转炉“生铁块渣补”应用实践
转炉渣的综合利用

转炉渣综合利用现状孙晓 10钢4 201003040213摘要:为了提高钢渣的合理回收,本文介绍了钢渣的各种处理技术,从而实现了资源化综合利用,并展望了钢渣综合利用的未来前景。
本文综合阐述了国内外钢渣综合处理技术,钢渣是炼钢工业的副产品。
分析了钢渣的基本物理特性、化学成份、矿物组成等理化性能。
介绍钢渣在筑路、烧结矿、水泥、建材、环境工程和农业等领域的综合利用。
关键词:钢渣综合利用环境保护Slag comprehensive utilizationSun Xiao 10 steel 4, 201003040213Abstract: in order to improve the reasonable recovery of steel slag, steel slag were introduced in this paper all kinds of processing technology, so as to realize the comprehensive utilization of resource, the prospect of comprehensive utilization of steel slag in the future was discussed. The paper expounds the steel slag comprehensive treatment technology at home and abroad, steel slag is a byproduct of steel industry. Analyzed the basic physical properties, chemical composition of steel slag, ore material composition such as the physical and chemical properties. Introduction to steel slag in road construction, sinter, cement, building materials, agricultural and environmental engineering in the field of comprehensive utilization.Keywords: steel slag comprehensive utilization of environmental protection1. 前言目前,由于对环境,节能和降低成本等方面的要求,国内外各钢铁厂都非常重视对二次资源综合利用技术研究。
转炉炼钢中留渣技术的原理及应用

2.3留渣安锂 近年来,随着我国转炉炼钢技术不断发展和完
善,由于顶底复合吹炼、溅渣护炉等一系列的工艺出 现之后,能有效地解决喷溅问题。对于渣循环来说, 它能够带来良好的经济效益,从单扎法中衍生出各 种各样的操作工艺,自从留渣技术应用之初,要考虑 到它自身的安全,采取留渣操作之后进入废钢以后,
间,这对前期脱离有着积极的推动作用,经过反复的 实践研究,其中影响脱离效率撮主要的因素就在于 物质的酸碱度和炉渣的含量,避免炉渣中氧化铁过 多,产生的喷溅,必须要确保它的游离氧含量大于 900x10电科学的调整留渣含量叫 32稳定留渣量
对于绝大部分的炼钢厂来说,冶炼效果和留渣 量的稳定性,两者密切相关。如果炉渣发泡过稀,此 时可以使用氮气进行溅渣 ,能有效的控制问题的发 生,进而实现渣量稳定控制。我国首先使用的是
钢工艺实践[J].新疆钢铁,2018(2):26-30.
(编辑:苗运平)
(下转第116页)
・116・
.山酉肖金 E—mail:sxyjbjb@
第44卷
问题根源,实施改进措施。
3结论 1) 棒材劈头堆钢主要由钢坯质量问题引起(偏
析、夹杂)。
2) 钢坯内裂属于铸造缺陷,但与冶炼时成分相关。 3) 冶炼时应避开包晶点,可以有效避免偏析、 内裂。
4) 提高钢中镒硫比例可防治方坯内裂。 5) 轧制过程中,粗轧岗位密切盯钢,尽量及时处 理钢质问题。
6 )年修时,对轧机的轧制线对正,跟换更耐磨的
3、5架导卫衬板。 7)适当调大2、4机架导卫扭转角。
参考文献
[1 ]王凯.降低高线粗轧机轧辐轴承消耗的措施[J] •轧钢,2006,23
安钢100t转炉加入含铁尘泥和渣钢进行冶炼的工艺实践

得到 的含 铁物 质 , 泥球 由转 炉 炼 钢尘 泥 加 粘结 剂 污
制成 , 化铁皮 和 切 割渣 分 别 由连 铸 切 割 和 轧钢 除 氧
磷工 序产 生 。这些 物 质 含 铁 量 比较 高 , 有 的其 它 含 杂质 也是 转炉 炼钢 良好 的造 渣剂 。
表 1 各 种含铁物质的成分 ( 量分数 ) 质 %
a d o e a in pr c s ,t e c ns m p in o t e t ra nd sa sr d e n p rt o e s h o u o t fse lmae i la lg wa e uc d,a d o e ain o n pon o n p r to fe d it
冷镦 钢 、 钢绞 线钢 等 , 年产 钢 10万 吨 。炼 钢 和连铸 3
生 产过 程 中产生 了大 量 的含铁 尘泥 、 连铸 切割 渣 、 渣
钢 等含 铁物 质 , 了减 少这 些含 铁物 的外 排 和污染 , 为 在 10 转 炉 上 进行 了 配加 含铁 尘 泥 和渣 钢 冶 炼 的 0t 生 产试 验 。转炉 加 入 这些 含 铁 物 质 后 , 过 对 现 有 通
c n r la d sa pls i g p oe to si p o e o to n lg s a h n r t cin wa m r v d. Bet rs ca nd e o o c lb n f swe e o ti e t o ila c n mia e e i r b an d. e t K e o ds c n et r e r u o y w r o v re ;f ro s c mpo n ;pr c s p i zng u ds o e so tmii
干法除尘工艺下转炉留渣操作的探索与实践

化学反 应 处于富 氧的气 氛下 ,熔 池 f } 1 的碳无 论是与
气体 氧接触 反应 ,还是与 金属 中溶解 的氧反应 ,生  ̄ g l f ' , j c o气体( 见化学 反应式 ( 3 ) ) 在排 m熔池 前 ,经过 化学反应( 4 ) 后 ,牛成物 以C O , 为主 :
放电, 与 C 0≥9 % ,O ≥6 %1 时, 或 { H , ≥3 %,
F } { 丁初 期 产 生 的CO全 部转 变h  ̄ , c o, .高浓 度
供稿} 张 书欣 ,马 旭 朝 ,张 朝 发 ’ ,宋悦 ,安 海 玉 ,王 生金
s h u x i n , M A Xu — Z h a o }z H Nc
,
,
一 ,t
}
?
