Q-P-4-44 A2 AOI点检不良确认表
PPAP点检表(厂家用)

厂家名称:
点检人:
审核:
PPAP检查标准
序号 检查项目 C-1 C-2 C-3 C-4 C-5 C-6 3 过程流程图 检查表(C) C-7 C-8 C-9 检查标准 表头填写是否规范?核心小组人员是否与过程流程流程图、DFMEA、PFMEA中的核心小组人员相一致? 过程流程图编号: 供应商可以按照自己公司体系文件编号要求编号。 样件、试生产、生产是否填写明确?(需提交生产过程流程图。) 零件名称/描述:只填写零部件明细上的零部件全称。 供方:填写供应商名字的全称(中文)。 过程流程图中的过程名称和操作描述是否和控制计划操作描述、PFMEA中过程名称序号功能要求一一对应 特殊特性分类是否与PFMEA、控制计划中的特殊特性分类相一致。 流程图是否说明了生产和检测岗位的顺序?操作描述是否包含了所有的工序? 流程图中产品特性、过程特性(支持产品特性)以及特殊特性(长城公司要求符号)的分类是否明确?过程流程图中明确符号 。且应于开发技术协议相一致。 是否包含了进货检验和出库的过程 产品特性和过程特性识别不全,特 殊特性分类没有识别或识别符号与 我公司不一致且没有备注 只提交试生产过程流程图,生产流 程图必须提交 零部件名称和代码和图纸开发协议 不一致 供应商名称为缩写 过程没有和控制计划一一对应 点检后打 (√ ) 常见错误 表头缺少信息
C-10 过程特性是否与产品特性相一致。 C-11 是否具备所有合适的FMEA(SFMEA,DFMEA),并用来协助制定过程流程图? C-12 流程图是否描述了怎样移动产品,如:辊式输送机、滑动容器等等? C-13 工序符号一定要有明确的要求。 C-14 每页应有公司的签字盖章。(合同章、公司章) 不盖章文件无效 没有描述怎么移动转移产品
PPAP检查标准
AOI点检不良项目清单

2
400L5
漏装
3 射频连接器\82_QMA50-0-26
漏装
4
贴片铝电解电容 \VUA101M1HTR-1010
极性反
J4 J5 C141
贴片电容\CC-060316 0.1UF/50V±10%X7R
立碑
低压差线性稳压器 17 \SPX29150T-L-5- 侧面偏移
0/TR\SIPEX
18
MOSFET\SUM110P0607L-E3\VISHAY
产品规格
NO
元件名称
AOI缺陷点检明细(2*60W)
ASBWCDMA RRH2*60W
版次
E4-1.8D
制订日期
缺陷名称
位号
NO
缺陷位置
缺陷名称
1 RF开关\AS186-302LF
反向
U20
15
陶瓷电容\CC-12064.7UF/50V±10%X7R
少锡
2015/10/30 位号
C106
射频连接器\119S102-
趾部偏移
C149 U7 Q3
5
贴片钽电容 \T491A106K016AT
极性反
6 稳压二极管\DL4745A 极性反
7
单片机 \ADUC7020BCPZ62I-RL
偏移
C42
射频电容 19 \100B120JT500XT
侧立
射频功率场效应管
D1
20 \MRF6S20010GN\Fre 反向
escale
错件
R49
24
LED\BL-HGB35A-AVTRB\百鸿
反向
D3
11
贴片电容\CC-120610uF/16V±10%X7R
产品品质异常记录表

产质量量异常记录表产质量量异常记录表时间客户品名规格不良造成原因4月3日BZHCHI收口管体长度短冠簧母插夹具夹太紧以致 2.0 地址4月7日XUZHOUMK?1.5*16变三角形针头宽度 0.7-0.03 偏大4月13日AOSHID B11B2针0.72 不良率 7%产品状态以及解决方案后续跟进方案图纸更新,操作员清楚包装部边优选边收口已与方强沟通认识〔图纸今后重视标记收口距离〕电镀回来后品管发现上报决定先出货确认出货等待反响截止5月3日客户暂未反响不良责任人〔跟可否流出备注进人〕无责任:自动车床是责任:二次加工〔组长已认识〕是责任:冲床插4月13日BZHCHI针插针头部一截短产品由电镀厂 1W直接发给朗通注塑,尔后交给退回货优选,别的决定以奔展驰,多的带回我们厂,被QC发现,已迅速后电镀前抽检尺寸知会朗通 - 奔展驰停止使用是与练沟通说模具爆,操作员未发现。
