旋转泵论文中英文对照资料外文翻译文献
循环球式转向器外文文献

Steering system profileAlong with automobile electronic technology swift and violent development, the people also day by day enhance to the motor turning handling quality request. The motor turning system changed, the hydraulic pressure boost from the traditional machinery changes (Hydraulic Power Steering, is called HPS), the electrically controlled hydraulic pressure boost changes (Elect ric Hydraulic Power Steering, is called EHPS), develops the electrically operated boost steering system (Elect ric Power Steering, is called EPS), finally also will transit to the line controls the steering system (Steer By Wire, will be called SBW).The machinery steering system is refers by pilot's physical strength achievement changes the energy, in which all power transmission all is mechanical, the automobile changes the movement is operates the steering wheel by the pilot, transmits through the diverter and a series of members changes the wheel to realize. The mechanical steering system by changes the control mechanism, the diverter and major part changes the gearing 3 to be composed.Usually may divide into according to the mechanical diverter form: The gear rack type, follows round the world -like, the worm bearing adjuster hoop type, the worm bearing adjuster refers sells the type. Is the gear rack type and follows using the broadest two kinds round the world -like (uses in needing time big steering force).In follows round the world -like in the diverter, the input changes the circle and the output steering arm pivot angle is proportional; In the gear rack type diverter, the input changes the turn and the output rack displacement is proportional. Follows round the world -like the diverter because is the rolling friction form, thus the transmission efficiency is very high, the ease of operation also the service life are long, moreover bearing capacity, therefore widely applies on the truck. The gear rack type diverter with follows round the world -like compares, the most major characteristic is the rigidity is big, the structure compact weight is light, also the cost is low. Because this way passes on easily by the wheel the reacting force to the steering wheel, therefore has to the pavement behavior response keen merit, but simultaneously also easy to have phenomena and so on goon and oscillation, also its load bearing efficiency relative weak, therefore mainly applies on the compact car and the pickup truck, at present the majority of low end passenger vehicle uses is the gear rack type machinery steering system.Along with the vehicles carrying capacity increase as well as the people to the vehicles handling quality request enhancement, the simple mechanical type steering system were already unable to meet the needs, the power steering system arise at the historic moment, it could rotate the steering wheel while the pilot to provide the boost, the power steering system divides into the hydraulic pressure steering system and the electrically operated steering system 2kinds.Hydraulic pressure steering system is at present uses the most widespread steering system.The hydraulic pressure steering system increased the hydraulic system in the mechanical system foundation, including hydraulic pump, V shape band pulley, drill tubing, feed installment, boost installment and control valve. It with the aid of in the motor car engine power actuation hydraulic pump, the air compressor and the generator and so on, by the fluid strength, the physical strength or the electric power increases the pilot to operate the strength which the front wheel changes, enables the pilot to be possible nimbly to operate motor turning facilely, reduced the labor intensity, enhanced the travel security.The hydraulic pressure boost steering system from invented already had about half century history to the present, might say was one kind of more perfect system, because its work reliable, the technology mature still widely is applied until now. It takes the power supply by the hydraulic pump, after oil pipe-line control valves to power hydraulic cylinder feed, through the connecting rod impetus rotation gear movement, may changes the boost through the change cylinder bore and the flowing tubing head pressure size the size, from this achieved changes the boost the function. The traditional hydraulic pressure type power steering system may divide into generally according to the liquid flow form: Ordinary flow type and atmospheric pressure type 2 kind of types, also may divide into according to the control valve form transfers the valve type and the slide-valve type.Along with hydraulic pressure power steering system on automobile daily popularization, the people to operates when the portability and the road feeling request also day by day enhance, however the hydraulic pressure power steering system has many shortcomings actually: ①Because its itself structure had decided it is unable to guarantee vehicles rotates the steering wheel when any operating mode, all has the ideal operation stability, namely is unable simultaneously to guarantee time the low speed changes the portability and the high speed time operation stability;②The automobile changes the characteristic to drive the pilot technical theinfluence to be serious; ③The steering ratio is fixed, causes the motor turning response characteristic along with changes and so on vehicle speed, transverse acceleration to change, the pilot must aim at the motor turning characteristic peak-to-peak value and the phase change ahead of time carries on certain operation compensation, thus controls the automobile according to its wish travel. Like this increased pilot's operation burden, also causes in the motor turning travel not to have the security hidden danger; But hereafter appeared the electrically controlled hydraulic booster system, it increases the velocity generator in the traditional hydraulic pressure power steering system foundation, enables the automobile along with the vehicle speed change automatic control force size, has to a certain extent relaxed the traditional hydraulic pressure steering system existence question.At present our country produces on the commercial vehicle and the passenger vehicle uses mostly is the electrically controlled hydraulic pressure boost steering system, it is quite mature and the application widespread steering system. Although the electrically controlled hydraulic servo alleviated the traditional hydraulic pressure from certain degree to change between the portability and the road feeling contradiction, however it did not have fundamentally to solve the HPS system existence insufficiency, along with automobile microelectronic technology development, automobile fuel oil energy conservation request as well as global initiative environmental protection, it in aspect and so on arrangement, installment, leak-proof quality, control sensitivity, energy consumption, attrition and noise insufficiencies already more and more obvious, the steering system turned towards the electrically operated boost steering system development.The electrically operated boost steering system is the present motor turning system development direction, its principle of work is: EPS system ECU after comes from the steering wheel torque sensor and the vehicle speed sensor signal carries on analysis processing, controls the electrical machinery to have the suitable boost torque, assists the pilot to complete changes the operation. In the last few years, along with the electronic technology development, reduces EPS the cost to become large scale possibly, Japan sends the car company, Mitsubishi Car company, this field car company, US's Delphi automobile system company, TRW Corporation and Germany's ZF Corporation greatly all one after another develops EPS.Mercedes2Benz 和Siemens Automotive Two big companies invested 65,000,000 pounds to use in developing EPS, the goal are together load a car to 2002, yearly produce 300 ten thousand sets, became the globalEPS manufacturer. So far, the EPS system in the slight passenger vehicle, on the theater box type vehicle obtains the widespread application, and every year by 300 ten thousand speed development.Steering is the term applied to the collection of components, linkages, etc. which allow for a vessel (ship, boat) or vehicle (car) to follow the desired course. An exception is the case of rail transport by which rail tracks combined together with railroad switches provide the steering function.The most conventional steering arrangement is to turn the front wheels using a hand–operated steering wheel which is positioned in front of the driver, via the steering column, which may contain universal joints to allow it to deviate somewhat from a straight line. Other arrangements are sometimes found on different types of vehicles, for example, a tiller or rear–wheel steering. Tracked vehicles such as tanks usually employ differential steering — that is, the tracks are made to move at different speeds or even in opposite directions to bring about a change of course.Many modern cars use rack and pinion steering mechanisms, where the steering wheel turns the pinion gear; the pinion moves the rack, which is a sort of linear gear which meshes with the pinion, from side to side. This motion applies steering torque to the kingpins of the steered wheels via tie rods and a short lever arm called the steering arm.Older designs often use the recirculating ball mechanism, which is still found on trucks and utility vehicles. This is a variation on the older worm and sector design; the steering column turns a large screw (the "worm gear") which meshes with a sector of a gear, causing it to rotate about its axis as the worm gear is turned; an arm attached to the axis of the sector moves the pitman arm, which is connected to the steering linkage and thus steers the wheels. The recirculating ball version of this apparatus reduces the considerable friction by placing large ball bearings between the teeth of the worm and those of the screw; at either end of the apparatus the balls exit from between the two pieces into a channel internal to the box which connects them with the other end of the apparatus, thus they are "recirculated".The rack and pinion design has the advantages of a large degree of feedback and direct steering "feel"; it also does not normally have any backlash, or slack. A disadvantage is that it is not adjustable, so that when it does wear and develop lash, the only cure is replacement.The recirculating ball mechanism has the advantage of a much greater mechanical advantage, so that it was found on larger, heavier vehicles while the rack and pinion was originally limited to smaller and lighter ones; due to the almost universal adoption of power steering, however, this is no longer an important advantage, leading to the increasing use of rack and pinion on newer cars. The recirculating ball design also has a perceptible lash, or "dead spot" on center, where a minute turn of the steering wheel in either direction does not move the steering apparatus; this is easily adjustable via a screw on the end of the steering box to account for wear, but it cannot be entirely eliminated or the mechanism begins to wear very rapidly. This design is still in use in trucks and other large vehicles, where rapidity of steering and direct feel are less important than robustness, maintainability, and mechanical advantage. The much smaller degree of feedback with this design can also sometimes be an advantage; drivers of vehicles with rack and pinion steering can have their thumbs broken when a front wheel hits a bump, causing the steering wheel to kick to one side suddenly (leading to driving instructors telling students to keep their thumbs on the front of the steering wheel, rather than wrapping around the inside of the rim). This effect is even stronger with a heavy vehicle like a truck; recirculating ball steering prevents this degree of feedback, just as it prevents desirable feedback under normal circumstances.The steering linkage connecting the steering box and the wheels usually conforms to a variation of Ackermann steering geometry, to account for the fact that in a turn, the inner wheel is actually traveling a path of smaller radius than the outer wheel, so that the degree of toe suitable for driving in a straight path is not suitable for turns.As vehicles have become heavier and switched to front wheel drive, the effort to turn the steering wheel manually has increased - often to the point where major physical exertion is required. To alleviate this, auto makers have developed power steering systems. There are two types of power steering systems—hydraulic and electric/electronic. There is also a hydraulic-electric hybrid system possible.A hydraulic power steering (HPS) uses hydraulic pressure supplied by an engine-driven pump to assist the motion of turning the steering wheel. Electric power steering (EPS) is more efficient than the hydraulic power steering, since the electric power steering motor only needs to provide assist when the steering wheel is turned, whereas the hydraulic pump must run constantly. In EPS the assist level is easily tunable to the vehicle type, road speed, and even driver preference.An added benefit is the elimination of environmental hazard posed by leakage and disposal of hydraulic power steering fluid.An outgrowth of power steering is speed adjustable steering, where the steering is heavily assisted at low speed and lightly assisted at high speed. The auto makers perceive that motorists might need to make large steering inputs while manoeuvering for parking, but not while traveling at high speed. The first vehicle with this feature was the Citroën SM with its Diravi layout, although rather than altering the amount of assistance as in modern power steering systems, it altered the pressure on a centring cam which made the steering wheel try to "spring" back to the straight-ahead position. Modern speed-adjustable power steering systems reduce the pressure fed to the ram as the speed increases, giving a more direct feel. This feature is gradually becoming commonplace across all new vehicles.Four-wheel steering (or all wheel steering) is a system employed by some vehicles to increase vehicle stability while maneuvering at high speed, or to decrease turning radius at low speed.In most four-wheel steering systems, the rear wheels are steered by a computer and actuators. The rear wheels generally cannot turn as far as the Alternatively, several systems, including Delphi's Quadrasteer and the system in Honda's Prelude line, allow for the rear wheels to be steered in the opposite direction as the front wheels during low speeds. This allows the vehicle to turn in a significantly smaller radius — sometimes critical for large trucks or vehicles with trailers.译文随着汽车电子技术的迅猛发展,人们对汽车转向操纵性能的要求也日益提高。
英文介绍水泵的作文
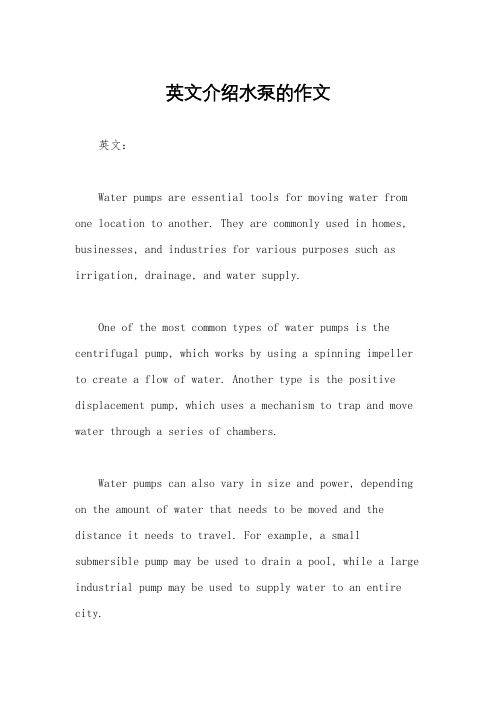
英文介绍水泵的作文英文:Water pumps are essential tools for moving water from one location to another. They are commonly used in homes, businesses, and industries for various purposes such as irrigation, drainage, and water supply.One of the most common types of water pumps is the centrifugal pump, which works by using a spinning impeller to create a flow of water. Another type is the positive displacement pump, which uses a mechanism to trap and move water through a series of chambers.Water pumps can also vary in size and power, depending on the amount of water that needs to be moved and the distance it needs to travel. For example, a small submersible pump may be used to drain a pool, while a large industrial pump may be used to supply water to an entire city.In addition, water pumps can be powered by various sources such as electricity, gasoline, or diesel. Some pumps even use solar power or wind power for a more sustainable and eco-friendly option.Overall, water pumps play a crucial role in our daily lives and are essential for ensuring the proper distribution and management of water resources.中文:水泵是将水从一个地方移动到另一个地方的必备工具。
水泵中英文对照

2一般术语2.1水力机械hydraulic machinery2.2 水轮机hydraulic turbine2.3 蓄能泵storage pump2.4 水泵水轮机reversible turbine,pump-turbine2.5 旋转方向direction of rotation2.6 机组unit2.13立式、卧式和倾斜式机组vertical,horizontal and inclined unit2.14可调式水力机械regulated hydraulic machinery2.15不可调式水力机械non-regulated hydraulic machinery2.16主阀main valve3.1水轮机3.1.1反击式水轮机reaction turbine3.1.2 混流式水轮机Francis turbine,mixed-flow turbine3.1.3 轴流式水轮机axial turbine3.1.4 轴流转桨式水轮机Kaplan turbine,axial-flow adjustable blad propeller turbine 3.1.5 轴流调桨式水轮机Thoma turbine3.1.6 轴流定桨式水轮机Propeller turbine3.1.7贯流式水轮机tubular turbine,through flow turbine3.1.8灯泡式水轮机bulb turbine3.1.9竖井贯流式水轮机pit turbine3.1.10全贯流式水轮机straight flow turbine,rim-generator unit3.1.11轴伸贯流式水轮机(S形水轮机)tubular turbine(S-type turbine)3.1.12 斜流式水轮机diagonal turbine3.1.13 斜流转桨式水轮机Deriaz turbine3.1.14斜流定桨式水轮机fixed blade of Deriaz turbine3.1.15冲击式水轮机impuls turbine,action turbine3.1.16水斗式水轮机Pelton turbine,scoop turbine3.1.17斜击式水轮机inclined jet turbine3.1.18双击式水轮机cross-flow turbine3.2蓄能泵3.2.1混流式(离心式)蓄能泵centrifugal storage pump,mixed-flow storage pump 3.2.2轴流式蓄能泵propeller storage pump,axial storage pump3.2.3斜流式蓄能泵diagonal storage pump3.2.4多级式蓄能泵multi-stage storage pump3.3水泵水轮机(又称可逆式水轮机)3.3.1单级水泵水轮机singal stage pump-turbine3.3.2多级水泵水轮机multi-stage pump-turbine3.4主阀与阀门3.4.1蝴蝶阀butterfly valve3.4.2 平板蝶阀biplane butterfly valve,through flow butterfly valve3.4.3 圆筒阀cylindrical valve,ring gate3.4.4 球阀rotary valve,spherical valve3.4.5 盘形阀mushroom valve,hollow-cone valve,howell-Bunger valve3.4.6 针形阀needle valve3.4.7 旁通阀by-pass valve3.4.8直空破坏阀vacuum break valve4结构部件4.1混流式水轮机4.1.1埋入部件embedded component4.1.2 引水室(turbine)flume4.1.3蜗壳spiral case4.1.4座环stay ring4.1.5 固定导叶stay vane4.1.6 蜗壳鼻端spiral case nose4.1.7基础环foundation ring,discharge ring4.1.8 尾水管draft tube4.1.9锥形尾水管conical draft tube4.1.10肘形尾水管elbow draft tube4.1.11尾水管锥管draft tube cone4.1.12尾水管肘管draft tube elbow4.1.13 尾水管扩散段draft tube outlet part4.1.14 尾水管支墩draft tube pier4.1.15 尾水管里衬draft tube liner4.1.16 机坑里衬pit liner4.1.17导水机构distributor4.1.18顶盖headcover,top cover4.1.19底环bottom ring,bottom cover4.1.20导叶guide vane,wicket gate4.1.21 控制环regulating ring,operating ring4.1.22 导叶臂guide vane lever,wicket gate lever4.1.23 分半键split key4.1.24 导叶连杆guide vanelink,wicket gate link4.1.25 导叶过载保护装置guide vane overload protection device 4.1.26 剪断销shear pin4.1.27 摩擦装置friction device4.1.28 导叶轴承guide vane bearing4.1.29 导叶止推轴承guide vane thrust bearing4.1.30 导叶轴密封guide vane stem seal4.1.31 导叶端面密封guide vane end seal4.1.32 导叶立面密封guide vane seal4.1.33抗磨板facing plates,wear plates4.1.34导叶限位块guide vane stop block4.1.35导叶接力器guide vane servomotor4.1.36 单导叶接力器individual guide vane servomotor4.1.37 推拉杆push and pull rod,connecting rod4.1.38 调速轴regulating shaft4.1.39 均压管balance pipe4.1.40 转动部件rotating component4.1.41 转轮runner4.1.42 叶片blade4.1.43 上冠crown4.1.44 下环band4.1.45 泄水锥runner cone4.1.46 转轮密封装置runner seal4.1.47 转轮止漏环runner wearing ring4.1.48 固定止漏环stationary wearing ring4.1.49 转轮减压板decompression plate4.1.50 主轴main shaft4.1.51 导轴承guide bearing4.1.52 轴领guide bearing collar4.1.53 轴瓦guide bearing shoe4.1.54 轴承体guide bearing housing4.1.55 主轴密封装置main shaft seal4.1.56 检修密封stand still seal4.1.57 联轴螺栓coupling bolt4.2 轴流式水轮机和斜流式水轮机。
中英文文献翻译-旋转泵
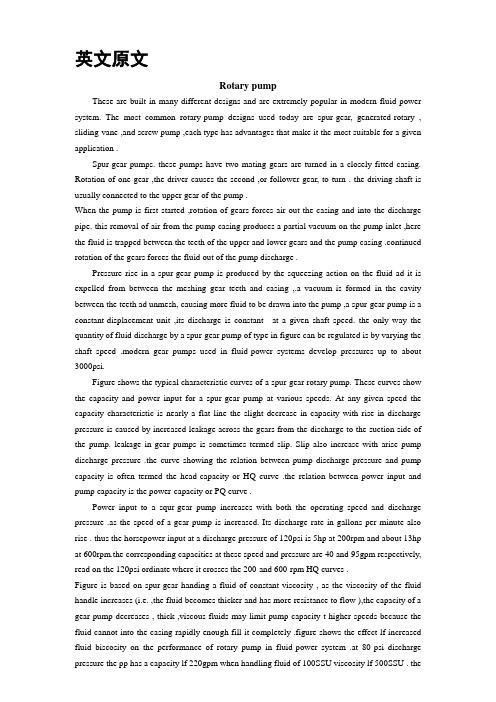
英文原文Rotary pumpThese are built in many different designs and are extremely popular in modern fluid-power system. The most common rotary-pump designs used today are spur-gear, generated-rotary , sliding-vane ,and screw pump ,each type has advantages that make it the most suitable for a given application .Spur-gear pumps. these pumps have two mating gears are turned in a closely fitted casing. Rotation of one gear ,the driver causes the second ,or follower gear, to turn . the driving shaft is usually connected to the upper gear of the pump .When the pump is first started ,rotation of gears forces air out the casing and into the discharge pipe. this removal of air from the pump casing produces a partial vacuum on the pump inlet ,here the fluid is trapped between the teeth of the upper and lower gears and the pump casing .continued rotation of the gears forces the fluid out of the pump discharge .Pressure rise in a spur-gear pump is produced by the squeezing action on the fluid ad it is expelled from between the meshing gear teeth and casing ,.a vacuum is formed in the cavity between the teeth ad unmesh, causing more fluid to be drawn into the pump ,a spur-gear pump is a constant-displacement unit ,its discharge is constant at a given shaft speed. the only way the quantity of fluid discharge by a spur-gear pump of type in figure can be regulated is by varying the shaft speed .modern gear pumps used in fluid-power systems develop pressures up to about 3000psi.Figure shows the typical characteristic curves of a spur-gear rotary pump. These curves show the capacity and power input for a spur-gear pump at various speeds. At any given speed the capacity characteristic is nearly a flat line the slight decrease in capacity with rise in discharge pressure is caused by increased leakage across the gears from the discharge to the suction side of the pump. leakage in gear pumps is sometimes termed slip. Slip also increase with arise pump discharge pressure .the curve showing the relation between pump discharge pressure and pump capacity is often termed the head-capacity or HQ curve .the relation between power input and pump capacity is the power-capacity or PQ curve .Power input to a squr-gear pump increases with both the operating speed and discharge pressure .as the speed of a gear pump is increased. Its discharge rate in gallons per minute also rise . thus the horsepower input at a discharge pressure of 120psi is 5hp at 200rpm and about 13hp at 600rpm.the corresponding capacities at these speed and pressure are 40 and 95gpm respectively, read on the 120psi ordinate where it crosses the 200-and 600-rpm HQ curves .Figure is based on spur-gear handing a fluid of constant viscosity , as the viscosity of the fluid handle increases (i.e. ,the fluid becomes thicker and has more resistance to flow ),the capacity of a gear pump decreases , thick ,viscous fluids may limit pump capacity t higher speeds because the fluid cannot into the casing rapidly enough fill it completely .figure shows the effect lf increasedfluid biscosity on the performance of rotary pump in fluid-power system .at 80-psi discharge pressure the pp has a capacity lf 220gpm when handling fluid of 100SSU viscosity lf 500SSU . the power input to the pump also rises ,as shown by the power characteristics.Capacity lf rotary pump is often expressed in gallons per revolution of the gear or other internal element .if the outlet of a positive-displacement rotary pump is completely closed, the discharge pressure will increase to the point where the pump driving motor stalls or some part of the pump casing or discharge pipe ruptures .because this danger of rupture exists systems are filled with a pressure –relief valve. This relief valve may be built as of the pump or it may be mounted in the discharge piping.Sliding-Vane PumpsThese pumps have a number of vanes which are free to slide into or out of slots in the pup rotor . when the rotor is turned by the pump driver , centrifugal force , springs , or pressurized fluid causes the vanes to move outward in their slots and bear against the inner bore of the pump casing or against a cam ring . as the rotor revolves , fluid flows in between the vanes when they pass the suction port. This fluid is carried around the pump casing until the discharge port is reached. Here the fluid is forced out of the casing and into the discharge pipe.In the sliding-vane pump in Figure the vanes in an oval-shaped bore. Centrifugal force starts the vanes out of their slots when the rotor begins turning. The vanes are held out by pressure which is bled into the cavities behind the vanes from a distributing ring at the end of the vane slots. Suction is through two ports A and AI, placed diametrically opposite each other. Two discharge ports are similarly placed. This arrangement of ports keeps the rotor in hydraulic balance, reliving the bearing of heavy loads. When the rotor turns counterclockwise, fluid from the suction pipe comes into ports A and AI is trapped between the vanes, and is carried around and discharged through ports B and BI. Pumps of this design are built for pressures up to 2500 psi. earlier models required staging to attain pressures approximating those currently available in one stage. Valving , uses to equalize flow and pressure loads as rotor sets are operated in series to attain high pressures. Speed of rotation is usually limited to less than 2500rpm because of centrifugal forces and subsequent wear at the contact point of vanes against the cam-ring surface..Two vanes may be used in each slot to control the force against the interior of the casing or the cam ring. Dual vanes also provide a tighter seal , reducing the leakage from the discharge side to the suction side of the pump . the opposed inlet and discharge port in this design provide hydraulic balance in the same way as the pump, both these pumps are constant-displacement units. The delivery or capacity of a vane-type pump in gallons per minute cannot be changed without changing the speed of rotation unless a special design is used. Figure shows a variable-capacity sliding-vane pump. It dose not use dual suction and discharge ports. The rotor rums in the pressure-chamber ring, which can be adjusted so that it is off-center to the rotor. As the degree of off-center or eccentricity is changed, a variable volume of fluid is discharged. Figure shows that the vanes create a vacuum so that oil enters through 180 of shaft rotation. Discharge also takesplace through 180 of rotation. There is a slight overlapping of the beginning of the fluid intake function and the beginning of the fluid discharge.Figure shows how maximum flow is available at minimum working pressure. As the pressure rises, flow diminishes in a predetermined pattern. As the flow decreases to a minimum valve, the pressure increases to the maximum. The pump delivers only that fluid needed to replace clearance floes resulting from the usual slide fit in circuit components.A relief valve is not essential with a variable-displacement-type pump of this design to protect pumping mechanism. Other conditions within the circuit may dictate the use of a safety or relief valve to prevent localized pressure buildup beyond the usual working levels.For automatic control of the discharge , an adjustable spring-loaded governor is used . this governor is arranged so that the pump discharge acts on a piston or inner surface of the ring whose movement is opposed by the spring . if the pump discharge pressure rises above that for which the by governor spring