转炉冶炼低碳钢终点氧含量控制
炼钢转炉冶炼低碳钢脱氧合金化工艺优化
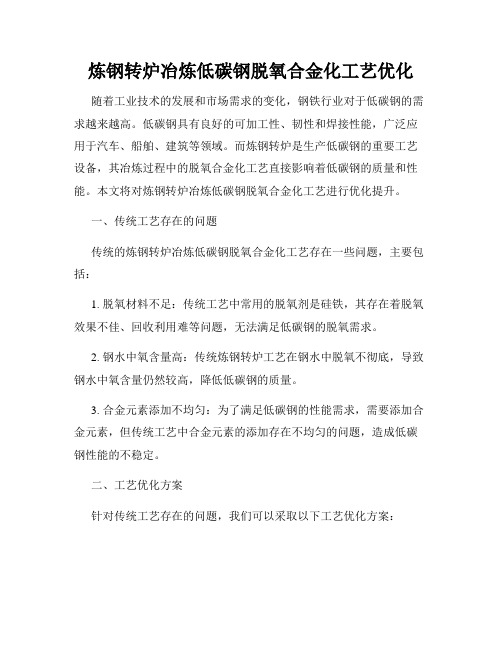
炼钢转炉冶炼低碳钢脱氧合金化工艺优化随着工业技术的发展和市场需求的变化,钢铁行业对于低碳钢的需求越来越高。
低碳钢具有良好的可加工性、韧性和焊接性能,广泛应用于汽车、船舶、建筑等领域。
而炼钢转炉是生产低碳钢的重要工艺设备,其冶炼过程中的脱氧合金化工艺直接影响着低碳钢的质量和性能。
本文将对炼钢转炉冶炼低碳钢脱氧合金化工艺进行优化提升。
一、传统工艺存在的问题传统的炼钢转炉冶炼低碳钢脱氧合金化工艺存在一些问题,主要包括:1. 脱氧材料不足:传统工艺中常用的脱氧剂是硅铁,其存在着脱氧效果不佳、回收利用难等问题,无法满足低碳钢的脱氧需求。
2. 钢水中氧含量高:传统炼钢转炉工艺在钢水中脱氧不彻底,导致钢水中氧含量仍然较高,降低低碳钢的质量。
3. 合金元素添加不均匀:为了满足低碳钢的性能需求,需要添加合金元素,但传统工艺中合金元素的添加存在不均匀的问题,造成低碳钢性能的不稳定。
二、工艺优化方案针对传统工艺存在的问题,我们可以采取以下工艺优化方案:1. 优化脱氧剂的选择:传统的硅铁脱氧剂可以通过其他脱氧剂进行替代,例如铝、锰等。
这些脱氧剂具有良好的脱氧效果和易回收利用的特点,可以提高低碳钢的质量。
2. 加强脱氧过程控制:通过提高脱氧剂的加入量和延长脱氧时间,确保炉料中的氧含量完全脱氧。
可以采用自动控制系统,实时监测钢水中氧含量,调整脱氧剂的加入量,实现钢水的有效脱氧。
3. 合金元素均匀添加:采用先进的合金元素添加技术,确保合金元素的均匀分布。
可以利用真空脱气设备将合金元素均匀加入钢水中,或者采用复合脱氧剂,使脱氧剂和合金元素同时添加,提高低碳钢的合金化效果。
4. 优化工艺参数:通过对炉温、转炉容量、吹氧时间等工艺参数的优化调整,提高低碳钢的冶炼效果。
可以利用计算机模拟技术对工艺参数进行优化设计,以实现低碳钢冶炼过程的最佳效果。
三、优化方案的效果及推广通过实施上述工艺优化方案,可以显著提高炼钢转炉冶炼低碳钢脱氧合金化的效果,进一步提升低碳钢的质量和性能。
转炉冶炼低级别RH钢“高碳低氧”工艺利弊浅析

V o 1 . 1 5 N o . 3
2 0 1 3年 9月
J O U R N A L O F L I A O N I N G I N S T I T U T E O F S C I E N C E A N D T E C H N O L O G Y S e p . 2 0 1 3
据和 理论 依据 。
脱碳 速 率 J , 从 而影 响整 个处 理周 期 。 即若 R H前钢 包氧 值过 低 , R H处 理 过程需 要进 行 补氧 气操 作 , 可 以 一定 程 度 上 弥 补 R H处 理前 氧
值 的不 足 , 但 由于 R H 真 空 处 理 的 不 可 随 意 重 复性 ( 即仅能 一 次 处 理 到 位 , 复压后需重新抽真空 ) , 增 加 了脱碳 终 点碳 含 量 和氧 值 控 制 的不稳 定 性 , 影 响 脱 碳速 率 ; 且 循环 时 间加 长 , 增 加 了蒸 气 的消 耗 量 ;
在 实 际生产 中应考 虑 此 因素 。
为挖 掘 降成本 潜 力 , 降低低级别 R H 钢 种 脱 氧
剂消耗 , 尝试转炉降低 出钢氧含量 ( 即“ 高拉碳 ” ) ,
出钢 过程 不加 脱 氧 剂 , 可在满足 R H 处 理 要 求 的基
础上 可 以减少 过程 冶炼 成本 。故 在试 验低 级别 炉 次 生产 时全 程跟 踪生 产情 况 , 总结 真实 生产 数据 , 得 出
摘要 : 降低 低 级 别 R H 钢 转 炉 出钢 自由氧 含 量 , 保证 R H 处理 前相 对 “ 高碳 低 氧 ”, R H轻 处理 后 可 以达 到 “ 降碳 降 氧 ” 的目
的, 可 以减 少过程氧化物 夹杂的生成、 压缩冶炼环节成本 ; 文章从 满足工艺要 求和 追求经 济效益最 大化 的角度 出发 , 通过 实 际
转炉炼钢氧化还原终点控制方法

题目:转炉炼钢氧化还原终点控制方法一、引言转炉炼钢是一种重要的钢铁冶炼工艺,其氧化还原终点控制是影响钢水质量的关键因素之一。
本文将介绍转炉炼钢的氧化还原终点控制方法,包括主要的控制参数和常见的控制手段。
二、转炉炼钢氧化还原终点控制参数1. 氧气流量:氧气是转炉炼钢中的主要氧化剂,在氧气吹炼过程中,通过控制氧气流量可以调节炉内氧化还原反应的进程,从而控制钢水的氧化还原程度。
2. 废钢加入量:废钢是转炉炼钢中的一种重要原料,其氧化还原性能直接影响到炉内氧化还原反应的平衡状态。
3. 利用率控制:利用率是炼钢过程中的重要参数,通过控制利用率可以调节转炉炼钢的氧化还原终点。
三、转炉炼钢氧化还原终点控制方法1. 控制氧气流量:通过调节氧气流量的大小,可以实现炉内氧气含量的控制,进而控制炼钢过程的氧化还原程度。
一般来说,增加氧气流量可以提高炉内氧化反应的速度,减少氧气流量可以减缓炉内氧化反应的速度。
通过对氧气流量的调节,可以控制转炉炼钢的氧化还原终点,达到预期的钢水质量。
2. 控制废钢加入量:废钢是转炉炼钢的一种重要原料,其氧化还原性能直接影响到炉内氧化还原反应的平衡状态。
通过控制废钢的加入量,可以影响炉内氧化还原反应的平衡状态,进而控制转炉炼钢的氧化还原终点。
3. 控制利用率:利用率是炼钢过程中的重要参数,通过控制利用率可以调节转炉炼钢的氧化还原终点。
利用率是指在炼钢过程中废气、废热、废渣等的综合利用程度,通过控制利用率,可以实现炼钢过程中的能量平衡和物质平衡,进而影响炉内氧化还原反应的平衡状态。
四、结论通过对转炉炼钢氧化还原终点控制方法的介绍,我们可以看到,氧化还原终点控制是影响转炉炼钢钢水质量的重要因素。
我们可以通过控制氧气流量、废钢加入量和利用率来实现对转炉炼钢氧化还原终点的控制,进而实现炼钢过程中的氧化还原平衡。