S O NG Y u e , A N H a i . y u , WA NG S h e n g - j i n
2 [ C 1 + { O 1 / [ O 1 = 2 { C O} { C 0} + [ 0 ] = { c o ! }
{ CO! } 十 [ C] = 2{ CO}
转 炉炼 钢 过 程 r I l ,炉 内 的铁 水 瓴气 发 ' 1 - 剧 烈 的化学 反应而 成大 } 的高 温炯气 ,伴 随炉 L = I 有
,
謇 留 渣 操 作 就 是 将 炼 钢 转 炉 上 一 炉 所 形 成 的 高 温 、 高 碱 度 、 含 有 一 定 量 F e 。 的 终 渣 全 部 或 部 分 留
导 在 炉 内,可 以显 著降低转 炉 台炼成本。 河钢 唐钢长材部 转炉采 用干 法除尘技 术 ,在投 产的初期 无法
一
部分卒气混 入 ,州 气主 芟成 分为C O、C O, 、O 、
转炉回余钢炼钢工艺开发与应用实践分析
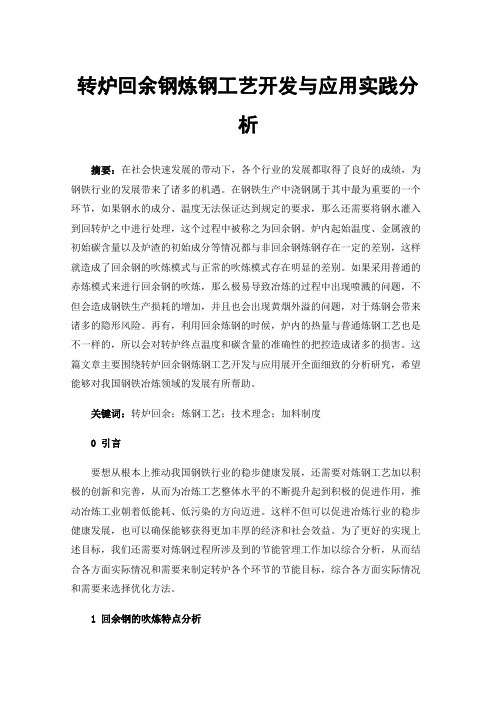
转炉回余钢炼钢工艺开发与应用实践分析摘要:在社会快速发展的带动下,各个行业的发展都取得了良好的成绩,为钢铁行业的发展带来了诸多的机遇。
在钢铁生产中浇钢属于其中最为重要的一个环节,如果钢水的成分、温度无法保证达到规定的要求,那么还需要将钢水灌入到回转炉之中进行处理,这个过程中被称之为回余钢。
炉内起始温度、金属液的初始碳含量以及炉渣的初始成分等情况都与非回余钢炼钢存在一定的差别,这样就造成了回余钢的吹炼模式与正常的吹炼模式存在明显的差别。
如果采用普通的赤炼模式来进行回余钢的吹炼,那么极易导致冶炼的过程中出现喷溅的问题,不但会造成钢铁生产损耗的增加,并且也会出现黄烟外溢的问题,对于炼钢会带来诸多的隐形风险。
再有,利用回余炼钢的时候,炉内的热量与普通炼钢工艺也是不一样的,所以会对转炉终点温度和碳含量的准确性的把控造成诸多的损害。
这篇文章主要围绕转炉回余钢炼钢工艺开发与应用展开全面细致的分析研究,希望能够对我国钢铁冶炼领域的发展有所帮助。
关键词:转炉回余;炼钢工艺;技术理念;加料制度0 引言要想从根本上推动我国钢铁行业的稳步健康发展,还需要对炼钢工艺加以积极的创新和完善,从而为冶炼工艺整体水平的不断提升起到积极的促进作用,推动冶炼工业朝着低能耗、低污染的方向迈进。
这样不但可以促进冶炼行业的稳步健康发展,也可以确保能够获得更加丰厚的经济和社会效益。
为了更好的实现上述目标,我们还需要对炼钢过程所涉及到的节能管理工作加以综合分析,从而结合各方面实际情况和需要来制定转炉各个环节的节能目标,综合各方面实际情况和需要来选择优化方法。
1 回余钢的吹炼特点分析对于回余钢的吹炼各方面情况加以综合分析,并且对回余钢的相关内容进行充实和完善,从而更好的保证实践工作的实施过程中能够将回余钢的实践作用发挥出来,保证钢材材料质量和性能都能够满足实际需要。
1.1 成分波动分析充分的结合钢材的各方面实际情况,对于回余钢所涉及到的各方面内容加以综合分析,因为回余钢的种类差异,所以导致回余钢的成本也会有所不同,并且最终所形成的炉渣的成本也是不一样的。
转炉炼钢中留渣技术的原理及应用分析

转炉炼钢中留渣技术的原理及应用分析发布时间:2021-11-17T02:43:17.083Z 来源:《中国科技人才》2021年第22期作者:郑信彬[导读] 伴随着转炉炼钢技术的不断升级,急需引进新技术强化钢渣回收利用,减少炼钢产生的能耗和污染。
基于此,对转炉炼钢中留渣技术原理展开了分析,并对技术应用要点进行了探究,发现需要通过开展工艺试验合理确定脱磷效率、留渣量等各项参数,确保技术应用取得理想效果。
郑信彬新疆天山钢铁巴州有限公司新疆 841300摘要:伴随着转炉炼钢技术的不断升级,急需引进新技术强化钢渣回收利用,减少炼钢产生的能耗和污染。
基于此,对转炉炼钢中留渣技术原理展开了分析,并对技术应用要点进行了探究,发现需要通过开展工艺试验合理确定脱磷效率、留渣量等各项参数,确保技术应用取得理想效果。
关键词:转炉炼钢;留渣技术;原理分析引言:作为国家重要的基础产业,钢铁工业在发展过程中一直存在资源消耗量多、废弃物排放量大等问题,不利于行业可持续发展。
在国内产钢量中,转炉炼钢占据较大比重,每年需消耗上千万吨石灰石和生白云石,产生的钢渣也数以千万计,造成资源消耗严重的同时,给环境发展带来了不利影响。
引入留渣技术开发新工艺,可以解决上述问题,加速产业转型升级。
1转炉炼钢中留渣技术的原理分析在转炉炼钢期间,钢渣密度比钢水小,将漂浮在钢水之上。