is set , the spring is compressed. This allows the pressure-chamber ring to move and take a position that is less off center with respect to the rotor. The pump theb delivers less fluid, and the pressure is established at the desired level. The discharge pressure for units of this design varies between 100 and 2500psi.The characteristics of a variable-displacement-pump compensator are shown in figure. Horsepower input values also shown so that the power input requirements can be accurately computed. Variable-volume vane pumps are capacity of multiple-pressure levels in a predetermined pattern. Two-pressure pump controls can provide an efficient method of unloading a circuit and still hold sufficient pressure available for pilot circuits.The black area of the graph of figure shows a variable-volume pump maintaining a pressure of 100psi against a closed circuit. Wasted power is the result of pumping oil at 100psi through an unloading or relief valve to maintain a source of positive pilot pressure. Two-pressure –type controls include hydraulic, pilot-operated types and solenoid-controlled, pilot-operated types. The pilot oil obtained from the pump discharge cannot assist the governor spring. Minimum pressure will result. The plus figure shows the solenoid energized so that pilot oil assists compensator spring. The amount of assistance is determined by the small ball and spring, acting as a simple relief valve. This provides the predetermined maximum operating pressure.Another type of two-pressure system employs what is termed a differential unloading governor. It is applied in a high-low or two-pump circuit. The governor automatically, Through pressure sensing, unloads the large volume pump to a minimum deadhead pressure setting. Deadhead pressure refers to a specific pressure level established as resulting action of the variable-displacement-pump control mechanism. The pumping action and the resulting flow at deadhead condition are equal to the leakage in the system and pilot-control flow requirements. No major power movement occurs at this time, even though the hydraulic system may be providing a clamping or holding action while the pump is in deadhead positionThe governor is basically a hydraulically operated, two-pressure control with a differential piston that allows complete unloading when sufficient external pilot pressure is applied to pilotunload port.The minimum deadhead pressure setting is controlled by the main governor spring A. the maximum pressure is controlled by the relief-valve adjustment B. the operating pressure for the governor is generated by the large-volume pump and enters through orifice C.To use this device let us assume that the circuit require a maximum pressure of 1000psi, which will be supplied by a 5-gpm pump. It also needs a large flow (40gpm) at pressure up to 500psi; it continues to 1000pso at the reduced flow rate. A two-pump system with an unloading governor on the 40-gpm pump at 500psi to a minimum pressure setting of 200psi (or another desired value) , which the 5-gpm pump takes the circuit up to1000psi or more.Note in figure that two sources of pilot pressure are required. One ,the 40-gpm pump, provides pressure within the housing so that maximum pressure setting can be obtained. The setting of the spring, plus the pressure within the governor housing, determines the maximum pressure capacity of the 40-gpm pump. The second pilot source is the circuit proper, which will go to 1000psi. this pilot line enters the governor through orifice D and acts on the unloading piston E . the area of piston E is 15 percent greater than the effective area of the relief poppet F. the governor will unload at 500psi and be activated at 15percent below 500psi, or 425psi. By unloading, we mean zero flow output of the 40-gpm pump.As pressure in the circuit increases from zero to 500psi, the pressure within the governor housing also increases until the relief-valve setting is reached, at which time the relief valve cracks open, allowing flow to the tank.The pressure drop in the hosing is a maximum additive value, allowing the pump to deadhead. Meanwhile, the system pressure continues to rise above 700psi, resulting in a greater force on the bottom of piston E than on the top. The piston then completely unseats poppet F, which results in a further pressure drop within the governor horsing to zero pressure because of the full-open position of the relief poppet F. flow entering the housing through orifice is directed to the tank pass the relief poppet without increasing the pressure in housing. The deadhead pressure of the 40-gpm pump then decreases to the lower set value. Thus , at the flow rate to the unloading governor ,the 40gpm pump goes to deadhead. The flow rate to the circuit decreases to 5gpm as the pressure to 1000psi, the 5-gpm pump is also at its deadhead setting, thus only holding system pressure.The 4-gpm pump unloads its volume at 500psi. It requires a system pressure of 600psi to unload the 40-gpm pump to its minimum pressure of 200psi. the 600-psi pilot supply enters through orifice D and acts on the differential piston E. The pumps volume is reduced to zero circuit-flow output at 500psi. The additional 100-psi pilot pressure is required to open poppet F completely and allow the pressure within the housing to decrease to zero.As circuit pressure decreases ,both pumps come back into service in a similar pattern.CNC machine toolsWhile the specific intention and application for CNC machines vary from one machine type to another, all forms of CNC have common benefits. Here are but a few of the more important benefits offered by CNC equipment.The first benefit offered by all forms of CNC machine tools is improved automation.The operator intervention related to producing work pieces can be reduced or eliminated. Many CNC machines can run unattended during their entire machining cycle, freeing the operator to do other tasks. This gives the CNC user several side benefits including reduced operator fatigue, fewer mistakes caused by human error, and consistent and predictable machining time for each workpiece. Since the machine will be running under program control, the skill level required of the CNC operator (related to basic machining practice) is also reduced as compared to a machinist producing workpieces with conventional machine tools.The second major benefit of CNC technology is consistent and accurate workpieces. Today's CNC machines boast almost unbelievable accuracy and repeatability specifications. This means that once a program is verified, two, ten, or one thousand identical workpieces can be easily produced with precision and consistency.A third benefit offered by most forms of CNC machine tools is flexibility. Since these machines are run from programs, running a different workpiece is almost as easy as loading a different program. Once a program has been verified and executed for one production run, it can be easily recalled the next time the workpiece is to be run. This leads to yet another benefit, fast change over. Since these machines are very easy to set up and run, and since programs can be easily loaded, they allow very short setup time. This is imperative with today's just-in-time (JIT) product requirements.Motion control - the heart of CNCThe most basic function of any CNC machine is automatic, precise, and consistent motion control. Rather than applying completely mechanical devices to cause motion as is required on most conventional machine tools, CNC machines allow motion control in a revolutionary manner2 . All forms of CNC equipment have two or more directions of motion, called axes. These axes can be precisely and automatically positioned along their lengths of travel. The two most common axis types are linear (driven along a straight path) and rotary (driven along a circular path).Instead of causing motion by turning cranks and handwheels as is required on conventional machine tools, CNC machines allow motions to be commanded through programmed commands. Generally speaking, the motion type (rapid, linear, and circular), the axes to move, the amount of motion and the motion rate (feedrate) are programmable with almost all CNC machine tools.A CNC command executed within the control tells the drive motor to rotate a precise number of times. The rotation of the drive motor in turn rotates the ball screw. And the ball screw drives the linear axis (slide). A feedback device (linear scale) on the slide allows the control to confirm that the commanded number of rotations has taken place3.Though a rather crude analogy, the same basic linear motion can be found on a common table vise. As you rotate the vise crank, you rotate a lead screw that, in turn, drives the movable jaw onthe vise. By comparison, a linear axis on a CNC machine tool is extremely precise. The number of revolutions of the axis drive motor precisely controls the amount of linear motion along the axis.How axis motion is commanded - understanding coordinate systems .It would be infeasible for the CNC user to cause axis motion by trying to tell each axis drive motor how many times to rotate in order to command a given linear motion amount4. (This would be like having to figure out how many turns of the handle on a table vise will cause the movable jaw to move exactly one inch!) Instead, all CNC controls allow axis motion to be commanded in a much simpler and more logical way by utilizing some form of coordinate system. The two most popular coordinate systems used with CNC machines are the rectangular coordinate system and the polar coordinate system. By far, the more popular of these two is the rectangular coordinate system.The program zero point establishes the point of reference for motion commands in a CNC program. This allows the programmer to specify movements from a common location.If program zero is chosen wisely, usually coordinates needed for the program can be taken directly from the print.With this technique, if the programmer wishes the tool to be sent to a position one inch to the right of the program zero point, X1.0 is commanded. If the programmer wishes the tool to move to a position one inch above the program zero point, Y1.0 is commanded. The control will automatically determine how many times to rotate each axis drive motor and ball screw to make the axis reach the commanded destination point . This lets the programmer command axis motion in a very logical manner.All discussions to this point assume that the absolute mode of programming is used. The most common CNC word used to designate the absolute mode is G90. In the absolute mode, the end points for all motions will be specified from the program zero point. For beginners, this is usually the best and easiest method of specifying end points for motion commands. However, there is another way of specifying end points for axis motion.中文译文旋转泵旋转泵应用于不同的设计中,在流体动力系统中极其常用。
外文翻译--泵的概述

外文原文:Pump's outlineThe pump is the application very widespread general machinery, may say that is place of the fluid flow, nearly has the pump in the work. Moreover, along with science's and technology's development, pump's application domain is expanding rapidly, according to the over-all state statistics, pump's power consumption approximately composes the national total output of electrical energy 1/5, obviously the pump is natural consumes energy the wealthy and powerful family. Therefore, raises the pump technical level to save the energy consumption to have the important meaning.First. Centrifugal pump's principle of workThe drive leads impeller revolving through the pump spindle to have the centrifugal force, under the centrifugal action of force, the liquid is flung along the leaf blade flow channel to the impeller export, the liquid sends in after the volute collection the eduction tube. The liquid obtains the energy from the impeller, • causes the pressure energy and the speed can increase, and depends upon this energy the hydraulic transport to the operating location. while the liquid is flung which exports to the impeller, the impeller eye center has formed the low pressure, • has had the differential pressure in the imbibition pot and between the impeller center liquid, in the imbibition pot's liquid under this differential pressure function, after inhales the pipeline and pump's suction chamber unceasingly enters in the impeller.Second, centrifugal pump's structure and main spare partA centrifugal pump mainly by the pump body, the impeller, the packing ring, the rotation axis, the axis seals parts and so on box to be composed, some centrifugal pumps are also loaded with the guide pulley, the inducer, the balance disc and so on.1. Pump body: Namely pump's shell, including suction chamber and delivery chamber.①Suction chamber: Its function is enables the liquid to flow in evenly the impeller.②Delivery chamber: Its function collects the liquid, and sends in it the subordinate impeller or guides the eduction tube, at the same time reduces the liquid the speed, causes the kinetic energy to further turn the pressure energy. The delivery chamber has the volute and the guide vane two forms.2. Impeller: It is in the centrifugal pump transmits the energy for the liquid only part, the impeller with the bond fixation on the axis, leads revolving alongwith the axis by the prime mover, passes to through the leaf blade prime mover's energy the liquid.Impeller classification:①According to liquid inflow classification: Single suction impeller (in impeller's one side has an entrance) and double attracts the impeller (liquid from impeller's lateral symmetry liudao impeller passage).②Is opposite according to the liquid in centerline's flow direction classification: Runoff type impeller, axial-flow propeller and interflow type impeller.③According to impeller's structural style classification: Shrouded impeller, open type impeller and semi-opened impeller.3. Axis: Is transmits the mechanical energy the important components, the • prime mover's torque passes to the impeller through it. The pump spindle is the pump rotor's major parts, on the axis is loaded with components and so on impeller, axle sleeve, balance disc. The pump spindle depending on the both sides bearing supporting, makes the high speed rotation in the pump, thus the pump spindle in a big way wants the bearing capacity, to be wear-resisting, to be anti-corrosive. Pump spindle's material selects the carbon steel or the alloy steel and after the quenching and retempering treatment generally.4. Packing ring: Is installs in the rotation impeller and the static pump housing (center-section and guide vane's assembly) between packing assembly. It is function is through controls between the two gap method, increases in the pump between the high and low pressure cavity the fluid flow resistance, reduces divulging.5. Axle sleeve: The axle sleeve is uses for to protect the pump spindle, causes it not to corrode and the attrition. When necessity, the axle sleeve may replace.6. Axis seals: The pump spindle and around packing box between end cover's installs short for axis to seal, mainly prevents in pump's liquid divulging and the air enters in the pump, achieves seals and prevents the air admission to cause the pump cavitation goal. the axis seals form: Namely has skeleton's rubber seal, the packing seal and the mechanical seal.7. axial force balancing unit.Third. Centrifugal pump's prime task parameter1. Current capacity: Namely the pump in unit of time discharges the liquid quantity, usually indicated with the Unit of volume that mark Q, the unit has m3/h, m3/s, l/s and so on,2. Lifting: The transportation unit weight's liquid (pump suction flange) (pump discharge flange) from the pump inlet place to the pump exit, its energy's increment, indicated with H, the unit is m.3. Rotational speed: Pump's rotational speed is the pump each minute revolving number of times, expressed with N. Electrical machinery rotational speed •N generally about 2900 n/min.4. Net positive suction head: Centrifugal pump's net positive suction head isNPSH • uses the expressed that pump's performance's main parameter,rsymbolic representation.5. Power and efficiency: Pump's power input is shaft power P, is also electric motor's output. Pump's output is the active power.Fourth, pump proper energy lossPump mechanical energy which obtains from the prime mover, has a part to transform into the liquid energy, but another part because in the pump consumes loses. In the pump all losses may divide into the following several items: 1. Hydraulic loss by the liquid in pump impact, the turbulent flow and the surface friction creates. The impact and the eddy current loss are because the liquid flow change direction produces. The liquid flows through the flow channel general meeting which contacts to present the surface friction, from this produces the energy loss is mainly decided by flow channel's length, the size, the shape, the surface roughness, as well as liquid speed of flow and characteristic.2. Volumetric loss: volumetric loss was already obtained the energy liquid to have a part to flee the result which in the pump the class and leaked outward.is 0.93~0.98 generally. Improves the packing Pump's volumetric efficiencyvring and the seal structure, may reduce the leakage, raises the volumetric efficiency.3. Mechanical loss mechanical loss refers to the impeller lap side and the pump housing friction loss between the liquid, namely the disc loses, as well as pump spindle when packing, bearing and balancing unit and so on mechanical part movement friction loss, generally before primarily.Fifth, pump's speed change--Proportionality law1. Centrifugal pump's speed change:A centrifugal pump, when its rotational speed change, its rated flow, lifting and the shaft power will have the change according to the certainproportion relations. At present, uses the frequency conversion velocity modulation electrical machinery to realize centrifugal pump's speed change, is a new important energy conservation way. 2. proportionality law expression:2121n n Q Q = 22121⎪⎪⎭⎫ ⎝⎛=n n H H 32121⎪⎪⎭⎫ ⎝⎛=n n N N In the formula, Q, H, N-- pump's rated flow, lifting and shaft power Thesubscript 1,2 express the different rotationalspeed separatelyn-- rotational speedSixth, centrifugal pump's ratio rotationCompared to the rotation is the comprehensive parameter which derives by the law of similarity, it is the operating mode function, to a pump, the different operating mode has differently compared to the rotation, for ease of carries on the comparison to the different type pump's performance and the structure, the application optimum condition (the peak efficiency spot) the ratio rotation represents this pump.When chooses the pump, may according to job requirement Q, H and unifies electrical machinery's rotational speed, calculates the n s number, determines pump's type approximately. At that time, 30<s n used the positive displacement pump generally, at that time, 30>s n used the centrifugal pump, the interflow pump, the axial flow pump and so on. Seventh,centrifugal pump'scavitation andinspirationcharacteristic1.Cavitation phenomenonsThe pumping station transportation medium's liquid condition and the gas are can transform mutually, the transformed condition is the pressure and the temperature. Under certain temperature, the liquid starts the critical pressure which vaporizes for the vaporization pressure. The temperature is higher, the liquid vaporization pressure is higher. Pump when revolution, if its overflow part local region (for example impeller blade import later somewhere), the liquid absolute pressure drops when pulled out delivers the liquid at that time under the temperature vaporization pressure, the liquid then in this place starts to vaporize, the bubble formation (air bubble internal pressure approximately wasequal to vaporization pressure). When these air bubbles along with liquid flow forward motion to high pressure region, down to around the air bubble high-pressured liquid causes the air bubble to reduce suddenly congeals. While air bubble vanishing, the liquid particle by the high speed packing hole, occurs hits mutually forms the intense pressure surge, causes the overflow part to receive the corrosion and the destruction. The above process is called the cavitation.2. Cavitation will cause serious results:(1). has the vibration and the noise.(2). is influential to pump's operating performance: When the cavitation develops the certain extent, the • steam bubble produces massively, will stop up the flow channel, will cause pump's current capacity, lifting, the efficiency and so on obviously to drop.(3). will have the destruction to flow channel's material quality: Is mainly nearby the leaf blade entrance the metal weary disintegration.3. centrifugal pump's inspiration characteristic:(1). Pump has the cavitation basic condition is: Under leaf blade entrance lowest liquid flow pressure k P <= this temperature liquid vaporization pressure v P .(2). effective net positive suction head: The pump entry (potential head is the entire flood peak which zero) the liquid has subtracts the value which the vaporization delivery head remains only, with expression.(3). pump essential net positive suction head: Liquid flow from pump inlet to impeller in minimal pressure point of force K place complete energy loss, with expression.(4). With r NPSH and a NPSH difference and relation:a NPSH >r NPSH Pump not cavitationa NPSH =r NPSH The pump starts the cavitationa NPSH <r NPSH Pump serious cavitation(5). regarding a pump, to guarantee that its safe operation does not have the cavitation, must the net positive suction head also be supposed to add asecurity allowance regarding the pump, therefore, pump's permission net positive suction head is:[]NPSH=()c1.1~NPSH5.14. Enhances the centrifugal pump anti-cavitation performance themethod to include:NPSH, is machine the pump (1). I mprovement machine pump structure, reducesrdesign question.(2). Enhancement installment effective net positive suction head. Most mainly the most commonly used method uses the irrigation inspiration installment.In addition, reduces the inspiration pipeline resistance loss as far as possible, reduces the liquid the saturated steam tension, namely when design inspiration pipeline selects caliber big as far as possible, length short, the bend and valve few, transportation liquid temperature as far as possible low and so on measures, may enhance the installment the effective cavitation remainder.5. axial force balancing unit(1). axial force production reason①Around because the impeller the both sides the fluid pressure distributed situation different (wheel cap lateral pressure is low, • wheel disk pressure high) causes axial force A1, its direction for from impeller back side direction impeller eye.②The fluid flows in and flows out dynamical reaction A2 which impeller's direction and the speed different produce, its direction and A1 are opposite, therefore line shaft directive force A=A1-A2, the direction is ordinary and A1 same (general A2 is small).(2). Axial force balanced①Uses double attracts the type impeller: The impeller lateral symmetry, the fluid from the both sides inspiration, the axial force automatic counter-balance achieves balanced.②Opens the balancing hole or installs the compensating pipe:A: Opens several balancing holes in the impeller wheel disk photograph well regarding the induction port place.B: After order to avoid the balancing hole, because the mainstream is disturbed increases the hydraulic loss, may suppose the compensating pipe to replace the balancing hole, namely uses an acorn tube leading-in point pressure to the wheeldisk back side.③Uses the balanced leaf blade: Casts several radial direction muscle piece at the back of the leaf wheel disk, the • muscle piece drives at the back of the impeller in the gap fluid to accelerate to revolve, increases the centrifugal force, •, thus causes at the back of the impeller the pressure obviously to reduce.④Using thrust bearing withstanding axial force. Generally in the small single suction pump the thrust bearing may withstand the complete axial force, prevents the pump spindle to flee moves.Eighth. centrifugal pump's operating procedure1. Centrifugal pump starts the inspection(1) Electrical machinery overhaul, before connecting the shaft coupling, inspects electrical machinery's rotation direction first to be whether correct.(2) inspection pumps out the inlet line and the attached pipeline, the flange, the valve installs whether to meet the requirement, foot bolt and grounding to be whether good, whether the shaft coupling does install.(3) jigger inspection, rotates whether normally.(4) inspection lubricating oil oil level is whether normal, refuels without the oil, and inspects the lubricating oil (fat) oil material nature.(5) turns on various cooling water valve, and inspects the pipeline to be whether unimpeded. Attention cooling water not suitable oversized or too small, will create the waste oversized, too small, then the cooling performance will be bad. Generally the cooling current of water becomes the striation(6) dozen of pumping's inlet valve, closes pump's outlet valve, and turns on the pressure gauge valve.(7) inspection machine pump's seal condition and oil seal opening. attention: The hot oil pump wants evenly before the start preheating.2. centrifugal pump's start(1) all operates the inlet valve, closes the outlet valve, the starting dynamo.(2), when the pump outlet pressure is bigger than the service pressure, inspects each work on six cylinders, turns on the outlet valve gradually.when(3) starting dynamo, if the start or has time the unusual sound, should the dump inspection, after eliminating the breakdown, immediately only then starts.when(4) start, pays attention to the human not to face the shaft coupling, by against departs offends somebody.3. the centrifugal pump stops the pump to operate(1) to close pump's outlet valve slowly.(2) shuts off electrical machinery's power source.(3) closes the pressure gauge valve.(4) parking, cannot stop the cooling water immediately, should pump's temperature only then cut off the water supply falling to 80 degrees below.(5) according to the need, closes the inlet valve, the pump body blows off.4. centrifugal pump operates when matters needing attention(1) centrifugal pump when revolution avoids the idle operation.(2) avoids when closes the outlet valve the long time revolution.(3) refuses the water used battery charger.the(4) centrifugal pump must in close in outlet valve's situation to start.中文译文:泵的概述泵是应用非常广泛的通用机械,可以说是液体流动之处,几乎都有泵在工作。
旋转机械故障的研究及常见故障的振动诊断毕业课程设计外文文献翻译、中英文翻译

