铸造工艺及其对铸件结构的要求[1]
铸件的结构设计

(a)直角连接 (b)圆角连接 图6-35 转角处的热节
(a)直角连接 (b)圆角连接 图6-36 金属结晶的方向性
2.避免锐角连接
如图6-37(a)所示,锐角连接会由于 内角散热条件差而增大热节,容易产生缩 孔、缩松等铸造缺陷。若两壁间的夹角小 于90°,则应采取过渡形式,如图6-37(b) 所示。
(b)改进后
图6-31 内腔的两种结构
2.便于砂芯固定、排气和铸件清理
如图6-32(a)所示,轴承架铸件的内腔需要采用两个砂芯,其中较 大的砂芯呈悬臂状,需用型芯撑支撑固定;如图6-32(b)所示,将轴承 架铸件的内腔改为整体砂芯,则砂芯的稳定性大大提高,并有利于排气。
(a)改进前
(b)改进后
图6-32 轴承架铸件
铸件中垂直于分型面的不 加工表面最好有结构斜度,以 便于起模或者便于用砂垛代替 砂芯。如图6-34(a)所示的铸 件结构设计不合理,对铸件的 结构斜度进行改进后的合理设 计如图6-34(b)所示。
(a)改进前
(b)改进后
图6-34 结构斜度的设计
二、合金铸造性能对铸件结构的要求
(一)铸件壁厚设计合理
工程材料及成形工艺
铸件的结构设计
一、铸造工艺对铸件结构的要求
铸件的结构设计不应只考虑对其结构性能的影响,还应有利于提高 铸件的工艺水平。所以铸件结构应尽可能使制模、造型、造芯、合箱和 清理过程简单化,防止产生废品,并为实现机械化生产创造条件。铸件 外形力求简单,铸件内腔设计合理是铸造工艺对铸件结构的主要要求。
为保证金属液充满铸型,避免浇不足、冷隔等缺陷的产生,铸件应当有合理 的壁厚。每种铸造合金都有其适宜的壁厚,选择得当,既能保证铸件力学性能, 又能防止铸造缺陷的产生。几种常用铸件在砂型铸造时的最小壁厚如表6-7所示。
铸件结构设计——铸件结构与铸造工艺的关系(精)

2.内腔设计少用芯 安芯排气与清理 事先考虑想仔细
3.“结构斜度”为起模; 设计图上画清晰。 “ 拔模斜度 ”模样留 工艺设计想周细。
减少应力避缺陷。
3. 正确连接铸件壁, 拐弯之处大弧渡, 厚薄不同缓慢过, 过渡结构代锐角。
4. 避免较大水平面
筋辐设计为强化,
合理布置效果显。
作业:
适当倾斜易成形
6.铸钢、铝件易裂处
薄壁筋条防裂好。
7.筋辐设计为强化,
合理布置效果显。
清.翠玉鼻烟壶$:200万
小结; 以下原则要在熟记同时不断深化理解, 力求能应用于工程实践之中。 4.组合铸件 一、结构应使工艺简化 化繁为简,大切小, 具体对铸件而言:
1.简化外形,分形少;
凸肋设计避活块
简化工艺再组合。
二、结构力求避免缺陷 1.壁厚 过厚过薄不合理, 添筋设肋降壁厚, 细化组织省金属, 减少热节防缺陷。 2.铸件壁厚求均匀,
第五章铸件结构设计第五章铸件结构设计铸件结构是指铸件的外形内腔壁厚及壁之铸件结构是指铸件的外形内腔壁厚及壁之间的连接形式加强肋板及凸台等
第五章铸件结构设计
铸件结构是指铸件的外形、内腔、壁厚及壁之 间的连接形式、加强肋板及凸台等。
进行铸件设计不仅要保证其工作要求和 力学性能,还必须考虑铸造工艺和合金铸造 性能对铸件结构的要求。 铸件结构合理与否,对提高铸件质量, 降低成本,增强产品的竞争力有直接关系。 这实际是学习本课的核心、关键、重中 之重,必须用心、努力掌握之。
.