柱主体 3.6 宽度的地址,4月14日GUANGY 电极柱超出公差有长有短4月19日HONGX大小电极总长度偏长 27-0.2 做到7.0*27+9.0*27出货等待反响严格依照图纸公差做货确认出货等待反响严格依照图纸公差做货是车床师傅知悉是责任部门自动车床4月13日QIANHE塞钢套〔塑胶〕内台阶披锋,外边披锋此款产品后续退货了,台阶处外径12.7 做到了 12.8-13.0.退回重新进行优选后平均还优选返工是处于 12.85 偏上,4月15日YASI鼻托五金组件客户发现几个焊接不良脱退回全检中出现 600个焊接隐患产品内部更换了焊接厂方,试是后续抽检时应提起警惕,特别是每一批必落焊接3000个须抽检局部确认。
4月15日TENGMEI AMP端子绝缘漆零散退回返工包装部韦秋英知悉是包装未放气,以致产品运输中碰撞掉漆4月22日QIANHE黑赛钢套台阶处外径 12.7 偏大到退货,优选,已经出货暂未接到客户连续投诉是后续产品生产中必定使用客户寄过来的治具进行装置确认。
IPQC巡查不合格项目对照表

9
无保养
10 机器/仪器/治 没有保养记录
11
夹具
每天上班前是没有对设备进行校验
12
涉及安全设备有无警示标或要求配带防护服或手套等
13
包装、库存方式不正确
14同一料ຫໍສະໝຸດ /包装袋/料筐内是否放有不同的材料
15
物料与标识不一致
16
指定物料区域摆放与实际不一致
材料/产品 (含
17
货仓)
材料盒/袋/筐没有标签做标识
18
没有对不良品进行区分标识
19
未按先进先出控制物料
20
备料配料不当使生产无法顺利进行
21
没有做好温湿度控制
22
不严格按指导书作业
23
作
有安全隐患工作岗位配戴手套或工作服及指甲套等
24
业
接触金属(含电镀、喷漆)成品、半成品时未配戴手 套或指甲套
28
员
磨床作业人员没有配戴了手套
30
/
作业人员头发、衣服不符合作业规范
IPQC 巡 查 不 合 格 项 目 对 照 表
项次
项
目
压铸/注塑
1
有无作业工艺文件?
2
作
工艺文件与实际作业不相符?
3
业
工艺文件不规范(含使用夹具、检具、电批扭力)
4
关键控制尺寸是否在检验指导文件上标识出来?
工
5
是否所有用于作业或检验指导工艺文件,作业员都能
艺
看到且理解?
8
压铸机或成型机参数是否按相关作业指导文件设定?
工
32
作
喷砂相关工位(有尘区域)人员未配戴防毒口罩或面 具
人
33
AOI 校正点检表-C

ECN No.
类别Informed 类别Informed type
ECN-MG-090610
□初版Initial release qualification MS-173 表单编号List No. 版次 总页数 C Version Total Pages 变更/发行原因(Change/Release cause): 文件編號變更 change): 变更前说明(Illustration before change): 更前说 初版发行
□准予发行Approve to release □准予变更,旧版于 起作废Approve to change, old document should be disqualified since: _________ □准予发行, 有效期Hold to execute ,effective date________ 核定主管Approval supervisor:_________
PT
主管签章 Checked by
提案人 PREPARED by
謝勇
□书面会签Papering signature □会议研讨Meeting review
会签与分发Sign and distribution 会签与分 与分发
▓无须会签(不影响生产、物料)Don’t need sign (without produce and materials affects)
核定 App.
