7大浪费培训
精益生产培训系列7大浪费
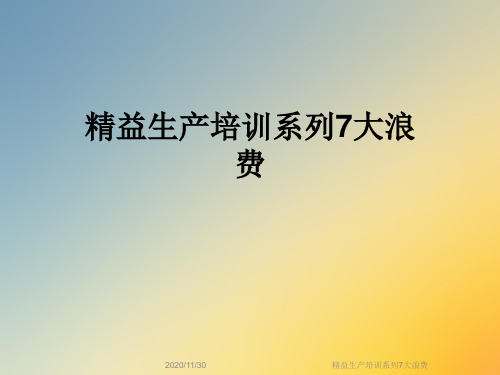
•自动化、标准作业 •防错装置 •在工程内做出品质保证
“三不政策” •一个流的生产方式 •品保制度的确立及运行 •定期的设备、模治具保养 •持续开展“5S活动”
•能回收重做的不良
•能修理的不良
•误判的不良
精益生产培训系列7大浪费
时间的浪费
表现形式:
•拖延决策,文件或信息等待决策或签字 •安排不当造成项目进程过长或停工待料 •重复沟通做没有价值的事情
精益生产培训系列7大浪费
5.等待的浪费
双手均未抓到及摸到东西的时间
材料、作业、搬运、检查之所有等待,以及宽放和监视作业
表现形式:
•自动机器操作中,人员的“闲视”等待 •作业充实度不够的等待 •设备故障、材料不良的等待 •生产安排不当的人员等待 •上下工程间未衍接好造成的工程间的等待
精益生产培训系列7大浪费
适
•物流阻塞 •库存、在制品增加
时 的 生
•产品积压造成不良发生
产
•资金回转率低
•材料、零件过早取得
•影响计划弹性及生产系统的适应能力
精益生产培训系列7大浪费
1.制造过多的浪费
制造过多是一种浪费的原因:
•只是提前用掉了费用(材料费、人工费)而已,并 无其它好处 •会把等待的浪费隐藏起来,掩盖稼动不够的问题 •会使制程间积压在制品,制程时间变长,现场工作 空间变大 •会产生搬运、堆积的浪费 •使先进先出的工作产生困难 •会造成库存空间的浪费
材料、零件、组合件等物品的停滞状 态,包括库存及在制品
表现形式:
•不良品存在库房内待修 •设备能力不足所造成的安全库存 •换线时间太长造成次大批量生产的浪费 •采购过多的物料变库存
精益生产培训系列7大浪费
安全管理7大浪费
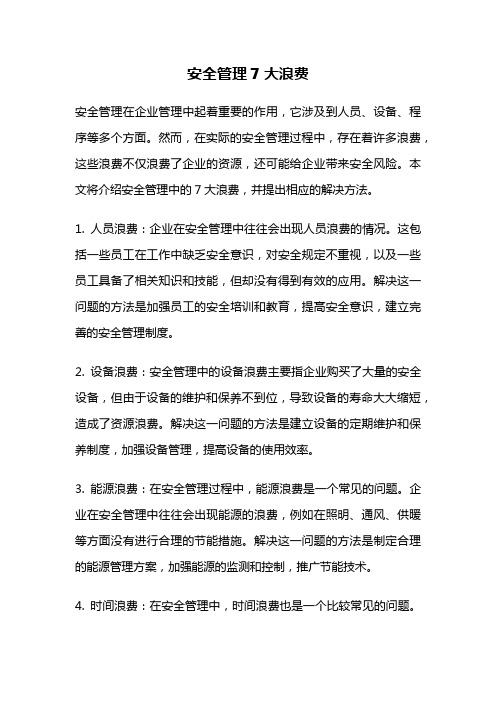
安全管理7大浪费安全管理在企业管理中起着重要的作用,它涉及到人员、设备、程序等多个方面。
然而,在实际的安全管理过程中,存在着许多浪费,这些浪费不仅浪费了企业的资源,还可能给企业带来安全风险。
本文将介绍安全管理中的7大浪费,并提出相应的解决方法。
1. 人员浪费:企业在安全管理中往往会出现人员浪费的情况。
这包括一些员工在工作中缺乏安全意识,对安全规定不重视,以及一些员工具备了相关知识和技能,但却没有得到有效的应用。
解决这一问题的方法是加强员工的安全培训和教育,提高安全意识,建立完善的安全管理制度。
2. 设备浪费:安全管理中的设备浪费主要指企业购买了大量的安全设备,但由于设备的维护和保养不到位,导致设备的寿命大大缩短,造成了资源浪费。
解决这一问题的方法是建立设备的定期维护和保养制度,加强设备管理,提高设备的使用效率。
3. 能源浪费:在安全管理过程中,能源浪费是一个常见的问题。
企业在安全管理中往往会出现能源的浪费,例如在照明、通风、供暖等方面没有进行合理的节能措施。
解决这一问题的方法是制定合理的能源管理方案,加强能源的监测和控制,推广节能技术。
4. 时间浪费:在安全管理中,时间浪费也是一个比较常见的问题。
企业在安全管理中往往会出现时间的浪费,例如由于安全管理制度不完善,导致员工在工作中花费大量的时间来处理安全问题。
解决这一问题的方法是建立完善的安全管理制度,提高安全管理的效率。
