汽车部件装配过程潜在失效模式PFMEA(参考)
PFMEA_电机制程潜在失效模式与影响分析

潜在失效模式与影响分析FMEA 编 WI-SC-PFM-号 005共(制程 4页,第FMEA )1页设计职责:编制满足汽车电器使用人:要求FMEA 日 马达型号 / 项目:QJT60QB关键日期:期(原始):核心小组:严 等发现行制 现行制程 程项目/ 功能 潜在失效 潜在失效 重 潜在失效 生 控制 控制 (要求)模式影响度 级 原因度 预防 探测啤换向器 / 将换向器与1、啤换向器尺 导致马达虚位过铁芯连接寸不达标 大或卡死 极2、换向器角度 1、马达火花大 5 1、模具调整不当 1互检4次/ 天不达标2、马达流速变 高收机错误化大绕线1、用错线径、 极 线类高1、转子电阻大 危 1、使用错误线类 IPQC 收机 开机、换线小、影响流速险2 员工自检 检查一次2、线圈数绕错 2、转子耐压等 82、设备设置错误100% 极综合测试级不足高检查一次3、拉力大小极 3、收机错误高点焊1、勾位焊接不 1、转子不通电 1、设备压力过小 良、漆皮未化 或通电不良2、焊接温度过低2、勾位通孔2、焊接位氧化极3、焊机焊嘴台阶 IPQC 收机员工全检位使用不正确3、线扁程度 1/2 3、过扁,勾位 44、压力过大 54次/ 天探 R 测 P度 N3 151 16240实施结果严发探R推荐措施 职责 目标完 采取有效 重生测P成日期 措施日期 度度度N生产/ 工模/ 品质人员共同收机组长511 5员工自检 PM 立即 互检永久IPQCIPQC收机时综合测试员工 立即转子全部进 永久2 1 16PM行点焊后综 8合测试增加显微镜员工立即 增加显微镜 永久全检全检42216至2/3易断线低5、焊接温度过大PM 调节4、爆漆过长4、邻勾线之间短路焊压敏1、虚焊1、压敏电阻不1、人工操作不当,起作用极焊锡不良2. 压敏电阻爆裂 2. 马达性能不足8 2、操作不当碰撞1 IPQC检查碎片致马达卡死高员工自检潜在失效模式与影响分析(制程FMEA)设计职责:满足汽车电器使用要求马达型号 / 项目:QJT60QB关键日期:核心小组:组长216培训员工手法IPQC 立即增加显微镜永久811 8 增加显微镜全检全检FMEA编WI-SC-PFM-号005共4页,第2页编制人:FMEA日期(原始):实施结果严等发现行制现行制探 R 严发探R 程程项目/ 功能测 P 重生测P 潜在失效潜在失效重潜在失效生控制控制推荐措施职责目标完采取有效(要求)模式影响度级原因度预防探测度 N 成日期措施日期度度度N精车/ 使换向器表面光1、圆度不良1、马达电流大1、车刀崩IPQC抽检洁度及圆度达到工程2、光洁度不达2、马达火花大低 6 2、V座水平度差 1 圆度仪上下午各 1 4 定量更换车刀PM 立即5000PCS/刀永久 6 1 1 6 规格标1次入垫片 / 降低磨擦调整1、马达入多或1、马达虚位大极1、操作人员失误4 无无3 968马达虚位入少垫片或小高铁盖压轴承 / 将轴承压入1、轴承孔扩孔1、马达杂音、1、模具导针外径轴承内孔IPQC抽检铁盖内2、轴承孔缩孔马达寿命不足极超规格2 过塞规4次/ 天3 48增加马达预装IPQC 立即马达预装永久8 2 1 163、轴承同心度2、马达不顺、82、铁盖来料内孔来料检验IQC检验高不足马达电流大小,轴承变形碳精入刷架 / 将碳精与1、碳刷裂1、马达寿命不1、工装调节不到刷架铆压在一起2、碳刷与刷架足极位、工装磨损有缝隙2、碳刷掉落,8 2、刷架来料孔齿 2 目测员工全检 5 80 加强抽检力度IPQC 立即加强抽检永久8 2 4 648 2 5 80 3、碳刷松动马达无功能高过大IPQC抽检潜在失效模式与影响分析FMEA编WI-SC-PFM- 号005共(制程 4页,第FMEA) 3页设计职责:编制满足汽车电器使用人:要求FMEA日马达型号 / 项目:QJT60QB 关键日期:期(原始):核心小组:实施结果严等发现行制现行制探 R 严发探R 程程项目/ 功能潜在失效潜在失效重潜在失效生控制控制测 P 推荐措施职责目标完采取有效重生测P (要求)模式影响度级原因度预防探测度 N 成日期措施日期度度度N刷架贴阻尼片 / 减震1、阻尼片贴不1、失去减震功极3 1、未贴牢 1 无无10 30 加强抽检力度IPQC 立即加强抽检永久 3 1 8 24牢能低胶盖装配 / 