大型外浮顶原油储罐机械清洗方案优化
原油油罐机械清洗技术介绍.doc
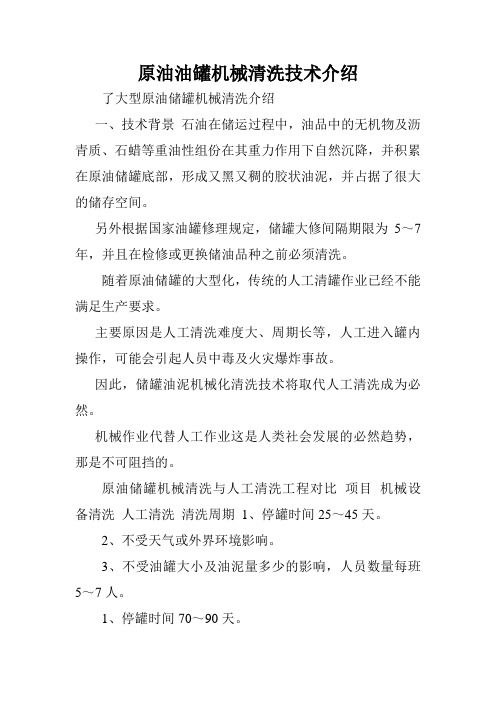
在中国市场,仅对大型原油储罐所需的机械清洗系统,粗略估计至少也需要80套以上。
另外还有其他小型储罐和成品油罐需要清洗,此清洗市场有很大提升空间。
因此这个市场中,必须要有多只非常专业的清洗队伍,并完全利用机械清洗技术进行清洗作业,才能满足生产需要。
2、不受天气或外界环境影响。
3、不受油罐大小及油泥量多少的影响,人员数量每班5~7人。
1、停罐时间70~90天。
2、恶劣天气及寒冷地带不宜进行清洗。
3、根据油罐大小及油泥量多少增加清洗人员,数量在30~50人。
清洗质量1、油罐内表面清晰可见。
2、清洗后的残渣为少量铁锈,沙粒等块状物。
1、油泥清洗不彻底。
2、油罐内的油砂残留多,造成恶性循环。
安全性1、封闭式清洗,不需人进入罐内清洗。
1、人必须进入罐内清洗,易发生人为疏忽,易引起事故。
2、注入惰性气体,防静电、防爆炸发生。
2、易产生静电,易发生爆炸事件。
保护环境1、清洗、回收是封闭式,并进行油水、油砂分离,无污油、污水、废气排出。
1、清洗后不可利用的沉积物多且不易处理,造成大气及水污染。
随着原油储罐的大型化,传统的人工清罐作业已经不能满足生产要求。
主要原因是人工清洗难度大、周期长等,人工进入罐内操作,可能会引起人员中毒及火灾爆炸事故。
因此,储罐油泥机械化清洗技术将取代人工清洗成为必然。
机械作业代替人工作业这是人类社会发展的必然趋势,那是不可阻挡的。
原油储罐机械清洗与人工清洗工程对比项目机械设备清洗人工清洗清洗周期1、停罐时间25~45天。
据我们了解,当前在用的和正在引进的国外机械清洗系统在40套左右,而且单套的处理能力各不相同。
超厚沉积物浮顶油罐的机械清洗

通 常情况 下 , 油是一 种胶 体溶 液 。其 中, 原 固体
烃 和沥青 质是 分 散相 , 而液 态烃 和 胶 质则 是 分散 介
剪切力的作用下 , 将影响体系内颗粒 的形状、 大小、
排列 和生 长速 度 等 。油 温 近 一 步 降 低 , 到失 流 点 达 时, 含蜡 原油发 生转 相 。在 此过 程 中 , 晶体 继续 析 蜡
厕渡 尜
文 章编 号 : 7 — 99 2 1 ) 2— 0 8— 6 1 1 8 0 (0 10 00 0 6
Cl a i o l e n ng W rd
清洗 世 界
第 2 卷第 2 7 期 2 1 2月 01 年
超厚 沉 积 物浮 顶 油 罐 的机械 清 洗
徐 锋 , 东辉 , 赵 张 军
量 的胶 质 和 沥 青 质 。组 成 原 油 的 主 要 元 素 是 碳 和
物厚度通 常为 1 以下 时 , m 由于 浮顶 可 以正 常下 降 ,
因此可采 用常 规 的机 械 清 洗 即 可 , 当然也 可 采 用 人 工清洗 。但对 于罐 内沉 积 物超 厚 时 , 即沉 积 物 的厚
A b t a t Th s p o o a s a c r i o p o e u e a d e p re c s o c a ia la i f e ta s r c : i r p s li c o dng t r c d r n x e n e f me h n c lce nng o xr - i t i k su g . I n lz st e meh d n h o e folmii g a d tm p r t r o toln . h c l d e ta ay e h t o s a d t e r s o i i xn n e e au e c n r l g i
大型立式原油罐清洗方案
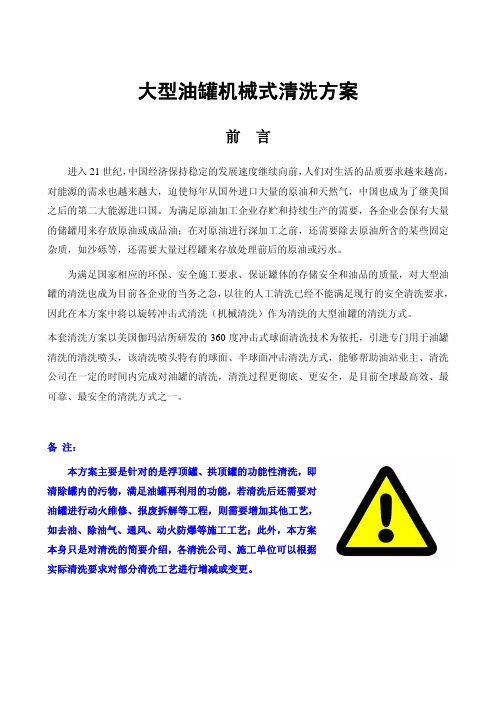
清除罐内的污物,满足油罐再利用的功能,若清洗后还需要对 油罐进行动火维修、报废拆解等工程,则需要增加其他工艺, 如去油、除油气、通风、动火防爆等施工工艺;此外,本方案 本身只是对清洗的简要介绍,各清洗公司、施工单位可以根据 实际清洗要求对部分清洗工艺进行增减或变更。
名称
Gamajet 4 型
Gamajet 8 型
PowerFLEX
密封套件 2.5″快速接头 2″快速接头
增压泵 污水泵 液环真空泵 柴油发电机组 真空罐 排污过滤器 过滤器 蝶阀 球阀 高压软管 压力表 其他管件 接地线 制氮设备 油水分离装置 电缆 电器控制箱 污水池 防爆工具
规格参数
数量
青铜、HV1/LM、两喷嘴 5/8″
5
万博克环保科技(北京)有限公司 400-688-5153 010-84885159 -811
4. 清洗系统配制
根据以上方案配置所需的清洗部件,主要的设备及部件:
序号
1
2
3
4 5 6 7 8 9 10 11 12 13 14 15 16 17 18 19 20 21 22 23 24 25
万博克环保科技(北京)有限公司 400-688-5153 010-84885159 -811
一、 概述
目前,大型储油罐大都采用浮顶结构,简称浮顶罐,浮顶罐的存储量从 5000 方~200000 方不等,由于其容量大、结构简单、空间利用率高,是原油转运码头、油田储油站、石化企 业的理想选择,被全世界广泛采用,我国目前最大的浮顶罐多为 100000 方。此外,在原油处 理/加工过程中,还需要一定量的工艺过程罐,这些过程罐体积较小,多采用拱顶机构,存储 量一般在 2000 方以下。
原油储罐cow全自动机械清洗方案

原油储罐cow全自动机械清洗方案
原油储罐COW全自动清洗施工方案
目录
一、施工组织设计……………………………………………………………
工程概况…………………………………………………………………
