氯化钾镀锌工艺的应用
浅谈氯化钾镀锌

浅谈氯化钾镀锌1 前言氯化钾镀锌是目前最主要的镀锌工艺之一, 镀锌层的整平性和光泽性较好, 电流效率较高, 废水处理简单, 特别是能在锌铁件、洋火件等表面处理难度较大的基材上镀覆。
因此, 氯化钾镀锌工艺得到广泛应用。
2 氯化钾镀锌工艺参数的影晌及控制2.1 镀液主要成分作用与控制(1) 氯化锌氯化锌是钾盐镀锌的主盐。
氯化钾浓度高, 允许电流密度范围大, 沉积速率快, 但镀液分散能力和深镀能力降低; 氯化锌浓度低, 浓差极化较大, 分散能力和深镀能力有所改善, 但允许电流密度范围变小, 沉积速率减小, 且高电流密度区容易烧焦等。
因此, 适宜的氯化锌浓度为40~70 g/L。
更为关键的是, 严格控制氯化锌/氯化钾在1:(3~5)为宜。
(2) 氯化钾氯化钾在钾盐镀锌液中既是配位剂又是导电盐,适当提高其含量可提高镀液的导电能力和分散能力。
但其含量高时,会使高电流密度区易出现烧焦,尤其是由于盐析作用使添加剂中载体光亮剂溶解度降低而析出,恶化镀层质量,且降低添加剂产生的光亮作用。
若氯化钾含量太低,会使镀液导电性和分散能力降低。
因此,一般钾盐镀锌工艺配方中氯化钾200~250g/L,最重要的是控制氯化锌/氯化钾的比值在较佳的工艺范围内。
(3) 硼酸硼酸在钾盐镀锌液中是缓冲剂,稳定镀液的pH值, 且在阴极膜中还能起弱配位作用, 对镀层沉积有催化作用。
其含量允许范围较大, 为25~40g/L。
但含量高时, 在温度偏低时容易结晶析出。
2.2 添加剂的影晌和控制市售钾盐镀锌添加剂种类繁多, 但其作用机理和组成基本相同, 都是由主光亮剂、载体光亮剂、辅助光亮剂、应力消除剂等有机物按一定比例复配而成的。
(1) 主光亮剂主光亮剂属于芳香酮类化合物, 能吸附于阴极表面, 增大阴极极化, 使锌镀层结晶细致。
使用比较多的, 如苄叉丙酮、邻氯苯甲醛、对氯苄叉丙酮等。
主光亮剂不溶于水, 要通过载体助溶、增溶、扩散到镀液中发挥其作用。
氯化钾镀锌工艺实践

的含量 要高些 。在 阳极 面 积正 常情 况下 ,很 少 补加 氯 化锌 ,仅补 充 因清除槽 底所造 成 的损 失部分 即可 。
有 化验 条 件 的可 根据 分 析 结果 补 加氯 化锌 ;没 有 条件 的凭经 验判 断 ;用 测 定溶 液 的 密度 估 算 氯化
目前 ,氯化钾 镀 锌工 艺 在 镀 锌体 系 中仍 占主导
表 I 镀 液 主 要成 分
地位 ,并在应 用 中不 断 得 到 改进 和 推 广 。氯 化钾 镀
Fig.1 Main content of plating bath p/(g·L )
锌工 艺更适合 滚 镀 ,具有 镀 层 光 亮 、电流效 率 高 、沉
摘 要 介绍实用型氯化钾镀 锌工艺(包括吊镀和滚镀 )的配方 ,工艺条件 (pH 5—6,温度 10—35℃),正确配制镀 液方法和镀液维护管理 ,镀前处理和后处理工序 ,针对 典型 问题产生 的原 因给出相应 的处 理方法 。为提 高氯化钾 镀锌溶液的稳定性和镀层 的可靠性 ,氯化钾镀锌生产过程 中应重点关 注以下几 个方面 :电镀前后处理质量 ;控制溶 液成分的含量 ;把握施镀的最佳工艺 条件 ;切实优化光亮剂性能 ;强化槽液 的科学管理 ;有效排除 电镀故障 。 关键词 氯化钾镀锌 ;镀液配制 ;镀液维护 ;银 白钝化 ;蓝 白钝化 ;彩钝化 ;镀锌 问题处理 中图 分 类 号 TQ153.15
第36卷 第5期
Vo1.36
No.5
金 属 制 品
Meta l Products
doi:10.3969/j.issn.1003—4226.2010.05.010
浅谈氯化钾镀锌的实践

②在 补充 添加剂 时 须用 温水稀 释 2~ 3倍 , 加 边 边搅拌, 确保完 全溶 解 。添加 剂补 充遵 循少 加 、 加 勤
的 原 则 , 达 到 一 定 光 亮 度 的 前 提 下 , 加 剂 尽 可 能 在 添
以少 加为 宜 , 忌 片面追求 光亮 度 而盲 目地 多加 。 切
维普资讯
・
4 ・ 0
Ma 0 6 y2 0
Eic r p a i g & P lut n Co tol e to l tn ol i n r o
V0 .6No. I2 3
・
经 验 ・
浅 谈 氯 化 钾 镀 锌 的 实 践
文斯雄 ( 阳市 12 贵 0 8信箱 , 州 贵 阳 5 00 ) 贵 5 25
2 氯 化 钾 镀 锌 工 艺 参 数 的影 响及 控 制
2 1 镀 液 主 要 成 分 作 用 与 控 制 . () 化锌 1氯
液 的操 作 温度 。常 用 的 载 体有 烷 基 醇 聚 氧 乙烯 醚 、
烷基 醇聚 氧 乙烯 、 聚氧丙 烯 Nhomakorabea醚 、 烷基 ( 或芳基 ) 聚氧 乙
烯醚 等 。载体 不仅 对主 光亮 剂助溶 、 溶 , 大允 许 增 扩
( ) 酸 3硼
硼 酸在 钾盐镀 锌液 中是 缓 冲剂 , 稳定 镀 液 的 p H
值, 且在 阴极 膜 中还能 起弱 配位作 用 , 对镀 层沉 积有
催化 作 用 。 其 含 量 允 许 范 围较 大 , 2 为 5~4 / 。 0gL 但含量 高时 , 温度偏低 时 容易结 晶析 出。 在 2 2 添加剂 的影 响和控 制 . 市售 钾 盐 镀锌 添 加 剂 种类 繁 多 , 其 作用 机 理 但
再谈氯化钾镀锌_周长虹 奥邦电镀

