压合课制程简介
压合制程学习
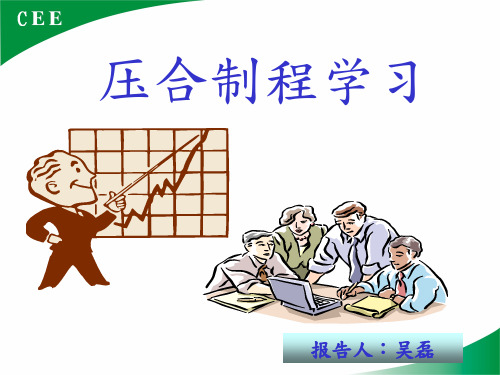
1.2压合流程简介
热熔
P/P打孔 铆 合 钢板打磨
进料检验
棕 组 叠 热 冷 拆 分 铣 化 合 板 压 压 板 割 靶 靶 边 边 修 出 货 P/P裁切 铜箔裁切
X-RAY钻靶
钻 捞 磨 检
2.棕化: 2.1目的: (1)粗化铜面,增加与树脂接触表面积 (2)增加铜面对流动树脂之湿润性 (3)使铜面钝化,避免发生不良反应 2.2流程:
投 板 酸 洗 纯水洗X2 碱 洗 热水洗
纯水洗X2
预 浸
棕 化
纯水洗X2
热水洗
烘 干
收 板
2.3棕化线主槽体作用简介: 1.酸洗槽:酸洗槽药水为SPS,H2SO4 ,主要作用是除去板子表面的 氧化物及异物(SPS药液浓度为:5-40g/L,H2SO4:4%~6%) 2.碱洗槽:碱洗含有: 碱洗主要成分是NaOH,主要作用是除去板 子表面残留的干膜,油脂及指纹印.(药液浓度为:NaOH:10~15%) 3.预浸槽:使用的药水是双氧水和KA-1,主要应用活化剤使板面 活化,使板面棕化更均匀,并防止前面的药液污染棕化槽导致棕 化异常(药液浓度H2O2:2%~3%) 4.棕化槽:使用的药水有四种,分别是双氧水、硫酸、KA-1和KR2,主要作用是:使铜面变的粗造增加基板与P.P的结合力,以防压 合爆板或分层. 5.各水洗段:清洗板面残留药水,避免污染下一个药水槽.
1.改良纯水 2.更换预浸槽 3.降低棕化槽的铜浓度
1.降低铜浓度 2.提高KA-1、KA-2浓度 3.更换棕化槽 1.加大清洁清洗力度 2.更换水洗槽 3.添加药水时严格按照 SOP操作 4.加强清洁处理,磨刷
2.板面发红
3.板上有异物
4.板面上有条纹 ,棕化膜薄的现 象 5.板的上部边缘 产生波纹状露铜
《压合制程培训》课件
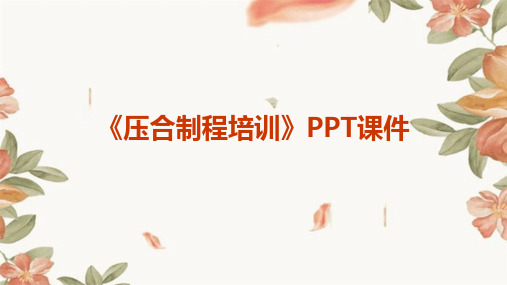
金属材料的种类与特性
钢铁材料
具有高强度、高硬度、良好的塑性和韧性等特性,广泛用于建筑、机械、交通 等领域。
有色金属材料
如铜、铝、镍等,具有良好的导电性、导热性、延展性和耐腐蚀性等特性,常 用于电子、电器、航空航天等领域。
金属材料的种类与特性
物理性能
包括密度、熔点、导电性 、导热性等。
废弃物分类与处理
对产生的废弃物进行分类,并按照相关规定 进行合理处理。
节约能源与资源
合理利用能源和资源,提高生产效率,降低 能耗和资源消耗。
安全与环保的持续改进
持续改进与创新
定期培训与考核
定期对员工进行安全和环保培 训,提高员工的安全意识和环 保意识。
定期检查与维护
对设备和环境进行定期检查和 维护,确保其安全、环保性能 良好。
根据粘接工艺和要求选择合适的胶粘剂。
胶粘剂的选择与特性
根据使用环境和条件选择合适的胶粘剂。 胶粘剂的特性
粘附力:胶粘剂能够将两个物体牢固地粘在一起的能力。
胶粘剂的选择与特性
01
02
03
耐温性能
胶粘剂在不同温度下的稳 定性和耐热性。
绝缘性能
胶粘剂的绝缘性能对于电 子产品的可靠性至关重要 。
化学稳定性
03
表面划痕
表面划痕可能是由于摩擦或硬 物刮擦造成。解决方案包括提 高操作过程中的防护措施,定 期检查和更换刮刀等工具。
04
脱层
压合过程中,如果材料之间未 能充分粘合,可能导致脱层现 象。解决方案包括确保材料清 洁度、优化胶粘剂涂布工艺等 。
质量持续改进的方法
01
02
03
04
压合制程介绍..

