线束生产工艺流程
汽车线束工艺流程

汽车线束工艺流程汽车线束是汽车电气系统的重要组成部分,其功能是将各种电气设备连接在一起,完成信号和电力的传输。
汽车线束工艺流程是指汽车线束从设计到生产的全过程,下面将详细介绍汽车线束工艺流程。
1. 汽车线束设计:设计人员根据车辆的具体需求,确定线束的布局和连接方式。
设计人员需要考虑到各种电器设备的位置、电线的电流负荷、电磁兼容性和防护等因素,以确保线束的可靠性和安全性。
同时,设计人员还需要选择合适的电线、连接器和保护套管等材料。
2. 线束生产准备:生产线束前,需要准备好所需的材料和设备。
这包括电线、连接器、绝缘带、绝缘套管、钳子、剥线机、压接机等。
同时,还需要制定生产计划和工艺文件,确保生产过程的顺利进行。
3. 制作线束:制作线束的第一步是剥皮。
工人使用剥线机将电线的一段外皮剥除,露出内部的导线。
然后,根据设计要求,工人将不同颜色和规格的电线按照一定的顺序编织在绝缘带上。
编织完成后,使用压接机将电线固定在连接器上。
4. 线束组装:将各个连接器上的电线根据设计要求组装在一起,形成线束。
工人需要根据线束的布局和连接方式,将电线从一端引入连接器,并通过卡扣或螺丝固定。
在组装过程中,需要注意电线的位置和排列顺序,以免出现接线错误或短路等问题。
5. 线束测试:组装完成后,需要对线束进行测试,确保其质量和性能达到要求。
测试内容包括电阻测量、绝缘测量和耐电压测试等。
通过测试,可以排除线束中存在的故障和缺陷,并及时修复或更换。
6. 线束包装:测试合格的线束将被包装并存放在指定的仓库中,待装配到汽车上。
包装过程中需注意线束的保护,防止受潮、破损或变形等。
7. 线束安装:线束安装是将线束装配到汽车上的过程。
装配人员根据汽车的布局和连接方式,将线束引入到相应的位置,并固定在车身的固定点上。
在安装过程中,需要仔细对照线束的设计图纸,确保连接正确、牢固和整洁。
8. 线束检验:安装完成后,需要对线束进行检验,确保其安装质量和可靠性。
线束工艺流程
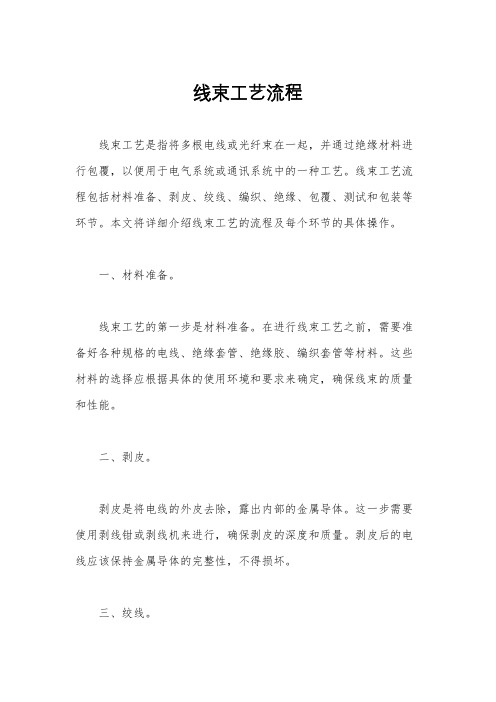
线束工艺流程线束工艺是指将多根电线或光纤束在一起,并通过绝缘材料进行包覆,以便用于电气系统或通讯系统中的一种工艺。
线束工艺流程包括材料准备、剥皮、绞线、编织、绝缘、包覆、测试和包装等环节。
本文将详细介绍线束工艺的流程及每个环节的具体操作。
一、材料准备。
线束工艺的第一步是材料准备。
在进行线束工艺之前,需要准备好各种规格的电线、绝缘套管、绝缘胶、编织套管等材料。
这些材料的选择应根据具体的使用环境和要求来确定,确保线束的质量和性能。
二、剥皮。
剥皮是将电线的外皮去除,露出内部的金属导体。
这一步需要使用剥线钳或剥线机来进行,确保剥皮的深度和质量。
剥皮后的电线应该保持金属导体的完整性,不得损坏。
三、绞线。
绞线是将多根电线按照一定的规则进行捆绑和绞合,使其成为一个整体。
这一步需要根据具体的线束设计要求进行操作,确保电线之间的布局合理、紧凑,并且不会相互干扰。
四、编织。
编织是将绞好的电线进行编织,以增强线束的抗拉强度和耐磨性。
编织材料可以是尼龙布、聚酯布等,根据具体的使用要求来选择。
编织后的线束应该外观整齐、紧密,不得有松散或交叉现象。
五、绝缘。
绝缘是为了保护线束中的电线不受外界环境的影响,使用绝缘套管或绝缘胶对电线进行包覆。
绝缘材料的选择应根据使用环境的温度、湿度等因素来确定,确保绝缘效果良好。
六、包覆。
包覆是将整个线束进行最终的包覆,通常使用PVC套管或热缩套管进行包覆。
包覆后的线束应该外观整洁、无气泡、无皱纹,确保线束的外观质量。
七、测试。
测试是对线束进行电学和机械性能的检测,确保线束的质量和性能达到要求。
电学测试包括导通测试、绝缘电阻测试等,机械性能测试包括拉力测试、耐磨测试等。