1.英文文献翻译1.1英文文献原文题目Chapter 2 Research and rotating machinery fault vibration fault diagnosis of common.Rotating machinery are those main function is to be completed by the rotary movement of mechanical equipment, such as steam turbines, gas turbines, generators, motors, centrifugal blowers, centrifugal compressor pumps, vacuum pumps and a variety of slow growth of the gears and other machinery equipment, all belong to the scope of rotating machinery. Rotating machinery is the application of machinery and equipment most widespread, the number of the largest and most representative one of machinery and equipment, especially in electric power, petrochemical, metallurgy, machinery, aviation, nuclear industry and other industries, rotating machinery is a significant share an important position.2.1 Classification of Rotating Machinery VibrationRotating machinery vibration failure was classified as a major form of failure, according to different classification methods, a variety may be as follows1.By vibration frequency classification(1) Vibration frequency;(2) Harmonic vibration, for example, two octave, 3 octave vibration;(3) The entire baseband frequency scores (such as 1 / 2, 1 / 3, etc.)of the vibration;(4) Frequency and baseband into the relationship between a certain percentages (eg 38% ~ 49%) of the vibration;(5) ultra-low-frequency (vibration frequency 5Hz below) vibration;(6) Ultra-high frequency (vibration frequency in 10 kHz and above) Vibration2. Amplitude direction according to classification(1) Diameter (horizontal) to the vibration that is the direction along the shaft diameter of the vibration is generally divided into horizontal vibration straight vibration.(2) Axial vibration, that is, the direction along the axis of vibration cutting;(3) Tensional vibration, that is, the vibration along the shaft rotation direction.3. by vibration of the reasons for classification(1) The vibration caused by rotor imbalance;(2) Shaft misalignment caused by vibration;(3) Sliding bearing and crankshaft vibration caused by eccentricity;(4) The machine parts caused by loose vibration;(5) Friction (such as seal friction, the rotor and the stator friction, etc.) caused by vibration;(6) Bearing damage caused by vibration;(7) Sliding bearing oil whirls and oil whip caused by vibration;(8) Air power and hydraulic vibration caused by factors such as;(9) Bearing stiffness asymmetry caused by vibration;(10) Electrical aspects of the reasons for the vibration caused by4. Vibration occurred by the site classification(1) Rotor or shaft (including the journal, shaft profile vane, etc.)vibration;(2) Bearings (including the film sliding bearings and rolling bearing) vibration;(3) Shell, bearing vibration;(4) Infrastructure (including aircraft seats, table, or bracket, etc.) vibration;(5) Other areas such as valves, pipe stem, and a variety of structural vibration, etc.In addition, if according to the characteristics and forms of vibration, but also separation of synchronous vibrations (forced vibration) and sub-synchronous (self-excited vibration), etc... Due to vibrations caused by the failure of its manifestations are diverse, in order to accurately identified the cause failures cause - generally speaking, have to rely on signal processing techniques and vibration theory, and other modern methods and means to conduct a comprehensive and integrated analysis and in accordance with the gradual accumulation of experience in the specific circumstances, the only way to achieve fault diagnosis success. Failure of rotating machinery and therefore must be characterized by research.2.2 The characteristics of rotating machinery faultThe implementation of fault in the dynamic monitoring of rotating machinery, we must pay attention to other features:2.2.1 Rotor FeaturesThe rotor component is the core of rotating machinery and equipment, which is fixed by the shaft and the installation of various types of circular discoid components (such as coupling, bearings, impeller, gear, balance disk, pulley, wheel, flywheel, etc.), formed. As the entire rotor in high-speedrotation movements, so its manufacture, installation, commissioning, maintenance and management have a very high demand. If you had problems with one of these components, or in connection with a change in part an exception occurred, they immediately drew a strong vibration unit. It can be said of dynamic monitoring rotating machinery monitoring and diagnosis is mainly the rotor state of motion.2.2.2 The frequency characteristics of rotating machinery vibrationMost of rotating machinery vibration signals is periodic signals, quasi-periodic signal, or a stationary random signal. Failure of rotating machinery vibration characteristics have a common point, namely, the failure of their characteristic frequency related with the rotor speed is equal to the rotor rotation frequency (referred to as transfer frequency, also known as frequency) and its octave or sub-frequency. Therefore, the analysis of vibration signals of the frequency and turn the relationship between the frequencies of rotating machinery fault diagnosis of a key.2.2.3 for rotating machinery vibration monitoring the main wayVibration signal analysis is the basic method for monitoring rotating machinery, the main three-pronged approach to obtain monitoring information1. Analysis of rotating machinery vibration frequency of each type of fault has its own characteristic frequency at the scene to make the frequency of the vibration signal analysis is the diagnosis of rotating machinery of the most effective method. Frequency speed of rotating machinery is like a "military demarcation line," the entire band is divided into sub-and super-asynchronous asynchronous vibration frequency of vibration of two sections, to seize this point, helps us to analyze and judge the fault2. Analysis of amplitude and direction of features in some cases(certainly not all occasions) different types of rotating machinery fault vibration on the performance characteristics of a clear direction. Therefore, the vibration of rotating machinery measurements, as long as conditions permit, the general measure of each measuring point should be horizontal, vertical and axial three directions, as in different directions to provide us with a different fault information. Leakage measured in one direction, you may losea message.3. Analysis of the relationship between the amplitude changes with the speed of a considerable portion of rotating machinery fault vibration amplitude and speed changes are closely related, so on-site measurements, when necessary, to create conditions for as much as possible, in the process of changing the speed amplitude measurement of the machine value.2.3 Rotating Machinery Vibration Fault DiagnosisAs mentioned earlier, equipment fault diagnosis is essentially a pattern classification are based on test analysis obtained on the state information, and grouped into a certain type of equipment failure. Therefore, the characteristics of each type of fault must have sufficient understanding. Equipment diagnostics development today, the people through a large number of experimental studies and a wide range of diagnostic practice, for a variety of devices (especially rotating machinery) of the failure mechanism, fault type and its characteristics have a considerable understanding of understanding. Statistics show that, with the production of a different nature, the type of equipment used is also different, so the proportion of various types of failures is also inconsistent. Here are several common fault diagnosis of rotating machinery vibration characteristics, diagnostic methods and examples.2.3.1 ImbalanceAccording to the information that various types of rotating machinery failure due to imbalance of about 30%, we can see that the machine rotor imbalance caused by rotating machinery vibration is a common multiple faults. To fully understand and grasp the characteristics and mechanism of unbalanced fault diagnosis is very important.1. The causes of imbalances caused by rotor imbalance are many reasons, such as:① unreasonable because it is designed geometry caused by different heart, or deviate from the geometric center line of rotary valve shaft;② Manufacture, installation error;③ Rotor material uneven, or heat unevenly;④ Rotor initial bending;⑤ Work medium in the solid impurities in the rotor on the uneven deposition;⑥ Rotor in the course of corrosion, wear and tear;⑦ Rotor parts loose, fall off.2. Rotor imbalance may lead to consequences for the flexible rotor may also generate additional degree of damage due to dynamic inertia of the centrifugal force caused by imbalance. For various reasons caused by rotor unbalance fault is a basically the same pattern. To sum up, the rotor imbalance may lead to the following undesirable consequences:(1) The rotor caused by repeated bending and internal stress, causing the rotor fatigue, even lead to rotor fault;(2) To enable the machine in operation during the excessive vibration and noise, so that it will accelerate the wear of bearings and other componentsto reduce life expectancy and efficiency of the machine;(3) Through the vibration of the rotor bearings, machine transmits to the base blocks and buildings, resulting in deterioration in working conditions.3. Rotor imbalance generally include the following four cases(1) Static unbalance;(2) double-sided imbalances;(3) Static and dynamic imbalance;(4) Dynamic imbalance. for example:2-1:Among them, static imbalance is an imbalance in the cross section, while the remaining three kinds of imbalance is an imbalance on the number of sections, and each inspired by a cross-section due to imbalances in the lateral vibration and static unbalance is the same as the mechanism of. In other words, the cross section generated by the phase and amplitude of vibration and its size may vary, but the vibration frequency is exactly the same, are the first-order rotation frequency (fundamental frequency),2-1f0 - a first-order frequency of the rotor, ie rotor fundamental frequency (Hz); n - rotor speed (r / min).Unbalanced rotor in rotation will produce a cycle of change was the imbalance in power, the cycle just that, as shown in Figure 2-2.With the rotor unbalance vibration signal, its time waveform and frequency spectrum of the typical curves shown in Figure 2-3, and generally has the following characteristics:(1) The vibration signal of the original time waveform of sine wave;(2) The frequency spectrum of vibration signal, its fundamental frequency component and a significant proportion, while other components such as frequency-doubling the proportion of relatively small.(3) In the process of speeding up or down, when (that is, when speed is less than the critical speed), the amplitude increases with the increase in W, both bearing the same direction of the force, while in the later, the amplitude increases with the W, but will decreases, and gradually tends to a smaller valuation.4. The basic method of diagnosis of unbalanced fault diagnosis of unbalanced faults, we must first analyze the signal frequency components, the existence of transponder prominent situation. Second, look at the direction of vibration characteristics, if necessary, further analysis of the changes in amplitude as speed or measuring the phase. Because the latter two tests carried out too much trouble to stop the problem involved, which in general is difficult in the production of the site done, and only to a non-for not only had to do when, but time can not be delayed too long.2.3.2 MisalignmentAs the rotor and turn on the sub-shaft connection between the use of connecting devices install properly, or due to bearing centerline deviation, or offset, or because the rotor bending, rotor and bearing clearance and load transfer in the bearing after the deformation and other reasons, tend to result in between the rotor (shaft) to the poor, resulting in vibration and lead to mechanical failure. It is also one of the very common mechanical failures .1. Shaft misalignment of the shaft does not include the three forms of coupling misalignment and bearing right in both cases, here we only discuss the coupling (shaft) misalignment. Coupling does not usually possesses the following three forms,For example2-4:(1) Parallel misalignment, this time through the rotor axis lines in parallel displacement.(2) The angle misalignment, this time to switch on the two axis lines intersect, or angle displacement.(3) Parallel synthesis misalignment angle, this time two lines intersect the rotor axis of displacement.Figure 2-5 shows the shaft vibration caused by misalignment angle parallel to the simple diagramIn general, the rotor shaft misalignment can cause additional load on the bearings, resulting in the bearing load between the re-allocation would lead to serious bearing damage caused by a strong vibration. On the other hand, with the coupling on both sides of bearing the load changes that may cause the system critical speed of the change in the uneven effects of an increase, giving rise to the coupling fatigue. When the bearing change is large, for the sliding bearing oil film may also cause instability.2. Shaft misalignment of the main features of a typical shaft misalignment radial vibration signal time waveform and frequency spectrum 2-6. And mainly has the following characteristics:(1) The vibration signal of the original time waveform distortion sinewave. (2) The radial vibration frequency spectrum of the signal to a multiplier, and second harmonic components of the main shaft misalignment more serious, and the second harmonic component of the greater proportion, in most cases more than one harmonic component of .(3) The axial vibration of components in the spectrum to octave higheramplitude.(4) Coupling on both sides of the axial vibration is essentially 180 °inverting.(5) A typical trajectory for the banana-shaped axis is precession.(6) Vibration on the more sensitive to changes in load, the generalvibration amplitude increases with the load increase.2.3.3 Rotor CrackIf the rotor rotating machinery are poorly designed (including the improper selection or structure is irrational) or improper processing methods, or the super life of running, it will cause stress concentration leading to cracks. On the other hand, fatigue, creep and stress corrosion can cause micro-cracks in the rotor, plus large change due to the twist and radial loadto form the mechanical stress state, resulting in continuous expansion of these micro-cracks eventually become a macro-crack.1. Three forms of rotor cracks(1) Closed crack. Rotor rotates; the crack was always closed state. When the crack zone in a compressive stress state, would constitute a closed crack, such as the rotor weight is not an unbalanced force smaller or unbalanced force precisely the opposite point to cracks, or uneven quality, moments generated by the rotor is greater than the quality of generated moment and so on. Closed crack little effect on the rotor thrust.(2) Open crack. When the rotor spins, the crack was always open state. Open cracks force the situation is exactly the opposite and closed crack; the crack area is always in tension stress state. Open crack will reduce the stiffness of the rotor, and its stiffness to the different nature of each, so that vibration increased.(3) The opening and closing crack. With the rotation of the rotor movement, crack was open and close alternately state, and generally turn the rotor of each week, the crack will be the corresponding open and closed each time. Crack opening and closing part of the open crack and the crack in the middle of a closed transition state, which is the most complex forms. Figure 2-7 shows the rotor with the opening and closing crack deflection curve diagram.Despite the change in the crack will affect the rotor vibration characteristics, but in most cases is not very sensitive, even the cracks in the rotor has a deep, sometimes hard to find significant changes in the vibration condition. For example, according to theoretical calculations, if there is a change in central depth is equal to 1 / 4 turn on the diameter of the crack, its stiffness is only about 10%, while the changes in critical speed is smaller, only 5%. Therefore, these changes will likely be completely submerged into the other signal, that is, from the observed changes in the natural frequency of the rotor, or when the normal operation of the vibration changes according to the early detection of cracks is very difficult. At present more effective way is to stop the process of measurement and analysis open the rate of change in amplitude.Generally speaking, when there open crack rotor, the rotor will become of all the stiffness of the differences. As a result, the vibration of the rotor with a non-linear nature of the spectrum, in addition to a harmonic component, there are twice, three times to five times the high-harmoniccomponents. Toward the crack, the stiffness of the rotor will be further reduced; a multiplier component, as well as twice or three times or five times, and other first-order harmonic components of the amplitude will be even greater.2. Be passed on to crack the monitoring and diagnosis is divided into three areas(1) Open, stopping when the variation of amplitude versus speed.(2) The impact of crack depth on the amplitude.Under normal circumstances, the vibration spectrum and the second harmonic component of twice the amplitude will increase with the depth of the monotonic crack growth, while the corresponding phase decreased with the increase of crack depth irregular fluctuations. It just can be used to distinguish between normal vibrations caused by imbalance.(3) The crack growth rate.But the crack propagation speed increases as the crack depth to accelerate, with a corresponding rate of increase in amplitude occurs phenomenon. In particular the rapid increase in second harmonic amplitude can often provide crack diagnostic information, so can take advantage of two trends in the changes in the harmonic components to diagnose the rotor cracks.3. Rotor cracks after the general characteristics of(1) The first-order critical speed is smaller than normal, especially when the crack worsens.(2) As the crack and stiffness caused by rotor asymmetry, the rotor speed of the formation of multiple resonance.(3) The crack rotor vibration response, one harmonic component of the degree of dispersion when compared with large crack-free.(4) A constant speed, the doubled, tripled the third harmonic and other components of the amplitude and the phase-order instability, and in particular to highlight the second harmonic component.(5) Due to the stiffness of cracked rotor asymmetry, so that pairs of rotor balancing difficulty.1.2中文翻译第2章旋转机械故障的研究及常见故障的振动诊断旋转机械是指那些主要功能是由旋转运动来完成的机械设备,如汽轮机、燃气轮机、发电机、电动机、离心式鼓风机、离心式压缩机泵、真空泵以及各种减速增速的齿轮传动装置等机械设备,都属于旋转机械范围。
泵类英汉翻译

泵类英汉翻译发一份泵类汉英对照表,请进入!汉语术语英文凹槽groove饱和压力Saturation Pressure保持环retaining ring保护层的形成Protective Layer Formation保护形式Types of Protection保证Guarantee背靠背叶轮泵Back-to-back Impeller Pump背叶片Back Vane泵pump泵测试效率pump test efficiency泵出力pump delivery泵的基础Pump Foundation泵的类型Pump Types泵的排出口Pump Discharge Nozzle泵的使用范围Application Fields for Pumps泵的输出功率Pump Output泵的旋转方向Direction of Pump Rotation泵房pump house(room)泵功率Pump Power泵和输送装置噪音Noises in Pumps and Pumping Installations 泵壳Pump Casings泵内沉积物Deposits in Pumps泵试验台Pump Test Bed泵输出功率的降低Reduction in Pump Output泵输入功率pump input power泵体pump casing泵吸入槽Pump Sump泵吸入管吸上高度pump lift泵吸入口Pump Suction Nozzle泵效率pump efficiency泵效率Pump Efficiency泵芯包pump cartridge泵性能曲线pump performance curve 泵站pumping house泵轴Pump Shaft比例泵proportioning pump比输送功Specific Delivery Work比转数Specific Speed边界层Boundary Layer变矩桨叶Variable Pitch Blade标准泵Standard Pump标准化工泵Standard Chemical Pump标准孔板Standard Orifice Plate标准喷嘴Standard Nozzle标准温度Standard Temperature标准文丘里管Standard Venturi Nozzle 标准压力Standard Pressure标准状态Standard Conditions表面保护Surface Protection表压Manometric Pressure并联运转Parallel Operation伯努利方程BERNOULLI Equation补偿器Compensator补给水泵make-up water pump部分负荷运转Part-load Operation残油输出装置Residual Pump-out Device槽slot测量的不精确性Uncertainty in Measurement 测量技术Measuring Technique测量孔板Measuring Orifice Plate测量偏差Measuring Tolerance测量误差Error of Measurement测量仪器Measuring Device测试转速test speed层流Laminar Flow齿轮泵gear pump齿轮传动泵Geared Pump齿轮箱Gearbox冲击冷凝Shock Condensation冲击压力Impact Pressure冲角Angle of Incidence抽出体积Extraction Volume抽气(吸)泵;真空泵suction pump出口侧盖板(大端盖)discharge cover出口截面Outlet Cross-section出口截面宽度Outlet Width出口弯管Outlet Elbow出口压力discharge pressure初始汽蚀Incipient Cavitation传输损失tansmission loss传送器Transmitter船头推进舵Bow Thruster Rudder船坞泵Dock Pump船用泵Marine Pump大气压Barometric Pressure大气压力Atmospheric Pressure带式过滤器Band Sereen单吸离心泵single-suctoin centrifugal单相交流电Single-phase Alternating Current单叶片叶轮Single Vane Impeller导向叶片Guide Vane导向装置Guide Arrangement低温泵Crygenic Pump低压泵Low Pressure Pump底料泵Sump Pump点蚀Pitting电感应式流量测量Inductive Flow Measurement电功率Electric Power电化学腐蚀Electrochemical Corrosion电机Electric Motor电机电耗Current Consumption of Electric Motors 电机温升Temperature Rise in Electric Motors电机转矩曲线Torque Curve of Electric Motors电解腐蚀Electrolytic Corrosion电缆密封压盖Cable Gland电力驱动Electric Drive电流current电路Electrical Circuits电气开关设备Electrical Switchgear电位序Electrochemical Series电压voltage电压降Voltage Drop顶点Apex定位螺栓fitted bolt动力液流Motive Water Flow动力粘度Dynamic Viscosity动量矩定理Theorem of Momentum动平衡Dynamic Balancing动下室排水泵Cellar Drainage Pump动压力Dynamic Pressure对开的润滑油密封split oil seal对轮the coupling对轮防护罩the coupling guard对轮螺栓coupling nut多级泵Multistage Pump多流式泵Multiflow Pump恩氏粘度Degrees Engler阀门和管件Valves and Fittings法兰结构Flange Construction反向流动Reversal of Flow反应堆泵Reactor Pump反转转速Reverse Rotational Speed防爆Explosion Protection防反转装置Reverse Rotation Locking Device 防腐Corrosion Protection防护装置guard放射Emission非堵塞式叶轮Non-clogging Impeller非扰动管道长度Undisturbed Length of Piping 非稳定流Non-steady Flow非稳定扬程曲线Unstable Throttling Curve费鲁德准数FROUDE Number费用Costs复算Re-evaluation干式安装Dry Installation干运转Dry Running高度Height高速离心泵High Speed Centrifugal Pump高压泵High Pressure Pump隔膜泵diaphragm pump隔膜式计量泵diaphragm type metering pump 给水泵feed water pump给水泵Feed Pump工业水泵industrial water pump工作特征Operating Characteristics公称尺寸Nominal Size公称压力Nominal Pressure功work功率power功率power功率测量power measurement功率调节power control功率损失power loss功率因数power factor cosφ供水泵Water Supply Pump固体颗粒的输送Conveying of Solids过流翼型Flow Profile过滤器Filter海水Sea Water海水泵Sea Water Pump海水淡化装置Sea Water Desalination Plant 海水箱Sea Chest 耗水量Water Consumption合适的流量corrected flowrate恒定油位油杯Constant Level Oiler虹吸流动Syphon Flow虹吸装置Syphoning Installation化工泵Chemical Pump化工稳定性表Chemical Stability Table环境保护Environmental Protection环形泵Ring-section Pump环形壳Annular casing回流导向叶片Return Guide Vane回路试验Loop Test混流叶轮Mixed-flow Impeller活塞传送器Piston Transmitter货船油泵Cargo Oil Pump机械传动Mechnical Drive机械密封Mechanical Seal机械效率Mechanical Efficiency基板Baseplate基本方程Fundation基础Foundation基建投资Capital Investment级Stage级间导叶interstage diffuser极数Number of Poles继电器Relay家用供水装置Domestic Water Supply Plant 间隙宽度Clearance Gap Width间隙密封Clearance Gap Seal间隙汽蚀Clearance Gap Cavitation间隙压力Clearance Gap Pressure监测装置Monitoring Device键key键槽keyway交流电Alternating Current角速度Angular Velocity接触器Contactor接通压力Switching-on Pressure节流调节throttling control节流系数throttling coefficient进液室Intake Chamber进液条件Intake Conditions进液弯管Intake Elbow浸蚀Erosion经济可行性计算Economic Viability Calcuation 净正吸入压头NPSH(Net Positive Suction Head)径向力Radial Force径向剖分壳体Radially Split Casing径向推力Radial Thrust径向叶轮Radial Impeller径向轴承journal bearing绝对速度Absolute Velocity卡诺冲击损失Carnot Shock Loss卡普兰弯管Kaplan Elbow铠装泵Armoured Pump抗腐蚀性Corrosion Resistance壳体Casing可抽出性withdrawability可调叶片adjustable vane空气泵Air Pump空气提升泵Air-Lift Pump空心旋涡Hollow Vortex孔板Oriffice Plate孔径比Apertuer Ratio扩压管(圆锥管)Diffuser(Conical Duct)扩压器(导轮)Diffuser(Guide Wheel)冷凝液泵Condensate Pump冷却剂泵Coolant Pump冷却水泵Cooling Water Pump离心泵centrifugal pump离心泵Centrifugal Pump离心泵的安装Installation of Centrifugal Pump离心泵的操作条件Operating Conditions of Centrifugal Pumps 离心泵的操作性能Operating Behaviour of Centrifugal Pumps 离心泵的冲击损失Shock Loss in Centrifugal Pumps离心泵的间隙损失Clearance Gap Loss in Centrifugal Pumps 离心泵的平稳运行Smoop and Quiet Running of Centrifugal Pumps 离心泵的验收试验规范Acceptance Test Codes for Centrifugal Pumps 离心泵的制造材料Construction Material for Centrifugal Pumps离心泵的注水Priming of Centrifugal Pumps离心泵调节Control of Centrifugal Pumps离心泵和驱动设备保养Care of Centrifugal Pumps and Drives 离心泵失衡Out-of-Balance of Centrifugal Pumps离心泵装置Centrifugal Pump Plant离心式鼓风机centrifugal blower离心式滤油机centrifugal oil filter离心式压缩机centrifugal compressor离心水泵centrifugal water pump立式泵vertical pump立式屏蔽泵(筒形泵)Vertical Can-type Pump立轴式井泵Vertical Spindle Well Pump利息支付Interest Payment连续性方程Continuity Equation两相流动Two-phase Flow临界转速Critical Speed of Rotation流程泵Process Pump流程型结构Process Type Construction 流道涡流Channel Vortex流动分离Flow Separation流动功Flow Output流量flowrate流量Flow流量(体积流量)Capacity流量测定Flow Measurement流量测量Capacity Measurement流量调节器Flow Controller流量系数Flow Coefficient流量指示器、流量观察窗flow indicators 流速Flow Velocity流体Fluid流体动力学Fluid Dynamics流体机械Fluid Flow Machine流线Flow Line轮毂比Hub Ratio螺杆泵screw pump(spiral pump)螺纹紧固件threaded fastener马达输出功率motor output power马达输入功率motor input power马达效率motor efficiency迷宫密封labyrinth gland迷宫密封箱体labyrinth gland housing 迷宫式密封Labyrinth Seal密封衬套shaft sleeve内效率Internal Efficiency那维尔-斯托克斯方程NAVIER-STOKES Equation耐酸泵Acid Pump焾Enthalpy能Energy能量级Energy Level逆时针旋转叶轮Counterclockwise Rotating Impeller 凝泵condensate extraction pump凝结水泵condensate transfer pump凝汽器抽气泵condenser air pump牛顿流体NEWTONian Fluid扭力杆T orsion Rod扭力计T orsion Dynamometer欧拉方程EULER Equation排出段Discharge Casing排出管线Discharge Line排出管嘴Discharge Nozzle排出损失Discharge Loss排灌站水泵Drainage Station Punp排气Venting排气阀Vent Valve排水泵Dewatering Pump排水量Water Yield排污泵blowdown pump(sewage pump)排污泵Faeces Pump旁路By-Pass皮带传动Belt Drive皮托管Pitot Tube频率frequency平垫片flat gasket平衡鼓balance drum平衡鼓螺母balance drum nut平衡孔balance'hole平衡液体流量balance water flow平衡装置balancing device平衡状态equilibrium condition平皮带传动flat belt drive屏蔽泵Canned Motor Pump起动Start Up起动过程Starting Process起动时间Starting Time起动转矩Starting T orgue气囊的形成Formation of Air Pockets 气体分离Gas Separation 汽蚀Cavitation汽蚀磨损Cavitation Wear汽蚀噪音Cavitation Noise强制循环泵forced-circulation pump切断压力Switching-off Pressure切换频率Switching Frequency氢指数Hydrogen Exponent清水泵Clean Water Pump驱动Drive热Heat热泵Heat Pump热含量Heat Content热虹吸Thermosyphon热量Quantity of Heat热载体泵Heat Transfer Media Pump热障Thermal Barrier容积泵Positive Displacement Pump入口导叶suction guide入口管嘴Entry Nozzle入口截面Inlet Cross-section入口压力suction pressure入口锥管Entry Cone润滑油泵Lubricating Oil Pump三相电机Three-phase Motor三相电流Three-Phase Current三相制Three-phase System设计工作点Design Duty Point声学Acoustics时间Time视在功率Apparent Power试验台T est Bed手动泵Hand Pump首级内泵壳first stage ring section输送黏性液体黏性泵centrifugal pump handling viscous liquids 甩油环,抛油环oil thrower双缸泵组Twin Pumping Set双流道泵two-channel impeller pump双流道叶轮two-passage impeller双蜗壳Double Volute水厂泵waterworks pumps水锤water hammer水的硬度hardness of water水力效率hydraulic efficiency水流量计water meter水泥壳泵concrete casing pump水喷射water jet水喷射泵water jet pump水温water temperature水下泵underwater pump水下电机underwater motor水下电机泵underwater motor pump水银泵mercury pump水硬度water