施工组织设计(方案)…………………………………………………
二、施工进度、供应计划…………………………………………………
三、工程验收………………………………………………………………
四、施工组织措施…………………………………………………………
五、工程质量及安全管理保证措施………………………………………
六、HSE作业计划书…………………………………………………
七、应急计划………………………………………………………………
八、现场文明施工措施……………………………………………………
一.施工组织设计
1工程概况
滨南采油厂原油末站20000m3的原油罐已经停用多年,原油储缸经过长期运行或闲置,产生太多的泥沙沉积物且混有内防腐脱落造成罐底板腐蚀产物。
采油厂计划拆除该原油罐,为满足环保,安全要求,需要对该油罐进行拆除前彻底清洗。
1.1 工程简介
(1)工程名称:20000m3的原油罐COW全自动清洗
(2)工程建设地点:滨南末站
(3)工程类别:2万方原油储罐COW全自动清洗
(4)储罐尺寸及工期要求:。
原油储罐机械清洗技术及应用

原油储罐机械清洗技术及应用摘要在石油工业中,储罐是必不可少的设备,但长期运行后会积累很多污垢和沉淀物,这些物质会导致储罐内部腐蚀和安全隐患。
因此,及时清洗储罐变得非常必要。
本文提出了一种机械清洗技术,可以高效、安全、节约成本地清洗原油储罐。
1. 原油储罐清洗的必要性原油储罐通常由一种或多种类型的原油混合物构成,这些原油混合物在储罐内长时间存放时容易形成沉积物和腐蚀。
这些积累物不仅会影响原油的品质,还会导致储罐本身的腐蚀和安全隐患。
因此,定期的储罐清洗是必不可少的。
传统的储罐清洗方法包括水冲洗、化学清洗以及手工清理等,这些方式都存在一些缺点。
水冲洗过程中,水很难进入难以清洗的角落和缝隙,可能导致残留物仍然存留在储罐中。
化学清洗的过程中,使用的化学物质会对环境造成污染,而手工清理的方式则需要消耗大量的人力,效率低下。
机械清洗技术则解决了上述问题,本文将介绍其具体过程及优势。
2. 原油储罐机械清洗技术机械清洗技术是一种高效的清洗方式,主要是通过机械设备对储罐内壁进行清洗,从而去除污垢和沉积物。
通常的机械清洗设备包括水平刮板机、旋转刮板机和高压清洗机等。
这些机械装置能够有效地清除铁锈、积垢以及其他罐内残留物。
具体来讲,机械清洗过程包括以下几个步骤:1.简单检查储罐外观和内部空气质量等情况,确保安全。
2.焊接机械臂和平台以便自上而下地对储罐进行清洗,清洗过程中,机械臂和平台将钢刷放入储罐内,通过转动钢刷完成清洗过程。
3.使用高压水枪清洗剩余杂质和残留物,确保储罐内部干净。
4.通过唧筒泵将污垢送到处理厂进行处理,以达到环保清洗的要求。
需要注意的是,机械清洗过程中需要严格把关火源,以免引发安全事故。
同时,清洗过程中如果储罐内氧气浓度过高,也会对人员造成危险。
3. 原油储罐机械清洗技术的优势相比于传统的清洗方式,机械清洗技术具有以下优势:1.高效:机械清洗技术的清洗速度非常快,通常只需要几个小时即可完成储罐的清洗任务。
大型原油储罐机械清洗介绍
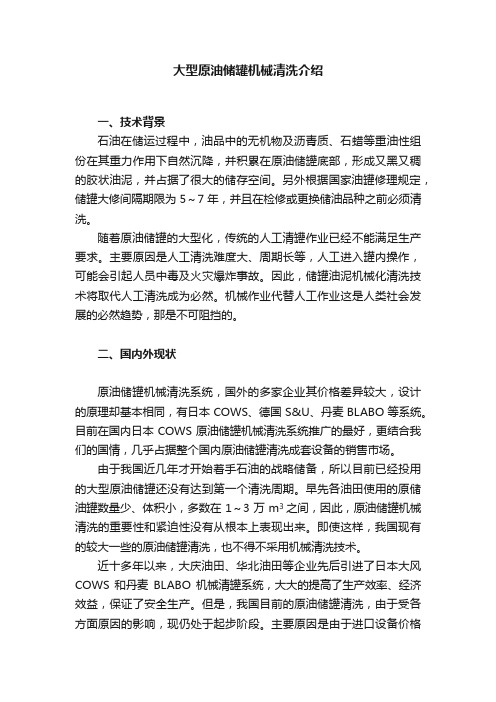
大型原油储罐机械清洗介绍一、技术背景石油在储运过程中,油品中的无机物及沥青质、石蜡等重油性组份在其重力作用下自然沉降,并积累在原油储罐底部,形成又黑又稠的胶状油泥,并占据了很大的储存空间。
另外根据国家油罐修理规定,储罐大修间隔期限为5~7年,并且在检修或更换储油品种之前必须清洗。
随着原油储罐的大型化,传统的人工清罐作业已经不能满足生产要求。
主要原因是人工清洗难度大、周期长等,人工进入罐内操作,可能会引起人员中毒及火灾爆炸事故。
因此,储罐油泥机械化清洗技术将取代人工清洗成为必然。
机械作业代替人工作业这是人类社会发展的必然趋势,那是不可阻挡的。
二、国内外现状原油储罐机械清洗系统,国外的多家企业其价格差异较大,设计的原理却基本相同,有日本COWS、德国S&U、丹麦BLABO等系统。
目前在国内日本COWS原油储罐机械清洗系统推广的最好,更结合我们的国情,几乎占据整个国内原油储罐清洗成套设备的销售市场。
由于我国近几年才开始着手石油的战略储备,所以目前已经投用的大型原油储罐还没有达到第一个清洗周期。
早先各油田使用的原储油罐数量少、体积小,多数在1~3万m3之间,因此,原油储罐机械清洗的重要性和紧迫性没有从根本上表现出来。
即使这样,我国现有的较大一些的原油储罐清洗,也不得不采用机械清洗技术。
近十多年以来,大庆油田、华北油田等企业先后引进了日本大风COWS和丹麦BLABO机械清罐系统,大大的提高了生产效率、经济效益,保证了安全生产。
但是,我国目前的原油储罐清洗,由于受各方面原因的影响,现仍处于起步阶段。
主要原因是由于进口设备价格昂贵,每套都在几千万以上,这样不仅增加了原油储罐的机械清洗成本,也限制了这一技术的普及和发展。
另外原因,原油储罐的机械清洗打破原有的人工清罐利益链,采用传统的人工清罐方法,虽然没有施工费用,但大量的罐底油进不了油田储运系统,造成资源浪费和经济损失。
机械清罐技术实施触动局部人的利益,因此技术推进受到很大阻力。
储油罐清理方案
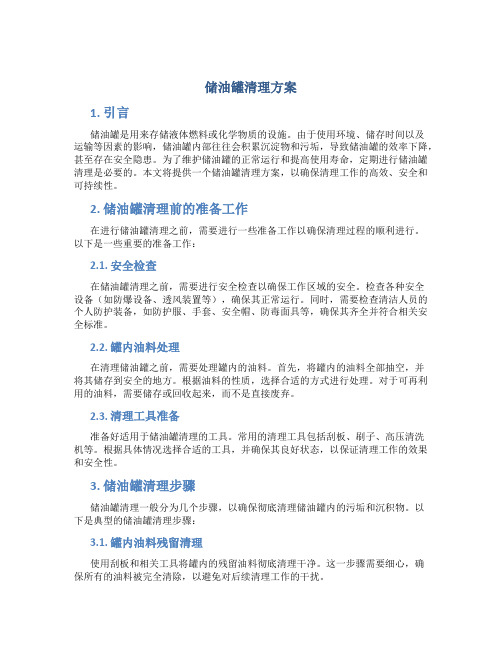
储油罐清理方案1. 引言储油罐是用来存储液体燃料或化学物质的设施。
由于使用环境、储存时间以及运输等因素的影响,储油罐内部往往会积累沉淀物和污垢,导致储油罐的效率下降,甚至存在安全隐患。
为了维护储油罐的正常运行和提高使用寿命,定期进行储油罐清理是必要的。
本文将提供一个储油罐清理方案,以确保清理工作的高效、安全和可持续性。
