机械加工工艺与装备
机械制造工艺与装备

H R Y B
图3-6 导轨扭曲引起的加工误差
H H 2 1 。 一般卧式车床 ,外圆磨床 B B 3
d、导轨与主轴回转轴线的平行度
理论上要求车刀刀尖的直线运动轨迹与主轴回转轴线在水
平面内和垂直面内都应相互平行,但实际上存在误差: 在水平面内不平行:两者处于同一平面,即为相交两直线, 这使工件产生锥度; 在垂直方向不平行:两者不在同一平面,即为空间交叉两 直线。该项误差与导轨在垂直面内的直线度误差上相似的,均 处于误差非敏感方向,故对工件的加工精度影响很小。
1、工艺系统的几何误差对加工精度的影响
工艺系统的几何误差主要是机床、刀具和夹具的制造误差、磨损 误差以及调整误差。这一类原始误差在刀具与工件发生关系(切削)之 前就已客观存在,在加工过程中反映到工件上去。
(1)机床几何误差
高精度的零件要依赖高精度的设备与工艺装备来生产,其中最重 要的是机床的精度。机床精度可以分为:①静态精度,机床在非切削 状态(无切削力作用)下的精度;②动态精度,机床在切削状态和振 动状态下的精度;③热态精度,机床在温度场变化情况下的精度。
(2)工艺系统受力变形引起的加工误差
在切削过程中,刀具相对于工件的位置是不断变化的,所以切削 力的大小及作用点的位置总是变化的,因而,工艺系统的受力变形也 随之变化。 1)切削力大小变化引起的加工误差——误差复映规律工件在切削 过程中,由于被加工表面的几何误差及材料硬度不均,引起切削力和 工艺系统变形的变化,如图3-7所示
1切削力大小变化引起的加工误差误差复映规律工件在切削过程中由于被加工表面的几何误差及材料硬度不均引起切削力和工艺系统变形的变化如图37所示2工艺系统受力变形引起的加工误差图37毛坯误差的复映切削过程中受力点位置变化引起的工件形状误差2切削力作用点位置变化引起的加工误差图38受力点变化引起的变形在工艺系统中由于零部件的自重也会产生变形
机械加工工艺及装备
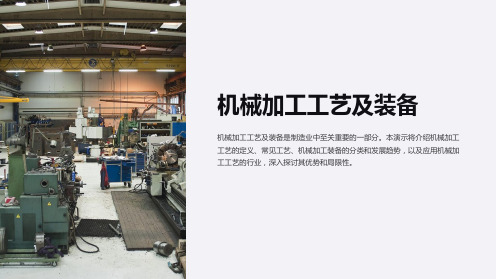
1 机械制造业
生产各类机械设备和零部 件的行业,如汽车制造、 航空航天等。
2 金属加工行业
加工金属材料的行业,如 钢铁、铝制品、工程机械 等。
3 电子制造业
生产电子器件和电路板的 行业,如手机、电脑、电 视等。
机械加工工艺的优势和局限性
优势
提供高精度的加工能力,批量生产效率高,适用于 各种材料。
局限性
常见的机械加工工艺
1 铣削
通过旋转刀具切削工件表面,用于加工各种 平面和曲线形状。
2 钻削
利用旋转的钻头在工件表面形成孔洞,常用 于钻孔和制作螺纹。
3 磨削
利用磨削磨料对工件表面进行切削和磨光, 提高工件的表面质量。
4 锯割
通过旋转锯片对工件进行切割,常用于金属 和木材的切割。
机械加工装备的分类
机械加工工艺及装备
机械加工工艺及装备是制造业中至关重要的一部分。本演示将介绍机械加工 工艺的定义、常见工艺、机械加工装备的分类和发展趋势,以及应用机械加 工工艺的行业,深入探讨其优势和局限性。
机械加工工艺的定义
1 什么是机械加工工艺?
机械加工工艺是通过机械装备对工件进行形状和尺寸上的变化,以达到所需的工艺要求。
工艺复杂、成本较高,对操作人员的技术要求较高。
结论及展望
机械加工工艺及装备在现代制造业中扮演着重要角色,随着技术的不断进步, 机械加工工艺将进一步实现自动化和智能化,并提供更高的加工精度和效率。
传统机床
如铣床、钻床、磨床等,通过人工操作进行加工。
数控机床
利用计算机控制系统进行加工,提高加工精度和效率。
机械加工工艺的发展趋势
1
自动化和智能化
采用机器人、自动化设备和智能化技术,提高生产效率和产品质量。
机械加工工艺规程及工艺装备

机械加工工艺规程及工艺装备1. 引言机械加工是一种广泛应用于制造业的加工方法,通过对工件进行加工,改变其形状、尺寸和表面质量,从而得到满足特定要求的产品。
为了保证机械加工的质量和效率,在加工过程中需要遵循一系列的工艺规程,并使用相应的工艺装备。
本文将介绍机械加工工艺规程的重要性以及常用的机械加工工艺装备。
2. 机械加工工艺规程2.1 工艺规程的定义工艺规程是指在进行机械加工时,根据加工对象的材料、形状、尺寸和加工要求,制定出一系列的加工步骤、加工参数和加工工具的规定,以达到预期的加工效果和质量要求。
2.2 工艺规程的重要性工艺规程在机械加工中起着至关重要的作用,其重要性体现在以下几个方面:- 提高加工效率:工艺规程明确了加工步骤和加工参数,使得加工操作更加有序,减少了加工中的不必要的时间浪费。
- 保证加工质量:工艺规程规定了合适的加工方法和加工工具,能够保证加工过程中不会对工件造成质量损害,提高加工精度。
- 降低成本:工艺规程设计合理,能够选择适当的加工工具和材料,减少废品率和修理率,降低生产成本。
