安监总管三〔2012〕31号
安监总管三〔〕号国家安全监管总局关于印发危险化学品企业事故隐患排查治理实施导则通知

国家安全监管总局关于印发危险化学品企业事故隐患排查治理实施导则的通知
安监总管三〔2012〕103号
各省、自治区、直辖市及新疆生产建设兵团安全生产监督管理局,有关中央企业:
隐患排查治理是安全生产的重要工作,是企业安全生产标准化风险管理要素的重点内容,是预防和减少事故的有效手段。
为了推动和规范危险化学品企业隐患排查治理工作,国家安全监管总局制定了《危险化学品企业事故隐患排查治理实施导则》(以下简称《导则》,请从国家安全监管总局网站下载),现印发给你们,请认真贯彻执行。
危险化学品企业要高度重视并持之以恒做好隐患排查治理工作。
要按照《导则》要求,建立隐患排查治理工作责任制,完善隐患排查治理制度,规范各项工作程序,实时监控重大隐患,逐步建立隐患排查治理的常态化机制。
强化《导则》的宣传培训,确保企业员工了解《导则》的内容,积极参与隐患排查治理工作。
各级安全监管部门要督促指导危险化学品企业规范开展隐患排查治理工作。
要采取培训、专家讲座等多种形式,大力开展《导则》宣贯,增强危险化学品企业开展隐患排查治理的主动性,指导企业掌握隐患排查治理的基本方法和工作要求;及时搜集和研究辖区内企业隐患排查治理情况,建立隐患排查治理信息管理系统,建立安全生产工作预警预报机制,提升危险化学品安全监管水平。
国家安全监管总局
2012年8月 7日附件:《危险化学品企业事故隐患排查治理实施导则》。
安监总管三 国家安全监管总局关于公布
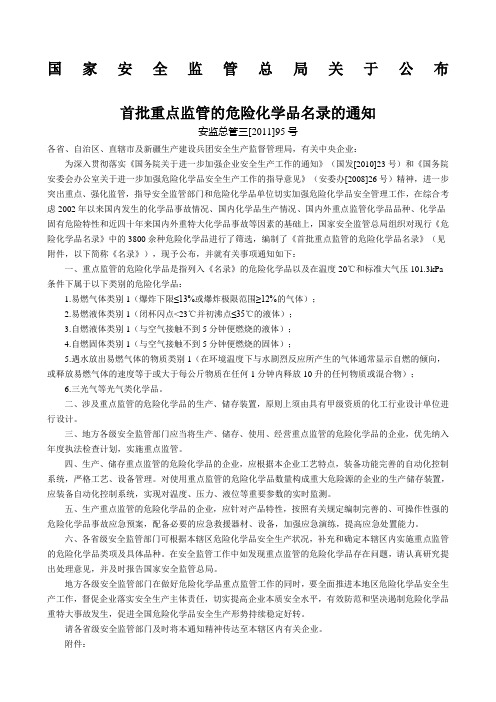
国家安全监管总局关于公布首批重点监管的危险化学品名录的通知安监总管三[2011]95号各省、自治区、直辖市及新疆生产建设兵团安全生产监督管理局,有关中央企业:为深入贯彻落实《国务院关于进一步加强企业安全生产工作的通知》(国发[2010]23号)和《国务院安委会办公室关于进一步加强危险化学品安全生产工作的指导意见》(安委办[2008]26号)精神,进一步突出重点、强化监管,指导安全监管部门和危险化学品单位切实加强危险化学品安全管理工作,在综合考虑2002年以来国内发生的化学品事故情况、国内化学品生产情况、国内外重点监管化学品品种、化学品固有危险特性和近四十年来国内外重特大化学品事故等因素的基础上,国家安全监管总局组织对现行《危险化学品名录》中的3800余种危险化学品进行了筛选,编制了《首批重点监管的危险化学品名录》(见附件,以下简称《名录》),现予公布,并就有关事项通知如下:一、重点监管的危险化学品是指列入《名录》的危险化学品以及在温度20℃和标准大气压101.3kPa 条件下属于以下类别的危险化学品:1.易燃气体类别1(爆炸下限≤13%或爆炸极限范围≥12%的气体);2.易燃液体类别1(闭杯闪点<23℃并初沸点≤35℃的液体);3.自燃液体类别1(与空气接触不到5分钟便燃烧的液体);4.自燃固体类别1(与空气接触不到5分钟便燃烧的固体);5.遇水放出易燃气体的物质类别1(在环境温度下与水剧烈反应所产生的气体通常显示自燃的倾向,或释放易燃气体的速度等于或大于每公斤物质在任何1分钟内释放10升的任何物质或混合物);6.三光气等光气类化学品。
二、涉及重点监管的危险化学品的生产、储存装置,原则上须由具有甲级资质的化工行业设计单位进行设计。
三、地方各级安全监管部门应当将生产、储存、使用、经营重点监管的危险化学品的企业,优先纳入年度执法检查计划,实施重点监管。
四、生产、储存重点监管的危险化学品的企业,应根据本企业工艺特点,装备功能完善的自动化控制系统,严格工艺、设备管理。
《关于加强“两重点一重大”企业安全监管 开展涉及爆炸性危险化学品生产、储存企业专项检查的通知》的通知

淄博市安全生产监督管理局(通知)淄安监字…2012‟38号关于转发省安监局《关于加强“两重点一重大”企业安全监管认真开展涉及爆炸性危险化学品生产、储存企业专项检查的通知》的通知各区县、高新区安监局,文昌湖区经发局,市管危险化学品企业:现将省安监局《关于加强“两重点一重大”企业安全监管认真开展涉及爆炸性危险化学品生产、储存企业专项检查的通知》(鲁安监发[2012] 38号)转发给你们,并结合我市实际,提出如下要求,请一并抓好贯彻落实。
一、摸清企业底数各区县、高新区、文昌湖区要全面、准确地掌握辖区内涉及“两重点一重大”(重点危险工艺、重点监管危化品和重大危险源)企业情况,建立完善的管理档案,将其作为重点监管对象,- 1 -落实责任,进一步强化监管措施。
请于4月20日前,将《重点危险工艺危险化学品企业统计表》(附件1)、《重点监管危险化学品企业统计表》(附件2)及《危险化学品重大危险源企业统计表》(附件3)报市安监局危化处。
二、强化安全监管一是加快化工装置设计安全诊断工作进度。
按照市安监局《转发省安监局关于开展化工装置设计安全诊断工作的意见的通知》(淄安监发[2011] 122号)要求,全市所有未经正规设计的化工生产装置和储存设施的安全诊断工作应于今年5月底之前全部完成。
请各区县加快进度,确保该项工作按期完成。
并于4月20日前将未经正规设计的化工生产装置和储存设施的安全诊断报告书汇总上报市安监局。
二是加大危险工艺自动化改造企业的监督、检查力度。
对照国家安监总局《首批重点监管的危险化工工艺安全控制要求、重点监控参数及推荐的控制方案》,对已实现危险工艺自动化改造的企业,按照淄安监发[2012] 18号要求,对运行情况进行检查,确保自动化装置的可靠有效运行。
三是根据省局部署,立即组织对涉及爆炸性危险化学品生产、储存企业开展专项安全检查。
摸清107种易爆炸重点危险化学品的生产、储存、经营(储存)企业底数,专项安全检查要求4月底前完成,请各区县、市管危险化学品企业并及时将检查情况报市安监局;5月底前,各区县安监局对检查发现问题的整改情况进行复查。
国家安全监管总局关于废止242件安全生产规范性文件的通知

劳部发〔1995〕398号 能源部海洋石油安全办 能源部海洋石油安全办 劳部发〔1995〕186号
危险化学品、化工、医药、 危险化学品、化工、医药、烟花爆竹行业安全监管类
42 43 44 45
安监管人字〔2002〕第12号 安监管人字〔2002〕第88号 煤安监人字〔2002〕第64号 煤安监司办字〔2002〕第19号
46
安监管人字〔2003〕31号
47
安监管人字〔2003〕85号
48
安监管人字〔2003〕139号
49
关于印发生产经营单位主要负责人和安全生 产管理人员安全资格证书样式的通知 关于印发《烟花爆竹生产经营单位主要负责 人、安全管理人员培训大纲及考核标准(试 行)》的通知 关于成立国家安全生产监督管理局(国家煤 矿安全监察局)培训工作指导委员会的通知 关于印发一二级安全生产培训机构评估标准 的通知 关于印发《煤矿主要负责人、安全生产管理 人员培训大纲及考核标准》的通知 关于进一步规范和加强特种作业操作证(IC 卡)管理工作的通知 关于印发2004年《注册安全工程师执业资格 考试大纲》的通知 关于印发《民用爆破器材生产经营单位主要 负责人、安全生产管理人员培训大纲及考核 标准(试行)》的通知 关于印发《安全评价人员考试管理办法(试 行)》和《安全评价人员考试要点(试行) 》的通知 关于印发《安全评价人员资格登记管理规则 》的通知 关于印发2006年《注册安全工程师执业资格 考试大纲》的通知 关于印发《2006年安全评价人员考试大纲》 的通知 关于印发开展安全评价人员继续教育工作的 通知 化学工业部关于加强对新入厂职工进行“三 级安全教育”的要求
65
关于国家安全生产监督管理局负责备案的石 油行业(不含石油化工、成品油管道)建设 项目(工程)安全预评价报告审查、备案事项 的通知 关于国家安全生产监督管理局负责备案的金 属非金属矿山及相关行业建设项目(工程) 安全预评价报告审查、备案的通知 关于海洋石油作业安全监督管理有关事项的 通知 关于国家安全生产监督管理局负责备案的金 属非金属及相关行业尾矿库安全预评价评审 、备案的通知 关于中央管理的非煤矿矿山企业安全生产许 可证颁发工作的函 关于贯彻落实《国务院关于进一步加强海洋 管理工作若干问题的通知》有关工作的通知 关于认真做好海洋石油天然气开采单位及生 产设施安全生产许可证颁发工作的通知 关于《非煤矿矿山企业安全生产许可证实施 办法》若干问题说明的通知 关于石油天然气企业安全生产许可证颁发工 作的补充通知 关于印发非煤矿矿山企业安全生产许可证申 请书等13种文书格式的通知 关于加强重大事故隐患安全监管工作的函 关于印发《金属非金属矿山安全质量标准化 企业考评办法及标准(试行)》的通知 关于做好非煤矿矿山企业安全生产许可证颁 发管理工作有关问题的通知 关于印发《海洋石油事故报告和调查处理指 导意见》的通知 关于加强非煤矿矿山及石油、冶金、有色、 建材等相关行业建设项目安全设施“三同时 ”工作的通知 关于加强非煤矿山及相关行业安全生产法规 和标准宣传贯彻工作的通知