2. 储油罐清理前的准备工作在进行储油罐清理之前,需要进行一些准备工作以确保清理过程的顺利进行。
以下是一些重要的准备工作:2.1. 安全检查在储油罐清理之前,需要进行安全检查以确保工作区域的安全。
检查各种安全设备(如防爆设备、透风装置等),确保其正常运行。
同时,需要检查清洁人员的个人防护装备,如防护服、手套、安全帽、防毒面具等,确保其齐全并符合相关安全标准。
2.2. 罐内油料处理在清理储油罐之前,需要处理罐内的油料。
首先,将罐内的油料全部抽空,并将其储存到安全的地方。
根据油料的性质,选择合适的方式进行处理。
对于可再利用的油料,需要储存或回收起来,而不是直接废弃。
2.3. 清理工具准备准备好适用于储油罐清理的工具。
常用的清理工具包括刮板、刷子、高压清洗机等。
根据具体情况选择合适的工具,并确保其良好状态,以保证清理工作的效果和安全性。
3. 储油罐清理步骤储油罐清理一般分为几个步骤,以确保彻底清理储油罐内的污垢和沉积物。
以下是典型的储油罐清理步骤:3.1. 罐内油料残留清理使用刮板和相关工具将罐内的残留油料彻底清理干净。
这一步骤需要细心,确保所有的油料被完全清除,以避免对后续清理工作的干扰。
3.2. 高压清洗使用高压清洗机进行罐内的高压清洗。
通过喷射高压水流,将罐壁上的污垢彻底清除。
在清洗过程中,需注意工作人员的安全,并确保喷水方向和角度适当,以避免对罐壁造成损坏。
3.3. 刷洗与吸尘使用刷子和吸尘器对罐内进行刷洗和吸尘,以进一步清除残留的污垢。
刷洗时需注意力度,以免对罐壁造成损伤。
吸尘时需使用专业吸尘设备,以确保清洁效果和工作人员的健康安全。
原油储罐机械清洗技术及应用
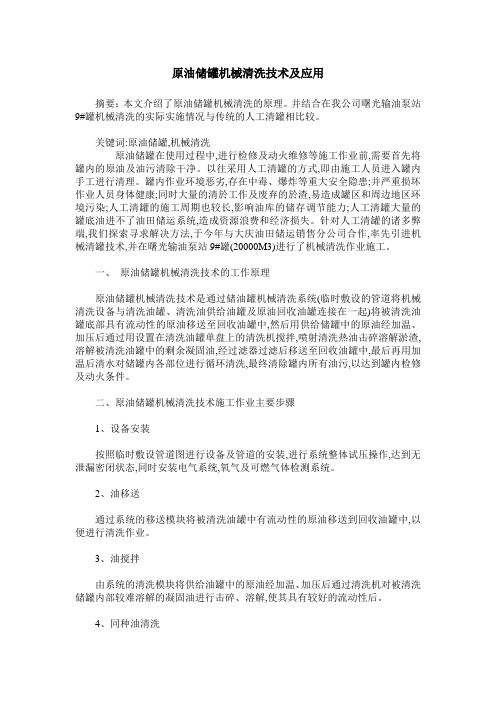
原油储罐机械清洗技术及应用摘要:本文介绍了原油储罐机械清洗的原理。
并结合在我公司曙光输油泵站9#罐机械清洗的实际实施情况与传统的人工清罐相比较。
关键词:原油储罐,机械清洗原油储罐在使用过程中,进行检修及动火维修等施工作业前,需要首先将罐内的原油及油污清除干净。
以往采用人工清罐的方式,即由施工人员进入罐内手工进行清理。
罐内作业环境恶劣,存在中毒、爆炸等重大安全隐患;并严重损坏作业人员身体健康;同时大量的清於工作及废弃的於渣,易造成罐区和周边地区环境污染;人工清罐的施工周期也较长,影响油库的储存调节能力;人工清罐大量的罐底油进不了油田储运系统,造成资源浪费和经济损失。
针对人工清罐的诸多弊端,我们探索寻求解决方法,于今年与大庆油田储运销售分公司合作,率先引进机械清罐技术,并在曙光输油泵站9#罐(20000M3)进行了机械清洗作业施工。
一、原油储罐机械清洗技术的工作原理原油储罐机械清洗技术是通过储油罐机械清洗系统(临时敷设的管道将机械清洗设备与清洗油罐、清洗油供给油罐及原油回收油罐连接在一起)将被清洗油罐底部具有流动性的原油移送至回收油罐中,然后用供给储罐中的原油经加温、加压后通过用设置在清洗油罐单盘上的清洗机搅拌,喷射清洗热油击碎溶解淤渣,溶解被清洗油罐中的剩余凝固油,经过滤器过滤后移送至回收油罐中,最后再用加温后清水对储罐内各部位进行循环清洗,最终清除罐内所有油污,以达到罐内检修及动火条件。
二、原油储罐机械清洗技术施工作业主要步骤1、设备安装按照临时敷设管道图进行设备及管道的安装,进行系统整体试压操作,达到无泄漏密闭状态,同时安装电气系统,氧气及可燃气体检测系统。
2、油移送通过系统的移送模块将被清洗油罐中有流动性的原油移送到回收油罐中,以便进行清洗作业。
3、油搅拌由系统的清洗模块将供给油罐中的原油经加温、加压后通过清洗机对被清洗储罐内部较难溶解的凝固油进行击碎、溶解,使其具有较好的流动性后。
4、同种油清洗由清洗系统的清洗模块将供给油罐中的原油经加温、加压后通过清洗机对被清洗储罐内部各部分的凝固油进行溶解,使其分散、具有流动性,再通过移送模块过滤后移送到回收油罐中。
AQT 3042 外浮顶原油储罐机械清洗安全作业要求
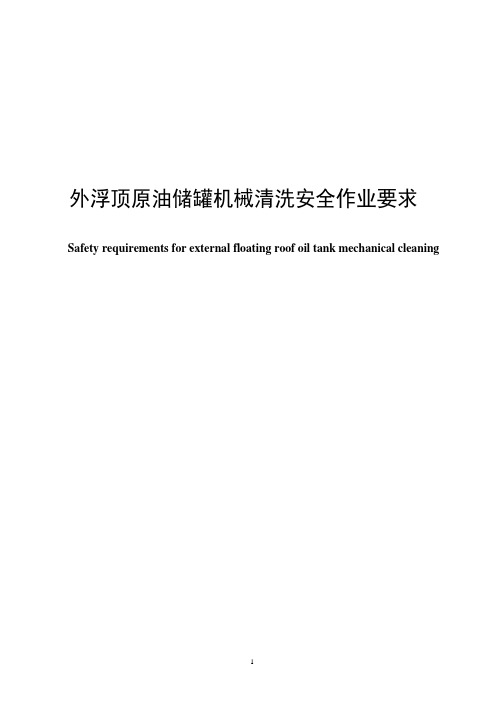
外浮顶原油储罐机械清洗安全作业要求Safety requirements for external floating roof oil tank mechanical cleaning外浮顶原油储罐机械清洗安全作业要求1范围本标准规定了外浮顶原油储罐机械清洗安全作业的一般要求和工艺要求。
本标准适用于地面常压外浮顶原油储罐的机械清洗作业。
内浮顶油罐、卧式油罐和拱顶油罐的机械清洗可参照使用。
2规范性引用文件下列文件对于本文件的应用是必不可少的。
凡是注日期的引用文件,仅所注日期的版本适用于本文件。
凡是不注日期的引用文件,其最新版本(包括所有的修改单)适用于本文件。
GB 5082 起重吊运指挥信号GB 8978 污水综合排放标准GB 12158 防止静电事故通用导则GB 50058-1992 爆炸和火灾危险环境电力装置设计规范GB 50194 建设工程施工现场供用电安全规范GBZ 2 工业场所有害因素职业接触限值SY/T 5858 石油工业动火作业安全规程SY 5984 油(气)田容器、管道和装卸设施接地装置安全检查规范SY/T 6696 储罐机械清洗作业规范3术语和定义下列术语和定义适用于本文件。
3.1清洗机jet cleaner用于油罐内表面清洗,能在一定压力下喷射液态介质,并可在受限空间内旋转和射流的装置。
3.2竖管vertical pipe连接地面管路和罐顶管路并沿清洗罐罐壁敷设的临时竖直管道。
3.3沉积物sludge沉积在油罐底部失去流动性的物质。
3.4旁接罐supply and receiving tank为清洗系统提供循环清洗介质、接收移送的油品的储罐。