八、包装。
最后一步是将测试合格的线束进行包装,通常使用塑料袋或纸箱进行包装。
包装后的线束应该标明产品型号、规格、生产日期等信息,确保产品的追溯和售后服务。
以上就是线束工艺的流程及每个环节的具体操作。
通过严格的工艺流程和质量控制,可以生产出质量可靠的线束产品,满足不同领域的使用需求。
线束生产工艺流程 ppt课件

图5, 不 合格压 接,绝缘 包筒刺 破线皮
9
端子外观检验
图4, 不合格压接,导体没有完全压 入导体包筒内
图5, 不合格,料带太 长
图6, 不合格, 料带不
可见,端子切伤
ppt课件
图7, 合 格, 热缩 套管完 全包住 导体
图8 不合 格 热缩 套管包的 太长
10
端子外观检验 合格
ppt课件
11
4.剥皮尺寸参考算法(如下图):
ppt课件
4
露出导体 导体铆压栅长度 可见导体和绝缘体
导体铆压栅长度
剥线长度
a 被覆铆压栅
可见导体 剥线长度
剥皮尺寸=导体铆压栅长度 +1/2a +0.5mm(线规: 0.3mm2 以下) 剥皮尺寸=导体铆压栅长度 +1mm (线规:0.3—1mm2 ) 剥皮尺寸=导体铆压栅长度 +2mm (最大线规:10mm2 )
开式端子
导体铆压栅 喇叭口 被覆铆压栅
嵌合部
卡口片
挤压沟
ppt课件
料带
8
端子外观检验
图1, 标准压接,外 皮处于导体包筒 和绝缘包筒之间
图2, 合格压接,外皮 刚好与导体包筒或 绝缘包筒平齐
图3, 不合格压接,外皮压入导体 包筒或绝缘包筒内
图4, 不 合格压 接,导 体伸入 到功能 区内
ppt课件
18
在铆压拉力和高度保证的前提下,理想的铆端状态:
1. 视窗 1 能看见导体又能看到绝缘体(外被)
2. 视窗 2 芯线(导体)露出长度0.5~1.5mm(具体依端子大小而定)
3. 嵌合部不可变形,卡口片不可变形
4. 芯线铆压栅、被覆固定栅中间沟槽不可有间隙,不可两边带毛刺
线束加工工艺流程
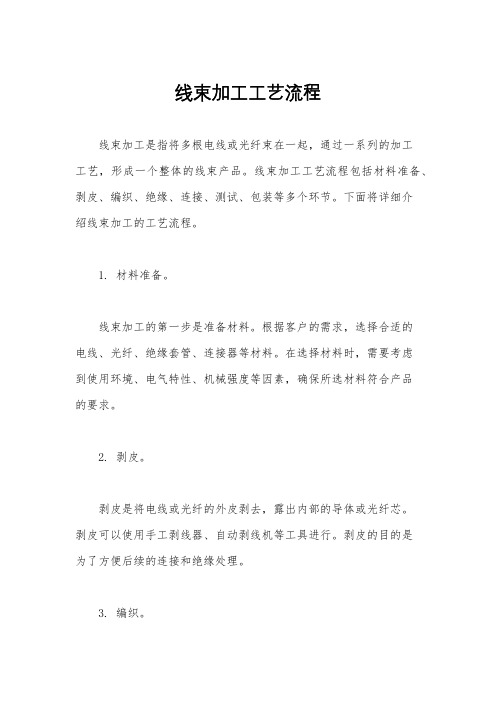
线束加工工艺流程线束加工是指将多根电线或光纤束在一起,通过一系列的加工工艺,形成一个整体的线束产品。
线束加工工艺流程包括材料准备、剥皮、编织、绝缘、连接、测试、包装等多个环节。
下面将详细介绍线束加工的工艺流程。
1. 材料准备。
线束加工的第一步是准备材料。
根据客户的需求,选择合适的电线、光纤、绝缘套管、连接器等材料。
在选择材料时,需要考虑到使用环境、电气特性、机械强度等因素,确保所选材料符合产品的要求。
2. 剥皮。
剥皮是将电线或光纤的外皮剥去,露出内部的导体或光纤芯。
剥皮可以使用手工剥线器、自动剥线机等工具进行。
剥皮的目的是为了方便后续的连接和绝缘处理。
3. 编织。
对于多根电线或光纤束,需要进行编织处理。
编织可以增加线束的机械强度,防止电磁干扰,提高线束的外观质量。
编织的方式有多种,可以根据产品的要求选择合适的编织工艺。
4. 绝缘。
绝缘是保护线束的重要工艺环节。
通过在导体或光纤周围套上绝缘套管或绝缘胶进行绝缘处理,确保线束在使用过程中不会因为外界环境导致短路或断线等问题。
5. 连接。
连接是将不同电线或光纤进行连接,形成一个完整的线束产品。
连接可以采用焊接、压接、插接等方式进行,确保连接牢固可靠,电气性能良好。
6. 测试。
在线束加工完成后,需要进行测试。
测试包括外观检查、电气性能测试、机械强度测试等多个方面。
通过测试,确保线束产品符合客户的要求和标准。
7. 包装。
最后一步是对线束产品进行包装。
包装可以采用盒装、卷装、托盘装等方式进行,确保产品在运输和储存过程中不受损坏。
通过以上的工艺流程,线束加工可以生产出符合客户要求的高质量线束产品。
线束加工工艺流程需要严格控制每个环节,确保产品的质量和性能达到标准要求。
同时,线束加工工艺流程也需要不断改进和优化,适应市场需求的变化,提高生产效率和产品质量。