hardness速度Velocity速度测定Measuring of Speeds速度测量Velocity Measurement速度三角形Velocity Triangle损失系数Loss Coefficient锁紧垫圈、防松垫圈lock-washer探头Probe特性Characteristic特性曲线Characteristic Curve特性因数Characteristic Factor体积流量Volume Flow停转时间Run-down Time通量线Flux Line同步转速Synchronous Speed铜导体Copper Conductor投资评价Capital Servicing透平驱动泵Turbine Driven Pump涂层Coat of Paint推力盘thrust collar推力瓦thrust pad推力轴承撑板thrust carrier ring 推力轴承室thrust bearing housing 托轮Jockey Pulley弯管Elbow弯管壳体泵Elbow Casing Pump卧式泵Horizontal Pump污泥泵Sludge Pump污水泵Sewage Pump无冲击流入Shock-free Entry无泄漏Leak-tightness吸入口Suction Nozzle吸入室Suction Chamber吸入性能Suction Behaviour吸入压头Suction Head吸入叶轮Sution Impeller纤维素Cellulose纤维性物料Fibrous Material相对速度Relative Velocity相合定律Congruence Law相似条件Similarity Conditions相位移Phase Displacement消防泵Fire-fighting Pump消声测量Noise Abatement Measures 销钉、定位销dowel pin 小舌片tab效率复算Efficiency Re-evaluation斜度Steepness斜流叶轮Diagonal Impelier斜盘式泵Swash Plate Pump泄漏出的密封水隔离门(相当于密封水卸荷阀)leak-off isolating valve 泄漏损失Leakage Loss星形轮Star Wheel星形-三角形起动器电路Star-delta Starter Circuit性能图Performance Chart许可公差Warranty Tolerance许可区域Warranty Zone旋流Swirl Flow旋塞阀Cock旋涡泵Peripheral Pump旋涡式叶轮Peripheral Impeller旋转方向Direction of Rotation旋转速度Rotational Speed压差Differential Pressure压降Pressure Drop压力Pressure压力波Pressure Wave压力波动Pressure Surge压力测量Pressure Fluctuation压力测量Pressure Measurement 压力等级Pressure Categories压力给水装置Hydrophor Plant压力计Manometer压力脉动Pressure Fluctuation压力容器Pressure Vessel压力损失Pressure Loss压力损失Head Loss压力系数Pressure Coefficient压头Pressure Head验收试验Acceptance Test扬程head扬程曲线Throttling Curve叶轮impeller叶轮ipeller叶轮impeller叶轮侧面摩擦Impeller Side Friction 叶轮的修整Trimming of Impellers 叶轮叶片Impeller Vane叶轮叶片节距调节Impeller Blade Pitch Adjustment叶片叶片vane叶片角Blade Angle叶片节距调节机构Blade Pitch Adjustment Gear叶片节距调节装置Blade Pitch Adjustment Device叶梢背部切削Cutting Back of Impeller Vane Tips叶栅vane cascade叶栅流动Cascade Flow液化气泵Liquefied Gas Pump液环泵Liquid Ring Pump异步电机Asynchronous Motor阴极保护Cathodic Protection音量级Sound Volume Level音速Sound Velociyt引水级Priming Stage应变测定技术Strain Measurement Technology应力腐蚀(裂纹)Stress Corrosion (Cracking)永久磁铁联轴器Permanent Magnet Coupling用入口导向叶片控制涡流Rotation Swirl Control by Inlet Guide Vanes 油泵Oil Pump油挡oil guard有势流动Potential Flow有效功率Acitive Power有效汽蚀余量n.p.s.h.r有用功率输出Useful Output右旋叶轮right-handed impeller诱导轮Inducer圆弧形叶片Circular Arc Vane圆周速度Peripheral Speed(Circumferential Velocity)运动粘度Kinematic Viscosity运行时数Number or Running Hours再生泵Regenerative Pump脏水泵Dirty Water Pump折旧Amortization振动Vibration正吸入压头positive suction head直径系数Diameter Coefficient直联泵组Close-coupled Pumping Set直流电Direct Current直流电机Direct Current Motor直流平板式起动器Direct Current Face Plate Starter 止动销stop pin纸浆泵Pulp Pump纸浆浓度Pulp Density纸浆输送Conveying of Pulp制造公差Manufacturing T olerance质量Mass质量惯性矩Mass Moment of Inertia质量流量Mass Flow中点线Mid-point Conductor中性线Neutral Conductor中压泵Medium Pressure Pump重力加速度Gravitational Constant重量Weight轴轴承Bearing轴承支架bearing housing轴承支架盖bearing housing cover轴封Shaft Seal轴封环Shaft Sealing Ring轴功率Shaft Power轴颈shaft journal轴流泵axial pump轴流泵Axial Pump轴流叶轮Axial Impeller轴套、衬套gland bush轴推力Shaft Thrust轴向力Axial Force轴向剖分壳体Longitudinally Split Casing 轴向推力Axial Thrust 主循环泵Primary Circulating Pump柱塞泵Plunger Pump转动惯量Moment of Gyration转矩Torque转矩的测定T orque Measurement转速传感器Rotational Speed Transmitter 自动调节Self-regulation自动断路器Self-acting Circuit Breaker自动开关Automatic Switches自耦变压器式起动器Autotransformer Starter 自吸泵Self-priming Pump自由流动泵Free-flow Pump总测量偏差Overall Measuring T olerance总静压头Total Static Head总偏差Overall Tolerance总效率Overall Efficiency总压力Tital Pressure总扬程T otal Headmeasured flowratevelocity headgauge/lever correctiongenerated headseal sleeve nuts短心轴stub axle轴axes轴axis轴axle(U.S.A)轴承衬套bearing bushing(U.S.A)轴肩挡圈;防护罩protecting collar巴氏合金;白合金;轴承合金white metal半贯流式轴流泵;弯管轴流泵angle-type axial flow pump半可调式轴流泵axial flow pump with blades adjustable when stationary 泵轴Pump Shaft泵轴承支架pump bearing bracket长轴深井泵borehole shaft driven(centrifugal) pump长轴深井泵(美)multistage vertical turbine pump衬套;轴套bushing齿形联轴器gear-type coupling出口轴面速度系数;流量系数capacity constant磁力联轴节齿轮泵magnetically coupled gear pump从动螺杆;从动心轴idler spindle从动轴driven shaft从动轴idler shaft弹性盘联轴器flexible disc coupling弹性圆柱销联轴器flexible pin coupling电磁联轴器electromagneic coupling电磁联轴器magneto coupling电磁联轴器magneto-coupling调节轴adjusting spindle副传动轴countershaft spindle副轴;中间轴;从轴auxiliary shaft刚性联轴器solid coupling刚性联轴器;刚性联接rigid coupling功率曲线;轴功率曲线;制动功率曲线brake horsepower curve 贯流泵;直管轴流泵rubular type axial flow pump滚动轴承anti-friction bearing滚动轴承ball/rolling bearing滚动轴承rolling contact bearing滚针轴承needle bearing恒定轴向间隙齿轮泵fixed axial clearance gear pump滑动轴承plain friction bearing滑动轴承sleeve bearing滑动轴承sliding bearing活塞销;轴头销gudgeon pin架;轴承衬套(美);泵支架(美) frame径向滚柱轴承radial roller bearing径向球轴承radial ball bearing径向轴封radial shaft seal可调式轴流泵axial flow pump with adjustable(or variable)pitch blades 可调式轴流泵propeller pump with adjustable or variable pitch blades 可逆叶片轴流泵axial flow pump with reversible blades可逆叶片轴流泵propeller pump with reversible blades空心轴hollow shaft shaft冷冻装置用无轴封泵glandless pump for refrigerating installation立轴式井泵Vertical Spindle Well Pump联轴器coupling笼形轴承托架bearing bracket lantern笼形轴承托架bearing housing lantern螺纹联轴器screwed coupling米切尔型推力轴承Michell type thrust bearing内轴承泵pump with internal bearing(s)挠性法兰联轴器flexible flange coupling挠性联轴器elastic coupling挠性联轴器flexible coupling挠性轴flexible shaft配流盘式轴向活塞泵flat valve axial piston pump配流盘式轴向活塞泵port plate axial piston pump配流盘式轴向活塞泵valve plate axial piston pump喷水推进轴流泵axial flow pump for water jet propulsion喷水推进轴流泵water jet propulsion axial flow pump偏心轴eccentric shaft强制润滑轴承;压力润滑轴承forced oil lubricated bearing球面推力轴承spherically mounted thrust bearing曲轴crankshaft曲轴防护罩crankguard曲轴防护罩crankshaft guard曲轴箱支座crankcase pedestal曲轴销crank pin驱动轴;传动轴drive shaft全可调式轴流泵axial flow pump with blades adjustable in operation 全可调式轴流泵axial flow pump with variable piteh blades水润滑轴承water lubricating bearing套筒联轴器sleeve coupling推力滚柱轴承thrust roller bearing推力球轴承ball thrust bearing推力轴承thrust bearing推力轴承;扇形块thrust bearing segment推力轴承扇形块thrust bearing pad外轴承泵pump with external bearing(s)万向轴cardan shaft无轴封泵glandless pump无轴封计量泵glandless metering pump橡胶轴承rubber bearing斜垫轴向推力轴承tilting pad axial thurst bearing斜缸型轴向柱塞泵tilting cylinder block type axial plunger pump 斜盘式轴向活塞泵cam plate type axial piston pump 斜盘式轴向活塞泵swash plate axial piston pump斜盘式轴向活塞泵wobble plate axial piston pump斜置轴流泵inclined axial flow pump斜轴式轴向活塞泵angle-type axial piston pump斜轴式轴向活塞泵bent axis axial piston pump旋涡轴线eddy axis旋涡轴线vortex axis压入式轴承盖pressed-in type bearing cover叶轮轴面形状;工作轮图profile of the impeller液体动力轴承hydrodynamic bearing永久磁铁联轴器Permanent Magnet Coupling油环轴承ring lubricating bearing油环轴承ring oiling bearing油脂润滑轴承grease lubricated bearing支轴销;支点销fulcrum pin支座;轴架pedestal中间心轴idler axle中间心轴intermediate axle中间轴;副轴;从轴counter shaft中间轴;副轴;从轴intermediate shaft轴shaft轴;心轴;锭子spindle轴承bearing轴承Bearing轴承衬(套)bearing bush轴承衬套bearing cartridge轴承衬套bearing insert轴承端盖bearing end cover轴承盖bearing cover轴承合金bearing alloy轴承架bearing bracket轴承架bearing pedestal轴承架bearing spider轴承架;泵托架headstock轴承架固定式泵pump with bearing bracket轴承浸泡试验;轴承泡胀试验bearing swelling test 轴承冷却室bearing cooling chamber轴承螺母bearing nut轴承套bearing sleeve轴承体;轴承箱bearing box轴承托架箱bearing bracket housing轴承瓦;轴承衬垫;轴承衬套bearing line轴承吸水试验bearing absorption test轴承箱;轴承体bearing housing轴承座bearing carrier轴对称axial symmetry轴对称;旋转对称rotational symmetry轴对称流axisymmetrical flow轴封shaft seal轴封Shaft Seal轴封环Shaft Sealing Ring轴功率;制动功率;制动马力brake horsepower轴护套Shaft Protecting Sleeve轴护套shaft tunnel tube轴护套(美)shaft enclosing tube轴肩挡圈loose(shaft) collar轴肩挡圈shaft collar轴肩挡圈shoulder ring轴颈neck journal轴颈shaft neck轴颈axle journal轴颈;期刊journal轴颈套;填料衬套neck bush轴流泵Axial Pump轴流泵;螺桨泵axial flow pump轴流泵叶轮室propeller bowl轴流式涡轮机axial-flow turbine轴流式叶轮axial flow impeller轴流叶轮Axial Impeller轴流增压器axial flow booster轴马力;轴功率shaft horsepower轴面流线meridian streamline轴面速度meridional velocity轴面投影图elevation view轴配流径向活塞泵pintle valve radial peston pump 轴配流径向活塞泵valve spindle radial piston pump 轴套shaft wearing sleeve 轴套Axis Guide轴套shaft sleeve轴套;套(筒)sleeve轴套拆卸器sleeve puller轴瓦;轴承箱;轴承体bearing sheet轴位指示器shaft position indicator轴吸泵axial inlet pump轴向单吸液环泵axial single entry liquid ring pump轴向导叶axial diffuser轴向滑移aixal slip轴向活塞泵axial piston pump轴向加速度axial acceleration轴向间隙axial clearance轴向间隙压力补偿齿轮泵gear pump with pressure-dependent axial clearance 轴向间隙压力补偿齿轮泵gear pump with pressurized side plate轴向力axial force轴向力Axial Force轴向流动axial flow轴向磨损指示器axial wear indicator轴向剖分壳体Longitudinally Split Casing轴向双吸液环泵axial double entry liquid ring pump轴向速度axial velocity轴向推力axial thrust轴向推力Axial Thrust轴向吸入泵axial suction pump轴向压力axial pressure轴向柱塞泵axial plunger pump主动螺杆;驱动心轴driving spindle主动轴driving shaft柱销联轴器pin coupling爪形联轴器claw coupling爪形联轴器dog coupling爪形联轴器jaw coupling锥形联轴器cone(type) coupling锥形联轴器taper coupling子午面;轴面meridian plane自锁轴套self-locking sleeve半贯流式轴流泵;弯管轴流泵angle-type axial flow pump半可调式轴流泵axial flow pump with blades adjustable when stationary 泵pump泵房pump house泵盖casing cover泵缸pump barrel泵缸pump cylinder泵缸套pump barrel line泵缸套pump cylinder line泵缸体pump cylinder block泵工况pump operating condition泵工况pump operating duty泵体pump body泵体衬套pump body insert泵体衬套pump casing insert泵托架pump bracket泵站设计design of pump station泵罩outer pump mantle泵支架pump bearing lantern泵轴承支架pump bearing bracket泵装置pumping device泵装置pumping machine泵组integral pump group泵座pump frame闭式叶轮泵pump with enclosed impellers波纹管泵bellows pump仓底泵bilge pump侧流道泵壳;旋涡泵泵体casing with transfer passages 侧流道泵壳;旋涡泵泵体annular casing长轴深井泵borehole shaft driven(centrifugal) pump 衬青铜泵bronze fitted pump齿轮比例泵abjustable discharge gear pump冲击波泵(振荡器)shock wave oscillator导流壳式多级泵pump with bowl-type vaned casing低温泵cryopump底料泵;塔底液泵bottoms pump底吸泵bottom inlet pump底吸泵bottom suction pump电磁驱动泵pump with cyclic electromagnetic drive 风动活塞泵air-powered piston pump辅泵;辅助泵auxiliary pump辅扫仓泵;副清仓泵auxiliary stripping pump附属泵attached pump工程用泵building site pump固定缸体泵pump with nonrotating cylinder固体输送泵pump for water-borne solids管网泵pump for pipe system灌泵priming of pump锅炉给水泵BFW锅炉给水泵boiler feed pump。
中英文文献翻译-液压泵

附录外文文献原文:The commonly used sources of power in hydraulic systems are pumps and accumulators .Similarly,accumulator connected to atmosphere will dischange oil at atmosphere pressure until it empty. only when connected to a system having resistance to flow can pressure be developed.Three types of pumps find use in fluid-power systems:rotary,reciprocating or piston-type, and 3,centrifugal pumps.Simple hydraulic system may use but one type of pump . The trend is to use pumps with the most satisfactory characteristics for the specific tasks involved . In matching the characteristics of the pump to the requirements of the hydraulic system , it is not unusual to find two types of pumps in series . For example , a centrifugal pump may be to supercharge a reciprocating pump , or a rotary pump may be used to supply pressurized oil for the contronls associated with a reversing variabledisplacement pumps . Most power systems require positive displacement pumps . At high pressure , reciprocating pumps are often preferred to rotary pumps .1、Rotary pumpsThese are built in many differnt designs and extremely popular in modern fluid power system . The most common rotay-pump designs used today are spurgear , internal gear ,generated rotor , sliding vane ,and screew pumps . Ehch type has advantages that make it most suitable for a given application .2、Gear pumpsGear pumps are the simplest type of fixed displacement hydraulic pump available . This type consists of two external gear , generally spur gear , within a closed-fitting housing . One of the gear is driven directly by the pump drive shaft . It ,in turn , then drives the second gear . Some designs utilize helical gears ,but the spur gear design predominates . Gear pumps operate on a very simple principle . As the gear teeth unmesh , the volume at the inlet port A expands , a partial vacuum on the suction side of the pump will be formed . Fluid from an external reservoir or tank is forced by atmospheric pressure into the pumpinlet . The continuous action of the fluid being carried from the inlet to the discharge side one of the pump forces the fluid into the system .3、Vane pumpsThe vane pump consists of a housing that is eccentric or offset with respect to the drive shaft axis . In some models this inside surface consists of a cam ring that can be rotated to shift the relationship between rotor are rectangular and extend radially from a center radius to the outside diameter of the rotor and from end to end . A rectangular vane that is essentially the same size as the slot is inserted in the slot and is free to slide in and out .As the rotor turns , the vanes thrust outward , and the vane tips track the inner surface of the housing , riding on a thin film of fluid . Two port or end plates that engage the end face of the ring provide axial retention .Centrifugal force generally contributes to outward thrust of the vane . As they ride along the eccentric housing surface , the vane move in and out of the rotor slots . The vane divide the area between the rotor and casing into a series of chambers .The sides of each chamber are formed by two adjacent vanes ,the port or end plates , the pump casing and the rotor . These chambers change in change in volume depending on their respective position about the shaft .As each chamber approaches the inlet port , its vanes move outward and its volume expands , causing fluid to flow into the expanded chamber . Fluid is then carried within the chamber around to the dischange port . As the chamber approaches the discharge port , its vanes are pushed inward ,the volume is reduced , and the fluid is forced out the discharge port .Vane pump speed is limited by vane peripheral speed . High peripheral speed will cause cavitation in suction cavity . which results in pump damage and reduced flow .An imbalance of the vanes can cause the oil film between the vane tips and the cam ring to break down , resulting in metal-to-metal contact and subsequent increased wear and slipage . One metheod applied to eliminate high vane thrust loading is a dual-vane construction .4、Piston-type pumpAll piston pumps operate by allowing oil to flow into a pumping cavity as a piston retreats and then forcing the oil out into another chamber as the piston advances . Design differences among pumps lie primarily in the methods of separating inlet from outlet oil .5、In-line piston pumpThe siplest typeof axial piston pump is the swash plate in-line design .The cylinder are connected though piston shoes and a retracting ring , so that the shoes beat anainst an angled swash plate . As the block turns ,the piston shoes follow the swash plate ,causing the piston to reciprocate . The ports are arranged in the valve plate so that the pistons pass the inlet port as they are being pulled out and pass the outlet port as they are being forcing back in .The angle of the swash plate controls the delibery . Where the swash plate is fixed , the pump is of the constant-displacement type . In the variable-displacement , inline piston pump , the swash plate is moumted on a pivoted yoke . As the swash plate angle is increased , the cylinder stroke is increase , resulting in a greater flow . A pressure compensator control can position the yoke automatically to maintain a constant output pressure .6、BENT-axis piston pumpAs the shaft roates , distance between any one piston and the valving surface changes continually . Each piston moves away from the valving surface during one half of the revolution and toward the valving surface during the other half . The inlet chamber is in line as the pistons move away , and the outletr chamber is in line as the pistons move closer , thus drawing liquiring in during one half of the inlet chamber as the pistons are moving away from the pintle . Thereforce , during rotation , pistons draw liquid into the cylinder bores as they pass the inlet side of the pinntle and force that liquid out of the bores as they pass the outlet side of the pintle . The displacement of this pump varies with the offset angle , the maximum angle being 30 degree ,the minimum zero . Fixed displacement models are usually avaiable with 23 degree angle .In the variable displacement construction a yoke with an external control is used to change the angle . With some contronls , the yoke can be moved over center to reverse the direction of flow from the pump .7、Pump/system interactionPressure-compensated variavle delivery pumps do not require a relief valve in the high pressure line . The pressure compensation feature eliminates the need for the relief valve .In nearly all working systems ,however , at least one is used on just-in-case basis . The use of a pressure compensator , while avoiding dependence on a relief valve , brings on its own problems .The actuator -spring-spool arrangement in the compensator is a dynamic , damped-mass-spring arrangement .However , when the system calls for a chang in axhievetheir maxmum volume as they reach the inlet port , the maximum volume of fluid will ve moved .If the relationship between housing and rotor is changed such that the chambers achieve their minimum of zero volume as they reach the inlet port , the pump delivery will be reduced to zero .Vane pump speed is limited by vane peripheral speed . High peripheral speed will cause cavitation in suction cavity , which results in pump damage and reduced flow . An imbalance of the vanes can cause the oil film between the cane tips and the cam ring to break down , resulting in metal-to-metal contact and subsequent increased wear and slipage . One method applied to eliminate high vane thrust loading is a dual-vane construction . In the dual-vane construction , tow independent vanes are located in each totor slot chmbered edges along the sides and top of each vane from a channel that essentially balances the hydraulic pressure on the top and bottom of each pair of vanes .Centrifugal force cause the vane to follow the contour of the cam-shaped ring .There is just sufficient seal between the vanes and ring without destroying the thin oil film .外文文献中文翻译:常用的液压系统的动力源是泵和蓄能器。
泵中英文对照

泵中英文对照序号设备英文名称设备对应中文型式备注1 D.O. Transfer pump with motor柴油输送泵卧式/齿轮泵2 F.O. Transfer pump with motor燃油输送泵卧式/齿轮泵3L.S.F.O. Transfer pump with motor低硫燃油输送泵卧式/齿轮泵4Main L.O. pump with motor主机滑油泵潜入式离心泵5Cylinder Oil pump with motor 汽缸油输送泵卧式/齿轮泵6L.O. Transfer pump with motor 滑油输送泵卧式/齿轮泵7Sludge pump with motor油渣泵卧式/齿轮泵8Sterm tube L.O. pump with motor 艉管滑油泵卧式/齿轮泵9Daily Bilge pump with motor 日用舱底泵卧式/齿轮泵10Bilge& G.S. pump with motor舱底总用泵立式/离心泵11Ballast pump with motor 压载泵立式/离心泵12Fire, &G.S. pump with motor 消防总用泵立式/离心泵13货舱舱底水喷射泵14压载水扫舱喷射泵15锚链舱喷射泵16艏尖舱喷射泵17Main L.T. Cooling F.W. pump with motor主机低温淡水冷却泵立式/离心泵18Cooling S.W.pump with motor冷却海水泵立式/离心泵19Cooling water pump with motor冷却水泄放泵卧式/离心泵20M/E Jecker Cooling F.W.pump with motor 主机高温淡水冷却泵立式/离心泵21Emergency Fire pump with motor应急消防泵立式/离心泵22Drinking water pump with motor饮用水泵卧式/离心泵23Hot water circulating pump with motor 热水循环泵卧式/离心泵24Fresh water pump with motor淡水泵卧式/离心泵25Sewage pump with motor污水泵卧式/离心泵26Bilge transfer pump with motor洗舱水驳运泵卧式/离心泵27MGO Transfer pump with motor MGO输送泵卧式/离心泵。
【翻译必备】水泵中英文对照表供参习
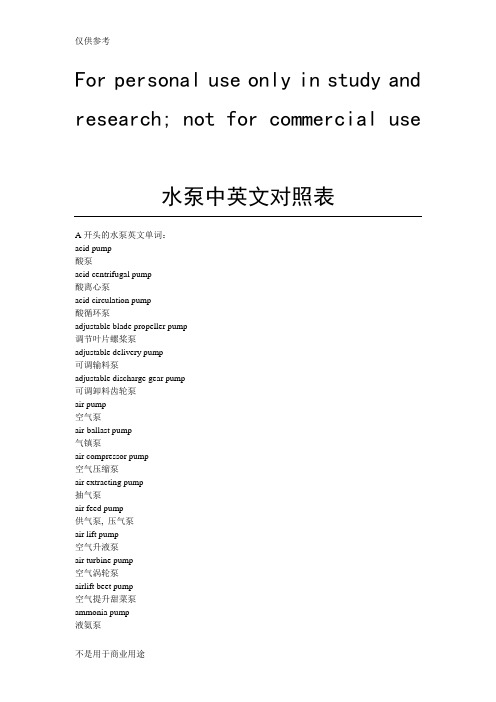
For personal use only in study and research; not for commercial use水泵中英文对照表A开头的水泵英文单词:acid pump酸泵acid centrifugal pump酸离心泵acid circulation pump酸循环泵adjustable blade propeller pump调节叶片螺桨泵adjustable delivery pump可调输料泵adjustable discharge gear pump可调卸料齿轮泵air pump空气泵air-ballast pump气镇泵air compressor pump空气压缩泵air extracting pump抽气泵air feed pump供气泵, 压气泵air lift pump空气升液泵air turbine pump空气涡轮泵airlift beet pump空气提升甜菜泵ammonia pump液氨泵Archimedean screw pump阿基米德螺旋泵artesian well pump自流井用抽水机articulated vane pump铰连叶片泵aspirator pump吸气泵; 抽气泵atomizing pump雾化式泵atmospheric pump空气泵, 抽气泵attached pump(主机)附备泵auto-grease pump自动注油泵automatic Sprengel pump自动施普伦格尔真空泵(将高真空泵与喷水抽气泵相联的自动抽真空装置) automatic tire pump自动气泵auxiliary pump辅助泵auxiliary air pump辅助空气泵auxiliary feed pump辅助进给泵auxiliary feed water pump辅助给水泵auxiliary fuel pump辅助燃料泵auxiliary lubrication pump辅助润滑油泵axial pump轴流泵axial piston pump轴向活塞泵axial plunger pump轴向柱塞泵B开头的水泵英文单词:backing pump级泵; 初级抽气泵backpack pumpbarrel pump桶式喷雾泵, 桶式泵barrel-type pump鼓形泵beam-balanced pump游梁平衡式抽油机beet pump甜菜泵biflex fuel pump燃料进料泵bilge pump喷射器; 船底排水泵blending pump混合泵boiler feed pump锅炉给水泵boiler proving pump锅炉试验泵booster pump升压泵, 前置泵, 增压泵booster diffusion pump增压扩散泵booster oil pump升压油泵booster oil diffusion pump增压油扩散真空泵, 辅助油扩散真空泵booster-type diffusion pump增压式扩散泵borehole pump深井泵, 钻井泵(一般为离心泵, 悬挂在钻井内) bottle pump玻璃水银扩散泵bottom pump井底车场水泵bottom hole pump井底沉没式泵brine pump盐水泵brine circulating pump盐水循环泵brine injection pump腌肉用盐水注射泵broad band light pumpbucket pump斗式唧筒[泵]built-on pump连发动机的泵松密度bulk plant pump油库泵bull deep-well pump杆式深井泵C开头的水泵英文单词:caisson pump沉箱泵cam pump凸轮泵cam-type axial piston pump 斜盘式轴向柱塞泵canned pump密封轻便泵canned-motor pump屏蔽电机泵; 密封电机泵canyon-type pump屏蔽型泵carbonic acid gas pump碳酸气泵cargo pump货船泵; 大排量的泵cargo oil pump装油泵cavitation pump水泵气蚀centrifugal pump离心泵, 离心抽机centrifugal booster pump 离心式增压泵centrifugal fish pump离心鱼泵centrifugal sewage pump 离心式污水泵centrifugal water pump离心式水泵centripetal pump向心泵链式泵charge pump进料泵charging pump充液泵; 辅助泵; 上水泵; 送料泵check-valve pump止回阀配流泵chopper-type muck pump带切碎器的液体厩肥泵circulating pump循环泵, 环流(水)泵circulating-water pump水循环泵circulation oil pump循环油泵clean-up pump清除泵, 吸收泵cloverotor pump纤维离解风送机coal lifting pump煤水泵cog-wheel pump齿轮泵cold pump低温泵collecting pump收集泵combination pump复合泵, 组合泵combined suction and force pump 吸压(两用)泵, 联合真空压力表compound pump复式唧筒[水泵]compression pump压缩机, 压气机[泵] compressor vacuum pump压气机真空泵concrete pump混凝土泵condensate [extraction] pump冷凝水泵condensate return pump冷凝回水泵condensation air pump凝汞抽气泵condenser pump冷凝泵conduction pump传导泵; 直流电磁泵constant rate pump定量泵constant volume pump恒容量泵constant-flow pump恒定流量泵controlled by-path injection pump旁通控制的喷油泵controlled volume pump计量泵coolant pump冷却液泵cooling medium pump冷却介质泵; 输送冷却介质的泵cooling water pump冷却水泵cream pump奶油泵crescent pump新月形齿轮泵cryogenic pump低温泵cryogenic fluid pump低温流体泵, 深冷流体泵, 冷剂泵cryosorption pump低温吸着泵cubic type portable gasoline meter pump 立方体型可搬运式计量器curd pump(干酪的)凝乳输送泵curing pump腌制盐水注射泵cycloidal pump摆旋泵D开头的水泵英文单词:deck pump甲板泵deep-well pump深井泵, 潜水泵delivery pump输送泵diaphragm pump隔膜泵, 膜片泵diaphragm-type fuel pump膜片式燃油泵diesel pump柴油泵differential pump差动泵diffuser pump扩散泵diffuser type centrifugal pump扩散形离心泵diode sputter-ion pump二极管溅射离子泵[抽机]direct-acting pump直接联动泵direct acting steam pump直动蒸汽泵direct-current electromagnetic pump 直流电磁泵direct-injection pump【航空】直接喷射式燃料泵discharge pump排水泵, 排气泵, 排泄泵dispensing pump分配泵, 量油泵displacement pump往复式泵, 活塞泵, 柱塞泵, 排代泵distillation products jet pump蒸气喷射真空泵distributor type fuel pump分配式燃料泵divergent nozzle pump发散喷嘴扩散泵diving pump潜水泵diving air pump潜水空气泵donkey pump气动往复泵, 辅助泵double pump双连泵double-action pump双动泵, 双作用(活塞)泵double air pump复式气泵double-casing volute pump双套涡囊泵double discharge gear pump 双出口齿轮泵double-direction gearpump双向齿轮泵double-pistonpump双活塞泵double-stroke deep well pump 深井双冲程水泵double-suction pump双吸泵downhole engine pump井底水力活塞泵drainage pump排泄泵draining pump排水泵draw-off pump抽取泵dredgepump吸泥泵, 排污泵, 泥浆泵driven well pump钻井泵drowned pump沉浸泵drum pump回转泵dry-air pump干(燥)空气泵, 干风泵dry vacuum pump干式真空泵dual pump复式泵, 双缸泵dual injection pump复式注油泵, 双缸注油泵duplex pump双缸泵, 双筒泵, 联式泵duplex air pump双缸气泵duplex double-acting pump复式双动水泵duplex geared pump双齿轮泵duplex steam pump双缸汽动泵E开头的水泵英文单词:eccentric-cylinder rotary oil pump 偏心缸回转油泵eccentric driven pump偏心泵eccentric sliding vane pump偏心滑叶泵ejector pump喷射泵ejector booster pump喷射增压泵ejector jet pump喷射器, 注射泵ejector vacuum pump喷射真空泵ejector water air pump喷水空气泵electric pump电泵electric booster pump电动增压泵electric coolant pump电动冷却液泵electrically driven pump电动泵electrically driven feed pump电动给水泵electrogenic sodium pump电致钠泵electro-ion pump蒸发离子泵electrolyte pump电解质泵electromagnetic pump电磁泵emergency pump应急泵emulsion pump乳胶输送泵engine air start pump空气起动压缩机evapor-ion pump蒸发离子泵exhaust pump排气泵external gear oil pump外啮合齿输油泵external gear rotary pump 外啮合齿轮泵external gear-type oil pump 外啮合齿轮油泵express pump高速泵extraction pump抽气泵, 排气泵, 凝结水泵extrusion pump挤压泵F开头的水泵英文单词:fan pump风扇式泵feathering pump顺浆泵feed pump进给泵; 给水泵fertilizer pump液肥泵filling pump注油泵, 灌注泵filter pump过滤泵fire pump消防泵fire extinguishing pump消防用泵fish pump鱼泵fixed pump固定泵fixed delivery pump定容量泵fixed-displacement pump 固定排量泵flexible hose pump挠性软管泵; 无脉动泵flexible-impeller pump挠性叶轮泵flow control pump可控流量泵, 计量泵foot pump脚踏泵foot-operated air pump脚踏打气筒forced lubrication pump 压力润滑泵forcing pump强制泵, 压力泵forcing and sucking pump 压气和吸气泵fore pump预抽真空泵, 前置泵forevacuum pump前级真空泵fresh feed pump进料泵fresh water pump淡水泵friction pump摩擦泵frozen-seal pump冷冻密封泵fuel pump燃油泵fuel feed pump供油泵fuel hand pump燃油手泵fuel injection pump燃料油喷射泵fuel jettison pumpfuel lift [oil] pump燃油泵fuel oil delivery pump燃油压送泵fuel oil injection pump燃油喷射泵, 高压油泵fuel oil service pump燃料油唧送泵[供料泵] fuel pressure pump燃油压力泵fuel-metering pump燃料计量泵fuel-oil transfer pump燃油输送泵, 输油泵furnace charge pump往炉内装料泵G开头的水泵英文单词:gas pump气体泵, 气泵gas ballast pump载气(真空)泵gas compression pump煤气压缩机gas oil pump气体油料泵gasoline feed pump汽油泵gasoline meter pumps汽油计量泵gasoline pressure hand pump 汽油压力手泵gathering pump辅助小水泵gear spinning pump纺丝齿轮泵gear wheel pump齿轮泵geared feed pump齿轮传动给水泵geared-on-gear pump外啮合齿轮泵齿轮泵general-purposepump通用泵geometricallysimilar pump几何相似泵getter pump离子溅射泵, 吸气泵, 抽气泵getter-ion pump吸气离子泵governor pump调速器泵grease pump黄油泵, 油脂泵, 润滑脂泵grout pump压浆泵H开头的水泵英文单词:hand pump手泵, 手压泵, 手摇泵, 手力唧筒hand air pump手动气泵, 手动气筒hand by-pass pump手增压泵hand fuel pump手摇燃料泵hand semi-rotatory pump手半转动泵heat pump热(力)泵; 蒸汽泵heat-exchanger pump热水泵heavy liquor pump浓液泵Hele-Shaw pump海伦-肖型(回转)径向柱塞泵helical gear pump斜齿齿轮泵helico-centrifugal pump螺旋离心泵helicoidal pump螺旋泵herringbone gear pump人字齿齿轮泵high density stock pump高浓浆泵high-lift pump高扬程水泵, 高压泵high-low pump高低压泵high-pressure pump高压泵high-pressure diaphragm pump高压隔膜泵high-pressure double cylinder oil pump 高压双缸油泵high-pressure manual pump手摇高压泵high-pressure oil pump高压油泵high-pressure plunger pump高压柱塞泵high-speed pump高速泵high-speed diffusion pump高速扩散泵, 高速扩散抽机high-specific speed pump高比转速泵high-vacuum pump高真空泵hoist pump起重机油泵hollow-plunger pump空心柱塞泵horizontal pump卧式泵horizontal centrifugal pump卧式离心水泵horizontal divergent-nozzle pump水平发散喷嘴扩散泵horizontal spindle pump卧式心轴泵hose pump软管泵hot oil pump热油泵hot oil centrifugal pumpHumphrey gas pump汉弗莱气爆水泵hydraulic pump水力泵, 液压泵hydraulic air pump液压抽气器hydraulic hand pump液压手泵hydraulic bottom-hole pump 水力井下泵hydraulic control pump液压控制泵hydraulic gear pump液压齿轮泵hydraulic oil pump液压油泵hydraulically driven pump 液压传动泵hydrostatic pump静液力泵Hyvac pump高真空泵I开头的水泵英语单词:ice cream pump冰淇淋(输送)泵idler gear pump内啮合齿轮泵immersed pump【航空】浸没式泵immersible pump潜水泵impeller pump叶轮泵inclined piston pump(直轴式)倾斜柱塞泵independent pump单动泵induction pump交流电磁泵injection pump喷射泵, 压注泵【刷】墨泵in-line pump管线泵in-line plunger pump直列式柱塞泵internal combustion pump内燃泵internal gear (rotary) pump内啮合齿轮泵ion-type vacuum pump离子式真空泵JK开头的水泵英语单词:Janney pump轴向回转柱塞泵jerk pump脉动作用泵, 高压燃油喷射泵jet air pump喷射泵jet-diffusion pump喷射扩散泵jury pump辅助泵, 备用泵kinetic pump动力泵L开头的水泵英语单词:Langmuir's diffusion pump朗格缪尔扩散泵, 兰米尔扩散泵laser pump激光泵; 激光抽运lead pump铅液泵lead circulating pump铅液循环泵lever action air pump杠杆抽气泵lift [suction] pump吸取泵, 吸取抽机, 提水泵light