凸模固定板
模具毕业设计实例冲裁模设计举例

冲裁模设计举例图2.69所示零件为电视机安装架下板展开坯料,材料为1Cr 13,厚度mm t 3=,未注圆角半径mm R 1=,中批量生产,确定产品的冲裁工艺方案并完成模具设计。
图2.69 零件图1. 冲裁件工艺性分析零件的加工涉及冲孔和落料两道工序。
除孔中心尺寸公差为±0.1mm 和孔径尺寸公差为+0.2mm 外,其余尺寸均为未注公差,查表2.4可知,冲裁件内外形的达到的经济精度为IT12~IT14级。
符合冲裁的工艺要求。
查表2.2可知,一般冲孔模冲压该种材料的最小孔径为d ≥1.0t ,t =3mm,因而孔径ø8mm 符合工艺要求。
由图可知,最小孔边距为:d =4mm ,大于材料厚度3mm ,符合冲裁要求。
2. 确定冲裁工艺方案及模具结构形式该冲裁件对内孔之间和内孔与外缘之间有较高的位置精度的要求,生产批量较大,为保证孔的位置精度和较高的生产效率,采用冲孔落料复合冲裁的工艺方案,且一次冲压成形。
模具结构采用固定挡料销和导料销对工件进行定位、弹性卸料、下方出料方式的倒装式复合冲裁模结构形式。
3. 模具设计与计算(1)排样设计排样设计主要确定排样形式、条料进距、条料宽度、材料利用率和绘制排样图。
1)排样方式的确定。
根据冲裁件的结构特点,排样方式可选择为:直排。
2)送料进距的确定。
查表2.7,工件间最小工艺搭边值为mm 2.2,可取mm a 31=。
最小工艺边距搭边值为mm 5.2,取mm a 3=。
送料进距确定为mm h 44.199=。
3)条料宽度的确定。
按照无侧压装置的条料宽度计算公式,查表2.8、表2.9确定条料与导料销的间隙和条料宽度偏差分别为mm mm b 0.1,0.10=∆=。
()()0100093132862-∆-∆-=+⨯+=++=b a L B4)材料利用率的确定。
%08.91%10044.1999344.19686=⨯⨯⨯==Bh A η 4)绘制排样图。
冲压模具名词术语大集合

上模:上模是整副冲模的上半部,即安装于压力机滑块上的冲模部分。
上模座:上模座是上模最上面的板状零件,工件时紧贴压力机滑块,并通过模柄或直接与压力机滑块固定。
下模:下模是整副冲模的下半部,即安装于压力机工作台面上模具部件术语上模:上模是整副冲模的上半部,即安装于压力机滑块上的冲模部分。
上模座:上模座是上模最上面的板状零件,工件时紧贴压力机滑块,并通过模柄或直接与压力机滑块固定。
下模:下模是整副冲模的下半部,即安装于压力机工作台面上的冲模部分。
下模座:下模座是下模底面的板状零件,工作时直接固定在压力机工作台面或垫板上。
刃壁:刃壁是冲裁凹模孔刃口的侧壁。
刃口斜度:刃口斜度是冲裁凹模孔刃壁的每侧斜度。
气垫:气垫是以压缩空气为原动力的弹顶器。
反侧压块:反侧压块是从工作面的另一侧支持单向受力凸模的零件。
导套:导套是为上、下模座相对运动提供精密导向的管状零件,多数固定在上模座内,与固定在下模座的导柱配合使用。
导板:导板是带有与凸模精密滑配内孔的板状零件,用于保证凸模与凹模的相互对准,并起卸料(件)作用。
导柱:导柱是为上、下模座相对运动提供精密导向的圆柱形零件,多数固定在下模座,与固定在上模座的导套配合使用。
导正销:导正销是伸入材料孔中导正其在凹模内位置的销形零件。
导板模:导板模:板模是以导板作导向的冲模,模具使用时凸模不脱离导板。
导料板:导料板是引导条(带、卷)料进入凹模的板状导向零件。
导柱模架:导柱模架是导柱、导套相互滑动的模架。
冲模:冲模是装在压力机上用于生产冲件的工艺装备,由相互配合的上、下两部分组成。
凸模:凸模是冲模中起直接形成冲件作用的凸形工作零件,即以外形为工作表面的零件。
凹模:凹模是冲模中起直接形成冲件作用的凹形工作零件,即以内形为工作表面的零件。
防护板:防护板是防止手指或异物进入冲模危险区域的板状零件。
压料板(圈):压料板(圈)是冲模中用于压住冲压材料或工序件以控制材料流动的零件,在拉深模中,压料板多数称为压料圈。
冲压工艺与模具设计:冲裁模的主要零部件结构设计

凹模厚(高)度
H=kb (≥15)
k见表2.22 凹模壁厚 C=(
1.5~2)H
(≥30~40)
计算值:
靠用标准,选择模架的依据。
2 工作零 件3.凸凹模
复合模中同时具有落料凸模和冲孔凹模作用的工作零件。
凸凹模的最小壁厚: 正装复合模,内孔不积存废料,胀力小,最小壁厚可以小些; 倒装复合模,若内孔为直筒形刃口形式,且采用下出料方式, 则内孔积存废料,胀力大,故最小壁厚应大些。
导料板的厚度:见表2.24
导料板结构
3 定位零件(续)
2)侧压装置
设置目的:若条料公差较大,为避免条料在导料板中偏摆,使最 小搭边得到保证。
结构形式:①弹簧式侧压装置 ②簧片式侧压装置 ③簧片压块式侧压装置 ④板式侧压装置
不宜设置侧压装置的场合:①板料厚度在0.3mm以下的薄板; ②辊轴自动送料装置的模具。
谢谢!
