降低连铸板坯内部裂纹改判率攻关实践
连铸板坯角部裂纹分析与改善措施

张建新1,王豫东2,吾塔1,于辉2,刘奉家1(1.宝钢集团八钢公司制造管理部 2.新疆八一钢铁股份有限公司)ZhANG Jian-xin 1,WANG Yu-dong 2,WU Ta1,YU Hui 2,LIU Feng-jia 1(1.M anufacturing M anagement Department,Bayi Iron&Steel Co.,Baosteel Group ,2.Xinjiang Bayi Iron&Steel Stock Co.,Ltd.Abstract:The phenomena that transversal cracks frequently occurred in continuous casing slab (CCS)corners of peri-tectic steel,hypo-peritectic steel and vanadium micro-alloyed steel is analyzed.Improving measurements are put forwardthrough classification statistic,and finally the transversal cracks on CCS corners are controlled effectively.Key words:CCS;secondary cooling;technics control连铸板坯角部裂纹分析与改善措施摘要:文章主要针对包晶钢,亚包晶含铌、钒微合金钢连铸板坯角部频繁出现横裂纹的现象进行分析。
通过分类统计,分析其成因,提出了改进措施,连铸板坯的角部横裂纹得到了有效控制。
关键词:连铸板坯;二次冷却;工艺控制中图分类号:TF777.1文献标识码:B文章编号:1672—4224(2011)02—00033—04Analysis and Improving Measurements of Transversal Crack in Continuous Casting Slab Corner联系人:张建新,男,49岁,本科,炼钢高级工程师,乌鲁木齐(830022)宝钢集团八钢公司制造管理部E-mail:zhangjx@1前言连铸坯的角横裂是中、厚板坯生产中常见的质量缺陷,角横裂的产生受连铸机设备精度、钢的高温力学性能、凝固特性等因素的影响。
马钢板坯连铸表面夹杂与裂纹的分析及预防措施
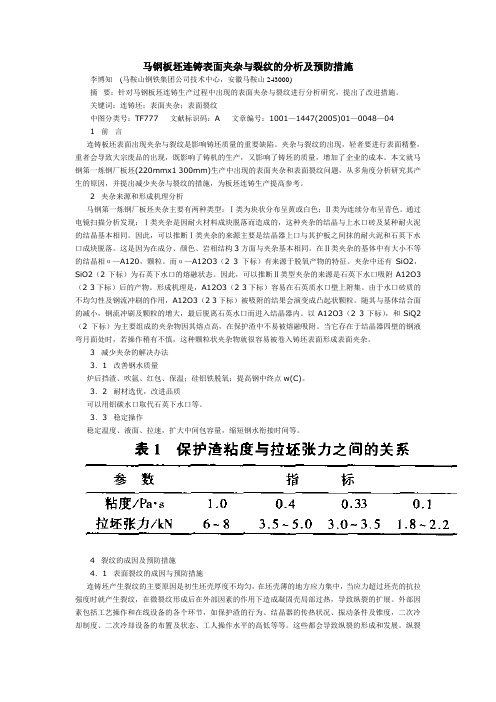
马钢板坯连铸表面夹杂与裂纹的分析及预防措施李博知(马鞍山钢铁集团公司技术中心,安徽马鞍山243000)摘要:针对马钢板坯连铸生产过程中出现的表面夹杂与裂纹进行分析研究,提出了改进措施。
关键词:连铸坯;表面夹杂;表面裂纹中图分类号:TF777 文献标识码:A 文章编号:1001—1447(2005)01—0048—041 前言连铸板坯表面出现夹杂与裂纹是影响铸坯质量的重要缺陷。
夹杂与裂纹的出现,轻者要进行表面精整,重者会导致大宗废品的出现,既影响了铸机的生产,又影响了铸坯的质量,增加了企业的成本。
本文就马钢第一炼钢厂板坯(220mmx1 300mm)生产中出现的表面夹杂和表面裂纹问题,从多角度分析研究其产生的原因,并提出减少夹杂与裂纹的措施,为板坯连铸生产提高参考。
2 夹杂来源和形成机理分析马钢第一炼钢厂板坯夹杂主要有两种类型:Ⅰ类为块状分布呈黄或白色;Ⅱ类为连续分布呈青色。
通过电镜扫描分析发现:Ⅰ类夹杂是因耐火材料成块脱落而造成的,这种夹杂的结晶与上水口砖及某种耐火泥的结晶基本相同。
因此,可以推断Ⅰ类夹杂的来源主要是结晶器上口与其护板之间抹的耐火泥和石英下水口成块脱落。
这是因为在成分、颜色、岩相结构3方面与夹杂基本相同。
在Ⅱ类夹杂的基体中有大小不等的结晶相α—A120,颗粒。
而α—A12O3(2 3下标)有来源于脱氧产物的特征。
夹杂中还有SiO2,SiO2(2下标)为石英下水口的熔融状态。
因此,可以推断Ⅱ类型夹杂的来源是石英下水口吸附A12O3(2 3下标)后的产物。
形成机理是,A12O3(2 3下标)容易在石英质水口壁上附集。
由于水口砖质的不均匀性及钢流冲刷的作用,A12O3(2 3下标)被吸附的结果会演变成凸起状颗粒。
随其与基体结合面的减小,钢流冲刷及颗粒的增大,最后脱离石英水口而进入结晶器内。
以A12O3(2 3下标),和SiQ2(2下标)为主要组成的夹杂物因其熔点高,在保护渣中不易被熔融吸附。
减少红钢连铸方坯内裂的生产实践
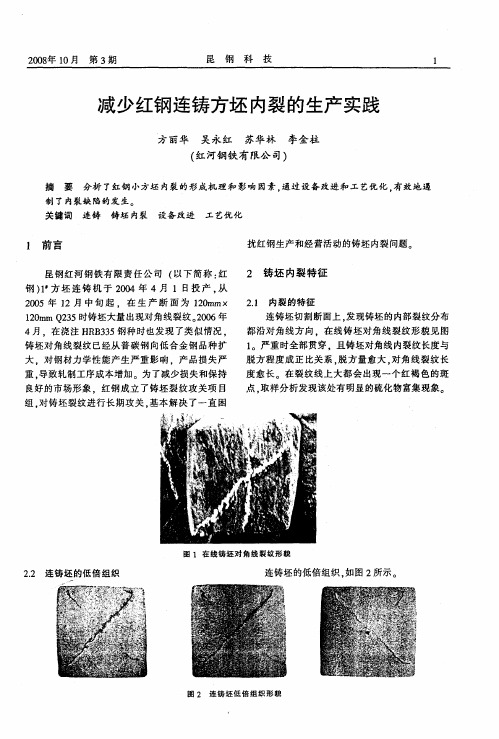
器编号挂牌使用 ,对离线检修 的结晶器铜管的倒 锥度 、 磨损 、 刮痕等参数详细记录 。 防止使用铜 管
损 坏严重 的结 晶器 。
的喷嘴 ,进一步提高了二冷水在喷嘴 出口处的压
对结 晶器过钢量进行严格控制。对 过钢量达
20年 1 0 8 0月
第 3期
昆
钢
科
技
减 少红钢连铸方坯 内裂的生产 实践
方丽华 吴永红 苏华林 李金柱
( 红河钢铁 有限公 司)
摘 要 分析 了红 钢 小方 坯 内裂 的 形成机 理 和 影 响 因素 , 过 设 备 改进 和 工 艺优 化 , 效地 遏 通 有 连铸 铸坯 内裂 设 备改进 工 艺优 化
题。 对二冷 I 段重新设计改造 , I 在 段相 同总长度
上缩短相邻喷嘴问的距离上 .经过理论计算将喷 嘴数 量 由原 来 的 9只增 加为 l 4只.喷嘴 间距 从 原
来的2 0 m缩小至 10 m 4r a 4r .改造前后的二冷 I a 段
见 图 3 。
关工序逐步开始实施改进。 31 连铸机 设备状 况的影 响及 改进 .
