3-推出机构-脱模力计算
《塑料成型模具设计》(3.9)
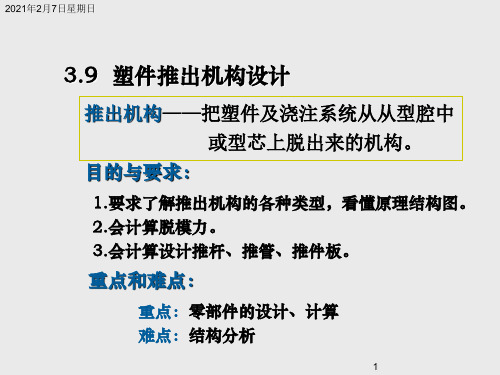
7
2021年2月7日星期日
3.9.1 概述
四、推出机构设计原则
5.尽量选在垂直壁厚的下方,可以获得较大的顶 出力。
6.每一副模具的推杆直径最好是加工成直径相同 的,使加工容易。
塑件对模具的粘附力
9
2021年2月7日星期日
3.9.1 概述
五、推出力
2. 影响推出力的因素 型芯成型部分的表面积及其形状 收缩率及摩擦因数 塑件壁厚和包紧型芯的数量 型芯表面粗糙度 成型工艺:P注、t冷
10
2021年2月7日星期日
3.9.1 概述
五、推出力
3. 推出力的估算
初始推出力 相继推出力 受力分析:
一、推杆推出机构
1.推杆的形状及尺寸
常用推杆形状: 等截面圆形推杆 阶梯形推杆 组合结构推杆
2021年2月7日星期日
17
一、推杆推出机构
1.推杆的形状及尺寸
圆柱头推杆
摘自GB/T 4169.1-2006
带肩推杆
摘自GB/T 4169.16-2006
2021年2月7日星期日
18
一、推杆推出机构
1.推杆的形状及尺寸
12
2021年2月7日星期日
3.9.2 简单推出机构
推杆推出机构 推管推出机构 推件板推出机构 推块推出机构 活动镶块及成型零件推出机构 多元件复合推出机构
13
3.9.2 简单推出机构
一、推杆推出机构
2021年2月7日星期日
14
3.9.2 简单推出机构
一、推杆推出机构
注塑模具设计结构篇--注塑模脱模系统的设计培训

29
30
31
4.推块脱模机构 对于端面平直的无孔塑件,或仅带有小孔的塑件,为保证塑件在模具打开 时能留到动模一侧,一般都把型腔安排在动模一侧,如果塑件表面不希望留下 推杆痕迹,必须采用推块机构推推塑件,如图4-86所示。对于齿轮类或一些带 有凸缘的制品,如果采用推杆推出容易变形或者是采用推板推出容易使制品粘 附模具时,也需采用推块作为推出零件。推动推块的推杆如果用螺纹连接在推 块上,则复位杆可以与推杆安装在同一块固定板上,如图4-86(a)所示。如果 推块与推杆无螺纹连接,必须采用图4-86(b)所示的复位方法。推块实际上成 为型腔底板或构成形腔底面大部分,推件运动的配合间隙既要小于溢料间隙, 又不产生过大的摩擦磨损,这就对配合面间的加工,特别是非圆形推块的配合 面提出很高要求,常常要在装配时研磨。
一次推出机构 塑件在推出零件的作用下,通过一次推出动作,就能将塑件全部脱出。 这种类型的脱模机构即为一次推出机构,也称为简单脱模机构。它是最常见 的,也是应用最广的一种脱模机构。一般有以下几种形式。
8
1.推杆脱模机构 (1) 机构组成和动作原理 推杆脱模是最典型的一次推出机构,它结构简单,制造容易且维修方便, 其机构组成和动作原理如图4-76所示。它是由推杆1、推杆固定板2、推板导套 3、推板导柱4、推杆垫板5、拉料杆6、复位杆7和限位钉8等所组成的。推杆、 拉料杆、复位杆都装在推杆固定板2上,然后用螺钉将推杆固定板和推杆垫板 连接固定成一个整体,当模具打开并达到一定距离后,注塑机上的机床推杆将 模具的推出机构挡住,使其停止随动模一起的移动,而动模部分还在继续移动 后退,于是塑件连同浇注系统一起从动模中脱出。合模时,复位杆首先与定模 分型面相接触,使推出机构与动模产生相反方向的相对移动。模具完全闭合后, 推出机构便回复到了初始的位置(由限位钉8保证最终停止位置)。
榨汁机设计

前言本设计分为两部分,一部分是对榨汁机的结构设计,一部分是对榨汁机模具设计。
所以本设计分两个阶段完成,第一阶段结构设计大概要一个月的时间;第二阶段模具设计大概要两个月的时间。
首先,根据榨汁机的结构特点进行分析计算,其中包括尺寸的计算及测量,根据各部件的形状确定部件的摆位,以次进行结构设计。
设计出来的形状力求使用,结构简单,外形美观。
同时设计的时候还要考虑加工制造的可能性。
因为滴注仪是用注塑模注塑成型的,所以在设计时应考虑设计的形状能注塑的可能性。
其次,根据设计出来的形状,对其进行模具设计,在进行模具设计时,根据塑件的形状并结合手册循序渐进的进行模具设计。
这次模具设计是对以前所学知识的一次实践。
由于我没有实践经验所以很多东西都要依靠手册。
包括数据的选取和工艺性的确定。
模具设计包括浇注系统、冷却系统及动、定个部分的结构的设计。
在近四个月的设计中,为了更好地完成任务,多次去图书管查阅资料,上网了解塑料模具的特点及发展形式,感谢老师对我们的关怀和指导,感谢同学们的帮助。
我这次设计的完成得益于老师的悉心指导和与同学们的交流。
由于本人水平有限,缺乏实践经验,所以在设计中难免产生不足和错误,请各位老师指正。
- -I摘要本毕业设计分为两个部分,第一部分为榨汁机的结构设计;第二部分是榨汁机的模具设计。