将刷架组合1、刷架变形1、影响马达性极装配手势不正确装入胶盖形成胶盖组合能如电流、转速 4 1 目测IPQC抽检 5 20 加强抽检力度IPQC 立即加强抽检永久 4 1 4 16 寿命低机壳压轴承 / 将轴承压入1、轴承孔扩孔1、马达杂音、1、模具导针外径轴承内孔IPQC抽检机壳内2、轴承孔缩孔马达寿命不足极8 超规格2过塞规4次/ 天3 48增加马达预装IPQC 立即马达预装永久8 2 1 163、轴承同心度2、马达不顺、高2、机壳来料内孔来料检验IQC检验不足马达电流大小,轴承变形磁石擦胶 / 使磁石粘在1、胶不干1、磁石跌落1、胶过保质期机壳内壁极2 1 IPQC检查5 10增加机冲跌落IPQC 立即跌落试验永久 2 1 3 6低2、配胶比例不员工自检试验抽检正确转子入机壳 / 组装马达1、轴撞伤轴承1、马达不顺、低 4 1、模具保证1IPQC检查IPQC抽检 1 4电流大每天/2 次胶盖入机壳 / 组装马达1、轴撞伤轴承1、马达不顺、低 4 1、模具保证1IPQC检查IPQC抽检 1 4电流大每天/2 次马达封口 / 将铁盖与机壳1、封口推力不1、马达分离低 4 1、模具保证1IPQC检查IPQC抽检 1 4锁死足低 4 1每天/2 次潜在失效模式与影响分析FMEA编WI-SC-PFM-号005共(制程 4页,第FMEA) 4页设计职责:编制满足汽车电器使用人:要求FMEA日马达型号 / 项目:QJT60QB 关键日期:期(原始):核心小组:实施结果严等发现行制现行制探 R 严发探R 程程项目/ 功能潜在失效潜在失效重潜在失效生控制控制测 P 推荐措施职责目标完采取有效重生测P (要求)模式影响度级原因度预防探测度 N 成日期措施日期度度度N马达压偏心轮 1. 偏心轮未到位 1. 马达转动不顺极IPQC检查IPQC抽检 5 IPQC 立即加强抽检永久 3 1 8 248 模具保证 2 员工自检4次/ 天80 加强抽检力度高上盖与底板焊接 1. 焊接不良马达流量小气压不够高 6 模具保证 2 IPQC检查IPQC抽检 5 60 加强抽检力度IPQC 立即加强抽检永久 3 1 8 244次/ 天马达印字 / 标明型号1、字模糊、少1、无法辨认型极1、喷印机缺墨日期,便于追溯字、断字号、 4 2、喷印机调整不 2 员工自检IPQC抽检 4 32 定期清洗喷头员工立即清洗喷头永久 4 2 2 162、无法追溯低当。
pfmea过程潜在失效模式及后果分析案例(从原材料-加工-出货整套案例分析)

1、注射压力大 2、锁模力不够 3.模具分型面有异物
4 调节注射压力 作业准备验证,适当调
整,并进行工艺监控 清理模具分型面
产品不合格
2
C 4.塑料温度太高
调节 56
5
制品质量符合 要求
气泡
1.原料含水分、溶剂或 易挥发物
3
原料检验
2.塑料温度太高或受热 时间长,易降聚或分解
标签贴错 漏检 纸箱受潮变形 数量不准确
产品型号错
误,顾客不满 2
意
不良品混入, 影响客户使用
5
纸箱变形破损 3
顾客不满意
1
C 包装人员粗心 C 检验人员操作失误 C 纸箱堆积太高 C 仓库计数错误
3 检查、更正 3 检验、及时标记 3 检查、更正 3 检查、更正
2 42
1 21
3 18 4 60 3 27 26
3.注射压力太小
调节注射压力
4.注射柱塞退回太早 产品不合格 7 A
5.模具温度太低
调节注射温度
6.注射速度快
调节注射速度
2 42
7.在料筒加料端混入空 气
6
制品质量符合 要求
凹痕、缩水
产品不合格 7
1、流道浇口太小
4
2、塑料件太厚或厚薄 不均
3、浇口位置不当
4、注射保压时间太短 A 5、加料量不夠
过程潜在失效模式及后果分析 (PFMEA)
类型/部件: 车型年:
核心小组:
设计责任: 关键日期:
RPN DETECT
OCCUR CLASS SEV
项目
设计功能/要 求
潜在失效模式
潜在失效后果
1 原材料采购 原材料不合格
PFMEA潜在失效模式及后果影响分析案例
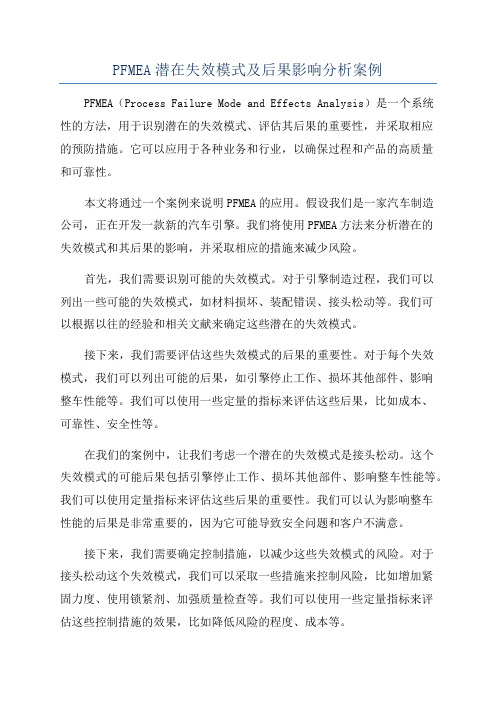
PFMEA潜在失效模式及后果影响分析案例PFMEA(Process Failure Mode and Effects Analysis)是一个系统性的方法,用于识别潜在的失效模式、评估其后果的重要性,并采取相应的预防措施。
