滚珠丝杠高速进给系统
在数控机床线性伺服进给系统中用于高速驱动的两颗“明星”——精密高速滚珠丝杠副与直线电动机
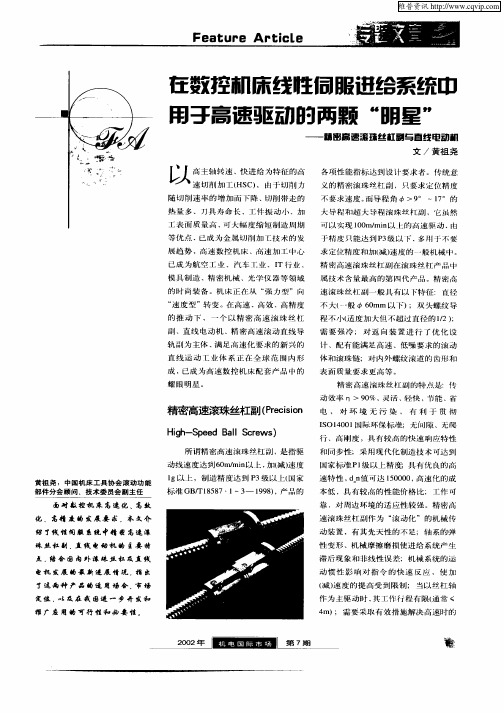
面 对 叙 控 机 床 高 速 化 、高 效
化 、高精 度 的 发 展 要 求 ,本 文 介
绍 了线 性伺 服 系统 中精 密 高速 滚
珠 丝 杠 副 直 线 电 动 机 的 主要 特
点 , 合 国 内 外 滚 珠 丝 杠 及 直 线 结 电机 发 展 的最 新 进 展 情 况 , 出 指 了这 两 种 产 品 的 适 用 场 合 、 场 市
展 趋 势 ,高速 数 控 机床 、高速加 工 中心
已 成 为 航 空 工 业 、 汽 车 _ 业 、I T T行 业 、
精 密 高速滚 珠 丝杠 副在 滚珠 丝 杠产 品 中 属 技 术含 量最 高 的第 四 代产 品 。精密 高
速 滚 珠 丝 杠 副 一 般 具 有 以 卜 征 : 直 径 特 不 大 ( 般 6 mm 以 下 ) 双 头 螺 纹 导 一 0 ; 程 不小 ( 度加 大但 不超 过直 径 的 1 ; 适 / 2) 需 要 强 冷 ; 对 返 向 装 置 进 行 了 优 化 设 计 、 配 有 能 满 足 高 速 、低 噪 要 求 的 滚 动
模 具 制造 、精 密 机械 、光学 仪 器等 领域
的 时 尚 装 备 。机 床 正 在 从 “ 力 型 ” 向 强
“ 度 型 ”转 变 。在 高速 、高 效 、高 精度 速 的 推 动 下 ,一 个 以 精 密 高 速 滚 珠 丝杠
副 、直 线 电 动 机 、精 密 高 速 滚 动 直 线 导
各项 性 能指标 达 到设 计要 求者 。传统 意
义 的 精 密 滚 珠 丝 杠 副 , 只 要 求 定 位 精 度
随 切 削 速 率 的 增 加 而 下降 、切 削 带 走 的 热 量 多 、 刀 具 寿 命 长 、工 件 振 动 小 、加 工 表 面 质 量 高 、 大 幅 度 缩 短 制 造 周 期 可 等 优 点 , 成 为 金 属 切 削 加 技 术 的 发 已
高速加工中滚珠丝杠进给系统性能分析

的负面影 响。闭此滚珠 地杠 进缔系统高速 化所面临的问题
很多 如 ( ) 滚 链市: 速 回 转 时 温 度 L升 驶 热 变 形 1 1 高 ;
圜 2 产生热问 题的主 要 因和 相关因素
()滚珠循 环系统 刚度和 强度 问题 : ()噪 声与振 动 ; 2 3
( )润 滑M题 ; c )夫导程加工技 术; 【 )定位精度变 4 5 6
广泛的应用 在 高速加 T机 床迅速发展的过程 中.进 给系 统速度 的提 高是实现 高速 的主要部件之一 。虽然 目前人们 为丁宴现 高建进给 『探索研 究出直线电机 、并联 虚拟轴 机 床,但 由于它们成本 高以及技 沭不完善等问题 ,还 没能被 广泛接受 .1 而高速滚珠 缱札 螺c 副传动系统 在高速 进给 q - ; J =
程 、降低 转速 是 降低 噪声 的方 式 之 一 ,但 增 大 导程 会 影 响
滚珠 数 与螺 母 长 度 ,因此 可 用 多 头 螺 纹 与 多 圈 数 克 服 。另 外 ,滚珠 丝杠 回转 时 的共 振 现 象 亦 应 考 虑 ,它 与两 端 固定 的 方 式 有 关 。 对 于 高 速 运 行 条 件 应 以 固 定 一 定 方 式 安 装 固 为 宜 ,配 合 中 空 轴 的设 计 不 仅 有 散 热 功 能 ,亦 可 利 用轴 内 液 体 减振 ,同 时 使 危 险速 度 也 提 高 了 2 % 口。 7 ]
驱 动 系统 中仍 然 占 主 导地 位 强 此 .发 展 高速 滚 珠 丝 杠 蝶 母副 是实 现 高 速 切 削 的 ) 键 技 术 之 ・ 乏
l 高建化漾 珠丝杠 系统所 临 州题
升和热变形对定位精度有很大的影响 图 2所示根据有美
表 Hale Waihona Puke 滚珠 丝杠高 速化 的发展历 程
滚珠丝杠副在高速条件下的热位移及抑制对策

虑滚珠丝杠副的预拉伸力 的1 。 ) / 3
2 . 选定并补充适当的润滑剂
滚珠 丝杠副的润滑 剂也影 响滚
增长和运行转速的提高,发热量也
方向发展,所以实现滚珠丝杠副高 速化主要依靠转速的提高。而滚珠 丝杠回转速度的提高必然导致滚珠
丝杠温 度的上升 ,随着温度的上升
随之增大,滚珠丝杠的温度也随之
从式中可以看出,温度每上升
1 ,每 米滚 珠丝杠 轴 长就会 延伸 ℃ 1. m。即使以高精 度加工滚珠 8 1
轴承所承受最大载荷
( 必须考
径有提高转速和加大导程两种,因 机械加工误差的影响,导程越大其
导程精度越 低 ,限制 了其向大导程
丝杠的导程 ,但如在高速的条件下
使用滚珠 丝杠 副 ,随 着运行时 间的
— —
值根据预加负荷类型
选定 ( 见表 1 )
表1 毒 值
臼 ——滚珠丝杠 ( 平均)温升
值 ,℃
L —— 滚珠丝杠长 度 ,m m
预加负荷类型 l 轻载荷l 中载荷f 重载荷 . l 0 . jo 5 . 5 o 0 o7 l 1
轴承座的预紧主要是指轴承的
预紧力 。所选 轴承 的预 紧力应大于
溯蝴
4 . 滚珠丝杠副防护罩的散热
性 能
滚珠丝杠副的使用环境必须是
清洁的,严禁灰尘、粉屑等进入滚 珠丝杠副内,所以必须与防护罩一 起使用。但防护罩的散热性能不能 忽视,因为其散热性能的好与坏直
滚珠丝杠的快速热平衡 强制冷
这制约着此项技术在制造技术中的
应用。
4 . 采用螺母驱动方式或双电 动机驱动结构
升降低 , 影响滚珠丝杠的热位移。
滚珠丝杠进给系统的动力学仿真

第2 2卷
第 1 期
金 陵 科 技 学 院 学 报
