元器件引脚成形与切脚工艺、检验规程
元器件引脚的加工整形及安装的说明
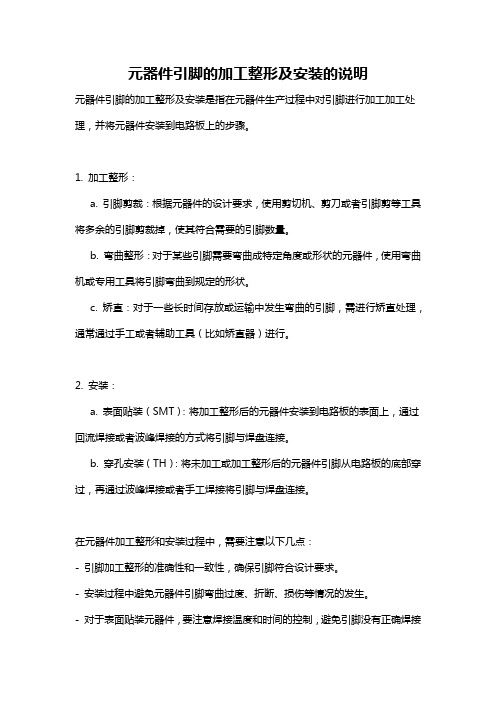
元器件引脚的加工整形及安装的说明
元器件引脚的加工整形及安装是指在元器件生产过程中对引脚进行加工加工处理,并将元器件安装到电路板上的步骤。
1. 加工整形:
a. 引脚剪裁:根据元器件的设计要求,使用剪切机、剪刀或者引脚剪等工具将多余的引脚剪裁掉,使其符合需要的引脚数量。
b. 弯曲整形:对于某些引脚需要弯曲成特定角度或形状的元器件,使用弯曲机或专用工具将引脚弯曲到规定的形状。
c. 矫直:对于一些长时间存放或运输中发生弯曲的引脚,需进行矫直处理,通常通过手工或者辅助工具(比如矫直器)进行。
2. 安装:
a. 表面贴装(SMT):将加工整形后的元器件安装到电路板的表面上,通过回流焊接或者波峰焊接的方式将引脚与焊盘连接。
b. 穿孔安装(TH):将未加工或加工整形后的元器件引脚从电路板的底部穿过,再通过波峰焊接或者手工焊接将引脚与焊盘连接。
在元器件加工整形和安装过程中,需要注意以下几点:
- 引脚加工整形的准确性和一致性,确保引脚符合设计要求。
- 安装过程中避免元器件引脚弯曲过度、折断、损伤等情况的发生。
- 对于表面贴装元器件,要注意焊接温度和时间的控制,避免引脚没有正确焊接
到焊盘上或者焊接过度,引起焊接质量问题。
- 安装前要仔细检查元器件引脚是否完好无损,并清理引脚上可能存在的氧化物、油污等物质,确保良好的焊接连接。
总之,元器件引脚的加工整形和安装是保证元器件在电路板上正确连接并能正常工作的重要环节,需要遵循技术规范和操作要求进行。
电子元器件贴片及接插件焊接检验标准

矩形元件 异形元件 元件引脚长度—双面有元件插件元件引脚弯度焊锡量—单面板焊锡量—双面板电路板对应丝印识别:电路板焊接一、焊接流程1、焊接开始前,整理好桌面及周边环境,为电路焊接工作准备一个有条理、整洁的环境。
2、仓库领料,并依据元件明细表核对物料,确保物料正确无误,遇到生疏元件及时向相关负责人询问。
3、依据元件明细表进行电路板焊接。
4、电路板焊接完成后,依据元件明细表核对元件,以保证无错焊、虚焊、漏焊、假焊、桥接。
特别是确认多引脚元件和有极性元件焊接正确。
同样重要的是检查和优化焊点,一块合格的电路板是焊点光滑、过渡均匀、无毛刺、元件排列整齐美观。
二、对焊接点的基本要求1、焊点要有足够的机械强度,保证被焊件在受振动或冲击时不致脱落、松动。
不能用过多焊料堆积,这样容易造成虚焊、焊点与焊点的短路。
2、焊接可靠,具有良好导电性,必须防止虚焊。
虚焊是指焊料与被焊件表面没有形成合金结构。
只是简单地依附在被焊金属表面上。
3、焊点表面要光滑、清洁, 焊点表面应有良好光泽,不应有毛刺、空隙,无污垢,尤其是焊剂的有害残留物质,要选择合适的焊料与焊剂。
三、焊接技术1、手工焊接的基本操作方法①焊前准备,准备好电烙铁以及镊子、剪刀、斜口钳、尖嘴钳、焊料、焊剂(我们这里是指焊锡丝,以下通指焊锡丝)等工具,将电烙铁及焊件搪锡,左手握焊料,右手握电烙铁,保持随时可焊状态。
②用烙铁加热备焊件。
③送入焊料,熔化适量焊料。
④移开焊料,当焊料流动覆盖焊接点,迅速移开电烙铁。
2、电子元器件焊接的顺序是由小到大,由低到高3、元器件焊接注意事项:1)批量将同侧的一端焊盘镀上适量焊锡(仅适用于贴装元器件)。
2)依据文件规定的元器件方向,正确焊接在镀锡焊盘上。
3)批量焊接元件另一端。
4)修复优化焊点,并做清理工作。
5)上述元器件,单个引脚焊接时间在保证焊接质量的前提下,一般1.5-4秒,以避免烫坏焊盘和元器件(对于比较大的元器件如:保险铜件、片形插头等焊接时间4-6秒)。
元器件引脚成形与切脚工艺、检验规程
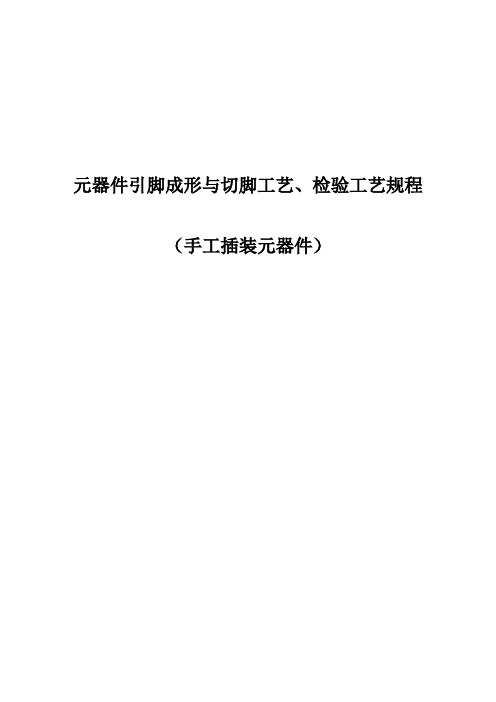
元器件引脚成形与切脚工艺、检验工艺规程(手工插装元器件)1.目的1.1.1.1.本规程规定了手工插装电子元器件引脚成形与切脚应满足的工艺要求,以及引脚成形与切脚过程的检验程序。
2.适用范围2.1.1.1.本规程适用于产品分立电子元器件插装前的引脚成形与切脚,规定了元器件引脚成形与切脚的技术要求和质量保证措施,同时也可作为设计、生产、检验的依据。
3.适用人员3.1.1.1.本规程适用于产品生产的工艺人员、电子装联操作人员、质量检验人员等。
4.参考文件4.1.1.1.IPC—A—610D 《电子组件的可接受性》。
4.1.1.2.IPC J-STD-001D 《焊接的电气和电子组件要求》.4.1.1.3.QJ 3171—2003 《航天电子电气产品元器件成形技术要求》。
4.1.1.4.QJ 165A—1995 《航天电子电气产品安装通用技术要求》.4.1.1.5.ANSI/ESD S20.20-2007 《静电放电控制方案》。
5.名词/术语5.1.1.1.功能孔:PCB上用于电气连接的孔。
5.1.1.2.非功能孔:PCB上用于机械安装或固定的孔。
5.1.1.3.支撑孔(Supported Hole):两层及多层PCB上的功能孔,孔壁上镀覆金属,俗称镀通孔。
5.1.1.4.非支撑孔(Unsupported Hole):单层或双层PCB上的功能孔,孔壁上不镀覆金属,俗称非镀通孔.5.1.1.5.淬火引脚(Tempered lead):元器件的引脚经过淬火处理。
6.工艺元器件成形与切脚是整个PCBA生产的首要工序,成形与切脚的质量直接影响后续的产品生产。
6.1.工艺流程6.1.1.成形与切脚的工艺流程图工艺要求工艺流程说明根据元器件的封装、包装形式、本体以及引脚直径、成形类型、成形间距、印制板厚度、切脚长度以及元器件数量等确定成形与切脚的工具或模具,制定元器件成形与切脚明细表;元器件成形与切脚操作人员应按照设计、工艺文件要求对元器件的名称、型号、规格进行确认;根据明细表中的元器件特性及参数,选择元器件成形与切脚的顺序;依据成形顺序使元器件成形与切脚的尺寸调整更加容易控制;根据元器件首件的成形与切脚试验流程操作;首件成形与切脚检验完成后,将不合格的试样单独存放或处理;成形过程中要不定时的对工具或工装成形面的光滑度进行检查,确保成形质量;当元器件数量超过100个时,操作人员必须对最后成形与切脚的10个元器件按照试验检验项进行检验(7.1.2节);成形与切脚后的一般性元器件密闭保存;静电敏感元器件使用防静电容器存放;湿敏元器件要干燥存储(详见元器件存储工艺规程);图6-1元器件成形与切脚工艺流程6.1.2.首件成形与切脚试验6.1.2.1.成形与切脚试验时,要根据成形与切脚明细表的参数要求调整好工具或工装,按图6-2所示流程进行。
元器件引脚成型工艺
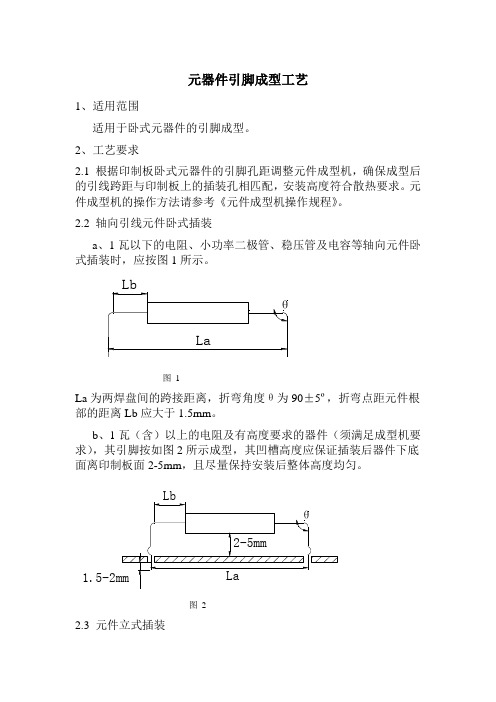
元器件引脚成型工艺1、适用范围适用于卧式元器件的引脚成型。
2、工艺要求2.1 根据印制板卧式元器件的引脚孔距调整元件成型机,确保成型后的引线跨距与印制板上的插装孔相匹配,安装高度符合散热要求。
元件成型机的操作方法请参考《元件成型机操作规程》。
2.2 轴向引线元件卧式插装a、1瓦以下的电阻、小功率二极管、稳压管及电容等轴向元件卧式插装时,应按图1所示。
图1La为两焊盘间的跨接距离,折弯角度θ为90±5º,折弯点距元件根部的距离Lb应大于1.5mm。
b、1瓦(含)以上的电阻及有高度要求的器件(须满足成型机要求),其引脚按如图2所示成型,其凹槽高度应保证插装后器件下底面离印制板面2-5mm,且尽量保持安装后整体高度均匀。
图22.3 元件立式插装轴向引线元件或径向引线元件立式插装时,按图3所示成型,R 应大于元件半径,r应大于引脚直径的2倍。
图3对于引脚跨距与电路板插装孔距匹配的径向引脚元件,不必成型,直接插装,如铝电解电容。
2.4元件引脚成型时,应保证插装到印制板后,其引脚端头露出板面长度为1.5-2mm。
2.5 印有型号、规格等字符的元件成型时应保证插装在印制板上后,标识明显可见,以便于检查或维修。
2.6 元件成型所造成的引脚裂纹和损伤,不得大于引脚直径的10%,不得暴露基底材料,否则作报废处理。
2.7 对于有焊点的引线,折弯处应距离焊点1.5mm以上。
2.8 集成块的成型,请参照《集成块引脚成型机操作规程J-06-005》。