压合制程目的:将铜箔(Copper Foil),胶片(Prepreg)与氧化处理(Oxidation)后的内层线路板,压合成多层基板.内层氧化处理(Black/Brown Oxide Treatment) 氧化反应A. 增加与树脂接触的表面积,加强二者之间的附着力(Adhesion).B. 增加铜面对流动树脂之润湿性,使树脂能流入各死角而在硬化后有更强的抓地力。
C. 在裸铜表面产生一层致密的钝化层(Passivation)以阻绝高温下液态树脂中胺类(Amine)对铜面的影响。
还原反应目的在增加氧化层之抗酸性,并剪短绒毛高度,至恰当水准以使树脂易于填充并能减少粉红圈( pink ring ) 的发生。
黑化及棕化标准配方:表一般配方及其操作条件上表中之亚氯酸钠为主要氧化剂,其余二者为安定剂,其氧化反应式。
此三式是金属铜与亚氯酸钠所释放出的初生态氧,先---生成中间体氧化亚铜----2Cu+[O] →Cu2O,再继续反应成为氧化铜CuO,若反应能彻底到达二价铜的境界,则呈现黑巧克力色之"棕氧化"层,若层膜中尚含有部份一价亚铜时,则呈现无光泽的墨黑色的"黑氧化"层。
制程操作条件( 一般代表),典型氧化流程及条件。
棕化与黑化的比较黑化层因液中存有高碱度而杂有Cu2O,此物容易形成长针状或羽毛状结晶。
此种亚铜之长针在高温下容易折断而大大影响铜与树脂间的附着力,并随流胶而使黑点流散在板中形成电性问题,而且也容易出现水份而形成高热后局部的分层爆板。
棕化层则呈碎石状瘤状结晶贴铜面,其结构紧密无疏孔,与胶片间附着力远超过黑化层,不受高温高压的影响,成为聚亚醯胺多层板必须的制程。
B. 黑化层较厚,经PTH后常会发生粉红圈(Pink ring),这是因PTH中的微蚀或活化或速化液攻入黑化层而将之还原露出原铜色之故。
棕化层则因厚度很薄.较不会生成粉红圈。
内层基板铜箔毛面经锌化处理与底材抓的很牢。
压合制程简介

疊 板
板面抽檢
黑化處理:
何為黑化:黑化俗稱黑氧化,是將內層板面之裸銅線路經 清潔後再經化學反應使其氧化,其氧化膜為 黑色,故稱為黑化。 目的:增加內層板銅面的表面粗糙度,進而增加樹脂與 銅皮之間的結合力。
內層板 熱 水 洗
水洗
清 潔 抗氧化 烘 乾
水洗 水洗
微 還
蝕 原
水洗 水洗
預 氧
浸 化
組合或預疊製程
絨毛結構
黑化品質重點
•Weight Gain:0.2~0.35 mg/cm2 •表面不可刮傷、露銅、色澤不均、嚴重之 Roller Mark 。 •黑化後上壓時間< 48 hr
黑化品質檢測項目:
1.微蝕速率(Etching rate) 2.絨毛重量差(Weight gain) 3.抗酸測試(Acid resistance) 4.抗撕強度(Peeling strength) 5.熱應力實驗(Thermal stress)
後處理流程:
割 邊 剖 半 銑 靶
品質抽檢
磨邊水洗
撈 邊
銑靶製程:
目的:依內層所曝之靶像銑出靶孔,以利成形或 鑽孔套 PIN用;若以二壓板而言,可作為 Mask曝光對位孔 使用設備:X-ray880與X-ray888鑽靶機 作業標準:不可破靶 靶距功用:檢測板子之漲縮值 內層板補償之依據 將內層對位之靶型,以X-ray掃描後 計算重心鑽出孔型,以利鑽孔定位。 (鉆孔精度為此製程重點)
壓 合 製 程 簡 介
何为压合
•藉由高温.高压制程将半硬化胶片(树脂 及玻璃布组成)、内层线路板、铜箔依所 设计之讯号传递方向与功能,有顺序黏合 成一体(多层板),使其具有一定程度之耐 热.抗酸碱等特性,以利于后制程加工。
压合制程简介教育内容

(2)上第二段壓時間
(3)壓力
6-4目前傳統壓合最適的壓條件為:(P.P用tetra-function)
(1)第一段溫度140℃40~50min
第二段溫度185℃70~80min
第一段壓力100~200psi30min
第二段壓力350~450psi90min
(2)升溫速率控制在1.6 ~1.8℃/min
.
烤箱溫度
.
黑化拉力test.
(2)鉚釘對準度.
(3)組合之P.P是否正確.
(4)疊板時的對準度.
(5)熱壓的溫度.壓力設定.
(6)裁半之板面檢查:針孔凹陷、鄒折、氣泡(凸出)……
(7)漲縮值.
(8)外框之尺寸及粗糙度.
(9)壓合後板厚測試.
二.壓合製程原物料介紹
2-1主要原料
2-1-1內層基板(Thin Laminate)
(2)粉紅圈:有專案報告
(3)阻抗值不足:有專案告
(4)白點:有專案報告
六.結論
6-1壓合流程為多層PCB相當重要的一站,若壓出品質不良,
很可能會造成成品板信賴度的問題.
6-2未來PCB趨勢為盲埋孔之HDI板及增層板,壓合流程更為重要
,且壓合的領域及知識又比傳統方式來得更新且差異性亦很大.
6-3目前傳統壓合影響品質的主要因子為
(1)檢查重點:
拉力強度.
抗酸強度.(抗化學測試)
表面檢查.
蝕銅後檢查板內.
爆板測試.
(2)一般內層基事板31mil以下板為不含銅箔.
31 mil (含)以上板原為含銅箔.