会签 分发Distribute 单位Department 分发项contents 会签 分发Distribute 单位Department 分发项contents Sign Web Paper Sign web Paper
AOI点检表

7
检查显示器是否正常工作,各按纽是否操作有效,表面是否有刮花
8
等
打开机器状态检测窗口检查XY 的原点和限位、到位信号是否正常 9
检查X\Y 检查工作区是否都在相机的可视范围内 10
检查相机的镜头上的光圈和调焦螺丝是否锁紧
11 软件部分 反复开关程序,看是否能正常开启AOI 软件,是否有报错 12
检查夹具夹板是否正常(板是否固定牢) 16
AOI点检表( 月)
序号
1
检查内容
检查结果
检查电源布线是否良好; 检查接地是否良好
2
检查摄像机固定螺丝是否牢固
3
检查光源连接是否稳固,晃动光源线时光源是否会闪烁
4 硬件部分 检查光源外罩是否会碰撞机器外壳; 用光盘检查光源是否有不亮的
5
LED
检查轨道螺丝是否紧固
6Hale Waihona Puke 检查设备电源总开关是否正常工作并检查其是否锁紧
检查设备系统备份是否正常。
17
检验人 备注
异常情况、处理 及结果
备注
1、表中○表示正常,△表示异常 2、凡出现异常,必须填写异常情况、处理及结果,并由责任部门主管签字确认
设备保养人:
批准:
审核:
常见缺陷不良处置查检表

空焊,锡少不良处置查检表查检项目查检时间查检结果说明处置措施效果确认确认者1.检查印刷是否缺锡不良.(若是,确认1.1-1.8,若否,则从点2确认).1.1 检查钢板是否孔塞.1.2 检查锡膏是否硬化.1.3 检查钢板上锡膏是否不足.1.4 确认锡膏印刷量是否有不足或印刷不干净.1.5 确认锡膏是否下锡不良或黏刮刀.1.6 检查钢板开孔有无不良.1.7 确认wiper 与solvent 是否正常.1.8 确认钢板高度(Stencil Height)是否正确.2.确认印刷是否偏移.(若是,确认2.1,若否,则从3点确认).2.1 调整OFFSET.3.确认置件有无偏移.(若是,调整坐标,若否,则从点4确认)〃4. Reflow Profile是否符合规范.(若是,则从点5确认,若否,则确认4.1-4.2)4.1 观察是否有有灯芯效应。
4.2 检查焊点是否光亮.5.确认Reflow链条是否过松导致震动.(若是,则通知制程工程师确认,若否,则从6点确认)6.确认原材是否不良或是否有摔盘零件或抛料,零件脚歪不良.(若是,则通知制程工程师确认,若否,则从7点确认).7.检查零件端电极或零件脚是否不粘锡.(若是,则通知制程工程师确认,若否,则从8点确认).8.检查PCB PAD是否氧化不粘锡.(若是,则通知制程工程师确认,若否,则从9点确认).9.有无手置元件或人员误碰零件.(若是,通知制程工程师确认,若否,则从10点确认).10.检查PCB是否断线(若是,通知制程工程师确认,若否,则从11点确认).11.检查ICT测试针是否松脱.(若是,通知ICT工程师确认,若否,则从12点确认).12.是否需更换钢板.(通知制程工程师确认).13.是否需更换锡膏.(通知制程工程师确认).14.其它.缺件不良处置查检表查检项目查检时间查检结果说明处置措施效果确认确认者1.确认锡膏是否有置件之痕迹.(若是,确认1.1-1.3,若否,则从2点确认).1.1检查Support Pin 位置是否正确.1.2检查Support Pin 高度是否正确.1.3检查Part Data零件厚度是否正确.2.确认是否为相同零件.