压铸机吨位的选用方法[高级教资]
压铸机吨位的选用(严选内容)
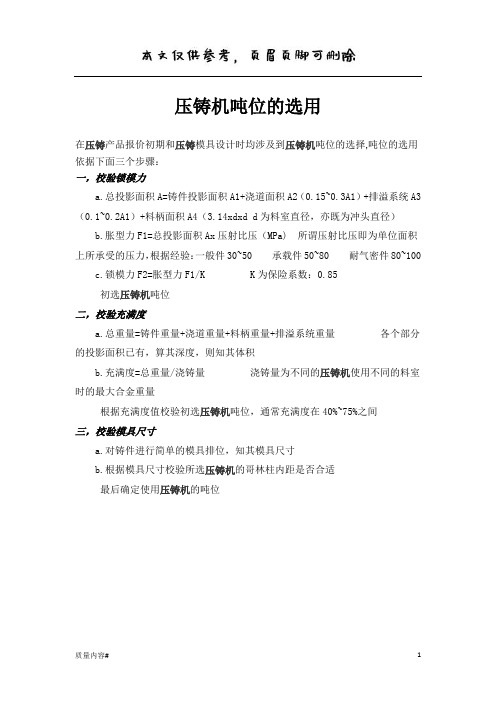
压铸机吨位的选用在压铸产品报价初期和压铸模具设计时均涉及到压铸机吨位的选择,吨位的选用依据下面三个步骤:一,校验锁模力a.总投影面积A=铸件投影面积A1+浇道面积A2(0.15~0.3A1)+排溢系统A3(0.1~0.2A1)+料柄面积A4(3.14xdxd d为料室直径,亦既为冲头直径)b.胀型力F1=总投影面积Ax压射比压(MPa) 所谓压射比压即为单位面积上所承受的压力,根据经验:一般件30~50 承载件50~80 耐气密件80~100c.锁模力F2=胀型力F1/K K为保险系数:0.85初选压铸机吨位二,校验充满度a.总重量=铸件重量+浇道重量+料柄重量+排溢系统重量各个部分的投影面积已有,算其深度,则知其体积b.充满度=总重量/浇铸量浇铸量为不同的压铸机使用不同的料室时的最大合金重量根据充满度值校验初选压铸机吨位,通常充满度在40%~75%之间三,校验模具尺寸a.对铸件进行简单的模具排位,知其模具尺寸b.根据模具尺寸校验所选压铸机的哥林柱内距是否合适最后确定使用压铸机的吨位合理选择压铸机的方法1:理论计算的锁模力一定要小于压铸机公称锁模力的大小2:理论计算压室容量应小于压铸机公称压室的容量3:理论计算的模具开模力和推件力应小于所选压铸机最大开模力和推件力4:模具的总厚度应大于压铸机最小合模距离5:压铸件最大开模距离应大于模具总厚度与产品高度总和6:模具安装在压铸机上的模板尺寸及孔位应与压铸机固定板尺寸及孔位位置相适应7:模具外形尺寸和伸出模体的外部机构的最大尺寸应不与压铸机拉杆相碰,不然会影响压铸机的正常运行和使用•如何选购压铸机?•压铸机的选择,通常依锁模力、射料量、铸造面积为依据。
一、确定压铸机的锁模力锁模力是选用压铸机时首先要确定的参数。
锁模力的作用主要是为了克服模腔内的涨型力,以锁紧模具的分型面,防止金属液飞溅,保证铸件的尺寸精度。
压铸机的锁模力计算如下:F=k×p×sF---计算锁模力k---安全系数p---压射比压s---投影面积安全系数K与铸件的复杂程度以及压铸工艺等因素有关,一般取1-1.3对于薄壁复杂铸件,由于采用较高的压射速度,压射比压和模具温度,使模具分型面受到较大的冲击,因此K应取较大值,反之取较小值。
压铸机的选用流程

压铸机的选用流程1.确定加工工艺和要求:在选用压铸机之前,需要首先明确加工的工艺和对成品的要求。
例如需要铸造哪种材料,零件的尺寸和重量范围是多少,是否需要进行二次加工等。
2.性能指标:根据加工工艺和要求,确定一些性能指标,如最大锁力、最大注射力、最大锁模行程、注射速度,以及对注射压力、速度和位置的控制精度等。
这些指标将决定压铸机的能力和性能。
3.型号选择:4.厂家选择:在确定了几个适用的型号后,需要选择可靠的压铸机厂家。
可以通过参观厂家的生产线和展示厅,了解其生产能力和技术水平。
还可以询问其他使用该压铸机厂家产品的企业的意见和评价,选择口碑较好的厂家。
5.配套设备:根据加工要求和压铸机的型号,确定是否需要购买配套设备。
配套设备包括铸造模具、冷却设备、气动和液压系统、电气控制系统等。
这些设备需要与压铸机配套使用,以便满足生产需求。
6.技术支持和售后服务:在购买压铸机之前,需要了解压铸机厂家的技术支持能力和售后服务。
良好的技术支持和售后服务能够有效地解决使用中遇到的问题,提高设备的使用率和生产效率。
7.成本和预算:最后,需要根据企业的预算,综合考虑性能、质量、价格和服务等因素,确定最终的选购方案。
同时需要注意避免一味追求低价而忽略了设备的性能和质量。
在选用压铸机时,以上步骤是基本的流程。
但是,需要根据实际情况进行调整和变化。
在整个选购过程中,建议与经验丰富的压铸机厂家和专业工程师进行多次沟通和交流,以确保选购到适合自己企业需求的压铸机。
合理选择压铸机的方法【技巧】

1:理论计算的锁模力一定要小于压铸机公称锁模力的大小