pump光泵light diffusion pump光扩散泵limed juice pump石灰混和汁泵, 加灰汁泵line pump(向)管线(中)泵送liquid pump液泵liquid-hydrogen pump液氢泵liquid ring pump液体环式泵liquid sludge pump泥浆肥料泵; 液体厩肥泵liquid oxgen pump液氧泵live hydraulic pump独立传动的液压泵lobe pump凸轮泵lobed element pump罗茨泵low head pump低压头泵, 低扬程泵low-head centrifugal pump低水头离心泵, 低扬程离心泵low-lift pump低压泵low-pressuer pump低压泵low-suction pump低压泵lube (oil) pump润滑油泵, 机油泵lubricant pump润滑唧泵, 油泵lubricating oil pump润滑油泵lubricating oil delivery pump 压油泵lubricating oil starting pump 起动机油泵lubricating oil suction pump吸油泵lubricating oil transfer pump 润滑油传送泵lye pump碱液泵M开头的水泵英语单词:magma pump糖膏泵, 泥浆泵magnetic pump磁力泵make-up pump补给[补充]水泵main circulation pump主循环泵main feed pump主给水泵main fuel pump主燃油泵, 主燃料泵main oil pump主油泵main scavenging pump主抽气泵, 主排气泵manual pump手动泵marine pump船用泵mashing pump浆料泵, 麦芽浆送料泵measuring pump计量泵, 定量泵, 量液泵mechanical pump机械泵mechanical fuel pump机械燃油泵, 薄膜式燃油泵mechanical roughening pump 机械初步抽空泵mechanical vacuum pump机械真空泵mechanically-driven pump机动泵medium lift pump中扬程泵, 中压泵membrane pump隔膜泵mercury pump水银(真空)泵mercury air pump汞(蒸气)泵mercury diffusion pump水银扩散泵mercury vacuum pump水银真空泵mercury vapor [air] pump汞汽泵, 汞汽(扩散)抽机mercury vapo(u)r diffusion pump汞汽扩散泵mercury vapor jet pump汞汽喷射泵metal(lic) diaphragm pump金属隔膜泵metal fractionary pump金属分馏真空泵meterflow pump计量流量泵metering pump计量泵microelectrolytic pump微量电解泵milk pump奶泵milk and cream pump牛奶与奶油泵milking machine pump挤奶装置泵minimal flow pump最小流量泵mixed-flow pump混流泵mixed-flow propeller pump混流式旋浆泵mixture pump混合液泵mobile diaphragm liquid manure pump 移动式薄膜厩液泵mobile engine-driven diaphragm pump 移动式机动薄膜泵mobile motor driven centrifugal pump移动式机动离心泵molasses pump糖浆泵molecular pump分子泵, 分子抽机molecular drag pump分子拖曳泵monoblock pump电动泵motor pump马达泵, 电动泵motor-driven pump电动泵motor-driven feed pump电动给水泵motor-mount pump马达泵, 电动泵mud pump抽泥泵, 污水泵mud suction pump(空气)吸泥机, 吸泥泵Muencke pump玻璃过滤泵(连在水龙头上用) multicellar pump多室泵multicylinder pump多缸泵,旋转活塞泵multi-lobe ballpump多瓣球泵multi-stage pump多级泵,多级抽机multiple centrifugal pump多级离心泵multiple impeller pump多级泵multiple piston pump多缸泵multiple vane pump复式叶轮泵multiple-piston rotary pump多活塞回转泵multiple-plunger pump多柱塞泵multiple-stage centrifugal pump多级离心泵multiple-nozzle pump多喷嘴扩散泵N开头的水泵英语单词:negative-displacement pump 负排量泵, 负排代泵normal stress pump法向应力泵nylon-roller pump尼龙滚子(旋转)泵O开头的水泵英语单词:off-gas pump抽气泵oil (air) pump油(抽气)泵oil circulating pump循环油泵oil delivery pump滑油输送泵oil diffusing pump油扩散泵oil drain pump排油泵oil ejector pump油喷射泵oil feed pump给油泵oil feed-back pump回油泵oil fuel pump燃油泵oil fuel feed pump给燃油泵oil fuel injecting pump燃油喷射泵oil gear pump回转活塞泵oil hand pump手压油泵oil hydraulic pump油压泵oil less pump无油泵oil pressure pump油压力泵oil rotary pump油旋转泵, 油回转泵oil scavenge [suction] pump吸油泵oil transfer pump输油泵oil vacuum pump油真空泵oil vapor pump喷油泵, 油蒸气泵oil-driven pump油动泵oil-line pump输油泵, 送油泵oil-refinery pump石油蒸馏泵oil-sealed rotary pump油封机械真空泵oil-well pump抽油泵one-shot pump单塞泵, 有一个冷活塞的油泵optical pump光泵oscillating pump摆动泵oscillating plunger pump摆动柱塞泵P开头的水泵英语单词:paddle pump浆式泵petrol pump汽油泵pharyngeal pump咽泵pickle pump盐水(注射)泵piston rotary pump活塞回转泵piston valve pump活塞阀泵pistonless steam pump蒸气抽水机piston-type pump活塞泵piston-type rotary pump活塞式回转泵piston-type spray pump活塞式喷雾泵pitcher pump浅井手摇泵pneumatic pump空气泵, 气压泵pneumatic diaphragm milk pump气动隔膜式牛奶泵polymer pump聚合泵portable pump轻便泵portable electric pump手提式电动泵port plate axial piston pump配流盘式轴向柱塞泵positive-displacement pump正排量泵, 容积式泵, 正位移泵positive-displacement type fuel pump 正排量式燃料泵power pump动力泵power steering pump动力转向泵pregreasing pump预润滑泵pressure pump压力泵pressure-compensated pump压力补偿式泵pressure gear pump压力齿轮泵pressure oil pump压油泵process pump作用泵, 运行泵propeller pump旋浆泵(流体流动与旋浆轴平行), 轴流泵, 离心泵proportioning pump配比泵, 比例泵pulp pump废粕泵pulsating steam pump蒸汽吸水机pulse pump脉冲泵pulse-free pump无脉冲泵pusher pump压气泵pulseless pump无脉动泵R开头的水泵英文词汇:radial pump径向活塞泵radial plunger oil pump旋转往复油泵, 旋转柱塞油泵ram-(type) pump柱塞泵rapid approach pump快动泵raw oil pump(管路和裂化设备的)原料油泵reaction water pump反动式[反作用式, 反击式]水泵reciprocating pump循环泵reciprocating air pump往复式空气压缩泵reciprocating diaphragmpump往复式隔膜泵reciprocatingfeed pump往复式加料泵reciprocating steam pump往复式蒸汽泵reciprocating vacuum pump往复式真空泵recycle pump循环泵recycle liquid pump循环液泵reflux pump回流泵(抽回流液用) regenerative pump再生泵, 涡流泵remote-controlled pump遥控泵reserve(d) pump备用泵return pump排气泵; 抽气泵reversible pump双向旋转泵reversing pump反向泵ring section feed pump环段式给水泵ring-shaped gear pump for lubricant 环形齿轮润滑泵rod(liner) pump杆式泵roller pump滚子泵roller impeller rotary pump滚子叶轮泵roller vane pump滚子叶片泵rolling piston radial pump旋转柱塞径向泵roll-type rotary sprayer pump滚柱式旋转喷雾泵Roots blower pump罗茨增压泵, 机械增压泵Roots high vacuum pump罗茨高真空泵rotary pump旋转式泵rotary abutment pump旋转隔板泵rotary air pump转式打气泵rotary block radial pump旋转缸体径向泵rotary circulating pump旋转式循环水泵rotary displacement pump回转泵, 旋转排量泵rotary dry vacuum pump旋转真空干燥泵rotary elliptical piston pump旋转式椭圆活塞泵rotary fuel-feed pump转子式输油泵rotary gas ballast pump回转载气泵rotary gear pump旋转齿轮泵rotary mercury pump旋转汞泵rotary motor pump回转式马达泵rotary oil pump回转油真空泵, 旋转式油泵rotary oil sealed mechanical pump 旋转式油封机械泵rotary oscillating pump回旋振荡泵rotary semi-displacement-type pump 旋转式半排量泵rotary type circulating water pump 旋转式循环水泵rotary type fuel feed pump旋转式供油泵rotary vacuum pump旋转真空泵rotary vane mixing pump回旋叶片混和泵rotary vane type pump回旋叶片式泵rotary-piston pump旋转式活塞泵rotary-plunger pump旋转柱塞泵rotating-field electromagnetic pump旋转(磁)场电磁泵rotopiston pump旋转活塞泵rotor pump旋转泵roughing pump低真空泵rubber hand pump橡皮手揿泵S开头的水泵英文词汇:salivary pump唾泵, 涎泵salvage pump应急排水泵sanitary pump卫生泵scavenge oil pump废油泵scavenger pump扫线用泵scavenging pump清洗泵, 换气泵, 回油泵, 扫气泵screw pump螺杆泵, 螺旋泵screw impeller pump螺旋浆式泵scum pump吸泥泵, 污水泵sea water pump海水泵seated valve pump座阀配流泵, 单向阀配流泵secondary lubricating pump第二滑油泵, 从动滑油泵, 惰行泵secondary scavenging pump从动排空泵, 从动回油泵, 第二回油泵self-fractionating pump自馏真空泵, 自行分馏泵, 净化泵self priming pump自吸泵, 自引泵(启动时不用灌水) self-sucking pump自吸泵semi-rotary pump半回转泵, 叶轮泵sewage ejector submersible pump 喷射式潜入污水泵shaft-driven oil pump主轴(驱动的)油泵shell pump壳式泵, 出泥泵, 泥沙泵shuttle-block oil pump有导板的旋转油泵sickle pump叶轮泵, 镰式泵, 活翼式泵simplex pump单缸泵single pump单流向的泵single valve knapsack pump (喷雾器的)背负式单阀泵single-acting hand pump单作用手摇泵single-cylinder pump单缸泵single-entry centrifugal pump单一入口离心泵single-impeller pump单叶泵single-stage pump单级泵single-suction centrifugal pump 单进口[单吸式]离心泵single-suction volute pump单级离心泵sinking pump沉没式泵; 凿井水泵; 潜水泵sirup pump糖浆泵sleeve pump套筒活塞泵slide valve pump滑阀泵slide valve reciprocating pump滑阀往复泵slide-vane type rotary pump刮板式旋转泵sliding vane pump滑片泵slime pump矿泥泵, 泥浆泵slippage pump补油泵slipper pump(径向柱塞泵的)滑履泵sludge pump污泥泵sludge and thick liquid pump泥浆和浓液泵slurry pump淤浆泵; 料浆泵slurry agitator pump混浆混合泵slurry snake pump蛇形泥浆泵slush pump污水泵sodium pump钠泵sodium-potassium exchange pump 钠钾交换泵solid pump固体吹散泵solution feed pump供液泵sorption pump吸气泵spinning pump纺丝泵, 抽丝泵spiral pump螺旋泵, 离心泵split flow pump双联泵spool valve pump滑阀配流的泵spray pump喷雾机, 喷淋系统泵spur-gear pump直齿齿轮泵sputter-ion pump离子溅射泵squeeze pump挤压泵squeeze-hose pump挤压软管泵squirtpump喷射泵stage pump多级泵standarizing pump标准化泵(例如泵入奶油使牛奶含脂量标准化) stand-by pump应急泵, 备用泵starting lube oil pump起动润滑油泵start-up feed pump起动给水泵stationary motor piston pump固定式动力活塞泵steam pump蒸汽泵steam feed pump汽动给水泵steam jet air pump蒸汽泵, 汽轮泵steam jet vacuum pump蒸汽喷射真空泵stoneware pump陶制泵storage pump蓄水泵straight spur gear-on-gear pump圆柱直齿[外啮合]齿轮泵straightway pump直流泵stuff pump纸料泵subclypeal pump唇基下泵sucker rod pump杆式泵sucking pump抽气泵suction pump吸水泵, 吸入泵, 抽吸泵; 抽气泵; 真空泵sugar juice pump糖汁泵sump pump井底水窝水泵, 油池泵supply pump供给泵surge pump膜式泵, 隔膜泵swashplate axial piston pump斜盘式轴向柱塞泵sweet water pump甜水泵swinging vane pump转叶泵syrup pump糖浆泵T开头的水泵英文词汇:tail pump残液泵tan liquor pump鞣液泵tandem pump双朕泵tank-cleaning pump油舱清洗泵tank truck pump油槽汽车泵test pump试验泵thermo-electro-magnetic pump热电磁泵three-screw oil pump三螺旋浆油泵three-throw pump三冲程泵titanium pump钛泵titanium sublimation pump钛升华泵transfer pump传送泵, 输送泵travelling-field electromagnetic pump行移场电磁泵(具有行波电磁场的泵)triple pump三联泵triple-barrel pump三联式筒泵(三个泵筒与一个吸液管相连, 由三拐曲轴驱动三个活塞产生均匀液流) triplet piston pump三联式活塞泵triplex pump三缸泵triplex reciprocating pump三缸往复泵trochoid pump余摆线(齿轮)泵tubing pump管式抽油泵turbine pump涡轮抽水机, 涡轮泵turbo molecular pump涡轮高真空泵, 涡轮分子泵, 汽轮分子泵turbulence pump涡流泵turret type pump立式泵twin pump双缸泵twin fuel pump双燃料泵twin-diaphragm pump双隔膜泵twin simplex pump (=twin single pump)双单动泵two-speed[`tU:spi:d][-stage] pump 两级泵two-stage air pump双级气泵two-stage centrifugal pump两级离心泵two-stage diffusion pump两级扩散泵two-stage vacuum pump二级真空泵two-way pump双向泵, 可逆泵two-way flow pump双联泵tyre [tire] pump轮胎打气泵UV开头的水泵英文词汇:unbalanced fuel pump不平衡供油的燃料泵uncompensated pump无补偿的泵underflow pump浓浆泵, 低流泵unit pump单位泵, 电动泵vacuum air pump真空泵vacion pump钛泵vacuum and pressure air pump 抽空压气两用泵vacuum booster pump预抽真空泵vane pump叶轮泵, 叶片泵vane motor pump叶轮电动泵vapour pump蒸汽泵, 扩散泵, 冷凝泵variable pump变量泵variable capacity pump可调流量泵, 变(流)量泵variable delivery pump变量输送泵variable stroke pump变量泵variable stroke injection pump变冲程喷油泵vertical pump立式泵volumetric type diaphragm pump 容量型隔膜泵volute pump蜗形管式离心泵, 蜗囊泵vortex pump涡动泵W开头的水泵英文词汇:washer [washout] pump冲洗泵waste water disposal pump污水泵water pump水泵water circulating pump循环水泵water ejector pump喷水抽气泵(一种机械真空泵) water jet pump喷射泵water jet air pump喷水空气泵water ring pump水环泵water service pump配水泵water supply pump供水泵, 冷水泵Waterbury pump沃特伯里轴向柱塞泵waterproof pump水泵waveguide pump波导泵wear pump耐磨泵(有磨损作用的物料的吸料泵) Weir pump威尔泵(蒸汽直动泵的一种)well pump井泵Wesco pump摩擦泵, 粘性泵wet air pump湿气泵wet vacuum pump湿真空泵wheel pump齿轮泵white water pump白水泵windmill pump风车泵wing pump轮叶泵, 叶式唧筒wobble plate pump 摆板泵以下无正文仅供个人用于学习、研究;不得用于商业用途。
离心泵毕业论文中英文资料对照外文翻译文献

离心泵毕业论文中英文资料对照外文翻译文献离心泵中英文资料对照外文翻译文献文献名称(外文)CENTRIFUGAL PUMPS IN THE CHEMICAL INDUSTRYAbstract : A centrifugal pump converts the input power to kinetic energy in the liquid by accelerating the liquid by a revolving device - an impeller. The most common type is the volute pump. Fluid enters the pump through the eye of the impeller which rotates at high speed. The fluid is accelerated radially outward from the pump chasing. A vacuum is created at the impellers eye that continuously draws more fluid into the pump . This article stresses on a series of centrifugal pumps,From a brief introduction to the principles.Keywords: centrifugal pump ,Introduction ,Working principle , Cavitation ,Mechanism of Cavitation ,Solution and Remedies1. IntroductionPump ,device used to raise ,transfer ,or compress liquids and gases .Four general classes of pumps for liquids are described below .In all of them ,steps are taken to prevent cavitation (the formation of a vacuum) ,which would reduce the flow and damage the structure of the pump .Pumps used for gases and vapors are usually known as compressors .The study of fluids in motion is called fluid dynamics.Water pump ,device for moving water from one location to another ,using tubes or other machinery .Water pumps operate under pressures ranging from a fraction of a pound to more than 10,000 pounds per square inch .Everyday examples of water pumps range from small electric pumps that circulate and aerate water in aquariums and fountains to sump pumps that remove water from beneath the foundations of homes .One type of modern pumps used to move water is the centrifugal pump .Early version of the centrifugal pump ,the screw pump ,consists of a corkscrew-shaped mechanism in a pipethat ,when rotated ,pulls water upward .Screw pumps are often used in waste-water treatment plants because they can move large amounts of water without becoming clogged with debris .In the ancient Middle East the need for irrigation of farmland was a strong inducement to develop a water pump .Early pumps in this region were simple devices for lifting buckets of water from a source to a container or a trench .Greek mathematician and inventor Archimedes is thought to have devised the first screw pump in the third century BC .Later Greek inventor Ctesibius develop the first lift pump .During the late 17th and early 18th Centuries AD ,British engineer Thomas Savery ,French physicist Denis Papin ,And British blacksmith and inventor Thomas Newcomen contributed to the development of a water pump that used steam to power the pump’ piston .The steam-powered water pump’s first wide use was in pumping water out of mines .Modern-day examples of centrifugal pumps are those used at the Grand Coulee Dam on the Columbia River .This pump system has the potential to irrigate over one million acres of land .Also known as rotary pumps ,centrifugal pumps have a rotating impeller ,also known as a blade ,that is immersed in the liquid .Liquid enters the pump near the axis of the impeller ,and the rotating impeller sweeps the liquid out toward the ends of the impeller blades at high pressure .The impeller also gives the liquid a relatively high velocity that can be converted into pressure in a stationary part of the pump ,known as the diffuser .In high-pressure pumps ,a number of impeller may be used in series ,and the diffusers following each impeller may contain guide vanes to gradually reduce the liquid velocity .For lower-pressure pumps ,the diffuser is generally a spiral passage ,known as a volute ,with its cross-sectional area increasing gradually to reduce the velocity efficiently .The impeller must be primed before it can begin operation ,that is ,the impeller must be surrounded by liquid when the pump is started .This can be done by placing a check valve in the suction line ,which holds the liquid in the pump when the impeller is not rotating .If this valve leaks ,the pump may need to be primed by the introduction of liquid from an outside source such as the discharge reservoir .A centrifugal pump generally has a valve in the discharge line to control the flow and pressure .For low flows and high pressures ,the action of the impeller is largely radial .For higher flows and lower discharge pressure ,the direction of the flow within the pump is more nearly parallel to the axis of the shaft ,and the pump is said to have an axial flow .The impeller in this case acts as a propeller .The transition from one set of floe conditions to the other is gradual ,and for intermediate condition , the device is called a mixed-flow pump .2.The Centrifugal PumpThe centrifugal pump is by far the most widely used type in the chemical and petroleum industries .It will pump liquids with very wide ranging properties and suspensions with a highsolids content including ,for example ,cement slurries ,and may be constructed from a very wide rang of corrosion resistant materials .The whole pump casing may be constructed from plastic such as polypropylene or it may be fitted with a corrosion-resistant lining .Because it operates at high speed ,it may be directly coupled to an electric motor and it will give a high flow rate for its size .In this type of pump ,the fluid is fed to the centre of a rotating impeller and is thrown outward by centrifugal action .As a result of the high speed of rotation the liquid acquires a high kinetic energy and the pressure difference between the suction and delivery sides arises from the conversion of kinetic energy into pressure energy .The impeller consists of a series of curved vanes so shaped that the flow within the pump is as smooth as possible .The greater the number of vanes on the impeller ,the greater is the control over the direction of the liquid and hence the smaller are the losses due to turbulence and circulation between the vanes .In the open impeller ,the vanes are fixed to a central hub ,whereas in the closed type the vanes are held between two supporting plates and leakage across the impeller is reduced .As will be seen later ,the angle of the tips of the blades very largely determines the operating characteristics of the pump .The liquid enters the casing of the pump,normally in an axial direction,and is picked up by the vanes of the impeller.In the simple type of centrifugal pump,the liquid discharges into a volute,a chamber of gradually increasing cross—section with a tangential outlet.A volute type of pump is shown in Fig.(a).In the turbine pump[-Fig.(b)]the liquid flows from the moving vanes of the impeller through a series of fixed vanes forming a diffusion ring.This gives a more gradual change in direction to the fluid and more efficient conversion of kinetic energy into pressure energy than is obtained with the volute type.The angle of the leading edge of the fixed vanes should be such that the fluid is received without shock.The liquids flows along the surface of the impeller vane with a certain velocity whilst the tip of the vane is moving relative to the casing of the pump.The direction of motion of the liquid relative to the pump casing--and the required angle of the fixed vanes—is found by compounding these two velocities.In Fig.c,c.v u is the velocity of the liquid relative to the vane and t u is the tangential velocity of the tip of the vane ;compounding these two velocities gives the resultant velocity 2u of the liquid .It is apparent ,therefore ,that the required vane angle in the diffuser is dependent on the throughput ,the speed of rotation ,and the angle of the impeller blades .The pump will therefore operate at maximum efficiency only over a narrow range of conditions .Virtual head of a centrifugal pumpThe maximum pressure is developed when the whole of the excess kinetic energy of the fluid is converted into pressure energy. As indicated below .the head is proportional to the square of the radius and to the speed ,and is of the order of 60m for a single —stage centrifugal pump ;for higher pressures ,multistage pumps must be used .Consider the liquid which is rotating at a distance of between r and r+dr from the centre of the pump(Fig .d).dThe mass of this element of fluid dm is given by 2πrdrdρ,where ρ is the density of the fluidand 6 is the width of the element of fluid 。
中英文对照 水泵英语 外贸英语 打印
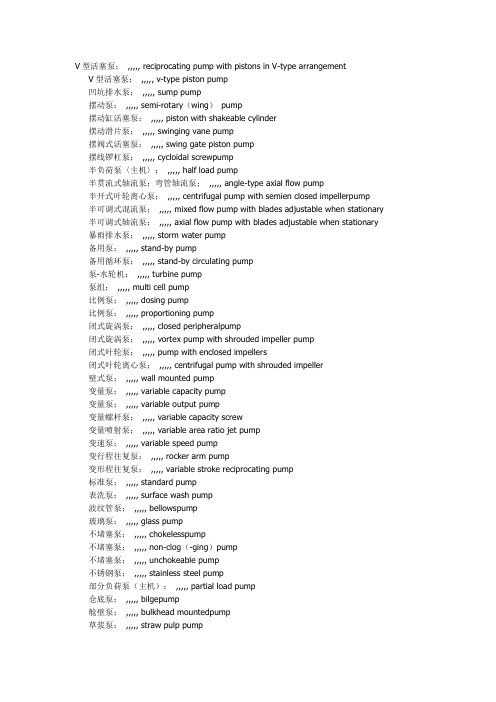
V型活塞泵;,,,,, reciprocating pump with pistons in V-type arrangement V型活塞泵;,,,,, v-type piston pump凹坑排水泵;,,,,, sump pump摆动泵;,,,,, semi-rotary(wing)pump摆动缸活塞泵;,,,,, piston with shakeable cylinder摆动滑片泵;,,,,, swinging vane pump摆阀式活塞泵;,,,,, swing gate piston pump摆线锣杠泵;,,,,, cycloidal screwpump半负荷泵〈主机〉;,,,,, half load pump半贯流式轴流泵;弯管轴流泵;,,,,, angle-type axial flow pump半开式叶轮离心泵;,,,,, centrifugal pump with semien closed impellerpump 半可调式混流泵;,,,,, mixed flow pump with blades adjustable when stationary 半可调式轴流泵;,,,,, axial flow pump with blades adjustable when stationary 暴雨排水泵;,,,,, storm water pump备用泵;,,,,, stand-by pump备用循环泵;,,,,, stand-by circulating pump泵-水轮机;,,,,, turbine pump泵组;,,,,, multi cell pump比例泵;,,,,, dosing pump比例泵;,,,,, proportioning pump闭式旋涡泵;,,,,, closed peripheralpump闭式旋涡泵;,,,,, vortex pump with shrouded impeller pump闭式叶轮泵;,,,,, pump with enclosed impellers闭式叶轮离心泵;,,,,, centrifugal pump with shrouded impeller壁式泵;,,,,, wall mounted pump变量泵;,,,,, variable capacity pump变量泵;,,,,, variable output pump变量螺杆泵;,,,,, variable capacity screw变量喷射泵;,,,,, variable area ratio jet pump变速泵;,,,,, variable speed pump变行程往复泵;,,,,, rocker arm pump变形程往复泵;,,,,, variable stroke reciprocating pump标准泵;,,,,, standard pump表洗泵;,,,,, surface wash pump波纹管泵;,,,,, bellowspump玻璃泵;,,,,, glass pump不堵塞泵;,,,,, chokelesspump不堵塞泵;,,,,, non-clog(-ging)pump不堵塞泵;,,,,, unchokeable pump不锈钢泵;,,,,, stainless steel pump部分负荷泵(主机);,,,,, partial load pump仓底泵;,,,,, bilgepump舱壁泵;,,,,, bulkhead mountedpump草浆泵;,,,,, straw pulp pump侧流道泵;,,,,, side channel pump侧吸泵;,,,,, side suction pump差动活塞泵;,,,,, differential pistonpump柴油机驱动泵;,,,,, dieaelpump产品泵;物料泵;,,,,, product pump长喉管喷射泵;,,,,, jet pump with long Venturi tube长轴深井泵(美),,,,, multistage vertical turbine pump长轴深井泵;,,,,, borehole shaft driven(centrifugal)pump超高压泵;,,,,, super-pressure pump超高真空泵;,,,,, ultrahigh vacuum pump超汽蚀泵;,,,,, super cavitation pump超声速泵;,,,,, supersonic pump沉积物泵;,,,,, sediment pump沉积物泵;,,,,, thick sludge pump衬胶泵;,,,,, rubber lined pump衬胶真空泵;,,,,, rubber lined vaccum衬青铜泵;,,,,, bronze fittedpump衬软胶泵;,,,,, soft rubber lined pump衬塑料泵;,,,,, plastic lined pump衬硬胶泵;,,,,, dbonitepump衬硬胶泵;,,,,, hard rubber lined pump成品泵;,,,,, discharge pump成品泵;,,,,, final productpump齿轮泵;,,,,, gearpump齿轮比例泵;,,,,, adjustable discharge gear pump齿轮比例泵;,,,,, gear dosingpump齿轮传动泵;,,,,, gearedpump冲洗泵;,,,,, flushingpump除氧化皮泵;,,,,, descalingpump除氧器供给泵;,,,,, deaerator liftpump除氧器循环泵;,,,,, deaerator recirculatingpump传导泵;,,,,, conductionpump船坞泵;,,,,, dock pump船用泵;,,,,, marine pump船用泵;,,,,, ships pump磁泵,磁感应驱动泵;,,,,, megnectic pump磁力联轴节齿轮泵;,,,,, magnectically coupled gear pump磁蠕动泵;,,,,, megnectic fluid actuating pump次摆线螺杆泵;,,,,, trochoid screw pump次摆线转子泵;,,,,, trochoid rotor pump粗糖泵;原液泵;,,,,, raw liquor pump带隔片的偏心转子泵;,,,,, eccentric rotary pump with dividing platepump 带柔性环的偏心滚柱泵;,,,,, eccentric rotary pump with elastic ringpump 单杠曲柄泵(美);,,,,, single (power)pump单杠曲柄泵(美);,,,,, single power pump单杠曲柄泵;,,,,, simplex power pump单杠往复泵;,,,,, single cylinder (reciprocating)pump单杠蒸汽直动泵(美);,,,,, single (steam)pump单杠蒸汽直动泵(美);,,,,, single steam pump单杠蒸汽直动泵;,,,,, simplex steam pump单列式柱塞泵;,,,,, in-line pistonpump单流道叶轮泵;,,,,, single channel impeller pump单螺杆泵;,,,,, helical rotor pump单螺杆泵;,,,,, mono pump单体泵;,,,,, close coupledpump单体斗式泵;,,,,, monoblock scoop pump单凸轮泵;,,,,, single lobe pump单吸泵;,,,,, single entry pump单吸泵;,,,,, single stage pump单吸泵;,,,,, single suction pump单向活塞泵;,,,,, reciprocating pump with unidirectional piston 单叶轮多级泵;,,,,, multistagepump with single impeller单柱塞泵;,,,,, single plunger pump单作用滑片泵;,,,,, single action vane pump单作用滑片泵;,,,,, single cell vane pump单作用活塞泵;,,,,, single action piston pump弹性刮片泵;,,,,, flexible vanepump淡水泵;,,,,, fresh waterpump导流壳式多级泵;,,,,, pump with bowl-type vaned casing导页泵;,,,,, diffuserpump灯笼架固定泵;,,,,, lantern mounted pump灯笼架支承泵;,,,,, lantern based pump灯笼架支承泵;,,,,, skirt mounted pump低比转速泵;,,,,, low specific speed pump低负荷泵(主机);,,,,, smalll load pump低速泵;,,,,, low-speed pump低压泵;,,,,, low pressure pump低噪音泵;,,,,, low sound level pump底脚固定泵;,,,,, foot mountedpump底料泵,塔底液泵;,,,,, bottomspump底吸泵;,,,,, bottom inletpump底吸泵;,,,,, bottom suctionpump地区取热泵;分区供暖泵;,,,,, district heating pump地下室排水泵;,,,,, cellar drainagepump地下水排水泵;,,,,, de-wateringpump地下水排水泵;,,,,, groundwater drainage pump水泵英语2电厂泵;,,,,, power station pump电磁泵;,,,,, electromagneticpump电磁隔膜泵;,,,,, electromagnetic diaphragmpump电磁计量泵;,,,,, electromagnetic meteringpump电磁偶合泵;,,,,, electromagnetically coupledpump电磁喷射泵;,,,,, electro-magnetic jetpump电磁驱动泵;,,,,, pump with cyclic electromagnetic drive电磁式比例泵;,,,,, electromagnetic proportioningpump电动泵;,,,,, electrically drivenpump电动泵;,,,,, motor driven pump电动冲脉;,,,,, electroimpuisepump电动给水泵;,,,,, electrically driven feedpump电动潜水泵;,,,,, electro-submersiblepump电动潜水排水泵;,,,,, electro-submersible drainagepump电离真空泵;,,,,, ionization vaccum pump吊泵;,,,,, sinking pump顶端吸入泵;,,,,, top inlet pump顶端吸入泵;,,,,, top suction pump定压泵;,,,,, constant pressurepump动力往复泵;曲柄泵;,,,,, power pump斗轮水车;戽斗水车;,,,,, wheel and bucket pump斗式泵;,,,,, scoop pump斗式泵;皮托泵;,,,,, pitot pump端部密封式活塞泵;,,,,, end-packed type pistonpump短喉管喷射泵;,,,,, jet pump with short Venturi tube短棉绒泵;,,,,, linters pump对向活塞泵;,,,,, reciprocating pump with counterrunning piston 对置活塞泵;,,,,, oppesed piston pump多齿轮泵;,,,,, multiple gearpump多出口泵;,,,,, multi dischargepump多缸曲柄泵;,,,,, multi throw crankpump多缸曲柄泵;,,,,, multiplexpump多缸曲柄泵;,,,,, multiplexpump多缸往复泵;,,,,, multi cylinder(reciprocating)pump多缸往复泵;,,,,, multi throw(reciprocating)pump多级泵;,,,,, multistagepump多级喷射泵;,,,,, multistage jet pump多流道叶轮泵;,,,,, multi channel impellerpump多流式泵;,,,,, multi flowpump多螺杆泵;,,,,, multi screwpump多喷嘴喷射泵;,,,,, multinozzle jetpump多凸轮泵;,,,,, multi lobepump多用泵;,,,,, multipurposepump多柱塞泵;,,,,, multi plungerpump阀板式活塞泵(美);,,,,, valve plate type piston pump阀板式活塞泵;,,,,, valve deck plate type piston pump阀室式活塞泵;,,,,, valve box type piston pump阀箱式活塞泵(美);,,,,, turret type piston pump阀形活塞泵;,,,,, valve type piston pump法兰式电动机驱动泵;,,,,, flanged motor drivenpump法兰悬臂泵;,,,,, flange mounteapump法兰悬臂泵;,,,,, flanged overhungpump反应堆泵;,,,,, reactor pump方形螺杆泵;,,,,, screw pump with square thread纺丝泵;,,,,, viscose spinning pump非接触齿轮泵;,,,,, contactless gearpump非密闭式螺杆泵;,,,,, non-hermetic screw pump废纸浆泵;,,,,, waste paper pulp pump分段泵;径向剖分泵;,,,,, radially split pump分段式多级泵(美),,,,, multistage turbine pump分段式多级泵;,,,,, multistage segmental type pump分段式多级泵;,,,,, segmental type pump分段式多级泵;,,,,, stage casing pump分置阀式活塞泵;,,,,, side pot type piston pump分置阀室式活塞泵;,,,,, separate valve box type piston pump 分子泵;,,,,, molecular pump分子空气泵;,,,,, molecular air pump分子空气泵;,,,,, molecular drag pump粪便泵;,,,,, fecalpump粪便泵;分流泵;,,,,, diverter pump风车驱动泵;,,,,, windmill (driven)pump风动泵;,,,,, pneumatic pump风动活塞泵;,,,,, air-powered piston pump弗里昂泵;,,,,, freonpump伏辊断头纸浆泵;,,,,, couch breakpump浮船坞泵;,,,,, floating dockpump浮动泵;,,,,, floatingpump辅泵;辅助泵;,,,,, auxiliary pump辅扫仓泵;辅清仓泵;,,,,, auxiliary stripping pump腐泥引进泵;接种污泥泵;,,,,, seed(ing)sludge pump附属泵;,,,,, attached pump干船坞泵;,,,,, drg dock pump干坑泵;,,,,, dry pit pump干坑泵;,,,,, dry sump pump干式真空泵;,,,,, dry vacuum pump干式自吸泵;,,,,, dry self-priming pump杆式泵;,,,,, rocking arm pump杆式泵;,,,,, walking beam pump感应泵;,,,,, inductionpump缸体旋转式径向活塞泵;,,,,, rotary-block radial pump高比转速泵;,,,,, higher specific speed pump高峰负荷泵;,,,,, peak load pump高速泵;,,,,, high speed pump高速离心泵;,,,,, high speed centrifugal pump高速叶片泵;,,,,, high speed rotodynamic pump高速叶片泵;,,,,, high speed turbo pump高温泵;,,,,, high temperature pump高压泵;,,,,, high pressure pump高压加热器疏水泵;,,,,, high pressure heater drains pump 隔膜泵;,,,,, diaphragmpump隔膜泵;,,,,, disc pump隔膜活塞泵;,,,,, diaphragm pistonpump隔膜式计量泵;,,,,, diaphragm meteringpump隔膜柱塞泵;,,,,, diaphragm plungerpump给料泵;,,,,, chargepump给料泵;,,,,, feedpump工程用泵;,,,,, building site pump工程用泵;,,,,, contractor’spump供水泵;,,,,, water conveying pump供水泵;,,,,, water supply pump汞(蒸汽)泵;,,,,, mercury air pump汞扩散泵;,,,,, mercury diffusion pump汞喷射泵;,,,,, mercury ejector pump汞蒸汽喷射泵;,,,,, mercury vapour jet pump汞蒸汽喷射泵;,,,,, mercury(vapour)jet pump固定刚体泵;,,,,, pump with nonrotating cylinder固定式泵;,,,,, stationary pump固体输送泵;,,,,, pump for water -borne solids固体输送泵;,,,,, solid (handling)pump管道泵;,,,,, pipeline mounted pump管道屏蔽泵;,,,,, pipeline canned motor pump管流泵;直管轴流泵;,,,,, tubular type axial flow pump管式深井泵;,,,,, tubewell pump管网泵;,,,,, pump for pipe system惯性脉冲泵;,,,,, inertia impulsepump惯性无曲柄泵;,,,,, inertia crankiesspump灌溉泵;,,,,, irrigation pump罐柜抽泄泵;,,,,, tank drainage pump滚轮泵;,,,,, roller pump锅炉给水泵;,,,,, BFW pump锅炉给水泵;,,,,, boiler feedpump锅炉回水循环泵;,,,,, boiler return circulatingpump锅炉酸洗泵;,,,,, pump for acid washing of boiler过滤泵;,,,,, filterpump海水泵;,,,,, sea water pump焊接管道泵;,,,,, pipeline mounted pump with welded connections 航空用泵;,,,,, aviation pump合金泵;,,,,, alloy pump合金钢泵;,,,,, alloy steel pump恒定轴向间隙齿轮泵;,,,,, fixed axial clearance gearpump恒速度;,,,,, constant speedpump横倾平衡泵;,,,,, heeling pump滑阀式回转活塞泵;,,,,, rotaru piston pump with slide gate !pump 滑阀型转子泵;,,,,, eccentric rotary pump with sliding sleeve滑履式泵;,,,,, slipper pump滑片泵;,,,,, sliding vane pump滑片真空泵;,,,,, sliding vane vacuum pump滑油泵;,,,,, lubricating oil pump滑脂泵;,,,,, grease pump化工用泵;,,,,, chemicalpump化学纸浆泵;,,,,, chemical pulppump化学纸浆泵;,,,,, chemical stockpump环壳泵;,,,,, annular casing pump环壳泵;,,,,, circular casingpump环氧树脂泵;,,,,, epoxide resinpump灰渣泵;,,,,, ash pump回流泵;,,,,, reflux pump回流泵;,,,,, top return pump回流污泥泵;,,,,, return sludge