汽车轻量化冲压技术及其数值模拟
汽车覆盖件冲压成形的数值模拟

汽车覆盖件冲压成形的数值模拟作者:王家昆李琦胡东勇罗英李再参一、引言对于制造业来说,21 世纪竞争的核心将是新产品的竞争。
围绕新产品的竞争,一场以信息技术为特征的新的制造业革命正在全球波澜壮阔地展开。
如何实现高质量、低成本、短周期的新产品开发,是赢得这场竞争的关键。
汽车覆盖件与一般薄板拉伸件相比,具有材料相对厚度小、结构尺寸大、形状复杂、尺寸精度和表面质量要求较高的特点。
其零件大多是由复杂的空间自由曲面组成,成形时,坯料上各部分的变形复杂、差别较大,各处应力也很不均匀,使零件的冲压工艺性较差,拉伸过程中容易产生起皱或破裂现象。
车身覆盖件的成形过程涉及几何非线性、材料非线性和复杂的接触与摩擦等问题,在传统的冲压生产过程中,无论是覆盖件模具的设计、制造,还是坯料形状和尺寸的确定,冲压工序、工艺参数的规划,都要设计制造原型,经过多次试生产和多次调试修正才能确定,这是一个试错逼近的过程,造成人力、物力和财力的大量消耗,生产成本高,周期长,质量不易控制。
随着计算机技术的不断发展,计算机辅助工程(CAE) 已广泛应用于板料成形过程分析,不仅可用于后期的工艺分析及模具设计,也可用于产品设计阶段,以确保零件具有较好的冲压成形工艺性。
预先在计算机上进行实际生产过程模拟,可在计算机屏幕上观察毛坯的成形过程,预示汽车覆盖件零件冲压成形的可行性,然后通过少量试模验证,就可得出较可靠的可行性结论。
现使用法国ESI 公司开发的PAM-STAMP 2G商业化专业板料冲压成形软件对汽车后盖内覆盖件进行冲压模拟分析。
二、数值模拟1、PAM-STAMP 2G软件简介PAM-STAMP 2G软件的新的系统框架可以在各模块之间进行无缝数据交换,还提供了可以客户化的应用程式编程界面。
PAM-DIEMAKER 通过参数迭代的方法获得实际的仿真模型,能在几分钟内生成模面和工艺补充面,并快速分析判断零件有无过切(负角) ,并计算出最佳的冲压方案,然后可非常简单地对模面和工艺补充面的几何形状进行修改,并参数化地完成所有前期模具设计的控制。
汽车覆盖件冲压模具轻量化技术及应用
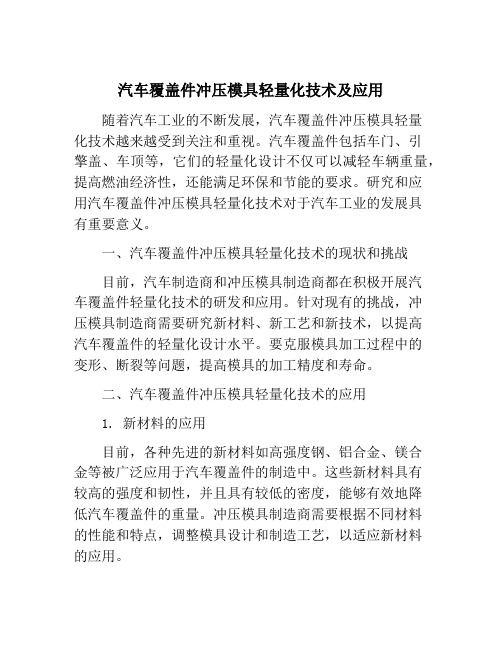
汽车覆盖件冲压模具轻量化技术及应用随着汽车工业的不断发展,汽车覆盖件冲压模具轻量化技术越来越受到关注和重视。
汽车覆盖件包括车门、引擎盖、车顶等,它们的轻量化设计不仅可以减轻车辆重量,提高燃油经济性,还能满足环保和节能的要求。
研究和应用汽车覆盖件冲压模具轻量化技术对于汽车工业的发展具有重要意义。
一、汽车覆盖件冲压模具轻量化技术的现状和挑战目前,汽车制造商和冲压模具制造商都在积极开展汽车覆盖件轻量化技术的研发和应用。
针对现有的挑战,冲压模具制造商需要研究新材料、新工艺和新技术,以提高汽车覆盖件的轻量化设计水平。
要克服模具加工过程中的变形、断裂等问题,提高模具的加工精度和寿命。
二、汽车覆盖件冲压模具轻量化技术的应用1. 新材料的应用目前,各种先进的新材料如高强度钢、铝合金、镁合金等被广泛应用于汽车覆盖件的制造中。
这些新材料具有较高的强度和韧性,并且具有较低的密度,能够有效地降低汽车覆盖件的重量。
冲压模具制造商需要根据不同材料的性能和特点,调整模具设计和制造工艺,以适应新材料的应用。
2. 结构优化设计通过结构优化设计,降低汽车覆盖件的重量是实现轻量化的重要途径之一。
采用材料去脂减肥的铸造法、压力铸造法等也能有效减轻汽车覆盖件的质量。
3. 模具材料和工艺的优化在冲压模具制造过程中,合理选择模具材料和优化模具工艺对于提高模具的使用寿命和加工精度至关重要。
采用先进的表面处理技术,如表面渗氮、表面喷涂等,可以提高模具的耐磨性和抗腐蚀性,从而提高模具的使用寿命。
三、汽车覆盖件冲压模具轻量化技术的未来发展趋势未来,随着汽车工业的不断发展和新材料、新工艺的应用,汽车覆盖件冲压模具轻量化技术将会迎来更大的发展空间。
冲压模具制造商需要不断提高自身技术水平,积极开展创新研发工作,以满足汽车工业对于轻量化技术的需求。
要加强与汽车制造商的合作,共同推动汽车覆盖件冲压模具轻量化技术的应用和推广。
结语汽车覆盖件冲压模具轻量化技术的研究与应用对于汽车工业的发展具有重要意义。
基于 Dynaform 的汽车覆盖件冲压成型数值模拟及优化

基于 Dynaform 的汽车覆盖件冲压成型数值模拟及优化∗熊保玉【摘要】It has gradually been paid more attention to study forming law for automobile panel by applying numerical simulation.Left and right inner plates on automobile rear wheels are investigated,the stamping process of auto rear wheel is simulated based on Dynaform software.Simulation of stamping forming by changing magnitude of blank holder force and setting drawbead,predicting wrinkle,fracture,thinning,rebound and other defects is done.Blank holding force and draw-bead of process and technical parameters of left and right inner plates on automobile rear wheels are determined by compa-ring the simulation results,and it provides a scientific basis for the practical products shaping.%应用数值模拟技术对汽车覆盖件成型规律进行研究逐渐受到重视。
以汽车左、右后轮罩内板为研究对象,介绍了应用 Dynaform 软件对轮罩冲压成型进行数值模拟的步骤。
通过模拟产品在设置不同压边力数值及有、无拉延筋情况下的成型性能,预测板料成型中可能出现的如起皱、拉裂、变薄和回弹等缺陷问题。
基于Abaqus的VRB板冲压成形数值模拟研究