它可以应用于各种业务和行业,以确保过程和产品的高质量和可靠性。
本文将通过一个案例来说明PFMEA的应用。
假设我们是一家汽车制造公司,正在开发一款新的汽车引擎。
我们将使用PFMEA方法来分析潜在的失效模式和其后果的影响,并采取相应的措施来减少风险。
首先,我们需要识别可能的失效模式。
对于引擎制造过程,我们可以列出一些可能的失效模式,如材料损坏、装配错误、接头松动等。
我们可以根据以往的经验和相关文献来确定这些潜在的失效模式。
接下来,我们需要评估这些失效模式的后果的重要性。
对于每个失效模式,我们可以列出可能的后果,如引擎停止工作、损坏其他部件、影响整车性能等。
我们可以使用一些定量的指标来评估这些后果,比如成本、可靠性、安全性等。
在我们的案例中,让我们考虑一个潜在的失效模式是接头松动。
这个失效模式的可能后果包括引擎停止工作、损坏其他部件、影响整车性能等。
我们可以使用定量指标来评估这些后果的重要性。
我们可以认为影响整车性能的后果是非常重要的,因为它可能导致安全问题和客户不满意。
接下来,我们需要确定控制措施,以减少这些失效模式的风险。
对于接头松动这个失效模式,我们可以采取一些措施来控制风险,比如增加紧固力度、使用锁紧剂、加强质量检查等。
我们可以使用一些定量指标来评估这些控制措施的效果,比如降低风险的程度、成本等。
最后,我们需要跟踪和更新PFMEA。
一旦我们实施了控制措施,我们需要不断跟踪失效模式的发生情况和其后果的重要性。
如果我们发现控制措施不够有效,我们可以采取进一步的改进措施,以减少风险。
通过以上的分析,我们可以有效地识别潜在的失效模式和其后果的重要性,并采取相应的预防措施来减少风险。
PFMEA是一个强大的工具,可以帮助我们提高产品和过程的质量和可靠性,从而提高客户满意度并降低成本。
过程失效模式及后果分析(PFMEA)

XXX汽车技术股份有限公司潜在失效模式及影响分析 PFMEA螺纹孔内无铝屑,机加工面边缘毛刺清理干净;螺纹孔内有铝屑,机加工面边缘未清理干净影响客户装配,客户抱怨61.丝锥损坏2.夹具松动3.切削液未正确喷淋,铝屑未吹掉31.首检记录表2.巡检记录表354None5XΦ0.341±0.01深0.55(英制)尺寸超差 1.毛坯不合格或尺寸变化大4XΦ0.232±0.01深0.5(英制)尺寸超差 2.夹具松动;3.程序错误2XΦ0.232±0.01深0.5(英制)尺寸超差 4.装夹失误2X4.34±0.02(英制)尺寸超差 1.毛坯不合格或尺寸变化大27.19±0.02(英制)尺寸超差 2.夹具松动;3.程序错误2X7.05±0.02(英制)尺寸超差 4.装夹失误2X11.72±0.02(英制)尺寸超差1.毛坯不合格或尺寸变化大1.25±0.02(英制)尺寸超差2.夹具松动;3.程序错误2.38±0.02(英制)尺寸超差 4.装夹失误1.56±0.02(英制)尺寸超差 1.毛坯不合格或尺寸变化大2.44±0.02(英制)尺寸超差 2.夹具松动;3.程序错误8XΦ0.118±0.01(英制)尺寸超差 4.装夹失误尺寸超差1.毛坯不合格或尺寸变化大2X45°±0.5°尺寸超差2.夹具松动;None3影响装配和功能7631.首检记录表2.巡检记录表3★3影响装配和功能7★31.首检记录表2.巡检记录表363NoneNone63影响装配和功能7★31.首检记录表2.巡检记录表3影响装配和功能7★31.首检记录表2.巡检记录表None影响装配和功能7★31.首检记录表2.巡检记录表36363None。
过程潜在失效模式及后果分析(PFMEA)已填写

半成品未做标示
使用统一的周转箱存放半成品 3
检查周转箱内的标示
3 45
热处理8.8级 130 热处理
工件表面处理未达到技术 要求
导致产品机械性能不合格
7
零件不得混淆
产品混杂
用户抱怨
3
热处理未按工艺严格执行
供应商定期评审
盛器未清理干净
1.定期评审; 2.定期对供应商质量考核。
2
1.核对供方检验报告; 2.抽检。
4
1.下单错误; 2.领料计数偏差过大。
1.生产部核对领料单; 2.领料员复验领料数量.
4 车间主任核对
4 64
原材料正确堆放
原材料损坏,变形
1.损坏材料无法使用; 2.缺陷材料造成零件不良
4
原材料搬运、存放过程中碰伤 1.按要求搬运;
、变形。
2.做防护措施。
5
1.工人作业时自检; 2.检验员巡检。
2.检测工具失效.
2.检具定期校正.