进行结构设计要考虑塑件的形状、功能和美观性要求。
对塑件上的孔、凸台等进行尺寸计算,根据计算结果对上盖和下盖上的各个部分尺寸和形状进行布置。
使设计的结构能满足使用要求。
模具设计部分对象结构比较复杂。
应用Pro/ENGINEER2001和AUTOCAD2000进行设计,大大提高了设计的质量和效率。
本设计结合了结构设计和模具设计,在进行结构设计的时候要考虑模具设计的可能性,每一部分都不能单独进行。
关键词:结构设计;模具设计;注塑模;Pro/E。
II- -ABSTRACTThis graduation design contains two sections,the first section is configuration design of instillation instrument wireless-control mainframe and the second is about the mold design of the instillation instrument wireless-control mainframe’s bottom cover. When making design for the instillation instrument wireless-control mainframe, we should think over the shape 、the function and the artistic of the plastic parts. calculate the sizes of those holes and flanges. On the basis of the result we can lay out every parts of the upper cover and bottom cover in good size and shape. Which will fulfil quality requirements. The part of mold design is just for the instillation instrument wireless-control mainframe’s bottom cover and includes pin-point gate, lateral core-pulling and the construction is very complex. Using PRO/ENGINEER2001 and AutoCAD2000 can improve the quantity and efficiency of mold design. The design combined the configuration design and mold design. View in whole, when making configuration design we should take the mold design in our mind. No one of them can be ignored.Keywords: configuration design; mold design; injection mold;Pro/E.III- -目录前言 (I)摘要 (II)ABSTRACT .......................................................................................................... I II 第1章文献综述 (1)1.1 模具及其在材料加工工业中的重要地位 (1)1.2 国内外塑料摸具技术现状及发展趋势 (3)1.3 塑件的结构设计 (6)1.3.1 功能结构设计 (6)1.3.2 工艺结构设计 (7)1.3.3 造型结构设计 (8)1.3.4 塑件尺寸、精度及表面粗糙度 (8)1.4 Pro/ENGINEER软件的集成制造技术 (9)第2章榨汁机的结构设计 (11)2.1 塑件材料的选择 (11)2.2 pvc的性能和成型特点 (11)2.3 塑料制件的结构工艺性 (14)2.3.1 脱模斜度 (14)2.3.2 尺寸公差和精度 (15)2.3.3 表面粗糙度 (15)2.3.4 壁厚 (15)2.3.5 圆角 (16)2.3.6 孔的设计 (16)2.3.7 凸台的设计 (17)2.4 结构设计方案 (18)2.4.1 用PRO/E设计滴注仪的上盖部分 (18)2.4.2 用PRO/E设计滴注仪的下盖部分 (23)第3章榨汁机的模具设计 (24)3.1 榨汁机的选择及型腔数目的确定 (24)3.1.1 塑件的质量体积分析及Pvc的注射工艺性 (24)3.1.2 型腔数目的确定 (25)- -I3.1.3 注塑机的选择 (25)3.2 分型面的选择 (27)3.3排气系统的设计 (28)3.4 浇注系统设计 (28)3.4.1 主流道部分设计 (28)3.4.2 冷料穴设计 (29)3.4.3 分流道设计 (30)3.4.4 浇口设计 (31)3.4.5 定位圈和浇口套的选择 (33)3.5 凹模型腔侧壁厚度与底板厚度的计算 (34)3.5.1 凹模侧壁厚度的计算 (34)3.5.2 底板厚度的计算 (34)3.6 模架的选取 (35)3.6.1 定位销的选择 (37)3.7 脱模机构的设计 (37)3.7.1 脱模方案的选择 (37)3.7.2 脱模力的计算和推杆数目的选择 (38)3.7.3 推杆的稳定性计算 (39)3.8复位杆设计 (40)3.9 导柱与导套的选择 (41)3.10 推出机构的导向 (43)3.11 侧向分型与抽芯机构的设计 (44)3.11.1 侧向分型与抽芯机构的选定 (44)3.11.2 抽芯距的确定与抽芯力的计算 (45)3.11.3 滑块定位装置的设计 (45)3.12 吊环螺钉的设计 (46)3.13 温度调节系统的设计 (46)3.13.1 温度调节系统分析 (46)3.13.2 冷却面积计算 (47)3.13.3 冷却系统设计 (48)第4章模具调试 (51)4.1 模具调试 (51)4.2 注射机的选用 (52)II- -4.3 模具的安装 (52)4.4 成型工艺条件的拟定 (54)结论 (55)致谢 (56)参考文献 (57)III- -第1章文献综述1.1模具及其在材料加工工业中的重要地位人类在劳动中学会了制造工具和使用工具,人们正是利用工具创造了巨大的精神文明和物质文明,生产工具三发展和不断改进代表着人类社会的进步,而模具是人类社会发展到一定程度所产生的一种先进的生产工具,人们用它制造了成千上万种生活用品和生产用品。
3-推出机构-脱模力计算

Ft = Fb ( µ cos α − sin α ) = Ap ( µ cos α − sin α )
由上面的式子可以看影响因素脱模力的大小主要有以下几点: 由上面的式子可以看影响因素脱模力的大小主要有以下几点: 影响因素脱模力的大小主要有以下几点
(l)主要与塑件包络型芯侧面积的大小有关。型芯的侧面积越大,所需的脱 主要与塑件包络型芯侧面积的大小有关。型芯的侧面积越大, 模力也越大。 模力也越大。 与型芯的脱模斜度有关。脱模斜度越大,所需的脱模力越小。 (2)与型芯的脱模斜度有关。脱模斜度越大,所需的脱模力越小。 (3)与型芯的表面粗糙度有关。表面粗糙度值越低,型芯表面越光洁,所需 与型芯的表面粗糙度有关。表面粗糙度值越低,型芯表面越光洁, 的脱模力就越小。 的脱模力就越小。 与塑件的结构有关。塑件厚度越大、形状越复杂, (4)与塑件的结构有关。塑件厚度越大、形状越复杂,冷却凝固时所引起的 包紧力和收缩应力越大,则所需的脱模力越大。 包紧力和收缩应力越大,则所需的脱模力越大。 与注射工艺有关。 (5)与注射工艺有关。 注射压力越大,则包紧型芯的力越大,所需脱模力越大; 注射压力越大,则包紧型芯的力越大,所需脱模力越大; 脱模时模具温度越高,所需的脱模力越小; 脱模时模具温度越高,所需的脱模力越小; 塑件在模内停留时间越长,所需的脱模力越大。 塑件在模内停留时间越长,所需的脱模力越大。 与成型塑件的塑料品种有关。不同的塑料品种,由于分子的结构不一样, (6)与成型塑件的塑料品种有关。不同的塑料品种,由于分子的结构不一样, 因而它们的脱模力也不一样。 因而它们的脱模力也不一样。
Fm cos α − Ft − Fb sin α = 0
Fm = ( Fb − Ft sin α ) µ
第10讲-脱模机构设计-PPT
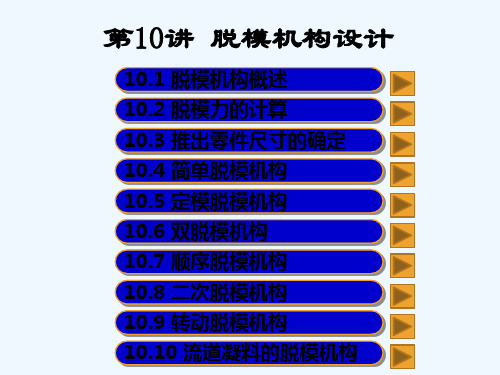
推杆的位置 1-推杆(兼复位杆)2-塑件 3-推杆 4-型芯 5-盘形推杆
10.4.1 常见脱模机构的类型
1.推杆脱模机构
2)应设在塑件强度刚度 较大处。
推杆不宜设在塑件的薄壁
处,应尽可能设在塑件厚壁、
凸缘处及筋与筋或壁与筋的交
点上,以免使塑件变形损坏。
如必须设在薄壁处时,应
增大推杆截面积,以降低单位
大家有疑问的,可以询问和交流
可以互相讨论下,但要小声点
10.2 脱模力的计算
概念
(1)定义:指将塑件从型芯上脱出时所需克服的阻力。 包括:
成型收缩的包紧力; 不带通孔的壳体类塑件的大气压力; 机构运动的摩擦力; 塑件对模具的粘附力;
10.2.1 影响脱模力的因素
(2)影响脱模力的因素
型芯成型部分的表面积及其形状. 收缩率及摩擦系数. 塑件壁厚和包紧型芯的数量. 型芯表面粗糙度. 成型工艺:P注、t冷.
