什么是PFMEA
FMEA参考手册解读1

九、PFMEA的说明和介绍9.1、PFMEA及其作用的简介制造过程的输出是产品,合格的产品是预期的输出。
通过PFMEA能识别过程变量,知道哪些因素影响产品质量。
过程特性就是影响产品质量的原因,过程特性不但要设计合理,而且还需要在后续的生产过程中进行管控,以确保过程特性符合管控要求。
比如工艺参数属于过程特性,有时即便工艺参数设计合理,但在生产过程中也可能需要对工艺参数进行监视,比如装配过程中的压装力的实时监控,比如电动扳手的扭力监控等,因为只有工艺参数满足设计时的要求,才能确保产品质量,所以制造过程的设计不但要确保过程特性设计的合理性,还要考虑制造过程后续的管控,以确保制造过程不生产不合格品,不流出不合格品,这才是制造过程设计的定位。
从制造过程设计角度考虑不流出不合格品,这也是制造过程设计的范围。
但产品设计就不同了,产品特性或设计特性设计合理了,就进行图纸发布,虽然量产后也需要对产品特性或产品质量进行管控或探测,但后续的产品质量管控或探测就不属于产品设计的范围了。
备注:和DFMEA相同的或类似的原则和内容,在第九章中就不再重复介绍。
PFMEA应当起一个催化剂的作用,通过PFMEA这个工具提供一个促进交流的平台,所以PFMEA的表格格式设计和内容应利于多方论证或跨职能交流,比如可以根据PFMEA中的失效影响,识别受影响的职能或人员参与到PFMEA的编制和评审过程中。
9.2、PFMEA的使用时机PFMEA应在可行性论证阶段或之前就启动,说明在可行性分析的时候就需要应用风险分析,如果是基于分析结果进行论证,就是在论证之前就应用风险分析。
对于过程FMEA应在工装和制造设备的开发、采购之前启动,也就是在决定买什么样的工装和设备之前就已经进行了FMEA分析,再细节一点,在工装设备的制造加工前也经过了FMEA分析。
如果型号或要求都确定了,采购订单都签了,再去分析有什么风险,FMEA的使用时机明显就滞后了。
从FMEA参考手册中也可知道,工装和设备也是需要进行FMEA分析的,至于是综合起来一起分析,还是基于一定条件分开分析,需要视实际情况而定。
DFMEA于PFMEA的区别

DFMEA于PFMEA的区别
潜在实效模式分析中为何分为DFMEA与PFMEA,两者具体的代表意义及区别是什么?
DFMEA:设计FMEA,应用于产品设计时,对产品失效的分析,检查产品设计是否满足所有要求,包括产品功能、性能、法规符合性、顾客特殊要求、可维修性、可用性等要求,有多大的风险,该怎样改进;
PFMEA:过程FMEA,应用于产品实现过程设计,包括原材料采购、零件生产、制造、处理、成品组装、运输、交付等一些列过程,其中对产品性能以及交付能力影响的因数进行分析,确认有多大的风险,该怎样改进。
DFMEA 直接对应的产品失效的模式,而PFMEA则针对各个环节可能造成产品的失效进行分析,两个过程似乎反着进行.
D为设计的FMEA,侧重产品本身的设计合理化和风险性评估,不考虑制程影响;
DFMEA和PFMEA区别:
1.输入不同
DFMEA输入QFD
PFMEA输入Process Mapping和C&E Matrix
2.分析角度不同
DFMEA分析:设计不合理导致的产品失效,不考虑制造本身的失效,只反映设计本身存在问题
PFMEA分析:制造过程不符合要求导致的产品失效,假设设计是合理
3.目的不同
DFMEA:识别出关键/重要的产品特性,并制定相关措施保证这些特性达到设计目的PFMEA:识别出关键/重要的过程特性,并制定相关措施保证这些特性符合过程目的。
什么是pfmea
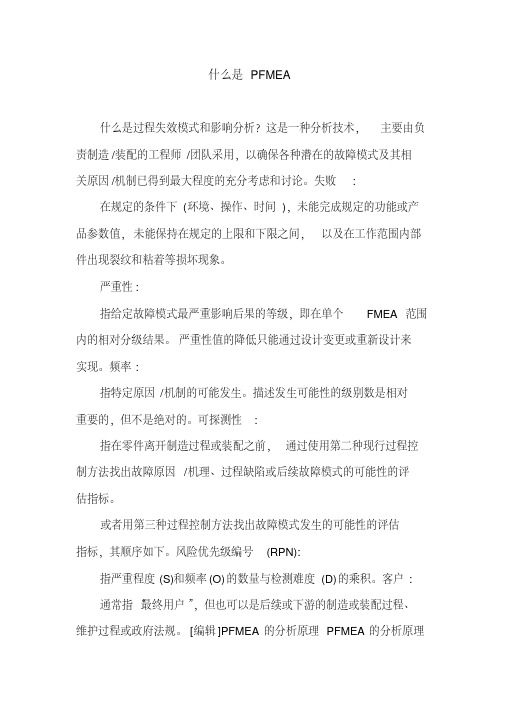
什么是PFMEA什么是过程失效模式和影响分析?这是一种分析技术,主要由负责制造/装配的工程师/团队采用,以确保各种潜在的故障模式及其相关原因/机制已得到最大程度的充分考虑和讨论。
失败:在规定的条件下(环境、操作、时间),未能完成规定的功能或产品参数值,未能保持在规定的上限和下限之间,以及在工作范围内部件出现裂纹和粘着等损坏现象。
严重性:指给定故障模式最严重影响后果的等级,即在单个FMEA范围内的相对分级结果。
严重性值的降低只能通过设计变更或重新设计来实现。
频率:指特定原因/机制的可能发生。
描述发生可能性的级别数是相对重要的,但不是绝对的。
可探测性:指在零件离开制造过程或装配之前,通过使用第二种现行过程控制方法找出故障原因/机理、过程缺陷或后续故障模式的可能性的评估指标。