国家安全监管总局关于宣布失效一批安全生产文件的通知

国家安全监管总局关于宣布失效一批安全生产文件的
通知
文章属性
•【制定机关】国家安全生产监督管理总局(已撤销)
•【公布日期】2018.02.12
•【文号】安监总政法〔2018〕28号
•【施行日期】2018.02.12
•【效力等级】部门规范性文件
•【时效性】现行有效
•【主题分类】法制工作
正文
国家安全监管总局关于宣布失效一批安全生产文件的通知
安监总政法〔2018〕28号各省、自治区、直辖市及新疆生产建设兵团安全生产监督管理局,各省级煤矿安全监察局:
为贯彻落实党中央、国务院关于加强法治政府建设和推进简政放权、放管结合、优化服务的决策部署,维护法令统一,进一步推进依法行政,国家安全监管总局对有关安全生产方面的部门文件进行了全面清理。
经商有关部委和单位,并经国家安全监管总局局长办公会议审议通过,决定对193件安全生产文件宣布失效,自本通知印发之日起一律停止执行,不再作为行政管理的依据。
附件:1.宣布失效的安全生产文件目录(2014年)
2.宣布失效的安全生产文件目录(2015年)
3.宣布失效的安全生产文件目录(2016年)
国家安全监管总局
2018年2月12日
附件1
附件2
附件3。
危险化学品企业事故隐患排查治理实施导则(安监总管三[2012]103号
![危险化学品企业事故隐患排查治理实施导则(安监总管三[2012]103号](https://img.taocdn.com/s3/m/6c6ffe4f7e21af45b307a855.png)
危险化学品企业事故隐患排查治理实施导则国家安全生产监督管理总局2012年7月目录1 总则2 基本要求3 隐患排查方式及频次3.1 隐患排查方式3.2 隐患排查频次确定4 隐患排查内容4.1 安全基础管理4.2 区域位置和总图布置4.3 工艺管理4.4 设备管理4.5 电气系统4.6 仪表系统4.7 危险化学品管理4.8 储运系统4.9 消防系统4.10 公用工程系统5 隐患治理与上报5.1 隐患级别5.2 隐患治理5.3 隐患上报附录A重大事故隐患风险评估方法附件各专业隐患排查表1安全基础管理隐患排查表2 区域位置及总图布置隐患排查表3 工艺隐患排查表4 设备隐患排查表5 电气系统隐患排查表6 仪表隐患排查表7 危险化学品管理隐患排查表8 储运系统隐患排查表9 公用工程隐患排查表10 消防系统隐患排查表1 总则1.1 为了切实落实企业安全生产主体责任,促进危险化学品企业建立事故隐患排查治理的长效机制,及时排查、消除事故隐患,有效防范和减少事故,根据国家相关法律、法规、规章及标准,制定本实施导则。
1.2 本导则适用于生产、使用和储存危险化学品企业(以下简称企业)的事故隐患排查治理工作。
1.3 本导则所称事故隐患(以下简称隐患),是指不符合安全生产法律、法规、规章、标准、规程和安全生产管理制度的规定,或者因其他因素在生产经营活动中存在可能导致事故发生或导致事故后果扩大的物的危险状态、人的不安全行为和管理上的缺陷,包括:(1)作业场所、设备设施、人的行为及安全管理等方面存在的不符合国家安全生产法律法规、标准规范和相关规章制度规定的情况。
(2)法律法规、标准规范及相关制度未作明确规定,但企业危害识别过程中识别出作业场所、设备设施、人的行为及安全管理等方面存在的缺陷。
2 基本要求2.1 隐患排查治理是企业安全管理的基础工作,是企业安全生产标准化风险管理要素的重点内容,应按照“谁主管、谁负责”和“全员、全过程、全方位、全天候”的原则,明确职责,建立健全企业隐患排查治理制度和保证制度有效执行的管理体系,努力做到及时发现、及时消除各类安全生产隐患,保证企业安全生产。
安监总厅管三〔 〕 号危险化学品建设项目安全设施设计专篇编制导则

危险化学品建设项目安全设施设计专篇编制导则1适用范围本导则适用于中华人民共和国境内新建、改建、扩建危险化学品生产、储存的建设项目以及伴有危险化学品产生的化工建设项目(包括危险化学品长输管道建设项目,以下统称建设项目)安全设施设计专篇的编制。
本导则不适用于下列建设项目:1)危险化学品的勘探、开采及其辅助的储存;2)原油和天然气勘探、开采的配套输送及储存;3)城镇燃气的输送及储存。
2术语和定义2.1危险化学品具有毒害、腐蚀、爆炸、燃烧、助燃等性质,对人体、设施、环境具有危害的剧毒化学品及其他化学品。
2.2安全设施在生产经营活动中用于预防、控制、减少与消除事故影响采用的设备、设施、装备及其他技术措施的总称。
2.3新建项目有下列情形之一的项目为新建项目:1)新设立的企业建设危险化学品生产、储存装置(设施),或者现有企业建设与现有生产、储存活动不同的危险化学品生产、储存装置(设施)的;2)新设立的企业建设伴有危险化学品产生的化学品生产装置(设施),或者现有企业建设与现有生产活动不同的伴有危险化学品产生的化学品生产装置(设施)的。
2.4改建项目有下列情形之一的项目为改建项目:1)企业对在役危险化学品生产、储存装置(设施),在原址更新技术、工艺、主要装置(设施)、危险化学品种类的;2)企业对在役伴有危险化学品产生的化学品生产装置(设施),在原址更新技术、工艺、主要装置(设施)的。
2.5扩建项目有下列情形之一的项目为扩建项目:1)企业建设与现有技术、工艺、主要装置(设施)、危险化学品品种相同,但生产、储存装置(设施)相对独立的;2)企业建设与现有技术、工艺、主要装置(设施)相同,但生产装置(设施)相对独立的伴有危险化学品产生的。
2.6危险源可能导致人身伤害、健康损害、财产损失、工作环境破坏或这些情况组合的根源或状态。
2.7危险和有害因素可对人造成伤亡、影响人的身体健康甚至导致疾病的因素。
2.8危险化学品数量长期或临时生产、加工、使用或储存危险化学品的数量。
国家安全监管总局关于河北克尔化工有限责任公司“2·28”重大爆炸事故情况的通报
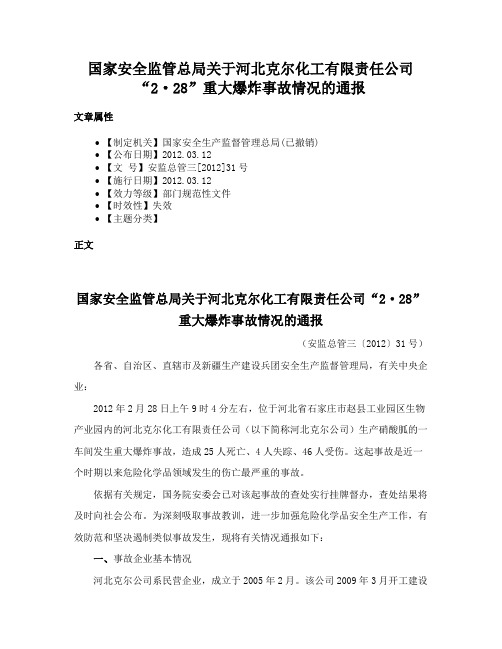
国家安全监管总局关于河北克尔化工有限责任公司“2·28”重大爆炸事故情况的通报文章属性•【制定机关】国家安全生产监督管理总局(已撤销)•【公布日期】2012.03.12•【文号】安监总管三[2012]31号•【施行日期】2012.03.12•【效力等级】部门规范性文件•【时效性】失效•【主题分类】正文国家安全监管总局关于河北克尔化工有限责任公司“2·28”重大爆炸事故情况的通报(安监总管三〔2012〕31号)各省、自治区、直辖市及新疆生产建设兵团安全生产监督管理局,有关中央企业:2012年2月28日上午9时4分左右,位于河北省石家庄市赵县工业园区生物产业园内的河北克尔化工有限责任公司(以下简称河北克尔公司)生产硝酸胍的一车间发生重大爆炸事故,造成25人死亡、4人失踪、46人受伤。
这起事故是近一个时期以来危险化学品领域发生的伤亡最严重的事故。
依据有关规定,国务院安委会已对该起事故的查处实行挂牌督办,查处结果将及时向社会公布。
为深刻吸取事故教训,进一步加强危险化学品安全生产工作,有效防范和坚决遏制类似事故发生,现将有关情况通报如下:一、事故企业基本情况河北克尔公司系民营企业,成立于2005年2月。
该公司2009年3月开工建设的年产10000吨噁二嗪、1500吨2-氯-5-氯甲基吡啶、1500吨西林钠、1000吨N-氰基乙亚胺酸乙酯项目,总投资2.17亿元。
一期工程包括一车间(硝酸胍)、二车间(硝基胍)、配电室、动力站(包括空压站和1台制冷机组)、固体库、一次水池和循环消防水池,设计单位为河北渤海工程设计有限公司(乙级资质),于2010年2月底竣工。
河北克尔公司现有职工351人,2010年9月6日取得了危险化学品安全生产许可证。
二、事故简要经过河北克尔公司一车间共有8个反应釜,依次为1-8号反应釜。
原设计用硝酸铵和尿素为原料,生产工艺是硝酸铵和尿素在反应釜内混合加热熔融,在常压、175-220℃条件下,经8-10小时的反应,间歇生产硝酸胍,原料熔解热由反应釜外夹套内的导热油提供。
危险化学品企业事故隐患排查治理实施导则安监总管三
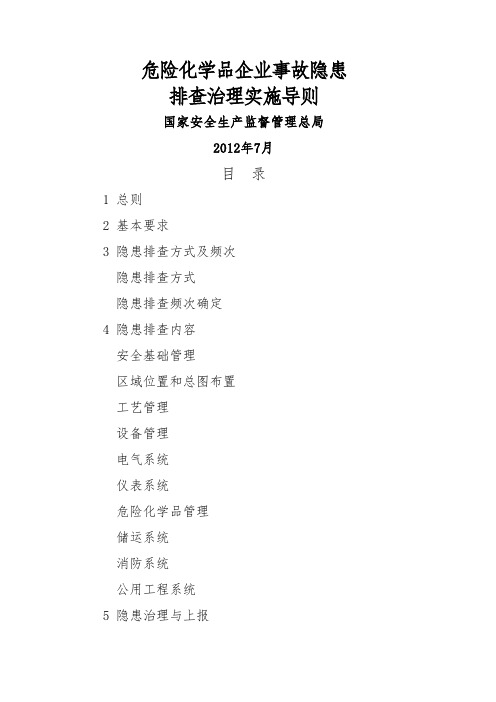
危险化学品企业事故隐患排查治理实施导则国家安全生产监督管理总局2012年7月目录1 总则2 基本要求3 隐患排查方式及频次隐患排查方式隐患排查频次确定4 隐患排查内容安全基础管理区域位置和总图布置工艺管理设备管理电气系统仪表系统危险化学品管理储运系统消防系统公用工程系统5 隐患治理与上报隐患级别隐患治理隐患上报附录A:重大事故隐患风险评估方法附件:各专业隐患排查表1安全基础管理隐患排查表2 区域位置及总图布置隐患排查表3 工艺隐患排查表4 设备隐患排查表5 电气系统隐患排查表6 仪表隐患排查表7 危险化学品管理隐患排查表8 储运系统隐患排查表9 公用工程隐患排查表10 消防系统隐患排查表1 总则为了切实落实企业安全生产主体责任,促进危险化学品企业建立事故隐患排查治理的长效机制,及时排查、消除事故隐患,有效防范和减少事故,根据国家相关法律、法规、规章及标准,制定本实施导则。
