浅谈增碳剂的使用
铸造中电炉增碳剂使用方法建议

关于Desulco 9018作微调,有以下使用建议:
如一炉铁水只出一包铁水,可选用炉内增碳(方案一),9018吸收率能达
到90%;如一炉铁水需出多包水,可选用包内增碳(方案二),9018吸收
率能达到70-80%; 9018做微调后,尽量在30分钟内浇注,这样能起到预
处理作用,提升铁液形核能力。
铁水化清后测碳,如发现碳低,进行微调,微调增碳时增碳量最好不超过
0.3%。
方案一(炉内增碳):
∙微调前扒渣。
∙按90%吸收率计算所加9018用量(前期试用时,用量可适当增加),加入到炉内铁水表面。
∙开动电炉使铁水翻花2-3分钟,观察9018变红直至全部溶入铁水,电炉调至保温功率。
∙2-3分钟后热分析仪测碳成分是否到达目标值。
方案二(包内增碳):
∙出铁前扒渣。
∙按图示将计算好的9018增碳剂放置在覆盖剂上方,如球化包有双坑,可将9018放置在没有球化剂的一个坑。
∙将铁水注入球化包,让铁水先流入加增碳剂的坑内,确保铁水先与增碳剂接触。
∙球化完成后扒渣。
增碳剂的使用方法

增碳剂的使用方法1、炉内投入法:增碳剂适于在感应炉中熔炼使用,但依据工艺要求具体使用也不尽相同。
(1)在中频电炉熔炼中使用增碳剂,可按配比或碳当量要求随料加入电炉中下部位,回收率可达95%以上;(2)铁液熔清如果碳量不足调整碳分时,先打净炉中熔渣,再加增碳剂,通过铁液升温,电磁搅拌或人工搅拌使碳溶解吸收,回收率可在90左右,如果采用低温增碳工艺,即炉料只熔化一部分,熔化的铁液温度较低的情况下,全部增碳剂一次性加入铁液中,同时用固体炉料将其压入铁液中不让其露出铁液表面。
这种方法铁液增碳可达1.0%以上。
2、炉外增碳:(1)包内喷石墨粉选用石墨粉做增碳剂,吹入量为40kg/t,预期能使铁液含碳量从2%增到3%。
随着铁液碳含量逐渐升高,碳量利用率下降,增碳前铁液温度1600℃,增碳后平均为1299℃。
喷石墨粉增碳,一般采用氮气做载体,但在工业生产条件下,用压缩空气更方便,而且压缩空气中的氧燃烧产生CO,化学反应热可补偿部分温降,而且CO的还原气氛利于改善增碳效果。
(2)出铁时使用增碳剂可将100—300目的石墨粉增碳剂放到包内,或从出铁槽随流冲入,出完铁液后充分搅拌,尽可能使碳溶解吸收,碳的回收率在50%左右。
宁夏宏辉炭素制品有限公司生产的无烟煤增碳剂具有低硫、低灰,含炭量高易吸收等特点。
一、增碳剂的加入时间不能忽视。
增碳剂的加入时间若过早,容易使其附着在炉底附近,而且附着炉壁的增碳剂又不易被熔入铁液。
与之相反,加入时间过迟,则失去了增碳的时机,造成熔炼、升温时间的迟缓。
这不仅延迟了化学成分分析和调整的时间,也有可能带来由于过度升温而造成的危害。
因此,增碳剂还是在加入金属炉料的过程中一点一点地加入为好。
如在一次加入量过大的情况下,可以结合感应电炉时采用的铁液过热操作结合考虑,保证增碳剂在铁液中的吸收时间10Min,一方面通过电磁搅拌作用使增碳剂充分扩散吸收,保证吸收效果。
另一方面可以减少增碳剂中带入的含氮量。
增碳剂使用注意事项

原文地址:中频电炉增碳剂使用注意事项作者:微笑现在大家对于感应电炉熔炼灰铁,球铁,在铸造熔炼中注重预处理,提高铁水的冶金质量,以及大量使用废钢做合成铸铁都比较熟悉了,增碳剂,碳化硅,高含钡的硅铁预处理剂的使用也逐步广泛,对于增碳剂来讲,结合最近得到的信息和以前实际经验,加上前人的发表文章,我感觉在熔炼中要注意几点: 1。
增碳剂的成分,应该以氮含量的多少来区分,则使用时,选择什么级别的氮含量,很重要!!!我们现在以感应电炉加入60%以上的废钢,熔炼合成铸铁,,由于其中钛等有害元素很低,所以应该使用低氮的增碳剂。
我在以前的帖子里面介绍过,美国,日本高端客户对普通灰铁的验收,需要化验铸铁里面氮,钛,铅,砷等等有害元素的含量,(机械性能方面,不仅要做抗拉,硬度,还要做灰铁的屈服强度),其中对于氮的含量,一般希望在80-120PPM最好,这时如果你使用高氮增碳剂(一般都属于低端增碳剂产品),由于铁水中钛的含量很低,不可能消耗大量的氮,使铸件容易因为氮含量太高而出现大量气孔,气缩或者有关缺陷,这种现象,已经在我以前工作过的单位发生,许多专家在其发表的文章中也谈过,增碳剂质量不好带给他们的重大损失。
(具体是谁?记不清了,好像是一位姓金的专家在铸造杂志上写过)。
很多铸造朋友以为,增碳剂硫量较高,不会影响普通灰铁(孕育铸铁)的质量,但是增碳剂硫量高,伴随着其中的氮也会很高,带来质量问题。
2。
99年在台湾首屋(台湾帝屋在青岛的工厂)工作时,其库房里面增碳剂很多,标牌注名只有高氮,中氮,低氮三种之分,但是根本不知其中缘故,现在经历多了,才逐步体会到此点。
当然很多东西在国内还在逐步适应,特别是高氮增碳剂,也在大量使用,石墨化不好的石油焦,精煤等等,这些低端产品针对什么铸铁熔炼使用?是否是高含钛铸铁使用?还需要今后逐步获得经验。
石墨化不好的增碳剂,加入铁水,一是吸收率低,慢,二是渣子多,三是其他有害元素影响铁水质量,希望大家注意! 3。
回转炉煅烧增碳剂

回转炉煅烧增碳剂1. 介绍回转炉煅烧增碳剂的概念和作用回转炉煅烧增碳剂是一种用于钢铁生产中的辅助材料,主要用于增加炉料中的碳含量。