图 1 板料柔性轧制
B
L1
L2
L3
L
T
t
(a) 模型装配图
(b) 坯料
注: 1— ——凸 模; 2—— —平板 压边 圈; 3—— —实 体 单 元 板 料 ; 4— ——壳单元板料 (具体用哪种依据仿真单元而定);5 凹模。
图 2 有限元模型及坯料
材料
B210P B210P
表 1 材料性能参数
厚度 (mm)
2 1
杨氏模量 (GPa)
210 210
泊松比
0.3 0.3
屈服强度 抗拉强度 (MPa) (MPa)
240
421
265
412
n值
0.265 0.241
【作者简介】张波,男,广西人,本科,任职于上汽通用五菱汽车股份有限公司技术中心,研究方向:车身结构设计、车身轻量化设计。
76 qiyekejiyufazhan
2019 年第 6 期(总第 452 期) 过渡区材料的屈服变小,而靠近薄测的过渡区材料的屈服增 大,故在冲压过程中,由于靠近薄侧的过渡区材料抵抗塑性 变形的能力增加,所以薄测圆角区域的开裂趋势增加。
5.1.2 圆角区域减薄 减薄率云图显示最大减薄率在盒形件的 4 个圆角处 (如
图 10 所示)。 3 种离散程度情况下 4 个圆角处的减薄率数值如图 11 所
车身第一纵梁冲压过程数值模拟与试制

1 模拟过程及分析
() 1 工艺 分析及模具
产 该 零 件 ,因 而在 改进 的 带 气垫 的 模 具 上 直 接 采 用 铝 合 金 6 09 进 0 来 行 ; 压 模 拟 。同样 未使 用 压边 圈 . 中 模 具 间 隙 为0. 4 mm ,摩 擦 因数 为
01 .2。毛 坯 形 状见 图7 在 图3毛 坯 (
图2 模具 薄体
点 处材 料 过 多 。 为解 决整 体 扭 曲 问
题 ,需 要 仿 照 实际 生 产 中 的模 具 , 在模 具 底 部 加上 气 垫 ,重 新 设 计 的
. 模 具 的投 入 ,有 必要 对 该 零件 进 行 使 用压 边 圈 ,模具 间隙 为04 mm ,
冲压模拟 用模具薄体 见图6 。
图3 毛坯 形状
车 身第一 纵梁零 件见 图1.该零 件 为复 杂难 成形 零件 ,图1 中A点处
顶部容易开裂 ,底 部材料堆积 ;B
点 处 是顶 部 材料 堆 积 ,底 部 容 易 开
裂 ;C点 与A点类 似 ,D点 与 B点 类
形 状 的 基 础 上 根 据 图4 结 果 作 了 的 改 进 ,主 要是 分 别增 大 了 图2 上 B、D处 的 圆角 ,并 在A点处 倒 圆 角) ,最终 变形 情 况见 图 8,F D L
20年 7 07 第 期
维普资讯
数 字 化 园 地
未 放 大 模 具 圆 角 的情
况 下 ,所 有 现 有 铝 合
金 材 料 均 不 能 成 形 该
零件 。图 1 一图2 ( 7 3 均 放 大 了 圆 角 )是 各 个
阶 段 的 试 制 情 况 图
果见 图1 。B、D两处基 本达 到 了要 重 。相 同模 具 ,6 2T 材料试冲 件 2 A0 一 4 求 ,而A点的开 裂无 法克服 ,需要修 有3 开裂 , 3 0 . 处 0 4O材料试 冲件有 1
汽车复杂梁形件冲压成形及回弹数值模拟