pump回水泵;,,,,, backwaterpump回转泵;,,,,, rotary pump回转滑阀活塞泵;,,,,, piston pump with rotary gate回转滑片泵;,,,,, rolling vane pump回转容积泵;,,,,, positive rotary pump回转式滑片泵;,,,,, rotary vane pump回转式滑片泵;,,,,, rotating vane pump回转式活塞泵;,,,,, rotary piston pump回转式计量泵;,,,,, rotary meterring pump回转式容积泵;,,,,, rotary-displacement pump回转式叶片真空泵;,,,,, rotary vane vaccum pump回转式真空泵;,,,,, rotary vaccum pump回转式柱塞泵;,,,,, rotary plunger pump混合型自吸泵;,,,,, self-priming pump with recirculation混料泵;,,,,, contactor pump水泵英语3混料泵;,,,,, mixing pump混流泵;,,,,, mixed flow pump混流泵;,,,,, semi-axial flow pump混凝土泵;,,,,, cement grout pump混凝土泵;,,,,, cementationpump混凝土泵;,,,,, concretepump混凝土涡壳泵;,,,,, concrete volutepump活塞泵;,,,,, piston pump活塞隔膜泵;,,,,, piston diaphragm pump活塞计量泵;,,,,, piston metering pump活性污泥泵,,,,, activated sludge pump活性污泥泵;,,,,, biological sludgepump货油泵;,,,,, cargo oilpump机械密封泵;,,,,, pump with mechanical seal机械木浆泵;,,,,, groundwood stock pump机械木浆泵;,,,,, mechanical wood pulp pump机械驱动泵;,,,,, mechanically driven pump基本负荷泵;,,,,, base loadpump基坑排水泵;,,,,, trench pump计量泵;,,,,, metering pump加硼泵;,,,,, boron additionpump加热器给水泵;,,,,, heater lift pump加油站泵;,,,,, petrol station pump加油站泵;配料泵;,,,,, dispensing pump夹装泵;,,,,, bung mountedpump家用供水泵;,,,,, domestic water supply pump甲板泵;,,,,, board pump甲板泵;,,,,, deckpump甲板冲洗泵;,,,,, deck washpump尖舱泵;,,,,, forepeakpump减摇泵;,,,,, anti-roll pump渐开线摆线螺杆泵;,,,,, involute cycloidal screw pump 浆液泵;,,,,, slurry pump浆液泵;污泥液泵;,,,,, sludge liquor pump脚踏泵;,,,,, footpump铰接盖式泵;,,,,, hinged cover pump铰链滑片泵;,,,,, articulated vane pump接力泵;,,,,, boostpump接力泵;,,,,, feederpump径流泵;,,,,, radial flow (centrifugal)pump径向活塞泵;,,,,, radial piston pump径向活塞泵;,,,,, radial plunger pump径向旋转活塞泵;,,,,, rolling piston radial pump救助泵;,,,,, salvage pump矩形螺杆泵;,,,,, square thread screw pump开式旋涡泵;,,,,, vortex pump with open impeller开式叶轮离心泵;,,,,, centrifugal pump with open impellerpump铠装泵;,,,,, armoured pump可变磁阻电动机泵;,,,,, variable reluctance motor pump可调隔膜泵;,,,,, adjustable diaphragm pump可调式混流泵;,,,,, mixed flow pump with adjustable or variable pitch blades可调式混流泵;,,,,, semi-axial flow pump with adjustable or variable pitch blades 可调式轴流泵;,,,,, axial flow pump with adjustable pitch blades可调式轴流泵;,,,,, propeller pump with adjustable or variable pitch blades可调叶片离心泵;,,,,, pivotal vane centrifugal pump可逆泵;,,,,, reversible pump可逆式螺杆泵;,,,,, reversible screw pump可逆叶片轴流泵;,,,,, axial flowpump with reversible blades可逆叶片轴流泵;,,,,, propeller pump with reversible blades ,可携式屏蔽电泵;,,,,, portable canned motor pump可移式泵;,,,,, mobile pump可移式泵;,,,,, portable pump可移式泵;,,,,, transportable pump可移式消防用泵;,,,,, portable fire (fighting)pump控制水位用泵;,,,,, level control库存泵;备用泵;,,,,, spare pump矿井泵;,,,,, pit pump矿井泵;,,,,, shaft pump矿井工作面泵;,,,,, coal facepump矿井排水泵;,,,,, mine drainage pump矿井筒袋泵;,,,,, pit barrel pump矿用泵;,,,,, mine pump扩散真空泵;,,,,, diffusion vaccumpump冷冻装置用无轴封泵;,,,,, glandless pump for refrigerating installation冷剂泵;,,,,, collantpump冷剂泵;,,,,, coolantpump冷剂泵;,,,,, cooling mediumpump冷煤泵;,,,,, refrigerating medium pump冷凝泵;,,,,, condensate extractionpump冷凝泵;,,,,, condensatepump冷凝泵;,,,,, hot-well pump冷凝泵;热井泵;冷凝水箱泵;,,,,, hot well pump冷却乳剂泵;肥皂液泵;,,,,, sudspump冷却水泵;,,,,, cooling waterpump冷套泵;,,,,, jacketed pump 〈cooled〉离心泵;,,,,, centrifugalpump离心机出料泵;,,,,, centrifugal run-offpump离心喷射泵;,,,,, centrifugal-jetpump离心-旋涡泵;,,,,, centrifugal-peripheral pump离心-旋涡泵;,,,,, centrifugal-turbinepump离子泵;,,,,, ion〈ization〉pump理想泵;,,,,, idealized pump立式泵;,,,,, vertical pump立式框架固定泵;,,,,, vertical frame mounted pump立式流程泵;,,,,, vertical process pump立式筒袋泵;,,,,, vertical barrel pump沥青泵;,,,,, bitumenpump炼油厂泵;,,,,, oil refinery pump链传动泵;,,,,, chain drivepump链式泵;,,,,, chainpump两级泵;,,,,, two stage pump裂化装置泵;,,,,, cracking pump流程泵;,,,,, process pump流道式叶轮泵;,,,,, channel impellerpump流体喷射泵;,,,,, fluid entrainmentpump流体喷射泵;,,,,, fluid jetpump禄乙烯塑料泵;,,,,, chlorovinyl plasticpump滤清污水泵;,,,,, decanted sewagepump滤渣泵;,,,,, filter residuepump罗茨泵;,,,,, lobe pump罗茨泵;,,,,, lobed element pump罗茨泵;凸轮泵;,,,,, rotary piston libe type pump罗茨泵;凸轮泵〈美〉;,,,,, lobular pump罗茨真空泵;,,,,, Root’s vacuum pump螺杆泵;,,,,, screw pump螺纹连接管道泵;,,,,, pipeline mounted pump with screwed connections 螺旋泵;,,,,, Archimedean screw pump螺旋提水机;阿基米德螺旋泵;,,,,, inclined Archimedean screw pump 螺旋形滑片泵;,,,,, screw vane pump螺旋形滑片泵;,,,,, screw vane pump脉冲容积泵;,,,,, pulsating (chamber)pump脉动计量泵;,,,,, metering pulse pump煤泥泵;,,,,, coal slurrypump煤水泵;,,,,, coalpump迷宫螺旋泵;,,,,, labyrinth screw pump密闭式螺杆泵;,,,,, airtight screw pump密闭式螺杆泵;,,,,, hermetic screw pump密闭式螺杆泵;,,,,, sealed screw pump模型泵;,,,,, model pump木浆泵;,,,,, wood pulp pump木浆泵;,,,,, wood stock pump水泵英语4内封闭式活塞泵;,,,,, inside-packed type pistonpump内混合型自吸泵;,,,,, self-priming pump with inner recirculation内密封式活塞泵;,,,,, internal-packed type piston pump内啮合齿轮泵;,,,,, crescent gearpump内啮合齿轮泵;,,,,, crescent seal gearpump内啮合齿轮泵;,,,,, internal gear pump内配流径向活塞泵;,,,,, centrally ported radial piston pump内配流径向活塞泵;,,,,, radial piston pump with interior admission内燃泵;汉弗雷泵;,,,,, Humphrey pump内燃机驱动泵;,,,,, engine drivenpump内循环形屏蔽泵;,,,,, canned motor pump with inner recirculationpump 内轴承泵,,,,, pump with internal bearing(s)耐碱泵;,,,,, lye pump耐磨泵;,,,,, abration resisting pump耐磨泵;,,,,, wear resisting pump耐蚀泵;,,,,, corrosion freepump耐蚀泵;,,,,, corrosion resistingpump耐酸泵;,,,,, acid pump挠型转子泵;,,,,, flexible rotarypump泥浆泵;,,,,, filter mudpump泥煤泵;,,,,, turf pump逆洗泵;,,,,, back washpump凝水回收泵;,,,,, condensate recoverypump凝水回收泵;,,,,, condensate returnpump凝水-增压泵;,,,,, condensate-booster凝水-增压-给水泵;,,,,, condensate-booster-feedpump牛奶泵;,,,,, milk pump扭转活塞泵;,,,,, rocking pintle piston pump农用喷药泵;,,,,, agricultural spray pump for chemicals排涝泵;,,,,, land reclamation pump排水泵;,,,,, draining pump盘状活塞泵;,,,,, bucket pistonpump配流盘式轴向活塞泵;,,,,, flatvalve axial pistonpump配流盘式轴向活塞泵;,,,,, port plate axial piston pump配流盘式轴向活塞泵;,,,,, valve plate axial piston pump喷灌泵;,,,,, agricultural spray pump喷淋池泵;,,,,, spary pond pump喷洒泵;喷淋泵;,,,,, spary pump喷射泵;,,,,, injectionpump喷射泵;,,,,, jet pump喷水泵;,,,,, injection waterpump喷水推进轴流泵;,,,,, axial flow pump for water jet propulsion喷水推进轴流泵;,,,,, water jet propulsion axial flow pump皮带传动泵;,,,,, belt drivenpump偏心径向活塞泵;,,,,, radial piston eccentric pump偏心螺杆泵;,,,,, eccentrie helical totorpump偏心转子泵;,,,,, eccentric rotarypump平衡转子式滑片泵;,,,,, balanced rotor vanepump屏蔽泵;,,,,, canned motorpump起动备用泵;,,,,, starting up stand-by pump起动用泵;,,,,, starting up pump起动用抽气泵;,,,,, evacuationpump起动用罐水泵;,,,,, priming pump气动隔膜泵;,,,,, membrane pump with pneumatic drive 气动泥浆泵;,,,,, air-pressure actuated slurry pump气举泵,气体升液泵;,,,,, gas liftpump气举泵;气体升液泵;,,,,, mammoth pump气密电动泵;,,,,, gastight motor drivenpump气泡泵;曼木特泵;气举泵;,,,,, air lift pump气泡泵;气举泵;,,,,, gas bubblepump气体喷射泵;,,,,, gas jetpump气体喷射真空泵;,,,,, gas jet vacuumpump气镇泵;,,,,, gas ballastpump汽车冲洗泵;,,,,, car wash pump汽车用泵;,,,,, automobile pump汽轮机驱动泵;,,,,, turbine driven pump汽轮机直联给水泵;,,,,, turbine feed pump前置泵,增压泵;,,,,, boosterpump潜水泵;,,,,, submerged pump潜水神井泵;,,,,, borehole submergedpump潜液式螺杆泵;,,,,, submerged screw pump浅井泵;,,,,, shallow well pump巧克力输送泵;,,,,, choclatepump撬式泵;滑移泵;,,,,, skid mounted pump切线增压泵;部分流泵;,,,,, partial emission pump切线增压泵;部分流泵;,,,,, sundyne pump切削冷却乳剂泵;,,,,, cutting oilpump倾斜活塞泵;,,,,, inclined piston pump清泥液泵;,,,,, supernatant liquor pump清水泵;,,,,, clean waterpump清水泵;,,,,, clear waterpump清水泵;供水泵;,,,,, raw water service pump清洗泵;,,,,, washery pump清洗泵;,,,,, washing pump清汁泵;,,,,, evaporator supplypump清汁泵;,,,,, fitered juice球形活塞泵;,,,,, ball pistonpump曲柄泵;,,,,, rotative reciprocating pump曲柄飞轮泵;,,,,, crank and flywheelpump取暖用泵;,,,,, heating pump全负荷泵;,,,,, full loadpump全可调式混流泵;,,,,, mixed flow pump with blades adjustable in operation 全可调式轴流泵,,,,, axial flow pump with blades adjustable in operation全可调式轴流泵;,,,,, axial flow pump with variable pitch blades全青铜泵;,,,,, all abronze pump燃油泵;,,,,, fuelpump燃油泵;,,,,, fuelpump燃油供给泵;,,,,, fuel oil supplypump燃油喷射泵;,,,,, fuel oil injectionpump燃油喷射泵;,,,,, oil burner pump燃油转送泵;,,,,, vuel oil transferpump染料泵;,,,,, dyepump热泵;,,,,, heat pump热电磁泵;,,,,, ther‘moelectromagnetic pump热水泵;,,,,, hot water pump热水循环泵;,,,,, hot water circulating pump热套泵;,,,,, jacketed pump 〈heated〉热油泵;,,,,, hot oil pump人字齿持论泵;,,,,, herringbone pump人字齿齿轮泵;,,,,, herringbone gear pump人字齿齿轮泵;,,,,, double helical gear pump容积泵;,,,,, pisitive displacement pump容积式真空泵;,,,,, vacuum displacement pump熔融液泵;,,,,, melt(liquor)pump熔盐泵;,,,,, pump for liquid salts鞣革液泵;,,,,, tannery fleshings pump乳剂泵;,,,,, emulsionpump软管泵,蠕动泵;,,,,, flexible tubepump软管泵;蠕动泵;,,,,, peristaltic pump软管式隔膜泵;,,,,, flexible tube diaphragmpump软管式隔膜泵;,,,,, flexible tube membranpump润滑剂泵;,,,,, lubricating pump三缸曲柄泵;,,,,, three throw crank pump三缸曲柄泵;,,,,, triplex pump三缸往复泵;,,,,, three cylinder reciprocating pump三缸往复泵;,,,,, three throw reciprocating pump三流道叶片泵;,,,,, three channel impeller pump三螺杆泵;,,,,, three screw pump三叶凸轮泵;,,,,, three lobe pump三柱塞泵;,,,,, triple plunger pump三作用滑片泵;,,,,, three cell vane pump扫仓泵;清仓泵;,,,,, stripping pump沙泵;,,,,, sand pump沙石泵;,,,,, gravel pump射流泥浆泵;,,,,, jet sludge pump深井泵;,,,,, boreholepump深井泵;,,,,, deepwellpump深井泵;,,,,, vertical turbine pump升华泵;提纯泵;,,,,, sublimation pump生物滤池腐殖质泵;,,,,, filter-humuspump湿坑泵(美);,,,,, wet pit pump湿坑泵;,,,,, wet sump pump湿式电动机泵;,,,,, wet motor pump湿式真空泵;,,,,, wet vacuum pump石灰浆泵;,,,,, lime slurry pump石灰乳泵;,,,,, milk of lime pump石灰汁泵,清汁泵;,,,,, clarified juicepump石灰汁泵;,,,,, limed juice pump石油泵;,,,,, petroleum pump实验室泵;,,,,, laboratory pump食品泵;,,,,, foodpump食品泵;,,,,, pump for edible fluids试压泵;,,,,, hydraulic 〈pressure〉test pump手动泵;手压泵;,,,,, hand pump手动泵;手压泵;,,,,, lever operated hand pump手动活塞泵;,,,,, hand piston pump手压泵,手动泵;,,,,, cottagepump手压抽排泵;手摇泵;,,,,, hand lift and force手压提升泵;,,,,, hand lift pump疏水泵;,,,,, drainage pump输油管线泵;管线泵;,,,,, oil line pump输油管线泵;管线泵;,,,,, pipline pump双缸串联蒸汽直动泵;,,,,, duplex compound steam pump 双缸曲柄泵;,,,,, duplex power pump双缸往复泵;,,,,, twin cylinder reciprocating pump双缸往复泵;,,,,, two cylinder reciprocating pump双缸蒸汽直动泵;,,,,, duplex steam pump双隔膜泵;,,,,, two diaphragm pump双滑片泵;,,,,, twin vane pump双壳泵;,,,,, barrel insertpump双流道叶轮泵;,,,,, double channel impeller pump水泵的英语5双曲线式罗杆泵;,,,,, hyperbolic screw pump双凸轮旋转活塞泵;,,,,, twin lobe pump双涡壳泵;,,,,, double volute pump双涡壳泵;,,,,, double-casing volute pump双吸泵;,,,,, balanced suctionpump双吸泵;,,,,, double suction pump双吸螺杆泵;,,,,, double entry screw pump双吸液环泵;,,,,, double entry liquid ring pump双柱塞泵;,,,,, double plunger pump双转子滑片泵;,,,,, double rotor vane pump双转子径向活塞泵;,,,,, two rotor radial piston pump双作用滑片泵;,,,,, double action vane pump双作用滑片泵;,,,,, two cell vane pump双作用活塞泵;,,,,, double acting piston pump水泵;,,,,, water pump水环泵;,,,,, water ring pump水环真空泵;,,,,, water ring vaccum pump水力采煤泵;,,,,, monitor pump水泥浆泵;,,,,, cement slurrypump水喷射泵;,,,,, water jet pump水套冷却泵;,,,,, jacket cooling pump水头泵;升水泵;甲板冲洗泵;,,,,, head pump水压机泵;,,,,, hydraulic press pump顺磁性氧气泵;,,,,, paramagnetic oxygen pump伺服系统油泵;,,,,, governor oil pump伺服系统油泵;,,,,, telemotor pump饲槽自动泵;家畜自动引水泵;,,,,, automatic trough pump饲槽自动泵;家畜自动饮水泵;,,,,, animal self-operated drinking water pump 塑料泵;,,,,, plastic pump碎渣泵;粉碎机泵;,,,,, disintegrator pump碎纸浆泵;,,,,, brokepump梭心转子泵;,,,,, rotoplunger pump梭心转子泵;,,,,, shuttle-block pump钛合金泵;,,,,, titanium alloy pump搪瓷泵;,,,,, enamel linedpump搪瓷衬里转子泵;,,,,, enamel lined rotorpump糖膏泵;,,,,, massecuit pump糖浆泵;,,,,, syrup(extraction)pump糖蜜泵;,,,,, molasses pump糖汁泵;,,,,, sugar liquor pump糖汁泵;〈浆〉汁泵;,,,,, juice pump陶瓷泵;,,,,, ceramicpump陶瓷酸泵;,,,,, ceramic acidpump梯形螺杆泵;,,,,, trapezoid screw pump甜菜泵;,,,,, beetpump甜菜根泵;,,,,, beet tailspump甜菜丝泵;,,,,, cossettepump通用泵;,,,,, general servicepump通用泵;,,,,, ordinary pump通用泵;,,,,, universal pump筒袋式泵;,,,,, barrelpump筒袋式油泵;,,,,, barrel oil pump凸轮泵;,,,,, cam pump凸轮转子式刮片泵;,,,,, cam rotor vanepump凸轮转子式刮片泵;,,,,, cam-vanepump土拉泵;旋流泵;,,,,, Turo pump托架固定泵;,,,,, headstock mounted pump托架固定泵;,,,,, pedestal mounted pump拖拉机泵;,,,,, tractor pump挖泥泵;,,,,, dredging pump外混合型自吸泵;,,,,, self-priming pump with outer recirculation外啮合齿轮泵;,,,,, external gear pump外啮合齿轮泵;,,,,, gear-on-gearpump外配流径向活塞泵;,,,,, peripherally ported radial piston pump外配流径向活塞泵;,,,,, radial piston pump with exterior admission外循环形屏蔽泵;,,,,, canned motor pump with outer recirculationpump 外轴承泵;,,,,, pump with external bearing(s)往复泵;,,,,, oscillating displacement pump往复泵;,,,,, reciprocating pump往复式深井泵;,,,,, borehole reciprocatingpump微计量泵;,,,,, micro-metering pump围垦泵;,,,,, dyke drainagepump尾矿泵;,,,,, tailings pump卫生泵;,,,,, sanitary pump温水泵;,,,,, warm water pump涡壳泵;,,,,, volute pump卧式泵;,,,,, horizontal pump污泥泵;,,,,, sludge pump污水泵;,,,,, effluentpump污水泵;,,,,, sewage pump污水泵;,,,,, waster water污水泛灌泵;,,,,, sewage broad irrigation pump污水喷灌泵;,,,,, sewage irrigation spray pump无阀隔膜泵;,,,,, valveless diaphragm pump无阀活塞泵;,,,,, valveless pump无阀振动泵;,,,,, valveless vibration pump无接触密封自吸泵;,,,,, nontacting sealed selfpriming pump无曲柄多缸泵;,,,,, crank-less multicylinderpump无曲柄污水泵;,,,,, crankless sewagepump无曲柄消防泵;,,,,, crankless firepump无叶片泵;,,,,, bladelesspump无轴封泵;,,,,, glandlesspump无轴封计量泵;,,,,, glandless meteringpump五螺杠泵;,,,,, five screwpump吸附真空泵;,,,,, adsorption vacuum pump吸入增压泵;,,,,, suction booster pump吸收泵;,,,,, absorption pump吸收泵;,,,,, sorption pump吸水箱水泵;,,,,, suction box water pump吸水箱水泵;,,,,, Sven-Pedersen pump洗舱泵;,,,,, butterworthpump洗矿用泵;,,,,, ore washing pump洗煤用泵;,,,,, coal washingpump洗气泵;,,,,, gas washingpump相对叶轮泵;背靠背叶轮泵;,,,,, pump with opposed impellers箱筒抽空泵;,,,,, barrel emptyingpump向心泵;,,,,, centripetalpump消防泵;,,,,, fire(fighting)pump消防喷淋系统供水泵;,,,,, sprinkler system supply pump消化污泥泵,腐泥泵,吸泥泵;,,,,, digeated sludgepump斜板泵;,,,,, inclined rotor pump斜板泵;,,,,, obleque plate pump斜齿齿轮泵;,,,,, helical gear pump斜缸型轴向柱塞泵;,,,,, tilting cylinder block type axial plunger斜盘式(往复)泵;,,,,, swash plate operated(reciprocating)pump 斜盘式轴向活塞泵;,,,,, cam plate type axial pistonpump斜盘式轴向活塞泵;,,,,, wobble plate axial piston pump斜置轴流泵;,,,,, inclined axial flow pump斜轴式轴向活塞泵;,,,,, angle-type axial piston pump斜轴式轴向活塞泵;,,,,, bent axis axial pistonpump谐振隔膜泵;,,,,, resonance diaphragm pump泄洪泵;,,,,, flood drainagepump行星转子型蠕动泵;,,,,, planet rotor pelstaltic pump蓄能泵;,,,,, storage pump悬臂叶轮泵;,,,,, pump with overhung impeller悬浮污泥泵;,,,,, floating sludgepump悬浮液泵;,,,,, suspension pump悬挂式泵;,,,,, suspended pump旋浆泵;,,,,, propeller pump旋流泵;土拉泵;,,,,, torque flow pump旋涡泵;,,,,, peripheral pump旋涡泵;,,,,, regenerative pump旋涡泵;,,,,, vortex pump循环泵;,,,,, circulatingpump压电泵;,,,,, piezoelectric pump压力补偿齿轮泵;,,,,, pressure-balanced gear pump压力水柜泵;,,,,, hydrophor pump压力油泵;,,,,, pressure oil pump压缩空气驱动泵;,,,,, air operated pump压缩空气驱动泵;,,,,, compressed airpump压载泵;,,,,, ballastpump盐水泵;,,,,, brinepump叶轮串并联泵;,,,,, pump with series or parallel connection impellers 叶片泵;,,,,, rotodynamic pump叶片泵;,,,,, turbo pump叶片泵;,,,,, vane pump叶片可逆转的泵-水轮机;,,,,, turbine pump with reversible blades液化天然气用低温泵;,,,,, cryopump for LNG液环泵;,,,,, liquid ring pump液态金属泵;,,,,, pump for liquid metals液体泵;,,,,, liquid pump液体肥料泵;,,,,, liquid manure pump液体肥料喷射泵;,,,,, liquid manure spraying pump液体活塞式转子真空泵;,,,,, rotary vaccum pump with liquid piston 液体火箭涡轮泵;,,,,, liquid rocket turbo pump液体喷射泵;,,,,, liquid ejector pump液压泵;,,,,, hydraulic pump液压活塞泵;,,,,, hydraulic piston pump液氧泵;,,,,, liquid oxygen pump医用泵;,,,,, medical pump饮用水泵;,,,,, drinking water pump应急泵;,,,,, emergencypump应急泵;,,,,, jury pump硬铅泵;,,,,, hard lead pump油泵;,,,,, oil pump油罐残油泵;,,,,, tank residue pump油罐车泵;,,,,, tanker pump油扩散泵;,,,,, oil diffusion pump油冷却泵;,,,,, oil cooler pump油轮用泵;,,,,, oil tanker’s pump油喷射泵;,,,,, oil ejector pump油喷射增压泵;,,,,, oil ejector booster pump水泵英语6油田泵;,,,,, oil field pump油蒸汽喷射泵;,,,,, oil vapour jet pump诱导轮离心泵;,,,,, centrifugalpump with inducer鱼泵;,,,,, fishpump原生污泥泵;,,,,, crude sludgepump原生污泥泵;,,,,, raw sludge pump原生污水泵;,,,,, crude sewagepump原生污水泵;,,,,, raw sewage pump原油泵;,,,,, crude oilpump原汁泵;,,,,, raw juice pump原汁循环泵;,,,,, raw juice circulating pump圆筒感应泵;,,,,, cylindric inductionpump载热剂泵;,,,,, heat transfer pump再循环泵;,,,,, recycle pump增压泵;,,,,, boostingpump增压给水泵;,,,,, booster-feed增压扩散泵;,,,,, booster diffusionpump渣泵;,,,,, bagassepump粘浆泵;,,,,, cellulose pulp pump真空泵;,,,,, vacuum pump蒸汽泵;,,,,, steam pump蒸汽喷射泵;,,,,, steam jet pump蒸汽喷射真空泵;,,,,, steam jet vaccum蒸汽直动活塞泵;,,,,, direct acting steam pump蒸煮锅放泄泵;,,,,, digester drain pump蒸煮锅酸液循环泵;,,,,, digester acid circulatingpump 正齿轮泵;,,,,, spur gear pump直接安装泵;,,,,, direct mounted pump直联泵;,,,,, unit construction pump直联泵;单体泵;,,,,, monoblock pump直列式柱塞泵,管道泵;,,,,, in-linepump直列式柱塞泵;,,,,, in-line plungerpump直通活塞泵(美);,,,,, straight way type piston pump 直通活塞泵;,,,,, straight through type piston pump值勤泵;,,,,, duty pump值勤泵;,,,,, service pump纸浆泵;,,,,, paper stock pump纸浆废水泵;,,,,, stock drain water pump纸浆水泵;浆水泵;,,,,, pulp water pump纸浆稀释水泵;,,,,, stock water pump中比转速泵;,,,,, medium specific speed pump中开泵;,,,,, axially splitpump中开泵;水平中开泵;,,,,, horizontal split pump中速离心泵;,,,,, moderate-speed centrifugal pump。
高速旋转机械中英文对照外文翻译文献

中英文对照外文翻译文献(文档含英文原文和中文翻译)Low Power Magnetic Bearing Design For High Speed Rotating MachineryP. E. Allaire, E. H. Maslen, and R. R. Humphris, Department of Mechanical and Aerospace Engineering University of Virginia Charlottesville, VA 22901C. K. Sortore Aura Systems, Inc. EI Segundo, CA 90245 P. A. Studer Magnetic Concepts Silver Springs, MD 20901 317SUMMARYAgnetic suspension technology has advanced to the point of being able to offer a number of advantages to a variety of applications in the rotating machinery and aerospace fields. One strong advantage of magnetic bearings over conventional bearings is the decrease in power consumption. The use of permanent magnets, along with electromagnets, is one appealing option which can further reduce the power consumption of the bearing.The design and construction of a set of permanent magnet biased, actively controlled magnetic bearings for a flexible rotor is presented. Both permanent magnets and electromagnets are used in a configuration which effectively provides the necessary fluxes in the appropriate air gaps, while simultaneously keeping the undesirable destabilizing forces to a minimum. The design includes two radial bearings and a thrust bearing.The theoretical development behind the design is briefly discussed. Experimental performance results for a set of operating prototype bearings is presented. The results include measurements of load capacity, bearing stiffness and damping and the dynamic response of the rotor. With few exceptions, the experimental measurements matched very well with the predicted performance. The power consumption of these bearings was found to be significantly reduced from that for a comparable set of all electromagnetic bearing.INTRODUCTIONMagnetic bearings have a number of strong advantages. One most obvious advantage is their non~ontacting, virtually friction-free characteristics. Entire lubrication systems and the need for mechanical oil seals, which add to friction losses and instabilities associated with cross coupled bearing coefficients, can be eliminated by using these types of bearings. The life expectancy of a magnetic bearing, in many cases, can be much higher than that of conventional bearing. Due to the non~ontacting nature of the bearings, mechanical parts do not wear out. This can obviously increase system reliability and decrease costly repairs and necessary maintenance which interrupt profitable machine operation. If designed properly, a magnetic bearing can perform under much harsher conditions and environments for extended periods of time which would not be possible with other types of bearings. One further advantage of the frictionless characteristic of these bearings is that of power loss. The power consumption of a conventional fluid-film bearing is in many cases much more than for a magnetic bearing. Power loss reductions of one order of magnitude or more canbe expected when a machine is converted from using conventional bearings to magnetic bearings.A variety of work has been accomplished on a number of different applications and aspects of magnetic bearings. An extensive amount of research has been performed by a number of university and industry researchers on the development of magnetic bearings in an· industrial canned motor pump [1]. A number of other successful industrial applications of magnetic bearings has been reported by Weise [21. Burrows et. al. [3] presents the development and application of a magnetic bearing specifically designed for the vibration control of a flexible rotor. Keith, et. al. [4] successfully developed a PC-based digital controller for magnetic bearings. Continuing research is being performed in the areas of digital and adaptive controls for magnetic bearings. In researching the use of permanent magnets in combination with electromagnets, of particular interest are two patents credited to Philip Studer [5, 6]. These patents contain a number of features, primarily dealing with permanent magnets, which have useful application to the bearings discussed in this paper. Wilson and Stu~er [7] have also applied the permanent magnet bias concept to a linear motion bearing. Ohkami et. al. [8] have performed some interesting comparison studies of magnetic bearings of various configurations which use permanent magnets. Another paper by Tsuchiya et. al. [9] studies and comments on the stability of a high speed rotor which is suspended in magnetic bearings biased with permanent magnets. Meeks [10] has also performed a comparison of the various magnetic bearing design approaches and concludes that the combining of actively controlled electromagnets with permanent magnets results in a superior magnetic bearing in terms of size, weight and power consumption. The rare earth permanent magnets of today, in particular Sm-Co and Nd-Fe-Bo magnets, offer very high performance characteristics in terms of magnetic strength, energy product and thermal qualities. The magnet designer is able to concentrate a very large amount of magnetic energy in a small package, making more efficient use of available space.The design concept for the permanent magnet biased magnetic bearing design discussed in this paper is a variation on research and development reported by Studer [5, 6]. The following two sections give a brief description of how the bearings conceptually operate.Radial MagnetiC Bearing DescriptionA diagram of a permanent magnet biased radial magnetic bearing is shown in Figure 1. This bearing is designed to operate at one end of the rotor and control radial forces only. Four axially magnetized arc segment magnets are positioned circumferentially adjacent to the stator. The bias flux generated by the permanent magnets passes down the laminatedstator pole leg, through the working air gap, axially along the shaft, then returns to the permanent magnet via . a radial bias pole piece. The active control flux generated by the coils also passes down the stator pole leg and through the working air gap. The return path for the active flux is then circumferentially around the stator, as shown in Figure 1. This design requires only four poles and four coils, unlike an all electromagnetic design which generally requires eight. In addition, since the coils for each bearing axis are connected in series, the bearing control system requires only five current amplifier channels, which is half as many as required of the all electromagnetic bearing.Combination Radial/Thrust Magnetic Bearing DescriptionA schematic of this bearing design, revealing the various magnetic paths, is shown in Figure 2. This bearing combines control of both radial and thrust forces. The radial portion of the bearing is identical to that which was described in the previous section. The thrust control however, is implemented by a unique magnetic flux configuration. The permanent magnet bias flux passing along the shaft splits equally between the two thrust poles before returning to the permanent magnet. A single active coil produces a magnetic flux, in the shape of a toroid, which symmetrically adds or subtracts to the bias flux in the working air gaps between the thrust disk and thrust poles.Design ConceptThe bearings designed for this project are different from all electromagnetic bearing designs in that they employ both permanent magnets and electromagnets. Permanent magnets generate the bias flux in the working air gaps and electromagnets are used to modulate this flux.The purpose of establishing a bias flux in the working air gaps is to linearize the governing force equation of the magnetic actuator. The bias flux is a nominal flux density about which the control flux is varied. If a bias flux of zero is used, (only one opposing actuator is operated at a time,) then the force generated by the actuator on the rotor follows a quadratic force law, i.e., the force will be proportional to the square of the flux density in the air gaps. Consequently, the force slew rate will be zero when the rotor is in the nominal balanced position and the transient response will be adversely effected. If, however, the bearing fluxes are modulated about a non-zero bias flux, (with opposing actuators symmetrically perturbed,) it is easily shown that the force becomes linearly related to the control flux. The following section demonstrates this important relation.Force RelationshipsThe force generated in an air gap of area Ag and length g by a magnetic actuator can be expressed by the direct relationwhere Bg is the flux density in the air gap and J.Lo is the permeability of free space. If only a single axis of the bearing is considered, then the net force acting on the shaft will be the difference of the two opposite acting actuator forces. Assuming the areas of the two opposing air gaps are the same, the force acting on the shaft by the magnetic bearing can be expressed asThe flux density in the air gaps is being supplied by two sources, i.e., the permanent magnet and the coil. In order to properly provide differential control, the fluxes in the two gaps are symmetrically perturbed so that the flux in one gap is increased while the flux in the opposite gap is decreased by the same amount. This implies thatwhere Bpm is the flux density generated by' the permanent magnet and Be is the flux density generated by the coil. Substituting Eqs. l3, 4) into Eq. (2), expanding and simplifying, the force acting on the shaft can now be expressed asBy expressing the equation for the force on the shaft in this form, it is interesting to note that the force is not only proportional to the bias level, Bpm, but it is also linearized with respect to the control flux, Be. .Open Loop Stiffness and Actuator Gain The force generated by the bearing in the horizontal direction, F x, can be accurately approximated by the truncated Taylor series expansion in the following way:If tne magnetic circuit is balanced, then the first term in Eq. (6) is equal to zero andwhere x represents the rotor displacement and ie represents the control current in the electromagnetic coil. The parameters Kx and Ki are defined ashe quantity Kx is referred to as the open loop stiffness and represents the change in the horizontal force due to horizontal displacement. The open loop stiffness is always negative which implies that the bearing is unstable in the