单晶生产工艺
单晶生产制造流程
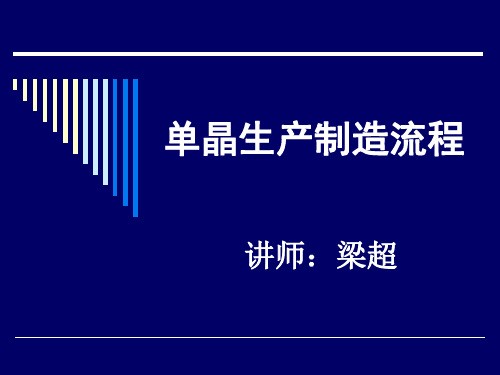
Shank you !
再见!
三种炉型对比
西安炉、 西安炉、京 运通炉( 运通炉(18 寸热场) 寸热场)
55KG 60KG 1100mm
汉虹炉( 汉虹炉(20 寸热场) 寸热场) 投炉量 最大投炉量 6英寸晶棒长 英寸晶棒长
80KG 95KG 1600mm
三种炉型的晶棒
京运通炉与 西安炉,棒 长1100mm
三种炉型的晶棒
单晶生产制造流程
讲师: 讲师:梁超
总目录
单晶车间简介 单晶炉类型 单晶生产工艺流程 后道工序
单晶车间简介
生产经理
行政助理
生产主管 A生产班长 B生产班长
工艺工程师
PMC
设备主管
C生产班长
评估组长
维修A组
维修B组
维修C组
直拉甲组 直拉A组 直拉辅助
直拉乙组 直拉B组 直拉辅助
直拉丙组 直拉C组 直拉辅助
配料员 划线组 切段组 退火组
成品包装组
单晶炉类型
1、京运通炉 2、汉虹炉 3、西安炉
返回总目录
京运通炉
返回目录
京运通炉触摸屏控制柜
汉虹炉
返回目录
汉虹炉控制柜
西安炉
返回目录
单晶生长工艺流程
1、备料(母合金称重、分料) 2、清炉 3、装料 4、抽空检漏 5、化料 6、挥发 7、引晶 8、放肩 9、转肩 10、等径 11、收尾 12、冷却 13、取棒
返回总目录
备料--母合金称重
返回目录
备料--分料
返回目录
清炉
返回目录装料返回源自录抽空检漏化料返回目录
挥发
引晶(颈)
返回目录
放肩
单晶硅工艺流程图

单晶硅工艺流程图单晶硅是目前最常用的半导体材料,广泛应用于集成电路、太阳能电池等领域。
下面是一幅简化的单晶硅工艺流程图,以便更好地了解单晶硅的生产过程。
第一步:原料准备原料通常为高纯度的二氧化硅(SiO2)。
首先将原料粉碎成较小的颗粒并进行筛分,以得到精细的粉末。
接下来,将粉末与一定比例的还原剂(如石煤)混合,以便在高温下还原。
第二步:气相法制备单晶硅将经过还原处理的粉末置于石英坩埚中,将坩埚放入高温炉中。
通过高温炉中的加热源(如电炉)提供热能,使粉末在适当的温度下融化。
在炉中引入气体流,使气体通过石英坩埚并与粉末反应。
反应产物是硅烷(SiH4),通过引入氢气(H2),使硅烷沿着一定的路径扩散并沉积在高温炉中的石英坩埚内壁上。
在此过程中,硅烷会发生化学反应以生成单晶硅。
第三步:生长单晶硅将生长的单晶硅棒置于单晶硅生长炉中,棒内壁为活性炭涂层,通过外加热源提供热能。
加热棒中心温度上升,熔融的硅逐渐凝固成为单晶硅。
生长的单晶硅棒沿着纵向方向生长,直至达到所需长度。
在单晶硅棒的生长过程中,需要定期添加掺杂剂(如磷、硼等),以调节单晶硅的导电性质。
第四步:切割硅锭将生长的单晶硅棒切割成所需的硅锭。
切割主要通过研磨和切割机器完成,将单晶硅棒分割成合适长度的硅锭。
切割出的硅锭表面需要经过打磨和抛光等处理,以获得平整的表面。
第五步:切割片材将硅锭进一步切割成更薄的硅片材料。