对于生产批量很大的制品,为提高生产率,可 采用结构比较复杂、自动化程度比较高的脱模机构。
10.1.3 推出机构的设计原则
5)推出零件应有足够的强度、刚度和硬度。 6)合模时应正确复位。并保证不与其他模具零 件相干涉。 7)脱模行程应恰当。应保证推出零件运动的初 始位置和终止位置恰当合理,以保证制品可靠脱模。
由上面的式子可以看影响因素脱模力的大小主要有以下几点:
(l)主要与塑件包络型芯侧面积的大小有关。型芯的侧面积越大,所需的脱 模力也越大。 (2)与型芯的脱模斜度有关。脱模斜度越大,所需的脱模力越小。 (3)与型芯的表面粗糙度有关。表面粗糙度值越低,型芯表面越光洁,所需 的脱模力就越小。 (4)与塑件的结构有关。塑件厚度越大、形状越复杂,冷却凝固时所引起的 包紧力和收缩应力越大,则所需的脱模力越大。 (5)与注射工艺有关。 注射压力越大,则包紧型芯的力越大,所需脱模力越大; 脱模时模具温度越高,所需的脱模力越小; 塑件在模内停留时间越长,所需的脱模力越大。 (6)与成型塑件的塑料品种有关。不同的塑料品种,由于分子的结构不一样, 因而它们的脱模力也不一样。
塑料模具选修课件:第9章 推出机构设计

第九章推出机构设计§9.1 推出结构的结构组成与分类§9.2 推出力的计算§9.3 简单推出机构§9.4 二次推出机构§9.5 定、动模双向顺序推出机构§9.6 浇注系统凝料的推出机构§9.7 带螺纹塑件的脱模–使塑件及其浇注系统凝料从模具(凸模或凹模)中脱出的机构,又称为脱模机构。
–动作方向与开启模的运动方向一致的,通常由安装在注射机上的顶杆或液压缸来完成。
–推出机构设计的合理性与可靠性直接影响到塑件的质量,因此也是注射模设计的一个重要环节。
1. 推出机构的组成(典型结构)§9.1 推出结构的结构组成与分类–推出部件:Ø推杆、拉料杆、推杆固定板、推出板–推出导向部件:Ø推杆导柱、推杆导套–复位部件:Ø复位杆–其他:Ø支承钉推杆固定板垫板支承钉推出板拉料杆推杆导柱推杆导套推杆复位杆a)合模b)塑件及系统凝料推出2. 推出机构的分类–按驱动方式分:Ø机动推出机构Ø液压推出机构Ø气动推出机构Ø手动推出机构–按推出元件的类别分:Ø推杆推出机构Ø推管推出机构Ø推板推出机构–按模具结构特征分:Ø简单推出机构Ø二级推出机构Ø定模推出机构Ø浇注系统自动切断推出机构Ø带螺纹塑件的推出机构3. 推出机构的设计要求①尽量使塑件留于动模一侧Ø塑件留于动模,推出机构简单,否则要设计定模推出机构。
②保证塑件在推出过程中不变形不损坏③推出位置尽量选在塑件内侧,保证塑件外观良好④合模时应使推出机构正确复位⑤工作可靠、运动灵活、制造和更换容易顶针压下时留下的痕迹(顶白/Visible ejector marks )由于顶出导致的强烈变形(Deformation during demolding)在下部凹陷区由于强行脱模而导致的变形§9.2 推出力(脱模力)的计算–脱模力:将塑件从型芯上脱出时所需克服的阻力–包括:Ø成型收缩的包紧力及脱模时的摩擦力Ø不带通孔的壳体类塑件的大气压力Ø机构运动的摩擦力Ø塑件对模具的粘附力l开始脱模时瞬间所要克服的阻力,称为初始脱模力,以后脱模所需的力称为相继脱模力,后者比前者小l所以计算脱模力的时候,总是计算初始脱模力。
模具抽芯机构的设计。(理论知识)
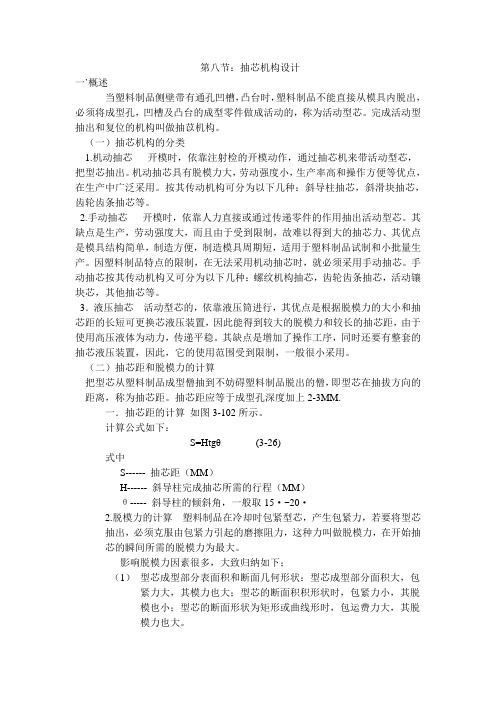
第八节:抽芯机构设计一`概述当塑料制品侧壁带有通孔凹槽,凸台时,塑料制品不能直接从模具内脱出,必须将成型孔,凹槽及凸台的成型零件做成活动的,称为活动型芯。
完成活动型抽出和复位的机构叫做抽苡机构。
(一)抽芯机构的分类1.机动抽芯开模时,依靠注射检的开模动作,通过抽芯机来带活动型芯,把型芯抽出。
机动抽芯具有脱模力大,劳动强度小,生产率高和操作方便等优点,在生产中广泛采用。
按其传动机构可分为以下几种:斜导柱抽芯,斜滑块抽芯,齿轮齿条抽芯等。
2.手动抽芯开模时,依靠人力直接或通过传递零件的作用抽出活动型芯。
其缺点是生产,劳动强度大,而且由于受到限制,故难以得到大的抽芯力、其优点是模具结构简单,制造方便,制造模具周期短,适用于塑料制品试制和小批量生产。