它由多种原料混合而成,经过特定的工艺处理后形成颗粒状,方便在回转炉中使用。
回转炉煅烧增碳剂在钢铁冶炼过程中起到了重要的作用,可以提高钢铁的质量和生产效率。
2. 回转炉煅烧增碳剂的原料和制备工艺回转炉煅烧增碳剂的原料主要包括焦炭、石墨、石油焦、木炭等。
这些原料经过破碎、筛分等处理后,按照一定比例混合,再进行加热、煅烧等工艺处理,最终形成所需的颗粒状增碳剂。
制备工艺主要包括以下几个步骤: 1. 原料准备:将焦炭、石墨、石油焦、木炭等原料进行破碎、筛分等处理,确保原料的粒度符合要求。
2. 混合配比:根据所需的成分比例,将不同原料按照一定比例混合。
3. 加热处理:将混合后的原料放入高温炉中进行加热处理,使其达到一定的温度。
4. 煅烧处理:将加热后的原料进行煅烧处理,使其形成颗粒状增碳剂。
5. 冷却和包装:将煅烧后的增碳剂进行冷却,并进行包装,以便于储存和运输。
3. 回转炉煅烧增碳剂的作用机理回转炉煅烧增碳剂在钢铁冶炼过程中的作用主要有两个方面:3.1 增碳作用回转炉煅烧增碳剂中的原料富含碳元素,当增碳剂投入回转炉中时,其碳元素会与炉料中的铁元素进行反应,生成高碳的铁合金。
这样可以增加炉料中的碳含量,提高钢铁的碳含量,使钢铁的强度、硬度等力学性能得到提高。
3.2 清洁作用回转炉煅烧增碳剂中的原料中还含有一定比例的灰分和硫等杂质。
当增碳剂投入回转炉中时,这些杂质会与炉料中的杂质进行吸附、还原等反应,从而减少钢铁中的杂质含量,提高钢铁的纯净度和质量。
4. 回转炉煅烧增碳剂的应用回转炉煅烧增碳剂主要应用于钢铁冶炼过程中。
在回转炉中,增碳剂可以通过喷吹、撒播等方式加入,与炉料一起进行反应。
增碳剂的投入量和投入时间可以根据具体的冶炼工艺和产品要求进行调整。
通过使用回转炉煅烧增碳剂,可以有效提高钢铁的质量和生产效率。
增碳剂标准

增碳剂标准
《增碳剂标准》
一、定义
增碳剂是一种促进机械加工表面硬度和抗磨性,增加加工的抗腐蚀性的一种材料。
由于碳原子在晶体中的分布均匀性,因而增碳剂能够有极大的提高材料的抗磨性,抗磨性提高了30%~50%。
二、标准要求
1、增碳剂的碳含量应不低于99.5%。
2、增碳剂的含氮量应不超过0.5%。
3、增碳剂的挥发性应为0.1%。
4、增碳剂的粒径分布应均匀,其粒径应大于1um,且小于5um。
5、增碳剂也可使用高碳含量的粉煤灰替代,高碳含量的粉煤灰的碳含量应不低于98.5%,含氮量不超过1%。
三、增碳剂的使用规则
1、增碳剂的粒径必须满足上述要求,以免造成错误的结果。
2、增碳剂应经过碾磨,以降低其粒径,以保证其加工的均匀性和均一性。
3、增碳剂的使用量应根据不同的加工条件来确定,一般为10%~20%,最高不超过25%。
4、增碳剂需与加工材料同时进入加工设备,以保证加工可控性。
5、增碳剂使用完毕后,应及时清除,以防止因杂质尘埃对加工设备和加工材料造成污染。
炼钢用高效增碳剂_概述及解释说明

炼钢用高效增碳剂概述及解释说明1. 引言1.1 概述炼钢是一种重要的工业生产过程,其中一个关键步骤就是增碳。
在过去的几十年里,为了提高炼钢效率和质量,不断寻求高效增碳剂成为了一个研究热点。
本文将对炼钢用高效增碳剂进行全面概述和解释说明。
1.2 文章结构本文将按照以下结构展开对炼钢用高效增碳剂的介绍和分析:引言部分概述文章的目的和结构;接着介绍炼钢用高效增碳剂的定义、作用以及常见类型与特点;然后阐述使用方法并提供注意事项;之后探讨影响增碳剂选择与研发的主要因素,并对当前常用增碳剂种类进行分析,并介绍最新的研发进展;接下来讲解应用于增碳剂生产中的煤气化技术,包括其概述、优势与挑战以及在增碳剂生产中的研究进展;最后总结文章主要观点与认识提炼,并对未来炼钢用高效增碳剂发展进行展望。
1.3 目的本文的目的是为了全面介绍和解释炼钢用高效增碳剂,包括其定义、作用、常见类型与特点、使用方法与注意事项、选择与研发现状,以及煤气化技术在增碳剂生产中的应用。
通过本文的阐述,读者可以更加深入地理解和掌握炼钢用高效增碳剂相关知识,并对未来该领域的发展进行展望。
2. 炼钢用高效增碳剂2.1 定义与作用:炼钢用高效增碳剂是指在炼钢过程中用于提高钢材中碳含量的一种添加剂。
由于碳元素在钢材中的含量对其物理和化学性能具有重要影响,因此增加钢材的碳含量可以改善其硬度、强度和耐磨性等特性。
高效增碳剂作为一种专门设计的添加剂,具有提高增碳效率、降低生产成本和改善产品质量等优点。
2.2 常见类型与特点:目前市场上常见的高效增碳剂主要包括焦炭、纯净焦油和人工石墨等。
这些增碳剂根据其原料来源和制备工艺不同,具有各自的特点。
焦炭是最常用的一种高效增碳剂,它由煤炭经过高温干馏得到。
焦炭具有较高的固定碳含量,并且灰分较少,因此可以有效地提供更多的可利用的纯粹碳源。
此外,焦炭还具有低挥发分和固态结构等特点,使其在炉料中具有较好的耐高温性能和流动性。
纯净焦油是从高效焦化过程中获得的副产品,在增碳剂的应用中也起到重要作用。
增碳剂 用途

增碳剂用途增碳剂是一种在冶金、炼钢、铸造等行业中广泛使用的化学添加剂。