2-1-2膠片(prepreg)
(1)檢查重點:
膠流量(Resinflow)
压合制程基础知识
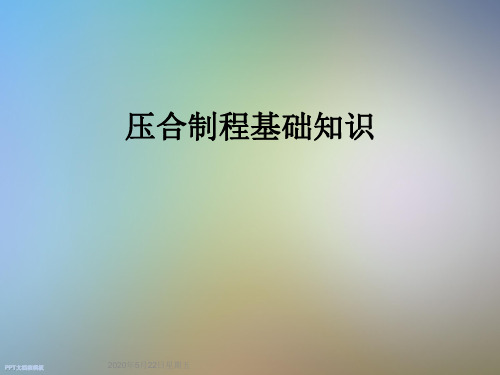
process B/F B/O
存放时间 72hrs 24hrs
(3天) (1天)
35
排版品质管制----潜在问题
❖ 多放或少放PP ❖ 铜箔起皱 ❖ dent ❖ 失压产生白边
36
品质管制----多放或少放PP
原因: 排版人员放错 问题改善:
➢ 放板人员在生产前要对照工单准备材料,每片放板后要再确认 PP数量
问题改善:
➢ 铝板在生产前必须经过CM5及粘布清洁 ➢ 每生产1cycle,必须更换粘布 ➢ 每星期用百洁布清洁铝板并检查,对有划伤或超过5个凹点的
铝板挑出报废 ➢ 排版生产必须确保除尘装置打开,每星期清洁除尘过滤网
39
品质管制----失压产生白边
原因:
❖ 镭射光线在排版生产中有偏移 ❖ table在排版生产中有偏移 ❖ 没有沿镭射光线放板
相邻行的dummy pad要错开设计,改善流胶
1.5mm
4.0mm
41
排版设计准则---内层板设计要求
在板内设计时,若在被Rout去掉区域比较大时,要求在Rout 区域 内加上dummy pad,以增加残铜率,减少填胶,要求pad直径为 4.0mm,间距要求为1.5mm
无用区域使用dummy pad.
问题改善:
在排版生产前必须固定镭射光线和table 在底盘上做标记,可及时发现在生产过程中镭射光线或table偏
移情况
在排版生产中必须沿镭射光线放板
40
排版设计准则---内层板设计要求
内层板板边用dummy pad 填充,要求pad直径为4.0mm,间距要求 为1.5mm,
在内层板相对应的两层dummy pad ,要求错开半个pad距离,以平 衡压合时压力
PCB压合制程基础知识精品文档

1
工序简介
压合是利用高温高压使半固化片受热融化,并使其流 动,再转变为固化片。从而将一块或多块内层蚀刻后板 (经黑化或棕化处理)以及铜箔粘合成一块多层板的制 程
本制程还包括将压合前的排版,压合后的多层板进行 钻定位孔及外形加工
所使用半固片张数: 1080 以下半固化片 18张; 2313以上半固 化片10张;
• 测试条件
– 压制温度: 150℃ – 压力:840 磅
22
指标测试—凝胶化时间
• 凝胶化时间(Gel time)定义
– 从半固化片树脂粉末加入热盘起至不再流动完全胶化时所持 续的时间.
• 仪器:凝胶测试仪 • 样品: 200±20 毫克树脂粉末 • 测试条件:171℃
62.3ห้องสมุดไป่ตู้
7628
Thickness Weight
RC
Mil (g/5.5x7x10inch2) (%)
4.7
80
37.0
4.81
81
37.8
4.93
82
38.5
5.05
83
39.3
5.17
84
40.0
5.28
85
40.7
5.4
86
41.4
5.52
87
42.1
5.63
88
42.7
5.75
89
43.4
5.87
在板角设计生产序号,RBM人员按照生产序号放板 在RBM机器上增加防错装置,并在所有料号上添加防错块
14
排版制程简介:
排版过程是根据结构要求,把内层core,半 固化片及铜箔用铝板分隔排好,并达到压 合所需要的高度
压合课制程讲解

目視 目視 目視
鋼板磨刷管制項目
管制項目 傳動速度 刷壓電流 刷幅寬度 烘干溫度 友大 3.5-4m/min 3.0±0.5A 1±0.2CM 75±15 ℃ 連毅 4m/min 3±1A 1±0.2CM 75±10 ℃
疊板目的
將鋼板、銅箔、組合板按一定順序疊到open內。
管制項目: 管理項目 標準 牛皮紙 20張用4次
主 講 人 : 羅 雲 龍
壓合主要功能
壓合是將內層板、PP膠片、銅箔按一定的順 序疊合后,然後通過高溫、高壓粘合在一起, 使之成為四層板或多層板。 四層板疊合方式:
1/2OZ PP 內層 PP 1/2OZ
各制程知識講解
一、黑化 作用:a.在內層銅面上生成一層細密的純化 層,陰絕在熱壓時,PP對銅面不良 的氯化和其它污染。 b.增加內層板銅面與PP的接觸面積。 目的:a.增強PP與內層的結合力和穩定性。 b.增強銅面感觀。
3.皺折 主要原因:1.銅箔未刷平。 2.上下層對位不準。 3.滑板。 4.牛皮紙使用次數過多。 5.鋼板有水。 改善對策:1.拉銅箔時將銅箔鋪平。 2.上下層不要滑動、以免錯位。 3.四周放置鐵夾子。 4.牛皮紙規定正確使用的次數。 5.檢查磨刷機烘干段及輸送滾輪。