这些控制方法对提高转炉炼钢的生产效率和钢水质量具有重要的意义。
五、氧化还原终点控制方法的改进传统的转炉炼钢氧化还原终点控制方法虽然能够实现对钢水质量的控制,但仍然存在一些问题,比如控制精度不高、操作复杂等。
转炉炼钢终点控制技术

转炉炼钢终点控制技术摘要:本文首先简要概述了转炉炼钢的终点控制,基于此,详细论述了转炉炼钢终点的静态控制、转炉炼钢终点的人工经验控制、转炉炼钢终点的动态控制以及转炉炼钢终点的自动控制,分析了其中的关键环节,仅供大家参考。
关键词: 炼钢、转炉、终点控制一、前言现阶段,转炉炼钢终点人工经验控制碳温命中率一般为60%~80%。
转炉炼钢终点动态控制终点碳温命中率一般可达70%~85%。
自动化炼钢终点碳温命中率一般可达85%以上。
本文将深入分析这几种转炉炼钢终点控制技术。
二、转炉炼钢终点静态控制炼钢静态模型是转炉炼钢终点静态控制的基础,根据原材料条件以及吹炼钢种的温度和目标成分,利用物料平衡和热平衡,通过由操作经验和统计分析等所得到公式,计算出废钢、铁水、渣料、冷却剂、铁合金的加入量及供氧量,并根据计算结果进行装料和吹炼操作,对转炉炼钢终点进行控制。
建立准确的静态模型是终点静态控制的关键。
静态控制借助吹炼过程的初始条件进行定量计算,从而免受人工经验控制时随机性的影响,然而静态控制无法针对冶炼状况修正吹炼过程,所以提高终点命中率较难的提高。
转炉炼钢静态控制常用的模型主要有: 经验模型、机理模型、统计模型以及人工神经网络模型。
增量模型是利用本次初始数据及历史数据和目标状态增量来进行本次的操作变量计算和确定,又称为静态经验控制模型或静态增量控制模型。
机理模型是分析假设冶炼过程中各种参数,计算热平衡、物料平衡,得到关于铁水、废钢以及石灰的装料模型,在生产中的转炉炼钢过程复杂程度很大,有很多因素的影响,部分热平衡、物料平衡数据的确定,必须要根据假设(经验)条件进行,所以常规的机理模型,大部分是半机理半经验模型,参数较多难以控制。
统计模型是以黑箱原理为依据,对过程中物理化学规律不予以考虑,仅仅对系统输入量与输出量的实际关系加以考虑,以收集大量试验数据为基础,利用数学统计,对各主要变量变化以及数值进行统计计算。
该类模型具有比较简单的结构,鉴于仅需考虑输出量与输入量间的统计关系,能够分析随机偏差,还能够克服随机因素的影响,所以可以确保一定的精度。
电弧炉冶炼终点碳的控制
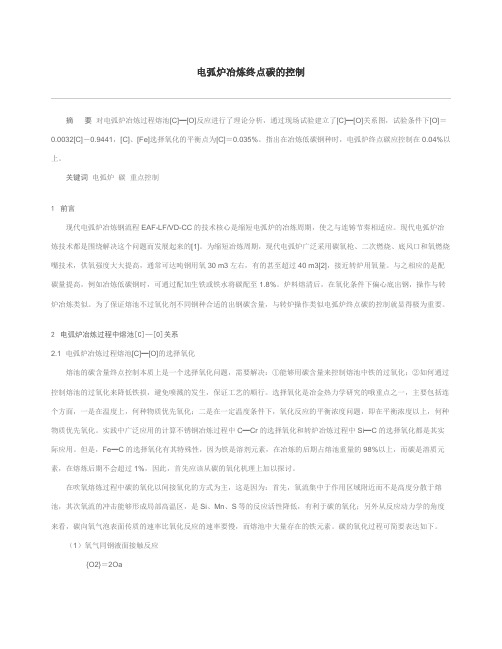
电弧炉冶炼终点碳的控制摘要对电弧炉冶炼过程熔池[C]—[O]反应进行了理论分析,通过现场试验建立了[C]—[O]关系图,试验条件下[O]=0.0032[C]-0.9441,[C]、[Fe]选择氧化的平衡点为[C]=0.035%。
指出在冶炼低碳钢种时,电弧炉终点碳应控制在0.04%以上。
关键词电弧炉碳重点控制1前言现代电弧炉冶炼钢流程EAF-LF/VD-CC的技术核心是缩短电弧炉的冶炼周期,使之与连铸节奏相适应。
现代电弧炉冶炼技术都是围绕解决这个问题而发展起来的[1]。
为缩短冶炼周期,现代电弧炉广泛采用碳氧枪、二次燃烧、底风口和氧燃烧嘴技术,供氧强度大大提高,通常可达吨钢用氧30 m3左右,有的甚至超过40 m3[2],接近转炉用氧量。
与之相应的是配碳量提高,例如冶炼低碳钢时,可通过配加生铁或铁水将碳配至1.8%。
炉料熔清后,在氧化条件下偏心底出钢,操作与转炉冶炼类似。
为了保证熔池不过氧化剂不同钢种合适的出钢碳含量,与转炉操作类似电弧炉终点碳的控制就显得极为重要。
2电弧炉冶炼过程中熔池[C]—[O]关系2.1 电弧炉冶炼过程熔池[C]—[O]的选择氧化熔池的碳含量终点控制本质上是一个选择氧化问题,需要解决:①能够用碳含量来控制熔池中铁的过氧化;②如何通过控制熔池的过氧化来降低铁损,避免喷溅的发生,保证工艺的顺行。
选择氧化是冶金热力学研究的哦重点之一,主要包括连个方面,一是在温度上,何种物质优先氧化;二是在一定温度条件下,氧化反应的平衡浓度问题,即在平衡浓度以上,何种物质优先氧化。
实践中广泛应用的计算不锈钢冶炼过程中C—Cr 的选择氧化和转炉冶炼过程中Si—C的选择氧化都是其实际应用。
但是,Fe—C的选择氧化有其特殊性,因为铁是溶剂元素,在冶炼的后期占熔池重量的98%以上,而碳是溶质元素,在熔炼后期不会超过1%,因此,首先应该从碳的氧化机理上加以探讨。
在吹氧熔炼过程中碳的氧化以间接氧化的方式为主,这是因为:首先,氧流集中于作用区域附近而不是高度分散于熔池,其次氧流的冲击能够形成局部高温区,是Si、Mn、S等的反应活性降低,有利于碳的氧化;另外从反应动力学的角度来看,碳向氧气泡表面传质的速率比氧化反应的速率要慢,而熔池中大量存在的铁元素。
转炉工艺操作规程
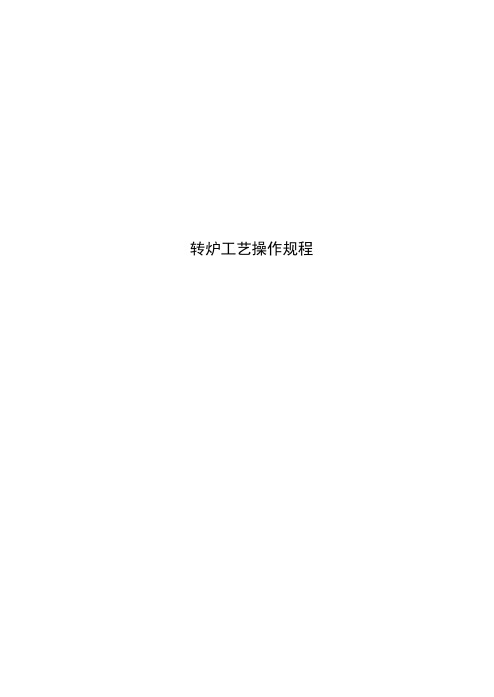
转炉工艺操作规程中铁炼钢部本标准适用于转炉冶炼工序。
1.工艺流程主操作本标准适用于转炉冶炼工序。
铁水1入炉铁水S含量按《冶炼标准》要求控制2入炉铁水计量误差范围不超过士500Kg3铁水带渣量:不超过1吨废钢理化性要求:符合原材料标准规定入炉废钢计量误差范围不超过士500Kg活性石灰理化性要求:符合原材料标准规定化学成分% :厂内活性石灰CaO > 91.3, SiO2< 2.8 , S< 0.025;厂外活性石灰CaO > 86.0, S< 0.045。
粒度范围:5~ 50 mm轻烧白云石理化性要求:符合原材料标准规定化学成分% : CaO >52.4, SiO2< 3.0, MgO >29.1, S< 0.040, P< 0.10粒度范围:5~ 30 mm轻烧镁球理化性要求:符合原材料标准规定化学成分% : MgO >65, CaO >5, S< 0.02粒度范围:5~ 30 mm锰矿理化性要求:符合原材料标准规定萤石理化性要求:符合原材料标准规定烧结矿理化性要求:符合原材料标准规定合成渣理化性要求:符合原材料标准规定硅铁理化性要求:符合原材料标准规定硅铁的化学成分锰铁理化性要求:符合原材料标准规定锰铁的化学成分硅锰理化性要求:符合原材料标准规定硅锰合金的化学成分硅钙包芯线理化性要求:符合原材料标准规定硅钙包芯线的化学成分铝线理化性要求:符合原材料标准规定增碳剂理化性要求:符合原材料标准规定增碳剂的化学成分钢包覆盖剂理化性要求:符合原材料标准规定本标准适用于转炉冶炼工序。