切割过程主要使用刀片或线锯,依靠机械力将硅锭切割成薄片。
切割出的硅片需要进行清洗和抛光等后续处理,以获得平整、干净的硅片。
第六步:高温退火与清洗将切割好的硅片通过高温退火炉进行热处理。
退火过程中,硅片经过一定的温度和时间,以消除内部应力和杂质,提高硅片的电学性能。
之后,将硅片进行清洗,以去除表面的杂质和污染物。
第七步:环接触涂覆为了与其他材料进行粘附和封装,硅片表面需要涂覆一层环接触剂。
这一层涂覆能够提供良好的粘接性能,并且能够防止硅片表面的氧化和污染。
单晶硅生产工艺流程

单晶硅生产工艺流程
单晶硅生产工艺流程如下:
1. 原料准备:将硅矿石经过破碎、筛分、洗涤等处理,得到纯度高的硅矿石粉末。
2. 炼制硅棒:将硅矿石粉末与氢气在高温下反应,得到气相硅,再通过化学气相沉积法(CVD)或物理气相沉积法(PVD)将气相硅沉积在硅棒上,形成单晶硅棒。
3. 切割硅片:将单晶硅棒用钻头切割成薄片,厚度通常为200-300微米。
4. 清洗硅片:将硅片放入酸碱溶液中清洗,去除表面杂质。
5. 氧化硅层形成:将硅片放入高温氧气中,形成氧化硅层,用于保护硅片表面。
6. 晶圆制备:将硅片切割成圆形,形成晶圆。
7. 掩膜制备:将晶圆涂上光刻胶,然后用光刻机进行曝光和显影,形成掩膜。
8. 沉积金属层:将晶圆放入金属蒸发器中,沉积金属层,形成电路。
9. 蚀刻:将晶圆放入蚀刻液中,去除未被金属层覆盖的氧化硅层和硅片,形成电路。
10. 清洗:将晶圆放入酸碱溶液中清洗,去除蚀刻液和其他杂质。
11. 封装:将晶圆封装在芯片封装中,形成芯片。
单晶硅生产工艺流程原理

单晶硅生产工艺流程原理单晶硅是一种重要的半导体材料,广泛应用于电子器件制造中,特别是在集成电路行业中扮演着关键角色。
单晶硅的制备是一个复杂而精细的工艺过程,需要经过多个步骤才能获得高纯度的单晶硅材料。
下面将介绍单晶硅的生产工艺流程原理。
原料准备单晶硅的生产过程以硅矿石为主要原料。
首先需要将硅矿石经过多道精炼工艺,去除杂质,得到高纯度的硅原料。
这些原料经过淬火、压制等处理后,形成硅棒的初始坯料。
制备硅棒制备硅棒是单晶硅生产的第一步,该过程采用Czochralski法(简称CZ法)或区熔法(简称FZ法)等方法。
在CZ法中,将初始坯料放入石英坩埚中,加热至高温熔化。
然后,在控制的条件下,缓慢降温并用旋转晶稳定法拉出硅棒。
晶棒切割硅棒制备完成后,需要将硅棒切割成薄片,常用的方法是采用金刚石线锯或者线切割机。
这一步骤旨在减小硅片的厚度,方便后续加工。
晶片处理切割后的硅片需要经过多道化学和物理处理,以去除表面杂质和缺陷。
包括去除氧化层、清洗、抛光等工艺,以确保硅片的表面光洁度和纯净度。
晶片生长经过处理后的硅片用作单晶硅的生长基板。
在生长炉中,将硅片加热至高温,通过控制炉内气氛和温度,使硅片逐渐生长为单晶体。
这一步骤需要高度精密的操作和控制,以确保单晶硅的质量和纯度。
晶片切割生长完成后的单晶硅坯料需要进行切割,以得到符合尺寸要求的硅片。