Vo . 2. . 12 No 1 Ma . 2 0 r ,0 6
20 06年 3月
J OUR NALOFJNLNG I TI I I NS TUT C EOFTE HNO O Y L G
中 国 分 类 号 : P 9 .2 T 3 1 4 文 献 标 识 码 : A 文 章 编 号 :6 2—7 5 2 0 )1 0 8—0 17 5 X{0 6 0 —0 3 5
Dy a i i u a i n o heBa ls r wsDrv y tm n m cS m l to ft l—c e ieS se
滚珠丝杠 进给 系统的动力学仿真
罗卫 平 ,冯 建 芬2
(. 1 金陵科技学 院 , 江苏
摘南京ຫໍສະໝຸດ 200 ; . 10 1 2 东南大学 , 江苏
南京 2 0 9 ) 1 0 7
要: 以高速数 控机床进 给系统为研究对象 , 根据 负载条 件 , 绍了如何 选择伺 服电机的方法 。利用 A A 介 D MS
LUO e—i g ENG in fn W i n ,F p Ja —e
(.nn stto T cnl y N nn 10 1 C i ; 1J lg n i e f eho g , ajg200 , h a ii I tu o i n
2 Suhat iesy N nig2 0 9 , h a .o tes Unvri 。 aj 1 0 6 C i ) t n n
ADAM S s fwa e o t r .Th t d ft e d n mi e p n e c a a t r t so y t m l o fr t e r s l es u y o h y a c r s o s h r c e i i fs se wi fe h e u t sc l
基于爬行理论的滚珠丝杆进给系统加工波纹度成因的研究

K e r s: sik si bals r w ;r l g g d - a w a i e s y wo d tc - l p; l c e oln uie w y; v n s i
0 引 言
加工 表 面 的 形貌 可 用 面 形 、 纹 度 和 粗糙 度 来 表 波 征 , 面 的几何 形 状 特 征 主要 是加 工进 给运 动 误 差 造 表 成 的。显 然粗 糙度 属 于 高频 成 分 , 纹度 属 于低 频 成 波
Ab ta t s r c :Ba e n t e r fs ik- l bals r w e d s tm a e e r h d a d fito o q e f t a ins s d o h o y o tc si p, l c e f e ys e w sr s a c e n c in t r u ucu to r l o s ce a ela ito u t a in f t e r lng g d - a e e d s u s d,t e balr nnn n a fba ss rw s w l sf ci n f c u to s o h o l uie w y w r ic s e r l i h l u ig i nd o t o h a e y u ft er c wa w a c n ie e o e m an r a o h m ,t e a ilf r e o he b l s rw yse n s o sd r d t b i e s n oft e h xa o c n t al c e s tm i・ c e s d t ucuai n o h ito o q ea xa o c e l ig t e s r w o a ts if e s d c e s d t r a e he f t to ft e f ci n t r u ,nd a ilf r e d ci n h c e c nt c tfn s e r a e he l r n s tm tfn s , hebals rw e d s e c ul tm o t a l n rt e f t a e rc in f r e w hc yse s if e s t l ce fe ys m o d no ves e di u de h ucu td fito o c , t y l ih g n r t d s ra e w a n s . e e ae u f c vie s
超精密滚珠丝杠进给系统谐响应的有限元分析
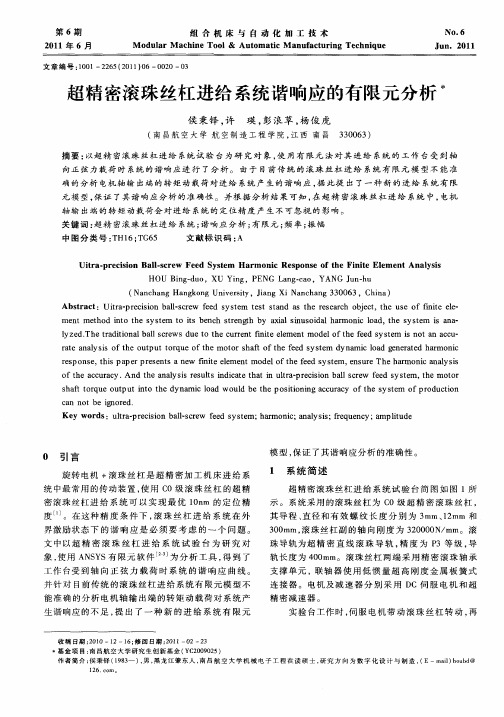
系 统 在 约 为 6 0 z 9 0 z时 , 响 应 的 振 幅 最 大 。 8H 和 9H 谐 所 以 , 实 际 加 工 过 程 中 应 尽 量 避 免 这 个 频 率 的 动 在 载 荷 , 免 造 成 机 床 较 大 的 振 动 , 响 加 工 精 度 。 以 影
图 2 滚 珠 丝杠 副简 化 前 的 模 型
其 导程 、 直径 和 有 效螺 纹 长 度 分 别 为 3 m、2 m 和 m 1m 3 0 m, 0 m 滚珠 丝 杠副 的轴 向 刚度 为 3 0 0 N m 2 0 0 / m。滚 珠 导轨 为超 精 密 直 线 滚 珠 导 轨 , 度 为 P 精 3等 级 , 导 轨长度 为 4 0 0 mm。滚珠丝 杠 两端 采用 精密 滚 珠轴 承 支撑单 元 , 联轴 器 使 用 低 惯量 超 高 刚 度 金属 板 簧 式