因塑料制品特点的限制,在无法采用机动抽芯时,就必须采用手动抽芯。
手动抽芯按其传动机构又可分为以下几种:螺纹机构抽芯,齿轮齿条抽芯,活动镶块芯,其他抽芯等。
3.液压抽芯活动型芯的,依靠液压筒进行,其优点是根据脱模力的大小和抽芯距的长短可更换芯液压装置,因此能得到较大的脱模力和较长的抽芯距,由于使用高压液体为动力,传递平稳。
其缺点是增加了操作工序,同时还要有整套的抽芯液压装置,因此,它的使用范围受到限制,一般很小采用。
(二)抽芯距和脱模力的计算把型芯从塑料制品成型僧抽到不妨碍塑料制品脱出的僧,即型芯在抽拔方向的距离,称为抽芯距。
抽芯距应等于成型孔深度加上2-3MM.一.抽芯距的计算如图3-102所示。
计算公式如下:S=H tgθ (3-26)式中S------ 抽芯距(MM)H------ 斜导柱完成抽芯所需的行程(MM)θ----- 斜导柱的倾斜角,一般取15·~20·2.脱模力的计算塑料制品在冷却时包紧型芯,产生包紧力,若要将型芯抽出,必须克服由包紧力引起的磨擦阻力,这种力叫做脱模力,在开始抽芯的瞬间所需的脱模力为最大。
影响脱模力因素很多,大致归纳如下;(1)型芯成型部分表面积和断面几何形状:型芯成型部分面积大,包紧力大,其模力也大;型芯的断面积积形状时,包紧力小,其脱模也小;型芯的断面形状为矩形或曲线形时,包运费力大,其脱模力也大。
第五节--推出机构的设计
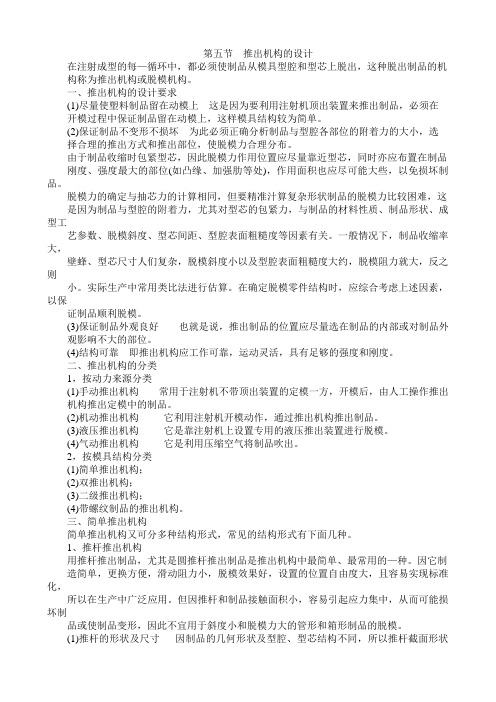
第五节推出机构的设计在注射成型的每—循环中,都必须使制品从模具型腔和型芯上脱出,这种脱出制品的机构称为推出机构或脱模机构。
一、推出机构的设计要求(1)尽量使塑料制品留在动模上这是因为要利用注射机顶出装置来推出制品,必须在开模过程中保证制品留在动模上,这样模具结构较为简单。
(2)保证制品不变形不损坏为此必须正确分析制品与型腔各部位的附着力的大小,选择合理的推出方式和推出部位,使脱模力合理分布。
由于制品收缩时包紧型芯,因此脱模力作用位置应尽量靠近型芯,同时亦应布置在制品刚度、强度最大的部位(如凸缘、加强肋等处),作用面积也应尽可能大些,以免损坏制品。
脱模力的确定与抽芯力的计算相同,但要精准汁算复杂形状制品的脱模力比较困难,这是因为制品与型腔的附着力,尤其对型芯的包紧力,与制品的材料性质、制品形状、成型工艺参数、脱模斜度、型芯间距、型腔表面粗糙度等因素有关。
一般情况下,制品收缩率大,壁蜂、型芯尺寸人们复杂,脱模斜度小以及型腔表面粗糙度大约,脱模阻力就大,反之则小。
实际生产中常用类比法进行估算。
在确定脱模零件结构时,应综合考虑上述因素,以保证制品顺利脱模。
(3)保证制品外观良好也就是说,推出制品的位置应尽量选在制品的内部或对制品外观影响不大的部位。
(4)结构可靠即推出机构应工作可靠,运动灵活,具有足够的强度和刚度。
二、推出机构的分类1,按动力来源分类(1)手动推出机构常用于注射机不带顶出装置的定模一方,开模后,由人工操作推出机构推出定模中的制品。
(2)机动推出机构它利用注射机开模动作,通过推出机构推出制品。
(3)液压推出机构它是靠注射机上设置专用的液压推出装置进行脱模。
(4)气动推出机构它是利用压缩空气将制品吹出。
2,按模具结构分类(1)简单推出机构;(2)双推出机构;(3)二级推出机构;(4)带螺纹制品的推出机构。
三、简单推出机构简单推出机构又可分多种结构形式,常见的结构形式有下面几种。
1、推杆推出机构用推杆推出制品,尤其是圆推杆推出制品是推出机构中最简单、最常用的—种。
脱模机构

脱模(推出) 第九章 脱模(推出)机构设计推出机构——把塑件及浇注系统从从型腔中或型芯上脱出来的 推出机构——把塑件及浇注系统从从型腔中或型芯上脱出来的 —— 机构。
机构。
第一节推出机构的组成及分类一、推出机构的组成推出机构组成:推出部件(推杆、拉料杆、推杆固定板、 推出机构组成:推出部件(推杆、拉料杆、推杆固定板、推杆 垫板、限位钉)、导向部件(推杆导柱、推杆导套)、 )、导向部件 )、复位部 垫板、限位钉)、导向部件(推杆导柱、推杆导套)、复位部 复位杆)。
件(复位杆)。