特殊侧刃:既可定距,又可冲裁零件的部分轮廓 宽度b
侧刃断面尺寸 其他尺寸按标准规定
侧刃凹模按侧刃实际尺寸配制,留单边间隙。
侧刃数量: 一个或两个 侧刃布置: 并列布置、对角布置
侧刃定位误差比较
1-导料板 2-侧刃挡块 3-侧刃 4-条料
尖 角 形 侧 刃
特殊侧刃
3 定位零件(续)
5)导正销
使用目的: 消除送进导向和送料定距或定位板等粗定位的误差。 主要用于: 级进模
1)导料销、导料板 导料销:两个,位于条料的同侧, 从右向左送料时,导料销装在后侧; 从前向后送料时,导料销装在左侧。 结构形式: 固定式、活动式
3 定位零件(续) 1)导料销、导料板(续) 导料板:设在条料两侧 结构形式:一种是标准结构,它与卸料板(或导板)分开制造 一种是与卸料板制成整体的结构。
冲压基础知识培训试题

冲压基础知识培训试题1. 落料和冲孔是常用的冲压分离工序,这两种方法合称为()。
[单选题] *A.冲裁工序(正确答案)B.弯曲工序C.拉深工序2. 冲孔工序中,模具从坯料上冲切下来的是()。
[单选题] *A.零件B.废料(正确答案)C.工具3.冲裁的变形过程包含以下三个阶段()。
[单选题] *A.弹性变形阶段、塑性变形阶段、断裂分离阶段(正确答案)B.分离阶段、变形阶段、断裂阶段C.变形阶段、成形阶段、断裂阶段4.在冲裁的变形过程中,哪个阶段冲裁件断面会产生粗糙的断裂带和毛刺()。
[单选题] *A弹性变形阶段B塑性变形阶段C断裂分离阶段(正确答案)5.冲裁的间隙可以分成五类,间隙最大的应该是()。
[单选题] *B.Ⅰ类C.Ⅴ类(正确答案)6.以下冲裁材料,硬度低,塑性好,容易冲裁成形的是()。
[单选题] *A.低碳钢、铝和铜的合金(正确答案)B.不锈钢、高碳钢C.硬质合金7.什么情况选择复合模?() [单选题] *A.工序不多,一般两三道工序时(正确答案)B.工序比较多,超过5道工序时C.只有一道工序8.冲压的卸料方式有两种()。
[单选题] *A.弹性卸料、刚性卸料(正确答案)B.被动卸料、主动卸料C.顶料、卸料9.正装式的冲压模,采用弹性卸料时,卸料板通常在()。
[单选题] *A.下模,和凹模在同一侧B.上模,和凸模在同一侧(正确答案)C.都可以10.冲压模具冲压的自动定位方式,一般采用()来定位。
[单选题] *B.侧刃(正确答案)C.都可以11.哪种排样法浪费材料少,材料利用率最高()。
[单选题] *A.有废料排样法B.少废料排样C.无废料排样法(正确答案)12.一次只能冲压一个零件的排样方法是()。
[单选题] *A.直排单排,斜排(正确答案)B.对排C.混排,多排13.适合于精度要求不高的冲压模,工作区域大,适合手工送料,特别是条料尺寸比较大的情况,能两个方向送料,会产生冲压力偏心()。
凸模的设计
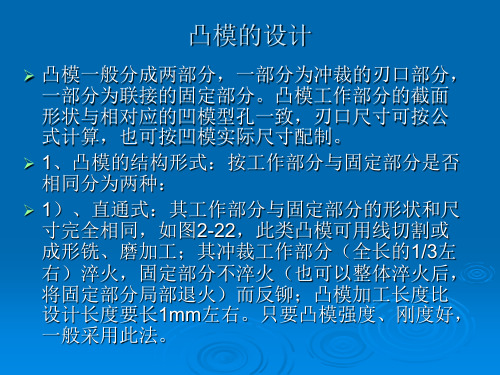
2.6.2 凸模的设计
淬火长度
说明:1.尺寸5,4.25按凸模实际尺寸配做,双面间隙0.19mm. 2.热处理HRC58-60.
