涂覆焊技术在航空发动机受感部安装中的应用研究
航空发动机涂层技术及应用
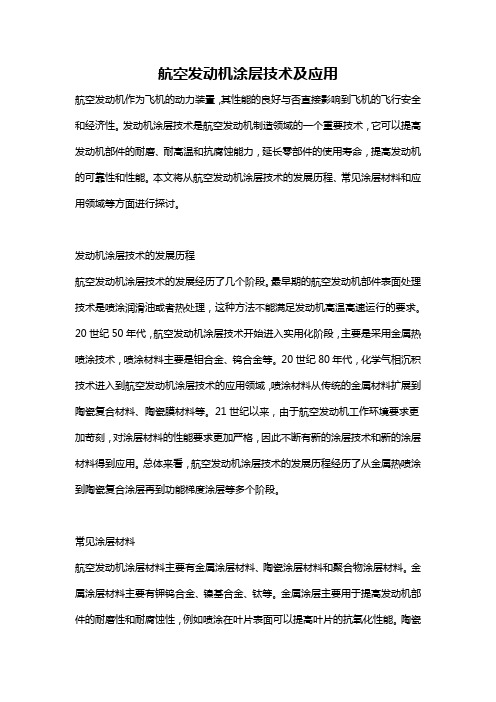
航空发动机涂层技术及应用航空发动机作为飞机的动力装置,其性能的良好与否直接影响到飞机的飞行安全和经济性。
发动机涂层技术是航空发动机制造领域的一个重要技术,它可以提高发动机部件的耐磨、耐高温和抗腐蚀能力,延长零部件的使用寿命,提高发动机的可靠性和性能。
本文将从航空发动机涂层技术的发展历程、常见涂层材料和应用领域等方面进行探讨。
发动机涂层技术的发展历程航空发动机涂层技术的发展经历了几个阶段。
最早期的航空发动机部件表面处理技术是喷涂润滑油或者热处理,这种方法不能满足发动机高温高速运行的要求。
20世纪50年代,航空发动机涂层技术开始进入实用化阶段,主要是采用金属热喷涂技术,喷涂材料主要是钼合金、钨合金等。
20世纪80年代,化学气相沉积技术进入到航空发动机涂层技术的应用领域,喷涂材料从传统的金属材料扩展到陶瓷复合材料、陶瓷膜材料等。
21世纪以来,由于航空发动机工作环境要求更加苛刻,对涂层材料的性能要求更加严格,因此不断有新的涂层技术和新的涂层材料得到应用。
总体来看,航空发动机涂层技术的发展历程经历了从金属热喷涂到陶瓷复合涂层再到功能梯度涂层等多个阶段。
常见涂层材料航空发动机涂层材料主要有金属涂层材料、陶瓷涂层材料和聚合物涂层材料。
金属涂层材料主要有钾钨合金、镍基合金、钛等。
金属涂层主要用于提高发动机部件的耐磨性和耐腐蚀性,例如喷涂在叶片表面可以提高叶片的抗氧化性能。
陶瓷涂层材料主要有氧化铝、氧化锆、氮化硅等。
陶瓷涂层主要用于提高发动机部件的耐高温性能,例如喷涂在燃烧室和涡轮喷嘴内表面可以提高这些部件的耐高温性能。
聚合物涂层材料主要有环氧树脂、聚苯乙烯等。
聚合物涂层主要用于提高发动机部件的摩擦和润滑性能,例如喷涂在轴承和齿轮表面可以提高这些部件的耐磨性。
涂层技术的应用领域航空发动机涂层技术的应用领域非常广泛,主要包括以下几个方面。
1. 发动机叶片和叶盘:涂层技术可以提高叶片和叶盘的抗高温、抗氧化和抗腐蚀能力,延长叶片和叶盘的使用寿命。
航空发动机涡轮叶片热障涂层研究现状
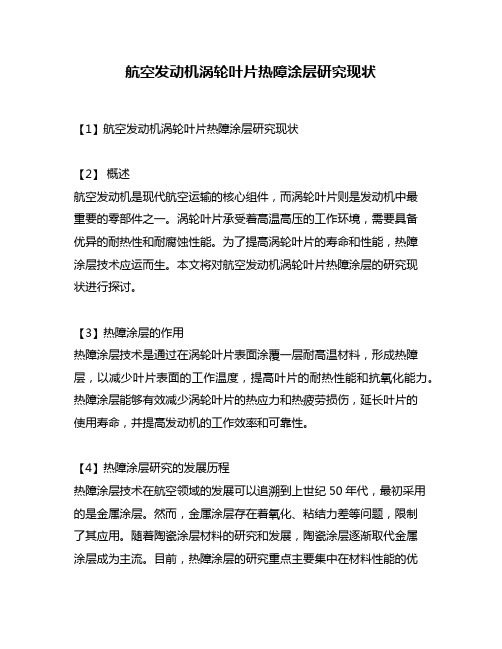
航空发动机涡轮叶片热障涂层研究现状【1】航空发动机涡轮叶片热障涂层研究现状【2】概述航空发动机是现代航空运输的核心组件,而涡轮叶片则是发动机中最重要的零部件之一。
涡轮叶片承受着高温高压的工作环境,需要具备优异的耐热性和耐腐蚀性能。
为了提高涡轮叶片的寿命和性能,热障涂层技术应运而生。
本文将对航空发动机涡轮叶片热障涂层的研究现状进行探讨。
【3】热障涂层的作用热障涂层技术是通过在涡轮叶片表面涂覆一层耐高温材料,形成热障层,以减少叶片表面的工作温度,提高叶片的耐热性能和抗氧化能力。
热障涂层能够有效减少涡轮叶片的热应力和热疲劳损伤,延长叶片的使用寿命,并提高发动机的工作效率和可靠性。
【4】热障涂层研究的发展历程热障涂层技术在航空领域的发展可以追溯到上世纪50年代,最初采用的是金属涂层。
然而,金属涂层存在着氧化、粘结力差等问题,限制了其应用。
随着陶瓷涂层材料的研究和发展,陶瓷涂层逐渐取代金属涂层成为主流。
目前,热障涂层的研究重点主要集中在材料性能的优化、工艺改进以及涂层与基底材料之间的耦合问题等方面。
【5】热障涂层材料的选择航空发动机涡轮叶片的热障涂层材料需要具备优异的耐高温性能、热膨胀系数匹配性和抗氧化能力。
目前常用的涂层材料主要有氧化铝、氧化锆和复合材料等。
不同的涂层材料具有各自的特点和优势,在应用中需要根据具体的工作环境和性能要求来选择合适的材料。
【6】研究热障涂层的关键技术热障涂层的研究涉及到材料制备、涂层工艺、热处理和性能评价等多个方面。
其中,材料制备的关键技术包括热喷涂和物理气相沉积等方法,涂层工艺的关键技术包括预处理、喷涂参数控制和后处理等。
涂层与基底材料之间的耦合问题也是热障涂层研究中的一个重要方向。
【7】热障涂层的性能评价热障涂层的性能评价主要包括热稳定性、热膨胀性、抗氧化性和机械性能等指标。
常用的测试方法有热循环试验、热膨胀系数测试、高温氧化试验和机械性能测试等。
通过对涂层性能的评价,可以为进一步改进和优化涂层设计提供参考和依据。
航空发动机涡轮叶片热障涂层研究进展
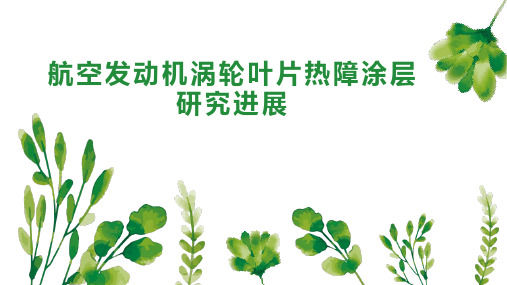
参考内容
热障涂层技术是近年来广泛应用于航空发动机和燃气轮机涡轮叶片的关键技 术之一。本次演示将详细探讨该技术的原理、应用场景以及发展趋势。
一、技术原理
热障涂层技术主要利用了热交换机理和温度控制原理。在航空发动机和燃气 轮机中,涡轮叶片是关键的高温部件,容易受到高温燃气流的冲刷和腐蚀。热障 涂层通过在涡轮叶片表面涂覆一层耐高温、抗腐蚀的材料,有效降低叶片表面温 度,减少高温燃气流的侵蚀,提高叶片的可靠性和使用寿命。
2、气动外形的设计
涡轮叶片作为航空发动机和燃气轮机中的关键部分,其气动外形设计对于整 个动力系统的性能有着重要影响。热障涂层技术在涡轮叶片表面涂覆一层耐高温、 抗腐蚀的材料,不仅可以提高叶片的可靠性和使用寿命,还可以通过优化气动外 形设计,减小气流在叶片表面的阻力,提高整机的性能。
