炼钢成本
炼钢生铁成本预算表生产初期(不含税)
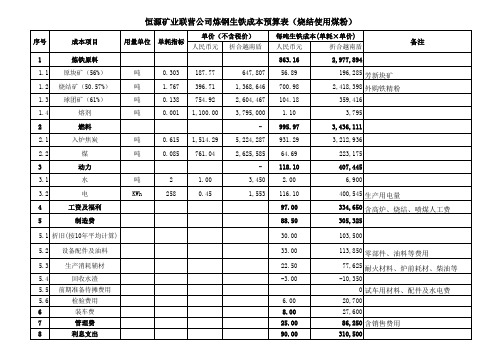
备注
5.1 折旧(按10年平均计算) 5.2 5.3 5.4 5.5 5.6 6 7 设备配件及油料 生产消耗辅材 回收水渣 前期准备待摊费用 检验费用 装车费 管理费
8 9 10
利息支出 综合成本合计 进项增值税
90.00 2,285.73 163.00
310,500 7,858,175 11,993,622
恒源矿业联营公司炼钢生铁成本预算表(烧结使用煤粉)
序号 1 1.1 1.2 1.3 1.4 2 2.1 2.2 3 3.1 3.2 4 5 成本项目 炼铁原料 原块矿(56%) 烧结矿(50.57%) 球团矿(61%) 熔剂 燃料 入炉焦炭 煤 动力 水 电 工资及福利 制造费 吨 KWh 2 258 1.00 0.45 吨 吨 0.615 0.085 1,514.29 761.04 吨 吨 吨 吨 0.303 1.767 0.138 0.001 187.77 396.71 754.92 1,100.00 647,807 1,368,646 2,604,467 3,795,000 5,224,287 2,625,585 3,450 1,553 用量单位 单耗指标 单价(不含税价) 人民币元 折合越南盾 每吨生铁成本(单耗×单价) 人民币元 863.16 56.89 700.98 104.18 1.10 995.97 931.29 64.69 118.10 2.00 116.10 97.00 88.50 30.00 33.00 22.50 -3.00 6.00 8.00 25.00 折合越南盾 2,977,894 196,285 芳新块矿 2,418,398 外购铁精粉 359,416 3,795 3,436,111 3,212,936 223,175 407,445 6,900 400,545 生产用电量 334,650 含高炉、烧结、喷煤人工费 305,325 103,500 113,850 零部件、油料等费用 77,625 耐火材料、炉前耗材、柴油等 -10,350 0 试车用材料、配件及水电费 20,700 27,600 86,250 含销售费用
钢材成本计算
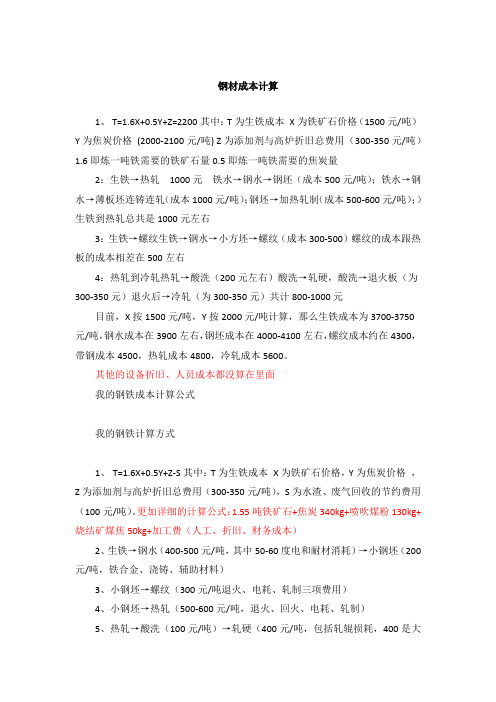
钢材成本计算1、T=1.6X+0.5Y+Z=2200其中:T为生铁成本X为铁矿石价格(1500元/吨)Y为焦炭价格(2000-2100元/吨) Z为添加剂与高炉折旧总费用(300-350元/吨)1.6即炼一吨铁需要的铁矿石量0.5即炼一吨铁需要的焦炭量2:生铁→热轧1000元铁水→钢水→钢坯(成本500元/吨);铁水→钢水→薄板坯连铸连轧(成本1000元/吨);钢坯→加热轧制(成本500-600元/吨);)生铁到热轧总共是1000元左右3:生铁→螺纹生铁→钢水→小方坯→螺纹(成本300-500)螺纹的成本跟热板的成本相差在500左右4:热轧到冷轧热轧→酸洗(200元左右)酸洗→轧硬,酸洗→退火板(为300-350元)退火后→冷轧(为300-350元)共计800-1000元目前,X按1500元/吨,Y按2000元/吨计算,那么生铁成本为3700-3750元/吨,钢水成本在3900左右,钢坯成本在4000-4100左右,螺纹成本约在4300,带钢成本4500,热轧成本4800,冷轧成本5600。
其他的设备折旧、人员成本都没算在里面我的钢铁成本计算公式我的钢铁计算方式1、T=1.6X+0.5Y+Z-S其中:T为生铁成本X为铁矿石价格,Y为焦炭价格,Z为添加剂与高炉折旧总费用(300-350元/吨),S为水渣、废气回收的节约费用(100元/吨)。
更加详细的计算公式:1.55吨铁矿石+焦炭340kg+喷吹煤粉130kg+烧结矿煤焦50kg+加工费(人工、折旧、财务成本)2、生铁→钢水(400-500元/吨,其中50-60度电和耐材消耗)→小钢坯(200元/吨,铁合金、浇铸、辅助材料)3、小钢坯→螺纹(300元/吨退火、电耗、轧制三项费用)4、小钢坯→热轧(500-600元/吨,退火、回火、电耗、轧制)5、热轧→酸洗(100元/吨)→轧硬(400元/吨,包括轧辊损耗,400是大钢厂指标)6、轧硬→退火(200元/吨)250罩退贵1007、轧硬→(退火50元/吨加热+锌层成本,按照50克锌层计算每平方米的)8、镀锌→彩涂(按每平米计算成本)。