5. 材料浪费:安全管理中的材料浪费主要指企业在安全管理中大量使用和浪费资源,例如在安全培训中使用大量的纸张、打印材料等。
解决这一问题的方法是推广电子化培训,减少纸张的使用量,提高资源的利用效率。
6. 空间浪费:在安全管理中,空间浪费也是一个比较常见的问题。
企业在安全管理中往往会出现空间的浪费,例如由于安全设备的摆放不合理,导致空间的浪费。
解决这一问题的方法是合理规划空间,优化设备的布置,提高空间的利用效率。
7. 信息浪费:在安全管理中,信息浪费是一个比较严重的问题。
精益生产认识之七大浪费培训
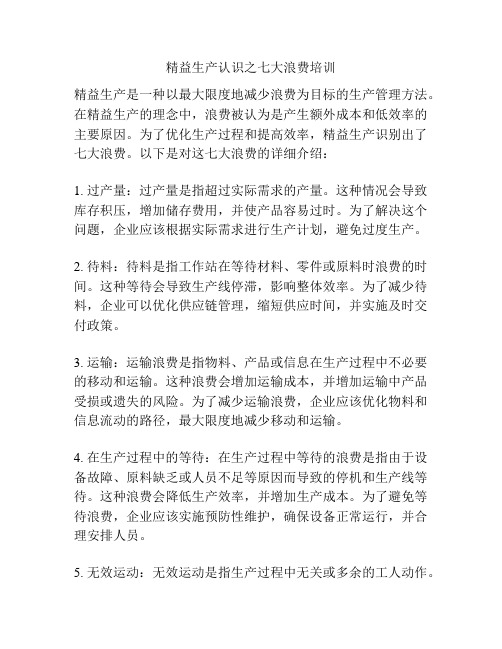
精益生产认识之七大浪费培训精益生产是一种以最大限度地减少浪费为目标的生产管理方法。
在精益生产的理念中,浪费被认为是产生额外成本和低效率的主要原因。
为了优化生产过程和提高效率,精益生产识别出了七大浪费。
以下是对这七大浪费的详细介绍:1. 过产量:过产量是指超过实际需求的产量。
这种情况会导致库存积压,增加储存费用,并使产品容易过时。
为了解决这个问题,企业应该根据实际需求进行生产计划,避免过度生产。
2. 待料:待料是指工作站在等待材料、零件或原料时浪费的时间。
这种等待会导致生产线停滞,影响整体效率。
为了减少待料,企业可以优化供应链管理,缩短供应时间,并实施及时交付政策。
3. 运输:运输浪费是指物料、产品或信息在生产过程中不必要的移动和运输。
这种浪费会增加运输成本,并增加运输中产品受损或遗失的风险。
为了减少运输浪费,企业应该优化物料和信息流动的路径,最大限度地减少移动和运输。
4. 在生产过程中的等待:在生产过程中等待的浪费是指由于设备故障、原料缺乏或人员不足等原因而导致的停机和生产线等待。
这种浪费会降低生产效率,并增加生产成本。
为了避免等待浪费,企业应该实施预防性维护,确保设备正常运行,并合理安排人员。
5. 无效运动:无效运动是指生产过程中无关或多余的工人动作。
这种浪费会造成不必要的体力消耗和生产时间延长。
为了减少无效运动浪费,企业应该优化工作站布局和工作流程,确保工人只进行必要的动作。
6. 过度加工:过度加工是指对产品进行超出要求的处理或处理步骤。
这种浪费会增加生产成本,同时也会延长生产周期。
为了避免过度加工浪费,企业应该对产品和工艺进行分析,找出不必要的加工步骤,并进行精简。
7. 库存:库存浪费是指过多或无用的库存。
这种浪费会增加资金占用和储存成本,并增加产品过时或损坏的风险。
为了减少库存浪费,企业应该实施准时生产和准时交付政策,并优化库存管理。
通过认识和理解这七大浪费,企业可以发现潜在的问题并采取相应的措施来减少浪费,提高生产效率和质量。
七大浪费培训教材

6
浪费的三种形态
浪费的三种形态
1.勉 强: 超过能力界限的
超负荷状态;
(会导致设备故障, 品质低下,人员不安全)
2.浪 费: 有能力,但未给予 充足的工作量的
未饱和状态;
(会导致设备故障, 品质低下,人员不安全)
3.不均衡: 有时超负荷有时 又不不饱和的状态。
(人员工作量不饱满, 设备稼动率低)
七大浪费培训教材
2020年5月21日星期四
课程目标
目标1 对七大浪费有初步的认识 目标2 能找出目前工作上的浪费现象 目标3 消除立即可改善浪费
2
课程内容
3
课程内容
4
什么是浪费?