二、推出机构分类按驱动方式分: 机动推出机构 液压推出机构 手动推出机构 按推出元件的类别分: 推杆推出机构 推管推出机构 推件板推出机构按模具结构分: 简单推出机构 二次推出机构 带螺纹的推出机构 浇注系统自动切断推出机构 多元联合脱模机构复杂推出机构三、推出机构设计原则1.尽量使塑件留于动模一侧塑件留于动模推出机构简单,否则要设计定模推出机构。
塑件留于动模推出机构简单,否则要设计定模推出机构。
设计定模推出机构2.保证塑件推出时不变形不损坏脱模力应作用于塑件刚度及强度最大的部位 作用力面积尽可能大3.推出位置尽量选在塑件内侧,保证塑件外观良好 4.合模时应使推出机构正确复位 5 .推出机构应动作可靠 推出和复位过程中,结构应简单,动作可靠、灵活, 推出和复位过程中,结构应简单,动作可靠、灵活, 无卡死与干涉现象。
机构本身应有足够的刚度、 无卡死与干涉现象。
机构本身应有足够的刚度、强度 和耐磨性。
和耐磨性。
第二节1.定义脱模力的计算脱模力——指将塑件从型芯上脱出时所需克服的阻力。
成型收缩的包紧力 大气压力 机构运动的摩擦力 塑件对模具的粘附力2.影响脱模力的因素型芯成型部分的表面积及其形状 收缩率及摩擦系数 塑件壁厚和包紧型芯的数量 型芯表面粗糙度 成型工艺:P注、t冷3.脱模力计算 受力分析: ∑Fx=0 F摩cosα-F脱-F正sinα=0 F脱= F摩cosα-F正sinα F摩=f·F正 F正=pA f—摩擦系数(0.15~1.0) p—因塑件收缩对型芯产生的单位正压力(12~20MPa) A—塑件包紧型芯的侧面积(mm2) F脱= pA(f·cosα-sinα) 总脱模力等于 总 脱 大气 大气压力影响:引气、不引气) 大气(大气压力影响 总脱模力等于F总=F脱+F大气 大气压力影响:引气、不引气) 等于 以上对脱模力的计算是一种比较粗略的方法。
模具推出机构

一、脱模机构类型与特点
2、推出机构特点
➢脱螺纹机构特点:
▪脱螺纹机构结构复杂,应能实现制品与型芯的相对旋转运动,同时制 品还应沿脱模方向同步移动; ▪机构工作的开始和终止,以及运动速度都需要适当控制。
二、塑件脱模力的计算 ➢脱模力的构成:
▪塑件冷却收缩对型芯产生的包紧力,脱模时表现为塑料与型芯的摩擦力 ; ▪大气压力(不通孔型芯); ▪塑料与型芯材料的粘结力(可忽略); ▪脱模机构运动的摩擦阻力(可忽略)。
二、脱模力计算
1、圆锥形型芯脱模力计算
➢对于厚壁件(t/d>1/20),塑件冷却收缩 对型芯产生的单位正压力p:
p
[(1
(k 2
)
1)E (1
)k
2
]
式中 k——法平面上内外曲率半径之比(简称径比),k=ρ0/ρi≈R/r; ρi——法平面上塑件内壁曲率半径即该点型芯半径; ρ0——法平面上塑件外壁曲率半径。
➢推板与引气装置:较大尺寸薄壁深腔壳形件,常增设引气 装置,以避免脱模时塑件变形。
三、简单推出机构
4、活动镶块或凹模推出机构 ➢应用:带侧凹或螺纹的制品采用活动镶块成型时,可利用 其进行推出,在模外取出镶件。
三、简单推出机构 4、活动镶块或凹模推出机构
三、简单推出机构
5、气压推出机构 ➢特点:采用压缩空气推出塑件,受力均匀,并简化模具; 气压一般在0.5MPa以下;主要用于大型薄壳件。
二、脱模力计算
1、圆锥形型芯脱模力计算
➢对于薄壁件(t/d<1/20),脱模力Fd:
Fd
Fp cos( f tg ) 1 f sin cos
10 A
2Etl cos ( f tg ) 10A 1 1 f sin cos
塑胶件的脱模机构

P cos(f tg)
Q1
P=c·h ·q
1 f sin cos
Q1 P
上式中 α——设计斜度 f——可查表 已知条件
经验公式 P=c·h·q 式中 c——型芯成型部分断面形状的周长
h——型芯成型部分的高度 q—— 塑料的收缩流利(一般取80~120kg/m2)
正压力P的理论计算公式
薄壁件: P 2Etl 1
点浇口自动切断机构
顶管和推板联合推出机构
二.脱模力的计算
对型芯进行受力分析
包紧力P——塑件冷却收缩将型芯或凸模包紧
脱模力Q1——初始脱模力
摩擦力F——塑料与钢材之间的粘附力 F f (P Q1sin )(1)
(1)代入(2)
∑Fx=0
F cos Q1 Psin (2)
f (P Q1 sin ) cos Q P sin