m e t me h d i o t e s tm o is b nc te t y xa ius i lham o i o d,t e s t m s a a n t o nt h yse t t e h s rngh b a ilsn oda r nc la h yse i n - l e . yz d Theta iina l s rw s d et hec re i i lm e tmo l h e d s t m sno n a c ・ r dto l bal ce u o t u rntf t ee n de t e fe yse i n e of ta c u rt n l i ft e o t utt r u ft e m o o ha ft e d s tm yn m i o d g n r t d h m o i a e a ayss o h u p o q e o h t rs f o hef e yse d a c l a e e ae a t r nc r s ns , h spa rpr s n s an w iie ee e o e ft e fe ys e , ns r e po e t i pe e e t e f t lm ntm d l h e d s t m e u e Theh r n o a monc a ayss i n l i o h c u a y. n h n l i e ut n c t h ti ta prcso l s rw e d s tm , hem o o ft e a c r c A d t e a ayss r s ls idia et a ul — e iin bal ce fe yse n r t tr s a o q u pu t h yn m i o d w o l e t h f t r ue o t ti o t e d a cl a ud b heposto i g a c a y o he s t m fpr d to t n iin c ur c ft ys e o o uci n n
滚珠丝杠工作原理
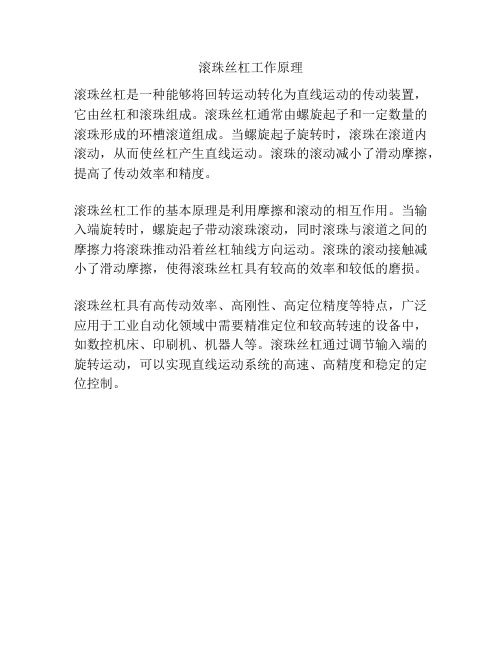
滚珠丝杠工作原理
滚珠丝杠是一种能够将回转运动转化为直线运动的传动装置,它由丝杠和滚珠组成。
滚珠丝杠通常由螺旋起子和一定数量的滚珠形成的环槽滚道组成。
当螺旋起子旋转时,滚珠在滚道内滚动,从而使丝杠产生直线运动。
滚珠的滚动减小了滑动摩擦,提高了传动效率和精度。
滚珠丝杠工作的基本原理是利用摩擦和滚动的相互作用。
当输入端旋转时,螺旋起子带动滚珠滚动,同时滚珠与滚道之间的摩擦力将滚珠推动沿着丝杠轴线方向运动。
滚珠的滚动接触减小了滑动摩擦,使得滚珠丝杠具有较高的效率和较低的磨损。
滚珠丝杠具有高传动效率、高刚性、高定位精度等特点,广泛应用于工业自动化领域中需要精准定位和较高转速的设备中,如数控机床、印刷机、机器人等。
滚珠丝杠通过调节输入端的旋转运动,可以实现直线运动系统的高速、高精度和稳定的定位控制。
滚珠丝杠精度等级标准【必看版】
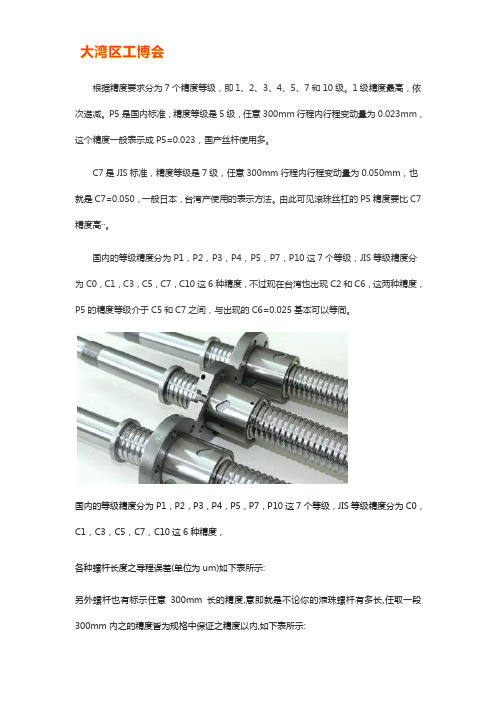
根据精度要求分为7个精度等级,即1、2、3、4、5、7和10级。
1级精度最高,依次递减。
P5是国内标准,精度等级是5级,任意300mm行程内行程变动量为0.023mm,这个精度一般表示成P5=0.023,国产丝杆使用多。
C7是JIS标准,精度等级是7级,任意300mm行程内行程变动量为0.050mm,也就是C7=0.050,一般日本,台湾产使用的表示方法。
由此可见滚珠丝杠的P5精度要比C7精度高··。
国内的等级精度分为P1,P2,P3,P4,P5,P7,P10这7个等级,JIS等级精度分为C0,C1,C3,C5,C7,C10这6种精度,不过现在台湾也出现C2和C6,这两种精度,P5的精度等级介于C5和C7之间,与出现的C6=0.025基本可以等同。
国内的等级精度分为P1,P2,P3,P4,P5,P7,P10这7个等级,JIS等级精度分为C0,C1,C3,C5,C7,C10这6种精度,各种螺杆长度之导程误差(单位为um)如下表所示:另外螺杆也有标示任意300mm长的精度,意即就是不论你的滾珠螺杆有多长,任取一段300mm內之的精度皆为规格中保证之精度以內,如下表所示:【机床定位精度要求与丝杠精度】滚珠丝杠的精度将直接影响数控机床各坐标轴的定位精度。
普通精度的数控机床,一般可选用D级,精密级数控机床选用C级精度滚珠丝杆。
丝杠精度中的导程误差对机床定位精度影响最明显。
而丝杠在运转中由于温升引起的丝杠伸长,将直接影响机床的定位精度。
当L为丝杠螺纹有效长度时,L即为方向目标值T,在丝杠图纸上标示为负值。
用户在定购滚珠丝杠时,必须提出滚珠丝杠的方向目标值。
【提高传动的精度和刚度】主要是提高进给系统中传动零件的精度和支承刚度。
首先是保证各个零件的加工精度,尤其是提高滚珠丝杠螺母副(直线进给系统)、蜗杆副(圆周进给系统)的传动精度。
另外,在进给传动链中加人减速齿轮传动副,对滚珠丝杠和轴承进行预紧,消除齿轮、蜗杆等传动件的间隙,从而提高进给系统的精度和刚度。
高速滚珠丝杠进给驱动系统机械模型的仿真研究

中 图分 类号 : 3 TH 1 2
文献 标志 码 : B
W U h mig .W ANG u k i Z i n J n u
The S m ul to o lM a hi r fH i h S e l S r w i i y t m i a i n M de c ne y o g pe d Ba l c e Drv ng S s e
Ke r s Hi h s e d,B l s r w ,Drv n y t m y wo d : g p e al ce ii g s s e
伴 随着 数控 机 床 加 工 精 度 的 不 断 提 高 , 定 位 其