切割方法包括金刚石刀切割、线切割等,确保硅片的准确尺寸和表面光洁度。
清洗和包装最后一步是对切割后的硅片进行清洗和包装。
在超纯水和化学溶剂中清洗硅片表面,去除残留的杂质和可溶性物质,然后精密包装,避免受到环境污染和损坏。
通过以上几个关键步骤,单晶硅的生产工艺流程得以完整实现。
每一个步骤都需要高度精密的操作和控制,以确保最终生产出高纯度、高质量的单晶硅材料,以满足电子器件制造的需求。
单晶硅的生产工艺虽然复杂,但正是这一系列精细工艺的完美结合,才使得单晶硅成为半导体产业中不可或缺的重要材料。
单晶多晶硅片生产工艺流程详解

在【技术应用】单晶、多晶硅片生产工艺流程详解(上)中,笔者介绍了单晶和多晶硅片工艺流程的前半部分,概述了一些工艺流程和概念,以及术语的相关知识。
而本文则是从切片工艺开始了解,到磨片和吸杂,看硅片如何蜕变。
切片切片综述当单晶硅棒送至硅片生产区域时,晶棒已经过了头尾切除、滚磨、参考面磨制的过程,直接粘上碳板,再与切块粘接就能进行切片加工了。
为了能切割下单个的硅片,晶棒必须以某种方式进行切割。
切片过程有一些要求:能按晶体的一特定的方向进行切割;切割面尽可能平整;引入硅片的损伤尽可能的少;材料的损失尽量少。
碳板当硅片从晶棒上切割下来时,需要有某样东西能防止硅片松散地掉落下来。
有代表性的是用碳板与晶棒通过环氧粘合在一起从而使硅片从晶棒上切割下来后,仍粘在碳板上。
碳板不是粘接板的唯一选择,任何种类的粘接板和环氧结合剂都必须有以下几个特性:能支持硅片,防止其在切片过程中掉落并能容易地从粘板和环氧上剥离;还能保护硅片不受污染。
其它粘板材料还有陶瓷和环氧。
石墨是一种用来支撑硅片的坚硬材料,它被做成与晶棒粘接部位一致的形状。
大多数情况下,碳板应严格地沿着晶棒的参考面粘接,这样碳板就能加工成矩形长条。
当然,碳板也可以和晶棒的其它部位粘接,但同样应与该部位形状一致。
碳板的形状很重要,因为它要求能在碳板和晶棒间使用尽可能少的环氧和尽量短的距离。
这个距离要求尽量短,因为环氧是一种相当软的材料而碳板和晶棒是很硬的材料。
当刀片从硬的材料切到软的材料再到硬的材料,可能会引起硅片碎裂。
这里有一些选择环氧类型参考:强度、移动性和污染程度。
粘接碳板与晶棒的环氧应有足够强的粘度,才能支持硅片直到整根晶棒切割完成,因此,它必须能很容易地从硅片上移走,只有最小量的污染。
刀片当从晶棒上切割下硅片时,期望切面平整、损伤小、沿特定方向切割并且损失的材料尽量小。
有一个速度快、安全可靠、经济的切割方法是很值得的。
在半导体企业,两种通常被应用的方法是环型切割和线切割。
单晶车间生产工艺
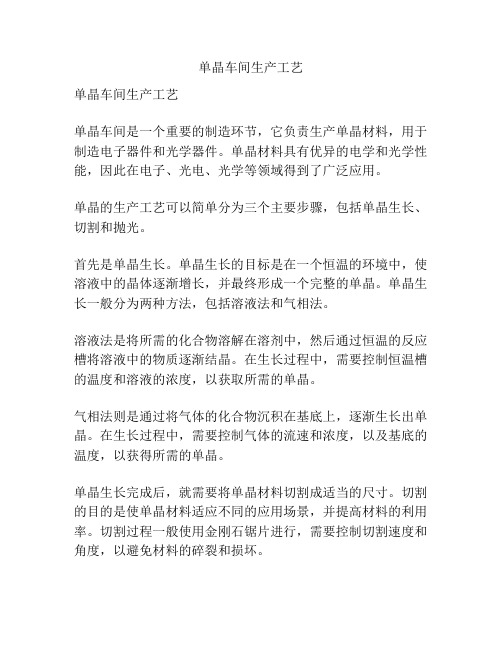
单晶车间生产工艺单晶车间生产工艺单晶车间是一个重要的制造环节,它负责生产单晶材料,用于制造电子器件和光学器件。
单晶材料具有优异的电学和光学性能,因此在电子、光电、光学等领域得到了广泛应用。
单晶的生产工艺可以简单分为三个主要步骤,包括单晶生长、切割和抛光。
首先是单晶生长。
