弹簧的淬火和回火
SK5弹簧钢薄带的工艺及热处理研究

SK5弹簧钢薄带的工艺及热处理研究摘要:回火通常可分为三种,即低温回火、中温回火和高温回火,三种回火温度、回火后组织及其性能、主要适用对象如下表所示。
一般弹簧钢的热处理工艺是淬火+中温回火处理,可以获得回火屈氏体,在保证获得良好的弹性极限基础上,还具有良好的韧性和塑性,如85钢,其规范的回火工艺是380℃~440℃。
回火保温时间的选择应尽量保证工件各部分温度均匀,同时保证组织转变充分,并尽可能降低或消除内应力。
回火过程一般在最初0.5h内硬度变化很剧烈,超过2h后,硬度变化很小,因此,一般弹簧钢回火时间均为1~2h。
[1]将淬火后的试样分别在150℃、200℃、250℃、300℃、350℃下进行回火处理,比对金相进行分析;测量硬度值;进行拉伸试验,记录断面收缩率、拉伸率、最大拉伸力等数据;进行试验,记录最大力、最大弯曲强度、弯曲弹性模量等数据。
相关研究发现,抗拉强度与硬度随着回火温度的上升而下降,不同温度阶段的下降趋势不同;断面收缩率在不同的温度范围里有不同的变化趋势。
弹簧钢最重要的性能要求是良好的弹性极限和硬度,通常硬度很高时,断面收缩率会较低,此时的回火温度并不合适,应该选取回火时强度和韧性都较好的回火温度。
关键词:SK5弹簧;热处理;回火温度引言弹簧在生产中的主要功能是吸收冲击能量及缓和振动。
弹簧钢在工业设备、机械零件、铁路、汽车、发动机等行业当中应用非常广泛。
[1]随着我国现代工业能力的增强、汽车、铁路工业稳步发展,工业设备向着载荷量大、运行速度高的方向发展,机械零件承受这越来越高的载荷和频率。
这些现实的需求,要求弹簧钢具备良好的力学性能(高弹性极限σE、屈服极限σs和屈强比σ0.2/σb)、极佳的抗疲劳性能、淬透性,以及优异的物理和化学性能(耐热性、耐腐蚀性、抗氧化性等)。
目前,国内外弹簧钢的研究集中在提升弹簧钢的强度和使用寿命上,主要研究合金成分、组织形态、生产工艺、热处理等问题[2]。
弹簧的热处理

, 沉淀硬化的不锈钢钢丝 , 钢
带和铜镍合金材料以冷成形工艺制作的弹簧 ,成形后需进行时效硬化处理 .
第三种 ,凡是用热成型和以退火材料冷卷的弹簧,均需进行淬火回火处理。
弹簧的淬火和回火
1 弹簧的淬火 淬火就是把钢加热到临界温度A C3 或 AC1 以上保温一定时间,使其奥氏体化,再以大于临界了冷却速度急剧了冷却,从而获
性 , 并采用高温快速加热的方法 , 对中小弹簧 , 可用脱氧良好的盐浴炉进行淬火加热 .
弹簧淬火宜在油中冷却 , 以避免变形和开裂 . 用尺寸较大的碳钢材料制造的弹簧 , 当
要求不高时 , 可用水冷 . 为了减小变形量 , 除了采用正确的加热和冷却方法外
, 有时还采用专用淬火夹具进行
成形淬火 , 例如板簧在弯板机上淬火 , 中 , 小型螺旋弹簧装在心轴上或专用夹具上进行加
50CrVA
820± 10
820± 10
870± 10 870± 10 850± 10
320--340 270
320--340 290 260 300
15--20 15
15--20 30 60 30
46--48 52--54 46--48
52 55--57
52
表 5--8 螺旋压缩弹簧轴心线对两端面的垂直度允许偏差
得马氏体组织的热处理方法。
对于一般热卷螺旋的弹簧,热弯板簧以及热冲压的蝶形弹簧,最好是在热成之后, 利用其余热立即淬火。这样可以省去一次加热,减少弹簧的氧化脱碳程度,既经济又改
善了弹簧的表面质量。例如 60Si2MnA 钢板弹簧目前采用的热处理工艺是在 900— 925℃
弯片之后,在 850— 880℃入油淬火。若受条件限制,也可在成形之后重新加热淬火。
弹簧钢的最终热处理应是淬火+低温回火。
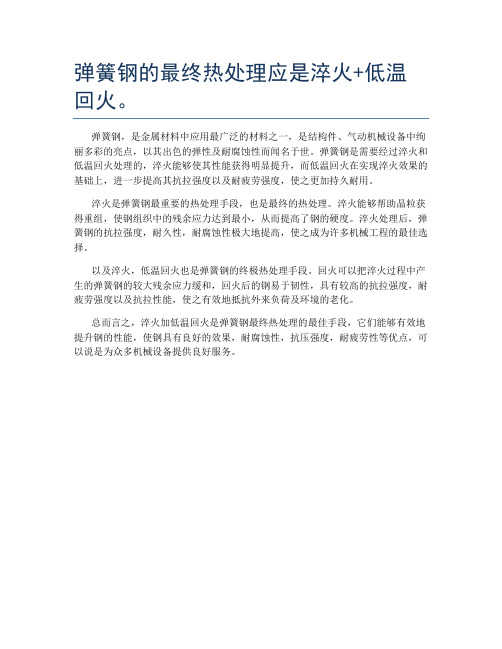
弹簧钢的最终热处理应是淬火+低温回火。
弹簧钢,是金属材料中应用最广泛的材料之一,是结构件、气动机械设备中绚丽多彩的亮点,以其出色的弹性及耐腐蚀性而闻名于世。
弹簧钢是需要经过淬火和低温回火处理的,淬火能够使其性能获得明显提升,而低温回火在实现淬火效果的基础上,进一步提高其抗拉强度以及耐疲劳强度,使之更加持久耐用。
淬火是弹簧钢最重要的热处理手段,也是最终的热处理。
淬火能够帮助晶粒获得重组,使钢组织中的残余应力达到最小,从而提高了钢的硬度。
淬火处理后,弹簧钢的抗拉强度,耐久性,耐腐蚀性极大地提高,使之成为许多机械工程的最佳选择。
以及淬火,低温回火也是弹簧钢的终极热处理手段。
回火可以把淬火过程中产生的弹簧钢的较大残余应力缓和,回火后的钢易于韧性,具有较高的抗拉强度,耐疲劳强度以及抗拉性能,使之有效地抵抗外来负荷及环境的老化。