炼钢厂成本核算规程细则4.2

第一章总则第一条目的为加强成本会计的管理作用,提高公司经济效益,根据《会计法》和《会计准则》的有关规定,结合炼钢厂的生产工艺特点,特制定本核算规程。
第二条本规程适用于黑龙江建龙钢铁有限公司炼钢厂。
第二章炼钢工序概况第三条黑龙江建龙钢铁有限公司炼钢厂投产于2006年6月,设计产能200万吨/年。
炼钢厂占地面积4.5万平方米。
主体设备包括一座900吨混铁炉、两座60吨顶底复吹转炉、一座80吨LF炉、一座80吨VD炉,一台六机六流方坯连铸机、一台六机六流圆坯连铸机;公用辅助设施包括:转炉一次烟气净化系统、二次烟气净化系统(包含混铁炉烟气除尘、散状材料上料系统除尘)、转炉浊循环水泵站及转炉污水处理设施。
1、生产产品:方坯:普通碳素结构钢、优质碳素结构钢。
代表钢种:Q195-235、20MnSiV、20MnSi、铸坯断面:150x150mm,定尺:6-12m圆坯:一般结构管用钢、流体管、石油套管用钢。
代表钢种:37Mn5 、36Mn2V、20#、N80、Q345B、P110;铸坯断面:φ150mm、φ160mm、φ180mm、φ210mm、φ270mm,定尺:4.2-12m。
工艺流程图及简要文字说明:炼钢厂现有生产作业区三个,按工艺顺序排列为:转炉作业区、方坯连铸作业区、圆坯连铸作业区。
2、转炉作业区:转炉公称容量60t,二座,采用顶底复合吹炼工艺,底部供气采用微机控制,氮、氩自动切换。
3、方坯连铸作业区:方坯连铸作业区现有六机六流小方坯连铸机一台,设计产能100万吨/年,采用敞开浇铸模式,生产铸坯直接热送轧钢厂.4、圆坯连铸作业区:(1)、圆坯连铸区现有六机六流圆坯连铸机一台,设计产能100万吨/年,配置有保护浇铸系统、气雾冷却、电磁搅拌、液面自动控制、打号机等先进设备.简要生产工艺流程图:见附件1第三章成本核算第四条成本核算对象1、为加强成本管理和业绩评价,对炼钢厂内部按其责任和控制范围划分为十一个成本中心:2、根据炼钢厂生产工艺特点,成本核算对象设定:按方、圆坯钢种类别分别计算总成本和单位成本。
短流程炼钢成本

短流程炼钢成本
短流程炼钢是一种高效的炼钢方法,通过简化炼钢工艺,减少设备和能源消耗,以及提高生产效率,以降低炼钢成本。
以下是一些可能的短流程炼钢成本降低措施:
1. 采用先进的高炉技术:使用高效节能的高炉技术,如高增益高炉和燃煤煤气化工艺,可以提高炼钢效率,降低原料损失和耗能。
2. 提高冶炼温度和炉内保温:增加冶炼温度和优化炉内保温措施,可以加快炼钢速度,减少能耗和生产周期。
3. 减少原料和能源消耗:通过优化原料配比,提高炉渣含铁率,减少废气和废渣的排放,降低原料和能源消耗。
4. 最小化下游处理流程:采用高质量的原料和高效的炼钢工艺,可以减少下游处理流程,如热处理、轧制和表面处理等。
5. 采用节能设备:使用节能设备和技术,如高效电弧炉、铁水预处理设备和废气余热回收系统,可以降低能耗和成本。
6. 优化生产计划和物流:通过优化生产计划和物流管理,减少库存和运输成本,提高生产效率和响应速度。
以上是一些可能的短流程炼钢成本降低措施,具体的成本降低效果还需要根据实际情况进行具体分析和实施。
炼钢成本分析
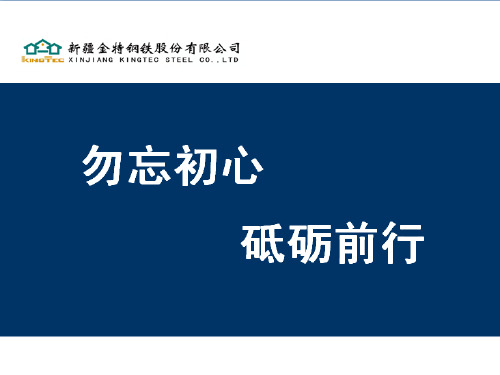
二
6月份与A对标及分析
3、(1)HRB400E合金完成情况及说明
HRB400E 成本项目
合金料 硅铁 硅锰合金 钒氮合金
元/吨 吨 吨 吨
硅钙合金
吨
碳化硅
吨
增碳剂
吨
4957.62 5418.8 129914.53
抛渣 单位 吨 吨 吨 吨 吨
月度指标预算
单耗 单位成本
单价
1115
2143.82
2037.71
960
1956.2
2037.71
50
101.89
1653.85
0
0
950
0
0
900
13
11.7
本月实际完成
单耗 单位成本
1110
2107.6
961.2 1958.67
20.6
41.8
41.5
68.62
8.8
15
62.17
1.5
7.44
7.5
40.64
0
0
1.5
3.94
4.5
8.19
0
0
本月实际
单耗
单位成本
14.1 1.1 8.1 0 0 4.5 0.43