在转炉倾至20~35°时,液面漫过出钢口前钢渣将先流入钢包,出渣量占总体20~30%,属于前期渣[1]。
出钢后,由于钢水产生涡旋,将表面钢渣吸入,产生30%出渣量。
全部钢水倒入后,最后流出的钢水下渣量较大,出渣量达到40~50%,属于终渣,需及时摇起转炉结束出钢。
由于钢渣中含有的磷、硫等元素将给钢材性能带来较大影响,所以需加强下渣量控制,避免过多钢渣进入钢包,减少钢水精炼时间和铁合金加入量,达到提高效率和节约成本的双重目标。
运用留渣技术,需要将上一炉约2/3终渣留在炉内,对铁液加入废钢。
转炉炼钢中留渣技术的原理及应用杨正府

转炉炼钢中留渣技术的原理及应用杨正府发布时间:2021-09-26T07:45:34.951Z 来源:《防护工程》2021年15期作者:杨正府[导读] 转炉留渣法炼钢技术的普及和推广应用,为冶炼技术发展做出了极大的贡献。
在明确技术应用方法和工艺的基础上,做好对技术的创新与完善,将会进一步提升留渣冶炼技术应用价值。
柳钢转炉炼钢厂广西壮族自治区柳州市 545002摘要:转炉留渣法炼钢技术的普及和推广应用,为冶炼技术发展做出了极大的贡献。
在明确技术应用方法和工艺的基础上,做好对技术的创新与完善,将会进一步提升留渣冶炼技术应用价值。
关键词:转炉炼钢;留渣技术;脱磷引言在钢铁行业降本增效大背景下,转炉炼钢留渣法作为一种能够显著降低辅料消耗、降低钢铁料消耗的技术,使得炼钢生产成本得到了切实的控制和降低,并且提升了生产效率。
随着钢铁工业技术日益向精细化发展,转炉留渣法炼钢技术应用效果也越来越明显,更多的炼钢企业和技术人员愿意挖掘这一技术的潜在应用价值,对转炉留渣法炼钢技术进行不断创新和完善,进一步拓展该技术的使用范围。
1 转炉炼钢留渣技术原理转炉留渣法技术原理:将上一炉部分终渣留在炉内,溅渣护炉后,作为下一炉初渣,利用其高温,高碱度,高T.Fe以及含有MgO的碱性渣特点,促进石灰轻烧快速熔化成渣和前期脱磷,从而降低熔剂消耗,降低生产成本。
通过大规模工业试验和对转炉脱磷过程热力学、动力学分析,得到转炉铁水“三脱”预处理各工艺参数和如下主要结论:(1)转炉铁水脱磷效果决定于采用的脱磷工艺,经过工业实践:低碱度高FeO渣脱磷率为55.4%,中高碱度高FeO渣脱磷率为83.4%,中高碱度低FeO渣脱磷率为86.4%。
三种方案相比,中高碱度低FeO渣脱磷效果好、铁损低,应是脱磷工艺的首选方案。
(2)炉渣碱度是提高脱磷率的关键,炉渣碱度增大,脱磷率增加。
(3)在相同炉渣碱度条件下,随脱碳量增加,脱磷率增大;说明炉渣的脱磷能力决定了熔池中C.P平衡关系,在相同熔池C条件下,炉渣碱度越高,与C平衡的P越低。
金属冶炼中的转炉与炉渣处理

烟气治理
采用高效除尘器、脱硫脱硝等设备对 烟气进行处理,减少烟尘和有害气体
的排放。
废水处理
采用物理、化学、生物等方法对废水 进行处理,去除其中的有害物质,达 到排放标准后再进行排放。
炉渣资源化利用
将炉渣进行回收、加工和再利用,减 少固体废弃物的排放,同时实现资源 的循环利用。
05
案例分析:某钢铁企业的转炉与 炉渣处理实践
金属冶炼的发展趋势
高效、节能、环保
随着能源和环境问题的日益突出,金属冶炼行业 正朝着高效、节能、环保的方向发展。
短流程、近终形
为了降低成本和提高生产效率,金属冶炼企业越 来越多地采用短流程、近终形的生产方式。
智能化、自动化
随着工业4.0和智能制造的兴起,金属冶炼行业正 逐步实现智能化、自动化生产。
优点
转炉冶炼具有工艺灵活、适应性强、生产效率高、成本低等优点。同时,通过 合理的工艺控制,可以生产出高质量的钢材。
缺点
转炉冶炼的缺点是会产生大量的废气和废渣,对环境造成一定的污染。同时, 由于高温熔炼过程中需要消耗大量的能源,因此也存在一定的能源消耗问题。
03
炉渣处理在金属冶炼中的重要性
炉渣的形成与分类
形成
炉渣是金属冶炼过程中,矿石、熔剂和燃料中的杂质被氧化后形成的。
分类
根据成分和性质,炉渣可分为酸性渣、碱性渣和中性渣。
炉渣对冶炼过程的影响
降低金属的纯度
炉渣中的杂质会混入金属,降低其纯度。
降低熔融温度
炉渣的加入可以降低熔融物的熔点,有助于 金属的提取。
对设备的腐蚀
高温下,炉渣可能腐蚀转炉和其它冶炼设备 。
干渣技术应用
01
采用干渣技术处理转炉炉渣,实现渣铁分离,提高金属回收率
莱钢60t转炉单渣留渣操作实践

莱钢60t转炉单渣留渣操作实践安全规律,因此一直没有得到大范围推广应用。
但氧气转炉留渣操作能够充分利用前炉钢终点炉渣的热量、碱度和氧化性,大幅降低渣料消耗,在转炉吹炼初期可以快速造就高碱度氧化渣,有利于提高生产效率,并具有显著的经济效益,特别在铁水资源不足的钢厂效益更加突出。