三、发展趋势
二、应用场景
1、发动机高温部件的温度控制
航空发动机和燃气轮机的高温部件,如涡轮叶片、燃烧室等,是整个动力系 统的关键部分。这些部件在高温、高压、高转速的极端环境下工作,对温度控制 的要求非常高。热障涂层技术通过在高温部件表面涂覆一层隔热性能优异的材料, 有效降低部件表面温度,提高发动机和燃气轮机的可靠性和性能。
感谢观看
关键技术
热障涂层的制备技术包括物理气相沉积(PVD)、化学气相沉积(CVD)、溶 胶-凝胶法等。其中,PVD和CVD技术能够制备出致密、均匀的涂层,但工艺温度 较高,容易导致基体热损伤;溶胶-凝胶法可以在较低的温度下制备出高纯度、 高致密度的涂层,但涂层的厚度和均匀性较差。因此,研究者们需要探索新的制 备方法,以获得具有优异性能的热障涂层。
2、涂层制备工艺的优化
热障涂层的制备工艺对于其性能和使用寿命有着重要影响。随着航空发动机 和燃气轮机性能的提高,对于热障涂层制备工艺的要求也更加严格。未来,需要 进一步优化涂层层的快速制备和大面积应用。
热喷涂焊接技术在航空发动机中的应用

热喷涂焊接技术在航空发动机中的应用航空发动机是现代航空器的核心部件,其性能直接关系到飞机的安全和效率。
为了提高航空发动机的工作效率和寿命,热喷涂焊接技术被广泛应用于航空发动机的制造和维修中。
热喷涂焊接技术是一种将金属粉末或线材喷涂在工件表面并进行熔化的方法,通过高速喷射的热能将金属材料与工件表面融合,形成一层坚固的涂层。
这种技术可以在航空发动机的叶片、涡轮、燃烧室等关键部件上应用,以提高其耐磨、耐腐蚀和高温性能。
首先,热喷涂焊接技术可以用于航空发动机叶片的修复和保护。
航空发动机叶片是承受高温、高速气流和离心力的重要部件,容易受到磨损和腐蚀的影响。
通过热喷涂焊接技术,在叶片表面形成一层高温合金涂层,可以有效地提高叶片的耐磨性和耐腐蚀性,延长叶片的使用寿命。
此外,热喷涂焊接技术还可以修复受损的叶片,使其恢复原有的性能。
其次,热喷涂焊接技术可以用于航空发动机涡轮的制造和修复。
航空发动机涡轮是将燃气能转化为机械能的重要部件,工作环境严苛,容易受到高温和高速气流的侵蚀。
通过热喷涂焊接技术,可以在涡轮叶片和叶盘表面形成一层高温合金涂层,提高涡轮的耐磨性和耐高温性,同时减轻涡轮的重量,提高发动机的效率。
此外,热喷涂焊接技术还可以用于航空发动机燃烧室的制造和维修。
航空发动机燃烧室是燃烧燃料的关键部件,工作环境高温、高压,容易受到高温气体和化学物质的侵蚀。
通过热喷涂焊接技术,在燃烧室内壁形成一层高温合金涂层,可以提高燃烧室的耐热性和耐腐蚀性,延长燃烧室的使用寿命。
总之,热喷涂焊接技术在航空发动机中的应用具有重要的意义。
通过这种技术,可以提高航空发动机的工作效率和寿命,减少维修成本,提高飞机的安全性和经济性。
未来,随着科学技术的不断发展,热喷涂焊接技术在航空发动机中的应用将会得到进一步的拓展和完善,为航空工业的发展做出更大的贡献。
表面涂层技术在航空发动机上的应用
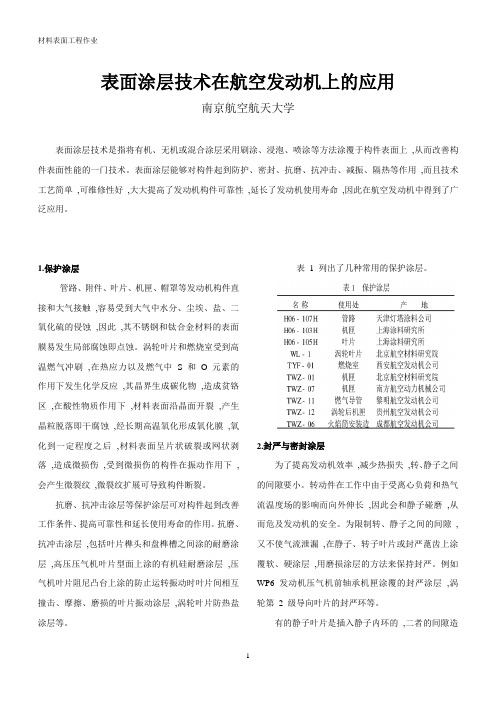
表面涂层技术在航空发动机上的应用南京航空航天大学表面涂层技术是指将有机、无机或混合涂层采用刷涂、浸泡、喷涂等方法涂覆于构件表面上,从而改善构件表面性能的一门技术。
表面涂层能够对构件起到防护、密封、抗磨、抗冲击、减振、隔热等作用,而且技术工艺简单,可维修性好,大大提高了发动机构件可靠性,延长了发动机使用寿命,因此在航空发动机中得到了广泛应用。
1.保护涂层管路、附件、叶片、机匣、帽罩等发动机构件直接和大气接触,容易受到大气中水分、尘埃、盐、二氧化硫的侵蚀,因此,其不锈钢和钛合金材料的表面膜易发生局部腐蚀即点蚀。
涡轮叶片和燃烧室受到高温燃气冲刷,在热应力以及燃气中S 和O 元素的作用下发生化学反应,其晶界生成碳化物,造成贫铬区,在酸性物质作用下,材料表面沿晶面开裂,产生晶粒脱落即干腐蚀,经长期高温氧化形成氧化膜,氧化到一定程度之后,材料表面呈片状破裂或网状剥落,造成微损伤,受到微损伤的构件在振动作用下,会产生微裂纹,微裂纹扩展可导致构件断裂。
抗磨、抗冲击涂层等保护涂层可对构件起到改善工作条件、提高可靠性和延长使用寿命的作用。
抗磨、抗冲击涂层,包括叶片榫头和盘榫槽之间涂的耐磨涂层,高压压气机叶片型面上涂的有机硅耐磨涂层,压气机叶片阻尼凸台上涂的防止运转振动时叶片间相互撞击、摩擦、磨损的叶片振动涂层,涡轮叶片防热盐涂层等。
表1 列出了几种常用的保护涂层。
2.封严与密封涂层为了提高发动机效率,减少热损失,转、静子之间的间隙要小。
转动件在工作中由于受离心负荷和热气流温度场的影响而向外伸长,因此会和静子碰磨,从而危及发动机的安全。
为限制转、静子之间的间隙,又不使气流泄漏,在静子、转子叶片或封严蓖齿上涂覆软、硬涂层,用磨损涂层的方法来保持封严。
例如WP6 发动机压气机前轴承机匣涂覆的封严涂层,涡轮第 2 级导向叶片的封严环等。
有的静子叶片是插入静子内环的,二者的间隙造成气流损失,这时可采用密封涂层封住,这要求密封涂层耐温、抗振、柔软,长期不老化。
航空发动机涂层技术研究

航空发动机涂层技术研究随着航空事业的不断发展,航空发动机的性能要求也不断提高。
而航空发动机受到高温、高压、高速等极端条件的影响,需要拥有更高的耐久性和抗腐蚀能力。
