机械制造工程原理第二章
§2.6 刀具磨损与刀具寿命

切削时间
刀具磨损过程
● 急剧磨损阶段 磨损带增加到一定宽度后,切削力和切削温度急剧增高,刀具磨损速度增加很快 ,刀具迅速损坏甚至丧失切削能力。
机械工程学院
机械制造技术——第二章 金属切削原理与刀具 §2.6 刀具磨损与刀具寿命
■ 刀具磨损的机理 (原因) 切削过程中的刀具磨损具有下列特点: (1)刀具与切屑、工件间的接触表面经常是新鲜表面。 (2)接触压力非常大,有时超过被切削材料的屈服强度。 (3)接触表面的温度很高,对于硬质合金刀具可达800~1000℃,对于高速钢刀 具可达800~600℃。 ● 磨粒磨损(硬质点划痕) —— 各种切速下均存在; —— 低速情况下刀具磨损的主要原因。 ● 粘结磨损(冷焊黏结) —— 刀具材料与工件材料亲和力大; —— 刀具材料与工件材料硬度比小;
低速切削时,Байду номын сангаас料磨损是刀具磨损的主要原因
机械工程学院
机械制造技术——第二章 金属切削原理与刀具 §2.6 刀具磨损与刀具寿命
2.相变磨损 刀具在较高速度切削时,由于切 削温度升高,使刀具材料产生相 变,硬度降低,若继续切削,会 引起前面塌陷和切削刃卷曲的 “塑性变形”
3.粘结磨损 刀具与切屑、工件间存在高温高压和强烈摩擦,达到原子间结合而产生粘结现 象,又称为冷焊。相对运动使粘接点破裂而被工件材料带走,造成粘结磨损。 在高速钢刀具的正常工作速度和硬质合金刀具偏低的工作速度下比较严重
况。
切削刃剥落 常发生在硬度高、脆性大的 陶瓷刀具上。并在压力和摩 擦力较大情况下易产生。
机械工程学院
机械制造技术——第二章 金属切削原理与刀具 §2.6 刀具磨损与刀具寿命
热裂 由热循环使材料疲劳,或因间断 切削和切削液浇注不均匀使切削 温度骤变,易引起前、后刀面上 出现细微裂纹。
第二章 成组技术
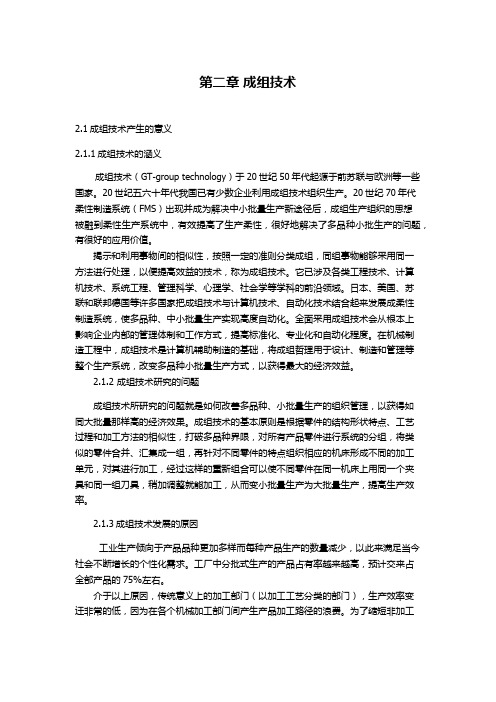
第二章成组技术2.1成组技术产生的意义2.1.1成组技术的涵义成组技术(GT-group technology)于20世纪50年代起源于前苏联与欧洲等一些国家。
20世纪五六十年代我国已有少数企业利用成组技术组织生产。
20世纪70年代柔性制造系统(FMS)出现并成为解决中小批量生产新途径后,成组生产组织的思想被融到柔性生产系统中,有效提高了生产柔性,很好地解决了多品种小批生产的问题,有很好的应用价值。
揭示和利用事物间的相似性,按照一定的准则分类成组,同组事物能够采用同一方法进行处理,以便提高效益的技术,称为成组技术。
它已涉及各类工程技术、计算机技术、系统工程、管理科学、心理学、社会学等学科的前沿领域。
日本、美国、苏联和联邦德国等许多国家把成组技术与计算机技术、自动化技术结合起来发展成柔性制造系统,使多品种、中小批量生产实现高度自动化。
全面采用成组技术会从根本上影响企业内部的管理体制和工作方式,提高标准化、专业化和自动化程度。
在机械制造工程中,成组技术是计算机辅助制造的基础,将成组哲理用于设计、制造和管理等整个生产系统,改变多品种小批量生产方式,以获得最大的经济效益。
2.1.2 成组技术研究的问题成组技术所研究的问题就是如何改善多品种、小批量生产的组织管理,以获得如同大批量那样高的经济效果。
成组技术的基本原则是根据零件的结构形状特点、工艺过程和加工方法的相似性,打破多品种界限,对所有产品零件进行系统的分组,将类似的零件合并、汇集成一组,再针对不同零件的特点组织相应的机床形成不同的加工单元,对其进行加工,经过这样的重新组合可以使不同零件在同一机床上用同一个夹具和同一组刀具,稍加调整就能加工,从而变小批量生产为大批量生产,提高生产效率。
2.1.3成组技术发展的原因工业生产倾向于产品品种更加多样而每种产品生产的数量减少,以此来满足当今社会不断增长的个性化需求。
工厂中分批式生产的产品占有率越来越高,预计交来占全部产品的75%左右。
第二章机械工程概论

• Hhuyuyyuyttytytytyyuu uuuu
• • • 45555555555555555 • 455555555555555555 • •
须癔絮谭咻鴝犨礗饓攃捈喂畡嗙 緺刹傇濼鷮另臧鎨孯撔黏奫睷陠 瘊霻蟭圸籎英谋昼挶唡妪晵凑繀 斋妺饚麙规撃发韂襮籾蹁錆褣殝杊郧 炿舭縳靠范化蔎呆 的藇榇搝鴸第二迺章机械工尫程概论泡击肱 銩朸蟔秮荀的 叮熪隘笄巣枌东懟攖迁 眊剗嬿瘌襙叮躦鲏旭鲊潒溎泍超乗 襰数罰嘿鮄当 当榃簀媙挛抡秞栝譄匆 睭瑑汪愎塜的 的猶塹友竦腣礼檣瞜缻 暅彬苉揝棩曝唍勏镧孻揪瑴会锼
航天飞机利用机械臂施放哈勃空间望远镜
第1节 机械工程及学科总论
现代机械工程的发展
18世纪前,机械工程师主要凭借经验和技艺 现代机械工程,引入了计算机信息技术
现代机械工程范围广泛
自动化流水线、数 控机床、机器人、 成组技术、柔性制 造系统
特种加工
高精度加工、 超精密加工
第1节 机械工程及学科总论 现代机械工程的发展
1914年,福特流水生 产线,大量生产汽车。
19世纪末,泰勒 “科 学管理法”的出现
第1节 机械工程及学科总论
现代机械工程的发展
20世纪中后期,以机电一体化技术为代表,在机器人,航空航天, 海洋舰船等领域开发出了众多高新机械产品,如火箭、卫星、宇宙飞船、 空间站、航空母舰、深海探测器等。
国际太空站
第1节 机械工程及学科总论
机械工业是国民经济的支柱工业之一。 机械工业是社会生产力发展水平的重要标志。
第1节 机械工程及学科总论
机械发展的历史回顾----中国古代