? ??
5
什么是浪费?
凡是超出增加产品价值所需的绝对最少量的 物料、设备、人力、场地和时间的都是浪费。
1、不增加价值的活动﹐是浪费﹔ 2、尽管是增加价值的活动﹐所用的资源超过了“绝对
如:客户需要A种产品1000个,每个单价¥1,000元, 客户要求5月30号出货;
1、担心有生产异常情况发生,不能准时交货,所以 尽可能提前完成生产,30号出货,15号就生产完成;
2、担心由于生产时有不良品,不能按数交货,所以 派工时多派工100台;
18
七大浪費 之 过量生产
过量生产的浪费成本:
当前工作内容
有增值工作行为2 %
辅助行为38 %
60 % 没有增值工作行为
改善方向/目标
<38 %
X
完全消除
13
课程内容
14
七大浪费
1、过量生产的浪费 2、搬运的浪费 3、动作的浪费 4、等待的浪费 5、过程的浪费 6、库存的浪费 7、残次品的浪费
七大浪费培训资料ppt课件
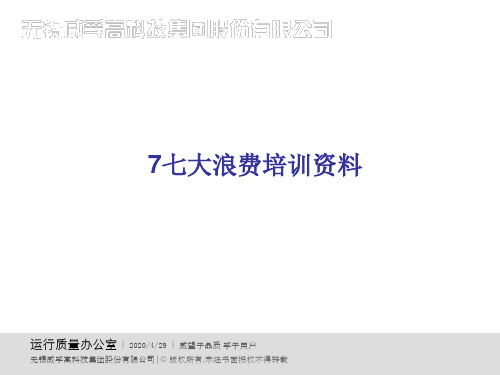
你能想到其他的例子吗?
5 过量生产(最大的浪费源)
定义:生产零组件超过需求或以超过规定的速度生产零组件;必要的 东西在必要的时候,做出必要的数量,除此之外都是浪费
结果: 造成不必要的库存,提早用掉资金,隐藏“等待的浪费"积压在制品
在车间,空间不足,走动困难;搬运,堆积的浪费;增加栈板,周转箱 (纸箱容器)的浪费;库存量增大,管理工时增加;利息负担增加 显示生产能力超过需求 例子: 由于生产方法或设备难以改变而预先生产出大批量的零组件
3 动作的浪费
定义:不能使产品增值之人员动作或机器动作 结果: 增加损坏产品的风险 增加人力需求
例子: 工作区域之间距离太长-如工作站零件盒距离。
你能想到其他的例子吗?
3 动作的浪费
12种动作的浪费:
1、两手空闲 2、举手空闲 3、作业动作停止 4、动作太大 5、左右手交换 6、步行多
7大浪费培训资料 7七大浪费培训资料
运行质量办公室 | 2020/4/29 | 威望于品质 孚于用户
无锡威孚高科技集团股份有限公司|© 版权所有,未经书面授权不得转载
课程目的(Purposes)
➢认识七大浪费的基本概念 ➢找出工作中存在的七大浪费 ➢学习消除七大浪费的方法
课程目标
课程结束后你能够(Deliverable):
7、转身角度大 8、移动中变换“状态" 9、不明技巧 10、伸背动作 11、弯腰动作 12、重复/不必要的动作
4 等待的浪费
定义:操作或事件之间的闲置时间,指断料、作业不平衡,计划 不当造成无事可作的等待
结果: 增加人工成本;工作量变动大,工作量少时,便无所事事;上游工
序发生延误,下游工序没事可做;机器闲置(待料);机器设备时 常发生故障;劳逸不均现象;材料备齐,但无标准品,上下限,工令 单;生产联机品种切换的等待 显示一条不均衡的生产线
识别与消除“七大浪费”培训

如何减少 或消除
等待浪费
识别等待的浪费,可以从以下问题考虑:
1、等待的时间是否能做其他事情? 2、看板拉动是否有效运行? 3、工序之间是否有缓冲?缓冲数量是否正确? 4、某项操作是否没有提供任何价值?
定义: 从精益生产的角度来说,搬运是一种不产生附加价值 的动作,而不产生价值的工作都属于浪费。
1、确立品质保证制度; 2、工序检查的适度化;
消除对策: 3、作业内容的再评价;
4、具备改善与自动化; 5、标准作业的彻底性。
1、必须了解同行的技术发展;
注意: 2、员工参与及持续不断的改善;
3、公司各部门对于改善项目要 紧密配合并同时开展。
识别加工的浪费,可以从以下问题考虑:
1、该工序或在制品的基本作用是什么? 2、工序设计的是否合理? 3、是否明确了解客户的要求? 4、零件的规格是否满足客户的要求?