精 度 已经成 为一 个非 常 重要并 急 需解 决 的 问题 。由
2 Teh oo yDe p rme t eHabn Eler moo a tAC/ DC t rCo Mo o .,Lt Habn 1 0 4 d, r i 5 0 0,Chn ) ia
Ab t a t T hi ap r e t ls d t g p e l s r w e di g s s e e ha c lm od 1 Theke o a a y e t e m e src : s p e sab ihe hehi h s e d bal c e fe n y t m m c nia e. yt n lz h — c nia ys e o h h e i i ng s s e nfu nc nd by usng f ha c ls t m f t e w ol s drvi y t m i l e e a i o M AT IAB c p e i u a in nayss an r — om ut r sm l to a l i d e
数控机床的进给传动系统

详细描述
刚度是指数控机床在受到外力作用时,进给 传动系统抵抗变形的能力。高刚度的数控机 床能够减小受力变形对加工精度的影响,提 高加工质量。
速度与加速度
总结词
速度与加速度是衡量数控机床进给传动系统 动态性能的指标。
详细描述
速度与加速度是指数控机床在加工过程中, 进给传动系统能够达到的最大移动速度和加 速度。高速度和高加速度的数控机床能够缩
更换磨损件
对磨损严重的部件进行更 换,保证进给传动系统的 正常运行。
调整参数
根据实际运行情况,对进 给传动系统的参数进行调 整,优化其性能。
常见故ቤተ መጻሕፍቲ ባይዱ诊断与排除
噪音异常
温度过高
检查进给传动系统是否有异常噪音, 判断是否需要更换轴承或齿轮。
检测进给传动系统的温度,如温度过 高,需检查润滑系统是否正常工作。
03
数控机床进给传动系统的分 类
滚珠丝杠螺母副传动
总结词
滚珠丝杠螺母副传动是数控机床中最常用的进给传动方式之一,具有高精度、 高刚度、高可靠性的特点。
详细描述
滚珠丝杠螺母副传动通过将旋转运动转换为直线运动,实现工作台的进给运动。 其优点在于传动效率高、传动精度稳定、使用寿命长,且具有较高的刚度,能 够满足大多数数控机床的进给传动需求。
运行抖动
观察进给传动系统的运行情况,如有 抖动现象,需检查传动轴是否松动或 损坏。
06
数控机床进给传动系统的未 来发展
高精度化
总结词
随着制造业对产品精度要求的不断提高,数控机床的进给传动系统需要实现更高程度的 精度控制。
详细描述
高精度化是数控机床进给传动系统未来的重要发展方向。通过采用先进的控制系统、高 性能的传动元件和精密加工技术,可以提高数控机床的定位精度、重复定位精度和加工
超精密滚珠丝杠进给系统的谐响应分析

( a c agH nk n nvr t, a c agJ nx 3 0 6 N n hn a go gU i s y N nh n i gi 3 0 3,C ia ei a hn )
Ab ta t n u t — r c s n b l s r w f e y tm ,n to l e e tr a x i t n i x s d i a l x a i ci n u lo s r c :I l a p e ii al c e e d s se r o o n y t xe n e c t i s e it n tb e a i d r t ,b tas h l ao e l e o
Ha m o c Re p ns a y i fUlr - r cso l r w e i y t m r ni s o e An l ss o t a p e ii n Ba lSc e Fe d ng S s e
HOU B n d o,XU Yig E ig u n ,P NG a g a L n c o,YA NG u h Jnu
的振荡特性都可能导致整个 进给系统产生振荡 ,而利用 目前 的滚珠丝杠进给 系统有 限元模型不能 准确地分析 出电机轴输 出
端 的转矩动载荷对进给系统产生的谐响应 。针对此问题 ,提 出一种新 的进 给系统有 限元模 型 ,保 证 了其谐 响应分析 的准确
性。
关键词 :超精密滚珠丝杠进 给系统 ;谐 响应分析 ;有限元 ;频率 ;振幅 中图分类号 :T 19 H 3 文献标识码 :A 文章编号 :10 —38 (0 2 0 1 8 1 2 1 )1—14— 2 2
21 0 2年 1 月
机床与液压
M ACHI NE TO0L & HYDRAUL CS I
滚珠丝杆的工业用途

滚珠丝杆的工业用途
滚珠丝杆是一种传动元件,主要用于精密机械传动系统中,具有高速、高精度、高效率的特点。
工业上常用的滚珠丝杆有以下几种用途:
1. 机床:滚珠丝杆可以用于各种机床的进给传动系统,例如铣床、车床、磨床等。
其高速、高精度的特点可以提高机床的加工效率和加工精度。
2. 机器人:滚珠丝杆被广泛应用于工业机器人的运动控制系统中,用于实现机器人的各个关节的精确移动和定位。
3. 自动化设备:滚珠丝杆也可以作为自动化设备中的传动元件,用于各种自动输送、装配和定位系统中。
例如用于电子设备的面板组装线、汽车工业的焊接生产线等。
4. CNC机床:在数控机床中,滚珠丝杆可以用于实现数控系
统的运动精度和定位控制。
5. 3D打印机:滚珠丝杆也可以用于3D打印机中,用于实现
打印平台的升降和定位控制。
总之,滚珠丝杆在工业中的用途非常广泛,主要应用于各种需要高速、高精度运动控制的设备和系统中。
数控机床的进给系统原理与自动控制方法