(若是,则确认2.1-2.9,若否,则从3点确认).2.1检查锡膏是否漏印.2.2检查钢板开窗是否恰当.2.3检查置件是否偏移.2.4检查Feeder是否不良.2.5检查Tape Leaf Cover尺寸是否正确.2.6检查Part Data吸嘴尺寸是否正确.2.7检查Part Data零件厚度是否正确.2.8是否混用不同Size Nozzle.2.9Transport速度是否过快.3.确认是否为相同区域.(若是,则确认31.-3.7,若否,则从点4确认).3.1PCB是否是否弯曲或变形3.2检查Support Pin位置是否正确.3.3检查Support Pin高度是否正确.3.4检查是否过Reflow是所掉落.3.5检查Support Plate下方是否卡有零件.3.6检查Support Base下方是否卡有零件.3.7设备内尺规PCB厚度设定是否正确(=1.60mm)4.缺件出现任意位置.(若是,则确认4.1-4.13,若否,则从5点确认).4.1PCB是否板弯.4.2检查Support Pin位置是否正确.4.3检查Support Pin高度是否正确.4.4检查印刷是否偏移.4.5检查置件是否偏移.4.6检查置件是否有甩件情形.4.7检查UV LAMP是否闪烁不定.4.8检查F4G及设备内尺规PCB厚度设定是否正确(=1.60mm).4.9检查出现Nozzle Skip之吸嘴是否不良.4.10.注视Monitor Display之Nozzle是否有吸不到料之情形. 4.11检查Nozzle中之弹簧是否赃污.4.12压触Nozzle,检查弹簧运作是否正常.4.13检查Holder动作是否正常.5.若缺件继续发生.(若是,则确认5.1-5.7,若否则从点6确认).5.1检查Holder内Filter(真空过滤棉) 是否赃污.5.2检查Z轴高度是否正确.5.3检查Table水平是否正确.5.4检查ST11气缸动作是否正常.5.5检查吸嘴真空吸力是否低於600 mm/Hg.5.6检查吸嘴真空破坏力量是否正常.5.7是否经常出现ST17与ST19 Error.6.其它.7.联络厂商处理.偏移、力碑不良处置查检表查检项目查检时间查检结果说明处置措施效果确认确认者1.确认印刷是否偏移.(若是,确认1.1,若否,从点2确认).1.1调整OFFSET.2.检查印刷是否缺锡不良.(若是,确认2.1-2.8,若否,则从点3确认).2.1检查钢板是否孔塞.2.2检查锡膏是否硬化.2.3检查钢板上锡膏是否不足.2.4确认锡膏印刷量是否不足或刮印不干净.2.5确认锡膏是否下锡不良或黏刮刀.2.6检查钢板开孔有无过大或过小.2.7确认wiper与solvent是否正常.2.8确认钢板高度(Stencil Height)是否正确.3.确认钢板开孔大小是否适当.(若是,确认点4,若否,则通知制程工程师确认).4.确认置件有无偏移.(若是,调整置件坐标及吸件位置,若否,则从点5确认).5.确认Feeder有无异常.(若是,更换不良Feeder,若否,则从6确认).6.确认吸嘴有无堵塞或弯曲或吸料不良,(若是,更换不良吸嘴,若否,则从7确认).7.检查锡炉内是否有异物或锡炉内轨道变形.(若是,通知设备工程师,若否,则从点8确认).8.确认Reflow链条是否过松导致震动.(若是,通知设备工程师,若否,则从点9确认).9.确认soaking zone温度曲线斜率,是否加热太快.(若是,通知制程工程师,若否,则从点10确认).10.检查是否有撞板.(若是,通知制程工程师,若否,则从点11确认).11.确认是否为原材不良.