6
1.按培训计划执行; 2.量检具检测报告
3 72
半成品按规定堆放、
90 搬至搓牙机床
移动
半成品按规定放置并
做标识
半成品损坏,变形 半成品混淆
无法使用
5
需要挑选半成品,浪费时 间和人力
5
产品搬运过程中碰伤,掉落 使用统一的周转箱和手推车 3 在下道工序生产时目视检验 3 45
零件/系统名称及编号: 车型年/车辆类型 核心小组
过程潜在失效模式及后果分析(PFMEA)
过程责任: 关键日期
工
序 号
过程描述
No.
要求
半成品按规定堆放、
140 搬至待待检区
过程潜在失效模式及其后果分析程序(PFMEA)分析

过程潜在失效模式及其后果分析程序页码:1 共 6 页过程潜在失效模式及其后果分析程序(PFMEA)编制:审核:批准:生效日期:受控标识处:发布日期:2007.9.14 实施日期:2007.9.141.0 目的确定与产品和过程相关的潜在的失效模式和潜在制造或装配过程失效的机理/起因,评价潜在失效对顾客产生的后果和影响,采取控制来降低失效产生频度或失效条件探测度的过程变量和能够避免或减少这些潜在失效发生的措施。
2.0 范围适用于公司用于汽车零组件的所有新产品/过程或修改过的产品/过程及应用或环境发生变更的原有产品/过程的样品试制和批量生产。
3.0 引用文件下列文件中的条款通过本程序的引用而成为本程序的条款。
凡是注日期的引用文件,其随后的修改单(不包括勘误的内容)或修订版均不适用于本程序,凡是不注日期的引用文件,其最新版本适用于本程序。
3.1 ISO/TS16949:2002《质量管理体系—汽车行业生产件与相关服务件的组织实施ISO9001:2000的特殊要求》。
3.2 《潜在失效模式及后果分析参考手册》(第3版,2001年7月)3.3 《产品实现策划程序》3.4 《文件控制程序》3.5 《质量记录控制程序》4.0 术语及定义4.1 FMEA:指Process Failure Mode and Effects Analysis(过程失效模式及后果分析)的英文简称。
由负责制造/装配的工程师/小组主要采用的一种分析技术,用以最大限度地保证各种潜在的失效模式及其相关的起因/机理已得到充分的考虑和论述。
4.2 失效:在规定条件下(环境、操作、时间),不能完成既定功能或产品参数值和不能维持在规定的上下限之过程潜在失效模式及其后果分析程序页码:2 共 6 页间,以及在工作范围内导致零组件的破裂卡死等损坏现象。
4.3 严重度(S):指一给定失效模式最严重的影响后果的级别,是单一的FMEA范围内的相对定级结果。
严重度数值的降低只有通过设计更改或重新设计才能够实现。
PFMEA过程失效模式及后果分析

PFMEA过程失效模式及后果分析PFMEA(Process Failure Mode and Effects Analysis)过程失效模式及后果分析是一种常用的质量管理工具,用于评估和改进产品制造过程中的潜在问题和风险。
它旨在预测和预防可能导致产品失效的过程步骤。
1.确定过程步骤:首先,识别和定义产品制造过程中的每个关键步骤,包括原材料采购、加工、装配、测试等。
2.确定失效模式:对于每个过程步骤,识别可能导致失效的模式。
失效模式可以是设备故障、人为错误、材料质量问题等。
3.评估失效后果:对于每个失效模式,评估其可能导致的后果和影响。
后果可以涉及到产品质量问题、安全风险、客户满意度等。
4.定义风险优先级:根据失效模式的严重性、发生频率和检测能力,为每个失效模式分配一个风险优先级。
这可以帮助制定合理的风险控制策略。
5.制定改进计划:对于评估出的高优先级失效模式,制定相应的改进计划和控制措施。
这可能包括优化生产工艺、提供培训和教育、改进设备维护等。
6.实施和监控措施:执行改进计划,并监控其有效性。
定期对PFMEA进行更新,以反映过程改进和新的风险评估。
通过实施PFMEA,可以有效地识别和消除潜在的制造过程问题,并降低产品质量问题的风险。
下面以汽车制造业为例,具体分析PFMEA的应用。
在汽车制造过程中,每个制造步骤都可能存在潜在的失效模式。
例如,原材料采购环节可能存在材料质量问题的风险,加工环节可能存在操作错误或设备故障的风险,装配环节可能存在组装错误或安装不良的风险,测试环节可能存在测试不准确或设备故障的风险。
针对这些潜在问题,可以使用PFMEA来识别并评估其风险。
例如,在加工环节,识别可能的失效模式可能包括不正确的参数设置、设备故障、操作错误等。
然后,评估这些失效模式可能导致的后果和影响,如产品偏差、生产延误、设备故障等。
根据评估结果,确定失效模式的风险优先级,以便制定相应的改进计划和控制措施。
例如,对于评估为高风险的加工失效模式,可以采取以下改进措施:加强对操作员的培训和教育,确保他们正确操作设备和设置参数;增加设备维护和保养频率,以减少设备故障的风险;实施过程监控和自动化控制,以确保稳定的生产环境。
过程潜在失效模式与效果分析表(PFMEA)
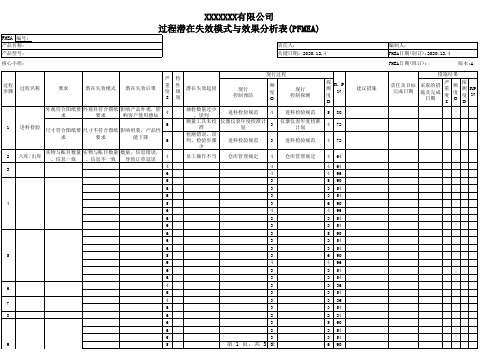
求
要求
响客户使用感知
4
1
进料检验 尺寸符合图纸要 尺寸不符合图纸 影响组装,产品性 6
求
要求
能下降
6
2
入库/出库
实物与账目数量 实物与账目数量 数量、信息错误, 、信息一致 、信息不一致 导致订单延误
4
抽检数量过少 、误判
进料检验规范
4
进料检验规范
5 80
测量工具未校 准
仪器仪表年度校准计 划
3