或者用第三种过程控制方法找出故障模式发生的可能性的评估指标,其顺序如下。
风险优先级编号(RPN):指严重程度(S)和频率(O)的数量与检测难度(D)的乘积。
客户:通常指“最终用户”,但也可以是后续或下游的制造或装配过程、维护过程或政府法规。
[编辑]PFMEA的分析原理PFMEA的分析原理如下表所示,其中包括以下关键步骤:(1)识别与过程生产或产品制造过程相关的潜在故障模式和原因;(2)评估失败对产品质量和顾客的潜在影响;(3)识别减少故障发生或故障情况的过程控制变量,并制定纠正和预防措施;(4)编制潜在失效模式分类表,确保优先控制严重失效模式;(5)跟踪控制措施的实施,更新故障模式分类表。
(1)“过程功能/要求”:指被分析的过程或过程。
该过程或过程可以是技术过程,例如焊接、产品设计、软件代码编写等。
或管理过程,如规划、设计评审等。
尽可能简单地解释过程或程序的目的。
如果过程包括许多具有不同故障模式的程序,这些程序或要求可以列为独立的程序。
(2)“潜在故障模式”:它是指过程中可能出现的不符合过程要求或设计意图的形式或问题点。
它是对不符合要求的特定过程的描述。
什么是PFMEA
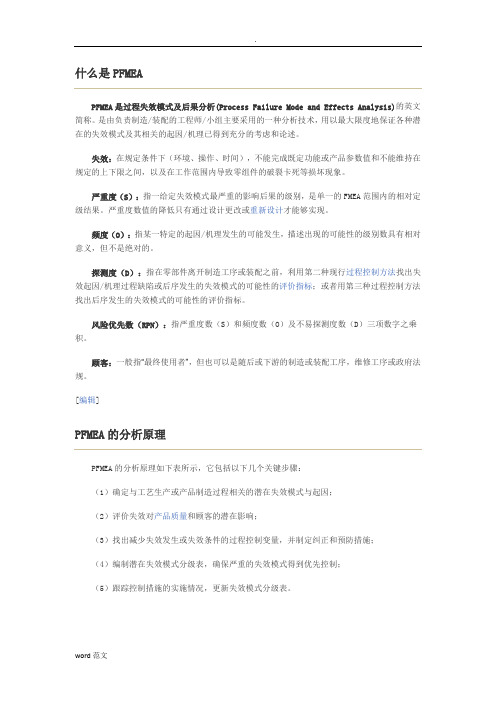
什么是PFMEAPFMEA是过程失效模式及后果分析(Process Failure Mode and Effects Analysis)的英文简称。
是由负责制造/装配的工程师/小组主要采用的一种分析技术,用以最大限度地保证各种潜在的失效模式及其相关的起因/机理已得到充分的考虑和论述。
失效:在规定条件下(环境、操作、时间),不能完成既定功能或产品参数值和不能维持在规定的上下限之间,以及在工作范围内导致零组件的破裂卡死等损坏现象。
严重度(S):指一给定失效模式最严重的影响后果的级别,是单一的FMEA范围内的相对定级结果。
严重度数值的降低只有通过设计更改或重新设计才能够实现。
频度(O):指某一特定的起因/机理发生的可能发生,描述出现的可能性的级别数具有相对意义,但不是绝对的。
探测度(D):指在零部件离开制造工序或装配之前,利用第二种现行过程控制方法找出失效起因/机理过程缺陷或后序发生的失效模式的可能性的评价指标;或者用第三种过程控制方法找出后序发生的失效模式的可能性的评价指标。
风险优先数(RPN):指严重度数(S)和频度数(O)及不易探测度数(D)三项数字之乘积。
顾客:一般指“最终使用者”,但也可以是随后或下游的制造或装配工序,维修工序或政府法规。
[编辑]PFMEA的分析原理PFMEA的分析原理如下表所示,它包括以下几个关键步骤:(1)确定与工艺生产或产品制造过程相关的潜在失效模式与起因;(2)评价失效对产品质量和顾客的潜在影响;(3)找出减少失效发生或失效条件的过程控制变量,并制定纠正和预防措施;(4)编制潜在失效模式分级表,确保严重的失效模式得到优先控制;(5)跟踪控制措施的实施情况,更新失效模式分级表。
(1)“过程功能/要求”:是指被分析的过程或工艺。
该过程或工艺可以是技术过程,如焊接、产品设计、软件代码编写等,也可以是管理过程,如计划编制、设计评审等。
尽可能简单地说明该工艺过程或工序的目的,如果工艺过程包括许多具有不同失效模式的工序,那么可以把这些工序或要求作为独立过程列出;(2)“潜在的失效模式”:是指过程可能发生的不满足过程要求或设计意图的形式或问题点,是对某具体工序不符合要求的描述。
PFMEA
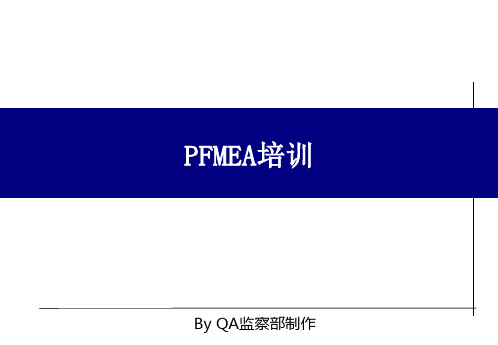
哪些操作步骤循环返工
与当前和期望之间有什么差异
2016/3/7
16
一、PFMEA基本知识
流程图的案例
2016/3/7
17
一、PFMEA基本知识
PFMEA开发应用的其它工具 • DFMEA • 产品/过程图纸和设计记录 • 过程清单 • 关系(特性)矩阵图 • 内部和外部的不符合(历史数据资料) • 质量和可靠性历史等
2016/3/7 26
二、PFMEA栏位项目介绍
过程功能 要求 潜在 失效模式 失效 潜在后果
严 等 重 级 度
潜在失效 起因/机理
频 度
现行 过程控制 预防 探测
探 测 度
R P N
建议措施
责任与 目标 完成日期
行动结果
频 采行措施 重 度 测 P 度 度 N 严 探 R
典型的失效模式:(体现产品特性上的失效)
可以做什么? -设计变更 -过程变更 -特别的控制 -标准、程序或 指南的更改
探测它 的方法 有多好?