因此,发动机涂层技术得到了广泛的研究和应用。
一、发动机涂层技术的发展历程发动机涂层技术最初应用于喷气发动机的涡轮叶片表面。
20世纪60年代,涡轮叶片表面喷涂金属材料的方法被广泛应用。
20世纪70年代,高速航空发动机的涂层技术开始使用陶瓷涂层,提高了航空发动机的稳定性和可靠性。
二、航空发动机涂层技术的分类1. 热障涂层:在航空发动机叶片表面涂覆热障涂层,可以有效降低高温下的材料熔融和氧化。
常用的热障涂层材料有Y2O3、ZrO2等。
2. 抗磨涂层:航空发动机需要耐高温、耐腐蚀、耐磨损,抗磨涂层是其中的一种。
其可以降低机件间的摩擦,减少磨损,提高机件的使用寿命。
3. 抗氧化涂层:航空发动机在高温下会发生氧化,导致表面的金属材料丧失其原有性能。
抗氧化涂层的应用可以有效提高发动机的抗氧化能力。
4. 先进材料涂层:随着材料科学技术的发展,航空发动机涂层材料也得到了不断的升级。
某些先进材料涂层如TiAlN、CrN等,具有极高的耐腐蚀性能、高的硬度和低的摩擦系数等特点,可以提高发动机的性能。
三、航空发动机涂层技术的应用1. 提高发动机性能:航空发动机涂层技术的应用可以有效提高发动机的综合性能。
例如,热障涂层可以降低高温下的材料熔融和氧化,提高发动机在高温环境下的可靠性。
2. 延长发动机使用寿命:航空发动机在使用过程中容易受到高温、高压、高速等极端条件的影响,导致金属材料发生氧化或熔化。
而涂层技术可以有效延长发动机的使用寿命,提高发动机的可靠性和耐用性。
3. 降低发动机维护成本:航空发动机的维护成本很高,但涂层技术的应用可以有效降低发动机的维护成本。
例如,抗氧化涂层可以降低发动机在高温下的氧化程度,延长金属材料的使用寿命,减少维护工作的频次和费用。
四、航空发动机涂层技术的未来发展随着航空事业的不断发展,航空发动机性能的提高要求也不断增加。
热障涂层技术在航空发动机上的应用与发展
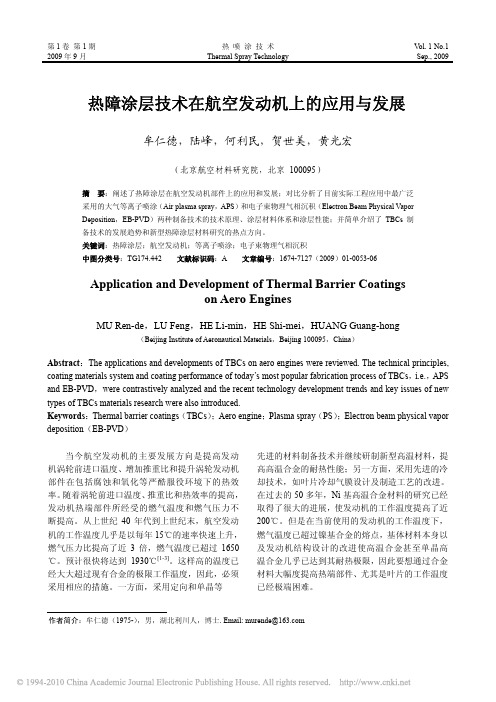
Application and Development of Thermal Barrier Coatings on Aero Engines
MU Ren-de,LU Feng,HE Li-min,HE Shi-mei,HUANG Guang-hong
(Beijing Institute of Aeronautical Materials,Beijing 100095,China)
要求,P&W 公司又成功地开发了第 3 代涡轮叶片 EB-PVD 热障涂层——PWA266。该涂层采用EB-PVD 制备 7YSZ 陶瓷面层、低压等离子喷涂(LPPS)的 NiCoCrAlY 金属粘结层,该涂层消除了叶片蠕变疲 劳、断裂和叶型表面抗氧化陶瓷的剥落,使其寿命 比未喷涂该涂层叶片的寿命延长了 3 倍。PWA266 以其极好的耐久性、抗热剥落性能和耐热性,在 JT9D 和 PW2000 发动机上得到成功验证之后,于 1989 年首先应用到 PW2000 发动机涡轮叶片上,之 后又应用至 JT9D-7R4、V2500、F100-PW-229 和 F119 等发动机涡轮叶片上。应用该涂层后,F119 发动机高压涡轮工作叶片工作温度比未喷涂该涂 层叶片的可提高 150K 左右。除此之外,PW 公司 在 JT3D 和 JT38D 发动机的风扇叶片、压气机叶片、 燃烧室、涡轮叶片等处均用了热障涂层。
航空工业中焊接技术的应用探究

航空工业中焊接技术的应用探究作者:于金玲王俊来源:《中国科技博览》2014年第28期[摘要]航空工业综合体现我国先进科学技术的发展状况,其中焊接技术是先进技术的重要组成部分。
简单来说焊接技术就是通过对两种或两种以上的材料的加压或加热等方式,使之不同材料的原子和分析相融合,从而使之链接在一起,这种焊接技术常被用在航空工业中。
本篇论文就针对该技术在航空工业中的具体应用做浅要分析。
[关键词]航空工业焊接技术应用中图分类号:TM691 文献标识码:A 文章编号:1009-914X(2014)28-0277-01焊接一直都在航空领域中的重要技术之一,其技术的不断研发,也推动着航空工业的发展。
焊接中加入先进的科学技术,使得焊接在速度、质量和自动化等方面取得显著的进步。
近几年我国在航空领域中突飞猛进,为了满足航空领域中不断提升的技术要求,焊接技术加入世界先进的工业技术,像是激光、电子等高科技,根据航空对不同材料的不同要求选择适当的焊接技术。
下面浅要介绍焊接技术在航空领域中的具体应用。
一、焊接技术的特点1. 激光焊接技术的特点激光焊接是以激光为焊接的热源来对物质进行焊接的技术。
该技术运用的原理是将光通过凹凸镜进行聚光,将其焦点控制在焊接部位。
激光焊接技术会在焊接材料之间形成一条明显的链接痕迹;该技术对于焊接而产生的热量能够有效的精准控制,甚至可以降到最低,并且因为光具有明显界限的特性可以控制热对材料的影响范围会很大程度上保证材料的原本形状;激光焊接技术省去了材料之间的焊接金属,增大了两种材料之间分子的融合程度;激光焊接技术避免了电对材料带来的污染和损害,很大程度避免了材料的变形;光的范围很容易控制,并且它是以穿孔时焊接还手段,也具有很强的穿透度;光线可以聚集在很小的一个点,因此有利于面积十分小的物件的焊接;该焊接技术可以对多种材料之间进行焊接;因为光线传递的特性,激光焊接技术基本上不受距离的影响,这一特性有利于远距离操控,实施自动化控制,适应机电设备自动化发展的趋势等。