58.51 5.35 44
0 0 8.16 0.99
预算比
单耗
单位成 本
-0.9 -3.66
-0.4 -2.09
0.6 3.36
0
0
-1.5 -3.94
307.67
318.01
炼钢成本核算流程

炼钢成本核算流程一、产量的确认与计量(一)、财务月报表的产量计算1、产品名称:钢坯2、计算方法:本期产量=本期库存产量+本期发出产量-上期库存产量3、库存产量的确认:前提:区分不同钢种及规格报告期日库存支数=盘点时点现场钢坯实际存储支数+报告期日时点至盘点时点发出支数-报告期日时点至盘点时点生产支数单支钢坯重量理论值计算公式=铸坯体积×7.8克/立方厘米(铁的密度)报告期日库存产量=报告期日库存支数×单支钢坯理论值重量4、发出产量的确认本期发出产量=供一轧产量+供二轧产量+直接外销产量⑴、供一轧产量的计算通过热送方式直接或由11#(12#)天车送往一轧厂,经炼钢厂、一轧厂、供应物资处三方区分不同钢种及规格分别记录发出支数,再由11#(12#)天车送往一轧厂过程中每班抽检三次,计算单支钢坯加权平均重量。
发出产量=发出支数×单支钢坯加权平均重量经上述方法确认计算发出产量后,由一轧厂开据产品验收入库单,于次日由拉矫组组长将产品验收入库单送至炼钢财务室,由核算员依产品验收入库单录入产量产销存日报表,并与一轧核算员相核对。
方坯发出产量时间结点:以本班作业时间为周期(本周期内连铸开浇炉次对应的发出量)⑵、供二轧产量的计算通过热送方式直接或由11#(12#)天车送往二轧厂,经炼钢厂、二轧厂双方区分不同钢种及规格分别记录发出支数,再由11#(12#)天车送往二轧厂过程中每班抽检三次,计算单支钢坯加权平均重量。
发出产量=发出支数×单支钢坯加权平均重量经上述方法确认计算发出产量后,由二轧厂开据产品验收入库单,于次日由拉矫组组长将产品验收入库单送至炼钢财务室,由核算员依产品验收入库单录入产量产销存日报表,并与二轧核算员相核对。
板坯发出产量时间结点:以上一班后半小时至本班7.5小时作业时间为周期(本周期内铸坯发出量)⑶、外销产量的计算由炼钢现场运往2#电子磅对外销售,于次日由拉矫组组长将验斤单送至炼钢财务室,由核算员依验斤单录入产量产销存日报表,并与磅称系统相核对。
钢铁成本计算公式

钢铁成本计算公式钢铁成本计算公式是指通过一系列的计算方法来确定钢铁产品的生产成本。
钢铁的生产成本包括原材料成本、人工成本、能源成本、设备维护成本等各个方面。
下面将逐一介绍这些成本的计算方法。
首先是原材料成本的计算。
钢铁的主要原材料是铁矿石和煤炭。
铁矿石的成本可以通过市场价格来确定,而煤炭的成本可以通过煤炭价格和消耗量来计算。
此外,还需要考虑到其他辅助材料的成本,如石灰石、脱硫剂等。
其次是人工成本的计算。
钢铁生产过程中需要大量的劳动力,包括生产工人、技术人员、管理人员等。
人工成本主要包括工资、福利待遇、培训费用等方面。
人工成本的计算需要考虑到工作时间、工作强度、员工素质等因素。
第三是能源成本的计算。
钢铁生产过程中需要大量的能源,包括电力、燃气、煤炭等。
能源成本的计算方法包括能源价格、能源消耗量等因素。
此外,还需要考虑到能源的利用效率、能源的供应稳定性等因素。
最后是设备维护成本的计算。
钢铁生产需要大量的设备和设施,包括高炉、转炉、轧机等。
设备的维护成本包括设备的折旧、维修费用、设备更换费用等方面。
设备维护成本的计算需要考虑到设备的使用寿命、设备的维护周期等因素。
钢铁成本的计算公式可以表示为:总成本 = 原材料成本 + 人工成本 + 能源成本 + 设备维护成本其中,原材料成本 = 铁矿石成本 + 煤炭成本 + 其他辅助材料成本人工成本 = 工资 + 福利待遇 + 培训费用能源成本 = 电力成本 + 燃气成本 + 煤炭成本设备维护成本 = 设备折旧 + 维修费用 + 更换费用通过以上公式,可以准确计算出钢铁产品的生产成本。
企业可以根据成本的计算结果,合理制定价格策略,优化生产过程,提高经济效益。
同时,钢铁成本的计算公式也为企业的决策提供了重要的参考依据。
钢铁产业是现代工业的重要支撑,钢铁成本的计算对于企业的发展具有重要意义。
通过合理的成本计算,企业可以准确评估自身的竞争力,优化资源配置,提高市场竞争力。
炼铁成本构成
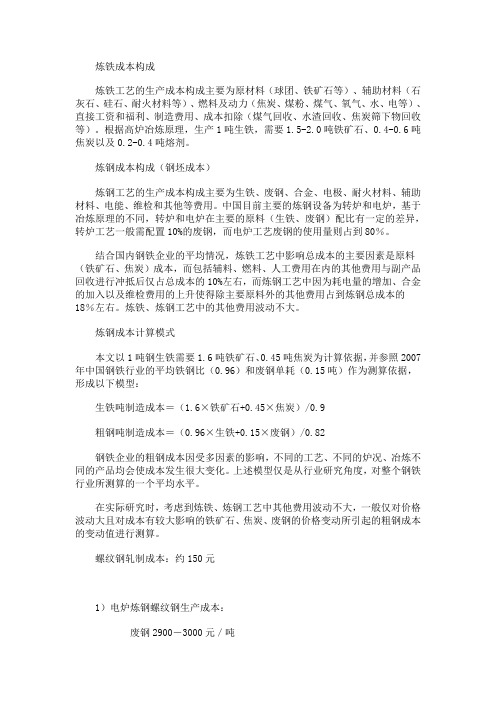