数控机床的进给系统原理与自动控制方法随着科技的不断进步和发展,数控机床已经成为现代制造业中不可或缺的重要设备。
数控机床的进给系统是其核心部件之一,它负责控制工件在加工过程中的进给速度和位置。
本文将介绍数控机床进给系统的原理和自动控制方法。
一、数控机床的进给系统原理数控机床的进给系统原理主要基于数学模型和控制理论。
它通过传感器采集工件的位置信息,再经过信号处理和数据分析,最终控制伺服电机的运动。
进给系统的主要组成部分包括伺服电机、滚珠丝杠、编码器和控制器。
伺服电机是进给系统的驱动源,它能够根据控制器的指令来调整自身的转速和转矩,从而实现工件的进给运动。
滚珠丝杠则负责将伺服电机的旋转运动转化为线性运动,通过滚珠丝杠的螺距和转动角度,可以精确控制工件的进给速度和位置。
编码器则用于测量工件的实际位置,将其反馈给控制器,以便及时进行误差修正和调整。
控制器是进给系统的核心,它根据预设的加工参数和工件的实际位置信息,计算出伺服电机的控制指令,并将其发送给伺服电机。
在控制器中,通常会采用PID 控制算法来实现对伺服电机的精确控制。
PID控制算法通过比较工件的实际位置和预设位置的差异,调整伺服电机的转速和转矩,使工件能够按照预设的轨迹进行进给运动。
二、数控机床的自动控制方法数控机床的自动控制方法主要包括手动控制和自动控制两种方式。
手动控制是指操作人员通过控制面板或手柄手动调节数控机床的进给速度和位置。
在手动控制模式下,操作人员可以根据实际情况进行微调和调整,以便更好地掌握加工过程。
手动控制在数控机床的调试和维修过程中起着重要的作用,它可以帮助操作人员及时发现问题并进行处理。
自动控制是指通过预设的加工程序和控制参数,实现数控机床的自动化操作。
在自动控制模式下,操作人员只需输入加工参数和工件的几何信息,数控机床就能够根据预设的程序自动完成加工过程。
自动控制不仅提高了加工效率和精度,还减少了人为因素对加工质量的影响,提高了生产的稳定性和一致性。
高速滚珠丝杠副气液二元冷却系统设计与仿真-中国机械工程

1暋滚珠丝杠副发热量与热变形关系
高速滚珠丝杠进给系统的主要热源有:滚珠丝
杠和螺母的摩擦发热、丝杠两端滚动轴承的摩擦发
热、丝杠端部驱动电机的功率损耗发热[4]。
由于影响机床加工精度的热变形主要是轴线
方向的热 变 形,因 此 不 考 虑 丝 杠 径 向 方 向 的 热 变
形,伸长量和温度的改变关系如下[1,6]:
目前,国内外普遍采用将冷却油通入空心丝杠 进行强制循环冷却的办法来抑制滚珠丝杠的发热 问题,这种全丝杠冷却方法在一定程度上带走了由 于丝 杠 与 螺 母 副 之 间 摩 擦 而 产 生 的 热 量。Kim 等[2]应用有限元方法研究了施 加 轴 向 预 载 荷 的 滚 珠丝杠在不同转速和运行时间下的温度分布规律; Wu等[3]研究 了 滚 珠 丝 杠 进 给 系 统 的 温 度 变 化 和 热变形情况,并用有限元法对滚珠丝杠的热特性进 行了仿真分析;夏 军 勇 等[4]以 传 热 学 理 论 为 基 础, 研究了滚珠丝杠受周期变化的多热源影响而产生 的温度响应及其变化特性。但是,机床在实际加工 过程中,丝杠螺母副并不是在整个丝杠长度上进行 摩擦运动,而 往 往 是 在 某 些 局 部 区 域 频 繁 相 对 运
收 稿 日 期 :2012—06—18 基金项目:国家科技重大专项(2009ZX04001-15);国 家 自 然科 学 基 金 资 助 项 目 (51265023)
动,因而局部区域产生的热量也相对较多。对丝杠 进行全行程 冷 却,只 能 整 体 降 低 丝 杠 的 平 均 温 升, 并不能对运动摩擦相对频繁的局部产生的温升进 行控制[5]。
0暋引言
滚珠丝杠副是高档数控机床进给系统的主要 传动部件。在高速滚珠丝杠副传动系统中,由于接 触区域(丝 杠 螺 母、轴 承 等)产 生 大 量 的 热,导 致 丝 杠产生热变形误差,从而影响机床加工精度并导致 进 给 系 统 传 动 刚 度 降 低[1]。 因 此 ,如 何 抑 制 或 降 低 滚珠丝杠副的热变形,对提高机床加工精度具有重 要意义。
丝杠进给系统的振动模态耦合分析

FglS rw N t c e ai Darm ._ ce u h m t iga S c
人员 利用具体实验对丝杠扭转振动进行 了研究 。 他们都认为耦
合 系统第一阶模态主要是轴向的, 而第二阶和第三阶主要是转角 的, 但是他们 的研究都是在一些 条件假设 以及 特定 环境 下进行
另 外有 : ’ l ox = ) () ( , @( £ )
=
c uc2 k2 “ 绕 轴 的转动刚度 和阻尼分别为 k 0 C 而丝杠 ,; C1 ; ,
同螺母 的接触部位 .是决定轴 向和扭转运动耦合 的关键部位 , 此 处我们同轴承一样 , 考虑其轴向和扭转 的刚度与阻尼外 , 我们引 人了l 台的振动位移 u()设丝杠在 轴方 向的轴向位移为 u T作 。 f ( t, , 而绕 轴的转角位移为 Oxto ) (,
m hn os dl f u d t nt aheehg e om c o t 1 c a iet l a ya o n ai c i ih r r a e nr . o n a o o v p f n c o
Ke or : i eSy t m ; l c e ; up e o i n; br to Fr que y yW ds Dr v se Ba lS r w Co l d M to Vi a i n e nc
【 摘
要】 随着现代机床高速高加速化发展 , 对进给 系统提 出了更高的要求。为研究丝杠进给 系统