本导则适用于生产、使用和储存危险化学品企业(以下简称企业)的事故隐患排查治理工作。
本导则所称事故隐患(以下简称隐患),是指不符合安全生产法律、法规、规章、标准、规程和安全生产管理制度的规定,或者因其他因素在生产经营活动中存在可能导致事故发生或导致事故后果扩大的物的危险状态、人的不安全行为和管理上的缺陷,包括:(1)作业场所、设备设施、人的行为及安全管理等方面存在的不符合国家安全生产法律法规、标准规范和相关规章制度规定的情况。
(2)法律法规、标准规范及相关制度未作明确规定,但企业危害识别过程中识别出作业场所、设备设施、人的行为及安全管理等方面存在的缺陷。
2 基本要求隐患排查治理是企业安全管理的基础工作,是企业安全生产标准化风险管理要素的重点内容,应按照“谁主管、谁负责”和“全员、全过程、全方位、全天候”的原则,明确职责,建立健全企业隐患排查治理制度和保证制度有效执行的管理体系,努力做到及时发现、及时消除各类安全生产隐患,保证企业安全生产。
煤安监监察〔2012〕32号 修改增加《煤矿建设项目安全设施设计审查与竣工验收报告书》部分内容

八 电气系统 1.高瓦斯矿井、煤(岩)与瓦斯(二氧化碳)突出矿井、瓦斯矿井中高瓦斯区的煤巷、半煤岩巷 和有瓦斯涌出的岩巷掘进工作面正常工作的局部通风机必须配备安装同等能力的备用局部通 风机,并能自动切换。正常工作的局部通风机必须采用三专(专用开关、专用电缆、专用变 压器)供电,专用变压器最多可向4套不同掘进工作面的局部通风机供电;备用局部通风机 电源必须取自同时带电的另一电源,当正常工作的局部通风机故障时,备用局部通风机能自 动启动,保持掘进工作面正常通风。 2.其他掘进工作面和通风地点正常工作的局部通风机可不配备安装备用局部通风机,但正常 工作的局部通风机必须采用三专供电;或正常工作的局部通风机配备安装一台同等能力的备 用局部通风机,并能自动切换。正常工作的局部通风机和备用局部通风机的电源必须取自同 时带电的不同母线段的相互独立的电源,保证正常工作的局部通风机故障时,备用局部通风 机正常工作。 3.使用局部通风机供风的掘进工作面必须实行风电闭锁和瓦斯电闭锁;使用2台局部通风机 供风的,2台局部通风机都必须同时实现风电、瓦斯电闭锁。 十一 矿山救援、保健与安全培训 4 安全管理 矿井必须建立安全管理机构,健全管理制度。 5 安全培训 安全培训机构设置、场所与设施符合批准的安全设施设计要求。
7.1 安全监控系统
新增
7.2
3.矿井各个人员出入井口、重点区域出入口、限制区域等地点均应设置分站,并能满足监测 携卡人员出入井、出入重点区域、出入限制区域的要求;巷道分支处应设置分站,并能满足 人员定位系统 监测携卡人员出入方向的要求。煤矿紧急避险设施入口和出口应分别设置分站,并能满足对 出、入紧急避险设施的人员进行实时监测的要求。 4.矿井调度室应设人员定位系统地面中心站。 1.所有井工煤矿应为入井人员配备额定防护时间不低于30min的隔离式自救器。
危险化学品生产使用企业老旧装置安全风险评估细则

陷,使用单位应当制定修复方案。修复后, 检验机构应当对修复部位进行检查确认; 对不易修复的严重缺陷,也可以采用安全 评定的方法,确认缺陷是否影响管道安全
查方案或 台账、报
告
运行到下一个全面检验周期。
压力管道的安全状况等级为 3 级的,一般
不超过 3 年检验一次,在使用期间内,使 用单位应当对管道采取有效的监控措施; 安全状况等级为 4 级的,使用单位应当对 管道缺陷进行处理(缺陷处理的方式包括 采用修理的方法消除缺陷或者进行合于使
存 设 施 风 险 基 准 》 50
(GB36894-2018);《危险化 学品重大危险源监督管理暂
行规定》(国家安全监管总局
令第 40 号)
3
在役装置应经过正规设计,未经过正 规设计的在役化工装置应进行安全 设计诊断。
查设计文 件
《关于开展提升危险化学品
领域本质安全水平专项行动 的通知》(安监总管三〔2012〕
生产技术工艺设备目录(第一
批)》(应急厅〔2020〕38 号);
《淘汰落后安全技术工艺、设
备目录(2016 年)》(安监总 50
科技〔2016〕137 号);《淘
汰落后安全技术装备目录
(2015 年第一批)》(安监总Βιβλιοθήκη 科技〔2015〕75 号)
《危险化学品生产装置和储
存设施外部安全防护距离确
定方法》(GB/T37243-2019); 《危险化学品生产装置和储
全技术监察规程》 (TSG21-2016;《压 力 容 器 》 ( GB/T 150.1-2011)
查相关制 《固定式压力容器安 度、文件、 全 技 术 监 察 规 程 》
证件 (TSG21-2016)
使用单位应对压力容器开展定期自行检 查,包括月度检查、年度检查。每月对所 使用的压力容器至少进行 1 次月度检查并 记录,当年度检查与月度检查时间重合时, 查记录、 可不再进行月度检查。每年对所使用的压 报告 力容器至少进行 l 次年度检查,并出具检 查报告,进行压力容器使用安全状况分析, 并对年度检查中发现的隐患及时消除。
电力行业安全评价依据的法律、法规、标准(最新整理)

1.2.1国家法律(1)《中华人民共和国安全生产法》(国家主席令[2014]第13号);(2)《中华人民共和国劳动合同法》(国家主席令[2012]第73号);(3)《中华人民共和国电力法》(国家主席令[2015]第24号);(4)《中华人民共和国消防法》(国家主席令[2008]第6号);(5)《中华人民共和国防震减灾法》(国家主席令[2008]第7号);(6)《中华人民共和国职业病防治法》(国家主席令[2011]第52号,2016年修订);(7)《中华人民共和国道路交通安全法》(国家主席令[2011]第47号);(8)《中国人民共和国突发事件应对法》(国家主席令[2007]第69号);(9)《中华人民共和国气象法》(国家主席令[1999]第23号,2009年修订);(10)《中华人民共和国清洁生产促进法》(国家主席令[2012]第54号);(11)《中华人民共和国防洪法》(国家主席令[1997]第88号,2016年修正版);(12)《中华人民共和国建筑法》(国家主席令[2011]第46号);(13)《中华人民共和国特种设备安全法》(国家主席令[2013]第4号);(14)《中华人民共和国社会保险法》(国家主席令[2010]第35号);(15)《中华人民共和国环境保护法》(国家主席令[2014]第9号);1.2.2国家法规(1)《建设工程安全生产管理条例》(国务院第393号令);(2)《建设项目安全设施“三同时”监督管理办法》(国家安监总局[2015]第77号令修改);(3)《电力监管条例》(国务院第432号令);(4)《中华人民共和国道路运输条例》(国务院第406号令);(5)《地质灾害防治条例》(国务院第394号令);(6)《特种设备安全监察条例》(国务院第549号令修订版);(7)《危险化学品安全管理条例》(国务院令第645号修正);(8)《生产安全事故报告和调查处理条例》(国务院第493号令);(9)《使用有毒物品作业场所劳动保护条例》(国务院第352号令);(10)《女职工劳动保护特别规定》(国务院第619号令);(11)《电力安全事故应急处置和调查处理条例》(国务院第599号令);(12)《易制毒化学品管理条例》(国务院第455号令,2017年修正);(13)《监控化学品管理条例》(国务院令第190号);(14)《国务院关于进一步加强企业安全生产工作的通知》(国务院第23号令);(15)《工伤保险条例》(国务院令第586号,2010年修订);(16)《气象灾害防御条例》(国务院第570号令,2017年修订);(17)《电力设施保护条例》(国务院第239号令,2011年修订);(18)《建设工程质量管理条例》(国务院令第279号,2017年修订);(19)《安全生产许可证条例》(国务院令第397号,2014年修订);(20)《工伤保险条例》(国务院第586号令,2010年修订);(21)《中华人民共和国防汛条例》(国务院令第441号,2011年修正);(22)《建设工程勘察设计管理条例》(国务院令第293号,2017年修订);(23)《电网调度管理条例》(国务院第115号令,2011年修正);(24)《国家突发公共事件总体应急预案》(国务院2006年1月8日);1.2.3地方性法规及文件(1)《山西省安全生产条例》(2016年12月8日山西省第十二届人民代表大会常务委员会第三十二次会议修订版);(2)《山西省人民政府办公厅转发省安委办关于加强安全生产三项建设的实施方案的通知