经 验再谈氯化钾镀锌周长虹1, 戴丽雯1, 肖洪兵1, 王宗雄2(1.武汉奥邦表面技术有限公司,湖北武汉420023;2.宁波市电镀协会,浙江宁波315016)中图分类号:T Q153 文献标识码:B 文章编号:1000 4742(2011)02 0047 030 前言氯化钾镀锌是上世纪80年代发展起来的一种光亮镀锌工艺。
近年来,我国在电镀添加剂研究开发上取得了显著进展,使得氯化钾镀锌工艺水准达到一个全新的高度,例如:LAN 930氯化钾镀锌工艺较为成功地解决了传统氯化钾镀锌工艺的3大难题:(1)镀层的耐盐雾试验性能比碱性镀锌差;(2)添加剂的分解产物多;(3)铁杂质易超标。
新型氯化钾镀锌添加剂的使用,降低了电镀生产厂商的生产成本,促进了国内电镀锌工艺朝更利于节约成本且环境友好的方向发展。
1 氯化钾镀锌成分及工艺条件的控制氯化钾镀锌工艺的常用配方的工艺条件范围是比较宽广的,其主要成分及工艺条件为:氯化锌30 ~80g/L,氯化钾180~280g/L,硼酸20~30g/L,添加剂适量,pH值4.5~6.0,10~50 。
1.1 氯化钾镀锌液主要成分的控制1.1.1 氯化锌氯化锌系主盐,溶于水中会大量放热。
当溶液的pH值 6.2时,有沉淀产生。
锌离子的质量浓度 90g/L时,光亮电流密度范围扩大,但镀液的分散能力和深镀能力会有所下降。
锌离子的质量浓度较低时,光亮电流密度的上限下降,高电流密度区易烧焦,此时的深镀能力较好,但镀层沉积速率较慢。
可增加阳极面积,同时保持镀液较低的pH值,从而使锌离子的质量浓度逐渐上升。
对挂镀而言,当氯化锌的质量浓度为60~70g/L时,镀液的分散能力最好。
氯化钾镀锌液中无强配位剂,其分散能力和深镀能力不如氰化物镀锌,更加不如无氰碱性锌酸盐镀锌。
有人喜欢在氯化钾镀锌液中加入少量氯化铵,但镀液中加入氯化铵后其分散能力和深镀能力均无改善;又会增加电镀废水的达标难度,所以当使用优良氯化钾镀锌光亮剂时,一般不建议加入氯化铵。
电镀加工:氯化钾镀锌水溶性光亮剂的研制与应用

电镀加工:氯化钾镀锌水溶性光亮剂的研制与应用现代电镀网3月28日讯:1、前言氯化钾镀锌添加剂从第一代的苄叉丙酮加载体组合,到第二代的邻氯苯甲醛加非离子表面活性剂组合,再发展到第三代的苄叉丙酮与邻氯苯甲醛合用加高温载体组合,正向着环境友好和资源节约的第四代产品组合发展。
第四代氯化钾镀锌光亮剂在原有第三代光亮剂优点的基础上,从改变操作人员的工作环境,减少环境污染出发,提高镀层分散能力及耐蚀性方面,着手研发创新。
我们根据国内外氯化钾镀锌光亮剂的发展趋势及市场对电镀加工产品提出的更高的要求出发,集众家之长,经过多年的研究,反复实验改进,在研发氯化钾镀锌水溶性光亮剂方面取得了重大突破。
氯化钾水溶性镀锌光亮剂的显著特点是:光亮剂是完全水溶性的,无刺激性气味,只在辅助剂中含少量的载体光亮剂及其他辅助光亮剂,在10℃-50℃范围内能连续生产,镀层脆性低,延展性非常好,易钝化,镀层可超过20um。
槽液中有机物含量大幅减少,降低废水处理难度及成本。
氯化钾镀锌添加剂组成包括主光亮剂、载体光亮剂、辅助光亮剂三大类。
主光剂的主要作用是出光、整平,增加光亮度。
载体光亮剂的主要作用是提高镀液的阴极极化,扩大光亮电流密度范围,并且有细化镀层结晶及良好的整平,同时兼顾溶解主光亮剂的作用。
辅助光亮剂主要作用是协同增加阴极极化,扩大阴极电流密度范围,增加低区走位与光亮度,预防高区烧焦等。
普通的主光亮剂多采用苄叉丙酮与邻氯苯甲醛,需要大量的非离子表面活性剂、载体及醇类溶剂进行溶解方能使用。
而氯化钾水溶性镀锌光亮剂则采用水溶性多醛多酮类衍生缩合物做为光亮剂。
辅助剂在载体方面,主要选用脂肪醇聚氧乙烯醚与萘酚聚氧乙烯醚经过磺化后得到的低泡的高温载体,组合使用,协同效果良好,使镀液的操作温度范围宽,镀层结晶细腻,光亮。
辅助光亮剂主要选用烟酸、肉桂酸、苯甲酸钠等。
2、氯化钾水溶性光亮剂的组成原理氯化钾水溶性镀锌光亮剂体系中的载体光亮剂主要选用我公司的最好的高温载体OCT-5、OCT-15及低泡表面活性剂OCT-14联合使用;OCT-15是目前市面上应用在氯化钾镀锌中结构最好的载体,它具有浊点高,结晶细腻,协同效果好等特点,OCT-14具有良好的分散能力。
实验四 氯化钾法镀锌

实验四氯化钾法镀锌一、实验目的学习电镀的原理和方法二、实验原理本实验为无氰电镀法,以锌片为阳极,镀件为阴极,以烧杯为电镀槽进行电镀,电镀液的主要成分为ZnCl2和KCl。
ZnCl2提供电镀所需锌离子,含量高,可以提高阴极电流密度和电流效率,并减少其他杂质的污染但会降低分散能力和深镀能力,过高会使镀层粗糙。
含量过低,浓度极差大电流密度开不大,会使光亮区变窄高电流密度区烧焦现象,一般要求40-100g/L.KCl主要起导电作用,浓度低,分散能力低,镀层光亮度下降,浓度过高引入过多氯离子,加速锌阳极自溶解,一般200g/L.H3BO3缓蚀剂,,防止镀液PH升高,25-30g/L光亮剂提高镀层光亮性,每L镀液中加入20ml为宜。
正极反应:Zn-2e=Zn2+ 2H2O-4e=O2+4H+负极反应:Zn2++2e=Zn 2H++2e=H2三、仪器与试剂直流稳压电源,滑线变阻器,烧杯,镀液,出光液,酸洗液,1:1盐酸酸洗液,硝酸四、实验步骤1.镀件前处理用砂纸打磨2片铁片去锈--除油--酸洗2.电镀按照P213图连接好装置,检查线路连接无误。
100ml烧杯中加入4/5体积电镀液,接通电源,调节电压在2.5v,调节变阻器使电流分别为0.1A,0.2,0.3,0.4,0.5,0.6,0.7,0.8,0.9A时对镀件进行电镀,时间为10min 3.镀件后处理冷水冲洗--出光液--水洗---晾干五、注意事项1.通电前,电压档开最小,电流档开最大2.导线的铜丝不能浸入电镀液,鳄鱼夹也不能接触镀液3.铁片镀件不能台靠近烧杯壁,影响锌离子的移动,影响电镀效果4.1:1酸洗时1-2s,即取出用水冲洗,倒立5.出光液浸1-2s,即水洗晾起来六、实验现象记录分析观察镀件的镀层质量镀层的颜色,致密与否,光亮程度,覆盖是否均匀等方面进行评定七、思考题1,2。
氯化钾在电镀中的作用