4.汽泡 主要原因:1.PP溫度太高。 2.PP、銅箔上有水。 3.壓力不足。 4.抽真空不良。 改善對策:1.PP儲存條件需達到要求。 2.避免PP、銅箔作業處有水產生。 3.在適當的時候,加大壓力。 4.上機時,檢查抽真空。
PP具吸水性,儲存條件由低溫到高溫會立刻吸 水、回潮,影響壓合品質,故PP的儲存條件: 溫度 22 ±2℃ 濕度≦60%
黑化主要品質問題點: 1.紅斑 產生原因:a.黑化槽藥水濃度不夠 b.黑化槽藥水溫度不夠 2.露銅 產生原因:a.膠跡露銅 3.刮傷 產生原因:搬運動作不規範。 4.臟物 產生原因:a.板面附有臟物 5.黑化不均 產生原因:a.微蝕藥水濃度不夠 b.微蝕藥水溫度不達標 b.槽液干凈 b.油墨露銅 c.臟物露銅 c.預浸槽濃度不夠。
PCB压合制程基础知识

23
指标描述-Resin content含胶量 半固化片含胶量(RC)
RC主要与层压板的厚度有关。 RC偏低,板的厚度偏薄; 如果RC的左中右偏差较大,就会造成板的厚度均一致性差。 控制好半固化片的RC,压合后就可以得到需要的厚度,并 提高厚度的Cpk值。
24
含胶量与PP厚度对照表
25
树脂填胶后厚度计算:
PP压合后厚度
厚度= 单张PP理论厚度 – 填胶损失 填胶损失 = (1-A面铜箔残铜率)x铜箔厚度+(1-B面铜箔残铜率)x铜箔厚 度+0.4*(D2)2*H(內层板厚度)*N(孔数)/整板面积
無埋孔
prepreg
prepreg
有埋孔 A
pre
17
半固化片规格
WHT/SQ Thread Count Fill Glass Style R/C type YD (g/m2 Warp ¡ À 3 ¡ À 3 ) 106 75 56 56 24.4¡ À 1 61 60 47 46.8¡ À 2 1080 63 60 47 46.8¡ À 2 65 60 47 46.8¡ À 2 1500 45 48 44 164.1¡ À 5 1506 48 48 44 164¡ À 5 1652 48 52 52 138.3¡ À 5 2113 56 60 56 78¡ À 2 48 60 58 103.8¡ À 3 2116 53 60 58 103.8¡ À 3 57 60 58 103.8¡ À 3 43 44 32 203.4¡ À 5 7628 48 44 32 203.4¡ À 5 press thickness( mil/ply) 2.5¡ À 0.3 2.8¡ À 0.3 3.0¡ À 0.3 3.2¡ À 0.3 6.3¡ À 0.5 7.0¡ À 0.5 5.8¡ À 0.5 4.0¡ À 0.4 4.5¡ À 0.4 5.0¡ À 0.4 5.5¡ À 0.4 7.5¡ À 0.5 8.7¡ À 0.5 Resin Content ¡ À 3.0% 75 61 63 65 45 48 48 56 48 53 57 43 48 Resin Flow ¡ À 5% 55 36 40 43 25 30 27 35 25 32 38 23 30 Volatile Gel Time Content ¡ À 20sec (Max. %) 0.5 145 0.5 145 0.5 145 0.5 145 0.5 145 0.5 145 0.5 145 0.5 145 0.5 145 0.5 145 0.5 145 0.5 145 0.5 145
TWT压合制程简介

左圖為將内層板與對應之PP鉚合機台。
Байду номын сангаас鉚钉机
Ps:铆合业界有铆钉铆合和热铆合两种作业方式 1、铆钉铆合指利用铆钉将前预叠pcb內層板铆合起 来; 2、热铆合指利用热铆机,采用局部加热的方式, 让该区域胶片熔融、硬化,将前预叠各层板材结合 起来,进而达到铆合效果。
Process Engineering Department
可能原因及對策
長時間停產後各藥液槽濃度偏低:分析並調整濃度至其控制範圍 清潔劑濃度超出範圍:分析並調整濃度 前工序残膠:檢查前工序 DI水中Cl-濃度超過3ppm:檢查DI水系统 H2O2中Cl-濃度偏高:使用Cl-<10ppm的H2O2
Process Engineering Department
Process Engineering Department
TWT
CHI CHAU PRINTED CIRCUIT BOARD (SUINING)CO., LTD.
