纤维环向缠绕复合材料气瓶冲击损伤容限研究
UHMWPE纤维缠绕铝内衬复合材料气瓶爆破压力预测
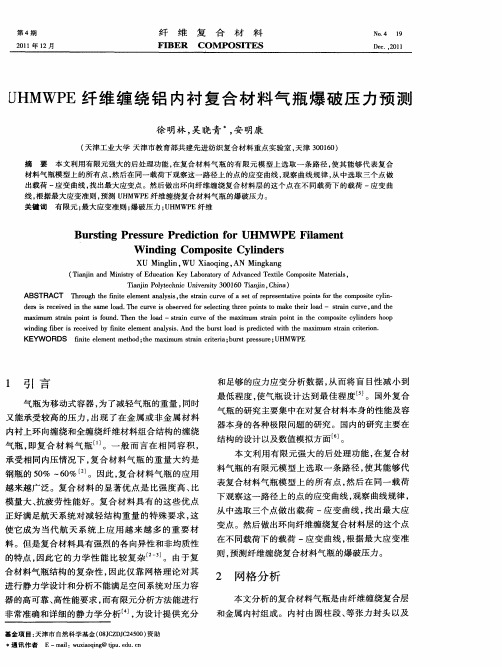
21年 1 01 2月
纤
维
复
合
材
料
No 4 .
1 9
FI BER Co M [ S TES Po I
De ., 0 1 c 2 1
L T HMWP E纤 维 缠 绕 铝 内衬 复 合 材 料 气 瓶 爆 破 压 力 预 测
徐 明林 , 吴晓青 , 明康 安
( 天津工业大学 天津 市教育部共建先进纺织 复合 材料重点实验室 , 津 3 0 6 ) 天 0 10 摘 要 本 文利用有 限元强 大的后 处理功能 , 复合 材料气 瓶 的有限元 模型上 选取一 条路径 , 其能够代 表复合 在 使
ma i m t i o n sf u d T e h o d—sr i u e o h x i m tan p i ti h o o i y i d r o p x mu sr n p i ti 0 n . a h n tela t n c r ft e ma mu s i o n n t e c mp st c l e h o a v r e n s w n ig f e sr c ie y f i l me t n l ss A d t e b r t o d i rd c e i h xmu s a n c t r n i d n b ri e ev d b i t ee n a y i. n h u s a sp e itd w t t e ma i m t i r e o . i n e a l h r i i
d r sr c ie n t e s le la . h u v so s r e o e e t g tr e p i t k h i a e s i e ev d i an d T ec re i b ev d frs l ci e o n st ma e te r o d— sr i u e a d te h o n h o l tan c r , n h v
压缩天然气纤维环缠绕气瓶外观检验标准

压缩天然气纤维环缠绕气瓶外观检验标准1范围本标准规定了汽车用压缩天然气金属内胆纤维环缠绕气瓶(以下简称:气瓶)的定期检验与评定的基本方法和技术要求。
本标准适用于公称工作压力为20或25MPa,公称水容积为30~450L,工作温度为-40℃~6℃的气瓶。
本标准适用本公司所有改装车辆。
2术语和定义磨损:因摩擦使材料磨损或擦伤而引起气瓶或附件的损坏。
冲击伤:强烈地撞击气瓶表面,可能会导致表面划伤、凿伤和凹痕等冲击伤。
冲击也可能导致缠绕层出现分层损伤,这种损伤在外观检查时很难被发现。
龟裂:树脂部分出现不透明的“霜状”细裂纹。
划伤:由尖锐器物进入气瓶表层而引起的损伤。
分层:在缠绕层之间发生分离的损伤。
分层通常是由于过大的载荷垂直冲击缠绕层材料表面而引起的损伤。
外涂层:气瓶表面透明的或有颜色的用于防护瓶体或改善外观的涂层。
螺旋缠:与气瓶轴向有一定夹角的圆周方向的缠绕。
环向缠绕:在气瓶圆柱部分进行环向缠绕。
增强纤维束的缠绕方向与气瓶的纵向约成90°。
一级损伤:在正常使用中发生的微小损伤。
这种损伤对气瓶的安全没有构成有害的影响,可继续使用。
在金属表面的涂层划伤或划痕没有明显深度,或缠绕层表面涂层和树脂有较小损伤,但没有明显纤维破损的现象均可判定为这类损伤。
二级损伤:损伤程度比一级损伤严重,但可以进行修复。
三级损伤:三级损伤的气瓶不能再继续使用也不能进行修复。
增强纤维:在复合材料中的连续纤维束,如:碳纤维、芳纶纤维及玻璃纤维,在压力作用下起承载作用。
修复:修理气瓶使其复原或达到一级损伤的程度。
树脂:用于粘接和固定纤维在指定位置的材料。
树脂通常是热塑性或热固性树脂。
应力腐蚀裂纹:由载荷和恶劣环境共同作用造成材料开裂。
缠绕层会出现垂直于纤维的裂纹或裂纹群。
3外观检查与评定损伤的证据外观检查气瓶表面是确定气瓶损伤的主要方式。
可能引起损伤的证据有如下各点:——腐蚀——划伤——擦伤——凿伤——纤维暴露——凹坑——凸起——破裂——材料损失——气瓶表面褪色(积碳、碳化、化学品浸伤等)——暴露于热环境的痕迹——冲击或事故——表面材料的损耗损伤级别无损伤或一级损伤不要求修复,可继续使用。
碳纤维缠绕复合材料气瓶的有限元数值分析的开题报告
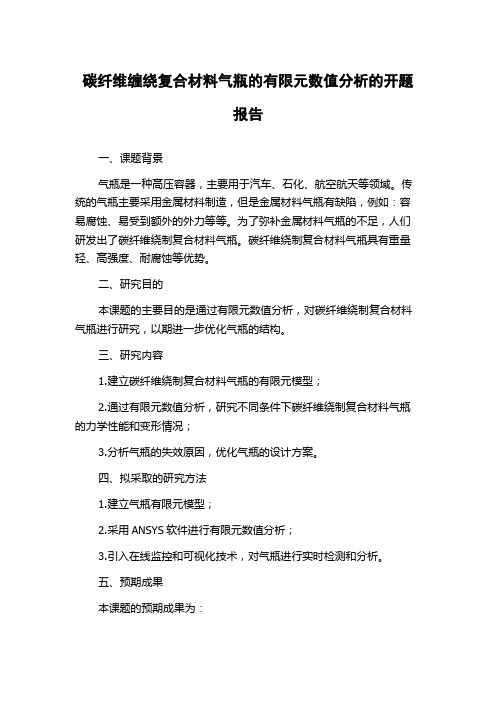
碳纤维缠绕复合材料气瓶的有限元数值分析的开题
报告
一、课题背景
气瓶是一种高压容器,主要用于汽车、石化、航空航天等领域。
传统的气瓶主要采用金属材料制造,但是金属材料气瓶有缺陷,例如:容易腐蚀、易受到额外的外力等等。
为了弥补金属材料气瓶的不足,人们研发出了碳纤维绕制复合材料气瓶。
碳纤维绕制复合材料气瓶具有重量轻、高强度、耐腐蚀等优势。
二、研究目的
本课题的主要目的是通过有限元数值分析,对碳纤维绕制复合材料气瓶进行研究,以期进一步优化气瓶的结构。
三、研究内容
1.建立碳纤维绕制复合材料气瓶的有限元模型;
2.通过有限元数值分析,研究不同条件下碳纤维绕制复合材料气瓶的力学性能和变形情况;
3.分析气瓶的失效原因,优化气瓶的设计方案。
四、拟采取的研究方法
1.建立气瓶有限元模型;
2.采用ANSYS软件进行有限元数值分析;
3.引入在线监控和可视化技术,对气瓶进行实时检测和分析。
五、预期成果
本课题的预期成果为:
1.建立碳纤维绕制复合材料气瓶的有限元模型;
2.得出不同工况下气瓶的力学性能和变形情况;
3.分析气瓶的失效原因,优化气瓶的设计方案。
六、结论
本课题的研究结果将为碳纤维绕制复合材料气瓶的设计和制造提供有力支持,具有较高的实用价值。
纤维缠绕复合材料气瓶研究进展

第39卷第4期应用科技V ol.39, No.4 2012年8月Applied Science and Technology Aug. 2012 doi:10.3969/j.issn.1009-671X.2012.04.005纤维缠绕复合材料气瓶研究进展徐君臣, 银建中连理工大学化工机械学院,辽宁大连116024摘要:纤维缠绕复合材料气瓶具有高比强度和比模量、抗疲劳、抗腐蚀等优点,已经成为研究的焦点. 文中分析了纤维缠绕复合材料气瓶在国内外的研究进展,并进行了归纳总结,主要内容包括:纤维缠绕复合材料气瓶的国内外标准、制造过程中应考虑的主要因素、失效准则、失效模式以及优化设计. 通过对比发现,Tsai-Wu失效准则预测的失效压力与实验值最接近. 提出了一些预防复合材料气瓶失效的措施,对气瓶的安全使用有一定的借鉴作用. 最后指出了未来研究的重点.关键词:复合材料气瓶;纤维缠绕;失效准则;失效模式;优化设计中图分类号:TQ 053.2文献标志码:A文章编号:1009-671X(2012)04-0004-09Progress in Filament-wound Composite gas CylindersXU Jun-Chen, YIN Jian-ZhongSchool of Chemical Machinery, Dalian University of Technology, Dalian 116024, ChinaAbstract:Filament-wound composite gas cylinders have become a research focus because they exhibit many advantages such as high strength-density and stiffness-density ratios, and excellent resistance to fatigue and corrosion. This review summarizes the progress in filament-wound composite gas cylinders at home and abroad. The domestic and abroad standards, consideration the main factors in manufacturing process, failure criteria, failure mode and optimal design of filament-wound composite gas cylinders are discussed here. By comparison, it was found that the Tsai-Wu failure criterion leads to most accurate failure pressure among all failure criteria. Some measures are put forward to prevent the failure of composite gas cylinders and it is very important to improve composite gas cylinders safety. The future research is summarized finally.Keywords:composite gas cylinders; filament wound; failure criterion; failure mode; optimal design随着科学技术的发展,复合材料已广泛应用在航空、航天、能源、化工、海洋工程、生物医药、武器工业等领域. 