总而言之,淬火加低温回火是弹簧钢最终热处理的最佳手段,它们能够有效地提升钢的性能,使钢具有良好的效果,耐腐蚀性,抗压强度,耐疲劳性等优点,可以说是为众多机械设备提供良好服务。
弹簧的技术要求
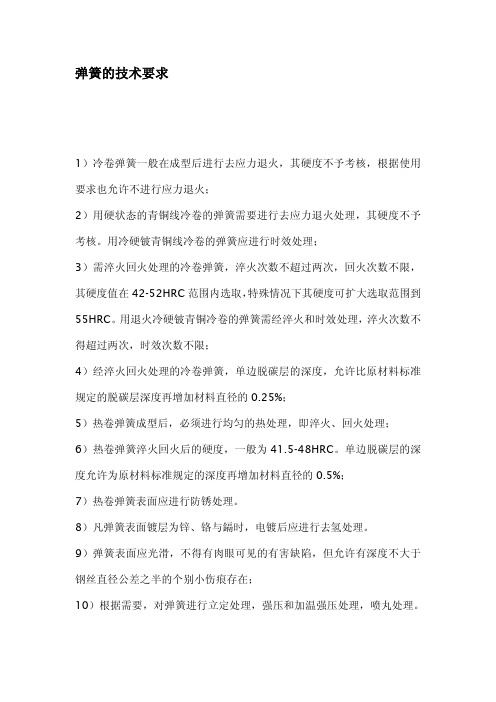
弹簧的技术要求1)冷卷弹簧一般在成型后进行去应力退火,其硬度不予考核,根据使用要求也允许不进行应力退火;2)用硬状态的青铜线冷卷的弹簧需要进行去应力退火处理,其硬度不予考核。
用冷硬铍青铜线冷卷的弹簧应进行时效处理;3)需淬火回火处理的冷卷弹簧,淬火次数不超过两次,回火次数不限,其硬度值在42-52HRC范围内选取,特殊情况下其硬度可扩大选取范围到55HRC。
用退火冷硬铍青铜冷卷的弹簧需经淬火和时效处理,淬火次数不得超过两次,时效次数不限;4)经淬火回火处理的冷卷弹簧,单边脱碳层的深度,允许比原材料标准规定的脱碳层深度再增加材料直径的0.25%;5)热卷弹簧成型后,必须进行均匀的热处理,即淬火、回火处理;6)热卷弹簧淬火回火后的硬度,一般为41.5-48HRC。
单边脱碳层的深度允许为原材料标准规定的深度再增加材料直径的0.5%;7)热卷弹簧表面应进行防锈处理。
8)凡弹簧表面镀层为锌、铬与鎘时,电镀后应进行去氢处理。
9)弹簧表面应光滑,不得有肉眼可见的有害缺陷,但允许有深度不大于钢丝直径公差之半的个别小伤痕存在;10)根据需要,对弹簧进行立定处理,强压和加温强压处理,喷丸处理。
主要是生产工艺不同,以压缩弹簧为例:热卷弹簧典型工艺:落料---端头加工(轧扁或锻扁)---加热---卷簧---淬火---回火---磨端面---压缩---(负荷测试)---喷丸(清理)---涂装。
冷卷弹簧使用不需要热处理的材料卷制,点行工艺:卷制→去应力退火→两端面磨削→(抛丸)、(校整)、(去应力退火)→立定或强压处理→检验→表面防腐处理。
整定处理Setting弹簧“立定处理”。
将热处理后的压缩弹簧压缩到工作极限载荷下的高度或压并高度(拉伸弹簧拉伸到工作极限载荷下的长度,扭转弹簧扭转到工作极限扭转角),一次或多次短暂压缩(拉伸、扭转)以达到稳定弹簧几何尺寸为主要目的的一种工艺方法。
2加温整定处理Hot-setting又称“加温立定处理”。
拉簧热处理标准
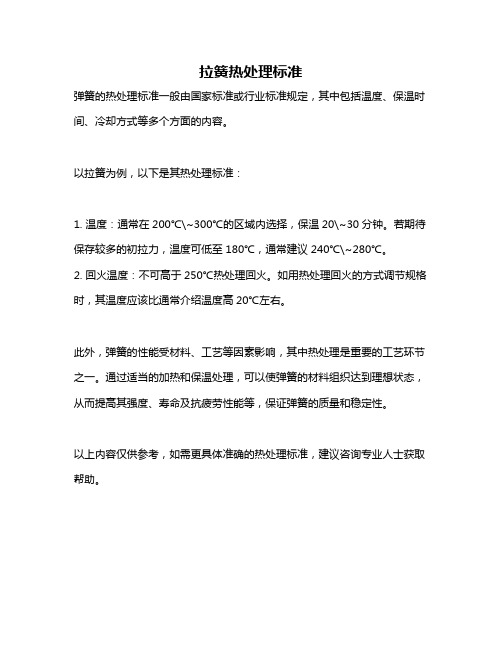
拉簧热处理标准
弹簧的热处理标准一般由国家标准或行业标准规定,其中包括温度、保温时间、冷却方式等多个方面的内容。
以拉簧为例,以下是其热处理标准:
1. 温度:通常在200℃\~300℃的区域内选择,保温20\~30分钟。
若期待保存较多的初拉力,温度可低至180℃,通常建议240℃\~280℃。
2. 回火温度:不可高于250℃热处理回火。
如用热处理回火的方式调节规格时,其温度应该比通常介绍温度高20℃左右。
此外,弹簧的性能受材料、工艺等因素影响,其中热处理是重要的工艺环节之一。
通过适当的加热和保温处理,可以使弹簧的材料组织达到理想状态,从而提高其强度、寿命及抗疲劳性能等,保证弹簧的质量和稳定性。
以上内容仅供参考,如需更具体准确的热处理标准,建议咨询专业人士获取帮助。
不锈钢弹簧热处理规范

1.奥氏体不锈弹簧钢的热处理(1)固溶处理(2)稳定回火处理2.马氏体不锈弹簧钢的热处理(1)马氏体不锈弹簧钢的预备热处理马氏体不锈弹簧钢属于马氏体相变强化钢马氏体不锈弹簧钢的预备热处理工艺(2)马氏体不锈弹簧钢的淬火、回火处理马氏体不锈弹簧钢制成弹簧后的最终热处理是淬火、回火。
1.均匀且美观的表面状态。
2.良好的成形性,均匀的弹性。
3.高塑性,抗疲劳强度,耐热耐腐蚀性能佳。
4.材料表面状态由用户选择:裸线、镀镍弹簧线、镀树脂弹簧线,不锈钢弹簧出厂又分为亮面、雾面、半亮面。
客户可根据产品精密美观程度的要求进行选择。
5.无论是无磁性或弱磁性的不锈钢弹簧。
均可广泛使用于电子,家电,工业,民用等产品。
编辑本段不锈钢弹簧的抛光第一步给不锈钢弹簧去油污、去氧化皮有两种使用方法:1.把不锈钢弹簧浸入放有用清水稀释的金属清洗剂A(清洗剂A与清水稀释配比为1:1或1:2左右)的塑料容器中,时间以弹簧表面无油污、无氧化皮恢复金属本色为宜,浸泡时间不宜过长,取出用清水洗净。
这样不锈钢弹簧表面就有亚光效果。
2.在超声波设备中清洗剂与清水的配比为1:30左右,时间以弹簧表面无油污、无氧化皮恢复金属本色为宜,取出用清水洗净,这样不锈钢弹簧表面就能达到亚光效果。
以上两种方法,可适用于精密度高的弹簧。