-确定加工难度:工艺规程通过对加工方法、材料和装备的选择,能够准确地评估加工难度,并采取相应的措施来解决加工中可能遇到的问题。
2.3 工艺规程的制定过程制定工艺规程需要经过以下几个步骤: 1. 分析加工对象:对于待加工的工件,需要进行形状、尺寸、材料等方面的分析,了解其特点和加工要求。
2. 选择加工方法:根据工件的情况,选择合适的加工方法,例如车削、铣削、磨削等。
3. 确定加工顺序:根据加工方法的特点和工件的形状,确定不同加工步骤的顺序,保证加工顺利进行。
4. 确定加工参数:根据工件的材料和要求,确定适当的切削速度、进给量和切削深度等加工参数。
5. 选择加工工具:根据工艺规程,选择适当的加工工具,如车刀、铣刀、磨料砂轮等。
6. 编写工艺规程:将以上信息整理并编写成工艺规程,包括加工步骤、加工参数和加工工具等。
机械加工工艺装备
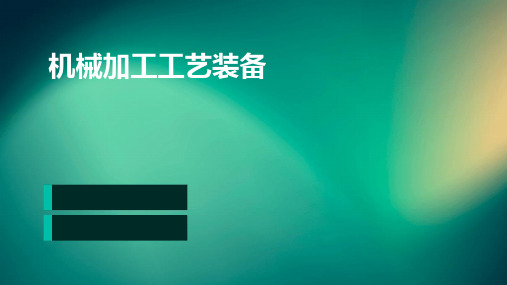
VS
增材制造技术
增材制造技术如3D打印等,将为机械加 工工艺装备带来新的制造方式。这种技术 能够快速、灵活地制造出复杂形状的零件 ,降低制造成本和提高生产效率。
绿色制造的推广
节能减排技术
随着环保意识的提高,节能减排技术 将在机械加工工艺装备中得到广泛应 用。通过采用高效节能技术和环保排 放技术,降低装备运行过程中的能耗 和排放,实现绿色制造。
循环利用技术
循环利用技术是绿色制造的重要组成 部分。通过采用再制造、再生利用等 技术,对机械加工工艺装备进行修复、 再利用,延长装备使用寿命,减少资 源浪费。
THANKS FOR WATCHING
感谢您的观看
促进技术创新
工艺装备的发展和应用是 推动机械制造业技术创新 的重要手段,能够促进产 业升级和转型。
机械加工工艺装备的发展历程
古代机械加工工艺装备
现代机械加工工艺装备
以手工工具为主,如铁锤、锯、刨等, 主要用于简单的金属加工。
随着计算机技术和智能制造的发展, 数控机床、智能夹具等高精度、高效 率的工艺装备成为主流。
磨削加工
总结词
磨削加工是一种高精度的加工方法,通过磨具对工件进行磨削,实现工件表面 的超精加工。
详细描述
磨削加工过程中,磨具的高速旋转产生切削力,对工件表面进行磨削,使工件 表面达到极高的精度和光洁度。常见的磨削加工有平面磨削、外圆磨削和内圆 磨削等。
特种加工
总结词
特种加工是一种新兴的加工方法,通过物理或化学方法实现工件材料的去除或变 形,具有非传统加工的特点。
刀具种类繁多,根据不同的加工需求可分 为通用刀具和专用刀具,还可按材料、切 削方式等进行分类。
刀具的切削参数
刀具的材料
机械切削加工工艺与装备
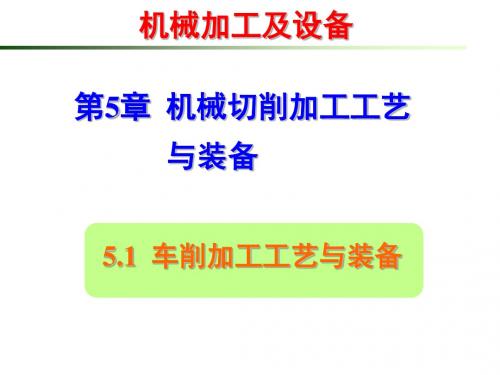
v
丝锥
工件
图5-14 攻丝
5.1.1 车削加工的概念及可加工的表面
车削可加工的表面
车内螺纹 车削时工件作旋转运动(主运动v ),工件每转一转 螺纹车刀轴向进给一个螺距(进给运动 f )。
工件
v f
车刀
图5-15 车内螺纹
5.1.1 车削加工的概念及可加工的表面
车削可加工的表面
滚花 车削时工件作旋转运动(主运动v ),滚刀沿径向或 轴向进给(进给运动 f ),以实现对外圆面的滚花。
② 用钻套导向; ③ 提高刃磨精度,使两主切削刃对称。
5.2.1 钻孔工艺及装备
钻孔的工艺特点
(2) 排屑困难;
容屑槽尺寸有限,钻屑较宽,被迫卷成螺旋状,流出 孔壁时与孔壁发生剧烈摩擦。影响钻进,降低工件表 面质量。 改进措施:
① 钻深孔时,反复退刀排屑; ② 修磨分屑槽。
(3) 切削热不易传散。
立式车床
图5-21 单立柱立式车床
5.1.2 车床的分类及结构组成
车床的分类
立式车床
图5-22 双立柱立式车床
5.1.2 车床的分类及结构组成
车床的分类
落地车床 落地车床又称花盘车床、端面车床、大头车床,主要适 用于车削直径大,长度短、重量较轻的盘形、环形工件或薄 壁筒形等工件。 落地车床广泛应 用于石油化工、重型 机械、汽车制造、矿 山铁路设备及航空部 件的加工制造。
机夹外切槽刀
焊接内切槽刀 机夹内切槽刀
图5-34 切槽刀
5.1.4 工件在车床上的装夹
三爪卡盘装夹
图5-35 三爪卡盘装夹
优点:自定心卡盘装夹工件方便、省时。 缺点:夹紧力没有单动卡盘大。 适用于:圆柱、套、盘类等圆形零件。
机械加工工艺装备组成
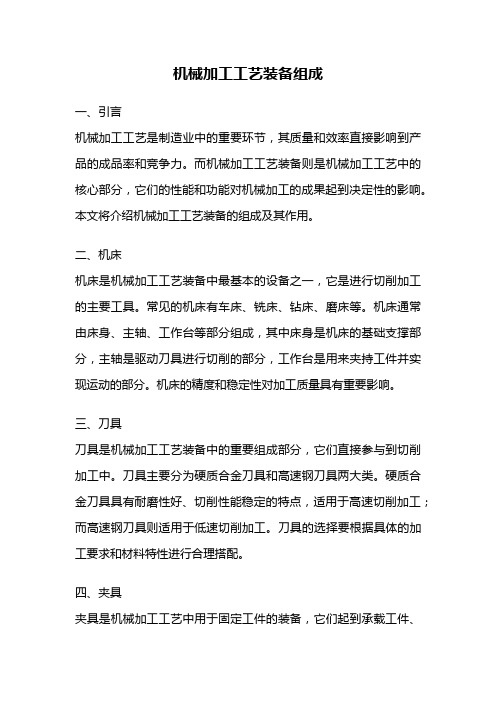
机械加工工艺装备组成一、引言机械加工工艺是制造业中的重要环节,其质量和效率直接影响到产品的成品率和竞争力。
而机械加工工艺装备则是机械加工工艺中的核心部分,它们的性能和功能对机械加工的成果起到决定性的影响。
本文将介绍机械加工工艺装备的组成及其作用。
二、机床机床是机械加工工艺装备中最基本的设备之一,它是进行切削加工的主要工具。
常见的机床有车床、铣床、钻床、磨床等。