4一般要求4.1作业人员和设备要求作业人员和设备应具符合下基本要求:——作业人员应经过油罐机械清洗设备操作培训合格后上岗;——伤疮口尚未愈合者,油品过敏者,职业禁忌者,在经期、孕期、哺乳期的妇女,有聋、哑、呆傻等严重生理缺陷者,患有深度近视、巅痫、高血压、过敏性气管炎、哮喘、心脏病和其他严重慢性病以及年老体弱不适应清罐作业等人员,不应进入现场;——浮顶油罐机械清洗应具备对清洗介质的抽吸、升压、换热、喷射能力,用惰性气体对清洗罐内气体的置换能力,对清洗罐内的可燃气体、氧气、硫化氢气体浓度的监测能力,热水清洗过程中的回收油品能力,热水清洗结束后的污水处理能力;——其它可按照 SY/T6696 标准规定执行。
大型原油储罐机械清洗安全分析及检测维修
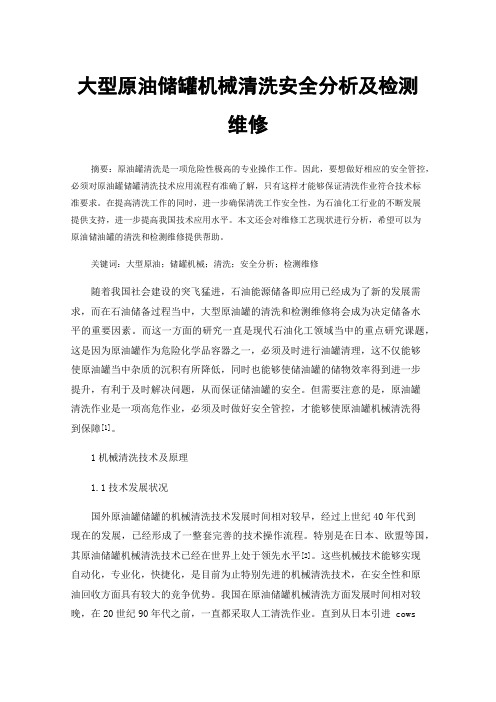
大型原油储罐机械清洗安全分析及检测维修摘要:原油罐清洗是一项危险性极高的专业操作工作。
因此,要想做好相应的安全管控,必须对原油罐储罐清洗技术应用流程有准确了解,只有这样才能够保证清洗作业符合技术标准要求。
在提高清洗工作的同时,进一步确保清洗工作安全性,为石油化工行业的不断发展提供支持,进一步提高我国技术应用水平。
本文还会对维修工艺现状进行分析,希望可以为原油储油罐的清洗和检测维修提供帮助。
关键词:大型原油;储罐机械;清洗;安全分析;检测维修随着我国社会建设的突飞猛进,石油能源储备即应用已经成为了新的发展需求,而在石油储备过程当中,大型原油罐的清洗和检测维修将会成为决定储备水平的重要因素。
而这一方面的研究一直是现代石油化工领域当中的重点研究课题,这是因为原油罐作为危险化学品容器之一,必须及时进行油罐清理,这不仅能够使原油罐当中杂质的沉积有所降低,同时也能够使储油罐的储物效率得到进一步提升,有利于及时解决问题,从而保证储油罐的安全。
但需要注意的是,原油罐清洗作业是一项高危作业,必须及时做好安全管控,才能够使原油罐机械清洗得到保障[1]。
1机械清洗技术及原理1.1技术发展状况国外原油罐储罐的机械清洗技术发展时间相对较早,经过上世纪40年代到现在的发展,已经形成了一整套完善的技术操作流程。
特别是在日本、欧盟等国,其原油储罐机械清洗技术已经在世界上处于领先水平[2]。
这些机械技术能够实现自动化,专业化,快捷化,是目前为止特别先进的机械清洗技术,在安全性和原油回收方面具有较大的竞争优势。
我国在原油储罐机械清洗方面发展时间相对较晚,在20世纪90年代之前,一直都采取人工清洗作业。
直到从日本引进 cows系统机械清洗技术才使得我国储罐机械清洗技术有所发展。
到目前为止,已经开始进行了大量应用,有效提高了我国原油储油罐机清洗效率。
1.2具体作业原理从实际作业过程来看机械清洗作业主要以喷头喷射为主,在喷水过程当中,往往需要对温度和压力进行控制,来达到最终的清洗效果,这种作业方式主要以同类型的原油或者是水对罐内的油泥进行喷射和破碎等。
清罐方案 1万立方浮顶储油罐(专业研究)
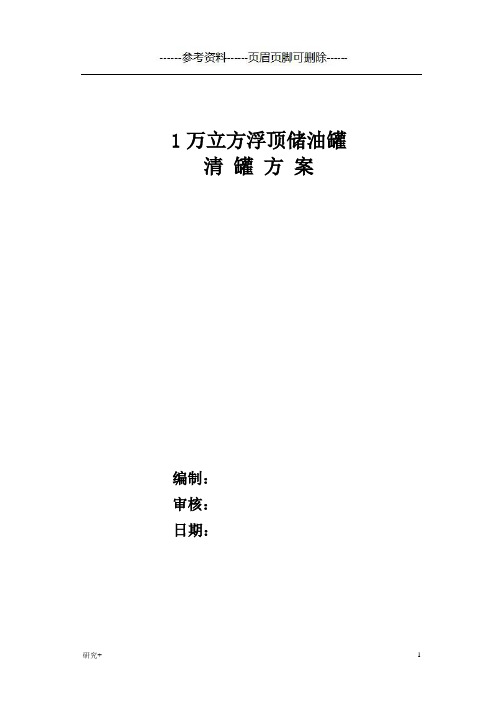
1万立方浮顶储油罐清罐方案编制:审核:日期:储油罐清罐方案为了保证2#油罐顺利进行维修, 确保设备及人员安全, 必须清除罐内原油, 对油罐进行检测,我们依据总公司企业标准《油罐清洗安全技术规程》的有关规定,特编制此清罐方案。
一、清罐前准备工作:1.按材料单进行物资、工具、器材的购置。
2.现场配备35Kg干粉推式灭火器2个、手提式8公斤消防器材4个、手提式4公斤消防器材4个。
3.在2#防火堤西侧开挖一个2.5米开口通道,用于清理油泥。
(蒸罐后)4.在2#油罐人孔北侧开挖4×5×1.5米污油池一个,作为罐内污油排放池,挖出的土围在排污孔四周。
5.清罐前与临濮站联系协商供蒸汽事项。
6.预制泥浆泵装置和管线DN80(100米)至1#储油罐人孔处,安装DN80阀门两个。
7.预制临时蒸汽管线:在我站食堂北侧伴热主管线上架设临时蒸汽管线DN100(200米)至2#储油罐北侧污油池。
8.制作DN50(3×4)米蒸汽盘管一组,用于加热污油池内的罐底油。
9.预制蒸罐管线DN50(20米)至2#储油罐人孔。
10.用70*70*7角钢预制通风机固定支架两个11.事先与临濮站消防队联系消防车一辆,作为清罐时安全专用。
二、清罐程序:1.2#油罐采用单进罐(来油-1#-2#-5#-2#罐) 流程,罐位至8米时采用单出罐(2#罐-5#-4#-主管线)流程,冲刷底部油泥,罐内原油进行外输至1.7m罐位时,岗位人员加密检尺,继续抽油到极限罐位1.5米,2#油罐退出生产运行。
2.把2#油罐进口2-2#阀、出口2-4#阀门、2-6#阀门关闭并上锁。
3.罐位1.5米时改用泥浆泵(70 立方米/时) 抽油,直到打不出油为止.4.打开浮顶罐人孔,站运销人员负责检尺,测量存油工作,并上报处运销科,由运销科组织来人核对罐底油量后,罐底油才可出罐。
5.打开所有人孔自然通风2--3天后, 再用防爆送引风机强制通风2--3天,直至油汽浓度达到规定值后,方可佩带呼吸器具入罐作业。
COWS储罐机械清洗技术应用探讨

COWS储罐机械清洗技术应用探讨摘要:在我国原油储罐清洗技术仍处于发展的前期,依旧有不少大型储罐的清洗使用传统人工化的方法进行储罐机械清洗方法。
但随着设备和相关技术的逐渐完善,以及原油储罐机械清洗技术所具有的优势,它在未来必将取代人工方式的清罐,带来更多的效益。
本文从经济、时效、安全、环保等方面对比人工清洗与机械清洗方法的优劣,重点研究了COWS技术的原理和工艺特点,并提出其在技术应用中的改进建议。
关键词:储罐清洗、COWS技术、技术应用1前言为了满足国内石油的需求,保障国家能源安全,健全国家石油储备体系,国家已经建立四大石油储备基地。