工艺台阶利加工 薄壁筋条防裂好。
铸钢、铝件易裂处
P88~2、3、 5、6、7
化繁为简,大切小, 简化工艺再组合。
二、结构力求避免缺陷
(一)壁厚
1.4 铸件结构设计

机械制造工艺基础----铸造工艺
机械制造工艺基础----铸造工艺
机械制造工艺基础----铸造工艺
3、铸件的结构斜度: 在垂直于分型面的非加工面上设 计结构斜度以便于起模。 结构斜度与起模斜度的区别。
机械制造工艺基础----铸造工艺
二、铸件的内腔设计:
1、减少型芯数量,避免不必要的型芯。 采用自带型芯。尽量采用堆砂。
机械制造工艺基础----铸造工艺
1.4 铸件结构设计
铸件的结构工艺性: 铸件结构主要指铸件的外形、内 腔、壁厚及壁间的连接形式等。
结构工艺性指铸件结构须满足铸
造工艺及合金铸造性能的要求。
机械制造工艺基础----铸造工艺
1.4.1 铸造工艺对铸件结构的要求
一、铸件的外形设计: 1、铸件的形状应尽可能由规则的几何 形体所组成。 2、铸件的外形应方便起模。 铸件外形上的凸台、耳、筋、外圆角等 结构设计常直接影响铸件起模的难易程度。 改进阻碍起模的凸台、凸缘和筋板的结构。 铸件外表尽可能不要有侧凹,减少砂芯数 量。
机械制造工艺基础----铸造工艺
2、铸件的内腔形状设计应有利于型芯的固 定、排气及铸件清理。
机械制造工艺基础----铸造工艺
3、铸件要有结构斜度
机械制造工艺基础----铸造工艺
1.4.2 合金铸造性能对铸件结构的要求
1、铸件的壁厚应均匀,不应过厚或过薄。 壁厚过厚,易产生缩孔、缩松和晶粒粗大; 壁厚过薄,易产生白口、浇不足和冷隔。 铸件尺寸愈大、壁厚可愈厚。但在满足浇注的情 况下,尽可能用筋来减少壁厚。 (1)采用挖空、设筋等减薄铸件壁厚。
机械制造工艺基础----铸造工艺
(2)合理设计铸件 壁厚: • 确定最小允许壁 厚。 • 推荐铸件最大壁 厚约等于三倍的 最小壁厚。 • 铸件的外壁、内 壁与筋的厚度比 约为1:0.8:0.6。
铸钢件生产工艺要求及质量标准
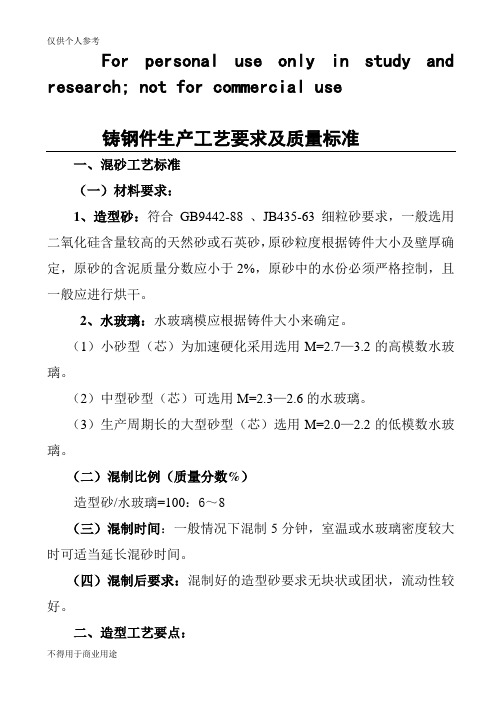
For personal use only in study and research; not for commercial use铸钢件生产工艺要求及质量标准一、混砂工艺标准(一)材料要求:1、造型砂:符合GB9442-88 、JB435-63细粒砂要求,一般选用二氧化硅含量较高的天然砂或石英砂,原砂粒度根据铸件大小及壁厚确定,原砂的含泥质量分数应小于2%,原砂中的水份必须严格控制,且一般应进行烘干。
2、水玻璃:水玻璃模应根据铸件大小来确定。
(1)小砂型(芯)为加速硬化采用选用M=2.7—3.2的高模数水玻璃。
(2)中型砂型(芯)可选用M=2.3—2.6的水玻璃。
(3)生产周期长的大型砂型(芯)选用M=2.0—2.2的低模数水玻璃。
(二)混制比例(质量分数%)造型砂/水玻璃=100:6~8(三)混制时间:一般情况下混制5分钟,室温或水玻璃密度较大时可适当延长混砂时间。
(四)混制后要求:混制好的造型砂要求无块状或团状,流动性较好。
二、造型工艺要点:(一)基本原则:1、质量要求高的面或主要加工面应放在下面。
2、大平面应放在下面。
3、薄壁部分应放在下面。
4、厚大部分应放在上面。
5、应尽量减少砂芯的数量。
6、应尽量采用平直的分型面。
(二)基本要求:1、木模:要求轮廓完整,无裂纹、无破损、无残缺,表面光洁,尺寸符合铸造工艺图纸要求,并经常进行尺寸校验。
2、砂箱:砂箱的尺寸大小应根据木模规格确定,大、中型砂箱应焊接箱筋。
3、浇注系统:根据铸件的结构特点的工艺要求,选择适宜的浇注系统,通常采用顶注式、底注式。