机床通常由床身、主轴、工作台等部分组成,其中床身是机床的基础支撑部分,主轴是驱动刀具进行切削的部分,工作台是用来夹持工件并实现运动的部分。
机床的精度和稳定性对加工质量具有重要影响。
三、刀具刀具是机械加工工艺装备中的重要组成部分,它们直接参与到切削加工中。
刀具主要分为硬质合金刀具和高速钢刀具两大类。
硬质合金刀具具有耐磨性好、切削性能稳定的特点,适用于高速切削加工;而高速钢刀具则适用于低速切削加工。
刀具的选择要根据具体的加工要求和材料特性进行合理搭配。
四、夹具夹具是机械加工工艺中用于固定工件的装备,它们起到承载工件、保持工件位置和实现工件与刀具之间相对运动的作用。
夹具的种类繁多,常见的有平口夹具、钳工夹具、分度头等。
不同的夹具适用于不同的加工需求,夹具的质量和精度直接关系到加工件的定位和加工精度。
五、测量设备测量设备是机械加工工艺中的重要组成部分,它们用于检测加工件的尺寸和形状精度,以确保加工质量的合格。
常见的测量设备有千分尺、游标卡尺、外径千分尺、内径千分尺等。
测量设备的准确性和稳定性对于加工件的质量控制至关重要。
六、辅助设备辅助设备是机械加工工艺中的补充装备,它们用于提高加工效率和保证加工的顺利进行。
常见的辅助设备有切削液供给系统、冷却系统、排屑装置、自动送料装置等。
这些设备能够减少切削热量、清除切削废料、提高加工速度,从而提高加工效率和降低生产成本。
七、数控系统数控系统是机械加工工艺中的关键技术之一,它能够实现机床的自动化操作和高精度加工。
机械加工工艺及装备课件

半精加工工艺
完善形状和尺寸
半精加工的主要目的是进一步 完善工件的形状和尺寸,使其
接近最终要求。
选择合适的刀具
根据工件的材料和形状,选择 合适的刀具进行半精加工。
切削速度和进给量
在半精加工过程中,通常采用 较小的切削速度和进给量以提 高加工质量。
切削液的使用
使用切削液可以降低切削温度 ,减少刀具磨损,提高加工质
06
案例分析与实践操作
案例一:某零件的机械加工工艺流程优化
总结词
工艺流程优化、降低制造成本、提高生产效率
详细描述
针对某零件的机械加工工艺流程进行了优化改进,包括调整工艺顺序、减少工装数量、采用高效刀具等措施,有 效降低了制造成本和提高了生产效率。
案例二:某企业数控机床的选型与使用
总结词
数控机床选型原则、设备利用率 、生产效益
随着人工智能和物联网技术的发展,智能化和自动化装备在机械加工领域的应用越来越广泛,如智能机器人、自动化 生产线等,提高了生产效率和产品质量。
绿色环保装备的应用
随着环保意识的提高,绿色环保装备在机械加工领域的应用越来越广泛,如节能型数控机床、环保型冷 却液等,降低了环境污染和能源消耗。
机械加工工艺及装备面临的挑战与解决方案
机械加工工艺及装备课件
目录
• 机械加工工艺概述 • 机械加工工艺流程 • 机械加工装备 • 机械加工工艺及装备的应用 • 机械加工工艺及装备的发展趋势与挑战 • 案例分析与实践操作
01
机械加工工艺概述
机械加工工艺的基本概念
机械加工工艺是将原材料通过机械设备和工具,经过多道工序加工成零件或产品的 过程。
03
机械加工装备
金属切削需求,金属切削 机床可分为卧式、立式、 斜式等。
机械加工工艺规程与工艺装备设计
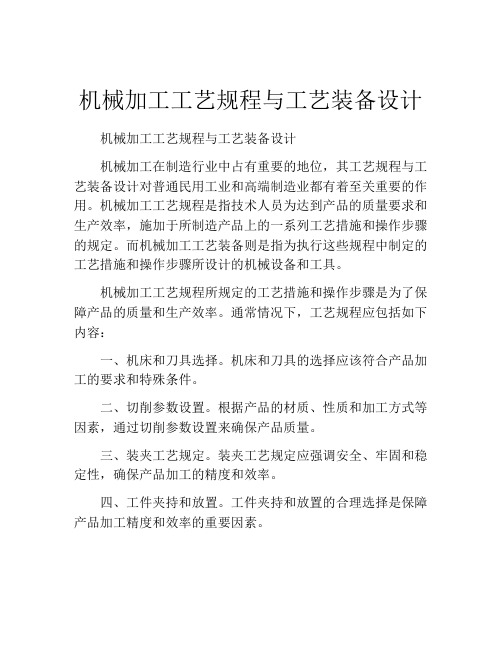
机械加工工艺规程与工艺装备设计机械加工工艺规程与工艺装备设计机械加工在制造行业中占有重要的地位,其工艺规程与工艺装备设计对普通民用工业和高端制造业都有着至关重要的作用。
机械加工工艺规程是指技术人员为达到产品的质量要求和生产效率,施加于所制造产品上的一系列工艺措施和操作步骤的规定。
而机械加工工艺装备则是指为执行这些规程中制定的工艺措施和操作步骤所设计的机械设备和工具。
机械加工工艺规程所规定的工艺措施和操作步骤是为了保障产品的质量和生产效率。
通常情况下,工艺规程应包括如下内容:一、机床和刀具选择。
机床和刀具的选择应该符合产品加工的要求和特殊条件。
二、切削参数设置。
根据产品的材质、性质和加工方式等因素,通过切削参数设置来确保产品质量。
三、装夹工艺规定。
装夹工艺规定应强调安全、牢固和稳定性,确保产品加工的精度和效率。
四、工件夹持和放置。
工件夹持和放置的合理选择是保障产品加工精度和效率的重要因素。
五、加工工艺步骤。
根据机加工工艺全过程,制定合理的加工顺序,避免出现重复加工等不必要的步骤,提高生产效率。
以上是机械加工工艺规程中的主要内容。
而为了执行这些规程中制定的工艺措施和操作步骤,需要有相应的机械加工工艺装备来实现。
机械加工工艺装备的设计,应基于以下两大原则:一、针对特定加工工件和加工工艺流程,设计专门的加工设备,使其在加工过程中可以高效地保证产品的质量和生产效率。
二、优化机械加工工艺装备的设计,追求设备的高效、节能、环保和安全性等特点,同时降低生产成本,提高经济效益。