在日益崇尚环境友好的今天,燃油汽车的使用导致能源枯竭和城市环境污染已引起全球的关注. 各国政府正在采取各种措施来解决这一问题,措施之一就是使用清洁燃料,如压缩天然气(compressed nature gas,CNG)和H2等,代替柴油和汽油;但这些清洁燃料需要使用压力容器. 一般使用钢制气瓶,这势必会增加车重、占用货箱的空间以及增加汽车行驶的能耗等. 采用纤维缠绕复合材料气瓶代替传统的钢制气瓶能够克服上述缺点,已经成为研究的热点.纤维缠绕复合材料气瓶具有以下优点:1)气收稿日期:2012-01-10.作者简介:徐君臣(1987-), 男,硕士研究生,主要研究方向:复合材料压力容器,E-mail:jzyin@.瓶重量轻、刚性好、强度高;2)金属材料的疲劳破坏通常是没有明显预兆的突发性破坏,而复合材料中的增强物与基体的结合既能有效地传递载荷,又能阻止裂纹的扩展,提高了气瓶的断裂韧性;3)复合材料中的大量增强纤维使得材料过载而少数纤维断裂时,载荷会迅速重新分配到未破坏的纤维上,使整个气瓶在短期内不至于失去承载能力;4)复合材料气瓶在受到撞击或高速冲击发生破坏时不会产生具有危险性的碎片,从而减少或避免了对人员的伤害;5)无需特殊处理就能满足耐腐蚀的要求.纤维缠绕复合材料气瓶一般由金属内衬、纤维、树脂等组成. 复合气瓶内衬内壁直接与介质接触,它的主要作用是气密、防腐、耐温和耐压;因此要求内衬材料具有良好的气密性、耐腐蚀性、耐温和高强度、高韧性等特点. 常用的内衬材料有铝·2·应用科技第39卷和塑料2种. 纤维缠绕增强复合材料层的主要作用是保证气瓶在受力的情况下,具有足够的强度、刚度和稳定性. 复合材料缠绕层承担绝大部分(75%~95%)的压力载荷,其中纤维是主要的承载体,树脂对纤维起粘结作用,并在纤维之间起着分布和传递载荷的作用;因此,选择高强度、高弹性的增强纤维和性能良好的树脂是提高结构承载能力的重要措施. 通常采用高强玻璃纤维环氧树脂或碳纤维环氧树脂和凯夫拉(Kevlar)纤维环氧树脂等高性能复合材料.复合材料气瓶一般采用2种分类方法,一是按照应用领域分为:1)天然气、氢气等燃料汽车的燃料气瓶;2)用于呼吸器系统,包括背负式呼吸器、小型呼吸器以及逃生用的呼吸面具等;(3)用于航空或航海,主要包括逃生滑梯充气装置和航空吸氧装置等. 二是按内胆材料和增强材料分类:按内胆材料可分为金属内胆缠绕气瓶和塑料内胆缠绕气瓶;还可以按增强材料分为高强玻璃纤维缠绕气瓶、碳纤维缠绕气瓶、芳纶纤维缠绕气瓶等. 由于铝内胆具有密封性好、抗疲劳性能强、循环寿命长、稳定性高及质量轻等优点,目前在碳纤维缠绕气瓶中得到了广泛的应用.1复合材料气瓶标准国际上对于复合材料气瓶没有统一的标准. 目前使用较多的标准有美国制定的DOT-CFFC《铝内衬全缠绕碳纤维增强复合气瓶的基本要求》,气瓶的最大水容积≤90.7 L,工作压力≤34.5 MPa. 美国国家标准所(ANSI)于1992年8月首次出版了NGV-2天然气汽车储气瓶标准,该标准包括了金属环向缠绕、金属内胆全缠绕、非金属内胆全缠绕. 对非金属内胆全缠绕,玻璃纤维的安全系数是 3.5,芳纶纤维是 3.0,碳纤维是 2.25. 1989年ISO/TC58/WG17也着手《车用压缩天然气气瓶》国际标准的制定工作,于1992年提出标准草案,经过多次修改,ISO 11439《车用压缩天然气高压气瓶》现已被中国在内的世界上大多数国家认可,标准第1版已于2000年9月正式颁布,它包括CNG-1金属气瓶、CNG-2金属内胆环向缠绕气瓶、CNG-3金属内胆全缠绕气瓶和CNG-4塑料内胆全缠绕气瓶. 此标准是在过去20年来各国经验的基础上制定的,因此目前国内车用压缩天然气气瓶也参考该标准. 国际标准化组织ISO于2002年批准了纤维缠绕复合气瓶标准——ISO 11119《复合结构气瓶−规范和实验方法》. 该标准主要包括环向缠绕复合气瓶、承载金属内胆纤维增强全缠绕复合气瓶、非金属内胆和不承载金属内胆纤维增强全缠绕复合气瓶. 此标准适用于容积450 L以下的容器,用于储存和运输压缩气体和液化气体,其水压实验压力≤65 MPa. 缠绕的纤维可为碳纤维、玻璃纤维、有机纤维或其混杂,但对环向缠绕标准中规定也可采用钢丝缠绕进行周向加强. 关于碳纤维复合气瓶主要的欧洲标准是英国HSE-A1-FW2以及欧洲大陆已批准的衍生版本——欧洲标准化技术委员会(CEN)编制的复合气瓶规范EN 12245-2002《可运输气瓶−全缠绕复合材料气瓶》,以及EN 12257-2002《可运输气瓶−无缝环向缠绕复合材料容器》等. 我国关于纤维缠绕复合材料气瓶的标准比较少,很多企业都参考国外标准,通过消化吸收国外先进技术和标准,制定了企业内部的标准. 我国参考国外的标准以及实际的生产和使用经验制定了GB 24160-2009《车用压缩天然气钢制内胆环向缠绕气瓶》. 该标准适用于设计、制造公称工作压力为20 MPa或25 MPa,公称水容积为30~450 L,工作温度为-40~65 C,设计使用寿命为15年的缠绕气瓶. 该标准还给出了试验方法和检验规则等. 内胆需要进行的试验项目有底部密封性试验、拉伸试验、冲击试验、冷弯试验、金相检查、底部解剖、无损检测、水压爆破试验等;缠绕气瓶需要进行的试验项目有缠绕层层间剪切强度试验、缠绕层抗拉强度试验、缠绕层外观试验、水压试验、水压爆破试验、气密性试验、常温压力循环试验、极限温度压力循环试验、加速应力破裂试验、枪击试验、火烧试验、裂纹容陷试验、酸环境试验、未爆先漏试验、高温蠕变试验等. 而我国至今还没有关于全复合材料CNG车用气瓶的技术标准. 为此,应在有关厂家生产实践的基础上,参照国外先进标准以及国内使用特点,尽快制定出此类气瓶的制造标准、定期检测标准和安全评定标准.2复合材料气瓶的制造复合材料气瓶的纤维增强层主要的作用是承受压力,所以纤维层对复合材料的力学性能有很大的影响. 在制造复合材料气瓶时纤维增强层主要考虑的因素有气瓶的缠绕张力、铺层顺序、缠绕角度、缠绕厚度、纤维缠绕的线型等.复合材料气瓶在缠绕制造过程中需要对纤维施加一定的张力,一方面是为了使纤维在内胆上按第4期徐君臣,等:纤维缠绕复合材料气瓶研究进展·3·照设计线型排列,另一方面是为了使气瓶内胆和缠绕层产生一定的预应力,从而改善气瓶的抗疲劳性能. 陈汝训[1]提出影响纤维强度发挥的重要原因是沿气瓶厚度方向各纤维受力不均匀,而缠绕张力又是纤维受力不均匀的重要因素,对壁厚较厚的气瓶尤其如此;因此,如何合理控制缠绕张力是提高气瓶纤维强度发挥的重要环节. 张宗毅[2]等提出了一种等效降温法,将缠绕张力产生的预应力等效为复合材料层降温产生的预应力,并通过有限元软件研究了缠绕张力对环向缠绕复合材料气瓶应力的影响. 研究结果表明:随着缠绕预应力的增大,环向缠绕复合材料气瓶内胆工作应力减小,复合层工作应力增大,缠绕张力产生的预应力较大时会抵消自紧工艺的效果. 王欣荣[3]研究了缠绕张力对碳纤维缠绕铝内胆复合材料气瓶爆破压力的影响,模拟结果表明有缠绕张力气瓶的爆破压力比无缠绕张力气瓶的爆破压力提高了3.03%. Cohen[4]采用实验设计方法确定了在缠绕工艺过程中纤维预应力对缠绕结构力学性能的影响,发现提高预应力可以有效增加在纤维缠绕结构中缠绕层的纤维体积百分比,从而提高结构的强度.Kalaycioglu等[5]研究了凯夫拉纤维缠绕6061-T6铝内衬的复合材料气瓶,主要集中在纤维的缠绕角度连续变化时,对称与非对称的铺层顺序对气瓶性能的影响,结构如图1所示. 研究结果表明,对称的铺层顺序相对于非对称的铺层顺序爆破压力提高了15%,主要是因为对称的铺层顺序使得气瓶纤维层的应力分布得更加均匀,减少了应力集中. Bertin等[6-7]对聚合物复合材料储氢气瓶进行了实验和模拟研究,主要集中在复合层的铺层顺序对复合材料力学性能的影响上,研究结果如表1所示. 从表中结果可以看出,对称的铺层顺序失效应力值最大. Velosa等[8]研究了以聚乙烯为内衬玻璃纤维缠绕的复合材料气瓶,结果发现纤维的方向、铺层的顺序和铺层的层数都会对纤维缠绕层的强度造成影响.(a)对称的铺层顺序;(b)非对称的铺层顺序图1 纤维缠绕的铺层顺序Wild等[9]通过网格分析得出纤维缠绕复合材料压力容器的最优角度为54.74︒. Parnas等[10]考虑了纤维缠绕复合材料气瓶的内压的作用,得出优化的缠绕角主要取决于几何形状和使用的失效准则,并给出缠绕角的范围为52.1︒~54.2︒. Rosenow[11]利用经典层合理论分析了薄壁复合容器的缠绕角度在15︒~85︒之间变化时的应力与应变情况;对于环向应力和轴向应力之比等于2的圆筒形容器,均衡性缠绕角最优值为55︒. Erkal等[12]对玻璃纤维缠绕塑料内衬的复合材料压力容器疲劳破坏进行了实验研究,玻璃纤维均采用对称的方式缠绕,缠绕的角度分为±75︒、±60︒、±55︒、±45︒,实验结果表明,当缠绕角度为±55︒时,爆破的压力最大,为10.2 MPa.