(1)浇注系统设置基本原则:浇口、冒口安放位置合理,大小适宜不妨碍铸件收缩,便于排气、落砂和清理,应使铸型尺寸尽量减少,简化造型操作,节省型砂用量和降低劳动强度。
(2)内浇道位置的注意事项。
1)内浇道不应设在铸件重要部位。
2)应使金属液流至型腔各部位的距离最短。
3)应不使金属液正面冲击铸型和砂芯。
4)应使金属液能均匀分散,快速地充满型腔。
简述铸造工艺对铸件结构的要求

简述铸造工艺对铸件结构的要求
铸造工艺是制造铸件的一种重要工艺,它的质量直接影响着铸件的结构和性能。
因此,铸造工艺对铸件结构的要求非常高。
下面我们来详细了解一下。
铸造工艺要求铸件的结构应该具有良好的一致性。
这是因为铸造工艺中,铸模的制作和铸造过程中的温度、压力等因素都会影响铸件的结构。
如果铸件的结构不一致,就会导致铸件的强度、硬度、韧性等性能不稳定,从而影响铸件的使用寿命。
铸造工艺要求铸件的结构应该具有良好的密度和均匀性。
这是因为铸造工艺中,铸模的制作和铸造过程中的温度、压力等因素都会影响铸件的密度和均匀性。
如果铸件的密度和均匀性不好,就会导致铸件的强度、硬度、韧性等性能不稳定,从而影响铸件的使用寿命。
第三,铸造工艺要求铸件的结构应该具有良好的表面质量。
这是因为铸造工艺中,铸模的制作和铸造过程中的温度、压力等因素都会影响铸件的表面质量。
如果铸件的表面质量不好,就会影响铸件的外观和使用寿命。
铸造工艺要求铸件的结构应该具有良好的尺寸精度。
这是因为铸造工艺中,铸模的制作和铸造过程中的温度、压力等因素都会影响铸件的尺寸精度。
如果铸件的尺寸精度不好,就会影响铸件的装配和
使用寿命。
铸造工艺对铸件结构的要求非常高,铸造工艺的质量直接影响着铸件的结构和性能。
因此,在铸造工艺中,需要严格控制铸模的制作和铸造过程中的温度、压力等因素,以确保铸件的结构、密度、表面质量和尺寸精度等方面都能够达到要求。
铸件的结构设计

避免大水平壁的结构
6、铸件结构应避免冷却收缩受阻和有利于减小变形
铸件在结构设计时,应尽量使其能自由收缩,以减小应力, 避免裂纹。如图所示的弯曲轮辐和奇数轮辐的设计,可使铸件 能较好地自由收缩。
拔模斜度在铸造工艺图上或 模型图上标出。它是对零件图 上没有结构斜度的立壁(垂直 于分型面的非加工面上),给 予的一个较小角度。
(二)铸件内腔的设计 1、 有利于砂芯的固定和排气
型芯的固定主要依靠芯头来保证,若采用图a的结构,则需要 两个型芯,而且其中大的型芯呈悬臂状态,装配时必须采用芯撑 作辅助支撑,若改成图b所示的形状,采用一个整体型芯来形成 铸件的空腔,则既可增加型芯的稳固性,又改善了型芯排气和清 理条件,显然后者的设计是合理的。
1、铸件应有合理的壁厚(铸件壁厚介于临界壁厚和最小壁
厚之间)
最小壁厚:在各种工艺条下,铸造合金能充满型腔的最小厚度。 主要取决于合金的种类、铸件的大小及形状等因素。 临界壁厚:各种铸造合金都存在一个临界壁厚,在砂型铸造条 件下,各种铸造合金临界壁厚约等于其最小壁厚的3倍。
缺陷:如果所设计铸件的壁厚小于允许的 “最小壁厚”,铸件就 易产生浇不足、冷隔等缺陷。在铸造厚壁铸件时,容易产生缩孔、 缩松、结晶组织粗大等缺陷,从而使铸件的力学性能下降。
铸件壁联结应尽量避免金属积聚
3)铸件壁与壁的连接 • 设计结构圆角(减小热节、内应力)
转角处形 成分界面,集 中许多杂质, 为铸件的薄弱 环节。
4、防止产生变形
某些壁厚均匀的细长铸件,较大面积的平板铸件,以及壁 厚不均匀的长形箱体都会由于应力而产生翘曲变形,应采用合 理的结构设计予以解决。
简述铸造工艺对铸件结构的要求

简述铸造工艺对铸件结构的要求铸造工艺是制造铸件的常用工艺之一,具有成本低、生产效率高、生产周期短等优点。
