不锈钢铰削加工工艺性能的分析
不锈钢工件加工工艺简介

不锈钢工件加工工艺简介不锈钢是一种耐腐蚀、美观、结构稳定的合金材料,具有广泛的应用领域。
在工业领域中,不锈钢工件加工是一项非常重要的工艺,对加工工艺的要求也非常高。
本文将就不锈钢工件加工的工艺过程进行简要介绍,希望能够对相关行业的从业人员和相关领域的学习者有所帮助。
一、不锈钢工件加工的工艺特点1. 耐腐蚀性高不锈钢具有良好的耐腐蚀性能,能够在酸、碱等腐蚀性介质中长期使用。
在不锈钢工件加工时,需要使用专门的材料和设备,以免污染不锈钢表面,影响其腐蚀性能。
2. 切削性能差由于不锈钢材料硬度高、强度大、塑性差,因此其切削加工难度较大,很容易造成刀具磨损和加工难度增加。
在加工不锈钢工件时,需要选用适当的刀具,并严格控制切削速度、进给量和切削深度,以获得良好的加工质量。
3. 热处理难度大不锈钢的热处理难度较大,容易产生氧化、变色等问题。
在不锈钢工件加工中,需要合理控制加热温度、加热速度和冷却方法,以避免对不锈钢材料产生不良影响。
二、不锈钢工件加工的工艺流程1. 加工前的准备在进行不锈钢工件加工之前,需要做好充分的准备工作。
包括对工件进行清洁、检测、卡盘夹具的安装等工作。
需要对加工设备和刀具进行检修和保养,保证加工设备和刀具的正常运转。
2. 刀具选择针对不锈钢材料的特点,需要选择适当的刀具。
一般来说,为了提高刀具的使用寿命和加工质量,应选择硬质合金刀具或涂层刀具。
在进行车削、铣削等加工时,还需要根据不同情况选择不同的刀具形状和材质。
3. 加工工艺参数的确定在确定加工工艺参数时,需要考虑切削速度、进给量、切削深度、刀具的切削速度等因素。
根据不同的不锈钢材料和加工要求,确定合理的加工工艺参数,以获得较好的加工效果。
4. 加工操作在进行不锈钢工件加工时,需要严格按照工艺要求进行操作。
包括对加工参数的严格控制、对加工设备和刀具的正常使用、对工件表面质量的检查等工作。
需要注意避免过度切削和切削过热,以免影响不锈钢工件的表面质量和耐腐蚀性能。
不锈钢车削加工特点及加工工艺
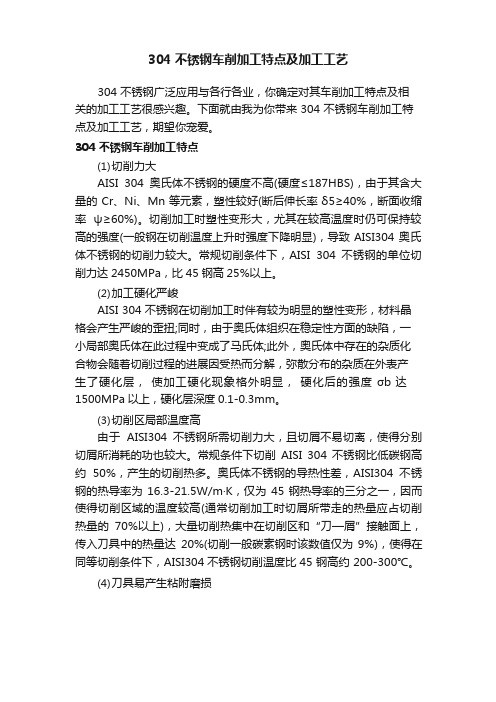
304 不锈钢车削加工特点及加工工艺304 不锈钢广泛应用与各行各业,你确定对其车削加工特点及相关的加工工艺很感兴趣。
下面就由我为你带来 304 不锈钢车削加工特点及加工工艺,期望你宠爱。
304 不锈钢车削加工特点(1)切削力大AISI 304 奥氏体不锈钢的硬度不高(硬度≤187HBS),由于其含大量的 Cr、Ni、Mn 等元素,塑性较好(断后伸长率δ5≥40%,断面收缩率ψ≥60%)。
切削加工时塑性变形大,尤其在较高温度时仍可保持较高的强度(一般钢在切削温度上升时强度下降明显),导致 AISI304 奥氏体不锈钢的切削力较大。
常规切削条件下,AISI 304 不锈钢的单位切削力达 2450MPa,比 45 钢高 25%以上。
(2)加工硬化严峻AISI 304 不锈钢在切削加工时伴有较为明显的塑性变形,材料晶格会产生严峻的歪扭;同时,由于奥氏体组织在稳定性方面的缺陷,一小局部奥氏体在此过程中变成了马氏体;此外,奥氏体中存在的杂质化合物会随着切削过程的进展因受热而分解,弥散分布的杂质在外表产生了硬化层,使加工硬化现象格外明显,硬化后的强度σb达1500MPa 以上,硬化层深度 0.1-0.3mm。
(3)切削区局部温度高由于AISI304 不锈钢所需切削力大,且切屑不易切离,使得分别切屑所消耗的功也较大。
常规条件下切削AISI 304 不锈钢比低碳钢高约50%,产生的切削热多。
奥氏体不锈钢的导热性差,AISI304 不锈钢的热导率为 16.3-21.5W/m·K,仅为 45 钢热导率的三分之一,因而使得切削区域的温度较高(通常切削加工时切屑所带走的热量应占切削热量的70%以上),大量切削热集中在切削区和“刀—屑”接触面上,传入刀具中的热量达20%(切削一般碳素钢时该数值仅为9%),使得在同等切削条件下,AISI304 不锈钢切削温度比 45 钢高约 200-300℃。
(4)刀具易产生粘附磨损由于奥氏体不锈钢的高温强度高,加工硬化倾向大,因此,切削负荷重,奥氏体不锈钢与刀具和切屑之间会由于切削过程中其与刀具之间的亲合趋势显著增加,从而不行避开地产生粘结、集中等现象,并生成“切屑瘤”,造成刀具粘附磨损。
不锈钢切削加工技术详解

不锈钢切削加工技术详解1 什么是不锈钢?通常,人们把含铬量大于12%或含镍量大于8%的合金钢叫不锈钢。
这种钢在大气中或在腐蚀性介质中具有一定的耐蚀能力,并在较高温度(>450℃)下具有较高的强度。
含铬量达16%~18%的钢称为耐酸钢或耐酸不锈钢,习惯上通称为不锈钢。
钢中含铬量达12%以上时,在与氧化性介质接触中,由于电化学作用,表面很快形成一层富铬的钝化膜,保护金属内部不受腐蚀;但在非氧化性腐蚀介质中,仍不易形成坚固的钝化膜。
为了提高钢的耐蚀能力,通常增大铬的比例或添加可以促进钝化的合金元素,加Ni、Mo、Mn、Cu、Nb、Ti、W、Co等,这些元素不仅提高了钢的抗腐蚀能力,同时改变了钢的内部组织以及物理力学性能。
这些合金元素在钢中的含量不同,对不锈钢的性能产生不同的影响,有的有磁性,有的无磁性,有的能够进行热处理,有的则不能热处理。
由于不锈钢所具有的上述特性,越来越广泛地应用于航空、航天、化工、石油、建筑和食品等工业部门及日常生活中。
所含的合金元素对切削加工性影响很大,有的甚至很难切削。
2 不锈钢可分为哪几类?不锈钢按其成分,可分为以铬为主的铬不锈钢和以铬、镍为主的铬镍不锈钢两大类。
工业上常用的不锈钢一般按金相组织分类,可分为以下五大类:1.马氏体不锈钢:含铬量12%~18%,含碳量0.1%~0.5%(有时达1%),常见的有1Cr13、2Cr13、3Cr13、4Cr13、1Cr17Ni2、9Cr18、9Cr18MoV、30Cr13Mo等。
2.铁素体不锈钢:含铬量12%~30%,常见的有0Cr13、0Cr17Ti、0Cr13Si4NbRE、1Cr17、1Cr17Ti、1Cr17M02Ti、1Cr25Ti、1Cr28等。
3.奥氏体不锈钢:含络量12%~25%,含镍量7%~20%(或20%以上),最典型的代表是1Cr18Ni9Ti,常见的还有00Cr18Ni10、00Cr18Ni14Mo2Cu2、0Cr18Ni12Mo2Ti、0Cr18Ni18Mo2Cu2Ti、0Cr23Ni28M03Cu3Ti、1Cr14Mn14Ni、2Cr13Mn9Ni4、1Cr18Mn8Ni5N等。
