热轧工艺润滑
热轧工艺润滑与粘铝的关系

变形区 轧辊表面润滑层转变区热轧工艺润滑与粘铝的关系作者:谢仁泽我们厂的热轧运转已经三年了,表面质量一直是影响我们产品质量的主要瓶颈。
热轧工序控制表面质量至关重要,性能良好的热轧润滑液对表面质量的控制具有十分重要的意义。
通常热轧都是在300℃以上的温度下进行的,由于铝的熔点低,屈服强度低,极易粘附,在轧制过程中容易产生粘铝的表面缺陷。
经阳极氧化后显露为黑斑。
严重影响产品质量,经冷轧轧制后也难以消除。
1. 铝合金热轧特点与乳液润滑机理1.1 铝合金热轧特点铝合金热轧的一个显著特点是在轧辊上覆盖一层“铝膜”的情况下进行。
从JohnA.Schey,<<LIGHT METAL AGE>>上可知这种“铝膜”主要由三氧化二铝和10%∽15%的铝粉及润滑剂及残渣的碳素物组成。
正因为轧制是在带有“铝膜”的辊面间进行,所以轧铝油性能的好坏和乳液的日常管理对铝材表面质量的控制具有十分重要的意义,它决定了辊面铝膜状态。
1.2 乳液润滑之物理分析热轧乳液的基本功能是减少摩擦,防止轧辊与轧件粘结,同时控制工作辊辊形与温度。
在轧制过程中乳液作为冷却润滑剂喷向轧辊和轧件,均匀而充足的乳液在变形区入口处形成楔形油楔(如图1)。
由流体动力学基本原理可知,当固体表面运动时,粘附于轧辊和轧件表面的润滑剂分别随运动的轧辊与轧件同步运动,中间流体作层流运动。
因此旋转的轧辊表面和运动的轧件表面使润滑剂增压进入楔形前区,越接近变形区入口平面润滑楔内产生的压力就越大。
当压力达到轧件发生塑性变形压力时,则有一定厚度的乳化液被带入变形区,还有轧辊与轧件的显微不平也将乳液带入变形区。
带入变形区的乳液受高温高压和剪切力作用而使油水分离,水蒸发带走热量,冷却轧辊轧件;分离出来的油相和添加剂与金属表面和金属屑反应,形成一层细密的辊面涂层,有效地隔离摩擦面而达到润滑的目的。
1.3乳液润滑之分子分析我们目前使用的热轧润滑剂是由合成油和多种添加剂与水混合而成的一种牛奶状液体,实际上是油以细小油滴形式分布于水中的水包油型乳化剂。
铝板带热轧工艺润滑剂的使用探究
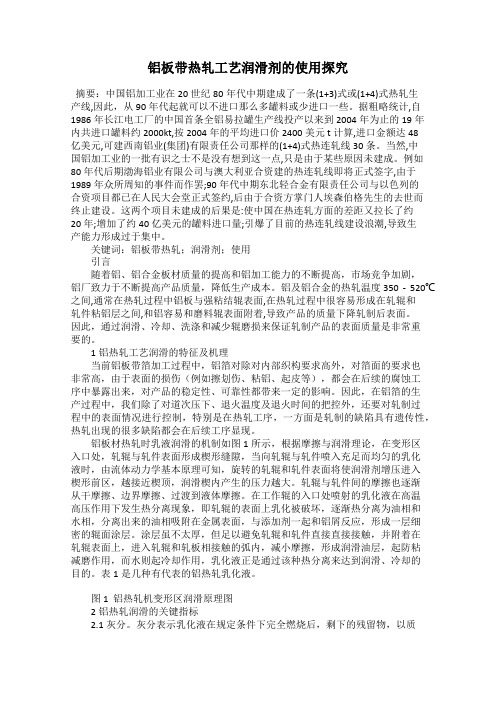
铝板带热轧工艺润滑剂的使用探究摘要:中国铝加工业在20世纪80年代中期建成了一条(1+3)式或(1+4)式热轧生产线,因此,从90年代起就可以不进口那么多罐料或少进口一些。
据粗略统计,自1986年长江电工厂的中国首条全铝易拉罐生产线投产以来到2004年为止的19年内共进口罐料约2000kt,按2004年的平均进口价2400美元t计算,进口金额达48亿美元,可建西南铝业(集团)有限责任公司那样的(1+4)式热连轧线30条。
当然,中国铝加工业的一批有识之士不是没有想到这一点,只是由于某些原因未建成。
例如80年代后期渤海铝业有限公司与澳大利亚合资建的热连轧线即将正式签字,由于1989年众所周知的事件而作罢;90年代中期东北轻合金有限责任公司与以色列的合资项目都已在人民大会堂正式签约,后由于合资方掌门人埃森伯格先生的去世而终止建设。
这两个项目未建成的后果是:使中国在热连轧方面的差距又拉长了约20年;增加了约40亿美元的罐料进口量;引爆了目前的热连轧线建设浪潮,导致生产能力形成过于集中。
关键词:铝板带热轧;润滑剂;使用引言随着铝、铝合金板材质量的提高和铝加工能力的不断提高,市场竞争加剧,铝厂致力于不断提高产品质量,降低生产成本。
铝及铝合金的热轧温度350 - 520℃之间,通常在热轧过程中铝板与强粘结辊表面,在热轧过程中很容易形成在轧辊和轧件粘铝层之间,和铝容易和磨料辊表面附着,导致产品的质量下降轧制后表面。
因此,通过润滑、冷却、洗涤和减少辊磨损来保证轧制产品的表面质量是非常重要的。
1铝热轧工艺润滑的特征及机理当前铝板带箔加工过程中,铝箔对除对内部织构要求高外,对箔面的要求也非常高,由于表面的损伤(例如擦划伤、粘铝、起皮等),都会在后续的腐蚀工序中暴露出来,对产品的稳定性、可靠性都带来一定的影响。
因此,在铝箔的生产过程中,我们除了对道次压下、退火温度及退火时间的把控外,还要对轧制过程中的表面情况进行控制,特别是在热轧工序,一方面是轧制的缺陷具有遗传性,热轧出现的很多缺陷都会在后续工序显现。
热轧工艺润滑问题与改进措施

热轧工艺润滑问题与改进措施高亮亮① 杨宝贵(北京首钢股份有限公司 河北唐山064400)摘 要 热轧工艺润滑能够明显提高热轧轧机效率、降低系统轧制力、改善板带表面质量、延长轧辊使用寿命等特点。
本文介绍了热轧工艺润滑系统组成,分析了在使用过程中存在的问题并提出了改进措施,通过改善极大的提高了工艺润滑的投入率及可靠性。
关键词 热轧 工艺润滑 改进中图法分类号 TG155.4 文献标识码 BDoi:10 3969/j issn 1001-1269 2022 Z2 0381 前言热轧工艺润滑轧制技术是指在轧制变形区内建立一层润滑油膜,改变辊面与轧件间的“金属—金属”直接接触,改善轧制过程,提高产品质量的一种手段[1]。
随着市场对热轧板带的质量要求越来越高,生产商不断提高生产率,大举开发新的钢材种类,新的金属轧制技术和设备的日益成熟,轧制应用的范围不断拓展,热轧工作辊的工作环境也变得越来越严酷。
为了保证质量,提高作业率,轧辊要具备长寿命、耐磨耐用的特性。
所以工艺润滑在轧制过程中逐步得到了更多地应用和研究[2]。
为了更好的在激烈的市场竞争中,不断拓宽产品结构、提升产品质量、降低产品成本,持续提升企业的核心竞争力,首钢股份公司2250热轧产线精轧机组实施工艺润滑改造,以提升热轧带钢表明质量、实现薄规格轧制高效稳定。
在工艺润滑投入后,出现了管路、喷嘴堵塞、油温提升缓慢、对轧制力改善效果不明显等多个问题,通过不断进行技术攻关及系列改善,工艺润滑系统得到充分的利用。
2 工艺润滑设备及润滑方式热轧工艺润滑系统采用专用喷嘴系统,以水为载体将油水混合后喷射在轧辊上,使热轧润滑达到最佳的使用效果,此系统容易控制、运行可靠、维护方便故障率低。
热轧工艺润滑油喷出后与高温带钢接触,燃烧后形成灰分,因而工艺润滑油不能重复利用,采用非循环方式。
工艺润滑可以降低轧机负荷、减少轧机能耗、改善工作辊面得工作状态、维持良好的带钢表面质量、提高生产率、提高轧机的稳定性等作用。
1700生产线热轧工艺润滑系统开发与应用

架 各 由一 个 油泵 独 立供 油 , 个 混合 器 完成 油水 一
混合 图 1为热 轧油 系统布 置简 图 。
2 12 水 系统 . .