线束加工工艺流程
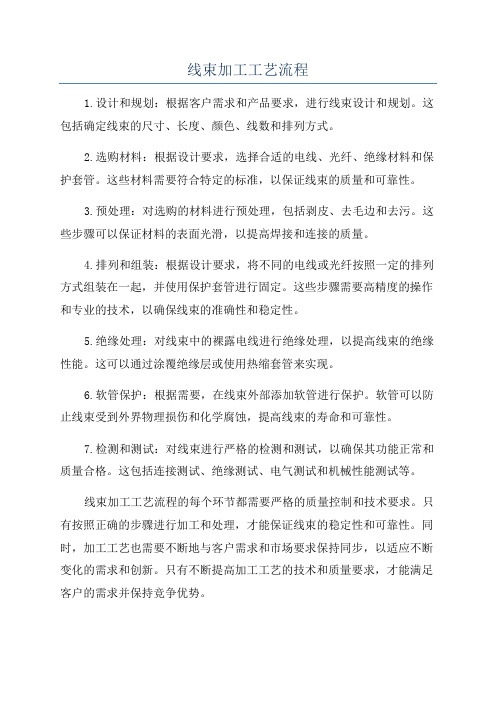
线束加工工艺流程
1.设计和规划:根据客户需求和产品要求,进行线束设计和规划。
这包括确定线束的尺寸、长度、颜色、线数和排列方式。
2.选购材料:根据设计要求,选择合适的电线、光纤、绝缘材料和保护套管。
这些材料需要符合特定的标准,以保证线束的质量和可靠性。
3.预处理:对选购的材料进行预处理,包括剥皮、去毛边和去污。
这些步骤可以保证材料的表面光滑,以提高焊接和连接的质量。
4.排列和组装:根据设计要求,将不同的电线或光纤按照一定的排列方式组装在一起,并使用保护套管进行固定。
这些步骤需要高精度的操作和专业的技术,以确保线束的准确性和稳定性。
5.绝缘处理:对线束中的裸露电线进行绝缘处理,以提高线束的绝缘性能。
这可以通过涂覆绝缘层或使用热缩套管来实现。
6.软管保护:根据需要,在线束外部添加软管进行保护。
软管可以防止线束受到外界物理损伤和化学腐蚀,提高线束的寿命和可靠性。
7.检测和测试:对线束进行严格的检测和测试,以确保其功能正常和质量合格。
这包括连接测试、绝缘测试、电气测试和机械性能测试等。
线束加工工艺流程的每个环节都需要严格的质量控制和技术要求。
只有按照正确的步骤进行加工和处理,才能保证线束的稳定性和可靠性。
同时,加工工艺也需要不断地与客户需求和市场要求保持同步,以适应不断变化的需求和创新。
只有不断提高加工工艺的技术和质量要求,才能满足客户的需求并保持竞争优势。
线束生产工艺流程

线束生产工艺流程
线束生产工艺流程是指对线束的加工和组装过程进行规划和操作的一种方法。
下面是线束生产工艺流程的具体步骤:
1. 计划和准备:首先,根据订单要求和客户需求,制定生产计划,并准备所需的原材料、工具和设备。
2. 剥线:将线束的外皮剥离,露出内部的导线。
使用剥线机或手动剥线工具进行剥线操作。
3. 引线:根据线束设计图纸,将导线按照要求进行剪裁和引线操作。
使用剪线器、弯线器等工具,在导线两端制作引线。
4. 根据线束设计图纸进行组装:根据线束设计图纸上的标记,将引线和其他组件按照正确的顺序和位置进行组装。
在组装过程中,使用扭簧工具、码器、绝缘胶带等进行连接和固定。
5. 绝缘处理:将组装好的线束进行绝缘处理,以提高线束的安全性和可靠性。
可以使用热缩管、绝缘胶带等材料进行绝缘处理。
6. 测试和质检:对组装好的线束进行测试和质检,以确保其符合设计要求和客户需求。
使用测试仪器和设备,检测线束的电气性能和质量。
7. 包装和出货:对通过测试和质检的线束进行包装,确保其安全和易于运输。
根据客户要求,选择适当的包装材料和方法。
8. 收尾和记录:对生产过程进行收尾和记录。
清理和整理生产现场,记录生产过程中的关键数据和信息,以便日后追溯和改进。
以上就是线束生产工艺流程的主要步骤。
不同企业和产品的线束生产工艺流程可能略有差异,但整体流程大致相同。
通过严格按照工艺流程进行操作,可以确保线束生产的质量和效率,并满足客户的需求。
线束生产工艺流程

线束生产工艺流程一、材料准备线束生产的第一步是准备所需材料。
根据产品要求,选择适当的导电线、电缆、连接器和保护管等材料,并将其按照设计要求进行切割和标记。
同时,对必要的连接器和接线端子进行钝化处理,以提高其耐腐蚀性能。
二、导线剥皮和绝缘处理将准备好的导线放入自动剥皮机中进行剥皮处理,剥去一定长度的外皮,露出内部的导体。
随后,进行绝缘处理,将绝缘套和绝缘盖等绝缘材料套在导线上,确保导线的绝缘性能。
三、连接器组装将准备好的连接器和接线端子插入导线中,并使用压接工具进行压接。
压接时,要确保接线端子紧固可靠,并与导线的金属部分保持良好的接触,以保证电流的传输质量。
四、线束组装根据产品要求,将已经处理好的导线、连接器和保护管等器件进行组装。