论述不锈钢材料切削加工的难点分析与解决方法

论述不锈钢材料切削加工的难点分析与解决方法摘要:结合实际,对不锈钢材料切削加工的难点分析与解决方法进行研究。
首先对不锈钢材料切削难点内容进行论述,其次在难点问题提出的基础上,给出了相关的解决方法。
关键词:不锈钢;材料切削;加工难点;解决方法1.引言和碳素钢进行对比分析,不锈钢中包含Cr、Ni、N、Nb、Mo等合金元素。
这些元素的存在使得不锈钢具备一定的耐腐蚀性,同时使得其性能得到了很大的提升。
比如马氏体不锈钢4Cr13与45号中碳钢进行对比分析,虽然含碳量是相同的,但是切削加工特性仅有45钢的58%。
2.不锈钢材料切削难点分析在金属加工的过程中,切削不锈钢环节,容易存在断刀、粘刀等问题。
这是因为不锈钢切削环节存在塑性变形过大的问题,导致切屑不易折断,粘连到主材上,造成切削环节的硬化比较严重,每次进刀都会给下一次切削产生硬化层,经过层层积累,不锈钢的切削硬度在大幅增大,切削力也要随之增加。
正式因为不锈钢切削环节存在上述的问题,会造成刀具和工件的摩擦力增大,切削温度也会相对较高,同时不锈钢的热传导系数比较小,散热性能不足,刀具和工具之间存在比较大的温度差,造成加工表面质量比较差。
此外,切削温度的上升会导致刀具磨损严重,刀具前刀面存在月牙洼,导致表面质量比较差,不仅使得加工效率下降,还会造成加工成本的增加。
3.提高不锈钢加工质量的方法3.1 刀具材料的选择刀具的选择对于加工来说是非常重要的,刀具是促进加工质量提升的关键性因素。
刀具如果质量比较差,就无法保证加工零件的合格;选择比较好的刀具,能够促进零件加工质量的提升,如果过高,则会导致资源浪费、成本的增加。
综合考虑到不锈钢材料的散热性比较差、产生硬化层、粘刀严重等特性,在刀具的选择过程中,需要达到耐热性强、耐磨性高、与不锈钢亲和力小等要求,从而可以保证加工可以顺利的进行。
3.1.1 高速钢高速钢中含有W、Mo、Cr、V、Go等合金元素,属于高合金工具钢的类型,工艺性能比较好,强度和韧性非常高,抗冲击振动效果都比较高。
不锈钢切削工作总结

不锈钢切削工作总结
不锈钢由于其自身特性,在切削加工过程中难度较大,容易产生磨损。
经过这次切削工作,我总结几点经验:
1. 使用正确的工具材料。
不锈钢最好使用陶瓷或超级陶瓷的刀具,降低磨损。
使用碳钢或高速钢的刀具在切削不锈钢时寿命较短。
2. 选择合适的切削参数。
切削速度和进给率不能太大,否则容易造成刀具断裂。
速度一般控制在100-150/之间,进给率控制在0.1-0.2/转之间。
3. 减小切屑厚度。
一次切除厚度控制在0.2以下,多次切削完成整个形状,减轻单次切削的负担。
4. 切削材料预热。
将不锈钢材料预热到150-200°,可以减少切削时的力量和延展冷缩应力,有利于延长刀具使用寿命。
5. 增大切削液流量。
合理使用切削液冷却和清洗作用,有效减少风化和磨损。
通过这次总结,下次切削不锈钢时能选择更合适的工具和参数,操作过程更顺利,也为日后不锈钢加工积累经验。
车削不锈钢零件的工艺分析与加工方法

车削不锈钢零件的工艺分析与加工方法摘要:不锈钢是机械装备制造领域的重要材料,因为其具有抗腐蚀性强、耐磨性佳的优势,所以以其为材料制作的零件韧性大、强度高、使用寿命长。
但受材料本身的影响,车削不锈钢零件时常会对刀具的切削性能、加工效率造成影响。
由于不锈钢零件加工对于机械装备而言有着重要意义,所以相关工作人员需采用科学合理的手段解决当下存在的问题,进一步提高车削效果。
本文就车削不锈钢零件的工艺与加工进行研究,以期为相关工作人员进行不锈钢零件的切削以及为研发人员改进切削加工技术提供参考。
关键词:车削;不锈钢零件;加工工艺;机械制造引言:目前,如何进行不锈钢零件的车削加工成为相关工作人员需要深入探讨的课题。
因为不锈钢零件的抗腐蚀性、机械性能较高,在进行车削加工时容易受到一些因素的影响,导致刀具出现磨损、“刀瘤”,不仅影响了刀具的切削性能,还引起了不锈钢零件加工效果与理想不符的情况。
为解决这些问题,下列进行了深入研究,以期解决上述存在的问题,进一步提高不锈钢零件的车削加工效率、质量,并为切削加工技术的不断改进提供参考。
1.不锈钢的车削特性以化学成分为依据,可以将不锈钢划分两个大类,一为铬不锈钢,二为镍不锈钢。
前者一般视情况而定选择含铬量,常见的为12%、17%、27%等。
含铬量通常与其靠腐蚀性能成正比。
铬镍不锈钢的含铬量、含镍量分别在17%~20%之间,8%~11%之间。
不锈钢的机械性能可直接影响其切削加工。
首先,在切削过程中会受到导热性的影响。
具体表现为:不锈钢本身的导热性越差,那么在车削过程中,热量会聚集于刀具上,而不是切屑中,所以刀具的切削性能会受到一定的影响,导致工作效率相对较低。
其次,不锈钢中含有碳化物杂质,其具有较强的磨蚀性,所以在切削时很容易出现磨损问题。
再次,不锈钢可在高温条件下保持较高强度和硬度,而刀具不能。
一旦超过其极限,便会产生塑性变形。
第四,不锈钢具有较强的粘附性,如果其黏附至刀具上时,便会产生“刀瘤”,导致车削工作的开展受到影响。
不锈钢切削加工性能探讨

时切屑不易折断 , 解决断 屑和排 屑 问题 也是顺 利切 削 取 l 。 2 。 5 一 0 较为适 宜 。
V 11 0 . 6№ . 6
NO 2 8 V. 00
不 锈 钢 切 削 加 工 性 能探 讨
李纯彬 , 聂广华 , 江华 侯
( 河南机 电高等专科学校 ,河南 新 乡 ̄3o ) o2
摘 要 : 对 不锈 钢 难加 工 的特 点 , 刀具 材料 、 具几 何 角度 、 削用 量 选择 及 润 滑 等 多个 方 面 进 行 分 析 , 讨 了 针 从 刀 切 探 不 锈 钢 切 削加 工 的合 理切 削条 件 , 给 出 了加 工 实 例。 并 关键词: 不锈 钢 ; 刀具 ; 削用 量 切
一
[63 2 .w ( ・ ) 只有 4 1.3— 22 / m k ] 5钢的 13切 削热导 使刀具磨损 加剧 。 /, 出较慢使切 削 区和刀 面 上 的温 度高 。加 之 不锈 钢 材 2 2 几 何参数选 择 . 料中的高硬度碳 化物 ( TC等 ) 成 的硬 度 点对 刀 如 i 形 前角 选 择 : 切削 热 的产 生 和散 热方 面考 虑 , 从 增 面的摩 擦 以及加工硬化等 原因 , 使刀具 容易磨损 。 大前角可 减小 切 屑热 的产 生 , 削 温 度不 至 于 太 高 , 切
面质 量 , 以得到光 洁的表 面。 难 14 切屑 不易卷 曲和折 断 .