仪器仪表年度校准 计划
4 96
18
6
第 2 页,共 3 页4
4 96
18
6
4
4 96
5
4
4 80
19
5
4
4 80
6
3
4 72
6
4
4 96
20
6
4
4 96
6
4
4 96
21
4
4
5 80
4
4
4 64
22
4
4
5 80
23
4
4
4 64
备注:S、O、D评分标准详见《过程潜在失效模式后果分析PFMEA管理程序》,仅需对新部件进行评价分析,当RPN值超过200时要制定改善措施。
核准:
会签:
审查:
拟制:
表单 编 号:
第 3 页,共 3 页
6
4
4 96
6
3
3 54
6
3
3 54
6
3
5 90
6
3
3 54
6
3
3 54
13
5
3
PFMEA分析范例

PFMEA分析范例PFMEA(Process Failure Mode and Effects Analysis)是指对流程中的潜在故障模式和潜在故障造成的影响进行分析的一种方法。
它通过系统地识别和评估潜在故障模式,以便采取措施来防止或减少这些故障的发生。
本文将以一个汽车制造公司生产流程的PFMEA分析为例,介绍其具体步骤和操作。
一、引言在汽车制造过程中,由于各种原因,可能会导致生产中出现故障和缺陷,影响产品的质量和安全性。
因此,对生产过程进行PFMEA分析非常重要。
二、流程步骤1.确定分析范围确定需要进行PFMEA分析的具体流程,例如车身焊接、喷漆、总装等。
2.建立团队组建跨部门的团队,包括制造、质量、工程等相关人员,以保证全面的分析和意见的综合考虑。
3.识别潜在失效模式对所选流程中可能出现的失效模式进行识别和描述。
例如,在车身焊接流程中,可能出现焊接不牢固、焊接缺陷等失效模式。
4.评估失效的严重性根据失效对产品质量、安全性和顾客满意度的影响,对每个失效模式进行评估,确定其严重性等级。
例如,焊接不牢固可能导致车辆结构不稳定,严重影响安全性。
5.确定失效的原因对于每个失效模式,分析可能导致该失效的原因和影响因素。
例如,焊接不牢固的原因可能是焊接工艺参数设置错误或操作不当等。
6.确定失效的检测控制为每个失效模式确定相应的检测控制措施,以防止或检测失效的发生。
例如,对焊接不牢固的失效模式,可以增加焊接检验工序,采用牢固度测试等方法。
7.计算和评估风险优先级数值根据失效模式的严重性、发生可能性和检测控制的有效性,计算并评估风险优先级数值。
优先级数值越高,表示失效的风险越大,应优先处理。
8.制定改进措施针对高风险优先级数值的失效模式,制定相应的改进措施,例如改进工艺参数、培训操作人员、优化检测方法等。
9.实施改进并持续监控根据制定的改进措施,对流程进行改进,并持续监控流程的稳定性和效果。
三、结论通过PFMEA分析,汽车制造公司可以识别潜在的失效模式,评估其对产品质量和安全性的影响,并采取相应的措施进行预防和控制。
PFMEA潜在失效模式及后果分析
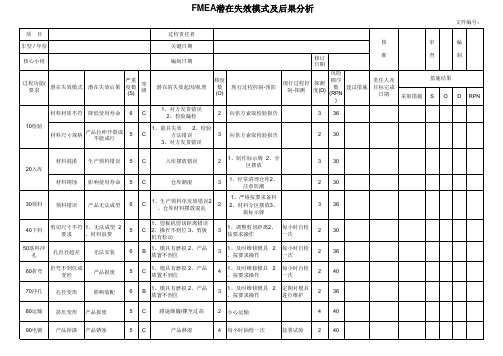
6C
1、搬运摆放混乱 2、标示牌丢失
2
1、贴标识牌 2、 每3天查看1次
出入库台账
3
36
备注:1.凡顾客指定特殊特性均按其特性符号标注,如◇表示配合/功能,○表示安全/符号,或顾客提出的其它符号要求。 2.顾客无特殊特性要求,本厂标准规定重要度控制标准符号要求如下:A —特殊特性 B—重要特性 C—一般特性
机有松动
3
1、调整剪切距离2、 按要求操作
每小时自检 一次
2
30
50落料冲 孔
孔直径超差
无法安装
6
B
1、模具有磨பைடு நூலகம் 2、产品 放置不到位
3
1、及时维修模具 2 、按要求操作
每小时自检 一次
2
36
60折弯
折弯不到位或 变形
产品报废
5
C
1、模具有磨损 2、产品 放置不到位
4
1、及时维修模具 2 、按要求操作
日期
材料材质不符 降低使用寿命 6 C
1、对方发货错误 2、检验漏检
2 向供方索取检验报告
3 36
10检验
材料尺寸规格
产品拉伸开裂或 不能成行
5
1、量具失效 2、检验
C
方法错误
3
3、对方发货错误
向供方索取检验报告
2 30
采取措施
审
编
查
制
措施结果 SOD
RPN
20入库
材料混淆 生产领料错误 5 C 材料锈蚀 影响使用寿命 5 C
入库摆放错误 仓库潮湿
2
1、制作标示牌 2、分 区摆放
3
1、经常清理仓库2、 注意防潮
3 30 2 30
过程潜在失效模式和故障分析(PFMEA)
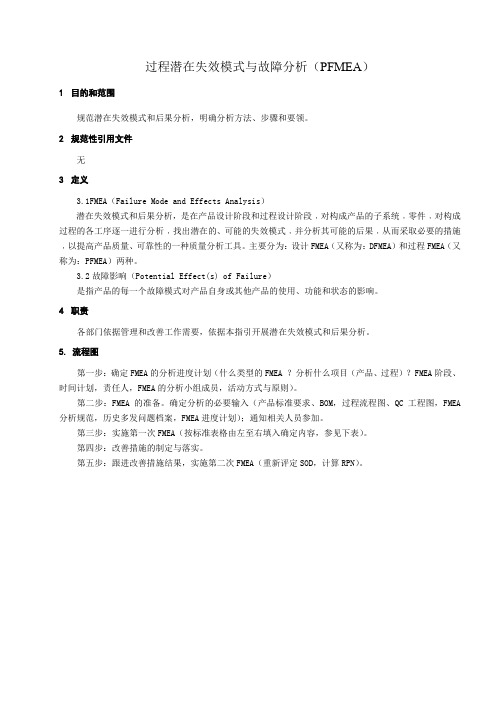
过程潜在失效模式与故障分析(PFMEA)1目的和范围规范潜在失效模式和后果分析,明确分析方法、步骤和要领。
2规范性引用文件无3定义3.1FMEA(Failure Mode and Effects Analysis)潜在失效模式和后果分析,是在产品设计阶段和过程设计阶段﹐对构成产品的子系统﹐零件﹐对构成过程的各工序逐一进行分析﹐找出潜在的、可能的失效模式﹐并分析其可能的后果﹐从而采取必要的措施﹐以提高产品质量、可靠性的一种质量分析工具。
主要分为:设计FMEA(又称为:DFMEA)和过程FMEA(又称为:PFMEA)两种。
3.2故障影响(Potential Effect(s) of Failure)是指产品的每一个故障模式对产品自身或其他产品的使用、功能和状态的影响。
4职责各部门依据管理和改善工作需要,依据本指引开展潜在失效模式和后果分析。
