线路板可靠性与微切片
白蓉生《电路板微切片手册》2

图4 上左100X图中可见到镀铜孔壁与铜箔孔环之间的拉离,完全是出自两次电镀铜本身的内应力,超过对铜箔孔环侧缘之附著力所致,由于尚未进行漂锡,故与热应力无关。
上右200X之正片法镀厚铜孔壁,也由于本身内应力超过对铜环的附著力,而逐步拉离的情形(两图观察前均出现微蚀过度)。
图5 上左500X图示热应力后其铜壁与孔环之间并未完全拉开,而局部拉开所隆起的部分还造成整体铜壁的轻微突出,此罕见之异常现象非常珍贵。
上右为100X漂锡孔在强大热应力的拉扯下,使一铜与二铜之间发生轻微的分离。
IPC-6012在表3-7中指出Class 2与Class 3板类,不能允收此种分离。
图6 上左1000X画面之漂锡孔,转角处之一次镀铜已被拉断,但二次铜则完好如初,也属一种"部分后分离"。
上右200X之漂锡孔,其环与壁互连处似乎已发生后分离,但从背光仔细观察时似乎又未全离。
前图5则恰好切到这种现象。
好奇之下在相同样板上又进行水平切片,以找出更多局部分离的证据。
图7 从许多水平切孔中找到一个样孔可证明上述说法,上左50X"孔环十字桥"(Thernal Pad)之全景,该PTH 是以十字桥与外面大铜面相通,四块无铜的基材区即为预防过度膨胀的"伸缩缝"。
此样左上方图8 孔铜制程后分离的例子很多,有的提早到镀完铜或半镀即呈现"微分",再续镀之下即成了真正的"分离"(开始不久即分离者会形成揩镀)。
上左图为100X,右图为200X之精采水平切片,可看到孔壁自孔环上出现图9 左200X为漂锡试验后"互连分离"之另一实例,不但环壁之间产生沟分,而且连内环黑化皮膜处与铜孔壁上亦均出现"树脂缩陷",热应力之大可见一斑。
右为1000X之环壁分离,其间的虚空不容掩饰,但也并不表示全壁整环已空,也不表示电性断路,只是逮到时就不免挂上问号而已。
PCB分析及相关标准
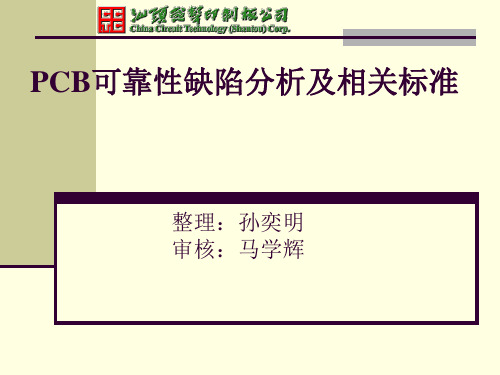
32
六、电镀
4)叠镀
原因:
1)孔壁粗糙度太大. 2)沉铜效果不好,没有将 孔壁覆盖完全. 3)电镀缸光剂/整平剂比例 失调. 4)电镀缸氯离子浓度过高. 5)电镀参数设定不当 标准:不允许
33
六、电镀
5)电镀杂物
原因:槽液中各种浮游固体粒子常会著落而成镀瘤
标准:不允许
34
六、电镀
孤立的厚或薄截面不应用于平均;
由于玻璃纤维突出引起孤立的铜厚度减薄 ,从突出末端量至孔壁时, 应符 合最小厚度要求;
如在孤立区域发现铜厚度规定的最小厚度要求 , 应作为一个空洞并从同一
检查批中重新抽样
31
六、电镀
3)深镀能力不足:
现象:孔口出现狗骨现象; 原因:光剂与整平剂不匹配; 测试方法:
9)芯吸:
原因:钻孔动作进给速度过大,或钻嘴破损不够锋利以致拉松
拉大玻织纱束;或本身B片纤维束有缺口,过于疏松;过度除钻 污使玻织纱束的树脂被溶掉而造成; 标准:对于芯吸作用(B)没有减少导线间距使之小于采购文件规 定的最小值
,芯吸作用(A)没有超过80mm[3.150min]
19
四、激光钻孔
11
三、机械钻孔
3)内层环宽:
原因:钻偏或内层涨缩与钻孔补偿不匹配; 标准:最小的环宽≥0.025mm 或满足客户要求
12
三、机械钻孔
4)内层隔离环宽
原因:钻偏或内层涨缩与钻孔补偿不匹配; 标准:最小的隔离环宽≥0.1mm
13
三、机械钻孔
5)内层焊盘脱落
原因:内层焊盘比较小,钻孔时被拉脱;(此问题在公司第
标准
2级 3级
盲孔 铜(平均最小)
最薄区域 铜(平均最小) 最薄区域
切片分析

切片分析目的:电路板品质的好坏、问题的发生与解决、制程改进的评估,在都需要切片做为客观检查、研究与判断的根据。
切片质量的好坏,对结果的判定影响很大。
切片分析主要用于检查PCB内部走线厚度、层数,通孔孔径大小,通孔质量观察,用于检查PCBA 焊点内部空洞,界面结合状况,润湿质量评价等等。
切片分析是进行PCB/PCBA失效分析的重要技术,切片质量将直接影响失效部位确认的准确性。
切片步骤:取样(Samplc culling)→封胶(Resin Encapsulation)→研磨(Crinding)→抛光(Poish)→微蚀(Microetch)→观察(Inspect)依据标准:制样:IPC TM 650 2.1.1,评判:IPC A 600, IPC A 610典型图片:表面贴装焊点切片图片BGA焊点切片图片通孔上锡质量切片图片PCB铜层质量切片图片链接:一、通孔焊接切片分析二、表面贴装焊接切片分析三、PCB产品切片分析四、PCB/PCBA失效分析切片方法链接一:通孔焊接切片分析通孔切片分析典型图片:R21200X200X50X50X20X信号脚接地脚20X链接二:表面贴装焊接切片分析● 实例1:BGA 焊点切片观察空洞、裂纹及未焊接现象BGA 焊点照片BGA 焊点失效照片CPU 焊点照片● 实例2:PTH/芯片引脚上锡量检查PTH 焊点切片图片外L 型引脚切片图片翼型引脚切片图片● 实例3:电容失效切片观察电容切片图片● 实例4:LED 邦定点切片表面形貌LED邦定点切片图片Bonding 点未键合链接三:PCB产品切片分析典型图片50X 100X 200X 200X通孔切片图片绿油基材绿油层厚度切片测试图片(200X)板面铜箔厚度切片测试图片(200X )链接四:PCB/PCBA 失效分析切片方法典型图片:通孔上锡不良焊点焊接不良LED 焊点失效切片图片基 材铜 层Bonding 线开裂发光层开裂爆板切片图片。
PCB印制电路板电镀层质量切片测试方法