机械加工工艺装备的设计,包括以下三个方面的内容:一、机械加工工艺装备的结构设计。
要求机械加工工艺装备的外形美观,具有良好的气密性和两性功能。
二、机械加工工艺装备的强度计算和筛选。
通过对加工强度、刚度、耐磨性、韧性等方面进行计算和筛选,达到提高机械加工工艺装备的耐用性和稳定性的目的。
三、机械加工工艺装备的电气、液压、气动等系统的设计。
应该考虑到机械加工工艺装备电气、液压、气动等系统的配备情况,在设计方案中必须与整机部件相协调,以确保各自系统协同操作。
机械制造技术基础

机械制造技术基础一、引言机械制造技术是指将原材料通过一系列的加工、转换和组装工艺,生产成符合人们需求的商品的工艺和方法。
机械制造技术的发展与机械工业的发展密切相关,它是现代工业化生产的基础和支撑。
机械制造技术基础是机械制造技术的核心内容,包括机械加工工艺与装备、材料工程以及机械设计等方面。
本文将对机械制造技术基础进行详细介绍。
二、机械加工工艺与装备2.1 机械加工工艺机械加工工艺是指将原材料进行加工和整形的过程。
常见的机械加工工艺包括车削、铣削、钻削、磨削等。
机械加工工艺的选择根据工件的材料、形状和加工要求来确定。
机械加工工艺主要包括以下几个方面:•车削:通过旋转刀具在工件上切削,使工件呈现旋转对称形状。
车削可分为外圆车削和内孔车削两种类型。
•铣削:利用分布在多刃刀具上的切削齿,在工件表面上切削出各种形状的凹凸面。
•钻削:通过旋转钻头在工件表面上切削出圆孔。
•磨削:利用砂轮与工件表面的相对运动,将工件表面切削到所要求的尺寸和表面粗糙度。
2.2 机械加工装备机械加工装备是进行机械加工工艺的主要设备。
随着科技的不断发展,机械加工装备也在不断更新和升级。
目前常见的机械加工装备包括:•数控机床:通过计算机控制系统实现工件的加工,具有高精度、高效率和高自动化程度的特点。
•传统机床:包括车床、铣床、钻床等,是一种经典的机械加工装备,适用于小批量生产。
•加工中心:综合了铣削、钻削、攻丝等多种功能于一体,具有高效率和高精度的特点。
•磨床:用于对工件进行磨削加工,可实现高精度和高表面质量的加工。
•切割设备:包括激光切割机、等离子切割机等,可用于对板材进行切割加工。
三、材料工程机械制造技术中的材料工程主要研究材料的选择、加工和性能等方面。
合理选择和使用材料是保证机械产品质量和性能的关键因素。
材料工程主要包括以下内容:•材料的分类和性能:材料根据其性能和用途的不同可分为金属材料、非金属材料和高分子材料等。
了解材料的性能和特点,有助于选择合适的材料。
机械制造工艺与装备课程设计指导书
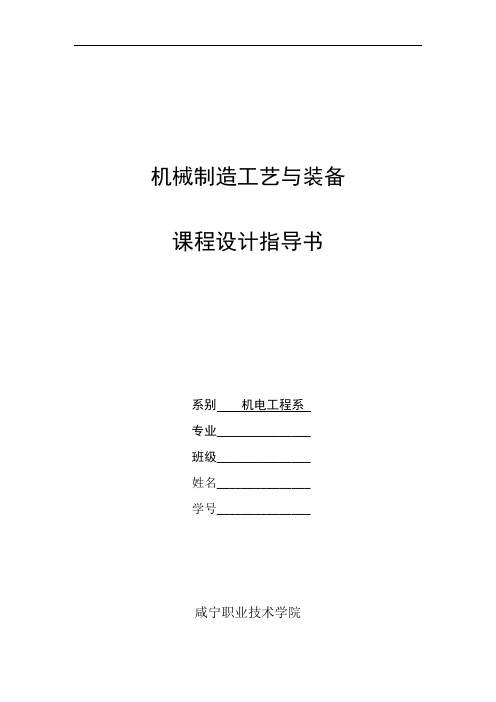
机械制造工艺与装备课程设计指导书系别机电工程系专业_______________班级_______________姓名_______________学号_______________咸宁职业技术学院机械制造工艺课程设计任务书姓名________专业__________班级_________学号__________设计题目:ZDⅢ41—4G型锥形电动机机轴加工工艺规程原始数据:材料40Cr、毛坯:圆钢Φ55,其余数据见附图设计工作量:设计说明书一份、机械加工工艺过程卡片一份(附表一)、机械加工工序卡片一套(附表二)指导教师:________________开始日期:________________完成日期: ___________概述机械制造工艺学是以机械加工工艺技术为主的技术科学,是实践性较强的一门学科,又是机械制造工程类专业的一门主修课。
所以,在完成了系统理论教学和实践教学后,学生还要通过课程设计和毕业设计进行理论联系实际的综合训练,并达到下列目的;(1)掌握编制机械加工工艺规程的原则、步骤和方法,并具有编制中等复杂程度零件机械加工工艺规程的能力。
(2)学会查阅与机械加工工艺设计相关的手册,资料,并能运用公式,表格等正确确定工艺参数和有关数据。
(3)能将所学的基础课、理论课和专业课知识应用于生产实际。
(4)培养学生分析和解决工艺问题的独立工作能力。
(5)了解现代制造技术的前沿及计算机辅助工艺规程设计(CAPP)。
第一节机械制造工艺设计基本知识1-1机械制造工艺设计要求及工作顺序一、设计内容机械制造工艺设计题目一般为:给出某零件的生产纲领及生产条件,编制某零件的机械加工工艺规程。
具体设计内容要求如下:1、分析并绘制零件工作图。
2、确定毛坯种类、余量、形状,并绘制毛坯——零件综合图。
3、拟定零件的机械加工工艺路线。
4、合理选择各工序的定位基准。
5、确定各工序的夹紧位置和夹紧力作用方向。
6、确定各加工表面的工序余量,工序尺寸及公差.7、确定各工序加工所用的装备.8、确定各工序的切削用量。
机械加工工艺装备夹具课件
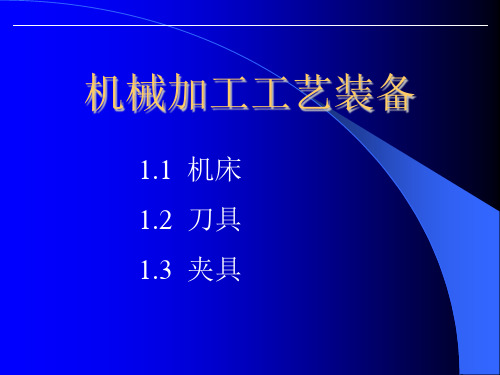