目前 , 国内 很多 热 轧厂 在 设 计 热轧 工 艺润 滑 系统 时 , 水 系 统 都与 其 它冷 却 系统 共 用 一个 系 其 统 , 样很难保 证 水压稳 定 , 影 响热 轧油使 用效 这 且
a da r d I edd o g t dut n cus n p l a o aeo ti lb c t n ss m e n bo ." e g t u h ,ajs a h n h me t o r a da p c t ns t f hs u r a o t a e ii t i i ye r
安 装 与应用 。
2 系 统设 计 方 案
2 1 硬件设计 .
2 1 1 系统布局 . .
F ~F 机 架共 用 一个水 系统 和油箱 , I 6 每个 机
得 到 了普 遍应 用 。最 初 提 出润 滑轧 制 的 目的 只是 为了提 高热轧 带钢 的质 量 , 发展 到今 天 , 但 它已成
轧 工艺 润 滑技 术 以减轻 精 轧 机组 负 荷 、 低 能耗 降 和 提高 生产 率就显 得非 常重要 。 为此 , 过 吸收 国 通
内外 热轧 工 艺润 滑 先进 技 术 , 发设 计 了一 套工 开
艺 润滑 系统 , 并在 1 0 7 0生产线 的精轧机 组 进行 了
史 乃 安 , 钢 技 术 专 家 , 级 工 程 师 , 9 9年 毕 业 予 西 安 冶 鞍 高 18 金建 筑 学 院金 属 塑 性 加 工 专业 , 工作 于 鞍 钢股 份 有 限 公 司 热 轧 现 带 钢厂 ( 10 1 。 14 2 )
轧制工艺润滑技术
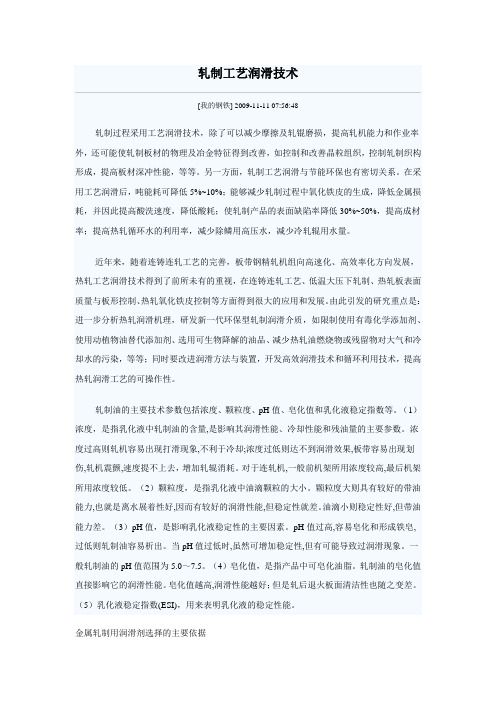
轧制工艺润滑技术[我的钢铁] 2009-11-11 07:56:48轧制过程采用工艺润滑技术,除了可以减少摩擦及轧锟磨损,提高轧机能力和作业率外,还可能使轧制板材的物理及冶金特征得到改善,如控制和改善晶粒组织,控制轧制织构形成,提高板材深冲性能,等等。
另一方面,轧制工艺润滑与节能环保也有密切关系。
在采用工艺润滑后,吨能耗可降低5%~10%;能够减少轧制过程中氧化铁皮的生成,降低金属损耗,并因此提高酸洗速度,降低酸耗;使轧制产品的表面缺陷率降低30%~50%,提高成材率;提高热轧循环水的利用率,减少除鳞用高压水,减少冷轧辊用水量。
近年来,随着连铸连轧工艺的完善,板带钢精轧机组向高速化、高效率化方向发展,热轧工艺润滑技术得到了前所未有的重视,在连铸连轧工艺、低温大压下轧制、热轧板表面质量与板形控制、热轧氧化铁皮控制等方面得到很大的应用和发展。
由此引发的研究重点是:进一步分析热轧润滑机理,研发新一代环保型轧制润滑介质,如限制使用有毒化学添加剂、使用动植物油替代添加剂、选用可生物降解的油品、减少热轧油燃烧物或残留物对大气和冷却水的污染,等等;同时要改进润滑方法与装置,开发高效润滑技术和循环利用技术,提高热轧润滑工艺的可操作性。
轧制油的主要技术参数包括浓度、颗粒度、pH值、皂化值和乳化液稳定指数等。
(1)浓度,是指乳化液中轧制油的含量,是影响其润滑性能、冷却性能和残油量的主要参数。
浓度过高则轧机容易出现打滑现象,不利于冷却;浓度过低则达不到润滑效果,板带容易出现划伤,轧机震颤,速度提不上去,增加轧辊消耗。
对于连轧机,一般前机架所用浓度较高,最后机架所用浓度较低。
(2)颗粒度,是指乳化液中油滴颗粒的大小。
颗粒度大则具有较好的带油能力,也就是离水展着性好,因而有较好的润滑性能,但稳定性就差。
油滴小则稳定性好,但带油能力差。
(3)pH值,是影响乳化液稳定性的主要因素。
pH值过高,容易皂化和形成铁皂,过低则轧制油容易析出。
钢厂热轧干油润滑系统的应用与维护陈沛沛

钢厂热轧干油润滑系统的应用与维护陈沛沛发布时间:2021-08-05T06:49:21.689Z 来源:《房地产世界》2020年20期作者:陈沛沛[导读] 润滑系统的润滑管道非常多,一般说来有专职人员负责管理维护保养。
目前我国绝大部分轧钢厂的加工线基本上都配置了双线或单线干油集中化润滑系统,但在使用中的实际效果并不是非常好。
陈沛沛身份证号码:32068119900412xxxx 摘要:润滑系统的润滑管道非常多,一般说来有专职人员负责管理维护保养。
目前我国绝大部分轧钢厂的加工线基本上都配置了双线或单线干油集中化润滑系统,但在使用中的实际效果并不是非常好。
很大一部分原因就是维护保养不及时,所以慢慢地被放弃,从而再度使用人工来润滑设备。
另外,干油集中化润滑系统润滑管道在关键设备维修保养时总是被损毁,从而导致关键设备机械故障过于频繁,这都是忽略了辅助机械设备的维护保养。