在组装过程中,要注意线束的布线规划和布线路径,确保线束的结构紧凑和排列合理。
同时,根据需求使用束线带、束线管或绑扎带等材料对线束进行固定,以防止松动和磨损。
五、验收和测试线束组装完成后,进行质量验收和测试。
通过对线束的外观、尺寸、绝缘性能和连接性能等进行检查和测试,确保线束符合产品要求和标准。
特别是对连接器和接线端子的插拔性能、电阻和绝缘电阻等进行测试,以验证线束的性能和可靠性。
六、包装和出厂线束生产工艺流程主要包括材料准备、导线剥皮和绝缘处理、连接器组装、线束组装、验收和测试、包装和出厂等步骤。
通过严格按照流程进行生产,能够提高线束产品的质量和可靠性,满足客户的需求和要求。
同时,对每一道工序进行严格的质量控制,确保每一道工序的合格率和一次性合格率,降低不良品率,提高生产效率。
线束加工流程
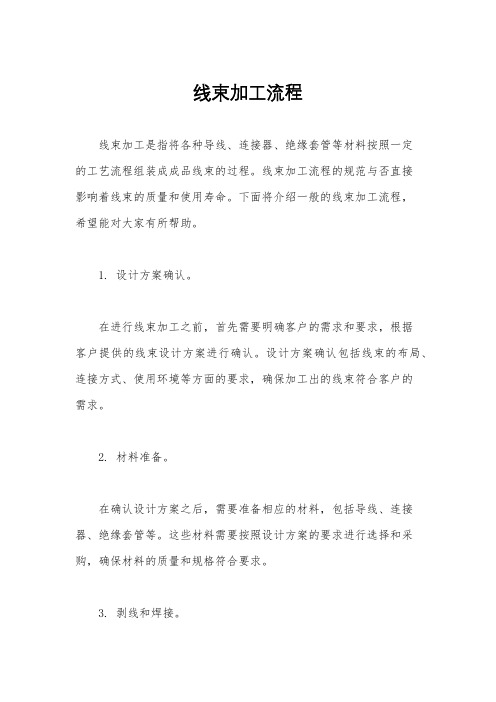
线束加工流程线束加工是指将各种导线、连接器、绝缘套管等材料按照一定的工艺流程组装成成品线束的过程。
线束加工流程的规范与否直接影响着线束的质量和使用寿命。
下面将介绍一般的线束加工流程,希望能对大家有所帮助。
1. 设计方案确认。
在进行线束加工之前,首先需要明确客户的需求和要求,根据客户提供的线束设计方案进行确认。
设计方案确认包括线束的布局、连接方式、使用环境等方面的要求,确保加工出的线束符合客户的需求。
2. 材料准备。
在确认设计方案之后,需要准备相应的材料,包括导线、连接器、绝缘套管等。
这些材料需要按照设计方案的要求进行选择和采购,确保材料的质量和规格符合要求。
3. 剥线和焊接。
接下来是对导线进行剥线和焊接。
剥线是指去除导线外部的绝缘层,使金属导体裸露出来,以便进行连接。
在剥线之后,需要根据设计方案的要求对导线进行焊接,将不同导线连接在一起,形成线束的基本结构。
4. 绝缘处理。
完成焊接后,需要对焊接部分进行绝缘处理,这通常包括使用绝缘套管或绝缘胶进行包裹,以防止导线之间的短路和外部环境的影响。
5. 组装和固定。
在完成绝缘处理之后,根据设计方案的要求进行线束的组装和固定。
这包括将连接器与导线连接,并使用绑扎带或者其他固定装置将线束固定在需要的位置上,确保线束的稳固性和整洁度。
6. 质量检验。
最后是对加工完成的线束进行质量检验。
质量检验包括外观检查、连接性能测试、绝缘电阻测试等,确保线束的质量符合设计要求和标准。
以上就是一般的线束加工流程,当然在实际加工过程中还会根据具体的要求和材料的不同进行一些特殊的加工步骤。
希望这些内容能够对线束加工有所帮助,谢谢阅读!。
线束工艺流程及注意事项
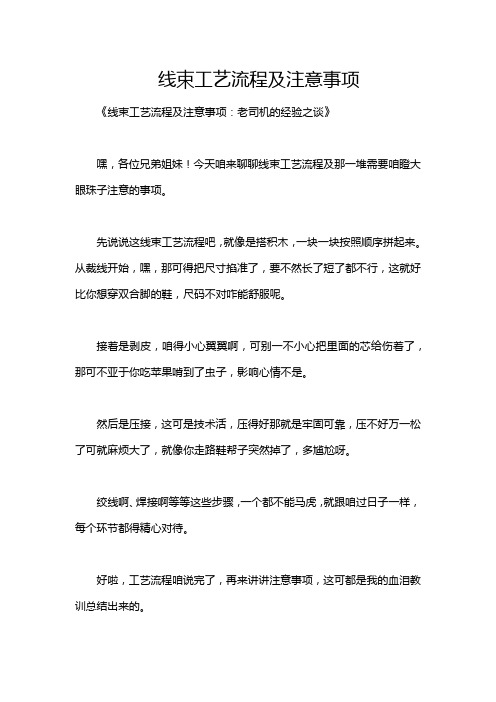
线束工艺流程及注意事项
《线束工艺流程及注意事项:老司机的经验之谈》
嘿,各位兄弟姐妹!今天咱来聊聊线束工艺流程及那一堆需要咱瞪大眼珠子注意的事项。
先说说这线束工艺流程吧,就像是搭积木,一块一块按照顺序拼起来。
从裁线开始,嘿,那可得把尺寸掐准了,要不然长了短了都不行,这就好比你想穿双合脚的鞋,尺码不对咋能舒服呢。
接着是剥皮,咱得小心翼翼啊,可别一不小心把里面的芯给伤着了,那可不亚于你吃苹果啃到了虫子,影响心情不是。
然后是压接,这可是技术活,压得好那就是牢固可靠,压不好万一松了可就麻烦大了,就像你走路鞋帮子突然掉了,多尴尬呀。
绞线啊、焊接啊等等这些步骤,一个都不能马虎,就跟咱过日子一样,每个环节都得精心对待。
好啦,工艺流程咱说完了,再来讲讲注意事项,这可都是我的血泪教训总结出来的。
首先,你得保持清醒的头脑,别迷迷糊糊的,不然一不小心就出错,就像你早上迷迷糊糊去上班,不是忘带钥匙就是忘带手机。
尺寸一定要量准确,不然生产出来的线束不是长了就是短了,那就好比你做衣服,尺寸不对穿起来能好看吗?
