增碳剂的使用方法
增碳剂作用

增碳剂作用增碳剂作用一、概述增碳剂是一种用于钢铁冶炼中的添加剂,主要是为了提高钢铁中碳含量,从而改善钢铁的物理性能和化学性能。
增碳剂通常是指含有高纯度碳素的物质,如石墨、焦炭、天然石墨等。
二、作用机理1. 增加钢铁中的碳含量增碳剂在钢铁冶炼过程中加入后,其中的高纯度碳素会与钢水中的氧化物反应生成CO气体,CO气体进一步与FeO反应生成CO2和Fe。
这个过程被称为还原反应。
在还原反应中,CO气体起到了还原FeO为Fe的作用,并且释放出大量的热量。
此时,增碳剂中的高纯度碳素也会参与到反应中去,生成C和CO2。
C会随着钢水流动而逐渐分散到整个钢水中,从而提高了钢水的碳含量。
2. 改善钢铁物理性能通过增加钢铁中的碳含量,可以改善其物理性能。
由于C元素在晶界处难以溶解,因此增加钢铁中的碳含量会使得晶界处的C元素浓度升高,从而增加了晶界处的强度,提高了钢铁的韧性和延展性。
3. 改善钢铁化学性能增碳剂中的高纯度碳素还可以与其他元素发生反应,从而改善钢铁的化学性能。
例如,在合金钢中加入一定量的Cr、Ni等元素后,通过增加碳含量可以形成相应的碳化物,从而提高合金钢的硬度和耐磨性。
三、常用增碳剂1. 石墨石墨是一种天然形成的含有高纯度碳素的物质。
由于其具有良好的导电性和导热性,在冶金工业中被广泛使用。
在钢铁冶炼过程中,石墨可以作为一种优质增碳剂使用。
2. 焦炭焦炭是一种由煤制成的固体燃料,在冶金工业中被广泛使用。
由于其含有大量纯净的碳素,因此也可以作为一种优质增碳剂使用。
3. 天然石墨天然石墨是一种天然形成的含有高纯度碳素的物质,其主要成分为石墨和石墨质。
由于其具有良好的导电性和导热性,在冶金工业中也被广泛使用。
四、使用注意事项1. 选择合适的增碳剂在选择增碳剂时,应该根据钢铁冶炼过程中的具体情况来选择合适的增碳剂。
例如,在高温下使用焦炭作为增碳剂时,由于焦炭易于氧化,因此需要加入一定量的保护剂来防止氧化。
2. 控制加入量在使用增碳剂时,应该控制其加入量,以避免过多或过少的加入对钢铁质量产生不利影响。
铸造中电炉增碳剂使用方法建议

关于Desulco 9018作微调,有以下使用建议:
如一炉铁水只出一包铁水,可选用炉内增碳(方案一),9018吸收率能达
到90%;如一炉铁水需出多包水,可选用包内增碳(方案二),9018吸收
率能达到70-80%; 9018做微调后,尽量在30分钟内浇注,这样能起到预
处理作用,提升铁液形核能力。
铁水化清后测碳,如发现碳低,进行微调,微调增碳时增碳量最好不超过
0.3%。
方案一(炉内增碳):
∙微调前扒渣。
∙按90%吸收率计算所加9018用量(前期试用时,用量可适当增加),加入到炉内铁水表面。
∙开动电炉使铁水翻花2-3分钟,观察9018变红直至全部溶入铁水,电炉调至保温功率。
∙2-3分钟后热分析仪测碳成分是否到达目标值。
方案二(包内增碳):
∙出铁前扒渣。
∙按图示将计算好的9018增碳剂放置在覆盖剂上方,如球化包有双坑,可将9018放置在没有球化剂的一个坑。
∙将铁水注入球化包,让铁水先流入加增碳剂的坑内,确保铁水先与增碳剂接触。
∙球化完成后扒渣。
增碳剂介绍

≤0.08 ≤0.03 ≤0.5 ≤0.5 ≤0.5 的作用
①提高碳当量; 提高碳当量; ②增加铁液石墨形核核心,降低白口倾向; 增加铁液石墨形核核心,降低白口倾向; ③增碳是防止或减轻收缩倾向最好的措施。由于铁液凝 增碳是防止或减轻收缩倾向最好的措施。 固过程中的具有石墨化膨胀的作用, 固过程中的具有石墨化膨胀的作用,因此良好的石墨化 会减少铁液的收缩倾向。 会减少铁液的收缩倾向。 的增碳剂, ④在铁水表面撒一层0.2~1mm的增碳剂,可起到“隔 在铁水表面撒一层 ~ 的增碳剂 可起到“ 离层”的作用,防止炉内铁水减碳。 离层”的作用,防止炉内铁水减碳。
4、增碳剂 、
增碳剂化学成份
化 学 成 分 % 型 号 固定碳 碳保 SK DJ MJ YJ ≥99.5 ≥98.5 ≥98.5 ≥98.5 灰 份 ≤0.08 ≤0.8 ≤1.0 ≤0.8 挥发份 ≤0.45 ≤0.5 ≤0.5 ≤0.8 硫 ≤0.01 ≤0.02 ≤0.05 ≤0.5 水 份 氮 主要功能 吸收率高 防止产生氮气孔 吸收率高 防止产生氮气孔 吸收率高 防止产生氮气孔 杂质较多、 杂质较多、含氮量高 吸收速度较慢