》(晋政办发[2009]180号);(3)《山西省防雷减灾管理办法》(山西省人民政府令第213号);(4)《山西省消防条例》(2010年11月1日起实施);(5)《山西省防雷减灾管理办法》(山西省人民政府令第213号);(6)《山西省安全生产应急预案管理办法》(晋安监应急字[2008]370号);(7)《山西省安全生产事故隐患排查治理制度》(晋政发[2008]3号);(8)《山西省危险化学品安全管理办法》(山西省人民政府令第184号);(9)《山西省建筑工程质量和建筑安全生产管理条例》(2011年7月1日施行);(10)《山西省人民政府关于贯彻落实国发[2010]23号文件精神进一步加强企业安全生产工作的意见》(晋政发[2010]24号);1.2.4政府部门规章及规范性文件(1)《<生产安全事故报告和调查处理条例>罚款处罚暂行规定》(国家安全生产监督管理总局第13号令);(2)《安全生产事故隐患排查治理暂行规定》(国家安监总局第16号令);(3)《安全生产事故信息报告和处置办法》(国家安监总局令2009年第21号);(4)《特种作业人员安全技术培训考核管理规定》(国家安监总局令第30号,63号令修改);(5)《建设项目安全设施“三同时”监督管理办法》(国家安监总局第36号令,2015年第77号修改);(6)《危险化学品重大危险源监督管理暂行规定》(国家安监总局第40号令,2015年第79号修改);(7)《安全生产培训管理办法》(国家安监总局令第44号,63号令修改);(8)《国家安全监管总局关于修改<生产安全事故报告和调查处理条例>罚款处罚暂行规定等四部规章的决定》(国家安监总局令第77号令);(9)《工贸企业有限空间作业安全管理与监督暂行规定》(安监总局令[2013]第59号,80号令修改);(10)《生产经营单位安全培训规定》(国家安全生产监督管理总局第80号令修正);(11)《生产安全事故应急预案管理办法》(国家安监总局令88号);(12)《用人单位劳动防护用品管理规范》(国家安监总厅安健[2015]124号);(13)《关于印发企业安全生产责任体系五落实五到位规定的通知》(安监总办[2015]27号);(14)《国家安全监管总局关于进一步加强企业安全生产规范化建设严格落实企业安全生产主体责任的指导意见》(安监总办[2010]139号);(15)《关于规范重大危险源监督与管理工作的通知》(安监总协调字[2005]125号);(16)《国家安全监管总局办公厅关于印发生产经营单位生产安全事故应急预案评审指南(试行)的通知》(安监总厅应急[2009] 73号);(17)《国家安全监管总局关于公布首批重点监管的危险化学品名录的通知》(安监总管三[2011]95号);(18)《国家安全监管总局办公厅关于开展工贸企业有限空间作业条件确认工作的通知》(安监总厅管四〔2014〕37号);(19)《国家安全监管总局关于印发开展工贸企业较大危险因素辨识管控提升防范事故能力行动计划的通知》(安监总管四〔2016〕31号);(20)《国家安全监管总局关于公布第二批重点监管危险化学品名录的通知》(安监总管三〔2013〕12号);(21)《危险化学品名录》(2015年版);(22)《机械行业较大危险因素辨识与防范指导手册》(安监总管四〔2016〕31号);(23)《国家安全监管总局办公厅关于印发《工贸行业重点可燃性粉尘目录(2015版)》和《工贸行业可燃性粉尘作业场所工艺设施防爆技术指南(试行)》的通知》(安监总厅管四〔2015〕84号);(24)《工贸行业重大生产安全事故隐患判定标准(2017版)》(安监总管四〔2017〕129号);(25)《国务院关于全面加强应急管理工作的意见》(国发[2006] 24号);(26)《国务院办公厅关于进一步做好防雷减灾工作的通知》(国办发明电[2006]28号);(27)《国务院关于进一步加强防震减灾工作的意见》(国发[2010]18号);(28)《国务院关于进一步加强企业安全生产工作的通知》(国发[2010]23号);(29)《国务院安委会关于深入开展企业安全生产标准化建设的指导意见》(安委[2011]4号);(30)《国务院关于坚持科学发展安全发展促进安全形势持续稳定好转的意见》(国发〔2011〕40号);(31)《国务院关于加强和改进消防工作的意见》(国发[2011]46号);(32)《国务院办公厅关于印发突发事件应急预案管理办法的通知》(国办发〔2013〕101号);(33)《企业安全生产费用提取和使用管理办法》(财政部、安监总局财企 [2012]第16号);(34)《起重机械安全监察规定》(国家质量监督检验检疫总局第92号令);(35)《锅炉压力容器使用登记管理办法》(国质检锅[2003]207号);(36)《气瓶安全监察规程》(国家质量监督检验检疫总局第46号令);(37)《压力管道安装安全质量监督检验规则》(国质检锅[2002]83号);(38)《国家质量监督检验检疫总局关于修改<特种设备作业人员监督管理办法>的决定》(国家质量监督检验检疫总局令[2011]140号);(39)《公安部关于修改(建设工程消防监督管理规定)的决定》(公安部第119号令);(40)《公安部关于修改(消防监督检查规定)的决定》(公安部第120号令);(41)《仓库防火安全管理规则》(公安部第6号令);(42)《建设工程消防监督管理规定》(公安部第106号);(43)《职业健康监护管理办法》(卫生部第23号令);(44)《建筑起重机械安全监督管理规定》(建设部令166号);(45)《工程建设标准强制性条文》(电力工程部分)(建标[2011]年版);(46)《关于加强重大工程安全质量保障措施的通知》(发改投资[2009]3183号);(47)《关于印发<危险性较大的分部分项工程安全管理办法>的通知》(建质[2009]87号);(48)《防雷减灾管理办法》(中国气象局第20号令);(49)《防雷装置设计及竣工验收规定》(中国气象局令第21号);(50)《国家电力监管委员会安全生产令》(电监会1号令);(51)《电力安全事故调查程序规定》(电监会31号令);(52)《电力监控系统安全防护规定》(国家发改委〔2014〕14号令);(53)《电力安全隐患监督管理暂行规定》(电监安全〔2013〕5号);(54)《国家电力监管委员会关于加强电力行业地质灾害防范工作的指导意见》(电监安全〔2013〕6号);(55)《电力可靠性监督管理办法》(电监24号令);(56)《电力安全生产监管办法》(国家发改委〔2015〕21号令);(57)《关于印发<国家电网公司十八项电网重大反事故措施>(修订版)的通知》(国家电网生[2012]352号);(58)(《关于印发〈电力突发事件应急演练导则(试行)〉等文件的通知》(电监安全[2009]22号);(59)《关于印发<电力企业应急预案管理办法>的通知》(电监安全[2009]61号);(60)《关于印发<发电企业安全生产标准化规范及达标评级标准>的通知》(电监安全[2011]23号);(61)《电力安全生产监管办法》(电监会令第2号);(62)《电力生产事故调查暂行规定》(电监会4号令);(63)《电力二次系统安全防护规定》(国家电力监管委员会令2004年第5号);(64)《防止电力生产事故的二十五项重点要求》(国能安全[2014]161号);1.2.5国家标准及规范(1)《危险化学品重大危险源辨识》(GB18218-2009);(2)《生产过程危险和有害因素分类与代码》(GB/T13861-2009);(3)《企业职工伤亡事故分类》(GB 6441-1986)(4)《生产过程安全卫生要求总则》(GB/T12801-2008);(5)《生产设备安全卫生设计总则》(GB5083-1999);(6)《常用化学危险品贮存通则》(GB 15603-1995);(7)《建筑设计防火规范》(GB 50016-2014)(2018版);(8)《建筑地基基础设计规范》(GB 50007-2011);(9)《建筑工程抗震设防分类标准》(GB 50223-2008);(10)《建筑结构荷载规范》(GB50009-2012);(11)《混凝土结构设计规范》(GB 50010-2010);(12)《中国地震动参数区划图》(GB 18306-2015)(13)《建筑照明设计标准》(GB50034-2013);(14)《建筑物防雷设计规范》(GB50057-2010);(15)《建筑抗震设计规范(附条文说明)(2016年版)》(GB50011-2010);(16)《构筑物抗震设计规范》(GB50191-2012);(17)《建筑物电子信息系统防雷技术规范》(GB50343-2012);(18)《建筑采光设计标准》(GB 50033-2013);(19)《室外给水设计规范》(GB50013-2006);(20)《室外排水设计规范(2016年版)》(GB50014-2006);(21)《建筑给水排水设计规范》(2009年版)(GB 