注塑件过程失效模式及后果分析表模板(PFMEA)
注塑PFMEA范本
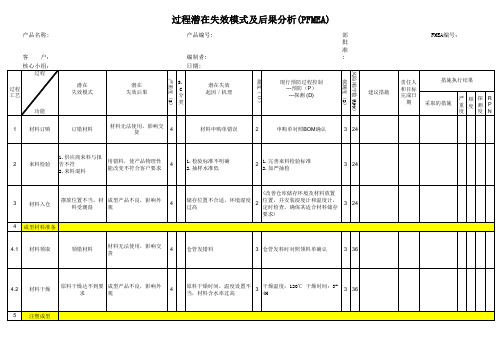
长,保压压力过大 4.模温过低,注射速度过 3
快,注射压力过大 5.注射速度过快,注射压力
过大 6.保压时间不合理,注射压
力不合理(第二段) 7.原材料中含有一定阻燃
剂,导致模具发红
1.升高料温,加大注射压力,延 长保压时间
2.加大注射剂量,加大注射压力 3.加强锁模力,降低料温,减小 注射压力,缩短保压时间,减小
1.制作参数参 照表;提高调 机员的技术水
平 2.经常性清洗 及更换模具配
件
7
2
3 42
5.3 首件确认
外观不良 产品尺寸超差
客户投诉,退货
4
客户投诉,退货
5
2
2 16
未按成型工艺参数表设定
按成型工艺参数表重新设定参数
2
3 30
产品名称:
客 户: 核心小组:
过程 过程 工艺
功能
6 生产自检
潜在 失效模式
责任人 和目标 完成日
期
措施执行结果
采取的措施
严频探 R 重度测 P 度 度N
4
成型条件不稳定
2
对设备进行维修或,使用备用机 台
3
24
7
IPQC 制程检 验
外观不良 产品尺寸超差
客户投诉,退货
4
客户投诉,退货
4
成型条件不稳定 成型条件不稳定
2
对设备进行维修或,使用备用机 台
3
24
2
对设备进行维修或,使用备用机 台
频度(O)
严重度(S)
过程潜在失效模式及后果分析(PFMEA)
产品编号:
编制者: 日期:
过程失效模式及后果分析(PFMEA)

XXX汽车技术股份有限公司潜在失效模式及影响分析 PFMEA螺纹孔内无铝屑,机加工面边缘毛刺清理干净;螺纹孔内有铝屑,机加工面边缘未清理干净影响客户装配,客户抱怨61.丝锥损坏2.夹具松动3.切削液未正确喷淋,铝屑未吹掉31.首检记录表2.巡检记录表354None5XΦ0.341±0.01深0.55(英制)尺寸超差 1.毛坯不合格或尺寸变化大4XΦ0.232±0.01深0.5(英制)尺寸超差 2.夹具松动;3.程序错误2XΦ0.232±0.01深0.5(英制)尺寸超差 4.装夹失误2X4.34±0.02(英制)尺寸超差 1.毛坯不合格或尺寸变化大27.19±0.02(英制)尺寸超差 2.夹具松动;3.程序错误2X7.05±0.02(英制)尺寸超差 4.装夹失误2X11.72±0.02(英制)尺寸超差1.毛坯不合格或尺寸变化大1.25±0.02(英制)尺寸超差2.夹具松动;3.程序错误2.38±0.02(英制)尺寸超差 4.装夹失误1.56±0.02(英制)尺寸超差 1.毛坯不合格或尺寸变化大2.44±0.02(英制)尺寸超差 2.夹具松动;3.程序错误8XΦ0.118±0.01(英制)尺寸超差 4.装夹失误尺寸超差1.毛坯不合格或尺寸变化大2X45°±0.5°尺寸超差2.夹具松动;None3影响装配和功能7631.首检记录表2.巡检记录表3★3影响装配和功能7★31.首检记录表2.巡检记录表363NoneNone63影响装配和功能7★31.首检记录表2.巡检记录表3影响装配和功能7★31.首检记录表2.巡检记录表None影响装配和功能7★31.首检记录表2.巡检记录表36363None。
注塑过程PFMEA失效模式及后果分析
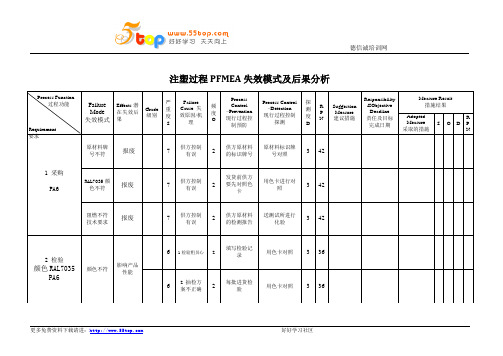
德信诚培训网更多免费资料下载请进: 好好学习社区注塑过程PFMEA 失效模式及后果分析Failure Mode 失效模式 Effects 潜在失效后果Grade 级别严重度SFailure Cause 失效原因/机理频度OProcess Control –Prevention 现行过程控制预防Process Control –Detection 现行过程控制探测探测度DR P N Suggestion Measure 建议措施Responsibility &Objective Deadline 责任及目标 完成日期Measure