氯化钾在电镀中的作用嘿,朋友们!今天咱们来聊聊电镀里的氯化钾,这可不是一般的小角色,那简直就是电镀世界里的超级英雄啊!你想啊,电镀就像是给金属来一场华丽的变身秀。
而氯化钾呢,就像是那个舞台背后默默操控一切的神秘魔法师。
它一加入到电镀溶液里,就好像是给溶液注入了一股神秘力量。
电镀溶液要是没有氯化钾,就像是炒菜没放盐一样寡淡无味。
氯化钾在里面就像一把神奇的钥匙,打开了一些奇妙的反应之门。
它让溶液里的离子们就像听到了集合的号角,规规矩矩地排列起来,准备在金属表面大展身手。
它就像一个超级交通指挥官,指挥着各种离子在溶液里穿梭。
那些金属离子就像是一群小喽啰,在氯化钾的指挥下,有序地奔向金属表面。
这个过程就像是一场盛大的马拉松比赛,而氯化钾就是那个规划赛道、确保每个选手都能顺利到达终点(也就是金属表面)的组织者。
在电镀的时候,金属表面就像是一个等待装饰的大舞台。
氯化钾让电镀层像一层华丽的金缕衣一样均匀地附着上去。
如果没有它,那电镀层可能就像一个调皮的孩子画的画,这儿一块那儿一块,完全不成样子。
而且啊,氯化钾在电镀中的作用还特别稳定,就像一个老黄牛一样,勤勤恳恳地一直工作着。
不管周围环境怎么变,它都坚守自己的岗位,让电镀过程顺利进行。
它就像是电镀溶液里的定海神针,有它在,一切都稳稳当当的。
有时候我觉得,氯化钾在电镀中的角色就像电影里的超级特工。
表面上看起来平平无奇,但实际上却有着非凡的能力,能在关键时刻拯救整个电镀过程于水火之中。
它不动声色地改变着溶液的性质,就像特工悄悄改变局势一样。
要是把电镀溶液比作一个小社会,氯化钾就是那个维护社会和谐稳定的重要角色。
它让各种离子之间的关系融洽,就像居委会大妈调节邻里关系一样,让整个电镀这个“小社会”充满生机与活力。
可以说,氯化钾在电镀中的作用那是不可或缺的,就像人离不开空气一样。
它是电镀这个神奇魔法世界里的魔法棒,轻轻一挥,就能让金属展现出全新的面貌,是不是超级厉害呢?哈哈!。
氯化钾镀锌硼酸的作用