50015-2003);(22)《工业循环冷却水处理设计规范》(GB/T 50050-2017);(23)《爆炸和火灾危险环境电力装置设计规范》(GB50058-2014);(24)《爆炸性气体环境用电气设备第14部分:危险场所分类》(GB3836.14-2014);(25)《火灾自动报警系统设计规范》(GB50116-2013);(26)《消防安全标志第1部分:标志》(GB13495.1—2015);(27)《消防安全标志设置要求》(GB 15630-1995);(28)《自动喷水灭火系统设计规范》(GB50084-2017);(29)《气体灭火系统设计规范》(GB 50370-2005);(30)《泡沫灭火系统设计规范》(GB50151-2010);(31)《消防给水及消火栓系统技术规范》(GB50974-2014);(32)《水喷雾灭火系统设计规范》(GB50219-2014);(33)《建筑灭火器配置设计规范》(GB50140-2005);(34)《建筑灭火器配置验收检查规范》(GB50444-2008);(35)《火灾自动报警系统设计规范》(GB50116-2013);(36)《固定式钢梯及平台安全要求第1部分:钢直梯》(GB4053.1-2009);(37)《固定式钢梯及平台安全要求第2部分:钢斜梯(GB4053.2-2009);(38)《固定式钢梯及平台安全要求第3部分:工业防护栏杆及钢平台》(GB4053.3-2009);(39)《机械安全防护装置固定式和活动式防护装置设计与制造一般要求》(GB /T8196-2003);(40)《机械安全避免人体各部位挤压的最小间距》(GB 12265.3-1997);(41)《机械安全火灾防治》(GB 23819-2009);(42)《毒害性商品储藏养护技术条件》(GB17916-2013);(43)《腐蚀性商品储藏养护技术条件》(GB17915-2013);(44)《易燃易爆性商品储藏养护技术条件》(GB17914-2013);(45)《工业管道的基本识别色、识别符号和安全标识》(GB7231-2003);(46)《工业企业设计卫生标准》(GBZ 1-2010);(47)《工作场所有害因素职业接触限值第1部分:化学有害因素》(GBZ2.1-2007);(48)《工作场所有害因素职业接触限值第2部分:物理因素》(GBZ 2.2-2007);(49)《工作场所有毒气体检测报警装置设置规范》(GBZ/T223-2009);(50)《工作场所职业病危害警示标识》(GBZ158-2003);(51)《个体防护装备选用规范》(GB/T11651-2008);(52)《工业金属管道设计规范》(GB50316-2000,2008版);(53)《工业建筑供暖通风与空气调节设计规范》(GB50019-2015);(54)《工业企业厂内铁路、道路运输安全规程》(GB4387-2008);(55)《工业企业总平面设计规范》(GB50187-2012);(56)《工业建筑防腐蚀设计规范》(GB 50046-2008);(57)《钢结构设计规范》(GB50017-2003);(58)《压缩空气站设计规范》(GB50029-2014);(59)《化学品生产单位特殊作业安全规程》(GB 30871-2014);(60)《安全标志及其使用导则》(GB2894-2008);(61)《气瓶颜色标志》(GB/T7144-2016);(62)《安全色》(GB2893-2008);(63)《安全阀一般要求》(GB/T12241-2005);(64)《普通柴油》(GB252-2015);(65)《石油库设计规范》(GB50074-2014);(66)《粉尘防爆安全规程》(GB15577-2007);(67)《20KV及以下变电所设计规范》(GB50053-2013);(68)《防止静电事故通用导则》(GB12158-2006);(69)《用电安全导则》(GB/T13869-2008);(70)《供配电系统设计规范》(GB50052-2009);(71)《低压配电设计规范》(GB50054-2011);(72)《3~110kV高压配电装置设计规范》(GB50060-2008);(73)《35kV~110kV变电站设计规范》(GB50059-2011);(74)《建设工程施工现场消防安全技术规范》(GB 50720-2011);(75)《生产经营单位安全生产事故应急预案编制导则》(GB/T 29639—2013);(76)《剩余电流动作保护装置安装和运行》(GB13955-2005);(77)《系统接地的型式及安全技术要求》(GB14050-2008);(78)《自动化仪表工程施工及验收规范》(GB 50093-2013);(79)《密闭空间作业职业危害防护规范》(GBZ/T205-2007);(80)《带式运输机安全规范》(GB14784-2013);(81)《工业控制计算机系统通用规范第一部分:通用要求》(GB/T26802.1-2011);(82)《职业安全卫生术语》(GB/T15236-2008);(83)《职业性接触毒物危害程度分级》(GBZ 230-2010);(84)《工业企业噪声控制设计规范》(GB/T50087-2013);(85)《防洪标准》(GB 50201-2014);(86)《电梯制造与安装安全规范》(GB7588-2003/XG1-2015);(87)《大中型火力发电厂设计规范》(GB 50660-2011);(88)《小型火力发电厂设计规范》(GB50049-2011);(89)《火力发电厂与变电站设计防火规范》(GB50229-2006);(90)《电力工程电缆设计规范》(GB50217-2007);(91)《电气装置安装工程电缆线路施工及验收规范》(GB50168-2006);(92)《电气装置安装工程电气设备交接试验标准》(GB50150-2016);(93)《电气装置安装工程旋转电机施工及验收规范》(GB50170-2006);(94)《六氟化硫电气设备中气体管理和检测导则》(GB/T8905-2012);(95)《电厂用运行中汽轮机油质量标准》(GB7596-2017);(96)《固定式发电用汽轮机规范》(GB/T5578-2007);(97)《发电机组并网安全条件及评价》(GB/T28566-2012);(98)《电气装置安装工程盘、柜及二次回路结线施工及验收规范》(GB50171-2012);(99)《电气装置安装工程接地装置施工及验收规范》(GB50169-2016);(100)《继电保护和安全自动装置技术规程》(GB/T14285-2006);(101)《电力安全工作规程发电厂和变电站电气部分》(GB26860-2011);(102)《火力发电机组及蒸汽动力设备水汽质量》(GB/T12145-2016);(103)《电力装置的继电保护和自动装置设计规范》(GB/T50062-2008);(104)《国家电气设备安全技术规范》(GB19517-2009);(105)《电力设施抗震设计规范》(GB50260-2013);(106)《外壳防护等级》(IP代码)(GB/T4208-2017);(107)《动力机器基础设计规范》(GB50040-1996);(108)《干式电力变压器技术参数和要求》(GB/T 10228-2015);(109)《交流电气装置的接地设计规范》(GB50065-2011);(110)《电力工程直流电源设备通用技术条件及安全要求》(GB/T19826-2014);(111)《工业锅炉水质》(GB/Tl576-2008);(112)《锅炉房设计规范》(GB 50041-2008);(113)《工业用水软化除盐设计规范》(GB/T 50109-2014);(114)《电业安全工作规程第1部分:热力和机械》(GB26164.1-2010);(115)《电业安全工作规程第2部分发电厂电气及变电部分》(GB26164.2-2010);(116)《电气装置安装工程母线装置施工及验收规范》(GB50149-2010);(117)《工业企业电气设备抗震设计规范》(GB50556-2010);(118)《电气装置安装工程电气设备交接试验标准》(GB 50150-2006);(119)《运行中变压器油质量》(GB/T7595-2017);(120)《秸秆发电厂设计规范》(GB50762-2012);(121)《起重机械安全规程第1部分:总则》(GB6067.1-2010);(122)《防火封堵材料》(GB 23864-2009);(123)《袋式除尘器技术要求》(GB/T 6719-2009);(124)《电厂运行中矿物涡轮机油质量》(GB/T 