表1 在准静态张力下实验和预测的失效应力值对比[ABABA]S [A2B2A]S [A3B2]S 极限应力实验值/MPa 100 75 72极限应力预测值/MPa 105 77 68 误差 5 2.5 4注:11+/)Aθθ=-(,22(/)Bθθ=+-,而15︒<1θ<35︒,75︒<2θ<90︒纤维缠绕的厚度并不是越厚越好,纤维缠绕得太厚不仅会增加制造成本,而且外层纤维的强度也得不到充分的发挥,造成材料的浪费. 古海波[13]对容积为2 L的碳纤维缠绕铝内胆复合材料气瓶的环向缠绕厚度进行了设计. 随着环向纤维厚度的增加,工作压力和最小爆破压力下内胆和纤维的应力水平降低,同时纤维的应力比减小. 根据DOT-CFFC标准,得出纤维单层厚度的取值范围为0.13≤t≤0.14 mm.对于纤维缠绕结构,纤维缠绕的线型是一个重要的设计参数. 目前基本的纤维缠绕线型有:环向缠绕、纵向缠绕和螺旋缠绕3种. 环向缠绕是沿容器圆周方向进行缠绕,只能在筒身段进行,纤维缠绕的角度通常在85︒~90︒之间,缠绕工艺简单. 纵向缠绕的纤维轨迹是一条单圆平面封闭曲线,缠绕角度较小,多用于粗短容器. 螺旋缠绕又称为测地线缠绕,缠绕时导丝头按特定速度沿芯模绕轴线匀速自转,可以对筒身段和封头进行纤维缠绕,缠绕角度约为12︒~70︒,缠绕工艺复杂. 池秀芬等[14]通过碰撞损伤研究发现螺旋缠绕方式抵抗损伤的能力要高于普通环向缠绕方式,所以在制造复合材料压力容器时尽量采用螺旋缠绕方式. 在复合材料气瓶·4·应用科技第39卷制造中,一般采用螺旋和环向组成的缠绕形式. 3 复合材料气瓶失效准则复合材料气瓶的失效主要是纤维层的失效,故设计也主要是设计纤维层的强度. 常用的失效准则有最大应力准则、最大应变准则、Tsai-Hill 准则[15]、Hashin 准则[16]、Hoffman 准则[17]和Tsai-Wu 准则[18]. 最大应力准则是指如果某一种材料主方向的应力超过其强度值,材料就破坏,通常适用于对强度有要求的场合. 最大应变准则也是将复合材料的各应力分量与基本强度分量相比较,区别是最大应变准则考虑了另外一个方向应力分量的影响,适用于对构件形状变形有严格要求的场合. 最大应力及Tsai-Wu 准则适用于拉、压应力,Tsai-Wu 及Tsai-Hill 准则都允许二次应力的相互作用;但Tsai-Hill 准则只是二阶标准,没有线性应力,而Tsai-Wu 准则有这种线性应力,并适用于平面的所有象限及三围问题. 其中Tsai-Wu 准则用的最广,表达式见式(1):2221112226661122121221;F F F F F F σσσσσσσ+++++≥ (1)111t c F X X =,221t cF YY =,6621tc F S =,111t c F X X =-,211t cF Y Y =-,12F =式中:F 为强度系数,X t 、X c 分别为纵向的拉伸和压缩强度,Y t 和Y c 分别为横向的拉伸和压缩强度,S tc 为平面的剪切强度,1σ、2σ分别为纵向和横向拉应力.张晓军等[19]采用了最大应变准则预测了纤维缠绕复合材料气瓶的爆破压力约为66 MPa ,而2次爆破试验中测得的爆破压力分别为65 MPa 和68 MPa. 由此可见,最大应变准则预测复合材料气瓶的爆破压力是比较准确的. Wang 等[20]也基于最大应变准则,采用ANSYS 有限元软件预测了碳纤维缠绕6061-T6铝内胆气瓶的爆破压力为65 MPa ,与实验值比较吻合. Park 等[21]在考虑各种载荷和边界条件的情况下,采用剪切变形理论和Tsai-Hill 失效准则分析了对称的复合材料层,并获得了最优化的设计方案. 在保持强度不变的情况下,Moharrerzadeh 等[22]基于Hoffman 准则对复合材料气瓶的质量进行了优化设计,并且取得了比较理想的结果. Liu 等[23]采用Tsai-Wu 准则设计了碳纤维缠绕铝内胆复合材料气瓶,并采用ANSYS 软件分别计算了复合材料气瓶在预应力、工作压力、水压实验压力、最小破坏压力等下的应力值,计算结果均满足美国制定的DOT-CFFC 标准的要求. 这说明了理论设计的可行性,也为工程上的实际应用提供了理论依据. Antunes 等[24]也采用了Tsai-Wu 准则设计了聚丙烯内衬玻璃纤维缠绕的复合材料气瓶,并采用有限元软件计算了内衬、复合层的应力以及最小的爆破压力,计算的结果均满足EN 12245标准的要求,为实际的生产提供了理论依据. 郑津洋等[25]研究了碳纤维缠绕铝内胆的储氢气瓶,采用了最大应力准则、Hoffman 准则、Tsai-Hill 准则和Tsai-Wu 准则预测了气瓶的失效压力,结果如表2所示[25]. 而实验测得气瓶的爆破压力为125~126 MPa ,通过对比可以看出,这4种准则预测的爆破压力与实验值一致,而Tsai-Wu 准则预测的爆破压力值与实验值最接近.表2 采用4种失效准则计算气瓶的爆破压力值 失效准则 最大应力 Hoffman Tsai-Hill Tsai-Wu 爆破压力/MPa120.6119.6119.6122.74 复合材料气瓶的失效模式气瓶失效是指气瓶丧失了其储存介质的功能. 常见的气瓶失效模式主要分为弹性失效、屈服失效、脆性断裂失效、塑性断裂失效、疲劳断裂失效、冲击断裂失效等类型,其主要表现形式包括瓶身漏气,内胆鼓包、裂纹,纤维断裂,基体开裂、冲击损伤等. 4.1 瓶身漏气全复合材料气瓶的塑料内胆一般采用高密度聚乙烯材料,经滚塑工艺加工成型. 塑料内胆主要对气瓶起密封的作用,而非强度作用;因此,其失效主要是指内胆失去其应有的密封性能,多表现为气瓶出现各种形式的泄露. 内胆由于漏气而失效的原因主要包括2个方面:一方面是内胆制造成型时产生的缺陷,这类原始缺陷在气瓶的使用过程中,经反复疲劳很可能诱发出各种形式的裂纹,最终导致内胆泄露;另一方面是气瓶在运输、安装和使用中遇到的冲击损伤,过大的冲击力导致内胆出现裂纹等缺陷. 可以通过以下措施来防止瓶身漏气而导致的失效. 首先,要合理选择气瓶的制造材料,正确制定和执行标准,实行严格的质量管理和工艺过程及质量认证试验;其次,安装时要避免碰撞、划伤等;最后,使用过程中充气的速率应尽可能小一些,充气气压高限值应控制在20 MPa 以内. 4.2 内胆鼓包、裂纹据报道在复合材料气瓶的定期检验中发现,不第4期徐君臣,等:纤维缠绕复合材料气瓶研究进展·5·合格气瓶中发生内胆鼓包、裂纹的气瓶占全部检测气瓶数的84.85%. 显然内胆鼓包、裂纹是复合材料气瓶失效的主要形式. 雷闽等[26]为了确定复合材料气瓶内胆出现鼓包、裂纹缺陷产生的原因,对复合气瓶内胆材质进行力学性能、微观分析、缠绕层和内胆材料线膨胀系数测试. 测试结果发现缠绕层和内胆材料的线膨胀系数不同是导致复合材料气瓶产生鼓包和裂纹的最根本原因. 充放气过程中,内压和温度的低周循环也是气瓶产生缺陷的直接因素. 夏立荣[27]对车用CNG全复合材料气瓶内胆鼓包的成因进行了研究,研究结果表明,气瓶受内压的变化、充放气过程中内部温度的变化、内胆材料与缠绕层复合材料线膨胀系数、弹性模量以及延伸率的差异以及结合界面本身粘结性较差等都会造成气瓶内胆鼓包,这样在气瓶内气压的高低循环下反复作用,如此一来就会对内胆的最薄弱部位产生循环折弯的疲劳损伤过程,造成内胆层微裂纹的损伤贯通,最终造成气瓶整体泄露失效. 可以适当增加内胆的刚度、在内胆与缠绕层之间增加一种缓冲材料、严格控制气瓶的泄压过程,尽可能使气瓶保持一定的余压(2 MPa左右)等措施来防止气瓶内胆鼓包和裂纹的产生.4.3 纤维断裂复合材料气瓶由于在拆装、搬运、使用等过程中操作不当,使气瓶受到外力冲击、碰撞等损伤,导致复合材料气瓶表面出现划痕,进而使气瓶表面纤维断裂. 在气瓶检测中往往根据经验来作为气瓶判废的标准[28-29],如建议在割伤深度超过0.15 mm 或磨损露出的纤维深度超过0.25 mm时气瓶便报废. 这些做法缺乏一定的理论依据,会造成不必要的浪费. 签于此,有很多学者对这方面的内容进行了研究. 徐延海等[30]研究了表面损伤对全复合材料车用天然气气瓶强度的影响. 文中取了气瓶嘴附近、上封头附近、筒身、下封头附近和筒底附近5个部位,在轴向和周向2个方向上设置了几种不同长度和深度的表面损伤组合来模拟纤维的断裂状态. 研究结果表明,气瓶在有表面损伤时的应力值比无表面损伤时明显增大;对于相同尺度的表面损伤,轴向表面损伤对气瓶应力的影响比周向表面损伤显著;随着表面损伤长度的增加,气瓶在该处的等效应力逐渐增大;筒身表面的损伤比其他部位损伤的危害性小. Makinson等[31]研究了划痕对碳纤维缠绕聚乙烯内衬的复合材料储氢气瓶爆破压力的影响. 文中研究了划痕分为纵向和环向,划痕的长度为57 mm,宽为 1 mm,深度分别为复合层厚度11.4 mm的10%、20%、30%和40%,对应的爆破压力分别为76.14、69.63、59.27和52.98 MPa,而没有划痕时的爆破压力为74.3 MPa,可见随着划痕深度的增加,气瓶的爆破压力逐渐减小. Kim等[32]研究了划痕对碳纤维缠绕铝内衬复合天然气气瓶疲劳寿命的影响. 文中研究划痕深度为1.5、2.0、3.0和4.0 mm,宽度为2 mm,长度分别为50、100和200 mm,一共进行了12组实验. 实验结果表明,当划痕的深度超过3.0 mm,长度超过100 mm时,对气瓶的疲劳寿命有显著的影响. 