所以,为了更好地维护保养干油集中化润滑系统,除了要有专职人员做好维护保养,与此同时,还要转变管理人员的传统观念,在思想方面重视起来。
本文对热轧设备的干油润滑系统开展了深入分析,并对其技术应用和维护保养实践经验进行了探析。
关键词:钢厂热轧;干油润滑系统;应用与维护1热轧干油系统概述 1.1干油润滑技术集中化润滑的通常是指仅设置一个干油站,然后通过润滑管道和调节器将干油传至各润滑设备点。
轧钢润滑系统的集中化干油润滑的配置功能模块通常会布置在炉前区、轧机区、冷床区和回收区。
干油站有两种类型:手动式和自动式。
手动式干油站适用于润滑的点少、远离其它的机械设备的设备或过于频繁挪动的设备。
当自动式干油站正常运行时,干油可以通过压差传至主管道,并经过供油器供油。
润滑管道配备有网状结构过滤装置,一定要定期进行清理和全面检查。
当润滑系统泵油结束后,安装在润滑管道尾端的末端阀(又被称为压力调节阀)开始运行,系统自动终止干油,使液压换向阀转换方向。
自动式干油站由系统自动的中间继电器调控,在润滑系统设置的时间段自主进行泵油[1]。
我国钢板热轧技术及工艺润滑的发展
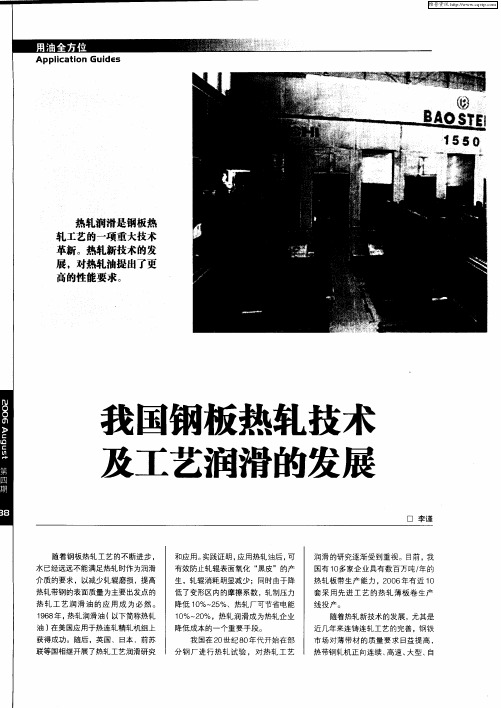
燃 烧 后残 炭 起润 滑作 用
热轧 时在 变形 区中轧辊表面的瞬
少 ,操 作简便 ,油水混合的浓度易于
控制 , 喷油 时间滞后 , 以控制 , 但 难 造
间温度可高达 4 0 5 0C,高于 润滑 0 ~0o 剂的燃点 ,一部分润滑油被 燃烧。燃
烧残留物主要是残炭 ,将轧辊与金属 表面隔开 。残炭 与金属和轧辊之 间的 摩擦系数小于金属与轧 辊之 间的固体 摩擦系数 。
成油耗过大 ,喷嘴容易堵塞 。
目前国内许 多热轧厂仍采用直 接
注入法 ,但 已进行 了不 断的改进 。
热 轧 油的应 用 润滑 技 术不仅 包
括热轧 油 品本 身 ,同 时还 包括很 多
的工艺参数优化 技术。例如从混合器
形 成高 温 高压 气 垫
由于 热轧 时变形 区中温 度高于润
润滑效 果 。 为此 必须根 据所 选用 的 润滑 油进 行现 场试验 ,对 混油点 位
水
—毛=喷轧制油 三 —哥 喷冷却水
支撑辊
油
方法 一 :油 水预搅 拌混 合法
油 水在 混合 器 中按 比例预 先 配
好 ,搅拌均 匀 ,调合成 油水 混合 液 后 , 到轧辊表 面。为保 证油 品 的流 送
温、 高速 、 高压状态下的动态过程 , 至
今 对热轧 的润滑 机 理 尚无统 一 的认
识。
方 法三 :直接 注 入法
该 方法是将轧制油直接注入轧机
通常认为热轧 油以三种状态起润
滑作 用。
原有的轧辊冷却水管路系统 中形成 油
水混合液 , 随冷却水喷射到轧辊表面。 此方 法是 传统 方式 ,设 备投 资
铝板带热轧工艺润滑剂的使用
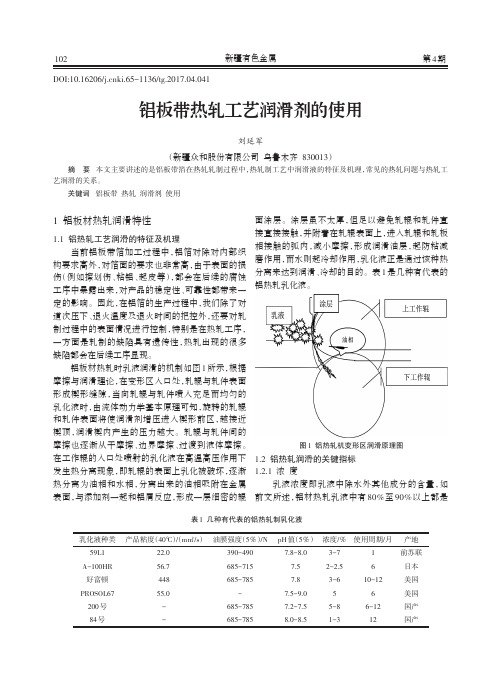
前文所述, 铝材热轧乳液中有 80%至 90%以上都是
乳液浓度即乳液中除水外其他成分的含量, 如
表 1 几种有代表的铝热轧制乳化液 乳化液种类 A-100HR 好富顿 PROSOL67 200 号 84 号 59L1 产品粘度 (40ħ) ( / m㎡/s) 油膜强度 (5%) /N 22.0 56.7 55.0 448 390-490 685-715 685-785 685-785 685-785 pH 值 (5%) 浓度/% 使用周期/月 7.8-8.0 7.5 7.8 2-2.5 3-6 5-8 1-3 5 3-7 1 6 6 产地 前苏联 日本 美国 美国 国产 国产
摩擦与润滑理论, 在变形区入口处, 轧辊与轧件表面 形成楔形缝隙, 当向轧辊与轧件喷入充足而均匀的 乳化液时, 由流体动力学基本原理可知, 旋转的轧辊 和轧件表面将使润滑剂增压进入楔形前区, 越接近 楔顶, 润滑楔内产生的压力越大。轧辊与轧件间的 摩擦也逐渐从干摩擦、 边界摩擦、 过渡到液体摩擦。 在工作辊的入口处喷射的乳化液在高温高压作用下 发生热分离现象, 即轧辊的表面上乳化被破坏, 逐渐 热分离为油相和水相, 分离出来的油相吸附在金属 表面, 与添加剂一起和铝屑反应, 形成一层细密的辊 1.2 铝热轧润滑的关键指标 1.2.1 浓 度
引起润滑过度; 生物活性表示乳液中细菌的含量, 细 废; 当乳液温度过高时, 也易引起乳液变质。
pH 值偏高时, 会导致润滑性能下降, 偏低时可能
[3]肖亚庆 . 铝加工技术手册 . 北京 . 冶金工业出版社 .2005. 版社 .2013.