一、PFMEA基本知识
人
机
料
失效模式 一般是发生 在产品上
失效后果 一般是指对 下工程或最 终顾客的影响
法
环
测
聚焦于导致产品失效的过程变异
2016/3/7 6
一、PFMEA基本知识
PFMEA是一种动态文件,主要体现在:
2016/3/7 28
二、PFMEA栏位项目介绍
过程功能 要求 潜在 失效模式 失效 潜在后果
严 等 重 级 度
潜在失效 起因/机理
频 度
现行 过程控制 预防 探测
探 测 度
R P N
建议措施
责任与 目标 完成日期
PFMEA教程
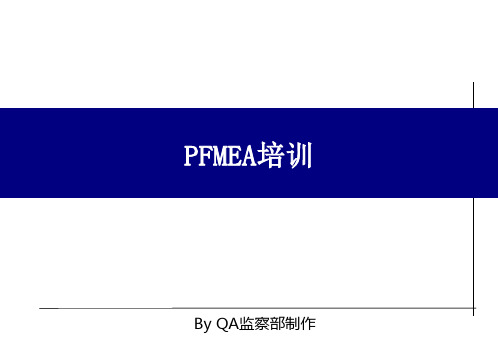
探 测 度
R P N
建议措施
责任与 目标 完成日期
行动结果
频 采行措施 重 度 测 P 度 度 N 严 探 R
潜在失效的后果:就是失效模式对系统功能的影响,就如顾客感受 的一样 失效后果应从具体的系统、子系统、零件和系统之间的关系来考虑 要根据顾客可能发现或经历的情况来描述失效产生的后果 顾客可能是内部的顾客,也可能是外部最终顾客,包括最终使用者、 组装客户、更高级系统、下一道工序,售后服务工作 PFMEA中的产品失效后果与DFMEA中的失效后果应该相一致。如 果失效模式可能影响安全或导致不符合法律法规,应在PFMEA中清 晰地加以阐述 如果潜在失效模式本身能预防下游去处理则评价制造影响,不需 要进一步分析。
2018/10/18
23
二、PFMEA栏位项目介绍
过程步骤 功能/要求 潜在 失效模式 失效 潜在后果
严 等 重 级 度
潜在失效 起因/机理
频 度
现行 过程控制 预防 探测
探 测 度
R P N
建议措施
责任与 目标 完成日期
行动结果
频 采行措施 重 度 测 P 度 度 N 严 探 R
填入被分析项目/工序的名称和编号 用尽可能简明的文字来说明被分析过程/工序要满足设 计意图的功能/要求 如果该项目有多种功能或多个工序,且有不同的失效 模式,应把这些工序独立列出。
PFMEA培训
By QA监察部制作
一、PFMEA基本知识
默菲定律:所有可能出错的地方都将会出错!
那么,在产品制造之前我们都担心一些什么呢?
FMEA:将问题扼杀在摇篮之中
一、PFMEA基本知识
失效的定义: • 在规定条件下(环境、操作、时间)不能完成既定功能 • 在规定条件下,产品参数值不能维持在规定的上下限 之间; • 产品在工作范围内,导致零组件的破裂、断裂、卡死 等损坏现象。
FMEA知识测试题目汇总分析
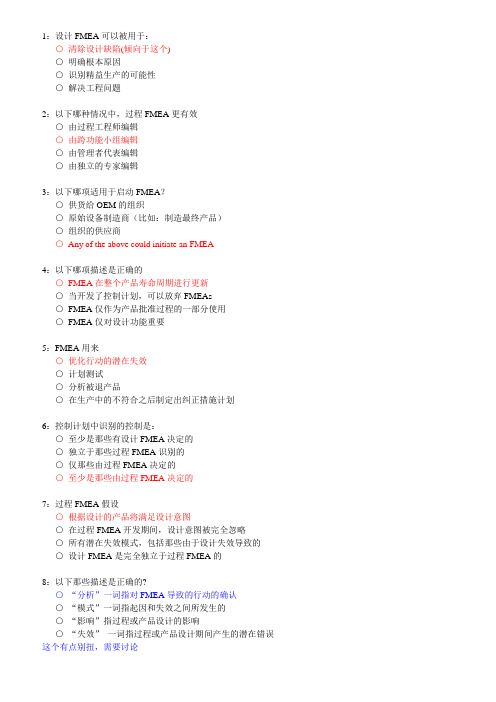
1:设计FMEA可以被用于:○清除设计缺陷(倾向于这个)○明确根本原因○识别精益生产的可能性○解决工程问题2:以下哪种情况中,过程FMEA更有效○由过程工程师编辑○由跨功能小组编辑○由管理者代表编辑○由独立的专家编辑3:以下哪项适用于启动FMEA?○供货给OEM的组织○原始设备制造商(比如:制造最终产品)○组织的供应商○Any of the above could initiate an FMEA4:以下哪项描述是正确的○FMEA在整个产品寿命周期进行更新○当开发了控制计划,可以放弃FMEAs○FMEA仅作为产品批准过程的一部分使用○FMEA仅对设计功能重要5:FMEA用来○优化行动的潜在失效○计划测试○分析被退产品○在生产中的不符合之后制定出纠正措施计划6:控制计划中识别的控制是:○至少是那些有设计FMEA决定的○独立于那些过程FMEA识别的○仅那些由过程FMEA决定的○至少是那些由过程FMEA决定的7:过程FMEA假设○根据设计的产品将满足设计意图○在过程FMEA开发期间,设计意图被完全忽略○所有潜在失效模式,包括那些由于设计失效导致的○设计FMEA是完全独立于过程FMEA的8:以下那些描述是正确的?○“分析”一词指对FMEA导致的行动的确认○“模式”一词指起因和失效之间所发生的○“影响”指过程或产品设计的影响○“失效”一词指过程或产品设计期间产生的潜在错误9:PFMEA开始于○当评审过程流程图的时候,第一个被小组认为“高风险”的过程步骤○第一个生产过程步骤○第一个关键过程步骤○提出的过程流程图的第一个步骤10:所有的FMEAs关注于○仅产品设计○潜在后果可能影响作为最终使用者的顾客○产品开发的设计和顾客希望需要的●产品或过程的设计11:过程FMEA○为组织提供工具以获取产品设计的失效○不考虑设计FMEA,如果可用,作为其分析的一部分●从降低失效的风险方面支持生产过程的开发○在过程方法中是可选的需要查书证实!12:过程FMEA○依靠产品设计更改,克服过程中的缺陷○不应利用流程图建立,流程图用于确认与每个操作关联的产品/过程特性●由开发过程希望做什么和不希望做什么开始,比如:过程的意图○在过程方法中是可选的13:在准备生产过程的过程FMEA的时候,FMEA小组需要○不要考虑没有符合的输入零件/材料的可能性○仅考虑在常规的操作条件下产生的那些失效的失效模式○忽略设计FMEA,以预防可能对过程有害的偏倚或限制○假设出入零件/材料是正确的14:当材料由于现有产品发生更改,FMEA小组需要对以下哪些情况的新的潜在失效模式进行分析:○当前FMEA中的所有项目○新材料,以及可能被影响的产品实现系统的任何等级○新材料,以及任何其他装配或完工变更○仅对新材料15:如果可能的话,在过程FMEA中,更倾向于以下哪种行动作为过程控制的方法?○预防失效模式的起因/机制的发生。