氧气氧气总管压力》1・2 Mpa;纯度》99.6%;氮气溅渣用氮气总管压力》1.2Mpa ;底吹用氮气总管压力》1.6Mpa ;纯度》99.99%;氩气氩气总管压力》1.6Mpa;纯度》99.99%;本标准适用于转炉冶炼工序。
1. 检测和计量系统确认完毕。
转炉炼钢终点控制技术

转炉炼钢终点控制技术摘要:本文首先简要概述了转炉炼钢的终点控制,基于此,详细论述了转炉炼钢终点的静态控制、转炉炼钢终点的人工经验控制、转炉炼钢终点的动态控制以及转炉炼钢终点的自动控制,分析了其中的关键环节,仅供大家参考。
关键词: 炼钢、转炉、终点控制一、前言现阶段,转炉炼钢终点人工经验控制碳温命中率一般为60%~80%。
转炉炼钢终点动态控制终点碳温命中率一般可达70%~85%。
自动化炼钢终点碳温命中率一般可达85%以上。
本文将深入分析这几种转炉炼钢终点控制技术。
二、转炉炼钢终点静态控制炼钢静态模型是转炉炼钢终点静态控制的基础,根据原材料条件以及吹炼钢种的温度和目标成分,利用物料平衡和热平衡,通过由操作经验和统计分析等所得到公式,计算出废钢、铁水、渣料、冷却剂、铁合金的加入量及供氧量,并根据计算结果进行装料和吹炼操作,对转炉炼钢终点进行控制。
建立准确的静态模型是终点静态控制的关键。
静态控制借助吹炼过程的初始条件进行定量计算,从而免受人工经验控制时随机性的影响,然而静态控制无法针对冶炼状况修正吹炼过程,所以提高终点命中率较难的提高。
转炉炼钢静态控制常用的模型主要有: 经验模型、机理模型、统计模型以及人工神经网络模型。
增量模型是利用本次初始数据及历史数据和目标状态增量来进行本次的操作变量计算和确定,又称为静态经验控制模型或静态增量控制模型。
机理模型是分析假设冶炼过程中各种参数,计算热平衡、物料平衡,得到关于铁水、废钢以及石灰的装料模型,在生产中的转炉炼钢过程复杂程度很大,有很多因素的影响,部分热平衡、物料平衡数据的确定,必须要根据假设(经验)条件进行,所以常规的机理模型,大部分是半机理半经验模型,参数较多难以控制。
统计模型是以黑箱原理为依据,对过程中物理化学规律不予以考虑,仅仅对系统输入量与输出量的实际关系加以考虑,以收集大量试验数据为基础,利用数学统计,对各主要变量变化以及数值进行统计计算。
该类模型具有比较简单的结构,鉴于仅需考虑输出量与输入量间的统计关系,能够分析随机偏差,还能够克服随机因素的影响,所以可以确保一定的精度。
100 t转炉-LF(VD)工艺冶炼轴承钢的氧含量控制

表 3 中间包钢水及 VD 离站炉渣成分 Table 3 Compositions of steel in tundish and ingredient of slag at finishing VD treatment
炉次
[Als] /%
TO /10 - 6
414952 0 . 003 16 414953 0 . 005 15 414954 0 . 007 14 414955 0 . 005 15 414956 0 . 004 9 15
· 48 ·
特殊钢
第 26 卷
═════════════════════════════════════════════════════════════
钢中的铝-氧远未达到平衡。因此,要降低 Ar 站
钢水中氧含量,要强化钢包钢水的动力学条件,加
强钢包底吹搅拌强度和保证一定的底吹时间。
从图 2 还可以看出,在铝、氧接近平衡时,钢
出钢过程钢水的脱氧主要用铝脱氧。图 2 给 出 Ar 站测定的钢水的活度氧含量,图中的1 600 ℃ 钢中铝-氧平衡线由铝的脱氧反应[2]计算得出。
从图 2 可知,对于 Ar 站钢水中氧含量距所计 算 的1 600 ℃ 时钢中铝-氧的平衡线[2]相差较多,
表 1 给出一些冶炼轴承钢炉次转炉终点、出 钢后钢水成分。从理论分析可得,转炉冶炼终点 碳含量高的炉次,出钢时钢中氧含量较低,出钢时 加入的铝块和氩站喂铝线量是相同的,出钢后钢 水酸溶铝含量应该是相同的。但从表中可知,对 于 414952 和 414953 炉次,冶炼终点钢水碳含量差 不多,出钢时钢水氧含量基本相同,出钢时加铝块 和氩站喂铝线量是相同的,但出钢后钢水中酸溶 铝含量相差较多。这说明出钢时转炉下渣量对于 钢水氧含量影响较大。因此,对于转炉的冶炼操 作应尽量降低冶炼终点炉渣(FeO)含量和减少转 炉下渣量,控制转炉下渣量小于 5 kg/t 钢。 2 . 3 LF 精炼过程钢水氧含量的控制
唐钢转炉冶炼中碳钢碳氧积的控制研究

过热度的情况下,尽力的去降低出钢温度。同时由于
顶底复合吹炼的影响,强化了熔池的搅拌作用,促进 熔池内的反应,使碳氧反应更趋近与平衡,可有效的 降低碳氧积。
2 温度对钢水终点碳氧积的影响
由前文碳氧积的计算可知,温度是碳氧积的主
要因素,降低出钢温度,则平衡常数 K 降低,碳氧积
也就降低。因此如何有效的降低出钢温度是降低碳
转炉终点氧位是转炉冶炼的重要指标,对于洁 净钢冶炼、合金料消耗、冶炼成本等影响较大。本文 从碳氧积入手,探讨唐钢转炉冶炼中碳钢过程的氧 位控制情况。唐钢第二钢轧厂现有 2 座公称容量 65t 转炉,炉容比为 0.93,采用顶底复吹技术,采用 4 孔 氧枪,喉口直径 26 mm,喷孔夹角 10.5°,设计氧气流 量 17000 Nm3/h,供氧强度 3.57 Nm3/tmin。底吹透气元 件为 4 支环缝式底吹枪。
的线性关系。随着终点温度的升高,氧位逐渐增加。
温度低于 1610 ℃或高于 1660℃ 时氧位开始出现震
荡,不排除炼钢工在过低温度和过高温度出钢控制
上的经验不足,因操作原因导致。