增碳剂使用注意事项

原文地址:中频电炉增碳剂使用注意事项作者:微笑现在大家对于感应电炉熔炼灰铁,球铁,在铸造熔炼中注重预处理,提高铁水的冶金质量,以及大量使用废钢做合成铸铁都比较熟悉了,增碳剂,碳化硅,高含钡的硅铁预处理剂的使用也逐步广泛,对于增碳剂来讲,结合最近得到的信息和以前实际经验,加上前人的发表文章,我感觉在熔炼中要注意几点: 1。
增碳剂的成分,应该以氮含量的多少来区分,则使用时,选择什么级别的氮含量,很重要!!!我们现在以感应电炉加入60%以上的废钢,熔炼合成铸铁,,由于其中钛等有害元素很低,所以应该使用低氮的增碳剂。
我在以前的帖子里面介绍过,美国,日本高端客户对普通灰铁的验收,需要化验铸铁里面氮,钛,铅,砷等等有害元素的含量,(机械性能方面,不仅要做抗拉,硬度,还要做灰铁的屈服强度),其中对于氮的含量,一般希望在80-120PPM最好,这时如果你使用高氮增碳剂(一般都属于低端增碳剂产品),由于铁水中钛的含量很低,不可能消耗大量的氮,使铸件容易因为氮含量太高而出现大量气孔,气缩或者有关缺陷,这种现象,已经在我以前工作过的单位发生,许多专家在其发表的文章中也谈过,增碳剂质量不好带给他们的重大损失。
(具体是谁?记不清了,好像是一位姓金的专家在铸造杂志上写过)。
很多铸造朋友以为,增碳剂硫量较高,不会影响普通灰铁(孕育铸铁)的质量,但是增碳剂硫量高,伴随着其中的氮也会很高,带来质量问题。
2。
99年在台湾首屋(台湾帝屋在青岛的工厂)工作时,其库房里面增碳剂很多,标牌注名只有高氮,中氮,低氮三种之分,但是根本不知其中缘故,现在经历多了,才逐步体会到此点。
当然很多东西在国内还在逐步适应,特别是高氮增碳剂,也在大量使用,石墨化不好的石油焦,精煤等等,这些低端产品针对什么铸铁熔炼使用?是否是高含钛铸铁使用?还需要今后逐步获得经验。
石墨化不好的增碳剂,加入铁水,一是吸收率低,慢,二是渣子多,三是其他有害元素影响铁水质量,希望大家注意! 3。
铸造用增碳剂
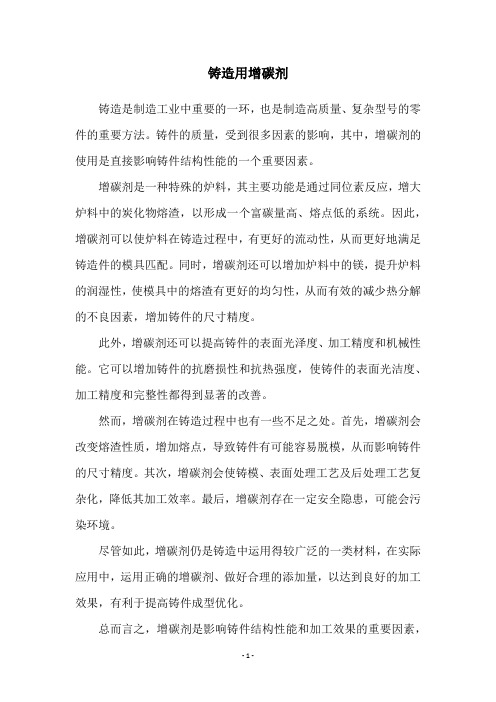
铸造用增碳剂
铸造是制造工业中重要的一环,也是制造高质量、复杂型号的零件的重要方法。
铸件的质量,受到很多因素的影响,其中,增碳剂的使用是直接影响铸件结构性能的一个重要因素。
增碳剂是一种特殊的炉料,其主要功能是通过同位素反应,增大炉料中的炭化物熔渣,以形成一个富碳量高、熔点低的系统。
因此,增碳剂可以使炉料在铸造过程中,有更好的流动性,从而更好地满足铸造件的模具匹配。
同时,增碳剂还可以增加炉料中的镁,提升炉料的润湿性,使模具中的熔渣有更好的均匀性,从而有效的减少热分解的不良因素,增加铸件的尺寸精度。
此外,增碳剂还可以提高铸件的表面光泽度、加工精度和机械性能。
它可以增加铸件的抗磨损性和抗热强度,使铸件的表面光洁度、加工精度和完整性都得到显著的改善。
然而,增碳剂在铸造过程中也有一些不足之处。
首先,增碳剂会改变熔渣性质,增加熔点,导致铸件有可能容易脱模,从而影响铸件的尺寸精度。
其次,增碳剂会使铸模、表面处理工艺及后处理工艺复杂化,降低其加工效率。
最后,增碳剂存在一定安全隐患,可能会污染环境。
尽管如此,增碳剂仍是铸造中运用得较广泛的一类材料,在实际应用中,运用正确的增碳剂、做好合理的添加量,以达到良好的加工效果,有利于提高铸件成型优化。
总而言之,增碳剂是影响铸件结构性能和加工效果的重要因素,
若正确选择和控制增碳剂的添加量,可以得到优质的铸件。
因此,在铸造生产中,增碳剂的选择和使用是非常重要的,应加强技术研究和实践探索,以提高铸件的质量。
增碳剂种类

增碳剂种类汇编一、转炉炼钢对增碳剂有什么要求转炉冶炼中、高碳钢种时,使用含杂质很少的石油焦作为增碳剂。
对顶吹转炉炼钢用增碳剂的要求是固定碳要高,灰分、挥发分和硫、磷、氮等杂质含量要低,并要干燥,干净,粒度要适中。
其固定碳ωC≥96%,挥发分≤1.0%,ωS≤0.5%,水分≤0.5%,粒度在1~5mm;粒度太细容易烧损,太粗加入后浮在钢液表面,不容易被钢水吸收。