减少各种拉坯阻力和摩擦力, 消除和减弱拉坯 3 铸坯 内裂影响 因素及设备 改进 和工艺措 效。
施
红钢 l方坯连铸机投产时间不是太长.由于 ・ 操作和检修人员经验不足, 对新设备适应性不强 。 对设备的检修维护质量不高 .铸机设备状况越来 越差. 各类生产事故和设备事故较多 , 致使设备条 件无法满足正常的生产工艺要求 。 另外 . 连铸工艺 参数调整频繁 .最佳的连铸生产工艺参数难以确 定 .也使铸坯内裂在较长时间内没有得到彻底根 除。经过一段时间的观察和分析 . 结合理论与生产 的实际情况. 基本上掌握铸坯内裂的发生规律. 相
连铸方坯中心裂纹成因分析及控制方法

连铸方坯中心裂纹成因分析及控制方法IMB standardization office【IMB 5AB- IMBK 08- IMB 2C】一钢厂4#连铸机中心裂纹的研究攻关摘要:对一钢厂4#连铸机方坯中心裂纹的成因进行了研究,分析了钢水过热度、二次冷却强度、拉速等对铸坯中心裂纹的影响,根据分析所得的结论,采取了合理的工艺措施并进行了适当的技术改造,使中心裂纹发生率降低到%以下。
关镇词:连铸机方坯中心裂纹1.前言韶钢一炼钢厂4#连铸机投产于1997年,该机为R6m,3机3流全弧形连铸机铸坯断面为160 mmX 160 mm,结晶器长850 mm,二冷段采用单管式表面喷淋冷却方式,火焰切割,中间包采用塞棒控制或采用长寿包定径水口浇铸。
敞开式浇注,生产钢种主要为Q235、Q215、HRB335.该连铸机投产以来生产的160 mm ×160 mm铸坯一直存在的中心裂纹缺陷。
随着韶钢的发展,高线厂将替代三轧四轧制,高线在轧制时出现冲钢事故,严重影响生产的顺行。
为此对我厂生产的铸坯提出了较高的的质量要求。
2008年由于中心裂纹挑废的占坯产量的5%。
,严重影响了一钢厂企业形象和经济效益。
为解决这一问题,一炼钢厂于月成立了攻关组。
目标是要把挑废率降到%。
我们结合了当前的生产形式和现场实际进行了公关,并取得了预期效果。
2. 中心裂纹的形态及对轧制产品的影响中心裂纹的形态﹙图-1 ﹚4#连铸机铸坯中心裂纹在断面上是呈不连续的岛状(点状)分布(如图-1),有时有两到三个点。
点之间的连线往往是线状的肉眼可见的中心线裂纹,严重时则沿整个铸坯长度方向连续分布并贯通,并伴随着中心偏析疏松。
单个点直径在5—15mm之间,裂纹长20^50mm在铸坯处于发红状态时中心裂纹不易察觉,铸坯冷却至室温时则清晰可辨,给在线控制带来很大困难。
2. 2对轧制产品的影响线材厂对中心裂纹铸坯进行的轧制表明,轧制过程轧成品裂纹不能焊合,经常出现断裂冲钢。
连铸板坯中心裂纹原因分析及对策刘
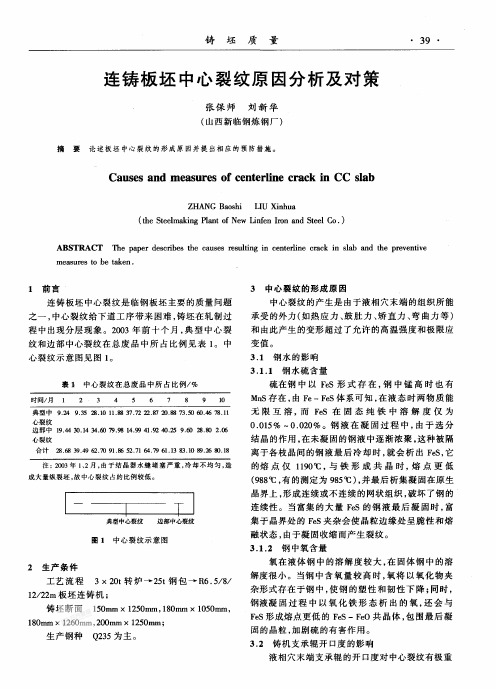
合计
8阴94 2 . 3 . 成. 9 . 5 . 砚. 6 . 8. 即. 即. 9 0 71 肠2 7 1 为1 13 1 3 0 笼 8 1
注: 的3 12 由于结晶器水缝堵塞严重, 2 年 、 月, 冷却不均匀 , 造
成大量纵裂坯 , 故中心裂纹 占的比例较低。
的熔点仅 n ℃, 0 9 与铁形成共 晶时, 点更低 熔 ( 8 有的测定为9 ℃)并最后析集凝固在原生 9 ℃, 8 5 8 ,
五个辊, 其中 3 号辊为传动辊, 其余为自由辊, 外弧
五个辊安装在同一底座上 , 内弧 12 4 5号辊安装 、 、、 在同一个盖上 , 上盖和底座之间用定位块调整内、 外 弧支承辊的开 口度 , 上传动辊可抬起、 压下 , 下传 上、 动辊之间没有定位块。如果传动辊压力过大, 未完 全凝固的铸坯通过传动辊时将被压薄, 出传动辊后, 由于自由辊的开口度比传动辊的大, 坯壳向外鼓胀 ,
M 存在, F 一 S S n 由 e F 体系可知, e 在液态时两物质能 无 限互 溶, FS在 固态 纯 铁 中溶 解 度 仅 为 而 e
005 00 %。 . %一 . 1 0 2 钢液在凝固过程中, 由于选分
结晶的作用, 在未凝固的钢液中逐渐浓聚, 这种被隔 离于各枝晶间的钢液最后冷却时, 就会析出 FS它 e ,
2 杨拉道 , 谢东钢 . 常规板坯连铸技术 . 2 2 . ] X (
铸 铸
坯
质 质
Hale Waihona Puke 量 重・3 ・ 9
连铸板坯中心裂纹原因分析及对策
张保师 刘新华
( 山西新临钢炼钢厂)
摘 要 论述板坯 中心裂纹 的形成原 因并提 出相应的预 防措施 。
Ca e n me s r so e triec a k i CC s b s u sa d a u e fc n i n r c n e I 8
连铸坯内部裂纹产生原因及解决措施
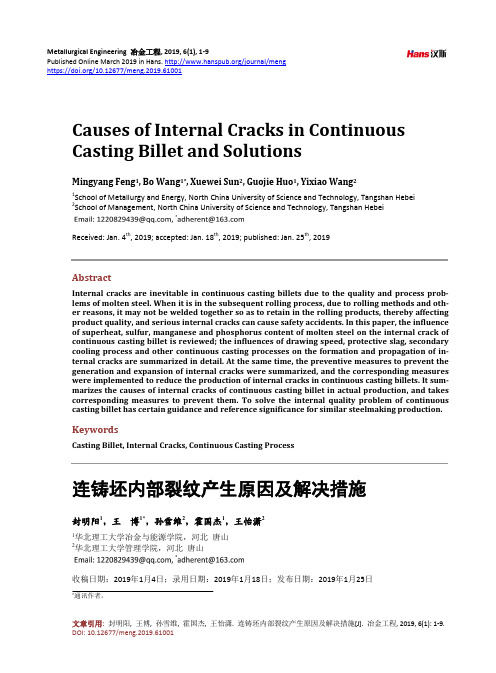
Metallurgical Engineering 冶金工程, 2019, 6(1), 1-9Published Online March 2019 in Hans. /journal/menghttps:///10.12677/meng.2019.61001Causes of Internal Cracks in ContinuousCasting Billet and SolutionsMingyang Feng1, Bo Wang1*, Xuewei Sun2, Guojie Huo1, Yixiao Wang21School of Metallurgy and Energy, North China University of Science and Technology, Tangshan Hebei2School of Management, North China University of Science and Technology, Tangshan HebeiReceived: Jan. 4th, 2019; accepted: Jan. 18th, 2019; published: Jan. 25th, 2019AbstractInternal cracks are inevitable in continuous casting billets due to the quality and process prob-lems of molten steel. When it is in the subsequent rolling process, due to rolling methods and oth-er reasons, it