Result 措施结果Adopted Measure 采取的措施S O D RPN1 采购PA6原材料牌号不符报废 7供方控制有误2供方原材料的标识牌号 原材料标识牌号对照3 42RAL7035颜色不符报废 7供方控制有误2发货前供方要先对照色卡用色卡进行对照3 42阻燃不符技术要求报废 7供方控制有误2供方原材料的检测报告 送测试所进行化验3 422 检验颜色RAL7035PA6颜色不符影响产品性能61检验粗员心 2填写检验记录用色卡对照 3 3662 抽检方案不正确2每批进货检验用色卡对照 3 36Process Function过程功能Requirement 要求。
制程失效模式及效应分析(PFMEA)表
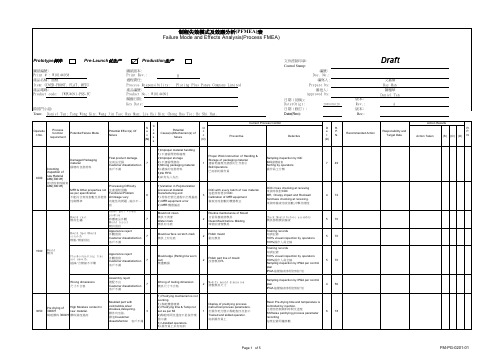
注塑壓力不足
預防性保養機器
IPQA 抽樣檢查參照控制計划
Apperance reject
外觀退貨 Customer dissatisfaction
7
客戶不滿
Apperance reject
外觀退貨 Customer dissatisfaction
7
客戶不滿
Apperance reject
外觀退貨 Customer dissatisfaction
7
客戶不滿
Apperance reject
外觀退貨 Customer dissatisfaction
7
客戶不滿
Injection speed is too slow 射速太慢 Injection perssure less 注塑壓力不足 Melt temprature low 料溫太低
Display of process parameters instructions Training records
Display of predrying process instruction/process parameters. 1 於操作地方展示焗乾程序及指示 Trained and skilled operator. 培訓操作員工
Resin Pre-drying time and temperature is
100% visual inspection by operators 100%操作人員全檢
5 70
運水不通 Injection pressure less
培訓操作員工調機 Preventive maintenance of Machine
Sampling inspection by IPQA per control plan
注塑件过程失效模式及分析PFMEA

3 54
___
___
___ _ _
产品飞边
外观质量下降, 使顾客对外观不 4
满意
材料熔融指数 偏大
5
原材料进货检 验
操作工自 检,检验员 首检、巡检
2
40
___
___
___ _ _
包装
产品变形、表 面擦毛
产品性能、外观 质量下降,顾客
不满意
6
6
操作工自 纸箱偏大或偏小 4 纸箱进货检验 检,检验员 2 48
___
___ _ _ ___ _ _ ___ _ _ ___ _ _ ___ _ _
___ _ _
涂装
产品表面无
项划目伤、颗粒 名、发花等不 车辆良年现/象车辆类型:
核油 符心漆 合小附 海组着南:力马 过自程达MES M功N 能600H标
准要求 要求
潜在 失效模式
潜在 失效后果
潜在失效模式及影响分析
巡检
___ ___
___ ___
___ _ _ ___ _ _
包装 包装完好, 便于储存运
包装损坏
产品外观质量、 性能下降
7
内包衬片偏小
操作工自 5 加强进货检验 检,检验员
巡检
2
70
纸箱附件 进货检验
质量科 衬片印刷所
2003.8.2 配用产品名
5
称
7
2
项目
名 车辆年/车辆类型:
核心小组:
过程 功能
满意
模具型腔划伤
5
模具定期维修 保养
操作工自 检,检验员 首检、巡检
3
90
模具定期 维修保养
生产科 2003.8.2
注塑件 PFMEA过程潜在失效模式及后果分析