氯化钾镀锌硼酸的作用氯化钾镀锌硼酸,听上去有点拗口,但其实它可是个不折不扣的“宝贝”哦。
大家可能会问,这玩意儿到底有啥用呢?好吧,让我来给大家讲讲。
想象一下,你正在给你的植物浇水,突然看到它们生机勃勃、枝叶繁茂,那种感觉就像看见孩子考了个满分,真让人开心。
氯化钾镀锌硼酸在这方面可是个大功臣呢。
它能给植物提供必需的营养元素,像是给植物的“补品”,让它们长得更加旺盛,简直是植物界的“超级英雄”。
不仅仅是植物,氯化钾镀锌硼酸对土壤的改良也能起到意想不到的效果。
想想看,如果土壤贫瘠,植物怎么能茁壮成长呢?就像一个人没吃饱饭,肯定干啥都没劲。
氯化钾镀锌硼酸就像是一道营养丰富的菜肴,滋养着土壤,提升土壤的肥力,简直是个土壤“保养专家”。
施了它之后,土壤里的微生物活跃得就像过年一样,植物也就跟着欢快地成长。
能让土壤变得“富裕”,谁不想呢?说到镀锌,咱们也得提一提它的防腐效果。
你知道的,金属一碰水就容易生锈,像是过期的食物,没过多久就得扔掉。
而镀锌处理就像给金属穿上了“防护服”,让它在潮湿的环境中也能保持“青春”。
这样一来,氯化钾镀锌硼酸在一些农业设施中使用时,可以大大延长它们的使用寿命,省去很多麻烦。
毕竟,谁都不想花钱买设备,然后三天两头修修补补,累不累啊?再来说说它的用途,嘿嘿,不止这些呢!氯化钾镀锌硼酸在工业上也有着不小的身影。
很多行业在制造的时候都需要用到它,真的是无处不在。
它在一些化学反应中作为催化剂,助力着各种反应进行,像是无形的“助推器”。
有了它的加入,反应速度快得就像开了外挂一样,省时省力又高效,简直是工作的小能手。
氯化钾镀锌硼酸还有个神奇的地方,就是它的环保性。
咱们现在越来越关注环保,氯化钾镀锌硼酸在使用过程中,几乎不会产生任何污染物,真是为绿色地球贡献了一份力量。
就像咱们平时提倡的“少开车,多步行”,其实就是想为环境减负。
而氯化钾镀锌硼酸在这方面做得也很到位,不会对土壤和水源造成负担,真是个“环保小卫士”。
氯化钾溶液镀锌工艺
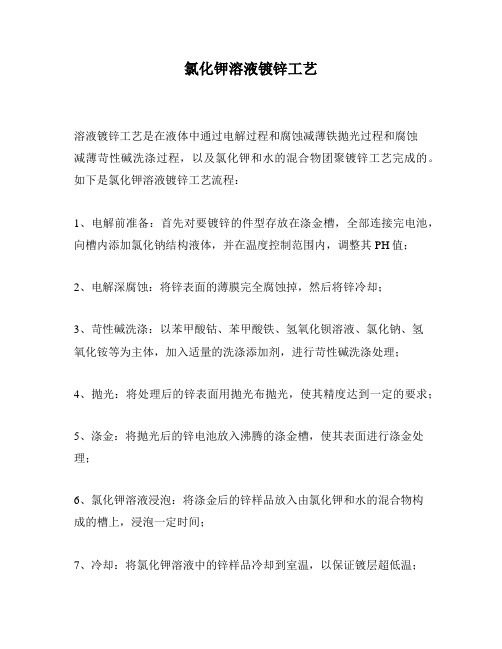
氯化钾溶液镀锌工艺
溶液镀锌工艺是在液体中通过电解过程和腐蚀减薄铁抛光过程和腐蚀
减薄苛性碱洗涤过程,以及氯化钾和水的混合物团聚镀锌工艺完成的。
如下是氯化钾溶液镀锌工艺流程:
1、电解前准备:首先对要镀锌的件型存放在涤金槽,全部连接完电池,向槽内添加氯化钠结构液体,并在温度控制范围内,调整其PH值;
2、电解深腐蚀:将锌表面的薄膜完全腐蚀掉,然后将锌冷却;
3、苛性碱洗涤:以苯甲酸钴、苯甲酸铁、氢氧化钡溶液、氯化钠、氢
氧化铵等为主体,加入适量的洗涤添加剂,进行苛性碱洗涤处理;
4、抛光:将处理后的锌表面用抛光布抛光,使其精度达到一定的要求;
5、涤金:将抛光后的锌电池放入沸腾的涤金槽,使其表面进行涤金处理;
6、氯化钾溶液浸泡:将涤金后的锌样品放入由氯化钾和水的混合物构
成的槽上,浸泡一定时间;
7、冷却:将氯化钾溶液中的锌样品冷却到室温,以保证镀层超低温;
8、烘干:将镀锌后的锌样品进行烘干,以保证样品表面没有水痕;
9、镀层质检:最后,对镀锌表面和样品进行质量检查,确保镀层质量。
溶液镀锌工艺的优点:
1、可以在暂时的抛光层后进行镀锌,有效地保护表面金属,提高物体
表面的强度;
2、可以更加平稳、可靠的产生多种形式的镀层,并且镀涂层结晶紧密,表面光洁度高;
3、操作简便,适用于更多形状的金属镀锌表面,可以大量处理。
锌酸盐镀锌与氯化钾镀锌工艺比较
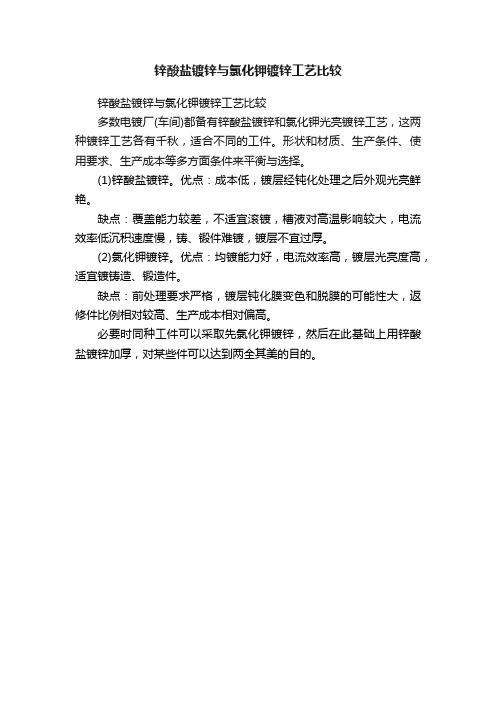
锌酸盐镀锌与氯化钾镀锌工艺比较
锌酸盐镀锌与氯化钾镀锌工艺比较
多数电镀厂(车间)都备有锌酸盐镀锌和氯化钾光亮镀锌工艺,这两种镀锌工艺各有千秋,适合不同的工件。
形状和材质、生产条件、使用要求、生产成本等多方面条件来平衡与选择。
(1)锌酸盐镀锌。
优点:成本低,镀层经钝化处理之后外观光亮鲜艳。
缺点:覆盖能力较差,不适宜滚镀,槽液对高温影响较大,电流效率低沉积速度慢,铸、锻件难镀,镀层不宜过厚。
(2)氯化钾镀锌。
优点:均镀能力好,电流效率高,镀层光亮度高,适宜镀铸造、锻造件。
缺点:前处理要求严格,镀层钝化膜变色和脱膜的可能性大,返修件比例相对较高、生产成本相对偏高。
必要时同种工件可以采取先氯化钾镀锌,然后在此基础上用锌酸盐镀锌加厚,对某些件可以达到两全其美的目的。
氯化钾在电镀中的作用

氯化钾在电镀中的作用
嘿,大家知道吗,氯化钾这玩意儿在电镀中可有着相当重要的作用呢!
先来说说电镀是啥。
就好比给一个东西穿上一件特别的“衣服”,让它变得更漂亮、更耐用。
而氯化钾在这个过程中就像是一个得力的小助手。
那氯化钾具体都干了些啥呢?它能帮助电解质更好地导电呀!这就好比是让电流在电镀这个“旅程”中能更顺畅地跑起来。
如果没有氯化钾,那电流可能就像在一条崎岖小路上艰难前行,效果肯定大打折扣啦!
它还能影响电镀层的质量呢!高质量的电镀层多重要啊,能让产品更耐磨、耐腐蚀。
氯化钾就像是一个神奇的魔法师,能让电镀层变得更加均匀、细致。
想象一下,如果电镀层坑坑洼洼的,那多难看呀,而且也不耐用,对吧?
而且哦,氯化钾的用量也不是随便来的呢。
用多了或者用少了,可能都会带来一些问题。
就跟做饭放盐一样,放多了太咸,放少了没味道,得恰到好处才行。
在实际的电镀操作中,工人们可得好好把握氯化钾的使用呢。
这就像一场精细的表演,每个环节都要拿捏到位。
总之,氯化钾在电镀中真的是不可或缺的呀!它就像是默默奉献的幕后英雄,虽然不那么起眼,但没有它还真不行呢!所以说,氯化钾在电镀中有着非常重要的作用,这一点可千万不能忽视呀!。
光亮氯化钾镀锌基本原理与实际生产(1)