3、质量标准3.1 元件成型后的跨距必须与印制板上的孔距相匹配。
3.2 折弯半径尽可能大,在折弯后不能损伤元件。
3.3 元件的两引脚折弯后应平行,并且保持折弯角度90±5℃。
3.4 元件两端折弯的部位距元件体中心的距离应相等。
3.5 将元件引脚压成“凹槽”时应保证元件插装后以规定距离平行于印制板。
3.6 成型后,保证元器件标识明显可见。
4、注意事项4.1 元件成型时须注意折弯尺寸。
元器件成型工艺规范
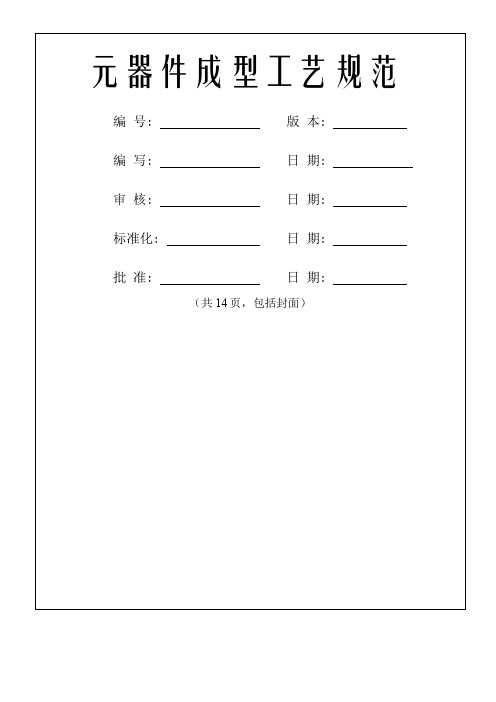
编 号:版 本:
编 写:日 期:
审 核:日 期:
标准化:日 期:
批 准:日 期:
(共14页,包括封面)
文 件 修 订 记 录
No.
修正后版本
修正人
修 正 内 容 概 要
修正日期
1.目的:
规范常用通孔插装元器件的成型工艺,加强元件前加工和成型的质量控制,避免和减少元件成型不良和报废,保障元器件的性能,提高产品可靠性。
4.6变向折弯:引线折弯后引线的伸展方向有发生改变,通常是90°
4.7无变向折弯:引线折弯后引线的伸展方向没有发生改变。非变向折弯通常用于消除装配应力或在装配中存在匹配问题时采用。如:打 Z 折弯和打 K 折弯。
打Z折弯 打K折弯
4.8抬高距离:安装于印制板上的元器件本体底部到板面的垂直距离。
4.9成形工具:包括尖嘴钳,斜口钳,自制或采购的成形工装等用于元器件成形的所有工具。
3.3 工程部经理负责本规范有效执行。
4.名词解释:
4.1元器件引线(Component/Device Lead):从元器件延伸出的用于机械和/或电气连接的单根或绞合金属线,或成型导线。
4.2元器件引脚(Component/Device Pin):不损坏就难以成形的元器件引线。
4.3通孔安装:利用元器件引线穿过支撑基板上孔与导体图形作电气连接和机械固定。
2.适用范围:
本规范仅适用于所有产品的生产操作、品质检验及控制、SOP文件制作依据,规范要求及所引用的规范文件如果与客户要求冲实,按照客户的要求执行。
3. 职责与权限:
3.1工程部IE工程师和IE技术员负责按本规范制定SOP,指导生产加工;
3.2 品质部IPQC负责按本规范对SOP及生产操作进行查检。
电子元器件生产检验操作规程
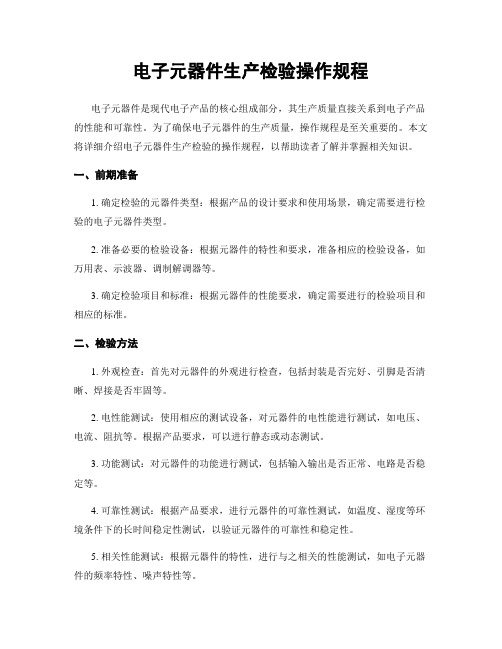
电子元器件生产检验操作规程电子元器件是现代电子产品的核心组成部分,其生产质量直接关系到电子产品的性能和可靠性。
为了确保电子元器件的生产质量,操作规程是至关重要的。
本文将详细介绍电子元器件生产检验的操作规程,以帮助读者了解并掌握相关知识。
一、前期准备1. 确定检验的元器件类型:根据产品的设计要求和使用场景,确定需要进行检验的电子元器件类型。
2. 准备必要的检验设备:根据元器件的特性和要求,准备相应的检验设备,如万用表、示波器、调制解调器等。
3. 确定检验项目和标准:根据元器件的性能要求,确定需要进行的检验项目和相应的标准。
二、检验方法1. 外观检查:首先对元器件的外观进行检查,包括封装是否完好、引脚是否清晰、焊接是否牢固等。
2. 电性能测试:使用相应的测试设备,对元器件的电性能进行测试,如电压、电流、阻抗等。
根据产品要求,可以进行静态或动态测试。
3. 功能测试:对元器件的功能进行测试,包括输入输出是否正常、电路是否稳定等。
4. 可靠性测试:根据产品要求,进行元器件的可靠性测试,如温度、湿度等环境条件下的长时间稳定性测试,以验证元器件的可靠性和稳定性。
5. 相关性能测试:根据元器件的特性,进行与之相关的性能测试,如电子元器件的频率特性、噪声特性等。
三、检验记录与报告1. 积极记录检验过程:对每一个检验项目,记录检验的时间、检验者、检验设备等信息,以确保检验的可追溯性。
2. 记录检验结果:对每一个检验项目的测试结果,记录在相关的检验表中,包括具体数值、合格与否等。
3. 编写检验报告:根据检验结果,编写详细的检验报告,包括样品信息、检验项目和结果、异常情况的分析等。
四、异常处理1. 异常情况的判定:当某个元器件在检验过程中出现异常情况时,需及时判定异常原因,如是否为元器件本身质量问题,还是操作不当导致的。
2. 异常分析与处理:对于出现的异常情况,及时进行分析和处理,找出根本原因,以预防类似问题的再次发生。
元器件成形及标准
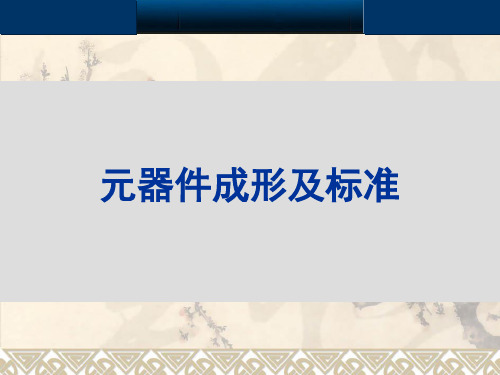
创 新 永 无 止 境
1.严格按照《作业指导书》作业,调整操 作设备. 2.操作时应注意自身及他人的人身安全。 3.元件成形时一定要注意成形的形状和尺 寸,以免造成物料浪费。 4.定时自检,并实装PCB检验,以免批量 浪费。 5.操作时必须戴好静电手环。
成形的注意事项
创 新 永 无 止 境
谢谢
特加工 物料 切脚刀
轨道架 控制面板
成品盒
全自动成形机
成形的治工具、设备
创 新 永 无 止 境
二)机器成形设备
手柄
紧固螺 丝
上成型 模 下成型 模
上成型 模紧固 螺丝 下 成 型 模 紧 固 螺丝
手动啤压机
成形的治工具、设备
创 新 永 无 止 境
三、元器件成形的形状及标准
元器件成形的形状及标准
创 新 永 无 止 境
一)元器件成形的形状 1、U型
2、F型
元器件成形的形状及标准
创 新 永 无 止 境
3、直角型
4、异型
元器件成形的形状及标准
创 新 永 无 止 境
二)元器件成形的标准 1、一般标准 使元件插入PCB板后,漏出PCB的脚长 在1.2~2mm之间。
元件插入PCB板后, 漏出PCB的脚长在 1.2~2mm之间。
加工剪短 元件脚加工成要求的脚长 元件脚来料时过长
成形工艺简介
创 新 永 无 止 境
2.加工成特定形状 因插件的要求,元件有时需要加工成特定的形状 例如:
加工成各种特定形状 元件来料时形状
成形工艺简介
创 新 永 无 止 境
二)成形方式 1.手工成形 指利用剪钳、尖嘴钳等工具以及各种成形治具将元 件进行元件脚剪短及元件成形。手式成形可以加工特殊 元件或加工特殊形状。 2.机器成形 指利用机器设备将元件进行元件脚剪短及元件成形。 机器成形具有快速、准确的特点。
零件加工检验标准
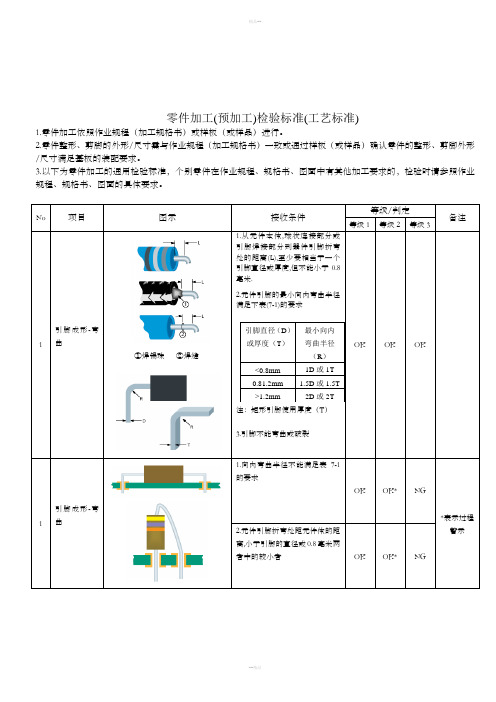
零件加工(预加工)检验标准(工艺标准)1.零件加工依照作业规程(加工规格书)或样板(或样品)进行。
2.零件整形、剪脚的外形/尺寸需与作业规程(加工规格书)一致或通过样板(或样品)确认零件的整形、剪脚外形/尺寸满足基板的装配要求。
3.以下为零件加工的通用检验标准,个别零件在作业规程、规格书、图面中有其他加工要求的,检验时请参照作业规程、规格书、图面的具体要求。
No 项目图示接收条件等级/判定备注等级1等级2等级31引脚成形-弯曲①焊锡珠②焊缝1.从元件本体,球状连接部分或引脚焊接部分到器件引脚折弯处的距离(L),至少要相当于一个引脚直径或厚度,但不能小于0.8毫米.2.元件引脚的最小向内弯曲半径满足下表(7-1)的要求注:矩形引脚使用厚度(T)3.引脚不能弯曲或破裂引脚直径(D)或厚度(T)最小向内弯曲半径(R)<0.8mm 1D或1T0.81.2mm 1.5D或1.5T>1.2mm 2D或2TOK OK OK1引脚成形-弯曲1.向内弯曲半径不能满足表7-1的要求OK OK*NG*表示过程警示2.元件引脚折弯处距元件体的距离,小于引脚的直径或0.8毫米两者中的较小者OK OK*NGNo项目图示接收条件等级/判定备注等级1等级2等级31引脚成形-弯曲1.元器件的本体、球状连接部分或引脚焊接部分有裂缝NG NG NG2引脚成形-压力释放1.成形引脚提供压力释放2.元件体外面的元件引脚与主体轴大约平行3.元件引脚进入通孔约与板面垂直4.由于压力释放弯曲的类型导致元件中心偏移OK OK OK2引脚成形-压力释放1.引脚弯曲离主体密封处小于一个引脚直径OK OK*NG*表示过程警示2引脚成形-压力释放1.元件体到引脚密封处的损伤或破裂2.无压力释放NG NG NG3引脚成形-引脚损伤1.元件引脚上的缺口或变形没有超过引脚直径的宽度或厚度的10%OK OK OK裂缝No项目图示接收条件等级/判定备注等级1等级2等级33引脚成形-引脚损伤1.引脚损伤超过引脚直径的10%2.引脚由于多次成形或粗心操作造成的引脚形变3.