图2-32 长圆形冲孔凸模
(3) 长圆形冲孔凸模为非圆形,且强度、刚度足够, 故也采用直通式铆接固定。如图2-32所示。
(4) 圆形冲孔凸模强度、刚度也无问题,但从加工方 便的角度可采用台阶式台肩固定。见图2-23。
9.98
2.6.2 凸模的设计
1. 尺寸5、4.25按凹模实际尺寸配做,双面间隙 0.19mm;
2. 材料CrWMn, 3热处理硬度60~62HRC。
图2-23 阶梯式冲圆孔凸模
2.6.2 凸模的设计
1-垫板2-凸模固定板3-凸模4-凸模5-防转销 6-上模座 图2-24 凸模的固定方法
对圆形断面Jmin = d 4
64
bh3
对矩形断面凸模,Jmin= 12
d-凸模工作刃口直径(mm)
b-凸模工作刃口宽度(mm)
h-凸模工作刃口长度(mm)
μ-支承系数。当凸模如图(a)所示的无导向装置时,视 为一端固定,另一端自由的支承,取μ=2;如图(b)所示的直
通凸模,由导板或料导向时,可视为一端固定,另一端铰支,
2.6.2 凸模的设计
4、凸模护套
当凸模自由长度大于max时,则应采用护套保护凸模。图 2-31 a)、b)是两种简单的圆形凸模护套。
图a)所示护套1、凸模2均用铆接固定。 图b)所示护套1采用台肩固定 图c)所示护套1固定在卸料板(或导板)4上。 图d)是一种比较完善的凸模护套,三个等分扇形块6固定
全部
2.6.2 凸模的设计
淬火长度
尺寸47.81、13.86按凹模实际尺寸配做,双面 间隙0.19mm;
圆形凸模的固定
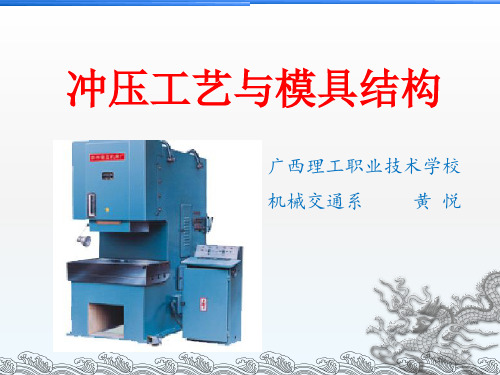
后两种固定方法是异形凸模设计中被广泛应用。
图2-20 异形凸模的固定方式
4、小凸模的固定
冲小孔的凸模强度和刚度差,容易弯曲和折断,所以必须采取措施 提高它的强度和刚度,从而提高其使用寿命。对冲小孔凸模加异向结构 就是保护措施的一种,如图a、图b所示。设计时,凸模与卸料板的间隙
图2-19
圆形凸模的固定方式
3、异型凸模的固定
在实际生产中广泛应用的非圆形凸模,可采用如图2-20所示的固定 方式,凸模与凸模固定板过渡配合。图2-20(a)所示为台肩固定,图2-
20(b)所示为铆接固定,这两种固定方法,只要工作部分截面是非圆形,
而固定部分是圆形的,就必须在固定端接缝处加防转销。图2-20(c)
要小于凸模与凹模间隙,同时应采用内导柱为卸料板导向。制造时,如
果卸料板进行淬火,可以不采用镶块结构。为了小凸模折断后容易更换, 往往将小凸模设计成易拆结构,如图c、d所示。图c为压板式,用于异
型小凸模,d用于圆形小凸模结构。
图2-21 小凸模的固定及易拆结构
冲压工艺与模具结构
广西理工职业技术学校 机械交通系 黄 悦
课题十:冲裁模具工作零件的结构——凸 模的固定方式
知识目标:
1、掌握冲裁模工作零件的凸模固定方式。
能力目标: 1、能够很好的掌握凸模的固定方式。
凸模的固定方式
1、大型凸模的固定
如图2-18所示,平面尺寸比较大的凸模,可以直接用螺钉吊 装固定,若空间允许,可以采用销钉定位,如图2-18(a)所示, 否则采用面定位,如图2-18(b)所示。
凸模固定板连接结构的改进设计