的振 动模 态 , 用拉 格 朗 日方程 建 立 了考虑 丝杠轴 向和转 角运动耦 合 的 系统运 动方程 , 利 用里兹 级 利 并 数 展 开对其各 阶模 态在不 同丝杠 导程 下耦 合特 性进行 分析 , 同时分析 了工作 台位 置和 负载质 量 变化 对
大导程滚珠丝杠进给系统动力学建模研究

大导程滚珠丝杠进给系统动力学建模研究张文凯;郑晓果;汤清双;李鹏;白维正【摘要】通过弹性力学中的赫兹接触理论,分析了进给系统动结合部(滑块副、丝杠螺母副、轴承副)的接触刚度.考虑了丝杠的柔性并利用达朗贝尔原理,建立了进给系统的集中参数动力学模型.根据动力学模型,利用MATLAB工具进行了仿真分析;并利用比利时LMS公司提供的b振动噪声测试模块对机床进给系统进行了实验验证.实验分析验证了理论分析的正确性.该建模方法较为准确地预测大导程滚珠丝杠副进给系统的动力学特性,为主动设计进给系统提供了理论依据.【期刊名称】《科学技术与工程》【年(卷),期】2013(013)029【总页数】5页(P8721-8724,8728)【关键词】大导程滚珠丝杠;进给系统;动结合部;接触刚度;集中参数动力学模型【作者】张文凯;郑晓果;汤清双;李鹏;白维正【作者单位】许继德理施尔电气有限公司,许昌461000;许继德理施尔电气有限公司,许昌461000;许继德理施尔电气有限公司,许昌461000;许继德理施尔电气有限公司,许昌461000;许继德理施尔电气有限公司,许昌461000【正文语种】中文【中图分类】O313.3数控机床是当代机械制造业的主流装备,国产数控机床从20世纪80年代开始至今已经历了30年,逐步发展至成熟期;但其高精、高效仍是设计制造数控机床的核心问题。
机床在运动过程中,各部件在不断地相互运动,这种相互运动就形成了动结合部。
诸多研究表明:机床的静刚度中30% ~50%由结合部的刚度特性决定,机床动柔度有60%以上源自结合部,尤其是机床的动结合部[1]。
在而在数控机床中,导轨副、螺丝母副等是最重要的可动结合部。
在机床的进给系统中,其动结合部,如丝杠螺母等,决定该进给系统的动力学特性[2—4]。
在机床进给系统的设计阶段如果没有很好地考虑机械传动部件的动态性能,就会导致工件的加工质量不达标。
张耀满和刘阳[5,6]考虑了滚动直线导轨对数控机床动态性能的影响,并进行了实例分析。
数控机床进给系统滚珠丝杠刚度

第6期(总第175期)2012年12月机械工程与自动化MECHANICAL ENGINEERING & AUTOMATIONNo.6Dec.文章编号:1672-6413(2012)06-0088-02櫜数控机床进给系统滚珠丝杠刚度分析江守生,汪世益,丁 卫,阮超波(安徽工业大学,安徽 马鞍山 243002)摘要:滚珠丝杠作为数控机床进给系统的重要元件,其性能直接影响了进给系统的定位精度。
对滚珠丝杠的刚度进行分析,通过理论计算和大型ANSYS分析软件两种方法分析了滚珠丝杠扭转刚度和轴向刚度对失动量的影响,为进给系统的机构设计和定位精度提高提供了可靠的理论依据。
关键词:滚珠丝杠;ANSYS;刚度;数控进给系统;定位精度中图分类号:TG659 文献标识码:櫜A安徽省教育厅重点项目(KJ2011A043)收稿日期:2012-05-14;修回日期:2012-07-17作者简介:江守生(1986-),男,安徽安庆人,在读硕士研究生,研究方向:数控技术。
0 引言滚珠丝杠由于具有传动效率高、磨损小、运动平稳等特点,在机床中得到了广泛的应用。
滚珠丝杠作为数控机床进给系统的重要元件,其性能直接影响了进给系统的定位精度。
滚珠丝杠的刚度是造成进给系统失动的重要因素[1],因此需要对滚珠丝杠进行刚度分析,以获得最大失动量,为进给系统的机构设计和定位精度提高提供依据。
1 滚珠丝杠刚度计算1.1 滚珠丝杠扭转刚度Kn滚珠丝杆扭转刚度指的是滚珠丝杠抵抗扭转变形的能力,一般用Kn表示,扭转刚度是材料的属性,一般跟材料的截面惯性矩有关[2]。
为简化计算将丝杠等效成实心轴,则对于丝杠来说,扭转刚度Kn(Nm/rad)由下式计算:Kn=GIpL=Gπd432L。
(1)…………………………其中:Ip为轴截面的极惯性矩;d为丝杠的等效直径,m;G为剪切弹性模量,Pa;L为丝杠的总长度,m。
转角θ为:θ=TKn。
(2)……………………………………其中:T为扭矩,N·m。
NNS-16数控冲槽机改造中滚珠丝杠的选择
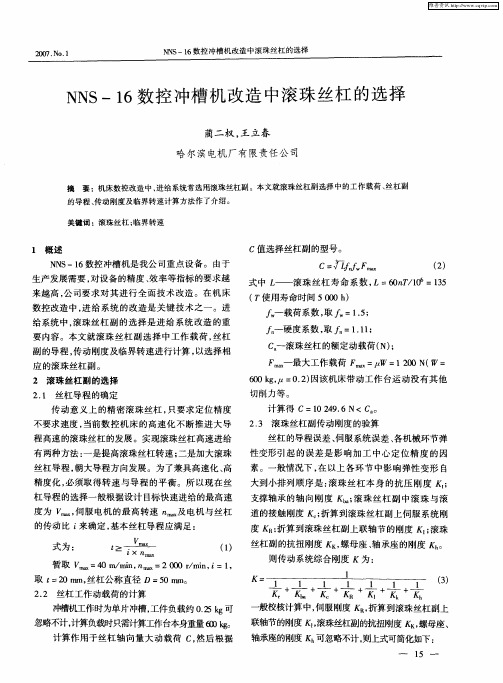
c~ 滚珠 丝杠 的额定 动载 荷 ( ; N) F 一 最大 工作载 荷 F =, =120N( = 一 u W 0 W 60k, =02 因该机床 带 动工 作 台运 动 没有 其 他 0 g/ .) x
切削 力等 。
传 动意 义 上 的精 密 滚珠 丝杠 , 只要 求 定位 精 度
式中 L ——滚珠丝杠寿命系数 , 6 n /0 =15 L= 0 T 1 6 3
( 使用 寿命 时 间 500h 0 )
一
载荷系数 , ^ =15 取 .;
硬度 系数 , 取 =1 1; .1
给系统中, 滚珠丝杠 副的选择是进给系统改造的重
一
要 内容 。本文 就 滚珠 丝 杠 副 选 择 中 工作 载 荷 , 杠 丝 副 的导程 , 动 刚度及 临界转 速 进行计算 , 传 以选择 相 应 的滚珠丝杠 副 。 2 滚珠 丝杠 副 的选择
联轴节 的刚度 l , 滚珠丝杠副 的抗扭刚度 , 螺母座 、
忽略不计, 计算负载时只 需计算工作台本身重量 6 奴。 0 0 计算作用于丝杠轴 向量大动载荷 c 然后根据 ,
轴承座的刚度 K 可忽略不计 , h 则上式可简化如下:
维普资讯
丝杠 副 的抗扭 刚度 K螺 母座 、 承座 的刚度 。 , 轴 则传 动 系统综 合刚度 为 :