may not be welded together so as to retain in the rolling products, thereby affecting product quality, and serious internal cracks can cause safety accidents. In this paper, the influence of superheat, sulfur, manganese and phosphorus content of molten steel on the internal crack of continuous casting billet is reviewed; the influences of drawing speed, protective slag, secondary cooling process and other continuous casting processes on the formation and propagation of in-ternal cracks are summarized in detail. At the same time, the preventive measures to prevent the generation and expansion of internal cracks were summarized, and the corresponding measures were implemented to reduce the production of internal cracks in continuous casting billets. It sum-marizes the causes of internal cracks of continuous casting billet in actual production, and takes corresponding measures to prevent them. To solve the internal quality problem of continuous casting billet has certain guidance and reference significance for similar steelmaking production.KeywordsCasting Billet, Internal Cracks, Continuous Casting Process连铸坯内部裂纹产生原因及解决措施封明阳1,王博1*,孙雪维2,霍国杰1,王怡潇21华北理工大学冶金与能源学院,河北唐山2华北理工大学管理学院,河北唐山收稿日期:2019年1月4日;录用日期:2019年1月18日;发布日期:2019年1月25日*通讯作者。
连铸板坯中间裂纹的成因分析与改进措施

炉号
1- 05447 2- 05626 1- 05330 1- 05332 1- 10311 1- 10310 3- 10667
拉速 /m/min 1.05 1.00 1.00 0.90 0.80 0.75 0.80
表 1 板坯横截面中间裂纹情况
裂纹起始位置距内弧 表面的距离 /mm 40 45 50 55 60 65 70
在本厂生产过程中发现如下问题,使用红外测温 仪测量进入矫直点前铸坯表面温度有时小于 900 ℃, 且温度分布不均匀;原设计扇形 1、2 段二冷喷嘴选型 不合理;二冷喷嘴堵塞严重尤其外弧水嘴清理不方 便;二冷喷嘴安装不正、喷偏现象普遍;冬季时常出现 压缩空气压力低,压缩空气管道内含水结冰现象等。 以上问题都不同程度导致中间裂纹的产生。 3.5 拉速对中间裂纹的影响
图 3 显示硫对中间裂纹的影响,随着钢中硫含量
高温晶界处富集氧、硫、磷等杂质,导致晶界熔化,降
的增加,铸坯中间裂纹的级别呈明显增加趋势。经过
低了钢的高温强度和高温塑性[1]。裂纹的生成过程是
大量数据统计分析结果表明,不论采用何种工艺参
铸坯在凝固过程中受力作用(热应力、弯曲矫直力、辊
数,钢中硫含量对铸坯内部裂纹(包括中间裂纹)产生
1 545 ℃。统计某月钢水温度发现,高温钢比例达
发达;钢中气体及夹杂物也较高,铸坯收缩量增大;影
50.8%,1 560 ℃以上温度占 9.5%。
响凝固坯壳的厚度和凝固末端的位置;特别是温度过
3.4 二冷冷却对中间裂纹的影响
高时拉速较低,导致铸机轴承损坏、夹辊严重弯曲,出
铸坯在二冷区域运行过程中,冷却效果对铸坯内
严密关注铸坯质量,增加取铸坯低倍试样的频 次,发现中间裂纹及时反馈处理,批量产生及时停浇 并检查相应扇形段。强化设备管理,树立“设备精度是 保证板坯内部质量的基础”的理念,严格控制每个工 序环节,严把备件质量关,对备件辊缝、弧度严格验 收,将问题全部解决在线外,确保上线设备满足工艺 要求。出台扇形段辊缝和接弧标准,保证接弧误差≤ 0.20 mm,辊缝误差≤0.30 mm,同时控制段与段之间 辊缝值的衔接尽量一致。减少铸机“带病”作业,设备 状况不佳时对有问题的扇形段及时维修或更换。加强 铸机的检修工作,尽量做到每周有 8 h 以上的检修时 间,同时利用生产间隙,增加扇形段辊缝和弧度的检 测次数,发现问题及时调整。 4.2 控制钢水成分和过热度
板坯中心线裂纹控制生产实践
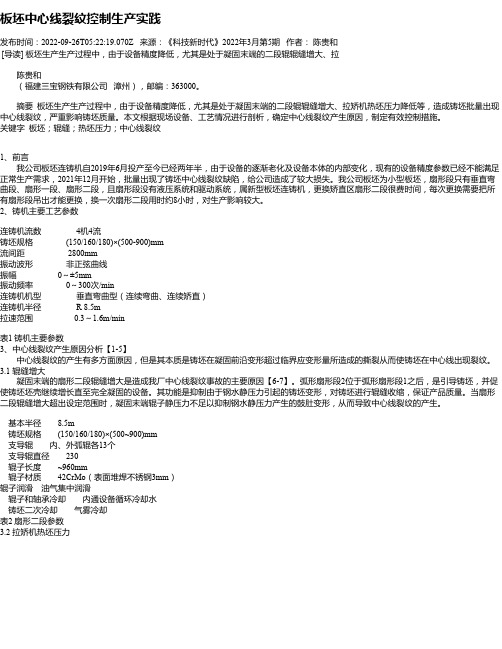
板坯中心线裂纹控制生产实践发布时间:2022-09-26T05:22:19.070Z 来源:《科技新时代》2022年3月第5期作者:陈贵和[导读] 板坯生产生产过程中,由于设备精度降低,尤其是处于凝固末端的二段辊辊缝增大、拉陈贵和(福建三宝钢铁有限公司漳州),邮编:363000。
摘要板坯生产生产过程中,由于设备精度降低,尤其是处于凝固末端的二段辊辊缝增大、拉矫机热坯压力降低等,造成铸坯批量出现中心线裂纹,严重影响铸坯质量。
本文根据现场设备、工艺情况进行剖析,确定中心线裂纹产生原因,制定有效控制措施。
关键字板坯;辊缝;热坯压力;中心线裂纹1、前言我公司板坯连铸机自2019年6月投产至今已经两年半,由于设备的逐渐老化及设备本体的内部变化,现有的设备精度参数已经不能满足正常生产需求,2021年12月开始,批量出现了铸坯中心线裂纹缺陷,给公司造成了较大损失。