(3) 推板的几种种固定方式
套在型芯上 与顶杆用过盈配合固定在一起、顶杆头部带螺纹 限制推板的脱落
4. 脱模系统的辅助零件
(1) 导向零件:导套、导柱 (2) 回程装置
回程杆回程 顶杆(顶管)兼回程杆回程 弹簧复位
弹簧复位
杠杆复位
摆杆复位
连杆复位
1
气动抽芯、液压抽芯
5.其他一些脱模机构
(2)设计顶杆脱模机构应注意的几点 顶杆直径:一般在2.5~12 顶杆位置 顶杆装配位置: 顶杆与模具装配间隙 材料 顶杆形状
①顶杆直径:一般在2.5~12mm
注意刚度和强度 直径不应过细,应有足够的刚度承受顶出力 当直径在3以下时可设计成阶梯形等形状
②顶杆位置
设置在脱模阻力大的地方 如图
局部有细而深的凸台或筋,应在其底部加设顶杆 如图
脱模力计算
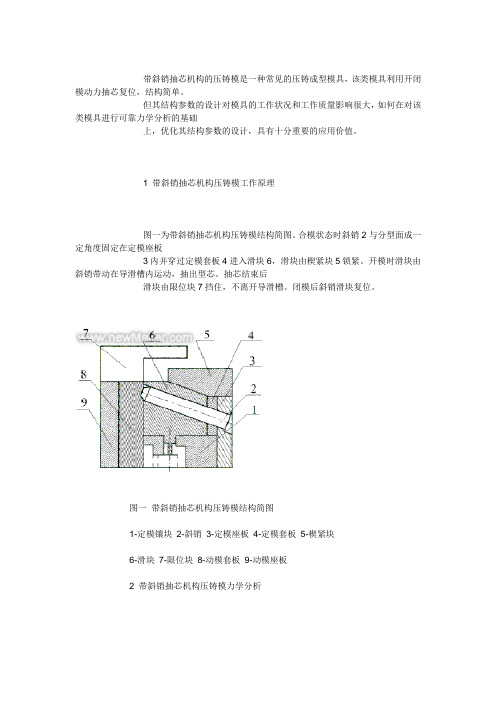
带斜销抽芯机构的压铸模是一种常见的压铸成型模具,该类模具利用开闭模动力抽芯复位,结构简单。
但其结构参数的设计对模具的工作状况和工作质量影响很大,如何在对该类模具进行可靠力学分析的基础上,优化其结构参数的设计,具有十分重要的应用价值。
1 带斜销抽芯机构压铸模工作原理图一为带斜销抽芯机构压铸模结构简图。
合模状态时斜销2与分型面成一定角度固定在定模座板3内并穿过定模套板4进入滑块6,滑块由楔紧块5锁紧。
开模时滑块由斜销带动在导滑槽内运动,抽出型芯。
抽芯结束后滑块由限位块7挡住,不离开导滑槽。
闭模后斜销滑块复位。
图一带斜销抽芯机构压铸模结构简图1-定模镶块2-斜销3-定模座板4-定模套板5-楔紧块6-滑块7-限位块8-动模套板9-动模座板2 带斜销抽芯机构压铸模力学分析2.1 滑块力学分析模具中斜销抽芯机构滑块能否正常工作与其受力情况有关,而滑块受力情况与其设计参数直接关联,所以分析滑块受力情况和自锁条件是合理设计斜销抽芯机构的基础。
图二为滑块受力情况。
a、b、c、h、s为滑块结构尺寸,F为抽芯力,N1为斜销对滑块的正压力,f1为斜销对滑块的摩擦力,N2、N3、N4分别指楔紧块、定模套板、动模套板对滑块的正压力,f2、f3、f4分别表示N2、N3、N4所对应的摩擦力。
图二滑块受力分析考虑到滑块不受弯矩作用,则开模瞬间滑块的静力平衡方程表示为:F f3 f4 f2·sinβ f1·sinα=N1·cosα N2·cosβ (1)N3 N1·sinα f1·cosα=N2·sinβ N4 (2)(N1·cosα-f1·sinα)b (N1·sinα f1·cosα)·(s btgα) f2(S-h)·sinβ N4(a/2-s)=Fc f3·b N2sinβ(s-h/2) N2cosβ(b-sinβh/2) N3(a/2-s) (3)因此,开模时滑块的受力情况既与抽芯力有关,同时与滑块及斜销的结构尺寸相关。
推出机构

3、回位零件
1)回针(R.P)
作用;借助模具闭合动作使推出机构复位的杆件。复位时 其顶面与分型面平齐。
注意: 当回位弹簧与回针在同一位置时,回位弹簧的内径要
比回针大一点(0.5-2mm)。
同时,安装回位弹簧的孔直径也要比回位弹簧的外径 要大(1-2mm)。
另外,在不发生干涉的前提下,回位弹簧可以像上面 一样放置在模具的上顶出板上。
• 當成品之高度較高或出模角較大時, 平面 圖上要把頂線畫出來, 這樣放頂針時就不 會出錯。當成品頂有較大 R位,平面圖上要 把 R的切線畫出來, 以作為放頂針的邊界.
1.6 圓柱,頂位設計.
較深的柱位最 好在柱底放頂 針,另可作疏氣 .
1.7司筒柱:兩個方法頂出 .
較深的有孔柱 位,可用司筒頂出 .
套筒(丝筒、推管)
用于推出圆筒形制品或圆形凸台制品。
优点:是推出动作均匀、可靠,制品上不会留下明 显痕迹。沉头固定在定模板上,顶针和推管同步运 动。不适用于软塑料或薄壁深筒形件的推出。
推管内径与型芯配合,外径与模板配合,H8/f8 (H8/f7) 推管壁厚一般不小于0.75mm
套筒 标准参数
备注:套筒尺寸需依照模具实际情况而定﹔沉头部分参照标准顶针﹐套筒壁厚一般为 0.75~~1.5MM;备料时需附图﹐总长须往正向取整数。
它的实际长度也需要在图上长度基础上加上5-20mm(预压 量).
