技术图纸要求
图纸上的技术要求汇总
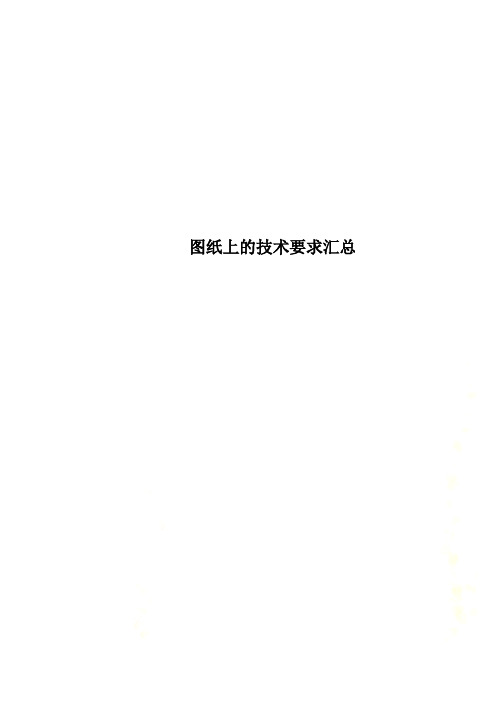
图纸上的技术要求汇总图纸技术要求一、一般技术要求制件去除表面氧化皮;制件不得有划痕、擦伤等损伤零件表面的缺陷;去除毛刺飞边;锐角倒钝;未注倒角均为0.5×45%%d;未注越程槽均为1.2×0.3;表面平整无毛刺;二、未注公差技术要求(金属件)未注公差尺寸的极限偏差按GB/T 1804-m;未注形位公差按GB/T 1184-K;未注长度尺寸允许偏差±0.5;三、表面处理技术要求表面镀白(黑)锌处理;表面喷漆(喷塑)处理;表面发黑处理;表面电泳处理;表面镀铬处理;表面抛光处理;表面滚花,直纹(网纹)m=0.4 GB/T 6403.3;四、热处理技术要求制件氮化450-480HV;制件毛坯须调质处理220-260HB;制件调质处理30-35HRC;制件高频淬火45~50HRC;制件渗碳处理,深度>0.1;制件进行高温回火处理;制件整体淬火40-45HRC;五、铸件技术要求1、压铸件技术要求未注公差尺寸的极限偏差按GB/T 1804-m;未注形位公差按GB/T 1184-K;未注倒角均为0.5×45%%d;未注壁厚2.5;未注筋板1.5~2;未注过渡圆角R0.5-R2;未注脱模斜度≤1%%d;制件饱满光洁、无气孔、缩松、裂纹、夹渣、缺料等缺陷;各脱模顶料推杆压痕均应低于该制件表面0.2;制件要求符合GB/T 15114《铝合金压铸件》标准规定;表面喷漆(喷塑)处理,不得污染到已加工表面;加工表面在表面处理后加工,加工后涂油保护;未注尺寸参照三维造型;制件表面处理及其它要求按客户定;2、砂型铸造技术要求未注铸造圆角R5-10;铸件应彻底清砂,浇冒口应清除平整;铸件需人工时效;铸件不得有砂眼、气孔、缩松、裂纹等缺陷;粗加工后应再次进行人工时效;不加工表面涂底漆;六、冲压件技术要求制件未注公差尺寸的极限偏差按GB/T 15055-m;制件未注形位公差按GB/T 13916-2级;制件不得有裂纹或缺损;制件表面平整,不得有沟痕、碰伤等损坏表面,降低强度及寿命的缺陷;去除边角毛刺;表面处理:七、塑料件技术要求未注公差尺寸的极限偏差按GB/T 14486-MT6级;制件应饱满光整、色泽均匀;无缩痕、裂纹、银丝等缺陷;浇口、溢边修剪后飞边≤0.3,且不得伤及本体;未注壁厚3;未注筋板1.5~2;表面打光(喷砂)处理;未注过渡圆角取R0.3~R1,脱模斜度≤0.3%%d;各脱模顶料推杆压痕均应低于该制件表面0.2;与对应装配结合面外形配合错位≤0.5;制件应进行时效处理;制件机械强度须符合GB 3883.1标准规定;制件内腔表面打上材料标记和回收标志;未注尺寸参照三维造型;制件表面处理及其它要求由客户定;八、焊接件技术要求未注公差线性及角度尺寸的极限偏差均按GB/T 19804-B级;未注形位公差按GB/T 19804-F级;焊缝应均匀平整,焊渣清理干净;焊缝应焊透,不得烧穿及产生裂纹等影响机械性能的缺陷;九、各类零、部件技术要求1、齿轮(齿轴)技术要求未注公差尺寸的极限偏差按GB/T 1804-m;未注形位公差按GB/T 1184-K;制件毛坯须调质220~260HB;制件材料的化学成分和力学性能应符合GB/T 3077的规定;齿面接触斑点:按齿高不小于40%,按齿长不小于50%;齿面高频淬火回火至49-52HRC;制件表面不应有锈迹、裂纹、灼伤等影响使用寿命的伤痕及缺陷;最终工序热处理表面不得有氧化皮;2、一般轴芯(无铣齿)技术要求未注公差尺寸的极限偏差按GB/T 1804-m;未注形位公差按GB/T 1184-K;未注倒角均为0.5×45%%d;未注越程槽均为1.2×0.3;制件毛坯须调质220~260HB;尺寸%%c 档车正反两条螺旋槽,螺距10,深0.4;螺纹表面不允许有磕碰、乱扣、毛刺等缺陷;热处理:表面处理:3、包轴毛坯(一次成型)技术要求未注公差尺寸的极限偏差按GB/T 1804-m;未注形位公差按GB/T 1184-K;绝缘层应饱满光洁,无裂纹、气孔、缺料、杂质等缺陷;包轴毛坯:绝缘层%%c 档(注:指冲片配合档)与轴芯间应能承受50Hz,实际正弦波电压2500V历时1min不击穿,其余绝缘层档3750V历时1min不击穿;一次成型:铁芯与轴芯间应能承受50Hz,实际正弦波电压2500V历时1min不击穿,其余绝缘层档3750V历时1min不击穿;4、包轴(加工)技术要求未注公差尺寸的极限偏差按GB/T 1804-m;未注形位公差按GB/T 1184-K;塑层应饱满光洁,无裂纹、气孔、缺料、杂质等缺陷;塑层%%c 档(注:指冲片配合档)与轴芯间应能承受50Hz,实际正弦波电压2500V历时1min不击穿,其余塑层档3750V历时1min不击穿;制件磨加工后应烘干除水处理;5、转子技术要求未注公差尺寸的极限偏差按GB/T 1804-m;未注形位公差按GB/T 1184-K;绕组接线按转子绕线原理图;绕组绝缘漆应均匀充满绕组并充分固化,漆膜应均匀无气泡或裂痕;云母槽开深0.8~1,槽宽0.6,槽内不得残留云母片;绕组冷态绝缘电阻不低于50MΩ;装风叶后校动平衡,其精度应不低于G6.3级;去重不允许有冲片铣穿、残缺现象;铁芯外圆不加工,绝缘漆不得高出铁芯外圆,并不得有明显积瘤;铁芯与轴芯间应能承受50Hz,实际正弦波电压2500V,1min不击穿;绕组与铁芯间应能承受50Hz,实际正弦波电压1250V,1min不击穿;匝间绝缘应能承受1000Hz,峰值为2100V,历时3s不击穿;换向器与轴芯间应能承受50Hz,实际正弦波电压3750V,1min不击穿;应去除铁屑、铜粉、油污等杂质;铁芯外圆应涂透明淡金水防锈处理;6、定子技术要求绕组绕制整齐无松散;引线接头应牢固可靠且充分绝缘;绕组与铁芯间应能承受50Hz,实际正弦波电压1250V历时1min不击穿;匝间绝缘应能承受1000Hz,峰值为2100V,历时3s不击穿;绕组绝缘漆应均匀充满绕组并充分固化,漆膜应均匀无气泡或积瘤;铁芯表面不得有明显绝缘漆;7、定、转子铁芯技术要求未注公差尺寸的极限偏差按GB/T 1804-m;未注形位公差按GB/T 1184-K;冲片叠装应紧密可靠,片间无夹杂,表面及槽内无污物和油渍;冲片按同一冲制方向压装;冲片齿槽口整齐与转轴平行,误差不大于0.5;铁芯两端弹开度不大于0.5;8、定、转子冲片技术要求制件未注公差尺寸的极限偏差按GB/T 