PFMEA开发教程
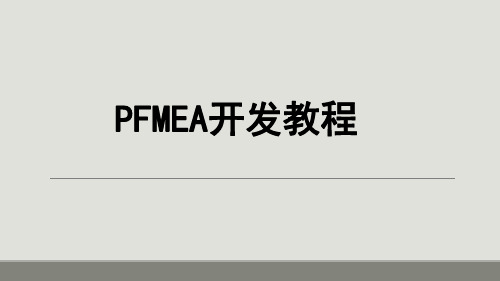
PFMEA开发教程目录•什么是PFMEA1•为什么要做PFMEA2•什么时候做PFMEA3•由谁来做PFEMA4•如何做PFMEA5•PFMEA和APQP的关联6PFMEA 中英文全称:过程失效模式和后果分析-> Process Failure Mode & Effect Analysis失效模式:指制造过程无法达到预定或规定的要求所表现出的现象;如:不合格品、不良设备状况后果:指失效模式在内部、车厂及顾客处(包括后续工序)所造成的不良影响PFMEA定义及其含义:PFMEA是一种分析工具,用于识别出产品或过程的潜在失效,从而可以采取相应的纠正措施FMEA的发展历史:●1949年由美国军方创建用于国防工业●上世纪50年代被航空航天工业采纳●上世纪70年代,汽车工业将FMEA作为在对其零件设计和生产制造的评审项目的重要部分-Ford公司首次应用于汽车工业●上世纪80年代,产品事故责任的费用突升和不断的法庭起诉事件发生,使FMEA成为降低事故的不可缺少的重要工具●1993年美国汽车工业行动集团(AIAG)首次发行了FMEA标准,定义了对OEM和供应商最基本的FMEA要求●2008年AIAG发布FMEA (第四版)FMEA的主要类型:●DFMEA: 在产品正式设计发布之前分析潜在失效—专注于产品由于设计造成的和功能相关的潜在失效●PFMEA: 用于分析制造和装配过程—专注于过程由于设计和操作造成的和功能相关的潜在失效模式0246810类别1类别2类别3110100设计开发过程开发售后阶段010080602040成本($)减少变更成本风险1:10:100设计改起来很麻烦,这个风险等以后有问题再改吧?FMEA评估和减小风险做PFMEA 之后,我们产品不良率能降低多少PPM 呢?M2M3.1M3.2M3.3M3PPAP发布初版u p d a t eu p d a t eu p d a t eu p d a t ePFMEA制作IQC SQEMEDSMT PQOQA评审PMMPPFMEA 是团队的成果过程步骤/功能要求潜在失效模式潜在失效影响潜在失效原因严重度频度控制预防控制探测探测度RPN5、DIETZ的PFMEA分析理论举个例子目前公司内所有的PCB板都会镭雕二维码以及相关信息,小小的二维码在追溯以及防错等方面发挥着重大作用。
PFMEA复习大纲201208

PFMEA复习大纲●什么是PFMEA?它有什么作用?PFMEA是过程潜在失效模式及后果分析)是由负责制造/装配的工程师的小组,对工艺流流程的评估、识别和消除制造/服务过程中每一个环节的潜在的隐患,最大限度地保证潜在的失效模式及其相关的起因/机理得到考虑。
作用:提高产品功能保证和可靠性,降低担保费用和折扣费用,缩短开发周期,减少批量投产时发生的问题,提高准时供货信誉,降低开发成本,改进服务,改善内部信息交流,将责任和风险管理联系起来。
1.过程FMEA的顾客是指?在PFMEA中,顾客是指最终使用者,也可能是后续或下工程制造或装配厂,或者是服务作业、政府法规。
2.过程FMEA是由哪些人组成的?负责制造过程的工程师主导,由装配、制造、物料、质量、服务与组织,以及负责下一阶段的装配部门。
3.过程FMEA在哪个阶段之前,哪个阶段之后初次执行?PFMEA应开始在可行性阶段之前进行,在工装或设备开发采购之前。
在第三阶段过程设计开发阶段初次执行。
4.减少频度的方法?降低严重度等级、降低发生率、探测度等级。
可以是防错、统计过程控制(SPC)或也可以是加工后评价的过程控制,修改尺寸公差、修改设计降低或取代零件弱点、修改材料规格、修改过程设计(设备、工装、参数)5、P FMEA识别的影响因素有哪些?机器变差、作业员变差、工装变差、材料/零部件变差、工具变差、量具变差、环境变差、预防性维护变差、过程参数设定变差6、FMEA、PFMEA、SEV、OCC、DET、RPN的中文意思是什么?SEV/OCC/DET均有几个评分等级?DFMEA设计失效模式及后果分析、PFMEA过程失效模式及后果分析、SEV严重度、OCC频度、DET探测度、RPN风险顺序数。
SEV/OCC/DET各有10各评分等级8、FMEA的目的是什么?FMEA是一种分析方法,致力于通过APQP确保所有潜在的问题都被考虑。
识别过程的功能和要求;识别与产品和过程相关的潜在失效模式;评估这些失效对顾客造成的潜在影响;识别制造或装配过程中潜在失效的起因和过程的变化,并且据以控制降低发生频次或失效情况的探测;识别过程的变化,并着重于过程控制;编制潜在失效模式的等级排序,并建立预防、纠正措施的优先体系;记录制造/装配过程的结果并以文件化。
PFMEA 过程失效和结果分析

13
PFMEA 表格模版举例 表格模版举例
14
过程失效的潜在原因
• 漏操作 • 误加工 • 错误的安装 • 遗失零备件 • 备件错用 • 错误的处理半成品 • 错误的操作 • 错误的调整 •设备润滑不当 设备润滑不当 •使用错误的工具
• 差的控制程序 • 不正确的设备维护 • 错误的配方 • 老化 • 缺乏安全 • 错误的机器设置 • 执行错误的程序 • 环境 • 连接错误 差的FMEA系统 • 差的 系统
6
PFMEA 流程
实施行动计划降低 4 RPN