2:理论计算压室容量应小于压铸机公称压室的容量
3:理论计算的模具开模力和推件力应小于所选压铸机最大开模力和推件力
4:模具的总厚度应大于压铸机最小合模距离
5:压铸件最大开模距离应大于模具总厚度与产品高度总和
6:模具安装在压铸机上的模板尺寸及孔位应与压铸机固定板尺寸及孔位位置相适应
7:模具外形尺寸和伸出模体的外部机构的最大尺寸应不与压铸机拉杆相碰,不然会影响压铸机的正常运行和使用。
铝压铸吨位

铝压铸吨位
500吨和600吨
铝合金压铸机吨位对应500吨和600吨。
根据查询相关公开信息显示,截止2023年2月21日,根据制造工厂表明目前铝合金压铸机吨位对应只有两位,分别是500吨和600吨,用于生产铝合金压铸件。
铝合金压铸机用于生产铝合金压铸件,特点是压铸范围广、铸件尺寸精度高、表面粗糙度低的特点。
铝合金压铸吨位是指铝合金压铸机的最大压铸力,通常用吨(T)作为单位。
铝合金压铸吨位越大,说明压铸机的压力越大,可以制造更大尺寸、更复杂的铝合金零件。
一般来说,对于中小型铝合金压铸件,选择200-500吨位的压铸机即可满足生产需求。
但如果铸件尺寸较大或生产速率较高,则需要更大吨位的压铸机。
压铸机的选择 压铸机的类型 压铸机的选用
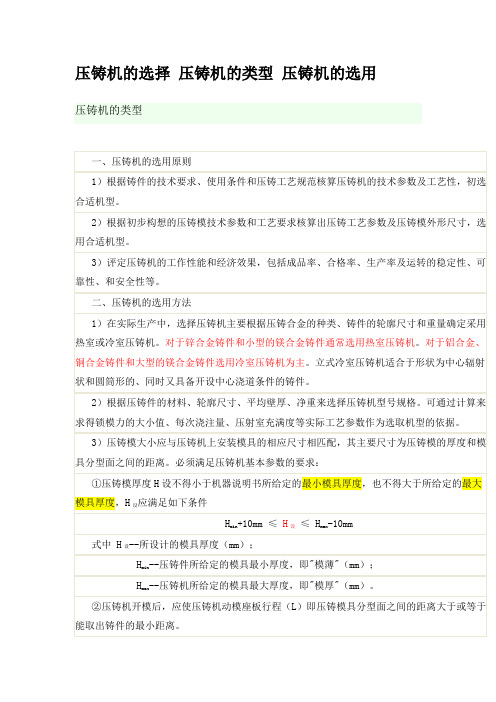
1)在实际生产中,选择压铸机主要根据压铸合金的种类、铸件的轮廓尺寸和重量确定采用热室或冷室压铸机。对于锌合金铸件和小型的镁合金铸件通常选用热室压铸机。对于铝合金、铜合金铸件和大型的镁合金铸件选用冷室压铸机为主。立式冷室压铸机适合于形状为中心辐射状和圆筒形的、同时又具备开设中心浇道条件的铸件。
2)根据压铸件的材料、轮廓尺寸、平均壁厚、净重来选择压铸机型号规格。可通过计算来求得锁模力的大小值、每次浇注量、压射室充满度等实际大小应与压铸机上安装模具的相应尺寸相匹配,其主要尺寸为压铸模的厚度和模具分型面之间的距离。必须满足压铸机基本参数的要求:
①压铸模厚度H设不得小于机器说明书所给定的最小模具厚度,也不得大于所给定的最大模具厚度,H设应满足如下条件
Hmin+10mm≤H设≤Hmax-10mm
式中H设--所设计的模具厚度(mm);
Hmin--压铸件所给定的模具最小厚度,即"模薄"(mm);
Hmax--压铸机所给定的模具最大厚度,即"模厚"(mm)。
②压铸机开模后,应使压铸机动模座板行程(L)即压铸模具分型面之间的距离大于或等于能取出铸件的最小距离。
压铸机的选择压铸机的类型压铸机的选用
压铸机的类型
一、压铸机的选用原则
1)根据铸件的技术要求、使用条件和压铸工艺规范核算压铸机的技术参数及工艺性,初选合适机型。
2)根据初步构想的压铸模技术参数和工艺要求核算出压铸工艺参数及压铸模外形尺寸,选用合适机型。
3)评定压铸机的工作性能和经济效果,包括成品率、合格率、生产率及运转的稳定性、可靠性、和安全性等。
L≥L取
如图5-6所示为推杆推出的压铸模取出铸件的最小距离。
L取≥L芯+L件+K
铝压铸吨位
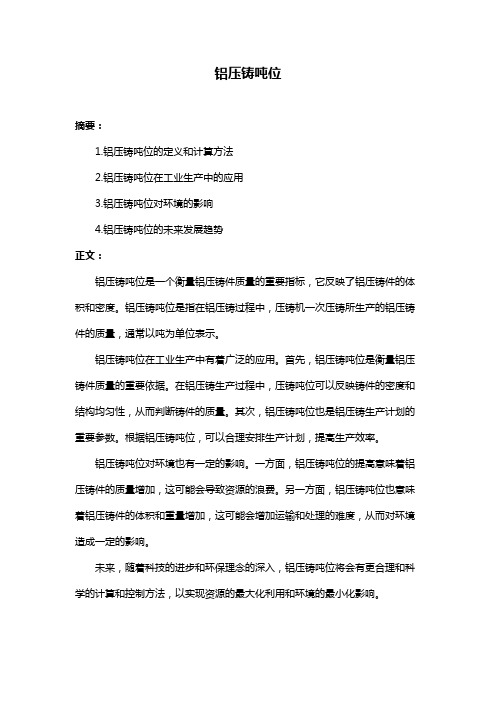
铝压铸吨位
摘要:
1.铝压铸吨位的定义和计算方法
2.铝压铸吨位在工业生产中的应用
3.铝压铸吨位对环境的影响
4.铝压铸吨位的未来发展趋势
正文:
铝压铸吨位是一个衡量铝压铸件质量的重要指标,它反映了铝压铸件的体积和密度。
铝压铸吨位是指在铝压铸过程中,压铸机一次压铸所生产的铝压铸件的质量,通常以吨为单位表示。
铝压铸吨位在工业生产中有着广泛的应用。
首先,铝压铸吨位是衡量铝压铸件质量的重要依据。
在铝压铸生产过程中,压铸吨位可以反映铸件的密度和结构均匀性,从而判断铸件的质量。
其次,铝压铸吨位也是铝压铸生产计划的重要参数。
根据铝压铸吨位,可以合理安排生产计划,提高生产效率。
铝压铸吨位对环境也有一定的影响。
一方面,铝压铸吨位的提高意味着铝压铸件的质量增加,这可能会导致资源的浪费。