15055-m;制件未注形位公差按GB/T 13916-2级;制件应表面平整,完整无缺料;尖角处允许用R0.3过渡;制件毛刺不大于0.05(注:高速冲时不大于0.02);制件应不含油脂,剪切油不能用机油;9、绝缘纸技术要求表面不得有划痕、折痕;裁边不起毛;10、换向器技术要求未注公差尺寸的极限偏差按GB/T 1804-m;未注形位公差按GB/T 1184-K;外观完整,表面光滑,应无裂纹、毛刺、锈蚀、气孔、夹杂等缺陷;绝缘电阻:室温下内孔与换向片之间大于50MΩ;云母片厚度取0.5;换向片对换向器轴线偏斜度不大于云母片厚度的1/3;介电强度:片间承受频率50Hz,泄露电流为0.1mA,实际正弦波电压600V历时1s不击穿;换向片与内孔轴芯间承受频率50Hz,泄露电流为0.25mA,实际正弦波电压3750V历时1min不击穿;试验与检验应符合JB/T 10107《电动工具换向器》标准要求;11、电缆线技术要求电缆线长度尺寸指工具电缆出口至插头的导线部分,不包括插头和插脚;软电缆应符合GB/T 5013《额定电压450V/750V及以下橡皮绝缘电缆》标准要求;聚氯乙烯电缆应符合GB/T 5023《额定电压450V/750V及以下聚氯乙烯绝缘电缆》标准要求;插脚与可触及插头表面的绝缘应能承受50Hz,实际正弦波电压3750V历时1min不击穿;制件还应符合GB 1002《家用和类似用途单相插头插座型式、基本参数和尺寸》和GB 2099《家用和类似用途插头插座》标准要求;12、开关技术要求未注公差尺寸的极限偏差按SJ/T 10628-7级;除本图要求的外形尺寸、功能、图形、文字外,试验和检验均应符合GB/T 22692《电动工具开关》标准要求;开关的使用性能应保证5万次无故障正常使用;13、电缆护套技术要求未注公差尺寸的极限偏差按GB/T 3672.1-2级;未注形位公差按GB/T 3672.2-M级;制件不得有缺料、破裂等缺陷。
图纸技术要求文本
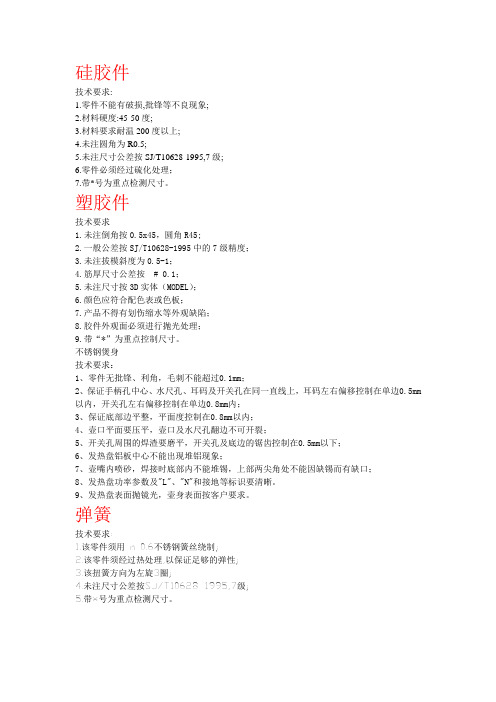
硅胶件技术要求:1.零件不能有破损,批锋等不良现象;2.材料硬度:45-50度;3.材料要求耐温200度以上;4.未注圆角为R0.5;5.未注尺寸公差按SJ/T10628-1995,7级;6.零件必须经过硫化处理;7.带*号为重点检测尺寸。
塑胶件技术要求1.未注倒角按0.5x45,圆角R45;2.一般公差按SJ/T10628-1995中的7级精度;3.未注拔模斜度为0.5-1;4.筋厚尺寸公差按#0.1;5.未注尺寸按3D实体(MODEL);6.颜色应符合配色表或色板;7.产品不得有划伤缩水等外观缺陷;8.胶件外观面必须进行抛光处理;9.带“*”为重点控制尺寸。
不锈钢煲身技术要求:1、零件无批锋、利角,毛刺不能超过0.1mm;2、保证手柄孔中心、水尺孔、耳码及开关孔在同一直线上,耳码左右偏移控制在单边0.5mm 以内,开关孔左右偏移控制在单边0.8mm内;3、保证底部边平整,平面度控制在0.8mm以内;4、壶口平面要压平,壶口及水尺孔翻边不可开裂;5、开关孔周围的焊渣要磨平,开关孔及底边的锯齿控制在0.5mm以下;6、发热盘铝板中心不能出现堆铝现象;7、壶嘴内喷砂,焊接时底部内不能堆锡,上部两尖角处不能因缺锡而有缺口;8、发热盘功率参数及"L"、"N"和接地等标识要清晰。
9、发热盘表面抛镜光,壶身表面按客户要求。
弹簧技术要求:1.该零件须用n0.6不锈钢簧丝绕制;2.该零件须经过热处理,以保证足够的弹性;3.该扭簧方向为左旋3圈;4.未注尺寸公差按SJ/T10628-1995,7级;5.带*号为重点检测尺寸。
图纸技术要求大全

图纸技术要求大全在工程和制造领域,图纸是至关重要的沟通工具,它能够清晰地传达设计意图和规范,确保产品或项目的顺利实施。
而图纸上的技术要求则是对设计的进一步补充和说明,为生产、加工、检验等环节提供了明确的指导。
下面我们就来详细了解一下图纸技术要求的方方面面。
一、尺寸与公差要求尺寸是图纸中最基本的元素之一,它准确地描述了零件或结构的大小和形状。
在标注尺寸时,需要遵循一定的标准和规范,确保尺寸的清晰、准确和完整。
同时,为了保证零件在制造过程中的互换性和功能性,还需要规定公差。
公差是允许尺寸的变动量,分为尺寸公差和形位公差。
尺寸公差控制零件的尺寸精度,形位公差则控制零件的形状和位置精度。
例如,对于一个圆柱形零件,不仅要规定其直径的尺寸和公差,还要规定圆柱度、同轴度等形位公差要求。
二、材料要求材料的选择直接影响到产品的性能、质量和成本。
在图纸技术要求中,需要明确指定所使用的材料种类、牌号、规格等信息。
例如,对于机械零件,可以指定使用 45 号钢、铝合金等材料,并注明其热处理要求,如淬火、回火等。
对于建筑结构,可能会指定使用混凝土的强度等级、钢材的型号等。
此外,还需要考虑材料的供应情况和成本,选择合适的替代材料方案。
三、表面处理要求表面处理可以提高零件的耐腐蚀性、耐磨性、美观度等性能。
常见的表面处理方法包括电镀、喷涂、氧化等。
在图纸技术要求中,需要明确表面处理的种类、工艺要求和质量标准。
例如,对于需要防锈的零件,可以要求进行镀锌处理,并规定镀层的厚度和质量要求。
对于外观要求较高的零件,可以进行喷漆处理,并指定漆的颜色、光泽度等要求。
四、加工工艺要求加工工艺是将原材料转化为成品的过程,它直接影响到产品的质量和生产效率。
在图纸技术要求中,需要根据零件的结构和功能,规定合理的加工工艺方法和顺序。
例如,对于一个复杂的零件,可能需要先进行铸造或锻造,然后再进行机械加工。
对于有精度要求的孔和轴,可能需要采用磨削加工工艺。
工程图纸技术要求
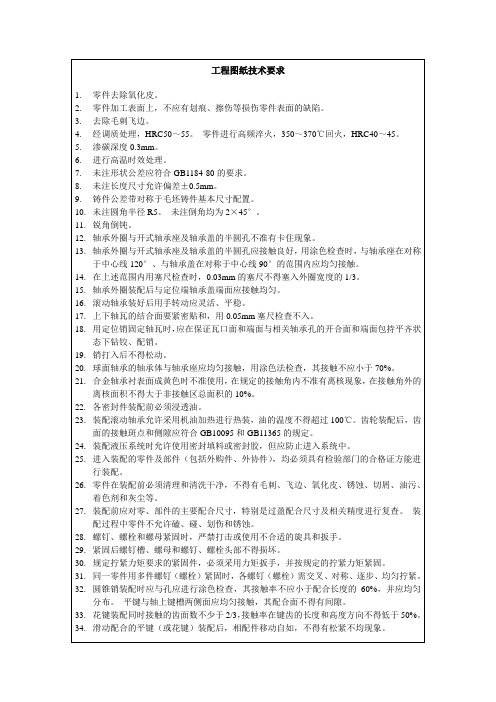
工程图纸技术要求1.零件去除氧化皮。
2.零件加工表面上,不应有划痕、擦伤等损伤零件表面的缺陷。
3.去除毛刺飞边。
4.经调质处理,HRC50~55。
零件进行高频淬火,350~370℃回火,HRC40~45。
5.渗碳深度0.3mm。
6.进行高温时效处理。
7.未注形状公差应符合GB1184-80的要求。
8.未注长度尺寸允许偏差±0.5mm。
9.铸件公差带对称于毛坯铸件基本尺寸配置。
10.未注圆角半径R5。
未注倒角均为2×45°。