在0.01 mol/L的醋酸锌Zn(C2H3O2)2溶液中,阴 极电流密度1 A/dn?时,氢气在锌上的过电位约-0.7 V[3],故,氢的析出电位为
(&2H+/H2 )析=(^2H+/H2 )平+过电位 = -0.355 V+(-0.7 V) =-1.055 V
要得到厚度均匀、结晶细致的氯化物镀锌层,选 用具有良好分散能力和深镀能力的镀锌工艺配方是 重要的,原材料和添加剂的质量同样很重要。若使用 的氯化钾、氯化锌、硼酸、添加剂等材料的质量欠佳, 就无法获得高质量的镀锌层。
1.2氯化钾镀锌的原理
1.2.1锌阳极的电化学溶解 在阳极上进行氧化反应,金属锌可能失去电子而
实用经验丨专题
Practical Experiences Special
V和1.18 V,锌的析出电位最小,根据判断反应方向 的规则,阳极首先进行电位的正直较小的氧化反应, 因此,阳极首先发生的是锌的电化学溶解。
1.2.2在阴极上镀锌时的电化学反应 在氯化钾镀锌溶液中镀锌时,阴极可能析出锌,
也可能析出氢气,谁先析出呢?这可以通过计算它们 的析出电位来决定。
溶解,氯离子、氢氧根离子可能失去电子而氧化,分别 生成氯气和氧气。
Zn -2e = Zn2+ Cl2 = 2d- - 2e 4OH- - 4e = 2H2O + O2 锌的平衡电位Ez”2+/z“见1.2.2,即-0.78 V,锌溶解 时的过电位也可以忽略不计。 根据镀锌溶液估计,KC1质量浓度约210 g/L左 右,即KC1提供的[C「] =2.82 mol/L,ZnCl2的质量浓 度约 65 g/L 左右,即]ZnCl2 ] = 0.48 mol/L,在 KC1 浓 度约1 mol/L时,25七条件下,KC1的活度系数⑵为 0.604,镀液中总C「浓度3.78,总C1「有效浓度为 (0.48x2+2.82) x0.604 = 2.283,氯气在锌上的过电位 取-0.5 Vo 氯的析出电位=Ecl2/2a-+过电位f
氯化钾镀锌的生产应用现状,及技术误区的探讨

氯化钾镀锌的生产应用现状,及技术误区的探讨氯化钾镀锌作为取代氰化镀锌的较成功工艺之一,得到广泛应用。
经30多年应用,但在生产实践中不少人仍对其缺乏深入全面的了解,对过去认知的优缺点应作重新审视;生产实践中反映出的不少问题,尚值得讨论。
在此,我结合个人实践体会,对一些问题提出看法,供同行参考。
1对工艺优缺点的重新审视当初推广氯化钾镀锌时对其优缺点有所评述,现经实践检验未必完全正确。
我人人这样认为,其主要优点有:(1)镀液呈微酸性,阴极电流效率可高达90%~95%,镀速较快,特别对铸件电镀有利;(2)镀液组分简单,易于调整;(3)相对于锌酸盐镀锌,对杂质敏感性低,允许容存量较大且易于处理;(4)比其他镀锌工艺易获得高亮度镀层,利于蓝白钝化与银白钝化;(5)镀前除油处理比锌酸盐镀锌要求低。
其原本存在及新暴露出来的主要缺点有:(1)镀层及钝化层防蚀性能在各种镀锌工艺中处于最差地位。
主要原因是为保证阴极极化,镀液中表面活性物质加入量很大,在镀层中的夹附量也很大,镀锌层纯度很差。
在发生电化学腐蚀时,因微电池作用,锌的腐蚀加快;钝化层中的有机夹杂也降低了其抗蚀力。
故该工艺不适合于防蚀性要求较高的汽车及电器产品镀锌。
(2)钝化层中因有机物夹附过多,蓝白钝化易泛彩、发花、发黄;白钝层易变灰暗,甚至长白灰、白毛;彩钝层色泽很易变淡,彩钝膜附着力远不如锌酸盐镀锌。
(3)过去认为废水处理简单而现在看来因无强配位剂,锌易处理,但废水中大量的表面活性剂成了废水处理的一大负担:即便采用成本高的活性炭处理也几乎无效,排放废水产生让人生厌的大量泡沫、必测指标化学耗氧量COD很易超标,阴离子表面活性剂ALS 也易超标。
(4)对设备腐蚀性较强,铜极杆等很易生成碱式碳酸铜。
2主要成分的控制2.1主盐氯化锌过去追求允许电流密度越大越好,实际不对。
由于镀液中无强配位剂(Cl-对Zn2+有微弱配位能力),必须保持适度的浓差极化,因而主盐浓度不能过高。
氯化钾镀锌工艺手册

氯化钾镀锌工艺手册1、氯化钾镀锌工艺规范 (2)2、镀液的配制 (2)3、主要成分的控制 (3)3.1氯化锌 (3)3.2氯化钾 (3)3.3 硼酸 (4)3.4 添加剂 (5)4、主要工艺参数的控制 (6)4.1 镀液温度 (6)4.2 镀液PH (6)4.3 搅拌 (6)4.4 电流密度 (6)4.5阳极 (6)5、镀液维护要点 (7)6、铁杂质问题 (7)6.1铁杂质的影响与判定 (7)6.2除铁方法 (7)7、加氯化铵的问题 (7)8、氯化钾镀锌常见故障及处理方法 (9)氯化钾镀锌是20世纪80年代初发展起来的一种光亮镀锌工艺。
我国近几年来添加剂开发有了显著进展,温度范围大为扩大、电流密度范围宽、分散能力和深镀能力已与碱性无氰镀锌相当,故发展速度明显加快。
近年来,电镀添加剂研究开发上取得了显著进展,使得氯化钾镀锌工艺水准达到一个全新的高度,成功地解决了传统氯化钾镀锌工艺的三大难题:(1)镀层的耐盐雾实验性能比碱性镀锌差;(2)添加剂的分解产物多;(3)铁杂质易超标。
氯化钾镀锌的优点:①氯化钾镀锌组成中无铵、无络合剂和螯合剂。
电镀废水处理比较简单。
②电流效率高达96%~99%,沉积速度快,约可增加25%~30%的产量,并可直接在难镀的基体材料如铸铁、锻钢、高碳钢等上镀锌。
③镀液导电性好,槽压低(挂镀3~5V、滚镀6~8V),能源消耗比氰化镀锌、锌酸盐镀锌低,约可节电50%之多,而且镀液操作温度宽(5~65℃),适应性很强。
④镀锌层结晶细致,具有极佳的光亮度和整平性,类似亮镍、亮铬的色泽。
⑤该工艺所得的镀层,适合低铬、超低铬钝化和三价铬钝化。
钝化膜色泽鲜艳,特别是白色、蓝白色钝化膜酷似装饰铬镀层。
⑥镀层延展性良好,加厚也不易龟裂和起泡,20μm厚的锌层无明显脆性。
⑦镀液稳定,操作维护简单可靠,镀液成本费用低廉。
氯化钾镀锌缺点:①镀液中有大量的氯离子,对设备有一定的腐蚀。
②对镀前处理要求较高,工件入槽前脱脂、除锈要干净,工件保持活化状态,才能保证锌层与基体良好的结合力。
水溶性氯化钾镀锌工艺