重, 切削产 生 的热量 不易 散掉 。一般 情况 下加 工不锈
钢时都采用 较 大 的前 角 , 大刀 具 前 角 , 增 可较 少 切 屑 由于不锈钢塑性高 、 韧性 大 , 高温 强度 高 , 削 切离 和清 除过 程 中所 遇 到 的阻 力 。所 示 刀具 前 角 且 切
不锈钢材料切削加工的难点分析与解决方法
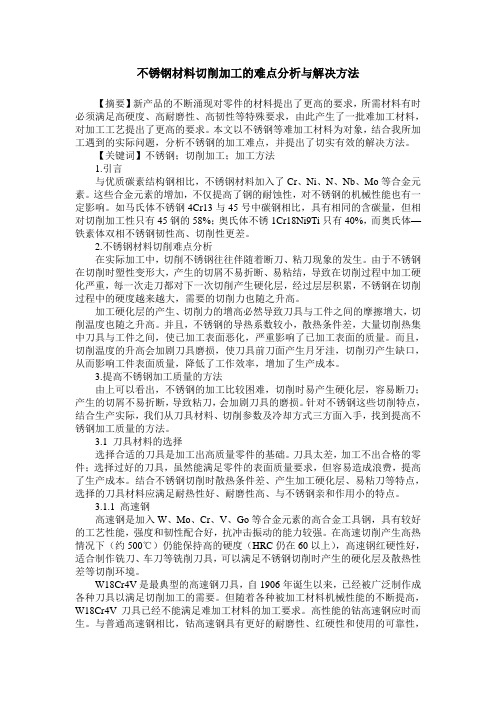
不锈钢材料切削加工的难点分析与解决方法【摘要】新产品的不断涌现对零件的材料提出了更高的要求,所需材料有时必须满足高硬度、高耐磨性、高韧性等特殊要求,由此产生了一批难加工材料,对加工工艺提出了更高的要求。
本文以不锈钢等难加工材料为对象,结合我所加工遇到的实际问题,分析不锈钢的加工难点,并提出了切实有效的解决方法。
【关键词】不锈钢;切削加工;加工方法1.引言与优质碳素结构钢相比,不锈钢材料加入了Cr、Ni、N、Nb、Mo等合金元素。
这些合金元素的增加,不仅提高了钢的耐蚀性,对不锈钢的机械性能也有一定影响。
如马氏体不锈钢4Cr13与45号中碳钢相比,具有相同的含碳量,但相对切削加工性只有45钢的58%;奥氏体不锈1Cr18Ni9Ti只有40%,而奥氏体—铁素体双相不锈钢韧性高、切削性更差。
2.不锈钢材料切削难点分析在实际加工中,切削不锈钢往往伴随着断刀、粘刀现象的发生。
由于不锈钢在切削时塑性变形大,产生的切屑不易折断、易粘结,导致在切削过程中加工硬化严重,每一次走刀都对下一次切削产生硬化层,经过层层积累,不锈钢在切削过程中的硬度越来越大,需要的切削力也随之升高。
加工硬化层的产生、切削力的增高必然导致刀具与工件之间的摩擦增大,切削温度也随之升高。
并且,不锈钢的导热系数较小,散热条件差,大量切削热集中刀具与工件之间,使已加工表面恶化,严重影响了已加工表面的质量。
而且,切削温度的升高会加剧刀具磨损,使刀具前刀面产生月牙洼,切削刃产生缺口,从而影响工件表面质量,降低了工作效率,增加了生产成本。
3.提高不锈钢加工质量的方法由上可以看出,不锈钢的加工比较困难,切削时易产生硬化层,容易断刀;产生的切屑不易折断,导致粘刀,会加剧刀具的磨损。
针对不锈钢这些切削特点,结合生产实际,我们从刀具材料、切削参数及冷却方式三方面入手,找到提高不锈钢加工质量的方法。
3.1 刀具材料的选择选择合适的刀具是加工出高质量零件的基础。
刀具太差,加工不出合格的零件;选择过好的刀具,虽然能满足零件的表面质量要求,但容易造成浪费,提高了生产成本。
不锈钢的切削加工性

不锈钢的切削加工性与45钢相比,不锈钢1Cr18Ni9Ti不锈钢的相对可切削性约为0.3-.05之间,是一种难切削材料。
其难加工性主要表现在:1、高温强度和高温硬度高,一般钢材切削时,随着切削温度的升高其强度会明显降低,切屑易被切离,而不锈钢1Cr18Ni9Ti在700度时仍不能降低其机械性能,故切屑不易被切离,切削过程中切削力大,刀具易磨损。
2、塑性和韧性高,虽然不锈钢1Cr18Ni9Ti的抗拉强度和硬度都不高,但综合性能很好,塑性和韧性高,它的延伸率、断面收缩率和冲击值都较高,不锈钢1Cr18Ni9Ti的延伸率是40%,是40#的210-237%,是45#的250-280%,是20Cr、40Cr钢的400-500%,所以切屑不易切离、卷曲和折断,切屑变形所消耗的功能增多,如切除一定体积的不锈钢1Cr18Ni9Ti 所消耗的能量比切除相同体积的低碳钢约高50%,并且大部分能量转化为热能,使切削温度升高。
3、不锈钢1Cr18Ni9Ti不易加工,切屑不易切离和折断,故刀具和工件之间所产生的摩擦热也多,而不锈钢1Cr18Ni9Ti的导热率低(约为普通钢的1/2-1/3),散热差,由切屑带走的热量少。
大部分的热量被刀具吸收,致使刀具的温度升高,加剧刀具磨损。
4、不锈钢对其他金属材料的亲和性强。
因此在和其它金属接触时,在一定的温度和压力下就会产生粘附现象。
在切削过程中,刀具易产生积屑瘤,不易获得表面粗糙度等级高的加工表面。
5、加工硬化倾向强。
奥氏体不锈钢强度一般为δb=539Mpa,但在室温冷加工时,由于加工硬化和形变会诱发马氏体转变,使强度提高至δb=1568 Mpa,这样就大大增加了切削时的摩擦、磨损和切削力,易使刀具磨损,并影响工件的表面粗糙度。
6、不锈钢1Cr18Ni9Ti材料中有许多微细的碳化物(如TiC)颗粒,会加剧刃具的磨损。
熔点低,易于粘刀,切削过程中易形成积屑瘤,由于不锈钢的韧性大,在切削过程中,刀具前导面和切屑之间存在很大的压力和很大高的温度,切屑很容易粘附在刀刃上,形成积屑瘤,影响表面加工质量。
浅谈不锈钢材料的车削加工

浅谈不锈钢材料的车削加工不锈钢是一种耐腐蚀、耐热、耐高温的材料,广泛应用于机械制造、汽车制造、航空航天、建筑装饰等行业。
在不锈钢的车削加工中,需要特别注意材料的性质、工艺参数以及切削工具的选择。
不锈钢的性质决定了它的车削加工相对复杂。
首先,不锈钢的硬度较高,所以切削力比较大,对车削刀具的耐磨性提出了更高的要求。
其次,由于不锈钢具有较好的导热性,切削时容易产生热量,导致刀具快速磨损和加工表面产生尺寸偏差,因此需要采取合理的降温和冷却措施。
此外,不锈钢还具有较好的韧性和塑性,容易产生切削硬化,使切削加工更加困难。
在不锈钢的车削加工中,选择合适的车削工艺参数非常重要。
首先,应根据不锈钢的成分和硬度,选择合适的切削速度、进给速度和切削深度。
一般来说,低硬度的不锈钢适合选择较高的切削速度和进给速度,以提高生产效率;而高硬度的不锈钢则需要选择较低的切削速度和进给速度,以避免过度切削或切削过热。
此外,还需根据加工的具体要求和工件的尺寸,选择合适的刀具和切削方式。
切削工具的选择也对不锈钢的车削加工起着至关重要的作用。
不锈钢的硬度和耐热性,要求使用高强度、高耐磨性的刀具。