炼铁成本构成炼铁工艺的生产成本构成主要为原材料(球团、铁矿石等)、辅助材料(石灰石、硅石、耐火材料等)、燃料及动力(焦炭、煤粉、煤气、氧气、水、电等)、直接工资和福利、制造费用、成本扣除(煤气回收、水渣回收、焦炭筛下物回收等)。
根据高炉冶炼原理,生产1吨生铁,需要1.5-2.0吨铁矿石、0.4-0.6吨焦炭以及0.2-0.4吨熔剂。
炼钢成本构成(钢坯成本)炼钢工艺的生产成本构成主要为生铁、废钢、合金、电极、耐火材料、辅助材料、电能、维检和其他等费用。
中国目前主要的炼钢设备为转炉和电炉,基于冶炼原理的不同,转炉和电炉在主要的原料(生铁、废钢)配比有一定的差异,转炉工艺一般需配置10%的废钢,而电炉工艺废钢的使用量则占到80%。
结合国内钢铁企业的平均情况,炼铁工艺中影响总成本的主要因素是原料(铁矿石、焦炭)成本,而包括辅料、燃料、人工费用在内的其他费用与副产品回收进行冲抵后仅占总成本的10%左右,而炼钢工艺中因为耗电量的增加、合金的加入以及维检费用的上升使得除主要原料外的其他费用占到炼钢总成本的18%左右。
炼铁、炼钢工艺中的其他费用波动不大。
炼钢成本计算模式本文以1吨钢生铁需要1.6吨铁矿石、0.45吨焦炭为计算依据,并参照2007年中国钢铁行业的平均铁钢比(0.96)和废钢单耗(0.15吨)作为测算依据,形成以下模型:生铁吨制造成本=(1.6×铁矿石+0.45×焦炭)/0.9粗钢吨制造成本=(0.96×生铁+0.15×废钢)/0.82钢铁企业的粗钢成本因受多因素的影响,不同的工艺、不同的炉况、冶炼不同的产品均会使成本发生很大变化。
上述模型仅是从行业研究角度,对整个钢铁行业所测算的一个平均水平。
在实际研究时,考虑到炼铁、炼钢工艺中其他费用波动不大,一般仅对价格波动大且对成本有较大影响的铁矿石、焦炭、废钢的价格变动所引起的粗钢成本的变动值进行测算。
螺纹钢轧制成本:约150元1)电炉炼钢螺纹钢生产成本:废钢2900-3000元/吨电炉消耗废钢成本:(1:1.1)(2900-3000)*1.1=(3190-3300)元电耗:400度/吨*0.7元/吨=280元其他:350元(铁合金,电极,耐材等)20MnSi连铸坯价格在3820-3930元/吨螺纹钢轧制成本在150元/吨电炉炼钢螺纹钢最终成本为3970元/吨-4080元/吨2)转炉炼钢螺纹钢生产成本:铁精粉66%按照1560元/吨计算,烧结矿按照1700元/吨计算,矿和焦按照75%和25%的比例混合。
最全钢厂成本核算(简明计算)

最全钢厂成本核算(简明计算)1.钢铁企业生产流程钢铁企业生产流程大致可以分为粗钢冶炼和轧钢两步。
(1)粗钢冶炼冶炼工艺分为长流程和短流程两种。
长流程系通过高炉将铁矿石等原燃料炼成铁水,再经过转炉,将铁水冶炼成粗钢;短流程系将废钢通过电炉将废钢冶成粗钢。
其中,长流程钢材生产大体可以分为两个环节:炼铁环节(高温下的氧化还原反应)和炼钢环节(高温下的氧化反应)。
(2)轧钢粗钢经过轧制后,就形成各种不同规规格的最终产品——钢材。
2.钢铁企业成本构成从表1炼铁环节的主要反应原理不难看出,炼铁环节成本主要来自于Fe2O3/Fe3O4,即原材料铁矿石成本。
此外,炼铁环节还涉及辅助材料(石灰石、锰矿石、萤石和耐火材料等)、燃料及动力(焦炭、煤粉、煤气、氧气、水电等)、制造费用和人工等耗费。
炼钢环节主要原材料是铁水,从表1看,炼钢环节的反应原理是通过氧化反应将铁水中的碳含量降低;同时,因冷却铁水或出于降低炼钢综合成本等原因,炼钢过程中还需要加入一定量废钢;因此,炼钢成本主要由铁水和废钢成本构成。
此外,炼钢环节还涉及合金(主要为硅锰)、耐火材料、辅助材料、电能、维检和其他等耗费。
炼钢环节所生产的粗钢最终用于钢材的轧制流程;因此,轧钢过程成本主要由粗钢构成。
不同类型钢材的轧制过程还需不同燃气、电能、轧辊损耗等耗费;其中,螺纹钢轧制费用约为150元/吨、热轧板轧制费用约为300元/吨、冷轧板轧制费用约为950元/吨(冷轧流程轧制费用约为650元/吨,其前序热轧流程轧制费用约为300元/吨)、中厚板轧制费用约为400元/吨。
钢铁企业吨钢成本测算2014~2015年,国内钢铁行业供需严重失衡,各类钢材价格大幅下跌,钢铁行业利润水平收窄直至出现全面亏损;其间,钢材成本虽然一路下行,但由于钢铁行业处于产业链中上游,成本下行滞后于产品价格。