引脚上留有夹具造成的夹痕NG NG NG4零件加工-元件损伤绝缘层破损玻璃本体破裂引脚受到外力拉拽/拉出1.元件本体破损,破裂2.引脚受到外力拉拽/拉出NG NG NG5加工尺寸-脚距1.脚距L=D±0.5mm, D为过孔距离2.可插付于PCB,可插到位,元件不可有浮件OK OK OK6加工尺寸-脚长1.脚长(短脚作业,波峰后不裁脚)2.脚长(长脚作业,波峰后裁脚)No项目图示接收条件等级/判定备注等级1等级2等级37零件加工-散热IC整形1.引脚形状/尺寸符合规格书要求或符合装配要求2.引脚无变形3.加工过程中引脚无受到机械外力导致引脚被拉出4.IC本体无破损*如有其他要求依照作业规程/加工规格书7零件加工-散热IC组装1.垫圈、绝缘套、绝缘垫片等不可漏装,不可有破损2.散热剂不可漏点,用量符合要求3.螺丝需锁付到位*如有其他要求依照作业规程/加工规格书8零件加工-绝缘套管9零件加工-导线-绝缘套管1.修剪后的绝缘层切口整洁,没有任何刺穿,拉伸,磨损,污染,烧焦的痕迹Good Good Good9零件加工-导线-绝缘套管1.由于机械剥离使绝缘层上出现轻微的均匀的压痕2.用于去除实心线绝缘层的化学熔剂,膏状或霜剂,未能引起导线性能的下降3.由于加热,绝缘层上出现轻微的变色,只要无烧焦,裂口或裂缝OK OK OK9零件加工-导线-绝缘套管1.绝缘层上的任何切割,断裂,裂纹,裂口2.绝缘皮熔化到绕线线股中绝缘层的厚度减少超过20%3.不均匀或粗糙的绝缘片(磨损,拖尾或碎片)大于绝缘层外直径的50%或1毫米,其中更大者4.绝缘层烧焦NG NG NGNo项目图示接收条件等级/判定备注等级1等级2等级39零件加工-导线-绝缘套管(接上页)OK OK OK10零件加工-导线-损伤1.绕线没有擦伤,缺口,切割,打倒,刮伤或其它的损伤Good Good Good10零件加工-导线-损伤1.股线被切割,折断,擦伤或更严重,但如果损伤或折断的股线没有超过表10-1的限制OK OK*OK**表示过程警示10零件加工-导线-损伤1.线股损伤的数量(刮伤,缺口或更严重)超过了表10-1所规定的限度OK OK OK10零件加工-导线-损伤表10-1股线数量最大允许股线刮伤,缺口或更严重级别1 ,2在安装前没有镀层的绕线的最大允许股线刮伤,缺口或更严重级别3在安装前有镀层的绕线的最大允许股线刮伤,缺口或更严重级别3少于7 0 0 07-15 1 0 116-25 3 0 226-40 4 3 341-60 5 4 461-120 6 5 5121或更多6% 5% 5%备注1: 用于6KV或更大电压的绕线不能有线股损伤备注2: 对于有镀层的绕线,没有暴露基层金属的可以看见的现象不能当作线股损伤No项目图示接收条件等级/判定备注等级1等级2等级311零件加工-导线-损伤1.股线没有不平整,搓紧的股线松开,有扣,打结或其它的变形Good Good Good11零件加工-导线-损伤1.在绝缘皮被去掉的地方股线是平直的.它们己被恢复到原来螺旋形的绕线放置2.绕线股扭绞OK OK OK11零件加工-导线-损伤无1.没有保持总的股线螺旋形放置OK NG NG12零件加工-导线-股线分离1.股线原来的放置位置未被扰乱Good Good Good12零件加工-导线-股线分离1.股线分离(鸟笼状),但没有超过2.一股线直径3.没有延伸超过绕线绝缘层外面的直径OK OK OK4.绕线股己分离超过了一根股线的直径,但没有延伸超过股线绝缘层外面的直径OK OK*NG*表示过程警示条件12零件加工-导线-股线分离1.绕线股延伸超过了绕线绝缘层外面的直径OK NG NG13引线引脚预镀锡1.在股线上均匀地涂上一层薄薄的焊锡,且单个股线清晰可见2.从绝缘端开始,不涂锡的股线长度不能大于一个导线的直径(D)Good Good GoodNo项目图示接收条件等级/判定备注等级1等级2等级313引线引脚预镀锡无1.焊锡浸润到导线的镀锡部分且渗透到股线的内股中2.倘若焊锡没有扩充到仍需保留能变形的导线部分3.镀锡留下光滑的焊锡涂层且股线轮廓清晰可见OK OK OK13引线引脚预镀锡4.股线不可瓣,不过过多的焊锡并不影响成形,安装或功能5.焊锡并没有渗透到导线的内股OK OK*OK*13引线引脚预镀锡1.针孔,空缺,无润湿超过需要镀锡区域的5%2.从绝缘端开始的非镀锡长度大于一个导线的直径OK OK*NG13引线引脚预镀锡3.焊锡未浸润到导线的镀锡部分4.在附件到终端或形成接合之前(而不是啮合)股线没被镀锡OK NG NG13引线引脚预镀锡1.焊接后,焊锡扩充流入导线内需要保留易弯曲变形的部分2.焊锡在镀锡导线区域内形成冰柱状,影响了后来的装配NG NG NG。
(新人培训)电子元器件插件工艺检验标准
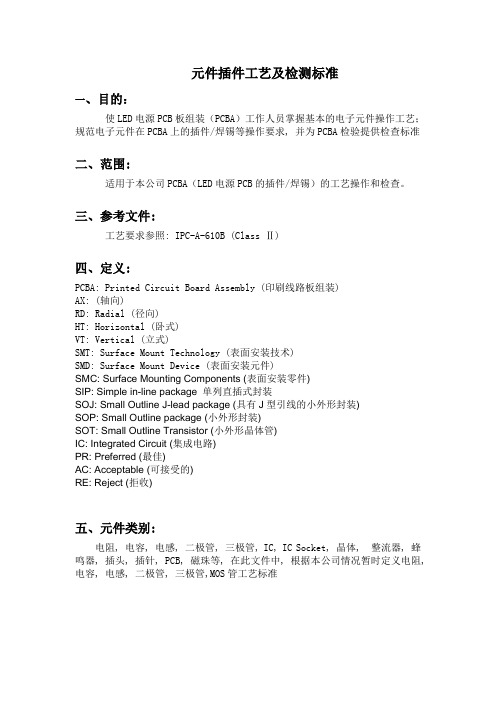
元件插件工艺及检测标准一、目的:使LED电源PCB板组装(PCBA)工作人员掌握基本的电子元件操作工艺;规范电子元件在PCBA上的插件/焊锡等操作要求, 并为PCBA检验提供检查标准二、范围:适用于本公司PCBA(LED电源PCB的插件/焊锡)的工艺操作和检查。
三、参考文件:工艺要求参照: IPC-A-610B (Class Ⅱ)四、定义:PCBA: Printed Circuit Board Assembly (印刷线路板组装)AX: (轴向)RD: Radial (径向) HT: Horizontal (卧式)VT: Vertical (立式) SMT: Surface Mount Technology (表面安装技术)SMD: Surface Mount Device (表面安装元件)SMC: Surface Mounting Components (表面安装零件)SIP: Simple in-line package 单列直插式封装SOJ: Small Outline J-lead package (具有J型引线的小外形封装)SOP: Small Outline package (小外形封装)SOT: Small Outline Transistor (小外形晶体管)IC: Integrated Circuit (集成电路)PR: Preferred (最佳)AC: Acceptable (可接受的)RE: Reject (拒收)五、元件类别:电阻, 电容, 电感, 二极管, 三极管, IC, IC Socket, 晶体, 整流器, 蜂鸣器, 插头, 插针, PCB, 磁珠等, 在此文件中, 根据本公司情况暂时定义电阻,电容, 电感, 二极管, 三极管,MOS管工艺标准六、元件插件工艺及检测标准1. 卧式(HT) 插元件卧式插元件主要是小功率, 低容量, 低电压的电阻, 电容, 电感, Jumper(跳线), 二极管, IC等, PCBA上的组装工艺要求和接收标准如下:1.1元件在基板上的高度和斜度1.1.1轴向(AX)元件1.1.1.1功率小于1W的电阻, 电容(低电压, 小容量的陶瓷材料), 电感, 二极管, IC等元件PR: 元件体平行于PCB板面且紧贴PCB板面, 如图示:AC: 元件体与PCB表面之间最大倾斜距离(D)不大于3mm, 元件体与PCB 表面最低距离(d)不大于0.7mm, 如图示:RE: 元件体与PCB板面距离D>3mm, 或d>0.7mm1.1.1.2耗散功率大于或等于1W的元件PR: 元件体平行于PCB板面且与PCB板面之间的距离D≥1.5mm, 如图示:AC: 元件体与PCB板面之间的距离D≥1.5mm, 元件体与PCB板面的平行不作要求RE: 元件体与PCB板面之间的距离D≤1.5mm1.1.1.3 ICPR: 元件体平行于PCB, IC引脚全部插入焊盘中, 引脚突出PCB面1.mm, 倾斜度=0, 如图示:AC: IC引脚全部插入焊盘中, 引脚突出PCB面大于0.5mm, 如图:RE: IC引脚突出PCB面小于0.5mm, 或看不见元件引脚, 如图:1.1.2径向(RD)元件(电容, 晶振)PR: 元件体平贴于PCB板面, 如图示:AC: 元件脚最少有一边贴紧PCB板面, 如图示:RE: 元件体未接触PCB板面, 如图示:1.2元件的方向性与基板对应符号的关系:1.2.1 轴向(AX) 无极性元件(电阻, 电感, 小陶瓷电容等)PR: 