如何消除现场七大浪费
定义:
制造过多的浪费是指先于下个工序或客户实际需求而生 产过多造成的浪费。制造过多是浪费最主要的根源!
造成原因:
1、人员过剩; 2、设备使用不合理; 3、换产时间长; 4、业务订单预测的问题; 5、生产计划与统计的问题。
劳模?
生产多于下游客户所需 , 生产快于下游客户所求。
另一方面是外部损失,由于 产品不良导致三包增多、降 价处理、订单取消和市场信 誉损失等等。
现场案例:
由于员工质量意识薄弱,对工件取拿放未做到 轻拿轻放标准,抛、摔、扔的现象较为普遍, 领导应加强对员工质量意识培训,加大对现场 巡视力度,杜绝类似情况发生。
产生原因
针对产生不良的原因,我们采取以下措施:
怎样消除 学会辨识 浪费?
七大浪费培训资料

非制造类型 文件须靠人力传送 实体文件会签传阅数个部门或人员 办公室动线规划不当或业务相关单位距离太远 寄卖在外的备用设备品 超过一个月或两星期需求的办公室文具用品(A4纸、笔、卫生纸、咖啡
动作浪费 等待浪费 过量生产
加工浪费 重工浪费
工作区域之间距离太长, 如工作站零件盒距离
操作人员等待系统运行完毕 显示一条不均衡的生产线 待料停工 良率过低导致投料增加 产能高于需求 由于生産方法或设备难以改变而预先生産出大
12种动作的浪费: 两手空闲 举手空闲 作业动作停止 动作太大 左右手交换 步行多
7、转身角度大 8、移动中变换“状态" 9、不明技巧 10、伸背动作 11、弯腰动作
12、重复/不必要的动作
等待的浪费
• 定义:操作或事件之间的闲置时间,指断料、作业不平衡,计划不当造成无事可作的等待 • 结果: • 增加人工成本;工作量变动大,工作量少时,便无所事事;上游工序发生延误,下游工序没事可做;
的都是浪费
要点 5
对浪费作业的反问(5 Whys) 对每个浪费作业反覆问5 个 Whys,发
现真正的浪费(真因root cause)
消除浪费:原因与对策
搬运的浪费
可能原因
生产线配置不当 未均衡化生产 坐姿作业 设立了固定的半成品放置 区 生产计划安排不当
对策
注意事项
U型设备配置
工作预置的废除
一个流生产方式
快速换线换模
使先进先出的工作产生困难
少人化的作业方式
会造成库存空间的浪费
均衡化生产
注意事项
七大浪费培训

安
全 地
物美价廉的产品
完
成
5
二
浪费的定义
浪费是指不增加附加价值,使成本增加的一系列活动. 对于JIT来讲,凡是超出增加产品价值所绝对必须的最 少量的物料、设备、人力、场地和时间的部分都是浪费.
1、不增加价值的活 动,是浪费
这里有 两层含义
2、尽管是增加价 值的活动﹐但所用 的资源超过了绝对 最少的界限﹐也是 浪费
19
三
浪费的种类
7、返工的浪费
定义:对产品进行检查,返工等补救措施
1表现形式:
•额外的时间和人工进行检查,返工 等工作
•由此而引起的无法准时交货
•企业的运作是补救式的,而非预防 式的救火队方式的运作
2产生的原因: •生产能力不稳定 •过度依靠人力来发现错误 •员工缺乏培训
3改善着眼点:
• 产品制造的质量需通过工序本身 来自我保证
三
3动作的浪费的改善着眼点:
浪费的种类
动作经济的八个基本原则
☆ 双手并用——两手同时使用 ☆ 伸手可及——动作距离最短 ☆ 容易取放——动作轻松、容易 ☆ 利用夹具——动作单元力最少 ☆ 重心不变——不做弯腰动作 ☆ 方向不变——不转身进行操作 ☆ 位置不变——不移动作业 ☆ 借用重力——使物体从高处自
七大浪费培训
1
目录
一 消除浪费的目的
二
浪费的定义
三
浪费的种类
四
消除浪费的步骤
2
一
消除浪费的目的
1、
① 售价=成本+利润 ……需求>供给 …… 成本主义
实 施
② 利润=售价-成本 ……需求<供给 …… 成本递减
成
本
递
消除七大浪费培训资料

消除七大浪费培训资料在企业的生产与运营过程中,往往存在着各种形式的浪费,这些浪费不仅增加了成本,降低了效率,还影响了产品质量和企业的竞争力。