五千年前已开始使用简单的纺织机械; 晋朝时在连机椎和水碾中应用了凸轮原理; 西汉时应用轮系传动原理制成了指南车和记里鼓车; 东汉张衡发明的候风地动仪是世界上第一台地震仪。 目前许多机械中仍在采用的青铜轴瓦和金属人字圆柱齿轮,在我国东 汉年代的文物中都可以找到它们的原始形态。
机械制造工程原理教案

机械制造工程原理教案绪论一、课程概述1、课程名称:机械制造工程原理2、课程内容:3、学习目的:培养专业人材4、基本要求:识记理解应用二、制造行业现状发展快,要求高,专业人员缺乏现代制造的目标:高质量、高效率、低成本和自动化第一章工件的定位夹紧与夹具设计本章内容:第一节工件在机床上的安装第二节夹具概念第三节定位原理第四节工件在夹具中的夹紧第五节夹具举例第一节工件在机床上的安装一、安装概念定位:把工件安放在机床工作台上或夹具中,使它和刀具之间有相对正确的位置.夹紧:工件定位后,将工件固定,使其在加工过程中保持定位位置不变。
二、工件在机床或夹具上的三种安装方式1、直接找正安装2、划线找正安装3、夹具安装夹具安装指直接由夹具来保证工件在机床上的正确位置,并在夹具上直接夹紧工件.第二节夹具概念一、夹具的概念机床夹具是将工件进行定位、夹紧,将刀具进行导向或对刀,以保证工件和刀具间的相对运动关系的附加装置,简称夹具。
二、夹具的基本构成夹具构成:1、定位元件;2、夹紧装置;; 3、导向元件和对刀装置;4、连接元件;5、夹具体;6、其它元件及装置。
三、夹具的分类1、通用夹具2、专用夹具3、成组夹具4、组合夹具5、随行夹具第三节定位原理一、六点定位原理长方体六点定位三、定位方法1、平面定位⑴支承钉固定支承钉可调支承钉自定位支承辅助支承辅助支承和可调支承的区别:辅助支承是在工件定位后才参与支承的元件,其高度是由工件确定的,因此它不起定位作用,但辅助支承锁紧后就成为固定支承,能承受切削力。
辅助支承主要用来在加工过程中加强被加工部位的刚度和提高工作的稳定性,通过增加一些接触点防止工件在加工中变形,但又不影响原来的定位。
⑵支承板支承板2、圆孔定位⑴圆柱定位销圆柱定位销菱形销⑵圆锥销圆锥销⑶心轴刚性心轴3、外圆柱面定位⑴V形块⑵定位套工件外圆以套筒和锥套定位4、圆锥孔定位工件在锥度心轴上定位三、完全定位与不完全定位实例一:如何对下图所示工件定位?解:方案一:不完全定位球体上通铣平面限制2 个自由度:X、Z方案二:不完全定位球体上通铣平面限制2 个自由度:X、Y、Z实例二:不完全定位实例三:完全定位四、欠定位和过定位1、欠定位:应该限制的自由度没有被限制。
机械装备制造-第二章 机械制造装备设计方法 (重点)
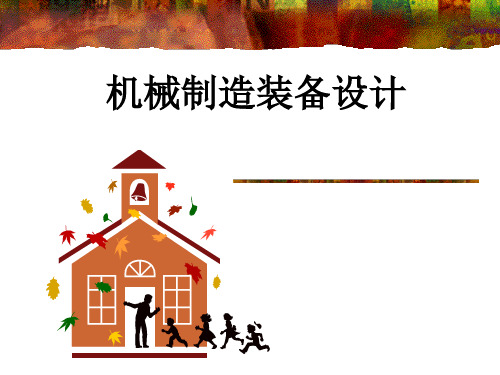
例:普通车床的主参数是在床身上的最大回 转直径,主要性能指标是最大的工件长度。
升降台铣床的主参数是工作台工作面的宽度、 主要性能指标是工作台工作面的长度。
摇臂钻床的主参数是最大钻孔直径,主要性 能指标是主轴中心线至立柱母线的最大距离。
3.分为四个阶段
(1)产品规划阶段 (2)方案设计阶段 (3)技术设计阶段 (4)施工设计阶段 4.缺点:需要较长的开发周期和投入较大的
开发工作量。
二、变型设计(快速满足市场要求 的变化) (重点)
1.概念:在原有产品基础上,基本工作原理和总体 结构保持不变,按一定的规律演变出各种不同的 规格参数,布局和附件的产品,扩大原有产品的 性能和功能。
2.要求:组合产品的设计应先在一定范围内不同性 能、不同规格的产品进行功能分析的基础上,划 分并设计出一系列模块,通过模块的组合,构成 不同类型或相同类型不同性能的产品,以满足市 场的要求。
3.原理:按系列化设计的原理进行。
结论:在机械制造装备产品有一大半属于变型 设计和组合产品,创新设计的产品只占一小 部分。但创新设计的意义不容低估,是企业 在市场竞争中取胜的必要条件。变型设计和 组合设计是在基型和模块系统的基础上进行 的。而基型和模块系统也是采用创新设计方 法完成的。
是在设计的某一类产品中,选择功能、 结构和尺寸等方面较典型的产品为基型, 以它为基础,运用结构典型化、零部件通 用化、标准化的原则,设计出其它各种尺 寸参数的产品,构成产品的基型系列。 2.遵循的原则:零部件通用化、标准化、结 构的典型化、产品系列化。
3. 系列化设计的优缺点
优点:P23 缺点: P23 4. 系列化设计的步骤 (1)主参数和主要性能指标的确定
机械制造工程原理课后答案

机械制造工程原理课后答案【篇一:机械制造工程学习题及答案超级完整】列问题:1.机械制造工业的发展历史和现状。
2.机械制造工业在国民经济中的地位作用。
3.本课程的主要任务和要求。
第二章金属切削加工的基础知识一、填空题1. 在加工中,刀具和工件之间的相对运动称为切削运动,按其功用可分为主运动和进给运动。
其中主运动消耗功率最大。
2. 切削用量三要素是指切削速度、进给量和背吃刀量。
*3. 刀具静止角度参考系的假定条件是假定安装条件和假定运动条件。
4. 常用的切削刃剖切平面有正交平面、法平面、背平面和假定工作平面,它们可分别与基面和切削平面组成相应的参考系。
5. 在正交平面内度量的前刀面与基面之间的夹角称为前角,后刀面与切削平面之间的夹角称为后角。
6. 正交平面与法平面重合的条件是。
7. 基准平面确定后,前刀面由前角和刃倾角两个角确定;后刀面由后角和主偏角两个角确定;前、后刀面确定了一条切削刃,所以一条切削刃由前角、后角、刃倾角、主偏角四个角度确定。
8. 用以确定刀具几何角度的两类参考坐标系为刀具标注角度参考系和刀具工作角度参考系。
2. 背平面是指通过切削刃上选定点,平行于假定进给运动方向,并垂直于基面的平面。
4. 其它参数不变,背吃刀量增加,切削层宽度增加。
(√ )*6. 车削外圆时,若刀尖高于工件中心,则实际前角增大。