二、增碳剂的分类按照材质分,一般可以分为:冶金焦增碳剂,煅煤增碳剂,石油焦增碳剂,石墨化增碳剂,天然石墨增碳剂,复合材料增碳剂。
1.石油焦增碳剂石油焦增碳剂采用石油焦煅烧提纯等加工而成,外观成圆粒或多棱形。
其特点高碳、低硫,低灰是冶金化工、机械、电力等行业理想的加碳材料和反应中间体,得到广泛应用。
增碳剂产品技术指标如下冶金焦增碳剂,就是通常冲天炉用的大焦,其作用除了熔炼之外,还有就是为金属炉料增碳。
煅煤增碳剂,主要产自宁夏石嘴山,内蒙乌海。
成分一般为C:90-93%,S0.3-0.5%。
主要用于炼钢企业使用,部分铸造企业用于灰铸铁。
缺点是,碳含量低,融化慢,浪费电能,残余量大。
石油焦增碳剂,主要产于辽宁,天津和山东,辽宁主要生产弹丸焦,用于铸造不太好,山东和天津的石油焦可以用于铸造灰铸铁。
成分一般为C:96-99%;S0.3-0.7%。
主要用于炼钢,灰铸铁,刹车片,包芯线等等。
石墨化增碳剂,主要产地为山东,河南等,生产厂家较少,主要材质是石墨化石油焦和石墨化电极。
一般成分为碳含量>98-99.5%;硫<0.05-0.03%。
主要用于球墨铸铁。
特点是吸收快,碳高硫低。
天然石墨增碳剂,主要是天然石墨,碳65-99%不等,主要用于炼钢厂,铸造厂不适用。
复合材料增碳剂,近期市面上有一些人工制造的棍状颗粒或者规则球状颗粒增碳剂,采用石墨粉,焦粉,石油焦等等下脚材料,添加粘结剂用机器压制成型,碳一般在93-97%之间,硫不稳定,一般在0.09-0.7%之间浮动。
炼钢用高效增碳剂_概述及解释说明

炼钢用高效增碳剂概述及解释说明1. 引言1.1 概述炼钢是一种重要的工业生产过程,其中一个关键步骤就是增碳。
在过去的几十年里,为了提高炼钢效率和质量,不断寻求高效增碳剂成为了一个研究热点。
本文将对炼钢用高效增碳剂进行全面概述和解释说明。
1.2 文章结构本文将按照以下结构展开对炼钢用高效增碳剂的介绍和分析:引言部分概述文章的目的和结构;接着介绍炼钢用高效增碳剂的定义、作用以及常见类型与特点;然后阐述使用方法并提供注意事项;之后探讨影响增碳剂选择与研发的主要因素,并对当前常用增碳剂种类进行分析,并介绍最新的研发进展;接下来讲解应用于增碳剂生产中的煤气化技术,包括其概述、优势与挑战以及在增碳剂生产中的研究进展;最后总结文章主要观点与认识提炼,并对未来炼钢用高效增碳剂发展进行展望。
1.3 目的本文的目的是为了全面介绍和解释炼钢用高效增碳剂,包括其定义、作用、常见类型与特点、使用方法与注意事项、选择与研发现状,以及煤气化技术在增碳剂生产中的应用。
通过本文的阐述,读者可以更加深入地理解和掌握炼钢用高效增碳剂相关知识,并对未来该领域的发展进行展望。
2. 炼钢用高效增碳剂2.1 定义与作用:炼钢用高效增碳剂是指在炼钢过程中用于提高钢材中碳含量的一种添加剂。
由于碳元素在钢材中的含量对其物理和化学性能具有重要影响,因此增加钢材的碳含量可以改善其硬度、强度和耐磨性等特性。
高效增碳剂作为一种专门设计的添加剂,具有提高增碳效率、降低生产成本和改善产品质量等优点。
2.2 常见类型与特点:目前市场上常见的高效增碳剂主要包括焦炭、纯净焦油和人工石墨等。
这些增碳剂根据其原料来源和制备工艺不同,具有各自的特点。
焦炭是最常用的一种高效增碳剂,它由煤炭经过高温干馏得到。
焦炭具有较高的固定碳含量,并且灰分较少,因此可以有效地提供更多的可利用的纯粹碳源。
此外,焦炭还具有低挥发分和固态结构等特点,使其在炉料中具有较好的耐高温性能和流动性。
纯净焦油是从高效焦化过程中获得的副产品,在增碳剂的应用中也起到重要作用。
增碳剂调整炉前样方法

炉前样使用增碳剂调整碳的方法
耐磨材料厂为近一步降本增效,使用了新材料(增碳剂),现将炉前样使用增碳剂调整碳的方法说明如下(炉前使用增碳剂只适用于炉前铁水含碳量低的情况下):
每加0.5公斤的增碳剂,炉前铁水将增加C:0.04的含碳量;
每加1公斤的增碳剂,炉前铁水将增加C:0.08的含碳量;以此类推。
备注:炉前使用增碳剂只适用于炉前铁水含碳量低的情况下使用。
例如:炉前铁水化验铁水含碳量是C:2.10 则方法如下:2.4-2.1=0.3的含碳量差值;
再用0.3除以0.08(即0.3/0.08=3.75),得出铁水含碳量是C:2.1的情况下,应加3.75公斤的增碳剂。