它的主要作用是增加金属材料的碳含量,以改善材料的硬度、强度和耐磨性等性能。
下面将从不同行业的角度介绍增碳剂的具体用途。
在冶金行业中,增碳剂被用于提高铸造铁和钢的碳含量。
铸造铁的碳含量决定了其硬度和强度,而增碳剂可以在铁水中释放出碳,使其达到所需的碳含量。
同时,增碳剂还可以有效地改善铸造铁的流动性和凝固性能,提高铸件的质量和表面光洁度。
在炼钢行业中,增碳剂主要用于调节钢的碳含量和改善钢的性能。
钢中的碳含量对其硬度、韧性和可焊性等性能有着重要影响。
通过添加适量的增碳剂,可以使钢材的碳含量达到理想水平,从而提高钢材的强度和耐磨性,增加其使用寿命。
在铸造行业中,增碳剂被广泛应用于铸件的生产过程中。
铸件通常需要具备一定的硬度和耐磨性,以保证其在使用过程中不易磨损或变形。
增碳剂可以提高铸件的碳含量,从而增加其硬度和耐磨性。
同时,增碳剂还可以改善铸件的凝固性能,减少铸件的缩孔和气孔等缺陷,提高铸件的质量。
除了上述行业,增碳剂还被广泛应用于其他领域。
例如,在石油钻探行业中,增碳剂可以用于改善钻头的硬度和耐磨性,提高钻探效率。
在化工行业中,增碳剂可以用于生产高纯度的有机化合物,提高产品的质量和纯度。
在电子行业中,增碳剂可以用于制备高纯度的半导体材料,提高电子元件的性能。
总结起来,增碳剂作为一种化学添加剂,在冶金、炼钢、铸造等行业中具有广泛的应用。
它的主要作用是增加金属材料的碳含量,以改善材料的硬度、强度和耐磨性等性能。
通过合理使用增碳剂,可以提高产品的质量和性能,满足不同行业的需求。
未来随着科技的进步和工艺的改进,增碳剂的应用将会越来越广泛,为各行各业的发展带来更多的机遇和挑战。
高强度高碳当量灰铸铁生产工艺问题2—合理地使用增碳剂
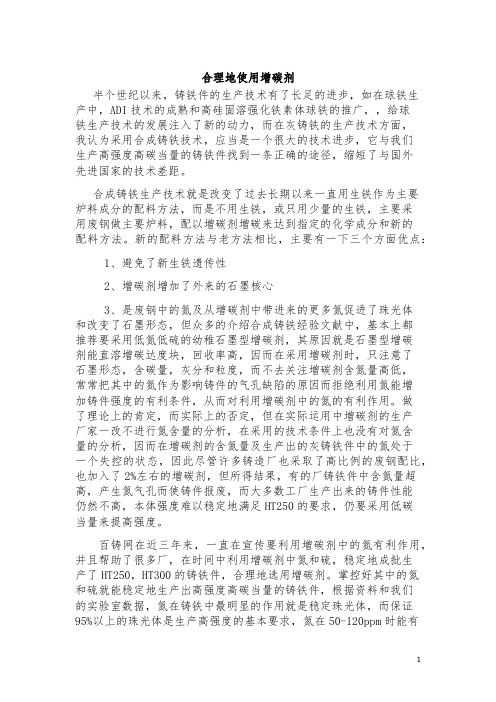
合理地使用增碳剂半个世纪以来,铸铁件的生产技术有了长足的进步,如在球铁生产中,ADI技术的成熟和高硅固溶强化铁素体球铁的推广,,给球铁生产技术的发展注入了新的动力,而在灰铸铁的生产技术方面,我认为采用合成铸铁技术,应当是一个很大的技术进步,它与我们生产高强度高碳当量的铸铁件找到一条正确的途径,缩短了与国外先进国家的技术差距。
合成铸铁生产技术就是改变了过去长期以来一直用生铁作为主要炉料成分的配料方法,而是不用生铁,或只用少量的生铁,主要采用废钢做主要炉料,配以增碳剂增碳来达到指定的化学成分和新的配料方法。
新的配料方法与老方法相比,主要有一下三个方面优点:1、避免了新生铁遗传性2、增碳剂增加了外来的石墨核心3、是废钢中的氮及从增碳剂中带进来的更多氮促进了珠光体和改变了石墨形态,但众多的介绍合成铸铁经验文献中,基本上都推荐要采用低氮低硫的幼稚石墨型增碳剂,其原因就是石墨型增碳剂能直溶增碳达度块,回收率高,因而在采用增碳剂时,只注意了石墨形态,含碳量,灰分和粒度,而不去关注增碳剂含氮量高低,常常把其中的氮作为影响铸件的气孔缺陷的原因而拒绝利用氮能增加铸件强度的有利条件,从而对利用增碳剂中的氮的有利作用。
做了理论上的肯定,而实际上的否定,但在实际运用中增碳剂的生产厂家一改不进行氮含量的分析,在采用的技术条件上也没有对氮含量的分析,因而在增碳剂的含氮量及生产出的灰铸铁件中的氮处于一个失控的状态,因此尽管许多铸造厂也采取了高比例的废钢配比,也加入了2%左右的增碳剂,但所得结果,有的厂铸铁件中含氮量超高,产生氮气孔而使铸件报废,而大多数工厂生产出来的铸件性能仍然不高,本体强度难以稳定地满足HT250的要求,仍要采用低碳当量来提高强度。
百铸网在近三年来,一直在宣传要利用增碳剂中的氮有利作用,并且帮助了很多厂,在时间中利用增碳剂中氮和硫,稳定地成批生产了HT250,HT300的铸铁件,合理地选用增碳剂。
掌控好其中的氮和硫就能稳定地生产出高强度高碳当量的铸铁件,根据资料和我们的实验室数据,氮在铸铁中最明显的作用就是稳定珠光体,而保证95%以上的珠光体是生产高强度的基本要求,氮在50-120ppm时能有效地抑制铁素体的生成,而当含量过高时有产生氮气孔的危险,我们控制厚大件的氮含量不超过80ppm,中小件不超过120ppm作为控制界限。
石墨球增碳剂

石墨球增碳剂石墨球增碳剂是一种常见的增碳剂,在许多工业领域都有广泛的应用。
本文将介绍石墨球增碳剂的定义、特点、用途以及制备方法。
一、石墨球增碳剂的定义石墨球增碳剂是由石墨粉末和粘结剂混合而成的球状颗粒物。
石墨球增碳剂具有高度的石墨化程度和良好的增碳效果,能够提高钢铁、铸件和合金材料的碳含量,改善其力学性能和工艺性能。
1. 高纯度:石墨球增碳剂采用高纯度的石墨粉末制备而成,具有较高的纯度,能够保证增碳效果的稳定性和可靠性。
2. 球状颗粒:石墨球增碳剂的颗粒形状为球状,具有较好的流动性和分散性,能够均匀地分布在熔体中,提高增碳的均匀性。
3. 耐高温:石墨球增碳剂具有较高的耐高温性能,能够在高温条件下保持其增碳效果,不易烧蚀和熔化。
4. 易于操作:石墨球增碳剂的使用方法简单,可直接投入熔体中,不需要额外的设备和工艺操作。
三、石墨球增碳剂的用途1. 钢铁冶炼:石墨球增碳剂可用于钢铁冶炼过程中的增碳操作,提高钢铁的碳含量,改善其硬度、强度和耐磨性。