在铸造工艺中,铸件结构的合理设计对提高工艺性能、提高产品质量和降低成本起着重要作用。
首先,铸造工艺对铸件结构要求有以下几点:1.简洁性:铸件的结构设计应尽量简洁,减少过多的孔洞、内腔和悬臂等复杂形状,以降低铸件的成本和制造难度。
2.精确性:铸件的结构设计要考虑到所需的精度和尺寸变化,在设计过程中要保证铸件的尺寸精度和形状精度。
3.可焊性:在铸造工艺中,铸件需要与其他零件进行焊接,因此铸件的结构设计要符合焊接要求,保证焊接良好。
4.强度和刚度:铸件结构设计要考虑到所需的强度和刚度,保证铸件在使用过程中的稳定性和可靠性。
5.声学性:铸件结构设计要考虑到声学要求,避免铸件在使用过程中产生过多的噪音。
其次,铸造工艺对铸件结构要求的具体内容如下:1.浇注系统:铸造工艺要求铸件具有合理的浇注系统,包括浇注口、导流冒、浇口、深水孔等。
浇注系统的设计合理与否直接影响到熔铁的进入、充实和充实性能,影响到铸件的质量。
2.冷却系统:铸造工艺要求在铸造过程中有效控制铸件的冷却速度,避免产生太多的内部应力和组织不均匀等缺陷。
冷却系统的设计包括冷却通道、冷铁、水冷壁等。
3.支撑系统:在铸造过程中,铸件需要支撑来防止变形和开裂。
支撑系统的设计要考虑到铸件的几何形状、重量和固定方式等因素。
4.清洁性:铸造工艺要求铸件具有良好的清洁性能,避免在铸造过程中产生太多的气泡、夹杂物和夹渣等缺陷。
5.铸型材料:铸造工艺要求铸件的结构设计与所选用的铸型材料相匹配,避免因材料特性不合适而导致的缺陷。
总而言之,铸造工艺对铸件结构的要求主要包括简洁性、精确性、可焊性、强度和刚度、声学性等方面。
合理的铸造工艺设计可以提高铸件的品质和可靠性,降低制造成本,为产品的应用提供可靠的基础。
简述铸造工艺对铸件结构的要求
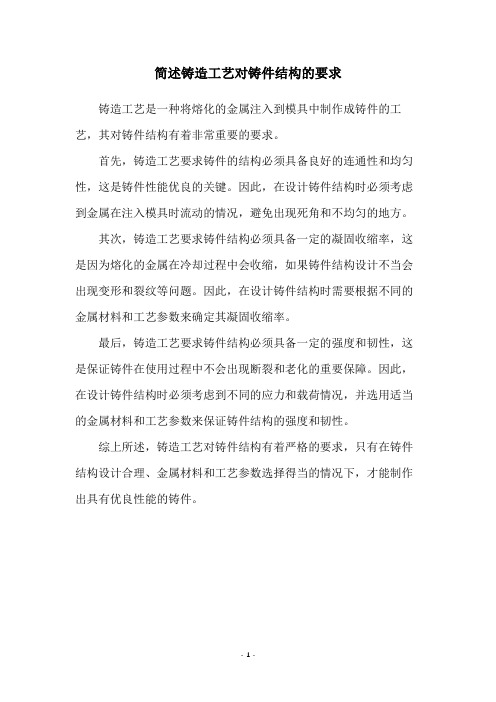
简述铸造工艺对铸件结构的要求
铸造工艺是一种将熔化的金属注入到模具中制作成铸件的工艺,其对铸件结构有着非常重要的要求。
首先,铸造工艺要求铸件的结构必须具备良好的连通性和均匀性,这是铸件性能优良的关键。
因此,在设计铸件结构时必须考虑到金属在注入模具时流动的情况,避免出现死角和不均匀的地方。
其次,铸造工艺要求铸件结构必须具备一定的凝固收缩率,这是因为熔化的金属在冷却过程中会收缩,如果铸件结构设计不当会出现变形和裂纹等问题。
因此,在设计铸件结构时需要根据不同的金属材料和工艺参数来确定其凝固收缩率。
最后,铸造工艺要求铸件结构必须具备一定的强度和韧性,这是保证铸件在使用过程中不会出现断裂和老化的重要保障。
因此,在设计铸件结构时必须考虑到不同的应力和载荷情况,并选用适当的金属材料和工艺参数来保证铸件结构的强度和韧性。
综上所述,铸造工艺对铸件结构有着严格的要求,只有在铸件结构设计合理、金属材料和工艺参数选择得当的情况下,才能制作出具有优良性能的铸件。
- 1 -。
铸造工艺对铸件结构的要求

铸造工艺对铸件结构的要求
铸造工艺对铸件结构的要求主要包括以下几点:
1. 确定合适的铸造工艺和材料,根据铸件的形状、尺寸、壁厚、质量等特点来选择合适的铸造工艺和材料,以确保铸件的成形和质量。
2. 控制铸造温度和速度,合理控制铸造温度和速度,以确保铸
件内部结构均匀致密,不出现太多缺陷和气孔。
3. 保证铸型的质量,铸造工艺要求铸型的质量高,铸型的寿命长,以确保铸件的表面光滑,无毛刺和裂缝。
4. 确保铸件的尺寸和形状精度,铸造工艺要求铸件的尺寸和形
状精度高,以确保铸件的加工量少,节约成本。
5. 控制材料组织和成分,铸造工艺要求铸件材料的组织和成分
均匀稳定,以确保铸件有良好的机械性能和耐腐蚀性能。
以上就是铸造工艺对铸件结构的要求的主要内容,可以帮助铸造