(若是,确认11.1-11.2及通知制程工程师,若否,则从点12确认).11.1检查零件端电极是否拒焊.11.2是否零件两端端电极沾锡性差异大.12.确认零件BODY SIZE与PCB PAD LAYOUT是否相符,(若是,确认点出13,若否,通知制程工程师).13.是否更换钢板(通知制程工程师确认).14.是否需更换锡膏.(通知制程工程师确认).15.其它.短路不良处置查检表查检项目查检时间查检结果说明处置措施效果确认确认者1.检查印刷是否锡厚或短路.(若是,确认1.1-1.13,若否,则从点2确认).1.1确认钢板与PCB间有无间隙,锡膏脱模是否良好.1.2确认刮刀是否刮干净,若刮不干净,则重做钢板高度和刮刀水平.1.3 检查印刷机Table是否倾斜.1.4确认刮刀是否损坏.1.5确认钢板状况(是否钢板孔塞,底部赃,胶带脱落).1.6 检查钢板孔有无不良.1.7 确认wiper 与solvent 是否正常.1.8 确认是否自动擦拭钢板1.9Wiper paper 松脱,碰触到焊膏1.10确认PIN摆放位置是否适当.1.11PCB零件面是否有锡珠.1.12锡膏搅拌时间是否异常.1.13确认所有印刷参数是否follow SIC.1.14确认钢板张力是否符合规范2.确认印刷是否偏移.(若是,确认2.1,若否,则从3点确认).2.1 调整OFFSET.3.确认置件有无偏移.(若是,调整坐标,若否,则从点4确认)〃4.确认置件深度是否过深.(若是,确认零件高度part data 设定是否正确,若否,则从点5 确认)5. Reflow Profile是否符合规范.(若是,则通知制程工程师确认,若否,则从点6 确认)6.确认Reflow链条是否过松导致震动.(若是,则通知设备工程师确认,若否,则从点7 确认)7.确认原材是否不良或是否有摔盘零件或抛料,零件脚歪不良.(若是,则通知制程工程师确认,若否,则从8点确认).8.有无手置元件或人员误碰零件.(若是,通知制程工程师确认,若否,则从9点确认).9.是否需更换钢板.(通知制程工程师确认).10.是否需更换锡膏.(通知制程工程师确认).11.其它.。
不合格品记录表

实用数
损耗数
退还数
偏差
装小盒
装瓶
贴标签
装说明书
装中盒
贴封口签
装合格证
装外箱
本批包装总数
本批并箱批号及数量
物料
衡
算
外包收率=
实际包装总数
×100%=
×100%=
领用数量
收得率范围:98.5~100%
结论:
检查人
留样数
取样数
备注
班长:工艺员:
物料退库单
退料部门
日期
年月日
物料名称
规格
数量
退库原因
备注
□符合
□不符合
□符合
□不符合
9
卫生洁具清洁,按定置放置
□符合
□不符合
□符合
□不符合
10
其它
结论
清场人
工艺员
质监员
内包清场记录
年月日
清场前产品名称
规格
批号
清场内容及要求
工艺员检查情况
质监员检查情况
备注
1
设备及部件内外清洁,无异物,模具清洁
□符合
□不符合
□符合
□不符合
2
无废弃物,无前批遗留物
□符合
□不符合
容器具
清洁、整齐、无异物、无脱落物。
洁具
整齐、干净,按定置要求放置。
物料
按定置位置摆放整齐、清洁、无尘,有状态标志。
标志
门外、设备、容器具上卫生标志符合要求。
结论
班长
质监员
在产物品标签
工序:年月日
品名
规格
批号
物料状态
数量
操作者
供应商稽核点检表

项目 序号
描述
4.1. 外观作业环境有助于达到质量要求吗?
4.2. 下述条件充足吗?
作业 4.3. 环境 4.4.
a.空间? b.光线?
4.5. c.噪音控制?