open loop control configuration. Unlike a actual spring with a positive stiffness, a positive dispacement of the rotor toward the magnet will increase the attractive force. The quantity Ki represents the actuator gain of the bearing. It represents changes in the horizontal force due to control current, ie. Equivalent expressions exist for the components of the vertical force expression. Expressions for the open loop stiffness and the actuator gain are determined by performing the appropriate differentiation of the force expression. These expressions take on the formwhere Land H represent the length and demagnetization force, respectively, of the permanent magnet and N is the number of turns in the electromagnetic coil.Control System DescriptionThe control elements of this system are those components which detect the motion of the shaft, determine the required control force and generate a coil current required by the magnetic bearing to generate this force. The magnetic bearing system consists of four distinct components: the magnetic actuator, the displacement sensors and associated conditioning circuits, the analog PID controller and the power amplifier.The actual magnetic bearing mainly consists of the electromagnetic coils, iron polepieces, rotor and permanent magnets. The signal conditioning component consists of the eddy current induction displacement sensors, signal amplification and coordinate transformation circuits. The analog controller primarily consists of three separate components. The components take the form of proportional (P), integral (I) and derivative (D) compensation networks. These three parallel stages are added together through a summing amplifier to produce the output of the analog controller. The last component in the control loop is the power amplifier. The amplifier, upon request of the controller, supplies the required current to magnetic coils to produce the necessary fluxes in the bearing.The dynamics of the bearing-rotor system can be combined with the operating characteristics of the control electronics to form a closed-loop control system. This control system is shown in a simplified block diagram form in Figure 3. The displacement sensor characteristics, analog controller and amplifier make up the relatively complex transfer function of the feedback controller, Gc(s). The feedback controller relates the rotor position to the actuator current. The closed-loop transfer function for this magnetic bearing system, as determined from this block diagram, is given bywhere m is the mass of the rotor supported by the bearing.Prototype Bearing ConstructionThe four-pole radial bearing stators, as shown in the diagrams of Figures 1 and 2, were designed to be identical for both bearings. The stators and rotors were constructed of 3% silicon-iron lamination material which had a thickness of 0.007 inches. Each laminated component consists of approximately 100 laminations. The laminations were glued together using a two part activator/resin adhesive and the shape was machined by wire EDM (electric discharge machining.) The bearing stators have an outside diameter of approximately 3.0 inches and an axial length of approximately 0.7 inches. The outside diameter of the laminated rotor is approximately 1.5 inches. The thrust bearing components were machined from soft magnet iron. The high energy permanent magnets, made out of a geodymium-Iron-Boron alloy, have a maximum energy product of 30 MG-Oe. The bearings support a shaft weighing approximately 3.7 Ibm.Load CapacityMeasurements of the maximum load applied to the shaft, before falling out of support,are plotted as a function of proportional controller gain, Kp, in Figure 4. The force in this test was applied by hanging weights on the shaft. A pulley system was constructed in such a way that the force could be applied in the desired direction. The force in the plots represents forces applied along the bearing axes.The variation of the maximum load at lower proportional gains is actually a measure of the stability threshold of the system. It is noted in Eq. t 8) that the open loop stiffness, Kx is defined at a nominal operating point, i.e., rotor position and control current equal to zero. However, as the bearing is loaded with a static force, the steady state current begins to increase. It can be shown analytically that Kx is a function of the operating point of the control current. That is, as the control current current increases, Kx also increases. Increasing proportional gain has the effect of compensating for this increase in Kx and consequently increasing the stability of the system.The measurements made at higher proportional gains represent a more accurate measure of the actual load capacity of the bearing. Enough stability is provided so that magnetic saturation is reached in the bearing pole structures. The maximum predicted loads in the plots of Figure 4 are calculated at the point of magnetic saturation.Equivalent Bearing Stiffness and DampingMeasurements of the equivalent stiffness of the bearings are shown in Figure 5. This simple measurement was performed by applying a constant force, ~F , and noting the displacement, ~x , of the shaft (controller integrators turned off.) The stiffness then is given simply by Keq= ~F / ~x. A linear regression was performed on the measured data, which resulted in very good correlation, as can be observed in the plots. It is noted that the proportional gain has a direct effect on the stiffness of the bearings, as has been previously demonstrated by Humphris, et. al. [11].Relative damping in the bearings was investigated from a white noise frequency response analysis of the bearing and rotor. The analysis was performed by injecting noise, composed of all frequencies of interest, into one axis of the turbine-end radial bearing, and performing a FFT (Fast Fourier Transform) analysis on the vibration response of that axis. This linear frequency response, composed of 100 averages, is shown in Figure 6. The derivative controller gain, Kr was varied through a range of values as noted in the plot. As expected, the derivative gain had a direct effect on the damping in the bearings [11]. The first large spike represents the first two modes of shaft vibration. They are very close together in frequency and essentially indistinguishable. The frequency of the second spike is the third mode of vibration and the third small spike at approximately 60,000 cpm is the fourth mode. It is noted that the variation of the derivative gain strongly effects the firsttwo modes, has a small effect on the third mode and virtually no influence on the vibration amplitude of the fourth mode.Critical Speeds and Rotor ResponseThe damped synchronous critical speeds of the flexible shaft supported by these bearings can be approximately determined from the white noise frequency response plots of Figure 6. These values, however, represent the zero speed natural frequencies, and the gyroscopic stiffening effects of any attached disks would not be included. Since the natural frequency is given by ,where k is the shaft stiffness and m in the modal mass of the rotor, it is of course expected that the observed critical speeds, when the shaft was spinning, would be higher.Plots showing the vibration magnitude and phase for the shaft speeds that were obtained is included in Figure 7. Amplitude information was taken directly from the magnetic bearing sensors and a key-phase sensor was used to provide the phase information. According to the maximum vibration amplitudes observed in Figure 7, the first vibration mode is observed to occur at approximately 10,000 rpm and the second at approximately 13,000 rpm.Power ConsumptionFinally, a number of power consumption measurements were made. Measurements of the power were taken with a wattmeter for a number of cases. This meter is used with the assumption that the measured voltage and current being supplied to the control electronics is sinusoidal in nature. In addition, it is realized that it represents a somewhat gross measurement as it includes all the inefficiencies of the various electronic components. Table 1 summarizes the results. The non~ssential electronic diagnostic components of the bearing system were observed to consume only about 7 watts. These measurements represent a significant improvement over the 500 watts of approximate total power consumed by a comparable current biased all electromagnetic bearing design.CONCLUSIONSThe brief theory which was presented in this paper established the basic electromagnetic and mechanical relationships necessary to develop a set of permanent magnet biased magnetic bearings. The design involved both radial and thrust bearings. The availability of newer rare-earth high energy permanent magnets made it possible to effectively provide the necessary bias fluxes in the bearing.The bearings and rotor were successfully constructed and operated. A number of tests and experiments were performed on the bearing-rotor system. The tests consisted of loadcapacity, stiffness and damping measurements. The results proved to be very positive in that the theoretical predictions and the observed performance matched reasonably well, giving credibility to the models which were used to perform the analysis. Of particular interest for this study was the measured power consumption of the bearings. It clearly demonstrates that the use of permanent magnets can improve the operating efficiency of an active magnetic bearing.It was successfully observed and demonstrated that these bearings have strong potential for future use as efficient, reliable bearings. However, further research and development is required in the areas of controls, magnetic materials and actuator design before it is possible to install them into a useful industrial application.R EFERENCES1. Allaire P.; Imlach, J.; McDonald, J.; Humphris, R.; Lewis, D.; Banerjee, B.; Blair, B.;Clayton, J.; Flack, R.: "Design, Construction and Test of Magnetic Bearings in an Industrial Canned Motor Pump," Pump Users Symposium, Texas A & M, Houston, TX, May 1989.2. Weise, D. A.: "Present Industrial Applications of Active Magnetic Bearings," Presentedat the 22nd Intersociety Energy Conversion Engineering Conference, Philadelphia, Pennsylvania, August 1987.3. Burrows, C. R., Sahinkaya, N.; Traxler, A.; and Schweitzer, G.: "Design andApplication of a Magnetic Bearing for Vibration Control and Stabilization of a Flexible Rotor," Proceedings of the First International Magnetic Bearings Symposium, ETH Zurich, Switzerland, June 1988.4. Keith F. J., Williams, R. D.; Allaire, P. E.; and Schafer, R. M.: "Digital Control ofMagnetic Bearings Supporting a Multimass Flexible Rotor," Presented at the Magnetic Suspension Technology Workshop, Hampton, Virginia, February 1988.5. Studer. P. A.: NASA, Magnetic Bearing, Patent 3865442, Patent Application 100637,February 1975. 6. Studer, P. A.: NASA, Linear Magnetic Bearing, Patent 4387935, Patent Application 214361, December 1980.7. Wilson, M.; and Studer, P. A.: "Linear Magnetic Bearings," Presented at the InternationalWorkshop on Rare Earth-Cobalt Magnets and Their Applications, Roanoake, Virginia, June 1981.8. Ohkami, Y., Okamato, 0.; Kida, T.; Murakami, C.; Nakajima, A.; Hagihara, S.; andYabuuchi, K.: "A Comparison Study of Various Types of Magnetic Bearings Utilizing Permanent Magnets," Presented at the International Workshop on Rare Earth-Cobalt Permanent Magnets and Their Applications, Roanoake, Virginia, June 1981.9. Tsuchiya, K; Inoue, M.; Nakajima, A.; Ohkami, Y.; and Murakami, C.: "On Stability ofMagnetically Suspended Rotor at High Rotational Speed,." Presented at the Aerospace Sciences Meeting, Reno, Nevada, January 1989.10. Meeks, C.: "Trends in Magnetic Bearing Design," Paper presented at Naval SeaSystems Command Magnetic Bearing Forum, Washington, D. C., July 1989.高速旋转机械的低功率磁力轴承设计总结:磁悬液研究具有先进的研发技术,有一定的优势,广泛应用于旋转机械和航空航天等领域。
水泵中英文对照

2一般术语2.1水力机械hydraulic machinery2.2 水轮机hydraulic turbine2.3 蓄能泵storage pump2.4 水泵水轮机reversible turbine,pump-turbine2.5 旋转方向direction of rotation2.6 机组unit2.13立式、卧式和倾斜式机组vertical,horizontal and inclined unit2.14可调式水力机械regulated hydraulic machinery2.15不可调式水力机械non-regulated hydraulic machinery2.16主阀main valve3.1水轮机3.1.1反击式水轮机reaction turbine3.1.2 混流式水轮机Francis turbine,mixed-flow turbine3.1.3 轴流式水轮机axial turbine3.1.4 轴流转桨式水轮机Kaplan turbine,axial-flow adjustable blad propeller turbine 3.1.5 轴流调桨式水轮机Thoma turbine3.1.6 轴流定桨式水轮机Propeller turbine3.1.7贯流式水轮机tubular turbine,through flow turbine3.1.8灯泡式水轮机bulb turbine3.1.9竖井贯流式水轮机pit turbine3.1.10全贯流式水轮机straight flow turbine,rim-generator unit3.1.11轴伸贯流式水轮机(S形水轮机)tubular turbine(S-type turbine)3.1.12 斜流式水轮机diagonal turbine3.1.13 斜流转桨式水轮机Deriaz turbine3.1.14斜流定桨式水轮机fixed blade of Deriaz turbine3.1.15冲击式水轮机impuls turbine,action turbine3.1.16水斗式水轮机Pelton turbine,scoop turbine3.1.17斜击式水轮机inclined jet turbine3.1.18双击式水轮机cross-flow turbine3.2蓄能泵3.2.1混流式(离心式)蓄能泵centrifugal storage pump,mixed-flow storage pump 3.2.2轴流式蓄能泵propeller storage pump,axial storage pump3.2.3斜流式蓄能泵diagonal storage pump3.2.4多级式蓄能泵multi-stage storage pump3.3水泵水轮机(又称可逆式水轮机)3.3.1单级水泵水轮机singal stage pump-turbine3.3.2多级水泵水轮机multi-stage pump-turbine3.4主阀与阀门3.4.1蝴蝶阀butterfly valve3.4.2 平板蝶阀biplane butterfly valve,through flow butterfly valve3.4.3 圆筒阀cylindrical valve,ring gate3.4.4 球阀rotary valve,spherical valve3.4.5 盘形阀mushroom valve,hollow-cone valve,howell-Bunger valve3.4.6 针形阀needle valve3.4.7 旁通阀by-pass valve3.4.8直空破坏阀vacuum break valve4结构部件4.1混流式水轮机4.1.1埋入部件embedded component4.1.2 引水室(turbine)flume4.1.3蜗壳spiral case4.1.4座环stay ring4.1.5 固定导叶stay vane4.1.6 蜗壳鼻端spiral case nose4.1.7基础环foundation ring,discharge ring4.1.8 尾水管draft tube4.1.9锥形尾水管conical draft tube4.1.10肘形尾水管elbow draft tube4.1.11尾水管锥管draft tube cone4.1.12尾水管肘管draft tube elbow4.1.13 尾水管扩散段draft tube outlet part4.1.14 尾水管支墩draft tube pier4.1.15 尾水管里衬draft tube liner4.1.16 机坑里衬pit liner4.1.17导水机构distributor4.1.18顶盖headcover,top cover4.1.19底环bottom ring,bottom cover4.1.20导叶guide vane,wicket gate4.1.21 控制环regulating ring,operating ring4.1.22 导叶臂guide vane lever,wicket gate lever4.1.23 分半键split key4.1.24 导叶连杆guide vanelink,wicket gate link4.1.25 导叶过载保护装置guide vane overload protection device 4.1.26 剪断销shear pin4.1.27 摩擦装置friction device4.1.28 导叶轴承guide vane bearing4.1.29 导叶止推轴承guide vane thrust bearing4.1.30 导叶轴密封guide vane stem seal4.1.31 导叶端面密封guide vane end seal4.1.32 导叶立面密封guide vane seal4.1.33抗磨板facing plates,wear plates4.1.34导叶限位块guide vane stop block4.1.35导叶接力器guide vane servomotor4.1.36 单导叶接力器individual guide vane servomotor4.1.37 推拉杆push and pull rod,connecting rod4.1.38 调速轴regulating shaft4.1.39 均压管balance pipe4.1.40 转动部件rotating component4.1.41 转轮runner4.1.42 叶片blade4.1.43 上冠crown4.1.44 下环band4.1.45 泄水锥runner cone4.1.46 转轮密封装置runner seal4.1.47 转轮止漏环runner wearing ring4.1.48 固定止漏环stationary wearing ring4.1.49 转轮减压板decompression plate4.1.50 主轴main shaft4.1.51 导轴承guide bearing4.1.52 轴领guide bearing collar4.1.53 轴瓦guide bearing shoe4.1.54 轴承体guide bearing housing4.1.55 主轴密封装置main shaft seal4.1.56 检修密封stand still seal4.1.57 联轴螺栓coupling bolt4.2 轴流式水轮机和斜流式水轮机。
工业机械臂控制中英文对照外文翻译文献

中英文对照外文翻译文献(文档含英文原文和中文翻译)Hand Column Type Power MachineFollow with our country the rapid development of industrial production, rapidly enhance level of automation, implementation artifacts of handling, steering, transmission or toil for welding gun, spraing gun, spanner and other tools for processing, assembly operations for example automation, should cause the attention of people more and more.Industrial robot is an important branch of industrial robots. It features can be programmed to perform tasks in a variety of expectations, in both structure and performance advantages of their own people and machines, in particular, reflects the people's intelligence and adaptability. The accuracy of robot operations and a variety of environments the ability to complete the work in the field of national economy and there are broad prospects for development. With the development of industrial automation, there has been CNC machining center, it is in reducing labor intensity,while greatly improved labor productivity. However, the upper and lower common in CNC machining processes material, usually still use manual or traditional relay-controlled semi-automatic device. The former time-consuming and labor intensive, inefficient; the latter due to design complexity, require more relays, wiring complexity, vulnerability to body vibration interference, while the existence of poor reliability, fault more maintenance problems and other issues. Programmable Logic Controller PLC-controlled robot control system for materials up and down movement is simple, circuit design is reasonable, with a strong anti-jamming capability, ensuring the system's reliability, reduced maintenance rate, and improve work efficiency. Robot technology related to mechanics, mechanics, electrical hydraulic technology, automatic control technology, sensor technology and computer technology and other fields of science, is a cross-disciplinary integrated technology.Current industrial approaches to robot arm control treat each joint of the robot arm as a simple joint servomechanism. The servomechanism approach models the varying dynamics of a manipulator inadequately because it neglects the motion and configuration of the whole arm mechanism. These changes in the parameters of the controlled system sometimes are significant enough to render conventional feedback control strategies ineffective. The result is reduced servo response speed and damping, limiting the precision and speed of the end-effecter and making it appropriate only for limited-precision tasks. Manipulators controlled in this manner move at slow speeds with unnecessary vibrations. Any significant performance gain in this and other areas of robot arm control require the consideration of more efficient dynamic models, sophisticated control approaches, and the use of dedicated computer architectures and parallel processing techniques.Manipulator institutional form is simple, strong professionalism, only as a loading device for a machine tools, special-purpose manipulator is attached to this machine. Along with the development of industrial technology, produced independently according to the process control to achieve repetitive operation, using range is wide "program control general manipulator", hereinafter referred to as general manipulator. General manipulator used to quickly change the workingprocedure, adaptability is stronger, so he is in constant transformation in the medium and small batch production of products are widely used.NO.1 The composition of the manipulatorManipulator is in the form of a variety of, some relatively simple, some more complex, but the basic form is the same, generally by the actuators, transmission system, control system and the auxiliary device.The actuator manipulator actuators, by the hand, wrist, arm, pillars. Hand is grasping mechanism, which is used to clamp and release artifacts, as a human finger, can complete staff of similar action. Is connected to the fingers and wrist arm components, can be up and down, left and right sides and rotary movement. Simple manipulator can not the wrist. Prop used to support the arm, can also according to need to make it move.The driving system movement of the actuator by the transmission system to achieve. Common mechanical transmission system of mechanical transmission, hydraulic transmission, pneumatic transmission and power transmission etc. Several forms.The control system of manipulator control system main function is to control the manipulator according to certain procedures, movement direction, position, speed, simple manipulator is generally not set special control system, only the stroke switch, relay, control valves and control circuit can realize dynamic transmission system, the executing agency action in accordance with requirements. Action complex manipulator should adopts the programmable controller, microcomputer control. NO.2 Classification and characteristics of the manipulator Robots generally fall into three categories the first is general manipulator doesn't need manual operation. It is a kind of independence is not attached to a host device. It can according to the need of the task program, the operation of the provisions to complete. It is with the characteristics of common mechanical performance, also has general machinery, memory, intelligence of three yuan. Thesecond is the need to do manually. Called Operating machine. It originated in the atom, military industry, first by Operating machine to complete a specific assignment, later to use radio signal Operating machine to explore the moon and so on. Used in the forging industry Operating machine falls under this category. The third kind is to use special manipulator, mainly attached to automatic machine or automatic line, used to solve machine tool material and workpiece to send up and down. This manipulator in a foreign country is called "the Mechanical Hand", it is in the service of the host, driven by the host; Except a few working procedures generally is fixed, so it is special.NO.3 The application of industrial manipulatorManipulator is in the process of mechanization, automation production, developed a kind of new type of device. In recent years, with electronic technology, especially the wide application of electronic computer, the robot's development and production has become a high technology developed rapidly in the field of an emerging technology, it promoted the development of the manipulator, make the manipulator can achieve better with the combination of mechanization and automation.Manipulator although it is not as flexible as manpower, but it can have repeated work and labor, do not know fatigue, is not afraid of danger, snatch heavy weights strength characteristics such as larger than man, as a result, the manipulator has been brought to the attention of the many departments, and have been applied more and more widely.(1) Machine tools machining the workpiece loading and unloading, especially in automatic lathe, use common combination machine tools.(2) Widely used in the assembly operation, it can be used to assemble printed circuit board in the electronics industry, it can be in the machinery industry to assemble parts.(3)Can be in working conditions is poor, repetitive easy fatigue of the work environment, to instead of human Labour.(4) The development of the universe and the ocean.(5) Military engineering and biomedical research and test.Application of robots can replace people in dull, repetitive or heavy manual work, to realize mechanization and automation of production, instead of human in harmful environment of manual operation, improve labor condition, ensure the personal safety. In the late 1940 s, the United States in the nuclear experiments, firstly adopts manipulator handling radioactive materials, people in the security room to manipulate manipulator for various operation and experiment. After the '50 s, robots gradually extended to industrial production department, for use in high temperature, serious pollution of local leave work pieces and the loading and unloading materials, as auxiliary device in the machine tool automatic machine, automatic production line and processing center in the application, complete the material up and down or from libraries take put the knives and replace tool operations such as fixed procedure. Manipulator is mainly composed of hand and motion mechanism. Hand mechanism varies according to the usage situation and operation object, the common are holding, hold and the adsorption type etc. Motion mechanism usually driven by hydraulic, pneumatic, electric devices. Manipulator can be achieved independently of scaling, rotation and lifting movement, generally speaking, there are 2 ~ 3 degrees of freedom. Robots are widely used in machinery manufacturing, metallurgy, light industry and atomic energy etc.Manipulator is used in the production process automation with grab and move the workpiece is a kind of automatic device, it is in the process of mechanization, automation production, developed a new type of device. In recent years, with electronic technology, especially the wide application of electronic computer, the robot's development and production has become a high technology developed rapidly in the field of an emerging technology, it promoted the development of the manipulator, make the manipulator can achieve better with the combination of mechanization and automation. Robots can replace humans do dangerous, repeat the boring work, reduce human labor intensity and improve labor productivity. Manipulator have been applied more and more widely, it can be used forparts assembled in the machinery industry, processing the workpiece handling, loading and unloading, especially on the automatic CNC machine, combination machine tools more common use. At present, the manipulator has developed into a flexible manufacturing system of FMS and flexible manufacturing cell is an important component of FMC. The machine tool equipment and manipulator of a flexible manufacturing system or flexible manufacturing unit, it is suitable for medium and small batch production, can save a large workpiece delivery device, structure is compact, but also has a strong adaptability. When the workpiece changes, flexible production system is easy to change, is advantageous to the enterprise continuously updated marketable varieties, improve product quality, better adapt to the needs of the market competition. But at present our country's industrial robot technology and its engineering application level and foreign than there is a certain distance, scale and industrialization level is low, research and development of the manipulator has direct influence on raising the automation level of production in our country, from the consideration on the economic and technology is very necessary. Therefore, carries on the research design of the manipulator is very meaningful.NO.4 The development trend of manipulatorCurrent industrial applications of the manipulator gradually expanding, constantly improve the technology performance. Due to the short development time, it has a gradual understanding of process, the manipulator and a technically perfect step by step process, its development trend is:1.To expand the application of manipulator and processing industryAt present domestic robots used in mechanical industry more in cold working operations, while in the hot work such as casting, forging, welding, heat treatment less, and the application of assembly work, etc. So processing work items heavy, complicated shape and high environmental temperature, bring many difficulties to manipulator design, manufacture, it is need to solve the technical difficulties, make the manipulator to better service for processing work. At the same time, in otherindustries and industrial sectors, also will with the constant improvement of the industrial technology level, and gradually expand the use of the manipulator2.Improve the work performance of the industry manipulatorManipulator in the working performance of the pros and cons, determines the application and production, it can normal manipulator working performance of the repetitive positioning accuracy and speed of work two indicators, decided to ensure the quality of manipulator can complete the operation of the key factors. Therefore to solve good working stability and rapidity of the manipulator's request, besides from solve buffer localization measures, should also be development meet the requirements of mechanical properties and low price of electro-hydraulic servo valve, servo control system was applied to the mechanical hand.3.Development of modular robotsVariable application manipulator from the characteristics of the manipulator itself, more adapted to the product type, equipment updates, many varieties, small batch, but its cost is high, the special manipulator and cheap, but the scope is limited. Therefore, for some special purpose, you need special design, special processing, thus improving the product cost. In order to adapt to the request of the application field of classify, the structure of the manipulator can be designed to the form of combination. Modular manipulator is a common parts according to the requirement of the job, select necessary to accomplish the function of the unit components, based on the base of combination, deserve to go up with adaptive control part, namely the manipulator with special requirements can be completed. It can simplify the structure, take into account the specificity and design on the use of generality, more in the series design and organization of standardization, specialized production, to improve quality and reduce cost of the manipulator, is a kind of promising manipulator4. Has a "vision" and "touch" of so-called "intelligent robots"For artificial has flexible operation and the need for judgment of the situation, industrial manipulator is very difficult to replace human labor. Such as in the working process of the accident, disorders and conditions change, etc., manipulator cannot be automatically distinguish correct, but to stop, after waiting for people to rule outaccident can continue to work. As a result, people puts forward higher requirements on mechanical hand, hope to make it a "vision", "touch", etc, make it to the judgment, the choice of object, can be continuously adjusted to adapt to changing conditions, and can perform a "hand - eye coordination. This requires a computer can handle a lot of information, require them to exchange of information with machine "dialogue".This "vision", "touch" feedback, controlled by computer, is one part of the "smart" mechanism is called "intelligent robots". Is the so-called "smart" includes: the function of recognition, learning, memory, analysis, judgment. And recognition is through the "visual", "touch" and "hearing" feel "organ" of cognitive object.Which has the function of sensory robot, its performance is perfect, can accurately clamping arbitrary azimuth objects, determine an object, weight, work over obstacles, the clamping force is measured automatically, and can automatically adjust, suitable for engaged in the operation of the complex, precision, such as assembly operation, it has a certain development prospects.Intelligent robots is an emerging technology, the study of it will involve the electronic technology, control theory, communication technology, television technology, spatial structure and bionic mechanical discipline. It is an emerging field of modern automatic control technology. With the development of science and intelligent robots will replace people to do more work.工业机械手随着我国工业生产的飞跃发展,自动化程度的迅速提高,实现工件的装卸、转向、输送或是操持焊枪、喷枪、扳手等工具进行加工、装配等作业的自动化,应越来越引起人们的重视。