F = FJ tan(φ2+α)
斜角α=10°~14° 一般摩擦系数f=0.1~0.15 摩擦角φ≈5°45′~8°32′ 图1.96 斜楔夹紧受力分析
◆斜楔的自锁条件
F1 ≥ F F1 =FJ tanφ1 F = FJ'tan(α-φ2)
FJ = FJ'
tanφ1≥tan(α-φ2)
φ1 = φ2 = φ, α≤2φ
电动夹具 磁力夹具 真空夹具
1.3.1 机床夹具概述
●机床夹具的组成
①定位元件 —确定工件的正确位置 ②夹紧装置 —夹牢工件,保证工件正确位置不变 ③对刀及导向装置 —迅速确定刀具与工件的相对位置 ④夹具体 —夹具的基础件 ⑤其他装置或元件 —分度装置、联接元件等
1.3.2 工件的定位
基准及其分类
1.3.2 工件的定位
1、工件定位的方式
(1)直接找正定位—精度取决于工人技术水平 单件小批生产,位置要求高
a)磨内孔时工件的找正 b)刨槽时工件的找正
图 1.60 直接找正定位
(2)划线找正定位—精度低 单件小批,复杂件,毛坯精度低
图1.61 划线找正定位
(3)夹具定位—生产率高,定位精度高成批及大量生产
①明确设计任务,收集设计资料
②拟订夹具结构 —定位方案;夹紧方案;刀具引导方式; 方案,绘制夹具 其他装置;总体结构及安装方式 草图
③绘制夹具总图 —工作位置为主视图
双点划线画工件(余量网纹表示) 画定位→夹紧→导向件→夹具体 标注总图技术要求 绘制夹具零件图
●夹具总图技术要求的标注
①轮廓尺寸 —L×H×B ②定位技术要求 —定位件与工件配合,定位件间要求 ③对刀技术要求 —对刀件与刀具配合,对刀件间要求 ④机床连接要求 —与机床联结尺寸、配合 ⑤夹具制造技术要求
第三章常用机械加工方法及其装备
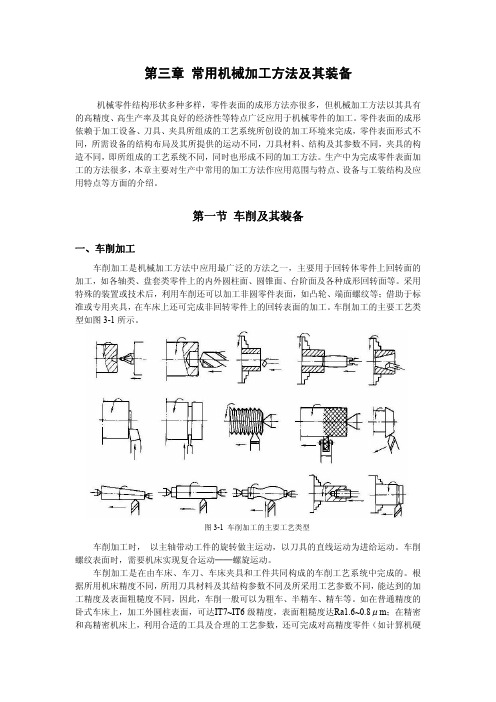
第三章 常用机械加工方法及其装备机械零件结构形状多种多样,零件表面的成形方法亦很多,但机械加工方法以其具有的高精度、高生产率及其良好的经济性等特点广泛应用于机械零件的加工。
零件表面的成形依赖于加工设备、刀具、夹具所组成的工艺系统所创设的加工环境来完成,零件表面形式不同,所需设备的结构布局及其所提供的运动不同,刀具材料、结构及其参数不同,夹具的构造不同,即所组成的工艺系统不同,同时也形成不同的加工方法。
生产中为完成零件表面加工的方法很多,本章主要对生产中常用的加工方法作应用范围与特点、设备与工装结构及应用特点等方面的介绍。
第一节 车削及其装备一、车削加工车削加工是机械加工方法中应用最广泛的方法之一,主要用于回转体零件上回转面的加工,如各轴类、盘套类零件上的内外圆柱面、圆锥面、台阶面及各种成形回转面等。
采用特殊的装置或技术后,利用车削还可以加工非圆零件表面,如凸轮、端面螺纹等;借助于标准或专用夹具,在车床上还可完成非回转零件上的回转表面的加工。
车削加工的主要工艺类型如图3-1所示。
图3-1 车削加工的主要工艺类型车削加工时,以主轴带动工件的旋转做主运动,以刀具的直线运动为进给运动。
车削螺纹表面时,需要机床实现复合运动──螺旋运动。
车削加工是在由车床、车刀、车床夹具和工件共同构成的车削工艺系统中完成的。
根据所用机床精度不同,所用刀具材料及其结构参数不同及所采用工艺参数不同,能达到的加工精度及表面粗糙度不同,因此,车削一般可以为粗车、半精车、精车等。
如在普通精度的卧式车床上,加工外圆柱表面,可达IT7~IT6级精度,表面粗糙度达Ra1.6~0.8μm;在精密和高精密机床上,利用合适的工具及合理的工艺参数,还可完成对高精度零件(如计算机硬盘的盘基)的超精加工。
二、车床车床是完成车削加工必备的加工设备。
它为车削加工提供特定的位置(刀具、工件相对位置)环境及所需运动及动力。
由于大多数机械零件上都具有回转面,加之机床较广的通用性,所以,车床的应用极为广泛,在金属切削机床中占有比重最大,约为机床总数的20%~35%。
机械工艺技术与工装设计及应用

机械工艺技术与工装设计及应用摘要:在开展新的机械工程时,前期的工装设计和工艺技术选用非常重要。
如果对于工艺设备和实践作业设计预期生产目标不符时,就会造成后期机械工程加工工序絮乱,引发机械部件损坏或者其他安全故障问题。
为了提高我国的机械工程工艺应用质量,除了引进新工艺和新设备以外,在专业人员的实际操作过程中应当结合科学的工装设计,满足实际的工程作业要求。
关键词:机械工艺技术;工装设计;应用1.机械加工工艺技术概念机械加工与工装设计是机械专业的必修课程之一,具有非常强的实践性质。
由于自身的范围广泛和实用性,成为我国工业发展的基石。
在机械工艺日新月异的更替之下,为了不断的推动机械领域的可持续性发展,在更新机械加工技术的同时应当在传统的加工方式上,引用新的设备和工艺,结合初期的工装设计图纸,结合先进的加工管理流程,更好的满足初期工装设计的基础要求。