为了增大储备基地的石油存储量,储罐大型化成为一种必然趋势。
伴随着大型化的趋势,储罐清洗成为热点话题,储罐机械清洗越来越受到各方的重视。
根据有关储油罐修理的规范规定,储油罐每运行5~7年要进行开罐检查,维修,这时就要对储油罐进行清洗。
大型储罐在长时间油品储存过程中会形成油泥沉淀,油泥必须进行清洗,而且这些油泥中含有大量的原油。
清洗的目的就是要除去堆积在油罐底部的淤渣及罐壁上的凝油和凝蜡。
原油储罐里的淤渣通常由无机沉积物和有机沉积物组成。
无机沉积物包括铁锈、砂、泥浆等;有机沉积物包括原油、蜡、沥青等。
分析原油储罐的沉积物,发现原油和蜡占全部淤渣的80%~95%,其他除了水之外,无机沉积物很少。
由此可见,原油储罐的沉积物中大部分是有用的物质,应加以回收利用。
人工清洗的方法受到很多方面的限制,特别是无法回收储罐中的原油,造成能源浪费,而机械清洗系统的原油回收率高达98%,能很好的避免资源浪费的问题。
原油储罐机械清洗技术就在这样的大环境下被引进中国,中石油、中石化、中海油已经使用这项技术,大罐清洗技术随科技应用不断创新,越来越先进、越合理、越安全,处理效果也越来越好,特别是COWS(Crude Oil Washing System)机械清洗技术在国内外应用最为广泛,也获得了可观的效益。
cow清洗优点

COW原油储罐机械清洗系统的主要优点烟台杰瑞集团大型COTWS 浮顶罐清洗系统简介COTWS(原油储油罐机械清洗)装置,本公司油罐清洗设备是基于多年来大型油罐的清洗经验,参考了日本、瑞士等国外设备改进装置.本装置从清洗油罐中回收油类,采用抽吸系统,通过将清洗所用主要机器实现组件化,不仅减少了临时设置作业,还使主要机器装置的集中管理成为可能,在丰富的实际操作和运行中发现和从结构上改进了国外设备许多的不足,使目前国际上在使用的比较先进的设备,同时我们还在不断的努力,常年跟踪维护改进我们客户的设备。
BJATL 储油罐机械清洗的优点:1. 缩短清洗期大容量罐含有大量沉积的淤渣,有些方法是利用人力,需6 个月至1 年清洗期。
这意味着长时间里无法使用油罐,存储设备的利用率很低。
因此要求无论油罐的大小和沉积物多少,清洗工程都应在短时期内完成。
2. 高效率清洗清洗法必须是具备信赖度和高效率且不受油罐大小,沉积物多少和其他因素影响。
3. 安全性掌握好工作中的安全性,这样应该可以避免因人为疏忽,和类似火灾和爆炸等灾难性因素带来的后果。
4. 资源再利用沉积物中有用的部分应该复原并作为资源再使用。
5. 复原油应完好地复原而不使其再腐化。
6. 减少大量沉积物的损失。
7. 环境保护。
8. 节省人力的机械化方法油罐中的工作是最脏和最危险的工作之一。
工作人员显然不愿意长时间在如此坏的环境里工作,火灾随时可能发生,此外在恶劣工作环境中容易因疲劳而造成工作效率低下。
应避免完全依赖人力的工作法,采用能最大限度减少油罐中肮脏工作量的方法,这意味着应该推进机械化和节省劳力。
9. 不受油罐位置影响的方法完成清洗工作可以不受蒸汽,电力,水,污水罐和废液处理设备等条件制约。
10. 经济性的方法清洗法应在各种投资方面是经济的,例如,公益费(蒸汽,水和电力),化学物质,沉积物处理,污水处理,还原油,复原油量,工作期,油罐使用停止期,机器,原材料和人力等方面的投资。
大型外浮顶原油储罐机械清洗方案优化

大型外浮顶原油储罐机械清洗方案优化摘要:针对华德石化有限公司在役的大型外浮顶原油储罐运用COWS机械清洗技术,进行机械清洗方案的优化,使COWS清洗技术在大型油罐的清洗上运用更成熟,不断提高清罐效率和安全系数。
关键词:大型油罐COWS技术优化一、前言华德石化拥有在役储油罐14座,其中马鞭洲首站12座5×104m3外浮顶储油罐,南边灶油库2座10×104m3外浮顶储油罐,为提高储运能力,南边灶油库正在建设的10×104m3外浮顶储油罐2座,5.5×104m3外浮顶储油罐2座(预计2013年8月份投产),为满足广州石化接卸原油多元化需求,还会有一些储油罐建成投产,华德石化1997年投产至今储运设备安全平稳运行,根据SY/T5921-2000标准中规定大型油罐检修周期为5~7年,2004年首次制定清罐检修方案,并委托茂名众合公司对第1台罐进行了机械清洗,取得了较好效果,截止2013年5月,已完成了16座储油罐机械清洗作业。
由于马鞭洲首站地处孤岛,公用工程设施有限,不能为清罐提供驱动用电源和蒸汽,所以对COWS(Crude Oil Washing System)清罐技术的运行又提出了更高要求。
二、清洗技术原理及清洗过程1.清洗技术原理COWS机械清洗是利用高压油喷射流将沉积、附着的油渣、蜡质等有机物击碎、溶解,并将其还原成接近标准的原油,最大限度地将罐底残油予以回收。
清洗过程分为同种油清洗和温水清洗,利用同种类油品为清洗油,由清洗泵增压,通过清洗机冲射罐顶顶板、罐壁和罐底,溶解一切可溶性附着物,将过滤后的油品全部回收,最后利用温水进行全方位的清洗。
详见原油罐机械清洗施工原理流程图:原油罐机械清洗施工原理流程图2.COWS清洗设备组成2.1回收装置A:利用液环真空泵提供动力将清洗油罐内剩余油抽吸出来,在用泵移送到回油罐;在进行油水分离时,将油水混合液送到油水分离槽。
原油储罐机械清洗工艺应用与优化

2018年07月原油储罐机械清洗工艺应用与优化杨凯侯嘉越李春晓(玉门油田分公司炼化总厂,甘肃玉门735200)摘要:储罐机械清洗由于其自身优势,被越来越广泛使用。
本文介绍机械清洗工艺在玉门炼化总厂原油储罐清洗中的应用,并提出工艺优化建议。
关键词:原油储罐;机械清洗;优化玉门炼化总厂储运车间原油罐区主要担负全厂外进原油的接收、储存及转输工作。