二、壓合流程
棕化產生之問題與分析
棕化層不均匀
棕化後所看到的棕化皮膜不均匀,一般是因為棕化槽的水刀流量不合適 所引起。太過强烈的流量,補丁狀和雲霧狀的斑點是分區域出現的;當 流量太低時,補丁狀和雲雾狀的斑點则會交错出現。另外,最後的水洗 也很重要,它的作用是將板面的化學物質清除掉,但如果喷嘴壓力過大 也會在皮膜表面留下斑點。
可能原因及對策
H2SO4或H2O2濃度不正確:分析並調整至控制範圍; Part-A補充量不正確:分析並調整至控制範圍; H2O2中Cl-濃度太高:分析Cl-濃度,使用Cl- <10ppm的H2O2; 流量太小:檢查並調高流量。同時檢查並清洗過濾芯和流量計; Di水中Cl-含量太高:檢查DI水系统,使用Cl- <3ppm的DI水。 顏色 OK 顏色 NG
压合制程培训

黑化不良
问题点 黑化 不良 原因分析 1、药水浓度失调 2、内层板去膜不良 3、水洗槽水被酸碱 污染 4、板面氧化或有油 脂 改善对策 1、化验分析调整至范 围内 2、保证内层去膜干净 3、更换新的水 4、加强前处理效果, 特别是微蚀
安全作业
站别
黑化
相关规定
1、添加药水时需戴胶手套、眼罩、穿水鞋 2、天车运行时,严禁人将身体伸到天车轨道 以内 3、进到天车运行轨道以内时,需按紧急停止 键,并在控制面板上挂好标识“线上有人” |”匆开机“
PP冲孔
目的
机台 使用
在PP上冲孔,便于铆合作业
PP冲孔机
管理 重点
①PP上所冲位置应与内层板铆合孔位置一致 (相对应) ②PP不能有折痕 ③冲针一定需对准模具套,以免断针
铆合
目的 用铆钉把两张或以上内层板与PP固定在一 起,保证内层板各个导通孔的相对位置, 避免层偏现象
管理重点 ①铆钉的尺寸应依内层厚度及PP规格张数 来选用 ②铆钉直径应与内层铆合也一致
H2SO4:2-4% SPS:40-50g/L CU2+:<15g/L 温度:30±2℃ 时间:1.5-2.5min ①生产500PNL添加2KgSPS ②生产2000m2或CU2+>15g/L时换槽 ③微蚀量控制在40-60g/L
在板面的铜,活化铜面,保护黑 化槽不被其它药水污染
①X-Ray两轴间距在280mm-610mm之 间,第三孔在50mm-150mm方能进行自 动钻靶作业 ②靶距允许值:+/-0.15 面积:30% 层间对位:20UM ③钻靶方式:以MARK中心钻靶.
管理重 点
捞边
目的 用CNC机按规定尺寸铣除四周多余部分,使 之尺寸一致,利于后制程作业
压合制程介绍

压合制程目的:将铜箔(Copper Foil),胶片(Prepreg)与氧化处理(Oxidation)后的内层线路板,压合成多层基板.内层氧化处理(Black/Brown Oxide Treatment) 氧化反应A. 增加与树脂接触的表面积,加强二者之间的附着力(Adhesion).B. 增加铜面对流动树脂之润湿性,使树脂能流入各死角而在硬化后有更强的抓地力。
C. 在裸铜表面产生一层致密的钝化层(Passivation)以阻绝高温下液态树脂中胺类(Amine)对铜面的影响。
还原反应目的在增加氧化层之抗酸性,并剪短绒毛高度,至恰当水准以使树脂易于填充并能减少粉红圈( pink ring ) 的发生。
黑化及棕化标准配方:表一般配方及其操作条件上表中之亚氯酸钠为主要氧化剂,其余二者为安定剂,其氧化反应式。
此三式是金属铜与亚氯酸钠所释放出的初生态氧,先---生成中间体氧化亚铜----2Cu+[O] →Cu2O,再继续反应成为氧化铜CuO,若反应能彻底到达二价铜的境界,则呈现黑巧克力色之"棕氧化"层,若层膜中尚含有部份一价亚铜时,则呈现无光泽的墨黑色的"黑氧化"层。
制程操作条件( 一般代表),典型氧化流程及条件。
棕化与黑化的比较黑化层因液中存有高碱度而杂有Cu2O,此物容易形成长针状或羽毛状结晶。
此种亚铜之长针在高温下容易折断而大大影响铜与树脂间的附着力,并随流胶而使黑点流散在板中形成电性问题,而且也容易出现水份而形成高热后局部的分层爆板。
棕化层则呈碎石状瘤状结晶贴铜面,其结构紧密无疏孔,与胶片间附着力远超过黑化层,不受高温高压的影响,成为聚亚醯胺多层板必须的制程。
B. 黑化层较厚,经PTH后常会发生粉红圈(Pink ring),这是因PTH中的微蚀或活化或速化液攻入黑化层而将之还原露出原铜色之故。
棕化层则因厚度很薄.较不会生成粉红圈。
内层基板铜箔毛面经锌化处理与底材抓的很牢。
压合工艺流程

一、工序简介1、层压是将经过内层,蚀刻、黑化(棕化)好的内层板两面加上不 同型号的PP片及铜箔利用高温高压结合在一起进行层压,而形成 的多层板。
2、随着电子技术的高速发展及大容量,低耗方面发展,多层板的应 用会越来越广泛,其层数会要求越来越高,因此层压成为多层板 生产中不可缺少的部分工艺。
二、压合制程工艺流程开PP 合格板开铜箔排板 压板 拆板 铣铜皮钻管位孔 外形加工QC 检板合格进行外层制作三、压合课各工作岗位的工艺及工作流程1、内层芯板来料检查。