从纯净钢的角度出发,出钢温度应控制在较低
水平,从根本上控制钢中夹杂物的生成。但矛盾的是
通常纯净钢的冶炼需要二次精炼处理,其过程需要
其中,Pθ 为大气压力;H 钢、H 渣为 CO 气泡以上
钢液、熔渣的高度;ρ 钢、ρ 渣为钢液、熔渣的密度;σ 为
金属液表面张力;rCO 为 CO 气泡半径。
碳氧积的主要影响因素为温度,这是由于碳氧
反应是放热反应,温度升高,则平衡常数 K 升高,碳
氧积值也就升高。这就要求我们根据不同的钢种和
不同的冶炼工艺,制定不同的出钢温度,在保证中包
大,偏离理论曲线更远,同时氧位更为分散。可知在
涟钢210转炉厂超低碳钢全氧控制技术

方式与渣全铁含量 、 R H炉 A L—O B量 ( 吹 氧 加
铝 工艺 ) 、 R H炉 纯脱 气时间等 5个 因素 与全氧 的相关性 , 本 次 分 析 共 采 集 了 2个 月 的 超 低 碳 钢 中间包钢水全 氧含量 , 每次都 是在 大包 1 0 0 t 钢水 同部位取样 。
予特别 的检查 , 直接 向客户交货 ; b . 而T [ O ] 在 3 O一5 5 p p m的 冷轧 板则 必须 严 格 检查 ; c . 对 T
[ O ]> 5 5 p p m 的冷轧 板采 取 降级使 用 。 因此 , 控制钢水 中的 T [ o 3 含量 是冶炼超 低碳铝 镇静 钢 的关键 技术之一 。 … 本 文对 影响 2 1 0转 炉厂超低碳钢连铸 中间 包全 氧含量 的影 响 因素进行 相关性 分 析 , 提 出 转 炉冶炼 、 R H炉 处理 和 连 浇等 工 艺 中影 响 氧 化 铝产生和去 除的关键 工艺 参数 , 为降 低 中间 包钢水 全氧含量 , 生产 洁净钢 提供依据 。
F e O、 M n O的高氧化性顶渣会将氧 传人钢水 中 , 造成钢水二 次氧 化 , 从R H合 金化 开始 到 连铸 浇注结束 , 顶渣 一 直 进行 传 氧 反应 , 尤 其在 连 铸大包浇 注 后期 , 随 着 大包 钢 水液 位 降 低 , 流 场活 跃 程 度 增 加 , 钢 渣 二 次 氧 化 进 一 步 加 剧¨ J I 。 目前 国 内 大 部 分 钢 厂 采 用 的 挡 渣 方 式为 “ 红外下渣检测 + 挡 渣镖 ” 工艺, 该挡渣工 艺 的效 果 与 挡 渣 镖 质 量 、 出 钢 口状 况 、 炉 型 等 因素 有 关 , 挡渣 效果 不稳定 。涟钢 2 1 0转 炉 厂 2 # 转炉采用挡渣 镖工艺 , 而为减 少转 炉高氧化 性渣流入 钢包 , 现 已将 1 # 转炉“ 红 外下 渣检测 + 挡渣镖挡渣 ” 升级为 “ 红外下 渣检测 +滑板 挡 渣 ”, 改造后 两挡渣工艺钢包 顶渣 厚度 、 钢 包 顶渣 T F e含 量 如 图 1 、 图 2, 可 见 滑 板 挡 渣 是 碳 含 量 要 求 极 低 的 钢 , 要 求 [ c ]<4 0 p p m, 甚 至要求 [ c ]<2 0 p p m, 如 I F 钢、 无取 向电工 钢 、 O 5板 等 。超 低 碳铝 镇 静钢 广泛用于汽 车板 、 易拉 罐等 产 品 , A 1 : O , 类 氧 化物夹杂对 钢的 内在质量 、 加工性 能 以及对 钢 材 的表 面质 量 和深 冲成 形加 工 性 能 有不 利 影
炼钢转炉冶炼低碳钢脱氧合金化工艺优化精编版

炼钢转炉冶炼低碳钢脱氧合金化工艺优化精编版近年来,随着全球环保意识的提升和新能源材料的广泛应用,对于炼钢转炉冶炼低碳钢脱氧合金化工艺的优化研究受到了广泛关注。
本文将就该工艺的优化进行精编论述。
低碳钢脱氧合金化工艺的目标是通过合理的调整转炉冶炼过程中的气体成分、温度、转炉操作等参数,减少钢中的氧含量,实现低碳钢的合金化。
目前常用的脱氧合金化剂有铝、硅、锰等,它们在转炉冶炼过程中能与钢中的氧反应生成相应的氧化物,从而降低钢中的氧含量。
在炼钢转炉冶炼低碳钢脱氧合金化过程中,需要注意以下方面的优化:首先,要合理选择脱氧剂,并确定其添加量。
一般来说,铝是最常用的脱氧剂,其添加量应根据钢的成分和规格进行合理调整。
同时,由于铝在钢中的溶解度较低,需要通过增加温度和延长保温时间来提高脱氧效果。
其次,要控制转炉中的气氛成分。
脱氧合金化反应是在氧化性气氛中进行的,因此需要确保转炉中的气氛保持适当的氧化性。
一般来说,通过调节煤气的流量和氧气的进气量等参数来控制气氛成分。
此外,还需要注意炉排煤气中的水蒸气含量,过高的水蒸气含量会影响脱氧合金化反应的进行。
此外,还要注意转炉操作的合理性。
在进行低碳钢的脱氧合金化时,需要合理控制吹氧时间、转炉的转速等参数。
合理的吹氧时间能够充分利用脱氧剂的作用,降低钢中的氧含量;而合理的转速可以确保转炉中的煤气和钢水充分接触,促进脱氧合金化反应的进行。
最后,要注意对炼钢转炉冶炼低碳钢脱氧合金化工艺进行监测和调整。
通过在线监测钢水中的氧含量和其他成分的变化,可以及时发现问题并采取相应的措施进行调整,确保工艺的稳定性和一致性。
总之,炼钢转炉冶炼低碳钢脱氧合金化工艺的优化对提高钢质和节约能源具有重要意义。
通过合理选择脱氧剂、控制气氛成分、优化转炉操作以及进行及时监测和调整,可以实现低碳钢脱氧合金化工艺的高效、稳定和可持续发展。
试论转炉炼钢终点控制技术

试论转炉炼钢终点控制技术作者:王志刚杨振宏谢治国来源:《中国机械》2013年第24期摘要:转炉炼钢是钢铁生产厂的重要生产和制造工艺,随着科学技术的发展和社会生产规模扩大以及优化生产结构与升级生产工艺的要求,在转炉炼钢的生产中,终点控制技术已经成为限制转炉炼钢工艺和质量的关键环节。
提高转炉炼钢的终点控制技术能够极大的降低能源消耗并提高炼钢的生产效率和生产厂家的经济效益。
关键词:转炉炼钢;终点控制;技术探讨0.引言转炉炼钢终点控制技术作为转炉冶炼技术的后期操作是非常关键的技术操作,终点控制水平对产品质量和生产效率都有直接的影响。