全厂外进原油按总厂月度生产计划和需求由西部管道通过管输进入储运车间原油储罐,化验分析后,按总厂计划由储运车间原油储罐输转至常减压车间进行炼化加工。
商品原油含有的机械杂质、胶质、泥沙等物质在储罐运行过程中不断沉积附着在罐底和罐壁上,导致进出口管道易被堵塞、降低储罐有效容积、罐底板垢下腐蚀等问题[1]。
为确保原油储罐安全运行,根据相关规定,原油储罐检修年限一般为5~7年,检修前必须清洗。
近几年,储运车间组织对原油储罐进行了安全高效的机械清洗,也发现了机械清洗工艺存在一些不足,仍需改进。
1机械清洗由于人工清罐过程中存在诸多安全问题,近年来逐渐被机械清洗替代。
机械清洗减少人员与油气接触时间,为员工提供安全环境,降低风险,减少泄漏和污染。
并且能够回收原油,减少不必要的损失,有巨大的经济效益和良好的社会效益。
近年来,玉门炼化储运车间原油储罐机械清洗作业主要由某两家清洗分公司公司承担,完成了储罐清洗预定目标。
1.1机械清洗流程及操作过程(以油罐142#清洗过程为例)这两家清洗公司对原油储罐的机械清洗均采用COWS 机械清洗技术,对罐内原油进行加温,泵送至另接油罐中到最低液位[2]。
通过清洗单位安装的临时管道,把机械清洗设备与需要清洗的油罐142#、回收油罐130#连接起来,形成一个封闭的清洗循环系统。
清洗油通过清洗装置增压,经过油罐罐顶上安装的清洗机,向罐内底板沉积淤油层、壁板顶板附着油层等进行高压清洗。
沉积油层破碎后溶解成为一种烃类混合液体,借助回收装置将混合液体回收分离,然后送往回收油罐130#。
某海上油田多级离心泵机械密封优化及冲洗方案改造

某海上油田多级离心泵机械密封优化及冲洗方案改造一、引言海上油田多级离心泵是用于输送原油和天然气的重要装置。
机械密封作为泵的关键部件,承担着泄漏控制和密封功能的重要任务。
然而,在长时间的运行过程中,机械密封容易出现泄漏和磨损等问题,影响泵的正常运行。
因此,对海上油田多级离心泵机械密封进行优化改造,并设计合理的冲洗方案,具有重要的现实意义。
二、机械密封优化改造1.选用合适的材料:针对海上油田工作环境的特殊性,选择耐磨、耐腐蚀的材料,如陶瓷、碳化硅等,提高机械密封的耐腐蚀性和耐磨性,延长其使用寿命。
2.优化密封结构:对机械密封的结构进行优化设计,减少泄漏点,提高密封效果。
采用多层次密封、双密封或管式密封等新型密封结构,提高密封效率,减少泄漏。
3.改善密封性能:采用预压弹簧或其他合适的方法,改善密封面之间的接触压力,减小泄漏量。
通过调整密封面的平行度和垂直度,提高密封的性能。
4.定期维护保养:定期对机械密封进行检查和维护,及时更换密封件,清理密封面,保证机械密封的正常运行。
1.实施离心泵自带冲洗:在设计阶段,加入离心泵自带冲洗功能,通过导入高压清水,冲洗机械密封,避免泄漏和磨损。
2.采用外部冲洗装置:为机械密封设计一个独立的外部冲洗装置,通过增加冷却液或清洗剂的流动,冷却机械密封,清洁密封面,减少泄漏。
3.设计冲洗控制系统:通过设计冲洗控制系统,实现冲洗时间、冲洗压力和冲洗液流量的自动调节,按需提供冲洗液体,保证冲洗效果,并减少能耗。
4.优化冲洗液的选择:根据机械密封的具体要求,选择合适的冲洗液体,如清水、脱盐水、润滑油等,减少对环境的污染。
四、结论通过对海上油田多级离心泵机械密封的优化改造和冲洗方案的改进,可以有效解决泄漏和磨损问题,提高离心泵的工作效率和可靠性,降低维护成本。
同时,合理的冲洗方案还可以减少能耗和环境污染。
因此,这些改进措施对于提高海上油田多级离心泵的性能具有重要的意义。
油罐的机械清洗技术

原油清罐与机械清洗技术摘要:2010年6月,荆门石化相继对成品罐区的原油14#罐,12#罐,8#罐(地下污油罐),15#罐进行了机械清洗。
在短短不到一年的时间里,机械清洗由最初的争议好奇,到最后得到广大领导,专家,技术人员,操作人员的普遍接受和高度认可!机械清洗技术在安全、环保、效益等方面表现出来的优势是人工清洗储罐所无法比拟的。
本文就储罐普遍采用的人工清洗技术与专业机械清洗技术做介绍,让大家更多的对机械清洗技术有所了解。
关键词:人工清洗机械清洗 HSE管理体系环境污染市场前景第一章、传统人工清洗技术油罐在储油过程中,大量的灰尘、杂技和水分进入,还有原料中未去除干净的催化剂,管线和储罐腐蚀产生的锈渣,罐内壁上附着的许多油垢等,都会淤积在罐底,形成油泥,加速油罐腐蚀,严重时还会引起底板穿孔,造成跑油漏油事故;同时,在油品输转过程中,由于杂质较多,堵塞过滤器,降低输送速度,增加过滤设备的损耗,造成设备磨损甚至报废;并且,过多沉积在罐底的油泥使储罐的有效容积减少,影响储油罐的效率。
因此,石油储罐需要定期进行检查维修和清除罐内的淤渣油泥。
目前国内传统的清洗方法主要是利用人工清洗。
人工清洗存在着劳动强度大、施工周期长、安全性差、原油回收率低、清洗效果差,污染环境等诸多问题:1、劳动强度大。
人工清罐的方法,大量的油泥,淤渣要靠作业人员进入罐底手工清除,工作环境差,劳动强度大。
另外因罐内经高温蒸罐后,通风不畅易引起作业人员缺氧窒息的危险。
2、施工周期长。
人工清洗周期时间长,一般平均需要2个月,从而降低了罐区的储存调节能力,直接影响罐区的正常安全工作生产。
3、安全性差。
清罐作业虽然不是经常性的作业,但是往往由于清罐时参与的人员和动用的设备多,并有可能作业时机选择不当,对进罐作业人员安全教育不够,使之对清洗安全作业和安全措施不熟悉和缺乏经验。
并且,油罐在清洗过程中易形成爆炸性混合气体,清罐作业中通常多种点火源并存,增加了着火爆炸的危险性,所以在进行油罐清洗时极易发生火灾、爆炸、中毒、窒息等事故。
石油储罐机械清淤技术
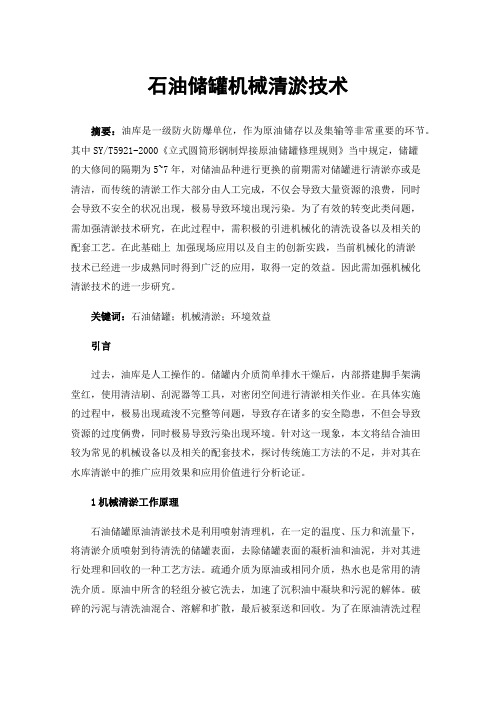