单晶生长的目标是在一个恒温的环境中,使溶液中的晶体逐渐增长,并最终形成一个完整的单晶。
单晶生长一般分为两种方法,包括溶液法和气相法。
溶液法是将所需的化合物溶解在溶剂中,然后通过恒温的反应槽将溶液中的物质逐渐结晶。
在生长过程中,需要控制恒温槽的温度和溶液的浓度,以获取所需的单晶。
气相法则是通过将气体的化合物沉积在基底上,逐渐生长出单晶。
在生长过程中,需要控制气体的流速和浓度,以及基底的温度,以获得所需的单晶。
单晶生长完成后,就需要将单晶材料切割成适当的尺寸。
切割的目的是使单晶材料适应不同的应用场景,并提高材料的利用率。
切割过程一般使用金刚石锯片进行,需要控制切割速度和角度,以避免材料的碎裂和损坏。
最后一步是抛光。
抛光的目的是去除切割过程中产生的瑕疵和表面不平整度,使单晶材料表面光滑、平整。
抛光是一个精细的工艺步骤,需要使用特殊的研磨液和抛光机器,以达到所需的表面质量。
在整个生产工艺中,对于单晶车间来说,关键的是温度和浓度的控制。
温度的控制对于单晶生长来说至关重要,过高或过低的温度都会导致生长的单晶材料质量下降。
浓度的控制对于溶液法来说也非常重要,溶液中物质的浓度会直接影响到生长出的单晶材料的性能。
除了温度和浓度的控制外,单晶车间还需要考虑工作环境的干净程度。
空气中的微粒和杂质都会影响到单晶材料的质量,因此需要保持车间空气的净化,并经常进行清洁。
总结起来,单晶车间的生产工艺包括单晶生长、切割和抛光三个主要步骤。
在整个生产过程中,温度和浓度的控制是关键,同时还需要保持良好的工作环境和设备的维护。
通过这些工艺步骤的合理控制和优化,可以生产出高质量的单晶材料,满足不同领域的需求。
碳化硅单晶生产工艺
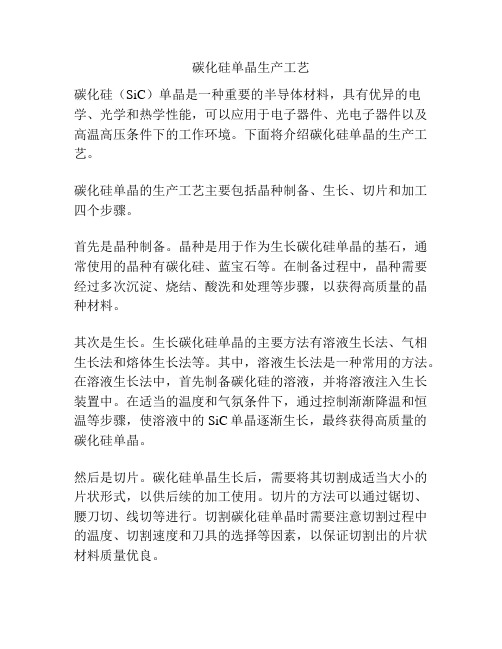
碳化硅单晶生产工艺碳化硅(SiC)单晶是一种重要的半导体材料,具有优异的电学、光学和热学性能,可以应用于电子器件、光电子器件以及高温高压条件下的工作环境。
下面将介绍碳化硅单晶的生产工艺。
碳化硅单晶的生产工艺主要包括晶种制备、生长、切片和加工四个步骤。
首先是晶种制备。
晶种是用于作为生长碳化硅单晶的基石,通常使用的晶种有碳化硅、蓝宝石等。
在制备过程中,晶种需要经过多次沉淀、烧结、酸洗和处理等步骤,以获得高质量的晶种材料。
其次是生长。
生长碳化硅单晶的主要方法有溶液生长法、气相生长法和熔体生长法等。
其中,溶液生长法是一种常用的方法。
在溶液生长法中,首先制备碳化硅的溶液,并将溶液注入生长装置中。
在适当的温度和气氛条件下,通过控制渐渐降温和恒温等步骤,使溶液中的SiC单晶逐渐生长,最终获得高质量的碳化硅单晶。
然后是切片。
碳化硅单晶生长后,需要将其切割成适当大小的片状形式,以供后续的加工使用。
切片的方法可以通过锯切、腰刀切、线切等进行。
切割碳化硅单晶时需要注意切割过程中的温度、切割速度和刀具的选择等因素,以保证切割出的片状材料质量优良。
最后是加工。
加工工艺是将切割后的碳化硅单晶进行各种形状和尺寸的加工制备。
加工方法包括研磨、抛光、清洗等操作。