转炉炼钢终点控制技术包括对钢水的温度和碳含量的控制,其中的碳含量控制过低会提高钢中的氮和氧的含量,但是如果控制的过高则会导致钢的脱磷和脱硫效果变差,从而影响钢的品质;而终点控制在温度上如果控制的过高或过低也会不同程度的增加冷却剂及副原材料的消耗,从而增加冶炼的时间和冶炼金属的消耗,对炉衬寿命产生很大的影响。
转炉炼钢的终点控制技术有拉碳补吹法、一吹到底增碳法、成分测算法等,在炼钢过程中还要注重对终点的静态和动态控制,并积极引进先进的和智能型的终点控制技术,提高转炉炼钢的质量和效率。
1.转炉炼钢终点人工经验控制技术1.1.拉碳补吹法拉碳补吹法是一种比较常见的以人工经验为主的控制技术。
主要工作内容是在吹炼后期,根据钢中的碳含量来判定是否达到目标和停止吹氧,但这种终点控制方法是以人工经验判定为主的。
但是,在钢的中、高碳含量生产过程中,由于钢中碳含量较高且碳的氧化速度比较快,所以人工经验判定钢中碳含量的难度比较大,此时,高拉碳加补吹调整的操作技术则是最佳的终点控制方法[1]。
这种方法的操作前提条件是要对供氧时间及其耗氧量以及吹炼时钢的特征来考虑,将终点判定定位在稍微高于炼钢中实际碳含量的上限,同时,在取样与测定温度后对炼钢的温度进行调节并补吹。
拉碳补吹法的操作的特征在于终点钢水中含氧量较少,钢中锰含量较高、脱氧剂消耗较少、金属获得率较高,此方法适合中、高碳钢的冶炼,但是它的终点一次命中率低。
氧气顶吹转炉炼钢终点碳控制的方法

氧气顶吹转炉炼钢终点碳控制的方法氧气顶吹转炉炼钢终点碳控制的方法终点碳控制的方法有三种,即一次拉碳法、增碳法和高拉补吹法。
一次拉碳法按出钢要求的终点碳和终点温度进行吹炼,当达到要求时提枪。
这种方法要求终点碳和温度同时到达目标,否则需补吹或增碳。
一次拉碳法要求操作技术水平高,其优点颇多,归纳如下:(1) 终点渣TFe含量低,钢水收得率高,对炉衬侵蚀量小。
(2) 钢水中有害气体少,不加增碳剂,钢水洁净。
(3) 余锰高,合金消耗少。
(4) 氧耗量小,节约增碳剂。
增碳法是指吹炼平均含碳量≥0.08%的钢种,均吹炼到ω[C]=0.05%~0.06%提枪,按钢种规范要求加入增碳剂。
增碳法所用碳粉要求纯度高,硫和灰分要很低,否则会玷污钢水。
采用这种方法的优点如下:(1)终点容易命中,比“拉碳法”省去中途倒渣、取样、校正成分及温度的补吹时间,因而生产率较高;(2)吹炼结束时炉渣Σ(FeO)含量高,化渣好,去磷率高,吹炼过程的造渣操作可以简化,有利于减少喷溅、提高供氧强度和稳定吹炼工艺;(3)热量收入较多,可以增加废钢用量。
采用“增碳法”时应严格保证增碳剂质量,推荐采用C>95%、粒度≤10毫米的沥青焦。
增碳量超过0.05%时,应经过吹Ar等处理。
高拉补吹法当冶炼中、高碳钢钢种时,终点按钢种规格稍高一些进行拉碳,待测温、取样后按分析结果与规格的差值决定补吹时间。
由于在中、高碳(ω[c]>0.40%)钢种的碳含量范围内,脱碳速度较快,火焰没有明显变化,从火花上也不易判断,终点人工一次拉碳很难准确判断,所以采用高拉补吹的办法。
用高拉补吹法冶炼中、高碳钢时,根据火焰和火花的特征,参考供氧时间及氧耗量,按所炼钢种碳规格要求稍高一些来拉碳,使用结晶定碳和钢样化学分析,再按这一碳含量范围内的脱碳速度补吹一段时间,以达到要求。
高拉补吹方法只适用于中、高碳钢的吹炼。
根据某厂30 t 转炉吹炼的经验数据,补吹时的脱碳速度一般为0.005%/s。
转炉终点钢中氧含量控制
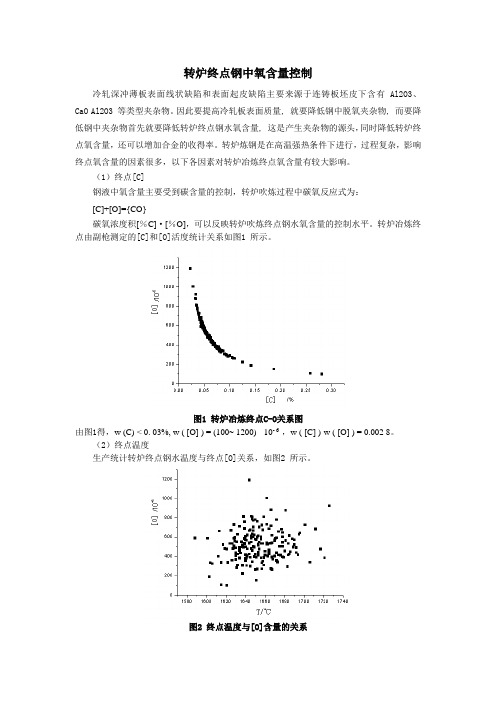
转炉终点钢中氧含量控制冷轧深冲薄板表面线状缺陷和表面起皮缺陷主要来源于连铸板坯皮下含有Al2O3、CaO·Al2O3 等类型夹杂物。
因此要提高冷轧板表面质量, 就要降低钢中脱氧夹杂物, 而要降低钢中夹杂物首先就要降低转炉终点钢水氧含量, 这是产生夹杂物的源头,同时降低转炉终点氧含量,还可以增加合金的收得率。
转炉炼钢是在高温强热条件下进行,过程复杂,影响终点氧含量的因素很多,以下各因素对转炉冶炼终点氧含量有较大影响。
(1)终点[C]钢液中氧含量主要受到碳含量的控制,转炉吹炼过程中碳氧反应式为:[C]+[O]={CO}碳氧浓度积[%C]·[%O],可以反映转炉吹炼终点钢水氧含量的控制水平。
转炉冶炼终点由副枪测定的[C]和[O]活度统计关系如图1 所示。
图1 转炉冶炼终点C-O关系图由图1得,w (C) < 0. 03%, w ( [O] ) = (100~ 1200) ×10- 6 ,w ( [C] )·w ( [O] ) = 0.002 8。
(2)终点温度生产统计转炉终点钢水温度与终点[O]关系,如图2 所示。
图2 终点温度与[O]含量的关系由图2可知,钢水中氧含量随温度升高而增加。
因此降低出钢温度,可以减少钢水中氧含量。
(3)炉渣对终点氧含量的影响转炉冶炼后期,炉渣中氧化铁的含量与钢水中氧含量有关联。
氧化铁的含量与钢水中氧含量存在着相对平衡关系。
一般地,炉渣中氧化铁的含量越高,炉渣氧化性就越强,钢中氧含量则相对较高,金属收得率就低。
(4)补吹操作生产统计转炉吨钢氧耗量与终点[C]关系,如图3 所示。
图3 氧耗量与终点[C]关系如图3所示,终点w ( [C] ) = 0. 02% ~ 0. 10% ,吨钢氧耗量在42~ 582m3 / t 之间。
说明终点[ C] 越低( 或补吹) , 吹入氧主要用来氧化铁, 使渣中FeO 大增, 同时增加了终点[O]。
转炉终点碳含量
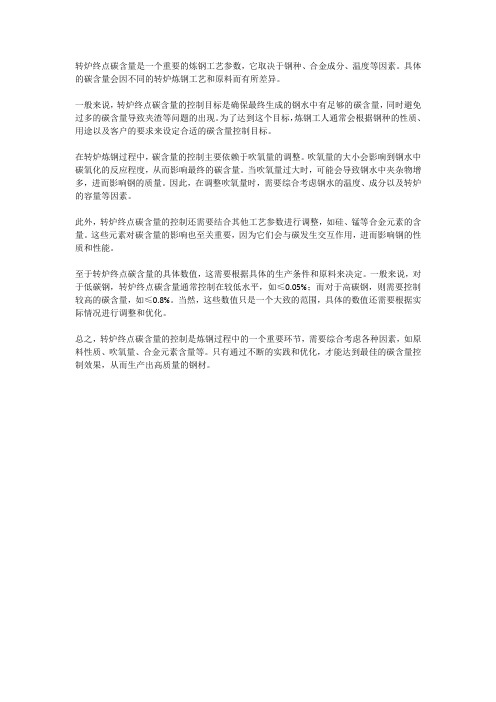
转炉终点碳含量是一个重要的炼钢工艺参数,它取决于钢种、合金成分、温度等因素。
具体的碳含量会因不同的转炉炼钢工艺和原料而有所差异。
一般来说,转炉终点碳含量的控制目标是确保最终生成的钢水中有足够的碳含量,同时避免过多的碳含量导致夹渣等问题的出现。
为了达到这个目标,炼钢工人通常会根据钢种的性质、用途以及客户的要求来设定合适的碳含量控制目标。
在转炉炼钢过程中,碳含量的控制主要依赖于吹氧量的调整。