化验室炉前铁水调整含碳量:低铬球按C:2.40调整,高铬球按C:3.00调整。
其他炉前调整方法“炉前铁水含碳量低加生铁调整方法、炉前铁水含碳量高加废钢调整方法,”跟炉前检验以往调整方法保持不变。
质量检验部 2018-1-1。
增碳剂 用途

增碳剂用途
增碳剂是一种用于增加碳含量的添加剂,广泛应用于冶金、化工、电力等行业。
它可以提高材料的硬度、抗磨性和耐腐蚀性能,是许多工业生产过程中不可或缺的重要材料。
在冶金行业中,增碳剂主要用于钢铁生产过程中的炉渣处理和钢水调质。
炉渣处理是指通过加入增碳剂来调整炉渣中的碳含量,以保证炉渣的稳定性和流动性。
钢水调质则是将增碳剂加入钢水中,通过增加钢水中的碳含量,提高钢的硬度和强度,同时改善钢的韧性和塑性,使其具有更好的机械性能。
在化工行业中,增碳剂常用于有机合成反应中的催化剂。
它能够提高反应物的碳含量,加速反应速率,提高反应的产率和选择性。
例如,增碳剂可以用于合成烯烃、芳烃等有机化合物,广泛应用于石油化工、医药等领域。
在电力行业中,增碳剂主要用于燃煤锅炉的燃烧过程中。
通过向燃烧系统中添加增碳剂,可以提高煤炭的燃烧效率,降低烟气中的氮氧化物和硫氧化物排放,减少环境污染。
同时,增碳剂还可以改善燃烧系统的稳定性和热效率,降低能源消耗,提高发电效率。
除了上述行业外,增碳剂还被广泛应用于其他领域。
例如,在农业中,增碳剂可以用于改善土壤质量,提高农作物的产量和品质。
在环保领域,增碳剂可以用于污水处理和废气处理,帮助净化环境。
在材料科学中,增碳剂可以用于改善材料的导电性和热导性,提高材料的性能和应用范围。
总的来说,增碳剂作为一种重要的添加剂,在各个行业中发挥着重要的作用。
它可以提高材料的性能和质量,改善工业生产过程,促进经济的发展。
随着科技的不断进步,增碳剂的应用范围和效果还将不断扩大和提高,为各行各业的发展带来更多的机遇和挑战。
感应电炉炼钢用增碳剂种类与使用方法

增碳剂介绍分炼钢用增碳剂(中华人民共和国黑色冶金行业标准,YB/T 192-2001炼钢用增碳剂)和铸铁用增碳剂,以及其他一些添加材料也有用到增碳剂,譬如刹车片用添加剂,作摩擦材料。
增碳剂属于外加炼钢、炼铁增碳原料。
优质增碳剂是生产优质钢材必不可少的辅助添加剂。
增碳剂的原料有很多种,生产工艺也各异,有木质碳类,煤质碳类,焦炭类,石墨类等,其中各种分类下又有很多小种类。
优质增碳剂一般指经过石墨化的增碳剂,在高温条件下,碳原子的排列呈石墨的微观形态,所以称之为石墨化。
石墨化可以降低增碳剂中杂质的含量,提高增碳剂的碳含量,降低硫含量。
增碳剂在铸造时使用,可大幅度增加废钢用量,减少生铁用量或不用生铁。
电炉熔炼的投料方式,应将增碳剂随废钢等炉料一起往里投放,小剂量的添加可以选择加在铁水表面。
但是要避免大批量往铁水里投料,以防止氧化过多而出现增碳效果不明显和铸件碳含量不够的情况。
增碳剂的加入量,根据其他原材料的配比和含碳量来定。
不同种类的铸铁,根据需要选择不同型号的增碳剂。
增碳剂特点本身选择纯净的含碳石墨化物质,降低生铁里过多的杂质,增碳剂选择合适可降低铸件生产成本。
2碳剂的使用在冶炼过程中,由于配料或装料不当以及脱碳过量等原因,有时造成钢中碳含量没有达到顶期的要求,这时要向钢液中增碳。
常用的增碳剂有增碳生铁、电极粉、石油焦粉、木炭粉和焦炭粉。
转炉冶炼中、高碳钢种时,使用含杂质很少的石油焦作为增碳剂。
对顶吹转炉炼钢用增碳剂的要求是固定碳要高,灰分、挥发分和硫、磷、氮等杂质含量要低,且干燥、干净、粒度适中。
其固定碳组分为:w(C)>96%,挥发分≤1.0%,w(S)≤0.5%,w(水分)≤0.55%,粒度为1一5mm.粒度太细容易烧损,太粗加入后浮在钢液表面,不容易被钢水吸收。
针对感应电炉的颗粒度在0.2-6mm,其中钢和其他黑色金属颗粒度在1.4-9.5mm,高碳钢要求低氮,颗粒度在 0.5-5mm,等等具体需要根据具体的炉型冶炼工件的种类等等细节具体判断和选用。
增碳剂

增碳剂增碳剂分炼钢用增碳剂(中华人民共和国黑色冶金行业标准,YB/T 192-2001炼钢用增碳剂)和铸铁用增碳剂,以及其他一些添加材料也有用到增碳剂,譬如刹车片用添加剂,作摩擦材料。