我公司板坯为小型板坯,扇形段只有垂直弯曲段、扇形一段、扇形二段,且扇形段没有液压系统和驱动系统,属新型板坯连铸机,更换矫直区扇形二段很费时间,每次更换需要把所有扇形段吊出才能更换,换一次扇形二段用时约8小时,对生产影响较大。
2、铸机主要工艺参数连铸机流数 4机4流铸坯规格 (150/160/180)×(500-900)mm 流间距 2800mm 振动波形非正弦曲线振幅 0~±5mm 振动频率 0~300次/min 连铸机机型垂直弯曲型(连续弯曲、连续矫直)连铸机半径 R 8.5m 拉速范围 0.3~1.6m/min 表1 铸机主要参数3、中心线裂纹产生原因分析【1-5】中心线裂纹的产生有多方面原因,但是其本质是铸坯在凝固前沿变形超过临界应变形量所造成的撕裂从而使铸坯在中心线出现裂纹。
3.1 辊缝增大凝固末端的扇形二段辊缝增大是造成我厂中心线裂纹事故的主要原因【6-7】。
弧形扇形段2位于弧形扇形段1之后,是引导铸坯,并促使铸坯坯壳继续增长直至完全凝固的设备。
连铸板坯三角区裂纹的成因及对策
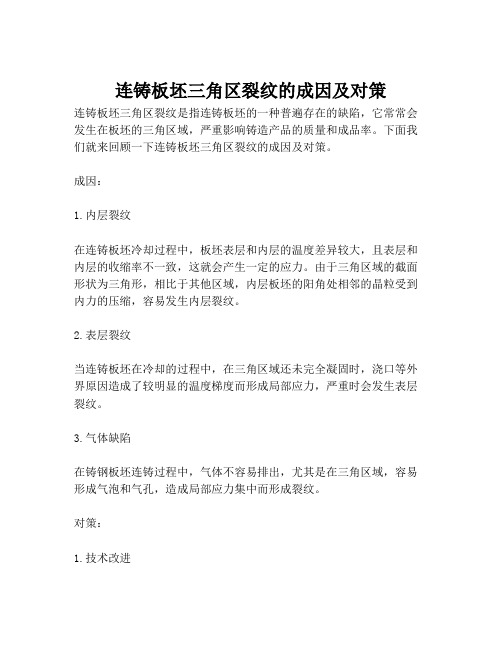
连铸板坯三角区裂纹的成因及对策连铸板坯三角区裂纹是指连铸板坯的一种普遍存在的缺陷,它常常会发生在板坯的三角区域,严重影响铸造产品的质量和成品率。
下面我们就来回顾一下连铸板坯三角区裂纹的成因及对策。
成因:1.内层裂纹在连铸板坯冷却过程中,板坯表层和内层的温度差异较大,且表层和内层的收缩率不一致,这就会产生一定的应力。
由于三角区域的截面形状为三角形,相比于其他区域,内层板坯的阳角处相邻的晶粒受到内力的压缩,容易发生内层裂纹。
2.表层裂纹当连铸板坯在冷却的过程中,在三角区域还未完全凝固时,浇口等外界原因造成了较明显的温度梯度而形成局部应力,严重时会发生表层裂纹。
3.气体缺陷在铸钢板坯连铸过程中,气体不容易排出,尤其是在三角区域,容易形成气泡和气孔,造成局部应力集中而形成裂纹。
对策:1.技术改进对于连铸板坯三角区裂纹的发生,可以先从技术的角度入手,采取改进措施,降低板坯的质量,减少三角区裂纹的发生。
例如:优化冷却过程,改善铸坯结构,以及适当的添加合金等。
2.材料改进连铸板坯三角区裂纹的发生与材料有一定的关系,因此在材料方面也可以采取一些措施,降低三角区裂纹的发生率。
例如,使用具有更好强度和韧性的材料,加入细小的晶粒改进剂等。
3.操作规范操作规范和操作技能的提高也是降低连铸板坯三角区裂纹发生率的关键。
对于操作者,需要按照正确的操作流程进行操作,严格掌握生产技术规范,避免因操作失误而导致的铸造缺陷。
总结:综上所述,连铸板坯三角区裂纹是铸造中一个比较复杂的问题,其造成的缺陷不仅影响产品质量,也影响生产效率。
因此,我们需要重视连铸板坯三角区裂纹缺陷的控制,采取一系列的改善措施,从技术,材料和操作规范等角度去降低三角区裂纹的发生率。
连铸坯裂纹的原因分析和改进措施
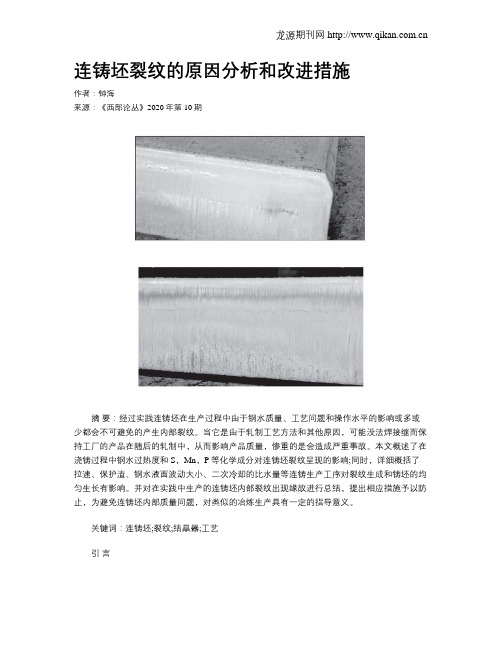
连铸坯裂纹的原因分析和改进措施作者:钟海来源:《西部论丛》2020年第10期摘要:经过实践连铸坯在生产过程中由于钢水质量、工艺问题和操作水平的影响或多或少都会不可避免的产生内部裂纹。
当它是由于轧制工艺方法和其他原因,可能没法焊接继而保持工厂的产品在随后的轧制中,从而影响产品质量,惨重的是会造成严重事故。
本文概述了在浇铸过程中钢水过热度和S,Mn,P等化学成分对连铸坯裂纹呈现的影响;同时,详细概括了拉速、保护渣、钢水液面波动大小、二次冷却的比水量等连铸生产工序对裂纹生成和铸坯的均匀生长有影响。
并对在实践中生产的连铸坯内部裂纹出现缘故进行总结,提出相应措施予以防止,为避免连铸坯内部质量问题,对类似的冶炼生产具有一定的指导意义。
关键词:连铸坯;裂纹;结晶器;工艺引言在炼钢过程中,一定要提升钢水的纯净度,把钢中的S、P成分降低,因此给连铸生产创造良好的条件,连铸生产的铸坯也因一些工艺问题而产生各种缺陷。
在铸坯的各式各样缺陷中,钢中的裂纹是严重的缺陷之一,大约占各类缺陷的50%之多。
这种裂纹会遗留在后面的轧制工艺与后续的产品中,继而很大程度上影响现实情况作业的工作效率。
加强工艺技术监督和加强操作本身的技术规范,这样能避免很多铸坯裂纹和夹杂的产生。
简述连铸坯的裂纹的种类第一个是板坯中心裂纹,铸坯中心液相穴在凝固点周边收缩,铸坯分层或鼓肚造成的,同时表示为中心偏析线。
中心裂纹出现在板坯断面的中心位置,与宽面平行,在断面上可看到呈现开口状的缺陷。
中心裂纹产生的原因主要有:因结晶器的冷却不均匀,拉速波动的变化而产生不均匀的凝固坯壳;凝固末端的凝固通道的不均匀强冷;辊缝开口度对弧不准确、不合理而在凝固通道上发生了异常压力中止了钢水的补充。
钢水的质量,钢水热度过高,拉速快慢,温度不满足和辊缝开口度扩大等等都对中心裂纹有影响。
第二个是板坯中间裂纹内部裂纹产生的原因是由于板坯表面温度反复回温、辊缝开口度、棍子的对弧精度、弯曲连续矫直等在凝固界面上产生拉伸应力而产生的裂纹,并往柱状晶薄弱处不断扩展延伸到坯壳高强度所能承受的抵抗应力为止。
连铸表面裂纹产生的原因和改进的技术措施3

姓名:陈守汪班级:冶094班学号:0990142142012 年5 月14 日连铸表面裂纹产生的原因和改进的技术措施摘要:连铸坯表面裂纹的产生主要取决于: 钢成分对裂纹敏感性、浇铸工艺条件及连铸机设备状况。
带液芯的连铸坯在连铸机内运行过程中受到外力作用是坯壳产生裂纹的外因, 钢的高温力学行为是产生裂纹的内因, 而设备和工艺因素是产生裂纹的条件。
根据所浇钢种, 对连铸机设备的调整应符合钢水凝固收缩规律, 以坯壳不发生变形为原则。
优化工艺参数, 使其处于能够保证连铸坯不产生裂纹或不足以造成废品的允许范围内, 得到合理的铸坯凝固结构。
关键词:铸坯表面纵裂纹、铸坯表面横裂纹主要内容:铸坯裂纹是影响连铸机产量和铸坯质量的主要缺陷。
据统计, 铸坯各类缺陷中有50%为裂纹缺陷。
铸坯出现裂纹, 轻者需进行精整, 重者会导致漏钢和废品, 既影响连铸坯生产率, 又影响产品质量, 增加生产成本。
1 铸坯表面纵裂纹1. 1 板坯表面纵裂纹特征表面纵裂纹可能在板坯宽面中心区域或宽面到棱边的任一位置产生。
综合分析表明, 纵裂纹有以下特征:( 1) 产生纵裂纹的表面常伴有凹陷( depression), 纵裂纹的严重性与表面凹陷相对应。
( 2) 裂纹沿树枝晶干方向扩展。
( 3) 裂纹内发现有硅、钙、铝等元素的夹杂物。
( 4) 在裂纹周围发现有P, S, Mn 的偏析。
( 5) 裂纹边缘出现一定的脱碳层, 说明裂纹是在高温下形成扩展的。