3 确定 S/O/D 的分级表
CI
D
5 检查并促进行
计算RPN并制
定优先计划
动计划的实施
只要一个流程没有从生产 线上退出, 线上退出,PFMEA 将永远 不会结束 6 执行可控的
C
2 绘制流程
图
1
标准程序
组队
7 改进后再次评
P
估 RPNs
A
识别失效模式: 识别失效模式 产品未能符合设计的意图或过程的要求 识别潜在要因 : 应按失效为何发生的迹象来确定,按照可纠正或可控制的情形来描述 识别潜在后果: 识别潜在后果:如果失效模式没有预防或纠正而导致顾客察觉的失效模式后果来定义
19
PFMEA 是 ISO9001 的一部分
Process Failure Mode and Effects Analysis
Statistical Process Control Quality System Analysis
Measurement System Analysis
ISO-9001 QS-9000
•操作步骤是否重复还是无顺序? •这些步骤是否频繁产生失误? •是否有循环的返工?
pfmea严重度打分规则

pfmea严重度打分规则PFMEA是一种常用的风险分析工具,用于评估产品或过程中潜在的失效模式和影响。
其中,严重度是PFMEA中一个重要的评分指标,用于衡量失效模式对产品或过程的潜在影响程度。
本文将介绍PFMEA严重度打分规则,以帮助读者更好地理解和应用该评分指标。
一、什么是严重度?严重度是指失效模式对产品或过程的潜在影响程度。
在PFMEA中,严重度评分通常基于两个主要因素:失效后果的严重性和失效发生的频率。
评分范围一般为1到10分,分值越高表示失效对产品或过程的影响越严重。
二、PFMEA严重度打分规则1. 10分:失效会导致严重的安全隐患,可能导致人员伤亡或重大财产损失,且失效发生的频率非常高。
2. 9分:失效会导致严重的安全隐患,可能导致人员伤亡或重大财产损失,且失效发生的频率较高。
3. 8分:失效会导致较严重的安全隐患,可能导致人员受伤或财产损失,且失效发生的频率较高。
4. 7分:失效会导致一定的安全隐患,可能导致人员受伤或财产损失,且失效发生的频率较高。
5. 6分:失效会导致轻微的安全隐患,可能导致人员受伤或财产损失,且失效发生的频率较高。
6. 5分:失效会导致一定的安全隐患,但可能导致的人员伤亡或财产损失较小,且失效发生的频率中等。
7. 4分:失效会导致轻微的安全隐患,但可能导致的人员伤亡或财产损失较小,且失效发生的频率中等。
8. 3分:失效会导致轻微的安全隐患,但可能导致的人员伤亡或财产损失较小,且失效发生的频率较低。
9. 2分:失效会导致一定的安全隐患,但可能导致的人员伤亡或财产损失较小,且失效发生的频率较低。
10. 1分:失效对安全没有直接影响,只会导致一些质量问题或影响产品的外观。
三、严重度打分规则的应用在实际应用中,评定失效的严重度需要结合具体的产品或过程进行分析。
可以通过以下步骤来进行评定:1. 确定失效模式:仔细分析产品或过程中可能出现的失效模式,包括其原因和后果。
2. 评估失效后果的严重性:根据失效后果对人员安全和财产损失的影响程度,进行评估和打分。
PFMEA输入信息的主要来源是什么?

PFMEA输入信息的主要来源是什么?
PFMEA输入信息的主要来源是什么?PFMEA也称为过程FMEA,是以过程为导向的潜在失效的分析技术,用以对新的或更改过程的一种规范化的评审和分析,从而预防、解决或监控新的或更改过的产品项目的潜在过程问题。
PFMEA是一种动态文件,应当在开始生产之前、产品质量策划过程中进行。
PFMEA以过程为导向,分析从原材料入库到成品出库的整个过程,包括材料搬运、接收、运输、储存和标识等所有可能影响制造和装配作业的过程。
PFMEA由负责过程的工程师或小组领导组织小组成员进行。
PFMEA以过程流程图所分析的过程为基础和导向,确定范围,以DFMEA分析的产品后果识别、特殊特性清单、过往历史信息等为输入,编制PFMEA表格。
PFMEA输入信息的主要来源包括:
①过程流程图。
②DFMEA。
③图样和设计记录。
④特殊特性清单。
⑤过程清单。
⑥特性矩阵图。
⑦内部和外部发生的不符合。
⑧质量和可靠性历史。
⑨以往类似过程的PFMEA。
天行健六西格玛顾问表示:PFMEA是制造过程的FMEA,输入是工艺流程图和矩阵图,只有那些会对产品品质造成直接影响的工序才需要进行分析,如烘料、储存等。
而有些工序则不需要,如检验工序、调参数等。
PFMEA_详解

如新设备的投入运行,我们亦可以预先进行MFMEA,分析、考虑由于设备可能造成的产 品品质问题及可靠度等原因,预防采取措施消除不良因素;现有设备、特定的一种设 备在运行中出现的设备故障等均采用FMEA进行改善,以确保设备的正常运转。
工序:铣沉孔(工序库存2000件)….安装门开关
失效模式:未加工 失效原因:铣刀断——4次/年 过程控制方法:
更换铣刀——1次/1000件 S=
O= 7or8 8(PPM=4*1000/200,000*106=20000)
D= 9or10(更换铣刀不是检测手段,所以此处可以按没有控制手段处理)
RPN
PFMEA
15.频度(Occurrence)
指具体的失效模式发生的频率(概率).或可获得的话,用历史数据.通常是由 授权单位,退货部门,维修部门和废品报告部门衡量. 若无法获得历史数据,则用客观评价.