汽车复杂梁形件冲压成形及回弹数值模拟刘晓晶;刘博;陈晓晓;潘强荣;张彦燊【摘要】回弹问题是影响高强钢板进一步应用的原因之一,为了降低回弹影响,通常可以通过设置合理的工艺参数的方法减小回弹.以材料为高强钢的复杂型面汽车后边梁为例,对成形过程进行数值模拟分析,采用设置等效拉延筋及改变压边力大小的方法优化零件的成形结果,并最终确定后边梁成形时的等效拉延筋位置分布、拉延筋阻力和压边力的大小.利用计算出偏移最大的节点之间距离的方法对后边梁的回弹量进行测量.采用局部增大拉延筋阻力以及减小压边力的方法,对后边梁成形后所产生的卸载回弹及修边回弹进行控制,等效拉延筋阻力与压边力进行合理配比使回弹减小到较小的范围.最后将模拟所得到的结果与实验结果对比,即零件回弹较小,成形精度较高,进而得出该回弹控制方法可用于指导实际生产的结论.【期刊名称】《哈尔滨理工大学学报》【年(卷),期】2015(020)001【总页数】5页(P75-79)【关键词】板料成形;数值模拟;回弹;拉延筋【作者】刘晓晶;刘博;陈晓晓;潘强荣;张彦燊【作者单位】哈尔滨理工大学材料科学与工程学院,黑龙江哈尔滨150040;哈尔滨理工大学材料科学与工程学院,黑龙江哈尔滨150040;哈尔滨理工大学材料科学与工程学院,黑龙江哈尔滨150040;哈尔滨理工大学材料科学与工程学院,黑龙江哈尔滨150040;哈尔滨理工大学材料科学与工程学院,黑龙江哈尔滨150040【正文语种】中文【中图分类】TG386高强度钢板具有较高的屈服强度和抗拉强度[1],符合汽车轻量化[2-3]的发展需求,目前已逐渐应用于汽车覆盖件的生产.但高强度钢较高的屈服强度引起的回弹是高强钢汽车覆盖件冲压成形中的主要成形缺陷[4].对回弹大小控制的准确性与否将严重影响冲压件的成形质量和尺寸精度[5-6].高强钢冲压成形中的回弹控制是学术研究和工业生产中共同关注的热点问题[7-10].目前,国内外学者进行了许多基于数值模拟技术的板材回弹问题的研究,主要是针对简单形状零件的回弹规律及控制方法的研究[11-14],对三维立体复杂零件的回弹研究相对较少.本文基于有限元法[15-16],对复杂型面汽车覆盖件进行成形及回弹研究,通过对成形工艺的优化,对复杂型面零件进行回弹的控制,从而得到成形质量及精度较高的汽车后边梁零件[17-20].材料为先进高强度钢板DP590[21],板坯几何尺寸为1 500×430 mm,厚度为1.8 mm,材料参数如表1所示.板坯采用Belytschko—Tsay薄壳单元.毛坯与工具之间的接触类型为单面接触,材料模型采用弹塑性材料模型,符合Barlat屈服准则[22].将后边梁曲面模型导入Dynaform软件,对后边梁曲面进行网格划分,网格采用自适应划分技术,最大自适应网格等级为3.板坯采用16号全积分壳单元公式,厚向积分点个数取7.板料成形模拟时,摩擦系数为0.125、压边圈闭合的最大虚拟速度设置3 000 mm/s、最大虚拟冲压速度设置为2 000 mm/s、模具间隙为1.1t 即1.98 mm.后边梁有限元模型如图1所示.次将压边力设置为1 800 kN、1 900 kN、2 000 kN、2 100 kN进行运算,其他参数不变,后边梁模型在拉延后都基本成形,没有发生拉裂,但是总体成形效果较差,由于材料失稳,所以导致出现了大片的起皱区域,同时存在许多没有得到充分拉深成形的区域.成形质量达不到工艺要求.后边梁成形模拟时,采用多组拉延筋成形方案进行模拟得到的成形效果如表2所示.成形模拟应用的拉延筋布置方案如图2所示.图3所示的成形极限对比图中直观的反映了每组工艺的成形效果和缺陷产生的位置.由于在不采用拉延筋的情况下,压边力增大至2 100 kN时R1区的起皱现象仍然很严重,第1组未充分拉延的两端按照方案A布置了拉延筋,成形后虽然R1区的起皱得到控制,但是却出现了多处拉裂,坯料整体的拉延程度也未得到改善;第2组改变了拉延筋布置,提高压边力降低拉延筋阻力进行模拟,坯料得到了充分拉延,并且消除了R1区和R2区的破裂;第3组模拟调整拉延筋布置,按照前几组成形效果重新分配拉延筋阻力,坯料拉延非常充分,只在R3区仍然存在拉裂;第4组对拉延筋布置进行微调,拉裂和起皱得到完全消除.后边梁的最终回弹量为卸载回弹和修边回弹的综合结果,将两次回弹最大偏移区域的节点坐标和回弹前的节点坐标进行对应,计算区域内每一节点在修边回弹后的位移取其最大值,即得到精确的后边梁最大回弹位移.如图4(a)所示为卸载回弹、测得节点最大位移发生在后边梁下端的侧壁入料口处,此处回弹造成的距离偏差达到了4.1 mm.图4(b)所示为修边回弹、测得节点位移最大偏移量仍然发生在下端部侧壁入料口处,回弹量为1.10 mm.按照第4组的成形工艺,后边梁的最大回弹位移约为5.2 mm.对于第4组的成形工艺,由于拉延筋阻力和自身型面复杂对回弹的抑制作用,后边梁中部的回弹并不突出,但是在下端部的回弹量较大.后边梁的下端接近U形梁的形状,是与前纵梁等零件装配的接合处,这一部位的回弹将引起严重的装配问题.前面的成形结果表明,增大后边梁下端部的拉延筋阻力,将会导致R3区的破裂.为减小后边梁回弹,采用降低压边力并细化拉延筋布置的措施对成形工艺进行优化.拉延筋布置方案如图5所示.第2次优化采用拉延阻力数据如表4所示.本次工艺优化后,成形极限图如6(a)所示,未出现起皱和拉裂缺陷,侧壁拉延充分,底边虽然存在未拉开区域,但并不影响后边梁的使用性能,符合成形要求.回弹计算得到的卸载回弹和修边回弹节点位移最大偏移量如图7所示.图6(b)为最终零件的厚度变化图,零件最薄厚度出现在R1区附近的胀形区,该区因胀形产生的厚度减薄属正常范畴.侧壁处的最小厚度大于1.31 mm,符合变薄率低于30%的要求.经过优化后,后边梁两次回弹的最大节点位移都小于1 mm,且卸载回弹的最大位移偏移出现在了型面中间位置的边缘,该处属于余料部分,修边后剩余边缘的二次回弹量非常微小.修边回弹的最大位移偏移仍然出现在下端部侧壁入料口处,但此处的卸载回弹的局部节点最大位移不到0.4 mm,总回弹量得到有效控制,符合了2 mm 工程的装配要求.采取工艺优化方案指导实际生产进行试模,经过切边和冲孔程序之后的模拟结果图与试模件的对比如图8所示,零件未有起皱和破裂缺陷,减薄率、未充分拉延区和起皱倾向区与模拟结果吻合,回弹量较小,实现了回弹的有效控制,验证了模拟结果的的准确性.1)针对复杂型面汽车后边梁零件,建立了有限元分析模型,进行了补充面及压边面的型面优化.2)在汽车后边梁模拟成形分析中,采用设置等效拉延筋及优化压边力的方法优化零件的成形结果,确定了后边梁的等效拉延筋位置分布及拉延筋阻力大小,得到了成形质量较好的后边梁零件.3)在回弹模拟分析中,确定了回弹模拟参数及回弹测量方法,通过采用局部增大拉延筋阻力以及减小压边力的方法,对回弹进行控制,等效拉延筋阻力与压边力进行合理配比使回弹减小到较小的范围.4)将模拟卸载回弹及修边回弹的最大总回弹量由优化前的约5.1 mm优化至约1.7 mm.5)采用优化工艺进行实验,得到了成形质量较高的汽车后边梁零件.将模拟结果与实验结果对比,零件回弹较小,成形精度较高.该回弹控制方法可用于指导实际生产.【相关文献】[1] 林建平,王立影,田浩彬, 等. 超高强度钢板热冲压成形研究与进展[J].热加工工艺,2008,37(21):140.[2] 汪文奇, 陈菊霞. 车身材料及制造轻量化技术的应用及挑战[J]. 汽车工艺与材料, 2010, 04: 4-5.[3] 亚楠, 温龙飞. 浅谈汽车材料的轻量化发展态势[J]. 汽车工业研究, 2007, 3: 33-35.[4] PAPELEUX L, GOHY S, COLLARD X etc. Springback Simulation in Sheet Metal Forming Using Implicit Algorithms[C]. NUMISHEET, France, 1999: 13-17.[5] 蒋浩民,陈新平,石磊,等.先进高强度钢板的冲压成形特性及其应用[J]. 塑性工程学报,2009,16(4):183-184.[6] 刁可山,蒋浩民,曹猛,等.基于CAE的DP600高强钢零件回弹特征分析及控制[J]. 锻压技术,2010,5(5):47-50.[7] 罗云华,王磊. 高强钢板冲压回弹影响因素研究[J]. 锻压技术,2009,34(1): 23-26.[8] 石磊,肖华,陈军,等. 先进高强度钢板弯曲类回弹特性的试验研究[J]. 材料科学与工艺,2009,17(5):672-679.[9] 刁可山,蒋浩民,曹猛,等. 基于CAE 的DP600 高强钢零件回弹特征分析及控制[J]. 2010,35(5):47-51.[10] 郭玉琴,姜虹,王小椿. 覆盖件冲压加工中回弹预测的研究[J].机床与液压,2005,3: 54-55.[11] 周杰, 霍春梅, 杨明. 差厚拼焊板U形件的回弹规律及控制的研究[J]. 热加工工艺,2009,38(7):17-19.[12] LIU W,YANG Y Y. Multi-objective Optimization of an Auto Panel Drawing die Face Design by Mesh Morphing [J].Computer-Aided Design,2007,39:863-869.[13] 林策,彭艳,孙建亮,等. 丁板形缺陷板料冲压变形及回弹仿真分析[J]. 锻压技术,2012,37(6):175-179.[14] NINSHU MA, YASUYOSHI UMEZU, YUKO WATANABE, etc. Springback Prediction by Yoshida-uemori Model and Compensation of Tool Surface Using Jstamp[C]// Interlaken: NUMISHEET, 2008: 473-478.[15] LUC PAPERLEUX, JEAN-PHILIPPE, PONTHOT. Finite Element Simulation of Springback in Sheet Metal Forming[J]. Journal of Materials Processing Technology, 2002, 125-126:785-791.[16] GHAEI A, TAHERIZADEH A, GREEN D E. The Effect of Hardening Model on Springback Prediction for a Channel Draw Process[C]. Interlaken: NUMISHEET, 2008: 485-489.[17] GAN WEI, WAGONER R H. Die Design Method for Sheet Springback[J]. International Journal of Mechanical Sciences, 2004, (46): 1097-1113.[18] 陈炜, 陈红辉, 谢俊, 等. 基于回弹补偿的模具型面设计方法研究[J]. 锻压技术, 2008, 33(6): 86-90.[19] KUBLI WALDEMAR, KRASOVSKYY ANDRIY, SESTER MATTHIAS. Advanced Modeling of Reverse Loading Effects for Sheet Metal Forming Processes[C]// Interlaken: NUMISHEET, 2008: 479-484.[20] BARTHEL C, SVENDSEN B. Parameter Identification for the Steel lh800 and its Application to the Simulation of Draw-bending and Deep-drawing[C]// Interlaken: NUMISHEET, 2008: 545-548.[21] 王金学. 高强钢和高性能钢在国外的应用[J]. 交通标准化, 2008(9): 121-123.[22] 俞汉清, 陈金德. 金属塑性成形原理[M]. 北京: 机械工业出版社, 1999: 50-65.。
数值模拟热冲压工艺参数的优化设计_单云