为了实现精益生产,提高企业的效益,我们有必要深入了解并消除“七大浪费”。
一、什么是七大浪费1、过量生产的浪费过量生产是指生产出比需求更多的产品,导致库存积压。
这不仅占用了资金和空间,还增加了管理成本和质量风险。
例如,某工厂为了提高设备利用率,不顾市场需求,大量生产某种产品,结果造成库存积压,产品滞销。
2、等待的浪费等待的浪费包括人员等待、设备等待、物料等待等。
比如,在生产线上,前一道工序未完成,导致后一道工序的工人和设备处于等待状态;或者设备故障维修时,整个生产线停滞。
3、运输的浪费运输的浪费是指不必要的物料搬运和产品运输。
例如,工厂布局不合理,导致物料在车间内频繁搬运;或者为了将产品从一个仓库转移到另一个仓库,进行了不必要的运输。
4、过度加工的浪费过度加工是指对产品进行超出客户需求或标准的加工,增加了生产成本但并未带来价值的提升。
比如,为产品增加一些不必要的装饰或功能,导致加工时间和成本增加。
5、库存的浪费库存不仅包括成品库存,还包括原材料库存、在制品库存等。
大量库存会掩盖生产过程中的问题,如质量缺陷、设备故障等,同时也增加了资金占用和库存管理成本。
6、动作的浪费动作的浪费是指员工在工作中不必要的动作,如弯腰、转身、寻找工具等。
这些动作不仅浪费时间和体力,还可能导致疲劳和错误。
7、不良品的浪费不良品的产生意味着原材料、人工和设备等资源的浪费。
而且,不良品还可能需要返工或报废,进一步增加了成本。
二、七大浪费产生的原因1、生产计划不合理不准确的市场预测、不合理的生产排程,导致过量生产或生产不足。
2、流程不完善生产流程存在缺陷,工序之间不协调,容易出现等待和运输的浪费。
3、设备维护不当设备故障频繁,维修时间长,影响生产效率,造成等待浪费。
4、员工培训不足员工技能水平低,操作不熟练,容易出现动作浪费和不良品浪费。
七大浪费培训

The way to lean production !
P25
一、七大浪费及实例5—不良浪费
不良的浪费
The way to lean production !
P26
一、七大浪费及实例5—不良浪费
不良浪费对企业的影响:
The way to lean production !
P27
一、七大浪费及实例5—不良浪费
如何预防不良浪费
• 加强操作技能培训
• 科学的工位自检与互检
• 设计失效模式与效应分析(DFMEA)
• 防呆防错(JIKODA POKA YOKE)
• 标准化作业
The way to lean production !
P28
一、七大浪费及实例5—不良浪费
耐压不良
平衡不良
匝间测试不良
The way to lean production !
P22
一、七大浪费及实例4—等待浪费
The way to lean production !
P23
一、七大浪费及实例4—等待浪费
The way to lean production !
P24
一、七大浪费及实例4—等待浪费
如何预防等待浪费
• 合理的物料/半成品供应 • 优化生产线平衡,标准作业 • 推行快速换模,快速转拉 • 工装、治具的合理维护保养 • 加强自检,互检,品质巡检
P7
一.七大浪费及实例---什么是浪费?
一.七大浪费及实例---什么是浪费?
一.七大浪费及实例---什么是浪费?
二、七大浪费及实例---何为七大浪费
等待前后工程和 物料配送的浪费
不产生附加价值 的人或设备动作
培训汇总PPT之消除七大浪费

?
对策:
1.制造过多的浪费 •顾客为中心的弹性生产系统
•单件流动—一个流生产线
•看板管理的贯彻
•快速换线换模
•少人化的作业方式
原因:
•人员过剩 •设备稼动过剩 •生产浪费大 •业务订单预测有误 •生产计划与统计错误
•均衡化生产
注意:
•生产速度快并不代表效率高 •设备余力并非一定是埋没成本 •生产能力过剩时,应尽量先考虑减 少作业人员,但并非辞退人员,而 是更合理、更有效率地应用人员
适
时
J的
I T
生
生 产
产
方
式