吹氧量的大小会影响到钢水中碳氧化的反应程度,从而影响最终的碳含量。
当吹氧量过大时,可能会导致钢水中夹杂物增多,进而影响钢的质量。
因此,在调整吹氧量时,需要综合考虑钢水的温度、成分以及转炉的容量等因素。
此外,转炉终点碳含量的控制还需要结合其他工艺参数进行调整,如硅、锰等合金元素的含量。
这些元素对碳含量的影响也至关重要,因为它们会与碳发生交互作用,进而影响钢的性质和性能。
至于转炉终点碳含量的具体数值,这需要根据具体的生产条件和原料来决定。
一般来说,对于低碳钢,转炉终点碳含量通常控制在较低水平,如≤0.05%;而对于高碳钢,则需要控制较高的碳含量,如≤0.8%。
当然,这些数值只是一个大致的范围,具体的数值还需要根据实际情况进行调整和优化。
总之,转炉终点碳含量的控制是炼钢过程中的一个重要环节,需要综合考虑各种因素,如原料性质、吹氧量、合金元素含量等。
只有通过不断的实践和优化,才能达到最佳的碳含量控制效果,从而生产出高质量的钢材。
转炉冶炼低碳钢终点氧含量控制

转炉冶炼低碳钢终点氧含量控制目录前言1.转炉冶炼低碳钢终点钢中氧含量控制2.转炉终点氧对RH处理钢中氧影响3.转炉冶炼低碳钢终点氧预报模型结语前言当转炉吹炼到终点时,钢水中溶解了过多氧称为溶解氧[O]溶(或a[O])。
出钢时钢水脱氧合金化的目的:(1)把钢水中[O]溶脱掉,转变为脱氧夹杂物——夹杂物工程;(2)合金化达到规定的钢种成分(C、Si、Mn、Als)。
经过脱氧和炉外精炼操作(吹Ar、LF、VD、RH),脱氧所生成夹杂物(Al2O3、MnO·SiO2、CaO·SiO2·Al2O3、CaO·Al2O3)。
85%上浮到钢包顶渣,夹杂物尺寸绝大部分<30μm,钢水中T[O]可以达到<30ppm,甚至小于10ppm,也就是说钢水很“干净”了。
因此,可以用钢的总氧量T[O]来表征钢的洁净度,也就是钢中夹杂物水平。
故T[O]可表示为:T[O]=[O]溶+[O]夹因此要降低T[O],则:(1)降低[O]溶:降低转炉吹炼终点氧,这是产生夹杂物的源头;(2)降低[O]夹:也就是减少钢中夹杂物:●降低脱氧产物:控制脱氧和精炼操作促进原生的脱氧产物上浮;●减少新的夹杂物生成:也就是减少钢水在连铸过程中钢水二次氧化。
如何保持铸坯中T[O]与炉外精炼后钢水中T[O]处在一个水平呢?否则炉外精炼的效果就前功尽弃了。
在连铸过程中的任务是:●防止钢水再污染(二次氧化);●设法进一步排除夹杂物(中间包冶金、结晶器冶金等)。
下面主要是讲转炉冶炼终点氧控制问题,这是产生夹杂物的源头。
1转炉冶炼低碳钢终点钢中氧含量控制T[O]=[O]溶+[O]夹杂出钢时:[O]夹杂→0,T[O]=[O]溶;生产统计表明,终点[O]溶(a[O])决定于:(1) 终点[C]从某厂转炉冶炼终点由副枪测定的[C]和a[O]统计关系如图1所示,由图可知:图1 转炉冶炼终点C-O关系图Ⅰ区:[O]溶波动在C-O平衡曲线附近(C<0.04%,[O]=600~900ppm) [C][O]=0.0027 炉龄<2500炉Ⅱ区:[O]溶远离C-O平衡曲线(C<0.04%,[O]=800~1400ppm) [C][O]=0.0031~0.0037 炉龄>2500炉当炉龄大于3000炉,达到7500炉甚至10000炉,钢水中[C][O]积远离平衡线,钢水中[O]波动较大,这可能与采用溅渣护炉操作,降低了复吹冶金效果有关。
转炉-精炼-连铸过程钢中氧的控制

15
• 当终点[C]=0.025~0.04%时,随着温度的升高, 终点[O]溶呈上升趋势。当T>1680℃时,终点[O] 溶明显增加。
• 1620℃~1680℃之间,氧含量总体水平较低,平 均为702ppm,该范围的炉次共占总炉次的30% 左右;
• 出钢温度大于1680℃时,终点钢水氧含量有明显 的升高趋势,平均为972ppm,占总炉次的70% 左右。
出钢时,进行脱氧合金化,[O]溶转变成 氧化物夹杂,可用[O]夹杂表示,所以钢中氧 可用总氧T[O]表示为:
T[O]=[O]溶+[O]夹杂
2021/7/9
3
1 钢中的氧-钢洁净度的量度
出钢时:钢水中[O]夹杂→0,T[O]=[O]溶;
脱氧后:根据脱氧程度的不同[O]溶→0, T[O]=[O]夹杂。
• 洁净钢是一个相对概念,钢中T[O]控制到 什么水平,决定于钢种和产品用途;
• 产品质量不仅要控制夹杂物数量,而且夹 杂物的形态、尺寸和分布也要得到控制。
2021/7/9
12
2. 转炉终点钢中氧的控制
T[O]=[O]溶+[O]夹杂
出钢时:[O]夹杂→0,T[O]=[O]溶; 生产统计表明,终点[O]溶(a[O])决定于:
2021/7/9
16
(3)终渣(FeO)
%
渣 中 ( FeO +MnO) 含 量
终 点 氧 含 量 ( pp m)
1800
终 点 [0]
1600 1400 1200 1000
800 600 400 200
0 12 14 16 18 20 22 24 26 炉 渣 中 ( FeO+MnO) 的 含 量 ( %)
UOE管 (厚
影响钢水终点氧质量因素实验报告

影响钢水终点氧质量因素实验报告摘要:为了降低转炉终点氧质量分数的含量,通过对我厂1#转炉现场生产数据的统计,分析了转炉影响钢水终点氧质量分数的影响因素,研究了终点碳质量分数、炉龄、终点残猛,终点温度等因素对终点氧的影响规律[1],从而获得最佳终点钢水终点氧质量分数,一方面可以减少脱氧合金消耗,降低钢铁成本,另一方面可以减少钢水中氧化物夹杂含量,提高钢铁产品的质量,对完善生产工艺提出了相应建议。
关键词:终点氧终点碳质量分数炉龄终点残锰终点温度引言:转炉吹炼终点钢水中的氧质量分数高低对钢的纯净度和金属收得率有着重要的影响,根据反应平衡的原理,随着钢中碳的降低其氧质量分数势必会增高,因此在出钢过程中,如何能在保证一定碳质量分数的同时,尽量降低钢水中的氧质量分数,对于低碳钢和高附加值钢的冶炼有着重要意义。