一般来说,硬质合金刀具可以满足这些要求,但也需要根据具体的加工情况选择合适的刀具材料和刀具几何形状。
此外,应根据切削参数和加工要求,合理选择切削润滑剂和冷却液,以降低切削温度、延长刀具使用寿命和提高加工质量。
总之,不锈钢材料的车削加工相对复杂,需要注意材料的性质、工艺参数和切削工具的选择。
在实际生产中,需要根据不锈钢的具体类型和加工要求,采取合适的加工工艺和切削方式,以提高加工效率和加工质量。
此外,还需加强刀具的研发和刀具涂层技术的应用,以适应不锈钢材料的车削加工需求。
不锈钢铰刀与铰削工艺

余量要取得小一些 ,见表 3 。
表 3 铰 子前 加 工 余 量 的 经 验 值 L
铰孔直径/ mm
3~4 5~ l l
I ~ I 2 8 l ~2 9 8
钻孔余量/ 扩孔或镗孔余 量/ mm mn
0. 3 l
I5 . 2
磨 损 极 限
公 差 的百 分 数 ( ) % 上 偏 差 下 偏 差 公 差 尺 寸 /t b m
铰孔 孔 径/ mm
5~ 8 8~ l 5 l 5~2 5 2 5~3 5
D > l mm 0
例如 :加工不锈钢  ̄ 0 7 的铰刀尺 寸及公差的计 3H 孔
算 。由公差表查得公差为 0 0 1 。则 : .2 mm 铰刀直径的上偏 差为 o o 1 0 = . lmm .2 mmx7 % 0 0 5 铰刀直 径的下偏 差为 00 1 m x 0 =0 0 9 .2 m % 4 .0 mm 铰 刀的制造公差为 0 0 1 3 % =0 0 6 .2 mm x 0 .0 mm
大 ,切屑不容易切离和形成 ,而且切屑 容易在铰 刀的齿 槽 内挤塞 ,从而影响孔表面的加工质量 。根 据不锈 钢的 特性 ,从实验可知不锈钢铰孑 余量要 比普通碳 素钢 铰孑 L L
1 不锈钢铰刀的结构 .
( )铰刀直径的尺寸及公差计算 由于不锈钢材 料 1 的特性较为复杂 ,选择 铰刀 时 ,不但要考虑 被加工孔 的 公差 ,而且要 考 虑 铰削 时孔 的 扩 张量 以及 铰 刀的 磨损
造铰刀材料 外 ,控制 加工 工艺参 数 ,消除各误 差 因素 ,
是行之有效 的方法 。
2 不锈钢铰孔时的切削工艺参数 .
()加工余量 1 铰孔时加工余量 的合 理性 ,对 铰孔
怎样对不锈钢进行铰孔

怎样对不锈钢进行铰孔?对不锈钢铰孔时,经常遇到的问题是:孔表面容易划出沟槽,粗糙度差,孔径超差,呈喇叭口,铰刀易磨损等。
不同种类不锈钢的切削加工性不同,在铰孔中所表现出的问题也不一样,如对1Cr18Ni9Ti等奥氏体不锈钢和耐浓硝酸不锈钢铰孔时,主要是铰刀磨损问题;而对2Cr13等马氏体不锈钢铰孔时,主要是不容易保证铰孔的粗糙度和尺寸精度问题。
为了避免这些问题,应注意以下事项:1) 合理选择铰刀和铰削用量,是保证铰孔顺利进行的关键。
2)提高预加工工序质量,防止预加工孔出现划沟、椭圆、多边形、锥度或喇叭口、腰鼓形状、轴心线弯曲、偏斜等现象。
3) 保持工件材质硬度适中,尤其对2Cr13马氏体不锈钢,调质处理后的硬度在HRC28以下为宜。
4) 正确安装铰刀和工件,铰刀必须装正,铰刀轴线应和工件预加工孔的轴线保持一致,以保证各刀齿均匀切削。
5) 选用合适的切削液,可以解决不锈钢的切屑粘附问题,并使之顺利排屑,从而降低孔表面粗糙度和提高刀具耐用度。
一般以使用硫化油为宜,若在硫化油中添加10%~20%CCl4或在猪油中添加20%~30%CCl4,对降低表面粗糙度有显著的效果。
由于CCl4对人体有害,宜采用硫化油85%~90%和煤油10%~15%的混合液。
铰刀直径较大时,可采用内冷却方式。
6) 认真注意铰孔的过程,严格检查刀齿的跳动量,是获得均匀铰削的关键。
在铰削过程中,注意切屑的形状,由于铰削余量小,切屑呈箔卷状或呈很短的螺卷状。
若切屑大小不一,有的呈碎末状、有的呈小块状,说明铰削不均匀。
若切屑呈条的弹簧状,说明铰削余量太大。
若切屑呈针状、碎片状,说明铰刀已经磨钝。
还要防止切屑堵塞,应勤于观察刀齿有无粘屑,以避免孔径超差。
使用硬质合金铰刀铰孔时,会出现孔收缩现象,为防止退刀时将孔拉毛,可采取加大主偏角来改善这种情况。
不锈钢材料磨削工艺分析

不锈钢材料磨削工艺分析不锈钢材料磨削工艺分析口韩中国空空导弹研究院雪河南洛阳471009摘要:不锈钢材料导热性差,韧性大,热强度高,线膨胀系数高,且多数不锈钢材料不能被磁化.以典型不锈钢材料1Crl8Ni9Ti为例,分析了不锈钢材料磨削特性及其加工难点,并针对其特性及难点进行了工序设计及加工方法优化,应用于实际磨削加工过程,取得了良好的效果.关键词:难磨材料1Cr18Ni9Ti变形磨削工装磨削参数子程序中图分类号:TH161;TG506.71文献标识码:B文章编号:1000—4998f2011)o5—0064—03随着科学技术和工业的发展,人们对机械产品及其零部件使用性能的要求越来越高.例如.要求材料比强度高,耐高温,热强性高,能承受复杂应力以及耐腐蚀等.为此,许多零件采用新型材料制造,在这些新型材料中,许多是难加工材料,如不锈钢,钛合金,高温合金等.所谓难磨材料系指磨削时加工性比较差的材料.难磨材料的显着特点是磨削力大,磨削温度高,磨削表面粗糙度差,加工表面层形成较大的残余拉应力,砂轮寿命低,磨削比很低,极易发生磨削烧伤等.由于磨削加工表面完整性差,因而降低了材料的疲劳寿命.在实际加工中,不锈钢材料零件的磨削存在材料韧性大,磨屑易粘附砂轮,磨削过程不易散热,材料线膨胀系数大使零件易变形,多数不锈钢不能被磁化引起装夹困难等问题.因此,本文对不锈钢材料零件磨削进行分析研究,并通过典型零件磨削实例来介绍不锈钢的磨削特性,磨削参数选择及如何在保证磨削质量的前提下提高磨削效率.1不锈钢材料磨削特点1)不锈钢的导热系数小,磨削时的高温不易导出,工件表面易产生烧伤,退火等现象,退火层深度有时可达0.01~0.02mm.