PCB印制电路板电镀层质量切片测试方法印制电路板(PCB)的电镀层质量是保证电路板性能和可靠性的关键因素之一、切片测试是一种常用的方法,用于评估电镀层的质量。
下面将介绍PCB电镀层质量切片测试方法。
1.切片测试的准备工作在进行切片测试之前,首先需要准备一块需要测试的PCB板。
确保该PCB板是从生产中随机选取的,以代表批量生产的质量水平。
同时,根据需要选择要测试的电镀层(如镀铜层、镀锡层等)。
2.制备切片样品将选取的PCB板切割成适当尺寸的样品,通常为20mm×20mm大小。
使用金刚石锯片或高速切割机进行切割,确保切口垂直于电镀层表面。
3.打磨和抛光使用打磨机和抛光机对样品进行打磨和抛光,以消除切割引入的划痕和表面不平整。
首先使用粗砂纸或磨粉进行初步打磨,然后逐渐使用细砂纸和磨粉进行多次打磨和抛光,直到达到所需的光洁度。
4.金相显微镜观察使用金相显微镜对抛光后的样品进行观察。
首先将样品放在显微镜台上,并调整焦距和照明条件,以获取清晰的显微图像。
然后使用不同倍率的目镜和物镜进行观察,以获取不同放大倍数的图像。
5.图像分析通过对金相显微镜观察的图像进行分析,可以评估电镀层的质量。
主要关注以下几个方面的特征:-镀层厚度:通过测量不同部位电镀层的厚度,可以评估电镀层的均匀性和一致性。
使用显微镜配合图像分析软件进行测量。
-结晶结构:观察电镀层中的晶粒结构,可以评估电镀层的结晶性和致密性。
无杂质、均匀细小的晶粒结构表示较高质量的电镀层。
-欠镀和过镀:观察电镀层是否存在部分区域过度或不足的电镀现象。
欠镀可能导致接触不良,而过镀则可能导致导电问题。
-结合强度:评估电镀层与基板之间的结合强度。
通过观察是否存在脱落、剥离或开裂现象,判断结合强度是否符合要求。
-杂质和缺陷:观察电镀层中是否存在杂质、气泡、裂纹等缺陷。
这些缺陷可能会影响电镀层的性能和可靠性。
6.结果分析和评估根据图像分析结果,对电镀层的质量进行评估。
微切片手册

第二部分:切片的制作程序
&研磨:
1.打开研磨机电源,并调节转速钮 2.在研磨过程中需加入适当之水量帮助研磨。 3.用150目砂纸,将观察孔研磨至孔邊。 4.用600目砂纸,将观察孔研磨至约1/4处。 5.用1200目砂纸,将观察孔研磨至约1/3处。 6.用2000目砂纸,将观察孔研磨至约1/2处。 7.研磨方向应与切片成45角,并不断以90旋转,以确保切片表面完全 研磨。 8.研磨时用力应均匀,防止磨偏。禁止用力过度,导致切片与压克力 胶分裂。 9.在接近孔中心时,应注意防止过磨,检查有无喇叭孔、磨偏及研磨不 够等缺陷
第四部分:導同孔常見異常及允收標准 &.除胶渣不良
圖示一 圖示二 不允收/钻孔时钻针与板材强力摩擦所产生的温度甚高,故所累积的热量常使得 孔壁瞬间温度高达200℃以上,如此一来不免使得部份树脂被软化而成为胶糊, 随着钻针的旋转而涂满孔壁,各内孔环的內層铜面也自不能幸免,冷却后变成胶 渣導致PTH后殘膠不能除盡
自動取樣機
手動取樣機
第二部分:切片的制作程序 &封胶:
1.将沖切下來的切片试样用吹风机吹干,并卡于灌胶模内(或以双面胶将 切片研磨边固定于塑料灌胶模内),竖直固定。 2.将压克力粉与硬化剂(约1:1)调和均匀,缓慢注入灌胶模,并检视无气 泡后,自然固化约15分钟。 注意事项: 1.若切片孔内存有气泡,则用棉花棒沿切片边缘来回移动,直至赶出气 泡为止。 2.固化时间必须充足,否则研磨时,会导致切片与压克力胶分裂。
B
第七部分:切孔的判讀
項目 允收規格及說明 圖片說明
粗糙度
≦1.2mil
回蝕
0.2-3 mil
第七部分:切孔的判讀
項目 允收規格及說明 圖片說明
PCB微切片

明视200X之斜 切片
暗视200X之斜 切片
三、制作技巧
微切片需填胶抛光与微蚀,才能看清各种真实品质.以下为 制作过程的重点:
1、取 样(Sample culling)
剥膜及蚀刻后尚未熔锡之画面,其二铜与锡铅之横 向扩镀
网印负片法熔锡后的切片
由圖可以看出二铜镀得特别厚,不但超越 油墨而且还侧爬颇远 ,孔环外缘截面呈现缺口
2、干 膜 阻 剂
此200X画面的油墨阻剂(如同墙壁)出现 异常,致使二次铜一开始往墙外恻向伸出, 有了镀铜层在非导体表面建立基地,锡铅镀 层当然就毫不客气顺理成章的成长,其结果 不免造成板子的报废。
各种直接电镀法),即全板镀铜直到完成孔壁铜厚之要求随即以 干膜进行盖孔式(Tenting)的影像转移,再直接蚀刻 .
4.1.2孔銅完整情形 1.銅瘤
是否有銅瘤(Nodule)夾雜物(Inclusion)孔口之階梯式鍍層 (Step plating)及銅層結晶情形.
一銅鍍銅不均形 成的铜瘤
鑽孔毛刺造成,鍍一銅時, 形成的瘤狀
膠渣會影響孔环与铜壁的互连 IPC-6012对此明文规定:过份除胶渣所造成的回蚀深度的不可超
过1mil。
内层孔环与孔壁之间有未除尽的残余胶渣
镀上的铜壁又被拉开的情形
一面镀一面不断被拉开的情形
重铬酸过镀除胶渣造成孔 壁表面的树脂全部溶出, 其缩陷造成断点整齐的玻 纤束突出
除膠渣良好圖片
未做除胶渣的双面板孔铜壁 经喷锡后退即出现了罕见的 严重拉离(Pull Away)
二、分类
电路板解剖式的破坏性微切法,大体上可分为三类: 1、 微 切 片
浅析PCB线路各种缺陷及切片观察