1. 2 表面纵裂纹产生的原因板坯表面纵裂纹在连铸机内产生原因如下:( 1) 板坯横断面低倍检验表明, 纵裂纹起源于激冷层薄弱处( 约2~3mm) 。
( 2) 结晶器的模拟试验表明, 纵裂纹起源于结晶器弯月面区( 几十毫米到150mm) 周边坯壳厚度薄弱处。
这说明纵裂纹起源于结晶器的弯月面区初生凝固壳厚度的不均匀性。
坯壳受下列所述力的作用:( 1) 板坯凝固壳四周温度不均匀而产生的收缩力;( 2) 板坯收缩时由钢水静压力产生的鼓胀力;( 3) 宽度收缩时受侧面约束产生的弯曲应力。
减少板坯边直裂纹缺陷率工艺实践

连铸板坯边直裂纹是发生在板坯宽面边部与浇铸方向平行的表面裂纹,属于重大的产品质量缺陷问题,严重影响板坯的表面质量和机械加工性能。
这种边直裂纹往往是成批次出现的,严重时会导致该批次产品大量报废。
邯钢连铸生产线在生产不同规格铸坯时,曾出现板坯边直裂纹的质量问题。
经过对连铸生产过程的分析认为,板坯边直裂纹缺的产生主要与结晶器内钢液的不均匀冷却有关,致使浇铸后的坯壳出现厚薄不均和边部薄弱部位裂纹有关。
在铸坯出结晶器后,由于铸坯冷却收缩不均匀,致使铸坯直裂纹继续扩大,最终形成较为严重的裂纹缺陷。
根据板坯边部直裂纹的产生机理,采取了提高钢液洁净度,改善钢液成分和优化浇铸方式等措施,使板坯边部直裂纹缺陷得到有效控制,大大降低了铸坯裂纹率,产品质量明显改善。
本文结合邯钢连铸线生产实践,对如何减少板坯边直裂纹缺陷率进行了探讨。
1板坯边部直裂纹产生的原因分析板坯边直裂纹是严重影响连铸产品质量和产量的表面缺陷问题。
2018年,邯钢连铸生产线浇铸的板坯曾出现大量边部直裂纹的情况,严重时直接导致铸坯作废,给企业造成了较大的经济损失。
铸坯表面的质量问题绝大多数都与结晶器污染和钢液成分有关,经过分析认为导致板坯表面裂纹产生的原因主要有以下:1.1钢液成分与洁净度的影响(1)含碳量的影响钢液中碳含量对于钢液的凝固收缩有一定的影响。
当钢液中含碳量在0.08%~0.15%范围内时,钢液冷却凝固时会发生包晶反应并产生较为显著的体积收缩。
此时,由于铸坯的体积收缩,结晶器内壁与铸坯之间就会形成较大的空隙。
由于中间空隙处热量散失较慢,因而导致铸坯表面中间部位与边部冷却速度的不一致和不均匀;初生坯壳在中间与边部的厚度也不一样。
在钢液静压力、热应力等多种作用力的影响下,铸坯边部就会形成裂纹,且随着冷却过程裂纹会逐渐加剧。
根据不同含碳量的铸坯统计数据来看,含碳量在0.1%~0.13%时属于裂纹敏感区。
(2)硫含量的影响钢液中的硫会增加铸坯的热脆性。
降低连铸坯内裂的攻关措施

系列措施 。
关 键词
铸 坯 内部 裂 纹
设备
M e s r so d c d S r n n e n lCr v c a u e f Re u e t a d l t r a e i e
内部 形 成 。
达, 降低 铸坯 的 强 度 。 冷却 强 度 太 弱 , 坯坯 铸
壳 过 薄 又 易 产 生 鼓 肚 , 终 也 会 导 致 内裂 的 最
产生 。
另外在冷却 过程中 , 由于 冷 却 水 过 滤 不 好 , 会 影 响 二 冷 区铸 坯 温 度 的均 匀 性 , 的 也 钢
Ta yu r d St e Gr up)Co. d. i an I on an e l( o Lt Ya o ng H ngg ng a
Ab t a t Co s r c mb n n t h e l y st a i n i i i g wih t e r a i iu to n NO.1 S e l ki g Pl n fTI CO ,t e p p r t t e ma n a t o S h a e
比热 是 随 温 度 的 变 化 而 变 化 的 , 以 温 度 不 所 同钢 的 收 缩 量 就 不 同 , 将 导 致 在 坯 壳 上 产 这
生热应力和相变应力 。
2 12 拉 速 ..
连 铸机 的 拉 速 高 低 、 化 及 与 变
注 温 的不 匹 配 对 铸 坯 的凝 壳 厚 度 、 金 长 度 、 冶 铸 坯 内部 组 织 结 构 都 有 极 大 的影 响 并 导 致 铸
连铸小方坯中间裂纹成因分析及改进实践
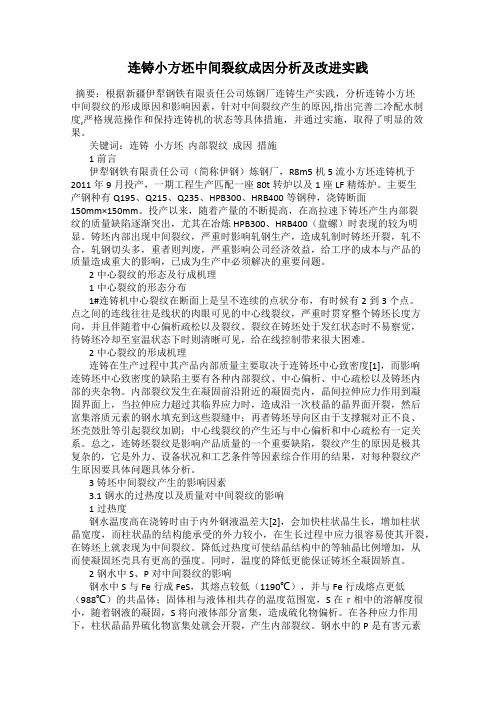
连铸过程中,在矫直点的铸坯表面温度应大于900℃。凝固坯壳的传导热流是由喷射到铸坯表面的水滴带走,这样会保持铸坯表面温度不产生回温现象。此外,由于坯壳厚度随拉坯进行逐渐增厚,传热阻力也逐渐增加,铸坯表面不会产生过大的冷却,也不会使坯壳厚度呈比例增加;相反会带来表面温度急剧下降、温度梯度增加,坯壳应力相应增加,从而造成铸坯裂纹。铸坯表面冷却不足,则铸坯表面回温过高,使凝固前沿产生热应力,产生内部裂纹,当冷却水强度过大时,铸坯经过喷水段的强冷后进入辐射冷却区,铸坯中心热量易向外传递,由于液芯温度高,坯壳温度较液芯温度低,使坯壳产生温度回升,引起坯壳膨胀,凝固前沿引起张力应变,当某一局部位置的张力应变超过该处的极限应变时,就会沿着柱状晶开裂,从而形成内裂。
4铸坯中间裂纹控制措施
4.1控制钢水过热度
控制中间包过热度,降低中包过热度。铸坯柱状晶发达时呈各相异性,裂纹容易扩展,且易出现“搭桥”现象。因此必须抑制柱状晶生长,扩大中心等轴晶区。柱状晶与等轴晶区的大小取决于浇注温度。温度高,钢水中气体、夹杂也高,铸坯收缩量大,相同冷却强度时坯壳薄、高温力学强度低。实行低过热度浇铸,过热度降低,铸坯在冷却时收缩量变小,相应产生的热应力也减小,铸坯产生中间裂纹的倾向也减小。因此本厂将过热度由原先的20-40℃降低至10-25℃,降低高过热度对铸坯中间裂纹倾向的影响。
3.2拉速的影响
确定浇铸拉速应考虑钢水过热度的影响,在合适的过热度下选择合适的拉速,有利于铸坯质量的保证和生产效率的提高。过热度小,拉速高;过热度大,拉速低。在同一过热度下,拉速越高,在结晶器内生成的坯壳越薄,不均匀性越明显;拉速越低,铸坯在冷却区所受到的冷却强度越大,越容易发生凹陷产生内裂。
3.3二冷区喷淋管不对中的影响
浅谈减少SD600连铸方坯表面裂纹的研究
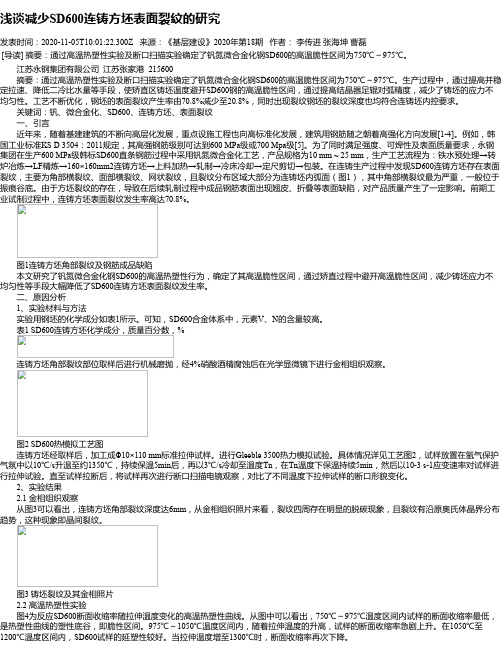
浅谈减少SD600连铸方坯表面裂纹的研究发表时间:2020-11-05T10:01:22.300Z 来源:《基层建设》2020年第18期作者:李传进张海坤曹磊[导读] 摘要:通过高温热塑性实验及断口扫描实验确定了钒氮微合金化钢SD600的高温脆性区间为750℃~975℃。