另一方面,铝压铸吨位也意味着铝压铸件的体积和重量增加,这可能会增加运输和处理的难度,从而对环境造成一定的影响。
未来,随着科技的进步和环保理念的深入,铝压铸吨位将会有更合理和科学的计算和控制方法,以实现资源的最大化利用和环境的最小化影响。
压铸机台吨位选择

56
100
2.67
0.785
2500
压铸机设备快压射位置、高速位置设定
铝台设 备快压
高速位置 设定
浇口前的 体积
浇口前的重 量
产品重量
渣包重量
材料密度
料筒截面 积
快压射行 程
mm
cm2
g
g
g
g/cm3
cm2
mm
181.70159 243.44569 650
550
100
2.67
38.46 63.298412
100%
mm
g
g
g
g/cm3
34.78% 125.19383 500
56
100
2.67
分体料筒 充满度
整模产品 所占料筒 产品重量 渣包重量 浇道重量 材料密度
长度
100%
mm
g
g
g
g/cm3
∏/4 料筒d2
0.785 0.785
mm2 2500
∏/4
料筒d2
0.785
mm2
21.77% 125.19383 500
增压位置 设定
浇口前的 体积
带浇口渣包 的产品体积
产品重量
渣包重量
浇口重量
材料密度
料筒截面 积
mm
cm2
cm2
g
g
g
g/cm3
cm2
485.26178 243.44569 318.35206 550
100
200
2.67
38.46
熔融金属从开始进入型腔到充满所需的 时间
充填时间 α 产品壁厚 产品壁厚
40
面积设定
压铸机吨位的选用
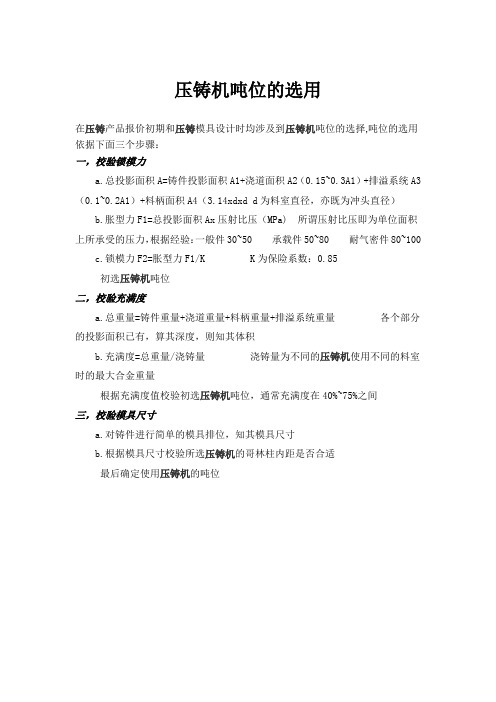
压铸机吨位的选用在压铸产品报价初期和压铸模具设计时均涉及到压铸机吨位的选择,吨位的选用依据下面三个步骤:一,校验锁模力a.总投影面积A=铸件投影面积A1+浇道面积A2(0.15~0.3A1)+排溢系统A3(0.1~0.2A1)+料柄面积A4(3.14xdxd d为料室直径,亦既为冲头直径)b.胀型力F1=总投影面积Ax压射比压(MPa) 所谓压射比压即为单位面积上所承受的压力,根据经验:一般件30~50 承载件50~80 耐气密件80~100c.锁模力F2=胀型力F1/K K为保险系数:0.85初选压铸机吨位二,校验充满度a.总重量=铸件重量+浇道重量+料柄重量+排溢系统重量各个部分的投影面积已有,算其深度,则知其体积b.充满度=总重量/浇铸量浇铸量为不同的压铸机使用不同的料室时的最大合金重量根据充满度值校验初选压铸机吨位,通常充满度在40%~75%之间三,校验模具尺寸a.对铸件进行简单的模具排位,知其模具尺寸b.根据模具尺寸校验所选压铸机的哥林柱内距是否合适最后确定使用压铸机的吨位合理选择压铸机的方法1:理论计算的锁模力一定要小于压铸机公称锁模力的大小2:理论计算压室容量应小于压铸机公称压室的容量3:理论计算的模具开模力和推件力应小于所选压铸机最大开模力和推件力4:模具的总厚度应大于压铸机最小合模距离5:压铸件最大开模距离应大于模具总厚度与产品高度总和6:模具安装在压铸机上的模板尺寸及孔位应与压铸机固定板尺寸及孔位位置相适应7:模具外形尺寸和伸出模体的外部机构的最大尺寸应不与压铸机拉杆相碰,不然会影响压铸机的正常运行和使用•如何选购压铸机?•压铸机的选择,通常依锁模力、射料量、铸造面积为依据。
一、确定压铸机的锁模力锁模力是选用压铸机时首先要确定的参数。
锁模力的作用主要是为了克服模腔内的涨型力,以锁紧模具的分型面,防止金属液飞溅,保证铸件的尺寸精度。
压铸机的锁模力计算如下:F=k×p×sF---计算锁模力k---安全系数p---压射比压s---投影面积安全系数K与铸件的复杂程度以及压铸工艺等因素有关,一般取1-1.3对于薄壁复杂铸件,由于采用较高的压射速度,压射比压和模具温度,使模具分型面受到较大的冲击,因此K应取较大值,反之取较小值。
压铸机的选用 压铸工艺参数的设定和调节