3.清洗剂A放入有粗磨料、弹簧的振动光饰机中或六角滚筒中(弹簧与粗磨料的体积比最佳为1:3,清洗剂用量为弹簧重量的1%--2%)研磨抛光以后用清水洗净,弹簧表面的划痕就没有了,提高了弹簧表面的光洁度。
但精密度高易缠绕的弹簧不宜用此法。
第二步给不锈钢弹簧上光:把光亮剂B放入有粗磨料的振动光饰机或六角滚筒内(弹簧与精磨料的体积比为1:3,光亮剂B的用量为弹簧重量的1%--2%左右,时间越长越亮)抛光后,取出用清水洗净晾干即可,这样不锈钢弹簧表面如镀镍一般光亮照人,永不褪色。
编辑本段不锈钢化学抛光化学抛光是不锈钢[3]常用的表面处理工艺,与电化学抛光工艺相比,其最大不锈钢抛光制品优点是不需要直流电源和特殊夹具,可以抛光形状复杂的零件,生产率很高。
油淬火,回火弹簧钢丝,弹簧钢线

汽车、摩托车悬架弹簧、稳定杆、气门弹簧、离合器弹簧、油泵弹簧、变速箱弹簧、摩托车减震弹簧、安全带弹簧、其它各类弹簧
化工、石油气体压缩机弹簧、化工管道阀门弹簧、石油钻机弹簧
机器制造、电动工具、电机、电器与造船各类用于荷重、张紧、缓冲、复位用压缩、拉伸、扭转、碟形、模具、继电器、电刷弹簧、船用柴油机和燃油泵弹簧、
弹簧众多的应用领域中,汽车和内燃机、摩托车制造业是弹簧最大的用户,销售额接近弹簧销售总额一半。铁路系统也是弹簧产品重要用户,国内高速铁路和城市轨道交通建设规模空前,对弹簧需求旺盛,但它的市场相对封闭,主要从本系统内采购,只有数量不能满足或品种不齐时才在系统外做一些补充采购。医疗和军工国防用弹簧的特征是高附加值,但对弹簧材料、性能都有特殊要求,极少数企业具有生产与配套能力。
轻工与纺织钟表发条弹簧、各种家用电器减震复位弹簧、纺织机摇架弹簧
仪器、仪表、IT弹性膜片传感器、力负荷指示弹簧、计算机用弹簧
冶金焦炉弹簧、钢包水封弹簧
煤炭井下液压支柱弹簧
医疗卫生心脑血管弹性支架、记忆合金齿科校正材料
农业、林业养鸡场饲料输送弹簧、森林机械弹簧
日用五金床垫弹簧、沙发弹簧、健身器弹簧、玩具、锁具、打火机弹簧、各种弹簧铰链
残油,时间长了会起火,可干粉灭火剂熄灭,结块的复盖剂应清除,加新的。
(五)水冷
钢丝回火后应保证水冷却,并将残留水吹干,以免钢丝生锈。
(六)涂防锈油
为了防止钢丝生锈,应将钢丝均匀涂上一层簿簿的防锈油。
(七)收线
收线速度设定按工艺要求,穿头用废丝应全部剪除,因故障停机时也应将炉中线剪除,
在生产过程中的所有电接头都要剪除。遇到钢丝被拉断时,要剪除线径不合格部分。
弹簧的热处理
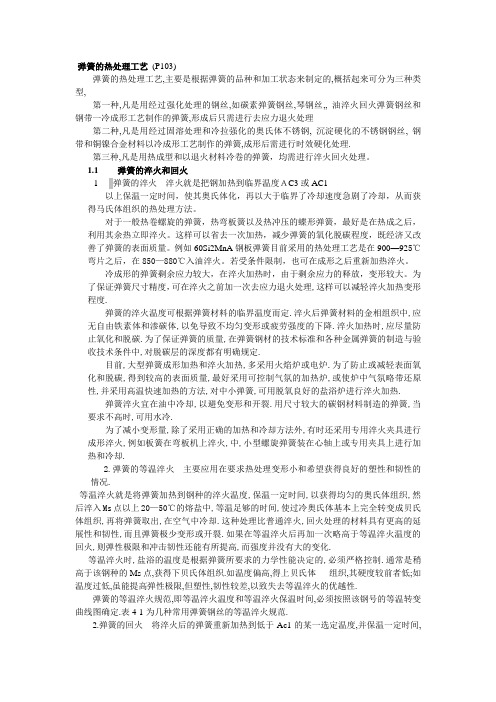
弹簧的热处理工艺(P103)弹簧的热处理工艺,主要是根据弹簧的品种和加工状态来制定的,概括起来可分为三种类型,第一种,凡是用经过强化处理的钢丝,如碳素弹簧钢丝,琴钢丝,, 油淬火回火弹簧钢丝和钢带一冷成形工艺制作的弹簧,形成后只需进行去应力退火处理第二种,凡是用经过固溶处理和冷拉强化的奥氏体不锈钢, 沉淀硬化的不锈钢钢丝, 钢带和铜镍合金材料以冷成形工艺制作的弹簧,成形后需进行时效硬化处理.第三种,凡是用热成型和以退火材料冷卷的弹簧,均需进行淬火回火处理。
1.1弹簧的淬火和回火1弹簧的淬火淬火就是把钢加热到临界温度AC3或AC1以上保温一定时间,使其奥氏体化,再以大于临界了冷却速度急剧了冷却,从而获得马氏体组织的热处理方法。
对于一般热卷螺旋的弹簧,热弯板簧以及热冲压的蝶形弹簧,最好是在热成之后,利用其余热立即淬火。
这样可以省去一次加热,减少弹簧的氧化脱碳程度,既经济又改善了弹簧的表面质量。
例如60Si2MnA钢板弹簧目前采用的热处理工艺是在900—925℃弯片之后,在850—880℃入油淬火。
若受条件限制,也可在成形之后重新加热淬火。
冷成形的弹簧剩余应力较大,在淬火加热时,由于剩余应力的释放,变形较大。
为了保证弹簧尺寸精度,可在淬火之前加一次去应力退火处理,这样可以减轻淬火加热变形程度.弹簧的淬火温度可根据弹簧材料的临界温度而定.淬火后弹簧材料的金相组织中,应无自由铁素体和渗碳体,以免导致不均匀变形或疲劳强度的下降.淬火加热时,应尽量防止氧化和脱碳.为了保证弹簧的质量,在弹簧钢材的技术标准和各种金属弹簧的制造与验收技术条件中,对脱碳层的深度都有明确规定.目前,大型弹簧成形加热和淬火加热,多采用火焰炉或电炉.为了防止或减轻表面氧化和脱碳,得到较高的表面质量,最好采用可控制气氛的加热炉,或使炉中气氛略带还原性,并采用高温快速加热的方法,对中小弹簧,可用脱氧良好的盐浴炉进行淬火加热.弹簧淬火宜在油中冷却,以避免变形和开裂.用尺寸较大的碳钢材料制造的弹簧,当要求不高时,可用水冷.