16.现行过程控制 是对尽可能防止失效模式的发生,或者探测 将发生的失效模式 的控制的描述. 两类控制方法: 1)预防——事先措施(防错)
产量:200,000件/年
工序:铣沉孔(工序库存20件)….安装门开关
失效模式:未加工 失效原因:铣刀断——4次/
年 过程控制方法:更换铣刀——1次/1000
件
止通规——1次/100件 后装配工序使用防错 检测仪
S= O= D= RPN7=
3(PPM=4*20/200,000*106=400)
品:门铰链总成 产
返修45分钟
量:200,000件/年
工序:铣沉孔(工序库存2000件)….安装门开关
失效模式:未加工
失效原因:铣刀断——4次/年 过程控制方法:
识别关键因子-PFMEA

(7).采取措施(action taken) 当执行“建议措施”后,需简要纪录执行结果,并 重新评估风险优先指数RPN(O、S、D) 。本项重点应 该着重在持续改进上。
(8).PFMEA表各欄位關連性說明
子系 潜 潜 严 级 潜 發 现行控 難 R 建 责任
统
在 在 重别在 生制
檢 P 议 及目
(3).失效原因(cause of failure) 为了对产品或制程之失效模式采取对策,必须探讨其 发生原因。发生原因大多是产品或制程之使用条件、 环境变化或制造过程参数设定不当所引起。失效原因 之检讨结果,将被用来改进制程或改善设计。造成失 效的原因有许多种,就机械而言,一般失效之原因大 致可归纳如下:(1)热处理不当,(2)材料不良,
2.PFMEA是表格化之管理方式,其重点项目如下:
(1).失效模式(failure mode) 产品或制程可能发生之故障状态或现象。 常见的失效模式分类如下:(1)磨耗/用坏(Worn Out),(2)破碎(Broken),(3)倒塌
(Collapsed),龟裂/破坏(Crack/Fractured), (5)撕裂/撕破/割裂(Ripped/Torn/Cut),(6)破
车削参数(进给量、转速、吃刀量)
表面粗糙度,各部位跳动
10
人工搬运到检验台
11
检验
外圆尺寸,轴向尺寸,外观、表面粗糙
度,径向跳动
12
人工搬运到下一工序
13
铣槽
圆弧槽尺寸,外观,表面粗糙度
铣削参数(进给量、转速、吃刀量)
14
移动到下一工序
辊式输送带速度
3、认识PFMEA (1).PFMEA(潜在的过程失效模式与后果分析) 。 (2).PFMEA是一种工程技术用以定义、确认及消除 产品在生产前的过程设计及产品还没有交付顾 客之前已知的或潜在的失效、问题等。 (3).PFMEA是生产前,早期预防失效及错误发生的最 重要且最有效的方法之一。
PFMEA教程(五大工具)

9
8 7 6 5 4 3 2 1
高:经常性失效
每月发生一次 每三个月发生一次
中:偶然性失效
每六个月发生一次 每年发生一次
低:相对很少发生
每1 – 3年发生一次 每3-6年发生一次
失效不太可能发生
每6-100年发生一次
Smiths Interconnect
23
2.4 PFMEA的实施步骤(8)
8.侦测度评价(D)
• 其含义是指“事件发生前”的措施,而不是“事实出现后”的演练。
• 为实现最大价值,FMEA必须在产品或过程开始之前进行。
• 事先花时间很好地完成FMEA分析,能够最容易、低成本地对产品 或过程进行更改,从而最大程度地降低后期更改的危机。 • FMEA能够减少或消除实施可能会带来更大隐患。
Smiths Interconnect
Smiths Interconnect
26
2.4 PFMEA的实施步骤(11)
11.针对重点项目制定改善措施
建议措施应该考虑下列,但不局限于: •为了减小失效发生的可能性,需要修改过程或设计。 •只有修改过程或设计,才能减少严重度。 •增加检查频次不是一个有效的预防/矫正措施,只能作为暂时的对策。为 了有助于失效的侦测,可以对某一具体部份进行设计变更。 •使用防错法来减小侦测度应为最优先实施的方法。 •重点要放在预防缺陷发生(如降低发生率)上,胜过去侦测它们; •应采用统计制程管制(SPC)和过程改进的方法,而不是只采用抽样检查 的方法。
检查 几乎不可能 非常微细的 微细 很低 低 中 中偏高 高 很高 很高,几乎肯定 标准 故障所造成的缺陷测试不到 偶尔能测试某些单位是否有缺陷 对所有单位进行系统采样和检查 所有的单位均进行人工检查 带有防错改动的人工检查 过程经过监视 (SPC) 并人工检查 采用SPC并对失控情况立即采取行动 象上面一样采用SPC,并对失控情况前后进行 100%的检查 所有单位都经过放错的自动检查 缺陷很明显,可防止其影响到顾客 X X X X X X X X X 检查种类 防错法 自动检查 人工检查 X X X X X 分数 10 9 8 7 6 5 4 3 2 1
- 1、下载文档前请自行甄别文档内容的完整性,平台不提供额外的编辑、内容补充、找答案等附加服务。
- 2、"仅部分预览"的文档,不可在线预览部分如存在完整性等问题,可反馈申请退款(可完整预览的文档不适用该条件!)。
- 3、如文档侵犯您的权益,请联系客服反馈,我们会尽快为您处理(人工客服工作时间:9:00-18:30)。