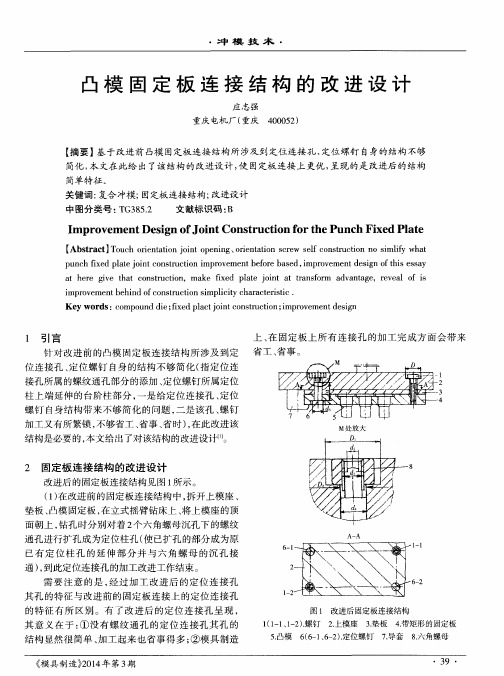
奇瑞汽车股份有 限公 司( 安徽 芜湖
2 4 1 0 0 9 )
【 摘要】 通过对四 门尖点 突出部位的整改方法的探讨 , 对 尖点 突出提 出具体措施 , 通过优化
制件结构 、 选择恰 当的预 弯工艺 、 选择合适的松 紧程度 、 开缺 口等 , 对 尖点 突出部位进行有
效整改。对压合 总成件合格率的提升和整车 匹配具有重要 意义。
【 A b s t r a c t 】 T o u c h o r i e n t a t i o n j o i n t o p e n i n g 、 o r i e n t a t i o n s c r e w s e l f c o n s t r u c t i o n n o s i m l i  ̄w h a t
p u n c h i f x e d p l a t e j o i n t c o n s t r u c t i o n i mp r o v e me n t b e f o r e b a s e d , i m p r o v e me n t d e s i g n o f t h i s e s s a y
l 引 言
位连接孑 L 、 定位螺钉 自身的结构不够简化 ( 指定位 连 接孑 L 所属 的螺纹通孑 L 部 分的添加 、 定位螺钉所属定位 柱上端延伸 的台阶柱部分 , 一是给定位连接孔 、 定位 螺钉 自身结构带来 不够简化 的问题 , 二是该孔 、 螺钉 加工又有所繁锁 , 不够省工 、 省事 、 省 时) , 在此改进该 结构是必要的 , 本文给 出了对该结构的改进设计u 。
需要 注意 的是 , 经 过 加 工 改 进 后 的定 位 连 接 孑 L
其孑 L 的特征与改进 前的 固定板连接 上的定位连接孔
凸模固定板机械加工工艺过程卡片

机械加工工艺过程卡片
产品型号
零件图号
产品名称
单工序落料模
零件名称
凸模固定板
共
1
页
第
1
页
材料
牌号
45钢
毛坯
种类
毛坯外形尺寸
85x85x30
每毛坯
可制件数
1
每台
件数
1
备注
工
序
号
工名
序称
工序内容
车
间
工
段
设备
工艺装备
工时/s
准终
单件
1
下料
45钢,锯床下料,板料85mmX85mmX30mm
机加工
数铣
数控铣床
虎钳,立铣刀,游标卡尺
8
描图
描校
底图号
装订号
设计(日期)
校对(日期)
审核(日期)
标准化(日期)
会签(日期)
标记
处数
更改文件号
签字
日期
标记
处数
更改文件号
签字
日期
保证表面粗糙度达到要求
机加工
数铣
数控铣床
虎钳,钻头,立铣刀,游标卡尺
5
钻螺
纹孔
钻螺纹孔4XM6,一次加工完毕,保证表面粗糙度达到要求
机加工
数铣
数控铣床
虎钳,钻头,立铣刀,游标卡尺
6
钻销
钉孔
钻销钉孔2XФ6,一次加工完毕,保证表面粗糙度达到要求
机加工
数铣
数控铣床
虎钳,钻头,立铣刀,游标卡尺
7
铣外
轮廓
精铣外轮廓,尺寸80mmX80mmX25mm
级进模装配工艺
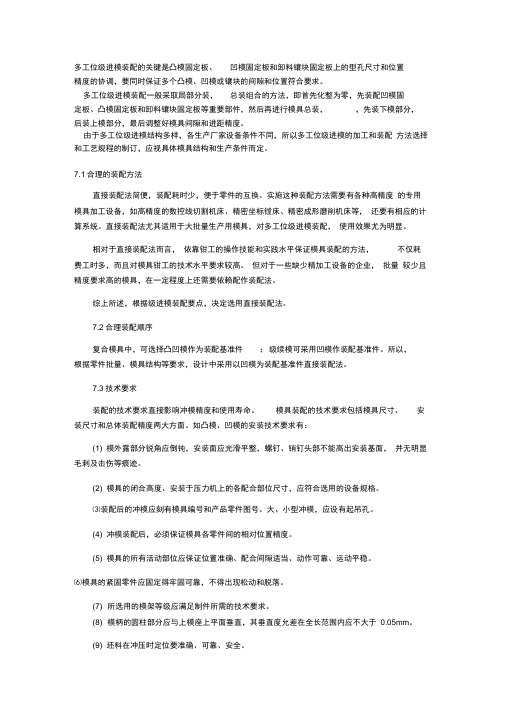