材料的变形速率对变形后材料的性能影响很大,在热冲压 过程中,冲压速度不仅影响模拟的时间,同时影响每一个时刻温 度场及应力场分布。冲压速度越快,成形过程耗费的时间越短,板 料温度下降也越小,成形时表现出良好好的塑性,应力也相对较 小。
在压边力为 35kN,凸模、凹模和压边圈初始温度 75℃条件 下,研究了冲压速度分别为 25mm/s、30mm/s、35mm/s、40mm/s 时 对热冲压应力的影响,成形后盒形件应力分布云图和最大应力随 冲压速度的变化曲线,如图 4 所示。
由结果可知,随着模具初始温度升高,板料和工具的温度差 减小,传热量减少,使得板料温度上升,增加材料软化,造成变形
No.12
Dec.2014
机械设计与制造
175
抗力和最大应力都下降。模具初始温度低时对最大应力的影响较 大,因为温度较低板料和模具的温差大,传热效果好,板料软化机 制低,应力增大。
740
3.3 模具初始温度对热冲压工艺的影响规律
冲压过程中,模具既是成形的工具,也是热传导的主体。模 具的初始温度越高,板料和模具的温差就越小,板料的散热效果 越差,这直接影响板料内部温度场和应力场的分布。
在冲压速度为 35mm/s,压边力为 35kN 的情况下,分别取凸 模、凹模和压边圈的初始温度为 50℃、75℃、100℃、150℃,进行热 力耦合有限元分析,得到的板料应力分布云图和最大应力变化曲 线,如图 5 所示。
20
25
30
35
40
45
压边力(kN)
图 3 板料最大应力随压边力变化曲线 Fig.3 The Changing of the Biggest Stress with the Holder Force
数值模拟在冲压过程中的应用

数值模拟在冲压过程中的应用对材料加工进行成型是在重工业领域中的重要手段之一。
随着社会日新月异的发展和人们对生产生活要求的全面提高,塑性加工也不断发展。
在塑性加工过程中充分利用计算机的快速、精确计算等优点已得到广泛的应用。
利用计算机的数值模拟制造已成为了新研究方法,可以对产品性能、质量进行分析,降低消耗和成本,提高产品开发效率如汽车外形、冲压模具、坯料,揭示各种成型规律并且进行优化工艺过程预报组织性能。
塑性成型的数值模拟方法主要有三种:上限法、边界元法和有限元法。
上限法主要用于分析较为简单的准稳态变形问题,边界元法主要用于模具设计分析和温度计算,而有限元法(FEM)主要用于大变形的体积成形和板料成型,变形过程呈现非稳态,材料的几何形状、边界、材料的性质等都会发生很大的变化。
有限元法将具有无限个自由度的连续体看成只具有有限个自由度的单元集合体。
单元之间只在指定节点处相互铰接,并在节点处引入等效相互作用以代替单元之间的实际相互作用。
对每个单元选择一个函数来近似描述其物理量,并依据一定的原理建立各物理量之间的关系。
最后将各个单元建立起来的关系式加以集成,就可得到一个与有限个离散点相关的总体方程,由此求得各个离散点上的未知量,得到整个问题的解。
它对问题的性质、物体的形状和材料的性质几乎没有特殊的要求,只要能构成与有限个离散点相关的总体方程就可以按照有限元的方法求解。
有限元法能考虑多种外界因素对变形的影响,如温度、摩擦、工具形状、材料性质不均匀等。
除边界条件和材料的热力学模型外,有限元的求解精度从理论上看一般只取决于有限元网格的疏密。
利用有限元进行数值分析可以获得成形过程多方面的信息,如成形力、应力分布、应变分布、变形速率、温度分布和金属的流动方向等[1]。
金属板料冲压成形是金属材料塑性成形的一种重要方法。
有限元法在板料成形领域的应用始于20世纪70年代,自此,在这一领域的研究逐渐发展起来[2]。
在机械制造业中有着广泛的应用,例如:汽车的车身、底盘、油箱、散热器片、锅炉的汽包、电动机等都是采用了板料冲压工艺加工成形。
汽车车身冲压零部件的轻量化设计与制造