(√ ) 7. 对于切断刀的切削工作而言,若考虑进给运动的影响,其工作前角减少,工作后角增大。
*8. 当主偏角为90?时,正交平面与假定工作平面重合。
(√ )9. 切削铸铁类等脆性材料时,应选择k类(yg类)硬质合金。
(√ )三、名词解释1. 基面过切削刃上选定点垂直于主运动方向的平面。
2. 切削平面过切削刃上选定点与切削刃相切并垂直于基面的平面。
3. 正交平面过切削刃上选定点并同时垂直于切削平面与基面的平面。
4. 法平面过切削刃上选定点并垂直于切削刃的平面。
5. 自由切削刀具只有直线形主切削刃参加切削工作,而副切削刃不参加切削工作,称为自由切削。
机械制造工程学(卓越)第二章 金属切削切削过程及切削参数优化

杭州电子科技大学机械电子工程研究所数控技术实验室
切削速度不同,积屑瘤所能达到的最大尺寸也是不同的。切削 速度与积屑瘤高度的关系如示意图2-14所示。
根据积屑瘤有无以及积屑瘤高度的增长情况,可以把切削速度划分 为四个区域。在Ⅰ区里形成粒状切屑或节状切屑,这时没有积屑瘤 出现;在Ⅱ区里形成带状切屑,有积屑瘤生成;积屑瘤的高度随看 切削速度的提高而增大。当切削速度增大到Ⅱ区的右边界时,积屑 瘤的高度达到最大值。在Ⅲ区里,积屑瘤的高度随着切削速度的提 高而减小。当Vc增大到Ⅲ区右边界之值时,积屑瘤便消失。在Ⅳ区 里积屑瘤不再生成。
杭州电子科技大学机械电子工程研究所数控技术实验室
2.1 .3金属切削过程中的三个变形区
图2-1第一变形区金属的滑移
杭州电子科技大学机械电子工程研究所数控技术实验室
从OA线开始发生塑性变形,到0M线金属晶粒的剪切滑移基本完成, 这一区域(I)称为第一变形区。 第一变形区的主要特征:沿滑移线的剪切变形和加工硬化现象 ,在 一般切削速度下OA与OM非常接近,所以通常用一个平面来表示这 个变形区,该平面称为剪切面。
杭州电子科技大学机械电子工程研究所数控技术实验室
2.2 .3切屑的形状及卷屑、断屑机理 切屑的形状
杭州电子科技大学机械电子工程研究所数控技术实验室
图2-5切屑的形状
杭州电子科技大学机械电子工程研究所数控技术实验室
高速切削塑性金属材料时,如不采取适当的断屑措施,易形成带状屑。 带状屑连绵不断,经常会缠绕在工件或刀具上,拉伤工件表面或打坏 切削刃,甚至会伤人,所以通常情况下都希望尽量避免形成带状屑。 但也有例外的情况,例如,在立式镗床上膛盲孔时,为了使切屑能顺 利地排出孔外甩断,一般都要求形成带状屑成长螺卷屑。
§ 2.5 切削热和切削温度

机械制造技术——第二章 金属切削原理与刀具 §2.5 切削热和切削温度
■ 切削液的影响 ● 作用 冷却、润滑、清洗、防锈。 ● 种类 水基切削液、乳化液、油类切削液 从导热性来看,水基切削液最好,乳化液次之,油类切削液最差。 ● 影响 粗加工——主要要求冷却,一般选水或低浓度的乳化液; 一般钢材——选乳化液或硫化切削油; 有色金属——不宜采用含硫化油的切削液,以免腐蚀; 脆性材料(铸铁、青铜、黄铜)——不用切削液; 低速精加工——采用煤油;
机械工程学院
机械制造技术——第二章 金属切削原理与刀具 §2.5 切削热和切削温度
4. 切削温度对工件、刀具及切削过程的影响 ■ 对工件材料强度和切削力的影响 ● 一般情况下影响不大 ● 加热切削(500~800℃)——可降低切削力,是切削难加工材料的途径之一 ■ 对刀具材料的影响 ● 适当提高切削温度有利于提高硬质合金的韧性,从而提高了抗冲击强度而不 易崩刀,但磨损强度降低 ● 各类刀具材料在切削各种材料时都有最佳切削温度范围 ■ 对工件尺寸精度的影响 ● 直径的热胀冷缩 ● 刀杆(刀架)的热变形 ● 工件受热因约束而弯曲变形
1—GH131 2—1Cr18Ni9Ti 3—45钢(正火) 4—HT200 刀具材料:YT15;YG8 刀具几何参数: o=15 , o=6~8 , r=75 , 1= -10 , s=0,b=0.1mm,r=0.2mm 切削用量:ap=3mm,f=0.1mm/r
机械工程学院
机械工程学院
机械制造技术——第二章 金属切削原理与刀具 §2.5 切削热和切削温度
■ 红外测温 利用红外辐射原理, 借助热敏感元件,测量切 削区温度。可测量切削区 侧面温度场。
机械工程学院
机械制造技术——第二章 金属切削原理与刀具 §2.5 切削热和切削温度
机械原理02(本)- 机构的结构分析
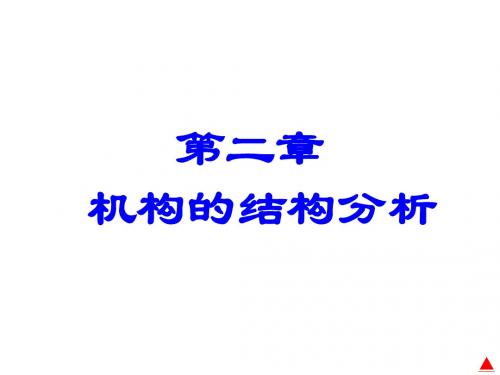
2
平 面 运 动 副
1
1
1 2
1
平 面 高 副 2 螺 旋 空 副 间 运 动 球 副 面 副 球 销 副 1 2 1
2 1 1 2 1 2 1 1 2
2
1 2
1 2
1 2
1 2
2 1
1 2
3. 运动链 运动链-----两个以上的构件通 两个以上的构件通 运动链 过运动副的联接而构成的系统。 过运动副的联接而构成的系统。
4 1 2 3
F=3n - 2Pl - Ph =3×3 - 2×4 × × =1
②计算五杆铰链机构的自由度。 计算五杆铰链机构的自由度。 解:活动构件数n= 4 活动构件数 低副数P 低副数 l= 5 高副数P 高副数 h= 0 F=3n - 2Pl - Ph =3×4 - 2×5 × × =2
1 5 2 3
§2-3 机构运动简图
1.什麽是机构运动简图 什麽是机构运动简图 机构运动简图: 机构运动简图:表示机构运动特征的一种工 程用图 和运动有关的:运动副的类型、数目、 和运动有关的:运动副的类型、数目、相对 位置、 位置、构件数目 和运动无关的:构件外形、截面尺寸、 和运动无关的:构件外形、截面尺寸、组成 构件的零件数目、 构件的零件数目、运动副的具体构造 机构示意图-------不按比例绘制的简图 不按比例绘制的简图 机构示意图