元件插在基板中心标记且元件标记清晰可见, 元件标记方向一致(从左到右, 从上到下), 如图:AC: 元件标记要求清晰, 但方向可不一致, 如图:RE: 元件标记不清楚或插错孔位, 如图:1.2.2 轴向(AX) 有极性元件, 如二几管, 电解电容等PR: 元件的引脚插在对应的极性脚位, 元件标记清晰可看见, 如图:AC: 元件的引脚必须插在相应的极性脚位上, 元件标记可看见, 如图:RE: 元件的引脚未按照极性方向插在相应的脚位上, 如图:1.3元件引脚成形与曲脚1.3.1引脚成形PR: 元件体或引脚保护层到弯曲处之间的距离L>0.8mm, 或元件脚直径弯曲处无损伤, 如图:AC: 元件脚弯曲半径( R )符合以下要求:元件脚直径或厚度( D/T ) 半径( R )≤0.8mm 1 X D0.8~1.2mm 1.5 X D≥1.2mm 2 X DRE: ( 1 ) 元件体与引脚保护弯曲处之间L<0.8mm, 且弯曲处有损伤, 如图:( 2 ) 或元件脚弯曲内径R小于元件直径, 如图:1.3.2屈脚PR: 元件屈脚平行于相连接的导体, 如图:AC: 屈脚与相间的裸露导体之间距离(H) 大于两条非共通导体间的最小电气间距, 如图:RE: 屈脚与相间的裸露导体之间距离(H) 大于两条非共通导体间的最小电气间距, 如图:1.4元件损伤程度1.4.1元件引脚的损伤PR: 元件引脚无任何损伤, 弯脚处光滑完好, 元件表面标记清晰可见, 如图:AC: 元件引脚不规则弯曲或引脚露铜,但元件或部品引脚损伤程度小于该引脚直径的10%,如图:RE: ( 1 )元件引脚受损大于元件引脚直径的10%,如图:( 2 )严重凹痕锯齿痕,导致元件脚缩小超过元件的10%,如图:1.4.2 IC元件的损伤PR: IC 元件无任何损伤, 如图:AC: 元件表面受损, 但未露密封的玻璃, 如图:RE: 元件表面受损并露出密封的玻璃, 如图:1.4.3轴向(AX)元件损伤PR: 元件表面无任何损伤,如图:AC: 元件表面无明显损伤,元件金属成份无暴露,如图:RE:( 1 )元件面有明显损伤且绝缘封装破裂露出金属成份或元件严重变形,如图:( 2 ) 对于玻璃封装元件,不允许出现小块玻璃脱落或损伤.1.5元件体斜度PR: 元件体与其在基板上两插孔位组成的连线或元件体在基板上的边框线完全平行,无斜度,如图:AC: 元件体与其在基板上两插孔位组成的连线或元件体在基板上的边框线斜度≤1.0mm,如图:RE: 元件体与其在基板上两插孔位组成的连线或元件体在基上的边框线斜度>1.0mm,如图:2. 立式(VT) 插元件2.1.1 轴向(AX) 元件PR: 元件体与PCB板面之间的高度H在0.4mm-1.5mm之间, 且元件体垂直于PCB板面, 如图:AC: H在0.4-3mm之间, 倾斜Q<15°,如图:RE: 元件体与PCB板面倾斜, 且间距H<0.4mm或H>3mm或Q>15°.2.1.2径向(RD)元件2.1.2.1引脚无封装元件PR: 元件体引脚面平行于PCB板面, 元件引脚垂直于PCB板面, 且元件体与PCB板面间距离为0.25-2.0mm, 如图:AC: 元件体与PCB板面斜倾度Q小于15°, 元件体与PCB板面之间的间隙H在0.20-2.0mm之间, 三极管离板面高度最高大于4.0mm, 如图: RE: 元件与PCB板面斜倾角Q>15°或元件体与PCB板面的间隙H>2.0mm或三极管>4.0mm.2.1.2.2:引脚有封装元件PR: 元件垂直PCB板面, 能明显看到封装与元件面焊点间有距离, 如图: AC: 元件质量小于10g且引脚封装刚好触及焊孔且在焊孔中不受力, 而焊点面的引脚焊锡良好(单面板), 且该元件在电路中的受电压<240VAC或DC, 如图:RE: 引脚封装完全插入焊孔中, 且焊点面焊锡不好, 可看见引脚封装料, 如图:2.2元件的方向性与基板符号的对应关系2.2.1轴向(AX)元件PR: 元件引脚插入基板时,引脚极性与基板符号极性完全吻合一致,且正极一般在元件插入基板时的上部,负极在下部,如图:AC: 元件引脚插入基板时,引脚极性与基板符号极性吻合一致,但元件在插入基板时,正极在上和负极在下不作要求,如图:RE: 元件引脚插入基板时,引脚极性与基板符号极性刚好相反,如图:2.2.2径向(RD)元件AC: 元件引脚极性与基板符号极性一致,如图:RE: 元件体引脚极性与基板符号极性相反,如图:2.3元件引脚的紧张度PR: 元件引脚与元件体主轴之间夹角为0°(即引脚与元件主轴平行, 垂直于PCB板面), 如图:AC: 元件引脚与元件体主轴袒闪角Q<15°,如图:RE: 元件引脚与元件体主轴之间夹角Q>15°.2.4元件引脚的电气保护在PCBA板上有些元件要有特殊的电气保护,则通常使用胶套,管或热缩管来保护电路PR: 元件引脚弯曲部分有保护套,垂直或水平部分如跨过导体需有保护套且保护套距离插孔之间距离A为1.0mm-2.0mm,如图:AC: 保护套可起到防止短路作用, 引脚上无保护套时, 引脚所跨过的导体之间的距离B≥0.5mm, 如图:RE: 保护套损坏或A>2.0mm时, 不能起到防止短路作用或引脚上无保护套时, 或引脚所跨过的导体之间距离B<0.5mm,如图:2.5元件间的距离PR: 在PCBA板上,两个或以上踝露金属元件间的距离要D≥2.0mm,如图:AC: 在PCBA板上, 两个或以上踝露金属元件的距离最小D≥1.6mm, 如图:RE: 在PCBA板上, 两个或以上踝露金属元件间的距离D<1.6mm, 如图:2.6元件的损伤PR: 元件表面无任何损伤,且标记清晰可见,如图:AC: 元件表面有轻微的抓、擦、刮伤等,但未露出元件基本面或有效面,如图:RE: 元件面受损并露出元件基本面或有效面积,如图:3. 插式元件焊锡点工艺及检查标准3.1单面板焊锡点单面板焊锡点对于插式元件有两种情形:a. 元件插入基板后需曲脚的焊锡点b. 元件插入基板后无需曲脚(直脚) 的焊锡点3.1.1标准焊锡点之外观特点A. 焊锡与铜片, 焊接面, 元件引脚完全融洽在一起, 且可明显看见元件脚B. 锡点表面光滑, 细腻, 发亮C. 焊锡将整个铜片焊接面完全覆盖, 焊锡与基板面角度Q<90°, 标准焊锡点如图示:3.1.2可接受标准A. 多锡焊接时由于焊锡量使用太多,使零件脚及铜片焊接面均被焊锡覆盖着,使整个锡点象球型,元件脚不能看到.AC: 焊锡点虽然肥大Q>90°,但焊锡与元件脚,铜片焊接面焊接良好,焊锡与元件脚,铜片焊接面完全融洽在一起,如图:RE: 焊锡与元件引脚, 铜片焊接状况差, 焊锡与元件脚/铜片焊接面不能完全融洽在一起, 且中间有极小的间隙, 元件引脚不能看到, 且Q>90°, 如图:B. 上锡不足(少锡)焊锡、元件引脚、铜片焊接面在上锡过程中,由于焊锡量太少,或焊锡温度及其它方面原因等造成的少锡.AC: 整个焊锡点, 焊锡覆盖铜片焊接面≥75%, 元件脚四周完全上锡,且上锡良好, 如图:RE: 整个焊锡点, 焊锡不能完全覆盖铜片焊接面<75%, 元件四周亦不能完全上锡, 锡与元件脚接面有极小的间隙, 如图:C. 锡尖AC: 焊锡点锡尖, 只要该锡尖的高度或长度h<1.0mm, 而焊锡本身与元件脚、铜片焊接面焊接良好, 如图:RE: 焊锡点锡尖高度或长度h≥1.0mm, 且焊锡与元件脚、铜片焊接面焊接不好, 如图:D. 气孔AC: 焊锡与元件脚、铜片焊接面焊接良好, 锡点面仅有一个气孔且气孔要小于该元件脚的一半, 或孔深<0.2mm, 且不是通孔, 只是焊锡点面上有气孔, 该气孔没有通到焊接面上, 如图:RE: 焊锡点有两个或以上气孔, 或气孔是通孔, 或气孔大于该元件脚半径, 如图:D. 起铜皮AC: 焊锡与元件脚、铜片焊接面焊接良好, 但铜皮有翻起h<0.1mm,且铜皮翻起小于整个Pad位的30%, 如图:RE: 焊锡与元件脚、铜片焊接面焊接一般, 但铜皮翻起h>0.1mm, 且翻起面占整个Pad位的的30%以上, 如图:E. 