菌含量过高易引起乳化液的变质, 导致乳液大量报
制在 4.0-7.0%范围, 这样既可以保证良好的润滑, 又 在合理范围。
轧制过程工艺润滑技术的发展和应用
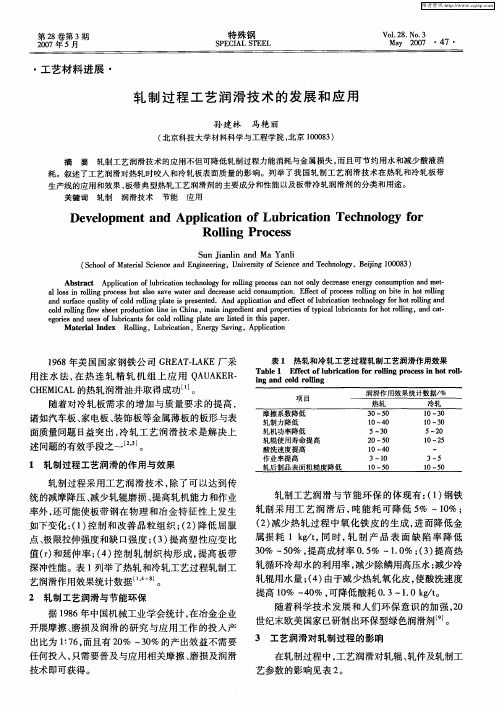
De e o m e t a d Ap ia i n o b ia i n Te h o o y f r v lp n n pl t fLu r c to c n l g o c o
RO l g Pr c s ln o es i
S n Ja l n ni u ini a dMaYa l n
随着对冷轧板需求的增加与质量要求的提高诸如汽车板家电板装饰板等金属薄板的板形与表面质量问题13益突出冷轧工艺润滑技术是解决上述问题的有效手段之一旧3j1轧制过程工艺润滑的作用与效果轧制过程采用工艺润滑技术除了可以达到传统的减摩降压减少轧辊磨损提高轧机能力和作业率外还可能使板带钢在物理和冶金特征性上发生如下变化
维普资讯
第2 8卷第 3期
20 07年 5月
特殊 钢
S E A 1 L P CI L s = EE
V0 . 8 No 3 12 . .
Ma 2 0 y 0 7 ・4 ・ 7
・
工 艺 材 料进 展 ・
轧 制 过 程工 艺 润滑 技 术 的发展 和 应 用
16 98年美 国 国家 钢 铁 公 司 G E TL K R A .A E厂采
Hale Waihona Puke 表 1 热 轧和冷 轧工艺过程轧制工艺润滑作用效果
Ta l Efe t f u rc to f r r l n r c s n h tr l b e1 f c l b a i n o ol g p o e si o o - o i i i d ol r li ng an c d o lng
( h o o t a Si c n nier g U ie i f i c n eh o g , e ig10 8 ) c S ol f e l ce eadE gne n , nvr t o e eadT cnl y B in 00 3 Ma r n i i sy S n c o j
热连轧工艺润滑新技术

要 预热 油 。 由于使 用 纯 油 , 滑 管道 中没 有 润
泡 沫形 成 , 以喷头不会 被堵 塞 。 所
3 喷射 性能
为 了获 得最 佳 喷射 效 果 , 制 好 油 和空 控 气 流速 是很 必要 的 。调 整空气 压力 能改 变喷 流 形状 和液滴 尺寸 。通 过空气 比例 阀精 确控 制 气流 。
方 面挖 掘轧机 的潜 力 。 通 过传统 乳 化 系统 进 行 润 滑 时 , 的 消 油
有 以下许 多优 点 :
・
高 效节 能
・
轧 制单 位长 ( 减少 轧辊磨 损 )
品种规 格多
表 面质 量好
・
・
耗 量 非 常低 , 因为 与水 混 合 后 浓 度 仅 为 1 %
一
5 。水 油 相 互 作 用 涉 及 到大 量 参 数 ( % 水
发 现 由于工业 油 中含有 添加 剂 , 因此 其 挥 发
4 1 健康 风 险 . 针 对纯 油润 滑时挥发 到 了空气 中的有 害 元素是否构成潜在 的健康风险这一问题 , 首
物 中含有 更 多有 害 元 素 , 当然其 含 量 没 有 超
过要 求 的安全值 。
4 2 火灾 风 险 . 在辊 缝 处 , 与 钢 带 接 触 时 温 度 大 约 油 9 0 。在 这个温 度条 件下 , 0℃ 油可 被点 燃或 被 降解 。为了排 除纯油 滑润 在机 架处 喷油 导致
太钢 译文
・ 9・ 2
热 连 轧工 艺 润 滑 新 技 术
白晋 钢译 陈 超校
1 概要
新技术是本着提高效率 , 减少维护 , 使用 如 植
CSP热轧工艺润滑效果研究

润 滑 与 密 封
LUBRI AT 0N C 1 ENGI NEERI NG
Sp 2 0 e . 01
第3 5卷 第 9期
Vo . 5 No 9 13 .
DOI 0 3 6 /.sn 0 5 :1 . 9 9 jis. 2 4—0 5 . 0 0 0 . 2 102 1.90 3
A s atT eefc f u r ai u n o l n f o at t ppo u t n( S bt c: h f t b i t nd r gh t ol go mp c r rd ci C P)w ss de ae ntep y — r e ol c o i r i c si o a t idb sdo h s u h
( c olo tr l ce c n n ier g nvri f ce c n e h ooy,B in 0 0 3, hn ) S h o f e a S in ea d E gn ei ,U iest o in ea dT c n lg Ma i n y S ej g1 0 8 C ia i
C P热 轧 工 艺 润 滑 效 果 研 究 S
马艳丽 孙建林 高 雅
北 京 10 8 ) 0 0 3
( 京科技大学材料科学与工程学院 北
摘 要 :在 理 化性 能 与摩 擦 学 性 能测 试 分析 的 基础 上 ,对 C P热轧 板 带 钢 工 艺 润 滑 应 用 效 果 进 行 轧 制 过 程 研 究 。 工 S 业 应 用试 验 表 明 : S C P热 轧板 带 钢过 程 中 ,并非 热 轧 油体 积 比越 高 ,工艺 润 滑 效果 越 好 ,选 择 中 低黏 度 、润 滑 性 能 良好 的热 轧油 ,其体 积 分 数在 0 2 时 即可 平均 降 低 轧制 力 1% ~ 0 ,使 连 轧 过 程张 力 波 动控 制 在 2 % 以 内 ,同 时对 冷 却 .% 0 2% 0 水 的 污染 也 不 明显 。摩 擦 学测 试 和 轧 制工 艺 润 滑应 用试 验 数 据 分析 表 明 ,控 制 热 轧油 体 积 分 数 在 l 以下 即可 满 足 热 轧 % 工 艺润 滑 作 用效 果 。 可根 据具 体 轧 制 产 品与 工艺 对 热 轧 油 黏 度 和 用 量 做 出 相应 调 整 ,应 以保 证 C P热 轧生 产平 稳 进 行 S
工艺润滑在热轧带钢生产中的实践

Li inh i Yi oq a a u , n Gu ing J
( h is t e l n i f a g h n I n a d S e l .L d He i a g h n 0 3 6 T eF rt e l S Rol gM l o T n s a o n t e , t . Be n S a 6 01 ) i l r Co T
Ke ywo d - s S e l l t ; o l n t p tc n l g u rc i n r s Ca t t e P ae h t o l g s i ;e h o o yl b a o r i r i t
l 言 前
唐 钢热 轧 C P生 产线 是 国 内第 一 条 以大 批量 S
此 在 轧机 上 采用 了特 殊 的切水 板 设 计 结构 , 即在
主 切水 板上 面在 安装 一个 活动 部 件 ,有 两 个 小气
表 1
缸 推 动 ,在 轧机咬 铡 时伸 出并 以一 定 的压 力 与工 作 辊辊面 接触 , 压紧 力为 7 0 1 0 N, 而保 证 了 0~ 00 从
出了如何提高工艺润滑效果的措施 , 实践证 明, 采用热轧工艺润滑系统对热轧带钢生产薄规格产品, 以获得 良好 可
的 带钢 表 面 质 量 , 降低 了 轧 辊 消耗 。 并 关键 词 : S ; 轧 带 钢 ; 艺润 滑 CP热 工
T c n lg u rc t ni h rd cino Ho RoldS r e h oo yL b iai nt eP o u t o o f t l e ti rcie pP a t c
P a t e h s p o e a s g t e h t o l g l b c in s se o e h a o l g t i s i r d c in p o u t r ci a r v d t t u i o - l u r a o y t m n t e r l n h c h n h r i n it h t i n u p p o u t r d c o s e i c t n a eag o ti u f c u l y a dr d c o s mp i n o r l p cf a i sc n b o d sr s ra eq a i , n e u et c n u t f o 1 i o p t he o .