而钢水终点的碳氧积又是评价转炉终点控制效果的一个重要指标,在碳质量分数一定时,它的高低是衡量钢中氧质量分数的重要依据。
终点氧低有利于降低合金消耗,减少脱氧过程中形成的夹杂物,提高钢水质量。
为此,本文研究了碳质量分数、炉龄、终点温度,终点残锰等因素对终点氧积影响规律,从而为更好的控制钢水终点氧质量分数提供参考依据。
1 实验数据处理通过我在我们钢厂公称容量为120 t 的1#顶底复吹转炉工作实践,选取2012 年3 月到2013年7 月1#转炉的生产数据3290组。
按照理论和统计的规律进一步对数据进行筛选。
在数据选择上对于冶炼中碳钢时,由于考虑成本,钢水氧含量低等因素,基本上不对钢水进行定氧,所以在这里只选取低碳钢的生产数据进行分析比较。
处理后获合理完整的数据,然后根据需要在从中筛选一些数据进行合理的统计分析。
但在转炉实际生产过程中,因为碳和氧的浓度不等于它们的活度,m不是一个常数,碳氧质量分数分布一般情况都会在理论值附近的一个范围内波动。
下图所示为1#转炉冶炼终点碳氧质量分数分布状况(在这里取温度值1630-1640摄氏度,终点残锰0.095%-0.105%,炉龄范围109-2238炉次)。
- 1、下载文档前请自行甄别文档内容的完整性,平台不提供额外的编辑、内容补充、找答案等附加服务。
- 2、"仅部分预览"的文档,不可在线预览部分如存在完整性等问题,可反馈申请退款(可完整预览的文档不适用该条件!)。
- 3、如文档侵犯您的权益,请联系客服反馈,我们会尽快为您处理(人工客服工作时间:9:00-18:30)。
第44卷 第5期 2009年5月钢铁Iron and SteelVo l.44,N o.5M ay 2009转炉冶炼低碳钢终点氧含量控制蔡开科(北京科技大学冶金与生态工程学院,北京100083)摘 要:用户对钢的洁净度要求越来越高,为此必须尽力减少钢中非金属夹杂物数量和尺寸,尤其是对高品质冷轧产品更为重要。
首先要控制转炉冶炼终点钢水中氧活度和渣中(FeO +M nO)含量,因为这是产生钢中夹杂物的根源。
根据在工厂进行的调查研究工作,讨论了冶炼低碳钢转炉终点氧含量控制因素,转炉终点氧含量对RH 脱碳结束氧的影响。
并提出了降低转炉终点氧含量的技术措施。
关键词:低碳钢;转炉;终点氧中图分类号:T F 71 文献标识码:A 文章编号:0449-749X(2009)05-0027-05Controlling Oxygen Activity in the Molten Steel atBlowing End -Point of BOF SteelmakingCAI Ka-i ke(Metallurgical and Ecolog ical Eng ineer ing School,Univer sity of Science and Technology Beijing,Beijing 100083,China)Abstract:Steel cleanliness is increased under cust omer .s r equirement.Steel pr oducers are striving to pr oduce cleaner steels.T her efore,to reduce t he quantity and size of no nmetallic inclusions in the steel is imperative,especially for high quality co ld -ro lled pro ducts.T he main contro lling is o xy gen activ ity in the mo lten st eel and FeO +M nO in the slag at t he blow ing end -point of BO F steelmaking,because they are the main source of pr oducing nonmetal inclu -sio ns.Based o n o ur study w or k and recent lit erature,o x yg en content co nt ro l of low carbon at the blow ing end -po int of BO F and influence o f the o xy gen co ntent at the blow ing end o n decarburization in the RH v essel ar e discussed.Ac -co rding to the r esults,decr easing measur ements of end -po int ox yg en content are put forw ard.Key words:low carbon steel;BOF ;end -po int ox yg en content作者简介:蔡开科(1936-),男,教授; E -mail :k aik ecai@metall.u ; 修订日期:2008-10-12当转炉吹炼到终点时,钢水中溶解了过多氧称为溶解氧[O]r (或a [O])。
出钢时钢水脱氧合金化的目的:把钢水中[O]r 脱掉,转变为脱氧夹杂物;合金化达到规定的钢种成分(C 、Si 、Mn 、Al s 等)。
经过脱氧和炉外精炼操作(吹Ar 、LF 、VD 、RH ),脱氧所生成夹杂物(Al 2O 3、MnO #SiO 2、CaO #SiO 2#A l 2O 3、CaO #Al 2O 3)。
大部分上浮到钢包顶渣,夹杂物尺寸绝大部分<30L m ,钢水中总氧w (T [O])可以达到<30@10-6,甚至小于10@10-6,也就是说钢水很/干净0了。
因此,可以用钢的总氧量T [O]来表征钢的洁净度,也就是钢中夹杂物水平。
故T[O]可表示为:T [O]=[O]r +[O]j 。