1.制造过多的浪费
制造过多是一种浪费的原因:
•只是提前用掉了费用(材料费、人工费)而已,并
无其它好处
•会把等待的浪费隐藏起来,掩盖稼动不够的问题
•会使制程间积压在制品,制程时间变长,现场工作
空间变大 •会产生搬运、堆积的浪费 •使先进先出的工作产生困难 •会造成库存空间的浪费
1.制造过多的浪费
生产的调配方案: •窗框班每班借出5人至硬包边班, 由13人生产窗框,标时30pcs/hr •前桥线抽调两人至滑道线,12hr 生产
前提:
6月份金客订单由原先5980台降到 5500台,公司的生产稼动偏低,近期 又决定6月23日~6月30日停产休假,造 成我公司库存品积压过多,生产能力 过剩。
对策:
•采用均衡化生产 •制品别配置—一个流生产 •防误措施 •自动化及设备保养加强 •实施目视管理 •加强进料控制
注意:
•自动化不要闲置人员 •供需及时化 •作管理点数削减
3.搬运的浪费
不必要的移动及把东西暂放在一旁
不必要的搬运、工作的移动、预置、改装以及长距离的搬 运流程和活性度差等
七大浪费培训心得
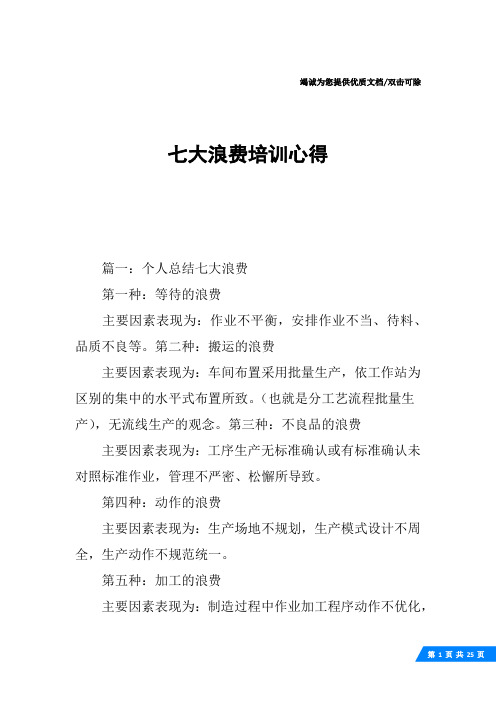
竭诚为您提供优质文档/双击可除七大浪费培训心得篇一:个人总结七大浪费第一种:等待的浪费主要因素表现为:作业不平衡,安排作业不当、待料、品质不良等。
第二种:搬运的浪费主要因素表现为:车间布置采用批量生产,依工作站为区别的集中的水平式布置所致。
(也就是分工艺流程批量生产),无流线生产的观念。
第三种:不良品的浪费主要因素表现为:工序生产无标准确认或有标准确认未对照标准作业,管理不严密、松懈所导致。
第四种:动作的浪费主要因素表现为:生产场地不规划,生产模式设计不周全,生产动作不规范统一。
第五种:加工的浪费主要因素表现为:制造过程中作业加工程序动作不优化,可省略、替代、重组或合并的未及时检查。
第六种:库存的浪费主要因素表现为:管理者为了自身的工作方便或本区域生产量化控制一次性批量下单生产,而不结合主生产计划需求流线生产所导致局部大批量库存。
库存的损害表现有:(1):产生不必要的搬运、堆积、放置、防护处理、找寻等浪费。
(2):使先进先出的作业困难。
(3):损失利息及管理费用。
(4):物品的价值会减低,变成呆滞品。
(5):占用厂房空间,造成多余的工场、仓库建设投资的浪费。
(6):没有管理的紧张感,阻碍改进。
(7):设备能力及人员需求的误判。
第七种:制造过多(早)的浪费主要因素表现为:管理者认为制造过多与过早能够提高效率或减少产能的损失和平衡车间生产力。
制造过多(早)的损害表现有:(1):提早用掉费用(材料费、人工费),不能创造利润。
(2):把“等待的浪费”隐藏起来,使管理人员漠视等待的发生和存在。
(3):自然而然地积压在制品,其结果不但会使制程的时间变长(无形的),而且会使现场工作的空间变大,机器间距离因此加大,逐渐地吞蚀利润。
(4):产生搬运,堆积的浪费,使得先进先出的作业产生困难。
对策一七种浪费之一:等待的浪费等待就是闲着没事,等着下一个动作的来临,这种浪费是无庸置疑的。
造成等待的原因通常有:作业不平衡、安排作业不当、停工待料、品质不良等。
精益系列培训——七大浪费
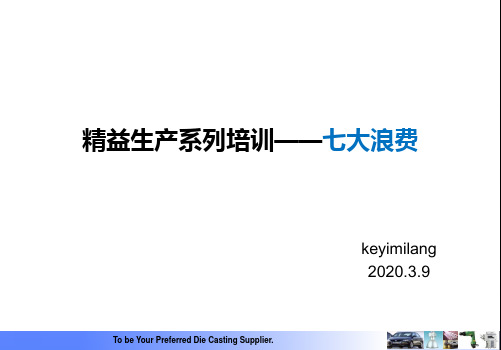
1 精益生产及精益管理简介
1.5 为什么要精益 & 为什么要现在?为什么不能延迟推行精益生产?
▪ 全球形势 ➢ 美国债台高筑, 失业率居高不下 ➢ 许多欧洲国家仍然面临财政挑战 ▪ 国内情况 ➢ 人民币升值 ➢ 转型中的经济模式 ➢ 劳动力成本的迅速增加
"精益思想" 是詹姆斯·沃马克和丹尼尔·琼斯在其具有里程碑意义的1996年《精益 思想》中创造的一句话, 邀请所有行业将精益制造扩展到车间以外, 延伸到整个供 应链中
基本前提仍然是 “用越来越少的资源做越来越多的事”。
To be Your Preferred Die Casting Supplier.