磨削过程中产生严重的挤压变形,导致磨削表面产生加工硬化,特别是磨削奥氏体不锈钢时,由于奥氏体组织不够稳定,磨削后易产生马氏体组织,使表面硬化严重.2)不锈钢的韧性大,热强度高,而砂轮磨粒的切削刃具有较大的负前角.磨削过程中磨屑不容易被切离.切削阻力大,挤压,摩擦剧烈,单位面积磨削力很大.磨削温度可达l000~1500℃.同时,在高温高压的作用下,磨屑易粘附在砂轮上,填满磨粒间的空隙,使磨粒失去切削作用.不锈钢的类型不同,产生砂轮堵塞收稿日期:2010年12月2011/5的情况也不相同.如磨削耐浓硝酸不锈钢及耐热不锈钢,粘附,堵塞现象比1Crl8Ni9Ti严重,而1Crl3,2Cr13等马氏体不锈钢就比较轻.3)不锈钢的线膨胀系数大,在磨削热的作用下易产生变形,其尺寸难以控制.尤其是薄壁和细长的零件,此现象更为严重.4)多数类型的不锈钢不能被磁化.在平面磨削时.只能靠机械夹固或专用夹具来夹持工件.利用工件侧面夹紧工件,容易产生变形和造成形状或尺寸误差,薄板工件更为突出,同时也会引起磨削过程中的颤振而出现鳞斑状的波纹.2不锈钢材料磨削方法1)选择切削性能较好的单晶刚玉磨料,粒度为46~60#.硬度为L~V,组织较疏松的砂轮.2)选择立方氮化硼砂轮,砂轮圆周速度保持在15~30m/s,径向进给量一般在0.002~0.O1mm之间.3)磨削过程中必须充分冷却,以带走大量的磨削热及进行冲刷,防止砂轮堵塞和工件表面烧伤.冷却液必须清洁,不能混入磨屑或砂粒.以免将工件拉毛.磨削不锈钢的冷却液,一般选用冷却性能较好的乳化液, 流量为20~40L/min,砂轮直径大时为80L/min.4)应及时修整砂轮,粗磨时砂轮要修整粗一些,精磨时砂轮要始终保持锋利.以免过热烧伤.修整后的砂轮两侧转角处.不允许有毛刺存在.5)表面粗糙度值要求较高的零件磨削时,粗,精磨应分别进行.精磨余量一般留0.05mm为宜,工件装夹误差大时可留0.1mm.6)不锈钢磨削余量应取小一些,外圆磨削时,直径磨削余量为0.15~0.3mm,精磨余量为0.05mm.内圆磨削的余量与外圆磨削基本相同.平面磨削时,对面积小,刚性好的零件,单边留余量为0.15~0.2mm,刚性差,面积大的零件,单边留磨削余量0.25~0.3mm.机械制造9卷第561期3不锈钢磨削的注意事项1)磨削不锈钢时,减小砂轮的粘附阻塞是提高磨削效率的重要因素,加工中要经常修整砂轮,保持切削刃的锋利.2)磨削不锈钢的砂轮选用自锐性好的砂轮是主要目标.一般选用硬度低的砂轮效果好,但也不能选择硬度太低,否则磨粒未磨钝就脱落.推荐选用J级. 3)为减小磨削时砂轮的粘附阻塞,应选用粗粒度的砂轮.粗磨时用36-46号粒度,精磨时选用60号粒度.4)磨削不锈钢时,采用GC砂轮可提高磨削效率.5)磨削液选用必须兼顾润滑和清洗两种作用,供给充足.可选用表面张力小,含极压添加剂的乳化液, 可获得高的表面质量.6)磨削用量的选择可根据加工余量确定.4不锈钢材料磨削加工典型实例4.1零件磨削难点分析端圈零件材料为1Crl8Ni9Ti,内孔尺寸62.86mm.深15mm的通孔,零件最薄处壁厚为0.2mm,且内孔外圆要求同轴度0.02mm.零件如图1所示.通常此类零件加工方法是车削加工,因为~LsJ,又深而且壁薄,并且材料韧性大,难加工,车床不能很好保证尺寸精度.基于此,我们选择数控坐标磨床来进行磨削加工,需解决的问题有确定零件装夹方式,砂轮的加工深度,零件的冷却,润滑,合理的磨削参数等.4.2解决措施由于该零件壁极薄易发生加工变形,且材料1Crl8Ni9Ti的导热性能极差,因此给零件的磨削带来机械制造49卷第561期许多困难.对此制定了如下解决方法:1)根据零件的技术要求,自制工装夹具解决零件的装夹问题.由于零件为薄壁零件,外圆不能受力,工装采用零件西7.8x0.6mm端面台压紧装夹零件,为保证加工的孑L与外圆同轴,设计自制工装如图2,图3所示.2)粗磨选用直径2.5mm,粒度46号的单晶刚玉砂轮,白刚玉砂轮具有良好的切削性和自锐性能,可使切屑变形小,磨削力和磨削温度低,而且磨粒不易变钝;良好的自锐性则可保证磨粒再磨钝后立即脱落.精磨时选用直径2.5mm的立方氮415硼(CBN)砂轮,由于CBN化学稳定性好,不与铁族元素发生415学亲和作用,因而CBN砂轮在磨削中不易黏附堵塞,可显着提高磨削比,又因其切削能力强,磨削力和磨削热均较低,工件表面不易产生磨削烧伤,大大改善了不锈钢磨削加工表面完整性.砂轮硬度取H;磨削壁薄零件时由于磨削热不易散出,工件易变形.因此应采用较软砂轮.采用陶瓷结合剂砂轮,因为陶瓷结合剂不仅能保持砂轮磨粒的切削性能,且不怕潮湿,有多孔性,能获得较高的生产率.另外,对刀杆进行改制.使其加工深度达15mm以上.3)为了在加工中使砂轮得到充分的冷却润滑,并保证砂轮表面的清洁,在工装压紧螺母侧面加工进水孔(如图3所示).4)为保证零件同轴度0.02mm.加工零件时,磨削加工前用千分表找正击5.67mm孔在0.005mm以内.精磨时采用风动磨头来装夹砂轮进行加工,砂轮转速为80000~100000r/min,行星运动800~1000r/min 进给量0.001~0.002mm,往复行程频率为0.5Hz,进刀完毕后,再进行光磨来确保零件表面粗糙度,光磨往复次数不小于5O次.5)编制专用的磨通孔循环子程序来进行磨削加2011/5多互佬圆锥面钻引专用夹粤的设计口胡运林四川I机电职业技术学院四川攀枝花617000摘要:通过对高压管道入口法兰的钻削夹具的设计,解决了在锥面上进行多工位钻孔的加工难点,使工件在钻削加工时,能准确的定位,可靠的夹紧和快捷的定位调整.并将钻模板设计成铰链式.方便工件的装卸.关键词:铰链式端面凸轮锥面定位中图分类号:TH162+.1文献标识码:B文章编号:1000—4998f2011)o5—0066—03 在多工位圆锥面钻孔加工时.