焊接技术在航空航天领域应用研究

焊接技术在航空航天领域应用研究一、焊接技术概述焊接是通过熔化金属,在两个或多个零部件之间形成永久连接的工艺。
焊接技术被广泛应用于航空航天领域,包括飞机、火箭、导弹、卫星、航天器等航空航天器件的生产制造过程中。
相比于其他连接技术,焊接技术连接强度高,连接点紧密,连接过程简便快捷等优势,被认为是航空航天领域中最为优越的连接方式之一。
二、焊接技术在航空航天领域的应用航空航天领域中大部分零部件的连接都依赖于焊接技术。
下面将针对不同类型的航空航天器件,从不同方面探讨焊接技术在航空航天领域的应用。
(一)飞机领域在飞机领域,焊接技术被广泛应用于飞机结构材料的制造和维护、修复。
因其高强度、轻量化、耐腐蚀、良好的氧化性能等特点,在飞机领域中得到了广泛地应用。
例如,在飞机机身外壳的焊接中,常用的焊接方法包括MIG、TIG、激光焊等方式。
通过将航空材料进行精细的焊接,使得飞机能够承受更大的气动载荷,而且更加耐久。
(二)火箭、导弹领域在火箭、导弹领域,焊接技术是制造强度高、耐氧化、耐高温腐蚀、高可靠性的材料连接的首选方式。
这些部件在实际使用过程中需要承受强大的机械、热载荷,因此要求焊缝质量非常高。
在这方面,弧焊和激光焊是最常用的焊接方法。
随着技术的不断发展,火箭、导弹零部件的焊接质量和可靠性也得到了极大的提高。
(三)卫星、航天器领域焊接技术在卫星、航天器领域的应用也非常广泛。
在这个领域,从航天器轻量化、强度提升的角度考虑,焊接技术有着更为重要的作用。
例如,在卫星整体结构中,由于重量问题,选择轻质的材料进行制造,但这些轻质材料在应对航天器在运行过程中产生的载荷方面需要焊接技术给予更大的帮助。
此外,金属表面状态、焊缝质量等问题同样成为航天器制造中需要研究解决的焦点。
三、焊接技术在航空航天领域中的发展趋势从目前来看,以弧焊为代表的变压器焊机市场占有率仍然是最高的,但是正面临千变万化的市场竞争和产品升级压力。
在深入研究现代焊接技术、模拟计算、材料表征、数字化化焊接等方向,推动新的焊接技术的开发和进步。
焊接技术在航空航天工业中的应用和发展建议_王亚军
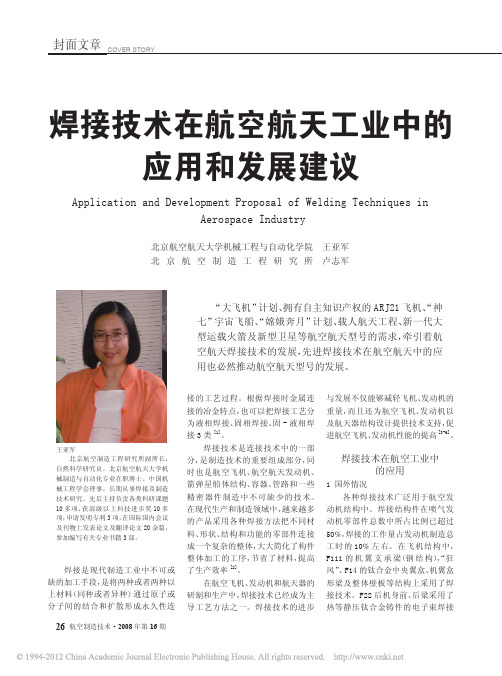
其他焊接技术在航空领域也得 有高强度钛合金 [14]。因此传统的弧
到了相应的应用和发展,例如,在美 焊工艺无法满足要求,需要先进的焊
国、加拿大、欧洲,中频电阻焊已经被 接技术。另外,中国一航第一飞机设
广泛用于高品质的焊接系统中。钎 计研究院、西飞公司和北京航空制造
盘和毂是构成航空发动机转子 的重要零件,一个盘毂组合件往往由 几级盘和(或)几级毂通过焊接或螺 栓连接而成。真空电子束焊接由于 具有焊接质量高、焊接变形小等一系 列优点而广泛应用在航空发动机盘 鼓组合的焊接中 。 [7-9]
进入 21 世纪,电子束焊接已经 成为大型飞机制造公司的标准配置, 是制造飞机主、次承力结构件和机翼 骨架的必选技术,也是衡量飞机制造 水平的一把标尺。国外电子束焊接 设备、技术已经相当成熟,成熟的电 子枪配以先进的逆变式高压电源,保 证了航空产品电子束焊接的高质量 要求。
(4)其他焊接技术。
28 航空制造技术·2008 年第 16 期
我国电子束焊接技术也应用在 如起落架、框、腹鳍、受油嘴等飞机结 构件上。发动机零部件采用电子束 焊接技术相对较多,如某型发动机高 压压气机转子、燃烧室机匣高压涡轮 组件等关键件均采用了电子束焊接 技术 。 [13]
我 国 西 飞 公 司 生 产 的 H6 系 列 飞机和 Y7 系列飞机,焊接的主要承 力结构件是飞机的主起落架和前起 落架零组件,焊接工艺均采用手工电 弧焊接工艺。将来要制造的大型运 输机,飞机起落架以及主承力梁、翼 盒的结构骨架和发动机挂架等将采 用焊接结构,其材料有高强度钢,也
高温合金 。 [10] 近年来激光焊接新的应用成果
是,用激光焊接技术取代传统的铆钉 进行铝合金飞机机身的制造从而减 轻飞机机身重量近 20%,提高强度近 20%。德国宇航公司 M B B 将激光焊 接用于飞机机身、机翼与内隔板和加 强筋的全部连接,取代了原有的铆接 工艺,被德国宇航界称为航空制造业 中的一大技术革命。空中客车公司 经过 8 年努力,成功地采用激光焊接 技术代替铆接技术,实现了 A340 飞 机的全部铝合金内隔板的激光加工, 使机身的重量减轻了 18%,制造成本 降低了近 25%,随后又将激光焊接加 工 技 术 推 广 应 用 到 A318、A380 飞 机 。 [10]
涂层技术在航空发动机中的应用(一)

涂层技术在航空发动机中的应用(一)涂层技术在航空发动机中的应用1. 提高发动机效率•热障涂层(TBC)热障涂层是一种高温耐受能力极强的陶瓷涂层,在航空发动机中有广泛应用。
它可以有效降低高温燃烧室和涡轮内部的表面温度,减少热量传递到其他部件,提高燃烧效率和涡轮的使用寿命。
热障涂层采用涂敷的方式施加在发动机部件表面,形成一层隔热层,同时具备优异的耐热性、耐腐蚀性和耐磨性。
•摩擦涂层摩擦涂层是一种能够减少摩擦阻力、降低能耗和延长机械部件寿命的涂层技术。