厂家生产出外形美观、尺寸精度高、质量稳定的铸件。
铸造3-铸件结构工艺性

铸件结构工艺性是指铸件结构应符合铸造 生产要求,即满足铸造性能和铸造工艺 对铸件结构的要求。总的原则是:优质、 高产、低耗。
一、铸造性能对铸件结构的要求
Requirements of Foundry Technological Properties to Casting Structure
离心铸机示意图
3、离心铸造的特点
离心铸造的优点: (1)铸件组织致密,无缩孔、缩松、气 孔、夹渣等缺陷。这些均集中在内表面。 (2)铸造中空铸件时,不用型芯和浇注 系统。金属液的充型能力得到提高,可 浇注流动性较差的合金铸件和薄壁铸件。 如涡轮和叶轮等。 (3)便于铸造双金属铸件。
离心铸造的缺点是
从避免铸造缺陷出发,与合金的铸 造性能有关的铸造缺陷如:浇不到、 缩孔、缩松、铸造应力、变形和裂 纹等与铸件结构的关系很密切。如 果采用更合理的铸件结构,便可消 除这些缺陷。 铸件壁及肋的结构特点
1.铸件的壁厚
2.壁的连接
3. 避免变形和裂纹的结构
二、铸造工艺对铸件结构的要求
Requirements of Foundry Technology to Casting Structure 从简化铸造工艺过程出发,高效率、 低成本地生产出合格铸件。 铸件外形及内腔的结构特点 1. 铸件外形力求简单
4、熔模铸造的特点和适用范围
(1)铸件的精度和表面质量较高,
尺寸公差等级为IT11~IT13。 表面粗糙度为Ra12.5~1.6μm。 (2)适用于各种合金铸件,尤其 适用于高熔点及难加工的高合 金钢,如耐热钢、不锈钢、磁 钢等。
(3)可制成形状复杂的铸件最 小孔径为1.5mm,最小壁厚可达 0.7mm。 (4)工艺过程复杂。生产周期 长,铸件成本较高,铸件重量不 超过25kg。
铸件结构工艺性

一. 铸造工艺对铸件结构的要求
2 铸件内腔的设计
一. 铸造工艺对铸件结构的要求
2 铸件内腔的设计 (2) 型芯要便于固定、排气和清理
型芯最好依靠型芯头固定, 尽量避免用型芯撑(使用 型芯撑有时造成渗漏), 同时型芯的排气和清理要方便。
一. 铸造工艺对铸件结构的要求
2 铸件内腔的设计
铸件结构斜度在设计 一. 铸造工艺对铸件结构的要求
液填充,易产生浇不足 和冷隔缺陷。
图2-41 罩壳铸件
故在设计时应避免大水平面, 或将大平面倾斜。
一. 铸造工艺对铸件结构的要求
1. 铸件外形的设计
(1) 分型面尽量减少, 并尽可能为平面
分型面容易使铸件生产错型,影响铸件外 形和尺寸精度,应力求避免两个以上的分型面. 对于机器造型,只允许一个分型面。
一. 铸造工艺对铸件结构的要求
1. 铸件外形的设计
一. 铸造工艺对铸件结构的要求
(2) 铸件外形应尽量方便造型
必要时在铸件薄弱部位设置加强肋板或筋板合理设计铸件壁厚铸件尺寸合金20020020020050050010126101250050018201520铸件壁厚尽可能均匀铸件壁厚均匀是避免因壁厚差别而形成热圆角过渡铸件壁之间圆角过渡可避免产生缩孔缩松以及砂眼和粘砂
§1. 4 铸件结构的工艺性
内容
一. 铸造工艺对铸件结构的要求
时考虑到铸造起模方便, 在垂直
3 铸件结构斜度的设计
于分型面的不加工立壁上应设计出
斜度。一般, 金属模机器造型的设计斜度为
0.5~1°;手工造型为1~3°; 铸件内壁的斜度大于外侧面。
二. 合金铸造性能对铸件结构的要求
1 合理设计铸件壁厚
铸件壁厚设计应大于该合金在一定条件下所
铸造工艺学讲义一(基础知识)

一.熔模铸造 二.金属型铸造 三.压力铸造
第五节 零件结构的铸造工艺性
一.铸件结构的合理性 二.铸件结构的工艺性 三.铸造方法对铸件结构的特殊要求