7596-2017);1.2.6电力行业标准及规范(1)《火力发电厂职业安全设计规程》(DL5053-2012);(2)《火力发电厂职业卫生设计规程》(DL5454-2012);(3)《火力发电厂总图运输设计技术规程》(DL/T5032-2005);(4)《火力发电厂保温油漆设计规程》(DL/T5072-2007);(5)《电力建设安全工作规程第一部分:火力发电》(DL5009.1-2014);(6)《火力发电厂除灰设计规程》(DL/T5142-2012);(7)《电力行业锅炉压力容器监督规程》(DL/T612-2017);(8)《电站锅炉压力容器检验规程》(DL647-2004);(9)《火力发电厂高温紧固件技术导则》(DL/T439-2006);(10)《电站汽轮机技术条件》(DL/T892-2004);(11)《火力发电厂汽轮机防进水和冷蒸汽导则》(DL/T834-2003);(12)《电厂用磷酸酯抗燃油运行与维护导则》(DL/T571-2007);(13)《火力发电厂汽轮机电液控制系统技术条件》(DL/T996-2006);(14)《火力发电厂金属技术监督规程》(DL/T438-2009);(15)《电力建设施工技术规范第2部分:锅炉机组》(16)《电力建设施工及验收技术规范汽轮机机组篇》(DL5190.3-2012);(17)《电力建设施工及验收技术规范(管道篇)》(DL5190.5-2012);(18)《火力发电厂汽水管道与支架维修调整导则》(DL/T616-2006);(19)《火力发电厂管道支吊架验收规程》(DL/T1113-2009);(20)《火力发电厂高温高压蒸汽管道蠕变监督规程》(DL/T441-2004);(21)《火电厂除氧器运行性能试验规程》(DL/T1141-2009);(22)《电力设备预防性试验规程》(DL/T596-1996);(23)《电力变压器运行规程》(DL/T572-2010);(24)《高压配电装置设计技术规程》(DL/T5352-2006);(25)《电缆防火措施设计和施工验收标准》(DLGJ154-2000);(26)《火力发电厂厂用电设计技术规程》(DL/T5153-2014);(27)《火力发电厂和变电站照明设计技术规定》(DL/T5390-2014);(28)《电力系统安全稳定导则》(DL775-2001);(29)《电力工程直流系统设计技术规程》(DL/T5044-2014);(30)《电力系统用蓄电池直流电源装置运行与维护技术规程》(31)《电力系统继电保护柜、屏通用技术条件》(DL/T720-2000);(32)《交流电气装置的过电压保护和绝缘配合》(DL/T620-1997);(33)《火力发电厂热工控制系统设计技术规定》(DL/T5175-2003) ;(34)《火力发电厂厂级监控信息系统技术条件》(DL/T924-2016);(35)《火力发电厂辅助系统(车间)热工自动化设计技术规定》(DL/T5227-2005);(36)《发电厂热工仪表及控制系统技术监督导则》(DL/T1056-2007);(37)《火力发电厂热工自动化试验室设计标准》(DL/T5004-2004);(38)《火力发电厂汽轮机控制系统验收测试规程》(DL/T656-2006);(39)《火力发电厂模拟量控制系统验收测试规程》(DL/T657-2006);(40)《火力发电厂热工自动化就地设备安装、管路及电缆设计技术规定》(DL/T5182-2004);(41)《火力发电厂热工自动化系统检修运行维护规程》(DL/T774-2015);(42)《火力发电厂热工保护系统设计规定》(DL/T 5428-2009);(43)《火力发电厂分散控制系统验收测试规程》(DL/T659-2006);(44)《火力发电厂开关量控制系统验收测试规程》(DL/T658-2006);(45)《电力建设施工及验收技术规范第5部分热工自动化》(DL/T5190.5-2004);(46)《发电厂化学设计规范》(DL5068-2014);(47)《电力建设施工及验收技术规范第4部分:电厂化学》(DL/T5190.4-2004);(48)《火力发电厂水工设计规范》(DL/T5339-2006);(49)《化学监督导则》(DL/T246-2015);(50)《发电厂供暖通风与空气调节设计规范》(DL/T5035-2016);(51)《火力发电厂辅助机器基础隔振设计规程》(DL/T5188-2004);(52)《电厂标识系统设计导则》(DL/T950-2005);(53)《火力发电企业生产安全设施配置》(DL/T1123-2009);(54)《火力发电厂油气管道设计规程》(DL/T5204-2005);(55)《电站锅炉风机选型和使用导则》(DL/T468-2004);(56)《等离子体点火系统设计与运行导则》(DL/T1127-2010);(57)《电力安全工作规程》(发电厂与变电站电气部分GB 26806-2011);(58)《火力发电厂和变电所照明设计技术规定》(DL5390-2014);(59)《电力设备典型消防规程》(DL5027-2015);(60)《继电保护和安全自动装置运行管理规程》(DL/T587-2016);(61)《火力发电厂中温中压管道(件)安全技术导则》(DL/T785-2001);(62)《火力发电厂汽水管道与支吊架维修调整导则》(DL/T616-2006);(63)《火力发电厂建筑设计规程》(DL/T5094-2012);(64)《火力发电厂汽水管道设计规范》(DL/T5054-2016);(65)《火力发电厂土建结构设计技术规定》(DL5022-2012);(66)《继电保护和电网安全自动装置检验规程》(DL/T995-2016);(67)《接地装置特性参数测量导则》(DL/T475-2017);(68)《火力发电厂焊接技术规程》(DL/T869-2012);(69)《火电厂汽水化学导则第4部分:锅炉给水处理》(DL/T 805.4-2016);(70)《火力发电厂生活、消防给水和排水设计技术规定(附条文说明)》(DLGJ24-1991);(71)《发电厂汽轮机、水轮机技术监督导则》(DL/T1055-2007);(72)《发电机励磁系统技术监督规程》(DL/T1049-2007);(73)《电力工程地基处理技术规程》(DL/T 5024-2005);(74)《电力系统数字微波通信工程设计技术规程》(DL/T 5025-2005);(75)《电力工程地下金属构筑物防腐技术导则》(DL/T 5394-2007);(76)《火力发电厂锅炉炉膛安全监控系统技术规程》(DL/T 1091-2008);(77)《火力发电厂辅助系统(车间)热工自动化设计技术规定》(DL/T 5227-2005);(78)《火力发电厂分散控制系统技术条件》(DL/T 1083-2008);(79)《火力发电厂、变电所二次接线设计技术规程》(DL/T5136-2012);(80)《火电厂和核电厂常规岛主厂房荷载设计技术规程》(DL/T5095-2013);(81)《电站锅炉安全阀应用导则》(DL/T959-2014);1.2.8其他行业技术标准、规范(1)《安全评价通则》(AQ8001-2007);(2)《安全预评价导则》(AQ8002-2007);(3)《危险场所电气防爆安全规范》(AQ3009-2007);(4)《压力管道安全技术监察规程—工业管道》(TSG D0001-2009);(5)《压力管道定期检验规则-公用管道》(TSG D7004-2010);(6)《压力管道定期检验规则-工业管道》(TSG D7005-2018);(7)《起重机械定期检验规则》(TSG Q7015-2016);(8)《场(厂)内专用机动车辆安全技术监察规程》(TSG N0001-2017);(9)《气瓶安全技术监察规程》(TSG R0006-2014);(10)《爆破片装置安全技术监察规程》(TSG ZF003-2011);(11)《安全阀安全技术监察规程》(TSG ZF001-2006);(12)《起重机械安全技术监察规程―桥式起重机》(TSG Q0002-2008);(13)《特种设备使用管理规则》(TSG 08-2017);(14)《固定式压力容器安全技术监察规程》(TSG 21-2016);(15)《特种设备事故报告和调查处理导则》(TSG 03-2015);(16)《特种设备安全技术规范制定导则》(TSG 01-2014);(17)《锅炉安全技术监察规程》(TSG G0001-2012);(18)《锅炉监督检验规则》(TSG G7001-2015);(19)《锅炉定期检验规则》(TSG G7002-2015);(20)《发电企业安全生产标准化规范及达标评报标准》;(21)《袋式除尘器安装技术要求与验收规范》(JB/T8471-2010);。
宣布失效的安全生产文件目录(2012年)

安监总安健〔2012〕137号
序号
文件标题
发文字号
55
国家安全监管总局办公厅关于印发建设项目职业病危害预评价报告审核(备案)申请书等文书的通知
安监总厅安健〔2012〕69号
56