2.工装设计常用理念分析2.1 定位分析在实际的工装设计过程中,相关人应当做好定位分析,选择仪器夹具时,如果要避免加工部位在定位期间不出现误差,就必须将实际的定位数据进行详细的计算。
在此过程中定位加工部件,如果出现误差,只要在范围内仍可继续进行加工工序作业。
在一般的加工过程中采用支撑杆和定位销进行辅助定位,使其结果能够更加准确,减少误差的产生。
在明确加工中三个支撑板限定规格时,零部件的支撑需要在两侧的支撑板就连那有出两个以上的自由度空间,使定位能够更加准确,保障整体加工的精度。
在避免由于误差引起了加工故障的同时,提升整体机械工程的质量。
2.2 夹紧力工装设计过程中,对于零部件的使用,要求装备产生的夹紧力能够满足制作加工的工件牢固要求,使其能够稳固的固定在支架上。
相关人员应当设置好其他辅助装备,使部件和夹紧方向一致,减少由于加工过程影响出现的变形现象发生。
另外在实际的加工期间,由于避免不了一些外在影响因素和客观因素影响,例如物理重力和和一些其他切削力影响作用下,及时的调整二者之间的方向,使其能够保持在同一水平线。
机械加工工艺与设备第一章

1.1 机械产品生产过程简介
1.1.6 入库
企业生产的成品、半成品及各种物料为防止遗失或损坏,放入仓库进 行保管,称为入库。 入库时应进行入库检验,填好检验记录及有关原始记录;在储存时注 意做好防锈,防潮处理,保证货物的安全;对量具、仪器及各种工具 做好保养、保管工作;对有关技术标准、图纸、档案等资料要妥善保 管;保持工作场地整洁、通风,注意防火、防湿,做好防盗安全工作。
1.2 机械制造工艺基础
1.2.4 制定工艺规程
3.制定工艺规程的步骤 (1)计算年生产纲领,确定生产类型。 (2)分析零件图及产品装配图,对零件进行工艺分析,形成拟定工艺规 程的总体思路。 (3)确定毛坯的制造方法。 (4)拟定工艺路线,选择定位基准,划定加工阶段。 (5)确定各工序所用的设备及刀具、夹具、量具和辅助工具。 (6)确定各工序的加工余量,计算工序尺寸及公差。 (7)确定各工序切削用量及工时定额。 (8)确定各主要工序的技术要求及检验方法。 (9)编制工艺文件。
1.1 机械产品生产过程简介
1.1.4 检验
检验是指采用测量器具对原材料、毛坯、零件、成品等进行尺寸 精度、形状精度、位置精度的检测,以及通过目视检验、无损探 伤、力学性能试验及金相检验等方法对产品质量进行的鉴定。 常用的量具有钢直尺、卷尺、游标卡尺、卡规、塞规、千分尺、 角度尺以及百分表等,用以检测零件的长度、厚度、角度、外圆 直径以及孔径等。另外,螺纹的测量可用螺纹千分尺、螺纹样板、 螺纹环规和螺纹塞规等进行。 常用量仪有浮标式气动量仪、电子式量仪、电动式量仪、光学量 仪以及三坐标测量仪等,除可用以检测零件的长度、厚度、外圆 直径、孔径等尺寸外,还可对零件的形状误差和位置误差等进行 测量。 特殊检验主要是指检测零件内部及外表的缺陷。其中无损探伤是 在不损害被检验对象的前提下,检测零件内部及外表缺陷的现代 检验技术。
机械制造工艺装备简介

机械制造工艺装备简介1. 背景介绍机械制造工艺装备是指在机械制造过程中所使用的各种设备和工具,包括加工设备、检测仪器、工装夹具等。
它们是实现机械加工、组装和质量控制的重要工具,对于提高生产效率、产品质量和制造精度起到关键作用。
本文将对机械制造工艺装备进行简要介绍。
2. 加工设备加工设备是机械制造过程中最常用的工艺装备之一。
它们可以根据加工方法的不同分为数控机床、普通机床、特种机床等。
下面将对几种常见的加工设备进行简单介绍。
2.1 数控机床数控机床是使用计算机数字控制系统来控制机床运动和加工过程的高精度设备。
它们可以实现复杂形状的加工,提高加工效率和精度。
数控机床的主要类型包括铣床、车床、钻床等。
2.2 普通机床普通机床是指非数控机床,主要由人工操作完成。
它们在机械制造领域仍然广泛使用,特别是在小批量生产和维修加工中。
普通机床包括铣床、车床、钻床、磨床等。
2.3 特种机床特种机床是根据特定加工要求设计的机床,用于加工特殊形状的工件或特殊材料。
例如,螺纹磨床、齿轮加工机床、镗床等。
检测仪器在机械制造中用于检测加工件的尺寸、形状和表面质量。
它们可以帮助制造商及时发现问题并采取措施,确保产品质量。
以下是几种常见的检测仪器。
3.1 三坐标测量机三坐标测量机是一种高精度的测量仪器,用于测量复杂形状的工件。
它可以实现多点测量、三维重构和曲面拟合等功能。
3.2 光学投影仪光学投影仪是一种利用光学投影原理来测量工件尺寸的设备。
它可以通过放大工件的影像来进行测量,并且可以实现多点、多线、多圆等形状的测量。
示波器是用于测量电信号的设备,可以用于检测电路中的信号变化和故障。
在机械制造中,示波器通常用于检测机械设备中的传感器信号。
4. 工装夹具工装夹具是用于固定工件或加工工具的装置,用于确保加工过程的稳定性和精度。