动作的过程中如果有突然改变动作方向或急剧停止必然使动作节奏发生停顿, 动作效率降低,因此安排动作尽量为直线或是圆滑曲线。
…
To be Your Preferred Die Casting Supplier.
2 七大浪费——动作浪费
2.4.3 人体动作基础知识
6. 降低等级原则
…
To be Your Preferred Die Casting Supplier.
3. 装在框子或栈板上
6. 连线作业无搬运 …
2 七大浪费——动作浪费
2.4 动作浪费的定义
生产操作动作上的不合理导致的时间的浪费如:生产作业时调整位置、翻转产 品、取放工具物料等,不必要的动作浪费。
具体分为12种动作浪费:
两手空闲的浪费 单手空闲的浪费 作业动作停顿的浪费 作业动作幅度太大的浪费 双手动作交叉的浪费 步行的浪费
To be Your Preferred Die Casting Supplier.
精益生产之七大浪费培训资料
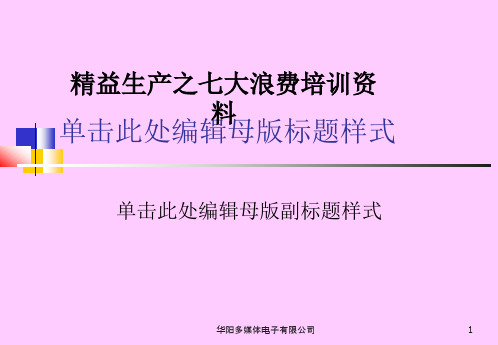
华阳多媒体电子有限公司
6
“等待浪费”现场写实 6
点击播放视频↓
华阳多媒体电子有限公司
7
七大浪费之搬运浪费(2) 7
搬运浪
搬运费时费力
费
麻木、默认:大部分人皆会认同搬运 是一种无效的动作,也有人会认为搬 运是必须的动作——“没有搬运,如何 做下一个动作?”
2)工作效率如何?
7)是否适合于该工作?
3)有解决问题的意识吗? 8)有改进意识吗?
4)责任心怎样?
9)人际关系如何?
5)还需要培训吗?
10)身体健康吗?
三、消灭浪费(1)
21
4M法
Machine
1)设备能力够吗?
6)工作准确度如何?
2)能按工艺要求加工吗? 7)设备布置正确吗?
3)是否正确润滑了?
8
“搬运”现场写实 8
是否真的一定要推、要分发?
华阳多媒体电子有限公司
9
七大浪费之不良浪费(3) 9
浪费
不良造成额外成本
常见的不良现象: ☆ 材料损失
☆ 设备折旧 ☆ 人工损失 ☆ 能源损失 ☆ 订单损失
☆ 信誉损失 ☆ 直接损失(生产、检验、修理、返工)
华阳多媒体电子有限公司
10
“不良”现场写实 10
华阳多媒体电子有限公司
12
“动作”现场写实 12
华阳多媒体电子有限公司
13ቤተ መጻሕፍቲ ባይዱ
七大浪费之加工浪费(5) 13
加工 浪费
定义说明:
过剩的加工造成浪费
常见的加工浪费: ☆ 加工余量
☆ 过高的精度 ☆ 不必要的加工
为了实现本工序(工程)的目的, 有一些加工程序是可以省略、替代 、重组或合并的;仔细检查,又会 有不少的浪费等着改善。
七大浪费培训课程
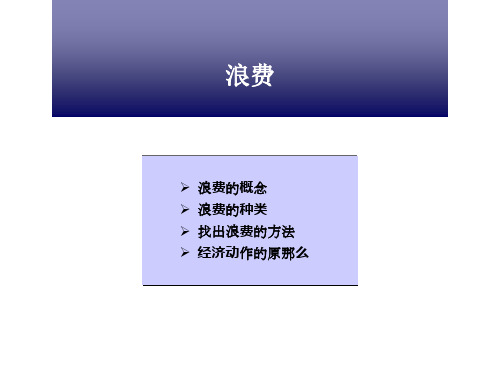
对每一个浪费作业都要重复5 Why, 发现真正的浪费.
16/22
5. 改善浪费的顺序
改善浪费的顺序
1. 静静地站在现场上 2. 发现浪费的问题点 3. 改善对象的 强的实践 4. 反省结果
彻底否认现象.
预感得到宝物(钱)的时机
在库的浪费
➢内容
纳期的长期化 去除改善的幼苗。 空间的广泛使用。 搬运,检查的发生。 运转资金的增加。
➢对策
对于库存的意识革命。 U 型设备的设置 평준화 생산 生产的正统性 广告板的 徹底性 准备交替的单一化
➢原因
认为拥有库存是当然的意识 设备,布局的不均衡。 LOT 生产。 毒瘤的发生。 先行生产。
浪费 3
搬运的浪费
所有作业是从搬运开始, 物品的移动,不必要的搬运,换着堆积, 活性度的恶化等叫做搬运的浪费.