还有啊,原材料可得选好的啊,要是用了劣质材料,那后面可得三天两头出问题,就像买了个便宜的电器,三天两头坏,多闹心呐。
工人的操作技能也很重要,得好好培训,别跟个二愣子似的瞎干,那就跟开汽车不考驾照一样,危险系数太高啦。
在整个过程中,大家可得相互配合好,团队协作很关键,不能各干各的,得劲儿往一处使,不然就像拔河的时候大家用力不统一,肯定输得很惨。
总之呢,线束工艺流程就像是一场战斗,我们是英勇的战士,得认真对待每一个环节,注意每一个细节,这样才能生产出高质量的线束,让我们的产品在市场上勇往直前!哈哈,大家一起加油干吧!。
线束生产工艺流程
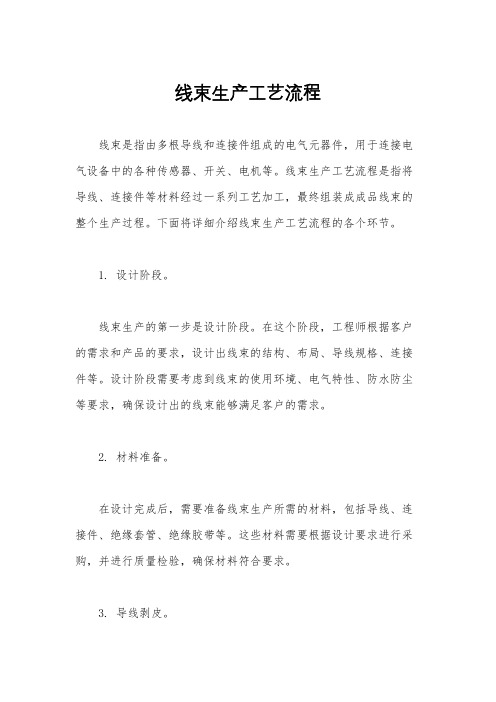
线束生产工艺流程线束是指由多根导线和连接件组成的电气元器件,用于连接电气设备中的各种传感器、开关、电机等。
线束生产工艺流程是指将导线、连接件等材料经过一系列工艺加工,最终组装成成品线束的整个生产过程。
下面将详细介绍线束生产工艺流程的各个环节。
1. 设计阶段。
线束生产的第一步是设计阶段。
在这个阶段,工程师根据客户的需求和产品的要求,设计出线束的结构、布局、导线规格、连接件等。
设计阶段需要考虑到线束的使用环境、电气特性、防水防尘等要求,确保设计出的线束能够满足客户的需求。
2. 材料准备。
在设计完成后,需要准备线束生产所需的材料,包括导线、连接件、绝缘套管、绝缘胶带等。
这些材料需要根据设计要求进行采购,并进行质量检验,确保材料符合要求。
3. 导线剥皮。
导线剥皮是线束生产的第一道工艺。
在这个环节,工人需要根据设计要求,将导线的外皮剥除,露出内部的金属导体。
导线剥皮需要使用专门的剥皮工具,确保剥皮的质量和速度。
4. 导线编织。
经过剥皮后的导线需要进行编织。
编织是指将多根导线按照设计要求进行组合和编织,形成线束的基本结构。
编织需要根据设计要求进行精确的排列和固定,确保线束的稳固性和电气性能。
5. 绝缘处理。
编织完成后的线束需要进行绝缘处理。
绝缘处理包括绝缘套管的安装、绝缘胶带的缠绕等工艺,确保线束在使用过程中能够有效地防水防尘,同时保护导线不受外部环境的影响。
6. 连接件安装。
线束中需要安装各种连接件,如插头、插座、端子等。
连接件安装需要根据设计要求进行精确的安装和固定,确保连接的可靠性和稳定性。
7. 终检。
线束生产的最后一道工艺是终检。
在终检环节,工人需要对线束进行外观检查、电气测试等,确保线束的质量和性能符合设计要求。
通过以上工艺流程,线束最终可以生产出符合客户要求的成品。
线束生产工艺流程需要严格按照设计要求和工艺标准进行操作,确保线束的质量和性能达到要求。
同时,线束生产工艺流程也需要不断改进和优化,以适应不同客户的需求和市场的变化。
线束加工工艺指导要求
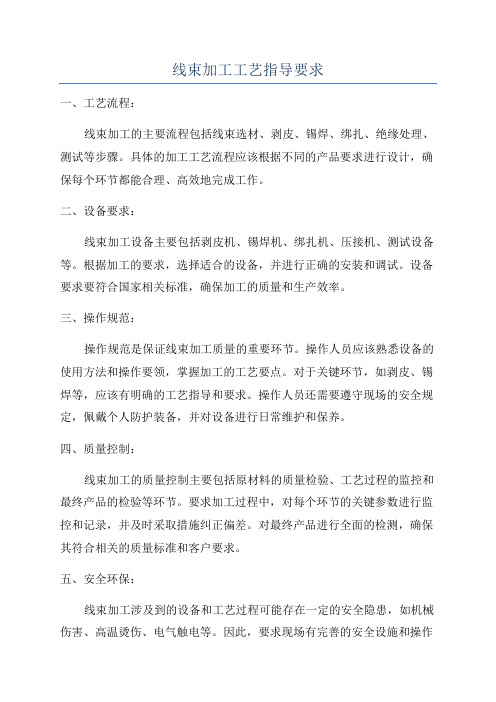
线束加工工艺指导要求
一、工艺流程:
线束加工的主要流程包括线束选材、剥皮、锡焊、绑扎、绝缘处理、测试等步骤。
具体的加工工艺流程应该根据不同的产品要求进行设计,确保每个环节都能合理、高效地完成工作。
二、设备要求:
线束加工设备主要包括剥皮机、锡焊机、绑扎机、压接机、测试设备等。
根据加工的要求,选择适合的设备,并进行正确的安装和调试。
设备要求要符合国家相关标准,确保加工的质量和生产效率。
三、操作规范:
操作规范是保证线束加工质量的重要环节。
操作人员应该熟悉设备的使用方法和操作要领,掌握加工的工艺要点。
对于关键环节,如剥皮、锡焊等,应该有明确的工艺指导和要求。
操作人员还需要遵守现场的安全规定,佩戴个人防护装备,并对设备进行日常维护和保养。
四、质量控制:
线束加工的质量控制主要包括原材料的质量检验、工艺过程的监控和最终产品的检验等环节。
要求加工过程中,对每个环节的关键参数进行监控和记录,并及时采取措施纠正偏差。
对最终产品进行全面的检测,确保其符合相关的质量标准和客户要求。
五、安全环保:
线束加工涉及到的设备和工艺过程可能存在一定的安全隐患,如机械伤害、高温烫伤、电气触电等。
因此,要求现场有完善的安全设施和操作
规范,并进行相关的培训和教育。
此外,还应该对废弃物的处理进行规范,遵守环保要求,减少对环境的污染。