4.6. d.安全措施?
5.1. 是否编制了所有生产设备的一览表?
5.2. 生产设备之各项参数设置是否与作业指导书一致?
5.3. 所有生产设备的维护与操作是否由取得合格证的人员负责?
储存 与出
7.12
货检 7.13
验 7.14
7.15
检验员,作业员是否按规定佩戴手套或静电环? 所使用之检验设备/仪器/治工具有无定期校验?及其标示与校验记录是否有效? 所使用之检测设备/仪器/治工具有无维护保养? 有无记录? 在规定须可追溯时,是否对每批或每个产品作特定的标记? 对所发现之不良问题是否立即进行分析与处理?有无相关之记录? 成品搬运过程中是否能确保产品质量不受损伤?
5.10. 所有工具,设备,仪器是否均接地?接地阻抗是否符合要求?
5.11. 是否有合格之工程样品供测试设备开机检查用?
5.12. 所有工具,设备,仪器使用之量测或加工程序及软件版本是否最新?
5.13. 是否运用统计技术管理量测质量?
5.14. 所用工具,设备,仪器是否有足够的安全及保护措施?
通过 不及格
证明
第 3 頁,共 6 頁 PDF 文件使用 "pdfFactory Pro" 试用版本创建
OEM外包产品稽核点检表
说明:稽核时若某个查核项目暂不适用时,请用"N/A"标明.
项目 序号
描述
通过
6.1. 作业流程是否畅通?工位安排是否合理?
6.2. 作业者是否有足够的工作空间?作业动作是否顺畅?
不合格品检查表

审核过程:不合格品管理流程
被审核部门:品管部
审核日期:
审核人员:
流程
审核要点
1.1来料(包括收货时及检验时)发现不合格时, 是 否有对不合格品进行标识/隔离?
判定 OK NG
审核记录
1.2经判定为不合格物料是否开具[不合格评审处理 单],并经审核/批?
1.来料 不合格
1.3是否按评审结果对不合格物料进行处理?
4.2如因品质异常引起客户退货,是否按要求对不 合 格原因进行分析,并有改善对策?
4.客户退 货
4.3是否按评审后的改善对策对不合格进行改善?
4.4改善后是否有进行效果验证工作并有记录?
4.5是否有对客户退货进行统计、分析?
5.1仓库不合格包括哪几个方面? 5.仓储不 5.2这些方面的不合格是如何处理的?
1.4是否有对不合格物料处理措施进行验证?
第 1 页,共 3 页 缺失描述
1.5对于不合格物料是否有进行统计、分析?
2.1注塑过程发现的不合格是否有进行标识/隔 离? 不同时机发现的不合格各有哪些标识方法?
2.2注塑过程发现的不合格处理方式有哪些?
2.注塑 不合格
2.3不合格产品返工后是否经重新检验并有检 验记 录?
表单编号:DC-015 B
体系过程审核检查表
审核过程:不合格品管理流程
被审核部门:品管部
ห้องสมุดไป่ตู้
审核日期:
审核人员:
流程
审核要点
判定 OK NG
审核记录
2.4由后工序处理的不合格品如何处理?
2.5对于注塑过程发生的不合格,是否有进行统计 、 分析?
3.1装配或成品出货检验时发现不合格是否有标识/ 隔离?