过程潜在失效模式及后果分析(PFMEA)产品型号: WX文件编号:版本编号:发布日期:客户名称: 项目名称: 产品料号: PFMEA 编号: 模具编号: 过程责任:关键日期:PFMEA 版本: 小组成员: 修订日期:工序号功能 步骤要求潜在失效 模式潜在失效后果严重度S特性符号失效的潜在 要因发生率O现有设计控制预期现有设计控制探测探测率DRPN建议措施目标完成日期措施结果采取 措施 S O D RPN05 来料检验符合ROHS 要求材料不符合ROHS 违反法律法规9▽供应商未做相应管控2 要求供应商对材质进行禁用合规检查供应商提供报告5 90要求供应商每年一次安排第三方测试并提交测试报告并建立《原材料合规报告管理台账》 2018/12/11供应商SGS 检测报告每年1次并登记《原材料合规报告管理台账》 9 2 4 72未向供应商要求提供禁用物质报告2 要求供应商对材质进行禁用合规检查供应商提供报告5 90UL 阻燃性能合规 原料不符合UL 阻燃要求 客户投诉索赔9▽ 未向供应商要求提供UL合规检测报告2 要求供应商提供UL合规检测报告供应商提供UL合规检测报告5 90建立《原材料合规报告管理台账》并进行2018/12/11 建立《原材料合规报告管理台账》并进行登记9 2 4 72来料规格符合图纸要求 来料规格不符合图纸要求 原材料不能使用 7 供应商送错货 2采购订单明确要求来料检验 4 56材料外观 合格 料粒色泽不均匀,有杂质 原材料不能使用7.供应商来料不良2 进料检验规范中明确定义来料标准 来料检验 4 56来料嵌件尺寸合格尺寸超差嵌件不能装入模具7 嵌件来料不良 2识别嵌件重要尺寸来料检验 4 56顾客投诉7 嵌件来料不良 2识别嵌件重要尺寸来料检验 4 56客户名称: 项目名称: 产品料号: PFMEA 编号: 模具编号: 过程责任:关键日期:PFMEA 版本: 小组成员: 修订日期:工序号功能 步骤要求潜在失效 模式潜在失效后果严重度S 特性符号失效的潜在 要因发生率O现有设计控制预期现有设计控制探测探测率D RPN建议措施目标完成日期措施结果采取 措施S O D RPN10 原料入库有检验合格标签,保证合格品入库 无检验合格 标签,无法辨别是否合格 使用不合格原料生产,使产品报废8原料未检验2 无合格标签,库管员不予办理入库 入库时库管员目视核查348 7 检验后 未贴标签3 无合格标签,库管员不予办理入库入库时库管员目视核查3 63批次清晰无批次标记或标记模糊难辨 无法执行先进先出,原料保质期存在风险6来料批次标记磨损脱落3来料批次登记备查 入库时库管员目视核查35415 生产领料 领用正确材质、牌号物料领料材质或牌号错误无法生产,影响功能和交期 7◇仓库发料错误2 仓库按单发料 受领双方核对456领料单填写错误 2领料单严格按BOM填写生产核料20拌料拌料时间 色纹 客户投诉 7 拌料时间不足2作业指导书中明确时间要求拌料员填写《拌料记录》巡检确认 4 56色粉配比正确色差外观不良 顾客投诉 7 色粉配比错误 3 作业指导书中明确配比要求 拌料员填写《拌料记录》 484 巡检核对《拌料记录》2018/11/12 巡检核对《拌料记录》并签字 7 3 363色粉添加正确且拌料机内清洁无异物颜色不良产品报废8 色粉颜色错误 2作业指导书中明确色粉规格 拌料员填写《拌料记录》348顾客抱怨 投诉7拌料机内有不符合要求物料或色粉残留3拌料前检查料桶拌料员检查并填写《拌料记录》3 63客户名称: 项目名称: 产品料号: PFMEA编号: 模具编号: 过程责任: 关键日期: PFMEA版本: 小组成员: 修订日期:工序号 功能步骤要求潜在失效模式潜在失效后果严重度S特性符号失效的潜在要因发生率O现有设计控制预期现有设计控制探测探测率DRPN 建议措施目标完成日期措施结果采取措施S O D RPN25 烘料 烘料时间、温度等设定正确原料结块无法成型影响效率5烘料时间过长31.作业指导书明确烘料时长及烘料温度2.烘料员自检并填写《烘料记录表》1.烘料员自检;2.巡检员巡检。