焊锡点高度对焊锡点元件脚在基板上的高度要求以保证焊接点有足够的机械强度AC: 元件脚在基板上高度0.5<h≤2.0mm, 焊锡与元件脚, 铜片焊接面焊接良好, 元件脚在焊点中可明显看见, 如图:RE: 元件脚在基板上的高度h<0.5mm或h>2.0mm, 造成整个锡点为少锡, 不露元件脚, 多锡或大锡点等不良现象, 如图:注:对用于固定零件之插脚如变压器或接线端子之插脚高度可接受2.5mm为限.3.1.3不可接受的缺陷焊锡点在基板焊锡点中有些不良锡点绝对不可接收, 现列举部分如下RE: ( 1 ) 冷焊(假焊/虚焊)如图:( 2 ) 焊桥(短路),锡桥,连焊,如图:( 3 ) 溅锡, 如图:( 4 ) 锡球, 锡渣, 脚碎, 如图:( 5 ) 豆腐渣, 焊锡点粗糙, 如图:( 6 ) 多层锡, 如图:( 7 )开孔(针孔),如图:3.2双面板焊锡点双面板焊锡点同单面板焊锡点相比有许多的不同点:a. 双面板之PAD位面积较小(即外露铜片焊接面积)b. 双面板每一个焊点PAD位都是镀铜通孔鉴于此两点, 双面板焊锡点在插元件焊接过程及维修过程就会有更高要求, 其焊锡点工艺检查标准就更高, 下面将分别详细讨论双面板之焊锡点收货标准3.2.1标准焊锡点之外观特点A. 焊锡与元件脚, 通孔铜片焊接面完全融洽在一起, 且焊点面元件脚明显可见.B. 元件面和焊点面的焊锡点表面光滑, 细腻, 发亮.C. 焊锡将两面的Pad位及通孔内面100%覆盖, 且锡点与板面角度Q<90°, 如图:3.2.2可接收标准A.多锡焊接时由于焊锡量过多, 使元件脚, 通孔, 铜片焊接面完全覆盖,不是使焊接时的两面元件脚焊点肥大, 焊锡过高AC: 焊锡点元件面引脚焊锡虽然过多, 但焊锡与元件脚, 通孔铜片焊接面两面均焊接良好, 且Q<90°, 如图:RE: 焊锡点元件面引脚肥大, 锡点面引脚锡点肥大, 不能看见元件脚且焊锡与元件脚, 铜片焊接面焊接不良, 如图:B. 上锡不良AC: 焊锡与元件脚, 通孔铜片焊接面焊接良好, 且焊接锡在通孔铜片内的上锡量高度h>75%·T (T: 基板厚度), 从焊点面看上锡程度大于覆盖元件脚四周(360°)铜片的270°, 或从元件面能清楚的看到通孔铜片中的焊锡, 如图:RE: 从焊点面看, 不能清晰的看到元件引脚和通孔铜片焊接面中的焊锡或在通孔铜片焊接面完全无焊锡或元件引脚到Pad位无焊锡或h<75%·T或上锡角度Q<270°(针对Solder Pad 360°而言), 如左图:C. 锡尖在焊接过程中由于焊锡温度过低或焊接时间过长等原因造成的锡尖AC: 焊锡点的锡尖高度或长度h<1.0mm, 而焊锡本身与元件引脚及通孔铜片焊接面焊接良好, Q<90°, 如图:RE: 焊锡点锡尖高度或长度h≥1.0mm, 且焊锡与元件引脚, 通孔铜片焊接面焊接不良, 如图:D. 气孔AC: 焊锡与元件脚, 铜片焊接面焊接良好, 锡点面仅有一个气孔且气孔要小于该元件脚的1/2, 且不是通孔(只是焊锡点表面有气孔, 未通到焊接面上), 如图:RE: 焊锡点上有两个或以上气孔, 或气孔是通孔, 或气孔大于该元件脚直径的1/2, 焊点面亦粗糙, 如图:E. 起铜皮AC: 焊锡点与元件脚, 通孔铜片焊接面焊接良好, 但铜皮翘起高度h<0.1mm, 翘起面积S<30%·F (F为整个焊盘的面积)RE: 焊锡与元件脚, 通孔铜片焊接面焊接质量一般, 但铜皮翘起h>0.1mm, 且翘起面积S>30%·F (F为整个焊盘的面积), 如图:F. 焊接点高度PR: 元件脚在焊锡点中明显可见, 引脚露出高度h=0.1mm, 且焊锡与元件脚, 通孔铜片焊接面焊接良好, 如图:AC: 元件脚露出基板的高度0.5mm<h≤2.0mm, 元件脚在焊锡点中可明显看见, 且焊锡与元件脚, 通孔铜片焊接面焊接良好. (但对于通孔铜片焊接面的双面PCB板, 基板厚度T>2.3mm, 则元件脚露出基板高度可接收0<h≤0.5mm), 如图:RE: 元件脚露出基板高度h<0.5mm或h>2.0mm (仅对于厚度T≤2.3mm 的双面板), 造成整个锡点为少锡, 不露元件脚, 多锡或大锡点等不良现象, 且焊接不良, 如图:3.2.3 不可接收的缺陷焊锡点:在双面板(镀铜通孔铜片焊接面)焊锡点中, 有些不良焊点绝对不可接收, 其不可接收程度完全同于单面板, 详细请参考3.1.3。
元器件引脚的加工整形及安装的说明
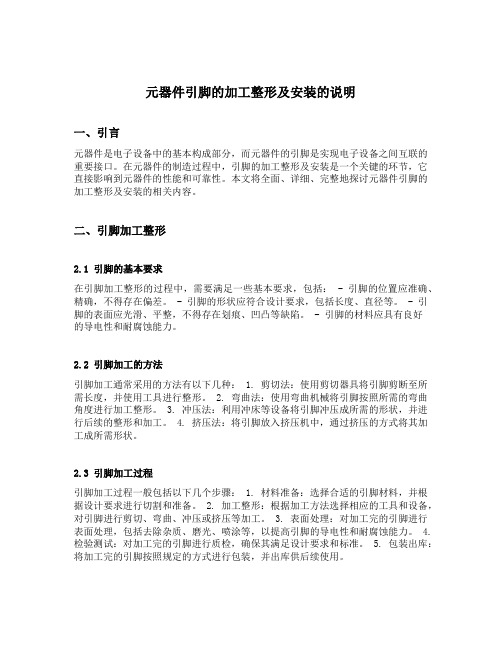
元器件引脚的加工整形及安装的说明一、引言元器件是电子设备中的基本构成部分,而元器件的引脚是实现电子设备之间互联的重要接口。
在元器件的制造过程中,引脚的加工整形及安装是一个关键的环节,它直接影响到元器件的性能和可靠性。
本文将全面、详细、完整地探讨元器件引脚的加工整形及安装的相关内容。
二、引脚加工整形2.1 引脚的基本要求在引脚加工整形的过程中,需要满足一些基本要求,包括: - 引脚的位置应准确、精确,不得存在偏差。
- 引脚的形状应符合设计要求,包括长度、直径等。
- 引脚的表面应光滑、平整,不得存在划痕、凹凸等缺陷。
- 引脚的材料应具有良好的导电性和耐腐蚀能力。
2.2 引脚加工的方法引脚加工通常采用的方法有以下几种: 1. 剪切法:使用剪切器具将引脚剪断至所需长度,并使用工具进行整形。
2. 弯曲法:使用弯曲机械将引脚按照所需的弯曲角度进行加工整形。
3. 冲压法:利用冲床等设备将引脚冲压成所需的形状,并进行后续的整形和加工。
4. 挤压法:将引脚放入挤压机中,通过挤压的方式将其加工成所需形状。
2.3 引脚加工过程引脚加工过程一般包括以下几个步骤: 1. 材料准备:选择合适的引脚材料,并根据设计要求进行切割和准备。
2. 加工整形:根据加工方法选择相应的工具和设备,对引脚进行剪切、弯曲、冲压或挤压等加工。
3. 表面处理:对加工完的引脚进行表面处理,包括去除杂质、磨光、喷涂等,以提高引脚的导电性和耐腐蚀能力。
4. 检验测试:对加工完的引脚进行质检,确保其满足设计要求和标准。
5. 包装出库:将加工完的引脚按照规定的方式进行包装,并出库供后续使用。
三、引脚安装3.1 引脚安装的目的引脚安装是将元器件固定在电路板或其他基板上的过程,其目的包括: - 保持元器件的稳定性和可靠性,防止在使用过程中引脚脱落或断裂。
- 实现元器件与基板之间的良好电气连接和传导。
- 便于元器件的维修和更换,减少维修成本和时间。
元器件引脚成形IPC标准
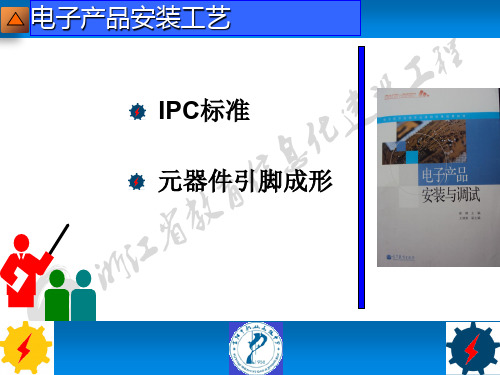
图(3)
图(3):引脚 由于多次或粗心 弯曲产生变形
形
安装在镀通孔中的元件,从器件的本体、球状连接部分 或引脚焊接部分到器件引脚折弯处的距离,至少相当于
一个引脚的直径或厚度或0.8毫米中的较大者。
电子产品安装工艺
成形形状
电
子
安
装
矩形脚采用厚度T
工
艺
最小内弯半径
---
引 引脚的直径(D)或厚度(T)
脚
成
小于0.8毫米
形
0.8毫米~1.2毫米
大于1.2毫米
电子产品安装工艺 IPC标准 元器件引脚成形
电子产品安装工艺
IPC-610C 工艺标准
美国IPC成立于1957年,曾先后取名为:
印制电路协会
The Institute of Printed Circuits
电子电路互连与封装协会
The Institute of Interconnecting and Packaging Electronic Circuits
电子制造业协会
Association Connecting Electronics Industries
IPC标准为国际通用标准,为电子行业广泛采用。
电子产品安装工艺
IPC标准电子产品分级
1级-----通用类电子产品
那些对外观要求不高而以其使用功能要求为主的产品,主要 为民用产品(电视机,电冰箱等)。
---
电子产品安装工艺
成形工具 电 子 安 装 工 艺
引 脚 成 形
元器件引线可用 专用模具、专用工具 和手工弯折。手工弯 折方法如图(a)所示。 用带园弧的长尖嘴钳 或捏子靠近元件的根 部,按弯折方向转动 引线即可。电子产品安装工艺源自成形位置电 子 安 装 工 艺
电子元器件质量检验标准

电子元器件质量检验标准1. 引言电子元器件是现代科技和信息产业的基础,对于确保电子产品的性能和可靠性起着至关重要的作用。
为了提高电子元器件的质量和可靠性,制定一套严格的检验标准是必不可少的。
本文旨在介绍电子元器件质量检验的标准、规范和规程,并讨论它们对于电子元器件质量控制的重要性。
2. 外观检验外观检验是评估电子元器件质量的首要步骤之一。
它包括检查元器件的尺寸、表面质量、焊盘和引脚等。