多工位级进模装配的关键是凸模固定板、凹模固定板和卸料镶块固定板上的型孔尺寸和位置精度的协调,要同时保证多个凸模、凹模或镶块的间隙和位置符合要求。
多工位级进模装配一般采取局部分装,总装组合的方法,即首先化整为零,先装配凹模固定板、凸模固定板和卸料镶块固定板等重要部件,然后再进行模具总装,,先装下模部分,后装上模部分,最后调整好模具间隙和进距精度。
由于多工位级进模结构多样,各生产厂家设备条件不同,所以多工位级进模的加工和装配方法选择和工艺规程的制订,应视具体模具结构和生产条件而定。
7.1合理的装配方法直接装配法简便,装配耗时少,便于零件的互换。
实施这种装配方法需要有各种高精度的专用模具加工设备,如高精度的数控线切割机床、精密坐标镗床、精密成形磨削机床等,还要有相应的计算系统。
直接装配法尤其适用于大批量生产用模具,对多工位级进模装配,使用效果尤为明显。
相对于直接装配法而言,依靠钳工的操作技能和实践水平保证模具装配的方法,不仅耗费工时多,而且对模具钳工的技术水平要求较高。
但对于一些缺少精加工设备的企业,批量较少且精度要求高的模具,在一定程度上还需要依赖配作装配法。
综上所述,根据级进模装配要点,决定选用直接装配法。
7.2合理装配顺序复合模具中,可选择凸凹模作为装配基准件;级续模可采用凹模作装配基准件。
所以,根据零件批量、模具结构等要求,设计中采用以凹模为装配基准件直接装配法。
7.3技术要求装配的技术要求直接影响冲模精度和使用寿命。
模具装配的技术要求包括模具尺寸、安装尺寸和总体装配精度两大方面。
如凸模、凹模的安装技术要求有:(1) 模外露部分锐角应倒钝,安装面应光滑平整,螺钉、销钉头部不能高出安装基面,并无明显毛刺及击伤等痕迹。
(2) 模具的闭合高度、安装于压力机上的各配合部位尺寸,应符合选用的设备规格。
⑶装配后的冲模应刻有模具编号和产品零件图号。
大、小型冲模,应设有起吊孔。
(4) 冲模装配后,必须保证模具各零件间的相对位置精度。
模具结构
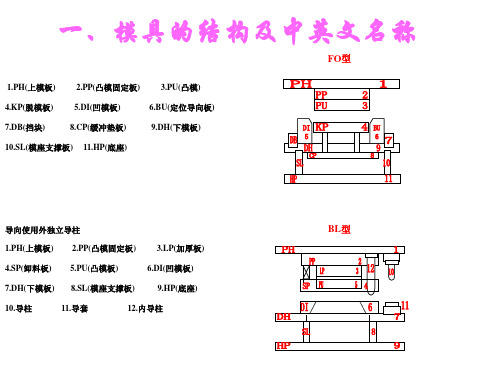
2.2.5 CO型模具简介 CO模叫复合落料模它是集外形落料,穿孔,翻边,压花,拉深,刻印,切断,折弯等符加工为一体的模具,它采用内外导柱,导向,能很好的保证部 品加工精度,当然这种模具本身的制作精度也很高,一但这种模具导向被破坏,修理起来很困难,所有的导向装置都将全部全换位置,而更换 后的模具,也很难达到初始的精度. 2.2.6 COA型与B型的区别: A型CO模是最普遍的复合落料模具,它采用弹簧卸料,这种模具结构形式在我公司多用于200T,110T,60T,及部45T. B型CO模具,是一种较特殊的复合落料模具这种模具适用于部品较小或部品加工的孔数较多时无法在SP板上布置弹簧的情况,它的工作 原理是通过顶杆将卸料力传送给SP板,在我公司的45T模具上使用较多,但当部品较小.以致不能布置弹簧时通常采用打料杆卸料. 2.2.7 CO型模具一般易出现的问题及造成的原因: 问题点:1.毛刺(原因:A.中心不重合;B.冲裁间隙不一致;C.中心位置偏移<导向不良>) 2.上下模粘料(原因:A.卸料力不足,<SP,SC板>;B.DU与SP,SC与PD变形或间隙变小.