注塑P-FMEA表--样表

修模或加工
第 3 页,共 4 页
{注塑(Injection
参照OK样板
Potential Failure Mode And Effective Analyse
潜在失效模式 潜在失效后果 严 重 分级 度 S 现行过程控制 潜在失效起因/机理 预防控制 频度 O 控制探测 风险顺 序数 探测 RPN 度D 建议措施 责任和目 标 完成日期 措施执行结果 采取的措施 严 重 度 频 度 探 测 度 R P N
射胶压力过小 保压压力过小 计量过小 参照OK样板 缩水 影响产品外观 6 射胶速度过慢 保压速度过慢 射胶时间过短 保压时间过短 模温过低/过高 按最新标准更 新的重量标准 重量过轻 重量过重 装配不良 装配不良 6 6 △ △ 注塑参数不合理 注塑参数不合理 出模不顺 I-1010 注塑 拉坏 影响产品功能 7 取出手法不当 擦花 影响产品外观 6 员工操作不当 原料有黑点 料温高,料碳化 使用X-R图控制 使用X-R图控制 《模具保养操作指 引》 严格按取放产品操 作指引操作 培训员工操作手法 每班清理车间环境 制定注塑成型参数 作业指示书,设定 成型参数 严格按《机器设备 保养操作指引》进 行保养 制定注塑成型参数 作业指示书,设定 成型参数、PQC 首检 制定注塑成型参数 作业指示书,设定 成型参数
退回供应商更 换 退回供应商更 换 调整成型参 数,修模 调整成型参数 调整成型参数 和检查模具
4 3
2 2
3 3
24 18
3
2
3
18
4 5 4
2 3 3 3 3 1 3 4 4 2 2 1 2 3
3 2 2 2 2 5 2 2 2 3 4 4 3 3
12 30 24 36 24 30 30 24 40 24 40 12 36 45
过程潜在失效模式及后果分析表PFMEA--注塑焊接

3
1、每个风轮都 要动平衡的测量 目视检测平衡 。 机上参考的读 2、人离开机时 数确认 风轮不能停在机 台上。
3
1、每个风轮都 要经过动平衡 机的测量。 54 2、人离开机时 风轮不能停在 机台上。
1、每个风轮都要 经过动平衡机的测 1.IPQC检验记录 量。 6 3 3 54 表2、工艺卡 2、人离开机时风 轮不能停在机台上 。
1.工具校正后使用 不当出现错误 无法精准的 5 2.工具校正误差太 测量不良点 大,不适用 3.工具校正过期
3
1.建立工具保 养维护制度 2.培训正确使 用工具
1.核查设备校正 清单 2.考核设备使用 维护
5
1.定期设备校正 清单更新 2.设备使用维护 75 培训考核 3.设备编号特定 授权管理
1.工具设备清单 2.设备校正计划 表 3.设备校正报告 4.工具维修保养 记录
过程潜在失效模式及后果分析(PFMEA)
PFMEA编号:
项目阶段/过程:注塑件、焊接风轮 类别或产品型号: 核心小组 过程责任:塑料部 关键日期:2016-1-5 PFMEA日期(编制)2016-1-5 共1页,第 1 页 修订:2016-7-4
严 频 工序功能/ 潜在的失 潜在的失效 重 潜在的失效起因/机 现行过程控制 度 效模式 后果 度 预防 要求 理 (O) (S)
1. SV750-5A烘 干记录表2、过 程检验规范3、 《烘干作业指导 书》
1、投料前先试验 好烘干机发热情况 。2. 首检与客人签 6 3 3 54 样作对比目测确认 。
配料(依据 《配料作 色差 业指导书 》)
配料员配色母或色 影响外观要 7 种的比例不符合规 求 定,造成色差。
3
1.投料单注明 相关要求 2.首检确认
PFMEA过程失效模式及后果分析
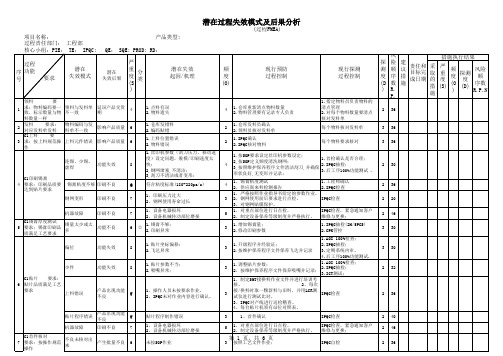
第 1 页,共 6 页
3 按照工艺文件作业;
IPQC检查,紧急通知客户 维修与更换;
IPQC自检
风
措施执行结果
探 测 度 (D )
险 顺 序 数 R. P.
