偏移:冲压过程中,模具可能会由于冲压压力过大、不均匀等原因导致偏移。
这通常是由于模具加工精度不高、模具安装不稳固或冲压设备不平衡等原因引起的。
解决方法包括:提高模具加工精度、重新固定模具、调整冲压设备。
7.模具寿命短:模具的寿命受到多种因素影响,包括材料质量、冲压参数、使用频率等。
如果模具寿命较短,可能是由于这些因素不合理引起的。
解决方法包括:选择优质的材料、优化冲压参数、适当减少使用频率。
总之,冲压模具在使用过程中常常会出现一些故障,但只要对问题进行准确分析并采取相应的解决方法,就可以及时解决问题,延长模具寿命,提高生产效率。
常见模具缺陷及解决办法

7)孔变形 判断方法:用眼睛看。 原因:冲头磨损。 处理办法:轻微的打油,严重的打油仍出现变形的应报告班长,通知修模
8)拉深不到位 判断方法:看压力点是否清晰。 原因:主压力偏小。 处理办法:适当调高
9)折边不良 判断方法:与样件比较 原因:件没摆好,定位装置问题。 应向班长报告,通知模修人员修模。
五、模具缺陷的分析和解决措施 1)凸模磨损太快 主要原因:①模具间隙偏小,一般建议模具总间隙为材 具的对中性不好,包括模座和模具导向组件及转塔镶套精度不足等原因造 过高,主要是由于同一模具连续长时间冲压造成冲头过热。④模具刃磨方 剧。⑤局部的单边冲切,如步冲、冲角或剪切时,侧向力会使冲头偏向一 磨损严重,如果机床模具安装精度不高,严重的会使冲头偏过下模,造成 (2)模具带料问题 模具带料会造成废料反弹,其相关因素:①模具刃口 越容易造成废料反弹。②模具的入模量,机床每个工位的入模量是一定的 反弹。③模具的间隙是否合理,如果模具间隙不合适,容易造成废料反弹 多的油物。⑤弹簧疲劳损坏。 防止模具带料的方法:①使用专用的防带料 利,并退磁处理。③增大凹模间隙。④采用斜刃口模具代替平刃口模具。 模具的入模量。⑦检查模具弹簧或卸料套的疲劳强度。 (3)模具对中性问题 模具在使用中容易发生冲芯各侧位置的磨损量不同 快,这种情况在细窄的长方模具上特别明显。该问题主要原因:①机床转 上下转盘的模具安装座的对中性不好。②模具的设计或加工精度不能满足 够。④模具间隙选择不合适。⑤模具安装座或模具导套由于长期使用磨损 磨损不一致,应:①定期采用对中芯棒对机床转塔和安装座进行对中性检 选用合适间隙的凸凹模具。③采用全导程模具。④加强操作人员的责任心 成更大损失。 (4)特殊成形模具使用 为满足生产需要,经常需要使用成形模具或特殊 窗模具、沉孔形模具、翻孔攻螺纹模具、凸台模具、拉伸模具、组合式模 大大提高生产效率,但是成形模具价格较高,通常是普通模具的 原则: ①模具安装时进行方向检查,确保模具凸凹模安装方向一致。 度,每次调整最好不超过0.15mm。 ③使用较低的冲切速度。 工位置应尽量远离夹钳。 ⑥成形模具使用时应避免向下成形操作。 使用成形模具。
模具试模问题点和对策

模具试模问题点和对策一、前言模具试模是模具制造过程中非常重要的环节,它直接关系到产品的质量和生产效率。
在实际操作中,我们会遇到各种各样的问题,如模具开裂、变形、尺寸偏差等,这些问题需要我们及时发现并采取措施解决。
本文将从试模前期准备、试模过程中常见问题及对策、试模后期总结三个方面进行阐述。
二、试模前期准备1.材料准备在进行试模前,首先需要准备好所需的材料。
包括塑料原料、辅助材料(如色母等)、注塑机所需的润滑油和冷却水等。
2.设备检查在开始试模之前,需要对注塑机进行全面检查。