增碳剂属于外加炼钢、炼铁增碳原料。
优质增碳剂是生产优质钢材必不可少的辅助添加剂。
增碳剂的原料有很多种,生产工艺也各异,有木质碳类,煤质碳类,焦炭类,石墨类等,其中各种分类下又有很多小种类。
优质增碳剂一般指经过石墨化的增碳剂,在高温条件下,碳原子的排列呈石墨的微观形态,所以称之为石墨化。
石墨化可以降低增碳剂中杂质的含量,提高增碳剂的碳含量,降低硫含量。
增碳剂在铸造时使用,可大幅度增加废钢用量,减少生铁用量或不用生铁。
目前绝大多数增碳剂都适用于电炉熔炼,也有少部分吸收速度特别快的增碳剂用于冲天炉。
电炉熔炼的投料方式,应将增碳剂随废钢等炉料一起往里投放,小剂量的添加可以选择加在铁水表面。
但是要避免大批量往铁水里投料,以防止氧化过多而出现增碳效果不明显和铸件碳含量不够的情况。
增碳剂的加入量,根据其他原材料的配比和含碳量来定。
不同种类的铸铁,根据需要选择不同型号的增碳剂。
增碳剂特点本身选择纯净的含碳石墨化物质,降低生铁里过多的杂质,增碳剂选择合适可降低铸件生产成本随着冶金技术的不断进步,为了适应强化冶炼、优质高效的炼钢技术的要求,在钢包内使用增碳剂作为一种补充手段已被普遍采用。
我厂研制开发的钢水增碳剂具有固定碳含量高,硫磷含量低增碳效果稳定,收得率高等优点,在使用时烟尘较小,不污染生产环境。
是钢水增碳的理想材料。
1、技术指标:成分C% S% 挥发物灰分%指标≥95≤0.5≤0.1≤22、产品特点:固定碳含量高,硫分低,增碳效果稳定,碳的收率高。
3、适用范围:用于各种电炉熔炼铸钢、铸铁的增碳。
4、粒度:常用粒度:0-10mm,或按用户特殊要求供货。
5、使用方法:1)配料时调整碳分,根据含碳量的要求熔化钢(铁)水时,随金属炉料加入电炉中部偏下部位,碳的收率可达90%-95%,增碳剂猛药熔化时不要打渣,否则易裹在非废渣里面,影响碳的收;2)钢(铁)水熔化后,调整碳分,可以加在钢(铁)水表面,通过电炉熔炼时钢(铁)水的涡流搅拌或人工搅拌使碳溶解收,碳的收率在85%左右。
增碳剂固定碳的化验方法
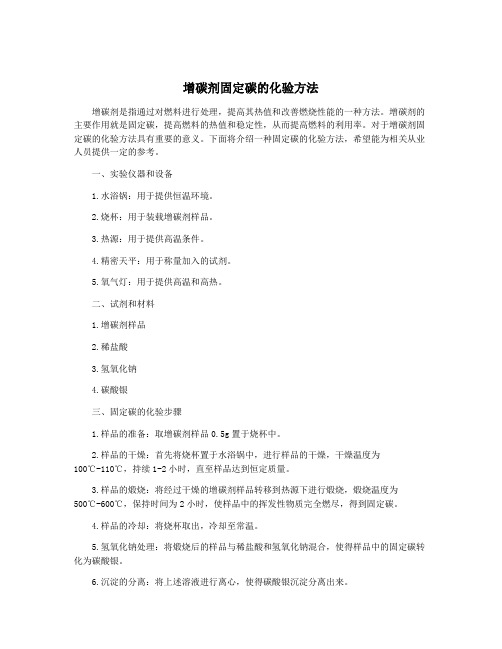
增碳剂固定碳的化验方法增碳剂是指通过对燃料进行处理,提高其热值和改善燃烧性能的一种方法。
增碳剂的主要作用就是固定碳,提高燃料的热值和稳定性,从而提高燃料的利用率。
对于增碳剂固定碳的化验方法具有重要的意义。
下面将介绍一种固定碳的化验方法,希望能为相关从业人员提供一定的参考。
一、实验仪器和设备1.水浴锅:用于提供恒温环境。
2.烧杯:用于装载增碳剂样品。
3.热源:用于提供高温条件。
4.精密天平:用于称量加入的试剂。
5.氧气灯:用于提供高温和高热。
二、试剂和材料1.增碳剂样品2.稀盐酸3.氢氧化钠4.碳酸银三、固定碳的化验步骤1.样品的准备:取增碳剂样品0.5g置于烧杯中。
2.样品的干燥:首先将烧杯置于水浴锅中,进行样品的干燥,干燥温度为100℃-110℃,持续1-2小时,直至样品达到恒定质量。
3.样品的煅烧:将经过干燥的增碳剂样品转移到热源下进行煅烧,煅烧温度为500℃-600℃,保持时间为2小时,使样品中的挥发性物质完全燃尽,得到固定碳。
4.样品的冷却:将烧杯取出,冷却至常温。
5.氢氧化钠处理:将煅烧后的样品与稀盐酸和氢氧化钠混合,使得样品中的固定碳转化为碳酸银。
6.沉淀的分离:将上述溶液进行离心,使得碳酸银沉淀分离出来。
7.碳酸银的烧杂:将碳酸银沉淀转移到氧气灯下烧杂,使其转化为纯净的金属银。
8.固定碳的计算:根据煅烧前后样品的质量差异,计算出增碳剂中固定碳的含量,计算公式为:固定碳含量(%)=(煅烧前质量-煅烧后质量)/样品质量*100%。
通过上述固定碳的化验方法,可以准确、快速地测定增碳剂中固定碳的含量,为燃料改性和燃烧效率的改进提供重要的数据支撑。
在进行实际应用中,应严格按照化验步骤操作,并注意安全操作规程,确保化验结果的准确性和可靠性。
增碳剂种类汇编

一、转炉炼钢对增碳剂有什么要求转炉冶炼中、高碳钢种时,使用含杂质很少的石油焦作为增碳剂。
对顶吹转炉炼钢用增碳剂的要求是固定碳要高,灰分、挥发分和硫、磷、氮等杂质含量要低,并要干燥,干净,粒度要适中。