不同类型的工装夹具适用于不同的加工需求。
以下是常见的几种工装夹具。
4.1 夹具夹具是用于固定工件的装置,可以使工件保持在正确的位置和姿态。
- 1、下载文档前请自行甄别文档内容的完整性,平台不提供额外的编辑、内容补充、找答案等附加服务。
- 2、"仅部分预览"的文档,不可在线预览部分如存在完整性等问题,可反馈申请退款(可完整预览的文档不适用该条件!)。
- 3、如文档侵犯您的权益,请联系客服反馈,我们会尽快为您处理(人工客服工作时间:9:00-18:30)。
数 控 车 削 的 工 艺 分 析
单位名称 工序号 工 安 步 装 号 1 2 1 1 2 3 4 5 6 3 1
××× 程序编号
产品名称或代号
零件名称 使用设备
加工中心
零件图号
×××
夹具名称 工步内容
车间
备 注
用三爪卡盘夹紧工件一端,加工右端至φ 64×38柱面。 用三爪卡盘夹紧工件φ 64一端,车端面、打中心孔。 用三爪卡盘夹紧工件φ 64一端,另一端用顶尖顶住。加工φ 64×62.02柱面 钻螺纹底孔 精车φ 20表面 加工14°锥面 攻螺纹 加工SR19.4圆弧面、φ 26圆柱面、角15°锥面和角15°倒锥面,装夹方式如图 所示。加工过程如下: l)先用复合循环若干次一层层加工,逐渐靠近由E—F—C—H—I等基点组成的 回转面。后两次循环的走刀路线都与B—C一D—E—F—C—H—I—B相似。完成 粗加工后,精加工的走刀路线是B—C—D—E—F—G—H—I一B,如图所示。 2)再加工出最后一个15°的倒锥面。
习题6
11、加工轴类零件,毛坯为Φ85×340棒材,零 件材料为45钢,无热处理和硬度要求,图中 Φ85mm外圆不加工。对该零件进行精加工。根 据图纸要求和毛坯情况,分析该零件数控车削工 艺。(小批量生产)
(1)分析零件图样
对图所示的零件进行精加工,图中
Φ85mm外圆不加工。该零件包括 圆柱、圆锥、凹圆弧及螺纹表面。 零件材料为45钢,毛坯为 Φ85mm×340mm棒材。
4
5 6 7 8
T04
T05 T06 T07 T08
1
1 1 1 1
镗孔及镗内孔锥面
镗孔 切 5mm 宽 螺 纹 退 刀槽 车内螺纹及螺纹孔 倒角 自右至左车外表面
0.4
0.4 0.3 0.2
9
编制
T09
93°左手偏刀
审核
1
自左至右车外表面
批准
0.2
共1页 第1页
数控加工工序卡片
(单位名称) 工序号 数控加工工序卡片 程序编号 产品名称或代号 数控车工艺分析实例 夹具编号 刀具 规格 / mm 25×25 φ4 零件名称 锥孔螺母套 使用设备 CJK6240 进给速度 /(mm· -1) min 背吃 刀量 /mm 1 2 15.75 40 0.2 0.1 40 40 0.8 0.2 1 材料 45钢 零件图号 车间 数控中心 备注 手动 手动 手动 自动 手动 自动 自动 手动 自动 40 25 0.5 0.1 自动 自动 手动 手动 0.4 0.1 30 30 0.2 0.2 共1页 自动 自动 自动 自动 第1页
外轮廓车削走刀路线
4、刀具选择
①车削端面选用45°硬质合金端面车刀; ②φ4中心钻,钻中心孔以利于钻削底孔时刀具找正; ③φ31.5高速钢钻头,钻内孔底孔; ④粗镗内孔选用内孔镗刀; ⑤内孔精加工选用φ32铰刀; ⑥螺纹退刀槽加工选用5mm内槽车刀; ⑦内螺纹切削选用60°内螺纹车刀; ⑧选用93°硬质合金右偏刀,副偏角选35°,自右到 左车削外圆表面; ⑨选用93°硬质合金左偏刀,副偏角选35°,自左到 右车削外圆表面; 将所选定的刀具参数填入数控加工刀具卡片中,以便 于编程和操作管理。
毛坯尺寸为φ66mm×100 mm。
经过分析可制定加工方案如下: 1:用三爪卡盘夹紧工件一端,加 工φ64×38柱面 2:用三爪卡盘夹紧工件φ64 一端,车端面、打中心孔。 用 顶 尖 顶 住 。 加 工 φ24×62 柱面,如图所示。 3:①钻螺纹底孔;②精车 φ20 表 面 , 加 工 14°锥面; ③攻螺纹,如图所示。
硬质合金螺纹车刀 1 审核
××× 批准
(6)轴的数控加工工序卡片
单位名称 工序号 ××× 程序编号
产品名称或代号
××× 夹具名称
零件名称
轴2 使用设备
零件图号
××× 车间
001
×××
三爪卡盘
刀具 规格 / mm
CK0630
主轴 转速 / r.min1
数控中心
背吃刀 量 / mm
工步号
工步内容
刀具号
5.确定切削用量
根据被加工表面质量要求、刀具材料和工 件材料,参考切削用量手册或有关资料选取切 削速度与每转进给量,然后根据公式计算主轴 转速与进给速度(计算过程略),计算结果填 入工序卡中。 背吃刀量的选择因粗、精加工而有所不同。 粗加工时,在工艺系统刚性和机床功率允许的 情况下,尽可能取较大的背吃刀量,以减少进 给次数;精加工时,为保证零件表面粗糙度要 求,背吃刀量一般取0.1~0.4mm较为合适。