检查内容包括:电气系统是否正常、液压系统是否正常、机械部分是否存在损坏或异响等。
如果发现问题需要及时处理。
3.注塑工艺参数设置根据产品要求和材料特性,合理设置注塑工艺参数。
包括:注射压力、保压时间、保压压力、融胶温度等。
4.清洁工作清洁工作是试模前必不可少的一项准备工作。
需要清洁注塑机、模具和周围环境,确保无杂质和灰尘。
三、试模过程中常见问题及对策1.模具开裂模具开裂是试模过程中常见的问题之一。
主要原因是注塑机的压力过大或者温度过高。
解决方法:适当降低注塑机的压力和温度,同时加强冷却。
2.模具变形在注塑过程中,由于注射压力和保压时间的作用,容易导致模具变形。
解决方法:增加支撑点或者加强模板结构,提高模具刚度。
3.尺寸偏差在生产中,产品尺寸偏差是一个非常严重的问题。
主要原因是注塑工艺参数设置不合理或者模具设计不合理。
解决方法:合理设置注塑工艺参数和优化模具结构。
4.热流道堵料热流道堵料会导致产品品质下降和生产效率降低。
主要原因是热流道内部积累了杂质或者色母等物质。
解决方法:定期清洗热流道,保持内部清洁。
5.模具表面粘附在注塑过程中,模具表面容易出现粘附现象。
主要原因是模具表面存在油污或者杂质等物质。
解决方法:定期清洗模具表面,保持干净。
四、试模后期总结试模结束后,需要对试模过程进行总结和分析。
从注塑工艺参数、模具设计、材料选择等方面进行分析,找出问题所在并采取措施解决。
- 1、下载文档前请自行甄别文档内容的完整性,平台不提供额外的编辑、内容补充、找答案等附加服务。
- 2、"仅部分预览"的文档,不可在线预览部分如存在完整性等问题,可反馈申请退款(可完整预览的文档不适用该条件!)。
- 3、如文档侵犯您的权益,请联系客服反馈,我们会尽快为您处理(人工客服工作时间:9:00-18:30)。
本次培训到此结束,谢谢!
8、产品不容易脱出ห้องสมุดไป่ตู้
通常在对部品进行排料时就应考虑部品的出料问题。一般情况下,我们采用以下几 种出料方式: ⑴:风吹出; 对于一些较小的产品,利用吹气销将其吹出。 ⑵:在重心作用下,产品自然滑落; 在下模铣一出料缺口,利用部品的自身重力滑落。 ⑶:零件推零件; 借助条料的传送力,将冲压完成后的部品推出模具。此时应注意模具的升料高度。 ⑷:零件由条料带出; 此方式一般运用在模具在最后工步对部品的外形进行整体落料的情况下采用,通过大力 弹簧将部品重新压入到条料中,在条料送出的同时将部品一同带出。 ⑸:零件整体落料; 在考虑运用此方式之前必须确认部品的毛刺方向是否允许? 为了避免部品粘附在卸料板或凹模板表面,通常会在最后工位的卸料板或凹模板上使用 小顶杆。
80
t
5° ~10°
°~
85
°
第 一 次 弯 曲
第 二 次 弯 曲
R
回弹抵消
回弹抵消
二次弯曲加工
7、模具容易磨损
影响因素:⑴:模具材料的选用; ⑵:模具润滑不够; ⑶:模具材质热处理不良; ⑷:模具间隙太小; 解决对策:⑴:选用合理优质的模具材料; ⑵:合理的润滑; ⑶:模具材料施以表面处理;(如镀钛) ⑷:选择合理的间隙;
5、冲头容易断裂
影响因素:⑴:由于模具间隙不均匀,冲头受到横向负荷而折断; ⑵:模具间隙小使冲头在脱料时受到横向负荷而折断; ⑶:冲头因导引不良使得冲头在冲切时有偏移现象; ⑷:冲头刃部长度过长; ⑸:冲头阶段部发生应力集中; ⑹:冲头所选用的材料; ⑺:冲屑堵塞造成冲头负荷增大; ⑻:卸料板因受到侧压而倾斜; 解决对策: ⑴:模具间隙要均匀; ⑵:模具间隙取大; ⑶:正确的冲头导引; ⑷:冲头刃部长度减短; ⑸:冲头阶段部施以R角; ⑹:使用高韧性的冲头材料; ⑺:凹模直段部取短及下模有确实的逃孔设计; ⑻:防止卸料板发生倾斜;