因此各钢厂一直在进行生产试验,以求实现留渣操作的稳定。
留渣操作主要有两方面的危害:一是兑铁时碳氧剧烈反应发生大喷;二是转炉开吹打不着火,转炉烟道内氧气和一氧化碳达到爆炸极限,产生烟道爆炸事故。
1.1兑铁大喷的原因及预防即温度低于1507℃时,铁水和上一炉的炉渣接触,首先是硅的氧化(但也不排除有碳的氧化,因为铁水中含碳量较高),也就限制了碳的激烈氧化。
另外,也可根据不同温度下各种纯氧化物的分解压力找出碳和硅优先氧化的温度。
由氧化物标准生成自由焓的变化与温度的关系可知:SiO2分解壓力曲线与CO分解压力曲线相交的对应温度为1530℃。
当t小于1530℃时,[Si]先于[C]被氧化;当t大于1530℃时则[C]先于[Si]被氧化。
既便是在热力学满足式(3)的情况下,反应也不一定进行或进行的很缓慢而不会造成喷溅,这是由复杂的动力学因素决定的。
上式表明,化学反应速度随温度升高而加快,也就是说温度越高发生喷溅的概率越大。
反之,化学反应速度降低,发生喷溅的概率越小。
从热力学和动力学的分析都可以看出,降低炉渣温度是避免出现兑铁大喷的关键因素,目前转炉大部分实现了溅渣护炉,溅渣后炉渣温度均低于1500℃。
可以说留渣操作的条件已经具备。
同时在溅渣操作时,通过溅干炉渣,防止有液态炉渣,溅渣终点由炉长亲自查看炉渣状态,溅渣时加入一部分石灰等渣料等措施,可以确保兑铁时不出现大喷危害。
1.2 开吹打不着火的原因及预防开吹打不着火主要是由于留渣操作炉渣、加入的废钢带入的渣钢以及铁水带入的铁水渣量大,漂浮在表面,导致氧气流股不能够直接穿透渣层,发生反应。
开吹打火时间超过40s,则前期氧气流股一部分冲击炉渣表面,造成(FeO)聚集,一部分进入烟道内,造成烟道内氧气含量大于2%。
炼钢转炉溅渣护炉技术的应用与实践
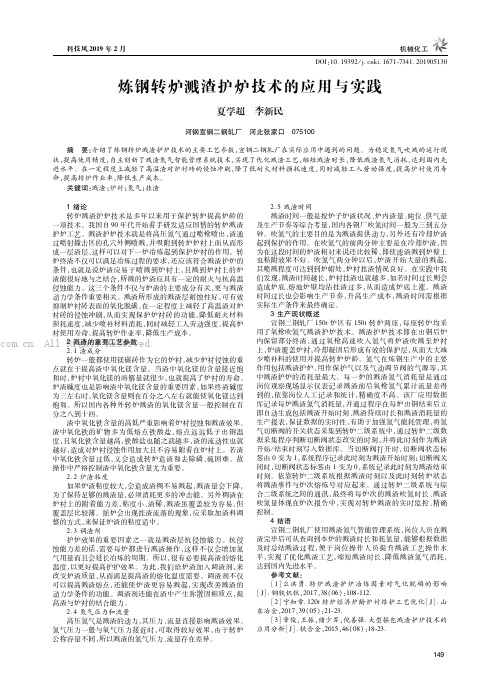
机械化工 DOI:10.19392/j.cnki.16717341.201905130
炼钢转炉溅渣护炉技术的应用与实践
夏学超 李新民ຫໍສະໝຸດ 河钢宣钢二钢轧厂 河北张家口 075100
摘 要:介绍了炼钢转炉溅渣护炉技术的主要工艺参数,宣钢二钢轧厂在实际应用中遇到的问题。为稳定氮气吹溅的运行现 状,提高使用精度,自主创新了溅渣氮气智能管理系统技术,实现了优化溅渣工艺,缩短溅渣时长,降低溅渣氮气消耗,达到国内先 进水平。在一定程度上减轻了高温渣对炉衬砖的侵蚀冲刷,降了低耐火材料损耗速度,同时减轻工人劳动强度,提高炉衬使用寿 命,提高转炉作业率,降低生产成本。
2.5溅渣时间 溅渣时间一般是按炉子炉渣状况、炉内渣量、吨位、供气量 及生产节奏等综合考量,国内各钢厂吹氮时间一般为三到五分 钟。吹氮气的主要目的是为溅渣提供动力,另外还有冷却炉渣 起到保护的作用。在吹氮气的前两分钟主要是在冷却炉渣,因 为在这段时间的炉渣相对来说还比较稀,即使滤渣溅到炉壁上 也粘附效果不 好。吹 氮 气 两 分 钟 以 后,炉 渣 开 始 大 量 的 溅 起, 其喷溅程度可达到到炉帽处,炉衬挂渣情况良好。在实践中我 们发现,溅渣时间越长,炉衬挂渣也就越多,如若时间过长则会 造成炉底、熔池 炉 壁 均 沾 挂 渣 过 多,从 而 造 成 炉 底 上 涨。 溅 渣 时间过长也会影响生产节奏,升高生产成本,溅渣时间需根据 实际生产条件来最终确定。 3生产现状概述 宣钢二钢轧厂 150t炉区有 150t转炉两座,每座转炉均采 用了氧枪吹氮气溅渣护炉技术。溅渣护炉技术即在出钢后炉 内保留部分终 渣,通 过 氧 枪 高 速 吹 入 氮 气 将 炉 渣 吹 溅 至 炉 衬 上,炉渣覆盖炉衬,冷却凝固后形成有效的保护层,从而大大减 少喷补料的使用并提高转炉炉龄。氮气在炼钢生产中的主要 作用包括溅渣护炉、用作保护气以及气动调节阀的气源等,其 中溅渣护炉的消耗量最大。每一炉的溅渣氮气消耗量是通过 岗位观察现场显示仪表记录溅渣前后氧枪氮气累计流量差得 到的,依靠岗位 人 工 记 录 和 统 计,精 确 度 不 高。该 厂 应 用 数 据 库记录每炉溅渣氮气消耗量,并通过程序在每炉出钢结束后立 即自动生成包括溅渣开始时刻、溅渣持续时长和溅渣消耗量的 生产报表,保证数据的实时性,有助于加强氮气能耗管理,将氮 气切断阀的开关状态采集到转炉二级系统中,通过转炉二级数 据采集程序判断切断阀状态改变的时刻,并将此时刻作为溅渣 开始 /结束时刻写入数据库。