2. 铸造工业:石墨球增碳剂可用于铸造工业中的增碳操作,提高铸件的碳含量,改善其铸造性能和机械性能。
3. 合金制备:石墨球增碳剂可用于合金制备过程中的增碳操作,提高合金材料的碳含量,改善其热处理性能和耐腐蚀性能。
四、石墨球增碳剂的制备方法1. 原料准备:将高纯度的石墨粉末和粘结剂按一定比例混合均匀。
2. 成型处理:将混合好的原料进行成型处理,通常采用压制的方式将其压制成球状颗粒。
3. 烧结处理:将成型好的石墨球增碳剂进行烧结处理,使其具有一定的强度和耐高温性能。
4. 表面处理:可对石墨球增碳剂进行表面处理,提高其流动性和分散性。
总结:石墨球增碳剂作为一种常见的增碳剂,具有高纯度、球状颗粒、耐高温和易于操作的特点。
它在钢铁冶炼、铸造工业和合金制备中有广泛的应用,能够提高材料的碳含量,改善其性能。
制备石墨球增碳剂的方法主要包括原料准备、成型处理、烧结处理和表面处理。
增碳剂 用途

增碳剂用途
增碳剂是一种用于增加碳含量的添加剂,广泛应用于冶金、化工、电力等行业。
它可以提高材料的硬度、抗磨性和耐腐蚀性能,是许多工业生产过程中不可或缺的重要材料。
在冶金行业中,增碳剂主要用于钢铁生产过程中的炉渣处理和钢水调质。
炉渣处理是指通过加入增碳剂来调整炉渣中的碳含量,以保证炉渣的稳定性和流动性。
钢水调质则是将增碳剂加入钢水中,通过增加钢水中的碳含量,提高钢的硬度和强度,同时改善钢的韧性和塑性,使其具有更好的机械性能。
在化工行业中,增碳剂常用于有机合成反应中的催化剂。
它能够提高反应物的碳含量,加速反应速率,提高反应的产率和选择性。
例如,增碳剂可以用于合成烯烃、芳烃等有机化合物,广泛应用于石油化工、医药等领域。
在电力行业中,增碳剂主要用于燃煤锅炉的燃烧过程中。
通过向燃烧系统中添加增碳剂,可以提高煤炭的燃烧效率,降低烟气中的氮氧化物和硫氧化物排放,减少环境污染。
同时,增碳剂还可以改善燃烧系统的稳定性和热效率,降低能源消耗,提高发电效率。
除了上述行业外,增碳剂还被广泛应用于其他领域。
例如,在农业中,增碳剂可以用于改善土壤质量,提高农作物的产量和品质。
在环保领域,增碳剂可以用于污水处理和废气处理,帮助净化环境。
在材料科学中,增碳剂可以用于改善材料的导电性和热导性,提高材料的性能和应用范围。
总的来说,增碳剂作为一种重要的添加剂,在各个行业中发挥着重要的作用。
它可以提高材料的性能和质量,改善工业生产过程,促进经济的发展。
随着科技的不断进步,增碳剂的应用范围和效果还将不断扩大和提高,为各行各业的发展带来更多的机遇和挑战。
增碳剂的详细介绍

增碳剂的详细介绍
增碳剂
洛阳华珩耐⽕材料增碳剂属于外加炼钢、炼铁增碳原料。
优质增碳剂是⽣产优质钢材必不可少的辅助添加剂。
优质增碳剂⼀般指经过⽯墨化的增碳剂,在⾼温条件下,碳原⼦的排列呈⽯墨的微观形态,所以称之为⽯墨化。
⽯墨化可以降低增碳剂中杂质的含量,提⾼增碳剂的碳含量,降低硫含量。
增碳剂在铸造时使⽤,可⼤幅度增加废钢⽤量,减少⽣铁⽤量或不⽤⽣铁。
⽬前绝⼤多数增碳剂都适⽤于电炉熔炼,也有少部分吸收速度特别快的增碳剂⽤于冲天炉。
⼀、增碳剂的分类
按照材质分,⼀般可以分为:冶⾦焦增碳剂,煅煤增碳剂,⽯油焦增碳剂,⽯墨化增碳剂,天然⽯墨增碳剂,复合材料增碳剂。
1.⽯油焦增碳剂
⽯油焦增碳剂采⽤⽯油焦煅烧提纯等加⼯⽽成,外观成圆粒或多棱形。
其特点⾼碳、低硫,低灰是冶⾦化⼯、机械、电⼒等⾏业理想的加碳材料和反应中间体,得到⼴泛应⽤。
增碳剂产品技术指标如下
含量/规格HYCPC-01HYCPC-02HYCPC-03
固定碳≥98.5%98.5%98-99%
挥发分≤0.5%0.5%0.5%
灰份≤0.3%0.5% 1.00-0.3%
硫份≤0.45%0.5%0.5%
⽔份≤0.3%0.3%0.3%
原料CPC CPC CPC
尺⼨
60-80⽬;80-100⽬;100-200⽬;200-300⽬;0-0.5mm;0.2-4.0mm;0.5-6.0mm;1-3mm;1-5mm;1-10mm;25-65mm;1-
100mm
备注CPC-煅后⽯油焦。
感应电炉炼钢用增碳剂种类与使用方法

增碳剂介绍分炼钢用增碳剂(中华人民共和国黑色冶金行业标准,YB/T 192-2001炼钢用增碳剂)和铸铁用增碳剂,以及其他一些添加材料也有用到增碳剂,譬如刹车片用添加剂,作摩擦材料。
增碳剂属于外加炼钢、炼铁增碳原料。
优质增碳剂是生产优质钢材必不可少的辅助添加剂。
增碳剂的原料有很多种,生产工艺也各异,有木质碳类,煤质碳类,焦炭类,石墨类等,其中各种分类下又有很多小种类。
优质增碳剂一般指经过石墨化的增碳剂,在高温条件下,碳原子的排列呈石墨的微观形态,所以称之为石墨化。
石墨化可以降低增碳剂中杂质的含量,提高增碳剂的碳含量,降低硫含量。
增碳剂在铸造时使用,可大幅度增加废钢用量,减少生铁用量或不用生铁。
电炉熔炼的投料方式,应将增碳剂随废钢等炉料一起往里投放,小剂量的添加可以选择加在铁水表面。
但是要避免大批量往铁水里投料,以防止氧化过多而出现增碳效果不明显和铸件碳含量不够的情况。
增碳剂的加入量,根据其他原材料的配比和含碳量来定。
不同种类的铸铁,根据需要选择不同型号的增碳剂。