2
前言
商代司母戊鼎
中国商代晚期的青铜器。1939年于河南安阳殷墟商代晚期墓 出土。因腹内壁铸有“司母戊”三字而得名。该鼎造型庄严雄伟。 长方形腹,每面四边及足上部饰兽面纹。双耳,外侧饰双虎噬人 首纹。四足中空。高133厘米、口长110厘米、口宽79厘米、重 832.84千克。该鼎的化学成分为:铜84.77%,锡11.64%,铅2.79%, 其他0.8%。是中国目前已发现的最大、最重的古代青铜器。
b) 进行去应力退火 铸件机加工之前应先采用时效或去应力退
液态收缩与凝固收缩 主要表现为体积的缩减,
产生缩孔、缩松 固态收缩
导致尺寸减小,产生内 应力和出现裂纹。
18
(三) 影响合金收缩的因素
1. 化学成分 不同成分的合金其收缩率一般也不相同。在常用铸造 合金中铸刚的收缩最大,灰铸铁最小。 2. 浇注温度 合金浇注温度越高,过热度越大,液体收缩越大。 3. 铸件结构与铸型条件 铸件冷却收缩时,因其形状、尺寸的不同, 各部分的冷却速度不同,导致收缩不一致,且互相阻碍,又加之 铸型和型芯对铸件收缩的阻力,故铸件的实际收缩率总是小于其 自由收缩率。这种阻力越大,铸件的实际收缩率就越小。
图1-7 缩松形成过程示意图
21
比较缩孔和缩松的特征
缩孔:集中性,位于上部,呈倒锥形,内表面粗糙。
缩松: 分散性,为细小缩孔,位于铸件壁的轴线区域。
22
2.缩孔、缩松的防止措施 1).定向凝固与同时凝固
按铸件壁厚分布均匀程度不同(即冷却快慢不同),分为: 定向凝固(或称顺序凝固)-薄部先凝固,厚部后凝固,冒口最后 凝固。 同时凝固(厚薄不同部位趋近同时凝固,金属液从薄部引入)。
铸造工艺及对产品设计的要求

4、砂孔、砂眼
特点是孔洞内有型砂。 来源:型腔的散砂(清理不干净), 冲砂(型砂强度不够,或有破损没有修好)。
三、铸造缺陷
5、渣孔(夹渣)
特点是形状不规则,孔洞内有非金属夹杂物。一般位于铸件造型位置 的上边面或死角处。 可分为两类: (1)外生夹渣,(一次)。熔炼、浇注完成以前形成。尺寸大,分布 集中(铁水扒渣不干净,瞬时孕育处理产生的渣,也有涂料,砂等)。 (2)内生夹渣(二次)浇注凝固过程形成,FeS、MnS,QT件多。
c、消失模铸造
二、工艺流程
• 铸造工艺流程简图
二、工艺流程
1、工艺方案
(1) 工艺性审查:通常指零件结构对铸造要求的适应程度。
(2) 生产能力审查:材质、大小、吨位、工装。 (3)最后确定工艺方案、编制工艺图。
铸造工艺规程编制水平的高低,对铸件质量、生产成本和效率起着关键
性的作用。
2、模型制作
制作外模、芯盒(木、金属、塑料)。
12、热处理
热时效 正火
13、入库,或发货
二、工艺流程
复杂热时效曲线
二、工艺流程
•实 例
底 座 零 件 图
二、工艺流程
•实 例
底 座 零 件 工 艺 图
二、工艺流程
•实 例
底 座 模 型
二、工艺流程
•实 例
准 备 造 型
二、工艺流程
•实 例
填 砂 造 下 型
二、工艺流程
•实 例
准 备 造 上 型
方 法。其中铸铁件占70%以上。
C、成本低
铸件在一般机器中占总重40-80%,而成本占25-30%。
机械制造基础第十章铸造习题解答
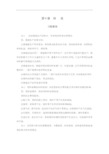
第十章铸造习题解答10-1 试述铸造生产的特点,并举例说明其应用情况。
答:铸造生产的特点有:①铸造能生产形状复杂,特别是内腔复杂的毛坯。
例如机床床身、内燃机缸体和缸盖、涡轮叫叶片、阀体等。
②铸造的适应性广。
铸造既可用于单件生产,也可用于成批或大量生产;铸件的轮廓尺寸可从几毫米至几十米,重量可从几克到几百吨;工业中常用的金属材料都可用铸造方法成形。
③铸造成本低。