六、持续改进:
在制定线束加工工艺指导要求时,需要结合具体的产品特点和生产环
境进行综合考虑。
同时,还要与相关部门和人员充分沟通和协调,确保指
导要求的有效实施。
线束生产工艺详细流程
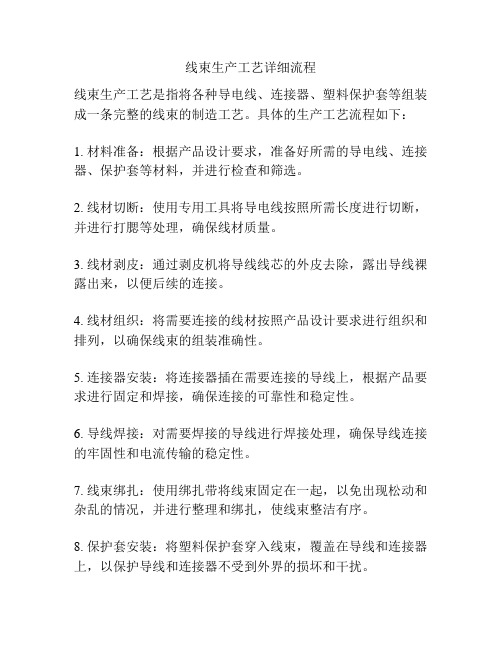
线束生产工艺详细流程
线束生产工艺是指将各种导电线、连接器、塑料保护套等组装成一条完整的线束的制造工艺。
具体的生产工艺流程如下:
1. 材料准备:根据产品设计要求,准备好所需的导电线、连接器、保护套等材料,并进行检查和筛选。
2. 线材切断:使用专用工具将导电线按照所需长度进行切断,并进行打腮等处理,确保线材质量。
3. 线材剥皮:通过剥皮机将导线线芯的外皮去除,露出导线裸露出来,以便后续的连接。
4. 线材组织:将需要连接的线材按照产品设计要求进行组织和排列,以确保线束的组装准确性。
5. 连接器安装:将连接器插在需要连接的导线上,根据产品要求进行固定和焊接,确保连接的可靠性和稳定性。
6. 导线焊接:对需要焊接的导线进行焊接处理,确保导线连接的牢固性和电流传输的稳定性。
7. 线束绑扎:使用绑扎带将线束固定在一起,以免出现松动和杂乱的情况,并进行整理和绑扎,使线束整洁有序。
8. 保护套安装:将塑料保护套穿入线束,覆盖在导线和连接器上,以保护导线和连接器不受到外界的损坏和干扰。
9. 绝缘处理:根据产品的要求,对整个线束进行绝缘处理,防止电线之间的短路和漏电,提高使用的安全性和可靠性。
10. 质量检验:对生产的线束进行质量检验,检查连接的牢固性、电阻和绝缘等指标是否合格。
11. 包装和出货:将合格的线束进行包装,并标明产品名称、规格、数量和生产日期等信息,然后装货出库。
通过以上的流程,可以保证线束的质量和可靠性,提高线束的生产效率和制造成本,并且可以适应不同的产品需求和生产要求。
同时,为了确保线束的有效运行和长期使用,还需要定期进行维护和保养,以延长线束的使用寿命。
线束工艺流程
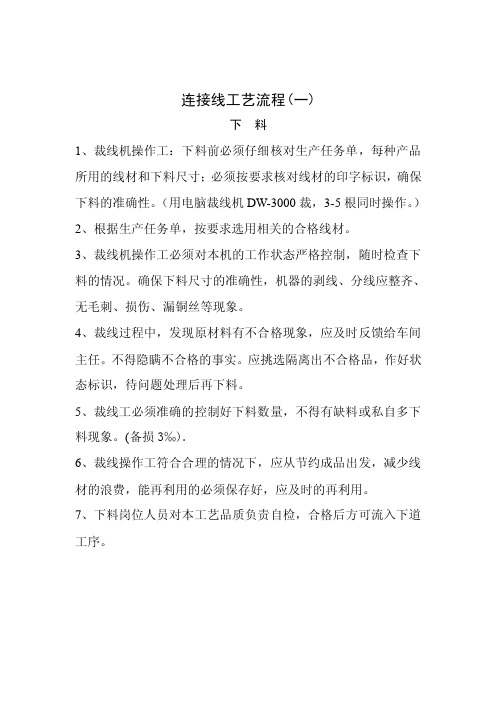
连接线工艺流程(一)下料1、裁线机操作工:下料前必须仔细核对生产任务单,每种产品所用的线材和下料尺寸;必须按要求核对线材的印字标识,确保下料的准确性。
(用电脑裁线机DW-3000裁,3-5根同时操作。
)2、根据生产任务单,按要求选用相关的合格线材。
3、裁线机操作工必须对本机的工作状态严格控制,随时检查下料的情况。
确保下料尺寸的准确性,机器的剥线、分线应整齐、无毛刺、损伤、漏铜丝等现象。
4、裁线过程中,发现原材料有不合格现象,应及时反馈给车间主任。
不得隐瞒不合格的事实。
应挑选隔离出不合格品,作好状态标识,待问题处理后再下料。
5、裁线工必须准确的控制好下料数量,不得有缺料或私自多下料现象。
(备损3‰).6、裁线操作工符合合理的情况下,应从节约成品出发,减少线材的浪费,能再利用的必须保存好,应及时的再利用。
7、下料岗位人员对本工艺品质负责自检,合格后方可流入下道工序。
捻线、沾锡1、捻线操作工必须需捻线、沾锡的产品要求掌握、明确。
2、选用适当的捻线头进行操作,铜丝经过捻线后应紧密均匀、直伸、无散碎铜丝和线头不紧呈散开状等现象。
3、捻线加工后的产品要小心放置好,保护好线头不被碰撞。
4、按照产品要求进行沾锡,控制沾锡部位尺寸的标准性,且沾锡表面应光亮、呈银白色、无余锡结集和漏沾锡现象的产品。
(线表皮无烧焦状态。
)5、沾锡操作工对自己的工艺质量负责、严格自选出漏沾锡,沾锡表面缺少和余锡结集不合格产品。
6、发现有导线表焊锡不良及其它质量问题要及时反馈给车间主任或主管部门,确保不良品的有效控制和及时的采取相应措施。
端子压接1、压接端操作者应先检查压接设备的通断运转是否完好,注意安全操作。
先给压接设备上油,以保证压接时正常生产。
2、操作者应按产品工艺标识卡上的要求领取相应的线材和端子进行压接,杜绝错压现象,要按照正确的压接方向和顺序。
3、随时检查端子的电镀质量,杜绝用氧化发黄、发黑和变形的不合格端子。
4、操作者应随时自检端子的压接抗拉力,是否达到标准要求。
线束制造工艺

检测工序:对线束进行电气性能 和外观质量的检测确保符合要求。
准备线束和连接器:选择合适的线束和连接器 确保线束的长度和连接器的型号符合要求。