的传动比 来确定 , 基本丝杠导程应满足 :
式为 : t 一 坚一 0 ^ /' ax 『 'm / () 1
暂取 一 =4 / i, 0m mn 一 =200rmn 1 0 / i, ,
取 t 2 i 丝杠公称直径 D= 0唧 。 = 0ml l , 5
22 丝杠 工作 动载荷 的计 算 . 冲罐机工作时为单片冲槽 , i 工件负载 约 02 g可 . k 5
- 1、下载文档前请自行甄别文档内容的完整性,平台不提供额外的编辑、内容补充、找答案等附加服务。
- 2、"仅部分预览"的文档,不可在线预览部分如存在完整性等问题,可反馈申请退款(可完整预览的文档不适用该条件!)。
- 3、如文档侵犯您的权益,请联系客服反馈,我们会尽快为您处理(人工客服工作时间:9:00-18:30)。
滚珠丝杠高速进给系统摘要:对高速机床的几种高速进给系统做了一些大致的比较。
着重介绍了高速滚珠丝杠进给系统的性能、特点,对滚珠丝杠高速化所产生的问题及采取的技术措施做了详细的阐述。
关键词:高速进给系统、滚珠丝杠、技术措施。
1.引言高速加工技术是现代先进制造技术之一,其产生是市场经济全球化和各种先进技术发展的综合结果。
高速加工技术逐步发展成为综合性系统工程技术,并得到了越来越广泛的应用。
高速加工是面向21世纪的一项高新技术,它以高效率、高精度和高表面质量为基本特征,在航空航天、汽车工业、模具制造、光电工程和仪器仪表等行业中获得了越来越广泛的应用,并已取得了重大的技术经济效益,是当代先进制造技术的重要组成部分。
在高速加工机床迅速发展的过程中,进给系统速度的提高是实现高速的主要部件之一。
虽然目前人们为了实现高速进给而探索研究出直线电机、并联虚拟轴机床,但由于它们成本高以及技术不完善等问题,还没能被广泛接受,因而高速滚珠丝杠螺母副传动系统在高速进给驱动系统中仍然占主导地位。
因此发展高速滚珠丝杠螺母副是实现高速切削的关键技术之一[1]。
2.几种高速进给系统2.1高速滚珠丝杠进给系统从1958年美国K&T公司生产出世界上第一台加工中心以来,“旋转电动机+滚珠丝杠”至今仍然是加工中心和其他数控机床进给系统采用的主要形式。
滚珠丝杠副传动系统采用交流伺服电机驱动,进给加速度可以达到1g,进给速度可以达到40~60 m/min,定位精度可以达到20~25μm。
相对于采用直线电机驱动的进给系统,采用旋转电机带动滚珠丝杠的进给方案,因为受工作台的惯性以及滚珠丝杠副结构限制,能够实现的进给速度和加速度比较小。
改进后的滚珠丝杠进给速度一般不超过60~80 m/min,加速度小于1.5g。
它在高速加工中心上的应用仍受到一定的限制。
采用滚珠丝杠副传动实现的高速进给系统与采用直线电机驱动的进给系统相比,可以大幅度降低成本。
日本精工已经研制出了进给速度高达100 m/min的滚珠丝杠,采取的改进措施主要有采用16~32mm 大导程,提高滚珠循环部分零件质量,采用多头螺纹以增加有效圈数,改进滚道形状等。
从而实现了进给系统的高速、高刚度以及高承载能力。
2.2直线电机进给驱动系统直线电机驱动实现了无接触直接驱动,避免了滚珠丝杠、齿轮和齿条传动中的反向间隙、惯性、摩擦力和刚度不足等缺点,可获得高精度的高速移动,并具有极好的稳定性。
直线电机的实质是把旋转电机径向剖切开,然后拉直演变而成。
直线电机的转子和工作台固定联结,定子则安装在机床床身上,在机床进给系统中采用直线电机后可以把机床进给传动链的长度缩短为零,从而实现所谓的“零传动”。
直线电机的结构本身也存在着一些不利因素,如直线电机的磁场是敞开的,尤其是采用永磁式直线电机时,要在机床床身上安装一排磁力强大的永久磁铁。
因此必须采取适当的隔磁措施,否则对其磁场周围的灰尘和切屑有吸收作用。
与同容量的旋转电机相比,直线电机的效率和功率因数要低。
尤其在低速时比较明显,但从整个装置和系统来看,由于采用直线电机后省去中间传动装置,系统的效率有时还是比采用旋转电机的高。
另外,直线电机特别是直线感应电动机的起动推力受电源电压的影响较大,故需要采取有关措施保证电源的稳定或改变电机的有关特性来减小或消除这种影响。
虽然采用直线电机驱动的数控机床需要解决如上问题,但是目前在加速度大于1g的情况下,直线电机仍是唯一的选择。
2.3基于并联机构的高速进给系统传统机床的结构一般都是由床身、工作台、立柱、导轨、主轴箱等部件串联而成的非对称的布局,因此机床结构不但要承受拉压载荷,而且还要承受弯扭载荷。
为了保证机床的整体刚度,只能采用结构比较笨重的支撑部件和运动部件,这不但要消耗大量的材料和能源,也制约了机床进给速度和加速度的进一步提高。
刀具和工件之间的相对运动误差是由各坐标轴运动误差线性叠加而成,机床结构的非对称还导致受力和受热的不均匀,这些都影响机床的加工精度。
为了克服传统机床布局上固有的缺陷,满足高速加工的要求,近年来出现了一种全新概念的机床进给机构即并联虚拟轴结构。
具有这种进给机构的机床也被称为并联运动机床。
并联机床是实现高速进给的一种崭新的运动机构,有非常好的应用前景。
但是由于并联机床结构上的限制,其在应用过程中也存在一定的问题,比如有效的工作空间比较小,六轴完全并联的机床运动范围很小,很难同时实现立卧加工,做出的机床往往体积大而实用的工作空间小,这是六杆机床发展初期普遍存在的问题.近年来各个国家都在大力发展混联机床,这种结构机床可以在很大程度上解决工作空间小的问题。
并联机床另一个比较严重的问题是加工精度不高,其原因主要有杆件热变形以及铰关节制造精度的提高十分困难.研究开发结构尺寸小、承载能力强、精度高的复合滚动关节部件是发展并联机床的关键基础技术问题。
并联机床的数控编程和误差补偿比较复杂。