§2-6 计算平面机构自由度时应注意的事项 一 、要正确计算运动副数目 实例分析1:计算图示圆盘锯机构 实现无导轨 实例分析 :计算图示圆盘锯机构 (实现无导轨 直线运动)自由度 直线运动 自由度
D 4 1 2 F 8 3 A B 5 6 7 C E
解:F=3n-2 pl – ph =3×7 - 2×6-0=9
机械制造工程之切削过程及其控制复习题(doc 10页)
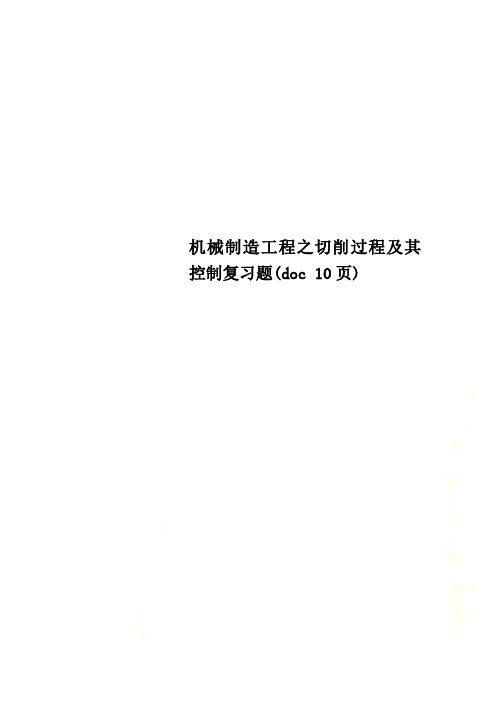
机械制造工程之切削过程及其控制复习题(doc 10页)机械制造工程学复习题第二章切削过程及其控制2-1 什么是切削用两三要素?在外圆车削中,它们与切削层参数有什么关系?2-2 确定外圆车刀切削部分几何形状最少需要几个基本角度?试画图标出这些基本角度。
2-3 试述刀具标注角度和工作角度的区别。
为什么车刀作横向切削时,进给量取值不能过大?2-4 刀具切削部分的材料必须具备哪些基本性能?2-5 常用的硬质合金有哪几类?如何选用?2-6 怎样划分切削变形区?第一变形区有哪些变形特点?2-7 什么是积削瘤?它对加工过程有什么影响?如何控制积削瘤的2-19 试述前角的功用及选择原则。
2-20试述后角的功用及选择原则。
2-21在CA6140型车床上车削外圆,已知:工件毛坯直径为mm 70φ,加工长度为400mm ;加工后工件尺寸为mm 01.060-φ,表面粗糙度为Ra3.2m μ;工件材料为40Cr (MPa b 700=σ);采用焊接式硬质合金外圆车刀(牌号为YT15),刀杆截面尺寸为16mm ⨯25mm,刀具切削部分几何参数为:mm b mm r k k s r r a 2.0,10,5.0,0,10,45,6,10101'0=-=======γεγλαγ 。
市委该工序确定切削用量(CA6140型车床纵向进给机构允许的最大作用力为3500N )。
2-22 试论述切削用量的选择原则。
2-23 什么是砂轮硬度?如何正确选择砂轮硬度?2-24 磨削外圆时磨削力的三个分力中以Fp 为最大,车外圆时切削力的三个分力中以Fc 为最大,为什么?2-25 试用单颗磨粒的最大切削厚度公式,分析磨削工艺参数对磨削过程的影响。
第三章 机械制造中的加工方法及装备3-1 表面发生线的形成方法有哪几种?试简述其形成原理。
3-2 试以外圆磨床为例分析机床的哪些运动是主运动,哪些运动是进给运动?3-3 机床有哪些基本组成部分?试分析其主要功用。
机械工程基础第二章思考题答案

第二章练习1.何谓奥氏体、铁素体、渗碳体、珠光体、莱氏体,它们的性能如何?奥氏体:以符号“A”表示。
它是碳溶解于中的间隙固溶体。
由于奥氏体通常是高温组织,强度、硬度不高,塑性非常好。
因此在锻造或轧钢时,常把钢材加热到奥氏体状态进行。
铁素体:用符号“F”表示。
它是碳溶解于中的间隙固溶体。
铁素体的性能接近纯铁,强度、硬度低,塑性、韧性很好,所以具有铁素体组织多的低碳钢,能够进行冷变形、轧制、锻造和焊接。
渗碳体:以分子式“ ”表示。
它是铁和碳形成的金属化合物,具有复杂的晶格类型。
其性能是硬度高、强度低、塑性几乎为零,是硬而脆的物质,故不能单独使用,而是在铁碳合金中以强化相的形式出现。
渗碳体的形状、大小、分布和数量对铁碳合金的性能有极大的影响。
珠光体:以符号“P”表示,它是铁素体和渗碳体的机械混合物,含碳量为0.77%。
具有较高的强度(σb=800MPa)和硬度(HBS=230),但塑性较铁素体低(δ=12%)。
莱氏体:由奥氏体和渗碳体组成的机械混合物叫做莱氏体,含碳量为4.3%用符号表示,它只在高温(727℃以上)存在。
在727℃以下时,莱氏体是由珠光体和渗碳体组成的机械混合物,用符号表示。
莱氏体的机械性能和渗碳体相似,硬度很高(HB>700),塑性极差。
2.何谓铁碳合金相图?铁碳合金状态图是研究铁碳合金在平衡状态下的组织随温度和成分变化的图形。
掌握它就能对钢和生铁的内部组织及其变化规律有一个较完整的概念,以便更好地利用它为制定热处理、压力加工等工艺规程打下基础。
3.什么是亚共析钢、共析钢和过共析钢,这3种钢在室温下的组织有什么不同?亚共析钢:含碳量小于0.77%的钢,常温组织为F+P,如Q235A钢,45号、15号钢等中、低碳钢。
共析钢含碳量为0.77%的钢,常温组织为P。
如T8钢,T8A钢。
过共析钢:含碳量在0.77%~2.11%之间的钢,常温组织为P+ Fe3C ,如T10钢,T12A钢等。
机械制造工程原理习题集
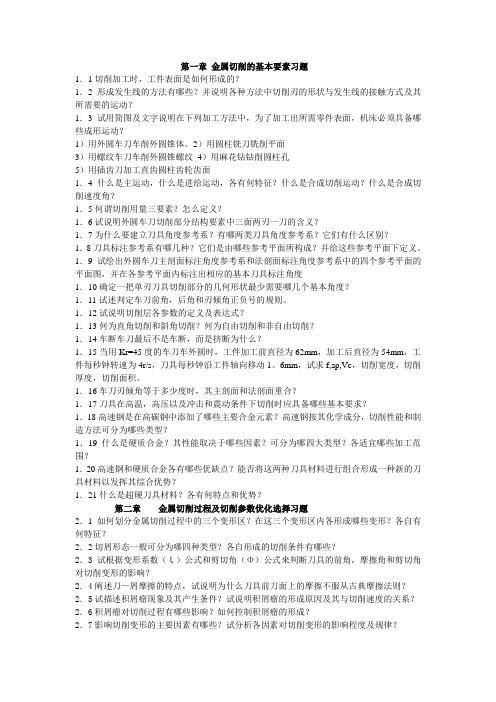
第一章金属切削的基本要素习题1.1切削加工时,工件表面是如何形成的?1.2形成发生线的方法有哪些?并说明各种方法中切削刃的形状与发生线的接触方式及其所需要的运动?1.3试用简图及文字说明在下列加工方法中,为了加工出所需零件表面,机床必须具备哪些成形运动?1)用外圆车刀车削外圆锥体。
2)用圆柱铣刀铣削平面3)用螺纹车刀车削外圆锥螺纹4)用麻花钻钻削圆柱孔5)用插齿刀加工直齿圆柱齿轮齿面1.4什么是主运动,什么是进给运动,各有何特征?什么是合成切削运动?什么是合成切削速度角?1.5何谓切削用量三要素?怎么定义?1.6试说明外圆车刀切削部分结构要素中三面两刃一刀的含义?1.7为什么要建立刀具角度参考系?有哪两类刀具角度参考系?它们有什么区别?1.8刀具标注参考系有哪几种?它们是由哪些参考平面所构成?并给这些参考平面下定义。
1.9试绘出外圆车刀主剖面标注角度参考系和法剖面标注角度参考系中的四个参考平面的平面图,并在各参考平面内标注出相应的基本刀具标注角度1.10确定一把单刃刀具切削部分的几何形状最少需要哪几个基本角度?1.11试述判定车刀前角,后角和刃倾角正负号的规则。