珠钢热轧机轧制润滑技术研究
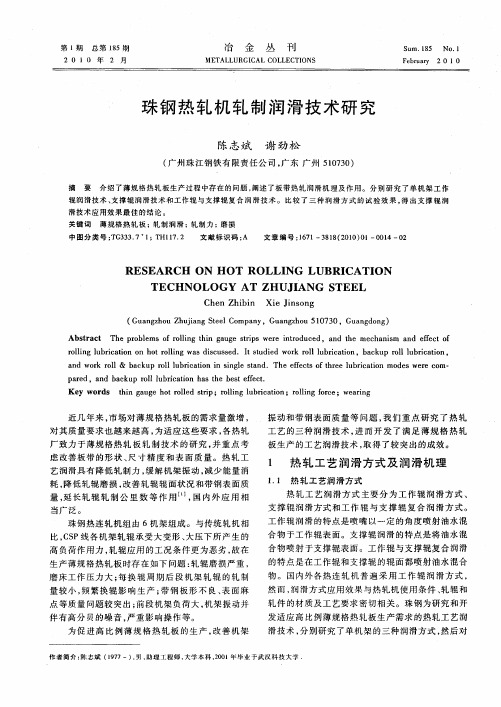
然而 , 润滑 方式应 用效 果与热 轧机 使用 条件 、 轧辊 和
轧件 的材质 及工 艺要求 密切 相关 。珠 钢为研究 和 开
振 动 和带钢 表面质 量 等 问题 , 我们 重 点研 究 了热 轧
工 艺 的三种 润滑技 术 , 而 开 发 了满 足 薄规 格 热 轧 进 板 生产 的工 艺润 滑技术 , 得 了较 突出 的成 效 。 取
1 热 轧 工 艺 润 滑方 式 及 润 滑 机理
1 1 热 轧 工 艺 润 滑 方 式 .
K e o ds t i a g o o ld srp;r li g l b i ain; rli g f re; we rn y w r h n g u e h tr le ti oln u rc to oln o c aig
近几 年来 , 市场对 薄规 格热 轧板 的需求量 激增 , 对 其质 量要求 也越来 越高 , 为适 应这些 要求 , 各热 轧 厂 致力 于薄规 格热 轧 板 轧 制技 术 的研 究 , 重点 考 并 虑 改善板 带 的形 状 、 寸精 度 和 表 面质 量 。热 轧工 尺 艺 润滑具 有降 低轧制 力 , 解机 架振 动 , 缓 减少 能量 消
r l n u rc t n o o oln sdic s e . I su i d wo k r l l b i ain,b c u o ll brc to o l g lb iai n h tr li g wa s u s d t t d e r ol u rc t i o o a k p r l u ia in, a d wo k rl n r ol& b c u o llbrc t n i i ge sa d. T fe t ft r e l b i ain mo e r o a k p r l u i ai n sn l tn o he ef cso h e u rc t d s we e e m— o p r d,a d b c u o ll b ia in h st e tefc . ae n a k p r l u rc t a he b s fe t o
热轧工艺润滑在唐钢1700生产线的应用

。r
》 V
卷取机
一 一 u5 一 弋 j 8 8 { { 8 8 j 8
加热炉 粗轧机
图 1唐钢 1 0 7 0生产线工艺布置
⑩^'.zm tus. 全  ̄s o t属世界 p jc . j w z
呈堡! _ 复塑■ z
维普资讯
台备 用 。
15℃时,板坯出炉 ,首先经过 1Ma高压水 除 20 8p 鳞, 除去氧化铁皮 , 进入带立辊 的可逆粗轧机 , 轧
一
一
n
{ 广) a C1虽 { . 1n f , §, 5 ) 】 — 】- { I l - r - 1
热卷箱 切头剪 尼流,却’ 窜 J
也增加了维护的难度 。这种 情况在澳大利亚和马
来西亚的热轧厂曾经发生过 。改成不锈钢管后情
况得到很好的改善。
() 6热轧油供水采用一个单独 的水箱 : 随着热 轧工艺润滑技术 的发展及越来越普 遍的应用 , 大 部分热 轧工艺润滑 系统 都有独 立的供 水水箱 , 以 便更好、更精确 的调整系统 的工作状态 ,例如水 温、 水压 、 流量等 参数的调整。热轧油供水温度在 冬季偏低也是喷嘴易堵塞 的原因之一 。 () 7喷嘴的维护 : 热轧工艺润滑 系统是一套 比
浓度 的调整不应频繁。
() 2换辊后轧烫辊材时暂停使用轧制油, 待轧
制 3 块钢后 , ~4 再投入轧制油。 () 3投入热轧油时, 由程序控制先 开水泵后开 油泵。 () 4 遇到打滑 、 堆钢时应立 即关闭轧制油。 () 5 由于氧化粉 尘的产 生及 管路 中存在杂质
管, 碳钢管容易被腐蚀生锈 , 产生的铁锈颗粒很容 易造成喷嘴堵塞 , 从而影响工艺润滑 的使用效果,
2024年轧钢安全技术工艺润滑介绍(3篇)
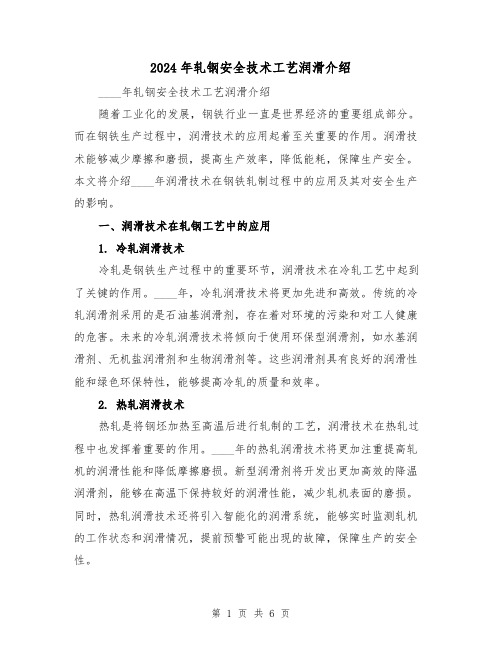
2024年轧钢安全技术工艺润滑介绍____年轧钢安全技术工艺润滑介绍随着工业化的发展,钢铁行业一直是世界经济的重要组成部分。
而在钢铁生产过程中,润滑技术的应用起着至关重要的作用。
润滑技术能够减少摩擦和磨损,提高生产效率,降低能耗,保障生产安全。
本文将介绍____年润滑技术在钢铁轧制过程中的应用及其对安全生产的影响。
一、润滑技术在轧钢工艺中的应用1. 冷轧润滑技术冷轧是钢铁生产过程中的重要环节,润滑技术在冷轧工艺中起到了关键的作用。
____年,冷轧润滑技术将更加先进和高效。
传统的冷轧润滑剂采用的是石油基润滑剂,存在着对环境的污染和对工人健康的危害。
未来的冷轧润滑技术将倾向于使用环保型润滑剂,如水基润滑剂、无机盐润滑剂和生物润滑剂等。
这些润滑剂具有良好的润滑性能和绿色环保特性,能够提高冷轧的质量和效率。
2. 热轧润滑技术热轧是将钢坯加热至高温后进行轧制的工艺,润滑技术在热轧过程中也发挥着重要的作用。
____年的热轧润滑技术将更加注重提高轧机的润滑性能和降低摩擦磨损。
新型润滑剂将开发出更加高效的降温润滑剂,能够在高温下保持较好的润滑性能,减少轧机表面的磨损。
同时,热轧润滑技术还将引入智能化的润滑系统,能够实时监测轧机的工作状态和润滑情况,提前预警可能出现的故障,保障生产的安全性。
3. 真空润滑技术真空润滑技术是指在轧制过程中,在缩小轧机轧制间隙的同时,利用真空技术降低轧机表面的气体压力,减少气体摩擦对轧机表面的影响。
____年,真空润滑技术将得到更加广泛的应用。
真空润滑技术具有润滑效果好、摩擦系数低、轧机使用寿命长等优点,能够提高轧机的工作效率和轧制质量。
真空润滑技术还将结合智能化控制系统,实现对轧机润滑参数的自动调节和监控,提高生产线的智能化程度。
二、润滑技术对轧钢安全生产的影响1. 提高生产效率润滑技术能够减少轧机表面的摩擦和磨损,降低能耗,提高生产效率。
采用先进的润滑技术,可以使轧机工作时的能量损失减少,轧制速度提高。
工艺润滑技术在莱钢1500mm热轧生产线上的应用

2 工 艺 润 滑 系统 工作 原 理及 特 点
2 1 系统 工作 原理 .