2.5 BE型模具
2.5.1 BE型模具结构及相应名称 1.PH(上模板) 2.PP(凸模固定板) 3.PU(V型凸模) 4.DI(V型凹模) 5.DH(下模板) 6.SL(模座支撑板) 7.HP(底座) 8.导柱 9.导套 10.保护柱 2.5.2 BE型模具各板所使用的材料 1,2,5,6,7,10使用45#钢,3,4使用SKD-11或铬钢 2.5.3 BE模具的简介 BE模又叫“V”型折弯模,它的折弯范围广,它可以折大于900小于1800的任何弯,如果可能它也可以折大于00小于1800的任何角, 而且还可以折Z型弯(如BE B型<如图>)BE折弯对垂直度的控制比较容易,也不会发生单边拉料现象,便它对折弯的平面度影响较大 ,BE模调试时模高不可下的太多,它是最容易破损的模具,为防止破损,BE模一般都有保护柱(SE)
凸模固定板机械加工工艺设计
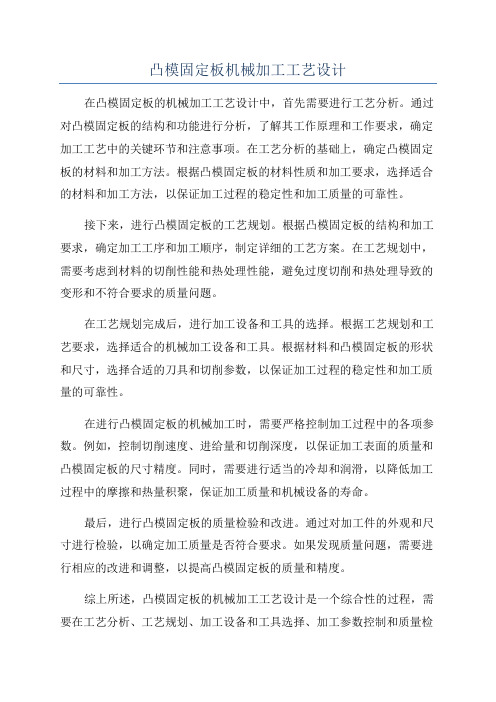
凸模固定板机械加工工艺设计在凸模固定板的机械加工工艺设计中,首先需要进行工艺分析。
通过对凸模固定板的结构和功能进行分析,了解其工作原理和工作要求,确定加工工艺中的关键环节和注意事项。
在工艺分析的基础上,确定凸模固定板的材料和加工方法。
根据凸模固定板的材料性质和加工要求,选择适合的材料和加工方法,以保证加工过程的稳定性和加工质量的可靠性。
接下来,进行凸模固定板的工艺规划。
根据凸模固定板的结构和加工要求,确定加工工序和加工顺序,制定详细的工艺方案。
在工艺规划中,需要考虑到材料的切削性能和热处理性能,避免过度切削和热处理导致的变形和不符合要求的质量问题。
在工艺规划完成后,进行加工设备和工具的选择。
根据工艺规划和工艺要求,选择适合的机械加工设备和工具。
根据材料和凸模固定板的形状和尺寸,选择合适的刀具和切削参数,以保证加工过程的稳定性和加工质量的可靠性。
在进行凸模固定板的机械加工时,需要严格控制加工过程中的各项参数。
例如,控制切削速度、进给量和切削深度,以保证加工表面的质量和凸模固定板的尺寸精度。
同时,需要进行适当的冷却和润滑,以降低加工过程中的摩擦和热量积聚,保证加工质量和机械设备的寿命。
最后,进行凸模固定板的质量检验和改进。
通过对加工件的外观和尺寸进行检验,以确定加工质量是否符合要求。
如果发现质量问题,需要进行相应的改进和调整,以提高凸模固定板的质量和精度。
综上所述,凸模固定板的机械加工工艺设计是一个综合性的过程,需要在工艺分析、工艺规划、加工设备和工具选择、加工参数控制和质量检验等方面进行全面考虑。
只有通过科学合理的工艺设计,才能保证凸模固定板的质量和精度,提高模具制造的效率和产品质量。
分析凸模压入固定板的工艺要点
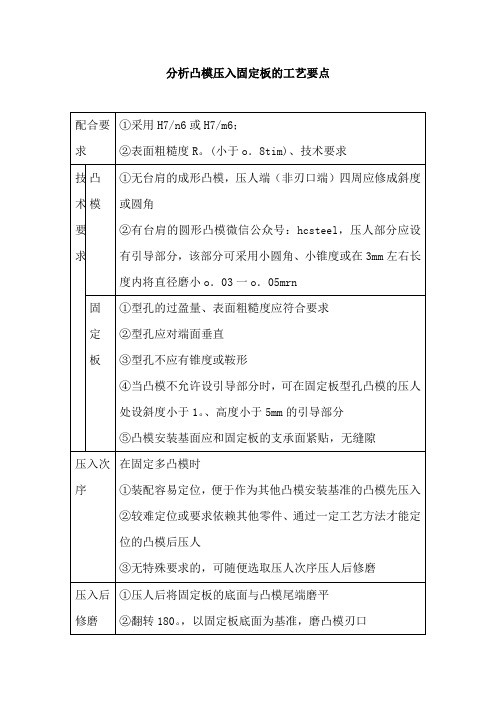
分析凸模压入固定板的工艺要点
配合要求①采用H7/n6或H7/m6;
②表面粗糙度R。
(小于o.8tim)、技术要求
技术要求凸
模
①无台肩的成形凸模,压人端(非刃口端)四周应修成斜度
或圆角
②有台肩的圆形凸模微信公众号:hcsteel,压人部分应设
有引导部分,该部分可采用小圆角、小锥度或在3mm左右长度内将直径磨小o.03一o.05mrn
固
定
板
①型孔的过盈量、表面粗糙度应符合要求
②型孔应对端面垂直
③型孔不应有锥度或鞍形
④当凸模不允许设引导部分时,可在固定板型孔凸模的压人
处设斜度小于1。
、高度小于5mm的引导部分
⑤凸模安装基面应和固定板的支承面紧贴,无缝隙
压入次序在固定多凸模时
①装配容易定位,便于作为其他凸模安装基准的凸模先压入
②较难定位或要求依赖其他零件、通过一定工艺方法才能定位的凸模后压人
③无特殊要求的,可随便选取压人次序压人后修磨
压入后修磨①压人后将固定板的底面与凸模尾端磨平
②翻转180。
,以固定板底面为基准,磨凸模刃口
注意事项①用手扳压力机或油压机压入凸模时,凸模放在压力机中心
②压人过程中,应经常检查垂直度,压人少许即要检查,压人1/3深度时再检查,保证垂直度符合要求
③压人时,严禁用锤。
落料-冲孔冲压工艺及模具设计说明书
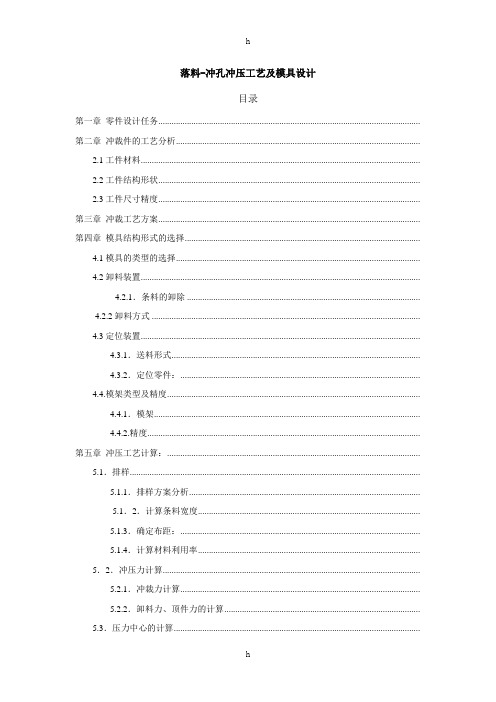
落料-冲孔冲压工艺及模具设计目录第一章零件设计任务....................................................................................................................... 第二章冲裁件的工艺分析...............................................................................................................2.1工件材料...............................................................................................................................2.2工件结构形状.......................................................................................................................2.3工件尺寸精度....................................................................................................................... 第三章冲裁工艺方案....................................................................................................................... 第四章模具结构形式的选择...........................................................................................................4.1模具的类型的选择...............................................................................................................4.2卸料装置...............................................................................................................................4.2.1.