增碳剂特点本身选择纯净的含碳石墨化物质,降低生铁里过多的杂质,增碳剂选择合适可降低铸件生产成本。
2碳剂的使用在冶炼过程中,由于配料或装料不当以及脱碳过量等原因,有时造成钢中碳含量没有达到顶期的要求,这时要向钢液中增碳。
常用的增碳剂有增碳生铁、电极粉、石油焦粉、木炭粉和焦炭粉。
转炉冶炼中、高碳钢种时,使用含杂质很少的石油焦作为增碳剂。
对顶吹转炉炼钢用增碳剂的要求是固定碳要高,灰分、挥发分和硫、磷、氮等杂质含量要低,且干燥、干净、粒度适中。
其固定碳组分为:w(C)>96%,挥发分≤1.0%,w(S)≤0.5%,w(水分)≤0.55%,粒度为1一5mm.粒度太细容易烧损,太粗加入后浮在钢液表面,不容易被钢水吸收。
针对感应电炉的颗粒度在0.2-6mm,其中钢和其他黑色金属颗粒度在1.4-9.5mm,高碳钢要求低氮,颗粒度在 0.5-5mm,等等具体需要根据具体的炉型冶炼工件的种类等等细节具体判断和选用。
增碳剂 用途

增碳剂的用途1. 引言增碳剂是一种在冶金工业中广泛应用的添加剂,它可以提高金属材料的碳含量,改善材料的力学性能和耐磨性。
本文将详细介绍增碳剂的用途、工作原理以及在不同行业中的应用。
2. 增碳剂的工作原理增碳剂主要是由含有高碳元素的物质组成,如焦炭、石墨等。
在冶金过程中,增碳剂加入到金属熔体中,通过与金属中的氧化物反应,将氧化物还原为金属,并将高碳元素引入金属中。
增碳剂中的高碳元素会与金属中的低碳元素结合,提高材料的碳含量,从而改善其力学性能。
3. 增碳剂在冶金工业中的应用3.1 钢铁冶炼钢铁冶炼是增碳剂最主要的应用领域之一。
在炼钢过程中,增碳剂可以有效地提高钢的碳含量,使得钢具有更好的可塑性和韧性。
增碳剂还可以改善钢的硬度和耐磨性,提高钢的使用寿命。
在不同的炼钢方法中,增碳剂的使用方式有所不同,但都能达到提高钢的碳含量的目的。
3.2 铸造工业在铸造工业中,增碳剂可以用于改善铸件的力学性能和耐磨性。
通过在铸造过程中添加增碳剂,可以提高铸件的碳含量,增强其硬度和强度。
增碳剂还可以改善铸件的组织结构,使其具有更好的耐磨性和抗拉强度。
在不同的铸造方法中,增碳剂的使用量和方式也有所不同。
3.3 焊接工艺在焊接工艺中,增碳剂可以用于提高焊接材料的碳含量,增强焊缝的强度和耐磨性。
增碳剂可以与焊接材料中的低碳元素结合,形成强度更高的化合物,从而提高焊缝的力学性能。
增碳剂的使用可以降低焊接过程中的温度和能量损失,提高焊接效率。
3.4 其他行业中的应用除了上述应用领域外,增碳剂还可以在其他行业中发挥重要作用。
例如,在化工工业中,增碳剂可以用于改善材料的耐热性和耐腐蚀性。
在电力工业中,增碳剂可以用于提高电极材料的导电性和耐磨性。
在汽车制造业中,增碳剂可以用于提高汽车零部件的硬度和耐磨性。
4. 增碳剂的发展趋势随着科技的不断进步,增碳剂的研发和应用也在不断发展。
未来,增碳剂可能会朝着以下几个方向发展:•高效性能:研发更高效的增碳剂,提高其增碳效果和使用效率。
江西无烟煤增碳剂用途规定

江西无烟煤增碳剂用途规定江西无烟煤增碳剂是一种用于冶金、化工、建材等行业的重要原料。
它主要用于增加原料中的碳含量,提高产品的质量和性能。
下面将详细介绍江西无烟煤增碳剂的用途规定。
首先,江西无烟煤增碳剂在冶金行业中的应用非常广泛。
在铁炉、钢炉和铸造过程中,无烟煤增碳剂可以用作还原剂,将金属氧化物还原为金属,从而提高金属的纯度和质量。
同时,增碳剂还可以调节金属的成分和性能,使其更加符合生产要求。
此外,无烟煤增碳剂还可以用于制备合金材料,提高合金的强度、硬度和耐磨性。
其次,江西无烟煤增碳剂在化工行业中也有重要的应用。
在化学反应中,增碳剂可以作为还原剂或催化剂,促进反应的进行。
例如,在有机合成中,无烟煤增碳剂可以用于还原酮、醛等有机化合物,合成醇类化合物。
此外,增碳剂还可以用于制备石墨、炭黑等碳材料,广泛应用于电池、涂料、橡胶等领域。
此外,江西无烟煤增碳剂还在建材行业中发挥着重要作用。
在水泥生产过程中,增碳剂可以用作燃料,提供热能,促进水泥的煅烧和熟化。
同时,增碳剂还可以调节水泥的成分和性能,改善水泥的强度、耐久性和抗裂性。
此外,无烟煤增碳剂还可以用于制备石墨砖、炭素纤维等建筑材料,提高材料的强度和耐火性。
此外,江西无烟煤增碳剂还可以用于其他行业。
在电力行业中,增碳剂可以用作燃料,提供热能,发电。
在环保行业中,增碳剂可以用于废气处理,吸附和净化有害气体。
在农业行业中,增碳剂可以用于改良土壤,提高土壤的肥力和保水性。
总之,江西无烟煤增碳剂是一种多功能的原料,广泛应用于冶金、化工、建材等行业。
它可以用作还原剂、催化剂、燃料等,用于提高产品的质量和性能。
随着科技的不断发展,无烟煤增碳剂的应用领域还将不断扩大,为各行各业的发展做出更大的贡献。
铸造增碳剂作用
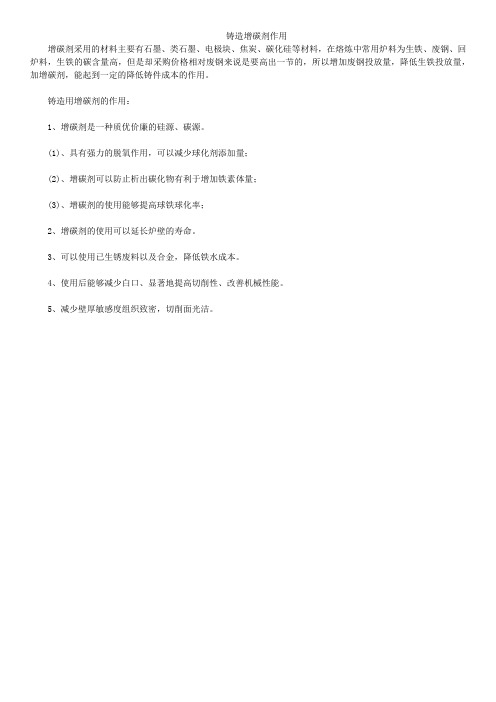
铸造增碳剂作用
增碳剂采用的材料主要有石墨、类石墨、电极块、焦炭、碳化硅等材料,在熔炼中常用炉料为生铁、废钢、回炉料,生铁的碳含量高,但是却采购价格相对废钢来说是要高出一节的,所以增加废钢投放量,降低生铁投放量,加增碳剂,能起到一定的降低铸件成本的作用。