其固定碳3C296%,挥发分WLO%,ωS≤0.5%,水分<0.5%,粒度在1〜5mm;粒度太细容易烧损,太粗加入后浮在钢液表面,不容易被钢水吸收。
二、增碳剂的分类按照材质分,一般可以分为:冶金焦增碳剂,燃煤增碳剂,石油焦增碳剂,石墨化增碳剂,天然石墨增碳剂,复合材料增碳剂。
1.石油焦增碳剂石油焦增碳剂采用石油焦燃烧提纯等加工而成,外观成圆粒或多棱形。
其特点高碳、低硫,低灰是冶金化工、机械、电力等行业理想的加碳材料和反应中间体,得到广泛应用Q增碳剂产品技术指标如下冶金焦增碳剂,就是通常冲天炉用的大焦,其作用除了熔炼之外,还有备注CPC-燃后石油焦就是为金属炉料增碳Q炊煤增碳剂,主要产自宁夏石嘴山,内蒙乌海。
成分一般为C:90-93%,SO.3-0.5%o主要用于炼钢企业使用,部分铸造企业用于灰铸铁。
缺点是,碳含量低,融化慢,浪费电能,残余量大。
石油焦增碳剂,主要产于辽宁,天津和山东,辽宁主要生产弹丸焦,用于铸造不太好,山东和天津的石油焦可以用于铸造灰铸铁。
成分一般为C:96-99%;SO.3-0.7%o主要用于炼钢,灰铸铁,刹车片,包芯线等等。
石墨化增碳剂,主要产地为山东,河南等,生产厂家较少,主要材质是石墨化石油焦和石墨化电极。
一般成分为碳含量>98-99.5%;硫<0.05-0.03%。
主要用于球墨铸铁。
特点是吸收快,碳高硫低。
天然石墨增碳剂,主要是天然石墨,碳65-99%不等,主要用于炼钢厂,铸造厂不适用。
复合材料增碳剂,近期市面上有一些人工制造的棍状颗粒或者规则球状颗粒增碳剂,采用石墨粉,焦粉,石油焦等等下脚材料,添加粘结剂用机器压制成型,碳一般在93-97%之间,硫不稳定,一般在0.09-0.7%之间浮动。
- 1、下载文档前请自行甄别文档内容的完整性,平台不提供额外的编辑、内容补充、找答案等附加服务。
- 2、"仅部分预览"的文档,不可在线预览部分如存在完整性等问题,可反馈申请退款(可完整预览的文档不适用该条件!)。
- 3、如文档侵犯您的权益,请联系客服反馈,我们会尽快为您处理(人工客服工作时间:9:00-18:30)。
增碳剂的使用方法1、炉内投入法:增碳剂适于在感应炉中熔炼使用,但依据工艺要求具体使用也不尽相同。
(1)在中频电炉熔炼中使用增碳剂,可按配比或碳当量要求随料加入电炉中下部位,回收率可达95%以上;(2)铁液熔清如果碳量不足调整碳分时,先打净炉中熔渣,再加增碳剂,通过铁液升温,电磁搅拌或人工搅拌使碳溶解吸收,回收率可在90左右,如果采用低温增碳工艺,即炉料只熔化一部分,熔化的铁液温度较低的情况下,全部增碳剂一次性加入铁液中,同时用固体炉料将其压入铁液中不让其露出铁液表面。
这种方法铁液增碳可达1.0%以上。
2、炉外增碳:(1)包内喷石墨粉选用石墨粉做增碳剂,吹入量为40kg/t,预期能使铁液含碳量从2%增到3%。
随着铁液碳含量逐渐升高,碳量利用率下降,增碳前铁液温度1600℃,增碳后平均为1299℃。
喷石墨粉增碳,一般采用氮气做载体,但在工业生产条件下,用压缩空气更方便,而且压缩空气中的氧燃烧产生CO,化学反应热可补偿部分温降,而且CO的还原气氛利于改善增碳效果。
(2)出铁时使用增碳剂可将100—300目的石墨粉增碳剂放到包内,或从出铁槽随流冲入,出完铁液后充分搅拌,尽可能使碳溶解吸收,碳的回收率在50%左右。
宁夏宏辉炭素制品有限公司生产的无烟煤增碳剂具有低硫、低灰,含炭量高易吸收等特点。
一、增碳剂的加入时间不能忽视。
增碳剂的加入时间若过早,容易使其附着在炉底附近,而且附着炉壁的增碳剂又不易被熔入铁液。
与之相反,加入时间过迟,则失去了增碳的时机,造成熔炼、升温时间的迟缓。
这不仅延迟了化学成分分析和调整的时间,也有可能带来由于过度升温而造成的危害。
因此,增碳剂还是在加入金属炉料的过程中一点一点地加入为好。
如在一次加入量过大的情况下,可以结合感应电炉时采用的铁液过热操作结合考虑,保证增碳剂在铁液中的吸收时间10Min,一方面通过电磁搅拌作用使增碳剂充分扩散吸收,保证吸收效果。
另一方面可以减少增碳剂中带入的含氮量。
二、加入方法上改进不要一次加入,分批加,最后熔化了加一部分,放一部分(一包左右)铁水到包里,再回冲炉里增碳剂1-2次,然后打渣,加合金。