在航空发动机中,喷涂摩擦涂层可以应用于涡轮叶片表面以减少摩擦热造成的能量损耗,提高发动机效率。
该涂层通常由涂料和固化剂组成,喷涂后会形成一层耐磨、耐热的涂层,提供涡轮叶片所需的低摩擦系数。
2. 保护发动机结构•防腐蚀涂层发动机作为飞机的核心部件,其表面容易受到腐蚀的影响。
防腐蚀涂层能够降低发动机金属部件受到酸性气体、高温、湿度等因素的腐蚀程度,提高其耐久性。
航空发动机中使用的防腐蚀涂层通常采用环氧树脂和特殊添加剂,能够有效隔离金属与外界环境,降低腐蚀速度,同时具备耐温性能。
•降噪涂层航空发动机产生的噪音是对航空乘客和地面居民造成的主要干扰。
降噪涂层是一种能够减少发动机噪音输出的技术。
该涂层通常由吸声材料和表面粗糙度调整剂构成,能够通过吸收噪音和改变噪音传播路径来降低发动机产生的噪音水平。
降噪涂层的应用可以有效改善乘客舒适度,减少航空噪声对环境的影响。
3. 增强结构强度•硬质涂层硬质涂层是一种附着在金属表面的高硬度涂层,可以提供结构件的抗磨损和抗腐蚀能力。
在航空发动机中,硬质涂层通常应用于涡轮轴承、气门、活塞等部件表面,能够减少零部件间的摩擦和磨损,提高结构件的使用寿命。
常见的硬质涂层材料包括碳化硅、氮化硼等。
•纳米涂层纳米涂层是一种厚度在纳米级别的超薄涂层,它能够提供出色的防腐蚀和防磨损性能。
航空发动机中的纳米涂层可应用于活塞环、气缸内壁等部件表面,能够减少部件摩擦和磨损,提高结构件的使用寿命。
航空发动机的表面涂层技术_GAOQS
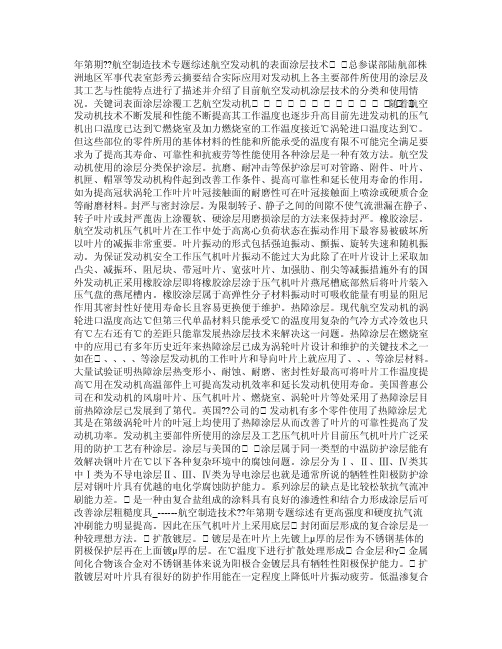
年第期??航空制造技术专题综述航空发动机的表面涂层技术 总参谋部陆航部株洲地区军事代表室彭秀云摘要结合实际应用对发动机上各主要部件所使用的涂层及其工艺与性能特点进行了描述并介绍了目前航空发动机涂层技术的分类和使用情随着航空况。
关键词表面涂层涂覆工艺航空发动机发动机技术不断发展和性能不断提高其工作温度也逐步升高目前先进发动机的压气机出口温度已达到℃燃烧室及加力燃烧室的工作温度接近℃涡轮进口温度达到℃。
但这些部位的零件所用的基体材料的性能和所能承受的温度有限不可能完全满足要求为了提高其寿命、可靠性和抗疲劳等性能使用各种涂层是一种有效方法。
航空发动机使用的涂层分类保护涂层。
抗磨、耐冲击等保护涂层可对管路、附件、叶片、机匣、帽罩等发动机构件起到改善工作条件、提高可靠性和延长使用寿命的作用。
如为提高冠状涡轮工作叶片叶冠接触面的耐磨性可在叶冠接触面上喷涂或硬质合金等耐磨材料。
封严与密封涂层。
为限制转子、静子之间的间隙不使气流泄漏在静子、转子叶片或封严蓖齿上涂覆软、硬涂层用磨损涂层的方法来保持封严。
橡胶涂层。
航空发动机压气机叶片在工作中处于高离心负荷状态在振动作用下最容易被破坏所以叶片的减振非常重要。
叶片振动的形式包括强迫振动、颤振、旋转失速和随机振动。
为保证发动机安全工作压气机叶片振动不能过大为此除了在叶片设计上采取加凸尖、减振环、阻尼块、带冠叶片、宽弦叶片、加强肋、削尖等减振措施外有的国外发动机正采用橡胶涂层即将橡胶涂层涂于压气机叶片燕尾槽底部然后将叶片装入压气盘的燕尾槽内。
橡胶涂层属于高弹性分子材料振动时可吸收能量有明显的阻尼作用其密封性好使用寿命长且容易更换便于维护。
热障涂层。
现代航空发动机的涡轮进口温度高达℃但第三代单晶材料只能承受℃的温度用复杂的气冷方式冷效也只有℃左右还有℃的差距只能靠发展热涂层技术来解决这一问题。
热障涂层在燃烧室中的应用已有多年历史近年来热障涂层已成为涡轮叶片设计和维护的关键技术之一如在 、、、、等涂层发动机的工作叶片和导向叶片上就应用了、、、等涂层材料。
热喷涂技术在航空制造中的应用
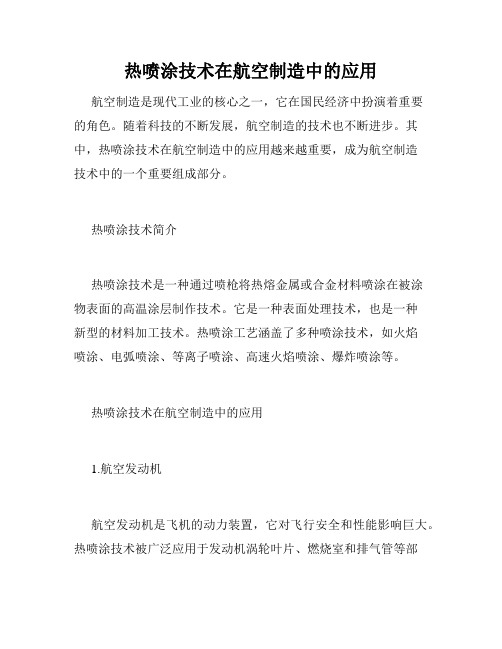
热喷涂技术在航空制造中的应用航空制造是现代工业的核心之一,它在国民经济中扮演着重要的角色。
随着科技的不断发展,航空制造的技术也不断进步。
其中,热喷涂技术在航空制造中的应用越来越重要,成为航空制造技术中的一个重要组成部分。
热喷涂技术简介热喷涂技术是一种通过喷枪将热熔金属或合金材料喷涂在被涂物表面的高温涂层制作技术。
它是一种表面处理技术,也是一种新型的材料加工技术。
热喷涂工艺涵盖了多种喷涂技术,如火焰喷涂、电弧喷涂、等离子喷涂、高速火焰喷涂、爆炸喷涂等。
热喷涂技术在航空制造中的应用1.航空发动机航空发动机是飞机的动力装置,它对飞行安全和性能影响巨大。
热喷涂技术被广泛应用于发动机涡轮叶片、燃烧室和排气管等部件的表面涂层。
涂层可以提高发动机的可靠性、耐久性和安全性。
同样可以降低飞机的噪音和减少污染排放。
2. 航空液压系统液压系统是重要的飞机控制部件之一,喷涂技术在航空液压系统中应用得越来越广泛。
热喷涂技术可以在液压系统中制造更耐磨、耐腐蚀和耐高温的涂层,提高整个液压系统的寿命和可靠性。
3. 航空发射器件航空发射器件是进行航空导航、控制和通讯的重要配件,它们的制造和质量对航空安全有重要影响。
热喷涂技术在航空发射器件的制造中也有广泛的应用。
喷涂技术可以在器件表面制作防护性的耐磨耐冲蚀膜层和高导热膜层,提高发射器件的工作效率和可靠性。
4. 航空结构件航空结构件是飞机的重要组成部分。
热喷涂技术在航空结构件的制造和修复中有着重要的应用。