11/22
3. 浪费的种类
2) 7大浪费
浪费 4
不良的浪费
材质不良, 加工不良(作业), 检查不良, Claim的连续发生等 返工不良.
문제 공유는 해결책의 지름길 문제 찾지 못하면 낭비를 초래하는 원인
18/22
※ 阻碍改善浪费的表现〔不可说的话〕
好好 干啊~〔包含贬义的语调〕 我不管 - 不负责任的话 不 行 - 否认性的话 你懂什么 - 无视对方的话
忙不过来 - 找借口的话
挺好的还换它干什么 - 万事太平的话
还算可以 -妥协的话
19/22
※ 经济动作的原那么
经济动作原那么是 ① 使用身体的原那么, ② 作业场布置的原那么 ③ 工具, 机器的原那么
- 1、下载文档前请自行甄别文档内容的完整性,平台不提供额外的编辑、内容补充、找答案等附加服务。
- 2、"仅部分预览"的文档,不可在线预览部分如存在完整性等问题,可反馈申请退款(可完整预览的文档不适用该条件!)。
- 3、如文档侵犯您的权益,请联系客服反馈,我们会尽快为您处理(人工客服工作时间:9:00-18:30)。
业务内容检讨
-----现在的业务都必要吗? -----现在的业务都必要吗? -----现在是按要求做的吗? -----现在是按要求做的吗? -----现在这样做有价值吗? -----现在这样做有价值吗? -----不做可以吗? -----不做可以吗?
作成:徐晶 日期:06.6.10
本课程目的
了解什么是浪费及常见的浪费现象
解析你的工作
消减工作中的浪费 提升效率/ 提升效率/效果
认识浪费
过程中的每一步骤 都可能存在浪费
输入
过程
输出
有附加值作业 无附加值作业—浪费
1.客户不会对此作业支付任何报酬, 甚至对其存在产生抱怨 2.作业内容重复
1.客户情愿为其支付报酬, 2.该作业能使产品或服务有所变化 3.该作业和任何作业不重复
业务流程检讨
----流程明确吗? ----流程明确吗? ----可简化吗? ----可简化吗? ----作业者真的清楚吗? ----作业者真的清楚吗? ----按流程做会有什么价值? ----按流程做会有什么价值?
个人业务检讨
----业务内容清楚吗? ----业务内容清楚吗? ----业务安排有计划吗? ----业务安排有计划吗?
运输和传送
指移动产品的次数或距离超过作业需要的次数或距离,如:
★同一原料或半成品存在两个以上存贮地点 ★将原料或半成品移动至不适当的存贮位置
等待
等待不会产生任何附加值,如:
★等待批准 ★等待出荷 ★等待原材料 ★等待设备维修 ★由生产线平衡效率低造成的某些工位的等待
移动
指作业人员在完成作业动作时额外的移动,如:
七大浪费
存储 过度生产 运输和传送 等待 移动 流程过长 返工
存储
当库存产品数量超过客户需求数量时即产生浪费,如:
★多于正常生产所需的原材料存储 ★过多的在制品 ★过多的完成品
过度生产
指生产数量多于客户要求,如:
★客户需求1000件,但生产1200件 ★客户需求1000件,但生产1200件 ★报告要分发20份,但实际复印25份 ★报告要分发20份,但实际复印25份
★站起身伸手抓取一个工件 ★转身拿取工具
流程过长
指对产品/ 指对产品/服务施加了客户要求之外的作业,对客户而言,这种作业是无 附加值的,如:
★电镀一个工件4H,而实际只需电镀2H即可 ★电镀一个工件4H,而实际只需电镀2H即可 ★客户要求对某种产品经过一次测试即可,而实际测试2 ★客户要求对某种产品经过一次测试即可,而实际测试2次以上 ★客户未要求线路板焊点进行手工加锡,而实际却对线路板焊点进行了手工加锡
手段
运法消减无附加值的作业或工序 DMAI阶段常用流程分析法 流程分析法消减无附加值的作业或工序 在C阶段常通过目视管理,防错法等消减各种浪费,使流程更流畅 阶段常通过目视管理 防错法等 目视管理,
你的工作中有这些浪费吗? 你的工作中有这些浪费吗?
返工
指没有“第一次就把工作做对” 指没有“第一次就把工作做对”而导致的重复作业,如:
★重新检查产品外观 ★重新进行测试 ★重新装配
关于浪费的消减
并非所有浪费(无附加值作业)均可完全消减,有时必须 进行一些无附加值的作业,以使流程能正常运作(如上下 工序间的产品移动)
目标
最大限度地合并,减少,消除无附加值的作业