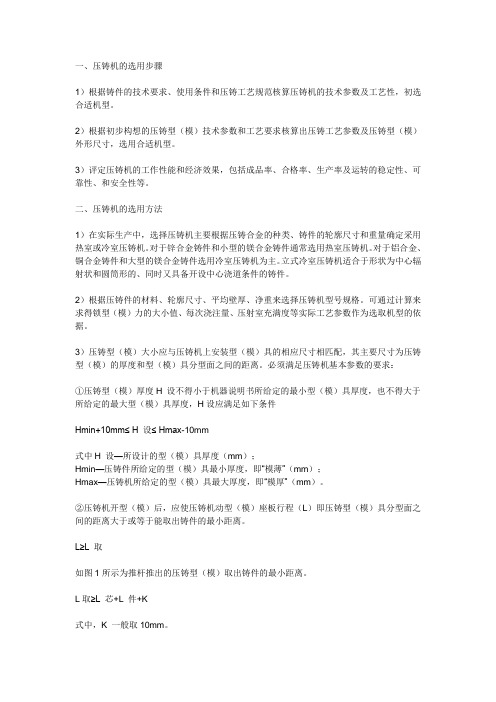
一、压铸机的选用步骤1)根据铸件的技术要求、使用条件和压铸工艺规范核算压铸机的技术参数及工艺性,初选合适机型。
2)根据初步构想的压铸型(模)技术参数和工艺要求核算出压铸工艺参数及压铸型(模)外形尺寸,选用合适机型。
3)评定压铸机的工作性能和经济效果,包括成品率、合格率、生产率及运转的稳定性、可靠性、和安全性等。
二、压铸机的选用方法1)在实际生产中,选择压铸机主要根据压铸合金的种类、铸件的轮廓尺寸和重量确定采用热室或冷室压铸机。
对于锌合金铸件和小型的镁合金铸件通常选用热室压铸机。
对于铝合金、铜合金铸件和大型的镁合金铸件选用冷室压铸机为主。
立式冷室压铸机适合于形状为中心辐射状和圆筒形的、同时又具备开设中心浇道条件的铸件。
2)根据压铸件的材料、轮廓尺寸、平均壁厚、净重来选择压铸机型号规格。
可通过计算来求得锁型(模)力的大小值、每次浇注量、压射室充满度等实际工艺参数作为选取机型的依据。
3)压铸型(模)大小应与压铸机上安装型(模)具的相应尺寸相匹配,其主要尺寸为压铸型(模)的厚度和型(模)具分型面之间的距离。
必须满足压铸机基本参数的要求:①压铸型(模)厚度H 设不得小于机器说明书所给定的最小型(模)具厚度,也不得大于所给定的最大型(模)具厚度,H设应满足如下条件Hmin+10mm≤ H 设≤ Hmax-10mm式中H 设—所设计的型(模)具厚度(mm);Hmin—压铸件所给定的型(模)具最小厚度,即“模薄”(mm);Hmax—压铸机所给定的型(模)具最大厚度,即“模厚”(mm)。
②压铸机开型(模)后,应使压铸机动型(模)座板行程(L)即压铸型(模)具分型面之间的距离大于或等于能取出铸件的最小距离。
L≥L 取如图1所示为推杆推出的压铸型(模)取出铸件的最小距离。
L取≥L 芯+L 件+K式中,K 一般取10mm。
三、压铸机选用方法举例例已知一盒形铸件,如图2所示。
下面以力劲机械厂有限公司生产的卧式冷室压铸机机型技术参数为依据进行选型分析。
产品压铸机吨位选择标准
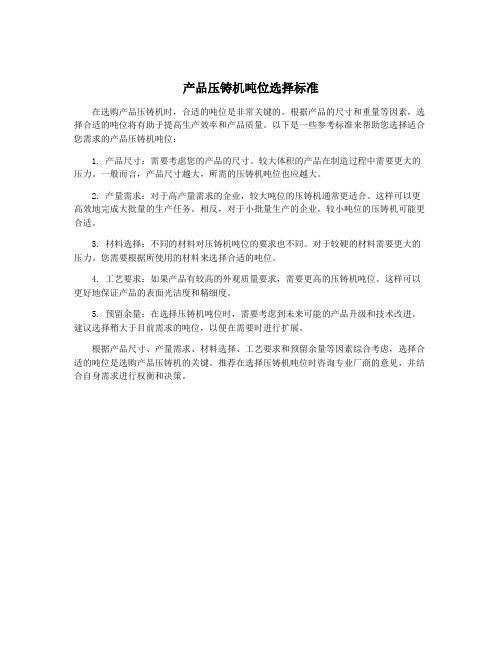
产品压铸机吨位选择标准
在选购产品压铸机时,合适的吨位是非常关键的。
根据产品的尺寸和重量等因素,选择合适的吨位将有助于提高生产效率和产品质量。
以下是一些参考标准来帮助您选择适合您需求的产品压铸机吨位:
1. 产品尺寸:需要考虑您的产品的尺寸。
较大体积的产品在制造过程中需要更大的压力。
一般而言,产品尺寸越大,所需的压铸机吨位也应越大。
2. 产量需求:对于高产量需求的企业,较大吨位的压铸机通常更适合。
这样可以更高效地完成大批量的生产任务。
相反,对于小批量生产的企业,较小吨位的压铸机可能更合适。
3. 材料选择:不同的材料对压铸机吨位的要求也不同。
对于较硬的材料需要更大的压力。
您需要根据所使用的材料来选择合适的吨位。
4. 工艺要求:如果产品有较高的外观质量要求,需要更高的压铸机吨位。
这样可以更好地保证产品的表面光洁度和精细度。
5. 预留余量:在选择压铸机吨位时,需要考虑到未来可能的产品升级和技术改进。
建议选择稍大于目前需求的吨位,以便在需要时进行扩展。
根据产品尺寸、产量需求、材料选择、工艺要求和预留余量等因素综合考虑,选择合适的吨位是选购产品压铸机的关键。
推荐在选择压铸机吨位时咨询专业厂商的意见,并结合自身需求进行权衡和决策。
压铸机吨位的选用方法