11.锐角倒钝。
12.轴承外圈与开式轴承座及轴承盖的半圆孔不准有卡住现象。
13.轴承外圈与开式轴承座及轴承盖的半圆孔应接触良好,用涂色检查时,与轴承座在对称于中心线120°、与轴承盖在对称于中心线90°的范围内应均匀接触。
14.在上述范围内用塞尺检查时,0.03mm的塞尺不得塞入外圈宽度的1/3。
15.轴承外圈装配后与定位端轴承盖端面应接触均匀。
16.滚动轴承装好后用手转动应灵活、平稳。
17.上下轴瓦的结合面要紧密贴和,用0.05mm塞尺检查不入。
18.用定位销固定轴瓦时,应在保证瓦口面和端面与相关轴承孔的开合面和端面包持平齐状态下钻铰、配销。
19.销打入后不得松动。
20.球面轴承的轴承体与轴承座应均匀接触,用涂色法检查,其接触不应小于70%。
21.合金轴承衬表面成黄色时不准使用,在规定的接触角内不准有离核现象,在接触角外的离核面积不得大于非接触区总面积的10%。
22.各密封件装配前必须浸透油。
23.装配滚动轴承允许采用机油加热进行热装,油的温度不得超过100℃。
齿轮装配后,齿面的接触斑点和侧隙应符合GB10095和GB11365的规定。
24.装配液压系统时允许使用密封填料或密封胶,但应防止进入系统中。
25.进入装配的零件及部件(包括外购件、外协件),均必须具有检验部门的合格证方能进行装配。
26.零件在装配前必须清理和清洗干净,不得有毛刺、飞边、氧化皮、锈蚀、切屑、油污、着色剂和灰尘等。
技术图纸管理制度

技术图纸管理制度一、背景技术图纸是企业在产品开发和生产过程中不可或缺的重要文档。
有效的技术图纸管理制度对于提高工程质量、降低成本、加强沟通协调具有重要意义。
为了规范技术图纸的编制、审批、发布和变更流程,确保技术图纸的准确性和可靠性,制定本技术图纸管理制度。
二、适用范围本制度适用于企业内部所有与技术图纸编制、审批、发布和变更相关的部门和人员。
三、技术图纸编制1.技术图纸的编制由专业的技术人员负责,确保技术图纸的准确性和规范性。
2.技术图纸应按照标准格式进行编制,包括图纸编号、名称、版本号、日期等基本信息,符号、尺寸、材料等详细规范。
3.技术图纸应根据实际需要设定图框和图幅,确保图纸的清晰易读。
四、技术图纸审批1.技术图纸的审批由专门的审批人员进行,确保技术图纸的合规性和可行性。
2.技术图纸的审批流程应明确,包括审批人员及其权限、审批意见记录、审批结果等内容。
3.技术图纸应经过逐级审批,确保每一级审批人员都对图纸内容进行仔细审核。
审批人员对图纸内容有异议时,应提出修改意见或反馈意见,并及时沟通解决。
五、技术图纸发布1.技术图纸的发布应由专门的发布人员进行,确保技术图纸的有效传达和使用。
2.技术图纸应在适当的平台上进行发布,确保相关人员可以方便地查看和下载图纸。
3.技术图纸的发布应及时更新,确保使用的是最新版本的图纸。
六、技术图纸变更1.在产品开发和生产过程中,技术图纸可能需要进行变更,变更应由专门的变更人员进行。
2.技术图纸的变更应经过严格的流程,包括变更申请、变更审批、变更发布等环节。
3.技术图纸的变更应及时通知相关人员,确保变更后的图纸能够及时被采用并替代原有图纸。
七、技术图纸存档1.已经发布和废弃的技术图纸应进行存档,确保技术资料的完整性和可追溯性。
2.存档的技术图纸应分类清晰,包括原始图纸、修改图纸、废弃图纸等不同类型。
3.存档的技术图纸应采取适当的措施进行保护,防止遭到不良环境或非授权人员的损害和篡改。
施工技术图纸控制要求
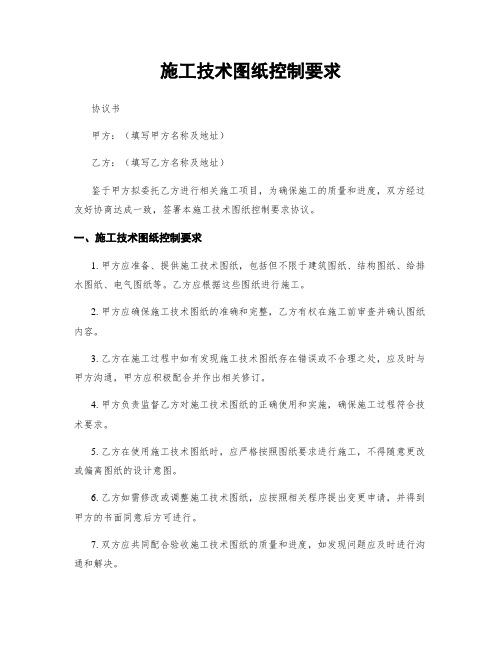
施工技术图纸控制要求协议书甲方:(填写甲方名称及地址)乙方:(填写乙方名称及地址)鉴于甲方拟委托乙方进行相关施工项目,为确保施工的质量和进度,双方经过友好协商达成一致,签署本施工技术图纸控制要求协议。
一、施工技术图纸控制要求1. 甲方应准备、提供施工技术图纸,包括但不限于建筑图纸、结构图纸、给排水图纸、电气图纸等。
乙方应根据这些图纸进行施工。
2. 甲方应确保施工技术图纸的准确和完整,乙方有权在施工前审查并确认图纸内容。
3. 乙方在施工过程中如有发现施工技术图纸存在错误或不合理之处,应及时与甲方沟通,甲方应积极配合并作出相关修订。
4. 甲方负责监督乙方对施工技术图纸的正确使用和实施,确保施工过程符合技术要求。
5. 乙方在使用施工技术图纸时,应严格按照图纸要求进行施工,不得随意更改或偏离图纸的设计意图。
6. 乙方如需修改或调整施工技术图纸,应按照相关程序提出变更申请,并得到甲方的书面同意后方可进行。
7. 双方应共同配合验收施工技术图纸的质量和进度,如发现问题应及时进行沟通和解决。
8. 如乙方在施工过程中遇到施工技术图纸不明确或存在矛盾之处,应及时向甲方反馈,并等待甲方确认后再进行施工。
9. 双方应确保施工技术图纸的保密,未经对方书面同意,不得向第三方披露或使用。
二、违约责任1. 如甲方未按照约定提供准确和完整的施工技术图纸,或未配合乙方修订图纸,甲方应承担由此引起的一切责任和损失。
2. 如乙方未严格按照施工技术图纸进行施工,或未经甲方书面同意随意更改图纸内容,乙方应承担由此引起的一切责任和损失。
三、协议的生效与解除1. 本协议自双方签字之日起生效,并在施工期内持续有效。
2. 如因不可抗力等不可预见的原因无法履行本协议,一方应及时通知对方,并在合理的时间内协商解决方式。
3. 本协议解除时,双方应互相清算,结算相关款项,并相互确认无其他未尽事宜。
四、争议解决双方如因本协议引起争议,应通过友好协商解决;若协商不成,应提交甲方所在地有管辖权的人民法院进行诉讼解决。
图纸通用技术要求
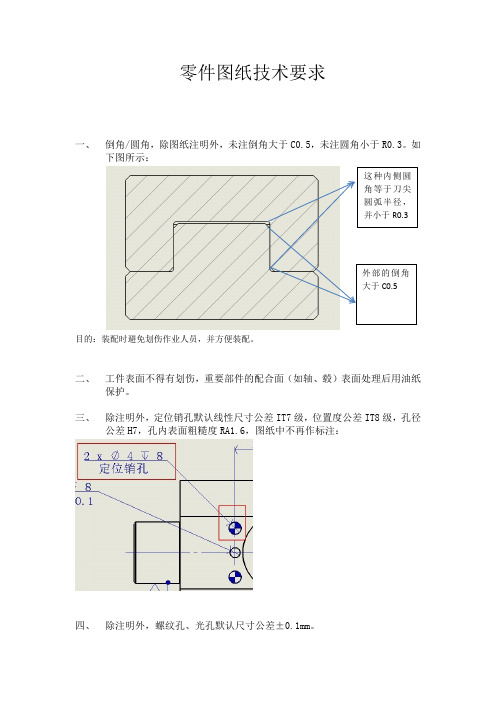
零件图纸技术要求
一、倒角/圆角,除图纸注明外,未注倒角大于C0.5,未注圆角小于R0.3。
如
下图所示:
目的:装配时避免划伤作业人员,并方便装配。
二、工件表面不得有划伤,重要部件的配合面(如轴、毂)表面处理后用油纸
保护。
三、除注明外,定位销孔默认线性尺寸公差IT7级,位置度公差IT8级,孔径
公差H7,孔内表面粗糙度RA1.6,图纸中不再作标注:
四、除注明外,螺纹孔、光孔默认尺寸公差±0.1mm。
这种内侧圆
角等于刀尖
圆弧半径,
并小于R0.3
外部的倒角
大于C0.5