建 议 措 施
责任和 采 目标完 取 成日期 的
措 施
严 重 度 (S)
频 度 (O )
探测 度 (D)
风险 顺 序数 R.P.N
2 36
3 36 3 36
领料
要
1
求:物料编码要一 领料与发料单 致,标示数量与物 不一致
延误产品交货 期
4
料数量一样
2
发料 要求: 对应发料单发料
物料编码与发 料单不一致
影响产品质量
6
C1上料 要
3 求:按上料规范操 上料元件错误 影响产品质量 6
作
连锡、少锡、 虚焊
功能失效
8
C1印刷锡膏
4 要求:印刷品质要 锡膏粘度不够 印刷不良
钢网变形
印刷不良
7
使用前未点检
1.接插件未防护; 2.作业操作失误;
1.摆放不按要求 2.重叠
1.上料位置错误 2.物料错误 1.丝印机参数(刮刀压力,移动速 度)设定问题,脱模/印刷速度太 快; 2,钢网堵塞,不清洁; 3,刮刀不清洁或者变形; 符合粘度标准(180-220pa/s)
1、印刷压力过大 2、钢网使用寿命过长
炉温设定错误
板未放到位 1、板与板叠放产生撞件 2、取放板时板跌落地面引起 3、PCB摆放错误 现场管理不到位 1、现场“5S”未做好 2.物品未标示 未执行工艺要求。 不良位置没有标识。
现场管理不到位 修理技术欠孰练 不按作业规范操作
过程失效模式及后果分析表(PFMEA)(第五版表格)
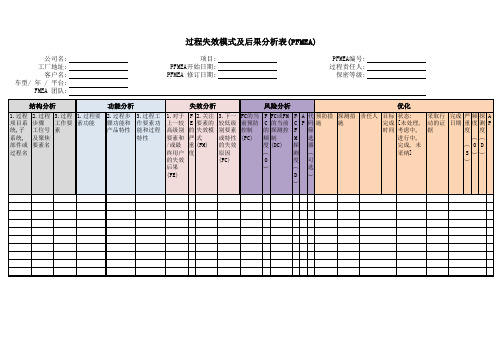
2.过程步 骤功能和 产品特性3.过程工 作要素功 能和过程 特性
1.对于 F 2.关注 3.下一 FC的当 F FC或FM F A 代 预防措 探测措 责任人 目标 状态:
上一较 E 要素的 较低级 前预防 C 的当前 C P 码 施
施
完成 [未处理,
高级别 的 失效模 别要素 控制 的 探测控 F 筛
时间 考虑中,
要素和 严 式
或特性 (PC) 频 制
M选
进行中,
/或最 重 (FM) 的失效
度 (DC) 探 器
完成, 未
()
终用户 度
原因
测
(
采纳]
的失效
(FC)
O
度可
后果
选
)
(FE)
D
采取行 完成 严 频 探 A
动的证 日期 重 度 测 P
据
度度
OD S
() ()
()
()
过程失效模式及后果分析表(PFMEA)
公司名: 工厂地址:
客户名: 车型/ 年 / 平台:
FMEA 团队:
项目: PFMEA开始日期: PFMEA 修订日期:
PFMEA编号: 过程责任人:
保密等级:
结构分析
功能分析
失效分析
风险分析
优化
1.过程 2.过程 3.过程 1.过程要 项目系 步骤 工作要 素功能 统,子 工位号 素 系统, 及聚焦 部件或 要素名 过程名
注塑成型PFMEA完整版
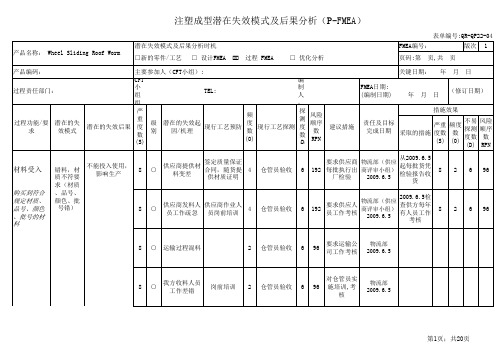
注塑成型潜在失效模式及后果分析(P-FMEA)
表单编号:QR-QP22-04
客户要求,造成退
客户要求,造成退
增加,成本增
风险顺序数(RPN)=(S)*(O)*(D) RPN值超过100需做改善行动. SC表示客户指定特殊特性. T 表示公司自己识别的特性
风险顺序数(RPN)=(S)*(O)*(D)
严重度数(S) 级别 频度数(O) 不易探测度数 (D) 无警告的严重危害 10 严重 ! 很 高 失效率≥1/10 Cpk〈0.33 10 绝对不肯定 10 有警告的严重危害 9 关键 ● 很 高 失效率 1/20 Cpk≥0.33 9 很微小 9 很 高 8 重要 ○ 高 失效率 1/50 Cpk≥0.51 8 微小 8 高 7 一般 --- 高 失效率 1/100 Cpk≥0.67 7 很小 7 中 等 6 客户指定特殊特性, 中 等 失效率 1/500 Cpk≥0.83 6 小 6 低 5 用客户的符号 中 等 失效率 1/2000 Cpk≥1.00 5 中等 5 很 低 4 中 等 失效率 1/10000 Cpk≥1.17 4 中上 4 轻 微 3 低 失效率 1/100000 CPK≥1.33 3 高 3 很 轻 微 2 很 低 失效率 1/1000000 Cpk≥1.50 2 很高 2 FMEA小组成员签署:。