由于加工刀具与工件之间难以占据正确的加工位置.使加工难度较大.如图1所示高压管路入口法兰,加难度在于8一西11孔及相应沉孔西17的加工,因为在锥面上加工,工件装夹困难.工件与刀具即钻头之间难以形成正确的位置关系.且属于多工位加工,加工完一孔后下一孔的快速准确定位也是加工中需要解决的问题.为保证加工质量,收稿日期:2010年11月提高工件定位和夹紧的效率,需设计专用钻削夹具来完成8一西11孔及相应沉孑L西17的加工.在钻削加工8一西11孔及相应沉孔西l7前,需完成工件外形轮廓及内TL~tl工.在30.斜面未车削前,完成21孔的钻削加工,以避免在斜面上钻孑L给加工带来的难度,而西21孑L将作为8一11孔及相应沉孔l7的加工定位孑L.以下为该工件的加工工艺安排:1)车削:完成工件外形和内孔的加工,30.斜面及工.该子程序循环利用坐标磨特有的行星螺旋线加工轨迹.由机床轴实现自动进给,对刀完毕开始磨削时.先将磨头退刀0.005mm下入孑L底,由孔底开始进刀,向上走刀,同时磨头由机床带动作行星运动进行磨削,自下而上的磨削能大幅降低零件的弯曲变形.5结论通过对不锈钢材料磨削加工典型案例的分析,得出了以下结论:1)不锈钢工件磨削加工时,因其薄壁件较多且多数不锈钢不导磁.要设计合适的装夹方法,来保证零件加工质量并防止加311变形.2)磨削不锈钢砂轮优先选择有以下几种:①切削性能较好的单晶刚玉砂轮,粒度选用范围为36~60#(粗磨时用36~46号粒度,精磨时选用60号粒度),硬度为L~v,组织较疏松的砂轮;②立方氮化硼砂轮:砂轮圆周速度保持在15~30rn/s,径向进给量一般在0.002-0.01 mm之间,选用CBN砂轮可大大提高磨削效率.3)磨削过程中必须充分冷却,以带走大量的磨削热和进行冲刷,防止砂轮堵塞和工件表面烧伤.冷却液选择必须兼顾润滑和清洗两种作用,使用时必须供给充足.保持清洁,不能混入磨屑或砂粒,以免将工件拉毛.磨削不锈钢的冷却液,一般选用表面张力小,冷却性能较好的极压乳化液,选用小直径砂轮时流量为20-40L/min2011/54)应及时修整砂轮,粗磨时砂轮要修整粗一些,精磨时砂轮要始终保持锋利,以免过热烧伤.修整后的砂轮两侧转角处,不允许有毛刺存在.5)不锈钢磨削余量应取小一些,内圆磨削时.直径磨削余量为0.15~0.3mm,精磨余量为O.05mm.外圆磨削的余量与内圆磨削基本相同.平面磨削时,对面积小,刚性好的零件,单边留余量为0.15~0.2mm,刚性差,面积大的零件,单边留磨削余量0.25~O.3mm.6)利用坐标磨床磨削通孔时,选用自编的专用磨孔循环子程序能更好的保证零件尺寸公差及表面质量,且能提高加工效率.不锈钢零件的磨削在现代制造业中非常常见,因此通过加工实例从各个方面分析研究此类零件的磨削加工过程.有助于更深地了解不锈钢磨削加工特点,从而保证产品质量.并提高零件的加工效率.参考文献[1]荆长生.机械制造工艺学[M].西安:西北工业大学出版社, 1995.[2]孟少农.机械加工工艺手册(第二卷)[M].北京:机械工业出版社.1996.[3]杜存臣.奥氏体不锈钢在工业中的应用[J],化工设备与管道,2003,40(2).[4]'任敬心.难加工材料的磨削[M].北京:国防工业出版社, 1999.△(编辑丁罡)机械制造49卷第561期。
不锈钢材料铣削加工工艺分析

不锈钢材料铣削加工工艺分析摘要:不锈钢材料因其导热性能差、热性大、热强度高以及膨胀系数大的优势被广泛的应用在各种机械工件加工中。
本文通过给出不锈钢在铣削加工中的加工参数,有效的解决了传统不锈钢材料切削加工难题,旨在为同行日后工作提供参考。
关键词:不锈钢;车削加工;耐磨材料随着生产力的提高和科学技术的进步,人们对机械产品以及零件性能要求日益严格,比如对材料的强度、耐高温、承力、耐腐蚀性能提出了新要求。
为此,目前许多零件制造企业和制造商都不断的引进各种先进的材料,比如铝合金、钛合金以及不锈钢等。
在这些材料中,以不锈钢材料的应用最为广泛,已成为当前各类机械产品中司空见惯的一种。
1 不锈钢材料概述通常来说,人们将含镉量或者是含镍量大于10%的合金钢材称之为不锈钢。
这种金属材料在大气中有着良好的抗腐蚀性能,并且在450摄氏度的条件下都具备良好的刚性。
根据过去多年的工作实践总结得出,一般来说钢材中铬含量超过12%的时候,它在与氧化性介质的接触上能够自我发出电化学作用,使得钢材表面形成一层富有铬元素的氧化层,从而保护金属内部不受腐蚀;但是在非氧化性质的影响下,这种元素一般都不会发生反应,也不会形成坚固的防护膜。
因此,为了更好的提高钢材的耐腐蚀性和强度,通常都是在原来的不锈钢基础上添加其他的微量元素,比如锰、铜等,这些元素本身都具备良好的抗腐蚀性,同时这些元素的应用有效的改变了内部组织及内部物理性质。
这些合金元素在钢材中的含量不同,对于不锈钢材料产生的影响也不尽相同,它所产生的性能包含了磁性、热性等。
由于不锈钢材料具备着上述的种种优势,因此它当前被广泛的应用在航空、航天、化工以及建筑等工业部门。
但是不锈钢材料因为内部存在这些特殊元素,这就给切削加工造成影响。
2 不锈钢切削加工工艺的特点不锈钢切削加工工艺与传统的碳钢加工工艺相差无几,通常都是采用普通的刚才切削加工进行比较,通过利用数控车床的进行处理和加工。
根据不锈钢在切削加工的过程中,具体的加工工艺特点包含以下方面:2.1 加工硬化严重在众多的不锈钢切削加工中,以奥氏体为核心的加工特点最为突出,这种加工方式在切削应力的作用下,大部分的奥氏体逐渐的转变成为马氏体;再加上其他的一些散杂物质受到加热作用发生分解,这使得整个切削加工的过程中极容易产生一层硬化层,甚至是在前层加工基础上产生严重的硬化现象,给后续工作的开展造成极大的影响。
不锈钢加工工艺