同理,2016年以来,供给侧结构性改革导致国内钢材价格显著回升,但吨钢生产成本亦显著上行。
钢铁厂成本计算

钢铁厂成本计算整个过程原材料→生铁→钢锭→螺纹、线材炼生铁成本构成主要为原材料(球团、铁矿石等) + 辅助材料(石灰石、硅石、耐火材料等) + 燃料及动力(焦炭、煤粉、煤气、氧气、水、电等) + 直接工资和福利、制造费用—成本扣除(煤气回收、水渣回收、焦炭筛下物回收等)1吨生铁:铁矿石吨 + 焦炭340kg + 喷吹煤粉130kg + 烧结矿煤焦65kg+加工费炼粗钢成本构成生铁 + 废钢+ ( 电极 + 耐火材料 + 辅助材料+ 电能 + 维检和其他等费用 )1吨粗钢:吨生铁 + 140kg废钢 + 加工费炼铁工艺中影响总成本的主要因素是原料(铁矿石、焦炭)成本,而包括辅料、燃料、人工费用在内的其他费用与副产品回收进行冲抵后,炼铁时其他费用+人工等费用越100元左右。
炼钢工艺中的其他费用大约400元左右焦炭340kg + 烧结矿煤焦65k ≈ 450kg 焦炭价格生铁吨制造成本= ×铁矿石+×焦炭+喷吹煤粉+100其它费用及人工费用粗钢吨制造成本= ×生铁+×废钢+400其他费用螺纹、线材成本 ==吨粗钢 + 压制费)×增值税:17%螺纹钢轧制费:约150元生铁吨制造成本=×铁矿石+×焦炭)/(根据高炉冶炼原理,生产1吨生铁,需要吨铁矿石、吨焦炭以及吨熔剂,而包括辅料、燃料、人工费用在内的其他费用与副产品回收进行冲抵后仅占总成本的10%左右)铁矿石焦炭粗钢吨制造成本=×生铁+×废钢)/(中国钢铁行业的平均铁钢比和废钢单耗吨)作为测算依据,炼钢工艺中因为耗电量的增加、合金的加入以及维检费用的上升使得除主要原料外的其他费用占到炼钢总成本的18%左右)生铁吨制造成* 570+*920)/=1473元/吨粗钢吨制造成本*1473+*1600)/=2017元/吨螺纹钢制造成本2017+150= 2167元/吨(螺纹钢轧制成本:约150元)。
钢材的生产成本计算
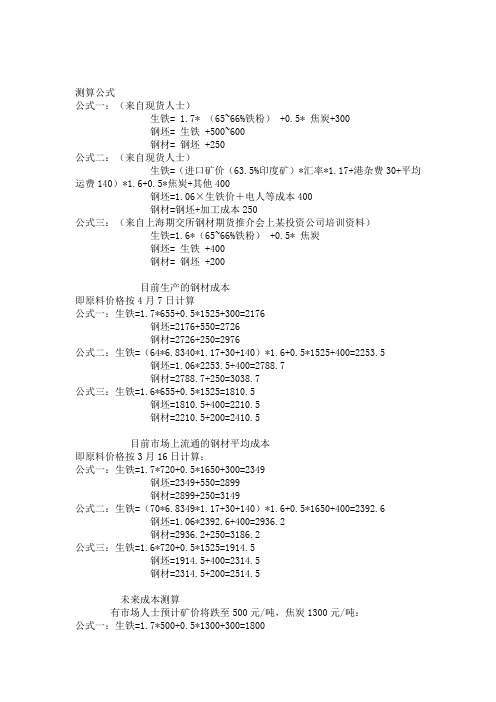
测算公式公式一:(来自现货人士)生铁= 1.7* (65~66%铁粉) +0.5* 焦炭+300钢坯= 生铁 +500~600钢材= 钢坯 +250公式二:(来自现货人士)生铁=(进口矿价(63.5%印度矿)*汇率*1.17+港杂费30+平均运费140)*1.6+0.5*焦炭+其他400钢坯=1.06×生铁价+电人等成本400钢材=钢坯+加工成本250公式三:(来自上海期交所钢材期货推介会上某投资公司培训资料)生铁=1.6*(65~66%铁粉) +0.5* 焦炭钢坯= 生铁 +400钢材= 钢坯 +200目前生产的钢材成本即原料价格按4月7日计算公式一:生铁=1.7*655+0.5*1525+300=2176钢坯=2176+550=2726钢材=2726+250=2976公式二:生铁=(64*6.8340*1.17+30+140)*1.6+0.5*1525+400=2253.5 钢坯=1.06*2253.5+400=2788.7钢材=2788.7+250=3038.7公式三:生铁=1.6*655+0.5*1525=1810.5钢坯=1810.5+400=2210.5钢材=2210.5+200=2410.5目前市场上流通的钢材平均成本即原料价格按3月16日计算:公式一:生铁=1.7*720+0.5*1650+300=2349钢坯=2349+550=2899钢材=2899+250=3149公式二:生铁=(70*6.8349*1.17+30+140)*1.6+0.5*1650+400=2392.6 钢坯=1.06*2392.6+400=2936.2钢材=2936.2+250=3186.2公式三:生铁=1.6*720+0.5*1525=1914.5钢坯=1914.5+400=2314.5钢材=2314.5+200=2514.5未来成本测算有市场人士预计矿价将跌至500元/吨,焦炭1300元/吨:公式一:生铁=1.7*500+0.5*1300+300=1800钢坯=1800+550=2350钢材=2350+250=2600公式三:生铁=1.6*500+0.5*1300=1450 钢坯=1450+400=1850钢材=1850+200=2050。
钢材成本计算