五、使用孔表的图纸(见下图),默认线性尺寸公差IT8级,位置度公差IT9级,孔径公差H8,孔内表面粗糙度RA3.2。
图纸中不再作标注。
六、零件出厂前应自检,合格后再发货。
发货前清除干净碎屑、毛刺等杂物,做到零件表面整洁美观。
七、机加零件涂油防锈,精密面采用油纸、纱网保护防止划伤,钣金零件不得多个叠放防止挤压变形。
钣金件喷涂、镀层前应注意螺纹保护。
塑胶制品防止挤压开裂、变形。
八、螺纹孔、光孔配合面必须倒角去毛刺。
倒角C0.3-C0.5
九、加工图纸必须随零件返回,即供应商送货零件必须附有图纸。
十、未注尺寸公差GB/T1804-2000-M;
未注形位公差GB/T1184-1996-K.。
图纸上的技术要求汇总

图纸技术要求一、一般技术要求制件去除表面氧化皮;制件不得有划痕、擦伤等损伤零件表面的缺陷;去除毛刺飞边;锐角倒钝;未注倒角均为0.5×45%%d;未注越程槽均为1.2×0.3;表面平整无毛刺;二、未注公差技术要求(金属件)未注公差尺寸的极限偏差按GB/T 1804-m;未注形位公差按GB/T 1184-K;未注长度尺寸允许偏差±0.5;三、表面处理技术要求表面镀白(黑)锌处理;表面喷漆(喷塑)处理;表面发黑处理;表面电泳处理;表面镀铬处理;表面抛光处理;表面滚花,直纹(网纹)m=0.4 GB/T 6403.3;四、热处理技术要求制件氮化450-480HV;制件毛坯须调质处理220-260HB;制件调质处理30-35HRC;制件高频淬火45~50HRC;制件渗碳处理,深度>0.1;制件进行高温回火处理;制件整体淬火40-45HRC;五、铸件技术要求1、压铸件技术要求未注公差尺寸的极限偏差按GB/T 1804-m;未注形位公差按GB/T 1184-K;未注倒角均为0.5×45%%d;未注壁厚2.5;未注筋板1.5~2;未注过渡圆角R0.5-R2;未注脱模斜度≤1%%d;制件饱满光洁、无气孔、缩松、裂纹、夹渣、缺料等缺陷;各脱模顶料推杆压痕均应低于该制件表面0.2;制件要求符合GB/T 15114《铝合金压铸件》标准规定;表面喷漆(喷塑)处理,不得污染到已加工表面;加工表面在表面处理后加工,加工后涂油保护;未注尺寸参照三维造型;制件表面处理及其它要求按客户定;2、砂型铸造技术要求未注铸造圆角R5-10;铸件应彻底清砂,浇冒口应清除平整;铸件需人工时效;铸件不得有砂眼、气孔、缩松、裂纹等缺陷;粗加工后应再次进行人工时效;不加工表面涂底漆;六、冲压件技术要求制件未注公差尺寸的极限偏差按GB/T 15055-m;制件未注形位公差按GB/T 13916-2级;制件不得有裂纹或缺损;制件表面平整,不得有沟痕、碰伤等损坏表面,降低强度及寿命的缺陷;去除边角毛刺;表面处理:七、塑料件技术要求未注公差尺寸的极限偏差按GB/T 14486-MT6级;制件应饱满光整、色泽均匀;无缩痕、裂纹、银丝等缺陷;浇口、溢边修剪后飞边≤0.3,且不得伤及本体;未注壁厚3;未注筋板1.5~2;表面打光(喷砂)处理;未注过渡圆角取R0.3~R1,脱模斜度≤0.3%%d;各脱模顶料推杆压痕均应低于该制件表面0.2;与对应装配结合面外形配合错位≤0.5;制件应进行时效处理;制件机械强度须符合GB 3883.1标准规定;制件内腔表面打上材料标记和回收标志;未注尺寸参照三维造型;制件表面处理及其它要求由客户定;八、焊接件技术要求未注公差线性及角度尺寸的极限偏差均按GB/T 19804-B级;未注形位公差按GB/T 19804-F级;焊缝应均匀平整,焊渣清理干净;焊缝应焊透,不得烧穿及产生裂纹等影响机械性能的缺陷;九、各类零、部件技术要求1、齿轮(齿轴)技术要求未注公差尺寸的极限偏差按GB/T 1804-m;未注形位公差按GB/T 1184-K;制件毛坯须调质220~260HB;制件材料的化学成分和力学性能应符合GB/T 3077的规定;齿面接触斑点:按齿高不小于40%,按齿长不小于50%;齿面高频淬火回火至49-52HRC;制件表面不应有锈迹、裂纹、灼伤等影响使用寿命的伤痕及缺陷;最终工序热处理表面不得有氧化皮;2、一般轴芯(无铣齿)技术要求未注公差尺寸的极限偏差按GB/T 1804-m;未注形位公差按GB/T 1184-K;未注倒角均为0.5×45%%d;未注越程槽均为1.2×0.3;制件毛坯须调质220~260HB;尺寸%%c 档车正反两条螺旋槽,螺距10,深0.4;螺纹表面不允许有磕碰、乱扣、毛刺等缺陷;热处理:表面处理:3、包轴毛坯(一次成型)技术要求未注公差尺寸的极限偏差按GB/T 1804-m;未注形位公差按GB/T 1184-K;绝缘层应饱满光洁,无裂纹、气孔、缺料、杂质等缺陷;包轴毛坯:绝缘层%%c 档(注:指冲片配合档)与轴芯间应能承受50Hz,实际正弦波电压2500V历时1min不击穿,其余绝缘层档3750V历时1min不击穿;一次成型:铁芯与轴芯间应能承受50Hz,实际正弦波电压2500V历时1min不击穿,其余绝缘层档3750V历时1min不击穿;4、包轴(加工)技术要求未注公差尺寸的极限偏差按GB/T 1804-m;未注形位公差按GB/T 1184-K;塑层应饱满光洁,无裂纹、气孔、缺料、杂质等缺陷;塑层%%c 档(注:指冲片配合档)与轴芯间应能承受50Hz,实际正弦波电压2500V历时1min不击穿,其余塑层档3750V历时1min不击穿;制件磨加工后应烘干除水处理;5、转子技术要求未注公差尺寸的极限偏差按GB/T 1804-m;未注形位公差按GB/T 1184-K;绕组接线按转子绕线原理图;绕组绝缘漆应均匀充满绕组并充分固化,漆膜应均匀无气泡或裂痕;云母槽开深0.8~1,槽宽0.6,槽内不得残留云母片;绕组冷态绝缘电阻不低于50MΩ;装风叶后校动平衡,其精度应不低于G6.3级;去重不允许有冲片铣穿、残缺现象;铁芯外圆不加工,绝缘漆不得高出铁芯外圆,并不得有明显积瘤;铁芯与轴芯间应能承受50Hz,实际正弦波电压2500V,1min不击穿;绕组与铁芯间应能承受50Hz,实际正弦波电压1250V,1min不击穿;匝间绝缘应能承受1000Hz,峰值为2100V,历时3s不击穿;换向器与轴芯间应能承受50Hz,实际正弦波电压3750V,1min不击穿;应去除铁屑、铜粉、油污等杂质;铁芯外圆应涂透明淡金水防锈处理;6、定子技术要求绕组绕制整齐无松散;引线接头应牢固可靠且充分绝缘;绕组与铁芯间应能承受50Hz,实际正弦波电压1250V历时1min不击穿;匝间绝缘应能承受1000Hz,峰值为2100V,历时3s不击穿;绕组绝缘漆应均匀充满绕组并充分固化,漆膜应均匀无气泡或积瘤;铁芯表面不得有明显绝缘漆;7、定、转子铁芯技术要求未注公差尺寸的极限偏差按GB/T 