为了减小变形量,除了采用正确的加热和冷却方法外,有时还采用专用淬火夹具进行成形淬火,例如板簧在弯板机上淬火,中,小型螺旋弹簧装在心轴上或专用夹具上进行加热和冷却.2.弹簧的等温淬火主要应用在要求热处理变形小和希望获得良好的塑性和韧性的情况.等温淬火就是将弹簧加热到钢种的淬火温度,保温一定时间,以获得均匀的奥氏体组织,然后淬入Ms点以上20—50℃的熔盐中,等温足够的时间,使过冷奥氏体基本上完全转变成贝氏体组织,再将弹簧取出,在空气中冷却.这种处理比普通淬火,回火处理的材料具有更高的延展性和韧性,而且弹簧极少变形或开裂.如果在等温淬火后再加一次略高于等温淬火温度的回火,则弹性极限和冲击韧性还能有所提高,而强度并没有大的变化.等温淬火时,盐浴的温度是根据弹簧所要求的力学性能决定的,必须严格控制.通常是稍高于该钢种的Ms点,获得下贝氏体组织.如温度偏高,得上贝氏体组织,其硬度较前者低;如温度过低,虽能提高弹性极限,但塑性,韧性较差,以致失去等温淬火的优越性.弹簧的等温淬火规范,即等温淬火温度和等温淬火保温时间,必须按照该钢号的等温转变曲线图确定.表4-1为几种常用弹簧钢丝的等温淬火规范.2.弹簧的回火将淬火后的弹簧重新加热到低于Ac1的某一选定温度,并保温一定时间,然后以适宜的冷却速度冷却的工艺方法,叫做回火.回火的目的是:获得所需要的力学性能,稳定弹簧的组织和尺寸以及消除内应力.表4-1 几种常用弹簧钢的等温淬火规范表1-8 美国弹簧标准名称和标准号(P20)。
弹簧的热处理

弹簧的热处理弹簧钢大部分为圆钢,盘条和扁钢,用于制造各种尺寸较大的热式冷成型螺旋谈话和板(片)簧。
弹簧钢的W(C)时0.3-1.2%(碳素弹簧钢W(C)为0.6-0.9%,合金弹簧钢为W(C)为0.45-0.7%(1)钢中碳含量增加有效提高冷变形强化或马氏体相变强化效果,获得较高强度和弹性极限,这是碳素弹簧钢主要优点。
但碳素弹簧钢淬透性小,抗应力松弛性能不够好,耐蚀性差和弹性模量温度系数较大,只能用于制造横截面积较小,工作温度不高的弹簧。
(2)合金弹簧钢分为:锰弹簧钢和硅锰弹簧钢硅鉻,硅鉻钒和硅锰钨弹簧钢鉻锰,鉻钒和鉻锰钒弹簧钢硼弹簧钢及稀出弹簧钢其他多元量少的低合金弹簧钢化学成分C Si Mn Cr V 其他合金65 0.62-0.70 0.17-0.37 0.50-0.80 ≤0.2570 0.67-0.75 0.17-0.37 0.50-0.80 ≤0.2585 0.82-0.90 0.17-0.37 0.50-0.80 ≤0.2565Mn 0.62-0.70 0.17-0.37 0.9-1.2 ≤0.2555Si2Mn 0.52-0.60 1.5-2.0 0.6-0.9 ≤0.3555Si2MnB 052-0.60 1.5-2.0 0.6-0.9 ≤0.35 B0.0005-0.00455SiMnVB 0.52-0.6 0.7-1.0 1.0-1.3 ≤0.35 0.08-0.16 B0.001-0.003560Si2Mn 0.56-0.64 1.5-2.0 0.6-0.9 ≤0.3560Si2MnA 0.56-0.64 1.6-2.0 0.6-0.9 ≤0.3560Si2CrA 0.56-0.64 1.4-1.8 0.4-0.7 0.7-1.060Si2CrV A 0.56-0.64 1.4-1.8 0.4-0.7 0.9-1.2 0.1-0.2 55CrMnA 0.52-0.6 0.17-0.37 0.65-0.95 0.65-0.9560CrMnA 0.56-0.64 0.17-0.37 0.7-1.0 0.7-1.060CrMnMo A 0.56-064 0.17-0.37 0.7-1.0 0.7-0.9 Mo0.25-0.3550CrV A 0.44-0.54 0.17-0.37 0.50-0.8 0.8-1.1 0.1-0.260CrMnBA 0.56-0.64 0.17-0.37 0.7-1.0 0.7-1.0 W0.0005-0.004 30W4Cr2V A 0.26-0.34 0.17-0.37 ≤0.40 2.0-2.5 0.5-0.8 W4.0-4.5 (1)65# 840油500℃回抗拉1000屈服80070# 830油480℃回抗拉1050屈服850用作一般机器上的圆,方螺旋螺弹簧或冷拔钢丝作小型机械弹簧(2)85# 820油冷480空冷抗拉1150屈服1000用作汽车,拖拉机及一般机器上的扁形弹簧,圆形螺旋弹簧,以及其他用途的钢丝等。
弹簧的热处理(一)

弹簧的热处理(一)来源:每天学点热处理弹簧及弹性元件,是量大面广的基础零件,可以说是无处不在。
在动力机械、电器、仪表、武器中作为控制性元件,也是非常关键的零件。