而ISO 19078标准中规定的划痕的深度要小于1.25 mm,这是比较保守的.4.4 基体开裂复合层基体开裂主要是由于树脂脆性大,断裂延伸率低,在外载荷作用下,树脂的开裂远早于纤维的断裂,使纤维附近的树脂及树脂与纤维之间的界面处产生应力集中,形成基体开裂. 基体开裂会导致层间分层以及纤维拉出、断裂,最后导致材料的破坏. 张晓兵等[33]对复合材料压力容器基体开裂损伤进行了研究,研究结果表明,缠绕张力能使树脂基体产生预应力,从而可提高基体抵抗开裂的能力. 缠绕张力不合适会造成树脂不均匀,在循环压力载荷作用下,将产生基体开裂、裂纹不断扩展和新裂纹的产生,导致压力容器的刚度、强度下降,影响使用寿命. 王晓宏等[34]采用渐进损伤的模型对纤维缠绕复合材料压力容器基体开裂损伤进行了分析,详细分析了压力容器不同部位随外载荷的增加逐渐失效的情况,与真实情况比较符合,为复合材料压力容器的设计提供了有用的参考价值. Orifici等[35]总结了基体开裂以及失效的准则,采用断裂力学理论预测了基体开裂对复合材料的破坏. 可以在树脂中加入其它助剂,在保证树脂固化后具有高的强度、模量的情况下使树脂具有一定的塑性和韧性,或者采用热塑性基体,这样可以减少基体开裂的发生.4.5 冲击损伤复合材料气瓶在使用的过程中容易受到外来物体的冲击而产生损伤,并且往往在表面损伤很小,而在气瓶内表面以及缠绕层之间损伤严重. 气瓶在冲击载荷作用下的损伤破坏表现为基体开裂、基体挤压、纤维断裂、分层损伤等. 冲击损伤使复合材料层的寿命和强度大大下降,严重影响材料的使用. 目前,对复合材料在冲击载荷作用下的研究主要集中在层合板在不同的冲击载荷作用下的损·6·应用科技第39卷伤规律,复合材料层合板的损伤机理等上. Choi等[36-37]通过实验和模拟的方法研究了在低速冲击载荷作用下复合材料层合板破坏的机理. 在冲击载荷作用下复合层基体开裂是最开始的失效模型,由于基体开裂会导致复合层出现分层和微裂纹;初始的微裂纹缺陷会显著降低复合层抵抗冲击破坏的性能;并且复合层的堆叠顺序对复合层的抗冲击性能有显著的影响. 张彦等[38]研究了碳纤维复合材料层合板在低速冲击作用下层内和层间的失效行为,并采用有限元软件对复合材料层合板在横向低速冲击作用下的损伤和变形行为进行预测分析,模拟的结果与实验的结果比较吻合. Kaneko等[39]采用有限元的方法对在横向载荷作用下的复合材料气瓶的失效进行了分析. 在建模时只考虑气瓶的筒体部分,筒体复合层最外层为玻璃纤维,其余为碳纤维缠绕,并且根据实际的情况考虑了气瓶的内压作用. 模拟使用的冲击器为刚性的半球形,半径为25 mm,质量为554 kg,冲击的速度为10 m/s. 模拟结果如图2所示[39].图2 复合层从开始到穿透载荷与位移的曲线从图2中可以看出,当气瓶内压为17.5~52.5 MPa时,穿透载荷随着内压的增加而增加,主要是因为压力越高,刚度越大;当内压为70 MPa时,穿透载荷反而小,由于压力太高,导致了轴向纤维失效的发生. 所以可以提高压力,但必须小于安全操作压力可以增强气瓶抵抗冲击破坏的能力.5 复合材料气瓶的优化设计优化设计的基本原理是通过建立优化模型,运用各种优化方法,求得满足设计要求范围内的目标函数极值,得到最优化方案. 纤维缠绕复合材料气瓶的优化主要集中在自紧压力的优化、质量的优化等上,主要的目的是改变工作压力下内衬和纤维层的应力分配,充分发挥复合材料高强度的特点,同时在保证强度的条件下尽量减轻气瓶的质量,提高经济性.5.1 自紧压力的优化自紧常常应用于金属厚壁高压容器. 在自紧压力下,让容器在靠近内壁的部分厚度范围内达到屈服而产生塑性变形. 当自紧压力卸掉后,内壁处产生残余压应力. 其目的是使得容器在工作压力下,容器内外壁的拉应力能够相近些,以较充分地利用材料. 纤维缠绕复合材料气瓶不算厚壁容器,但由于内胆和缠绕层材料力学性能的巨大差异,当内胆已经屈服时,纤维还处于低应力状态,纤维优良的高强度性能得不到充分发挥. 复合材料气瓶面临的这个问题恰好通过自紧可以来解决. 古海波等[40]采用有限元软件对2 L的碳纤维全缠绕铝内胆气瓶的预紧压力进行了优化,得到了预紧压力对气瓶应力影响的结果. 并对照DOT-CFFC标准,得到了预紧压力的范围为35.9 MPa≤P pre≤36.6 MPa,取最佳的预紧压力为P pre=36.6 MPa. 李小明等[41]对某型复合材料气瓶进行了优化设计,自紧压力由40 MPa 提高到44 MPa,铺层角度由10︒增加到12︒,而工作压力下气瓶内胆应力减少了25%,可见进行优化分析是有必要的. 郑津洋等[42]对70 MPa车用轻质高压复合材料储氢气瓶进行了自增强处理,内衬圆柱段的应力从147 MPa下降到135 MPa,而纤维层的应力有少量增加. 自增强处理后,内衬材料的承载能力得到提高,在反复充装气体时,不会产生塑性变形的积累. 李玮[43]采用有限元软件对4.3 L碳纤维缠绕铝内胆复合材料气瓶的自紧压力进行了优化. 在满足DOT-CFFC标准的情况下,自紧压力的取值范围为55.1~56.2 MPa. 相对未自紧气瓶而言,通过自紧作用大大提高了气瓶的力学性能,使气瓶具有很强的安全性和可靠性.5.2 气瓶质量的优化在满足气瓶强度要求的情况下,气瓶的质量是设计的重要参数. 纤维的价格相对较高,通过结构优化,减薄纤维层的厚度,可以节省材料,降低成本. 边文凤等[44]对纤维缠绕的车用气瓶进行了整体优化设计,从轻型角度出发给出了优化的目标函数,同时也给出了爆破压力最大的优化约束函数. 这样做的目的是保证了产品在安全使用的前提下,汽车有较高的动力性和较长的续驶里程. 王志辉等[45]采用零阶和一阶方法并按照美国DOT-CFFC设计要求对复合材料气瓶进行了优化设计. 通过优化,纤维强度转换率得到提高,复合材料层体积由306 cm3减小到232 cm3,气瓶的容重比由7.24提高。
纤维缠绕复合材料压力容器渐进损伤分析

柱段部分: 由于每一单层的厚度和纤维缠绕角 在整个柱段上是常数, 这部分的建模相对比较简单。
为了保证单元形状的规则, 不使局部区域出现 较大的计算误差或矩阵奇异而终止计算, 均使用映 射网格。最后得到压力容器及封头部位有限元模型 如图 2 所示。 21 21 3 加载与求解
由于压力容器是轴对称结构, 故选择容器沿轴 线上的单元进行分析, 当压力为 41 5 M Pa 时, 容器 最外层沿纤维方向, 应变的分布如图 3 所示。同时, 选取容器上左封头( 点 1) , 桶身( 点 2) , 右封头上 ( 点 3) 点的模拟结果与试验结果[ 3] 的比较如图 4 所示。说明该有限元模型真实反映压力容器的力学 特性, 可用于进一步的分析。
3 压力容器渐进损伤分析
复合材料结构的破坏是一个十分复杂的问题, 它具有多种破坏模式, 对于不同的破坏模式, 复合 材料有不同的强度, 因此如何知道一个实际的复合 材料结构, 在复杂外载荷条件下的破坏模式及破坏 强度, 一直是人们十分关心的问题。过去通常只能 采用结构试验的方法, 这种方法一般来说既费时又 费钱。随着计算机软、硬件的不断发展, 利用计算机
S12
0 0 0 0 0 0 C12 S12
E11 0
0
0
0
0
E11
0 kE 22 0
0
0
0
E22
0
纤维缠绕复合材料气瓶的发展及其标准情况

纤维缠绕复合材料气瓶的发展及其标准情况1引言在压力容器中,中低压容器一般以板焊结构为主,而高压容器则出现多种结构:单层结构有整体锻造式、锻焊式、厚板卷焊式、电渣重熔式;多层结构有层板包扎式、螺旋包扎式、热套式、整体包扎多层式;缠绕结构有绕丝式、绕板式、扁平钢带倾角错绕式和型槽绕带式。
但这些结构都是指金属材料而言,单台压力容器重量根据容积大小和压力高低,最重的甚至可达数千吨。
而高压气瓶过去制造和使用的主要是金属材料即钢质和铝质的,按制造方法分有冲拔拉伸(E 法)、管材收口(M法)以及冲压拉伸(C法)等。
随着材料科学和制造工艺技术的进步,由于气瓶为移动式容器,为了减轻气瓶的重量,同时又能承受较高的压力,也出现了在金属或非金属材料内胆上环缠绕和全缠绕纤维材料组合结构的缠绕气瓶,即复合材料气瓶。
复合材料缠绕气瓶目前主要应用于呼吸器(如消防呼吸系统、登山、老人及病人吸氧、航空及航天系统等)及车用压缩天然气燃料气瓶两大领域,也可用于某些压缩气体和液化气体及其混合物。
现就纤维缠绕复合气瓶的发展及其标准的有关情况作一简要说明。
2纤维缠绕复合材料气瓶的发展及其标准情况2.1复合材料气瓶的发展复合材料气瓶的发展始于20 世纪50 年代,是基于火箭发动机复合材料机壳技术。
早期的复合气瓶是用玻纤浸渍环氧树脂缠绕于橡胶内胆上,虽然其重量比钢质轻,但由于玻纤较低的抗应力断裂及静态疲劳能力,以及气体渗透率较大,因此需要采用较高的安全系数。
20世纪60 年代开始使用金属内胆,如果内胆足够厚,允许纤维全缠绕或环缠绕增强。
复合气瓶采用金属内胆的渗透率比橡胶内胆的低得多,但内胆的疲劳寿命却受到限,薄壁内胆可在100~1000次循环产生开裂到泄漏,而厚壁内胆可在10000~30000 次循环产生泄漏。
复合材料容器和气瓶最早于20世纪50年代和60 年代用于国防和航天,这些容器或气瓶用于军用飞机的喷射系统,紧急动力系统和发动机重新启动应用系统,它们也用于航天试验室的氧气罐和导弹系统的压力源。
复合材料层合板低速冲击损伤容限的改进方法和影响因素.