1804-m;未注形位公差按GB/T 1184-K;冲片叠装应紧密可靠,片间无夹杂,表面及槽内无污物和油渍;冲片按同一冲制方向压装;冲片齿槽口整齐与转轴平行,误差不大于0.5;铁芯两端弹开度不大于0.5;8、定、转子冲片技术要求制件未注公差尺寸的极限偏差按GB/T 15055-m;制件未注形位公差按GB/T 13916-2级;制件应表面平整,完整无缺料;尖角处允许用R0.3过渡;制件毛刺不大于0.05(注:高速冲时不大于0.02);制件应不含油脂,剪切油不能用机油;9、绝缘纸技术要求表面不得有划痕、折痕;裁边不起毛;10、换向器技术要求未注公差尺寸的极限偏差按GB/T 1804-m;未注形位公差按GB/T 1184-K;外观完整,表面光滑,应无裂纹、毛刺、锈蚀、气孔、夹杂等缺陷;绝缘电阻:室温下内孔与换向片之间大于50MΩ;云母片厚度取0.5;换向片对换向器轴线偏斜度不大于云母片厚度的1/3;介电强度:片间承受频率50Hz,泄露电流为0.1mA,实际正弦波电压600V历时1s不击穿;换向片与内孔轴芯间承受频率50Hz,泄露电流为0.25mA,实际正弦波电压3750V历时1min不击穿;试验与检验应符合JB/T 10107《电动工具换向器》标准要求;11、电缆线技术要求电缆线长度尺寸指工具电缆出口至插头的导线部分,不包括插头和插脚;软电缆应符合GB/T 5013《额定电压450V/750V及以下橡皮绝缘电缆》标准要求;聚氯乙烯电缆应符合GB/T 5023《额定电压450V/750V及以下聚氯乙烯绝缘电缆》标准要求;插脚与可触及插头表面的绝缘应能承受50Hz,实际正弦波电压3750V历时1min不击穿;制件还应符合GB 1002《家用和类似用途单相插头插座型式、基本参数和尺寸》和GB 2099《家用和类似用途插头插座》标准要求;12、开关技术要求未注公差尺寸的极限偏差按SJ/T 10628-7级;除本图要求的外形尺寸、功能、图形、文字外,试验和检验均应符合GB/T22692《电动工具开关》标准要求;开关的使用性能应保证5万次无故障正常使用;13、电缆护套技术要求未注公差尺寸的极限偏差按GB/T 3672.1-2级;未注形位公差按GB/T 3672.2-M级;制件不得有缺料、破裂等缺陷。
图纸上的技术要求汇总
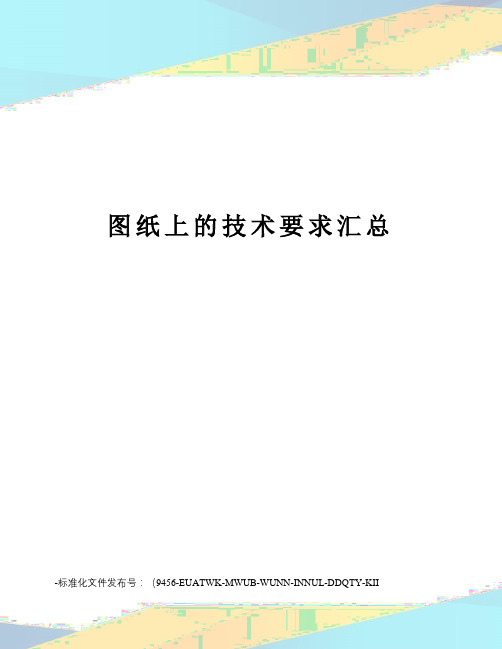
图纸上的技术要求汇总-标准化文件发布号:(9456-EUATWK-MWUB-WUNN-INNUL-DDQTY-KII图纸技术要求一、一般技术要求制件去除表面氧化皮;制件不得有划痕、擦伤等损伤零件表面的缺陷;去除毛刺飞边;锐角倒钝;未注倒角均为0.5×45%%d;未注越程槽均为1.2×0.3;表面平整无毛刺;二、未注公差技术要求(金属件)未注公差尺寸的极限偏差按GB/T 1804-m;未注形位公差按GB/T 1184-K;未注长度尺寸允许偏差±0.5;三、表面处理技术要求表面镀白(黑)锌处理;表面喷漆(喷塑)处理;表面发黑处理;表面电泳处理;表面镀铬处理;表面抛光处理;表面滚花,直纹(网纹)m=0.4 GB/T 6403.3;四、热处理技术要求制件氮化450-480HV;制件毛坯须调质处理220-260HB;制件调质处理30-35HRC;制件高频淬火45~50HRC;制件渗碳处理,深度>0.1;制件进行高温回火处理;制件整体淬火40-45HRC;五、铸件技术要求1、压铸件技术要求未注公差尺寸的极限偏差按GB/T 1804-m;未注形位公差按GB/T 1184-K;未注倒角均为0.5×45%%d;未注壁厚2.5;未注筋板1.5~2;未注过渡圆角R0.5-R2;未注脱模斜度≤1%%d;制件饱满光洁、无气孔、缩松、裂纹、夹渣、缺料等缺陷;各脱模顶料推杆压痕均应低于该制件表面0.2;制件要求符合GB/T 15114《铝合金压铸件》标准规定;表面喷漆(喷塑)处理,不得污染到已加工表面;加工表面在表面处理后加工,加工后涂油保护;未注尺寸参照三维造型;制件表面处理及其它要求按客户定;2、砂型铸造技术要求未注铸造圆角R5-10;铸件应彻底清砂,浇冒口应清除平整;铸件需人工时效;铸件不得有砂眼、气孔、缩松、裂纹等缺陷;粗加工后应再次进行人工时效;不加工表面涂底漆;六、冲压件技术要求制件未注公差尺寸的极限偏差按GB/T 15055-m;制件未注形位公差按GB/T 13916-2级;制件不得有裂纹或缺损;制件表面平整,不得有沟痕、碰伤等损坏表面,降低强度及寿命的缺陷;去除边角毛刺;表面处理:七、塑料件技术要求未注公差尺寸的极限偏差按GB/T 14486-MT6级;制件应饱满光整、色泽均匀;无缩痕、裂纹、银丝等缺陷;浇口、溢边修剪后飞边≤0.3,且不得伤及本体;未注壁厚3;未注筋板1.5~2;表面打光(喷砂)处理;未注过渡圆角取R0.3~R1,脱模斜度≤0.3%%d;各脱模顶料推杆压痕均应低于该制件表面0.2;与对应装配结合面外形配合错位≤0.5;制件应进行时效处理;制件机械强度须符合GB 3883.1标准规定;制件内腔表面打上材料标记和回收标志;未注尺寸参照三维造型;制件表面处理及其它要求由客户定;八、焊接件技术要求未注公差线性及角度尺寸的极限偏差均按GB/T 19804-B级;未注形位公差按GB/T 19804-F级;焊缝应均匀平整,焊渣清理干净;焊缝应焊透,不得烧穿及产生裂纹等影响机械性能的缺陷;九、各类零、部件技术要求1、齿轮(齿轴)技术要求未注公差尺寸的极限偏差按GB/T 1804-m;未注形位公差按GB/T 1184-K;制件毛坯须调质220~260HB;制件材料的化学成分和力学性能应符合GB/T 3077的规定;齿面接触斑点:按齿高不小于40%,按齿长不小于50%;齿面高频淬火回火至49-52HRC;制件表面不应有锈迹、裂纹、灼伤等影响使用寿命的伤痕及缺陷;最终工序热处理表面不得有氧化皮;2、一般轴芯(无铣齿)技术要求未注公差尺寸的极限偏差按GB/T 1804-m;未注形位公差按GB/T 