当切断阀打开时,切断阀状态标 签由 0变为 1,系统程序记录此时刻为溅渣开始时刻;切断阀关 闭时,切断阀状态标签由 1变为 0,系统记录此时刻为溅渣结束 时刻。依靠转炉二级系统根据溅渣时刻以及此时刻转炉状态 将溅渣事件与炉次熔炼号对应起来。通过转炉二级系统与综 合二级系统之间的通讯,最终将每炉次的溅渣吹氮时长、溅渣 吹氮量体现在炉次报告中,实现对转炉溅渣的实时监控、精确 控制。 4结语 宣钢二钢轧厂使用溅渣氮气智能管理系统,岗位人员在溅 渣完毕后可从查询到本炉的溅渣时长和耗氮量,能够根据数据 及时总结溅渣 过 程,便 于 岗 位 操 作 人 员 提 升 溅 渣 工 艺 操 作 水 平,实现了优化溅渣工艺,缩短溅渣时长,降低溅渣氮气消耗, 达到国内先进水平。 参考文献: [1]么洪勇.转炉溅渣护炉冶炼因 素 对 气 化 脱 磷 的 影 响 [J].钢铁钒钛,2017,38(06):108112. [2]宁知常.120t转炉经济炉龄炉衬维护工艺优化[J].山 东冶金,2017,39(05):2123. [3]章俊,王振,储少军,倪善强.大型摇包溅渣护炉技术的 应用分析[J].铁合金,2015,46(08):1823.
一种转炉用生铁块补炉工艺

一种转炉用生铁块补炉工艺
转炉是一种冶炼炉,用于将生铁转化为钢。
补炉是指在转炉冶炼过程中,补充一定比例的生铁块来保持转炉内铁水的炉温和成分稳定。
下面是一种常见的转炉用生铁块补炉工艺。
1. 准备生铁块:选择高质量的生铁块,注意控制成分和温度。
一般情况下,选择含碳量较高的生铁块,由于转炉喷吹氧气的炉墙活塞会对生铁块进行报正,因此补炉时应适当考虑活塞报正的损耗。
2. 给料装置:将准备好的生铁块通过给料装置加入转炉中。
给料装置通常由自动加煤车或者装有提升机的储存斗组成。
这种装置可以确保补炉过程中的连续供料,从而减少炉内的温度和成分波动。
3. 补料方式:在转炉补炉过程中,可以选择不同的补料方式,如全料、分料等。
全料方式是一次性将全部生铁块加入转炉,分料方式是将生铁块分批加入转炉,以保持炉内温度和成分的稳定。
选择补料方式要根据具体情况和操作要求进行。
4. 控制补料速度:补料速度是补炉过程中需要重点控制的参数之一。
补料速度需要根据转炉设备的技术性能和操作要求进行调整。
一般情况下,补料速度应不超过转炉喷吹氧气的强度,以防止转炉内铁水流动不畅或者破块现象发生。
5. 监测温度和成分:在补炉过程中,需要对转炉内的温度和成分进行实时监测。
温度和成分的监测可以通过设备自动控制,
以尽量减少人为误差。
及时调整补料速度和比例,以保持炉内温度和成分的稳定。
综上所述,一种常见的转炉用生铁块补炉工艺包括准备生铁块、给料装置、补料方式、控制补料速度和监测温度和成分等步骤。
这种工艺可以保持转炉内铁水的炉温和成分稳定,提高转炉冶炼的效率和产能。
转炉单渣留渣高效冶炼技术的研究与应用

转炉单渣留渣高效冶炼技术的研究与应用发布时间:2023-04-25T08:58:03.624Z 来源:《科技新时代》2023年1期1月作者:黄耀宁[导读] 在我国全面推进经济建设工作的形势下,钢铁行业之中所运用到的诸多专业技术水平随之不断的提升黄耀宁陕西龙门钢铁有限责任公司,陕西渭南 715405摘要:在我国全面推进经济建设工作的形势下,钢铁行业之中所运用到的诸多专业技术水平随之不断的提升,与此同时诸多资源的被开发利用,再加上钢铁行业正在朝着低成本、低能耗的方向迈进,以往老旧的转炉冶炼模式很显然已经无法满足社会发展的实际需要了,为了更好的推动钢铁行业的持续健康发展,国内外所有的钢铁厂都在转炉冶炼技术的创新方面投入了更多的精力,并且取得了良好的成绩。
关键词:转炉;单渣留渣高效冶炼技术0 引言在我国社会经济水平得到快速发展的带动下,为钢铁行业的发展带来了诸多的机遇。
在这种发展形势下,炼钢企业逐渐的增强了单渣留渣工艺的研究,并且切实地将单渣法与留渣法进行良好的整合,能够有效的提升炼钢工艺的利用效率的提升,并且也可以控制留渣辅料,从而提升资源回收效率,这样就可以实现控制钢材资源成本的目标。
1 快速精准留渣技术转炉留渣数量以及渣中FeO含量情况往往会对过程冷料添加量造成巨大的影响,转炉所采用的单渣留渣工艺所形成的留渣量较少,这样对于前期化渣工作的实施会造成诸多的不利。
而留渣量较多,不但会对冶炼工作的实施带来诸多的困难,并且冶炼的效果也无法保障,后续升温以及脱碳的速度会有所下降[1]。
所以,炼钢厂需要在生产过程中充分的结合生产情况以及单留渣工艺过程化渣的情况来对留渣量加以确定。
针对各方面情况加以综合分析,并且按照留渣量的情况选择适合的方法进行倒渣和留渣,并且结合留渣的黏度情况来调整倒渣摇炉的角度,从而切实地对留渣量加以把控。