浅析PCB线路各种缺陷及切片观察PCB线路是电子产品中非常重要的组成部分,它连接了各个电子元件,传递电信号和电能。
然而,在PCB线路制造过程中,往往会出现各种缺陷,这些缺陷会影响电路的性能,甚至导致故障。
本文将对几种常见的PCB线路缺陷进行浅析,并介绍如何通过切片观察来判断线路的质量。
1.走线缺陷:走线缺陷是指PCB线路板上电信号走线存在问题。
常见的走线缺陷包括走线间距不合适、走线过窄、走线断裂等。
这些问题都会导致电路的可靠性降低,信号传输效果不理想。
可以通过切片观察走线的质量以及是否存在缺陷。
2.焊盘缺陷:焊盘是连接电子元件和PCB线路板的关键部分,它们直接影响元件和线路板之间的连接质量。
常见的焊盘缺陷包括焊盘孔径不合适、焊盘冷焊、焊盘开裂等。
通过切片观察焊盘的质量,可以判断焊盘是否存在缺陷,并及时采取措施修复。
3.绝缘层缺陷:绝缘层是PCB线路板上各个线路之间的隔离层,防止线路之间短路发生。
绝缘层缺陷可能导致线路之间的电路短路,造成电路故障。
通过切片观察绝缘层的厚度、均匀性,以及是否存在气泡、裂纹等缺陷,可以判断绝缘层的质量。
4.阻抗不匹配:PCB线路上的信号传输需要符合一定的阻抗匹配要求,以保证信号传输的质量。
当连接线路的阻抗不匹配时,会引起信号反射、衰减等问题。
切片观察可以通过测量线路的宽度和距离来判断阻抗是否匹配。
在切片观察PCB线路时,可以使用显微镜等仪器来观察和测试PCB线路的质量。
首先,将PCB线路切片,然后使用显微镜观察切片的表面和内部结构。
可以通过观察线路的走向、良好的焊接、焊盘是否光滑、绝缘层是否均匀、阻抗是否匹配等来判断线路的质量。
总而言之,PCB线路在制造过程中可能会出现各种缺陷,这些缺陷会影响电路的性能和可靠性。
通过切片观察可以及早发现并解决这些问题,提高PCB线路的质量和可靠性。
电路失效分析、可靠性、稳定性测试

随着电子电器行业的不断发展,消费者水平也在不断提升,人们已经不仅仅满足于产品的外观和功能,电子电器产品的可靠性已成为产品质量的重要部分。
RTS.LTD 可靠性测试能帮助电子电器制造企业尽可能地挖掘由设计、制造或机构部件所引发的潜在性问题,在产品投产前寻找改善方法并解决问题点,为产品质量和可靠性做出必要的保证。
失效分析RTS.LTD 可靠性实验室配备了扫描电子显微镜、傅立叶转换红外光谱仪、能谱仪、切片、金相显微镜等精密设备提供失效分析,可进行切片测试、焊点拉伸强度、可焊性测试、镀层厚度测试、锡须观察、成分分析等实验。
气候环境试验RTS.LTD 环境可靠性实验室拥有一批国际、国内著名的专业环境试验设备制造商生产的气候环境试验设备,设备技术先进、性能稳定、功能齐全,可编程控制,自动绘制试验曲线。
测试项目测试范围高温室温~300 ℃低温室温~-70 ℃恒温恒湿20 ℃~ 95 ℃,20 ~ 98%RH低湿 5 ℃~ 95 ℃,5 ~ 98%RH温度/ 湿度循环-70 ℃~ 150 ℃,20 ~ 98%RH冷热冲击-65 ℃~ 150 ℃快速温变-70 ℃~ 150 ℃,25~98%RH ,≦15 ℃/min高压蒸煮105 ℃~ 142.9 ℃, 75~100%RH, 0.020~0.196Mpa盐雾中性盐雾、醋酸盐雾、铜加速醋酸盐雾气体腐蚀SO 2, H 2 S, Cl 2 , NO 2 ,NH 3臭氧测试0---500ppmUV 老化UV exposure UVA340, UVA351,UVB313太阳辐射辐照度:450W/m 2 ----1200W/m 2低气压室温~200 ℃,常压~10kPa防水滴水、摆管淋雨、喷水(IPX0~IPX8 )防尘钢球、铰接试指、金属丝、防尘箱(IP0Y~IP6Y )机械环境实验RTS.LTD 机械环境实验室拥有具有国际先进水平的高频振动实验系统和机械冲击实验系统,100kg 自由跌落实验台等机械环境实验设备。
PCB板可靠性试验(线路板可靠性试验)

斑、起泡及板面 (2).:置于温度288 +/-5℃之锡
或孔内有分层现 炉内 浸锡10 -11秒,共循环三
象。
次.
1.外观检查PP与铜箔无分层, 无裂开、无气泡.
2.显微镜观察无孔裂、断角 、,镀层分离.
新单首次做
1) 锡炉 (2) 烤箱 (3) 切片
冲床 (4) 研磨
机 (5) 显微
镜
NO 信赖性测试项目 试验目的
擦 (3) 异丙
醇
(1). 选取板边至少25.4mm处的
测试线;
8
抗剥离强度试 检验铜箔与基材
验
的结合力.
(2). 用小刀挑起一段不超过 12.7mm的线路;
(3). 用拉力计夹子夹住被挑起
测试线末端;
(4). 测量3次求均值;
(1).H/H铜箔≧6LB/in; (2).1/1铜箔≧8LB/in; (3).2/2铜箔≧10LB/in
铜厚: Min. 0.8 mil;Max.2.0mil; 总面铜 厚:0.5OZ:Min.1.3mil;1OZ:Mi n.2.0mil ;2OZ:Min.3.2mil. 喷锡厚: Min. 0.2 mil、绿油 厚: Min. 0.4 mil; 检验规范 及允收标准:铜厚:薄铜区需满 足最下限的要求,偏厚亦需满 足孔径及板厚的规格要求.无 断角、分层、孔壁分离、焊环
否合适。
间,电压应加在每层导体图形之 间,和每一相邻层的绝缘图形之
间.。 (3).尽可能均匀地将电压从0升 到规定的值,除非另有规定,其速 率约每秒100V(有效值或直流),.
试验结果不可有火花、闪光或 烧焦,无以上异常则判定PASS,
否则判定Fail
依客户要求 (若客户无要求 的则每月随机抽
pcba切片实验原理