汽车车身冲压零部件的轻量化设计与制造随着环保意识的增强和能源储备的不断减少,汽车工业正面临着巨大的挑战和机遇。
在这个背景下,轻量化成为了汽车行业发展的重要方向之一。
汽车车身冲压零部件作为车身结构的重要组成部分,其轻量化设计与制造的研究显得尤为重要。
一、轻量化设计的需求汽车车身冲压零部件的重量直接影响到整车的燃料消耗和排放量。
因此,轻量化设计成为了很多汽车制造商关注的焦点。
在设计过程中,我们应该充分考虑零部件在使用寿命内的受力情况,采用优化设计的方法,合理选择材料,并通过优化结构以减少重量。
二、轻量化设计的原则1. 综合考虑强度和刚度要求轻量化设计不是追求薄而易碎的结构,而是通过合理的结构优化来减少材料消耗。
我们需要确保在满足强度和刚度要求的前提下,尽可能减少材料的使用量。
2. 使用高强度材料选择高强度材料是汽车车身冲压零部件轻量化设计的重要策略之一。
高强度材料可以在保证零部件安全性的同时,减少材料的使用量,达到轻量化的目的。
3. 结构优化设计通过结构优化设计,可以进一步减少汽车车身冲压零部件的重量。
比如,通过合理的拓扑优化设计,可以减少材料消耗,同时提高车身零部件的刚度和强度。
三、轻量化制造的方法1. 使用先进的冲压工艺冲压是汽车车身零部件制造的常用工艺方法。
通过采用先进的冲压工艺,如热成型、超高速冲压等,可以大幅提高冲压效率和零部件质量,并且减少材料的使用量。
2. 采用复合材料复合材料具有重量轻、强度高的特点,被广泛应用于汽车工业中。
在汽车车身冲压零部件的制造中,采用复合材料可以有效减少零部件的重量,提高整车的燃油经济性。
3. 精确控制制造工艺在轻量化制造过程中,精确控制制造工艺非常重要。
包括冲压工艺参数的优化、模具设计的精密制造等,都可以提高零部件质量,减少废品产生。
四、轻量化设计与制造的挑战虽然轻量化设计与制造有着广阔的前景,但也面临一些挑战。
首先,轻量化设计可能会增加设计和制造成本。
其次,新材料和新工艺的应用需要充分考虑可行性和安全性。
汽车发动机罩板冲压成形及回弹过程的数值模拟
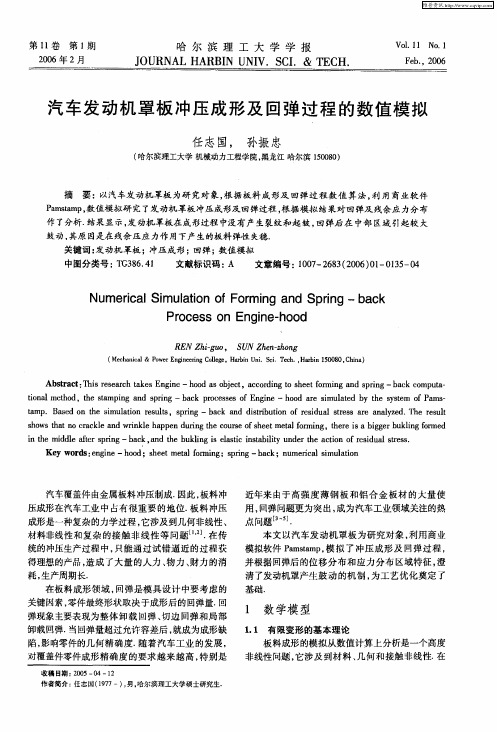
作 了分析. 结果显示, 发动机罩板在成形过程 中没有产生裂纹和起 皱, 回弹后在 中部 区域 引起较大 鼓动, 其原 因是 在 残余压 应 力作 用下产 生的板料 弹性 失稳 .
关 键词 : 动机பைடு நூலகம்罩板 ;冲压 成形 ; 弹 ; 发 回 数值模 拟
中图分类 号 : G 8 .1 T 364
任志 国, 孙振 忠
( 哈尔滨理7大学 机 械动力工程学院 , - 黑龙江 哈尔滨 108 ) 500
摘
要 :以汽 车发 动机 罩板 为研 究对 象 , 据 板料 成形 及 回弹 过 程 数 值 算 法 , 用 商业 软 件 根 利
P m t p 数值 模拟研 究 了发 动机 罩板冲 压成形及 回弹过程 , 据模 拟 结果对 回 弹及 残余应 力分 布 asm , a 根
清 了发 动机罩 产 生鼓 动 的机 制 , 为工 艺 优 化 奠定 了
基础.
得理想的产品, 造成 了大量的人力 、 物力 、 财力的消 耗, 生产周期 长. 在板料成形领域 , 回弹是模具设计 中要考虑的 关键因素, 零件最终形状取决 于成形后 的回弹量. 回 弹现象主要表现为整体卸载 回弹 、 切边 回弹和局部 卸载回弹. 当回弹量超过允许容差后 , 就成为成形缺 陷, 影响零件的几何精确度. 随着汽车工业的发展 , 对覆盖件零件成形精确度 的要求越来越高 , 特别是
文献 标识码 : A
文章 编号 :10 — 6 3 2 0 )l 0 3— 4 07 2 8 ( 06 O 一 15 0
Nu r a mua in o o mig a d Sp ig — b c me i l c Si lt fF r n n r o n —ak P o e s o n ie h o r c s n E gn — o d
汽车纵梁冲压成形数值模拟及试验验证