热喷涂技术可以用来覆盖部件表面的脆弱区域、修理修补缺陷、加固弱化部件。
例如,用热喷涂技术对飞机的表面进行防腐涂层处理、增强飞机零部件的硬度、强度和韧性等。
热喷涂技术未来的发展热喷涂技术在航空制造中的应用已经得到广泛的发展,但是,它还有很大的发展空间。
未来,这项技术将会进一步发展应用到航天、高速列车、无人机等领域,以及与航空相关的领域。
例如,喷涂出高硬度、高强度的多层涂层,提高零部件的寿命和可靠性;增加自主修复功能等。
航空发动机高温防护涂层材料技术发展现状与趋势
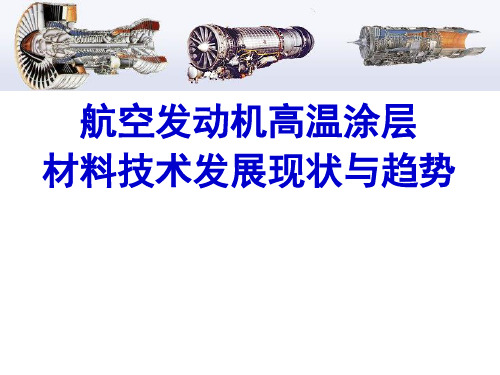
➢ 显著提高发动机推力:高 温合金能够承受更高的使 用环境温度,提高涡轮前 进口温度。工作温度提高 14-15K,推力增加100kgf (总推力增加 1-2%)
➢ 降低热端部件温度:大幅 度提高发动机寿命(表面 温度每降低14K,二级导向叶片 ➢ Boeing 747
CF6-80一级工作叶片 ➢ A300/330 ➢ Boeing 747/767 ➢ F414
CF6-80二级导向叶片 ➢ A300/330 ➢ Boeing 747/767
CFM56-7一级导向叶片 ➢ Boeing 737系列
YSZ(Yttria Stabilized Zirconia)
低活性渗Al时,高温合金中的Ni向外扩散为主,和渗剂 中的Al形成β-NiAl相。 低活性渗Al一般在较高温度进行:980~1100℃ 优点:涂层向外延生长,受合金成分影响较小。 缺点:靠高温合金一侧产生Kirkendall孔洞,并且有固
体颗粒(如:氧化铝)进入涂层
包埋渗Al-高活性渗Al
高活性渗Al时,Al向内扩散,高温合金原始表面基本保 持不动。渗Al后多形成富Al相,如Ni2Al3等脆性相,需 要进一步进行热处理,形成β-NiAl相。 高活性渗Al一般在较低温度进行:700-800℃ 优点:涂层不会因为扩散不平衡而产生Kirkendall孔洞。
等离子喷涂热障涂层
电子束物理气相沉积热障涂层
热障涂层陶瓷层的主要制备方法
热喷涂(Thermal Spray)技术
热喷涂:材料经热源加热至熔化或半熔化态,用高压 气流令其雾化并喷射于工件上,形成涂层的一种表面 加工方法。
大气等离子喷涂:陶瓷层和粘结层 低压等离子喷涂:粘结层 HVOF喷涂:粘结层 爆炸喷涂:陶瓷层和粘结层
表面涂层技术在航空发动机中的具体应用
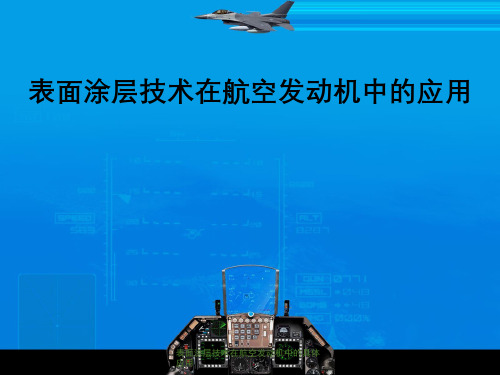
• 航空发动机压气机叶片在工作中处于高离心负 荷状态,在振动作用下最易被破坏。
表面涂层技术在航空发动机中的具体 应用
减振措施
• 在叶片结构设计上采取加凸尖、减振环、阻尼块、 带冠叶片、宽弦叶片、加强肋、削尖等减振措施。
• 采用橡胶涂层,即将橡胶涂层涂于压气机叶片燕尾 槽底部,然后将叶片装入压气机盘的燕尾槽内。
表面涂层技术在航空发动机中的具体 应用
2.航空发动机表面涂层技术分类
热喷涂涂表层面涂在层技飞术在机航空发发动动机中机的具体中的应用示意图 应用
2.航空发动机表面涂层技术分类
• 保护涂层 • 封严密封涂层 • 橡胶涂层 • 热障涂层
表面涂层技术在航空发动机中的具体 应用
2.1保护涂层
主要保护部位
表面涂层技术在航空发动机中的具体 应用
双辉等离子表面合金化技术
双辉等离子渗金属技术的基 本原理: 在使工件和源极分别产生所 谓双层辉光放电现象。辉光 放电所产生的氩离子轰击, 使源极溅射出合金元素并飞 向工件,而工件经离子轰击 被加热到高温。合金元素借 助于轰击吸附和扩散而渗入 工件表面,从而形成含有欲 渗合金元素的合金层。
2.2密封封严涂层
封严涂层 为限制转子、静子之间的间隙, 不使气流泄漏,
在静子、转子叶片或封严蓖齿上涂覆软、硬涂层, 用磨损涂层的方法来保持封严。 密封涂层
有的静子叶片是插入静子内环的,二者的间隙 造成气流损失,这时可采用密封涂层封住,这要求密 封涂层耐温、抗振、柔软,长期不老化。 可磨耗封严涂层
抗磨、抗冲击涂层: 叶片榫头和盘榫槽之间涂的耐磨涂层 高压压气机叶片型面上的有机硅耐磨涂层 压气机叶片阻尼凸台上的叶片振动涂层 涡轮叶片防热盐涂层 涡轮叶片叶冠接触面硬质合金耐磨涂层
航空发动机涂层技术及应用_武洪臣

良好的韧性和结合强度、抗氧化、 等离子喷涂、多弧离子
耐腐蚀
镀
涡轮叶片
压气机 / 涡轮叶片榫头和 榫槽、紧固件连接部位、摩
擦副结构
阻燃涂层 环境障碍涂
层
憎水涂层
阻止摩擦热的积累,有效延缓或阻止燃 燃烧热值低、抗氧化、导热性好、可 等离子喷涂、多弧离子
烧的进展
磨耗、摩擦系数低、较高的硬度
镀
阻止或减小发动机环境对高温结构材 料性能的影响
尾
隐身涂层
红外隐身、雷达隐身
吸收雷达波、热发射率低
等离子喷涂
尾喷管
表3 热障涂层制备技术对比
工艺
等离子喷涂
EB-PVD
沉积速度
高
适中
粗糙度
粗糙
光滑
缺陷
结构不均匀,往往产生微孔、非粘结界面、 晶粒间界、夹杂等缺陷
结构均匀、致密
结构
层状结构
柱状晶结构
冷却气孔影响 结合强度 寿命
冷却通道易堵塞 20~40MPa,机械结合,弱
涂层技术 COATING TECHNOLOGY
航空发动机涂层技术及应用
Surface Coating Technology and Application for Aeroengine