标准规范要求元器件无裂纹、无气泡、无划痕,并且焊盘和引脚要整齐、无偏折、无损伤。
3. 封装和包装检验封装和包装是保护电子元器件不受机械应力、湿度和温度等环境因素影响的重要手段。
标准规范要求封装和包装要与元器件匹配,并具备一定的防尘、防水和防静电能力。
4. 电性能检验电性能检验是评估电子元器件质量的关键环节,它涉及到元器件的电压、电流、电阻、电感、电容等参数的测量。
标准规范要求元器件的电性能要符合设定的规范范围,且测试结果要与元器件规格书中给出的数值相符。
5. 可靠性检验可靠性是衡量电子元器件质量的重要指标之一。
可靠性检验主要包括温度试验、湿度试验、振动试验、冷热冲击试验等。
这些试验模拟了元器件在不同环境条件下的工作性能,以此来评估其在实际应用中的可靠性。
6. 材料分析和成分检验材料分析和成分检验是对电子元器件质量进行深入研究和评估的一种手段。
通过对元器件的材料成分、结构和组织进行分析,可以判断元器件的纯度、韧性、导电性和耐腐蚀性等特性是否满足要求。
7. 可焊性检验可焊性检验是评估电子元器件封装材料和引脚焊接性能的重要手段。
标准规范要求元器件的引脚表面涂层要具备良好的可焊性,且焊盘和引脚之间要有适当的间隙和粘附力,以确保焊接质量和连接性能。
8. 特殊检验要求某些特殊类型的电子元器件需要额外的检验标准和规范。
例如,在医疗器械领域使用的电子元器件需要符合特定的医疗标准,而航空航天领域使用的电子元器件需要具备抗辐射和抗振能力。
元器件引脚成形
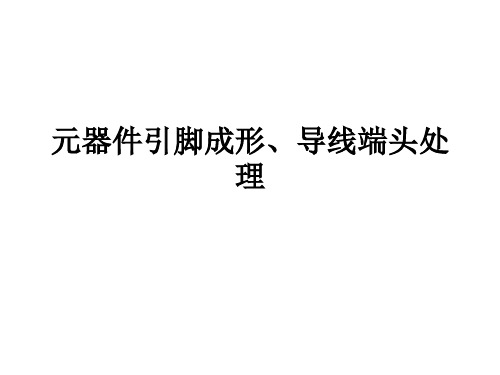
一、 引脚成形方法和技术要求
• 1.手工整形 手工整形工具主要有镊子和尖嘴钳,
基本步骤及如图所示。
基本步骤 将引脚用镊子铆直
用尖嘴钳夹住引脚根部,逐个将引脚弯曲
根据整形的整体效果对折弯方向不一致的引 脚进行修整
图示
3.引脚成形的技术要求
(1) 引脚成形后,元器件本身不能受伤,不 可以出现模印、压痕和裂纹。 (2) 引脚成形后,引脚直径的减小或变形 不可以超过原来的10% 。 (3) 若引脚上有焊点,则在焊点和元器件 之间不准有弯曲点,焊点到弯曲点之间应 保持2 mm 以上的间距。 (4) 通常各种元器件的引脚尺寸都有不同 的基本要求。
引脚和印制板上的焊盘。
件温度过高
2.标记朝向 引脚成形、安装以后,元器件的标记朝向如图 所示。
标
记
侧前方
朝上
朝
向
标识朝前便于观察图 解ຫໍສະໝຸດ 第一色环位置第一环
符合习惯 (由左到右) (由近到远)
5K1
103
3.引脚弯折处理 当安装、焊接固定元件时,为防止元件掉出来应折
弯引脚,并且要注意整形效果。具体操作如图3 所示。
• 4.安装时注意事宜 在安装时,不要用手直接触碰元器件
分开地线(屏蔽层)与芯线
绞合地线与芯线
对地线与芯线搪锡
热熔后加绝缘导管
元器件成形、导线处理注意事项
• 1.安装方式 电子元器件成形的安装方式图示及说明如图所示。
安装方式
图示
说明
贴板安装
引脚容易处理,插装简单,但不利于散热
悬空安装
2~6 cm
引脚长,有利于散热,但插装较复杂
整形难度高,对散热更加有利,并保证焊接时不会使元 倒装
项目一-任务十一-元器件引脚加工
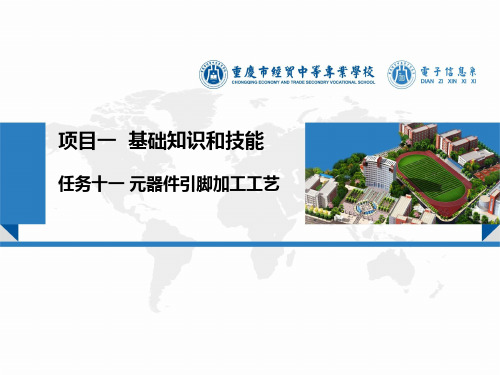
二、元器件引脚的成形方法
2.引脚成形要求 (1)成形尺寸准确,形状符合要求; (2)元器件引脚弯曲处,离元器件根部距离要大 于1.5mm; (3)弯曲半径要大于2倍的引脚直径,且要保证 两端引脚平行; (4)轴向引脚元器件成形时要尽量保证两端弯曲 的距离相等; (5)成形时不能损伤元器件,刮伤引脚镀层; (6)成形后不允许有机械损伤。
达标元件
一、装配前元器件的检验
2.仪表检查。 用万表等仪表测量各个元器件的好坏。
万用表
二、元器件引脚的成形方法
1.手工成型和模具成型。 (2)手工成型方法: 原始元件→引脚拉直→去氧化→搪锡→测焊孔距→成 型。
二、元器件引脚的成形方法
手工成型和模具成型。 (2)模具成型方法: 原始元件→引脚拉直→去氧化→搪锡→测元件及焊孔 距离→放入模具→成型。如下图所示:
二、元器件引脚的成形方法
3.元器件引线的成形 (1)预加工处理 元器件引线在成形前必须进行加工处理。这是由于元 器件引线的可焊性虽然在制造时就有这方面的技术要求, 但因生产工艺的限制,加上包装、贮存和运输等中间环节 时间较长,在引线表面产生氧化膜,使引线的可焊性严重 下降。引线的再处理主要包括引线的校直,表面清洁及上 锡三个步骤,要求引线处理后,不允许有伤痕,镀锡层均 匀,表面光滑,无毛刺和残留物。
二、元器件引脚的成形方法
3.元器件引线的成形 (2)引线成形的基本要求 引线成形工艺就是根据焊点之间的距离,做成需要的 形状。目的是使它能迅速而准确地插入孔内,基本要求如 下: ①元件引线开始弯曲处,离元件端面的最小距离应不 小于2mm。 ②弯曲半径不应小于引线直径的两倍。 ③怕热元件要求引线增长,成形时应绕环。 ④元件标称值应处于在便于查看的位置。 ⑤成形后不允许有机械损伤。
引脚切筋成型工艺流程
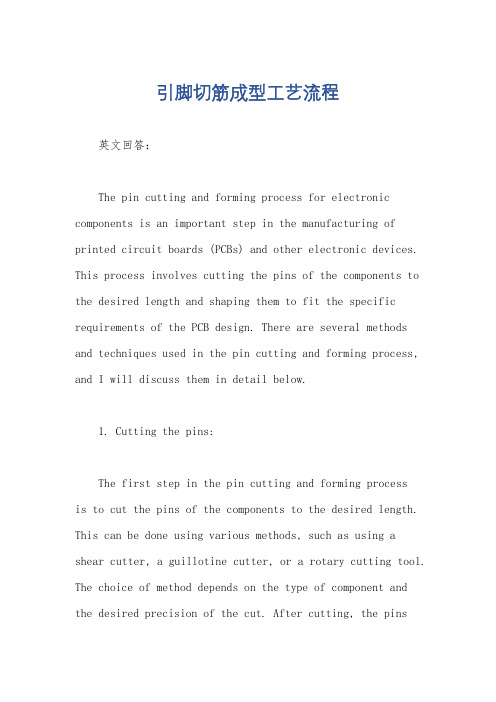
引脚切筋成型工艺流程英文回答:The pin cutting and forming process for electronic components is an important step in the manufacturing of printed circuit boards (PCBs) and other electronic devices. This process involves cutting the pins of the components to the desired length and shaping them to fit the specific requirements of the PCB design. There are several methods and techniques used in the pin cutting and forming process, and I will discuss them in detail below.1. Cutting the pins:The first step in the pin cutting and forming processis to cut the pins of the components to the desired length. This can be done using various methods, such as using a shear cutter, a guillotine cutter, or a rotary cutting tool. The choice of method depends on the type of component and the desired precision of the cut. After cutting, the pinsare typically left with sharp edges, which need to befurther processed in the forming step.2. Forming the pins:Once the pins are cut to the desired length, they needto be shaped to fit the specific requirements of the PCB design. This can be done using different forming techniques, such as bending, crimping, or stamping. The choice of technique depends on the shape and size of the pins, aswell as the mechanical and electrical properties requiredfor the connection.Bending: This