1184-K;未注倒角均为0.5×45%%d;未注越程槽均为1.2×0.3;制件毛坯须调质220~260HB;尺寸%%c 档车正反两条螺旋槽,螺距10,深0.4;螺纹表面不允许有磕碰、乱扣、毛刺等缺陷;热处理:表面处理:3、包轴毛坯(一次成型)技术要求未注公差尺寸的极限偏差按GB/T 1804-m;未注形位公差按GB/T 1184-K;绝缘层应饱满光洁,无裂纹、气孔、缺料、杂质等缺陷;包轴毛坯:绝缘层%%c 档(注:指冲片配合档)与轴芯间应能承受50Hz,实际正弦波电压2500V历时1min不击穿,其余绝缘层档3750V历时1min不击穿;一次成型:铁芯与轴芯间应能承受50Hz,实际正弦波电压2500V历时1min不击穿,其余绝缘层档3750V历时1min不击穿;4、包轴(加工)技术要求未注公差尺寸的极限偏差按GB/T 1804-m;未注形位公差按GB/T 1184-K;塑层应饱满光洁,无裂纹、气孔、缺料、杂质等缺陷;塑层%%c 档(注:指冲片配合档)与轴芯间应能承受50Hz,实际正弦波电压2500V历时1min不击穿,其余塑层档3750V历时1min不击穿;制件磨加工后应烘干除水处理;5、转子技术要求未注公差尺寸的极限偏差按GB/T 1804-m;未注形位公差按GB/T 1184-K;绕组接线按转子绕线原理图;绕组绝缘漆应均匀充满绕组并充分固化,漆膜应均匀无气泡或裂痕;云母槽开深0.8~1,槽宽0.6,槽内不得残留云母片;绕组冷态绝缘电阻不低于50MΩ;装风叶后校动平衡,其精度应不低于G6.3级;去重不允许有冲片铣穿、残缺现象;铁芯外圆不加工,绝缘漆不得高出铁芯外圆,并不得有明显积瘤;铁芯与轴芯间应能承受50Hz,实际正弦波电压2500V,1min不击穿;绕组与铁芯间应能承受50Hz,实际正弦波电压1250V,1min不击穿;匝间绝缘应能承受1000Hz,峰值为2100V,历时3s不击穿;换向器与轴芯间应能承受50Hz,实际正弦波电压3750V,1min不击穿;应去除铁屑、铜粉、油污等杂质;铁芯外圆应涂透明淡金水防锈处理;6、定子技术要求绕组绕制整齐无松散;引线接头应牢固可靠且充分绝缘;绕组与铁芯间应能承受50Hz,实际正弦波电压1250V历时1min不击穿;匝间绝缘应能承受1000Hz,峰值为2100V,历时3s不击穿;绕组绝缘漆应均匀充满绕组并充分固化,漆膜应均匀无气泡或积瘤;铁芯表面不得有明显绝缘漆;7、定、转子铁芯技术要求未注公差尺寸的极限偏差按GB/T 1804-m;未注形位公差按GB/T 1184-K;冲片叠装应紧密可靠,片间无夹杂,表面及槽内无污物和油渍;冲片按同一冲制方向压装;冲片齿槽口整齐与转轴平行,误差不大于0.5;铁芯两端弹开度不大于0.5;8、定、转子冲片技术要求制件未注公差尺寸的极限偏差按GB/T 15055-m;制件未注形位公差按GB/T 13916-2级;制件应表面平整,完整无缺料;尖角处允许用R0.3过渡;制件毛刺不大于0.05(注:高速冲时不大于0.02);制件应不含油脂,剪切油不能用机油;9、绝缘纸技术要求表面不得有划痕、折痕;裁边不起毛;10、换向器技术要求未注公差尺寸的极限偏差按GB/T 1804-m;未注形位公差按GB/T 1184-K;外观完整,表面光滑,应无裂纹、毛刺、锈蚀、气孔、夹杂等缺陷;绝缘电阻:室温下内孔与换向片之间大于50MΩ;云母片厚度取0.5;换向片对换向器轴线偏斜度不大于云母片厚度的1/3;介电强度:片间承受频率50Hz,泄露电流为0.1mA,实际正弦波电压600V历时1s不击穿;换向片与内孔轴芯间承受频率50Hz,泄露电流为0.25mA,实际正弦波电压3750V历时1min不击穿;试验与检验应符合JB/T 10107《电动工具换向器》标准要求;11、电缆线技术要求电缆线长度尺寸指工具电缆出口至插头的导线部分,不包括插头和插脚;软电缆应符合GB/T 5013《额定电压450V/750V及以下橡皮绝缘电缆》标准要求;聚氯乙烯电缆应符合GB/T 5023《额定电压450V/750V及以下聚氯乙烯绝缘电缆》标准要求;插脚与可触及插头表面的绝缘应能承受50Hz,实际正弦波电压3750V历时1min不击穿;制件还应符合GB 1002《家用和类似用途单相插头插座型式、基本参数和尺寸》和GB 2099《家用和类似用途插头插座》标准要求;12、开关技术要求未注公差尺寸的极限偏差按SJ/T 10628-7级;除本图要求的外形尺寸、功能、图形、文字外,试验和检验均应符合GB/T 22692《电动工具开关》标准要求;开关的使用性能应保证5万次无故障正常使用;13、电缆护套技术要求未注公差尺寸的极限偏差按GB/T 3672.1-2级;未注形位公差按GB/T 3672.2-M级;制件不得有缺料、破裂等缺陷。
常用图纸技术要求
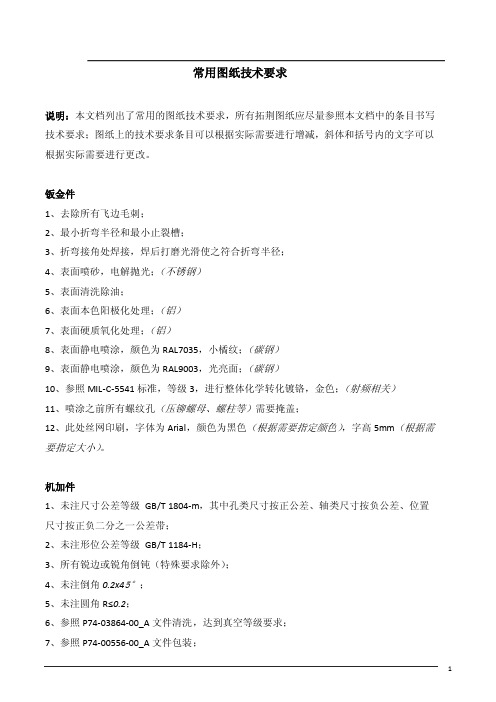
常用图纸技术要求说明:本文档列出了常用的图纸技术要求,所有拓荆图纸应尽量参照本文档中的条目书写技术要求;图纸上的技术要求条目可以根据实际需要进行增减,斜体和括号内的文字可以根据实际需要进行更改。
钣金件1、去除所有飞边毛刺;2、最小折弯半径和最小止裂槽;3、折弯接角处焊接,焊后打磨光滑使之符合折弯半径;4、表面喷砂,电解抛光;(不锈钢)5、表面清洗除油;6、表面本色阳极化处理;(铝)7、表面硬质氧化处理;(铝)8、表面静电喷涂,颜色为RAL7035,小橘纹;(碳钢)9、表面静电喷涂,颜色为RAL9003,光亮面;(碳钢)10、参照MIL-C-5541标准,等级3,进行整体化学转化镀铬,金色;(射频相关)11、喷涂之前所有螺纹孔(压铆螺母、螺柱等)需要掩盖;12、此处丝网印刷,字体为Arial,颜色为黑色(根据需要指定颜色),字高5mm(根据需要指定大小)。
机加件1、未注尺寸公差等级GB/T 1804-m,其中孔类尺寸按正公差、轴类尺寸按负公差、位置尺寸按正负二分之一公差带;2、未注形位公差等级GB/T 1184-H;3、所有锐边或锐角倒钝(特殊要求除外);4、未注倒角0.2x45°;5、未注圆角R≤0.2;6、参照P74-03864-00_A文件清洗,达到真空等级要求;7、参照P74-00556-00_A文件包装;8、此处激光刻字:P15-00154-00_AXXXX-YYMM-SSS其中XXXX为四位供应商编码,YYMM为四位出厂日期码,YY为年编码,MM为月编码,SSS为此零件在此月内的序列号,从001开始计数,字体为Arial,字高5mm,行间距3mm;9、材料热处理方法:正火、调质、淬火,热处理后表面应达到的硬度;(根据需要)10、注明表面处理要求(渗碳、氰化、淡化、喷丸等)、表面涂层或镀层(油漆、发兰、镀铬、镀镍等)以及表面修饰(去毛刺、清砂)等(根据需要),可参考钣金表面处理。