中航工业北京航空制造工程研究所 武洪臣 高 巍
在诸多涂层中,热障涂层结构最为复杂,并且在高温工 作环境中承担着重要角色。尤其是利用电子束作为热源的 热障涂层沉积技术,在航空航天领域得到了广泛应用并发 挥了巨大作用。
近几年,随着涡轮进口温度要求 越来越高,人们开始研发相稳定温度 更高的涂层材料与结构,烧绿石结构
2013 年第 9 期·航空制造技术 81
涂层技术 COATING TECHNOLOGY
激光熔敷_焊_技术在航空发动机生产中的应用_王茂才
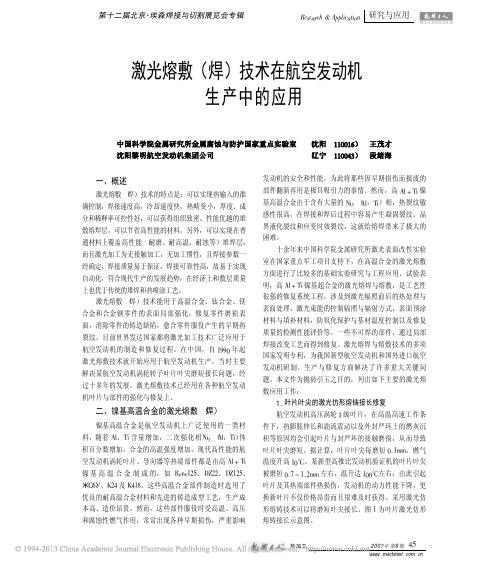
热加工
!""# 年 第 $ 期 %0 !!! ’ "#$%&’&() ’ $*" ’ $’
六、结语
激光复合焊将两种焊接方法结合起来,它采用了两 者各自的优点,获得了最佳的焊接效果,更高的焊接速 度与良好的焊缝搭桥能力。它是目前最先进的焊接方法 之一,实现了高焊接速度与良好焊接质量的完美结合。 激光复合焊技术是汽车工业中一种全新的焊接技 术,尤其是对于激光束焊无法实现或在经济上不可行的 装配间隙要求。它具有宽广的应用范围和高效的特性, 同时减少投资成本、缩短生产时间、节约生产成本和提 高生产率,具有更强的竞争力。
采用激光仿形熔铸技术成功地解决了许多技术难 题。例如,将磨短的高压一级叶片接长 " # $%%,及时 确保了国家重大工程顺利试车达标;使 &’(( 黑鹰战机 一级转子叶片叶尖烧蚀区变形得到修复;将海军在役的 )*+ 一级到二级和 )*+ 二级涡轮叶片端部接长 (,-%%, 现已飞行 "((. 以上。到目前,已实现批量接长修复。 !" 叶片冠部阻尼面的激光敷层强化与修复 航空发动机带冠转子叶片联锁面在高温燃气和高速 转动运行的工况下,会发生严重的高温腐蚀和微振磨损 使本来装配紧密的叶片发生严重的松动,由此引起燃气 油漏和叶片的摆动,使叶片根部遭受到很大的扭弯应力 至断裂,为此叶片联锁面必须施加防蚀抗磨涂层来强化。 采用激光熔敷稀土改性的钴基合金粉末可以实现阻尼 面强化和恢复磨损的阻尼面构形。图 " 为低压涡轮叶片阻 尼面激光熔敷钴基涂层的典型形貌及显微硬度分布。
研究与应用
是钛合金由于其耐磨性和抗机械疲劳性较差,而易产生 磨损与疲劳裂纹。某飞机的 !"#$ 合金防冰壳体内壁与 其配合件之间发生微振磨损,导致其配合密封面发生台 阶式磨损沟槽而失效,如图 %& 所示。采用钛合金高纯 净激光熔敷焊一整套工艺方法,可使壁厚仅有 #’$(( 的 壳体得到无变形修复,其补焊区为冶金结合,组织均匀 致密,如图 %) 所示。
搅拌摩擦焊技术在军用飞机航空修理中的应用分析

搅拌摩擦焊技术在军用飞机航空修理中的应用分析军用飞机是航空兵的主要技术装备,军用飞机的使用拓展了战斗的空间,也就是由地面拓展到了天空,它对军事战略技术以及军队的部署都具有非常重要的影响。
保持军用飞机的战斗性能是非常重要的,随着科学技术的不断发展,军用飞机的类型更加广泛,相应的维修技术也在逐渐发生着改变,只有这样才能确保军用飞机的使用安全和强大的战斗力。
一、搅拌摩擦焊技术的发展现状和工作原理所谓的摩擦焊技术简单来说就是利用工作过程中工件的各个端面进行相互运动和相互摩擦所产生的热量,让处于端部的材料达到一种热塑性的状态,并在这种状态下,以比较快速的时间进行顶锻,完成焊接的工作。
这种技术的优越性在于它可以实现对同等或是异种材料的完美焊接,比如各种金属材料、复合型材料、塑料或是陶瓷等,这种焊接技术的工作效率较高而且焊接的质量较好,因此具有较为广泛的使用价值。
搅拌摩擦焊技术(Friction Stir Welding,简称FSW)是于上世纪九十年代初期由英国焊接研究所(The Welding Institute)发明的一项专利焊接技术。
搅拌摩擦焊技术有效的改善了传统技术中存在的弊端,它能够通过不同种类的接头形式和在不同的焊接位置进行有效的连接。
早在1998年,美国波音公司的空间和防御实验室就引进了该项技术,将其用于焊接某些火箭部件。
搅拌摩擦焊技术虽具有常规技术所不具备的优点,但是它的焊接热源同样来源于摩擦热和塑形变形热。
在使用搅拌摩擦焊技术时,技术人员需要将圆柱形状的搅拌针(welding pin)深入到工件的接缝处,借助焊头在工作过程中所产生的高速旋转与所需焊接的工件材料之间相互摩擦所产生的高热量,对焊接的材料部位进行软化,在软化的同时对材料进行不断的搅拌直至焊接完成。
在进行搅拌摩擦焊技术的过程中,焊头的高速旋转会使工件的接缝处与工件之间产生一定的位移,所以在事先一定要将所需焊接的工件牢固的固定在背垫上。
- 1、下载文档前请自行甄别文档内容的完整性,平台不提供额外的编辑、内容补充、找答案等附加服务。
- 2、"仅部分预览"的文档,不可在线预览部分如存在完整性等问题,可反馈申请退款(可完整预览的文档不适用该条件!)。
- 3、如文档侵犯您的权益,请联系客服反馈,我们会尽快为您处理(人工客服工作时间:9:00-18:30)。