条料的卸除 ..........................................................................................................4.2.2卸料方式 ..........................................................................................................................4.3定位装置...............................................................................................................................4.3.1.送料形式.................................................................................................................4.3.2.定位零件:.............................................................................................................4.4.模架类型及精度...................................................................................................................4.4.1.模架.........................................................................................................................4.4.2.精度............................................................................................................................ 第五章冲压工艺计算:...................................................................................................................5.1.排样....................................................................................................................................5.1.1.排样方案分析.........................................................................................................5.1.2.计算条料宽度.....................................................................................................5.1.3.确定布距:.............................................................................................................5.1.4.计算材料利用率.....................................................................................................5.2.冲压力计算.....................................................................................................................5.2.1.冲裁力计算.............................................................................................................5.2.2.卸料力、顶件力的计算.........................................................................................5.3.压力中心的计算................................................................................................................5.4.模具工作部分尺寸及公差................................................................................................5.4.1.落料凸凹模尺寸.....................................................................................................5.4.2.冲孔凸凹模尺寸..................................................................................................... 第六章主要零部件设计.................................................................................................................6.1.凹模的设计........................................................................................................................6.2.凸模的设计........................................................................................................................6.2.1.冲孔凸模:................................................................................................................6.2.2.落料凸模....................................................................................................................6.2.3.凸模的校核:.........................................................................................................6.3.固定板的设计....................................................................................................................6.3.1.凸模固定板: ...............................................................................................................6.4.模架以及其他零部件的选用............................................................................................ 第7章校核模具闭合高度及压力机有关参数...............................................................................7.1 校核模具闭合高度..............................................................................................................7.2 冲压设备的选定.................................................................................................................. 第8章设计并绘制模具总装图及选取标准件............................................................................... 第9章结论..................................................................................................................................... 第10章参考资料……………………………………………………………………………第一章零件设计任务材料为ST12,材料厚度为2mm,大批生产。
冲模 球锁紧凸模固定板 第1部分:A型和B型 轻载长方形和正方形-最新国标

冲模球锁紧凸模固定板第1部分:A型和B型轻载长方形和正方形1 范围本文件规定了A型(长方形)和B型(正方形)球锁紧凸模固定板及其垫板的尺寸和公差,单位为毫米。
该类型固定板及其垫板主要用在钢板冲孔过程中,对符合ISO 10071-1规定的球锁紧凸模起固定作用。
本文件还给出了材料选用指导,并规定了符合本文件要求的球锁紧凸模固定板的硬度和标记。
2 规范性引用文件下列文件中的内容通过文中的规范性引用而构成本文件必不可少的条款。
其中,注日期的引用文件,仅该日期对应的版本适用于本文件;不注日期的引用文件,其最新版本(包括所有的修改单)适用于本文件。
ISO 273:1979 紧固件螺栓和螺钉用通孔ISO 4762:2004 内六角圆柱头螺钉ISO 8735:1997 内螺纹圆柱销淬硬钢和马氏体不锈钢ISO 10071-1 冲模球锁紧凸模第1部分:轻载球锁紧凸模3 术语和定义本文件没有需要界定的术语和定义。
4 尺寸一般公差所有尺寸的未注公差值为± 0.25 mm。
A型球锁紧凸模固定板(长方形)长方形球锁紧凸模固定板(A型)的尺寸应符合图1和表1的要求。
标引序号说明: 1——尺寸单位为毫米表面粗糙度单位为微米垫板。
a 15°角和22 mm 尺寸的公差由制造者确定。
b排气槽尺寸 2 mm × 2 mm 。
图1 A 型球锁紧凸模固定板(长方形)表1 A型球锁紧凸模固定板(长方形)尺寸单位为毫米B型球锁紧凸模固定板(正方形)正方形球锁紧凸模固定板(B型)的尺寸应符合图2和表2的要求。
标引序号说明:1——尺寸单位为毫米表面粗糙度单位为微米垫板。
a15°角和22 mm尺寸的公差由制造者确定。
b排气槽尺寸 2 mm × 2 mm。
图2 B型球锁紧凸模固定板(正方形)表2 B型球锁紧凸模固定板(正方形)尺寸单位为毫米5 材料及硬度材料由制造者选定。
球锁紧凸模固定板的硬度应为43 HRC~56 HRC,垫板硬度应为50 HRC~60 HRC。
凸模固定板的作用
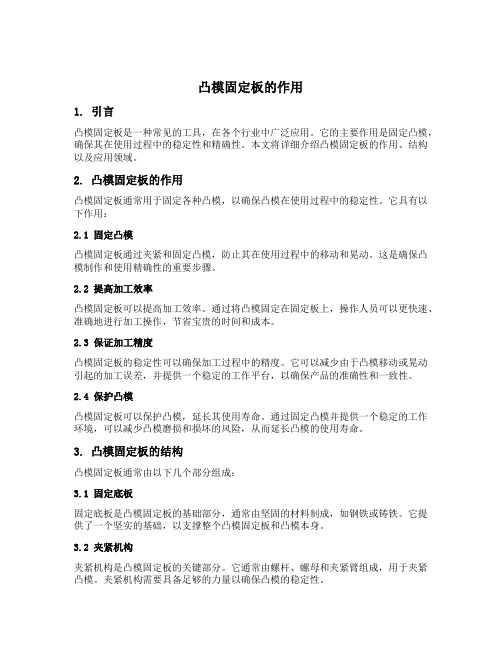
凸模固定板的作用1. 引言凸模固定板是一种常见的工具,在各个行业中广泛应用。
它的主要作用是固定凸模,确保其在使用过程中的稳定性和精确性。
本文将详细介绍凸模固定板的作用、结构以及应用领域。
2. 凸模固定板的作用凸模固定板通常用于固定各种凸模,以确保凸模在使用过程中的稳定性。
它具有以下作用:2.1 固定凸模凸模固定板通过夹紧和固定凸模,防止其在使用过程中的移动和晃动。
这是确保凸模制作和使用精确性的重要步骤。
2.2 提高加工效率凸模固定板可以提高加工效率。
通过将凸模固定在固定板上,操作人员可以更快速、准确地进行加工操作,节省宝贵的时间和成本。
2.3 保证加工精度凸模固定板的稳定性可以确保加工过程中的精度。
它可以减少由于凸模移动或晃动引起的加工误差,并提供一个稳定的工作平台,以确保产品的准确性和一致性。
2.4 保护凸模凸模固定板可以保护凸模,延长其使用寿命。
通过固定凸模并提供一个稳定的工作环境,可以减少凸模磨损和损坏的风险,从而延长凸模的使用寿命。
3. 凸模固定板的结构凸模固定板通常由以下几个部分组成:3.1 固定底板固定底板是凸模固定板的基础部分,通常由坚固的材料制成,如钢铁或铸铁。
它提供了一个坚实的基础,以支撑整个凸模固定板和凸模本身。
3.2 夹紧机构夹紧机构是凸模固定板的关键部分。
它通常由螺杆、螺母和夹紧臂组成,用于夹紧凸模。
夹紧机构需要具备足够的力量以确保凸模的稳定性。
3.3 可调节部件凸模固定板通常配备可调节部件,以适应不同大小和形状的凸模。
可调节部件允许操作人员根据需要调整凸模的位置和角度,以获得最佳的加工效果。
4. 凸模固定板的应用领域凸模固定板广泛应用于以下领域:4.1 金属加工凸模固定板在金属加工中发挥着重要作用。
它可以用于夹紧金属凸模,确保凸模的稳定性和精确性。
金属加工领域包括锻造、冲压和铸造等行业。
4.2 塑料加工凸模固定板也常用于塑料加工领域。
它可以固定塑料凸模,确保在注塑、挤出和压延等过程中的稳定性和精度。