品质异常统计表

序
日期
异常问题点
原因分析
处理措施
预防措施
责任人
跟踪人
备注
1
7月1日
7421B齿轮箱座穿线糟太窄,电线穿不过
表面批锋及铸渣过大;来料检验员漏检至使不合格品流入
对现场产品及库存品进行全检,不合格品通知供应商到现场进行磨处理
来料检验员按标准检验,发现不合格通知采购部退回供应商,装配品检员对箱座重点跟踪,对上工序来料进行接收质量检查。(7月17日已全部返工完,到8月3日为止,没出现不合格零件)
有一部分图纸问题,有一部分是机加没安图纸做。
技术部已经确定更改好15个问题:其中5处更改图纸,5处确认图纸是对的,机加没按要求做好。
更改的图纸已下发《设计更改通知书》,机加、数控要严格按图纸作业。
肖志群
18
7月20日
排钻:滑块M6孔图纸要求攻牙20mm深,实际没达到要求,约15mm。造成部件安装不了。
焊接的面是斜的,机加没按要求进行加工;出现此问题很少,员工大意,安装没有对零件进行检验。
把装好的电器件拆下来,更换好的配件,再进行总装(7月16日跟进时,以上动作已作好---用时两小时)
机加要严格按要求进行加工,员工安装前要对零件进行自检,发现不合格的一定要进行更换处理。
储俊
14
7月15日
压料轮跟压料梁接处面高低不平,导致装机后,轮子不转。(从7月15日--20日上午,4.5天的时间共发现179个不良品,平均一天40个)
杨江宏
21
7月29日
7月29日装配员工发现:气缸座连接法兰,槽打偏,造成安装困难。加工400件,39件出现问题(MZ7104-0220)
①加工时,没注意零件具体情况(内孔没铣,不均匀),定坐标方法没掌握好,导致质量不稳定;
QSA内部品质稽核查核表汇总

(4.2.4.3)
4.2.5 持续改进
2.19** 是否有证据证明在质量(特别是产品性能)、服务(时间安排
和交付)和价格方面实施了有利于所有顾客的持续改进?
(4.2.5.1 4.16)
2.20 持续改进是否涉及到产品的性能尤其是特殊特性?
(4.2.5.1)
2.21 当过程显示出稳定性, 制造能力及产品性能可以接受时,
- 检验的方法、频次等发生改变?
(4.2.3.7)
评定人记录 – 实施证据
4.2.4 产品批准程序
2.16* 供方是否完全遵守生产件批准程序(PPAP)手册中提出的
所有要求?
(4.2.4.1)
问
题
2.17* 供方是否对分供方采用了生产件批准程序?
(4.2.4.2)
2.18* 是否有证据表明对产品更改进行了适当的确认?
等?
G.4 北美部的供方是否每年至少验证一次其是否在采用通用汽车公
司程序的最新版本?
G.5 供方是否有与顾客交流的最新信息?
G.6* 供方是否满足顾客规定的 PPM 目标或者制定顾客批准的质量 改进计划以满足顾客规定的 PPM 指针?
G.7 发运标识是否包含了最新更改的序号和日期?
G.8* 供方是否有具体的行动计划以解决 2000 年(Y2K)时, 与产品、
要素 通用特殊要求
评定人记录
结果
问
题
G.1 供方是否有代替通用汽车公司程序的必要的程序和过程?
G.2 北美部生产现场的供方是否使用在线的 TFE 基础资料(GP—5)?
G.3* 是 否 有 符 合 通 用 汽 车 公司 有 关 程 序 的 证 据 , 例如 GP--9 、 GP--10、GP—12 和通用汽车公司特殊要求如 GM1825、GM1797
4M确认检查表

1.1 1.2 1.3 1.4 1.5 1.6 1.7 1.8 1.9 1.10 1.11 1.12 1.13 1.14 2.1 2.2 2.3 2.4 2.5 2.6 2.7 2.8 2.9 2.10 2.11 2.12 2.13 2.14 2.15 2.16 2.17 2.18 2.19 2.20 2.21 2.22 2.23 2.24 2.25 2.26 2.27 2.28 2.29 2.30 2.31 2.32 2.33 2.34 2.35 2.36 2.37 2.38 2.39 2.40 1.1问 题的 描述
对策 有效 确认地点 顾客处不良是否在顾客处进行效果验证? 性的 关联性 是否在解决一个问题时,产生另一个问题? 确认 重复性 对策实施后是否有不良再次发生? 是否建立可衡量的对策评价方法? 是否确认再发生的可能性? 人员间 产品间 过程间 纠正性
不良的对策方法(对策的合理性)是否在相关人员(管理人员)中展开培训? 不良的对策方法(对策的合理性)是否在相关人员(一线员工)中展开培训? 有效的对策是否能应用在其它型号的产品上? 有效的对策是否能应用在其它的作业工序中? 是否需要更新产品的图纸、产品的规格书? 是否需要更新控制计划、作业标准? 是否需要更新检验(进货、过程、成品)文件? 是否需要更新DFMEA和PFMEA? 是否需要更新质量管理体系中的控制文件(质量记录、管理指导书、程序文件、质量手册)?