有以下几个方面需要注意的:1.增碳剂比较难吸收(没有经过煅烧的)2.增碳剂灰分多颗粒分布不均匀3.加入时间太晚4.加入方法不对,采用分层加入。
避免铁液镜面又太多渣的时候加入5.尽量别用太多铁锈的材料。
三、影响增碳效果的因素1、增碳剂粒度对吸收率的影响使用增碳剂的增碳过程包括溶解扩散过程和氧化损耗过程。
增碳剂的粒度大小不同, 溶解扩散速度和氧化损耗速度也就不同, 而增碳剂吸收率的高低就取决于增碳剂溶解扩散速度和氧化损耗速度的综合作用。
在一般情况下, 增碳剂颗粒小, 溶解速度快, 损耗速度大; 增碳剂颗粒大,溶解速度慢, 损耗速度小。
例如, 在110kg 高频感应炉中, 粒度015 ~018mm 的增碳剂溶解速度很快, 在没来得及氧化损耗前大部分已溶解于铁液中, 只有少部分损耗掉, 因此吸收率高。
在60kg 感应炉中, 炉膛的直径和容量较大, 增碳剂粒度015~018mm , 相对炉膛的直径和容量太小, 损耗速度很快, 吸收率低; 而粒度116~312mm 相对于炉膛直径和容量来说, 增碳剂溶解速度较快, 损耗速度较慢, 溶解占据主导作用, 吸收率高〔6〕。
因此, 增碳剂粒度大小的选择与炉膛直径和容量有关, 一般情况下, 炉膛的直径和容量大, 增碳剂的粒度要大一些; 反之, 增碳剂的粒度要小一些。
2、增碳剂加入量对吸收率的影响在一定的温度和化学成分相同的条件下, 铁液中碳的饱和浓度一定。
铸铁中碳的溶解极限为〔C %〕= 113 + 010257 T - 0131〔Si %〕- 0133〔P %〕- 0145 〔S %〕+ 01028〔Mn %〕( T 为铁液温度) 。
在一定饱和度下, 增碳剂加入量越多, 溶解扩散所需时间就越长, 相应损耗量就越大, 吸收率就会降低。
3、饱和浓度一定, 温度对增碳剂吸收率的影响从动力学和热力学的观点分析, 铁液的氧化性与C - Si - O 系的平衡温度有关, 即铁液中的O 与C、Si 有如下的反应〔7〕: 〔Si〕+ 2 〔O〕= SiO2 (s) ,〔C〕+〔O〕= CO(g) ,SiO2 (s) + 2 〔C〕= 〔Si〕+ 2CO(g) 。
Δ G 0T = 549359 - 309145 T (3)lg 〔Si〕〔C〕2 = -27486T+ 15147 (4)平衡温度T 随目标C、Si 含量不同而变化, 如式(4)所示。
依式(4) 可以计算出平衡温度。
当铁液成分( %) 为: 219~311C、110~112Si 时, 平衡温度为1380 ℃左右。
铁液在平衡温度以上时, 优先发生碳的氧化, C 和O 生成CO 和CO2 。
这样, 铁液中的碳氧化损耗增加。
因此, 在平衡温度以上时, 增碳剂吸收率降低。
当增碳温度在平衡温度以下时, 由于温度较低, 碳的饱和溶解度降低, 同时碳的溶解扩散速度下降, 因而收得率也较低。
因此, 增碳温度在平衡温度时, 增碳剂吸收率最高。
但由于在实验室和生产过程中, 铁液温度总会受到诸多因素的影响, 所以, 实际增碳温度在计算出的平衡温度上加减10 ℃左右波动。
4、铁液搅拌对增碳剂吸收率的影响在增碳剂未完全溶解前, 搅拌时间长, 吸收率高。
搅拌有利于碳的溶解和扩散, 减少增碳剂浮在表面被烧损。
搅拌还可以减少增碳保温时间, 使生产周期缩短, 避免铁液中合金元素烧损。
但搅拌时间过长, 不仅对炉子的使用寿命有很大影响, 而且在增碳剂溶解后, 搅拌会加剧铁液中碳的损耗。
因此, 适宜的铁液搅拌时间应以保证增碳剂完全溶解为适宜。
5、铁液化学成分对增碳剂吸收率的影响初始碳量每增加0.1% , 增碳剂吸收率大约降低1 %~2 %; 硅量每增加0.11% , 增碳剂吸收率大约降低3 %~4 %; 硫量每增加0.1% , 增碳剂吸收率大约降低1 %~2 %; 锰量每增加0.1 % , 增碳剂吸收率大约提高2 %~3 %。
由此可见, 当铁液中初始碳含量高时, 在一定的溶解极限下, 增碳剂的吸收速度慢,吸收量少, 烧损相对较多, 增碳剂吸收率低。
当铁液初始碳含量较低时, 情况相反。
另外, 铁液中硅和硫阻碍碳的吸收, 降低增碳剂的吸收率。
而锰元素有助于碳的吸收, 提高增碳剂吸收率。
就影响程度而言, 硅最大, 锰次之, 碳、硫影响较小。
因此, 在实际生产过程中, 应先增锰, 再增碳, 最后增硅。