1.1 接来料内芯板须认真核对数量。
1.2 核对数量无误后三、四层板交QC 检查,四层以上板先交打靶人员 将铆钉孔冲出在交QC检查。
2.黑化(棕化)2.1 黑化(棕化)目的是增强内层板与PP 片之间的结合力。
压合制程工艺流程QC 检查 黑化 烘板 QC 2.2 流程:进板 清洁 热水洗 酸洗(H 2SO 4) 纯水洗预浸 棕化 纯水洗 烘干 收板3、开PP 料及注意事项3.1 进入开PP 间必须穿防静电服,戴帽子和口罩,开PP 间的温度要 求为21±3℃,温度为50±10%。
3.2 开PP 人员接MI 后,严格按要求进行开料,一般PP 料的尺寸须比芯板大2-3mm ,且PP 料的经纬线须与芯板的经纬向一致。
3.3 PP 料的保存期为三个月,开pp 料必须先进行为原则。
4、预叠4.1目的:根据MI (生产制作指示)在内层板两面帖上不同的型号的PP胶片,经压合后使内外层紧密结合并绝缘。
4.2 预叠时必须戴防静电手套,穿防尘工衣作业。
4.3 预叠时应认真仔细双面检查板面是否有擦花露铜及棕化线不良等,否则挑出重工处理。
4.4 预叠之前应根据MI 检查排板结构PP 的横直料是否与内层板躲横直料相同。
如下图:5、铆钉5.1 目的:(是指六层以上的板)将两个内层板用铆钉铆合在一起。
5.2 手工打铆钉是有线路层放在下面,操作时须戴静电手套或胶手指套。
压合课制程讲解

±1kg/cm2 ±5min ±10kg/cm2
50分鐘以上 40
100
壓合品質重點
1.凹陷 主要原因:1.疊板室、組合室清潔度不夠。 2.物料不潔。 3.機器臟。 4.人員進出管制不當。 改善對策:1.根據疊板室的實際情況,建立正確的清潔方案 2.減少物料與外界的接觸,對物料進行檢查。 3.擬定適當的機器保養方案。 4.建立疊板室進出管制,減少人員進出次數。
3±1A 1±0.2cm
75 ±10℃
下風刀垂直 上風刀前傾3.5。
壓合課管制重點
3.疊板 目的:將銅箔、組合板按順序疊合在open里。 管制項目 疊板層數 氣壓 鋼板清潔度 銅箔清潔度 牛皮紙 無塵刷子 控制範圍 13層鋼板 6-8kg/cm2 無臟物、無水 無污染、無水 14張新6張舊 2open更換一次
7628HR 7628 2116 1080
含膠量
50 ±3% 43 ±3% 52 ±3 ±5%
凝膠時間 160 ±20sec 150 ±20 sec 160 ±20 sec 160 ±20 sec
厚度 0.25mm 0.23mm 0.144mm 0.08mm
30 ±5% 35 ±5%
本課量產用銅箔為1/2OZ
壓合課主物料
3.牛皮紙 厚度:0.254MM 作用: 1.熱壓時,減緩傳熱速率,均衡溫度和壓力,減少方向溫差。 2.隔在板與板之間,防止板刮花及存放時氧化。 4.銑刀 作用:裝於SPINDLE高速旋轉切割壓合板。 規格:¢ 2.5mm 規格:45〞*32〞 面積:160G/M2
微蝕
30 ℃±5℃
2-3min
預浸 黑化
1.5min 4-6min
壓合課管制重點
2.鋼板磨刷 目的:清潔鋼板表面 管制項目 傳送速度 鋼板間距 水洗壓力 刷壓電流 刷幅寬度 烘干溫度 風刀角度 友大磨刷機 3.5-4m/min 30-40cm 2.5-3kg/cm2 3.0 ±0.5A 1 ±0.2cm 75 ±15 ℃ 邊毅磨刷機 4m/min 40-50cm 2.5-3kg/cm2
压合课流程讲议

10.測板厚
功效:
每個open取1pnl測 量壓合板厚,檢驗 壓合板厚與工單要 求板厚是否相符.
11.冷吹
功效:
將下料之板用風扇 冷吹至常溫,減小 板子的漲縮.
12.X-RAY鑽靶
功效:
利用X-RAY射線將 內層靶形照出,然 后將靶孔鑽穿,方 便后制程上PIN定 位,也可測量板子 漲縮.
13.成型
功效:
將板邊多餘流膠及 邊料撈掉,使板尺 寸與工單要求成型 尺寸相符.
14.磨邊
功效:
將撈邊后之板邊 的毛刺, 打磨圓滑, 使板面不易刮傷.
15.品檢
功效:
對壓合板進行板面 檢查,不良項目有: 凹陷,銅破,皺折,刮 傷,氣泡,氧化,撈邊 不良,磨邊不鋼板磨刷 熱壓 冷壓 鑽靶 PP裁切 銅箔裁切 下料 撈邊 測量板厚 磨邊 品檢.
PP沖孔、熔合
(六層板以上)
疊板 冷吹
1.棕化(水平)
功效:
將內層板銅表面以 微蝕粗化與有機物 結合成有機銅錯合 粗糙表面,增加內 層板與PP經壓合后 之結合力.
棕化(垂直)
3.預疊、熔合
功效:
依工單之壓合疊構 對裁切后之PP與棕 化后之內層板組合 在一起,四層以上 板需對PP衝孔后再 進行PP與內層板熔 合或鉚釘作業.
4.鋼板磨刷
功效:
分為人工打磨和機 器磨刷,將鋼板表 面異物去除,防止 出現壓合板面凹陷.
5.銅箔裁切
功效:
依工單選用所需 之銅箔型號,再將 卷筒狀之銅箔裁 成與鋼板大小相 同之尺寸.
功效:
利用微蝕粗化銅面 進行氧化銅結晶絨 毛,再利用EDTA將 氧化銅結晶絨毛去 除90-95%,增加內 層板與PP經壓合后 之結合力.