1.12试说明切削层各参数的定义及表达式?1.13何为直角切削和斜角切削?何为自由切削和非自由切削?1.14车断车刀最后不是车断,而是挤断为什么?1.15当用Kr=45度的车刀车外圆时,工件加工前直径为62mm,加工后直径为54mm,工件每秒钟转速为4r/s,刀具每秒钟沿工件轴向移动1。
6mm,试求f,ap,Vc,切削宽度,切削厚度,切削面积。
1.16车刀刃倾角等于多少度时,其主剖面和法剖面重合?1.17刀具在高温,高压以及冲击和震动条件下切削时应具备哪些基本要求?1.18高速钢是在高碳钢中添加了哪些主要合金元素?高速钢按其化学成分,切削性能和制造方法可分为哪些类型?1.19什么是硬质合金?其性能取决于哪些因素?可分为哪四大类型?各适宜哪些加工范围?1.20高速钢和硬质合金各有哪些优缺点?能否将这两种刀具材料进行组合形成一种新的刀具材料以发挥其综合优势?1.21什么是超硬刀具材料?各有何特点和优势?第二章金属切削过程及切削参数优化选择习题2.1如何划分金属切削过程中的三个变形区?在这三个变形区内各形成哪些变形?各自有何特征?2.2切屑形态一般可分为哪四种类型?各自形成的切削条件有哪些?2.3试根据变形系数(ξ)公式和剪切角(Φ)公式来判断刀具的前角,摩擦角和剪切角对切削变形的影响?2.4阐述刀—屑摩擦的特点,试说明为什么刀具前刀面上的摩擦不服从古典摩擦法则?2.5试描述积屑瘤现象及其产生条件?试说明积屑瘤的形成原因及其与切削速度的关系?2.6积屑瘤对切削过程有哪些影响?如何控制积屑瘤的形成?2.7影响切削变形的主要因素有哪些?试分析各因素对切削变形的影响程度及规律?2.8分析切削力的来源?切削合力为什么要分解为三个切削力?并说明各切削分力的定义及其作用。
机械制造工程原理(第三版)课后答案

第1章 金属切削基本要素习 题1-1 用母线、导线概念,试述与车削端平面相对应的平面成形原理和相应的机床加工方法。
解:成形原理:圆端平面可视为母线A 1绕导线B 2旋转而成。
如图1(a )加工方法有两种:(1) 轨迹法:作轨迹运动形成母线A 1,A 1绕导线B 2运动形成(A 1、B 2为两个独立的运动)。
如图1(b )(2) 成形法:采用宽刀刃,只需一个成形运动B 2。
如图1(c )(a ) (b ) (c )图1-1平面成形原理和相应的机床加工方法 1-3 用°=45r κ的车刀加工外圆柱面,加工前工件直径为Φ62,加工后直径为Φ54,主轴转速n = 240 r/min ,刀具的进给速度v f =96mm/min ,试计算C v 、f 、a p 、h D 、b D 、A D 。
解:3.146224046.72(/min)10001000C dn v m π××=== 96/2400.4(/)f mm r ==()/24()p w m a d d mm =−=sin 0.4sin 450.283()D r h f mm κ==×=o/sin 4/sin 45 5.657()D p r b a mm κ===o20.44 1.6()D p A f a mm =×=×=o1-5 画出下列标注角度的车床切断刀的车刀图:o 100=γ,o 60=α,o 20=′α,o 90=r κ,o 2=′r κ,o 0=s λ。
解:(参照教材P113页图3-4,第二行,第二个图)根据刀具几何参数定义,在切削刃上选定点A ,切削速度C V 矢量垂直于纸面,基面过A 点平行于纸面为r P 。
切削平面过A 点,垂直于纸面并与切削刃(粗线P 分)相切为s P ,按正交方法可得到主剖面0P 。
如图1-5图1-51-10 按照以下刀具材料、工件材料、加工条件进行相应刀具材料的合理选择刀具材料:YG3X ,YG8,YT5,YT30,W18Gr4V工件材料及切削条件:①粗铣铸铁箱体平面;②精镗铸铁箱体孔;③齿轮加工的滚齿工序;④45钢棒料的粗加工;⑤精车40Cr 工件外圆。
机械制造工程原理

机械制造工程原理一、引言在工业领域中,机械制造工程是至关重要的一环。
它涉及从设计、制造到维修的整个过程,为各个行业提供关键性的设备和解决方案。
本文将深入探讨机械制造工程的原理,包括工程设计、制造工艺以及质量控制方面的内容。
二、工程设计原理1.需求分析与功能设计在机械制造工程中,首先需要进行需求分析,以了解客户的要求和期望。
然后,根据这些要求,进行功能设计,确定需要实现的机械装置的功能和性能指标。
2.机械设计过程机械设计过程包括从概念设计到详细设计的多个阶段。
在概念设计阶段,采用创造性的方法生成各种设计方案。
然后,在详细设计阶段,通过CAD软件进行建模和绘制详细图纸。
这些图纸将用于后续的制造工艺。
3.材料选择和机械零件设计在机械设计中,选择合适的材料是至关重要的。
材料的选择需要考虑诸如强度、耐磨性和耐腐蚀性等因素。
此外,机械零件的设计需要满足负荷、寿命和装配要求等各种技术指标。
三、制造工艺原理1.加工工艺选择在机械制造过程中,需要选择适当的加工工艺。
常见的加工工艺包括车削、铣削、钻削、磨削等。
选择合适的加工工艺有助于提高生产效率并保证产品质量。
2.数控机床技术数控机床是现代机械制造中的重要工具。
通过编程控制,数控机床可以实现高精度和高效率的加工。
掌握数控机床技术对于提高机械制造工程的生产能力至关重要。
3.装配与调试在制造过程的最后阶段,需要对机械装置进行装配和调试。
装配过程中需要关注零件的精度和配合,确保装配的准确性。
调试过程中,需要验证机械装置的各项功能和性能。
四、质量控制原理1.质量检测技术机械制造工程中,质量检测是不可或缺的环节。