技术部图纸制图的要求

一、技术部图纸制图的要求为了保证图纸的完整性、标准性和统一性,确保设计和生产工作的顺利进行,制图要符合GB/T4458.1-2002机械制图标准,按比例绘图。
此外,还要符合以下要求。
1、软件版本要求为了统一制图软件版本,要求存入主机的图纸是AUTOCAD2008或CAXA2007,能够用AUTOCAD2008或CAXA2007打开和编辑。
2、标题栏和明细栏1)为了保证图纸的准确性和合理性,标题栏要有设计、审核、批准内容。
2)为了便于生产管理和成本管理,标题栏和明细栏要有数量和质量且要求准确填写。
特别是公司标准产品、模块产品(类似标准产品)。
3)公司名称统一“长沙万马牧业机械科技有限公司”。
4)外购件要注明型号和厂家,标准件要注明国标或行业标准号。
3、图纸编号规则1)为了便于交流,设备型号的编写要与行业的规则统一。
如“DTG15/9”,头轮直径为150mm斗宽90mm的固定斗式提升机。
2)设备总图图号为设备型号,如“DTG15/9”3)部件图号为总图图号.+. “.01\.02…. ”,的顺序号,如“DTG15/9.01”4)零件图号为总图图号(或部件号).+. “-1\-2…. ”,的顺序号,如“DTG15/9-1”、“DTG15/9.01-1”4、设备总图饲料机械的特点是设备组合集群,为了便于组合设计,设备总图必须具备三个视图,还要有外形尺寸、设备总重、设备接口尺寸和主要参数。
5、零部件材质分类:零件材质要按实际材质,如“45”、“Q235”等。
部件材质统一为“焊件“组件”“部件”部件--设备的一部分,具备独立的功能焊件—钢结构焊接件组件—含有几个零件的装配体,但不具备独立的功能。
6、图纸的签署1)电子版图纸必须填写设计者或绘图者,其他可以不填写。
2)纸质版设计者或绘图者可以是打印,但审核、批准必须手写。
产品总图和项目总装图必须填写设计、审核、批准和标准。
部件图必须填设计、审核和标准。
零件图必须填设计和标准。
一般的图纸技术要求填写
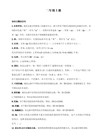
铸钢件表面堆焊接时,焊道间的重叠量不得小于焊道宽度的1/3。
10.锻件要求:
每个钢锭的水口、冒口应有足够的切除量,一以保证锻件无缩孔和严重的偏折。
锻件应在有足够能力的锻压机上锻造成形,以保证锻件内部充分锻透。
锻件不允许有肉眼可见的裂纹、折叠和其他影响使用的外观缺陷。局部缺陷可以清除,但清理深度不得超过加工余量的75%,锻件非加工表面上的缺陷应清理干净并圆滑过渡。
滑动配合的平键(或花键)装配后,相配件移动自如,不得有松紧不均现象。
粘接后应清除流出的多余粘接剂。
轴承外圈与开式轴承座及轴承盖的半圆孔不准有卡住现象。
轴承外圈与开式轴承座及轴承盖的半圆孔应接触良好,用涂色检查时,与轴承座在对称于中心线120°、与轴承盖在对称于中心线90°的范围内应均匀接触。在上述范围内用塞尺检查时,0.03mm的塞尺不得塞入外圈宽度的1/3。
渗碳深度0.3mm。
进行高温时效处理。
3.公差要求:
未注形状公差应符合GB1184-80的要求。
未注长度尺寸允许偏差±0.5mm。
铸件公差带对称于毛坯铸件基本尺寸配置。
4.零件棱角:
未注圆角半径R5。
未注倒角均为2×45°。
锐角倒钝。
5.装配要求:
各密封件装配前必须浸透油。
装配滚动轴承允许采用机油加热进行热装,油的温度不得超过100℃。
规定拧紧力矩要求的紧固件,必须采用力矩扳手,并按规定的拧紧力矩紧固。
同一零件用多件螺钉(螺栓)紧固时,各螺钉(螺栓)需交叉、对称配合长度的60%,并应均匀分布。
平键与轴上键槽两侧面应均匀接触,其配合面不得有间隙。
图纸技术要求大全

图纸技术要求大全-标准化文件发布号:(9456-EUATWK-MWUB-WUNN-INNUL-DDQTY-KII1.零件去除氧化皮。
2.零件加工表面上,不应有划痕、擦伤等损伤零件表面的缺陷。
3.去除毛刺飞边。
4.经调质处理,HRC50~55。
5.零件进行高频淬火,350~370℃回火,HRC40~45。
6.渗碳深度0.3mm。
7.进行高温时效处理。
8.未注形状公差应符合GB1184-80的要求。
9.未注长度尺寸允许偏差±0.5mm。
10.铸件公差带对称于毛坯铸件基本尺寸配置。
11.未注圆角半径R5。
12.未注倒角均为2×45°。
13.锐角倒钝。
14.各密封件装配前必须浸透油。
15.装配滚动轴承允许采用机油加热进行热装,油的温度不得超过100℃。
20.齿轮装配后,齿面的接触斑点和侧隙应符合GB10095和GB11365的规定。
21.装配液压系统时允许使用密封填料或密封胶,但应防止进入系统中。
22.进入装配的零件及部件(包括外购件、外协件),均必须具有检验部门的合格证方能进行装配。
23.零件在装配前必须清理和清洗干净,不得有毛刺、飞边、氧化皮、锈蚀、切屑、油污、着色剂和灰尘等。
24.装配前应对零、部件的主要配合尺寸,特别是过盈配合尺寸及相关精度进行复查。
25.装配过程中零件不允许磕、碰、划伤和锈蚀。
26.螺钉、螺栓和螺母紧固时,严禁打击或使用不合适的旋具和扳手。
紧固后螺钉槽、螺母和螺钉、螺栓头部不得损坏。
27.规定拧紧力矩要求的紧固件,必须采用力矩扳手,并按规定的拧紧力矩紧固。
28.同一零件用多件螺钉(螺栓)紧固时,各螺钉(螺栓)需交叉、对称、逐步、均匀拧紧。
29.圆锥销装配时应与孔应进行涂色检查,其接触率不应小于配合长度的60%,并应均匀分布。
30.平键与轴上键槽两侧面应均匀接触,其配合面不得有间隙。
31.花键装配同时接触的齿面数不少于2/3,接触率在键齿的长度和高度方向不得低于50%。
技术图纸管理要求

xxxxxx有限公司企业标准
技术图纸管理要求(试运行稿)
1.目的
通过对技术图纸的签署、分类、标识、保存及过程管理控制,确保公司所有文件的有效性、正确性和统一性。
2.适用范围及归口