technique involves bending the pins at specific angles to fit the layout of the PCB. It can bedone manually using pliers or automated using specialized bending machines. The angle and radius of the bend are critical parameters that need to be controlled to ensure proper alignment and electrical connection.Crimping: Crimping is a technique used to create a secure connection between the pin and the PCB. It involvescompressing the pin onto the PCB pad using a crimping tool or machine. This creates a reliable mechanical andelectrical connection, especially for components withlarger pins.Stamping: Stamping is a technique used to shape the pins into specific forms, such as hooks or loops, to provide additional mechanical stability or electrical contact. This is often done using a stamping machine that applies pressure to the pins, shaping them into the desired form.After the pins are cut and formed, they are ready to be inserted into the PCB and soldered in place. The pincutting and forming process is crucial in ensuring the proper functioning and reliability of the electronic components and the overall electronic device.中文回答:电子元件的引脚切割和成型工艺是印刷电路板(PCB)和其他电子设备制造过程中的重要步骤。
集成电路元器件管脚成形方法及工艺分析
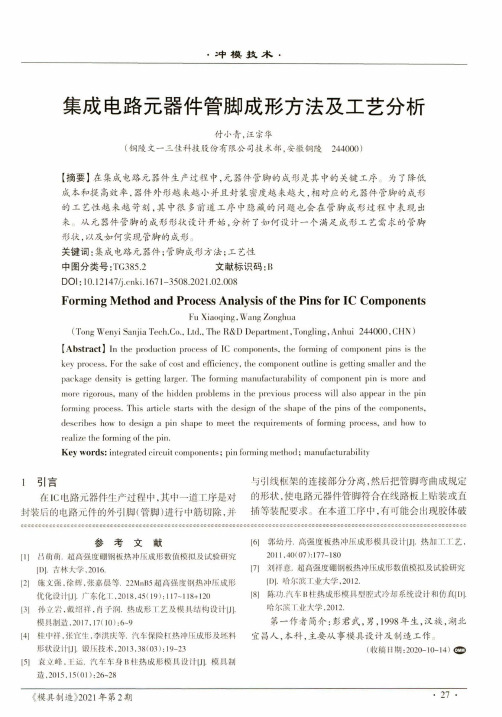
集成电路元器件管脚成形方法及工艺分析付小青,汪宗华(铜陵文一三佳科技股份有限公司技术部,安徽铜陵244000)【摘要】在集成电路元器件生产过程中,元器件管脚的成形是其中的关键工序为了降低成本和提高效率,器件外形越来越小并且封装密度越来越大,相对应的元器件管脚的成形的工艺性越来越苛刻,其中很多前道工序中隐藏的问题也会在管脚成形过程中表现出来从元器件管脚的成形形状设计开始,分析了如何设计一个满足成形工艺需求的管脚形状,以及如何实现管脚的成形关键词:集成电路元器件;管脚成形方法;工艺性中图分类号:TG385.2 文献标识码:BDOI:10.12147/ki.1671 -3508.2021.02.008Forming Method and Process Analysis of the Pins for IC ComponentsFu Xiaoqing,Wang Zonghua(Tong Wenyi Sanjia Tech.Co.,Ltd.,The R&D Department,Tongling,Anhui244000,CH N)【Abstract】In the production process of IC components,the forming of component pins is thekey process.For the sake of cost and efficiency,the component outline is getting smaller and thepackage density is getting larger.The forming manufac*tural)ility of component pin is more andmore rigorous,many of the hidden problems in the previous process will also appear in the pinforming process.This article starts with the design of the shape of the pins of the components,describes how to design a pin shape to meet the requirements of forming process,and how torealize the forming of the pin.Key words:integrated circuit components;pin forming method;manufacturabilityi引言 与引线框架的连接部分分离,然后把管脚弯曲成规定在丨c电路元器件生产过程中,其中一道工序是对的形状,使电路元器件管脚符合在线路板上贴装或直封装后的电路元件的外引脚(管脚)进行中筋切除,并插等装配要求。
- 1、下载文档前请自行甄别文档内容的完整性,平台不提供额外的编辑、内容补充、找答案等附加服务。
- 2、"仅部分预览"的文档,不可在线预览部分如存在完整性等问题,可反馈申请退款(可完整预览的文档不适用该条件!)。
- 3、如文档侵犯您的权益,请联系客服反馈,我们会尽快为您处理(人工客服工作时间:9:00-18:30)。
元器件引脚成形与切脚工艺、检验工艺规程(手工插装元器件)1.目的1.1.1.1.本规程规定了手工插装电子元器件引脚成形与切脚应满足的工艺要求,以及引脚成形与切脚过程的检验程序。
2.适用范围2.1.1.1.本规程适用于产品分立电子元器件插装前的引脚成形与切脚,规定了元器件引脚成形与切脚的技术要求和质量保证措施,同时也可作为设计、生产、检验的依据。
3.适用人员3.1.1.1.本规程适用于产品生产的工艺人员、电子装联操作人员、质量检验人员等。
4.参考文件4.1.1.1.IPC-A-610D 《电子组件的可接受性》。
4.1.1.2.IPC J-STD-001D 《焊接的电气和电子组件要求》。
4.1.1.3.QJ 3171—2003 《航天电子电气产品元器件成形技术要求》。
4.1.1.4.QJ 165A—1995 《航天电子电气产品安装通用技术要求》。
4.1.1.5.ANSI/ESD S20.20-2007 《静电放电控制方案》。
5.名词/术语5.1.1.1.功能孔:PCB上用于电气连接的孔。
5.1.1.2.非功能孔:PCB上用于机械安装或固定的孔。
5.1.1.3.支撑孔(Supported Hole):两层及多层PCB上的功能孔,孔壁上镀覆金属,俗称镀通孔。
5.1.1.4.非支撑孔(Unsupported Hole):单层或双层PCB上的功能孔,孔壁上不镀覆金属,俗称非镀通孔。
5.1.1.5.淬火引脚(Tempered lead):元器件的引脚经过淬火处理。
6.工艺元器件成形与切脚是整个PCBA生产的首要工序,成形与切脚的质量直接影响后续的产品生产。