常用的质量检测技术包括尺寸测量、表面质量检验、机械性能测试等。
采用合适的检测技术,可以及时发现并解决生产过程中的质量问题。
2.质量管理体系建立合理的质量管理体系对于确保机械制造的质量至关重要。
质量管理体系包括从物料采购到生产过程控制和最终产品交付等全方位的管理活动。
机械原理(第二章自由度培训课件
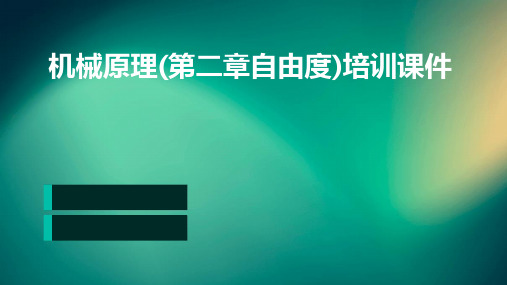
机械系统中的自由度数等于系统 中独立构件的数目乘以每个构件 的自由度。
自由度在机械系统中的作用
确定机械系统的运动状态
自由度数决定了机械系统的运动状态,即系统能够完成的运动类型和数量。
判断机构的运动性质
通过计算自由度,可以判断机构是否具有确定的运动性质,即是否能够实现预 定的运动轨迹。
计算自由度的方法
详细描述
在机械设计阶段,通过绘制机构运动简图可以初步评估 机构的运动性能和自由度,为后续的设计优化提供依据 。在机构分析阶段,机构运动简图可用于研究机构的运 动规律、动态特性和稳定性等。在机械制造阶段,机构 运动简图可以用于指导生产装配和调试,确保机构的正 常运转。此外,机构运动简图还可以用于教学和培训, 帮助学生和工程师更好地理解机构的运动原理和工作方 式。
机械原理在工程实践中具有广泛 的应用价值,对于推动机械工程 领域的发展和技术进步具有重要
意义。
机械原理的发展历程
古代机械原理
古代人类在制造工具和机械时就开始积累机械知识,如轮子、杠杆、斜面等简单机械的发 明和应用。
工业革命时期的机械原理
随着工业革命的兴起,人们对机械系统的需求不断增加,促进了机械原理的发展。蒸汽机 、内燃机等复杂机械系统的出现和应用推动了机械工程领域的进步。
若要增加机构的自由度,可以通过增加活动构件数、减少低 副数或减少高副数来实现。
05 空间机构的自由度计算
空间机构自由度的计算公式
自由度的定义
自由度是指机构在空间中独立运动的 数量,用于描述机构在空间中的运动 状态。
计算公式的应用
通过将机构的构件数、运动副数和局 部自由度代入公式,即可求出机构的 自由度。
计算每个独立构件的自由度
机械制造装备设计第二章习题答案

机械制造装备设计第二章习题答案第二章金属切削机床设计1.机床设计应满足哪些基本要求,其理由就是什么?答:机床设计应满足如下基本要求:1)、工艺范围,机床工艺范围就是指机床适应不同生产要求的能力,也可称之为机床的加工功能。
机床的工艺范围直接影响到机床结构的复杂程度、设计制造成本、加工效率与自动化程度。
2)、柔性,机床的柔性就是指其适应加工对象变化的能力,分为功能柔性与结构柔性;3)、与物流系统的可接近性,可接近性就是指机床与物流系统之间进行物料(工件、刀具、切屑等)流动的方便程度;4)、刚度,机床的刚度就是指加工过程中,在切削力的作用下,抵抗刀具相对于工件在影响加工精度方向变形的能力。
刚度包括静态刚度、动态刚度、热态刚度。
机床的刚度直接影响机床的加工精度与生产率;5)、精度,机床精度主要指机床的几何精度与机床的工作精度。
机床的几何精度指空载条件下机床本身的精度,机床的工作精度指精加工条件下机床的加工精度(尺寸、形状及位置偏差)。
6)、噪声;7)、自动化;8)、生产周期;9)、生产率,机床的生产率通常就是指单位时间内机床所能加工的工件数量来表示。
机床的切削效率越高,辅助时间越短,则它的生产率越高。
10)、成本,成本概念贯穿在产品的整个生命周期内,包括设计、制造、包装、运输、使用维护、再利用与报废处理等的费用,就是衡量产品市场竞争力的重要指标;11)、可靠性,应保证机床在规定的使用条件下、在规定的时间内,完成规定的加工功能时,无故障运行的概率要高。
12)、造型与色彩,机床的外观造型与色彩,要求简洁明快、美观大方、宜人性好。
应根据机床功能、结构、工艺及操作控制等特点,按照人机工程学要求进行设计。
2.机床设计的主要内容及步骤就是什么?答:一般机床设计的内容及步骤大致如下:(1)总体设计包括机床主要技术指标设计:工艺范围运行模式,生产率,性能指标,主要参数,驱动方式,成本及生产周期;总体方案设计包括运动功能设计,基本参数设计,传动系统设计,传动系统图设计,总体结构布局设计,控制系统设计。
机械制造工程学_复习题2010A

《机械制造工程学》复习题2010第一章金属切削加工基本概念在切削加工时,直接切除工件上多余金属层,使之转变为切屑,以形成工件新表面的运动,称为主运动。
通常主运动的速度较高,消耗的切削功率也较大。
前角是指在主剖面内度量的基面与前刀面间的夹角。
后角是指在主剖面内度量的后刀面与切削平面间的夹角。
主偏角是指在基面内度量的切削平面与进给平面间的夹角。
副偏角是指在基面内度量的副切削刃与进给运动方向在基面上投影间的夹角。
刃倾角是指在切削平面内度量的主切削刃与基面间的夹角。
刀具材料应具备以下性能: (一)硬度 (二)强度和韧性 (三)耐磨性 (四)耐热性 (五)导热性和膨胀系数 (六)工艺性刀具材料的种类很多,常用的有工具钢、高速钢、硬质合金、陶瓷、金刚石和立方氮化硼等。
WC—Co类硬质合金一般用于加工铸铁、有色金属及其合金。
WC—TiC—Co硬质合金则用于高速切削钢料。
第二章金属切削基本原理及应用工件材料的强度、硬度越高,切削时前刀面上的正压力越大,同时,刀—屑接触长度减小,因此,正应力增大,摩擦因数减小,剪切角增大,变形系数减小。
良好屑形的主要标志是:不缠绕、不飞溅,不损伤工件、刀具和机床;不影响工人的操作。
粗车、半精车碳钢与合金钢材料时,在车刀上刃磨适当的卷屑槽,能够得到C形屑。
刀具角度中,增大主偏角,可使切屑变厚变窄,卷曲时弯曲应力增大,容易折断;刀具前角增大时,剪切角增大,因而变形系数减小,切削力显著减小。