适用公司所有的技术图纸, 归口管理部门为技术部;
3.定义
3.1图纸类别:1、新机型试制用图纸;2、非生产用图纸;3、生产用图纸(a外寄件图纸、b订单非标件图纸、c常规生产用图纸);
4.图纸标识
4.1试制用图纸:需要盖上试制章和日期;
4.2非生产用图纸: 需要盖上非生产用途章和日期;
4.3生产用图纸: 需要盖上生产用途章和日期;(备注:订单非标件图纸必须在图纸的左上角注明:客户名称及定单号、定制件字样)
5.文件发放方式及要求:
5.1新机型试制用图纸
技术部将试制用图交生产部长签收并登记;
5.2生产用图纸:
a、常规生产用图纸(含外寄件图纸):需求部门填写图纸申请单交技术部签发并登记;
b、订单非标件图纸:技术科根据生产单技术要求进行图纸设计和清单制作,经过技术科经理审批后下发生产部制作;(下发的信息有:订单非标件图纸、非标件零件清单及外购件清单)
5.3本规定签发之日开始,没有符合以上签章要求的图纸,生产部不能接收生产,质量部不能接收检验,同时向流转部门反映协调解决;
6.在加工过程(内、外部加工商)流转中遗失的图纸和工序单均以10元一张进行处罚;
7.以上所有下发的图纸在本批次加工完成后,领用部门将盖章的原件图纸交还技术部保存,6个月后将残缺不齐的图纸进行统一销毁。
- 1、下载文档前请自行甄别文档内容的完整性,平台不提供额外的编辑、内容补充、找答案等附加服务。
- 2、"仅部分预览"的文档,不可在线预览部分如存在完整性等问题,可反馈申请退款(可完整预览的文档不适用该条件!)。
- 3、如文档侵犯您的权益,请联系客服反馈,我们会尽快为您处理(人工客服工作时间:9:00-18:30)。
技术图纸要求
一.图纸
1.图纸图幅应符合国家制图标准允许使用的图幅,其中A4应为竖幅,其
他均为横幅;
2.图纸应有完整、标准的标题栏,打印时因图纸缩小的标题栏应保证栏内
文字清晰;
3.每张图纸应有必要的技术要求,根据图纸的性质(装配图、部件图零件
图)撰写,内容可包括:技术参数、装配要求(装配工艺、重点、精度)、加工要求(热处理、抛光、喷砂、拉丝、配作、去毛刺、倒角、倒锐、倒棱、焊接、打磨、清渣、清洗、除尘等)、检测、防护、标记、包装、运输等及其他;
4.技术要求等文字、字母应清晰、文字简洁、明了,一般选用“四号仿宋
字”;技术要求一般置于图纸右下方;
5.加工图纸都应有粗糙度要求,有位置、形状要求的应标注形位公差;
6.装配图应有基本的外形尺寸及必要的装配尺寸(配合公差等);
7.由于技术人员使用的绘图软件未统一,各人所出图纸差异较大,但设计
者不能因软件不同而降低图纸质量,在正确、清楚的情况小,应考虑布图美观、合理;
8.由于产品以薄板件为主,厚度小,绘图时线条极易重叠,可能会引起误
读、造成错误,因此,应尽量用放大、剖面、局部视图等手段,保证图纸质量;
9.成台产品图纸标题栏内的设计、审核、批准栏的签名必须完整(姓名、
日期),一般图纸必须有设计、审核签名;
10.图纸必须加盖“受控”章才可下发,有“受控”章图纸只发一份至生
产部(见附表:图纸发放记录表),其他用图(外协、检验等)只能“复制”;
11.成套产品必须有《零件明细表》、《外购件明细表》,在图纸下发时一起
提供生产部(加盖“受控”章)。
因生产需要,《外购件明细表》可以提前下发或分几次下发,但最后必须整理成正式技术文件存档;
12.结构简单、图纸上明细表清楚的产品,单件产品和没有外购件的产品
可以不出《零件明细表》、《外购件明细表》。
二.图纸的更正、更换
1. 图纸下发后,其他部门或职工发现或指出的错误,应及时更正。
根据图
纸错误程度,可采取换图或原图上改正的办法,一般由设计者决定,更
换的图纸必须收回,原图上改正必须由设计者在改正处签名;
2. 图纸下发后,其他部门或职工提出的异议,应耐心听取、了解并及时处
理,重要的可开会进行专门讨论决定;
3. 图纸更正、更换应及时与各部门相关人员沟通,同时将更正、更换情况
及时输入电子文档,作好记录。
三.图纸的借用
借用是指技术人员设计不同产品时,部分零件采用公司现有的产品图纸资料而不再重新设计的情况(例如:法兰、管道、手柄、支座等等)。
公司的技术资料、文件必须共享,共享程度的高低,可以反映一个企业的技术水及产品设计规范程度,因此,设计中提倡互相借用已生产过、在使用中成熟、可靠的零部件图。
1. 技术部将建立一个公共图库。
设图库管理员一名,技术人员应向其提供
所有图纸,由其挑选、整理出共享图纸,推广借用。
2. 技术人员应尽可能使用借用件;借用件的图号、名称应该是唯一的;四.图号的编制
图号编制规范、统一是我公司提高技术管理水平的必须,现初步规定如下。
1. 根据公司的惯例,由技术部设计下发的受控图纸,图号的第一位用“惠
心”拼音中的字母“H”表示;
2. 已列入本公司《关于产品命名、型号编制规定》的产品,图号编制方法
如下:
HⅩⅩⅩⅩⅩⅩ—00 —ⅩⅩⅩⅩⅩⅩ
型号:规格:用数字表示2位数字表示2-5位数字表示同型号、规格系列用字母表示不超过4位总装配图:00 前2位,小部件图号号(改进、扩展等)
部件图:01-99 后3位,零件图号用字母表示
原则:
1)凡是有装配关系的产品,必须有装配图;
2)凡是有装配图,必须填写明细表;
3)只要是在装配图上能表达清楚,满足加工、装配的,可不出零件图,在明细表“备注”栏内填写“本图”;
4)凡是不出零件图的零件(明细表“备注”栏内填写“本图”的零件),在明细表内,只填写“序号”,不填写“代号”;
5)根据公司的实际情况,尽可能减少不出零件图的零件数量,尤其可以判定要“机加工”的零件,应该出零件图;
6)装配图中的外购件将型号、规格列入明细表,标准件必须将标准号列入明细表,规格的标注方法应按规定填写;
7)同型系列产品其结构、功能、位置相同的部件,部件号应该按常规的机型编写。
某个产品没有常规部件的,其部件号空缺;增加的部件,其部件号只能在常规的部件号后延续。
3. 定制产品图号编制方法如下:
RⅩⅩⅩⅩⅩⅩ—ⅩⅩⅩⅩⅩ
型号:规格:用数字表示2-5位数字表示前2位部件图号
用该产品名称不超过4位,总装配图:00 其余部件:01-99
的两个字母表示如无,也可不设后3位:零件图号
例如:每小时输送5吨的输送机装配图图号RSS5—00
其第一个部件“输送架”图号RSS5—01
输送架的第一个零件“外护板”图号RSS5—01001。