0.1~0.5mm
0.8t
3、卸料板脱料困难
影响因素:⑴:模具卸料力过小; ⑵:冲头发热膨胀卡住卸料板; ⑶:卸料板发生倾斜; 解决对策:⑴:增加模具卸料力; ⑵:设计冲头冷却装置; ⑶:合理安排工位,使卸料板受力均衡;
4、高的毛刺
影响因素:⑴:模具间隙太大或过小; ⑵:模具间隙有偏量; ⑶:冲头或凹模刃口磨损或有崩缺; ⑷:凹模直段部过长; ⑸:冲切速度; ⑹:冲头刃部侧面有伤痕; 解决对策:⑴:选择适当的间隙; ⑵:修正模具间隙使之均匀平衡; ⑶:研磨刃口; ⑷:刃件角部设计0.25~0.5T的R角; ⑸:凹模直段部长度减短; ⑹:增加冲切速度; ⑺:检讨模具材料及热处理条件; ⑻:增加去毛刺工序;(倒角、振磨)
对于直剪切冲头,通常要保存部分W/C保留段,以防冲头在键槽处断 裂时,前端部脱落,造成炸模。详见下图:
固定端
W/C保留段
剪切端
6、回弹
回弹是指在冲压弯曲加工时,由于金属材料具有塑性特征,当离开模具后部品的 弯曲部角度将产生回复效果。 影响因素:⑴:被加工材料的变形抵抗大(硬质材); ⑵:弯头R角大; ⑶:弯曲时的间隙太大; ⑷:压料力太小; ⑸:弯曲部压料不完全; ⑹:弯曲深度浅; 解决对策:⑴:使用软质被加工材料; ⑵:弯头R角取小; R ⑶:弯曲时模具间隙较料厚小; ⑷:压料力增强; ⑸:弯曲深度加深; ⑹:预测弯曲回弹角度进行过弯曲; ⑺:弯曲内侧底面施以压肩; ⑻:弯曲部施加肋部; ⑼:弯曲外R部施以面打加工; ⑽:进行二次弯曲加工; ⑾:连续加工时在后工步采用校正工序;
TBP
吹气
SP
BP
PP
冲头内加顶杆
冲头内开吹气孔
冲头端面作锥形加工
材料 剪切形状
0 .0 0 5 ~ 0 .0 1
空气 材料 剪切形状
修边加工冲屑 跳上防止对策
侧边剪切冲屑 跳上防止对策
凹模切刃切沟槽加工
2、导正钉拉料
影响因素:⑴:导正钉与条料的间隙过小; ⑵:送料步距不准确; ⑶:导正钉插入条料太多; ⑷:条料在传送过程中发生偏斜; 解决对策:⑴:导正钉与条料之间选择合理的间隙; ⑵:调整送料步距; ⑶:缩小导正钉长度(突出卸料板0.8t); ⑷:条料进入模具前采用引料装置;
生产中常见的模具问 题及解决方法
1、跳废料
跳废料即指冲屑由凹模型腔中跳出,造成部品有压印等不良; 其产生的主要原因有:⑴:模具间隙大; ⑵:冲切形状(形状单纯); ⑶:冲头上升造成真空吸引作用; ⑷:冲切加工时造成高压空气层之推上作用; ⑸:油膜的粘附作用; ⑹:冲头压缩力造成冲头与材料之密着; 解决对策: ⑴:模具间隙取小; ⑵:改变冲切形状; ⑶:改变部分的模具间隙; ⑷:自凹模下方以空气吸引; ⑸:冲头内装设顶杆; ⑹:冲头内开空气孔及吹气; ⑺:冲头端面作成斜剪角; ⑻:凹模刃部作成微小R或C角; ⑼:在凹模壁上增加废料卡紧特征;
2° ~5° 0.5min a° -2~5° a° R1 R1 t t
R2 0.05~0.1t C=t-0.02~0.05 A A
R2
弯头R角取小
采用压肩
过弯曲
A = 1/2 ~ 2/3 R2 = R1 + t (厚板用)
1 1 2~ 3t
A = R2 R2=R1+ 1 1 3~1 (一般用)
1
2t