信息 获取
不良 的描述 临时措施 1.2 紧急 (临 时) 处置 方法
紧急 措施
不良品数 2.1不 量调查 良品 (整条供 的调 应链) 查
不良状况
过程方法
2.2 过程 的调 查 (实 际工装
材料
人员
五个 为什 么 3.1 3.2 3.3 3.4 3.5 3.6 3.7 3.8 3.9 3.10 3.11 3.12 3.13 3.14 4.1 4.2 4.3 4.4 4.5 4.6 4.7 4.8 4.9 发生 原因 调查 和对 策 方法
供应商QPA稽核点检表(SMT外发)
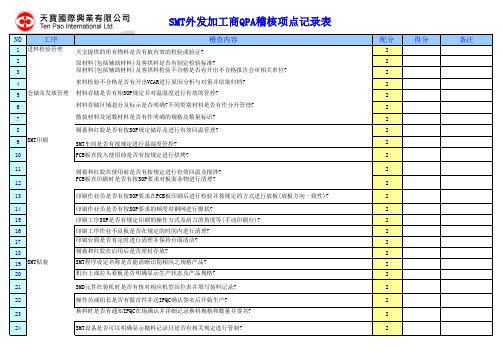
NO工序稽查内容配分得分备注1天宝提供的所有物料是否有被有效的检验或验证?22原材料(包括辅助材料)及客供料是否有制定检验标准?23原材料(包括辅助材料)及客供料检验不合格是否有开出不合格报告会审相关单位?24来料检验不合格是否有开出VCAR进行原因分析与对策并结案归档?25材料存储是否有相SOP规定并对温湿度进行有效的管控?26材料存储区域划分及标示是否明确?不同类别材料是否有作分开管理?27散装材料及尾数材料是否有作明确的规格及数量标识?28锡膏和红胶是否有按SOP规定储存及进行有效回温管理?29SMT车间是否有按规定进行温湿度管控?210PCB板在投入使用前是否有按规定进行烘烤?211锡膏和红胶在使用前是否有按规定进行有效回温及搅拌?212PCB板在印刷时是否有按SOP要求对板面杂物进行清理?213印刷作业员是否有按SOP要求在PCB板印刷后进行检验并按规定的方式进行放板(放板方向一致性)?214印刷作业员是否有按SOP要求的频度对钢网进行擦拭?215印刷工序SOP是否有规定印刷的操作方式及刮刀的角度等(手动印刷台)?216印刷工序作业不良板是否在规定的时间内进行清理?217印刷台面是否有定时进行清理并保持台面清洁?218锡膏和红胶在启用后是否密封存放?219SMT程序设定名称是否能清晰识别相应之规格产品?220机台上或拉头看板是否明确显示生产状态及产品规格?221SMD元件在装机时是否有核对相应机型站位表并填写装料记录?222操作员或组长是否有做首件并送IPQC确认签名后开始生产?223换料时是否有通知IPQC在场确认并详细记录换料规格和数量并签名?224SMT设备是否可以明确显示抛料记录且是否有相关规定进行管制?2SMT外发加工商QPA稽核项点记录表进料检验管理仓储及发放管理SMT印刷SMT贴装。