pcba切片实验原理PCBA切片实验原理PCBA(Printed Circuit Board Assembly,印刷电路板组装)是指将已经完成印制电路板上的元器件进行焊接组装的过程。
在PCBA 生产过程中,为了确保组装质量和元器件的可靠性,需要进行切片实验。
本文将介绍PCBA切片实验的原理和步骤。
一、PCBA切片实验的目的1. 检测焊接过程中是否存在焊接不良,如焊接短路、焊接开路等问题。
2. 检测元器件与印刷电路板之间的粘合性能,确保元器件在工作环境中不会脱落。
3. 检测PCBA的结构和层间连接是否满足设计要求。
二、PCBA切片实验的原理PCBA切片实验采用横向切片的方式,即将PCBA垂直切割成若干薄片,然后对薄片进行观察和测试。
切片实验主要包括以下几个步骤:1. 样品制备:从生产线上取下一块完整的PCBA板,根据需要选择切片区域。
然后将PCBA板固定在切片机上,以确保切片过程中的稳定性。
2. 切片:将PCBA板放置在切片机上,进行切片操作。
切片机通过旋转刀片的方式,将PCBA板切割成若干薄片。
切片的厚度通常在0.1mm左右,可以根据需要进行调整。
3. 粘合剂处理:将切割好的薄片进行粘合剂处理。
粘合剂主要用于固定薄片的结构,以防止在后续的测试过程中薄片松动或脱落。
4. 观察和测试:将处理好的薄片放置在显微镜下,观察PCBA的内部结构和焊接质量。
同时,可以对薄片进行电学测试,以检测焊接点的电阻和连通性。
5. 结果分析:根据观察和测试的结果,分析PCBA的焊接质量和结构性能。
如果发现焊接不良或结构问题,需要及时进行修复或更换。
三、PCBA切片实验的注意事项1. 切片过程中要确保PCBA板的稳定性,避免切割过程中的震动或位移。
2. 切片的厚度需要根据PCBA的要求进行选择,太薄会导致薄片易碎,太厚则可能无法观察到内部结构。
3. 粘合剂的选择要考虑到与PCBA材料的相容性和粘接强度,以确保粘合效果良好。
PCB可靠性分析

PCB可靠性分析PCB(Printed Circuit Board,印刷电路板)作为电子设备的重要组成部分,其可靠性对产品的性能和寿命具有重要影响。
通过对PCB的可靠性分析,可以帮助我们了解和评估电路板的性能和故障特性,进而优化设计和生产过程,提高产品质量和可靠性。
本文将介绍PCB可靠性分析的相关内容,包括可靠性指标、故障分析方法和提高可靠性的措施等。
一、可靠性指标1. MTBF(Mean Time Between Failures,平均无故障工作时间):指在给定条件下,设备平均无故障工作的时间。
MTBF是衡量设备可靠性的重要指标,可以通过故障数据统计和可靠性预测等方法得到。
2. 故障率(Failure Rate):是指在单位时间内发生故障的频率。
故障率与可靠性相互关联,可以通过故障数据统计和可靠性预测等方法得到。
3.可靠性指标:还包括各种可靠性指标,如可靠性增长、可靠性指标分布等,用于描述和评估设备的可靠性水平。
二、故障分析方法1.故障模式与效应分析(FMEA):通过分析PCB中存在的潜在故障模式和可能的故障效应,确定关键零部件和关键工艺,进而制定相应的预防和控制措施,提高PCB的可靠性。
2.可靠性预测:通过统计故障和失效数据,应用可靠性预测模型,进行可靠性预测和评估。
可靠性预测可以指导产品设计和可靠性改进措施的制定。
3.故障树分析(FTA):通过分析电路板中故障的可能原因和关系,构建故障树,分析故障发生的概率和可能性,找出故障发生的主要原因,并制定相应的改进措施。
4.场效应分析(FMEA):通过局部强氧化和电泳法,研究PCB中微小缺陷的几何形态和电学特性,进而评估缺陷对PCB可靠性的影响。
5.老化试验和可靠性测试:通过在特定环境条件下进行PCB的老化试验和可靠性测试,模拟和加速PCB在使用过程中的老化和故障情况,验证和评估PCB的可靠性。
三、提高可靠性的措施1.合理的设计和布局:包括选择合适的材料、合理布局电路、减少焊点和焊盘数量、避免过度热应力等,从而减少故障的可能性。
浅析PCB两种重要可靠性测试方法

浅析PCB两种重要可靠性测试方法黄世清;张利华【摘要】PCB reliability testing is the most frequent subject the manufacturers and costumers devoted into. Intercenect stress test(IST)and thermal cycle test(TCT)are two of the most polular and effective test methods for evaluating the reliability of PCB in long term application within shot testing time. This paper introduce the test method and standard of IST and TCT, and presentate how to analysis test failures by introducing some study cases the auther have devoted into, and also recommend some improve dicection for IST and TCT failures.%电路板可靠性评估是每个制造厂家、客户研究得最多的课题,互联应力测试及冷热循环测试是现有的在短时间内评估电路板的长期可靠性的有效测试方法。
文章对互联应力测试及冷热循环测试方法及标准进行了详细介绍,并通过简单的实际测试研究案例来介绍如何分析失效并找出失效原因,并提出一些失效原因的改善方向。
【期刊名称】《印制电路信息》【年(卷),期】2014(000)004【总页数】7页(P88-94)【关键词】可靠性;互联应力测试;冷热循环测试【作者】黄世清;张利华【作者单位】深南电路有限公司,广东深圳 518053;深南电路有限公司,广东深圳 518053【正文语种】中文【中图分类】TN411 前言随着电子行业的不断发展,PCB行业对产品的长期可靠性要求越来越重视。
白容生切片分析说明