5. 流程图第一步:确定FMEA的分析进度计划(什么类型的FMEA ?分析什么项目(产品、过程)?FMEA阶段、时间计划,责任人,FMEA的分析小组成员,活动方式与原则)。
第二步:FMEA的准备。
确定分析的必要输入(产品标准要求、BOM,过程流程图、QC工程图,FMEA 分析规范,历史多发问题档案,FMEA进度计划);通知相关人员参加。
第三步:实施第一次FMEA(按标准表格由左至右填入确定内容,参见下表)。
第四步:改善措施的制定与落实。
第五步:跟进改善措施结果,实施第二次FMEA(重新评定SOD,计算RPN)。
6.管理内容6.1第一步,确定PFMEA的分析进度计划6.1.1确定FMEA的类型:PFMEA。
6.1.2确定PFMEA分析的具体过程。
对涉及到生产工艺变更(新材料、新工艺)的新产品项目必须应用PFMEA分析,重点分析本项目新产品新工艺的失效分析。
对生产工艺没有变更的新产品项目可以不用进行PFMEA分析。
工厂所有分厂、所有产品生产过程都要进行PFMEA分析。
潜在失效模式及后果分析PFMEA

Part name:Proces TechnicalPrepared By:Approval By:零件名称:过程责技术部编制:批准:Part number:KeyDateFMEA Date(Orig):FMEA Date(Rev.):Rev.A/0零件号:关键日FMEA 日期(编制):FMEA 日期(修订):版本:A/0Core Team:general manager :主要参加人:总经理:, 技术部: , 销preservation溶解,保温Part name:Proces TechnicalPrepared By:Approval By:零件名称:过程责技术部编制:批准:Part number:KeyDateFMEA Date(Orig):FMEA Date(Rev.):Rev.A/0零件号:关键日FMEA 日期(编制):FMEA 日期(修订):版本:A/0Core Team:general manager :主要参加人:总经理:, 技术部: , 销Part name:Proces TechnicalPrepared By:Approval By:零件名称:过程责技术部编制:批准:Part number:KeyDateFMEA Date(Orig):FMEA Date(Rev.):Rev.A/0零件号:关键日FMEA 日期(编制):FMEA 日期(修订):版本:A/0Core Team:general manager :主要参加人:总经理:, 技术部: , 销Part name:Proces TechnicalPrepared By:Approval By:零件名称:过程责技术部编制:批准:Part number:KeyDateFMEA Date(Orig):FMEA Date(Rev.):Rev.A/0零件号:关键日FMEA 日期(编制):FMEA 日期(修订):版本:A/0Core Team:general manager :主要参加人:总经理:, 技术部: , 销Part name:Proces TechnicalPrepared By:Approval By:零件名称:过程责技术部编制:批准:Part number:KeyDateFMEA Date(Orig):FMEA Date(Rev.):Rev.A/0零件号:关键日FMEA 日期(编制):FMEA 日期(修订):版本:A/0Core Team:general manager :主要参加人:总经理:, 技术部: , 销Part name:Proces TechnicalPrepared By:Approval By:零件名称:过程责技术部编制:批准:Part number:KeyDateFMEA Date(Orig):FMEA Date(Rev.):Rev.A/0零件号:关键日FMEA 日期(编制):FMEA 日期(修订):版本:A/0Core Team:general manager :主要参加人:总经理:, 技术部: , 销。
pfmea潜在失效模式及后果分析

编制《出货作业制 出货检验
Not implemented according to the
导书》Compile Shipment check
2 shipment
1
4
instruction
operation
instruction
Supplier Program Management Document
1/1
3
3
合的冷却塔
温度计/日常点检
Thermometer/Dai
配置模温机
ly check
1 Configuration of
3
18
mold machine
供水不足supply water not enough
1
水位监测控制
Wate压r 力le表ve/l日i常ns点pe检ct Pressure
con1trol
1
水泵故障water pump trouble
定期检修Check andm压em力taei表rn/t/Da日aiin常lyp点er检iodically
1
Pressure
1
1
水泵故障water pump trouble
1 定期检修Check andm压 Perm力teaesi表rsn/ut/Dra日aeiin常lyp点er检iodica1lly
1
4 2 12
空压机故障 Air compress machine broken.