石油储罐机械清淤技术摘要:油库是一级防火防爆单位,作为原油储存以及集输等非常重要的环节。
其中SY/T5921-2000《立式圆筒形钢制焊接原油储罐修理规则》当中规定,储罐的大修间的隔期为5~7年,对储油品种进行更换的前期需对储罐进行清淤亦或是清洁,而传统的清淤工作大部分由人工完成,不仅会导致大量资源的浪费,同时会导致不安全的状况出现,极易导致环境出现污染。
为了有效的转变此类问题,需加强清淤技术研究,在此过程中,需积极的引进机械化的清洗设备以及相关的配套工艺。
在此基础上加强现场应用以及自主的创新实践,当前机械化的清淤技术已经进一步成熟同时得到广泛的应用,取得一定的效益。
因此需加强机械化清淤技术的进一步研究。
关键词:石油储罐;机械清淤;环境效益引言过去,油库是人工操作的。
储罐内介质简单排水干燥后,内部搭建脚手架满堂红,使用清洁刷、刮泥器等工具,对密闭空间进行清淤相关作业。
在具体实施的过程中,极易出现疏浚不完整等问题,导致存在诸多的安全隐患,不但会导致资源的过度俩费,同时极易导致污染出现环境。
针对这一现象,本文将结合油田较为常见的机械设备以及相关的配套技术,探讨传统施工方法的不足,并对其在水库清淤中的推广应用效果和应用价值进行分析论证。
1机械清淤工作原理石油储罐原油清淤技术是利用喷射清理机,在一定的温度、压力和流量下,将清淤介质喷射到待清洗的储罐表面,去除储罐表面的凝析油和油泥,并对其进行处理和回收的一种工艺方法。
疏通介质为原油或相同介质,热水也是常用的清洗介质。
原油中所含的轻组分被它洗去,加速了沉积油中凝块和污泥的解体。
破碎的污泥与清洗油混合、溶解和扩散,最后被泵送和回收。
为了在原油清洗过程中使用纯原油,需要一个与待清洗罐相邻的储油罐,该储油罐也用作原油回收罐。
原油清洗设备、清洗罐以及回收罐通过工艺管道连接在一起,形成一个清洗系统。
2石储罐底油泥的特性及危害在罐底以及罐壁上构成的这层粘合剂作为一种复杂的混合物,主要包含各种碳氢化合物、胶质以及沥青构成,其中包含含有一定量的有毒物质。
浅谈大型储油罐机械清洗
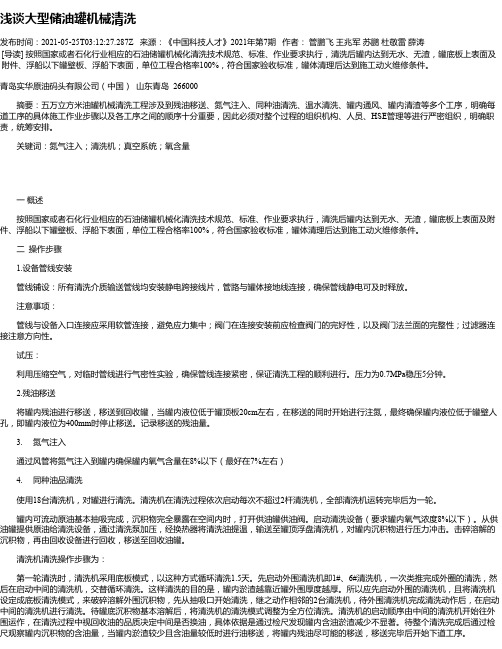
浅谈大型储油罐机械清洗发布时间:2021-05-25T03:12:27.287Z 来源:《中国科技人才》2021年第7期作者:管鹏飞王兆军苏鹏杜敬雷薛涛[导读] 按照国家或者石化行业相应的石油储罐机械化清洗技术规范、标准、作业要求执行,清洗后罐内达到无水、无渣,罐底板上表面及附件、浮船以下罐壁板、浮船下表面,单位工程合格率100%,符合国家验收标准,罐体清理后达到施工动火维修条件。
青岛实华原油码头有限公司(中国)山东青岛 266000摘要:五万立方米油罐机械清洗工程涉及到残油移送、氮气注入、同种油清洗、温水清洗、罐内通风、罐内清渣等多个工序,明确每道工序的具体施工作业步骤以及各工序之间的顺序十分重要,因此必须对整个过程的组织机构、人员、HSE管理等进行严密组织,明确职责,统筹安排。
关键词:氮气注入;清洗机;真空系统;氧含量一概述按照国家或者石化行业相应的石油储罐机械化清洗技术规范、标准、作业要求执行,清洗后罐内达到无水、无渣,罐底板上表面及附件、浮船以下罐壁板、浮船下表面,单位工程合格率100%,符合国家验收标准,罐体清理后达到施工动火维修条件。
二操作步骤1.设备管线安装管线铺设:所有清洗介质输送管线均安装静电跨接线片,管路与罐体接地线连接,确保管线静电可及时释放。
注意事项:管线与设备入口连接应采用软管连接,避免应力集中;阀门在连接安装前应检查阀门的完好性,以及阀门法兰面的完整性;过滤器连接注意方向性。
试压:利用压缩空气,对临时管线进行气密性实验,确保管线连接紧密,保证清洗工程的顺利进行。
压力为0.7MPa稳压5分钟。
2.残油移送将罐内残油进行移送,移送到回收罐,当罐内液位低于罐顶板20cm左右,在移送的同时开始进行注氮,最终确保罐内液位低于罐壁人孔,即罐内液位为400mm时停止移送。
记录移送的残油量。
3. 氮气注入通过风管将氮气注入到罐内确保罐内氧气含量在8%以下(最好在7%左右)4. 同种油品清洗使用18台清洗机,对罐进行清洗。
- 1、下载文档前请自行甄别文档内容的完整性,平台不提供额外的编辑、内容补充、找答案等附加服务。
- 2、"仅部分预览"的文档,不可在线预览部分如存在完整性等问题,可反馈申请退款(可完整预览的文档不适用该条件!)。
- 3、如文档侵犯您的权益,请联系客服反馈,我们会尽快为您处理(人工客服工作时间:9:00-18:30)。
大型外浮顶原油储罐机械清洗方案优化
摘要:针对华德石化有限公司在役的大型外浮顶原油储罐运用cows机械清洗技术,进行机械清洗方案的优化,使cows清洗技术在大型油罐的清洗上运用更成熟,不断提高清罐效率和安全系数。
关键词:大型油罐cows 技术优化
一、前言
华德石化拥有在役储油罐14座,其中马鞭洲首站12座5×104m3外浮顶储油罐,南边灶油库2座10×104m3外浮顶储油罐,为提高储运能力,南边灶油库正在建设的10×104m3外浮顶储油罐2座,5.5×104m3外浮顶储油罐2座(预计2013年8月份投产),为满足广州石化接卸原油多元化需求,还会有一些储油罐建成投产,华德石化1997年投产至今储运设备安全平稳运行,根据sy/t5921-2000标准中规定大型油罐检修周期为5~7年,2004年首次制定清罐检修方案,并委托茂名众合公司对第1台罐进行了机械清洗,取得了较好效果,截止2013年5月,已完成了16座储油罐机械清洗作业。
由于马鞭洲首站地处孤岛,公用工程设施有限,不能为清罐提供驱动用电源和蒸汽,所以对cows(crude oil washing system)清罐技术的运行又提出了更高要求。
二、清洗技术原理及清洗过程