不锈钢加工工艺在采取钻、铰、镗工艺加工一些奥氏体组织及马氏体组织不锈钢材料如1Cr18Ni9Ti、2Cr13孔时,加工过程中会出现刀具磨损加快、加工表面完好性差、切屑排除困难等共性问题,严重影响了此类材料零件的加工质量、生产周期及加工成本。
按照金属工艺学、金属切削原理等理论对上述材质加工难点进行分析,摸索出一套行之有效的不锈钢材料钻、铰、镗加工工艺。
不锈钢材料加工难点分析不锈钢材料加工难点主要有以下几个方面:切削力大,切削温度高该类型材料强度大,切削时切向应力大、塑性变形大,因而切削力大。
此外材料导热性极差,造成切削温度升高,且高温往往集中在刀具刃口附近的狭长区域内,从而加快了刀具的磨损。
加工硬化严重奥氏体不锈钢以及一些高温合金不锈钢均为奥氏体组织,切削时加工硬化倾向大,通常是普通碳素钢的数倍,刀具在加工硬化区域内切削,使刀具寿命缩短。
3. 容易粘刀无论是奥氏体不锈钢还是马氏体不锈钢均存在加工时切屑强韧、切削温度很高的特点。
当强韧的切屑流经前刀面时,将产生粘结、熔焊等粘刀现象,影响加工零件表面粗糙度。
刀具磨损加快上述材料一般含高熔点元素、塑性大,切削温度高,使刀具磨损加快,磨刀、换刀频繁,从而影响了生产效率,提高了刀具使用成本。
不锈钢零件加工工艺通过上述加工难点分析,不锈钢的加工工艺及相关刀具参数设计与普通结构钢材料应具有较大的不同,其具体加工工艺如下:1.钻孔加工在钻孔加工时,由于不锈钢材料导热性能差,弹性模量小,孔加工起来也比较困难。
解决此类材料的孔加工难题,主要是选用合适的刀具材料,确定合理的刀具的几何参数以及刀具的切削用量。
钻削上述材料时,钻头一般应选用W6Mo5Cr4V2Al、W2Mo9Cr4Co8等材质的钻头,这些材质钻头缺点是价格比较昂贵,而且难以采购。
而采用常用的W18Cr4V普通标准高速钢钻头钻孔时,由于存在顶角较小、切屑太宽而不能及时排出孔外、切削液不能及时冷却钻头等缺点,再加上不锈钢材料导热性差,造成集中在刀刃上的切削温度升高,容易导致两个后刀面和主刃烧伤及崩刃,使钻头的使用寿命降低。
不锈钢分类及切削性能解析

不锈钢分类及切削性能解析⼀不锈钢分类及定义1 不锈钢定义⼀种主要成分是铁 (Fe) 元素的合⾦铬含量⾼于12%碳含量通常较低 (C ≤ 0.05%)添加镍 (Ni)、铬 (Cr)、钼 (Mo)、铌 (Nb) 和钛 (Ti) 等各种合⾦元素,赋予材料不同的特性,例如耐腐蚀性和⾼温强度。
铬 (Cr) 与氧 (O) 结合,在钢表⾯产⽣⼀层氧化铬 (Cr2O3)保护膜,从⽽使这种材料具有不锈特性。
2 切削加⼯性概述不锈钢的切削加⼯性依其合⾦元素、热处理和制造⼯艺 (锻造、铸造等) 的不同⽽不同。
通常,合⾦含量越⾼,切削加⼯性就越差,但所有不锈钢组均包含易切削或切削加⼯性改进的材料。
长切屑材料切削控制在铁素体/马⽒体不锈钢加⼯中⽐较容易,但在奥⽒体和双相不锈钢加⼯中则变得更复杂特定切削⼒:1800-2850 N/mm2加⼯时产⽣⾼切削⼒、积屑瘤、⾼热量和加⼯硬化表⾯氮 (N) 含量较⾼的奥⽒体组织可提⾼强度并提供⼀定的耐腐蚀性,但却会降低切削加⼯性,同时增加形变硬化添加的硫 (S) ⽤于改善切削加⼯性⾼碳含量 (> 0.2%) 将导致相对较重的后⼑⾯磨损钼 (Mo) 和氮 (N) 会降低切削加⼯性。
但是,它们能够提供耐酸侵蚀特性并且有助于增加⾼温强度有的不锈钢切削加⼯性经过改进,改进⽅法是优化硫化物和氧化物的含量,⽽没有削弱耐腐蚀性。
3 不锈钢的分类及材料参数⼆⼯件材料的识别不锈钢的显微组织主要取决于其化学成分,其中,主要合⾦成分铬 (Cr) 和镍 (Ni) 最为重要。
事实上,由于⽤于稳定奥⽒体或铁素体的其他合⾦成分的影响,显微结构的变化范围可能很⼤。
热处理或某些情况下的冷加⼯也可能改变显微结构。
沉淀硬化铁素体或奥⽒体不锈钢具有更⾼的抗拉强度。
1 铁素体和马⽒体不锈钢定义:⼀般铬 (Cr) 含量为12-18%。
只存在少量的其他合⾦元素。
马⽒体不锈钢的碳含量相对较⾼,因此会硬化。
铁素体不锈钢具有磁性。
- 1、下载文档前请自行甄别文档内容的完整性,平台不提供额外的编辑、内容补充、找答案等附加服务。
- 2、"仅部分预览"的文档,不可在线预览部分如存在完整性等问题,可反馈申请退款(可完整预览的文档不适用该条件!)。
- 3、如文档侵犯您的权益,请联系客服反馈,我们会尽快为您处理(人工客服工作时间:9:00-18:30)。
不锈钢铰削加工工艺性能的分析
摘要:本文介绍了不锈钢铰削加工工艺性能的特点和使用时容易出现的不良现象及原因,提出完善铰削加工工艺性能的措施。
结合铰削加工工艺的实际使用情况,指出不锈钢在铰削加工中合理的铰削加工工艺,进一步提高加工准确性和综合性能。
关键词:不锈钢;铰削加工;工艺性能;分析
前言
不锈钢材料本身具备良好的化学稳定性和抗腐蚀性,在外界物质的影响下也会体现出一定的自我保护能力,较强的强度使不锈钢材料大量应用在化工、建筑等领域中。
但是不锈钢中含有大量的合金元素,在对材料进行铰削加工时,这些内部的合金元素会提高不锈钢材料的韧性、塑性变形、热强度,加工出现严重的硬化现象,大大提高了铰削加工的难度。
不锈钢材料自身会产生大量的铰削热,破坏自身的结构,对铰削加工的刀具来说也会加大道具磨损的情况。
基于此,在对不锈钢材料进行铰削加工时,需要结合材料的综合性能指标,确定合理的铰削加工工艺模式,使铰削加工工艺可以简化难加工材料的加工流程。
1.不锈钢铰削加工工艺性能特点
1.1加工硬化严重
在对不锈钢材料进行铰削加工时,奥氏体和奥氏体+铁素体的不锈钢材料的加工硬化现象最为突出,加工难度也越大,奥氏体不锈钢硬化后的强度为1470-1960MPa,随着加工工艺性能的改变,强度也会随着改变,如果强度处于提高的状态,不锈钢材料的屈服极限也会升高。