p o e w sa h e e oa o d t e e e t n te d n mi ef r n e a d a s r h eo n i esr cu e a r ih n s , u t e h e o n i e r b a c iv d t v i f c h y a cp r ma c n s u e t e a re gn t , r i t t e s f rh rt e a re gn h o o ut g t s ef i n ya d s f t e eg a a t e . e t f c e c n a ey w r u r n e d i
有 的机 械 安装 、 焊 压 片 固定 、 粘 固定 等 方 法会 引 点 胶
可达毫米级 , 最大尺寸不受限制 ; 涂覆后受感部性能
不受影 响 。 凭其 具有 的上述 优 良性 能 ,涂 覆 焊技 术
适用于各种金属基体 , 尤其不锈钢和高温合金基体的
_件 的加工 , I 二 因此 适用 于发 动机测 试 受感部 安装 。 本 文对 航 空发 动 机 受感 部 涂 覆 焊安 装 T 艺进 行
基体 具 有一致 或更 好 的性 能 ; 加T 表 面的最 小 尺寸 被
摘要 : 满足 发动机测试技 术发展 的需求 , 为 解决 发动机测试 改装和安装带 来的流
场 扰 动 问题 , 析 了设 备 参 数 对 涂 覆 焊 效 果 的 影 响 , 展 了 涂覆 焊技 术 的 直 用 研 究 , 分 开 获
取 了可靠的测试数据, 从而实现 了发 动机 测试 受感部 的埋设 式安装, 避免 了测试对发动 机 气动性能的影响, 保证 了发动机结 构的气密性, 保障 了后续试聆试车的效果和发动卞 丌
张兴 (9 5 , , 15 )男 高级 程 师 , 从事 航空发动机测试研究工作 。 收稿 日期 :0 1 0 一 8 2 1— 8 i
Pr b o e Mou t n
ZH AN G n Xi g,LI Zho —k ,X U E i U ng ni X u—s ng he ,ZH AN G Yu—xi n
Hale Waihona Puke d su b n e b o g tb h e t rf t g a d mo n ig h q i e n a a tr efc n t e c a ig we l w s a ay e ,a p ia in i r a c ru h y t e ts e t n n u t ,t e e u p me tp r me e f to h o t h a n l s d p l t t i i n e n c o
第3 7卷 第 6期 21年 1 01 2月
航 空 发 动 机
V ]7N . o3 o6 -
De ,20ll c .
涂覆焊技术在航牢发动机受感部
安装 中的应用研究
张 兴 , 忠 奎 , 秀生 , 刘 薛 张玉 新
( 中航 T 业 沈 阳发 动 机 没 计研 究所 , 阳 10 1 ) 沈 10 5
( AVI h n a g E gn s na d Pee rh Istt, h n a g 1 0 , ia C S e y n n ieDei n .sac n tue S e y n 0 1 Chn ) g i 1 5
Ab t c : T me t h rq ie n o e o n ie e t n s le h f w i l sr t o a e t e e u rme t f a r e g n ts a d ov t e l f ( o eI
r s rh o h o tn l sde eo d.The r la e ts t s a q r d.Th it n mou tng o e o n i e e tm e s r m e t e eac ft e c ai g wed wa v lpe e ibl e tdaa wa c uie e bul-i n i fa r e g n ts a u e n
的安 全 性
关键 词 : 涂覆焊 ; 受感部 ; 安装; 空发动机 ; 航 测试
Ap l ain o a ig W ed Te h iu re gn a u e pi t f c o Co t n l c nq e i Ae o n ie Me s r me t n n
Ke r s c ai g wed me s r me tp b ; u t a r e gn ; e t y wo d : o t l ; a u e n r e mo n; e o n ie ts n o
0 引 言
航空发动机的整机 、 耐久性 、 部件 、 高空台和飞行
等试验 , 需要 进 行 大量 测 试 , 以获 得 发动 机 的状态 数 据。 随着航 空 发动 机 向高推 重 比的发 展和 内流计 算 的 需 要 , 发 动机 试 验 和测 试 技术 提 出 了新 要 求 , 对 对 也 测试 改 装 中测试受 感部 的安装方 法 提 出了新要 求 。 原
了应用 研究 。
1 工艺参数对涂覆焊效果的影响
在 应用 中发 现 , 工艺参 数 的选择 直接 影 响涂覆 焊
起发动机内流场的扰动 , 在一定程度上影响发动机的 气动性 能 ,从而影 响设计 验证 和故障信息 的精确判
断。 金属结构表面涂覆焊技术是基于沉积涂层基本原 理的 1 种高能电微弧脉冲冷焊接技术( 简称涂覆焊 ) 。 其特点是 : T件本体无需预加热 , 属冷加T , T件受热 影响小 , 无变形 ; 涂覆层与工件基体为冶金性结合 , 和