国家安全监管总局办公厅关于加强职业卫生技术服务机构资质管理的通知
安监总厅安健〔2012〕86号
57
国家安全监管总局办公厅关于深化石英砂加工等四项职业病危害专项治理的通知
安监总厅管四函〔2012〕69号
52
国家安全监管总局办公厅关于印发安全隐患排查治理信息系统建设和重点示范样板地区联网共享工程实施工作 方案的通知
安监总厅管四函〔2012〕198号
53
国家安全监管总局关于贯彻落实《职业病防治法》认真做好职业卫生监管工作的通知
安监总安健〔2012〕10号
54
国家安全监管总局关于印发职业卫生技术服务甲级机构跨省(自治区、直辖市)服务备案管理办法的通知
安监总统计〔2012〕98号
16
国家安全监管总局 国家煤矿安监局关于切实加强矿山提升运输安全管理工作的通知
安监总管一〔2012〕37号
17
国家安全监管总局关于印发金属非金属矿山建设项目安全专篇编写提纲等文书格式的通知
安监总管一〔2012〕45号
18
关于印发全国尾矿库专项整治行动2011年工作总结和2012年重点工作安排的通知
安监总厅规划〔2012〕141号
13
国家安全监管总局办公厅关于开展安全生产统计工作异地督查的通知
安监总厅统计函〔2012〕116号
14
国家安全监管总局办公厅关于工矿商贸企业职业卫生统计试点工作情况的通报
安监总厅统计函〔2012〕212号
危险化学品企业事故隐患排查治理实施导则(安监总管三[2012]103号资料
![危险化学品企业事故隐患排查治理实施导则(安监总管三[2012]103号资料](https://img.taocdn.com/s3/m/e7bcc4cf19e8b8f67c1cb95a.png)
危险化学品企业事故隐患排查治理实施导则国家安全生产监督管理总局2012年7月目录1 总则2 基本要求3 隐患排查方式及频次3.1 隐患排查方式3.2 隐患排查频次确定4 隐患排查内容4.1 安全基础管理4.2 区域位置和总图布置4.3 工艺管理4.4 设备管理4.5 电气系统4.6 仪表系统4.7 危险化学品管理4.8 储运系统4.9 消防系统4.10 公用工程系统5 隐患治理与上报5.1 隐患级别5.2 隐患治理5.3 隐患上报附录A重大事故隐患风险评估方法附件各专业隐患排查表1安全基础管理隐患排查表2 区域位置及总图布置隐患排查表3 工艺隐患排查表4 设备隐患排查表5 电气系统隐患排查表6 仪表隐患排查表7 危险化学品管理隐患排查表8 储运系统隐患排查表9 公用工程隐患排查表10 消防系统隐患排查表1 总则1.1 为了切实落实企业安全生产主体责任,促进危险化学品企业建立事故隐患排查治理的长效机制,及时排查、消除事故隐患,有效防范和减少事故,根据国家相关法律、法规、规章及标准,制定本实施导则。
1.2 本导则适用于生产、使用和储存危险化学品企业(以下简称企业)的事故隐患排查治理工作。
1.3 本导则所称事故隐患(以下简称隐患),是指不符合安全生产法律、法规、规章、标准、规程和安全生产管理制度的规定,或者因其他因素在生产经营活动中存在可能导致事故发生或导致事故后果扩大的物的危险状态、人的不安全行为和管理上的缺陷,包括:(1)作业场所、设备设施、人的行为及安全管理等方面存在的不符合国家安全生产法律法规、标准规范和相关规章制度规定的情况。
(2)法律法规、标准规范及相关制度未作明确规定,但企业危害识别过程中识别出作业场所、设备设施、人的行为及安全管理等方面存在的缺陷。
2 基本要求2.1 隐患排查治理是企业安全管理的基础工作,是企业安全生产标准化风险管理要素的重点内容,应按照“谁主管、谁负责”和“全员、全过程、全方位、全天候”的原则,明确职责,建立健全企业隐患排查治理制度和保证制度有效执行的管理体系,努力做到及时发现、及时消除各类安全生产隐患,保证企业安全生产。
安监总管三〔 〕 号《危险化学品从业单位安全生产标准化评审标准》

2.主要负责人组织和参与安全生产标准化建设的记录;
3.安全文化建设计划或方案。
1.安全生产标准化实施方案内容,一项不符合扣2分;
2.无主要负责人组织或参与安全生产标准化记录,扣3分;
3.未制定安全文化建设计划或方案,扣2分。
二级企业应初步形成安全文化体系。
查文件:
安全文化体系有关文件。
4.安全生产目标责任书的考核与奖惩记录。
询问:
1.主要负责人及各级组织负责人是否了解各自安全生产目标;
2.抽查从业人员是否了解本组织的安全生产目标。
未签订各级组织的安全目标责任书,扣20分(B级要素否决项)。
1.每缺一个组织的安全生产目标责任书,扣2分;
2.安全生产目标责任书内容与本组织的安全生产职责不符,扣1分;
询问:
主要负责人及有关人员对安全文化内容掌握情况。
二级企业
未初步形成安全文化体系,扣100分(A级要素否决项)。
一级企业有效运行安全文化体系。
查文件:
安全文化体系有关文件;
询问:
主要负责人及有关人员对安全文化内容掌握情况。
现场检查:
现场检查安全文化运行效果。
一级企业未有效运行安全文化体系,扣100分(A级要素否决项)。
建立从安全生产委员会到管理部门、车间、基层班组的安全生产管理网络,各级机构要配备负责安全生产的人员。
3.未按规定进行领导带班制度执行情况考核,扣2分;
4.主要负责人不清楚领导干部带班情况,扣2分。
职责
(30分)
1.企业应制定安委会和管理部门的安全职责。
制定安委会和各管理部门及基层单位的安全职责。
查文件:
安全生产责任制文件及内容。
安监总厅管三〔2012〕43号国...

安监总厅管三〔2012〕43号国...国家安全监管总局办公厅关于印发危险化学品安全生产许可文书的通知安监总厅管三〔2012〕43号各省、自治区、直辖市及新疆生产建设兵团安全生产监督管理局,有关中央企业:根据《危险化学品生产企业安全生产许可证实施办法》(国家安全监管总局令第41号)的有关规定,我局编制了《危险化学品生产企业安全生产许可证申请书》、《危险化学品生产企业安全生产许可证审查书》、《危险化学品生产企业安全生产许可证延期申请书》、《危险化学品生产企业安全生产许可证变更申请书》、《危险化学品生产企业安全生产许可证申请材料补正告知书》、《危险化学品生产企业安全生产许可证申请受理通知书》、《危险化学品生产企业安全生产许可证现场核查通知书》、《危险化学品生产企业安全生产许可证申请不予受理通知书》、《危险化学品生产企业安全生产许可证征求意见书》、《危险化学品生产企业安全生产许可证不予颁发通知书》等10种文书的格式和内容要求,自2012年4月10日起使用。
现将上述文书式样及有关文书说明印发给你们(电子文本可从国家安全监管总局政府网站下载),请自行印制,并通知辖区内危险化学品生产企业。
国家安全生产监督管理总局办公厅二〇一二年四月五日《危险化学品生产企业安全生产许可证申请书》《危险化学品生产企业安全生产许可证审查书》《危险化学品生产企业安全生产许可证延期申请书》《危险化学品生产企业安全生产许可证变更申请书》《危险化学品生产企业安全生产许可证申请材料补正告知书》《危险化学品生产企业安全生产许可证申请受理通知书》《危险化学品生产企业安全生产许可证现场核查通知书》《危险化学品生产企业安全生产许可证申请不予受理通知书》《危险化学品生产企业安全生产许可证征求意见书》《危险化学品生产企业安全生产许可证不予颁发通知书》申请编号:受理编号:申请日期:受理日期:危险化学品生产企业安全生产许可证申请书申请单位经办人联系电话填写日期国家安全生产监督管理总局制样填写说明一、本申请书封面“申请编号”、“申请日期”、“受理编号”、“受理日期”由安全生产许可证颁发管理机关经办人填写,本申请书的其他内容由申请安全生产许可证的单位填写。
特种作业人员、三同时、设备管理制度

建设项目“三同时”管理制度1目的为了规范,保证新建装置投产符合国家规定,创造较好的作业环境和劳动条件,保护职工的生命安全和健康,特制定此制度。
2范围适用于七台河北方水泥有限公司范围内,所有新建、改建、扩建项目。
3编制依据依据《安全生产法》、国家安全生产监督管理总局第23号令、《国家安全监督总局关于进一步做好冶金有色建材机械轻工纺织烟草商贸等行业建设项目“三同时”工作的通知》(安监总管四(2009)159)《建设项目安全设施“三同时”监督管理暂行办法》(国家安监局2011第36号,制定本制度。
4职责由安全管理部门联系各相关部门具体实施。
5具体内容5.1、“三同时”内容5.1.1 一切新建、改建、扩建工程和采取技术措施增加生产能力的挖潜、革新、改造项目,都必须严格执行“三同时”,即:主体工程与安全设施同时设计,同时施工,同时投入生产使用。
5.1.2 在编制计划任务书时,必须同时提出劳动保护要求,其内容包括劳动保护设施、安全消防设施、收尘设施和“三废”处理等措施等。
5.1.3安全设施投资应当纳入建设项目概算5.1.4本规定所称的建设项目安全设施,是指在生产经营活动中用于预防生产安全事故的设备、设施、装置、构(建)筑物和其他技术措施的总称。