钢材成本计算1、T=1.6X+0.5Y+Z=2200其中:T为生铁成本X为铁矿石价格(1500元/吨)Y为焦炭价格(2000-2100元/吨) Z为添加剂与高炉折旧总费用(300-350元/吨)1.6即炼一吨铁需要的铁矿石量0.5即炼一吨铁需要的焦炭量2:生铁→热轧1000元铁水→钢水→钢坯(成本500元/吨);铁水→钢水→薄板坯连铸连轧(成本1000元/吨);钢坯→加热轧制(成本500-600元/吨);)生铁到热轧总共是1000元左右3:生铁→螺纹生铁→钢水→小方坯→螺纹(成本300-500)螺纹的成本跟热板的成本相差在500左右4:热轧到冷轧热轧→酸洗(200元左右)酸洗→轧硬,酸洗→退火板(为300-350元)退火后→冷轧(为300-350元)共计800-1000元目前,X按1500元/吨,Y按2000元/吨计算,那么生铁成本为3700-3750元/吨,钢水成本在3900左右,钢坯成本在4000-4100左右,螺纹成本约在4300,带钢成本4500,热轧成本4800,冷轧成本5600。
其他的设备折旧、人员成本都没算在里面我的钢铁成本计算公式我的钢铁计算方式1、T=1.6X+0.5Y+Z-S其中:T为生铁成本X为铁矿石价格,Y为焦炭价格,Z为添加剂与高炉折旧总费用(300-350元/吨),S为水渣、废气回收的节约费用(100元/吨)。
更加详细的计算公式:1.55吨铁矿石+焦炭340kg+喷吹煤粉130kg+烧结矿煤焦50kg+加工费(人工、折旧、财务成本)2、生铁→钢水(400-500元/吨,其中50-60度电和耐材消耗)→小钢坯(200元/吨,铁合金、浇铸、辅助材料)3、小钢坯→螺纹(300元/吨退火、电耗、轧制三项费用)4、小钢坯→热轧(500-600元/吨,退火、回火、电耗、轧制)5、热轧→酸洗(100元/吨)→轧硬(400元/吨,包括轧辊损耗,400是大钢厂指标)6、轧硬→退火(200元/吨)250罩退贵1007、轧硬→(退火50元/吨加热+锌层成本,按照50克锌层计算每平方米的)8、镀锌→彩涂(按每平米计算成本)。
钢材的生产成本计算

钢材的生产成本计算1.原材料成本:钢材的原材料通常是矿石,如铁矿石。
首先需要考虑的是矿石的采购成本,这涉及到矿石的价格、采购渠道等。
除了矿石采购的成本,还需要考虑其他辅助原材料的成本,如焦炭、螺纹钢等。
2.设备和人工成本:钢材的生产需要大量的设备投入,如高炉、连铸机等。
首先需要考虑设备的购买和维护成本。
设备购买成本包括设备本身的价格和相关设备的运输、安装等费用。
设备维护成本包括设备的保养、修理以及磨损零件的更换费用。
此外,还需要考虑人工成本,即工人的工资、福利等费用。
3.能源成本:4.生产过程中的其他成本:5.其他间接成本:以上是钢材生产成本计算的一般项目,以下是一个简单的例子,详细说明了其中的一些成本项目:假设钢材生产厂计划生产一批100吨钢材,利用电弧炉进行钢水冶炼和连铸。
1.原材料成本:假设铁矿石的购买价格为每吨2000元,总共需要采购100吨铁矿石,那么原材料成本为2000元/吨×100吨=200,000元。
2.设备和人工成本:假设电弧炉和连铸机的购买和设备维护费用为1000万元,每批生产需要10名工人,每名工人的薪资和福利共计8000元/月。
假设生产周期为1个月,那么设备和人工成本为1000万元+10人×8000元/月×1个月=1080万元。
3.能源成本:4.生产过程中的其他成本:假设水的购买费用为每吨2元,每批生产需要消耗1000吨水,那么其他成本为2元/吨×1000吨=2000元。
此外,若需要进行废气、尾渣的处理,还需要考虑相应的费用。
5.其他间接成本:综上所述,钢材的生产成本计算包括原材料成本、设备和人工成本、能源成本、生产过程中的其他成本以及其他间接成本等多个方面。
通过合理计算和控制这些成本,可以帮助企业提高经济效益和竞争力。
炼钢成本分析报告
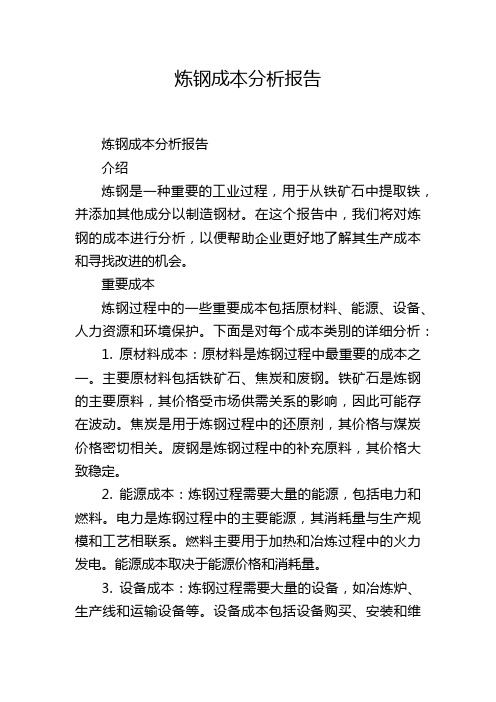
炼钢成本分析报告炼钢成本分析报告介绍炼钢是一种重要的工业过程,用于从铁矿石中提取铁,并添加其他成分以制造钢材。
在这个报告中,我们将对炼钢的成本进行分析,以便帮助企业更好地了解其生产成本和寻找改进的机会。
重要成本炼钢过程中的一些重要成本包括原材料、能源、设备、人力资源和环境保护。
下面是对每个成本类别的详细分析:1. 原材料成本:原材料是炼钢过程中最重要的成本之一。