在加工过程中,需要注意工艺参数的选择和加工表面的平整度和光洁度的控制,以提高碳化硅单晶材料的使用性能。
总的来说,碳化硅单晶的生产工艺包括晶种制备、生长、切片和加工四个步骤,每个步骤都需要严格控制工艺参数和操作条件,以获得高质量的碳化硅单晶材料。
目前,碳化硅单晶的生产工艺已经相对成熟,并且在半导体和光电子领域得到广泛应用。
半导体晶体制备

半导体晶体的制备主要包括单晶制备和晶圆制备两个步骤。
单晶制备的方法主要有:
从熔体中拉制单晶:使用与熔体相同材料的小单晶体作为籽晶,当籽晶与熔体接触并向上提拉时,熔体依靠表面张力也被拉出液面,同时结晶出与籽晶具有相同晶体取向的单晶体。
区域熔炼法制备单晶:使用一籽晶与半导体锭条在头部熔接,随着熔区的移动,结晶部分即成单晶。
从溶液中再结晶。
从汽相中生长单晶:包括液相外延和汽相外延两种方法。
液相外延是将所需的外延层材料溶于某一溶剂成饱和溶液,然后将衬底浸入此溶液,逐渐降低其温度,溶质从过饱和溶液中不断析出,在衬底表面结晶出单晶薄层。
汽相外延生长则是用包含所需材料为组分的某些化合物气体或蒸汽通过分解或还原等化学反应淀积于衬底上。
晶圆制备的过程则包括切割、抛光和清洗等步骤。
首先,将生长好的晶体进行切割,得到薄片状的晶圆。
然后,通过机械和化学方法对晶圆进行抛光,以获得平整的表面。
最后,对晶圆进行清洗,去除表面的杂质和污染物。
在制备过程中,还可能涉及到掺杂的步骤,掺杂是为了改变半导
体材料的导电性能,通常将杂质原子引入晶体中。
掺杂分为两种类型:n型和p型。
n型半导体是通过掺入少量的五价元素(如磷)来增加自由电子的浓度,而p型半导体则是通过掺入少量的三价元素(如硼)来增加空穴的浓度。
掺杂可以通过不同的方法实现,如扩散、离子注入和分子束外延等。
以上是半导体晶体制备的简要步骤和方法,实际制备过程可能因材料、设备和技术等因素而有所不同。
- 1、下载文档前请自行甄别文档内容的完整性,平台不提供额外的编辑、内容补充、找答案等附加服务。
- 2、"仅部分预览"的文档,不可在线预览部分如存在完整性等问题,可反馈申请退款(可完整预览的文档不适用该条件!)。
- 3、如文档侵犯您的权益,请联系客服反馈,我们会尽快为您处理(人工客服工作时间:9:00-18:30)。
装
料
• 适当的装料可以尽量避免挂边、搭桥、溅 适当的装料可以尽量避免挂边、搭桥、 硅现象的出现及漏硅事故的发生, 硅现象的出现及漏硅事故的发生,而且间 接影响了坩埚变形; 接影响了坩埚变形; • 装料规范 : 装料规范 a.打开真空包装取出石英坩埚,检查有无异 物,对光检查石英埚有无气泡、裂纹,如 有直径超过3㎜里层气泡拒绝使用。 b.确认无误后轻轻放入石墨埚内,放平,高 出石墨埚部分要均匀.
20112011-3-23 28
稳定