压铸机吨位的选用方法压铸机吨位的选用方法在压铸产品报价初期和压铸模具设计时均涉及到压铸机吨位的选择吨位的选用依据下面三个步骤:一,校验锁模力a.总投影面积A=铸件投影面积A1+浇道面积A2(0.15~0.3A1)+排溢系统A3(0.1~0.2A1)+料柄面积A4(3.14xdxd d为料室直径,亦既为冲头直径)b.胀型力F1=总投影面积Ax压射比压(MPa) 所谓压射比压即为单位面积上所承受的压力,根据经验:一般件30~50 承载件50~80 耐气密件80~100c.锁模力F2=胀型力F1/K K为保险系数:0.85 初选压铸机吨位二,校验充满度a.总重量=铸件重量+浇道重量+料柄重量+排溢系统重量各个部分的投影面积已有,算其深度,则知其体积b.充满度=总重量/浇铸量浇铸量为不同的压铸机使用不同的料室时的最大合金重量根据充满度值校验初选压铸机吨位,通常充满度在40%~75%之间三,校验模具尺寸a.对铸件进行简单的模具排位,知其模具尺寸b.根据模具尺寸校验所选压铸机的哥林柱内距是否合适最后确定使用压铸机的吨位按目前国内发展分类:500T以下属小型1300T---600T属中型2800T---800属大型目前国内已制造出4000吨特大压铸机,以后可能出现5000吨。
以上是凭个人经验。
注:T 代表吨平常说的多少吨的压铸机即是指压铸机的锁模力是多少吨,比如400吨即4000KN的力。
谢谢!压铸机和模具常用语(中英文对照)冷/热室压铸机cold/hot chamber pressure die-casting machine司筒shot sleeve鎚头piston料壶melting pot sleeve射咀nozzle流道/浇口runner/gate直浇道sprue浇道套sprue bush鹅颈gooseneck压射缸injection cylinder压射冲头injection plunger钢呤steel piston ring排气vent中央熔炉center furnace熔化金属molten metal注料口filling port顶针ejector pin顶针痕 ejector pad哥林柱/导柱tie bar前(定)机板/后(动)机板 machine platen (moving/fixed)前(定)模/后(动)模 cover die half(stationary half)/ ejector die half (moveable half)冷却水通道water cooling channel样板模prototype die生产模production die成套模 unit die组合模sectional die冲模trim die模胚/模肉standardized main die frame/ replaceable cavity units 行位/柯(型芯) core slides/core镶件casting insert模具钢热处理 die steel heatment模具排位图 die layout夹具jig/fixture模具寿命 die life浇注系统gating/running system浇注系统设计design of gating system铸件凝固数值模拟numerical simulation of casting solidification铸件工艺计算机辅助设计computer-aided design (CAD) of the casting process浇口杯pouring cup芯头斜度 core taper直浇道spure直浇道窝sprue base横浇道runner内浇道ingate冒口riser/feeder head留型时间/开型时间opening time抽芯机构core puller溢流槽overflow顶针ejector pin垃圾位/余料biscuit /slug锁模力locking force模板尺寸size of die platen回炉料foundry returns废金属料scrap熔/炉渣slag沉/浮渣sludge/dross重熔remelting哥林柱间距/直径space between tie bars/tie bar diameter 开模行位die stroke最大/最小压模厚度maximum/minimum die height 干燥周期dry cycle射料力injection force压射位置shot position压射行程injection stroke鎚头直径plunger diameter坩埚容积melting pot专用射料压力specific injection pressure最大压铸面积casting area射料量casting weight顶出力ejector force顶出行程ejector stroke最大压力clamp force max.