江苏永钢集团有限公司江苏张家港 215600摘要:通过高温热塑性实验及断口扫描实验确定了钒氮微合金化钢SD600的高温脆性区间为750℃~975℃。
生产过程中,通过提高并稳定拉速、降低二冷比水量等手段,使矫直区铸坯温度避开SD600钢的高温脆性区间,通过提高结晶器足辊对弧精度,减少了铸坯的应力不均匀性。
工艺不断优化,钢坯的表面裂纹产生率由70.8%减少至20.8%,同时出现裂纹钢坯的裂纹深度也均符合连铸坯内控要求。
关键词:钒、微合金化、SD600、连铸方坯、表面裂纹一、引言近年来,随着基建建筑的不断向高层化发展,重点设施工程也向高标准化发展,建筑用钢筋随之朝着高强化方向发展[1-4]。
例如,韩国工业标准KS D 3504:2011规定,其高强钢筋级别可达到600 MPa级或700 Mpa级[5]。
为了同时满足强度、可焊性及表面质量要求,永钢集团在生产600 MPa级韩标SD600直条钢筋过程中采用钒氮微合金化工艺,产品规格为10 mm ~ 25 mm,生产工艺流程为:铁水预处理→转炉冶炼→LF精炼→160×160mm2连铸方坯→上料加热→轧制→冷床冷却→定尺剪切→包装。
在连铸生产过程中发现SD600连铸方坯存在表面裂纹,主要为角部横裂纹、面部横裂纹、网状裂纹,且裂纹分布区域大部分为连铸坯内弧面(图1),其中角部横裂纹最为严重,一般位于振痕谷底。
由于方坯裂纹的存在,导致在后续轧制过程中成品钢筋表面出现翘皮、折叠等表面缺陷,对产品质量产生了一定影响。
前期工业试制过程中,连铸方坯表面裂纹发生率高达70.8%。
图1连铸方坯角部裂纹及钢筋成品缺陷本文研究了钒氮微合金化钢SD600的高温热塑性行为,确定了其高温脆性区间,通过矫直过程中避开高温脆性区间,减少铸坯应力不均匀性等手段大幅降低了SD600连铸方坯表面裂纹发生率。
连铸板坯内部裂纹的控制
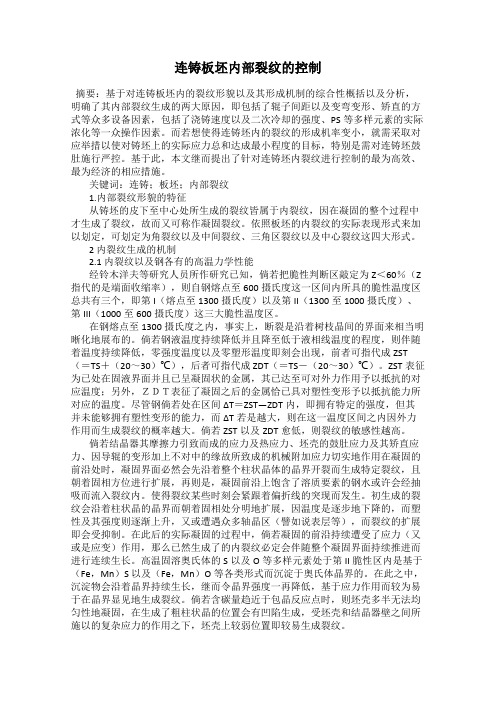
连铸板坯内部裂纹的控制摘要:基于对连铸板坯内的裂纹形貌以及其形成机制的综合性概括以及分析,明确了其内部裂纹生成的两大原因,即包括了辊子间距以及变弯变形、矫直的方式等众多设备因素,包括了浇铸速度以及二次冷却的强度、PS等多样元素的实际浓化等一众操作因素。
而若想使得连铸坯内的裂纹的形成机率变小,就需采取对应举措以使对铸坯上的实际应力总和达成最小程度的目标,特别是需对连铸坯鼓肚施行严控。
基于此,本文继而提出了针对连铸坯内裂纹进行控制的最为高效、最为经济的相应措施。
关键词:连铸;板坯;内部裂纹1.内部裂纹形貌的特征从铸坯的皮下至中心处所生成的裂纹皆属于内裂纹,因在凝固的整个过程中才生成了裂纹,故而又可称作凝固裂纹。
依照板坯的内裂纹的实际表现形式来加以划定,可划定为角裂纹以及中间裂纹、三角区裂纹以及中心裂纹这四大形式。
2 内裂纹生成的机制2.1 内裂纹以及钢各有的高温力学性能经铃木洋夫等研究人员所作研究已知,倘若把脆性判断区敲定为Z<60%(Z 指代的是端面收缩率),则自钢熔点至600摄氏度这一区间内所具的脆性温度区总共有三个,即第I(熔点至1300摄氏度)以及第II(1300至1000摄氏度)、第III(1000至600摄氏度)这三大脆性温度区。
在钢熔点至1300摄氏度之内,事实上,断裂是沿着树枝晶间的界面来相当明晰化地展布的。
倘若钢液温度持续降低并且降至低于液相线温度的程度,则伴随着温度持续降低,零强度温度以及零塑形温度即刻会出现,前者可指代成ZST (=TS+(20~30)℃),后者可指代成 ZDT(=TS-(20~30)℃)。
ZST表征为已处在固液界面并且已呈凝固状的金属,其已达至可对外力作用予以抵抗的对应温度;另外,ZDT表征了凝固之后的金属恰已具对塑性变形予以抵抗能力所对应的温度。
尽管钢倘若处在区间ΔT=ZST—ZDT内,即拥有特定的强度,但其并未能够拥有塑性变形的能力,而ΔT若是越大,则在这一温度区间之内因外力作用而生成裂纹的概率越大。
降低连铸板坯表面纵裂纹的生产实践
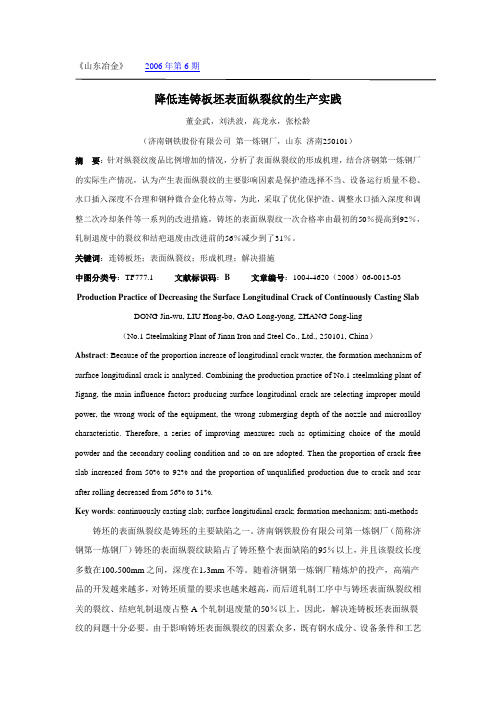
《山东冶金》2006年第6期降低连铸板坯表面纵裂纹的生产实践董金武,刘洪波,高龙永,张松龄(济南钢铁股份有限公司第一炼钢厂,山东济南250101)摘要:针对纵裂纹废品比例增加的情况,分析了表面纵裂纹的形成机理,结合济钢第一炼钢厂的实际生产情况,认为产生表面纵裂纹的主要影响因素是保护渣选择不当、设备运行质量不稳、水口插入深度不合理和钢种微合金化特点等,为此,采取了优化保护渣、调整水口插入深度和调整二次冷却条件等一系列的改进措施,铸坯的表面纵裂纹一次合格率由最初的50%提高到92%,轧制退废中的裂纹和结疤退废由改进前的56%减少到了31%。
关键词:连铸板坯;表面纵裂纹;形成机理;解决措施中图分类号:TF777.1文献标识码:B文章编号:1004-4620(2006)06-0013-03 Production Practice of Decreasing the Surface Longitudinal Crack of Continuously Casting Slab DONG Jin-wu, LIU Hong-bo, GAO Long-yong, ZHANG Song-ling(No.1 Steelmaking Plant of Jinan Iron and Steel Co., Ltd., 250101, China)Abstract: Because of the proportion increase of longitudinal crack waster, the formation mechanism of surface longitudinal crack is analyzed. Combining the production practice of No.1 steelmaking plant of Jigang, the main influence factors producing surface longitudinal crack are selecting improper mould power, the wrong work of the equipment, the wrong submerging depth of the nozzle and microalloy characteristic. Therefore, a series of improving measures such as optimizing choice of the mould powder and the secondary cooling condition and so on are adopted. Then the proportion of crack free slab increased from 50% to 92% and the proportion of unqualified production due to crack and scar after rolling decreased from 56% to 31%.Key words: continuously casting slab; surface longitudinal crack; formation mechanism; anti-methods 铸坯的表面纵裂纹是铸坯的主要缺陷之一。