铸造所用的原材料来源广泛,价格低廉,还可利用废旧的金属材料,一般不需要价格昂贵的设备。
④铸件的力学性能不及锻件,一般不宜用作承受较大交变、冲击载荷的零件。
⑤铸件的质量不稳定,易出现废品。
⑥铸造生产的环境条件差等。
10-2 型砂由哪些材料组成?试述型砂的主要性能及其对铸件质量的影响。
答:型砂由原砂、粘结剂和附加物组成。
型砂的主要性能有:①耐火度。
型砂的耐火度好,铸件不易产生粘砂缺陷。
②强度。
若强度不足,铸件易产生形状和砂眼等缺陷。
③透气性。
透气性差,浇注时产生的气体不易排出,会使铸件产生气孔缺陷。
④可塑性。
可塑性好,造型时能准确地复制出模样的轮廓,铸件质量好。
⑤退让性。
退让性不好,易使铸件收缩时受阻而产生内应力,引起铸件变形和开裂。
10-3 试列表分析比较整模造型、分模造型、挖砂造型、活块造型和刮板造型的特点和应用情况。
答:列表进行比较:10-4 试结合一个实际零件用示意图说明其手工造型方法和过程。
答:以双联齿轮毛坯手工造型为例,手工造型过程如下:①造下砂型——②造上砂型——③开外浇口、扎通气孔——④起出模样——⑤合型——⑥浇注铁水——⑦带浇口铸件。
10-5 典型浇注系统由哪几个部分组成?各部分有何作用?答:典型浇注系统由浇口杯、直浇道、横浇道和内浇道组成。
浇口杯的作用是将来自浇包的金属引入直浇道,缓和冲击分离熔渣。
直浇道为一圆锥形垂直通道,其高度使金属液产生一定的静压力,以控制金属液流入铸型的速度和提高充型能力。
横浇道分配金属液进入内浇道,并起挡渣的作用,它的断面一般为梯形,并设在内浇道之上,使得上浮的熔渣不致流入型腔。
铸造工艺设计:浇注位置的选择原则、分型面的选择原则[行业荟萃]
![铸造工艺设计:浇注位置的选择原则、分型面的选择原则[行业荟萃]](https://img.taocdn.com/s3/m/68c98db2524de518964b7d61.png)
8
锥齿轮铸件的浇注位置
❖ 锥齿轮铸件的浇注位置
行业借鉴
9
❖ 缸筒和卷筒等圆筒形铸件的关键部位是内外圆 柱面,要求加工后金相组织均匀、无缺陷,其 最佳浇注位置应是内、外圆柱面呈直立状态。
图3 起重机卷筒的浇注位置
(a) 不合理; (b) 合理 行业借鉴
10
铸造工艺设计 一 浇注位置的选择
2 大平面铸件应朝下:
1、铸造工艺对铸件结构的要求
(一)铸件的外形设计 1.铸件应避免外部侧凹以便于起模,减少分型面
端盖的设计
行业借鉴
52
1、铸造工艺对铸件结构的要求
(一)铸件的外形设计 2. 应尽量使分型面平直 平直的分型面可避免操作费时的挖砂造型或假箱造型; 同时,铸件的毛边少,便于清理。
行业借鉴
53
1、铸造工艺对铸件结构的要求
铸造圆角的半径应与铸件的壁厚相适应,一般内圆角
半径可按相邻两壁平均厚度的1/3-l/5选取;外圆
角半径可取内圆角半径的一半。铸造圆角也可在技术
要求中作统一说明。
在相交两平面中,任问一个表面加工后;圆角就被切
去,此时该处就应画成尖行业角借鉴。
47
行业借鉴
48
在确定浇注位置、分型面和各项工艺参数之后,再 经过浇注系统,冒口等的设计,即可按规定的工艺 符号或文字绘制铸造工艺图。
41
行业借鉴
42
3. 收缩率
❖ 铸件冷却后的尺寸比型腔尺寸略为缩小,为 保证铸件的应有尺寸,模样尺寸必须比铸件
放大一个该合金的收缩率。铸造收缩率K表达
式为:
行业借鉴
43
4. 型芯头
❖ 【芯头】是指砂芯的外伸部分,用来定位和 支承砂芯。芯头设计的好坏,对型芯的定位、 稳固、排气和从铸件中的清理,起至关重要 的作用。芯头有垂直和水平芯头两种。芯座 是指铸型中专为放置芯头的空腔。芯头和芯 座尺寸主要有芯头长度 L(高度H)、芯头斜
铸件结构工艺性分析.