夹具行程clamp stroke工作压力normal pressure液压系统工作液体gydraulic fluid油箱容积oil tank capacity泵流量/型号pump capacity/type蓄压器型号accumulator type氮气压力nitrogen pressure燃烧装置burning units煤气炉gas furnace燃气炉型号burner type最大输入量Max. input电流强度current电压voltage马达型号/功率motor type/capacity。
铝压铸吨位

铝压铸吨位
摘要:
1.铝压铸吨位的定义和重要性
2.铝压铸吨位的分类和表示方法
3.铝压铸吨位的影响因素
4.铝压铸吨位的选择与应用
5.铝压铸吨位的发展趋势
正文:
铝压铸吨位是指在铝压铸过程中,压铸机一次压铸所能产生的最大压力。
它是压铸机性能的重要指标,直接影响到压铸件的尺寸、形状和质量。
铝压铸吨位可分为不同的分类和表示方法,包括按压力、速度和锁模力等。
铝压铸吨位的影响因素主要有以下几个方面:首先,压铸机的结构和设计。
不同类型的压铸机结构和设计会影响到其吨位;其次,压铸机的材料和使用寿命。
高质量的材料和合理的使用寿命可以提高压铸机的吨位;最后,压铸过程的参数设置,如压力、速度和温度等,也会对铝压铸吨位产生影响。
在选择和应用铝压铸吨位时,需要根据压铸件的具体要求和生产条件进行综合考虑。
选择合适的铝压铸吨位可以提高生产效率和产品质量,降低生产成本。
随着铝压铸技术的不断发展,铝压铸吨位也在不断提高。
压铸机吨位的选用方法[高级教资]
![压铸机吨位的选用方法[高级教资]](https://img.taocdn.com/s3/m/cf17c5abf90f76c660371a1f.png)
东岩公司压铸参数选用方法
专业倾力
1
在压铸产品报价初期和压铸模具设计时均涉及到压铸机吨位的选择,吨位的选用依
三,校验模具尺寸
a.对铸件进行简单的模具排位,知其模具尺寸
b最.根后据确模定具使尺用寸压校铸验机所的选吨压位铸机专的业哥倾力林柱内距是否合适
2
为了便于分析压铸工艺参数,下面示出如图1和图2所示的卧式冷室压铸机 压射过程图以及压射曲线图。压射过程按三个阶段进行分析。
第一阶段:由0 -Ⅰ和Ⅰ-Ⅱ两段组成。0 -Ⅰ段是压射冲头以低速运动,封 住浇料口,推动金属液在压射室内平稳上升,使压射室内空气慢慢排出, 并防止金属液从浇口溅出;Ⅰ-Ⅱ段是压射冲头以较快的速度运动,使金属 液充满压射室前端并堆聚在内浇口前沿。
载件50~80 耐气密件80~100
c.锁模力F2=胀型力F1/K
K为保险系数:0.85
初选压铸机吨位
二,校验充满度
a.总重量=铸件重量+浇道重量+料柄重量+排溢系统重量
各个部分的投影面积已有,算其深度,则知其体积
b.充满度=总重量/浇铸量
浇铸量为不同的压铸机使用不同的料室时的最大合金重量
根据充满度值校验初选压铸机吨位,通常充满度在40%~75%之间
第二阶段:Ⅱ-Ⅲ段,压射冲头快速运动阶段,使金属液充满整个型腔与浇 注系统。
第三阶段:Ⅲ-Ⅳ段,压射冲头终压阶段,压射冲头运动基本停止,速度逐 渐降为0。
压铸机的机型及选择方法
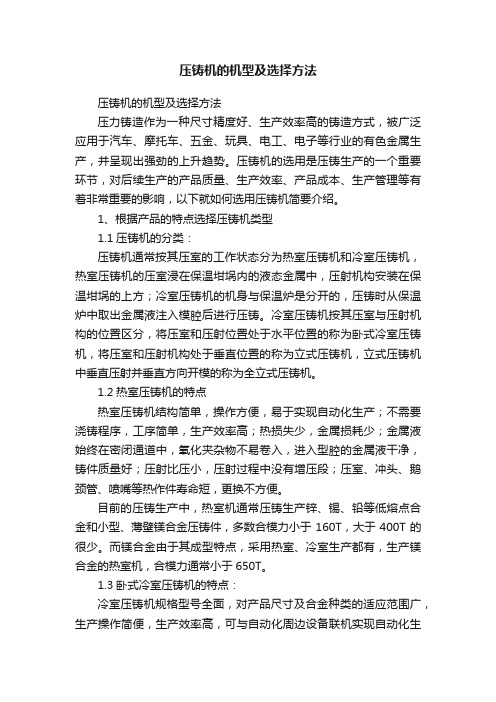
压铸机的机型及选择方法压铸机的机型及选择方法压力铸造作为一种尺寸精度好、生产效率高的铸造方式,被广泛应用于汽车、摩托车、五金、玩具、电工、电子等行业的有色金属生产,并呈现出强劲的上升趋势。
压铸机的选用是压铸生产的一个重要环节,对后续生产的产品质量、生产效率、产品成本、生产管理等有着非常重要的影响,以下就如何选用压铸机简要介绍。