5.1.5 公司新上项目,都必须执行“三同时”规定。
5.2根据国家规定,下列建设项目在进行可行性研究时,公司应当分别对其安全生产条件进行论证和安全预评价:5.2.1非煤矿矿山建设项目;5.2.2生产、储存危险化学品(包括使用长输管道输送危险化学品,下同)的建设项目;5.2.3生产、储存烟花爆竹的建设项目;5.2.4化工、冶金、有色、建材、机械、轻工、纺织、烟草、商贸、军工、公路、水运、轨道交通、电力等行业的国家和省级重点建设项目;5.2.5法律、行政法规和国务院规定的其他建设项目5.3生产经营单位对本规定15.5.2规定的建设项目进行安全条件论证时,应当编制安全条件论证报告。
- 1、下载文档前请自行甄别文档内容的完整性,平台不提供额外的编辑、内容补充、找答案等附加服务。
- 2、"仅部分预览"的文档,不可在线预览部分如存在完整性等问题,可反馈申请退款(可完整预览的文档不适用该条件!)。
- 3、如文档侵犯您的权益,请联系客服反馈,我们会尽快为您处理(人工客服工作时间:9:00-18:30)。
国家安全监管总局关于河北克尔化工有限
责任公司“2·28”重大爆炸事故情况的通报
安监总管三〔2012〕31号
各省、自治区、直辖市及新疆生产建设兵团安全生产监督管理局,有关中央企业:
2012年2月28日上午9时4分左右,位于河北省石家庄市赵县工业园区生物产业园内的河北克尔化工有限责任公司(以下简称河北克尔公司)生产硝酸胍的一车间发生重大爆炸事故,造成25人死亡、4人失踪、46人受伤。
这起事故是近一个时期以来危险化学品领域发生的伤亡最严重的事故。
依据有关规定,国务院安委会已对该起事故的查处实行挂牌督办,查处结果将及时向社会公布。
为深刻吸取事故教训,进一步加强危险化学品安全生产工作,有效防范和坚决遏制类似事故发生,现将有关情况通报如下:
一、事故企业基本情况
河北克尔公司系民营企业,成立于2005年2月。
该公司2009年3月开工建设的年产10000吨噁二嗪、1500吨2-氯-5-氯甲基吡啶、1500吨西林钠、1000吨N-氰基乙亚胺酸乙酯项目,总投资2.17亿元。
一期工程包括一车间(硝酸胍)、二车间(硝基胍)、配电室、动力站(包括空压站和1台制冷机组)、固体库、一次水池和循环消防水池,设计单位为河北渤海工程设计有限公司(乙级资质),于2010年2月底竣工。
河北克尔公司现有职工351人,2010年9月6日取得了危险化学品安全生产许可证。
二、事故简要经过
河北克尔公司一车间共有8个反应釜,依次为1-8号反应釜。
原设计用硝酸铵和尿素为原料,生产工艺是硝酸铵和尿素在反应釜内混合加热熔融,在常压、175-220℃条件下,经8-10小时的反应,间歇生产硝酸胍,原料熔解热由反应釜外夹套内的导热油提供。
实际生产过程中,将尿素改用双氰胺为原料并提高了反应温度,反应时间缩短至5-6小时。
事故发生前,一车间有5个反应釜投入生产。
2月28日上午8时,该车间当班人员接班时,2个反应釜空釜等待投料,3个反应釜投料生产。
8时40分左右,1号反应釜底部放料阀(用导热油伴热)处导热油泄漏着火;9时4分,
一车间发生爆炸事故并被夷为平地,造成重大人员伤亡,周边设备、管道严重损坏,厂区遭到严重破坏,周边2公里范围内部分居民房屋玻璃被震碎。
三、事故原因初步分析
硝酸铵、硝酸胍均属强氧化剂。
硝酸铵是国家安全监管总局公布的首批重点监管的危险化学品,遇火时能助长火势;与可燃物粉末混合,能发生激烈反应而爆炸;受强烈震动或急剧加热时,可发生爆炸。
硝酸胍受热、接触明火或受到摩擦、震动、撞击时,可发生爆炸;加热至150℃时,分解并爆炸。
经初步调查分析,事故直接原因是:河北克尔公司一车间的1号反应釜底部放料阀(用导热油伴热)处导热油泄漏着火,造成釜内反应产物硝酸胍和未反应完的硝酸铵局部受热,急剧分解发生爆炸,继而引发存放在周边的硝酸胍和硝酸铵爆炸。
事故的详细原因正在进一步调查。
根据目前事故初步调查的情况,该事故暴露出河北克尔公司存在以下突出问题:
一是装置本质安全水平低、工厂布局不合理。
装置自动化程度低,反应温度缺乏有效、快捷的控制手段;加料、出料、冷却等作业均需人工操作,现场操作人员多。
一车间与二车间厂房均采用框架砖混结构,同向相距约25米布置,且中间建有硫酸储罐。
一车间爆炸后波及到二车间,造成厂房损毁和重大人员伤亡。
二是企业安全管理不严格,变更管理处于失控状态。
河北克尔公司在没有进行安全风险评估的情况下,擅自改变生产原料、改造导热油系统,将导热油最高控制温度从210℃提高到255℃。
三是车间管理人员、操作人员专业素质低。
包括车间主任在内的绝大部分员工为初中文化水平,对化工生产的特点认识不足、理解不透,处理异常情况能力低,不能适应化工安全生产的需要。
四是厂区内边生产,边建设。
事故企业边生产,边施工建设,厂区作业单位多、人员多,加剧了事故的伤亡程度。
五是安全隐患排查治理不认真。
2011年6月,国家安全监管总局公布了首批重点监管的危险化学品名录,对重点监管危险化学品的安全措施和应急处置原则提出了明确要求,要求在隐患排查治理工作中将其作为重点进行排查,切实消除安全隐患。
但从此次事故的初步调查情况来看,该企业在隐患排查中没有发现
生产工艺所固有的安全隐患和变更生产原料、提高导热油最高控制温度等所带来的安全隐患。
四、认真吸取事故教训,切实加强危险化学品安全生产工作
(一)进一步加强对爆炸性危险化学品的安全监管。
地方各级安全监管部门要立即组织对本地区涉及爆炸性危险化学品的生产、储存装置开展专项安全检查,借助专家力量对有关企业的工厂布局、工艺技术路线及装备的安全可靠性、自动化控制水平、人员素质等安全生产条件,进行全面的检查和论证,及时发现各类隐患并限期整改,确保生产安全。
要严格涉及爆炸性危险化学品生产、储存企业的安全准入条件,把有关企业纳入重点监管范围。
要将受热、遇明火和受到摩擦、震动、撞击时可发生爆炸的危险化学品全部纳入重点监管的危险化学品范围,进一步强化各项安全措施,落实安全监管责任,杜绝事故的发生。
(二)切实加强涉及重点监管危险化学品、重点监管危险化工工艺和危险化学品重大危险源(以下统称“两重点一重大”)企业的安全监管。
地方各级安全监管部门要将涉及“两重点一重大”的企业作为重点监管对象,进一步强化监管措施。
要尽快全面完成化工企业危险工艺自动化控制系统改造;尽快启动涉及重点监管危险化学品的生产、储存装置和危险化学品重大危险源自动化监控系统改造完善工作,提高装置的自动化控制水平,增强装置的安全可靠性,减少现场操作人员,提高本质安全水平。
要督促危险化学品企业切实加强变更管理,严格执行变更审批制度,履行变更程序,进行风险辨识和控制,消除安全隐患,不断提高安全生产水平。
(三)进一步加强危险化学品建设项目安全设计管理,提高本质安全水平。
危险化学品建设项目必须由具备相应资质、相应能力的单位负责设计,工厂的布局要科学合理,选择成熟、可靠的生产工艺和设备,装备自动化控制系统;对涉及“两重点一重大”的装置,在设计阶段要按照《化工建设项目安全设计管理导则》(AQ/T3033-2010)的要求进行危险与可操作性分析(HAZOP),进一步消除设计缺陷,提高装置的本质安全水平。
地方各级安全监管部门要严把安全生产条件审查关,对建设项目的工艺设备安全可靠性、周边安全距离以及企业总体布局等安全设计内容进行全面、系统的论证和审查,从源头上消除安全隐患;进一步加强对安全评价机构的监督、检查与指导,确保建设项目各个环节的评价质量,对在评价过程中不负责任、弄虚作假的评价机构要严肃处理,直至取消评价资质。
有关企业要避免边生产、边施工建设,确实不能避免的,要采取有效的安全防范措施。
(四)进一步严格从业人员的准入条件,强化培训教育,提高从业人员素质。
危险化学品企业要严格操作人员的招录条件,适度提高操作人员的准入门槛,涉及“两重点一重大”的装置,应招录具有高中以上文化程度的操作人员、大专以上的专业管理人员,确保从业人员的基本素质;要持续不断地加强员工培训教育,使其真正掌握作业场所和工作岗位存在的危险因素及防范措施、应急预案和安全管理制度,切实增强安全操作技能。
(五)进一步抓实隐患排查治理工作。
地方各级安全监管部门要督促危险化学品企业认真落实《国务院安委会办公室关于认真贯彻落实中央领导同志重要批示精神进一步加强安全生产工作的通知》(安委办明电〔2012〕6号)等要求,深刻吸取事故教训,举一反三,防微杜渐,切实加强危险化学品安全管理,进一步加大安全隐患排查治理力度,持续深入做好隐患排查治理工作,并加强监督检查。
对因隐患排查治理工作不认真、走过场而发生事故的企业,要依法依规严肃追究企业主要负责人和有关人员的责任。
请各省级安全监管局于2012年5月1日前将对涉及爆炸性危险化学品生产、储存企业开展专项安全检查的情况上报国家安全监管总局。
国家安全生产监督管理总局
二○一二年三月十二日。