]
F ig . 2Nor a of i nc i [7]
○:resin; ●:modified resin . F ig . 3I mpact damage resistance of CFRPs aga i n st i n ter -lam i ner fracture toughness of co mposite , G c C [8]
F ig . 5of i n str ips on delam i nation
area [15]
○:w ith interleaves ; ●:w ithout interleaves
.
F ig . 6The effect of i n terleaved adhesive layers on CA I
properties of co mposites [13]
○:w ith interleaves ; ●:w ithout interleaves .
究结果。因为层间断裂韧性的提高,所以层间插入条也能够减少炭纤维复合材料层合板等结构的冲击损伤面积,提高CA I值,从而改善复合材料的冲击性能以及损伤容限能力[14]。对断裂面的微观分析发现,插入层有效地控制了铺层内横向裂纹继续扩展,或转变成层间裂纹[9]。由于铺层内横向裂纹和层间分层的扩展受到插入物的阻碍,因此复合材料的冲击损伤形式也发生了变化。F ig . 5和F ig . 6是M aster等人[13, 14]所给出的层间插入对冲击损伤面积以及CA I值的影响,这些结果充分说明了该方法的有效
。
F ig . 7The effect of volu me fraction of polyethylene f ibers on
i m pact perfor mance of co mposite lam i nates [18]
纤维缠绕复合材料气瓶的发展过程及其损伤检测方法
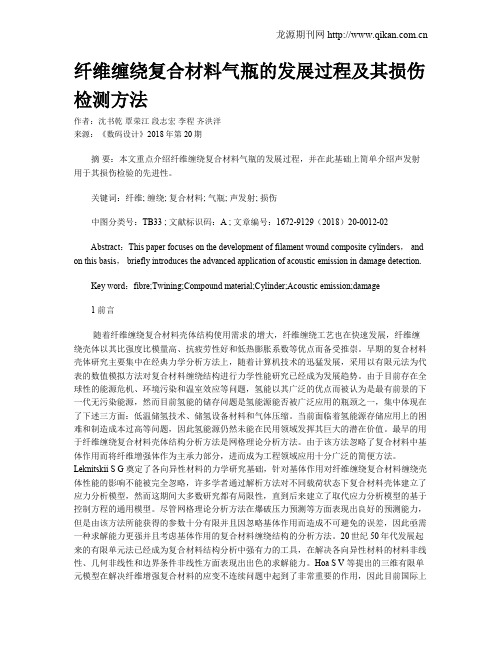
纤维缠绕复合材料气瓶的发展过程及其损伤检测方法作者:沈书乾覃荣江段志宏李程齐洪洋来源:《数码设计》2018年第20期摘要:本文重点介绍纤维缠绕复合材料气瓶的发展过程,并在此基础上简单介绍声发射用于其损伤检验的先进性。
关键词:纤维; 缠绕; 复合材料; 气瓶; 声发射; 损伤中图分类号:TB33 ; 文献标识码:A ; 文章编号:1672-9129(2018)20-0012-02Abstract:This paper focuses on the development of filament wound composite cylinders, and on this basis, briefly introduces the advanced application of acoustic emission in damage detection.Key word:fibre;Twining;Compound material;Cylinder;Acoustic emission;damage1 前言随着纤维缠绕复合材料壳体结构使用需求的增大,纤维缠绕工艺也在快速发展,纤维缠绕壳体以其比强度比模量高、抗疲劳性好和低热膨胀系数等优点而备受推崇。
早期的复合材料壳体研究主要集中在经典力学分析方法上,随着计算机技术的迅猛发展,采用以有限元法为代表的数值模拟方法对复合材料缠绕结构进行力学性能研究已经成为发展趋势。
由于目前存在全球性的能源危机、环境污染和温室效应等问题,氢能以其广泛的优点而被认为是最有前景的下一代无污染能源,然而目前氢能的储存问题是氢能源能否被广泛应用的瓶颈之一,集中体现在了下述三方面:低温储氢技术、储氢设备材料和气体压缩。
当前面临着氢能源存储应用上的困难和制造成本过高等问题,因此氢能源仍然未能在民用领域发挥其巨大的潜在价值。
最早的用于纤维缠绕复合材料壳体结构分析方法是网格理论分析方法。
由于该方法忽略了复合材料中基体作用而将纤维增强体作为主承力部分,进而成为工程领域应用十分广泛的简便方法。
关于复合材料缠绕压力容器冲击损伤的几点思考
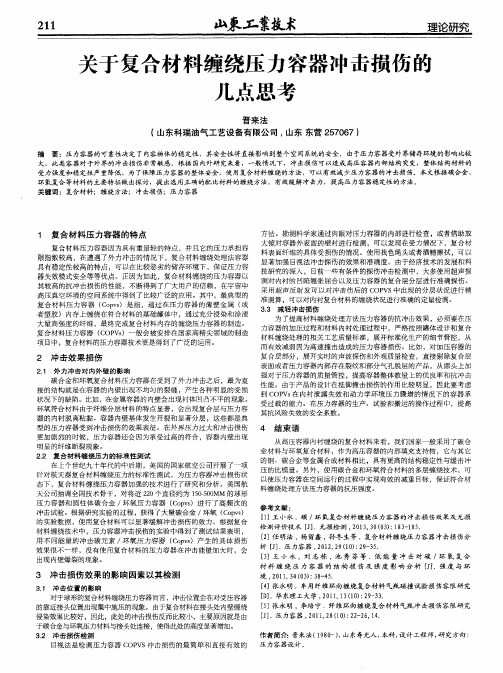
复合材料 压力容 器 ( C o p v s )是 指 ,通过 在压力容 器的薄壁 金属 ( 或 3 . 3 减 轻 冲 击损 伤 者塑胶 )内存上缠绕在符合材料 的基础 罐体 中 ,通过充分浸染和涂渍 为 了提 高材料缠 绕处 理方法压力容器的抗冲击效果 ,必须要在压 大量 高强度的纤维 ,最终完成复合材料 内存 的缠绕压力容器的制造 。 力容器 的加压 过程 和材料内衬处理过程中 ,严格按照罐体设计和复合 复合 材料压力容器 ( C O P V s )一般会被安排在 国家高精尖领域的制造 材料缠绕处理 的相关 工艺质量标准 ,展开标准化生产的细节管控 ,从 项 目中,复合材料 的压力容器技术更是得到了广泛的运用。 而有效减弱 因为高速撞击造成的压力容器损伤 。比如 ,对加压容器 的 复合层部分 ,展开 实时的声 波探伤和外观质量检查 ,直接剔除复合层 2 冲 击 效 果 损 伤 表面或者压力容器 内部存在 裂纹 和部分气孔脱层的产 品,从源头上加 2 . 1 外 力 冲击 对 内外 壁 的影 响 强对于压力容器 的质 量管 控 , 提 高容器整体数量上的优 良率和抗冲击 碳合金和环 氧复合材料压力容器在受到 了外力 冲击之 后 ,最为直 性能 。由于产 品的设计在抵 御撞击 损伤 的作用比较明显 ,因此要考虑 接 的结构就 是在 容器的 内壁出现不均匀 的裂缝 ,产生 各种 明显的受损 到C OP Vs 在 内衬 泄露失效和 动力学环境 压力骤增 的情况下 的容器承 状况下的缺 陷。比如 , 在金属容器 的内壁会 出现衬体 凹凸不平的现象 。 受过载的能力 。在压力容器 的生产 、试验和 搬运的操作过程中 ,提高 环氧符合材料 由于 纤维分层材料的特点显著 ,会 出现 复合层 与压 力容 其抗风险失效的安全 系数 。 器 的内衬脱 离粘 黏、容 器 内壁基体发生开裂和显著分层 , 这 些都是典 型的压力容器受 到冲击 损伤的效果表征 。在外界压力过大和 冲击 损伤 4 结束语 更加剧烈 的时候 ,压力容器还会 因为承受过高 的符合 ,容器 内壁 出现 从高压容器 内衬缠绕 的复合材料来 看 , 我们 国家一般采用了碳合 明显的纤维断裂现象。 金材料与环氧复合材料 ,作为高压容器 的内部填 充支持 物 ,它与其它 2 . 2 复合材料缠绕压力的标 准性测试 的钢、碳合金等金属合成材料相 比,具有更高 的结构稳 定性 与缓击冲 在上个世纪九十年代 的中后期 ,美 国的 国家航空公司开展 了 一项 压的比模量 。另外 ,使用碳合金和环氧符合材料 的多层缠绕技术 ,可 针对航天器复合材料缠绕压 力的标准性测试 ,为压力容器冲击损伤状 以使压 力容器在空间运行的过程 中实现有效 的减重 目标 ,保证 符合 材 态下 ,复合材料缠绕压力容器 加强的技术进行 了研究和分析 。美 国航 料 缠绕处 理方法压力容器 的抗压强度 。 天公司抽调全国技术骨干 ,对将近 2 2 0 个直径约为 1 5 0 — 5 0 0 MI V I 的球形 压力容器 和 圆柱体 碳合金 / 环 氧压力容 器 ( C o p v s )进行 了高频次 的 参 考 文献 : 冲击试验。根据研究实验的过程 , 获得 了大量碳合金 / 环氧 ( C o ws ) 【 1 ] 王 小永 .碳 /环氧复合村料 缠绕压力容 器的冲击损伤效果及无损 的实验数据 ,使用复合材料可 以显著缓解 冲击损伤的效力 。根据复合 检 测评 价 技 术 【 J ] .无 损 检 测 , 2 0 1 3 , 3 0 ( 0 3 ) : 1 8 3 - 1 8 5 . 材料缠绕技术中 ,压力容器冲击 损伤 的实验 中得到了测试结果表 明, [ 2 ] 任 明法 , 杨 留鑫 , 孙冬生 等 . 复合材料缠绕压 力容器冲击损伤分 用不 同能量 的冲击 碳元素 /环氧压 力容器 ( C o p v s )产 生的具 体损伤 析 [ J ] .压 力容器 , 2 0 1 2 , 2 9 ( 1 0 ) : 2 9 - 3 5 . 效果很 不一样 ,没有使用复合材料 的压 力容器 在冲击能量加大时 ,会 [ 3 】王 小 永 ,刘 志 栋 ,池 秀 芬 等 .低 能 量 冲 击 对 碳 /环 氧 复 合 出现 内壁爆裂 的现象 。 材 料 缠 绕 压 力 容 器 的 结 构 损 伤 及 强度 影 响 分 析 [ J ] .强度 与 环