主要原材料包括铁矿石、焦炭和废钢。
铁矿石是炼钢的主要原料,其价格受市场供需关系的影响,因此可能存在波动。
焦炭是用于炼钢过程中的还原剂,其价格与煤炭价格密切相关。
废钢是炼钢过程中的补充原料,其价格大致稳定。
2. 能源成本:炼钢过程需要大量的能源,包括电力和燃料。
电力是炼钢过程中的主要能源,其消耗量与生产规模和工艺相联系。
燃料主要用于加热和冶炼过程中的火力发电。
能源成本取决于能源价格和消耗量。
3. 设备成本:炼钢过程需要大量的设备,如冶炼炉、生产线和运输设备等。
设备成本包括设备购买、安装和维护等费用。
设备成本的水平和效率将直接影响到炼钢的生产效率和生产能力。
4. 人力资源成本:炼钢过程需要大量的劳动力,包括技术人员、炼钢工人和管理人员等。
人力资源成本包括工资、培训和福利等费用。
5. 环境保护成本:炼钢过程会产生大量的废气、废水和固体废弃物等。
为了符合环境保护要求,企业需要投入大量的资源用于废物处理和环境治理。
环境保护成本将直接影响到炼钢厂的运营成本。
成本分析为了更好地管理和控制成本,企业可以采取以下措施:1. 优化原材料采购:企业可以通过制定长期的原材料采购计划,优化原材料的供应链。
此外,企业还可以与供应商建立长期的合作关系,以获得更好的价格和质量。
2. 提高能源利用效率:企业可以采用先进的能源管理技术,如高效燃烧和余热回收等,以提高能源利用效率。
3. 更新设备和技术:企业可以定期更新设备和引入新的技术,以提高生产效率和降低生产成本。
4. 建立合理的人力资源管理制度:企业可以通过优化人力资源的配置和提供培训计划来提高员工的工作效率,并通过提供合理的薪酬和福利来提高员工的满意度和忠诚度。
炼钢厂成本管理工作总结
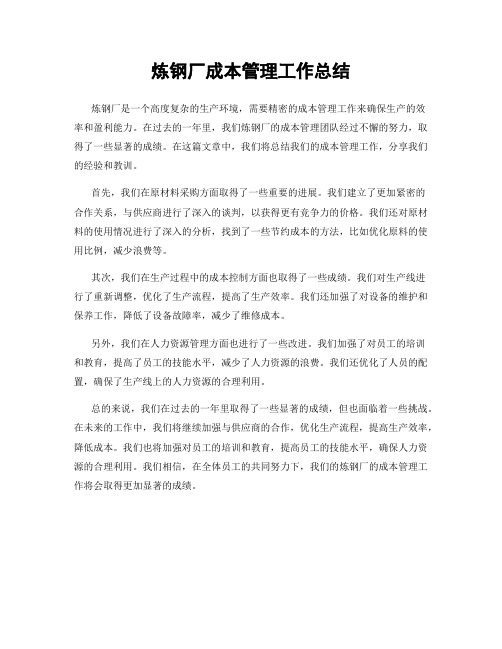
炼钢厂成本管理工作总结
炼钢厂是一个高度复杂的生产环境,需要精密的成本管理工作来确保生产的效
率和盈利能力。
在过去的一年里,我们炼钢厂的成本管理团队经过不懈的努力,取得了一些显著的成绩。
在这篇文章中,我们将总结我们的成本管理工作,分享我们的经验和教训。
首先,我们在原材料采购方面取得了一些重要的进展。
我们建立了更加紧密的
合作关系,与供应商进行了深入的谈判,以获得更有竞争力的价格。
我们还对原材料的使用情况进行了深入的分析,找到了一些节约成本的方法,比如优化原料的使用比例,减少浪费等。
其次,我们在生产过程中的成本控制方面也取得了一些成绩。
我们对生产线进
行了重新调整,优化了生产流程,提高了生产效率。
我们还加强了对设备的维护和保养工作,降低了设备故障率,减少了维修成本。
另外,我们在人力资源管理方面也进行了一些改进。
我们加强了对员工的培训
和教育,提高了员工的技能水平,减少了人力资源的浪费。
我们还优化了人员的配置,确保了生产线上的人力资源的合理利用。
总的来说,我们在过去的一年里取得了一些显著的成绩,但也面临着一些挑战。
在未来的工作中,我们将继续加强与供应商的合作,优化生产流程,提高生产效率,降低成本。
我们也将加强对员工的培训和教育,提高员工的技能水平,确保人力资源的合理利用。
我们相信,在全体员工的共同努力下,我们的炼钢厂的成本管理工作将会取得更加显著的成绩。
螺纹钢冶金成本分析

螺纹钢冶金成本分析一、螺纹钢工艺简介目前,我国螺纹钢生产工艺大致有二种,一为连铸连轧,二为调坯轧材。
后者是在今后若干年中被明令淘汰的落后工艺,这种加工方法的最大特点是需要异地将钢坯再度加热。
也就是说,调坯轧材厂在购置钢坯时,需要在运输、仓储、人工等方面额外承担一定的费用;在正式加工时,还需要再度加热,消耗一定的能源。
目前,这种采用这种的生产企业多是一些小企业,且市场份额占有率较低,因此我们估算螺纹钢成本时将不采用这种方法。
二、炼铁成本构成炼铁工艺的生产成本构成主要为原材料(球团、铁矿石等)、辅助材料(石灰石、硅石、耐火材料等)、燃料及动力(焦炭、煤粉、煤气、氧气、水、电等)、直接工资和福利、制造费用、成本扣除(煤气回收、水渣回收、焦炭筛下物回收等)。
根据高炉冶炼原理,生产1吨生铁,需要1.5-2.0吨铁矿石、0.4-0.6吨焦炭以及0.2-0.4吨熔剂。
三、炼钢成本构成(钢坯成本)炼钢工艺的生产成本构成主要为生铁、废钢、合金、电极、耐火材料、辅助材料、电能、维检和其他等费用。