它的基本功能是利用材料的弹性和弹簧的结构特点,在产生及恢复变形时,可以把机械功或动能转换为形变能,或者把形变能转换为动能或机械功,以达到缓冲或减振、控制运动或复位、储能或测量等目的。
所以,在各类机械设备、仪器仪表、军工产品、电器、家具、家电甚至文具、玩具中都广泛使用弹簧。
影响弹簧质量和使用寿命的因素很多,如设计、选材、生产工艺及工况条件等等。
其中,材质和热处理对弹簧的各种性能及其使用寿命有重要的甚至是决定性的影响。
本文分四个主题,分别介绍各类机械设备中常用的弹簧材料和典型弹簧的热处理,对于特殊用途的弹性材料和元件的热处理只做扼要介绍。
一、弹簧的分类、服役条件、失效方式和性能要求1 弹簧分类弹簧种类很多,可按形状、承载特点、制造方法、材料成分和不同用途进行分类。
每一类中又分为若干小类和不同规格。
GB/T1805弹簧的标准中列出了22种,弹簧行业1990年提出的内部标准《弹簧种类》中,把弹簧分为15个小类。
弹簧行业多按形状分类,在机械制造业中多按用途分类或按上述两者综合命名。
如表1 。
▼表1 弹簧的分类典型螺旋弹簧及板簧如图1所示。
▲图1 典型螺旋弹簧及板簧2 弹簧的服役条件和失效形式2.1 弹簧的服役条件和应力状态弹簧的服役条件是指它的工作环境(温度和介质)及应力状态等因素。
工作温度可分为低温(室温以下)、室温、较高温(120℃~350℃)、高温(350℃以上)几个档次。
工作环境介质有空气、水蒸气、雨水、燃烧产物、以及酸、碱水溶液等。
普通机械弹簧一般是在室温或较高工作温度、大气条件下承受载荷。
也有用于耐蚀、承受高应力等各种特殊用途的弹簧。
工作持续时间也是一个值得考虑的重要因素。
▲气门弹簧是要求最严苛的弹簧之一弹簧的载荷特性由弹簧变形时的载荷(P或T)与变形(F或)之间的关系曲线表示。
弹簧钢回火索氏体-概述说明以及解释
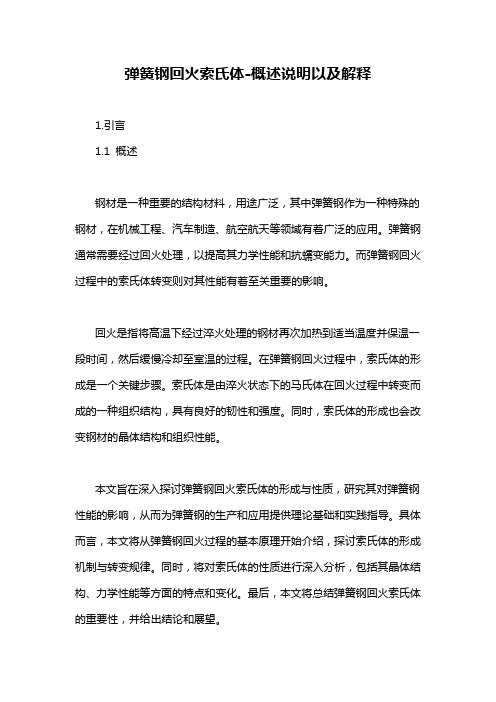
弹簧钢回火索氏体-概述说明以及解释1.引言1.1 概述钢材是一种重要的结构材料,用途广泛,其中弹簧钢作为一种特殊的钢材,在机械工程、汽车制造、航空航天等领域有着广泛的应用。
弹簧钢通常需要经过回火处理,以提高其力学性能和抗蠕变能力。
而弹簧钢回火过程中的索氏体转变则对其性能有着至关重要的影响。
回火是指将高温下经过淬火处理的钢材再次加热到适当温度并保温一段时间,然后缓慢冷却至室温的过程。
在弹簧钢回火过程中,索氏体的形成是一个关键步骤。
索氏体是由淬火状态下的马氏体在回火过程中转变而成的一种组织结构,具有良好的韧性和强度。
同时,索氏体的形成也会改变钢材的晶体结构和组织性能。
本文旨在深入探讨弹簧钢回火索氏体的形成与性质,研究其对弹簧钢性能的影响,从而为弹簧钢的生产和应用提供理论基础和实践指导。
具体而言,本文将从弹簧钢回火过程的基本原理开始介绍,探讨索氏体的形成机制与转变规律。
同时,将对索氏体的性质进行深入分析,包括其晶体结构、力学性能等方面的特点和变化。
最后,本文将总结弹簧钢回火索氏体的重要性,并给出结论和展望。
通过本文的研究,我们可以更好地理解弹簧钢回火索氏体的形成机制及其对材料性能的影响,为弹簧钢的制备和工程应用提供科学依据。
同时,本文的研究也有助于推动弹簧钢回火索氏体相关领域的发展,进一步提高弹簧钢材料的质量和性能。
1.2 文章结构文章结构部分的内容可以包括以下内容:本文主要分为引言、正文和结论三个部分。
在引言部分,我们首先会对弹簧钢回火索氏体进行概述,简单介绍它的定义以及与弹簧钢回火过程的关系。
接着,我们会明确文章的结构,说明各个部分的内容和重点,并简要描述每个部分的目的和意义。
接下来是正文部分,主要分为两个小节。
第一个小节将着重讲解弹簧钢回火过程,包括回火的定义、回火工艺参数的确定和回火过程对弹簧钢性能的影响等。
第二个小节将重点探讨索氏体的形成与性质,包括索氏体的定义、形成机制和结构特点,以及它对弹簧钢回火过程的影响等。
弹簧热处理及强压立定工艺
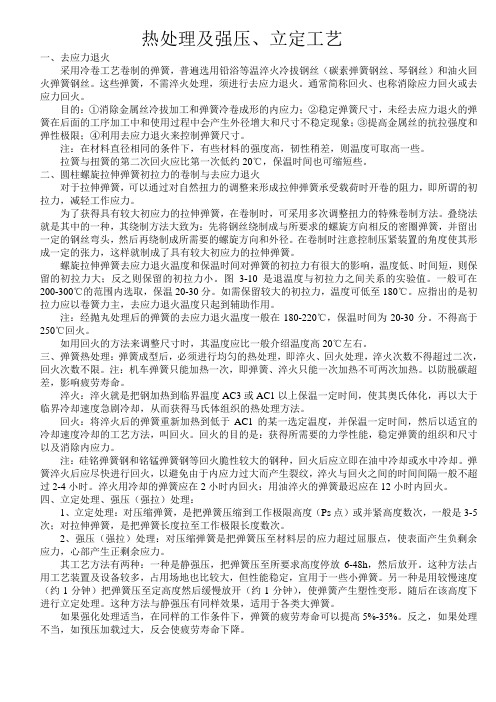
热处理及强压、立定工艺一、去应力退火采用冷卷工艺卷制的弹簧,普遍选用铅浴等温淬火冷拔钢丝(碳素弹簧钢丝、琴钢丝)和油火回火弹簧钢丝。
这些弹簧,不需淬火处理,须进行去应力退火。
通常简称回火、也称消除应力回火或去应力回火。
目的:①消除金属丝冷拔加工和弹簧冷卷成形的内应力;②稳定弹簧尺寸,未经去应力退火的弹簧在后面的工序加工中和使用过程中会产生外径增大和尺寸不稳定现象;③提高金属丝的抗拉强度和弹性极限;④利用去应力退火来控制弹簧尺寸。
注:在材料直径相同的条件下,有些材料的强度高,韧性稍差,则温度可取高一些。