铜合金铸件铸造技术 课程
铸件结构工艺性分析
2.铸件 结构 分析 的要 点
1)最 小壁 厚
2)最 小孔 和槽
3)壁 厚的 均匀 性和 壁的 连接
4)平 面大 小
5)顺 序凝 固的 要求
铸件结构设计要力求避免分散的和孤立的热 节,便于实现顺序凝固,以防止产生缩孔和缩 松。
使用横浇道的浇冒口系统
铜合金铸件铸造技术 课程
最大深度 孔的直径 3~5 通孔 5~10 盲孔 5
>5~10
>10~20 >20~40 >40~60
>10~30
>30~60 >60~120 >120~200
>5~15
>15~25 >25~50 >50~80
>60~100
>100
>200~300
>300~350
>80~100
>100~120
铜合金铸件铸造技术 课程
铸件结构工艺性分析
1)最小壁厚 2) 最小孔和槽 3)壁 厚的均匀性和壁的 连接 4)平面大小
2.铸件结构分析的 要点
5)顺序凝固的要 求
注意事项
需要指出的是,铸件结构主要是零件设计人员根据零件的使用要 求及生产、加工等方面要求设计决定的,对某些工艺结构不很合理的 铸件,铸造技术人员应和设计、加工等方面技术人员协商解决。 同时,铸件结构工艺性并不是一个一成不变的概念。随着生产技术、 新材料、新工艺的创新和应用,铸件结构的工艺性问题也会发生变化, 原来难以铸造的铸件变得简易可行了。 ★★第一节课到此结束
铜合金铸件铸造技术 课程
铸件结构工艺性分析
2.铸件结 构分析的 要点 1)最小壁 厚 2)最 小孔和槽
3)壁厚的 均匀性和 壁的连接
4)平面大 小
铸造工艺知识及对产品设计的要求
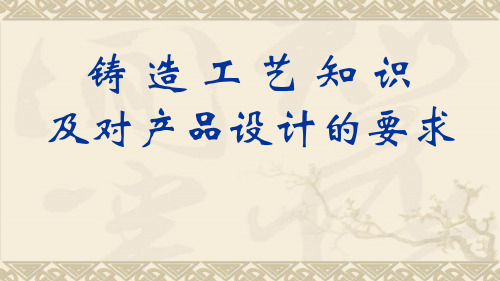
1、铸造工艺流程
2、铸造工艺方案
铸造合金的种类、零件的结构与技术要求、生 产批量的大小和生产条件是确定铸造工艺方案的 依据。
确定铸造工艺方案主要是选择合理的浇注位置 和分型面。
分型面的选择应尽量与浇注位置一致,以避免 合型后翻转砂型。但平做立浇的铸件除外,如压 力机导套。
❖ 使用上表时的几点规定: ❖ ①当铸件尺寸公差等级和铸件机械加工余量等级确定后,其
加工余量数值应按有加工要求的表面上最大基本尺寸和该表 面距它的加工基准间尺寸两者中较大的尺寸所在范围,从表 2中选取加工余量数值。 ❖ ②确定旋转体加工余量时,铸件基本尺寸取其直径或高度 (长度)中较大的尺寸。 ❖ ③当砂型铸件底、侧面所采用的加工余量等级选定后,其顶 面的加工余量等级原则上采用降一级所对应的数值。 ❖ ④砂型铸造孔的加工余量等级由铸造工艺的保证性确定,可 适当加大。原则上降一级。 ❖ ⑤一般情况下一种铸件只能选取一个尺寸公差等级,当有特 殊要求时,可由供需双方商定采用非标准的加工余量。 ❖ 检验与评定时,当铸件实际测量尺寸位于铸件基本尺寸的公
用途是:制造模样、模板、芯盒等,并作为生 产准备和模样验收依据;是用于生产的指导性技 术文件及铸件尺寸验收依据。
铸造工艺卡片
三、铸铁件的热时效处理
对于不进行特殊热处理的重要铸铁件,特别是 机床铸件都要进行低温退火以降低或去除残余应 力,从而保持零件的尺寸精度,这种热处理又称 为热时效。
热时效是将铸件加热至弹塑性温度范围,为使 铸件各部分温度均匀和残余应力在此区间得到松 弛和稳定化而予以保温,然后缓慢冷却至弹性变 形的温度范围内,出炉空冷。
②有色金属铸件:主要生产铜合金铸件和 铝合金铸件。铜合金铸件以压力机铜套为主, 采用电炉熔炼、离心铸造工艺。铝合金铸件 采用砂型(红砂)、电炉熔炼工艺。