汽车纵梁冲压成形数值模拟及试验验证一、引言介绍汽车纵梁的作用及制造过程存在的问题,阐述数值模拟在汽车制造领域的重要性,并概述本文的研究目的和方法。
二、汽车纵梁冲压成形数值模拟建模选取合适的数值模拟软件对汽车纵梁的冲压成形过程进行建模,详细描述材料模型、边界条件、网格划分等关键参数的选择和设置,并进行数值分析和模拟。
三、数值模拟结果分析与优化对数值模拟结果进行分析和对比,探究不同参数对汽车纵梁成形质量的影响,提出针对性的优化方案,并进行后续数值模拟验证。
四、试验验证及实验结果分析将优化后的数值模拟方案实际应用于汽车纵梁的冲压成形实验,对试验过程进行详细描述,并对实验结果进行数据处理和分析,验证数值模拟的准确性和可靠性。
五、结论与展望总结本文的研究成果,指出数值模拟在汽车纵梁冲压成形方面的应用价值和局限性,并提出今后进一步深入研究的方向和可行性建议。
第一章引言随着汽车工业的快速发展,汽车的安全性和稳定性也成为社会关注的焦点。
而汽车纵梁是支撑汽车主体结构的重要部件,直接关系到汽车的整体刚度和安全性。
其制造工艺和质量的稳定性对整车品质的影响愈发凸显,因此研究汽车纵梁的制造过程并不断改进和优化,是提升汽车整车品质的有效途径之一。
在汽车纵梁的制造过程中,冲压成形作为一种常见的加工方法,广泛应用于汽车制造业。
传统的汽车纵梁冲压成形技术存在问题如:成形过程中容易出现材料撕裂、形变不良等质量问题;后续焊接和涂装工艺复杂,严重影响制造效率和成本等。
近年来,随着计算机应用技术的快速发展和模拟技术的普及,数值模拟已经成为汽车制造业中的重要工具,可以对汽车零部件的设计和制造进行精准的分析和优化。
本文旨在通过数值模拟与试验验证相结合的方法,对汽车纵梁冲压成形过程进行模拟建模与优化,并验证模拟结果的正确性和可靠性。
第二章汽车纵梁冲压成形数值模拟建模汽车纵梁制造中的冲压成形过程是一个非线性多变量的复杂问题。
选取合适的数值模拟软件是进行数值模拟建模的关键,Autodesk Simulation Mechanical软件是一种常用的数值模拟软件。
冲压加工过程的数值模拟与优化

冲压加工过程的数值模拟与优化一、引言冲压加工是制造业中常见的一种成形工艺。
在汽车、家电、航空航天等行业特别是多品种、小批量、高精度产品制造中占有很重要的地位。
传统的冲压加工工艺依靠工人的经验和试验来保证成形精度。
现在随着计算机仿真技术的日益发展和普及,冲压加工过程的数值模拟与优化显得越来越重要。
二、冲压加工的数值模拟冲压加工的数值模拟分为两类:一是对冲压零件进行成形仿真,二是对冲压模具进行热、机械等仿真分析。
1、冲压零件的成形仿真冲压零件的成形仿真以有限元法为核心,奠定了冲压加工数值仿真的基础。
通过利用有限元法建立材料力学与变形理论模型,模拟冲压加工过程中工件的变形和应力状态。
其主要目的是预测冲压过程中的变形和裂纹形成。
其精度直接决定了冲压加工的质量和成本。
2、冲压模具的仿真分析冲压模具的仿真分析是通过数值模拟和计算机仿真对模具的设计进行验证和改进。
常用的模拟仿真技术有有限元法和计算流体力学(CFD)技术。
有限元法主要用于对模具的结构和预测模具的损伤,而CFD技术主要用于分析模具的加热和冷却效果,以优化冲压成形过程的温度分布,比如模具的冷却、润滑和温度控制等等。
通过仿真分析,可以优化模具的结构,降低冲压过程中的损耗,提高模具的使用寿命和工作效率。
三、冲压加工的数值优化现在的数值模拟可以精确模拟出冲压过程中的变形和位移等信息,为进一步提高冲压工艺的质量和效率提供了有力的手段。
这里我们主要从工件、模具和料的角度探讨优化方法。
1、工件的优化工件的设计和加工精度都会对数值优化产生影响。
传统的冲压加工中,生产者通常采用经验主义来设计工件型号和工艺参数。
大量重复性测试的缺点大大降低了生产率,并造成巨大的浪费。
对此,工艺优化技术可通过对未来加工过程的仿真来预测零件在加工过程中适应性。
制定最佳加工方案可最大程度地减少加工浪费并大大提高零件的质量。
2、模具的优化冲压模具是直接决定成品质量的因素之一,同时还对加工效率产生巨大的影响。
汽车用6016铝合金板材预时效工艺研究及冲压成形数值模拟

摘要6016铝合金板材主要制造汽车覆盖件,特别是乘用车内外罩、后行李箱和门框等汽车外板,是汽车轻量化的关键材料。
而目前国内的铝合金板材仍存在着成形性、抗凹性及零件成形后质量差等问题,无法满足使用要求。
因此开展6016铝合金板材关键的预时效工艺和冲压成形工艺研究,对提高板材的成形质量十分重要。
本文将545 o C固溶30 min的6016铝合金(Al-0.55%Mg-1.0%Si-0.18%Cu)板材水淬后,经60 o C~160 o C×5 min~30 min预时效,室温停放25天后,进行185 o C×20 min的模拟烤漆处理。
采用硬度、拉伸试验,结合示差扫描量热法(DSC)、扫描电子显微镜(SEM)等分析技术,研究预时效工艺对合金的力学性能及微观组织的影响规律。
通过数值模拟仿真实际的冲压过程,并预估零件成形后可能出现的质量缺陷,优化关键成形工艺参数。
结果表明:①固溶淬火后立即进行预时效可以抑制自然时效过程,T4P态合金的成形性和烘烤硬化性能都得到改善。
烤漆前后的硬度随着预时效温度升高,出现先缓慢增加后迅速增加的趋势。
预时效温度为100 o C,预时效时间为20 min合金烘烤前屈服强度低于120 MPa,延伸率在25%左右;烘烤后屈服强度高于180 MPa(预变形2%合金烘烤硬化值达到104 MPa),烘烤后的延伸率在22%左右,综合比较优于其他预时效工艺。
②结合DSC曲线对β”析出温度和激活能进行计算,研究发现,随预时效温度升高,β”析出峰左移,激活能也降低。
说明预时效可以抑制合金自然时效过程,提高合金T4P态成形性能,而且促进烘烤过程中β”的析出,增强烘烤硬化效果。
③以铝制汽车发动机罩内板为对象,建立冲压CAE模型,对板料冲压过程仿真,研究了不同成形工艺对成形后最大减薄率、最大增厚率及最大回弹量的影响规律。
④对多因素的优化问题,首先通过灰色关联分析法,获得较优的工艺参数为:压边力500 KN,摩擦系数0.1,凹凸模间隙1.1t(1.32 mm)、凸模速度3 m/s,仿真试验后出现了少量拉裂缺陷。
新能源汽车铝合金冲压轻量化技术