6、增碳工艺对铸铁组织和性能的影响增碳工艺对铸铁组织的影响经过用增碳剂增碳处理后的铸铁, 在铁液中生成了大量弥散分布的非均质结晶核心, 降低了铁液的过冷度, 促使生成以A 型石墨为主的石墨组织; 同时, 由于生铁用量少, 其遗传作用大为削弱, 因此使A 型石墨片分枝发达不易长大, 使得石墨短小且均匀。
(1)炉料要求:无油无锈, 废钢要求表面不许有过度氧化现象。
(2)一般按每加入100公斤废钢加入增碳剂4公斤准备。
(3)出炉温度控制在1550℃,预计球化降温100℃,手包降温50℃。
(4)第一炉生产时采取在电炉底加入10-20公斤优质铁削。
第二炉起生产时采取上一炉剩余铁液20-40公斤。
(5)铁削加入后用塑料口袋装入规定配入的增碳剂放入铁削上。
第二炉起在剩余铁液20-40公斤上投入塑料口袋装得增碳剂投入铁液面。
(6)加入碳素小颗粒(小于50×50面积)废钢50公斤,紧密覆盖整个炉塘。
(7)启动熔化,加入剩余废钢→加配入生铁→加配入回炉铁(注意回炉铁的表面粘砂不要过多(防止增碳剂与砂粘合影响吸收)。
(8)铁液熔化完毕后用覆盖剂覆盖,温度达到1400℃时反复2-3次清理炉渣。
(9)球化处理吊包装入球化剂、硅铁后用优质铁削覆盖表面。
(10)熔炼完毕用优质除渣剂清理炉内液面溶渣2-3次,检测铁液温度1550℃-1600℃。
(11)铁液出炉采用出铁三分之二铁液时,立即在炉嘴处顺流加入二次硅钡孕育剂。
(12)用优质除渣剂清理溶渣。
提出了当前对增碳剂的认识存在的误区,以及优质增碳剂的选择。
把加增碳剂的熔炼新工艺与传统熔炼(只加生铁)工艺进行对比,分析了增碳剂对熔炼的影响,说明使用中应当注意的问题,阐明了增碳剂的正确使用方法。
关键词:增碳剂;熔炼;一种含碳量很高的黑色或者灰色颗粒(或块状)的焦碳后续产物,加入到金属冶炼炉里,提高铁液里碳的含量,一方面可以降低铁液里氧的含量,另一方面更重要的是提高冶炼金属或者铸件的力学性能。
增碳剂的来源很多,形态各异,根据其加工工艺和成分等不同,价格差异很大。
传统的熔炼方式类似冲天炉熔炼:使用生铁、回炉料、废钢、铁合金等作为金属炉料;新的合成铸铁生产工艺:使用废钢作炉料,利用增碳剂来调整铁液的碳当量。
后一种生产方式更容易保证优质铁液,同时通过少用或者取代生铁改用废钢大大降低成本。
通俗的说,利用增碳剂,我们能用最差的(废钢)炼出最好的(铸件)。
国外增碳技术已经日趋成熟,国内此项新工艺近几年才开始发展,业内很多人对增碳剂的品质和质量了解不够深入,有些铸造工作者选用增碳剂存在误区。
例如混淆增碳剂的固定碳含量和含碳量的含义,固定碳值是根据样品的水分、挥发分、灰分、硫分计算得出的,而含碳量直接测碳仪便可以获得。
有些增碳剂的灰分高,含碳量也高,但是它的固定碳值一定不会太理想。
还有些铸造工作者片面的从增碳剂的固定碳含量和其物质性质便断定其是否优质,其结果很可能误入歧途,导致购入的增碳剂物不所值。
一、增碳剂的选择及其指标性能在冶炼过程中,由于配料或装料不当以及脱碳过量等原因,有时造成钢或铁中碳含量没有达到预期的要求,这时要向钢或铁液中增碳。
通常用来增碳的主要物质有无烟煤粉、增碳生铁、电极粉、石油焦粉、沥青焦、木炭粉和焦炭粉。
对增碳剂的要求是,固定碳含量越高越好,灰分、挥发分及硫等有害杂质含量越低越好,以免污染钢。
铸件的冶炼使用含杂志很少的石油焦经过高温培烧后的优质增碳剂,这是增碳工艺中最重要的环节。
增碳剂质量好坏决定了铁液质量的好坏,也决定了能否获得好的石墨化效果。
简言之,减少铁液收缩增碳剂起到举足轻重的作用。
全废钢电炉熔炼时,优先选用经过了石墨化处理的增碳剂,经过高温石墨化处理的增碳剂,碳原子才能从原来的无序排列变成片状排列,片状石墨才能成为石墨形核的最好核心,以利促进石墨化。
因此,我们应该要选用经过高温石墨化处理的增碳剂。
因为高温石墨化处理时,硫分被生成SO2气体逸出而降低。
所以高品质的增碳剂含硫分很低, w(s)一般小于0.05%,更好的w(s)甚至小于0.03%。
同时,这也是判断是否经过高温石墨化处理以及石墨化是否良好的一个间接指标。
如果选用的增碳剂没经过高温石墨化处理,石墨的形核能力就大大降低,石墨化能力减弱,即使也能达到同样的碳量,但结果完全不一样。