• 稳定就是从高温状态冷却熔体直到合适的 引晶温度; 引晶温度; • 稳定温度是引晶必不可少的工序,温度是 稳定温度是引晶必不可少的工序, 否稳定直接影响引晶操作及细颈的质量; 否稳定直接影响引晶操作及细颈的质量; • 开启温度自动控制 开启温度自动控制. • 开启熔体温度自动控制 开启熔体温度自动控制. • 坩埚匀速上升到引晶埚位. 坩埚匀速上升到引晶埚位
20112011-3-23 25
c.取碎料3-5㎏平铺于埚底;大块材料放置边 上,为了稳固可放一些小块料;中等块的 材料,放置中间,将剩下的小块料放入, 尽量填缝隙;最后整理上部材料,高出石 英埚的要向内倾斜。 d.装料完毕后,将埚转设置为2转/分钟,用吸 尘嚣吸净装料时附着在石墨材料上的Si粉, 石墨埚下降到化料埚位后停止转动,放置 好保温盖和导流筒,保证原料不接触导流 筒。
20112011-3-23
6
单晶硅
• 单晶硅就是单晶态的高纯硅,它的 质量可以用一系列参数来表述,包 括:电阻率、型号、晶向、位错、 少数载流子寿命、氧含量、碳含量、 直径等 这些参数缺一不可
20112011-3-23
7
单晶硅生产
• 单晶硅生产有两大任务:一是要解决杂质控制问 题,另一个是要解决晶体结构问题。 • 杂质控制问题又分两方面,一方面要把有害的杂 质控制在目标含量之下, 另一方面要把三、五族 杂质及氧含量控制在目标范围之内。 • 晶体结构问题 要使硅原子极为有序地按一定方向 排列,不能有任何错位 • 目前硅单晶硅生产主要有两种方法:CZ法和FZ法, CZ法俗称直拉法,也称有坩埚法是由一个捷克人 切克劳斯基发明的,CZ是他姓的头两个字母。FZ 法也就是区域熔化法,简称区熔法, FZ是 floating zone (悬浮区域)的头两个字母,与有 坩埚法相对应,也称无坩埚法。
20112011-3-23
17
不同直径的1 不同直径的1公斤晶体的理论长度
晶体直径 (英寸) 3 4 5 6 8
晶体直径 76.2 (毫米) 晶体长度 94.1 (毫米)
101.6
127
152.4
203.2
52.9
33.9
23.5
13.24
20112011-3-23
18
重量 体积= 密度
体积 高度= 底面积
20112011-3-23 15
CZ 法单晶硅生长
1. 2. 3. 4. 5. 6. 7. 备料 装炉 抽空/检漏 抽空 检漏 化料 稳定 引晶 放肩
8. 转肩 9. 等径生长 10. 收尾 11. 停炉 热检漏 停炉/热检漏 12. 拆炉
20112011-3-23
16
直 径
• 直径也是太阳能用硅单晶的重要参数, 一般滚完圆的单晶直径为150mm。拉 出来的单晶直径应该在153mm 155mm之间,这样有利于后工序的生 产。现在硅单晶的交易中经常以理论 直径 的长度作为计量单位,如1米多少 钱。因此直径控制的精度是生产过程 中的重要因素,直接关系到生产成本。
中卫市银阳新能源 有限公司
培训资料
20112011-3-23
1
单晶生产工艺
Wafer
• Czochralski (CZ) Method
• Float Zone (FZ) Method
20112011-3-23
2
硅的性质