关于《电路板微切片手册》一、白蓉生教授自序微切片(Microsectioning)技术应用范围很广,电路板只是其中之一。
对多层板品质监视与工程改善,倒是一种花费不多却收获颇大的传统手艺。
不过由于电路板业扩展迅速人材青黄不接,尤其是纯手艺的技术员更是凤毛麟角。
虽然每家公司也都聊备设施安置人员,也都有模样的切磨抛看,然而若就一般判读标准而言,则多半所得到书面的成绩,虽不至惨不忍睹的地步,多也只停留在不知所云的阶段。
考其原因不外:客户内行者太少、老板们不深入也不重视,工程师好高骛远甚少落宝基本。
是以在欠缺教材乏人指导下,当然只有自我摸索闭门造车了。
至于国外同业的水准,经笔者多年用心观察与比较下,除了设备比我们贵与好之外,手艺方面则不仅乏善可陈,而且还颇为优越自大。
甚至IPC贩售录影带中的讲师,也只是西装笔挺振振有词,根本拿不出几张晶莹剔透眉清目秀的宝物彩照,何况是经年累月众多量产的心血结晶。
国外同业在诸多故障方面的累积经验,也远去国内厂商甚多。
持远来和尚会念经的想法,想要从国外引进微切片技者应只是缘木求鱼竹篮打水罢了。
笔者二十五年前进入PCB业,即对动手微切片发生兴趣,每每找到重点再印证于产品改善时,不仅心情雀跃深获成就感外,且种种经验刻骨铭心至今不忘。
如此亲身实地之经验累积,比诸书本当然大有不同在焉。
多年来共集存了二千多张各式微切片原照,特于投老之际仔细选出730张编辑成书,希望为业界后起留下一些可资比较的样本,盼在无师之下而能自通,抛开包袱减少误导。
由于版面有限许多珍贵照片必须裁剪以利编辑,每在下刀之际就有切肤之痛难以割舍,实乃岁月不居件件辛苦得之不易也。
本书除以全彩印刷极高成本之外,每帧照片也都绝对是费时耗力所有赀,放眼全球业界以如此大手笔成书者应属首见。
本书能顺利编辑,须感谢台湾电路公司切片实验室小姐先生们之鼎力协助,若以简易切片方式而言,从广经阅历的笔者看来,台路的几位老手们应列国内之顶尖。
微切片制作及缺陷分析

分层/起泡(Delamination/Blister)
IPC-A-600G对分层/起泡的要求:
允收-2、3级: 无分层或起泡。
拒收-2、3级: 有分层或起泡。
共127页
31
互连后分离
多层板各内层孔环与后来之铜孔壁完成互连后,大功即 告成一半,但这些介面的“互连”(Interconnecting)还要 耐得住后续各种高温考验而不分离才算合格。通常模拟 方法即“288℃十秒钟之漂锡”,称为热应力试验或漂锡 试验(Thermo-Stress Test or Solder Floating Test)。经过此 严苛试验而不出现分离的板件才能允收。IPC-6012只要求 一次漂锡,但部分日本客户却要求连做五次才行 。 按IPC-6012B 3.6.2.1节“镀层完整性”规定,镀覆层的镀 层完整性应符合表3-6所列述的要求。对于2级和3级产品, 不应有镀层分离(除表3-6中注明外)或镀层裂缝,且内层 互连处不应有镀覆孔孔壁与内层间的分离或污染。
共127页
16
IPC-A-600F对孔壁粗糙的要求
允收-1、2、3级
拒收-1、2、3级 粗糙或节瘤已使镀层厚度或 孔径减少到低于最小的规定 要求。
粗糙或节瘤没有使镀层厚度 或孔径减少到低于最小的规 定要求。
共127页
17
孔壁粗糙
过度去钻污造成的孔壁 粗糙。
轻微的撞破。
钻孔的机械挖破(Gouging)与过度除钻污(De-smear)所造成 的孔壁粗糙,两者从不清楚的切片上有时是很难分辨的 。
共127页 11
图电前后判读标准
共127页
12
孔无铜
特点:孔口边缘断
铜,断铜面较整齐;
原因:基本可断定
PCB可靠性分析

PCB可靠性分析PCB(印刷电路板)的可靠性分析是指评估和预测PCB在使用过程中的性能和寿命。
因为PCB是电子器件的关键组成部分,其可靠性对于整个电子系统的正常运行至关重要。
首先,PCB设计是影响其可靠性的关键因素之一、在设计过程中,需要考虑电路的布局、布线的合理性、电源和地线的设计、信号完整性、EMC(电磁兼容性)和ESD(电气静电放电)等因素。
通过使用CAD软件来模拟和分析电路板的布局和布线,可以提前预测和解决潜在的问题,从而提高PCB的可靠性。
其次,材料选择也是影响PCB可靠性的重要因素。
选择适用的基板材料、有良好热传导性能的铜箔、可靠的封装材料等等对于提高PCB的可靠性至关重要。
材料的优良特性可以降低PCB的损耗、提高整个电路的工作效率和稳定性。
制造过程中的工艺控制也是确保PCB可靠性的重要环节。
例如,PCB 的裂纹、焊点的质量、表面镀层的粘附力等缺陷都可能影响其可靠性。
因此,在制造过程中,需要进行严格的质量控制,包括使用先进的设备和工艺,确保每个工艺步骤的良好执行,以减少制造缺陷。
最后,对于已制造的PCB,需要进行可靠性测试。
可靠性测试是评估PCB在不同环境条件下的可靠性和稳定性的重要手段。
通过对PCB进行加速老化测试、温度循环测试、振动测试、湿度测试等,可以模拟实际使用条件下的PCB的可靠性表现。
在进行可靠性分析时,应该综合考虑上述因素,并结合产品的实际应用环境和使用条件来评估和预测PCB的可靠性。
通过合理的设计、优质的材料、良好的制造工艺和可靠性测试,可以提高PCB的可靠性,从而确保电子系统的正常运行。
总之,PCB可靠性分析是确保电子产品正常工作的重要环节。
通过综合考虑设计、材料、制造和测试等因素,可以提前发现和解决潜在的问题,从而提高PCB的可靠性,确保整个电子系统的可靠工作。
微切片讲解