铸造用增碳剂的作用:
1、增碳剂是一种质优价廉的硅源、碳源。
(1)、具有强力的脱氧作用,可以减少球化剂添加量;
(2)、增碳剂可以防止析出碳化物有利于增加铁素体量;
(3)、增碳剂的使用能够提高球铁球化率;
2、增碳剂的使用可以延长炉壁的寿命。
3、可以使用已生锈废料以及合金,降低铁水成本。
4、使用后能够减少白口、显著地提高切削性、改善机械性能。
5、减少壁厚敏感度组织致密,切削面光洁。
增碳剂的使用方法
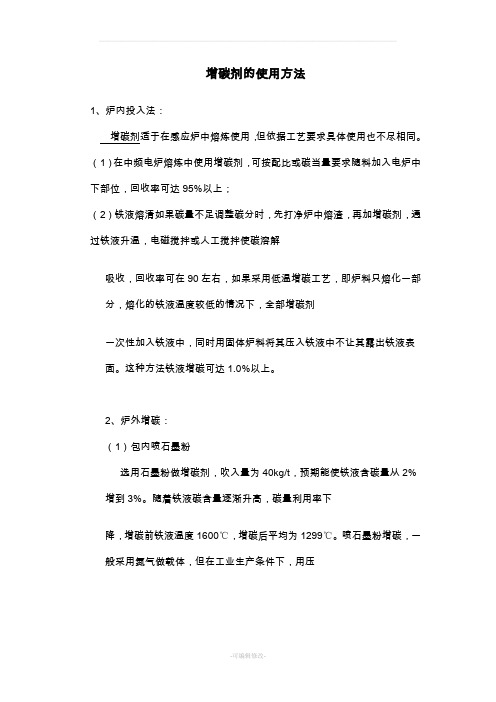
增碳剂的使用方法1、炉内投入法:增碳剂适于在感应炉中熔炼使用,但依据工艺要求具体使用也不尽相同。
(1)在中频电炉熔炼中使用增碳剂,可按配比或碳当量要求随料加入电炉中下部位,回收率可达95%以上;(2)铁液熔清如果碳量不足调整碳分时,先打净炉中熔渣,再加增碳剂,通过铁液升温,电磁搅拌或人工搅拌使碳溶解吸收,回收率可在90左右,如果采用低温增碳工艺,即炉料只熔化一部分,熔化的铁液温度较低的情况下,全部增碳剂一次性加入铁液中,同时用固体炉料将其压入铁液中不让其露出铁液表面。
这种方法铁液增碳可达1.0%以上。
2、炉外增碳:(1)包内喷石墨粉选用石墨粉做增碳剂,吹入量为40kg/t,预期能使铁液含碳量从2%增到3%。
随着铁液碳含量逐渐升高,碳量利用率下降,增碳前铁液温度1600℃,增碳后平均为1299℃。
喷石墨粉增碳,一般采用氮气做载体,但在工业生产条件下,用压缩空气更方便,而且压缩空气中的氧燃烧产生CO,化学反应热可补偿部分温降,而且CO的还原气氛利于改善增碳效果。
(2)出铁时使用增碳剂可将100—300目的石墨粉增碳剂放到包内,或从出铁槽随流冲入,出完铁液后充分搅拌,尽可能使碳溶解吸收,碳的回收率在50%左右。
宁夏宏辉炭素制品有限公司生产的无烟煤增碳剂具有低硫、低灰,含炭量高易吸收等特点。
一、增碳剂的加入时间不能忽视。
增碳剂的加入时间若过早,容易使其附着在炉底附近,而且附着炉壁的增碳剂又不易被熔入铁液。
与之相反,加入时间过迟,则失去了增碳的时机,造成熔炼、升温时间的迟缓。
这不仅延迟了化学成分分析和调整的时间,也有可能带来由于过度升温而造成的危害。
因此,增碳剂还是在加入金属炉料的过程中一点一点地加入为好。
如在一次加入量过大的情况下,可以结合感应电炉时采用的铁液过热操作结合考虑,保证增碳剂在铁液中的吸收时间10Min,一方面通过电磁搅拌作用使增碳剂充分扩散吸收,保证吸收效果。
另一方面可以减少增碳剂中带入的含氮量。
增碳剂在铸铁生产中的应用

加入重量 %按 #()R4 批 料 计 算 &’R4
&& (* () #() ! #+$! #+() !
7 料中 铁液中
’+!) )+"*
)+!) )+)"
!+$)
)+,’ #+", #+") )+,)
! !+*)
元素 !%%& =>
料中 铁液中
#+’) )+!, )+!) )+)" #+() )+()
X X )+$!#+) )+$!&+) #+)!(+) #+)!(+) X X X X X
帝 首 固 增 碳 剂 (!)
西安长泰特种合金厂
(’) (!) (!) (#) (!) (!)
#,$
5’
5)+&
5#
5#
#!#)
X
煅烧无烟煤增碳剂 #,$
5’
5)+&
5#
5#
#!$
X
#,’
5$
5)+&
5#
5#
)+!!!
表 #! 炉 料 计 算 表
序号
# ! &
’ $ !
材料名称
本溪生铁 2#’ 低碳废钢 回炉料 合!计
烧损后实得 石墨碳%按#))%7 计烧损$%& 硅铁%含 =>按*$%计烧损#)%&
最 终 铁 液 成 分 %计 算 值 &
增碳剂在铸造生产中的应用
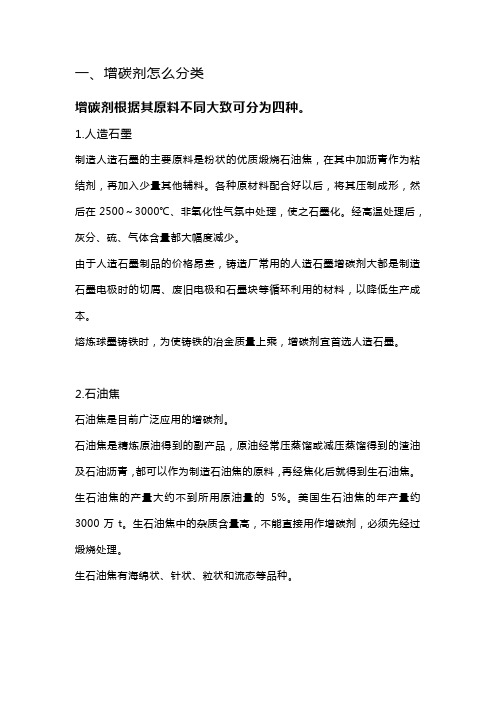
一、增碳剂怎么分类增碳剂根据其原料不同大致可分为四种。
1.人造石墨制造人造石墨的主要原料是粉状的优质煅烧石油焦,在其中加沥青作为粘结剂,再加入少量其他辅料。
各种原材料配合好以后,将其压制成形,然后在2500~3000℃、非氧化性气氛中处理,使之石墨化。
经高温处理后,灰分、硫、气体含量都大幅度减少。
由于人造石墨制品的价格昂贵,铸造厂常用的人造石墨增碳剂大都是制造石墨电极时的切屑、废旧电极和石墨块等循环利用的材料,以降低生产成本。
熔炼球墨铸铁时,为使铸铁的冶金质量上乘,增碳剂宜首选人造石墨。
2.石油焦石油焦是目前广泛应用的增碳剂。
石油焦是精炼原油得到的副产品,原油经常压蒸馏或减压蒸馏得到的渣油及石油沥青,都可以作为制造石油焦的原料,再经焦化后就得到生石油焦。
生石油焦的产量大约不到所用原油量的5%。
美国生石油焦的年产量约3000万t。
生石油焦中的杂质含量高,不能直接用作增碳剂,必须先经过煅烧处理。
生石油焦有海绵状、针状、粒状和流态等品种。
海绵状石油焦是用延迟焦化法制得的,由于其中硫和金属含量较高,通常用作煅烧时的燃料,也可作为煅烧石油焦的的原料。
经煅烧的海绵焦,主要用于制铝业和用作增碳剂。
针状石油焦,是用芳香烃的含量高、杂质含量低的原料,由延迟焦化法制得的。