1、根据产品的特点选择压铸机类型1.1压铸机的分类:压铸机通常按其压室的工作状态分为热室压铸机和冷室压铸机,热室压铸机的压室浸在保温坩埚内的液态金属中,压射机构安装在保温坩埚的上方;冷室压铸机的机身与保温炉是分开的,压铸时从保温炉中取出金属液注入模腔后进行压铸。
冷室压铸机按其压室与压射机构的位置区分,将压室和压射位置处于水平位置的称为卧式冷室压铸机,将压室和压射机构处于垂直位置的称为立式压铸机,立式压铸机中垂直压射并垂直方向开模的称为全立式压铸机。
1.2热室压铸机的特点热室压铸机结构简单,操作方便,易于实现自动化生产;不需要浇铸程序,工序简单,生产效率高;热损失少,金属损耗少;金属液始终在密闭通道中,氧化夹杂物不易卷入,进入型腔的金属液干净,铸件质量好;压射比压小,压射过程中没有增压段;压室、冲头、鹅颈管、喷嘴等热作件寿命短,更换不方便。
目前的压铸生产中,热室机通常压铸生产锌、锡、铅等低熔点合金和小型、薄壁镁合金压铸件,多数合模力小于160T,大于400T的很少。
而镁合金由于其成型特点,采用热室、冷室生产都有,生产镁合金的热室机,合模力通常小于650T。
1.3卧式冷室压铸机的特点:冷室压铸机规格型号全面,对产品尺寸及合金种类的适应范围广,生产操作简便,生产效率高,可与自动化周边设备联机实现自动化生产,压射行程的分段控制、调节容易实现,对不同要求的压铸件工艺的满足性好。
缺点是压射过程金属液热量损失大,金属液与空气接触,容易卷入氧化夹杂物及空气,对高致密度或要求热处理的产品须采取特殊的工艺。
- 1、下载文档前请自行甄别文档内容的完整性,平台不提供额外的编辑、内容补充、找答案等附加服务。
- 2、"仅部分预览"的文档,不可在线预览部分如存在完整性等问题,可反馈申请退款(可完整预览的文档不适用该条件!)。
- 3、如文档侵犯您的权益,请联系客服反馈,我们会尽快为您处理(人工客服工作时间:9:00-18:30)。
据下面三个步骤:
一,校验锁模力
a.总投影面积A=铸件投影面积A1+浇道面积A2(0.15~0.3A1)+排溢系统A3
(0.1~0.2A1)+料柄面积A4(3.14xdxd d为料室直径,亦既为冲头直径)
b.充满度=总重量/浇铸量
浇铸量为不同的压铸机使用不同的料室时的最大合金重量
根据充满度值校验初选压铸机吨位,通常充满度在40%~75%之间
三,校验模具尺寸
a.对铸件进行简单的模具排位,知其模具尺寸
b最.根后据确模定具使尺用寸压校铸验机所的选吨压位铸机专的业哥倾力林柱内距是否合适
2
为了便于分析压铸工艺参数,下面示出如图1和图2所示的卧式冷室压铸机 压射过程图以及压射曲线图。压射过程按三个阶段进行分析。
专业倾力
5
F主=APb/10
式中 F主-主胀型力(KN);
A-铸件在分型面上的投影面积(cm2);
Pb-压射比压(MPa)。
分胀型力(F分)的大小是作用在斜销抽芯、斜滑块抽芯、液压抽芯锁紧面上的分 力引起的胀型力之和。
(4)锁型(模)力 锁型(模)力是表示压铸机的大小的最基本参数,其作用是克 服压铸填充时的胀型力。在压铸机生产中应保证型(模)具在胀型力的作用下不致 胀开。压铸机的锁型(模)力必须大于胀型力才是可靠的,锁型(模)力和胀型力 的关系如下:
固过程中,氢析出形成气孔。
氢的来源:
1) 大气中水蒸气,金属液从潮湿空气中吸氢。 2) 原材料本身含氢量,合金锭表面潮湿,回炉料脏,油污。 3) 工具、熔剂潮湿。
专业倾力
8
(3)压铸过程产生气体分析 由于压室、浇注系统、型腔均与大气相通,而金属液是以高压、高速充填,如 果不能实现有序、平稳的流动状态,金属液产生涡流,会把气体卷进去。 压铸工艺制定需考虑以下问题: 1) 金属液在浇注系统内能否干净、平稳地流动,不会产生分离和涡流。 2) 有没有尖角区或死亡区存在 3) 浇注系统是否有截面积的变化? 4) 排气槽、溢流槽位置是否正确?是否够大?是否会被堵住?气体能否有效、 顺畅排出?