什么是PFMEAPFMEA是过程失效模式及后果分析(Process Failure Mode and Effects Analysis)的英文简称。
是由负责制造/装配的工程师/小组主要采用的一种分析技术,用以最大限度地保证各种潜在的失效模式及其相关的起因/机理已得到充分的考虑和论述。
失效:在规定条件下(环境、操作、时间),不能完成既定功能或产品参数值和不能维持在规定的上下限之间,以及在工作范围内导致零组件的破裂卡死等损坏现象。
严重度(S):指一给定失效模式最严重的影响后果的级别,是单一的FMEA范围内的相对定级结果。
严重度数值的降低只有通过设计更改或重新设计才能够实现。
频度(O):指某一特定的起因/机理发生的可能发生,描述出现的可能性的级别数具有相对意义,但不是绝对的。
探测度(D):指在零部件离开制造工序或装配之前,利用第二种现行过程控制方法找出失效起因/机理过程缺陷或后序发生的失效模式的可能性的评价指标;或者用第三种过程控制方法找出后序发生的失效模式的可能性的评价指标。
风险优先数(RPN):指严重度数(S)和频度数(O)及不易探测度数(D)三项数字之乘积。
顾客:一般指“最终使用者”,但也可以是随后或下游的制造或装配工序,维修工序或政府法规。
[编辑]PFMEA的分析原理PFMEA的分析原理如下表所示,它包括以下几个关键步骤:(1)确定与工艺生产或产品制造过程相关的潜在失效模式与起因;(2)评价失效对产品质量和顾客的潜在影响;(3)找出减少失效发生或失效条件的过程控制变量,并制定纠正和预防措施;(4)编制潜在失效模式分级表,确保严重的失效模式得到优先控制;(5)跟踪控制措施的实施情况,更新失效模式分级表。
(1)“过程功能/要求”:是指被分析的过程或工艺。
该过程或工艺可以是技术过程,如焊接、产品设计、软件代码编写等,也可以是管理过程,如计划编制、设计评审等。
尽可能简单地说明该工艺过程或工序的目的,如果工艺过程包括许多具有不同失效模式的工序,那么可以把这些工序或要求作为独立过程列出;(2)“潜在的失效模式”:是指过程可能发生的不满足过程要求或设计意图的形式或问题点,是对某具体工序不符合要求的描述。
它可能是引起下一道工序的潜在失效模式,也可能是上一道工序失效模式的后果。
典型的失效模式包括断裂、变形、安装调试不当等;(3)“失效后果”:是指失效模式对产品质量和顾客可能引发的不良影响,根据顾客可能注意到或经历的情况来描述失效后果,对最终使用者来说,失效的后果应一律用产品或系统的性能来阐述,如噪声、异味、不起作用等;(4)“严重性”:是潜在失效模式对顾客影响后果的严重程度,为了准确定义失效模式的不良影响,通常需要对每种失效模式的潜在影响进行评价并赋予分值,用1-10分表示,分值愈高则影响愈严重。
“可能性”:是指具体的失效起因发生的概率,可能性的分级数着重在其含义而不是数值,通常也用1—10分来评估可能性的大小,分值愈高则出现机会愈大。
“不易探测度”:是指在零部件离开制造工序或装备工位之前,发现失效起因过程缺陷的难易程度,评价指标也分为1—10级,得分愈高则愈难以被发现和检查出;(5)“失效的原因/机理”:是指失效是怎么发生的,并依据可以纠正或控制的原则来描述,针对每一个潜在的失效模式在尽可能广的范围内,列出每个可以想到的失效起因,如果起因对失效模式来说是唯一的,那么考虑过程就完成了。
否则,还要在众多的起因中分析出根本原因,以便针对那些相关的因素采取纠正措施,典型的失效起因包括:焊接不正确、润滑不当、零件装错等;(6)“现行控制方法”:是对当前使用的、尽可能阻止失效模式的发生或是探测出将发生的失效模式的控制方法的描述。
这些控制方法可以是物理过程控制方法,如使用防错卡具,或者管理过程控制方法,如采用统计过程控制(SPC)技术;(7)“风险级(RPN)”:是严重性、可能性和不易探测性三者的乘积。
该数值愈大则表明这一潜在问题愈严重,愈应及时采取纠正措施,以便努力减少该值。
在一般情况下,不管风险级的数值如何,当严重性高时,应予以特别注意;(8)“建议采取的措施”:是为了减少风险发生的严重性、可能性或不易探测性数值而制定的应对方案,包括行动计划或措施、责任人、可能需要的资源和完成日期等。
当失效模式排出先后次序后应首先对排在最前面的风险事件或严重性高的事件采取纠正措施,任何建议措施的目的都是为了阻止其发生,或减少发生后的影响和损失;(9)“措施结果”:是对上述“建议采取的措施”计划方案之实施状况的跟踪和确认。
在明确了纠正措施后,重新估计并记录采取纠正措施后的严重性、可能性和不易探测性数值,计算并记录纠正后的新的风险级值,该数值应当比措施结果之前的风险级值低得多,从而表明采取措施后能够充分降低失效带来的风险。
[编辑]PFMEA的目的1)发现评价过程中潜在的失效及后果。
2)找到能够避免或减少这些潜在失效发生的措施。
3)书面总结上述过程,完善设计过程,确保顾客满意。
[编辑]PFMEA的适用范围1)所有新的总成/部件/过程;2)更改的总成/部件/过程;3)应用环境有变化的原有总成/部件/过程。
[编辑]PFMEA案例分析[编辑]案例一:PFMEA在SMT装配应用举例[1]在实际应用中,SMT装配有诸如单面贴装、双面贴装、双面混装等操作方式,各种操作方式的具体生产工艺流程各不相同。