黄弹簧的最大压缩量为≤自由长度%45 簧
蓝弹簧的最大压缩量为≤自由长度的%42 簧
頂針設計中二個最常見的缺陷問題
1. 頂白 通常當頂針數量不夠或產品局部包模 力很大,而頂針布置不當造成頂針的頂 部膠料出現發白的現象.
2. 變形 通常是由于頂針排布不合理造成.
塑料模具成型第七章 脱模机构

2、制件不变形损坏3、良好制件的外观1、顶杆固定在顶出板固定板和顶出板,螺钉连接,注射机的顶出力作用在顶出板上。
2、导柱、导套为顶出平稳,顶出零件不致于弯区、卡死,长设顶出系统的导柱、导套。
3、回程杆为完成顶出板的回程,靠回程杆实现。
四、脱模机构结构组成4、勾料杆(拉料杆)5、挡销并不是所有的模具都必须由这些零件,主要由结构决定,有的还有挡销。
2个作用:(1)使顶出板与底板之间有间隙,以便清除废料及杂物(多用于压制模);(2)由调节挡销厚度来控制顶板的位置和顶出距离。
第二节简单脱模机构凡在动模一边施加一次顶出力,就可实现制件的脱模。
形式:推杆、顶管、推板、多元件综合脱模机构、气压脱模机构、活动镶件或型腔脱模机构。
一、顶杆脱模机构1、特点:(1)广泛应用,加工简单,易更换,效果好;(2)易引起应力集中,面积小,顶穿或变形)2、组成(1)推出部件:推杆、推杆固定板、推板;(2)导向部分:导柱、导套;平稳、不弯曲、不卡死(3)复位部件:复位杆、弹簧;(4)固定零件:螺钉、挡销。
设计要点:(1)应该设在脱模阻力大的地方;(2)应该足够的强度和刚度承受推出力;弯曲或折断直径=2.5-12mm 当直径﹤3mm 时,要做阶梯形(3)断面和型腔应同一平面或高出0.05-0.10mm (4)带侧抽芯的模具,要开设侧抽芯(5)有冷却水道的模具,避免推杆穿过冷却水道,防止漏水(6)对格子板状塑件,断面为矩形推杆(7)对于薄壁壳体塑件,用断面为D 形推杆(8)在模内排气困难处,设推杆(9)阻力大的部位,多设推杆(10)顶杆材料选用45#钢,顶头应该淬火处理(11)顶杆特殊形式A 型:用途广泛,最简单;D-d=4-6mm B型:阶梯型,用于顶杆直径小的情况;d 1=2d 提高强度C型:阶梯插入式,顶杆较细,与塑料接触的滑动部分,选用优质钢。
d 插入d 1,过渡配合M=(4-6)d E型:特殊断面插入式顶杆,为防止拔出,在顶杆两端铆接使之固定。
- 1、下载文档前请自行甄别文档内容的完整性,平台不提供额外的编辑、内容补充、找答案等附加服务。
- 2、"仅部分预览"的文档,不可在线预览部分如存在完整性等问题,可反馈申请退款(可完整预览的文档不适用该条件!)。
- 3、如文档侵犯您的权益,请联系客服反馈,我们会尽快为您处理(人工客服工作时间:9:00-18:30)。
(1)定义:指将塑件从型芯上脱 出时所需克服的阻力。包括:
成型收缩的包紧力; 不带通孔的壳体类塑件的大气压力;
(2)影响脱模力的因素
型芯成型部分的表面积及其形状. 收缩率及摩擦系数. 塑件壁厚和包紧型芯的数量. 型芯表面粗糙度. 成型工艺:P注、t冷.
机构运动的摩擦力;
Fm cos Ft Fb sin 0
Fm ( Fb Ft sin )
Fb ( cos sin ) Ft 1 cos sin
Ft Fb ( cos sin ) Ap( cos sin )
力平衡的公式
2
5.顶出力(脱模力)计算
3
塑件对模具的粘附力;
1
5.顶出力(脱模力)计算
F
k
0
F m-脱模时型芯受到的摩擦阻力; F b -塑件对型芯的包紧力; F t -脱模力; Α -脱模斜度 ; μ -塑件对钢的摩擦系数,一般为 0.1~况下: 模外冷却的塑件,p 取(2.4~3.9×107Pa; 模内冷却的塑件,p 取(0.8~1.2)×107Pa。
Ft Fb ( cos sin ) Ap( cos sin )
由上面的式子可以看影响因素脱模力的大小主要有以下几点:
(l)主要与塑件包络型芯侧面积的大小有关。型芯的侧面积越大,所需的脱 模力也越大。 (2)与型芯的脱模斜度有关。脱模斜度越大,所需的脱模力越小。 (3)与型芯的表面粗糙度有关。表面粗糙度值越低,型芯表面越光洁,所需 的脱模力就越小。 (4)与塑件的结构有关。塑件厚度越大、形状越复杂,冷却凝固时所引起的 包紧力和收缩应力越大,则所需的脱模力越大。 (5)与注射工艺有关。 注射压力越大,则包紧型芯的力越大,所需脱模力越大; 脱模时模具温度越高,所需的脱模力越小; 塑件在模内停留时间越长,所需的脱模力越大。 (6)与成型塑件的塑料品种有关。不同的塑料品种,由于分子的结构不一样, 因而它们的脱模力也不一样。