2 单渣留渣冶炼工艺自动化技术炼钢厂内所采用的自动炼钢模型属于不留渣普通自动炼钢模型,因为之前模型的计算没有对留渣工艺运用所产生的留渣中的FeO对氧平衡参数的影响以及留渣量对热平衡参数影响进行综合分析。
转炉补炉方法
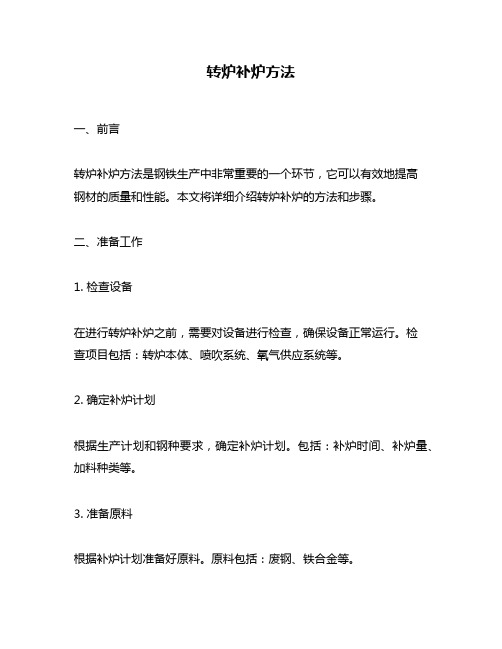
转炉补炉方法一、前言转炉补炉方法是钢铁生产中非常重要的一个环节,它可以有效地提高钢材的质量和性能。
本文将详细介绍转炉补炉的方法和步骤。
二、准备工作1. 检查设备在进行转炉补炉之前,需要对设备进行检查,确保设备正常运行。
检查项目包括:转炉本体、喷吹系统、氧气供应系统等。
2. 确定补炉计划根据生产计划和钢种要求,确定补炉计划。
包括:补炉时间、补炉量、加料种类等。
3. 准备原料根据补炉计划准备好原料。
原料包括:废钢、铁合金等。
三、转炉补炉步骤1. 推出残余钢水在进行转炉补炉之前,需要先将残余钢水推出。
具体步骤如下:(1)停止喷吹氧气。
(2)将废渣推到一侧,并清理出口处。
(3)打开出口门,将残余钢水推出。
2. 加入原料在推出残余钢水之后,需要加入原料。
具体步骤如下:(1)将铁合金、废钢等原料按照计划加入转炉中。
(2)启动喷吹氧气,进入补炉阶段。
3. 调整操作参数在进行转炉补炉的过程中,需要根据实际情况调整操作参数。
主要包括:(1)氧气流量:根据钢种要求和喷吹效果调整氧气流量。
(2)温度控制:通过监测温度曲线,调整喷吹氧气的位置和流量,控制转炉内部温度。
4. 检查钢液质量在进行转炉补炉之后,需要对钢液质量进行检查。
具体步骤如下:(1)取样:在钢液进入包浆前取样,并送往实验室检测。
(2)分析结果:根据分析结果调整操作参数,确保钢液质量符合要求。
5. 出钢当补炉结束后,需要将钢水出口门打开,将精炼好的钢水倒入包浆车中。
同时关闭喷吹系统和出口门。
四、注意事项1. 安全第一在进行转炉补炉的过程中,需要严格遵守安全操作规程,确保人员和设备的安全。
2. 喷吹氧气要均匀喷吹氧气要均匀,避免出现“打喷嚏”等现象。
3. 控制温度控制温度是转炉补炉过程中非常重要的一个环节。
需要根据实际情况调整操作参数,确保温度控制在合理范围内。
4. 检查钢液质量钢液质量对最终产品的质量和性能有着非常重要的影响。
在进行转炉补炉之后,需要对钢液质量进行检查,并根据检查结果调整操作参数。
转炉补炉方法

转炉补炉方法概述转炉补炉是指在转炉炼钢过程中,为了达到预定的钢种成分和温度要求,对转炉进行加热和处理的操作。
补炉的目的是通过加入适当的炉料和调整炉内的工艺参数,使炉内的钢水成分得到调整、达到要求,并保持炉渣中的氧、硅、锰的含量稳定,以确保钢水质量的稳定和一致。
本文将详细介绍转炉补炉方法的流程、原理和控制参数等方面内容。
转炉补炉方法流程转炉补炉的一般流程如下:1.准备工作:包括炉前布料、调整燃烧系统、检查设备及炉前状况等。
2.炉料装入:将预先配制好的炉料加入到转炉中,包括生铁、废钢、喷吹剂等。
3.吹吸:启动转炉的风机系统,将炉料中的杂质氧化吹出,并同时控制转炉底吸气系统,将炉渣中的杂质吸除。
4.调温冶炼:根据操作要求和钢种要求,调整转炉的燃烧系统,控制转炉内的温度。
5.化验分析:定期进行炉内钢水成分的化验分析,以控制炉料的投放和燃烧系统的调整。
6.补料补剂:根据化验分析结果和操作要求,适时向转炉中加入补料和补剂,用于调整钢水成分和温度。
7.出钢:根据转炉内的炉料消耗情况和达到要求的钢水成分,决定合适的出钢操作。
8.清理转炉:待转炉内钢水出完后,清理炉渣、准备下一炉的操作。
转炉补炉方法原理转炉补炉的原理主要涉及以下几个方面:1. 炉料控制通过控制炉料的投入量和配比,可以改变转炉内的钢水成分。
生铁、废钢等炉料的加入量和种类选择将直接影响到钢水的成分和质量。
2. 炉渣控制炉渣是转炉炼钢过程中产生的副产物,它不仅对炉膛的保护和温度控制起到重要作用,还对钢水的成分和温度有一定的影响。
通过调整炉渣的组成和温度,可以对炉内的钢水质量进行调控。
3. 气体控制转炉炼钢中的氧气和废气排放等气体对炉内的化学反应起到至关重要的作用。
通过控制转炉废气和进气的流量、温度和氧含量等参数,可以实现钢水成分和温度的精确控制。
4. 温度控制转炉补炉过程中,准确控制转炉内的温度是非常重要的。
通过调整炉膛的氧气和燃料的供给量,控制炉内的燃烧反应,实现温度的精确控制和调整。
- 1、下载文档前请自行甄别文档内容的完整性,平台不提供额外的编辑、内容补充、找答案等附加服务。