因此要降低T[O],则:降低[O]r ,降低转炉吹炼终点氧,这是产生夹杂物的源头;降低[O]j ,也就是减少钢中夹杂物:降低脱氧产物,控制脱氧和精炼操作促进原生的脱氧产物上浮;减少新的夹杂物生成,也就是减少在连铸过程中钢水二次氧化。
生产实践表明,冷轧深冲薄板表面线状缺陷(Sliver)和表面起皮缺陷(Pencil blister)主要来源于连铸板坯皮下含有Al 2O 3、CaO #Al 2O 3等类型夹杂物。
因此要提高冷轧板表面质量,就要降低钢中脱氧夹杂物,而要降低钢中夹杂物首先就要降低转炉终点钢水氧含量,这是产生夹杂物的源头。
1 转炉冶炼低碳钢终点钢中氧含量控制钢中总氧含量T[O]可表示为:T [O]=[O]r +[O]j出钢时:[O]j y 0,T[O]=[O]r根据作者与合作者在某钢厂的生产统计表明,转炉终点[O]r (a [O])决定于[1]:(1)终点[C]从某厂转炉冶炼终点由副枪测定的[C]和a [O]统计关系如图1所示,由图可知:Ñ区:[O]r 波动在C -O 平衡曲线附近w (C)<0.04%,w ([O])=(600~900)@10-6,w ([C])#w ([O])=0.0027,炉龄<2500炉;Ò区:[O]r 远离C -O 平衡曲线w (C)<0.04%,w ([O])=(800~1400)@10-6),钢 铁第44卷图1 转炉冶炼终点C -O 关系图Fig.1 Relationship between C and O at the end -point of BOFw ([C])#w ([O])=0.0031~0.0037,炉龄>2500炉。
当炉龄大于3000炉,达到7500炉甚至10000炉,钢水中[C][O]积远离平衡线,钢水中[O]r 波动较大,这可能与采用溅渣护炉操作,降低了复吹冶金效果有关。
(2)终点温度生产统计转炉终点钢水温度与终点[O]r 关系如图2所示。
图2 终点温度与[O]r 关系Fig.2 The relationship between dissolved oxygenand temperature of liquid steel at the end -point of BOF当终点w ([C])=0.025%~0.040%时,随着温度的升高,终点[O]r 呈上升趋势。
当温度>1680e 时,终点[O]r 明显增加。
(3)终渣(FeO)如图3、4所示,当终点w ([C])=0.02%~0106%时,终点渣中w ((FeO +M nO ))为14%~24%,而终点[O]r 波动较大。
(4)后吹操作如图5所示,终点w ([C])=0.02%~0.06%,氧耗量在48~58m 3/t 之间。
说明终点[C]越低(或后吹),吹入氧主要用来氧化铁,使渣中FeO 大增(图4),同时增加了终点[O]r (图3)。
后吹小于1#28#第5期蔡开科:转炉冶炼低碳钢终点氧含量控制min,补充氧800~1000m3,渣中w((FeO))升高5%~15%。
生产实践证明,如表1所示,采用良好的底吹气搅拌操作,可明显降低渣中FeO和钢水[O]r。
表1转炉出钢渣中(FeO)、钢水[O]和[C]的关系(质量分数)Table1Relationship among(FeO)in slag,[O]and[C]出钢w([C])/%渣中w((FeO))/%w([O])/10-60.0222/24550/6000.0320/22400/5000.0418/20300/400在铁水成分和吹炼制度一定的条件下,要降低转炉终点[O]r,必须准确控制终点钢水碳和温度:(1)控制w([C]z)不要<0.035%;(2)控制终点温度在1640~1680e;(3)渣中w((FeO+M nO))在14%~18%;(4)提高转炉终点碳和温度的命中率,杜绝后吹;(5)强化复吹效果(尤其是对低碳钢)。
w([C]z)=0.02%~0.05%顶吹终点w([O]r)=(700~900)@10-6w([C]z)=0.02%~0.05%复吹终点w([O]r)=(250~600)@10-6采用动态控制,提高转炉[C]和温度的双命中率(90%~93%),减少后吹,加强溅渣护炉后高炉龄的复吹效果是降低转炉终点[O]r含量的有效措施。
既可节约铁合金消耗,更重要的是从源头上减少钢中夹杂物生成,提高钢的洁净度,这对生产低碳钢或超低碳钢的冷轧薄板是非常重要的。
因此,对生产低碳、超低碳钢用于深冲用途的薄板,应强调复吹效果降低终点[O],保证产品质量。
而不是强调溅渣护炉,提高炉龄。
2转炉终点氧对RH脱碳结束钢中氧影响生产超低碳钢时,转炉终点w([C])= 0.02%~0.04%,经RH脱碳达到目标w([C])= (30~20)@10-6,作者统计的RH脱碳前后钢水中氧的关系如图6[1,2]所示。
图6RH脱C前后氧含量变化Fig.6Change of oxygen content bef oreand af ter RH decarburization由图6可知,转炉吹炼终点[O]高,RH脱C结束后钢水[O]也高。
RH脱碳前后钢水中[C]、[O]含量变化如表2所示。
表2RH脱碳前后的C、O含量变化(质量分数)Table2Change of[C]and[O]content bef ore and after RH decarburization[C]范围初始[C]p/%初始[O]p/10-6脱碳后[C]p/%脱碳后[O]p/10-6$[O]t/10-6<0.020.0188430.00226132350.02~0.030.0267850.00245452480.03~0.040.0336970.00284433070.04~0.050.0426040.0027356277>0.050.0534740.0033240324注:下角p代表实测平均值,下角t代表计算值。
由表2可知:初始w([C])=0.02%~0.05%经RH脱C 后,目标w([C])平均为(30~20)@10-6。