剥线:根据需要使用剥线钳或剥线机将线束的外 皮剥离露出线芯。
压接:将剥好的线芯插入连接器中使用压接工具 将连接器的端子压接到线芯上。
检测:对压接好的线束进行电气性能和机械性能 检测确保符合要求。
添加 标题
注意事项:使用这些设备时需注意安全遵循操作规程避免发生意外事故。同时应定期维护和保养设备确 保其正常运转。
测量工具:用于测量线束的长度、直径、角度等尺寸保证线束的精度和质量。 检测工具:用于检测线束的导通性、绝缘性、耐压性等电气性能确保线束的质量和安全性。 检验夹具:用于检验线束的装配质量和外观保证线束的合格和美观。 测试设备:用于测试线束的整体性能和功能保证线束的性能和可靠性。
识别问题:对 生产过程中出 现的质量问题 进行准确判断
和记录
分析原因:对 每个问题进行 深入分析找出
根本原因
制定措施:根 据分析结果制 定有效的改进
措施
ห้องสมุดไป่ตู้
实施改进:确 保改进措施得 到有效执行并 进行持续监控
轻量化材料:如碳 纤维复合材料可提 高线束的强度和减 轻重量
高温材料:能够承 受更高的温度增强 线束的耐久性和安 全性
添加标题
智能化制造技术将逐步普及实现 生产过程的自动化和智能化。
定制化生产的需求将进一步增加 推动线束制造企业向个性化、柔 性化生产转型。
发展前景:随着汽车行业的不断 发展和智能化趋势线束制造行业 将迎来更多的发展机遇市场需求 将持续增长。
技术创新:为了应对挑战和抓住 机遇线束制造行业需要不断进行 技术创新和升级提高生产效率和 产品质量。
fakra线束加工流程

fakra线束加工流程Fakra线束加工流程是指将Fakra连接器与电缆进行连接并进行固定的一系列工艺过程。
下面是一个典型的Fakra线束加工流程:1. 材料准备:收集所需材料,包括Fakra连接器、电缆、绝缘套以及其他所需配件。
确保材料的质量符合要求。
2.测量和切割:使用测量工具测量所需电缆的长度,然后使用切割工具将电缆切割成正确的尺寸。
3.焊接:将电缆的外皮剥离一段,然后根据连接器型号的规定,将内部绞线剥离一小段。
使用焊接设备将中心导体与连接器的引线焊接在一起。
确保焊接质量可靠,避免接触不良或断开。
4.绝缘处理:在焊接完成后,将焊接点部分用绝缘套进行绝缘处理,以确保焊接点的安全性和可靠性。
根据实际情况,可能需要使用热缩套管、塑料套管等不同类型的绝缘材料。
5.固定连接器:将连接器插入固定夹具或支架中,然后使用固定工具对连接器进行固定,确保连接器与电缆的连接牢固可靠。
6.测试和检验:进行线束的基本测试和检验,包括导通测试、绝缘测试、抗拉强度测试等。
确保线束的质量符合规定的标准和要求。
7.产品检验:对加工完成的线束进行全面检验,包括外观检查、焊接点检测、引线的接触性检测等。
确保线束没有焊接错误、松动或其他质量问题。
8.包装和存储:对通过检验的线束进行包装,使用合适的包装材料进行保护,然后进行标识和分类。
存储线束时需要避免受潮、受压和受热等可能影响线束质量的因素。
总的来说,Fakra线束加工流程需要经过材料准备、测量和切割、焊接、绝缘处理、固定连接器、测试和检验、产品检验、包装和存储等一系列工序。
这些步骤确保了线束的质量和性能,并且使得线束能够在实际应用中可靠地连接和传输信号。
- 1、下载文档前请自行甄别文档内容的完整性,平台不提供额外的编辑、内容补充、找答案等附加服务。
- 2、"仅部分预览"的文档,不可在线预览部分如存在完整性等问题,可反馈申请退款(可完整预览的文档不适用该条件!)。
- 3、如文档侵犯您的权益,请联系客服反馈,我们会尽快为您处理(人工客服工作时间:9:00-18:30)。
料带太长
料带不可见,
图7, 合格, 热缩 套管 完全 包 图8住 导 不体 合 格热 缩套 管包 的太 长
端子外观检验 合格
端子外观检验 不合格
端子高铆度端测量高度测量:作为确保正常压着性能的管 理方法,有必要进行铆端高度测定,设定高度虽然 是在铆端机方面设定的,但就其测定却是在铆端 之物上进行的,测试时使用铆端高度测定用仪器 ——千分尺,用其测定铆端体的“固定栅”和“ 挤压栅”的各中心部位,测试时需避开“挤压沟 ”,且确认用的线材应为生产使用之线材.