压缩空气减压阀损坏 Air compress valve broken. 冷却塔流量不足 Cooling tower flux not enough
环境温度过低 environment temperature low
潜在的失效模式及后果分析(PFMEA)-63210118
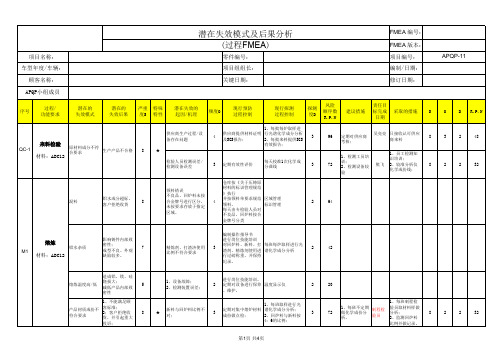
S
O
D R.P.N
气密测试 不符合IP66标准 影响产品功能 M8
水压测试 漏气,密封失效 影响产品功能
8
1、产品平面度超 ★ 差;
2、检测装置误差;
6
1、制作专用测试工 1、检验人员对产品
装;
100%做气密性测试;
2
1、产品平面度超
8
★
差; 2、打密封胶不均
匀;
3
1、使用打胶机均匀 打胶,保证打胶连贯 性;
1、检验人员对产品 100%做气密性测试;
2
1、产品加工时
96
保证产品平面 度; 2、变形产品作
蔡建华 持续
1、对不合格品 检查漏气位置后 做返工处理。
8
2
2
32
较形返工;
48
1、监测产品平 面度; 2、使用自动打 胶机;
1、产品平面度 检测; 蔡建华 2、螺丝拧入时 采用对角平衡方 式;
8
1
2
16
潭熙存
1、设计制作专 用加工夹具。
8
2
3
48
42
24 30 30 54
45 54 48
第3页 共4页
序号
过程/ 功能要求
潜在的 失效模式
潜在的 失效后果
严重 特殊 度S 特性
潜在失效的 起因/机理
频度O
现行预防 过程控制
现行探测 过程控制
探测 度D
风险 顺序数 R.P.N
建议措施
责任目 标完成 采取的措施
8
1、压铸机台参数 由压铸领班铱工艺 要求设定; 2、规范员工操作 规程; 3、模具易损件作 抛光并加硬回火处 理;
1、首件确认并对 比前次生产未件; 2、压铸工艺参数 记录表; 3、工序检验记录 表; 4、生产自检;
PFMEA分析范例

PFMEA分析范例PFMEA(Potential Failure Mode and Effects Analysis)是一种常用于产品设计和生产过程中的风险评估工具。
它通过系统地识别潜在的失效模式,并评估这些失效对产品性能、生产效率和客户满意度的影响,从而帮助企业采取相应的措施来预防和降低潜在失效的风险。
本文将以汽车制造业为例,介绍PFMEA分析的具体步骤和相关应用。
1. 背景介绍汽车制造业面临着严格的质量要求和市场竞争压力。
在生产过程中,如果存在失效模式而未能及时发现或纠正,将会导致产品质量问题、客户投诉以及生产效率下降等严重后果。
因此,采用PFMEA分析方法能够帮助企业降低失效风险,提高产品质量和生产效率。
2. PFMEA分析步骤2.1 制定团队PFMEA分析需要跨职能团队共同参与,包括设计工程师、生产工程师、供应商等相关人员。
团队成员应根据其专业知识和经验来确定潜在失效模式及其影响因素。
2.2 识别失效模式团队成员根据产品设计和制造过程,逐一识别可能存在的失效模式。
例如,在汽车制造过程中,可能存在供应商提供零部件质量不合标准、零部件装配不准确等失效模式。
2.3 评估失效影响针对每个失效模式,团队成员评估其对产品性能、生产效率和客户满意度的影响程度。
评估指标可以根据实际情况进行确定,如利用5W1H法(What、When、Where、Why、How)来进行细致拆解。
2.4 评估失效原因团队成员分析导致每种失效模式的潜在原因,可以运用鱼骨图(也称因果图)或5W1H法来帮助识别。
例如,失效模式为零部件装配不准确,潜在原因可能包括操作员技能不足、装配工具磨损等。
2.5 制定控制措施团队成员针对每个失效模式及其原因,制定相应的控制措施,以预防或降低失效风险。
控制措施可以包括提高操作员培训、更换装配工具等。
2.6 评估控制效果实施控制措施后,团队成员应不定期进行监控和评估,以确定措施的有效性。
如果控制措施无效,需要重新进行评估并采取其他措施。
潜在失效模式及后果分析PFMEA(案例)

3
42
无
2
押出
铜丝拉细
导体电阻过大