纤维缠绕气瓶的检测常用标准和指标
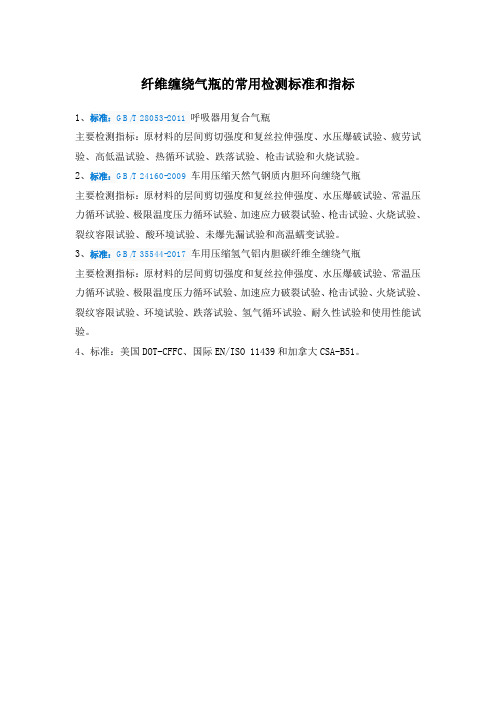
纤维缠绕气瓶的常用检测标准和指标
1、标准:GB/T 28053-2011 呼吸器用复合气瓶
主要检测指标:原材料的层间剪切强度和复丝拉伸强度、水压爆破试验、疲劳试验、高低温试验、热循环试验、跌落试验、枪击试验和火烧试验。
2、标准:GB/T 24160-2009 车用压缩天然气钢质内胆环向缠绕气瓶
主要检测指标:原材料的层间剪切强度和复丝拉伸强度、水压爆破试验、常温压力循环试验、极限温度压力循环试验、加速应力破裂试验、枪击试验、火烧试验、裂纹容限试验、酸环境试验、未爆先漏试验和高温蠕变试验。
3、标准:GB/T 35544-2017 车用压缩氢气铝内胆碳纤维全缠绕气瓶
主要检测指标:原材料的层间剪切强度和复丝拉伸强度、水压爆破试验、常温压力循环试验、极限温度压力循环试验、加速应力破裂试验、枪击试验、火烧试验、裂纹容限试验、环境试验、跌落试验、氢气循环试验、耐久性试验和使用性能试验。
4、标准:美国DOT-CFFC、国际EN/ISO 11439和加拿大CSA-B51。
CNG环向缠绕气瓶纤维应力比研究的开题报告

CNG环向缠绕气瓶纤维应力比研究的开题报告一、选题背景CNG(压缩天然气)作为一种新型清洁能源受到了越来越多的关注和应用。
CNG储气瓶是CNG燃气车辆的重要组成部分,而纤维环向缠绕材料是CNG储气瓶中最常用的材料之一。
在CNG储气瓶的设计和制造过程中,纤维应力是一个重要的参数,影响储气瓶的安全性能和使用寿命。
目前,已有一些关于CNG储气瓶纤维应力比的研究,但仍存在一些问题和挑战。
因此,本研究旨在深入探讨CNG储气瓶纤维应力比的影响因素和控制方法,为CNG储气瓶的设计和制造提供理论基础和实践指导。
二、研究内容1. 纤维应力比的概念及影响因素:通过文献综述和实验分析,介绍纤维应力比的定义和计算方法,探讨纤维应力比与储气瓶强度、刚度、重量等性能之间的关系,并分析纤维应力比的影响因素。
2. 筒体结构对纤维应力比的影响:通过有限元分析和实验测试,研究筒体结构对纤维应力比的影响,探讨不同结构参数(如筒体直径、壁厚、缠绕层数等)对纤维应力比的影响规律。
3. 环向缠绕工艺对纤维应力比的影响:通过模拟分析和实验测试,研究环向缠绕工艺对纤维应力比的影响,探讨不同缠绕角度、缠绕速度、纤维张力等工艺参数对纤维应力比的影响规律。
三、研究意义和预期效果本研究对于优化CNG储气瓶的设计和制造具有重要意义,可以探索新的减轻储气瓶重量、提高瓶体强度和安全性的方式和方法。
预期效果如下:1. 深入理解纤维应力比的概念和影响因素,为CNG储气瓶设计和制造提供理论依据。
2. 探讨筒体结构和缠绕工艺对纤维应力比的影响规律,为优化储气瓶的工艺流程提供实践指导。
3. 提高CNG储气瓶的使用寿命和安全性能,为推广和应用CNG燃气车辆做出贡献。
四、研究方法1. 文献综述:通过查阅相关文献资料,了解和总结已有的关于CNG 储气瓶纤维应力比的研究成果,为后续实验设计和数据分析做好准备。
2. 实验测试:利用传统的材料力学测试方法,对储气瓶进行拉伸、弯曲、冲击等多种载荷试验,获取不同工况下的应力应变曲线并计算纤维应力比。
UHMWPE复合材料气瓶爆破压力预测

UHMWPEF 缠绕铝内衬复合材料气瓶的爆破压力预测 摘要:本文利用有限元强大的后处理功能,在复合材料气瓶的有限元模型上选取一条路径,使其能够代表复合材料气瓶模型上的所有点,然后在同一载荷下观察这一路径上的点的应变曲线,观察曲线规律,从中选取三个点做出载荷-应变曲线,找出最大应变点。
然后做出环向纤维缠绕复合材料层的这个点在不同载荷下的载荷-应变曲线,根据最大应变准则,预测UHMWPE 纤维缠绕复合材料气瓶的爆破压力。
关键词: 有限元;最大应变准则;爆破压力;网格分析引言气瓶为移动式容器,为了减轻气瓶的重量,同时又能承受较高的压力,出现了在金属或非金属材料内衬上环缠绕和全缠绕纤维材料组合结构的缠绕气瓶,即复合材料气瓶[1]。
一般而言在相同容积,承受相同内压情况下,复合材料气瓶的重量大约是钢瓶的50%-60%[2]。
因此,复合材料气瓶的应用越来越广泛。
复合材料的显著优点是比强度高、比模量大、抗疲劳性能好。
复合材料具有的这些优点正好满足航天系统对减轻结构重量的特殊要求,这使它成为当代航天系统上应用越来越多的重要材料。
但是复合材料具有强烈的各向异性和非均质性的特点,因此它的力学性能比较复杂[1]。
此外结构在形成过程中有组分材料的物理和化学变化发生,构件的性能对复合工艺的依赖性很大[2-3]。
这些因素决定了复合材料气瓶结构的复杂性,因此仅靠网格理论对其进行静力学设计和分析不能满足空间系统对压力容器的高可靠、高性能要求,而有限元分析方法能进行非常准确和详细的静力学分析[4],为设计提供充分和足够的应力应变分析数据,从而将盲目性减小到最低程度,使气瓶设计达到最佳程度[5]。
国外复合气瓶的研究主要集中在对复合材料本身的性能及容器本身的各种极限问题的研究。
国内的研究主要在结构的设计以及数值模拟方面[13]。
本文利用有限元强大的后处理功能,在复合材料气瓶的有限元模型上选取一条路径,使其能够代表复合材料气瓶模型上的所有点,然后在同一载荷下观察这一路径上的点的应变曲线,观察曲线规律,从中选取三个点做出载荷-应变曲线,找出最大应变点。
纤维缠绕复合材料损伤演化多尺度表征方法构建

纤维缠绕复合材料损伤演化多尺度表征方法构建目录1. 内容简述 (2)1.1 研究背景及意义 (2)1.2 纤维缠绕复合材料的基本特性及损伤类型 (4)1.3 现有损伤表征方法的优缺点 (5)1.4 研究目标及内容 (6)2. 多尺度损伤演化理论与模型 (7)2.1 宏观尺度损伤演化模型 (8)2.1.1 损伤力学理论基础 (9)2.1.2 常见的损伤力学模型 (11)2.2 中观尺度损伤演化模型 (12)2.2.1 基于断裂力学的模型 (13)2.2.2 基于有限单元法的模型 (14)2.3 微观尺度损伤演化模型 (15)2.3.1 基于纤维和基体界面界面相互作用的模型 (16)2.3.2 基于大分子模拟的模型 (17)3. 多尺度表征方法构建 (19)3.1 多尺度数据获取技术 (20)3.2 数据融合与多尺度关联算法 (21)3.2.1 统计分析与机器学习方法 (22)3.2.2 有限元分析和多尺度建模方法 (23)3.3 损伤演化多尺度表征模型构建 (25)4. 举例应用 (26)4.1 某特定纤维缠绕复合材料损伤演化表征 (27)4.2 在工程应用场景中的多尺度表征方法应用 (28)5. 结论与展望 (30)1. 内容简述本文档旨在构建一种纤维缠绕复合材料损伤演化多尺度表征方法,以实现对纤维缠绕复合材料在不同工况下的损伤演化过程进行有效监测和分析。
纤维缠绕复合材料作为一种新型的结构材料,具有轻质、高强、耐腐蚀等优点,广泛应用于航空航天、汽车制造、能源等领域。
然而,由于其复杂的结构和多种损伤因素的共同作用,纤维缠绕复合材料的损伤演化过程往往难以直接观察和分析。
因此,研究一种有效的多尺度表征方法具有重要的理论和实际意义。
本文档旨在构建一种纤维缠绕复合材料损伤演化多尺度表征方法,以期为纤维缠绕复合材料的研究和应用提供有力的理论支持和技术指导。
1.1 研究背景及意义纤维缠绕复合材料作为一种由连续纤维增强树脂基体材料构成的新型材料,在航空航天、汽车、体育器材等多个领域得到了广泛应用。
复合材料层合板损伤容限敏感性参数研究

第丨期 纤维复合材料No.I36 2021 年3 月FIBER COMPOSITES Mar. 2021复合材料层合板损伤容限敏感性参数研究武海鹏,韩琳(哈尔滨玻璃钢研究院有限公司,哈尔滨150028)摘要本文针对碳纤维增强复合材料层合板冲击下的损伤容限参数敏感性进行分析。