- 2、"仅部分预览"的文档,不可在线预览部分如存在完整性等问题,可反馈申请退款(可完整预览的文档不适用该条件!)。
- 3、如文档侵犯您的权益,请联系客服反馈,我们会尽快为您处理(人工客服工作时间:9:00-18:30)。
作用。控制合适的炉渣成分,使出钢后炉渣中高熔 点矿物,快速冷却凝固在渣面炉衬部位,从而起到耐 火材料的作用。这个过程主要是利用炉渣与炉衬界 面存在的温度差,通过矿物间相互扩散,同类矿物重 结晶,如2CaO・Si02,MgO,3CaO・Si02等,使炉渣 与炉衬成为一个整体达到补炉的效果,减缓炉衬砖 的侵蚀速度,从而提高转炉的炉龄。 利用生铁块将转炉渣快速冻结在需要垫补的部 位,由于生铁块与炉渣的粘合性,使垫补的部位在摇 炉过程中多次挂渣;在加料过程中生铁块与铁水发 生化学反应,在炉衬表面生成一层高熔点的矿物质。 转炉快速补炉是在补炉的前几炉,确认转炉渣 面需要垫补的部位后,补炉的前一炉做好炉渣,达到 补炉的炉渣要求。出钢后直接加入干燥的生铁块, 再把转炉摇到一定角度,炉渣和生铁块流动到需要 修补的位置静置4 rain后,使炉渣和生铁块的反应 产物凝结在炉衬上,再将转炉摇正溅渣完成补炉。
目前3座50 t转炉按高铁水耗冶炼,装入量为 55∥炉,按49 t铁水、6 t废钢配比;炼钢要完成日产
75
万方数据
总第216期
≥138炉,每班单座炉要平均冶炼≥16炉钢(冶炼时 间为(27±1)rain)。根据现有的转炉炉况及冶炼模 式,每班生产炉数必须≥46炉钢的生产计划,就可 以达到铁水进出平衡的关系。以上计算不含设备检 修、炉况维护和成分异常停炉停机的事故。 提高转炉作业率、降低耐材消耗是转炉生产的 一项重要指标,也反映了炼钢厂的操作水平和综合 管理水平。炼钢厂通过控制炉渣成分、碱度等参数, 摸索出适合转炉挂渣补炉技术的炉渣MgO含量、碱 度和冷却时间等参数;利用生铁块与炉渣的粘合性, 加入1.8 t生铁块后使炉渣冷凝粘护炉技术的应用, 转炉需要垫补的部位在摇炉过程中多次挂渣,并利 用加料过程中生铁块与铁水的冲击作用,达到护炉 的目的。转炉挂渣补炉技术的应用,使炼钢耐材消 耗大幅度下降,解决了护炉与生产之间的矛盾。
3
气的消耗,在装料期和冶炼中期也适当加入一定数 量的废钢。装料时炉体要倾动到一定角度,用料斗 先向炉内加入废钢,然后兑人铁水。因此,炉衬要受 到炉料以及自重等静载荷的作用,遇到因加入废钢、 兑入铁水时产生的动载荷冲击、冲刷与机械磨损,从 而会造成炉衬受损。
4
渣补护炉的原理 炉渣能够熔损炉衬,同时又能起到耐火材料的
总第216期
2013年第12期
HEBEl
河北冶金
METALLURGY
Toral No.216 2013,Number 12
转炉“生铁块渣补"应用实践
雷浩洪 (福建三安钢铁有限公司炼钢厂,福建泉州362411) 摘要:在转炉生产中,提高炉衬的使用寿命对提高生产率、炉龄、钢产量、钢水质量及降低耐火材料消耗、 增加经济效益有重要意义。分析了影响转炉炉衬寿命的主要因素,利用生铁块渣补技术解决了兑铁水、 加废钢对炉衬的冲刷及机械磨损,减少了炉料的使用量和停炉的补炉时间,解决了生产与护炉之间的矛 盾。该技术的应用,使转炉炉况明显好转、炉龄由11 000炉提高到15 000炉,耐材消耗降低30%,为炼 钢进一步提升产能和经济技术指标开辟了一条新路。 关键词:转炉;生铁块渣补法;应用 中图分类号:TFT02
万方数据
万方数据
线倒灌站、1座600 t混铁炉、3座50 t氧气顶底复吹 转炉(装入量55 t,炉产量为51 t,冶炼周期平均为
27
min/炉)、R7m弧160
mm
x
160
mm四机四流连
铸机3台,主要冶炼钢种有HRB系列和普碳钢,平 均出钢温度1645
2.1铁水量情况
1 050
oC。
m3高炉铁水量≥3350 t/天,2座550
(Steelworks,Vujian
Abstract:In
increase tion converter
Sanan Iron and
production,prolonging
the
productivity,steel output,prolong the furnace life,improve molten steel quality,reduce consump・ materials and increase economic profit.The main factors to affect the lining life
250
m3
高炉,铁水量共≥3
7 100
t/天;日出铁量在6
t。