水溶性氯化钾镀锌工艺引言氯化钾镀锌工艺以其电流效率高、镀层光亮度好、废水中重金属离子较易处理、能在各类基材上直接电镀等优点,自上个世纪八十年代以来,在生产中的应用越来越广泛,直到占据了整个镀锌量的半壁江山。
但传统的氯化钾镀锌工艺,因为主光亮剂的溶解度问题而含有大量的表面活性剂、助溶剂等。
因此,存在镀后清洗困难、镀层中有机夹杂物多、钝化膜结合力差且易变色,生产废水中表面活性剂含量高、泡沫多、COD超标,生产区域充满刺鼻的气味等缺陷[1]。
尤其废水中COD易超标,COD处理起来甚至比氰化物还麻烦,这也是氯化钾镀锌工艺比较头疼的一个问题。
此外,光亮剂中大量使用的烷基酚聚氧乙烯醚类化合物因为降解周期长、降解不彻底等,其使用已经在欧盟受到限制。
这些都是我们电镀工作者所面临的新课题。
1 氯化钾镀锌光亮剂的发展历程和存在的问题通常使用的氯化钾镀锌光亮剂一般含有主光亮剂、载体光亮剂和辅助光亮剂三种成分。
在这些成分中,主光亮剂通过改变结晶结构使镀层结晶更加细致并呈现光亮外观;载体光亮剂的作用是增溶不溶于水的主光亮剂,使其均匀地分散到镀液中,同时能明显提高镀液的阴极极化,使镀层结晶细致[2];辅助光亮剂能使镀层光亮区向高、低电流密度区双向扩展,使镀层的光亮度进一步提高[3-4]。
主光亮剂为分子中具有共轭羰基的芳香醛、酮,使用最多的是苄叉丙酮、邻氯苯甲醛等。
载体光亮剂为烷基聚氧乙烯醚、烷基酚聚氧乙烯醚、烷基聚氧乙烯聚氧丙烯醚等非离子型表面活性剂,以及它们磺化后的阴离子型表面活性剂。
以前使用的化合物的结构通式是:R1O-(-C2H4O-)n-R2,其中R1是不同长度的直链或支链烷基、或烷基苯环、烷基萘环等;R2是H或磺酸基团或磺基取代的其他基团,如低聚度环氧丙烷等;n是聚合度,介于3~30之间。
辅助光亮剂则包括低电流区光亮剂、增光剂等,如苯甲酸钠、肉桂酸、烟酸、NNO、NMS、糖精等。
有人根据使用的主光亮剂和载体光亮剂的发展时期,将氯化钾镀锌光亮剂分为三代[5]。
氯化钾镀锌及三价铬钝化工艺的应用

应用技术氯化钾镀锌及三价铬钝化工艺的应用顾卫忠,沈婉萍(上海应用技术学院,上海200235)摘 要:提出了氯化钾镀锌和三价铬钝化工艺,能满足大多数镀锌件的装饰、防护和不含Cr6+的要求。
使用自行配制的添加剂能降低生产成本。
并阐述了工艺中各组分及操作条件的影响和控制。
认为溶液对钝化的影响较小,而操作条件的影响较显著。
只要协调好p H、温度、时间三者关系,能稳定地获得蓝色均匀、符合要求的钝化膜。
提出了钝化液中Fe3+控制的措施和处理的方法。
关键词:电镀;镀锌;三价铬;钝化中图分类号:TQ153.1;TG178 文献标识码:A 文章编号:10052748X(2008)0320137203 Pota ssium Chloride Zinc Pla ting and Trivalent Chromium Passiv a tion TechnologyGU Wei2zhong,S H EN Wan2pi ng(Institute of Shanghai Tec hnology,Shanghai200235,China)A bstract:The technology of potassium chloride zinc plating a nd trivale nt chromium pa ssivation is satisf actor y fordecoration and protectio n of mo st zinc pla ted pa rts and Cr6+f ree require me nt.U sing certain raw chemical s a s additive s can lower t he pla ting cost.The eff ect of bath compo sition and t he control of ope rating conditions are discussed.The trivale nt chromium pa ssiva tio n is le ss affect by the ba th a nd mar kedly by the ope rating conditio ns.As long as the three factor s of p H,temper ature and time are well cont rolled,a unifor m bluish film ca n be stably obtained.The measures of controlling Fe3+are proposed.K ey w or ds:electroplating;zinc pla ting;trivale nt chromium;pa ssivation0 引 言近年来镀锌工艺主要有氰化物镀锌、锌酸盐镀锌、酸性氯化钾镀锌三大种。
氯化钾镀锌使用至今

氯化钾镀锌使用至今,虽保留了一些优点,但也逐渐暴露出其镀层防蚀力差、彩钝层结合力差且色泽易变淡、废水中富含的有机物难以处理等缺点。
强调在工艺维护、主光剂选择、杂质处理及减少氨氮引入、工艺适用范围等方面予以特别关注。
0前言氯化钾镀锌作为取代氰化镀锌的较成功工艺之一,得到广泛应用。
经30多年应用,不少人仍对其缺乏深入全面的了解,对过去认知的优缺点应作重新审视;生产实践中反映出的不少问题,尚值得讨论。
笔者是国内较早采用该工艺者之一。
在此,结合个人实践体会,对一些问题提出看法,供同行参考。
1对工艺优缺点的重新审视当初推广氯化钾镀锌时对其优缺点有所评述,现经实践检验未必完全正确。
现可这样认为,其主要优点有:(1)镀液呈微酸性,阴极电流效率可高达90%~95%,镀速较快,特别对铸件电镀有利;(2)镀液组分简单,易于调整;(3)相对于锌酸盐镀锌,对杂质敏感性低,允许容存量较大且易于处理;(4)比其他镀锌工艺易获得高亮度镀层,利于蓝白钝化与银白钝化;(5)镀前除油处理比锌酸盐镀锌要求低。
其原本存在及新暴露出来的主要缺点有:(1)镀层及钝化层防蚀性能在各种镀锌工艺中处于最差地位。
主要原因是为保证阴极极化,镀液中表面活性物质加入量很大,在镀层中的夹附量也很大,镀锌层纯度很差。
在发生电化学腐蚀时,因微电池作用,锌的腐蚀加快;钝化层中的有机夹杂也降低了其抗蚀力。
故该工艺不适合于防蚀性要求较高的汽车及电器产品镀锌。
(2)钝化层中因有机物夹附过多,蓝白钝化易泛彩、发花、发黄;白钝层易变灰暗,甚至长白灰、白毛;彩钝层色泽很易变淡,彩钝膜附着力远不如锌酸盐镀锌。
(3)过去认为废水处理简单而现在看来因无强配位剂,锌易处理,但废水中大量的表面活性剂成了废水处理的一大负担:即便采用成本高的活性炭处理也几乎无效,排放废水产生让人生厌的大量泡沫、必测指标化学耗氧量CODCr很易超标,阴离子表面活性剂ALS也易超标。
(4)对设备腐蚀性较强,铜极杆等很易生成碱式碳酸铜。
A02-330酸性氯化钾镀锌光剂使用说明书