泵站相关中英文对照资料
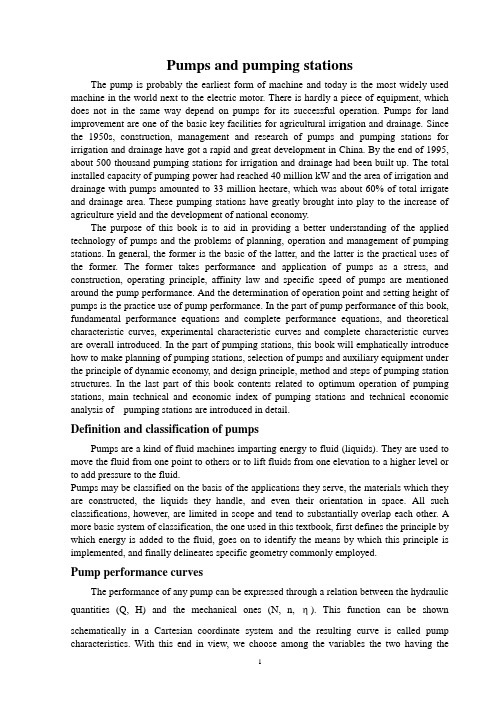
Pumps and pumping stationsThe pump is probably the earliest form of machine and today is the most widely used machine in the world next to the electric motor. There is hardly a piece of equipment, which does not in the same way depend on pumps for its successful operation. Pumps for land improvement are one of the basic key facilities for agricultural irrigation and drainage. Since the 1950s, construction, management and research of pumps and pumping stations for irrigation and drainage have got a rapid and great development in China. By the end of 1995, about 500 thousand pumping stations for irrigation and drainage had been built up. The total installed capacity of pumping power had reached 40 million kW and the area of irrigation and drainage with pumps amounted to 33 million hectare, which was about 60% of total irrigate and drainage area. These pumping stations have greatly brought into play to the increase of agriculture yield and the development of national economy.The purpose of this book is to aid in providing a better understanding of the applied technology of pumps and the problems of planning, operation and management of pumping stations. In general, the former is the basic of the latter, and the latter is the practical uses of the former. The former takes performance and application of pumps as a stress, and construction, operating principle, affinity law and specific speed of pumps are mentioned around the pump performance. And the determination of operation point and setting height of pumps is the practice use of pump performance. In the part of pump performance of this book, fundamental performance equations and complete performance equations, and theoretical characteristic curves, experimental characteristic curves and complete characteristic curves are overall introduced. In the part of pumping stations, this book will emphatically introduce how to make planning of pumping stations, selection of pumps and auxiliary equipment under the principle of dynamic economy, and design principle, method and steps of pumping station structures. In the last part of this book contents related to optimum operation of pumping stations, main technical and economic index of pumping stations and technical economic analysis of pumping stations are introduced in detail.Definition and classification of pumpsPumps are a kind of fluid machines imparting energy to fluid (liquids). They are used to move the fluid from one point to others or to lift fluids from one elevation to a higher level or to add pressure to the fluid.Pumps may be classified on the basis of the applications they serve, the materials which they are constructed, the liquids they handle, and even their orientation in space. All such classifications, however, are limited in scope and tend to substantially overlap each other. A more basic system of classification, the one used in this textbook, first defines the principle by which energy is added to the fluid, goes on to identify the means by which this principle is implemented, and finally delineates specific geometry commonly employed.Pump performance curvesThe performance of any pump can be expressed through a relation between the hydraulic quantities (Q, H) and the mechanical ones (N, n, η). This function can be shown schematically in a Cartesian coordinate system and the resulting curve is called pump characteristics. With this end in view, we choose among the variables the two having thegreatest importance in the study of the operating conditions, while the other quantities are considered as parametrical. In practice, we study the relations of head, power and efficiency versus flow rate under a certain rotational speed. Thus we have: the pumping head characteristic curve, H=f (Q ); the power characteristic curve, N=f (Q ); the efficiency characteristic curve, η=f (Q ) etc. A complete characteristic includes all these separatecurves.These curves can be got by theory. But the real performance curves are difficult to get exactly by theory analysis. They usually are got by experiments due to imperfection of the theory and the complex of the flow within the impeller.The performance characteristic curves are very useful to three interested parties: (1) the pump designer, for choosing the final structural solution after lab and actual tests; (2) the pumping station designer, to help him in the choice of the most adequate pump for application; (3) the user, to help him in the choice of the best operating conditions.Usually, there are 6 kinds of characteristic curves associated with pumps, namely the theoretical, real, relative, universal, comprehensive and complete characteristic curves. Pump housePump house is a major structure in the pumping station for the installation of main pumping units and their auxiliary facilities. Proper design can not only provide a better working condition for mechanical and electrical equipment and workers, but also is of significance for the reduction of project cost and safe operation.Pump house design includes selection of structural types, arrangement of internal equipment, determination of sizes of different parts, calculation of whole stability and the analysis. Types of pump houseDetermination of the type of pump house depends on the properties of pumping stations (permanent or transitional ), pump type (size, suction capacity, horizontal or vertical shaft, specific speed, etc), water lever fluctuation of water source, subgrade, etc. According to the structural types of the foundation, stationary pump houses may be classified into four types, namely, separate footing, dry-pit, wet-pit and block foundation. There are also movable pump house, such as pump boat and pump vehicle.The principle characteristic of separate-footing pump house lies in that there is no underwater structure. To prevent vibrations and mutual interference, each pump unit has its own footing, and it is separated from the foundation of the pump house.泵与泵站泵可能是最早的机器形式,如今在全世界除了电动机之外应用最为广泛。
- 1、下载文档前请自行甄别文档内容的完整性,平台不提供额外的编辑、内容补充、找答案等附加服务。
- 2、"仅部分预览"的文档,不可在线预览部分如存在完整性等问题,可反馈申请退款(可完整预览的文档不适用该条件!)。
- 3、如文档侵犯您的权益,请联系客服反馈,我们会尽快为您处理(人工客服工作时间:9:00-18:30)。
中英文对照资料外文翻译文献附件1:外文资料翻译译文旋转泵旋转泵应用于不同的设计中,在流体动力系统中极其常用。
今天最常用的旋转泵是外齿轮泵、内齿轮泵、摆线转子泵、滑动叶片泵和螺旋泵。
每种类型的泵都有优点,适合于特定场合的应用直齿齿轮泵,这种泵有两个啮合的齿轮在密封壳体内转动。
第一个齿轮即主动轮的回转引起第二个齿轮即从动轮的回转。
驱动轴通常连接到泵上面的齿轮上。
当泵首次启动时,齿轮的旋转迫使空气离开壳体进入排油管。
这种泵内空气运动使泵吸入口处形成了真空,于是外部油箱的液体在大气压的作用下,由泵的入口进入,聚集在上下齿轮和泵壳体之间,齿轮连续的旋转使液体流出泵的出口。
直齿齿轮泵的压力的升高是由挤压啮合齿轮和腔体内的液体产生的。
当齿轮脱开啮合时,腔内形成真空,使更多的液体被吸入泵内。
直齿齿轮泵是定排量的元件,当轴转速不变时,输出流量恒定。
只有一种方法即改变输入轴的转速,能调节这种直齿齿轮泵的排量。
现代应用在流体动力系统的齿轮泵的压力可达3000psi。
图示为直齿齿轮泵的典型特性曲线。
这些曲线表明了泵在不同速度下的流量和输入功率。
当速度给定时,流量曲线接近于一条水平的直线。
泵的流量随出口压力的升高而稍有降低,这是由于泵的出油口到吸油口的齿轮径向泄漏所增加而造成的。
渗漏有时定义为泄漏,泵出口压力的增加也会使泄漏增加。
表征泵的出口压力和流量之间关系曲线常叫做水头流量曲线或泵的HQ曲线;泵的输入功率和泵流量关系曲线叫做功率流量特性曲线或PQ曲线。
直齿齿轮泵的输入功率随输入速度和出口压力的增加而增加。
随着齿轮泵速度的增加,流量(加仑/分)也增加。
于是在出口压力为120psi,转速为200rpm时,输入功率是5马力。
在转速为600rpm时,输入功率是13马力。
纵坐标压力是120psi,横坐标是200rpm和600rpm时,在HQ曲线上可以读出相应的流量分别为40gpm和95gpm。
图示是直齿齿轮泵在粘度不变时的情况。
随着流体粘度的增加(即流体变稠,不易流动),齿轮泵的流量降低。
粘稠的流体在油泵高速运转时,因为这种流体在油泵中不能迅速进入泵体完全充满真空区,所以油流量受到限制。
图示为在流体动力系统中流体粘度的增大对旋转泵工作情况的影响。
当流体的粘度值为100SSU,出口压力为80psi时,泵流量为220gpm。
当流体的粘度值为500SSU时,泵流量减少到150gpm。
由功率特性曲线可知,泵输入功率也会增加可以用齿轮或其他内部元件每转一圈输出多少加仑来表示泵的流量。
如果封闭定量泵的出口,则出口压力将会增加,直至驱动马达停止或泵内其他部分或排油管破裂。
由于存在着破裂的危险,几乎所有的流体动力系统都安装压力溢流阀。
这种溢流阀可安装在泵内,也可安装在排油管路。
滑动式叶片泵:这些泵有大量的叶片,叶片能在转子的槽内自由的滑进滑出。
当驱动转子时,离心力,弹簧或压力油使叶片伸出槽子,顶在泵壳体的内腔或凸轮环上。
随着转子的旋转,叶片之间的流体经过吸油口时,完成吸油。
流体顺着泵壳体到达排出口。
在排出口,流体被排出,进入排油管。
图示的滑动式叶片泵中的叶片安装在椭圆形的腔内。
当转子开始旋转时,离心力使叶片伸出槽子。
同时叶片又受到其底部腔内压力油的作用力,压力油来源于槽子端部的配流盘。
吸油口通过A和A1口相通,他们位于直径的相对位置。
同样两排油口位于类似的位置。
油口这样配置,使叶片转子保持压力平衡,从而使轴承不受重载影响。
当转子逆时针旋转时,从吸油管出来的流体进入A和A1口,聚集在叶片之间,沿周向流动后,通过B和B1口排出。
这样设计的泵压力可达2500psi。
的泵必须分级才能达到这么大的压力,而现在用一级泵即可达到。
在转子上应用均流均压阀可以达到高压。
转速通常限制在2500rpm这是因为考虑到离心力和凸轮环表面叶片之间的磨损。
图示为泵在转速为1200rpm粘度在100F的条件下的特性曲线。
每个槽内安装两个叶片可以控制其作用于壳体内部和凸轮环上的力。
双叶片会产生更紧的密封,能减少从排油口到吸油口之间的泄漏这种入口和出口相对应的设计也能维持液压平衡。
这些都是定量泵。
不改变转速就不能改变叶片泵的流量,除非油泵采用特殊设计。
图示为滑动式变量叶片泵。
它不用双吸油和排油口。
转子在压力腔内转动,转子形成的偏心量是可调的。
随着偏心的程度或偏心率的变化,流体的流量也随着变化。
图示为转子在旋转180°范围内,产生一真空度以便于油液进入,同时压油区也在180°范围内旋转。
吸油区和压油区的起始段梢有重叠。
图示,在最小的工作压力下可以得到最大的流量。
随着压力的升高,流量按预设的规律减少。
当流量减到最小值,压力增大到最大值。
泵只需要提供补充回路中元件滑动配合间隙中泄漏流体这种变量泵的设计可以保护管路,溢流阀不是必须的。
其他回路中,为阻止局部压力超过正常压力水平,可以用安全阀或溢流阀来控制为了自动控制流量,采用可变弹簧负载调节器。
安装这种调节器,泵的出口压力作用于活塞或定子内表面,压缩的弹簧产生位移。
如果泵的出口压力高于调节器弹簧的设定值时,弹簧被压缩。
这使压力环(定子)移动,减少相对于定子的偏心量,于是,泵的流量减少,得到所需的压力。
这种油泵设计的出口压力在100psi 和2500psi之间。
图示为变量泵补偿器的特性,标出输入功率值,可以准确计算所需的输入功率。
变量泵可以预先设定不同压力值的变化规律。
高低压泵控制既能提供有效的卸荷回路,也能为先导控制回路提供足够压力图示阴影区域为变量泵在背压100psi压力下的闭式回路。
油液以100psi卸荷阀或溢流阀排出,可以维持正常的控制回路压力,这些是消耗的功率。
两级压力控制回路包括:先导液压控制和电磁控制。
图示负号表示电磁铁不带电,先导控制油回油箱。
于是泵排出的控制油的力小于调节器弹簧力,所以得到最小压力。
图示正号为电磁铁带电,控制油的力大于调节器弹簧力。
与简单的溢流阀原理一样,小球和弹簧决定控制力的大小。
这样预先设定最大工作压力。
另一种两级压力控制系统是利用所谓的差动卸荷调节器。
它应用于高低压或双泵回路中。
调节器通过压力传感器自动卸荷大流量泵以达到最小的空载压力设定值。
空载压力指的是由于变量泵控制机构工作所形成的特定压力。
泵的实际空载流量等于系统的泄漏量与控制流量之和。
当泵空载时,即使液压系统在提供加紧或保压作用,也不会需要较大的功率。
调节器是液压操纵的,差动活塞带有双压力控制,当外部控制压力作用于控制卸荷口时,差动活塞允许完全卸荷。
空载压力的最小设定值由调节器主弹簧A控制。
最大压力由溢流阀调节点B控制。
调节器的操作压力由大容积泵提供,从小孔C进入。
为了说明如何使用这种装置,假设回路需要1000psi的最大压力,由一个5-gpm 来提供。
在压力达到500psi时,需要大流量(40gpm),继续上升到1000psi,流量减少。
由流量为40-gpm的带有卸荷调节器的泵组成的双泵系统可满足要求。
我们可以把40-gpm的泵从500psi卸荷压力调整至200psi最小设定压力(或另一需求值),这样5-gpm泵可以使回路达到1000psi或更高压力。
图中为双泵系统控制压力源。
由一个40-gpm的泵提供调节器腔内压力,就可以达到最大设定压力。
弹簧设定力加上调节器的腔内压力共同决定了40-gpm泵的最大压力。
第二个控制源是特殊的回路,它能达到1000psi。
控制油通过小孔D进入调节器作用于卸荷活塞E。
活塞E面积比安全阀中提动阀F的有效面积大15%。
因此卸荷差动力大约为15%。
调节器将在500psi卸荷,会在500psi以下15%或425psi时起作用。
这里所谓的卸荷,指的是40-gpm的泵无输出量。
随着回路中压力从0到500psi的增加,调节器腔内的压力也随着增加,直到溢流阀的设定值时,溢流阀打开,流体流出油箱。
调节器腔内的压力降是最大的叠加值,允许油泵达到卸荷状态。
同时,当系统压力继续增加超过700psi时,导致活塞E最底部的压力比顶部的压力大。
活塞使提升阀F完全打开,溢流提升阀全部开启导致调节器腔内压力进一步下降至零。
流体通过小孔C进入调节器腔,经过溢流提升阀直接回油箱,不增加调节器腔内的压力。
40-gpm的泵卸荷压力可以减小至更低的设定值。
调整卸荷调节器,40-gpm的泵达到卸荷。
随着压力到1000psi,回路的流量减至5gpm。
在1000psi时,5-gpm 泵也达到卸荷设定,于是流量仅仅维持系统压力。
在500psi时,40-gpm的油泵卸荷。
需要600psi的系统压力把40gpm的泵卸荷到最小压力200psi。
600psi的先导控制油通过孔D进入并作用于差动活塞E。
在500psi时,泵流量减少到零。
100psi 的附加压力需要完全打开提升阀,使调节器腔内的压力减小至零。
当回路压力减小时,两个泵以同样的方式来工作。
附件2:外文原文Rotary pumpsThese are built in many different designs and are extremely popular in modern fluid-power system. The most common rotary-pump designs used today are spur-gear, generated-rotary , sliding-vane ,and screw pump ,each type has advantages that make it the most suitable for a given application .Spur-gear pumps. these pumps have two mating gears are turned in a closely fitted casing. Rotation of one gear ,the driver causes the second ,or follower gear, to turn . the driving shaft is usually connected to the upper gear of the pump .When the pump is first started ,rotation of gears forces air out the casing and into the discharge pipe. this removal of air from the pump casing produces a partial vacuum on the pump inlet ,here the fluid is trapped between the teeth of the upper and lower gears and the pump casing .continued rotation of the gears forces the fluid out of the pump discharge .Pressure rise in a spur-gear pump is produced by the squeezing action on the fluid ad it is expelled from between the meshing gear teeth and casing ,.a vacuum is formed in the cavity between the teeth ad unmesh, causing more fluid to be drawn into the pump ,a spur-gear pump is a constant-displacement unit ,its discharge is constant at a given shaft speed. the only way the quantity of fluid discharge by a spur-gear pump of type in figure can be regulated is by varying the shaft speed .modern gear pumps used in fluid-power systems develop pressures up to about 3000psi.Figure shows the typical characteristic curves of a spur-gear rotary pump. These curves show the capacity and power input for a spur-gear pump at various speeds. At any given speed the capacity characteristic is nearly a flat line the slight decrease incapacity with rise in discharge pressure is caused by increased leakage across the gears from the discharge to the suction side of the pump. leakage in gear pumps is sometimes termed slip. Slip also increase with arise pump discharge pressure .the curve showing the relation between pump discharge pressure and pump capacity is often termed the head-capacity or HQ curve .the relation between power input and pump capacity is the power-capacity or PQ curve .Power input to a squr-gear pump increases with both the operating speed and discharge pressure .as the speed of a gear pump is increased. Its discharge rate in gallons per minute also rise . thus the horsepower input at a discharge pressure of 120psi is 5hp at 200rpm and about 13hp at 600rpm.the corresponding capacities at these speed and pressure are 40 and 95gpm respectively, read on the 120psi ordinate where it crosses the 200-and 600-rpm HQ curves .Figure is based on spur-gear handing a fluid of constant viscosity , as the viscosity of the fluid handle increases (i.e. ,the fluid becomes thicker and has more resistance to flow ),the capacity of a gear pump decreases , thick ,viscous fluids may limit pump capacity t higher speeds because the fluid cannot into the casing rapidly enough fill it completely .figure shows the effect lf increased fluid biscosity on the performance of rotary pump in fluid-power system .at 80-psi discharge pressure the pp has a capacity lf 220gpm when handling fluid of 100SSU viscosity lf 500SSU . the power input to the pump also rises ,as shown by the power characteristics.Capacity lf rotary pump is often expressed in gallons per revolution of the gear or other internal element .if the outlet of a positive-displacement rotary pump is completely closed, the discharge pressure will increase to the point where the pump driving motor stalls or some part of the pump casing or discharge pipe ruptures .because this danger of rupture exists systems are filled with a pressure –relief valve. This relief valve may be built as of the pump or it may be mounted in the discharge piping.Sliding-Vane Pumps,These pumps have a number of vanes which are free to slide into or out of slots in the pup rotor . when the rotor is turned by the pump driver , centrifugal force , springs , or pressurized fluid causes the vanes to moveoutward in their slots and bear against the inner bore of the pump casing or against a cam ring . as the rotor revolves , fluid flows in between the vanes when they pass the suction port. This fluid is carried around the pump casing until the discharge port is reached. Here the fluid is forced out of the casing and into the discharge pipe.In the sliding-vane pump in Figure the vanes in an oval-shaped bore. Centrifugal force starts the vanes out of their slots when the rotor begins turning. The vanes are held out by pressure which is bled into the cavities behind the vanes from a distributing ring at the end of the vane slots. Suction is through two ports A and AI, placed diametrically opposite each other. Two discharge ports are similarly placed. This arrangement of ports keeps the rotor in hydraulic balance, reliving the bearing of heavy loads. When the rotor turns counterclockwise, fluid from the suction pipe comes into ports A and AI is trapped between the vanes, and is carried around and discharged through ports B and BI. Pumps of this design are built for pressures up to 2500 psi. earlier models required staging to attain pressures approximating those currently available in one stage. Valving , uses to equalize flow and pressure loads as rotor sets are operated in series to attain high pressures. Speed of rotation is usually limited to less than 2500rpm because of centrifugal forces and subsequent wear at the contact point of vanes against the cam-ring surface..Two vanes may be used in each slot to control the force against the interior of the casing or the cam ring. Dual vanes also provide a tighter seal , reducing the leakage from the discharge side to the suction side of the pump . the opposed inlet and discharge port in this design provide hydraulic balance in the same way as the pump, both these pumps are constant-displacement units.The delivery or capacity of a vane-type pump in gallons per minute cannot be changed without changing the speed of rotation unless a special design is used. Figure shows a variable-capacity sliding-vane pump. It dose not use dual suction and discharge ports. The rotor rums in the pressure-chamber ring, which can be adjusted so that it is off-center to the rotor. As the degree of off-center or eccentricity is changed, a variable volume of fluid is discharged. Figure shows that the vanes create a vacuum so that oil enters through 180 of shaft rotation. Discharge also takes placethrough 180 of rotation. There is a slight overlapping of the beginning of the fluid intake function and the beginning of the fluid discharge.Figure shows how maximum flow is available at minimum working pressure. As the pressure rises, flow diminishes in a predetermined pattern. As the flow decreases to a minimum valve, the pressure increases to the maximum. The pump delivers only that fluid needed to replace clearance floes resulting from the usual slide fit in circuit components.A relief valve is not essential with a variable-displacement-type pump of this design to protect pumping mechanism. Other conditions within the circuit may dictate the use of a safety or relief valve to prevent localized pressure buildup beyond the usual working levels.For automatic control of the discharge , an adjustable spring-loaded governor is used . this governor is arranged so that the pump discharge acts on a piston or inner surface of the ring whose movement is opposed by the spring . if the pump discharge pressure rises above that for which the by governor spring is set , the spring is compressed. This allows the pressure-chamber ring to move and take a position that is less off center with respect to the rotor. The pump theb delivers less fluid, and the pressure is established at the desired level. The discharge pressure for units of this design varies between 100 and 2500psi.The characteristics of a variable-displacement-pump compensator are shown in figure. Horsepower input values also shown so that the power input requirements can be accurately computed. Variable-volume vane pumps are capacity of multiple-pressure levels in a predetermined pattern. Two-pressure pump controls can provide an efficient method of unloading a circuit and still hold sufficient pressure available for pilot circuits.The black area of the graph of figure shows a variable-volume pump maintaining a pressure of 100psi against a closed circuit. Wasted power is the result of pumping oil at 100psi through an unloading or relief valve to maintain a source of positive pilot pressure. Two-pressure –type controls include hydraulic, pilot-operated types and solenoid-controlled, pilot-operated types. The pilot oil obtained from thepump discharge cannot assist the governor spring. Minimum pressure will result. The plus figure shows the solenoid energized so that pilot oil assists compensator spring. The amount of assistance is determined by the small ball and spring, acting as a simple relief valve. This provides the predetermined maximum operating pressure.Another type of two-pressure system employs what is termed a differential unloading governor. It is applied in a high-low or two-pump circuit. The governor automatically, Through pressure sensing, unloads the large volume pump to a minimum deadhead pressure setting. Deadhead pressure refers to a specific pressure level established as resulting action of the variable-displacement-pump control mechanism. The pumping action and the resulting flow at deadhead condition are equal to the leakage in the system and pilot-control flow requirements. No major power movement occurs at this time, even though the hydraulic system may be providing a clamping or holding action while the pump is in deadhead position The governor is basically a hydraulically operated, two-pressure control with a differential piston that allows complete unloading when sufficient external pilot pressure is applied to pilot unload port.The minimum deadhead pressure setting is controlled by the main governor spring A. the maximum pressure is controlled by the relief-valve adjustment B. the operating pressure for the governor is generated by the large-volume pump and enters through orifice C.To use this device let us assume that the circuit require a maximum pressure of 1000psi, which will be supplied by a 5-gpm pump. It also needs a large flow (40gpm) at pressure up to 500psi; it continues to 1000pso at the reduced flow rate. A two-pump system with an unloading governor on the 40-gpm pump at 500psi to a minimum pressure setting of 200psi (or another desired value) , which the 5-gpm pump takes the circuit up to1000psi or more.Note in figure that two sources of pilot pressure are required. One ,the 40-gpm pump, provides pressure within the housing so that maximum pressure setting can be obtained. The setting of the spring, plus the pressure within the governor housing, determines the maximum pressure capacity of the 40-gpm pump. The second pilotsource is the circuit proper, which will go to 1000psi. this pilot line enters the governor through orifice D and acts on the unloading piston E . the area of piston E is 15 percent greater than the effective area of the relief poppet F. the governor will unload at 500psi and be activated at 15percent below 500psi, or 425psi. By unloading, we mean zero flow output of the 40-gpm pump.As pressure in the circuit increases from zero to 500psi, the pressure within the governor housing also increases until the relief-valve setting is reached, at which time the relief valve cracks open, allowing flow to the tank.The pressure drop in the hosing is a maximum additive value, allowing the pump to deadhead. Meanwhile, the system pressure continues to rise above 700psi, resulting in a greater force on the bottom of piston E than on the top. The piston then completely unseats poppet F, which results in a further pressure drop within the governor horsing to zero pressure because of the full-open position of the relief poppet F. flow entering the housing through orifice is directed to the tank pass the relief poppet without increasing the pressure in housing. The deadhead pressure of the 40-gpm pump then decreases to the lower set value. Thus , at the flow rate to the unloading governor ,the 40gpm pump goes to deadhead. The flow rate to the circuit decreases to 5gpm as the pressure to 1000psi, the 5-gpm pump is also at its deadhead setting, thus only holding system pressure.The 4-gpm pump unloads its volume at 500psi. It requires a system pressure of 600psi to unload the 40-gpm pump to its minimum pressure of 200psi. the 600-psi pilot supply enters through orifice D and acts on the differential piston E. The pumps volume is reduced to zero circuit-flow output at 500psi. The additional 100-psi pilot pressure is required to open poppet F completely and allow the pressure within the housing to decrease to zero.As circuit pressure decreases ,both pumps come back into service in a similar pattern.。