但是,退火状态下的奥氏体不锈钢材料的屈服极限不会超过自身强度30%-45%,而加工硬化后达85%-95%,这就说明,不锈钢材料的加工硬化层深度比较深,已经可以影响到材料的形态。
不锈钢材料在铰削加工中会展现出非常大的塑性,强化系数也很大,但奥氏体不够稳定,加工形态无法有效控制,在化合物杂质的作用下,铰削热的作用会直接作用在材料上,大大提高了材料硬化水平[1]。
1.2铰削力度大
随着不锈钢使用范围的扩大,不锈钢材料在铰削过程中表现出的塑性变形能力也会提高,这时操作人员会施工会增加铰削力,尤其是奥氏体不锈钢材料,综合材料的强度和韧性,施工的力度的伸长率超过45号钢的1.5倍以上,而不锈钢材料出现的加工硬化现象严重,会增加铰削的难度。
不锈钢材料本身指标系数的改变,在较高热强度的条件下,增大的铰削抗力,切屑的卷曲折断也比较困难[2]。
1.3铰削温度高
不锈钢材料在铰削时,由于刀具作用在不绣钢材料表面时间的加长,不锈钢材料的塑性变形及与刀具间的摩擦力会加大,在铰削操作中就会产生大量的铰削热。
在不锈钢材料导热系数范围的比较下,产生的铰削热已经高出原件温度的1/2-1/4,大量铰削热在不锈钢材料表面的长时间停留,会转移部分铰削热到刀具上,降低了切屑接触界面的性能,也阻碍了铰削热的消除途径,导致铰削温度过高[3]。
2.不锈钢铰削加工工艺的应用以及提高加工工艺性能的措施
2.1不锈钢铰削加工工艺的应用
利用铰刀从已加工的孔壁切除不锈钢材料,以获得精确的孔径和几何形状以及较低的表面粗糙度的切削加工,不锈钢铰削加工一般在钻孔、扩孔或镗孔以后进行,用于加工精密的圆柱孔和锥孔,加工孔径范围一般为3~100毫米,操作人员也可以结合实际的使用需求,调节孔径。
由于铰刀的切削刃长,铰削时各刀齿同时参加切削,这样可以提高不锈钢加工和生产的效率,实际操作时,固定不锈钢材料,由铰刀旋转并向孔中作轴向进给。
在车床上铰削时,不锈钢要能随着加工流程进行旋转,铰刀作轴向进给,铰削过程中,铰刀前端的切削部分进行切削,后面的校准部分起引导、防振、修光和校准作用。
铰孔在不锈钢材料铰削加工属于二次精加工,其作用是满足对孔的尺寸、形状等要求,为了提高铰削加工的精度,提高加工工艺的性能,操作人员必须要按照规范的行为和方法对不绣钢材料进行加工,利用合理的技术降低铰削加工的难度[4]。
2.2提高不锈钢铰削加工工艺性能的措施
首先,根据对不锈钢材料的分析,确定铰削加工方案,选择合适的刀具材料,根据铰削加工的经验,操作人员需要使用含有Co、Al等高性能的高速钢刀具,不锈钢材料的不同使用刀具材料也可以不同,但是要确保不会因为不锈钢材料较强的强度,而破坏刀具结构。
在实际铰削加工中,操作人员要严格控制铰削加工的深度,铰削余量不宜过大或过小,以免降低孔的精度,影响到铰刀的使用,切削速度一般情况下会控制在小于3m/min的范围内。
提高不锈钢铰削加工工艺性能最重要的环节就是改进加工工艺,实际操作之前需要对不锈钢工件进行适当热处理,使其可以具备一定的抵抗热度的能力,并要保持工件材质硬度不变,针对奥氏体不锈钢材料来说,可在高温下退火,通过这种途径降低自身的切屑硬度,改善其切削加工性能。
对马氏体不锈钢来说,采用调质处理的方式最合适,调质处理可以把马氏体不锈钢的硬度控制在28-35HRC之间,尤其对2Cr13马氏体不锈钢,调质处理后的硬度应在28HRC以下,这种状况下不锈钢铰削加工工艺性能最好[5]。
提高不锈钢铰削加工工艺性能还需要操作人员注意加工工序的步骤,确保每一个加工步骤的准确性,防止出现不正规的操作,而破坏加工孔的结构,刀具安装要满足实际加工的需求,使刀具和加工工件可以处于正确的加工位置。
铰刀必
须装正,避免加工过程中刀具的松动对操作人员造成伤害,铰刀轴线应和工件预加工孔的轴线保持一致,以保证各刀齿均匀切削,提高加工工件的综合质量。
做好充分的准备之后,操作人员要注意严格控制铰削的全过程,消除一切影响因素的影响,注意铰孔的过程,对使用的刀具进行严格检查,确保刀齿的跳动量,降低刀具受到损坏的几率。
在实际铰削的过程中,操作人员要通过实时的监控,注意切屑材料的形状,如果铰削余量小,材料会残留一部分原件,这时需要操作人员及时调整切屑的力度,使材料的大小和形状都得到统一,提高铰削的均匀度。
如果切屑材料呈现出条的弹簧状,说明施加的铰削余量不够大,不能满足材料的尺寸要求,这时通过对针状、碎片状材料的测量,确定调节尺度的大小,可以进一步提高调节的准确性,防止切屑堵塞。
加工过程中,操作人员还需要观察刀齿是否有粘屑,避免孔径超出预定的尺寸,使用硬质合金铰刀铰孔时,材料会出现孔收缩现象,要设置一定的措施,防止孔的结构变化。
3.结语
在上文的分析中,笔者分析了不锈钢铰削加工工艺性能的特点,进而确定了对性能造成影响的因素,所以在实际加工的过程中,操作人员必须要深入到每一个加工环节中,才能从根本上找到影响不锈钢铰削加工工艺性能的因素,最终制定出更加高效的处理方法。
不锈钢铰削加工工艺需要极其严格的规格控制,可见,细节决定了不锈钢铰削加工工艺性能的高低,提高加工工艺性能,基本措施就是提高操作水平。
参考文献:
[1]张有为,何黎明,马先雨,等.不锈钢铰削加工工艺性能的分析[J].工具技术,2010,11(14):170-172.
[2]张世杰,高秀芝,唐力杰,等.高锰钢铰削加工工艺性能的分析[J].工具技术,2013,03(14):372-374.
[3]张世杰,张志平,李德龙,等.基于不锈钢铰削加工工艺性能的分析[J].煤矿机械,2013,10(19):106-108.
[4]解贝,高珊珊,高露,等.机件加工中深孔的铰削工艺及技术分析[J].科技视界,2014,02(17):197-217.
[5]李桂玉,宋金燕,李明宇,等.叠层复合材料钻削加工缺陷产生机理及工艺参数优化[J].山东大学学报(社会科学版),2011,04(19):150-155.。