连铸板坯中间裂纹控制实践
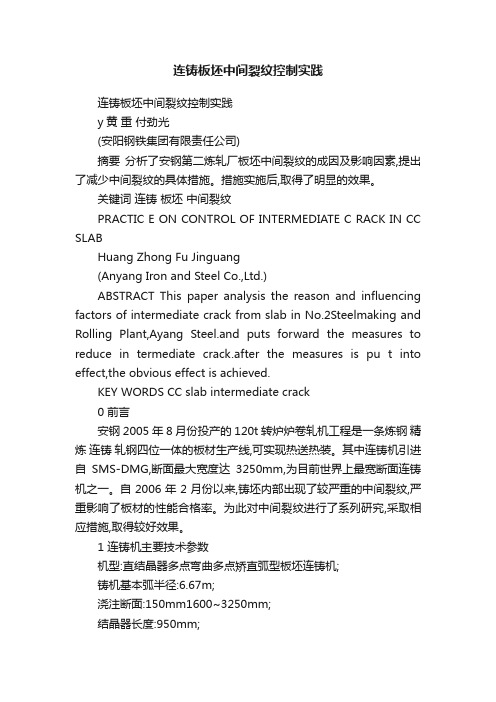
连铸板坯中间裂纹控制实践连铸板坯中间裂纹控制实践y黄重付劲光(安阳钢铁集团有限责任公司)摘要分析了安钢第二炼轧厂板坯中间裂纹的成因及影响因素,提出了减少中间裂纹的具体措施。
措施实施后,取得了明显的效果。
关键词连铸板坯中间裂纹PRACTIC E ON CONTROL OF INTERMEDIATE C RACK IN CC SLABHuang Zhong Fu Jinguang(Anyang Iron and Steel Co.,Ltd.)ABSTRACT This paper analysis the reason and influencing factors of intermediate crack from slab in No.2Steelmaking and Rolling Plant,Ayang Steel.and puts forward the measures to reduce in termediate crack.after the measures is pu t into effect,the obvious effect is achieved.KEY WORDS CC slab intermediate crack0 前言安钢2005年8月份投产的120t转炉炉卷轧机工程是一条炼钢精炼连铸轧钢四位一体的板材生产线,可实现热送热装。
其中连铸机引进自SMS-DMG,断面最大宽度达3250mm,为目前世界上最宽断面连铸机之一。
自2006年2月份以来,铸坯内部出现了较严重的中间裂纹,严重影响了板材的性能合格率。
为此对中间裂纹进行了系列研究,采取相应措施,取得较好效果。
1 连铸机主要技术参数机型:直结晶器多点弯曲多点矫直弧型板坯连铸机;铸机基本弧半径:6.67m;浇注断面:150mm1600~3250mm;结晶器长度:950mm;冶金长度:18.687m;拉速范围:0.2~2.0m min;中包容量:33t(工作) 36t(溢流)。
板坯边裂、结疤攻关总结
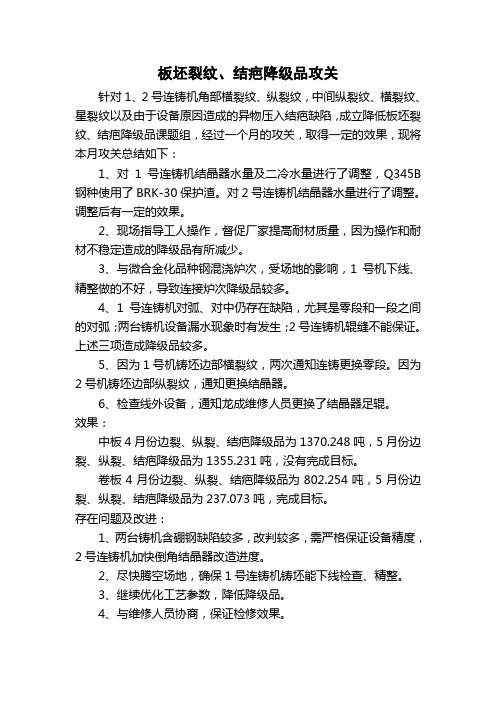
板坯裂纹、结疤降级品攻关
针对1、2号连铸机角部横裂纹、纵裂纹,中间纵裂纹、横裂纹、星裂纹以及由于设备原因造成的异物压入结疤缺陷,成立降低板坯裂纹、结疤降级品课题组,经过一个月的攻关,取得一定的效果,现将本月攻关总结如下:
1、对1号连铸机结晶器水量及二冷水量进行了调整,Q345B 钢种使用了BRK-30保护渣。
对2号连铸机结晶器水量进行了调整。
调整后有一定的效果。
2、现场指导工人操作,督促厂家提高耐材质量,因为操作和耐材不稳定造成的降级品有所减少。
3、与微合金化品种钢混浇炉次,受场地的影响,1号机下线、精整做的不好,导致连接炉次降级品较多。
4、1号连铸机对弧、对中仍存在缺陷,尤其是零段和一段之间的对弧;两台铸机设备漏水现象时有发生;2号连铸机辊缝不能保证。
上述三项造成降级品较多。
5、因为1号机铸坯边部横裂纹,两次通知连铸更换零段。
因为2号机铸坯边部纵裂纹,通知更换结晶器。
6、检查线外设备,通知龙成维修人员更换了结晶器足辊。
效果:
中板4月份边裂、纵裂、结疤降级品为1370.248吨,5月份边裂、纵裂、结疤降级品为1355.231吨,没有完成目标。
卷板4月份边裂、纵裂、结疤降级品为802.254吨,5月份边裂、纵裂、结疤降级品为237.073吨,完成目标。
存在问题及改进:
1、两台铸机含硼钢缺陷较多,改判较多,需严格保证设备精度,2号连铸机加快倒角结晶器改造进度。
2、尽快腾空场地,确保1号连铸机铸坯能下线检查、精整。
3、继续优化工艺参数,降低降级品。
4、与维修人员协商,保证检修效果。
- 1、下载文档前请自行甄别文档内容的完整性,平台不提供额外的编辑、内容补充、找答案等附加服务。
- 2、"仅部分预览"的文档,不可在线预览部分如存在完整性等问题,可反馈申请退款(可完整预览的文档不适用该条件!)。
- 3、如文档侵犯您的权益,请联系客服反馈,我们会尽快为您处理(人工客服工作时间:9:00-18:30)。
域 则无 水冷却 产生 回温鼓 肚 。通 过所 作 的 I、 Ⅲ Ⅱ、
维普资讯
第 2期
何字明等 : 降低连铸板坯 内部裂纹改判率攻关实践
区 喷嘴布 置 的 5种冷 却 方 案 的对 比, 出 了效果 最 选 佳 的方 案 V, 坯侧 面和 角部温 度得 到提 高 , 面温 铸 弧 度更均 匀 , 角区 部位弧 面与 侧面的 温差减 小 , 角 三 三 区裂纹得 以控 制 。 】区单排 布置的气 水 喷嘴改 为 Ⅲ、『 、 了双 排 布置 , 坯温 横 向差 从 4 ~ 5 o 0℃降 到 1~ 2 0 0 C, 坯壳 所受 的横 向热 应 力减小 , 有利 于减 少中间裂
实 现 , 既 保证 了 生产 组 织和 工 艺 的稳 定 又保证 了 这
钢水 温度高会 引起 铸 坯柱状 晶发达 , 中气体 、 钢 夹 杂也较 高 , 铸坯 收缩 量较大 , 同冷却 强度 时坯壳 相 更薄 , 坯壳高 温力 学强度相 对较 低 , 别是温 度过 高 特 时 拉速 较 低 , 而 导 致 铸机 轴 承 损 坏 、 辊 严 重 弯 从 夹 曲, 出现浇铸 高温铜 后 内部 裂纹 大量产 生 的现象 。 中 间包铜 水温度 与 内部 裂纹 的关 系如表 1 所示 。
维普资讯
第3卷 6
第2 期
钢
铁
V0. 6 1 3 .N0 2 .