- 1、下载文档前请自行甄别文档内容的完整性,平台不提供额外的编辑、内容补充、找答案等附加服务。
- 2、"仅部分预览"的文档,不可在线预览部分如存在完整性等问题,可反馈申请退款(可完整预览的文档不适用该条件!)。
- 3、如文档侵犯您的权益,请联系客服反馈,我们会尽快为您处理(人工客服工作时间:9:00-18:30)。
1080
60士10m/min
2116
45士15m/min
其它
40士10m/min
1.1.3 刀片的更換
刀片的更換頻率
75m/次
刀片更換頻率直接影響PP裁切的效果,不及時更換,則PP裁切后
的邊緣粗糙,PP粉(環氧樹脂)與玻璃纖維布結合力差,搬運及疊
P 33
合過程中,PP粉易掉落,形成PP粉凹陷,且刀片不鋒利,裁斷玻 纖布時,玻纖絲受力大而外露,且玻纖束中的玻纖絲因受較大 的力而鬆散,易脫落、飛散,形成玻纖凹陷 1.1.2.4 PP (Prepreg)的經緯向
2.2.9 其它 如:附著性、表面粗度、抗撕強度、抗化學藥品性、抗焊性等等.
牛皮紙
待棕化 多層板
P 21
1.黑化簡介
棕化工藝介紹
黑化工藝在多層板生產中占據著重要位置,是大家非常熟悉的工藝,它 不但直接影響著多層板的物理性能如熱衝擊實驗,而且還影響著多層板的 外觀,黑化不均勻很容易引起客戶的退貨;另外粉紅圈也著實令人頭痛,避 免粉紅圈大量出現就是黑化后增加后處理,可成本也跟著增加了.
種,電解銅箔(ED-Foil)由於兩面粗糙度不同,較粗糙之一面經處
理后,與PP(Prepreg)熱壓時,可和樹脂產生很強的接著力,較適
於做Байду номын сангаас銅面積層板的原料.
銅箔規格的區分,由之前的絕對厚度改為以基重(area weight)表示
反面銅 箔
正面銅 箔
正面銅箔 輸送
反面銅箔 輸送
P 15
2.2 銅箔的品質要求
P 25
4.2.6.物理及化學特性 a.外觀:乾凈液體 b.氣味:N/A c.PH值:12 d:可熔 e.沸點:高於1300C g.冰點:-200C h:比重:1.020@200C
4.3.100a 4.3.1.化學成分:有機酸混合物 4.3.2.用途:銅箔涂層轉換 4.3.3.主要特征:無色或黃色的酸性,嚴重刺激及眼睛,皮膚 4.3.4.潛在健康影響因素:
P4
1.1.3.樹脂:大概可分為熱塑性樹脂與熱硬化性樹脂,而用於印刷電路 板所用的樹脂都是熱硬化性樹脂,熱硬化樹脂的單體除了 兩只手(官能基)外,尚有內部的手彼此交接而成網狀結構, 但在加壓加熱的同時,多餘的手也全部交接而不動, 亦即變 硬,此種狀態稱為硬化.樹脂的種類有<1>酚醛樹脂 <2>環氧 樹脂 <3>聚亞硫胺樹脂 <4>聚四氟乙烯樹脂
压合课制程简介
2020年5月22日星期五
治具制作 P/P打孔 鉚合
X-RAY鑽靶 裁板磨邊機
進料檢驗 棕化 組合 疊板 熱壓 冷壓 拆板 分割 銑靶
鑽靶 撈邊 磨邊 清洗
P2
P/P裁切 銅箔裁切
檢修
出貨
P3
壓合主物料介紹
1.1.PP(Prepreg):
主要由玻璃纖維布以及樹脂組成,與一般玻璃類似,但以鈣、鋁、矽、 硼等氧化物為主,絕緣性及延展性比一般玻 璃重要. 1.1.1.玻璃纖維:是將玻璃原料調配好在12300c的高溫下,使之熔融成為
漂錫 測試
1.在樣板鍍上錫鉛之后; 2.放入溫度為288士5.50C的錫爐中,時間為10sec、15sec 、20sec 、 30sec; 3.同時測量放置不同時間時拉力的變化;
4.完成上述試驗后,做切片分析,檢查有無爆片分層;
檢測下述兩個條件下完成的測試樣板的爆板分層狀況;
沉錫 1.2600C 20秒 浸泡一個循環 測試 2.2880C 10秒 漂一個循環
a.外觀:清潔,黃色液體 b.PH值:小於0.8 c.可溶性:可溶 d.詣點:高於1000C e.冰點:低於00C f.比重:1.090@200C
P 27
4.4.100b 4.4.1.化學成份:Alkgl Sulforic Acid Sodium Salt Compound 4.4.2.用途:銅箔涂成轉換 4.4.3.主要特征:無色或黃色的酸性藥水,嚴重刺激眼睛、皮膚 4.4.4.潛在健康影響的因素 a.眼睛:引起眼睛灼熱,可能也引起不可治癒的傷害 b.皮膚:引起皮膚灼熱,持續接觸會引起組織壞死 c.吸入:引起呼吸器管的傷害 d.吞咽:會引呼吸道受到伴有灼熱的疼痛的刺激,引起嚴重的傷 害 4.4.5.儲存:放置在陰冷、乾燥的地方,遠離熱量或火星,有足夠的通 風系統保證空氣流通 4.4.6.物理及化學特性:
P 26
a.眼睛:引起眼睛灼熱,可能也引起組織壞死 b.皮膚:引起皮膚灼熱,持續接觸會引起組織壞死 c.吸入:引起呼吸管的傷害 d.吞咽:會引起呼吸道受到伴有灼熱的疼痛的刺激,引起嚴重的傷害 4.3.5.儲存:放置在陰冷,乾燥的地方,遠離熱量或火星,有足夠的通風
系統保證空氣的流通 4.3.6.物理及化學特性
3.3檢驗項目
基重、厚度、密度、尺寸、吸水性.表面狀況,升溫速率的變化,耐高 溫、高壓性能
P 18
2.2.7 抗氧化性 (Tarnish resysarce) 在搬運及存放期間,銅箔表面不可氧化變色.