A02-330酸性氯化钾镀锌光剂使用说明书一、特点➢光亮剂溶解性好,泡沫量少,镀层白亮,易于钝化,抗变色性能好➢可操作的电流密度范围广,有极佳的深镀能力,适用于有深凹孔位的复杂工件。
➢镀液浊点高,温度操作范围广,镀层延展性好,不起泡。
➢抗杂能力好,具备好的耐盐雾性能。
三、镀液的配制方法1、配槽用的原材料尽可能选用纯度较高的材料。
氯化钾应采用淬火级或电镀专用级,氯化锌易采用品牌或大厂产品。
2、先用5倍于硼酸重量的80℃以上热水完全溶解计算量的硼酸。
3、用总体积50%的水溶解计算量的氯化钾、氯化锌,充分搅拌至完全溶解。
然后将溶好的硼酸溶液加入,搅拌均匀,加水至规定体积。
4、加入1-2g/L的锌粉,搅拌2小时,再加1-2g/L的活性碳强力搅拌,静置数小时至镀液澄清,进行过滤,过滤后小电流电解数小时。
根据所取镀液打霍尔槽试片情况确定是否进行下一步操作。
若打片合格,可调整镀液PH值至规定范围,加入光剂进行电镀;若不合格,继续进行弱电解处理。
5、添加光剂时,须事先用5倍的水稀释后再加入槽内镀液中,搅拌均匀。
四、镀液的维护1、主盐的控制应定期化验氯化钾、氯化锌及硼酸含量,根据化验结果,补充欠缺的成分。
将其控制在工艺范围之内。
2、光剂的用量及补给光剂的添加应遵循少加勤加的原则,最好在添加前用水或槽液稀释5倍后添加。
光剂的添加量一般按照电镀所用电量千安小时耗量补入。
A02-330光剂的消耗数据如下:A02-330A光亮剂150-200ml/ KA·h,A02-330B柔软剂50-100L ml/KA·h。
光剂的消耗不仅与用电量——KA·h(千安培·小时)有关,还与工件的形状及光亮度、电流密度大小、镀液温度高低、锌离子浓度高低等相关。
以上光剂消耗量数据是指我们推荐的最适合的操作参数来说的,实际生产中光剂的维护可通过定期做赫尔槽试验来判断和加入。
3、镀液中有害杂质的处理镀液中的有机杂质主要为光剂的分解产物,当其在镀液中积累到一定量时,会使镀层变暗,内应力增加。
锌添加剂