物理性质: 物理性质: 硅呈灰色金属光泽,性质较脆,切割时易 碎裂。硅的比重较小,硬度较大。硅属半金属, 是极为重要的元素半导体。在液态时,其表面 物 张力较大,从液态凝成固态时,体积膨胀较多。 性 熔 点: 1416±4℃, 质 1416± 理 沸 点: 3145℃; 3145℃ 固态密度: 20℃ 2.33克 固态密度:(20℃)2.33克/厘米3 液态密度: 1420℃ 2.54克 液态密度:(1420℃)2.54克/厘米3
20112011-3-23
32
等径生长
• • • • • • • 保持晶体的直径生长. 保持晶体的直径生长 晶体直径要稍大于目标直径以利于滚磨 按照生长工艺参数进行全自动控制: 按照生长工艺参数进行全自动控制 直径--拉速. 直径 温度 拉速 埚转(磁场强度 磁场强度) 氧含量 --- 埚转 磁场强度 晶体缺陷. 晶体缺陷 SPC 控制直径 控制直径.
20112011-3-23 26
化 料
• 化料最低埚位:平口以下100-110㎜ • 化料过程中注意观察炉内情况和电流、电 压表情况,如果电流表指针摆动单晶炉内 打火立即停炉; • 塌料后立即升高坩埚并开启埚转2转直至原 料完全熔化, 观察硅液面有无杂质,将其 杂质提出,化料情况记录在随工单上; • 硅原料化至只剩下20%时降低化料温度, 进行二次加料。
Wafer
20112011-3-23
14
直拉法的特点
• 用此方法生长直径200mm以上的硅单晶是 不困难的,单晶长度一般为1000mm以上。 这种方法生长的单晶硅径向杂质分布比较 均匀。但纵向分布就差一些。另外拉制单 晶时熔体直接与石英坩埚接触,会引进一 些氧原子及碳沾污,用直拉法生长的单晶 一般用于普通硅器件和集成电路的制造。 不适合做大功率可控硅等器件,因为它的 含氧、碳量高。击穿电压上不去,
20112011-3-23 22
母合金
• 所谓“母合金”就是杂质元素与硅的合金。 常用的母合金有硅磷和硅硼两种,杂质浓 度一般大于1013原子/cm3(ρ≈10-2—103 .cm)。采用母合金作掺杂剂是为了使掺 杂量更容易控制,更准确。
20112011-3-23
23
杂质补偿
1.P型单晶,N 型单晶,为什么掺硼 的单晶是P型的,为什么掺磷的单 晶是N 型的? 2.半导体导电类型和载流子浓度的是 两种杂质补偿后的净浓度, 即(ND5-NA3)或(NA-ND) 当ND>NA时,半导体呈N型; 当NA>ND时,半导体呈P型。
20112011-3-23 27
二次加料
1、在原料剩下20%未化完时,降温,准备二次加料 器加料。 A、首先要检查二次加料器底部四瓣叶片,是否完好, 有无裂纹。如果有裂纹必须更换。 B、检查后用无水乙醇擦拭干净,完好合并四瓣叶片。 C、将加料器垂直放入晶体框内,把原料倒入。 D、移开副室将加料器升入,打开副室泵,抽空,加 料。 E、升降加料器时,必须时刻注意加料器情况。防止 加料器的耳朵挂在副室口,导致拉断钢丝绳。 2、加料时注意温度控制,加完料后迅速提出加料器, 防止烧坏加料器,在提升加料器时,升到高温化料。