2、 封 胶(Resin Encapsulation) 封胶之目的是为夹紧检体减少变形,系采用适宜的树脂类将通孔灌满 及将板样封牢。把要观察的孔壁与板材予以夹紧固定,使在削磨过程中 其铜层不致被拖拉延伸而失真 (封膠形式有很多種,本廠是购买现成的 压克力成型模塊,将待檢切片固定在模塊槽中灌入冷凝胶封膠。)
5、机 械 外 力 效 果
上三图均为电性测试时,发现断路(Continuity Failure 或Open)时,再去 做切片发现是因镀锡铅不良而于蚀刻时被咬断的孔。这种不通的孔常会多测 一两次,以致孔口出现被探针所顶挤变形的样,电测机所施加压力的影响可 见一般
上三图均为V-Cut之圖片。左邊上下切口对齐度较好,中間稍歪,右图未對齊 且上下切口深度不同(欧洲客户尤其是德国客戶十分在意V-Cut對準度)
过度钉头几乎一定会出现较大的挖破,出自钻 孔的纵向玻璃纱束之挖破,除与钻针尖部的"刃 角"损耗有密切关系外,也与钻针的偏转(Run Out)或摇摆(Wobble)有关
过度除胶引起的孔壁 粗糙度
轻微的撞破引起的孔 壁粗糙度及釘頭
由于玻织纱束中的破洞造成 的孔壁粗糙度
画面右边的黑洞及中央的断层,由于落差太大连化学铜与一次铜都镀不上, 可见粗糙之严重性。这种由于玻织布中断纱太多而不良的基材板,进而又造 成孔壁的粗糙,並不是鑽孔造成的粗糙度
本廠的孔壁粗糙度的允收標準為:
鑽孔粗糙度<1200U” 電鍍孔壁粗糙度<1500U”
互连后分离
多层板各内层孔环与后来之铜孔壁完成互连后(Interconnecting)还要耐得住 后续各种高温考验而不分离才算合格,通常模拟方法即“288°C十秒钟之漂锡” 即热应力试验或漂锡试验(Thermo-Stress Test or Solder Floating Test), 美式规范(如IPC-6012或MIL-P-5511OE)都只要求一次漂锡,但部分日商客户 却要连做五次才行 IPC-6012 中規定通孔热应力漂锡后各内环与孔壁之互连 处不可分离 产生后分离的原因主要是内层孔环之侧面,在化学铜或直接电镀之前, 就可能存在氧化物或钝化物皮膜,使得二者附著力不够牢靠所致
pcba切片标准

pcba切片标准PCBA(Printed Circuit Board Assembly,印刷电路板组装)是指将元器件焊接到印刷电路板上的过程。
在PCBA制造过程中,切片是一个重要的环节。
PCBA切片标准是制定了对PCBA切片的要求和规范,确保切片质量和工艺稳定性。
本文将介绍PCBA切片标准的主要内容和作用。
PCBA切片标准的主要内容如下:1. 尺寸标准:PCBA切片的尺寸标准主要涉及长、宽、厚度、及边缘的要求。
切片尺寸必须与设计要求相符,以确保PCBA在安装后能够正确适配。
2. 表面平整度:切片的表面平整度要求高,不得有凹凸不平、杂质和水印等缺陷。
平整度的要求可以通过目测和触摸进行检验。
3. 边缘平整度:切片边缘的平整度要求高,不能有毛刺或锋利的边缘。
平整的边缘可以有效避免PCBA与其他零部件或设备的损坏。
4. 表面处理:切片的表面处理有多种方法,如喷镀锡、喷镀金、喷镀银等。
不同的表面处理方法适用于不同的元器件和使用环境。
PCBA切片标准应规定适用的表面处理方法,并保证其质量和可靠性。
5. 印刷信息:PCBA切片上应有清晰、完整的印刷信息,如型号、序列号、批次号等。
这些信息有助于追溯和管理PCBA的质量和生产过程。
PCBA切片标准的作用如下:1. 保证切片质量:PCBA切片标准规定了对切片质量的要求,包括尺寸、平整度和表面处理等。
切片质量的好坏直接影响到PCBA的稳定性和可靠性。
2. 提高工艺稳定性:PCBA切片标准规范了工艺流程和要求,使生产过程更加规范和稳定。
按照标准进行切片可以减少生产中的失误和缺陷,提高产品的一致性和品质。
3. 降低生产成本:PCBA切片标准对材料和工艺的要求更加明确,可以避免因为质量问题导致的重新加工或报废,减少了不必要的成本。
4. 提高生产效率:PCBA切片标准规定了生产流程和标准化要求,操作人员可以按照标准进行操作,提高生产效率和工作效率。
总之,PCBA切片标准对PCBA制造过程中的切片环节有着重要的指导作用。
电路板微切片制作的三类方法

电路板微切片制作的三类方法1.概述品质的好坏,问题的发生与解决,制程改进的情况,在在都需要微切片(croseconing)做为观察研究与判断的根据,微切片做的好不好,真不真与讨论研判的正确与否大有关系在焉。
一般生产线为品质监视(monitoring)或出货时品管为求品质的保证等所做的多量切片,因系在匆忙及经验不足情况下所赶出的,故至多只能看到真相的六、七成而已,有的在缺乏指导及比较情况下,甚至连一半的实情都看不到,在一片模糊及含混的影像下,能看出什么来?这样的切片有什么意义?若只是为了应付公事当然不在话下,若的确想要做好品质及彻底找出问题解决问题,则必须仔细做切、磨、抛及咬等功夫才会有清晰可看的微切片,不致造成误判。
2.分类板的解剖式破坏性切片法大体上可分为三类:(1)一般切片(正式名称为微切片)可对区及板面其它区域灌满封胶后做了垂直切片(Vercal Secon),也可对通孔做水平切片(Horizontal Secon)是一般常见的做法。
(2)切孔是小心用钻石锯片将一排通孔自正中央切成两半,或用砂纸将一排通孔磨去一半,将切半不封胶的通孔置于20x-40x的立体显微镜(或称实体显微镜)下观察半个的全部情况。
此时若也将通孔的后背再磨的很薄时,则底材将呈透明状,可进行背光法(Back light)检查孔铜层敷盖的情形。
(3)斜切片(45°或30°)可对面区或通孔区做层次间45°的斜切,然后以实体显微镜观察45°切面上导体间的情形。
3.制作技巧除第二类切孔法是用以观察半个孔壁的原状表面情况外,其余第一及第三类都需最后的仔细抛光,才能看到各种真实的情况,此点为切片的成败关键,此点至为重要不可掉以轻心。
以下为制作过程的重点。
3.1取样:以特殊的切模自板上任何处取样或用剪床剪样,注意不可太逼近孔边,以防造成通孔受拉力而变形,也应注意取样的方法,最好先切剪下来,再用钻石锯片切下所要的切样,减少应力的后患。
微切片之分类图解