自动报 警及 切换 以保 证水 的连续 使 用 。
作者简介 : 张桂南( 9 5一) 男 ,9 7年 7月毕业于华东 冶金学 院压 16 , 18 力加工 专业 , 高级工程师。现为板带 厂技术科科 长。
主 油箱 和供 油箱 有 蒸 汽 加 热及 温度 控 制 , 利 于 油 有
的输 送 和与 水 的混 合 。整 个供 油 系统分 两套 供 油装
置, 每三 台机架 使用一套 供油装置 。每套供 油装 置有
两 台增压 供油泵及 过滤器 , 一备 。高精 度计 量泵 一用
高作业 率 , 能 提 高 带 钢 产 品 的表 面 质 量 。莱 钢 1 并
套 , 别 由喷 嘴 、 合 器 、 分 混 电磁 阀 、 力 调节 装 置 、 压 自 循 环 系统 等组成 , 证 通 过 的油 水 充 分 混合 并 使 润 保
滑 油颗粒 均 匀弥 散 在 水 中形 成 机 械 混 合 状 态 , 短 在 时 间 内不 易 聚合 , 以保 证 获得 良好 均衡 的润 滑效 果 。 喷 嘴采用 不 锈钢 制 作 , 嘴 的 型 式 要保 证 喷 出 的水 喷
O 前 言
工 艺润 滑 技 术是 在 轧 制 的 过程 中 , 向轧 辊 辊 面 喷 射一 种 特 殊 的 润 滑 剂 ( 制 油 ) 通 过 轧 辊 的 旋 轧 ,
由供油 箱 、 油箱 、 泵 、 滤 器 等 组 成 。 主油 主 油 过 箱 有液 位控 制 , 当液 位 降到一 定位 置 时 , 油箱 油泵 供
步提 高 , 品厚 度逐 渐 向薄规 格延 伸 , 产 轧辊 工作 负荷
热轧板带钢工艺润滑的研究

Q —HB一1 5 90
. 2 8 0.
长期 以来 , 水一直作 为热 轧板 带钢 时轧辊 的润滑和冷却介质使
用。 但 随 着 轧 机 向高 速 化 、 续 化 、 连 自动 化 和 大 压 下 量 方 向发 展 , 轧
脂肪油
4 0
由 表 可 看 出 , 肪 油 表 现 出较 好 的 降 低 轧 制 力 的 能 力 , 脂 肪 脂 但
如轧 后钢板表面 的清洁性较差 : 另外脂肪 油在 辊工作负荷明显增加 , 使轧辊 的剥落与磨损加速 , 造成频繁换 辊 , 作 油 也存在致命缺 陷, 高温 条件 下油烟较重 , 恶化工作环境。另外不同种类的添加剂降低 业率降低。水 已远远不能满足热 轧时作为润滑介质 的需要 。 热 轧 工艺 润 滑 的 主 要作 用 轧制压力也 明显不 同, 影响效果如图所 示
科学实践 0
热轧板带钢工艺润滑 的研究
韩彦光 陈同学 ( 钢 衡 薄 限 任公 ) 邯 集团 水 板有 责 司
摘要 : 本文介绍了关于热轧带钢的工艺润滑机 理及其 应用效果 , 同时介
绍了热轧油的种类。本文着重介绍 了采用工艺润滑对节 能降耗 带来 的显著 作用。 关键词 : 工艺润滑 抗乳化性 离水展着性 润湿性
一
11 降低摩擦 系数 , . 降低轧制力 由于磨擦 系数 的减小 ,使轧制 力降低 ,一般 为可 降低 轧制力 1 %一 5 , 0 2 % 这样降低 了轧制功率 , 节约 了能耗 , 。 12 减 少轧辊消耗 , . 提高作业 率
压 下率 热轧条件下 , 作轧辊面 因与冷却水长 期接触发生氧 化 , 工 形成 五 工 艺 润 滑对 轧辊 磨 损 的 影 响 黑皮 , 这是造成轧辊异常磨损的主要原因。采用特殊的润滑剂能够 采用工艺润滑可大大降低轧辊的磨损 , 轧时轧辊应有足够冷 热 有效 阻止辊面黑皮 的形成 , 延长轧辊 使用寿命 , 减少换辊 次数 , 提高 却与润滑。通过现场对 比试验 , 轧制 带钢产量 与轧辊磨损 的关系在 轧机作业率。 不 同 的 轧 制 条件 下 有 很 大 的 差 异 , 图所 示 如 1 . 3改善 轧 后 表 面 质量 轧 轧辊磨损的降低 , 黑皮 的减少直接改善了轧后板面质量。 辊 厝 1 . 4改善制品内部组织性能 掘 深 工 艺 润 滑可以 』 改善, 提高其 中 性能。 度 1 . 能 降 耗 5节 / m 0 1 0 2 0 3 0 4 0 5 O a r 0 0 0O 00 00 00 l —无工艺润滑轧制 —采用工艺澜 采用工 艺润 滑后 ,热 轧吨钢 平均 节 电 3度 ;酸 洗酸 液减 少 带确 产t爪 随轧制量增加 , 轧辊磨损加剧 , 由于磨损 的不均 匀性 , 将严重影 03 .k ; .—1 g 金属消耗降低 1O g-L O .k 车 辊的消耗 能降低 3 %~ 0 0 5 %。 二 热轧 工 艺 润 滑 的 机理 响到轧后的板面质量 , 采用润滑后, 轧辊磨 损的速度要缓慢得多。 通常热轧润滑剂是 以油水混合液 的形 式被送到 轧辊表面 的, 水 采用工 艺润滑后 , 轧辊磨 损大大减 少, 沿辊 身长度上 的磨 损也 1 4 是载体 , 少量 的油均匀分散在水 中。油水混合液的作用过程是水包 变得较为均匀 ,这样对 热轧带钢 的板形 非常有利。下图为 F F 油相向油 包水相 的转变过程。混合液体到达辊面后 , 以水包油的形 4 0连轧机 组轧辊的磨损情况 : 0 式迅速地在辊面展开 , 当进入 变形 区与高温 轧件 接触 时 , 由于 温度 和压 力的作用 , 很快蒸发并转 变成 油包水相 , 水 一部 分油燃烧成 以 灰 分 为主 的燃 烧 物 ; 部 分油 则 以油 膜 的 形 式均 匀 地覆 盖在 轧辊 与 一 轧件 的接触弧面上 , 两者在 变形 区内大约 00 s的时间 内都 能起 到 .1 润滑 的作用。 4 0车 l 上 怍 琨 断 面 膳 璜 囝 一 0 三 热 轧 工艺 润 滑 剂 的选 用 实践 表明 , 采用微量 的润滑剂完全可 以达到降低轧辊磨损的 目 3 1 热@ z艺润滑剂的性 能 . L 的,轧辊的润滑效 果及磨损程 度并不是 与润滑剂用量 及浓度成正 311良好且稳定 的润滑性能 .. 比, 相反 , 滑剂的用量过大 , 润 会造成打滑 、 轧件咬入困难 , 同时造成 31 .. 2良好 的润湿性和黏着性 ,能均匀地分散在 轧辊表 面并牢 污 染 。 六 存 在 的 问题 固地黏 着 。 