Fe r a y b u r 200 1
2 0 0 1年 2月
I RON AND STEEL
降低连铸板 坯 内部裂纹改判率攻关 实践
何 宇明 朱 斌 胡 兵 周 仁 云 陈 文 满
有 极其严 重的影 响 。 Nhomakorabea恒速 浇铸 ” 钢 水 温 度 符 合 中 间 包 目标 温度 指 时, 非特殊情 况 拉速就 恒定在 典 型拉速 不变 。 步工 前
43 钢水 质量对 内部 裂纹 的影响 .
4 3 1 钢 水温度 ..
序则通过保证 中间包 目标温度来保证“ 恒速浇铸” 的
果 。由于铸 坯凝 固过 程中各 种外部 应 力和钢 水凝 固
时产生 的 内部 应 力作用 在液相 穴前沿 的固液交 界面 及 附近 区域上 , 当综 合应 力 和 应变 超 过 了该 钢 种的
固相 线 温度 附近 的临 界强 度 和极 限 应变 量 时 , 固液
Ta l R lto e we n t n i iu d s e lt mp r t r be 1 e a in b t e u d s l i t e e e a u e h q
4 导致 连铸板 坯 内部裂 纹形成 的 因素 41 连铸工 艺对 内部 裂纹的 影响 .
4 1 1 二次 冷却效 果 ..
硫形 成 Ⅱ类硫化物 引起 晶间脆性成 为 裂纹优 先 扩 展 的地 方 , 3 Q2 5B钢 c> 01 比 c≤ 01 . 5 . 5 裂 纹敏感 性强 。 中硫 、 对 内部 裂纹 有较 大的影 铜 碳
控 制 。19 9年 板 坯 内 部 裂 纹 改 判 率 从 19 9 97年 的 1 .6 降低 到 0 8 , 少 经 济 损 失 1 5 0 34 .1 减 5 4万 4
元。
图 1 连 铸 扳 坯 内部 裂 纹 常 见 类 型
Fi. Co g 1 mmo n e n lca k y n n itr a r c stpei
a e d s u s d i h a e . On t e a i o r c  ̄e o e u i g t e a n m e t r t f r ic s e n t e p p r h b ss f p a t f r d c n h me d n a e o
该 钢种 高温力学 强度 不 能抵抗综 合应 力和 应变 的结
联 系凡: 何字 明, 高鳜工程师 重庆( 00 4 重庆钢铁段僻有限公司七 厂技术科 408)
维普资讯
钢
铁
第 3 卷 6 表 1 Q2 5B钢 中间包温 度与内部裂纹的关 系 3一
a ditr a rc si 2 5 B se l n n en l a k nQ 3 te c
界面处 的 坯壳 已不能抵抗 应 力和应变 的作用 而产生 开裂 并 向固相 扩 展 , 由于 钢 液 已成 半凝 固态 或 固态
使钢水 无法补 充 , 裂纹得 以在铸 坯 内部 形成 。
4 2 2 液 压压力 ..
表 3 Q2 5B钢 中[ ] 内部裂纹的关系 3 c与 Tal Re t nb t en[ ]aditra cak be3 l i ew e c n enl rc s ao n
- Q2 5 B s e l 力 3 - te
44 管理 与 内部裂纹 的关 系 . 板 坯 内部裂 纹的改 判与管 理 问题密 不可分 。造 成 内部 裂 纹改 判的责任未 划 清楚 易于引起 责 任单位
t a h a a e n l y n i p r a tr l n p o u t n h tt e m n g me tp a s a m o t n oei r d ci . o KEY ORDS c n i u u a ts a W o t o s c s l b,i t r a c a k,i fu n i g f c o ,s e n nen l rc n e cn a t r t p l
( o g ig Io n t e C .,Lt . Ch n qn r n a d S e 1 o d ) AB TRAC Th e s n n n le cn a t r fi tr a r c s i o tn o s c s lb S T e ra o s a d i f n i g f co so n e n l a k n c n iu u a tsa u c
之 间的相互推诿 , 导致内部裂纹改判率越来越高。
5 防止 内部 裂纹产 生的 措施 5 1 连 铸工 艺的改 进 .
5 1 1 恒 速浇铸 ” . . 的推 广
铸机 开 口度 是 由机架 油缸 和拉辊油 缸 的压力 来 保证的, 机架 压紧缸和 拉辊 油缸 压力失控 及 阀 台、 油 缸 、 网的故障 导 致 的液 压 压力 异 常对 铸坯 质 量 都 管
二冷 水供水 的稳定 , 相穴也 不会 有太 大的变 化 , 液 有 利于减 少板 坯 内部裂纹 。 512 二冷 供水 制度 的优化 ..
2 号机 I I 、 区弧面喷嘴导致铸坯角部过冷 , 且
I、 Ⅱ区侧 面冷 却过强 , Ⅲ区在 三角 区裂纹形 成 区 而
43 2 钢水化学成分 ..
( 重庆 钢铁 股份有 限公 司)
摘 要 结合重帮七厂近 3 来降低板 坯内部裂纹 改判率攻关实践 , 年 就连 铸板坯 内部裂纹 的形成原因和影响 连铸板坯 内部裂纹 影响因素 措施
因素逐一进行 了探讨 . 系统 回顾 了攻关期 闻所做的工作 , 指出了管理 在攻 关活动中至关重 要的作用 关麓词
PRACTI CE 0F REDUCI NG AM ENDM ENT RATE
0F CoNTI NUoUS CAS S T LAB F0R NTERNAL I CRACKS
HE m i g Z Yu n HU i HU i g ZHOU n u CHEN e ma Bn Bn Re y n W n n
4 1 2 拉 坯速 度 ..
铸 机 的拉 速 高低 及 变 化速 率 对 铸 坯 的 凝壳 厚 度 、 固末 端位 置 、 凝 凝固组织 的构 成都有极 大 的影 响 并导致铸 坯高 温力 学强度过 低 。 42 连铸 设备对 内部 裂纹 的影响 . 42 1 铸 机弧度 、 口度 .. 开 从结 晶器 内钢 水 开始凝 固至凝 固末端 为 止的全 过 程, 由于 钢水静 压力 的作 用 , 坯壳 始终 存在鼓 肚趋 向。 随钢水 的逐 渐凝 固和 坯壳厚 度 的不断 增加 , 坯 铸 尺 寸 应逐渐减 小 。但 在生产实 际 中由于诸 多 因素的 影 响 , 口度 、 度 满足 不 了前 述 要求 , 坯 壳上 产 开 弧 在 生较大 的鼓肚 或挤 压力 作用而 导致 内部裂 纹产 生 。
度不一 致 。铸 坯 纵向冷 却水量 分布不 当导 致坯 温的 降低 或 回升速 度过 快 , 因钢 的 比热 容随 温 度 的变 化
而 变化 , 坯温不 同铜 的收缩 量也就 不 同 。 温的不一 坯 致 将在 坯壳上产 生热 应力 和相变 应力 。铸 坯过冷将 导 致柱状 晶发达 , 降低钢 的高温强 度 。 坯 冷却不 足 铸 坯 壳过 薄又 易产 生鼓 肚 。
1 前言
殊优质钢 不得 有 肉眼可 见三 角区裂纹 及 中心裂 纹和 偏 析 。当炉改 判及 报废 量超过 垒炉 的 13时则 垒炉 / 改判。
2
内部 裂 纹是连铸 板坯 常 见的质量缺 陷之 一 。本 文 研 究了 铸 坯 内部 裂 纹 形 成 机理 以及 相 应 防止 措
施, 并形成一套适合各 自铸机特点的预防其出现的 技术 和管理 标准 , 这对 于连铸 坯生 产企业 保证质 量 、 提高经济效益具有重要意义。重钢七厂 2 号和 4 号 板坯连铸机 自投产以来就存在内部裂纹 问题, 经过 攻关 , 中心裂纹 、 角 区裂纹 、 三 中间裂 纹 均得 到 有效
于 3 , 内眼可见的 中间裂 纹 , 根 有 中心裂纹长度>
1 0mm 或开 口度 > 0 5mm 或 同一切 割 面 累计 长 0 .
度 >10mr, 此铸坯 作报废 处理 。一般 优 质钢 仅 0 f 则 t 允许 长度 <3 且未 开 口的三 角区裂纹 存在 。 0mm 特
3 对连铸板坯 内部裂纹形成原因的认识 根 据 前 人 对 连 铸 板 坯 内部 裂 坟 形 成 机 理 的研 究“ , 合七 厂实 际 , 者 认为 : 结 笔 内部 裂 纹 的 产生 是