设备管理与维修2018翼9(上)新能源汽车铝合金冲压轻量化技术张生林(南京天河汽车零部件股份有限公司,江苏南京211200)摘要:汽车车身轻量化技术的研究发展是推动汽车节能、减排的关键。
铝合金材料冲压技术是实现汽车车身轻量化的重要课题,可实现约2/3的减重,对于汽车轻量化、市场的可持续发展具有深远意义。
关键词:铝合金;新能源汽车;冲压件;轻量化;模具中图分类号:U462.2文献标识码:B DOI :10.16621/ki.issn1001-0599.2018.09.700引言随着汽车能源的不断开发与消耗,全球动力燃油资源日益枯竭。
在当今发动机动力技术提升难度日益加大、动力电池效率不高的背景下,燃油车与新能源动力汽车白车身冲压零部件轻量化技术成为行业一项共性的研发技术。
铝合金是一种具有优良性能的轻型材料,也是整个汽车行业轻量化技术研究运用及产业化生产的必选材料。
目前,整个白车身重量占汽车总重量的38%左右,对于降低汽车能耗而言,整个白车身轻量化技术起着至关重要的作用。
可以设想,当汽车车身重量减少其自身重量的1/2时,所有类型的燃油汽车或新能源汽车的驱动装置要比原来小(轻),能源消耗同样比原来要少(或跑的更远),这时动力能源体积又可以针对市场需求优化减小。
当汽车车身轻量化达到一定的阶段,汽车车身的各部件都会跟着减小、减轻。
1汽车轻量化技术发展的背景及意义伴随着我国汽车智能现代化的进程,整个汽车工业的研究、开发及生产的发展,汽车产业已成为我国经济的重要支柱产业之一。
据2005—2017年中国汽车市场销量及增长走势(图1),2017年我国汽车产量达到2888万辆,同2016年相比增加了30%,成为世界第一大汽车生产国。
截至目前,我国汽车保有量达到2.32亿辆。
汽车轻量化,是在确保汽车安全行驶的条件下,保证汽车各部位的受力强度,通过优化汽车整体重量提高汽车行驶的高效动力能力,促使动力能源与执行机构减小,减少燃料消耗,降低排气污染。
SUV车型侧围外板冲压工艺的数值模拟分析

SUV车型侧围外板冲压工艺的数值模拟分析I. 引言- 研究背景和意义- 国内外研究进展综述- 论文主要内容和结构安排II. 数值模拟方法与流程- 侧围外板冲压工艺流程- 数值模拟方法介绍- 模型建立与边界条件设置- 材料模型与参数选择III. 模拟结果与分析- 冲压工艺过程仿真结果- 冲压过程中的应力分布与变形情况分析- 优化后的工艺参数与结果比较分析IV. 工艺参数优化与验证- 基于数值模拟结果的工艺参数优化- 实际工艺参数验证试验- 试验结果与仿真结果比较分析V. 结论与展望- 研究结论总结- 不足之处与展望- 对即将进行的研究提出建议和展望VI. 参考文献注:此提纲并非成品论文,具体内容和文献需要根据实际情况进行调整和完善。
一、引言在汽车制造过程中,侧围外板是SUV车型中一种重要的构件,其作用是连接车门和车辆底盘,承担着保护车辆乘员和车身稳定的作用。
侧围外板冲压加工工艺是侧围外板制造的关键之一,其质量和工艺速度对整个车辆制造过程都有着重要的影响。
为了确保SUV车型侧围外板的高质量制造,必须进行精细的数值模拟分析。
本论文旨在通过数值模拟的方法分析SUV车型侧围外板的冲压加工工艺,探究优化工艺参数和提高制造质量的方法。
二、数值模拟方法与流程(一)侧围外板冲压工艺流程侧围外板冲压加工工艺是这样的一个过程:首先根据设计要求制定模具和冲压工艺方案,然后将金属板材放置于冲床上方,通过一定的力量,板材在冲床上沿着一定的轨迹进行形变,最终形成所需的构件。
整个冲压加工过程可以分为四个步骤:模具安装,板材握紧,侧围外板坯料加工和铆合。
(二)数值模拟方法介绍在数值模拟侧围外板冲压加工工艺的过程中,使用了ABAQUS有限元分析软件。
该软件可以对三维固体模型进行建模和模拟,模拟仿真过程中为模型应用边界条件,分析模型的应变和应力分布。
ABAQUS可以根据材料力学性质和标准化材料卡,确定材料本身性能和材料本身与模具之间的摩擦效果。
中型卡车顶盖冲压成形数值模拟分析及其优化的开题报告

中型卡车顶盖冲压成形数值模拟分析及其优化的开题报告题目:中型卡车顶盖冲压成形数值模拟分析及其优化一、研究背景随着社会经济的不断发展,交通运输行业也迎来了快速发展的机遇。
中型卡车作为道路运输行业的主力车型,占据了很大的市场份额。
中型卡车的生产制造过程中,冲压成形是关键的制造工艺之一。
中型卡车的顶盖是冲压成形的重要零部件之一,其质量和外观直接关系到整个车身的品质。
传统的顶盖制造工艺依赖于经验和试验,存在生产成本高、加工周期长、生产效率低等问题。
为此,本研究旨在通过数值模拟方法,对中型卡车顶盖冲压成形过程进行分析,并提出优化生产工艺措施,以提高生产效率和产品质量。
二、研究目的和内容本研究的目的是通过有限元分析方法,对中型卡车顶盖的冲压成形过程进行数值模拟分析,并针对分析结果提出优化的生产工艺方案和措施,以提高顶盖的成形质量和生产效率。
具体研究内容包括:1. 中型卡车顶盖冲压成形的工艺流程和参数设定的研究。
2. 建立中型卡车顶盖的有限元模型,进行数值模拟分析。
3. 分析成形过程中的应力、应变分布情况,发现可能出现的成形缺陷,并提出优化方案。
4. 对比分析不同工艺参数对成形质量的影响,进行优化设计。
三、研究方法本研究主要采用有限元分析方法进行研究。
具体方法包括:1. 构建中型卡车顶盖的有限元模型,对成形过程进行数值模拟分析。
2. 通过有限元分析软件对顶盖的应力、应变状态进行分析,发现可能出现的成形缺陷。
3. 对比分析不同工艺参数对成形质量的影响,进行优化设计。
四、研究意义本研究的意义在于:1. 提高中型卡车顶盖的生产效率和产品质量。
2. 研究中型卡车顶盖的冲压成形工艺,为生产实践提供参考和指导。
3. 推广有限元分析方法,在制造业中的应用范围。
五、预期成果本研究的预期成果包括:1. 中型卡车顶盖冲压成形的数值模拟分析方法的构建和验证。
2. 提出优化的生产工艺方案和措施,提高成形质量和生产效率的方法。
3. 研究结果的实用性和重要性得到验证,并在中型卡车制造企业中得到应用。
基于数值模拟的车身结构件多步冲压工艺优化