这种焦炭具有易于破裂的针状结构,有时称之为石墨焦,煅烧后主要用于制造石墨电极。
粒状石油焦呈硬质颗粒状,是用硫和沥青烯含量高的原料,用延迟焦化法制得的,主要用作燃料。
流态石油焦,是在流态床内用连续焦化法制得的,呈细小颗粒状,结构无方向性,硫含量高、挥发分低。
石油焦的煅烧,是为了除去硫、水分、和挥发分。
将生石油焦于1200~1350℃煅烧,可以使其成为基本上纯净的碳。
煅烧石油焦的最大用户是制铝业,70%用以制造使铝矾土还原的阳极。
美国生产的煅烧石油焦,用于铸铁增碳剂的约占6%。
3.天然石墨天然石墨可分为鳞片石墨和微晶石墨两类。
微晶石墨灰分含量高,一般不用作铸铁的增碳剂。
石墨化增碳剂作用
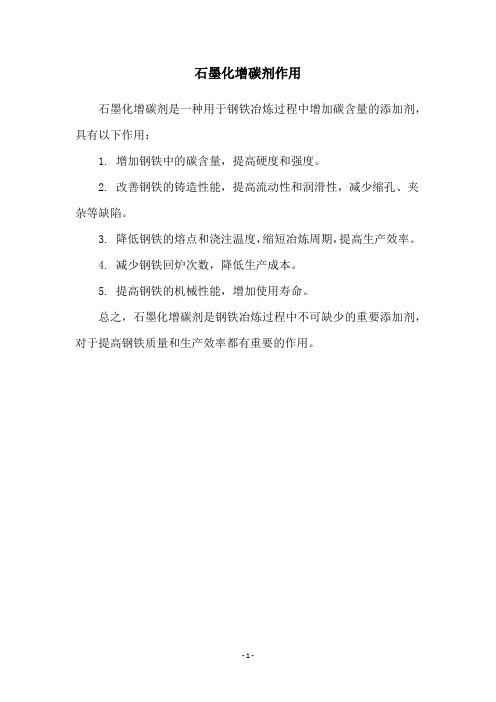
石墨化增碳剂作用
石墨化增碳剂是一种用于钢铁冶炼过程中增加碳含量的添加剂,具有以下作用:
1. 增加钢铁中的碳含量,提高硬度和强度。
2. 改善钢铁的铸造性能,提高流动性和润滑性,减少缩孔、夹杂等缺陷。
3. 降低钢铁的熔点和浇注温度,缩短冶炼周期,提高生产效率。
4. 减少钢铁回炉次数,降低生产成本。
5. 提高钢铁的机械性能,增加使用寿命。
总之,石墨化增碳剂是钢铁冶炼过程中不可缺少的重要添加剂,对于提高钢铁质量和生产效率都有重要的作用。
- 1 -。
- 1、下载文档前请自行甄别文档内容的完整性,平台不提供额外的编辑、内容补充、找答案等附加服务。
- 2、"仅部分预览"的文档,不可在线预览部分如存在完整性等问题,可反馈申请退款(可完整预览的文档不适用该条件!)。
- 3、如文档侵犯您的权益,请联系客服反馈,我们会尽快为您处理(人工客服工作时间:9:00-18:30)。
浅谈增碳剂的使用
摘要:提出了当前对增碳剂的认识存在的误区,以及优质增碳剂的选择。
把加增碳剂的熔炼新工艺与传统熔炼(只加生铁)工艺进行对比,分析了增碳剂对熔炼的影响,说明使用中应当注意的问题,阐明了增碳剂的正确使用方法。
关键词:增碳剂;熔炼;
一种含碳量很高的黑色或者灰色颗粒(或块状)的焦碳后续产物,加入到金属冶炼炉里,提高铁液里碳的含量,一方面可以降低铁液里氧的含量,另一方面更重要的是提高冶炼金属或者铸件的力学性能。
增碳剂的来源很多,形态各异,根据其加工工艺和成分等不同,价格差异很大。
传统的熔炼方式类似冲天炉熔炼:使用生铁、回炉料、废钢、铁合金等作为金属炉料;新的合成铸铁生产工艺:使用废钢作炉料,利用增碳剂来调整铁液的碳当量。
后一种生产方式更容易保证优质铁液,同时通过少用或者取代生铁改用废钢大大降低成本。
通俗的说,利用增碳剂,我们能用最差的(废钢)炼出最好的(铸件)。
国外增碳技术已经日趋成熟,国内此项新工艺近几年才开始发展,业内很多人对增碳剂的品质和质量了解不够深入,有些铸造工作者选用增碳剂存在误区。
例如混淆增碳剂的固定碳含量和含碳量的含义,固定碳值是根据样品的水分、挥发分、灰分、硫分计算得出的,而含碳量直接测碳仪便可以获得。
有些增碳剂的灰分高,含碳量也高,但是它的固定碳值一定不会太理想。
还有些铸造工作者片面的从增碳剂的固定碳含量和其物质性质便断定其是否优质,其结果很可能误入歧途,导致购入的增碳剂物不所值。
一、增碳剂的选择及其指标性能
在冶炼过程中,由于配料或装料不当以及脱碳过量等原因,有时造成钢或铁中碳含量没有达到预期的要求,这时要向钢或铁液中增碳。
通常用来增碳的主要物质有无烟煤粉、增碳生铁、电极粉、石油焦粉、沥青焦、木炭粉和焦炭粉。
对增碳剂的要求是,固定碳含量越高越好,灰分、挥发分及硫等有害杂质含量越低越好,以免污染钢。
铸件的冶炼使用含杂志很少的石油焦经过高温培烧后的优质增碳剂,这是增碳工艺中最重要的环节。
增碳剂质量好坏决定了铁液质量的好坏,也决定了能否获得好的石墨化效果。
简言之,减少铁液收缩增碳剂起到举足轻重的作用。
全废钢电炉熔炼时,优先选用经过了石墨化处理的增碳剂,经过高温石墨化处理的增碳剂,碳原子才能从原来的无序排列变成片状排列,片状石墨才能成为石墨形核的最好核心,以利促进石墨化。
因此,我们应该要选用经过高温石墨化
气体逸出而降低。
所以处理的增碳剂。
因为高温石墨化处理时,硫分被生成SO
2
高品质的增碳剂含硫分很低, w(s)一般小于0.05%,更好的w(s)甚至小于0.03%。
同时,这也是判断是否经过高温石墨化处理以及石墨化是否良好的一个间接指标。
如果选用的增碳剂没经过高温石墨化处理,石墨的形核能力就大大降低,石墨化能力减弱,即使也能达到同样的碳量,但结果完全不一样。
所谓增碳剂,就是要在加入后可以有效提高铁液中碳的含量,所以增碳剂的固定碳含量一定不能太低,否则要达到一定的含碳量,就需要加入相比高碳的增碳剂更多的样品,这样无疑增加了增碳剂中其他不利元素的量,使铁液不能获得较好的收益。
低的硫、氮、氢元素是防止铸件产生氮气孔的关键,这样就要求增碳剂的含氮量越低越好。
增碳剂的其他指标,诸如水分、灰分、挥发分的量越低的固定碳量就越高,所以高的固定碳量,这些有害成分的含量一定不会高。
针对不同的熔炼方式、炉型以及熔炼炉的尺寸,选择合适的增碳剂颗粒度也很重要,可以有效提高铁液对增碳剂的吸收速度和吸收率,避免因过小的颗粒度而引起的增碳剂氧化烧损。