粗车外圆至尺寸φ71mm光轴
掉头车另一端面,保证长度尺寸76mm
粗镗螺纹底孔至尺寸φ34mm
精镗螺纹底孔至尺寸φ34.2mm
切5mm内孔退刀槽
φ34.2mm孔边倒角2×45°
粗车内孔螺纹
精车内孔螺纹至M36×2-7H (装心轴)自右至左车外表面 (装心轴)自左至右车外表面
审核
习题14(P185)如图是模具芯轴的零件简图。
(5)选择刀具
产品名称或代 ××× 号
序号 刀பைடு நூலகம்号 刀具规格名称
零件名称 典型轴
数 量 加工表面
零件图 ×× 号 ×
备注 刀尖 半径/mm
1 2 3 编制
T01 T02 T03
硬质合金外圆车刀 1 硬质合金切槽刀 1
外轮廓面加工
(作图法确定刀具的副偏 角)
切3mm×Φ 45mm的槽 车M48×1.5螺纹 ××× 共 页 第页
2、确定装夹方案
内孔加工时以外圆定位,用三爪自动定心卡盘 夹紧。加工外轮廓时,为保证同轴度要求和便于装 夹,以坯件左端面和轴心线为定位基准,为此需要 设计一心轴装置,用三爪卡盘夹持心轴左端,心轴 右端留有中心孔并用尾座顶尖顶紧以提高工艺系统 的刚性。
外轮廓车削心轴定位装夹方案
3、确定加工顺序及走刀路线
1 2 3 数控车 工艺分 析实例
零件 名称
锥孔螺 母套 数 量
1 1 1
零件 图号
加工表面 车端面 钻φ4mm中心孔 钻孔
程序编号
刀尖 半径 /mm 0.5 备注
刀具 号
T01 T02 T03
刀具规格名称 45°硬质合金端面车刀 φ4中心钻 φ31.5mm的钻头 镗刀 φ32mm的镗刀 内槽车刀 内螺纹车刀 93°右手偏刀
零件的径向尺寸公差为±0.01mm,角度公差 为±0.1°,材料为45钢。小批量生产。试分 析其数控加工工艺。
典型数控车削零件的工艺分析
一、轴类零件的数控车削工艺
数 控 车 削 的 工 艺 分 析
图示是模具芯轴的零件简图。零件的径向尺寸 公差为±0.01mm,角度公差为±0.1°,材料为45 钢。
习题12:如图所示为锥孔螺母套零件,零件材料为45 钢,介绍数控车削加工工艺。小批量生产,编制零件 数控车削加工工艺。
螺母套零件图
1、零件工艺分析
该零件表面由内外圆柱面、圆锥面、顺圆弧、逆 圆弧及内螺纹等表面组成,其中多个直径尺寸与 轴向尺寸有较高的尺寸精度、表面粗糙度和形位 公差要求。零件图尺寸标注完整,符合数控加工 尺寸标注要求;轮廓描述清楚完整;零件材料为 45钢,切削加工性能较好,无热处理和硬度要求。 通过上述分析,采取以下几点工艺措施。 ① 左右端面均为多个尺寸的设计基准,相应工序 加工前,应该先将左右端面车出来。 ② 内孔圆锥面加工完后,需掉头再加工内螺纹。
进给速 度 / (mm· -1) r
备 注
1 2 3
编制
从右至左车各面 切3mm×Φ 45mm的槽 车M48×1.5螺纹
×× ×
审核
T01 T02 T03
批准
20×20 20×20 20×20
×××
630 315 200
年 月
0.15 0.16 1.5
日 共 页
×× ×
第 页
轴套类零件数控车削加工工艺
工步 号 1 2 3 4
工步内容
刀具号 T01 T02 T03 T04
主轴 转速 /(r/min) 320 950 200 320 32 320 320 320 320 320 320 320 320 320 320 320 320
5
6 7 8 9 10 11 12 13 14 15 16 17 编制
(2)选择设备
根据被加工零件的外形和材
料等条件,选定CK7815型 数控车床。
(3)确定零件的定位基准和装夹方式
以Φ85mm外圆 及右中心孔为工艺基准。 2)装夹方法 采用三爪自定心 卡盘自定心夹紧。
1)定位基准
(4)制定加工方案
首先根据图纸要求按先主后次的加工原则,确定工 艺路线 1)以Φ85mm外圆及右中心孔为工艺基准,用三爪 自定心卡盘夹持Φ85mm外圆,用机床尾座顶尖顶 住右中心孔。 2)工步顺序: ①自右向左进行外轮廓面加工:倒角—切削螺纹外 圆—切削锥面—车Φ62mm外圆—倒角—车Φ80mm 外圆—车R70mm圆弧—车Φ80mm外圆; ②切3mm×Φ45mm的槽; ③车M48×1.5螺纹。
加工顺序的确定按由内到外、由粗到精、先近 后远的原则确定,在一次装夹中尽可能加工出较 多的工件表面。结合本零件的结构特征,可先粗、 精加工内孔各表面,然后粗、精加工外轮廓表面。 由于该零件为单件小批量生产,走刀路线设计不 必考虑最短进给路线或最短空行程路线,外轮廓 表面车削走刀路线可沿零件轮廓顺序进行。
6、填写工艺文件
(1)按加工顺序将各工步的加工内容、所 用刀具及切削用量等填入数控加工工序卡 片中。
(2)将选定的各工步所用刀具的刀具型号、 刀片型号、刀片牌号及刀尖圆弧半径等填 人数控加工刀具卡片中。 (3)将各工步的进给路线绘成文件形式的 进给路线图。
数控加工刀具卡片