注塑件过程失效模式及分析PFMEA
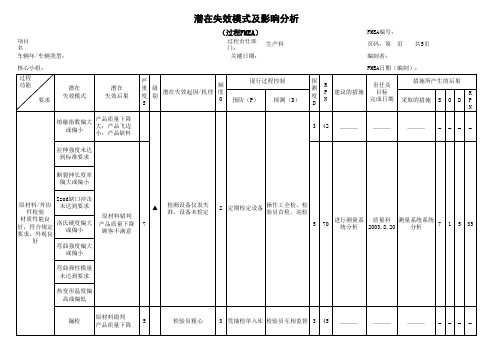
项目名称:侧围(见附表) 过程责任部门:生产科关键日期:
编制者:
FMEA日期(编制):页码:第 页 共5页车辆年/车辆类型:核心小组:
项目名称:侧围(见附表) 过程责任部门:生产科关键日期:
编制者:
FMEA日期(编制):页码:第 页 共5页车辆年/车辆类型:核心小组:
项目名称:侧围(见附表) 过程责任部门:生产科关键日期:
编制者:
FMEA日期(编制):页码:第 页 共5页车辆年/车辆类型:核心小组:
项目名称:侧围(见附表) 过程责任部门:生产科关键日期:
编制者:
FMEA日期(编制):页码:第 页 共5页车辆年/车辆类型:核心小组:
项目名称:侧围(见附表) 过程责任部门:生产科关键日期:
编制者:
FMEA日期(编制):页码:第 页 共5页车辆年/车辆类型:核心小组:
项目名称:侧围(见附表) 过程责任部门:生产科关键日期:
编制者:
FMEA日期(编制):页码:第 页 共5页车辆年/车辆类型:核心小组:▲为与安全和法规无关的产品特殊特性标记。
过程失效模式及后果分析模板(PFMEA)

潜在失效模式
严
潜在失效后果
重 度
级 别
S
潜在失效原因机理
频 度 O
现行控制
探 测 度 D
R P N
建议采取的措施
责任人 完成日期
措施结果 验证 S O D RPN
长度超出上限 下限 报废
4
员工计算失误
4
员工计算失误
6 首件检验 2 首件检验
板材开裂
2
折弯
外型扭曲
报废 报废
4
周转/搬运碰到
XXX 2019/3/2 XXX 2019/3/2 XXX 2019/3/2 XXX 2019/3/2 XXX 2019/3/6 XXX 2019/3/6 XXX 2019/3/6 XXX 2019/3/6 XXX 2019/3/6 XXX 2019/3/7 XXX 2019/3/7 XXX 2019/3/9 XXX 2019/3/9 XXX 2019/3/9
4
周转/搬运碰到
4 巡检 1次/2hr 2 巡检 1次/2hr
孔径规格不符 影响装配
8
钻孔设备精度不够 2 巡检 1次/2hr
3
钻孔 尺寸超差
影响装配
7
钻头定位不准
2 首件检验
位置不对中心 影响装配
7
钻头定位不准
2 首件检验
焊渣飞溅
影响外观
设备调试不良
3 巡检 1次/2hr
3
毛刺未及时磨掉
4 巡检 1次/2hr
过程失效模式及后果分析(PFMEA)
Process Failure Modes and Effects Analysis
产品名称: XXXXXXXXXXXXXXX 小组成员: XXX(开发)、XXX(生产)、XX(品质)、XXX(技术)…
PFMEA 过程失效模式及后果分析
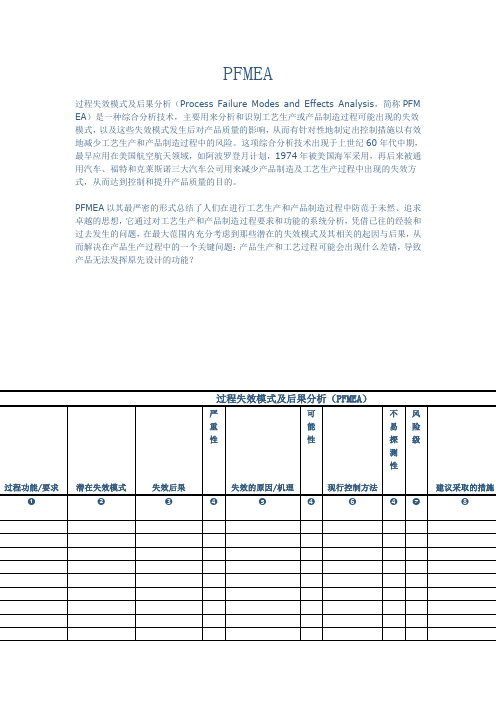
PFMEA过程失效模式及后果分析(Process Failure Modes and Effects Analysis,简称PFM EA)是一种综合分析技术,主要用来分析和识别工艺生产或产品制造过程可能出现的失效模式,以及这些失效模式发生后对产品质量的影响,从而有针对性地制定出控制措施以有效地减少工艺生产和产品制造过程中的风险。