其粒度最好为:100kg炉小于10mm,500kg炉小于
15mm,1.5吨炉小于20mm,20吨炉小于30mm。
转炉冶炼中,高碳钢种时,使用含杂质很少的增碳剂。
对顶吹转炉炼钢用增碳剂的要求是固定碳要高,灰分,挥发分和硫,磷,氮等杂质含量要低,且干燥,干净,粒度适中。
其固定碳C≥96%,挥发分≤1.0%,S≤0.5%,水分≤0.5%,粒度在1-5mm。
粒度太细容易烧损,太粗加入后浮在钢液表面,不容易被钢水吸收。
针对感应电炉的颗粒度在0.2-6mm,其中钢和其他黑色金属颗粒度在1.4-9.5mm,高碳钢要求低氮,颗粒度在
0.5-5mm,等等具体需要根据具体的炉型冶炼工件的种类等等细节具体判断和选用。
二、加增碳剂熔炼新工艺对比传统工艺
生铁中有许多粗大的过共晶石墨,这种粗大的石墨具有遗传性,熔炼温度低,粗大石墨不易被消除,粗大的石墨从液态遗传到了固态铸铁组织中,一方面降低铸铁所能达到的强度,降低了材料的性能,另一方面使凝固过程中本来应该产生的石墨化析出的膨胀作用削弱,使铁液凝固过程中的收缩倾向增大。
在冲天炉熔炼时,尽量降低生铁炉料的用量,使用增碳剂来保证高碳当量,相对提高废钢用量。
这样,在高温熔炼的条件下,可以渗碳方式获得活性好,石墨化作用更显著的碳。
在铸件上反映出石墨的形态更好,从而有利于提高力学性能,减少收缩倾向,改善加工性能。
电炉熔炼时,同样通过低生铁用量甚至零用量,以渗碳方式获得优质铁液。
从材质性能上来说,过去那种大比例的生铁用量做法,与同样成分的高废钢用量相比,其力学性能也要低半个牌号。
因此,加增碳剂熔炼的新工艺比传统上那种大比例的生铁用量相比无论从成本还是成品性能都要优越。
三、增碳剂对熔炼的影响及使用
同样的化学成分,采用不同的熔炼工艺、不同配料和配料比,铁液的冶金质量完全不同。
获得好的渗碳效果,电炉采用的是增碳技术,冲天炉采用的是高温熔炼技术。
增碳剂对熔炼的影响主要有三方面。
1.铁液增碳技术,在熔炼过程中特别是电炉熔炼,可以增加石墨晶核。
冲天炉熔炼中加入碳化硅还能增加铁液的长效石墨晶核,同时减少铁液氧化。
2.增碳是防止或减轻收缩倾向最好的措施。
由于铁液凝固过程中的具有石墨化膨胀的作用,因此良好的石墨化会减少铁液的收缩倾向。
3. 在高的碳量条件下,为获得高强度的灰铸铁铸件,熔炼过程采用全废钢加增碳剂的工艺,使铁液更加纯净,生产的铸件材料性能高。
熔炼要用不含油污的干净料,避免产生漏电或浮渣过多的现象。
某厂前几炉因使用了油浸废铁屑,使线圈出现电火花,曾认为是炉衬料含铁太高而产生漏电。
其实是因为熔炼的铁屑含有油污,容易出现碳沉积。
碳积沉部位是在炉衬冷面,
↑甚至沉积到隔热层中,由于炉衬尚未充分烧结,CO渗入炉衬后部,发生CO→C+O
2
反应,生成C沉积在炉衬冷面或隔热材料的气孔中。
当产生碳沉积时,会造成炉体接地漏电,造成线圈冒火花。
改用纯净料即可避免。
另外一个厂因为采购的废钢来源混乱,甚至表层涂附有油漆、石灰、煤等物质,造成浮渣多,在后期除渣工作消耗了大量的人力与物力。
一般认为,铁水温度越高,作用时间越长,碳的吸收率越高。
但实际正好相反,在感应电炉内是低温增碳,高温增硅,即在高温时,非但不增碳,反而是降碳,这是因为:①石墨碳主要损失于向炉外大气的气相扩散;②铁水中的氧化性
与C-Si-O的平衡有关,铁水中的CO不断地被氧化为CO
2,而CO
2
又会被C还原,
反应产生的CO,CO
2
气体上浮溢出铁水表面,使铁水中的碳含量下降。
反应速度与平衡温度有关,而平衡温度又随着碳硅含量的不同而变化。
对于球铁原铁水,平衡温度大约为1450℃±20℃,灰铁原铁水约为1400℃±20℃。
铁水在平衡温度以上碳的氧化变得剧烈。
反应的结果使铁水中的碳不断地被氧化烧损,硅的烧损减少。
这时在铁水表面加入的增碳剂使铁水中的增碳和降碳达到平衡。
根据以上分析,下面是增碳剂在感应电炉内增碳的正确使用方法:
1.使用5T以上的电炉,原料单一稳定,我们推荐分散加入法。
根据含碳量的要求,按配料比,将增碳剂与金属炉料随各批料一同加入电炉中下部位,一层金属炉料一层增碳剂,碳的吸收率可达90%-95%,增碳剂在熔化时不要打渣,否则易裹在废渣里,影响碳的吸收;
2.使用3T左右中频感应电炉,原料单一稳定,我们推荐集中加入法。
在炉内先熔化或剩余少量铁水时,将需配加的增碳剂一次性加在铁水表面,并立即加金属炉料,将增碳剂全部压入铁水中,使增碳剂与铁水充分接触,吸收率在90%以上;
3.使用小型中频电炉,原料夹有生铁等高碳物质的,我们推荐增碳剂微调。
钢/铁水熔化后,调整碳分,可以加在钢/铁水表面,通过电炉熔炼时钢(铁)水的涡流搅拌或人工搅拌使本产品溶解吸收,碳的吸收率在93%左右。
四、优质增碳剂具备的特性
1.颗粒大小适中,孔隙度大,吸收速度快。
2.化学成分纯净,高碳、低硫、有害成分极微,吸收率高。
3.产品石墨晶体结构好,提高原铁液的形核能力。
在孕育中增加球墨铸铁的墨球数量,在电炉铁液中增加石墨晶核。
细化、均匀化石墨在铸件中的分布。
4.性能优异、稳定。
选用合适的增碳剂有助于降低冶炼生产成本,提高冶炼金属及铸件的质量,让冶炼金属厂、铸造厂等获得财质双收的经济效益。