拉簧与扭簧的第二次回火应比第一次低约20℃,保温时间也可缩短些。
二、圆柱螺旋拉伸弹簧初拉力的卷制与去应力退火对于拉伸弹簧,可以通过对自然扭力的调整来形成拉伸弹簧承受载荷时开卷的阻力,即所谓的初拉力,减轻工作应力。
为了获得具有较大初应力的拉伸弹簧,在卷制时,可采用多次调整扭力的特殊卷制方法。
叠绕法就是其中的一种,其绕制方法大致为:先将钢丝绕制成与所要求的螺旋方向相反的密圈弹簧,并留出一定的钢丝弯头,然后再绕制成所需要的螺旋方向和外径。
在卷制时注意控制压紧装置的角度使其形成一定的张力,这样就制成了具有较大初应力的拉伸弹簧。
螺旋拉伸弹簧去应力退火温度和保温时间对弹簧的初拉力有很大的影响,温度低、时间短,则保留的初拉力大;反之则保留的初拉力小。
图3-10是退温度与初拉力之间关系的实验值。
一般可在200-300℃的范围内选取,保温20-30分。
如需保留较大的初拉力,温度可低至180℃。
应指出的是初拉力应以卷簧力主,去应力退火温度只起到辅助作用。
注:经抛丸处理后的弹簧的去应力退火温度一般在180-220℃,保温时间为20-30分。
不得高于250℃回火。
如用回火的方法来调整尺寸时,其温度应比一般介绍温度高20℃左右。
三、弹簧热处理:弹簧成型后,必须进行均匀的热处理,即淬火、回火处理,淬火次数不得超过二次,回火次数不限。
弹簧和紧固件的热处理
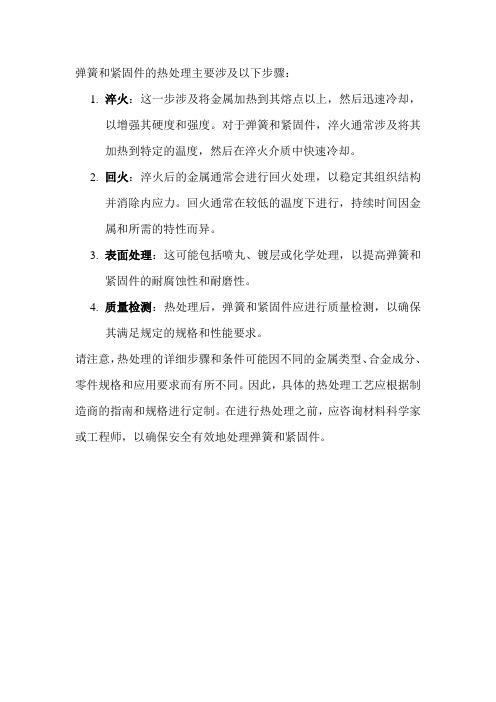
弹簧和紧固件的热处理主要涉及以下步骤:
1.淬火:这一步涉及将金属加热到其熔点以上,然后迅速冷却,
以增强其硬度和强度。
对于弹簧和紧固件,淬火通常涉及将其
加热到特定的温度,然后在淬火介质中快速冷却。
2.回火:淬火后的金属通常会进行回火处理,以稳定其组织结构
并消除内应力。
回火通常在较低的温度下进行,持续时间因金
属和所需的特性而异。
3.表面处理:这可能包括喷丸、镀层或化学处理,以提高弹簧和
紧固件的耐腐蚀性和耐磨性。
4.质量检测:热处理后,弹簧和紧固件应进行质量检测,以确保
其满足规定的规格和性能要求。
请注意,热处理的详细步骤和条件可能因不同的金属类型、合金成分、零件规格和应用要求而有所不同。
因此,具体的热处理工艺应根据制造商的指南和规格进行定制。
在进行热处理之前,应咨询材料科学家或工程师,以确保安全有效地处理弹簧和紧固件。
弹簧钢的最终热处理应是淬火+中温回火
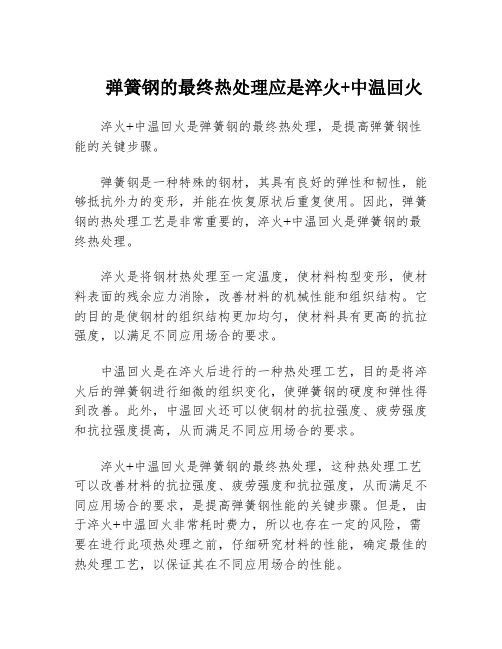
弹簧钢的最终热处理应是淬火+中温回火
淬火+中温回火是弹簧钢的最终热处理,是提高弹簧钢性能的关键步骤。
弹簧钢是一种特殊的钢材,其具有良好的弹性和韧性,能够抵抗外力的变形,并能在恢复原状后重复使用。
因此,弹簧钢的热处理工艺是非常重要的,淬火+中温回火是弹簧钢的最终热处理。
淬火是将钢材热处理至一定温度,使材料构型变形,使材料表面的残余应力消除,改善材料的机械性能和组织结构。
它的目的是使钢材的组织结构更加均匀,使材料具有更高的抗拉强度,以满足不同应用场合的要求。
中温回火是在淬火后进行的一种热处理工艺,目的是将淬火后的弹簧钢进行细微的组织变化,使弹簧钢的硬度和弹性得到改善。
此外,中温回火还可以使钢材的抗拉强度、疲劳强度和抗拉强度提高,从而满足不同应用场合的要求。
淬火+中温回火是弹簧钢的最终热处理,这种热处理工艺可以改善材料的抗拉强度、疲劳强度和抗拉强度,从而满足不同应用场合的要求,是提高弹簧钢性能的关键步骤。
但是,由于淬火+中温回火非常耗时费力,所以也存在一定的风险,需要在进行此项热处理之前,仔细研究材料的性能,确定最佳的热处理工艺,以保证其在不同应用场合的性能。
总之,淬火+中温回火是弹簧钢的最终热处理,它可以改善材料的机械性能和弹性,提高其在不同应用场合的性能,是提高弹簧钢性能的关键步骤。
但是,由于这种热处理工艺耗时费力,所以应在进行此项工艺之前,仔细研究材料的性能,确定最佳的工艺参数,以保证其在不同应用场合的性能。
11种常见弹簧热处理工艺概念解释
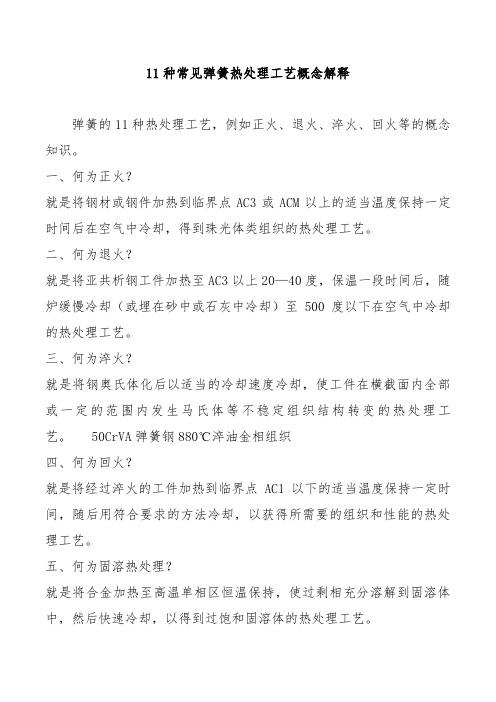
11种常见弹簧热处理工艺概念解释弹簧的11种热处理工艺,例如正火、退火、淬火、回火等的概念知识。
一、何为正火?就是将钢材或钢件加热到临界点AC3或ACM以上的适当温度保持一定时间后在空气中冷却,得到珠光体类组织的热处理工艺。
二、何为退火?就是将亚共析钢工件加热至AC3以上20—40度,保温一段时间后,随炉缓慢冷却(或埋在砂中或石灰中冷却)至500度以下在空气中冷却的热处理工艺。