这项综合分析技术出现于上世纪60年代中期,最早应用在美国航空航天领域,如阿波罗登月计划,1974年被美国海军采用,再后来被通用汽车、福特和克莱斯诺三大汽车公司用来减少产品制造及工艺生产过程中出现的失效方式,从而达到控制和提升产品质量的目的。
PFMEA以其最严密的形式总结了人们在进行工艺生产和产品制造过程中防范于未然、追求卓越的思想,它通过对工艺生产和产品制造过程要求和功能的系统分析,凭借已往的经验和过去发生的问题,在最大范围内充分考虑到那些潜在的失效模式及其相关的起因与后果,从而解决在产品生产过程中的一个关键问题:产品生产和工艺过程可能会出现什么差错,导致产品无法发挥原先设计的功能?PFMEA的分析原理如表1-1所示,它包括以下几个关键步骤:§确定与工艺生产或产品制造过程相关的潜在失效模式与起因;§评价失效对产品质量和顾客的潜在影响;§找出减少失效发生或失效条件的过程控制变量,并制定纠正和预防措施;§编制潜在失效模式分级表,确保严重的失效模式得到优先控制;§跟踪控制措施的实施情况,更新失效模式分级表;表1-1 过程失效模式及后果分析这里,(1)“过程功能/要求”:是指被分析的过程或工艺。
该过程或工艺可以是技术过程,如焊接、产品设计、软件代码编写等,也可以是管理过程,如计划编制、设计评审等。
尽可能简单地说明该工艺过程或工序的目的,如果工艺过程包括许多具有不同失效模式的工序,那么可以把这些工序或要求作为独立过程列出;(2)“潜在的失效模式”:是指过程可能发生的不满足过程要求或设计意图的形式或问题点,是对某具体工序不符合要求的描述。
注塑件过程失效模式及分析pfmea
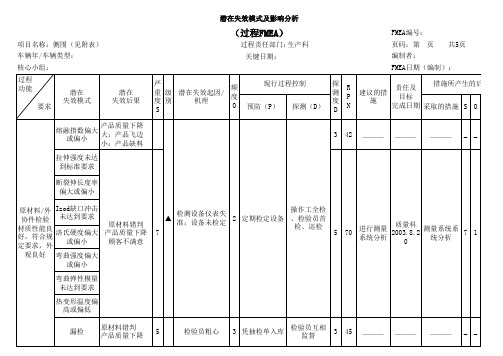
项目名称:侧围(见附表) 过程责任部门:生产科关键日期:
页码:第 页 共5页车辆年/车辆类型:编制者:
核心小组:FMEA日期(编制):
项目名称:侧围(见附表) 过程责任部门:生产科关键日期:
页码:第 页 共5页车辆年/车辆类型:编制者:
核心小组:FMEA日期(编制):
项目名称:侧围(见附表) 过程责任部门:生产科关键日期:
页码:第 页 共5页车辆年/车辆类型:编制者:
核心小组:FMEA日期(编制):
项目名称:侧围(见附表) 过程责任部门:生产科关键日期:
页码:第 页 共5页车辆年/车辆类型:编制者:
核心小组:FMEA日期(编制):
项目名称:侧围(见附表) 过程责任部门:生产科关键日期:
页码:第 页 共5页车辆年/车辆类型:编制者:
核心小组:FMEA日期(编制):
降,顾客不满意
(过程FMEA)
项目名称:侧围(见附表) 过程责任部门:生产科关键日期:
FMEA编号:
页码:第 页 共5页车辆年/车辆类型:编制者:
核心小组:FMEA日期(编制):
产品表面无划伤、颗粒
、发花等不良现象油漆附着力
(过程FMEA)
项目名称:侧围(见附表) 过程责任部门:生产科关键日期:
FMEA编号:
页码:第 页 共5页车辆年/车辆类型:编制者:
核心小组:FMEA日期(编制):
▲为与安全和法规无关的产品特殊特性标记。
- 1、下载文档前请自行甄别文档内容的完整性,平台不提供额外的编辑、内容补充、找答案等附加服务。
- 2、"仅部分预览"的文档,不可在线预览部分如存在完整性等问题,可反馈申请退款(可完整预览的文档不适用该条件!)。
- 3、如文档侵犯您的权益,请联系客服反馈,我们会尽快为您处理(人工客服工作时间:9:00-18:30)。
6
包装破损
零件污染,客户投 诉
5
产品碰伤砸伤 客户投诉
6
装箱时确认不足 货物堆积过高
搬运不规范
2
无
3
试验后制定合理堆 积标准
2
无
100目测 100目测 100目测
5 60 5 75 4 48
标签贴错 发错货,客户投诉 5
标签与实物未核对 2
无
100目测
4 40