2.2.8 蝕刻斑點 (Etching stain) 蝕刻后,積板表面不得有殘銅及銅粒等斑點存在.
Ltigh Relative Humidity
Temp./Time
P5
PP吸濕性极強,當其 吸收大量水分,則粘 度降低,壓合過程中 會造成流膠增大白點 白邊
P6
1.3PP(Prepreg)的特性
固化區 黏彈狀區
黏稠狀區
流體狀區
a
b
時間
c
P7
整個壓制程預溫過程,是B階段樹脂從難以流動的黏彈狀,逐漸轉變成流體 狀,再轉變成凝膠狀的變化過程;在這個過程中,樹脂於高溫下進行熔融和 流動,並同時完成對玻璃纖維的進一步浸潤.樹脂的流動性是按指數上升, 隨著分子鏈的不斷增長,隨即產生交聯作用,樹脂內部逐步建立起自身的 內聚強度,又使樹脂黏度不斷增大,它的流動性又沿指數規律下降,最后達 到不再流動的膠凝狀,直至固化為止.
2.2.1 純度(Rurity) 生箔(未經任何表面處理之銅箔)之純度要求,電解銅箔需高於 99.8%,壓延銅箔需高於99.9%(由於銀的導電度和銅相近,且電 解時銀很容易和銅一起被折出,因此純度計算通常將銀亦算在內
P 16
2.2.2 針孔 (pinholes) 1/2QZ以下(厚度)之銅箔不可有大於0.10m/m大小之針孔,1/2QZ銅 箔針孔數不可多10點/ft2,大小不得大於0.05m/m.1QZ以上銅箔,針 孔數不得多於5點/ft2,且在任何5ft2內,不得有大於0.125mm之針孔 發生.
液體,然后由白金所做的小口徑抽口用力擠出,並快速噴 出冷卻及做上漿處理,而成多根並合的玻璃絲,此200~400 根並合在一束稱為玻璃紗,再由單紗或多根併燃的復紗 按經緯方向織布,即完成玻璃布的制作. 1.1.2.織布:有平織法、格子法、針織法、提花法、斜織法…..但目前線 路板則采用單紗平織法,因其尺寸安定性最好.
1.棕化槽液混合均勻后 再做板
2.調整棕化槽液的流量 3.加大清潔力度
7.“月牙露銅”現 因挂架變形與板的銅面接觸發 挂架變形的地方不插
象
生反應
板
P 32
壓合工藝介紹
1.疊板工藝介紹
1.1.PP裁切工藝介紹
1.1.1 作用:將一卷PP按要求裁切成與內層板一樣大小的PP片,用來組
合內層板.
1.1.2 PP裁切的速度控制:
隨著多層板輕型化發展,大量0.2mm甚至0.1mm的內層開始出現,傳統黑化 工藝的局限性更加突出:
1.1.一般的挂藍無法解決板重疊的問題 1.2.特殊的挂藍(如用teflon線)成本很高,並且操作不方便,效率低,在
此種情況下,棕化工藝應運而生.
P 22
2.棕化反應原理
在棕化槽內,由於H2O2的微蝕作用,使基體銅表面形成一種碎石狀微 觀結構,同時立即沉積上一層薄薄的有機金屬膜,由於有機金屬膜與基體
1.4.PP(Prepreg)之參數:
1.4.1 膠化時間: (gel time) 1.4.2 膠含量: (resyn content) 1.4.3 膠流量: (resin flow) 1.4.5 揮發份: (Volarill content)
PP
常用PP型號
型號
含膠量
流膠量
7630
50.1
30.3
P 28
a.外觀:清潔,黃色液體 b.PH值:小於0.35 c.可溶性:可溶 d.詣點:高於1000C e.冰點:低於00C f.比重:1.020@200C
P 29
5.棕化信賴性測試
測試 項目
測 試方 法
評定 備 標準 注
拉力 測試
1.將銅箔用膠紙貼在基板上,因為使用膠紙藥水不能滲入到銅箔內 ; 2.棕化后,在基板上貼上3-5張1080的PP進行壓合; 3.在樣板上用膠紙或干膜裁成寬度為1CM條狀來阻止蝕刻(一般在 拉力時,我們可以簡單的用刀裁即可); 4.我們可以用以上樣品做結合力測試;
沸水 將待測試樣板放入溫度為1000C的沸水中1個小時,再來檢測有無 測試 爆板或分層
6.棕化品質分析及控制
不良狀況
產生原因
P 30
解決辦法
1.板大面積棕 化不上
2.板面發紅
1.純水不符合要求 2.預浸應該更換或被污染 3.棕化槽中銅濃度超標
1.棕化槽中銅濃度超標 2.KA-1、KA-2濃度偏低 3.棕化槽液失效或受污染
P 31
1.補充棕化槽中.KA-1
4.板面上有條紋, 1.棕化槽中.KA-1、KA-2濃度偏 、 KA-2
棕化膜薄的現象 低
2.更換預浸槽
5.板的上部邊緣 1.棕化槽槽液藥水比例失調 產生波紋狀露銅
及時分析、及時補充
6.板面棕化不均
1.棕化槽液混合不均勻 2.棕化槽液流動過大 3.內層處理去墨不盡