对复合材料层合板损伤容 限的影响参数、纤维角度、铺层顺序、层合板厚度、冲击速度和冲击角度等进行冲击损伤仿真,采用蔡-吴强度 准则评价层合板冲击的剩余强度,并对各参数影响的敏感性排序,确定纤维角度和铺层顺序为复合材料层合板冲 击下损伤容限的敏感参数。
关键词复合材料;损伤容限;冲击;敏感性参数Research on the Damage Tolerance SensitiveParameters of Composite LaminateWU Haipeng, HAN Lin(Harbin FRP Institute Co. ,Ltd. ,Harbin 150028)ABSTRACT This article aims on the analysis of the damage tolerance sensitive parameters of carbon fiber reinforced laminate under impact. The test simulates the impact damage on damage tolerance effective parameters of composite laminate, fiber orientation, ply stacking sequence, thickness of laminate, impact velocity and impact angle, using the Tsai -Wu strength criterion to evaluate the residual strength of laminate impact and sequencing all parameters *effective sensibility,and confirmed that fiber orientation and ply stacking sequence are the sensitive parameter of damage tolerance of composite laminate under impact.KEYWORDS composite material ;damage tolerance;impact;sensitive parameter1引言由于复合材料质量轻、强度高,因此在航空航 天领域得到了广泛的应用,但复合材料层合板结构 在使用和维护过程中容易受到低能量载荷冲击,如冰雹碎石的冲击、维修时工具的坠落等。
试述碳纤维缠绕复合材料储氢气瓶的研制
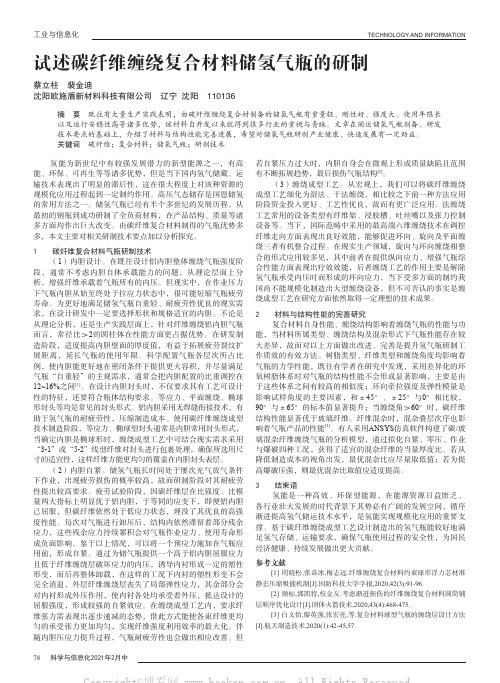
能,当材料所属类型、缠绕结构及混杂形式下气瓶性能存在较 大差异,故而对以上方面做出改进、完善是提升氢气瓶研制工 作质效的有效方法。树脂类型、纤维类型和缠绕角度均影响着 气瓶的力学性能,既往有学者在研究中发现,采用差异化的环 氧树脂体系时对气瓶的结构性能不会形成显著影响,主要是由 于这些体系之间有较高的相似度;环向牵拉强度及弹性模量是 影响试样角度的主要因素,和±45°、±25°与0°相比较, 90°与±65°的标本值显著提升;当缠绕角>60°时,碳纤维 结构性能显著优于玻璃纤维。纤维混杂时,混杂叠层次序也影 响着气瓶产品的性能[3]。有人采用ANSYS仿真软件构建了碳/玻 璃混杂纤维缠绕气瓶的分析模型,通过拟化自紧、零压、作业 与爆破四种工况,获得了适宜的混杂纤维的当量厚度比。若从 降低制造成本的视角出发,最优混杂比应尽量取低值;若为提 高爆破压强,则最优混杂比取值应适度提高。
1 碳纤维复合材料气瓶研制技术
(1)内胆设计。在既往设计铝内胆整体缠绕气瓶强度阶 段,通常不考虑内胆自体承载能力的问题,从理论层面上分 析,增强纤维承载着气瓶所有的内压。但现实中,在作业压力 下气瓶内胆从始至终处于拉应力状态中,很可能短缩气瓶疲劳 寿命。为更好地满足储氢气瓶自重轻、耐疲劳性优良的现实需 求,在设计研发中一定要选择形状和规格适宜的内胆。不论是 从理论分析,还是生产实践层面上,针对纤维缠绕铝内胆气瓶 而言,常径比>2的圆柱体在性能方面更占据优势。在研发制 造阶段,适度提高内胆壁面的厚度值,有益于拓展疲劳裂纹扩 展距离,延长气瓶的使用年限。科学配置气瓶各层次所占比 例,使内胆能更好地在密闭条件下提供更大容积,并尽量满足 气瓶“自重轻”的主观需求,通常会把内胆配置的比重调控在 12~16%之间[1]。在设计内胆封头时,不仅要求其有工艺可设计 性的特征,还要符合瓶体结构要求。等应力、平面缠绕、椭球 形封头等均是常见的封头形式。铝内胆采用无焊缝衔接技术,有 助于氢气瓶的耐疲劳性,压缩制造成本。使用碳纤维缠绕成型 技术制造阶段,等应力、椭球型封头通常是内胆常用封头形式, 当确定内胆是椭球形时,缠绕成型工艺中可结合现实需求采用 “3-1”或“5-2”线型纤维对封头进行包裹处理,确保所选用尺 寸的适宜性,这样纤维方能更均匀的覆盖在内胆封头表层。
不同缠绕工艺下复合材料气瓶力学性能研究

不一样环绕工艺下复合资料气瓶力学性能研究复合资料气瓶因质量轻、强度高、抗疲惫性能好等长处, 已成功应用到诸多领域中。
但是 , 当前对复合资料气瓶的构造设计和性能剖析仍存在很多不足。
如在复合资料气瓶损害无效方面, 仅剖析了复合资料层的无效形式, 并未给出整体构造的无效过程 ; 在复合资料气瓶非测地线环绕方面, 研究只逗留在改变环绕角度, 并未考虑到螺旋环绕角对筒体环绕层厚度再分派的影响 ; 在复合资料气瓶的瓶肩聚积方面 , 工程上不过依靠环绕经验 , 采纳扩孔法减少瓶肩的纤维聚积 , 但有关的理论研究较少。
针对以上存在的不足 , 本文联合理论剖析和数值模拟方法 , 对复合资料气瓶的构造和性能进行研究剖析 , 主要工作及研究结果以下 :(1) 本文采纳渐进损害方法 , 模拟复合资料气瓶的整体无效过程。
基体开裂第一出此刻筒体复合资料层上 ,由等厚段向两头扩展 ; 在封头上出现较晚 , 由两头向中心扩展。
基体所有开裂此后 ,气瓶上的纤维还保持完满。
内压持续增添 , 当达到某一值后 , 筒体上的纤维出现了局部断裂, 与基体扩展方向不一样 , 纤维断裂除了由初始地点向两头扩展外, 还沿径向局部扩展。
纤维的断裂极大程度上降低了气瓶的承载能力, 内胆在纤维断裂初始地点变形增大, 而后破碎 , 致使气瓶最后整体无效。
计算获得 , 该类气瓶的最后爆破压力为112MPa,接近试验值 108MPa。
(2)依据 DOT-CFFC标准要求 , 确立复合资料气瓶自紧压力的变化范围。
在此基础上 , 研究自紧压力对气瓶疲惫寿命的影响 , 结果表示筒体等厚段的等效应力幅跟着自紧压力的增大而增大。
进而 , 确立出该类气瓶的最正确自紧力约为 54MPa。
(3)针对非测地线的研究不足 , 本文考虑环绕角对筒体环绕层厚度再分派的影响 , 经过封头的非测地线理论剖析, 得出误差角的同意范围 , 并联合误差角对气瓶应变的影响 , 确立出其最正确值。
复合材料的冲击、损伤容限和吸能-12

利用有限元软件,进行计算的过程
研究结果表面:在冲头上升前损伤面 积最大,并发现层合复合材料的损伤 面积与撞击能有很好的线性关系。
Hopkinson法冲击实验原理
如其核心部分是两段分离的弹性压杆: 输入和输出杆。
子弹以一定的速度撞击输入杆,在其中产生一入射脉冲 i ,
试样在该应力脉冲作用下被高速压缩变形,同时向输出杆传播
一透射波 t 和向输入杆返回一反射波 r 。
根据SHPB 实验 的一维假定和均 匀性假定,利用一 维应力波理论可 得试样的应变率εt (t) 、应变ε( t) 以 及应力σ( t) :
主要可分为如下几种: • 摆锤式冲击试验(包括简支梁型和悬臂梁型) • 落锤式冲击试验 • 弹射式实验装置 • Hopkinson压杆实验装置 • 简支梁型冲击试验是摆锤打击简支梁试样的中央; • 悬臂梁法则是用摆锤打击有缺口的悬臂梁试样的
自由端。
摆锤式实验的特点
摆锤式冲击试验试样破坏所需的能量实际 上无法测定。 试验所测得的除了产生裂缝所需的能量及 使裂缝扩展到整个试样所需的能量以外, 还要加上使材料发生永久变形的能量和把 断裂的试样碎片抛出去的能量。把断裂试 样碎片抛出的能量与材料的韧性完全无关, 但它却占据了所测总能量中的一部分。