产品数量不正确
客户投诉
6
80-出货检验
关键尺寸超差
第 1 页,共 2 页
注塑件过程失效模式及后果分析表模板(PFMEA)
零件号
设计责任部门
FMEA 编号
零件名称
关键日期
编制人
车型/年份
系统/子系统/部件
编制日期
核心小组
序号
过程
潜在的失效模式
严 潜在的失效后果 重
度
级 别
潜在的失效原因/机理
频 度 数
现行预防性设计控 制
现行探测性设计控 制
探 测 度
5 60 5 75
建议措施
责任人和目标 完成日期
无
采取的措施
严频探 R 重度测 P 度数度 N
无
无
无
无
不同产品分区放置, 并做好标识
6
2 5 60
无
对纸箱进行固定 6 2 5 60
无
无
无
无
无
不同产品分区放置, 并做好标识
6
2 5 60
无
对纸箱进行固定 6 2 5 60
无
40-原材料烘料
烘料时间不对 烘料温度不对
表面料花 色差
5 SC 4 SC
料没烘干
2
无
烘干过度
2
无
每班检查次 4 40
无
每班检查一次 4 32
无
注射压力时间不正 确
缺料,产品报废
6
SC
工艺参数设定不合理 2
无
注射压力,保压压 产品飞边,影响产
力不正确
品装配
5
SC
工艺参数设定不合理 2
无
注射速度不正确
R P N
包装破损
材料污染 5
来料运输过程中作业不 规范
2
督促供应商 规范作业
100%目测
3 30
10-进料检验
颜色偏差
注塑产品有色 差,客户投诉
3
原材料色差
2
无
用标准色板进行比 对
3
18
牌号不对
影响生产进度 5
供应商送错货
1
无
核对采购单与送货 单、实物是否一致
3
15
20-原材料入库
包装袋破损 混放
第 2 页,共 2 页
序5号0-注塑产品 过程
潜在的失效模式
严 潜在的失效后果 重
度
级 别
保压时间不正确
表面缩痕,影响外 观,客户投诉
5
SC
潜在的失效原因/机理
频 度 数
现行预防性设计控 制
现行探测性设计控 制
探 测 度
R P N
工艺参数设定不合理 3
无
首检/过程巡检 4 60
关键尺寸超差
影响产品装配, 客户投诉
影响产品装配, 客户投诉
6
产品混装
客户投诉
6
包装破损
零件污染,客户投 诉
5
设备失效,计数不准确 1 检验设备定期送检 巡检抽查
4 24
注射压力不正确/注射速度不正确/ 保压压力不正确/保压时间不正确
2
定期检查全尺寸
首检/过程巡检 5 60
装箱时确认不足 货物堆积过高
2
无
3
试验后制定合理堆 积标准
100目测 100目测
材料污染 5
发错料
4
搬运不规范 标识不清
2
无
领料时检查包装袋 是否有破损
3
30
2
制定管理规范:定置管 理,先进先出
100%目测
3 24
30-领料
领错料
影响计划进度 4
混放/标识不清/ 未核对清楚型号
2
无
确认材料的原包装 标识, 并同领料单进行核对
4
32
修订日期
建议措施
责任人和目标 完成日期
无
无
无
无
无
6
SC
注射压力不正确/注射速度不正确/ 保压压力不正确/保压时间不正确
2
定期检查全尺寸
首检/过程巡检 5 60
标签贴错 发错货,客户投诉 5
标签与实物未核对 2
无
100目测
4 40
60-包装
产品数量不正确
客户投诉
6
设备失效,计数不准确 1 检验设备定期送检 巡检抽查
4 24
70-入库
产品混装
客户投诉
烧焦,影响外观、 产品报废
5
SC
工艺参数设定不合理 2
无
50-注塑产品
模具温度,注塑温 熔接痕,影响性
度不正确
能,客户投诉
5
SC
工艺参数设定不合理 3
无
首检/过程巡检 3 36
无
首检/过程巡检 4 40
无
首检/过程巡检 4 40
无
首检/过程巡检 4 60
无
采取的措施
严频探 R 重度测 P 度数度 N