印制电路板显微剖切技术研究1前言印制电路板制造质量的好坏、使用可靠性的高低、制造过程中问题的发生与解决、制程能力及改进的评估,往往都需要采用显微剖切来作为客观检察、研究和判断的依据。
显微剖切(Microsectioning),又称微切片、金相切片,它的制作有着一套相对专业的制造技术和检测手段。
微切片制作质量的好坏,将直接关系到研究和判断的正确性。
俗话说得好,外行看热闹、内行看门道,各家有各家的高招。
真应了那句名言——条条大路通罗马。
作者长期从事各类印制电路板的制造工艺及品质控制技术的研究,曾专长于金相切片的制作,并有大量第一手金相切片照片在握。
本不该在各位专家面前献丑,但每每翻看这些照片,总有一种与人共研之冲动。
今特将之分类后,陆续登出,望各位不吝赐教,共同为业界之发展贡献些许绵力。
2微切片制作工艺流程2.1取样待检印制电路板试样的采取有以下几种方法:(1)采用机械装置剪切或辊切、锯切;(2)平面冲头之冲切;(3)凹陷冲头之冲切;(4)铣切;(5)带锯切割;上述诸种方法,各有利弊。
从对待检印制电路板部位的损伤来讲,第一种和第二种较为严重;第三种和铣切则适中。
266至于带锯切割法,虽然同冲切和铣切一样的快速、便捷,但对操作者来说,存在潜在的伤害危险。
2.2试样续处理2.3试样入模方式用双面胶粘住样品的正截面(较薄的板用订书子夹住样品待检测的侧截边),使样品垂直立于凝胶模中央。
如是试验切片,建议一个模放两个样品,待检测的侧截边分放于切片的两面,以便从两面磨孔均能磨到孔中央,但样品间要保持最少2mm间距,以免固化后影响样品的牢固性。
2.4调胶处理本处理的重点在于各组分混合充分均匀,且尽可能减少搅拌所造成的气泡产生量。
正误搅拌方式对比请参见下左图9。
搅拌方式对比2.5灌胶入模将上述搅拌均匀的胶料,缓慢倒入模内,直至淹没横担试样的铅芯或鱼线(对于待检部位在模具底部之情况除外)。
对于可能粘附于试样上的气泡,可通过轻敲模壁或用牙签将其引出。
- 1、下载文档前请自行甄别文档内容的完整性,平台不提供额外的编辑、内容补充、找答案等附加服务。
- 2、"仅部分预览"的文档,不可在线预览部分如存在完整性等问题,可反馈申请退款(可完整预览的文档不适用该条件!)。
- 3、如文档侵犯您的权益,请联系客服反馈,我们会尽快为您处理(人工客服工作时间:9:00-18:30)。
线路板可靠性与微切片1、Abrasion Resistance耐磨性在电路板工程中,常指防焊绿漆的耐磨性。
其试验方法是以1 k g 重的软性砂轮,在完成绿漆的IP-B-25样板上旋转磨擦50 次,其梳型电路区不许磨破见铜(详见电路板信息杂志第54 期P.70),即为绿漆的耐磨性。
某些规范也对金手指的耐磨性有所要求。
又,Abrasive是指磨料而言,如浮石粉即是。
Accelerrated Test(Aging)加速试验,加速老化也就是加速老化试验(Aging)。
如板子表面的熔锡、喷锡或滚锡制程,其对板子焊锡性到底能维持多久,可用高温高湿的加速试验,仿真当板子老化后,其焊锡性劣化的情形如何,以决定其品质的允收与否。
此种人工加速老化之试验,又称为环境试验,目的在看看完工的电路板(已有绿漆)其耐候性的表现如何。
新式的"电路板焊锡性规范"中(ANSI/J- STD-003,本刊57 期有全文翻译)已有新的要求,即高可靠度级CLASS 3的电路板在焊锡性(Solderability)试验之前,还须先进行8 小时的"蒸气老化"(Steam Aging),亦属此类试验。
2、Accuracy 准确度指所制作的成绩与既定目标之间的差距。
例如所钻成之孔位,有多少把握能达到其"真位"(True Position)的能力。
3、Adhesion 附着力指表层对主体的附着强弱而言,如绿漆在铜面,或铜皮在基材表面,或镀层与底材间之附着力皆是。
4、Aging 老化指经由物理或化学制程而得到的产物,会随着时间的经历而逐渐失去原有的品质,这种趋向成熟或劣化的过程即称之"Aging"。
不过在别的学术领域中亦曾译为"经时反应"。
5、Arc Resistance 耐电弧性指在高电压低电流下所产生的电弧,当此电弧在绝缘物料表面经过时,物料本身对电弧抗拒力或忍耐力谓之"耐电弧性"。
其耐力品质的好坏,端视其被攻击而造成碳化物导电之前,所能够抵抗的时间久暂而定。
6、Bed-of-Nail Testing 针床测试板子进行断短路(Open/Short)电性试验时,需备有固定接线的针盘(Fixture),其各探针的安插,需配合板面通孔或测垫的位置,在指定之电压下进行电性测试,故又称为"针床测试"。
这种电性测试的正式名称应为Continuity Test,即"连通性试验"。
7、Beta Ray Backscatter 贝他射线反弹散射是利用同位素原子不安定特性所发出的β 射线,使透过特定的窗口,打在待测厚的镀层样本上,并利用测仪中具有的盖氏计数管,侦测自窗口反弹散射回来部份的射线,再转成厚度的资料。
一般测金层厚度仪,例如UPA 公司的Micro-derm 即利用此原理操作。
8、Bond strength 结合强度指积层板材中,欲用力将相邻层以反向之方式强行分开时(并非撕开),每单位面积中所施加的力量(LB/in2)谓之结合强度。
9、Breakdown V oltage 崩溃电压造成板子绝缘材料(如基材或绿漆)失效的各种高压中,引发其劣化之最低最起码之电压即为"崩溃电压"或简称"溃电压"。
或另指引起气体或蒸气达到离子化的电压。
由于"薄板"日渐流行,这种基材的特性也将要求日严。
此词亦常称为Dielectric Withstanding V oltage。
10、Burn-In 高温加速老化试验完工的电子产品,出货前故意放在高温中,置放一段时间(如7 天),并不断测试其功能的劣化情形,是一种加速老化试验,也称为高温寿命试验。
11、Chemical Resistance 抗化性广义是指各种物质对化学品的忍耐或抵抗能力。
狭义是指电路板基材对于溶剂或湿式制程中的各种化学品,以及对助焊剂等的抵抗性或忍耐性。
12、Cleanliness 清洁度是指完工的板子,其所残余离子多寡的情形。