应用计算机模拟充填过程,就是为了分析以上现象,以作判断来选择合理的工艺 参数。
专业倾力
9
(4)涂料产生气体分析 涂料性能:如发气量大对铸件气孔率有直接影响。
喷涂工艺:使用量过多,造成气体挥发量大,冲头润滑剂太多,或被烧焦,都 是气体的来源。 (5)解决压铸件气孔的办法 先分析出是什么原因导致的气孔,再来取相应的措施。 1) 干燥、干净的合金料。 2) 控制熔炼温度,避免过热,进行除气处理。 3) 合理选择压铸工艺参数,特别是压射速度。调整高速切换起点。 4) 顺序填充有利于型腔气体排出,直浇道和横浇道有足够的长度(>50mm), 以利于合金液平稳流动和气体有机会排出。可改变浇口厚度、浇口方向、在形 成气孔的位置设置溢流槽、排气槽。溢流品截面积总和不能小于内浇口截面积 总和的60%,否则排渣效果差。 5) 选择性能好的涂料及控制喷涂量。
F锁 ≥K(F主 +F分)
式中 F锁--压铸机应有的锁型(模)力(KN);
K--安全系数,一般取1.25;
F主--主胀型力(KN);
F分--分胀型力(KN)。
在压铸生产过程中,锁型(模)力大小的选择直接反映到压铸分型面处有否料液飞
溅、铸件内组织的密度、有否气孔、成形是否完整、有否飞边及毛刺等。调整时,
气孔特征。有光滑的表面,形状是圆形或椭圆形。表现形式可以在铸件表面、或 皮下针孔、也可能在铸件内部。
(1)气体来源 1) 合金液析出气体—a与原材料有关
b与熔炼工艺有关 2) 压铸过程中卷入气体—a与压铸工艺参数有关
b与模具结构有关 3) 脱模剂分解产生气体—a与涂料本身特性有关
b与喷涂工艺有关 (2)原材料及熔炼过程产生气体分析 铝液中的气体主要是氢,约占了气体总量的85%。 熔炼温度越高,氢在铝液中溶解度越高,但在固态铝中溶解度非常低,因此在凝
专业倾力
4
(2)比压 比压可分为压射比压和增压比压。 在压射运动过程中0-Ⅲ段,压射室内金属液单位面积上所受的压射力称为压射比 压;在Ⅲ-Ⅳ段,压射室内金属液单位面积上所受的增压压射力称为增压比压。比 压是确保铸件质量的重要参数之一,推荐选用的增压比压如下表所示。
增压比压选用值(单位:MPa)
3)胀型力 压铸过程中,充填型腔的金属液将压射活塞的比压传递至型(模)具型 腔壁面上的力称为胀型力。主胀型力的大小等于铸件在分型面上的投影面积(多腔 模则为各腔投影面积之和),浇注系统、溢流、排气系统的面积(一般取总面积的 30%)乘以比压,其计算公式如下
b.胀型力F1=总投影面积Ax压射比压(MPa)
所谓压射比压即为单位面积上所承受的压力,根据经验:一般件30~50 承
载件50~80 耐气密件80~100
c.锁模力F2=胀型力F1/K
K为保险系数:0.85
初选压铸机吨位
二,校验充满度
a.总重量=铸件重量+浇道重量+料柄重量+排溢系统重量
各个部分的投影面积已有,算其深度,则知其体积
在保证铸件合格的前提下尽量减小锁专型业(倾模力)力。
6
为简化选用压铸机时各参数的计算,可根据压铸机具体的工作性能作出“比压、投 影面积与胀型力关系图”,参见下图。在已知型(模)具分型面上铸件总投影面积 ∑A和所选用的压射比压Pb后,能从图中直接查出胀型力。
专业倾力
7
压铸件缺陷中,出现最多的是气孔。
第三阶段:Ⅲ-Ⅳ段,压射冲头终压阶段,压射冲头运动基本停止,速度逐 渐降为0。
卧式冷室压铸机压射过程图
专业倾力
3
卧式冷室压铸机压射曲线图 s--冲头位移曲线 P0--压力曲线 v--速度曲线
1、压力参数
(1)压射力 压射冲头在0-Ⅰ段,压射力是为了克服压射室与压射冲头和液 压缸与活塞之间的摩擦阻力;Ⅰ-Ⅱ段,压射力上升,产生第一个压力峰,足 以能达到突破内浇口阻力为止;Ⅱ-Ⅲ段,压射力继续上升,产生第二个压力 峰;Ⅲ-Ⅳ段,压射力作用于正在凝固的金属液上,使之压实,此阶段有增压 机构才能实现,此阶段压射力也叫增压压射力。
第一阶段:由0 -Ⅰ和Ⅰ-Ⅱ两段组成。0 -Ⅰ段是压射冲头以低速运动,封 住浇料口,推动金属液在压射室内平稳上升,使压射室内空气慢慢排出, 并防止金属液从浇口溅出;Ⅰ-Ⅱ段是压射冲头以较快的速度运动,使金属 液充满压射室前端并堆聚在内浇口前沿。
第二阶段:Ⅱ-Ⅲ段,压射冲头快速运动阶段,使金属液充满整个型腔与浇 注系统。