1.清洗技术原理
cows机械清洗是利用高压油喷射流将沉积、附着的油渣、蜡质等
有机物击碎、溶解,并将其还原成接近标准的原油,最大限度地将罐底残油予以回收。
清洗过程分为同种油清洗和温水清洗,利用同种类油品为清洗油,由清洗泵增压,通过清洗机冲射罐顶顶板、罐壁和罐底,溶解一切可溶性附着物,将过滤后的油品全部回收,最后利用温水进行全方位的清洗。
详见原油罐机械清洗施工原理流程图:原油罐机械清洗施工原理流程图
2.cows清洗设备组成
2.1回收装置a:利用液环真空泵提供动力将清洗油罐内剩余油抽吸出来,在用泵移送到回油罐;在进行油水分离时,将油水混合液送到油水分离槽。
2.2清洗装置b:提供同种清洗油加压给清洗机,对清洗油罐进行同种油清洗;在油水分离及温水清洗时,将油水槽内的温水抽出加压给清洗机对清洗油罐进行温水清洗。
2.3油水分离槽:包括20m3水箱一个和0.5 m3的收油槽一个。
2.4过滤器2台:尺寸dn 200,pn1.6,用于油移过程中的油过滤,将油渣及杂物滤出。
2.5清洗枪:清洗油及温水通过清洗装置b加压后,经清洗枪产生喷射流击碎、溶解清洗罐内的淤渣。
2.6惰性气体装置(锅炉、制氮机):锅炉燃烧产生的废气和制氮机产生的n2作为惰性气体加注进清洗罐,降低罐内的氧含量和可燃气体含量。
2.7气体浓度检测装置:自动检测清洗油罐内的氧气浓度和可燃
气体浓度,并指示和记录其测试值。
2.8柴油发电机:为cows的设备运转提供电源。
3.cows清洗施工过程
3.1临时设置工程,制定施工方案、工艺处理方案、按照施工方案进行设备及管道、电气系统、惰性气体装置、可燃气检测系统等设备的安装,进行系统整体的气密性试验。
3.2清罐前工艺处理工作:确定好供油罐和回油罐的液位控制,用油泵进行抽低位操作,为加装盲板和安装供、回油管做准备,工艺处理后将油罐交出检修。
3.3同种油清洗工程:由清洗装置提供动力,用清洗机喷射供油罐提供的干净油,击碎、溶解油罐内的油渣。
3.4温水清洗工程:通过同种油清洗后,基本上除掉了油罐内的凝油和淤渣,但为了进一步进行脱油,要进行温水(冷水在油水分离槽内加热到50~60℃)清洗。
这种清洗,是用清洗装置b抽取油水分离槽中温水,加压后用清洗机喷射打到油罐各个部位,再用回收装置a抽出油水混合物打回油水分离槽内,使油和水分离,将浮油用外加收油泵移送给接收油罐,如此循环,边加热边进行清洗,最终把残油移送干净。
3.5安全防爆工程:本作业作为安全措施,往油罐内的空间部分注入氮气,将氧气浓度保持在8%以下的惰性环境,氮气的注入应从同种油清洗一直持续到热水清洗结束。
3.6内部最终清扫:打开油罐检查孔,足够时间的通风排掉罐内
残留可燃气体,经检测合格后,清扫局部清洗不良部位,把残余积水、淤渣等清除到罐外。
清洗程度可达到直接动火条件。
三、cows清洗施工过程中的技术问题及优化
以马鞭洲首站2#罐清罐为例,对每个步骤提出优化。
1.cows地面装置设置优化
1.1供油口选择2#罐和相邻1#罐的抽罐底油管线盲端(共2处)连接供油软管,使供油量充足,提高供油能力。
1.2清洗油罐抽吸口的设定要尽可能多,并沿油罐外周分布要均匀,这样就能从油罐各个部位均匀抽吸,提高抽吸效果,能够避免罐底板不平造成的抽吸不均匀现象。
2#罐抽吸口设定在3个人孔和2个排污门,共5处。
1.3降低抽吸口高度,在保证清洗效果的同时就可以减少单次供油量,单次运转更灵活,2#人孔处抽吸口采用向下延伸设置,管口距离底板面为30mm,排污门处抽吸管设置为直管,管口距离底板面设置为40mm。
1.4抽吸移送管道与原有设备连接时,为了避免因热膨胀、收缩、振动而导致设备损伤,要使用挠性软管,其后安装阀门。
为了在抽吸管道因淤渣等堵塞时,能通过清洗液倒流来清除堵塞而敷设倒洗管道。
1.5可燃性气体采样设3个插入点进行监测,取平均值,由经验得出,一般插入深度控制在单盘下30~40mm,可以与可燃气体充分接触,插入太深容易吸出油。
2.工艺处理方案优化
将2#罐输至低位2.5m(单盘起伏高度为1.7m),选择轻质原油(9#罐阿曼油,密度867kg/m3,50℃时粘度为12.7mm2/s)作为清洗油的供油,选择好回油罐(5#罐,液位控制在8m,给出足够的空间回油)。
用油泵对清洗油罐进行抽低位作业,抽至油泵抽空(使剩余液位满足打开人孔安装回油管的液位要求)。
要在油罐抽低位作业与注氮时间上进行紧密接合,一旦浮盘支柱着底,便会产生油气空间,应立即开启惰性气体装置进行惰性气体的加注,使油气空间中氧含量降低,破坏危险环境。
3.清洗机在单盘上的位置布置优化
3.1清洗机采用大凤am型喷射清洗机,驱动使用气动马达,喷嘴驱动角度水平方向0~360℃,垂直方向0~140℃,进行全面清洗,将罐顶部分支拔出(支柱拔出数控制在支柱总数的20%以下,5×104m3罐单盘支柱总数160根),利用罐顶支柱口安装固定清洗机,3.2清洗机的安装要避开管内软管和加热盘管等附件,在清洗罐底板时,喷嘴设置高度距底板1.3m,清洗底板最大有效清洗半径为17m,清洗顶板时,要放低喷嘴位置,设定距底板高度1m为宜,清洗顶板最大有效清洗半径13m,喷嘴的旋转速度设定为1分45秒~2分,全面清洗油罐时,以顶板清洗有效距离13m为基准设定。
3.3由于油罐的外周部底板比其他部位低,故残油、淤渣多集中在外周部,集中在进油口对面位置的淤渣最多。
另外,由于外周部罐壁刮板及一次密封处结构复杂,加热盘管也沿外周底板设置,有
时会产生喷射死角部位,考虑到这一点,清洗机的配置设计要以外周为起点,选定距壁板5~8m位置上的支柱进行外周的配置,再依次决定内周部分的设置,在清洗机的配置上,使各个清洗机的有效清洗范围相互重合, 2#罐共布设18台清洗机才能进行全面覆盖清洗。