三、何为淬火?就是将钢奥氏体化后以适当的冷却速度冷却,使工件在横截面内全部或一定的范围内发生马氏体等不稳定组织结构转变的热处理工艺。
50CrVA弹簧钢880℃淬油金相组织四、何为回火?就是将经过淬火的工件加热到临界点AC1以下的适当温度保持一定时间,随后用符合要求的方法冷却,以获得所需要的组织和性能的热处理工艺。
五、何为固溶热处理?就是将合金加热至高温单相区恒温保持,使过剩相充分溶解到固溶体中,然后快速冷却,以得到过饱和固溶体的热处理工艺。
井式回火炉六、何为固溶处理?就是使合金中各种相充分溶解,强化固溶体并提高韧性及抗蚀性能,消除应力与软化,以便继续加工成型。
七、何为时效?就是合金经固溶热处理或冷塑性形变后,在室温放置或稍高于室温保持时,其性能随时间而变化的现象。
八、何为时效处理?就是在强化相析出的温度加热并保温,使强化相沉淀析出,得以硬化,提高强度。
九、何为钢的碳氮共渗?就是碳氮共渗是向钢的表层同时渗入碳和氮的过程。
习惯上碳氮共渗又称为氰化,目前以中温气体碳氮共渗和低温气体碳氮共渗(即气体软氮化)应用较为广泛。
中温气体碳氮共渗的主要目的是提高钢的硬度,耐磨性和疲劳强度。
低温气体碳氮共渗以渗氮为主,其主要目的是提高钢的耐磨性和抗咬合性。
十、何为调质处理?就是将淬火加高温回火相结合的热处理称为调质处理。
调质处理广泛应用于各种重要的结构零件,特别是那些在交变负荷下工作的连杆、螺栓、齿轮及轴类等。
调质处理后得到回火索氏体组织,它的机械性能均比相同硬度的正火索氏体组织为优。
弹簧淬火+回火后的抗拉强度和硬度
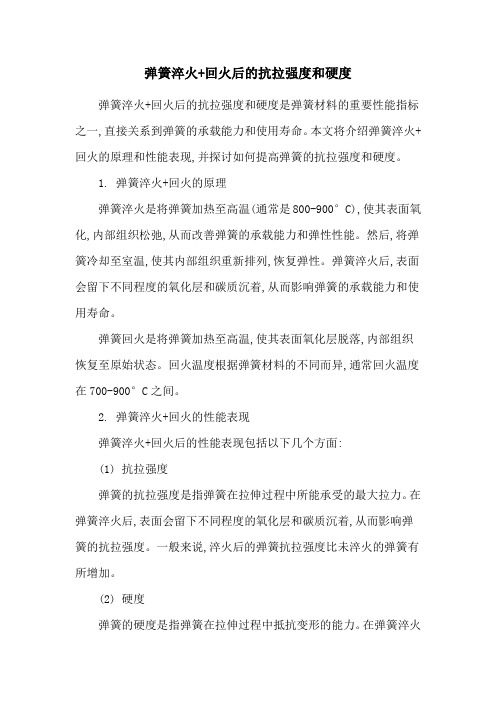
弹簧淬火+回火后的抗拉强度和硬度弹簧淬火+回火后的抗拉强度和硬度是弹簧材料的重要性能指标之一,直接关系到弹簧的承载能力和使用寿命。
本文将介绍弹簧淬火+回火的原理和性能表现,并探讨如何提高弹簧的抗拉强度和硬度。
1. 弹簧淬火+回火的原理弹簧淬火是将弹簧加热至高温(通常是800-900°C),使其表面氧化,内部组织松弛,从而改善弹簧的承载能力和弹性性能。
然后,将弹簧冷却至室温,使其内部组织重新排列,恢复弹性。
弹簧淬火后,表面会留下不同程度的氧化层和碳质沉着,从而影响弹簧的承载能力和使用寿命。
弹簧回火是将弹簧加热至高温,使其表面氧化层脱落,内部组织恢复至原始状态。
回火温度根据弹簧材料的不同而异,通常回火温度在700-900°C之间。
2. 弹簧淬火+回火的性能表现弹簧淬火+回火后的性能表现包括以下几个方面:(1) 抗拉强度弹簧的抗拉强度是指弹簧在拉伸过程中所能承受的最大拉力。
在弹簧淬火后,表面会留下不同程度的氧化层和碳质沉着,从而影响弹簧的抗拉强度。
一般来说,淬火后的弹簧抗拉强度比未淬火的弹簧有所增加。
(2) 硬度弹簧的硬度是指弹簧在拉伸过程中抵抗变形的能力。
在弹簧淬火后,硬度会增加,因为表面氧化层和碳质沉着会增加弹簧的硬度和耐磨性。
(3) 弹性模量弹簧的弹性模量是指弹簧在拉伸过程中所储存的弹性能量。
在弹簧淬火后,弹性模量会增加,因为表面氧化层和碳质沉着会增加弹簧的弹性储存能力。
3. 如何提高弹簧的抗拉强度和硬度为了提高弹簧的抗拉强度和硬度,可以采取以下措施:(1) 控制弹簧淬火和回火的温度和时间。
(2) 采用先进的制造工艺,如表面光洁度控制、表面氧化层控制和碳质沉着控制等。
(3) 采用高质量的弹簧材料。
(4) 定期进行弹簧检查和维护,以保证弹簧的正常使用寿命。
弹簧淬火+回火后的抗拉强度和硬度是弹簧材料的重要性能指标之一,直接影响弹簧的承载能力和使用寿命。
通过控制弹簧淬火和回火的温度和时间、采用先进的制造工艺、采用高质量的弹簧材料以及定期进行弹簧检查和维护,可以提高弹簧的抗拉强度和硬度,从而提高弹簧的承载能力和使用寿命。
弹簧的淬火回火原理有哪些
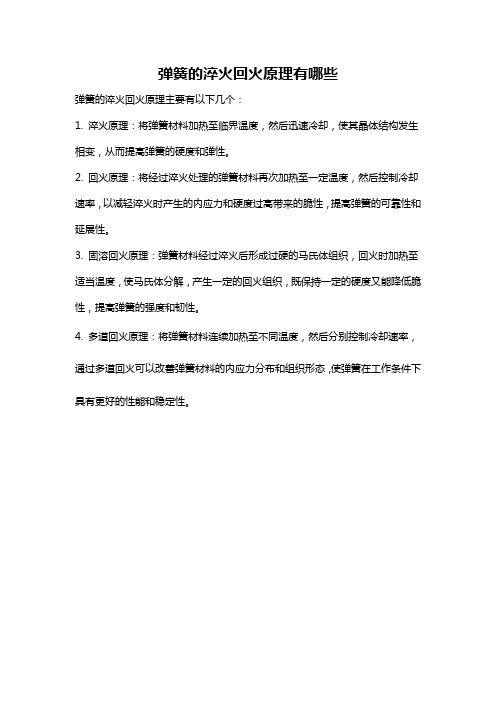
弹簧的淬火回火原理有哪些
弹簧的淬火回火原理主要有以下几个:
1. 淬火原理:将弹簧材料加热至临界温度,然后迅速冷却,使其晶体结构发生相变,从而提高弹簧的硬度和弹性。
2. 回火原理:将经过淬火处理的弹簧材料再次加热至一定温度,然后控制冷却速率,以减轻淬火时产生的内应力和硬度过高带来的脆性,提高弹簧的可靠性和延展性。
3. 固溶回火原理:弹簧材料经过淬火后形成过硬的马氏体组织,回火时加热至适当温度,使马氏体分解,产生一定的回火组织,既保持一定的硬度又能降低脆性,提高弹簧的强度和韧性。
4. 多道回火原理:将弹簧材料连续加热至不同温度,然后分别控制冷却速率,通过多道回火可以改善弹簧材料的内应力分布和组织形态,使弹簧在工作条件下具有更好的性能和稳定性。