20112011-3-23
29
籽晶浸入/ 籽晶浸入/引晶
• • • • • • 籽晶下降接触熔体. 籽晶下降接触熔体 确保合适的温度使籽晶与熔体的接触. 确保合适的温度使籽晶与熔体的接触 开始引晶. 开始引晶 保持引晶时希望的拉速和直径以排除位错. 保持引晶时希望的拉速和直径以排除位错 CCD/SIMS 自动控制引晶直径 拉速 自动控制引晶直径 拉速. 控制引晶直径/拉速 直径控制开启. 直径控制开启
20112011-3-23
10
Float Zone (FZ) Method
Wafer
CZ method
20112011-3-23
11
区溶法生长的单晶
• 特点:纵向杂质分布比较好,但径向分布 不如直拉法的单晶,因为用这种方法生长 单晶时。熔体不接触任何东西(在真空或 保护气氛中生长),含氧量低且纯度高。 适于做大功率可控硅等器件。
20112011-3-23 20
型 号
• 型号分P型和N型两种: —— P型指其中的导电杂质以三族元素为主, 正电荷导电或者称之为空穴导电; ——N型指其中的导电杂质以五族元素为主, 负电荷导电或者称之为电子导电; • 型号用型号测试仪测量,常用的有冷热笔 法及整流法。 太阳能电池常用的是P型硅单晶。
20112011-3-23 19
电阻率
• 电阻率是常用的半导体材料参数,它反映了半导 体内杂质浓度的高低和半导体材料导电能力的强 弱。 • 电阻率为材料内平行于电流方向的电位梯度与电 流密度之比。 流密度之比。 • 电阻率是表现材料导电性质的物理量,是载流子 电阻率是表现材料导电性质的物理量, 在材料内流通难易程度的度量。 在材料内流通难易程度的度量。它是导电率的倒 数值上等于长一厘米、 数,数值上等于长一厘米、截面一平方厘米的材 料的电阻,单位为Ω 料的电阻,单位为Ω·cm。 。 • 电阻率也是硅单晶中三、五族元素杂质浓度一种 表示方式
20112011-3-23
30
•
用籽晶引出单晶后,开始缩颈。缩颈是为了排 除引出单晶中的位错。下种时,由于籽晶和熔硅 温差较大,高温的熔硅对籽晶造成强烈的热冲击, 籽晶头部产生大量的位错。通过缩颈后,使晶体 在生长中将位错“缩掉”,长成无位错单晶。缩 颈的方法有两种:慢缩颈和快缩颈。慢缩颈时熔 硅温度较高,主要控制温度,生长速度一般每分 钟0.8~2毫米.快缩颈时熔体温度较低,主要控制生 长速度,生长速度一般为每分钟2~8毫米.细颈的 直径一般为2~4毫米.沿(111)方向生长的硅单晶, 缩细颈的长度等于细颈直径的6~8倍,沿(100)方 向生长的硅单晶,缩细颈的长度等于细颈直径的 5~6倍.
20112011-3-23
3
温度对半导体材料电阻率的影响
• 对金属导体来说,当温度升高时,它的电 阻率增大,但变化幅度不大,而半导体与 此相反,当温度升高时,电阻率降低,温 度下降时,电阻率增大,而且变化幅度很 大。当温度变化300℃时,电阻率会改变几 千倍到几十万倍。当温度下降至接近绝对 零度(-273℃)时,半导体就成为绝缘体。