313高温下 良好的抗氧化性和耐分解性 ,保证在 与轧件 接触 .. 热轧带钢采用工艺润 滑后 , 使轧件 的咬入条件发生变化. 不利于 前不产生燃烧和 分解 。  ̄i 的顺利 咬入, 以通过间歇供油 的方式来解决。 L- C - 可 由于采用润滑后 31 .. 4良好 的抗乳化性和 离水展着性。 摩擦 系数 的下降 , 对板 宽、 厚将产生很 大影响 , 板 且不 易控 制 , 可在 315无毒 无味, .. 同时分解 中产生的气体也无毒无 味 , 燃烧产 物 条件成 熟时采用 A GC厚 度 自动控制系统 ,对厚 度精度 进行有效 控 无毒 , 不污 染 环 境 。 制, 且能获得更加 良好的板形。此外由于轧制油的燃烧 , 使工人恶劣 32热轧工艺润滑剂 的组成及种类 . 的工作 条件 比以前有所加剧 , 间油烟较大 , 车 需专设排烟系统 。 热轧油有水基 硒由 基两种形式, 目前大部分厂家采用油基热#油。 L 参 考 文献 : 【】 1贺毓辛 现代轧制理论 北京 冶金 工业出版社 1 9 93 般热 轧油 由基础油和油性剂两部 分组成 ,基础油有矿物油 、
- 1、下载文档前请自行甄别文档内容的完整性,平台不提供额外的编辑、内容补充、找答案等附加服务。
- 2、"仅部分预览"的文档,不可在线预览部分如存在完整性等问题,可反馈申请退款(可完整预览的文档不适用该条件!)。
- 3、如文档侵犯您的权益,请联系客服反馈,我们会尽快为您处理(人工客服工作时间:9:00-18:30)。
热轧工艺润滑技术(一)工艺润滑机理及应用1前言热轧工艺润滑技术1957首先在美国获得成功应用,板带热轧机上的运用已有较长的历史,日本应用该技术已超过30年,宝钢1580mm,2050mm热轧在90年代已应用此技术。
采用热轧润滑技术,不仅可以降低能耗,提高生产率,降低轧辊成本和改善带钢表面质量,而且可使带钢的晶粒组织得以改善,使之具有理想的深冲性能。
随着产品品种扩大,用户对产品要求提高,短流程连铸连轧工艺的发展以及市场对厚度小于1mm热轧带钢需求的增加,热轧润滑技术已引起广泛注意并得到普遍应用。
目前,随着高速钢轧辊的使用,热轧润滑技术更显得重要。
实践证明,如果采用高速钢轧辊,在同样条件下,轧制力有所增加;欲减少轧制力,热轧润滑是最有效的手段。
在日本,欧洲等多家工厂正在研究热轧润滑的生产应用。
在欧洲,世界上轧制润滑油生产的主要厂商正与钢厂合作研究“高速钢轧辊和热轧工艺润滑”这一课题。
2热轧工艺润滑机理及作用2.1 热轧工艺润滑机理热轧工艺润滑是一个动态过程,在变形区高温,高压,高速状态下润滑油所起的变化难以实验模拟,其中一种意见认为热轧时,在辊缝中严酷的工作条件下,轧辊表面极易磨损,因而导致表面产生凹坑和麻点;而凹坑和麻点又加剧磨损,造成恶性循环,轧辊因磨损而迅速报废。
如果能在轧件进入辊缝之前,在轧件表面喷涂润滑物质,形成润滑膜,尽管这层膜有一小部分可能在进入辊缝前即被高热的轧件烧掉,但大部分还是被咬入辊缝,在工作辊和轧件的接触面上形成一层薄薄的润滑膜。
虽然油膜与轧辊的接触时间只有百分之几秒的暂短瞬间,但是油膜在烧掉之前可以起到润滑作用,可减轻轧辊磨损,避免很快出现凹坑和麻点。
由于现代热轧工艺特点是高温,高压,高速,热轧工作辊辊面瞬时温度可达600∽700℃,经冷却散热而稳定在50∽80℃,因此,为适应热轧工艺特点,热轧润滑油应具有以下特性:(1)具有高极性分子的构成,在轧辊表面有极好的湿润性,可迅速形成均匀的薄层润滑膜,降低摩擦,减少磨损。
(2)润滑膜粘着力强,具有瞬时抗高压能力,可在辊缝中提供稳定而极好的润滑,可防止或减少在工作辊和支撑棍上形成氧化物。
(3)在辊缝中润滑膜可阻止轧辊和轧件的直接接触,避免在高温下轧辊和轧件间形成粘着。
(4)轧机出口带钢上的残余润滑油要在尽可能短的时间内燃烧尽,防止残油遗留在带钢表面上,形成新的污染物。
(5)润滑油有具高的闪点和热分解稳定性。
2.2 热轧工艺润滑的作用在热轧轧制中应用润滑技术具有明显的优越性:(1)可降低热轧时轧辊与轧件间的摩擦系数无润滑时的摩擦系数一般为0.35。
采用有效润滑时的摩擦系数可降至0.12。
(2)可降低轧制力,容易轧制薄规格带钢一般可降低轧制力10%~25%,从而降低了能耗。
(3)可减少轧辊消耗和储备,提高作业率在热轧条件下,工作辊与带钢和冷却水接触会生成Fe3O4和Fe2O3等硬度很大的氧化物,其粘在轧辊表面,使轧辊生成黑暗色的表面,即黑皮。
黑皮是造成轧辊异常磨损的主要原因。
采用热轧润滑后,轧辊与轧件之间被一层边界润滑膜隔开,可防止轧辊表面产生黑皮,减少轧辊磨损,延长工作辊的使用周期;可减少换辊时间,提高轧制作业率,减少工作辊储备量。
同时也减少了支撑辊的磨损和储备量。
(4)可减少氧化皮压入,改善轧辊表面状态采用热轧润滑后,由于轧辊与轧件之间被一层润滑膜隔开,防止轧辊表面黑皮产生,因而提高了产品的表面质量,也提高了酸洗效率。
(5)可延长轧制公里数,减少换辊次数,增加作业时间。
3 .热轧工艺润滑出现和应用背景3.1 热轧轧辊材质的改变及热轧工艺润滑的出现近年来,市场对热轧板带的质量要求越来越高。
为了适应这一需求,生产厂商大力开发新品种,生产特殊钢、高强度钢、易加工钢和极薄带钢等产品,并致力于全面提高板带的行状、尺寸精度和表面质量,因而出现了HC轧机,PC轧机, CVC轧机等新型轧机。
为了提高生产率,出现了连铸连轧、自由规格轧制、粗—精轧连续轧制(无头轧制)、高速连轧等新的轧制方法。
随着这些技术和设备的日益成熟和应用范围的扩大,热轧工作辊的工作条件将越来越严酷,而为了保证质量,提高作业率,又要求轧辊耐用,具有长寿命。
为了达到这一要求,人们首先致力于开发新材质的高耐磨轧辊,以延长轧辊使用周期。
同时,将减少轧辊磨损、延长其使用寿命的研究作为重点。
在这种背景下,热轧润滑得到了日益增多的研究和应用。
精轧机前几架,对于轧辊的耐表面缺陷性能要求很高。
在轧制薄规格、超低碳钢等高负荷条件下,轧辊易出现表面缺陷,轧制不锈钢时易出现辊面热粘着。
对于精轧机的后几架,轧辊的耐表面缺陷性能最重要。
因此,在轧辊材质方面,要进行不断的改进。