- 1、下载文档前请自行甄别文档内容的完整性,平台不提供额外的编辑、内容补充、找答案等附加服务。
- 2、"仅部分预览"的文档,不可在线预览部分如存在完整性等问题,可反馈申请退款(可完整预览的文档不适用该条件!)。
- 3、如文档侵犯您的权益,请联系客服反馈,我们会尽快为您处理(人工客服工作时间:9:00-18:30)。
弹簧的淬火和回火
1.弹簧的淬火淬火就是把钢加热到临界温度Ac,或Ac:以上保温一定时间,使其奥氏体化,再以大于临界冷却速度急剧冷却,从而获得马氏体组织的热处理方法。
对于一般热卷螺旋弹簧、热弯板簧以及热冲压的碟形弹簧,最好是在热成形之后,利用其余热立即淬火。
这样可以省去一次加热,减少弹簧的氧化脱碳程度,既经济又改善了弹簧的表面质量。
例如60Si2MnA 钢板弹簧目前采用的热处理工艺是在900—925C弯片之后,在850~880℃入油淬火。
若受条件限制,也可在成形之后重新加热淬火。
冷成形的弹簧剩余应力较大,在淬火加热时,由于剩余应力的释放,变形较大。
为了保证弹簧尺寸精度,可在淬火之前加一次去应力退火处理,这样可以减轻淬火加热变形程度。
弹簧的淬火温度可根据弹簧材料的临界温度而定。
淬火后弹簧材料的金相组织中,应无自由铁素体和渗碳体,以免导致不均匀变形或疲劳强度的下降。
淬火加热时,应尽量防止氧化和脱碳。
为了保证弹簧的质量,在弹簧钢材的技术标准和各种金属弹簧的制造与验收技术条件中,对脱碳层的深度都有明确规定。
目前,大型弹簧成形加热和淬火加热,多采用火焰炉或电炉。
为了防止或减轻表面氧化和脱碳,得到较高的表面质量,最好采用可控制气氛的加热炉,或使炉中气氛略带还原性,并采用高温快速加热的方法。
对中小弹簧,可用脱氧良好的盐浴炉进行淬火加热。
弹簧淬火宜在油中冷却,以避免变形和开裂。
用尺寸较大的碳钢材料制造的弹簧,当要求不高时可用水冷。
为了减小变形量,除了采用正确的加热和冷却方法外,有时还采用专用淬火夹具进行成形淬火,例如板簧在弯板机上淬火,中、小型螺旋弹簧装在心轴上或专用夹具上进行加热和冷却。
2.弹簧的等温淬火主要应用在要求热处理变形小和希望获得良好的塑性和韧性的情况。
等温淬火就是将弹簧加热到该钢种的淬火温度,保温一定时间,以获得均匀的奥氏体组织,然后淬入Ms点以上20~50C的熔盐中,等温足够的时间,使过冷奥氏体基本上完全转变成贝氏体组织,再将弹簧取出,在空气中冷却。
这种处理比普通淬火、回火处理的材料具有更高的延展性和韧性,而且弹簧极少变形或开裂。
如果在等温淬火后再加一次略高于等温淬火温度的回火,则弹性极限和冲击韧性还能有所提高,而强度并没有大的变化。
等温淬火时,盐浴的温度是根据弹簧所要求的力学性能决定的,必须严格控制。
通常是稍高于该钢种的Ms点,获得下贝氏体组织。
如温度偏高,得上贝氏体组织,其硬度较前者低;如温度过低,虽能提高弹性极限,但塑性、韧性较差,以致失去等温淬火的优越性。
弹簧的等温淬火规范,即等温淬火温度和等温淬火保温时间,必须按照该钢号的等温转变曲线图确定。
表l为几种常用弹簧钢的等温淬火规范。
表1 几种常用弹簧钢的等温淬火规范
表2为几种弹簧材料等温淬火与普通淬火、回火工艺的力学性能对比表。
表2 等温淬火与普通淬火、回火工艺的力学性能比较
3.弹簧的回火将淬火后的弹簧重新加热到低于Ac1的某一选定温度,并保温一定时间,然后以适宜的冷却速度冷却的工艺方法,叫做回火。
回火的目的是:获得所需要的力学性能,稳定弹簧的组织和尺寸以及消除内应力。
各类弹簧经淬火、回火后的硬度为:一般螺旋弹簧HRC45—50;工作应力较高的弹簧(如喷油器调压弹簧)HRC47~52;钢板弹簧HRC42—47或HRC45~50;碟形弹簧HRC45~50。
对于淬火后变形的弹簧,可根据相变超塑性的原理(即钢由一种组织转变为另一种组织时,具有很大的塑性变形能力),在回火时,装上限形夹具,使变形在回火过程中得到回复和矫正。
对于硅铬弹簧钢和铬锰弹簧钢等回火脆性较大的钢种,回火后应立即在油中冷却或水中冷却。
回火的保温时间与弹簧材料的直径或厚度有关。
表3所列为不同规格的硅锰和铬钒弹簧钢回火时(硝
盐炉)的保温时间,供参考。
表3 硅锰和铬钒弹簧钢在回火温度为400~520C时的保温时间
回火是对弹簧使用性能有显著影响的热处理工序。
一般说来弹簧钢的弹性极限在回火温度为350~450~C 时出现最大值;而疲劳极限出现最大值的回火温度为450—500℃左右。
此外,回火温度较高时,钢的塑性及韧性得到改善,对缺口(及裂纹)的敏感性及过载损伤的倾向性也相应减小。
弹簧淬火后应尽快进行回火,以避免由于内应力过大而产生裂纹,淬火与回火之间的时间间隔一般不超过2~4h。