600~
t,平均值为6
800
收稿日期:2013—09—26
2.2转炉冶炼情况
作者简介:雷浩洪(1972一),男,高级工程师,2007年毕业于北京科 技大学冶金工程专业,现在福建三安钢铁有限公司炼钢厂工作,E—
mail:1hh200836@126.com
furnace life increases from 1 1 000 to 1 5 000 heats,the consump—
refractory materials reduces by 30%.
converter with pig iron plus slag;application
Key
Words:converter;fettling
5
影响转炉炉衬寿命的因素 (1)兑入铁水、加入废钢时,对炉衬的冲刷及机
械磨损。 (2)冶炼过程中,钢水、炉渣以及炉气对炉衬的 机械冲刷。 (3)炉渣、炉气对炉衬的化学侵蚀。 (4)在兑人铁水、停吹、出钢以及装料时,炉内 温度变化使炉衬砖受损。 加强炉体维护是延长炉衬寿命的重要措施,要 合理选择炉衬耐材,提高冶炼操作水平,重视炉体维 护。根据炉衬损坏的程度及部位,可采用不同的护 炉、补炉方法:溅渣护炉、渣补、热补、湿法喷补、干法 喷补等方法。 氧气转炉炼钢的金属料主要是铁水,占转炉金 属料的70%左右。为了降低铁水量、造渣材料和氧
表1
Tab.1
渣补护炉的操作步骤及要点 (1)提前通知操作工,控制碱度在3.0以上和
5.1操作步骤
渣中MgO含量在9%以上,提高炉渣的粘性见表1。
终渣的化学成分
%
%
Chemical composition of end slag
(2)垫补用的生铁块要求干燥、干净,防止补炉 时引起安全事故和外来杂物影响补炉效果。 (3)补炉炉次要保证钢水出完,炉渣要避免高 氧化性,确保补炉效果。 (4)补炉时生铁块用量控制在1.8 t左右(需过 磅),补炉部位控制在钢水熔池上方,防止吹炼过程 生铁熔化影响钢水终点成分。 (5)放人生铁块后,立刻将炉子摇平(930左右)
文献标识码:B
文章编号:1006—5008(2013)12—0075—03
APPI,ICA.I'ION
SLAG PLUS PIG
OF‘‘FETTI,ⅨG WrrH
IRON"TECHNIQUE IN CONVERTER
Lei Haohong Steel Co.,Ltd.,Quanzhou,Fujian,3624 1 1) work life of furnace lining is of important significance to
or
scrap,reduces charge amount and fettling
time,solves the contradiction between production and furnace protection.With the technique the converter
condition gets obviously well and well,the tion of
ale aria—
of refractory
lyzed.The technique of fettling with pig iron plus slag is introduced.This method solves the problem of
scour
and
mechanical wear of lining caused by adding hot metal
76
ቤተ መጻሕፍቲ ባይዱ
停留约3 min进行溅渣护炉操作,进行下炉冶炼。 (6)渣补第一炉要化好渣,不“返干”,过程温度 控制合适,出钢后做好溅渣护炉工作。 (7)生铁块渣补炉次,在安全防范方面与渣面 大补同等重视,执行相关安全操作规定,后续炉次出 钢时,炉口前方不得有人通行。
5.2要点
(1)生铁快速补炉仅用于补渣面钢水液面以上
1
前言 “生铁块渣补法”是在转炉出完钢后,将事先准
降低了吨钢生产成本。
2
实际生产条件 福建三钢炼钢厂年产粗钢225万t,现有2座在
备好的生铁块(1.8 t左右)倒入转炉内渣面受损的 部位,将转炉立刻摇平短暂停留3~4 min,摇起转炉 进行溅渣操作后将余渣倒净再进行下一炉冶炼。为 稳定炉前生产节奏、减少炉前补炉时间、为后续大生 产作准备,福建三钢炼钢厂立足自身实际,勇于学习 创新,为减少兑入铁水、加入废钢时对炉衬的冲刷及 机械磨损,大胆采用转炉补炉新技术“生铁块渣补 法”,改变炉前补炉作业方式,有效提高了转炉炉 龄,降低了职工的劳动强度,延长了转炉作业时间,