到20世纪80年代以前,精轧机组的前几架主要使用高碳镍铬耐磨辊和高铬工作辊。
自90年代起,开始使用高速钢轧辊,最近先进的热轧机几乎全部使用高速钢轧辊。
精轧机组的后几架,在八九十年代主要是使用高碳镍铬铸铁耐磨辊,目前主要使用高速钢轧辊。
粗轧机组的轧辊在要求耐磨、耐表面缺陷的同时,还要求良好的咬入性能。
原来以高镍铬锻钢辊为主,近年来也开始试用高速钢轧辊。
到目前为止,对于板带热精制机组,高速钢轧辊具有良好的耐磨、耐表面缺陷及强韧性等优良的综合性能,其使用范围日益扩大。
由于其高温硬度、耐磨性、耐表面缺陷及强韧性均很高,轧辊平均寿命是原来各种材质轧辊的3~7倍,因而可保证轧件的表面质量,提高板厚精度。
由于其耐磨性好,可抗局部磨损,便于实现自由规程轧制。
而且,使换辊次数减少,作业时间延长,作业率提高,并减少了轧辊消耗和储备。
广泛使用高速钢轧辊,是轧制工具的一个明显的进步。
但是,高速钢轧辊也有明显的缺点,即摩擦系数大,辊面凸度难于控制。
由于摩擦系数大,则轧制力大,采用高速钢轧辊,在同样条件下,会使轧制力增加10%~20%;欲减少轧制力,保证设备负荷,采用热轧工艺润滑是最有效的手段,如果使用高速钢轧辊,则更需要采用热轧工艺润滑。
3.2 热轧工艺润滑的特殊要求在热轧工艺润滑的开始阶段,并没有专用的热轧润滑油,只是使用普通矿物油加动物油作为热轧润滑油。
而且没有根据不同的轧机、轧件的材质和轧辊材质对润滑油进行选择,而是只要具有良好的给油稳定性、良好的润湿性和附着性即可。
随着轧制技术的进步,轧辊和轧件质量的提高,对热轧润滑油的要求开始细化,并且要求越来越高。
自80年代开始,陆续出现了各种性能不同的专用热轧工艺润滑油。
如QUAKER公司的N HB–18–H–1,和QUAKER HB–18KT两种油品分别用于精轧前后机架,根据油品不同,被选择用于粗轧、精轧前几架,或是精轧后几架;用于高速轧制,或是高润滑轧制;而且对油的浓度也进行探索,各有不同,2050mm 热轧油的浓度为3%,而1580热轧油的浓度为0.4%,对应于不同的轧辊材质,考虑主要是用于轧制一般钢材时防止热粘着,还是用于轧制不锈钢材时防止热粘着,根据不同品种。
90年代后期,随着高速钢轧辊进入生产实用,又出现了专门适用于该种轧辊的热轧润滑油。
表1是按照热粗轧、热精轧前几架、后几架区分的轧制负荷条件及轧辊磨损情况统计。
在热粗轧和热精轧前几架容易因氧化铁皮而产生黑皮,形成表面缺陷,轧制不锈钢时易产生热粘着。
热精轧后几架不产生氧化铁皮,以磨损为主。
对不同的轧制条件,选择适用的轧辊材质,例如:使用高镍铬和高铬轧辊时,氧化铁皮形成的黑皮可以提高轧辊的耐表面缺陷性能和耐磨损性能,因此要尽量利用黑皮。
图1是各种材质的轧辊和黑皮的高温硬度。
黑皮的高温硬度很高,具有良好的耐磨损性能。
但是如果黑皮过度增厚,则易形成龟裂和剥落,造成更严重的轧辊表面缺陷,高速钢轧辊具有很高的高温硬度,与黑皮相接近,即使没有黑皮也有良好的耐磨性能,所以高速钢轧辊要控制黑皮的形成。
氧化铁皮具有耐磨性能,但是容易形成辊面缺陷。
在轧制薄规格不锈钢时,由于氧化铁皮易落入辊缝中,造成板面麻点,因此,要求根据不同的轧制轧件材质,选用适宜的热轧润滑油.表1 热粗轧、精轧的工作辊负荷和磨损情况统计轧辊的表面损伤表面损伤剥落形成黑皮-脱落轧不锈钢热粘着其他表面缺陷—容易产生黑皮—粗轧后段产生凹坑其他轧辊表面缺陷因轧辊材质和负荷条件不同而不同多发生于精轧的前几架不产生黑皮多发生于精轧的前几架精轧后段产生凸凹裂纹和咬入热冲击折叠轧件厚时因咬入冲击形成——折叠多发生于精轧后段磨损在精轧的后段磨损严重热轧工艺润滑对于减轻轧制负荷和减少轧辊磨损有明显的作用。
随着产品表面质量要求的提高,热轧润滑对于现代化板带轧制的作用日益重要。
(二)热轧润滑效果1 热轧工艺润滑在我国的应用效果热轧工艺润滑在我国已得到广泛应用,它的效果也被大家认可,现以我国某厂板带热连轧机采用热轧工艺润滑技术后所取得明显效果为例,见表2。
从表2可以看出,辊耗降低50%。
同时,也降低了轧制力和轧制力矩,见表3。
表2 我国某厂热连轧机使用润滑前后工作辊磨损情况注:使用轧制油时轧制重量1297t,轧制长度47.6km; 未使用轧制油:时轧制重量1230t,轧制长度42.0km。
表3热连轧机使用润滑前后的轧制力和主电机电流对比注:有润滑:来料厚度40mm,宽度1263mm,成品厚度2.03mm,宽度1233mm;最大轧制速度16.48m/s。
无润滑:来料厚度40mm,宽度1055mm,成品厚度2.03mm,宽度1025mm;最大轧制速度16.48m/s。
采用热轧润滑后明显降低轧辊磨损,换辊一次的轧制量可以增加40%~50%,每天可以减少换辊次数1.5次,年纯轧时间增加112h。
使用润滑后,钢板表面的氧化皮细孔状况大为改善,明显提高了产品的表面质量,减少酸洗时间和耗酸量。
按年轧制240万t钢板,每吨钢消耗轧制油0.16L计算,去掉购买轧制油的费用后,直接减少轧辊采购费用和电费1800万元。
将提高作业率和提高产品表面质量的效益计算上去,年总经济效益超过4000万元。
我国热轧工艺润滑自1996年宝钢1580 mm热轧引进日本三菱技术,同时也引进了热轧工艺润滑技术和设备,接着宝钢2050mm热轧,珠钢连铸连轧,鞍钢1780mm热轧,一钢1780mm热轧,攀钢1450 mm热轧,梅山1422 mm热轧,太钢1549 mm热轧等等也相继采用了热轧工艺润滑技术,现把她们的应用效果列表4如下:表4热轧工艺润滑使用主要效益指标2.热轧工艺润滑在国外的应用效果国外采用工艺润滑也非常普遍,如新日铁系统的大分,君津,名古屋,八幡,室兰等厂,住友鹿岛厂,川崎制铁的和歌山,千叶厂以及英钢联,美钢联等也采用,现以瑞典SSAB厂热轧润滑为例,见表5所示:表5瑞典SSAB钢厂热连轧机使用工艺润滑前后的轧制力对比表以上仅是SSAB厂热轧工艺润滑的经验,其它新日铁,川崎,住友,美钢联,英钢联等也有不少成绩,列表6如下:表6国外热轧厂工艺润滑的效益指标从以上表格可以说明不论中国还是国外热轧工艺润滑效果是十分明显的,是值得可以大力推广的新技术。