中国目前主要的炼钢设备为转炉和电炉,基于冶炼原理的不同,转炉和电炉在主要的原料(生铁、废钢)配比有一定的差异,转炉工艺一般需配置10%的废钢,而电炉工艺废钢的使用量则占到80,。
结合国内钢铁企业的平均情况,炼铁工艺中影响总成本的主要因素是原料(铁矿石、焦炭)成本,而包括辅料、燃料、人工费用在内的其他费用与副产品回收进行冲抵后仅占总成本的10%左右,而炼钢工艺中因为耗电量的增加、合金的加入以及维检费用的上升使得除主要原料外的其他费用占到炼钢总成本的18,左右。
炼铁、炼钢工艺中的其他费用波动不大。
因此,不难看出制约螺纹钢成本的关键是铁矿石和焦炭价格。
四、炼钢成本计算模式本文以1吨钢生铁需要1.6吨铁矿石、0.45吨焦炭为计算依据,并参照中国钢铁行业的平均铁钢比(0.96)和废钢单耗(0.15吨)作为测算依据,形成以下模型: 生铁吨制造成本,(1.6×铁矿石+0.45×焦炭)/0.9粗钢吨制造成本,(0.96×生铁+0.15×废钢)/0.82钢铁企业的粗钢成本因受多因素的影响,不同的工艺、不同的炉况、冶炼不同的产品均会使成本发生很大变化。
- 1、下载文档前请自行甄别文档内容的完整性,平台不提供额外的编辑、内容补充、找答案等附加服务。
- 2、"仅部分预览"的文档,不可在线预览部分如存在完整性等问题,可反馈申请退款(可完整预览的文档不适用该条件!)。
- 3、如文档侵犯您的权益,请联系客服反馈,我们会尽快为您处理(人工客服工作时间:9:00-18:30)。
炼钢成本
生铁吨制造成本=(1.6×铁矿石+0.45×焦炭)/0.9
粗钢吨制造成本=(0.96×生铁+0.15×废钢)/0.82
钢坯生产成本计算公式:矿石价格*1.6*1.13+焦炭价格*0.5+600挑费,普碳坯成本计算公式=铁水*1.1+其他费用300 ,炼铁成本=烧结矿*1.7+焦炭*0.5+其他费用250。
钢坯生产成本:按铁矿石最低价1000元/吨计算,一吨铁水需1.6吨铁矿石,为1600元;焦炭价格1800元/吨,一吨铁水消耗500公斤,计900元;加上其它费用200元/吨,铁水的成本为2900元/吨。
铁水转化为钢水,制造费400元/吨,为3300元/吨,另加80元/吨合金材料费用,为3380元/吨,轧制螺纹钢线材等建筑钢材的低合金钢坯和普碳方坯之间成本差价基本为100元/吨,由此推算出目前低合金方坯的生产成本为3480元/吨,加上设备折旧和人员费用150元/吨,低合金方坯直接成本为3630元/吨,而市场售价目前在3750元/吨左右,钢坯生产厂家还有一定的利润空间,而加上轧制成本后,二级螺纹钢的生产成本在3720元/吨左右,三级螺纹钢的生产成本在3800元/吨左右,反观目前的市场成交价格,已经基本贴近钢厂的生产成本区域,唯一需要关注的就是原料的下跌幅度和深度,如钢坯价格短期内不能止跌企稳,不排除钢厂开始杀跌清理库存,加速生产的可能性。
炼铁工艺的生产成本构成主要为原材料(球团、铁矿石等)、辅助材料(石灰石、硅石、耐火材料等)、燃料及动力(焦炭、煤粉、煤气、氧气、水、电等)、直接工资和福利、制造费用、成本扣除(煤气回收、水渣回收、焦炭筛下物回收等)。
根据高炉冶炼原理,生产1吨生铁,需要1.5-2.0吨铁矿石、0.4-0.6吨焦炭以及0.2-0.4吨熔剂。
炼钢工艺的生产成本构成主要为生铁、废钢、合金、电极、耐火材料、辅助材料、电能、维检和其他等费用。
中国目前主要的炼钢设备为转炉和电炉,基于冶炼原理的不同,转炉和电炉在主要的原料(生铁、废钢)配比有一定的差异,转炉工艺一般需配置10%的废钢,而电炉工艺废钢的使用量则占到80%。
结合国内钢铁企业的平均情况,炼铁工艺中影响总成本的主要因素是原料(铁矿石、焦炭)成本,而包括辅料、燃料、人工费用在内的其他费用与副产品回收进行冲抵后仅占总成本的10%左右,而炼钢工艺中因为耗电量的增加、合金的加入以及维检费用的上升使得除主要原料外的其他费用占到炼钢总成本的18%左右。
炼铁、炼钢工艺中的其他费用波动不大。
以1吨钢生铁需要1.6吨铁矿石、0.45吨焦炭为计算依据,并参照2007年中国钢铁行业的平均铁钢比(0.96)和废钢单耗(0.15吨)作为测算依据。
在实际研究时,考虑到炼铁、炼钢工艺中其他费用波动不大,一般仅对价格波动大且对成本有较大影响的铁矿石、焦炭、废钢的价格变动所引起的粗钢成本的变动值进行测算。