并联机床的自动编程。
特别是自动补偿的难度和工作量都是比较重要和困难的工作[2]。
诚然,直线电机高速进给系统和基于并联结构的高速进给系统具有很多好的优点,但是由于直线电机高速进给较滚珠丝杠成本较高,对一般的加工企业来说承担不起,而基于并联结构的高速进给系统技术发展还不完善。
因此,对滚珠丝杠高速化的研究依然是一个重要方向。
3滚珠丝杠高速化所带来的问题理论上来说,滚珠丝杠的线速度可以简单地通过提高转速实现,但是,提高丝杠的转速也同样存在很多问题,主要表现在以下几个方面:3.1滚珠丝杠螺母副传动系统的刚度较低,受系统共振临界转速的限制。
由滚珠丝杠螺母副组成的振动系统产生共振的临界转速N c,其计算公式为:式中:λ,由支承形式决定的支承系数;L,丝杠支承间距,mm;E,丝杠轴材料的纵向弹性模量,Mpa;I,丝杠轴底径的最小惯性矩,mm4;g,重力加速度,mm/s2;γ,丝杠轴材料的密度,N/mm3;A,丝杠轴底径的横截面积,mm2。
从上式可以看出,丝杠螺母副系统产生共振的临界转速与丝杠轴材质、支承形式、支承间距、丝杠轴底径等因素有关,要提高丝杠的转速不是一个简单的问题[3]。
3.2滚珠受安全转速的限制为了表示滚珠在丝杠螺纹滚道和循环装置内滚动的安全性、可靠性,通常借用滚珠轴承的d0n值(此处d0为滚珠丝杠的名义直径,n为丝杠的转速)来表示滚珠丝杠副的高速极限,实际上,d0n值反映的是滚珠中心线速度的大小。
为方便计算,工程中常以螺杆外径D取代d0n,将该数值称作DN值。
对于φ50mm×30mm的滚珠丝杠,在丝杠转速为3000r/min时,DN值可达15万,进给速度为90m/min。
但同滚动轴承相比,滚珠丝杠螺母副没有防止滚珠之间相互摩擦的保持架,反而多了循环返向装置,这使得滚珠丝杠螺母副的DN值比滚珠轴承的DN值小得多,从而使滚珠能安全、畅通流动的转速受到限制。
3.3温升和热变形的限制丝杠螺母副在高速回转下发热比较严重,使丝杠有较大的温升和热变形,从而影响机床传动精度,有关实验表明,滚珠丝杠螺母副的发热量主要取决于摩擦力,当回转速度增大时,丝杠螺母副产生的热量无法实时散发而造成温升,引起滚珠丝杠轴变形,改变了工件和刀具之间的相对位置,使得加工精度降低。
3.4噪声较大,环保性差据有关试验表明,在未采取降噪减振措施时,滚珠丝杠的转速每提高 1000r/min,噪声提高4~5dB[4]。
高速回转时滚珠丝杠螺母副噪声的来源是滚珠与导珠管的碰撞、滚道表面粗糙度、滚道表面形状和滚珠之间的碰撞,这些因素取决于滚珠丝杠螺母副的加工工艺。
4滚珠丝杠副高速化的技术对策要实现精密滚珠丝杠的高速化,上述问题是必须要面对和解决的,解决上述问题的基础是结构的创新,同时要提高工艺水平和制造质量。
为此,国内外做了大量的工作,也取得了可喜的成绩,其中以日本、瑞典和德国的成绩最引人注目,而日本 NSK 的研究和制造水平更是代表了当今世界精密高速滚珠丝杠副研究和生产的最高水平和发展方向。
在精密滚珠丝杠副的高速化方面主要采用了以下的技术和对策:4.1增大丝杠的导程和螺纹头数滚珠丝杠的进给速度为转速与导程的乘积,因此,实现滚珠丝杠的高速进给的两种方法:一是提高滚珠丝杠转速;二是加大滚珠丝杠导程,朝大导程方向发展。
所谓大导程就是使丝杠导程与丝杠轴外径之比大于或等于1/2。
目前,世界各滚珠丝杠制造商都已经采用了这种技术,日本的NSK还开发了3倍导程系列的产品。
加大丝杠的导程,会使丝杠的导程误差加大,难以保证精度,而且随着导程的加大,启力矩也变大,这会影响传动的平稳性。
所以单纯采取加大丝杠导程的方法难以满足市场需求,须将两种方法配合使用才行。
为了兼具高速化、高精度化,必须取得转速与导程的平衡。
因此滚珠丝杠高速回转能力的提升,也同样非常重要。
采用双头螺纹可以增加滚珠的有效承载圈数,从而提高丝杠的刚度和承载能力,提高滚珠丝杠螺母副在高速运行中的平稳性[5]。
4.2采用空心强冷技术最早将空心强冷技术用于精密高速滚珠丝杠副的日本 NSK 公司,1998 年推出用于高速数控机床的HZC,HZF 和HDF系列高速滚珠丝杠副产品,直径36~55mm,导程16~30mm,DN值150000,最高线速度100m/min,加速度1.3g,双头螺纹。
该公司曾对中空丝杠的各种冷却方法进行试验对比,试验结果表明,采用强制冷却技术效果十分明显,一是温升幅度很小,只有2℃左右,二是到达稳定温度的时间明显缩短,只需要30分钟左右[6]。
日本 MaKino 公司还研制开发了电子冷却器控制系统,可适时监控滚珠丝杠的温升,使其保持在允许范围内。
我国台湾PMI银泰科技公司在空心强冷技术方面采取在一端封闭的空心丝杠中插入冷却油管的专利技术(台湾专利107485)[7],其特点是改变冷却液在丝杠体的循环方式,达到更好的制冷效果,而且结构简单,当线速度为100m/min时可使温度变化控制在1℃内。
该公司在 CIMT2001上展出了FSW,FDW系列双头、多头高速滚珠丝杠产品及噪声测量装置,该产品DN值130000~140000,线速度达到100~120m/min。
为了增强丝杠轴的抗振能力,NSK公司发明了在中空丝杠孔内配置“内藏减振阻尼器”的专利技术[8],使临界转速N C和DN值进一步提高,用较简便的办法实现低成本提速,而且把行程范围扩大到4m以上,可实现长行程高速驱动。
据介绍,该公司在试验室已能使DN值达到200000。
4.3改进滚珠循环返向装置和滚珠的流畅性4.3.1优化滚珠反向器的结构采用三维型导珠管,优化回珠曲线,沿内螺纹的导程角方向插入滚珠螺母体内并与滚道相切(而不是相交),三维导珠管顺利导引滚珠流畅地出入循环返向装置,使布氏撞击耗损明显减小,摩擦力矩平滑,噪声低。