需要确定如下物理量;
• 冲击载荷输入历程和大小; • 结构载荷响应历程、大小和分布; • 结构位移响应历程、大小和分布; • 测量的应变率响应特点
Hopkinson Pressure Bar
飞机上的缓冲吸能部件(结构)
各类吸能结构
各类吸能结构
各类吸能结构
各类吸能结构
各种缓冲结构的吸能比较
A 0 : 试样初始截面积 l 0 : 试样初始长度
Z-pin增强复合材料冲击性能及损伤容限研究进展

Z-pin增强复合材料冲击性能及损伤容限研究进展
史建猛;杜金波;张皓为;毕运波
【期刊名称】《材料科学与工程学报》
【年(卷),期】2022(40)6
【摘要】本文总结了碳纤维复合材料Z-pin增强的联桥机制、Z-pin植入产生的面内纤维屈曲效应以及富树脂区的形成,重点分析了Z-pin植入密度、直径、植入角度及不同复合材料层合板厚度和铺层对冲击性能和冲击后剩余力学性能的影响。
研究表明:Z-pin在较低冲击能量下对冲击阻抗的影响不明显;Z-pin对于分层损伤起始影响不大;Z-pin的存在会提高中等厚度(4.5 mm)板抗分层性能;Z-pin并不会改变冲后压缩试验的失效形式,在一定冲击能量范围内Z-pin会极大地提高剩余压缩强度;试件在低速冲击表面不可见损伤情况下,Z-pin对复合材料疲劳性能基本没有影响;在较高冲击能量下Z-pin体积分数越高,疲劳性能增益效果越明显。
【总页数】6页(P1073-1078)
【作者】史建猛;杜金波;张皓为;毕运波
【作者单位】中航西安飞机工业集团股份有限公司;浙江大学机械工程学院
【正文语种】中文
【中图分类】TB332
【相关文献】
1.基于黏聚区模型的Z-pin增强复合材料T型接头分层损伤研究
2.复合材料加筋壁板冲击损伤特性及损伤容限研究进展
3.国产复合材料冲击损伤容限可靠性分析
4.z-pin增韧复合材料层合板低速冲击损伤过程研究
5.Z-pin增强陶瓷基复合材料拉伸性能及损伤研究
因版权原因,仅展示原文概要,查看原文内容请购买。
- 1、下载文档前请自行甄别文档内容的完整性,平台不提供额外的编辑、内容补充、找答案等附加服务。
- 2、"仅部分预览"的文档,不可在线预览部分如存在完整性等问题,可反馈申请退款(可完整预览的文档不适用该条件!)。
- 3、如文档侵犯您的权益,请联系客服反馈,我们会尽快为您处理(人工客服工作时间:9:00-18:30)。
tei a t fc mp st NG c l d rrsd a t n h h mp c o o i C yi e eiu l r g .T ers l h w a h rn h pe itro e o e n set h e ut s o t t eb a c rdco f h s h t t
关键词: 复合材 料 气瓶 ; 冲击损 伤 ; 剩余 强度 ; 伤 容 限 损
中图分类号 :Q 5 . 0 4 . T 0 32;3 7 3 文献标 识码 : A 文章编号 :0 1 4 3 (0 1 1 0 2 0 10 — 8 7 2 1 )0— 0 2— 5
di1.9 9 ji n 10 43 .0 .0O 4 o:0 3 6/.s .0 1— 8 7 2 1 1 .O s 1
纤维环 向缠绕复合材料气瓶冲击损伤 容限研究
张 永明 。 培 宁 李 ( 东理 工大 学 , 海 华 上 20 3 ) 0 27
摘 要: 为研 究纤 维缠 绕复合 材料 层 C G气瓶 冲击 后损伤 容 限 问题 , N 采用 疲 劳应 变 比率作 为损 伤 变 量 , 立疲 劳累 积损伤 模 型 ; 气瓶缠 绕层 的冲 击损 伤剩余 强度 采 用开孔 等效 计算 方 法 , 建 对 应用 N i us .
0 引 言
明 , 冲击 损 伤 的 层 合 板 试 件 剩 余 强 度 衰 减 明 受 显 J 车用 C G气 瓶 比一 般 移 动 式 压 力 容 器 的 。 N 安 全 问题更 加突 出 , 因此 需 要 对 影 响其 安 全 性 的 因素加 以研 究 , 尤其 是 C G气 瓶 的 冲击 损 伤 容 限 N
c muain fn t no xmu srs n e s ela f oe miaersd a t n h,a d st n p u lt u ci f o o ma i m t sa dtn i o do lsl n t eiu l r g e l h a set n et gu i
St y o o p —wr p d Co po ie Cy i d r ud fH o — a pe m st ln e s I pa tFa l r lr nc m c iu e To e a e
ZHIPe i
a c s u s h e e t d sr i ae r s d a a g a a l sa l h te f t u a g c u l- n e i e ,t e r p ae tan r t sa e u e s d ma e v r b e e t bi i e d ma e a c mu a s i s h a g
( at hn nvr t o cec n e h o g ,hn h i 0 2 7, hn ) E s C iaU i s y f i ea dT c nl y S ag a 2 0 3 C ia e i S n o
Abs r c : rt e su y o l me t—wo n a n t d c mpo i t a t Fo h t d ff a n i u d lmi ae o st CNG y i e fe mpa td ma e tl r e cl nd rat ri c a g oe —
to d 1 Th u a e so yi d r e i u lsr n t fi a td ma ec l u ai n u i g t q i a i n mo e . e wo nd ly r fc ln e sr sd a te gh o mp c a g ac lto sn hee u v — l n p n n s App ia in Nuime e to e i g . lc to s r—W hi e v r g te s c tro a c r i g wi ai e d ma e a — t y a e a e sr s r e n, c o d n t ftg a g c n i i h u
prpo e n ltc lmo e c n f h o o i yi d r a g s e s n tn r sb h x e t . o s d a a yia d a tt e c mp st c ln e sd ma e a s sme tsa da d y t e e p rs i e
m r Wh ny e — i e 平均应力准则, t 关联疲劳累积损伤 函数中的最大应力与拉伸载荷下 的含孔层合板剩 余 强度 的关 系 , 立适 用于在 疲 劳 载荷 下 的含 孔 层 合 板 结构 剩 余 强 度 的估 算 方 法 , 于 复 合 材 料 建 用
C G 气瓶 冲 击剩余 强度 的预 测 。结果表 明 , 中提 出 的分 析模 型预 测结 果 与专 家 提 出的复合 材 料 N 文 气瓶 冲击损 伤评定 标 准基本 吻合。 ’
f rt e ft u a o e mi a e s u t r ft er s u l te g h o e e t t n me h d ,fr c s n o h ai e l d h ls l n t t cu e o e i a r n f h s mai t o s o e a t g g o a r h d s t t i o i
Ke r s c mp st yid r ;mp c a g r s u te gh; a g oea c y wo d :o o i c l es i atd ma e;ei a s n e n d l r t d ma etlrn e
等损伤, 使其 强度 和寿命 发 生变 化 。试验 表 j