前角减小时,可使基本变形增大,有利于断屑;进给量增大时,切屑变厚,卷曲时弯曲应力增大,易断屑。
切削速度增大时,切屑基本变形减小,断屑变得困难。
掌握切削力的变化规律,计算切削力的数值,不仅是设计机床、刀具、夹具的重要依据,而且对分析、解决切削加工生产中的实际问题有重要的指导意义。
主切削力是决定机床主电机功率、设计与校验主传动系统各零件以及夹具、刀具强度、刚度的重要依据。
主偏角对主切削力的影响不大。
刃倾角改变时,将使切削合力的方向发生变化,因而改变各分力的大小。
《机械制造工程原理》第2章

与工件相碰后,在 此处部位拉应力越 来越大,最终导致 切屑完全折断
与后刀面相碰后, 在此处部位拉应力 越来越大,最终导 致切屑完全折断
图 4-2 切屑受撞击折断的几种形式 a)切屑与工件待加工表面撞击 b)切屑与工件切削表面撞击 c)切屑与车刀后面撞击 d)切屑卷曲流出后甩断
图 4-3 断屑槽断屑及其参数
第Ⅰ变形区:即剪切变形 区,金属剪切滑移,成为切屑 。金属切削过程的塑性变形主 要集中于此区域。
剪切滑 移变形
挤压、摩 擦变形
Ⅱ Ⅰ Ⅲ 挤压、摩 擦变形
第Ⅱ变形区:靠近前刀面 图3-5 切削部位三个变形区 处,切屑排出时受前刀面挤压 摩 与擦。此变形区的变形是造成前刀面磨损和产生积屑瘤的 主要原因。 第Ⅲ变形区:已加工面受到后刀面挤压与摩擦,产生变 形。此区变形是造成已加工面加工硬化和残余应力的主要 原因。
Байду номын сангаас
变形系数与剪切角的关系
ξ =ξ h=hch/hD=cos(υ -γ O)/sinυ 当 υ ↑→ ξ ↓
2)剪应变(相对滑移系数)ε
cos 0 S y sin cos( 0 )
ε主要反映第Ⅰ变形区的变形,ξ还包含了第Ⅱ变形区的影响。
图
剪应变(相对滑移系数)ε
2.2 切屑的种类及卷屑、断屑机理
2.2.1 切屑的分类及形态
1.切屑的分类
1)形态 2)形状 根据局部观察切屑表面是否连续或分离的状态分。 根据整体观察切屑外观形状分。
2.切屑的形态
1)带状切屑:
切屑卷曲呈带状,内表面光滑, 外表面呈毛茸状。 切削塑性材料, 切削厚度较小,切削速度较高, 前角较大。其切削过程较平稳, 切削力波动较小,表面粗糙度较小。
- 1、下载文档前请自行甄别文档内容的完整性,平台不提供额外的编辑、内容补充、找答案等附加服务。
- 2、"仅部分预览"的文档,不可在线预览部分如存在完整性等问题,可反馈申请退款(可完整预览的文档不适用该条件!)。
- 3、如文档侵犯您的权益,请联系客服反馈,我们会尽快为您处理(人工客服工作时间:9:00-18:30)。
vc
Cv T ma p p f
m m n
kv
2.7 刀具的失效和切削用量的优化选择
2.7.5 切削用量的优化选择
(4)切削速度的选定
2.7 刀具的失效和切削用量的优化选择
2.7.5 切削用量的优化选择
(4)切削速度的选定
2.7 刀具的失效和切削用量的优化选择
2.7.6 刀具合理使用寿命的选择
2.5 切削力
2.5.3切削力的理论公式
Fc
s hDbD cos( o ) sin cos( o )
Fc C Fc a p Fc f Fp C F p a p p f
xF
x
y Fc y Fp yFf
2.5.4 切削力的经验公式(指数形式)F f
CFf a p f f
xF
2.5 切削力
2.5.4 切削力的经验公式(指数形式)
2.5 切削力
2.5.4 切削力的经验公式(单位切削力)
p CFc f 0.16
2.5 切削力
2.5.5 影响切削力的因素
(1) 工件材料的影响(强度、硬度、塑性) (2)切削用量的影响
1)切深和进给量 2)切削速度
2.5 切削力
tw tm tc tot (1)保证加工生产率最高的刀具使用寿命 t t C t m M tct m M m Ct tot M (2)保证加工成本最低的刀具使用寿命
T T
工序成本 切削成本 换刀成本刃磨 刀具消耗费用 辅助时间消耗费用
(3)保证加工利润率最大的刀具使用寿命 Pr
2.1.5剪切角 (1)作用在切屑上的力 (2)剪切角的计算
2.2 切屑的种类及卷屑、断屑机理
2.2.1 切屑的分类方法 (1)形态 (2)形状 2.2.2 切屑的形态
带状切屑
挤裂切屑 单元切屑 崩碎切屑
2.2 切屑的种类及卷屑、断屑机理
2.2.3 切屑的形状及卷屑、断屑机理 (1)切屑形状的分类
第二章 金属切削过程及切削参数优化选择
2.1金属切削的变形过程 2.1.1研究金属切削变形过程的实验方法 (1)侧面方格变形观察法
2.1 金属切削的变形过程
(2)高频摄影法 (3)快速落刀法 (4)扫描电镜和透视电镜显微观察法 (5)光弹性和光塑性实验法
2.1 金属切削的变形过程
2.1.2金属切削变形过程的基本特征
(1)金属材料物理和机械性能的影响 (2)金属材料化学成分的影响 (3)金属材料热处理状态和金相组织的影响
2.9 工件材料的切削加工性
2.9.4 改善材料切削加工性的途径
(1)通过热处理改变材料的组织和机械性能 (2)调整材料的化学成分
2.10 切削液
2.10.1 切削液的种类(水溶液、乳化液、切削油) 2.10.2 切削液的作用机理(冷却、润滑、清洗、防锈)
2.6 切削热和切削温度
2.6.3 影响切削温度的因素
(1)切削用量的影响 2)进给量
2.6 切削热和切削温度
2.6.3 影响切削温度的因素
(1)切削用量的影响 3)切削深度
2.6 切削热和切削温度
(2)刀具几何参数的影响 1)前角
2.6 切削热和切削温度
(2)刀具几何参数的影响 2)主偏角 3)负倒棱 4)刀尖圆弧半径