目视检测中拒绝接收的例举
四.组装胶壳
将铆压好之端子卡口片方向与塑壳卡同 向,再将端子平推入塑壳,当听到卡喀声后,再回 轻拉线材,以确定端子正确卡入塑壳,无脱落则 合格.注意依工程图要求组装,不可插错位.
卡片口卡于 卡位上
五.通电测试
测试目的:检测产品功能是否正常,以确定产品性 能是否符合客户要求.
在铆压拉力和高度保证的前提下,理想的铆端 状态: 1. 视窗 1 能看见导体又能看到绝缘体(外被) 2. 视窗 2 芯线(导体)露出长度0.5~1.5mm(具体 依端子大小而定) 3. 嵌合部不可变形,卡口片不可变形 4. 芯线铆压栅、被覆固定栅中间沟槽不可有
以下为在目视检测中拒绝接收的例举
目视检测中拒绝接收的例举
图1, 标准压 接,外皮处 于导体包筒 和绝缘包筒 之间
图2, 合格压 接,外皮刚好 与导体包筒 或 平绝齐缘图不包4合筒,
格压 接, 导体
图3, 不合格压接,外 皮压入导体包筒或 绝缘包筒内
图5, 不合 格压 接, 绝缘
端子外观检验
图4, 不合格压接,导体 没有完全压入导体包 筒内
图5, 不合格, 图6, 不合格,
2.调试作业: 由技术人员调试好机台,试作 2-3 条, 确认合格后方可批量作业 。
3.注意事项: ①端子铆压拉力或高度需符合要求; ②不可有深打、浅打、飞丝、端子变形, 铆压过高 或过低等不良开;③式端注子 意安导体全铆压,铆栅 压喇叭时口 切被勿覆铆将压栅手伸入刀模 内。
嵌合部
卡口片
挤压沟
料带
端子外观检验
线束生产工艺讲解
2017年8月
一.线材外观检验
图1,线材印字不清,无法 辩认,不合格
图2,同一线材外被颜色明显不 大于1,不合格
图3,线材外被严重变 形,不合格
图4,线材表面起鼓>0.5mm,发
图5,线材 表面脏污 并不可去 除,不合格
图6,线材芯线露 铜,不合格
图7,线材表面刮伤\划痕长度 >5mm,深度>0.15mm,不合格
端子高度测试
端子高度测试
端子高度测试
拉力测量
拉力测量:是为了进行铆压栅的铆端高度是否 适宜之判断的一种确认项目,其确认方法为 拉扯 被压着的端子与线材确认其破坏强度以及保证 其强度, 无论铆端高度是多么恰如其分,仍有缺陷 ,故为弥补高度检测的缺陷,测拉力强度是必要的 。
用拉力计测试端子拉力将端子固定好后,将拉 力计归零,再进行拉力测试,当拉力达到规定值时, 停止拉动,固定位置,保持 1 分钟,如端子没有脱落 则合格,每 1—2 小时抽测一次。
国标GB17196-1997
m㎡
N
Kgf
0.5
56
5.8
0.75
84
8.6
1
108
11
1.5
150
Байду номын сангаас
15.3
2.5
230
23.5
4
310
31.7
6
360
35.7
备注:
N:牛顿 Kgf:公斤力;
1Kgf=9.8N(牛顿)
端子检查
目视检测确认之目的是为了通过外观检查,检查 出铆端高度拉力测试中未能查出的压着不良与 模具不良,进一步通过压着状态良否的判断,发 现组装插件时的不适合等。
图8,线材烧焦, 不合格
1.准备工作: 检查机台是否正常,刀口是否完 二. 剥好皮无损,工作台面是否干净以及无其它产品,余
物.
2.调试好机台,试作2-3 条,确认合格后方可批 量作业 .
3.注意事项: ①尺寸须在公差范围内; ②不可 剥断导体铜丝;③切剥口须平整 .
4.剥皮尺寸参考算法(如下图):
六.包装入库
包装时注意不可有少装或多装,以及混装,标识
谢谢!
剥线正确图
剥线不正确图
剥皮不良原因: 1.操作不当 2.刀距不正确 3.刀口损伤
剥离刀钝或刀之间距离不正确, 绝缘层切割不正确
剥离刀钝 绝缘层切割不正确
剥离刀之间距离太小 绞合线损伤或切断
剥离刀钝或调节不正确, 导线的剥离处附有绝缘微粒
剥离工具夹钳损坏或内有金属屑 绝缘层损坏
被覆铆压栅
1.准备工作: 检查机台是否正常,刀模是否完好无损 ,工作台面是否干净以及无其它产品 、余物.
露出导体 导体铆压栅长度
可见导体和绝缘体
导体铆压栅长度
a 剥线长度 被覆铆压栅 可见导体剥线长度
剥皮尺寸=导体铆压栅长度 +1/2a +0.5mm(线规: 0.3mm2 以下) 剥皮尺寸=导体铆压栅长度 +1mm (线规:0.3— 1mm2 ) 剥皮尺寸=导体铆压栅长度 +2mm (最大线规: 10mm2 )