6.1.工艺流程6.1.1.成形与切脚的工艺流程图工艺要求工艺流程说明根据元器件的封装、包装形式、本体以及引脚直径、成形类型、成形间距、印制板厚度、切脚长度以及元器件数量等确定成形与切脚的工具或模具,制定元器件成形与切脚明细表;元器件成形与切脚操作人员应按照设计、工艺文件要求对元器件的名称、型号、规格进行确认;根据明细表中的元器件特性及参数,选择元器件成形与切脚的顺序;依据成形顺序使元器件成形与切脚的尺寸调整更加容易控制;根据元器件首件的成形与切脚试验流程操作;首件成形与切脚检验完成后,将不合格的试样单独存放或处理;成形过程中要不定时的对工具或工装成形面的光滑度进行检查,确保成形质量;当元器件数量超过100个时,操作人员必须对最后成形与切脚的10个元器件按照试验检验项进行检验(7.1.2节);成形与切脚后的一般性元器件密闭保存;静电敏感元器件使用防静电容器存放;湿敏元器件要干燥存储(详见元器件存储工艺规程);图6-1元器件成形与切脚工艺流程6.1.2.首件成形与切脚试验6.1.2.1.成形与切脚试验时,要根据成形与切脚明细表的参数要求调整好工具或工装,按图6-2所示流程进行。
注:n为元器件成形与切脚的试验次数,①指成形与切脚实验检验项(7.1.2节)。
图6-2成形与切脚试验过程6.2.工艺原理6.2.1.1.元器件成形与切脚的目的是通过机械的方式,将元器件的引脚变形成预期的形状,依此来满足插装过程中的工艺要求。
此过程的工艺要求不仅包括插装时的尺寸要求,而且还包括应力释放、散热、高度等要求。
6.3.工艺要求6.3.1.应力释放要求元器件成形的应力释放的一般要求:6.3.1.1.成形元器件封装根部和焊接点间的引脚部分要有应力释放。
6.3.1.2.元器件引脚的延伸尽量与元器件本体的轴线平行。
6.3.1.3.安装在镀通孔内的元器件引脚尽量与印制板表面垂直。
6.3.1.4.因应力释放弯曲要求而采用不同引脚弯曲类型时,允许元器件本体产生偏移。
6.3.2.成形与切脚一般要求6.3.2.1.成形与切脚工具(设备)使用前应保持清洁,以防止残留的污垢、油脂及其它杂质对元器件引脚产生污染。
6.3.2.2.对静电敏感元器件成形与切脚时,必须在防静电工作台上进行操作,同时操作人员应穿戴防静电工作服、工作帽和工作鞋,并佩戴防静电腕带;禁止裸手直接接触元器件引脚。
6.3.2.3.成形与切脚过程中工具和设备应可靠接地,静电敏感元器件弯曲成形时应使用金属夹具。
6.3.2.4.使用模具成形时,夹具与引脚的接触面应光滑、平整,以免损伤引脚镀层。
6.3.2.5.引脚成形、剪切过程中,禁止扭转和沿轴向拉伸引脚,以避免损坏元器件内部引线或封装根部。
6.3.2.6.操作人员在成形与切脚过程中中途离开,应暂停成形与切脚工作;当再次成形与切脚时,要重新进行成形与切脚试验(6.1.2节)。
6.3.2.7.若成形与切脚过程中,有不当的设备移动、设备部件松动或撞击等可能影响成形与切脚参数的行为,必须重新进行成形与切脚试验(6.1.2节)。
6.3.2.8.成形与切脚后的元器件要放入封闭器具内,比如:屉式元件盒;静电敏感元器件应放置在防静电容器内。
6.3.2.9.元器件必须按照焊盘间距进行弯曲成形,弯曲基本对称,保证元器件安装后标识明显可见,如图6-3 所示;特殊情况下,标识外露的优先顺序为极性、数值、型号。
图6-3元器件标识朝向范围示意6.3.2.10.弯曲引脚时,弯曲的角度不能超过最终成形的弯曲角度。
6.3.2.11.引脚弯曲一次成形,不能反复弯曲。
6.3.2.12.不能在引脚较厚的方向弯曲,如对扁平形状的引脚不能进行横向弯曲。
6.3.2.13.淬火引脚不能弯曲成形,如继电器、电连接器等元器件引脚。
6.3.2.14.元器件引脚成形中,对有极性元器件,如:电解电容、二极管、三极管,注意引脚极性与成形方向之间的关系,切勿使方向弄反。
6.3.2.15.若使用短插工艺,则成形后的尺寸要符合元器件插装后的引脚伸出长度要求。
6.3.2.16.元器件引脚无论手工或机械成形,均不能有明显的刻痕或夹伤超过引脚直径或厚度的10%,也不能有引脚基材外露情况(元器件引脚切脚时的断面除外)。
6.3.3.引脚末端折弯要求6.3.3.1.引脚弯曲应沿着焊盘最长尺寸方向或沿与焊盘相连的印制导线方向折弯,如图6-4所示。
图6-4引脚折弯方向6.3.3.2.DIP元器件应该至少有两个对角线上的引脚沿元器件体的纵轴向外折弯。
6.3.3.3.直径或厚度大于1.3mm的引脚,以及淬火引脚(如继电器、电连接器等)都不应使用折弯进行固定。
6.3.3.4.通孔插装元器件引脚可以部分折弯与印制板板面垂线有15°~75°的夹角,用在焊接操作中固定组件,如图6-5所示。
①部分折弯②全折弯图6-5引脚折弯6.3.3.5.当元器件过轻,以致部分折弯不能满足后续焊接时的机械固定,可采用全折弯;全折弯的元器件引脚与印制板板面垂线的夹角为75°~90°,如图6-5。
6.3.3.6.非支撑孔中的引脚折弯45°~90°,保证在焊接中充分起到机械固定作用。
6.3.4.引脚末端突出要求6.3.4.1.支撑孔中的元器件引脚,其伸出部分L最小值要能使焊料中的引脚末端可辨识,L最大值为1.5mm,如图6-6所示。
图6-6引脚伸出长度6.3.4.2.非支撑孔中的元器件引脚,其伸出部分L最小值要能使引脚足够折弯,L最大值要满足最小电气间隙。
6.3.4.3.对于板厚大于2.3mm的印制板,如果使用固定引脚长度的元器件,如DIP、插座、连接器,作为最小的元器件引脚支撑肩需与印制板板面平齐,但是在后续焊接中允许引脚末端不在镀通孔中突出,但至少与板面平齐,如图6-7所示。
图6-7板厚H>2.3mm时,DIP等元器件的支撑肩与引脚伸出要求6.3.5.轴向引脚元器件要求引脚从本体两端引出的元器件,称为轴向引脚元器件。
6.3.5.1.水平安装轴向引脚元器件的引脚成形,元器件引脚的延伸尽量与元器件本体。
6.3.5.2.的轴线平行,弯曲引脚与板面垂直,不垂直度小于等于10°,如图6-8所示。
图6-8引脚成形不垂直度6.3.5.3.引脚从根部到弯曲点或从熔接点到弯曲点之间的距离L,至少相当于一倍引脚的直径或厚度但不小于0.8mm,如图6-9所示。
①从元器件本体测量②从焊料球测量③从熔接缝测量图6-9引脚弯曲保留长度L6.3.5.4.当元器件为小型玻璃封装并采用一般成形时,L1、L2最小值为2mm;如图6-10所示。
图6-10小型玻璃封装保留长度L(L1、L2)≥2mm6.3.5.5.最小内侧弯曲半径(表6-1);引脚的直径(D)或厚度(T)最小内侧弯曲半径(R)小于0.8mm(0.031in) 1×直径/厚度0.8mm(0.031in)~1.2mm(0.0472in) 1.5×直径/厚度大于1.2mm(0.0472in) 2×直径/厚度图6-11引脚直径(D)、厚度(T)、内侧弯曲半径(R)6.3.5.6.元器件紧贴印制板安装时,本体与板面间最大允许间距为0.5mm,如图6-12所示。
①贴板未打弯②贴板紧锁式打弯图6-12元器件贴板安装6.3.5.7.特殊引脚弯曲;1)对功率大于2W的散热元器件进行架高处理,要保证元器件的本体距印制板板面间;2)距大于1.5mm;3)在靠近印制板板面安装的散热元器件的引脚可参照图6-13所示进行成形;在非支撑孔安装时,必须按图②、③所示的在靠近板面部位进行打弯处理。
①架高元器件引脚无打弯处理(元器件较轻时) ②架高元器件引脚外向打弯处理③架高元器件引脚内向打弯处理④架高元器件引脚锁紧打弯处理图6-13元器件的架高处理6.3.6.径向引脚元器件要求元器件的两个或多个引脚从同一方向伸出,称为径向元器件。
6.3.6.1.引脚间距与安装孔距不等1)利用限位装置来达到机械支撑或元器件重量补偿的径向元器件的成形形式如图6-14 所示。
①合格(引脚变形适当)②不合格(变形过度)图6-14带限位装置2)引脚间距小于安装孔距,需要弯曲时,引脚根部到弯曲点距离B≥2D,且不小于0.8mm;最小弯曲半径R符合表6-1规定,如图6-15所示。
①合格(引脚变形适当)②不合格(变形过度)图6-15不带限位装置6.3.6.2.元器件的侧装,由于安装空间、安装难度及散热等要求,元器件需要侧装时,引脚成形按如下要求:1)径向引脚元器件侧装引脚成形,弯曲半径R最小为引脚的直径D,但至少为0.8mm,最大弯曲半径为3D,如图6-16所示;图6-16元器件侧装2)多引脚径向元器件侧面成形如图6-17 所示。
图6-17多引脚元器件侧装6.4.工作环境6.4.1.1.环境温度在18~30°C,相对湿度在30~70%。
6.4.1.2.工作台台面的光照度不低于1000lm/m²。
6.4.1.3.工作场地应清洁、整齐,并具有可靠的防静电接地系统。