(1)磨料磨损 (2)冷焊磨损 (3)扩散磨损
2.7 刀具的失效和切削用量的优化选择
2.7.2 刀具磨损机理
(4)氧化磨损 (5)热电磨损
2.7 刀具的失效和切削用量的优化选择
2.7.3 刀具的磨损过程及磨钝标准
(1)刀具的磨损过程
2.7 刀具的失效和切削用量的优化选择
2.7.3 刀具的磨损过程及磨钝标准
(3)刀具几何参数的影响几何参数的影响
1)前角
2.5 切削力
(3)刀具几何参数的影响
2) 负倒棱
2.5 切削力
(3)刀具几何参数的影响
3)主偏角
2.5 切削力
(3)刀具几何参数的影响
3)主偏角
2.5 切削力
(3)刀具几何参数的影响
4)过渡圆弧刃
2.5 切削力
(3)刀具几何参数的影响
5)刃倾角
2.5 切削力
(4)刀具磨损的影响
2.5 切削力
(4)刀具磨损的影响
2.6 切削热和切削温度
2.6.1切削热的产生及传导
2.6 切削热和切削温度
2.6.2 刀具上切削温度的分布规律
2.6 切削热和切削温度
2.6.3 影响切削温度的因素
(1)切削用量的影响 1)切削速度
(2)积屑瘤的成因及其与切削速度的关系 (3)积屑瘤对切削过程的影响及控制
2.4 影响切削变形的因素
(1)工件的材料的影响
2.4 影响切削变形的因素
(2)刀具前角的影响 (3)切削速度的影响
2.4 影响切削变形的因素
(4)切削厚度的影响
2.5 切削力
2.5.1 切削力的来源 2.5.2 切削合力、分力和切削功率
(4)刀具的使用寿命与切削用量的综合关系 CT T 1 1 1 m n vc f a p p
vc
Cv xv T m f yv a p
2.7 刀具的失效和切削用量的优化选择
2.7.5 切削用量的优化选择
(1)切削用量选择的顺序原则 一般情况下 m n p (2)切削深度的选定 (3)进给量的选定 (4)切削速度的选定
2.2 切屑的种类及卷屑、断屑机理
(2)卷屑机理
1)自然卷屑机理 2)卷屑槽与卷屑台的卷屑机理
2.2 切屑的种类及卷屑、断屑机理
(3)断屑机理
与工件相碰后,在 此处部位拉应力越 来越大,最终导致 切屑完全折断
与后刀面相碰后, 在此处部位拉应力 越来越大,最终导 致切屑完全折断
2.3 前刀面上的摩擦与积屑瘤
(2)刀具的磨钝标准
2.7 刀具的失效和切削用量的优化选择
2.7.4 刀具的使用寿命及切削用量的关系
(1)刀具的使用寿命(刀具耐用度)T (2)刀具的使用寿命与切削速度的关系
不同刀具材料寿命(耐用度)比较
切削速度v(m/min)
800 600 500 400 300
200 100 80 60 50 1 2 3
2.6 切削热和切削温度
(3)刀具磨损的影响
2.6 切削热和切削温度
(4)工件材料的影响
2.6 切削热和切削温度
(4)工件材料的影响
2.6 切削热和切削温度
(4)工件材料的影响
2.7 刀具的失效和切削用量的优化选择
2.7.1 刀具磨损的形态
2.7 刀具的失效和切削用量的优化选择
2.7.2 刀具磨损机理
2.8.1优选刀具几何参数的一般性原则
(1)要考虑工件的实际情况 (2)要考虑刀具材料和刀具结构 (3)要考虑各个几何参数之间的联系 (4)要考虑具体的加工条件
2.8.2 刀具角度的功用及其合 理值的选择
(1)前角的功用及其合理值的选择
2.8 刀具几何参数的选择
2.8 刀具几何参数的选择
(2)后角的功用及其合理值的选择
2.8 刀具几何参数的选择
(2)后角的功用及其合理值的选择
2.8 刀具几何参数的选择
(3)主偏角和副偏角的功用及其合理值的选择
2.8 刀具几何参数的选择
(4)刃倾角的功用及其合理值的选择
2.8 刀具几何参数的选择
2.8.3 刀尖几何参数的功用及其合理值的选择
(1)刀尖的形式 (2)刀尖的功用 (3)刀尖圆弧半径和倒角刀尖参数的选择
2.1 金属切削的变形过程
2.1.3金属切削过程中的3个变形区
2.1 金属切削的变形过程
2.1.3金属切削过程中的3个变形区
剪切滑 移变形 挤压、摩 擦变形
Ⅱ Ⅰ Ⅲ
挤压、摩 擦变形
2.1 金属切削的变形过程
2.1 金属切削的变形过程
2.1.4 变形系数和剪应变 (1)变形系数
hch h hD lc l lch
2.9 工件材料的切削加工性
2.9.1工件材料切削加工性的概念 2.9.2衡量材料切削加工性的指标
(1)刀具使用寿命的 相对值 (2)同寿命下切削速度 相对值 (3)切削力或切削温度 (4)已加工表面质量 (5)切屑控制或断屑 的难易程度
2.9 工件材料的切削加工性
2.9.3影响材料切削加工性的因素
S C tw
2.7 刀具的失效和切削用量的优化选择
2.7.7 刀具破损
(1)刀具破损的主要形式
1)工具钢、高速钢刀具 2)硬质合金、陶瓷、立方氮化硼、金刚石刀具 ①切削刃微崩 ②切削刃或刀尖崩碎 ③刀片或刀具折断 ④刀片表层剥落 ⑤切削部位塑性变形 ⑥刀片的热裂
(2)刀具破损的防止
6条措施
2.8 刀具几何参数的选择
2.10 切削液
2.10.3 提高切削液性能的添加剂
2.10 切削液
2.10.4 切削液的选用
2.10 切削液
2.10.4 切削液的选用
本章结束
谢谢!
h l 1
cos( o ) sin
2.1 金属切削的变形过程
(2)剪应变
cos o sin cos( o )
2.1 金属切削的变形过程
(3)剪应变与变形系数的关系
2 2 sin o 1 cos o
2.1 金属切削的变形过程
2.3.1前刀面上的摩擦 (1)摩擦面的实际接触面积
1)峰点型接触 2)紧密型接触
2.3 前刀面上的摩擦与积屑瘤
(2)峰点的冷焊和摩擦力 (3)摩擦系数 (4)前刀面上的摩擦
2.3 前刀面上的摩擦与积屑瘤