基于数值模拟的车身结构件多步冲压工艺优化
仲志刚;方禾;陈炜;吕盾;陈磊
【期刊名称】《轻型汽车技术》
【年(卷),期】2004(000)003
【摘要】车身结构件在实际生产过程中,常需要多道冲压成形工序才能加工出来,工序数量及各工序内容(即塑性变形程度)都会决定成形过程能否顺利完成并影响产品最终成形质量.首先分析了左后悬挂架成形特点,决定采用两步拉延方式完成成形;然后确定首次拉延的四种方案,来研究不同变形形式和变形量对后继拉延所造成的成形质量的影响;通过数值模拟结果中的FLD曲线、材料厚度分布图、最大主应变分布图和拉延成形变形裕度,来研究车身结构件多步冲压工艺设计.
【总页数】4页(P33-36)
【作者】仲志刚;方禾;陈炜;吕盾;陈磊
【作者单位】跃进汽车集团南京模具装备有限公司;跃进汽车集团南京模具装备有限公司;江苏大学机械工程学院;江苏大学机械工程学院;江苏大学机械工程学院【正文语种】中文
【中图分类】U4
【相关文献】
1.车身结构件多步冲压工艺数值模拟 [J], 陈炜;杨继昌;仲志刚;方禾;朱国璋
2.基于接触式淬火的车身板热冲压成形数值模拟 [J], 冉毅
3.半盒形特征件全工序多步冲压成形工艺优化 [J], 王利;黄昭明;胡李勇;张成
4.全载体车身结构件级进冲压成形排样设计 [J], 罗林;王利;沈晨;叶彩霞;李陶胜
5.汽车车身结构件冲压模具维护保养 [J], 韦清云
因版权原因,仅展示原文概要,查看原文内容请购买。
- 1、下载文档前请自行甄别文档内容的完整性,平台不提供额外的编辑、内容补充、找答案等附加服务。
- 2、"仅部分预览"的文档,不可在线预览部分如存在完整性等问题,可反馈申请退款(可完整预览的文档不适用该条件!)。
- 3、如文档侵犯您的权益,请联系客服反馈,我们会尽快为您处理(人工客服工作时间:9:00-18:30)。
h y d r o f o r mi n g a n d h o t s t a mp i n g ,t h e n u me r i c a l s i mu l a t i o n o f J S T AMP / N V i s i n t r o d u c e d b y t a k i n g t h e
s t a mp i n g
0 引 言
安全 、 节能 、 环 保 是 汽车 技 术 发展 的永 恒 主 题. 安 全和舒 适 的功能 装 备 会增 加 汽 车 的 质量 , 『 而节 化 已成 为 当前 汽
车行业 的发展潮 流 , 得到 广泛 关注 . 在 汽车 冲压件 的
s i mu l a t i o n o n s h e e t s t a mp i n g i s a n i mpo r t a n t a n d e f f e c t i v e wa y t o a c h i e v e r a p i d i mp l e me n t a t i o n o f a u t o mo t i v e l i g h t we i g h t s t a mp i n g t e c h no l o g y .
a u t o mo t i v e i n n e r d o o r p a n e l ,a u x i l i a r y f i - a me a nd B— p i l l a r a s e x a mp l e s . Th e a p p l i c a t i o n o f n ume r i c a l
应用技 术与技 巧
文章编号 : 1 0 0 6 — 0 8 7 1 ( 2 0 1 3 ) 0 6 - 0 0 9 0 — 0 5
汽 车轻 量 化 冲压 技 术 及其 数 值 模 拟
李彦 波 , 刘 红 武
( 广 州 中国科 学 院 工 业技 术研 究 院 , 广州 5 1 1 4 5 8 )
第2 2卷 第 6期 2 0 1 3年 l 2月
计 算 机 辅 助 工 程
Co mp u t e r Ai de d En g i n e e r i n g
Vo 1 . 2 2 No . 6 De c .2 0l 3
Ap p l i c a t i o n T e e h n i q u e a n d S Ⅻ l s
d e s c r i b e d. As t o t h r e e ma i n a d v a n c e d p r o c e s s p r o d u c t i o n t e c hn o l o g i e s s u c h a s l a s e r t a i l o r we l d i n g,
收 稿 日期 : 2 0 1 3 — 1 2 - 0 3 基 金 项 目 :广 州 市 南 沙 区科 技 计 划 ( 2 0 1 2 0 3 0 0 4)
需求 . 采 用板料 冲 压 成型 的 数值 模 拟 技 术 可 以很 好
地 解决 该 问题 , 在欧美 、 日本 等发 达 同 家 和地 区 , 该 技 术 已成为缩 短 汽车 冲压件 模 具 研 发周 期 、 提高 产
设计 和生 产过程 中 , 采 用 传 统方 法 并 依 靠工 程 师 经 验 的成 型工艺 分析 及设计 已不 能满 足新产 品开 发的
和 环保要 求 减 少 c o :气 体 的排 放 以及 良好 的 回收
再利 用 . 国外研 究表 明, 在一般 情况下 , 车 体 减 轻 1 0 %, 可节 省燃 油 3 %~ 7 % .¨冈此 , 随着 全 球环 境
汽车轻 量化 冲压技 术有 效应 用的 重要 途 径. 关键词 :汽 车轻 量化 ; 数值 模拟 ;管材液 压成 型 ;激光拼 焊 ; 热 冲压
中图分 类号 : U 4 6 3 . 8 2 ; T B I 1 5 . 1 文 献标 志码 : B
Au t o mo t i v e l i g h t we i g h t s t a m pi ng t e c h no l o g y a n d
Ke y wo r d s:a u t o mo t i v e l i g h t we i g h t ;n u me r i c a l s i mu l a t i o n;t u b e h y d r o f o r n in f g;l a s e r t a i l o r we l d i n g;h o t
摘 要 :简述 汽 车轻量 化技 术 的途 径和基 于 J S T A MP / N V的仿 真流程 , 针对 目前 汽车轻 量化采 用 的激
光拼 焊 、 液压 成 型和 热冲 压成型 等 3种 主要 的先进 加 工制造 技 术 , 以车 门 内板 、 副 车 架和汽 车 B柱
典 型零 件 为 实例说 明 J S T A MP / N V数 值模 拟 的应 用. 应 用板 料 冲压 成 型数 值 模 拟技 术是 快 速 实现
i t s n u me r i c a l s i mu l a t i o n
LI Ya n b o,L I U Ho n g wu
Ab s t r a c t :T h e wa y o f a u t o mo t i v e l i g h t we i g h t a n d t h e s i mu l a t i o n p r o c e s s b a s e d o n J S T AMP / N V a r e