由于电路板曾经过多种湿式制程,一旦清洗不足而留下导电质的离子时,将会降低板材的绝缘电阻,造成板面线路潜在的腐蚀危机,甚至在湿气及电压下点引起导体间(包含层与层之间)的电子迁移(Electromigration)问题。
因而板子在印绿漆之前必须要彻底清洗及干燥,以达到最良好的清洁度。
按美军规MIL-P-55110E 之要求,板子清洁度以浸渍抽取液(75%异丙醇+25%纯水)之导电度(Conductivity)表示,必须低于2×10-6 mho,应在2×106 ohm以,才算及格。
13、Comb Pattern 梳型电路是一种"多指状"互相交错的密集线路图形,可对板面清洁度及绿漆绝缘性等,进行高电压测试的一种特殊线路图形。
14、Corner Crack 通孔断角通孔铜壁与板面孔环之交界转角处,其镀铜层之内应力(Inner Stress)较大,当通孔受到猛烈的热冲击时(如漂锡),在Z 方向的强力膨胀拉扯之下,其孔角。
其对策可从镀铜制程的延展性加以改善,或尽量降低板子的厚度,以减少Z 膨胀的效应。
15、Crack 裂痕在PCB 中常指铜箔或镀通孔之孔铜镀层,在遭遇热应力的考验时,常出现各层次的局部或全部断裂,谓之Crack。
其详细定义可见IPC-RB-276 之图7。
16、Delamination 分层常指多层板的金属层与树脂层之间的分离而言,也指"积层板"之各层玻纤布间的分开。
主要原因是彼此之间的附着力不足,又受到后续焊锡强热或外力的考验,而造成彼此的分离。
17、Dimensional Stability 尺度安定性指板材受到温度变化、湿度、化学处理、老化(Aging) 或外加压力之影响下,其在长度、宽度、及平坦度上所出现的变化量而言,一般多以百分率表示。
当发生板翘时,其PCB 板面距参考平面(如大理石平台) 之垂直最高点再扣掉板厚,即为其垂直变形量,或直接用测孔径的钢针去测出板子浮起的高度。
以此变形量做为分子,再以板子长度或对角线长度当成分母,所得之百分比即为尺度安定性的表征,俗称"尺寸安定性"。
本词亦常指多层板制做中其长宽尺寸的收缩情形,尤其在压合后,内层收缩最大,通常经向约万分之四,纬向约万分之三左右。
18、Electric Strength(耐)电性强度指绝缘材料在崩溃漏电以前,所能忍受的最高电位梯度(Potential Gradient,即电压、电位差),其数值与材料的厚度及试验方法都有关。
此词另有同义字为(1)Dielectric Strength介质强度(2)Dielectric Break Down介质崩溃(3)Dielectric Withstand V oltage介质耐电压等,一般规范中的正式用语则以第三者为多。
19、Entrapment 夹杂物指不应有的外物或异物被包藏在绿漆与板面之间,或在一次铜与二次铜之间。
前者是由于板面清除不净,或绿漆中混有杂物所造成。
后者可能是在一次铜表面所加附的阻剂,发现施工不良而欲"除去"重新处理时,可能因清除未彻底留下残余阻剂,而被二次铜所包覆在内,此情形最常出现于孔壁镀铜层中。
另外当镀液不洁时,少许带电固体的粒子也会随电流而镀在阴极上,此种夹杂物最常出现在通孔的孔口,下二图所示即是典型镀铜的Entrap。
20、Fungus Resistance 抗霉性电路板面若有湿气存在时,可能因落尘中的有机物而衍生出霉菌,此等菌类之新陈代谢产物会有酸类出现,将有损板材的绝缘性。
故板面的导体电路或所组装的零件等,都要尽量利用绿漆及护形漆(Conformal Clating ,指组装板外所服贴的保护层)予以封闭,以减少短路或漏电的发生。
21、Hipot Test 高压电测为High Potential Test 的缩写,是指采用比在实际使用时更高的直流电压,去进行仿真通电的电性试验,以检查出可能漏失的电流大小。
22、Hole pull Strength 孔壁强度指将"整个孔壁"从板子上拉下所需的力量,也就是孔壁与板子所存在的固着强度。
其试验法可将一金属线押进孔中并在尾部打弯,经并经填锡牢焊在通孔中。
如此经5次焊锡及 4 次解焊,然后去将整个通孔壁连同填锡焊点,一并往板面垂直方向用力拉扯,直到松脱所呈现的力量为止。
其及格标准为500 PSI,此种耐力谓之孔壁强度。
23、Ion Cleanliness 离子清洁度电路板经过各种湿制程才完成,下游组装也要经过助焊剂的处理,因而使得板面上带有许多离子性的污染物,必须要清洗干净才能保证不致造成腐蚀,而清洗干净的程度如何,须用到异丙醇(75%)与纯水(25%)的混和液去冲洗后,再测其溶液的电阻值或导电度,称为离子清洁度,而由于离子所造成板面的污染,则称为"离子污染"(Ionic Contamination)。
24、Ionizable(Ionic)Contamination 离子性污染在电路板制造及下游组装的过程中,某些参与制程的化学品,若为极性化合物而又能溶于水时,则其在板上的残迹,将很可能会因吸潮而溶解成导电性的离子,进而造成板材的漏电构成危害。
此类化学品最典型者即为:助焊剂中之活性物质、电镀液或蚀刻液之残余、指印汗水等。
皆需彻底洗净以达到规范所要求的清洁度或绝缘度。
25、Microsectioning 微切片法是对电路板之板材组织结构,与板材在各制程站的细部品质,以及零件组装情况等,在微观下做进一步深入了解的一种技术,是一种公认的品检方法。
在正确拋光与小心微蚀后的切片试样上,于放大100~400 倍下,各种细部详情均将一览无遗,而多数的问题根源也为之无所遁形。
不过微切片正确判读所需的智识,却远超过其制作的技术,几乎是集材料、制程及品管等各种学理与规范于一身的应用。
此种微切片法是源自金属材料,及矿冶科技的学问领域。
26、Moisture and Insulation Resistance Test 湿气与绝缘电阻试验此试验原来的目的是针对电路板面的防焊绿漆,或组装板的护形漆(Conformal Coating)等所进行的加速老化试验,希望能藉助特殊的梳形线路,自其两端接点处施加外电压(100 VDC?0%)下,试验出此等皮膜"耐电性质"的可靠度如何,以Class 2品级的板类而言,须在50℃?℃及90~98%RH的环境下,放置7天(168小时),且每8小时检测一次"绝缘电阻"。