7
▲
放线张力过大
2
操作员用OD表首检铜丝线径
4
56
无
热收缩不良
使用时绝缘收缩严重使端部导体外露
6
未过预热器
2
操作员每换规格目测检查是否过预热器
7
84
无
潜在失效模式及后果分析
(过程FMEA)
FMEA编号:PF001第3页,共4页
2
检验员目测全检线材标识
7
70
无
PE膜包覆不完全
线材局部裸露,运输过程中使线材表面擦伤,顾客不满意
5
操作员因疏忽而导致包装不完全
2
检验员目测全检线材包装
7
70
无
频度O
现行过程控制预防
现行过程控制探测
探测度
R
P
N
建议措施
责任及目标完成日期
措施结果
采取的措施
S
O
D
R
P
1
束绞
铜丝跳股
引起成品线材表面有股纹、起包,火花电压测试通不过
7
绞线机内导轮不灵活
2
每班开始时手感检查导轮是否灵活
操作工每两小时目测一次。检验员每两小时目测检查,查看是否有跳股
7
98
无
7
放线张力不同
7
98
无
线材偏心
最小点厚度小于规定值,导致绝缘电阻过低使漏电流过大,引起仪表指示不灵敏
7
▲
模具未调好
2
检验员投影仪首检、每两小时目测检查,查看是否偏心,操作工每小时目测一次。
潜在失效模式分析PFMEA

对模具作模流分析,选择合适位置、 3 形状、大小的浇口,使结合线位置满 5
足要求
3
由低到高逐步调整注射压力,得到合 适值
5
C 顶出受力不平衡
3
增加顶杆数目或加大顶出面积,并确 保其均匀分布、受力平衡
5
C 注塑压力过大
3
由小到大调整,使得到一适合的注塑 压力值
5
C 保压压力过大
3
由低到高逐步调整保压,得到合适的 保压值
(ABS电镀级)
原材料性能不能满足 要求
产品性能不能满足
7
禁用/限用物质超标 客户投诉,产品报废 7
燃烧性能﹥80mm/min 车易燃烧
8
10.3
验收方头螺栓 、纸箱、气泡
尺寸超差
影响装配
6
袋
C
不符合原材料采购技术 要求
2
每批1次1袋目视检查原料实物 (比对样料)
6 72
无
C
不符合原材料采购技术 要求
5
C
注塑时间过长
4
由低到高的调整注塑时间,以得到稳 定合适的注射时间后锁定工艺
4
第 3 页,共 10 页
操作人员 100%检 108 查,巡检2 小时一次 进行抽查
操作人员 100%检 108 查,巡检2 小时一次 进行抽查
90
无
锁定生产样 108 件成型工艺
参数
操作人员 72 100%检
查,巡检2 操作人员 108 100%检 查操,作巡人检员2 108 100%检 查操,作巡人检员2 108 100%检 查操,作巡人检员2 108 100%检 查,巡检2 小时一次
4
4
7 外观不合格,客户不满 意
- 1、下载文档前请自行甄别文档内容的完整性,平台不提供额外的编辑、内容补充、找答案等附加服务。
- 2、"仅部分预览"的文档,不可在线预览部分如存在完整性等问题,可反馈申请退款(可完整预览的文档不适用该条件!)。
- 3、如文档侵犯您的权益,请联系客服反馈,我们会尽快为您处理(人工客服工作时间:9:00-18:30)。
項目名
過程責任部
門:
生產部
關鍵日期:
編制者:Andy Liu
FMEA日期(編制):2003.07.10
頁碼:第 頁 共5頁車輛年/車輛類型:核心小組:
項目名
過程責任部
門:
生產部
關鍵日期:
編制者:Andy Liu
FMEA日期(編制):2003.07.10
頁碼:第 頁 共5頁車輛年/車輛類型:核心小組:
項目名
過程責任部
門:
生產部
關鍵日期:
編制者:Andy Liu
FMEA日期(編制):2003.07.10
頁碼:第 頁 共5頁車輛年/車輛類型:核心小組:
項目名
過程責任部
門:
生產部
關鍵日期:
編制者:Andy Liu
FMEA日期(編制):2003.07.10
頁碼:第 頁 共5頁車輛年/車輛類型:核心小組:
項目名
過程責任部
門:
生產部
關鍵日期:
編制者:Andy Liu
FMEA日期(編制):2003.07.10
頁碼:第 頁 共5頁車輛年/車輛類型:核心小組:A 关键特性。