锌添加剂:镀锌电解液的基本类型—氯化钾镀锌工艺及操作条件氯化钾镀锌工艺及操作条件(一)镀液基本成分及作用1.氯化锌氯化锌为主盐,它易吸潮、易溶解,有放热现象。
氯化锌提供锌离子,ZnCl2的含量取上限时,能提高阴极电流密度;ZnCl2的含量取下限时,能提高分散能力,减少镀件带出液的损失,并降低配槽和废水处理的成本。
ZnCl2的含量过低时,浓差极化较大,导致电流开不大,会使光亮区变窄,高电流密度区易出现烧焦现象。
对于较难电镀的基体金属,如铸铁件,锌含量可取上限值,以增加阴极极限电流密度;夏天锌含量可取下限值。
氯化锌的浓度可在40~80g/L范围内变动,原则上挂镀时比滚镀时含量高一些。
有阴极移动的挂镀槽,氯化锌含量以55~65g/L为好;没有阴极移动装置,则氯化锌含量以65~75g/L为好。
滚镀锌时的氯化锌含量,控制在40~55g/L为好。
2.氯化钾氯离子对锌虽有微弱的配位作用,但氯化钾在溶液中主要是起导电作用。
浓度一般控制在180~230g/L,而尤以185~210g/L为好。
氯化钾的浓度过高,冬天5℃以下时会有结晶析出。
氯化钾浓度过低,不但导电性差,而且镀液的分散能力也降低,镀层的光亮度也差。
KCl应定期分析,定期补加。
一般KCl浓度控制在200g/L左右。
3.硼酸和醋酸硼酸的主要作用是抑制镀液pH值的升高,能使镀层均匀光亮。
硼酸含量偏低,电流密度上限低,镀层容易烧焦,导致镀层粗糙。
为稳定镀液的pH值,保持适当的硼酸含量是必要的。
但硼酸含量又不宜太高,在一般的温度下,超过45g/L就会结晶析出沉淀。
所以硼酸适含量为25~30g/L,冬天取25g/L为宜。
夏天,硼酸适含量可提高到30~35g/L。
此外要注意硼酸品质,严防硝酸根等的干扰。
醋酸的加入,也起缓冲剂作用。
醋酸根还有扩大电流密度范围和提高分散能力的作用。
一般用得较少。
4.主盐成分变化对电镀技术参数的影响氯化锌是锌离子的供给者,氯化钾在氯化物镀锌溶液中,既是导电盐,又是锌离子的弱配位体。
- 1、下载文档前请自行甄别文档内容的完整性,平台不提供额外的编辑、内容补充、找答案等附加服务。
- 2、"仅部分预览"的文档,不可在线预览部分如存在完整性等问题,可反馈申请退款(可完整预览的文档不适用该条件!)。
- 3、如文档侵犯您的权益,请联系客服反馈,我们会尽快为您处理(人工客服工作时间:9:00-18:30)。
() 1装篮一 ( ) 2化学除油一 ( ) 3 热水洗一 ( ) 4 流动水冼一 () 5 热 mi后取出钝化 、 干 n 烘 然后 夹在 台钳 中反复弯 曲直 至基 体和镀 浓盐酸酸洗 一 【 ) 动水 洗一 ( ) 6流 7 活化 一 ( ) 8 镀锌 一 ( ) 动 水 层 9流 洗一 l0 热水烫洗一 ( I甩干一 (2 除氢一 (3脱膜一 (4 流动 1) 】) 1) 1) 1) (9 检验一(0 老化一 ( 1装箱 。 1) 2) 2) 非弹性零件不经 1 ~1 1 3工序。 的试件置 人 2 ( D℃电热烘 箱中恒 温 3 i. 后立即取 出投 人冷 0m n然
} d } h l Ⅱ ・ T
2 镀 锌 工 艺
2 1 镀液成 分及 工艺 流程 .
工 艺参 数 吊镀
() 电 流密 度 采用 27 n 5 6 d霍 尔 槽镀 液 , 片规格 10 斌 ( / ml 6 ix1mt碳钢 试片 . i× 0ml i l l t 电镀有 效面积 0 5(l 槽 液温度 . I2 |. l 2 3℃ , 电镀时间为 1 i。当外加 电流为 IA时 . 0mn 锌镀层 光亮 区 的电流密 度范 围是 1 / i ; —5A d z 当外加 电流 为 2A 镀层 光亮 区的 n .
() 结台力 1 ( )弯曲试验 a 将 1 i×2 i×】衄n试 0ml 0mt l t 件挂 八槽 温为 2 1℃的镀液 中, 在外加 1A的电流条件 下电镀 l 5 起断 裂 口处 无镀层脱 落。( )骤拎试 验 断 b 晦 镀锌钝化 后
阴极移动
8 0次/ i ~1 mn
“
条件 : 槽温 2 2℃ , 施加总电流 2A, 电镀时间 1 i 镀层厚度采 0mn 0 “ 5 0 用 s H数字 测厚仪测试 , c_ 其结果 为 4 % 25 () 深镀能力 2 将 ∞ ml的弹 簧钢丝 绕制 成 帖 ml×2 i l i ( l D
_ l
我厂 曾选用 P M型低应力氯化钾镀锌 替代氰 化物镀镉 工艺 ,
2年 5 月
M AT口姒 料 保 材 L PR 护 ON S OTEc 1 1
.5 N . 3 o 5
M8 0 2 .2 O V
氯 化 钾 镀 锌 工 艺 的 应 用
王朝铭 , 刘 艳
( 义长征 电器 电镀 厂 . 州 遵 义 53 0 ) 遵 贵 6 0 2
了添 加 剂 质 量 不稳 定 的 问题
( ) 电流效率 3
采用 5 ix2 i×2ml的钢试片 . 0ml 5ml i l l l 经酸
清洗 烘干后置 于分析天平 中称重 , 然后 , 取出拄 人 2 2℃镀液 然而 . 无论采用 P M型还是氯锌 1 型氯化钾 添加剂 的电镀 洗 、 号 外加电流 1 , 电镀 3 i A 0mn并取 出清诜 、 烘干 、 称重 , 所得 镀层 液, 弹性零件 的端部 由于 电流密度分 布相对较 大而 易烧 焦 . 降低 中 , 的重量 与 理 沦上 算 出 的 镀层 重 量 之 比再 乘 1 % . 结 果 为 0 0 其 了镀锌零件 的台格率 。2 年初 . 厂采 用 自制 的 C ( D1 我 Z一2 A型氯 化钾镀锌添加剂 , 大批量用 于弹性零 件和非 弹性 零件 镀锌 生 产。 实践证 明, 该添加剂陈 了具 有与氯锌 1 添加 剂相 同的性 能 外 号 主要优点是 : 液 电流密度 大 , 件 边缘 不易烧 焦 , 镀 零 易维 护 和管
[ 关键词 ] 电镀锌 ; : 蒂加荆 ;氢脆 [ 中图分类号 ] T I28 G 7 .2 [ 文献标识码 ] B [ 文章编号] 10 —16 (C  ̄0 0 5 — 2 ( 1 50 20 )S一 0 2 0 / '
1 前
言
“) 均镀能力
采用 霍尔槽 阴极 试样 ( 8 法 ) 一测试 即
值
巩 (L d 2 :/i ) n
1 ~2 5 0 10 6 4 ~10
55 ~6 2
0 2 50 ~
() 浊点 6
取 卯 【 镀 液倒 人玻 璃试管 中 【 I l 边搅拌 边水浴加
热至镀液开始变浑浊并记录 当时的温度 . 镀液的浊 氧为 8 o
2 3 镀 层 . 性能
电流 密 度 范 围 是 1 /i 。 ~8A d 2 n
氯化锌 氯化钾
硼 酸
( L j ( L J
( L 1
6 ~7 0 0 20 1 0 ~20
2 ~3 5 5
c 一A 配槽) ( lL z2 ( m/ ) ( 2( z一A 补充) 【 lk ) m/  ̄ h
解决 了弹性零件无氰镀锌不能除氢 处理 的难题 , 并获得 了很 好的 经济效益 和社 会环境效 益 l l :但 由于制造 P M型氯化 钾镀 锌添
ml的紧密拉簧零件竖直悬挂在 电镀槽 中 与锌 阳极 板平行 ; i l 电镀
1 电流密度按 2, m 施加(  ̄d z 无阴极移动 槽 液温度为 ; 加剂的原材料 购买困难 . 质量很难 保证 , 后来选 用 氯锌 】 号氯化 件共 20件 ; 2 5℃ ; 电镀时问 3 i, 0r n其结果镀件内孔 全部 镀上 a 钾镀锌添加剂 通过大量的对比试验后 . 取代 了 P 添加剂 . M 解决
理 , 加 荆 生 产 消耗 低 , 量稳 定 添 质
9 7%
( ) 沉 积速 度 4
将标准 的 0 3d 的试样挂人 2 . Ⅱ 3℃的镀液
中 外加 l A电流并 电镀 3 i 0mn后取出清洗。烘干称重减 除试件 镀前重量得 到锌 镀层重 量 。再 除 以 0 0 1gd z 一并 计算 出 : .7 , m / 当试 件 的 电流 密 度 为 3 / 时 , 层 的 沉 积 速 度 为 5 3 l d ^ 镀 l