为了说明如何将PFMEA应用于SMT装配过程,现在就以工艺流程相对简单的单面贴装为对象,阐述应用PFMEA的方法。
单面贴装过程功能描述如下:单面贴装的主要环节有印刷焊膏、贴装元器件、焊接元器件,其工艺流程是:印刷焊膏一一贴装元器件一一AOT检验一一回流焊接一一焊点检验,该装配过程涉及的主要设备有丝印机、贴片机、回流焊炉和检测设备。
通过对长期SMT生产过程的总结,单面贴装工作方式中暴露的焊点常见失效模式有:焊锡球、冷焊、焊桥、立片,其因果分析图如图所示。
根据图2中对这几种失效模式的因果分析和检验、设计人员的实践经验,现对这些失效模式分析如下:焊锡球焊锡球是回流焊接中经常碰到的一个问题。
通常片状元件侧面或细间距引脚之间常常出现焊锡球。
失效后果:焊锡球会造成短路、虚焊以及电路板污染。
可能导致少部分产品报废或全部产品返工,将严重度评定为5。
现有故障检测方法:人工目视和x射线检测仪检测。
失效原因为:焊膏缺陷——粘度低、被氧化等,频度为5,检测难度为5,风险指数PRN为125。
现行控制措施使用能抑制焊料球产生的焊膏,装配前检测焊膏品质。
助焊剂缺陷——活性降低,频度为3,检测难度为6,风险指数PRN为90。
模板缺陷——开孔尺寸不当焊盘过大等,频度为5,检测难度为4,风险指数PRN为100。
回流温度曲线设置不当,频度为7,检测难度为5,风险指数PRN为175。
现行控制措施:调整回流焊温度曲线使之与使用焊膏特性相适应。
冷焊冷焊的表象是焊点发黑,焊膏未完全熔化。
失效后果:产生开路和虚焊,可能导致少部分产品报废或全部产品返工,严重度评定为50现有故障检测方法:人工目视和x射线检测仪检测。
失效原因为:回流焊接参数设置不当,温度过低,传送速度过快,频度为3,检测难度为5,风险指数为750现行控制措施:按照焊膏资料或可行经验设置回流焊温度曲线。
焊桥焊桥经常出现在引脚较密的丁C上或间距较小的片状元件间,这种缺陷在检验标准中属于重大缺陷。
焊桥会严重影响产品的电气性能,所以必须要加以根除。
失效后果;焊桥会造成短路等后果,严重的会使系统或主机丧失主要功能,导致产品全部报废,用户不满意程度很高,严重度评定为s。
现有故障检测方法:人工目视和x射线检测仪检测。
失效原因为:模板缺陷——开孔尺寸过大等,频度为7,检测难度为6,风险指数PRN为336。
焊膏缺陷——粘度不当等,频度为5,检测难度为5,风险指数PRN为200。
焊膏印刷工艺参数设置不当,频度8,检测难度为6,风险指数PRN为384。
现行控制措施:保持刮刀压力一定,减慢印刷速度,实现焊膏好的成型。
此外,控制脱模速率和模板与PCB 的最小间隙。
回流焊接预热温度和预热时间设置不当,频度为5,检测难度为4,风险指数PRN为160。
现行控制措施:降低预热温度,缩短预热时间。
立片立片主要发生在小的矩形片式元件(如贴片电阻、电容)回流焊接过程中。
引起这种现象的主要原因是元件两端受热不均匀,焊膏熔化有先后所致。
失效后果:导致开路,引发电路故障,会使系统或整机丧失主要功能,严重度评定为7e现有故障检测方法:人工目视检测。
失效原因分别为:贴片精度不够,频度为3,检测难度为5,风险指数PRN为IOS.回流焊接预热温度较低,预热时间较短,频度为5,检测难度为4,风险指数PRN为140。
现行控制措施:适当提高预热温度,延长预热时间。
焊膏印刷过厚,频度为5,检测难度为5,风险指数PRN为1750现行控制措施:针对不同的器件选用适当厚度的丝印模板。
在计算了各潜在失效模式的RPN值之后,后续工作就是开展相应的工艺试验,探寻针对高RPN值和高严重度的潜在失效模式的纠正措施,并在纠正后,重新进行风险评估,验证纠正措施的可行性与正确性。
[编辑]案例二:如何利用PFMEA分析制造过程风险[2]现以汽车内饰产品——汽车内饰件的制造过程为例,来简单介绍如何利用PFMEA分析制造过程风险,并予以改进的。
为了使PFMEA进行的条理清晰,需使用一个表样,(见表一),按照表格中对应的数字编号的内容进行介绍。
1.基本数据在表格上部填上所分析的零部件及PFMEA小组成员的相关信息。
2.过程功能/要求简单描述将被分析的过程或作业,并进行编号。
根据过程流程图,对所规划的过程进行准确地描述,描述必须完整。
如果含许多不同潜在失效模式的作业,可把这些以独立项目列出。
潜在失效模式所谓潜在失效模式是指过程可能潜在不满足过程要求,是对具体作业不符合要求的描述。
搜集在各过程<工序中可能的缺陷,即使特定条件下可能发生的缺陷模式也应列出。
也包括以往历史的经验。
潜在失效后果是指失效模式对顾客的影响,站在顾客的角度描述失效的后果,这里的顾客可以是下道工序或是最终使用者。
就举例中的汽车门内饰板对最终使用者来说,失效后果可以是漏水、噪声、外观不良等,对下道作业失效后果可以是无法安装无法钻孔等。
5.严重度是对一个已假定失效模式的最严重影响的评价等级。
要减少严重度识别等级,只能通过对零件的设计变更,或对过程重新设计,否则,严重度不会发生变化。
严重度分1(无影响)-10(后果严重)级。
6.分类是对过程控制的一些特殊过程特性进行分类,其符号是公司内部的规定,或是顾客的规定。
7.失效起因/机理简单说就是每一种缺陷发生的可能的原因,原因可以是生产或装配所决定的。
需对每一原因尽可能简要地描述。