齿轮轴冷挤压模具设计说明书
齿轮轴的冷挤压成型工艺毕业设计

齿轮轴的冷挤压成型工艺摘要本文主要对齿轮轴的冷挤压加工进行了分析研究。
将齿轮轴由过去的切削加工工艺改变成冷挤压成形工艺,实现少废料加工,并改善齿轮轴制件质量,是加工方法的进步。
在过去齿轮的生产,主要采用滚、插、铣等传统工艺,但传统工艺加工的齿轮存在生产效率低和产品质量差等缺点。
为了克服这些缺点,近年出现了渐开线齿轮的冷挤压加工工艺。
采用该工艺加工渐开线齿轮,不但使生产效率大大提高,产品尺寸稳定,表面粗糙度低,材料利用率达70%~80%,而且冷挤压使工件表面产生压应力,可以增加产品的疲劳强度。
基于冷挤压加工的优点,我们在生产中引进了这一加工工艺。
为了在制造齿轮轴时减少工艺不合理性所带来的误差及难以加工等现象,本课题主要介绍了齿轮轴的冷挤压加工,通过加工中挤压成型中受力的分析,解决细长轴挤压出现的镦粗变形情况及冷挤压工件的热处理方法。
应此本课题的研究具有重要的现实意义。
关键词:齿轮轴;冷挤压;加工工艺,热处理AbstractMain gear shaft of cold extrusion processing were analyzed. Gear shaft from the previous machining process change into cold extrusion forming process, less waste processing, gear shaft and improve part quality, advances in processing methods.In the past the gear production, mainly by rolling, insert, milling and other traditional techniques, but the traditional processing of gear has low production efficiency and poor product quality. In order to overcome these shortcomings, in recent years, the involute gear cold extrusion process. The processing technology of involute gear, not only improves the production efficiency, product size stability, low surface roughness, material utilization rate up to70%~80%, and cold extrusion of the workpiece to produce compressive stress, can increase the product fatigue strength. Based on the cold extrusion processing advantages, we in the production of the introduction of the process.In order to reduce the process of manufacturing gear shaft is not reasonable and the difficulty of processing error caused by the phenomenon, this paper mainly introduces the gear 0axis cold extrusion processing, through the processing of extrusion force analysis, solve the elongated shaft extrusion of upsetting and extrusion workpiece heat treatment method. Should this topic research has the important practical significance.Keywords: Gear shaft Cold extrusion Processing Heat treatment目录第1章绪论 (1)1.1毕业设计选题的背景及意义 (1)1.2冷挤压在国内外研究概况及发展趋势 (1)1.2.1 冷挤压技术发展趋势 (2)1.3冷挤压工艺对模具的要求 (2)1.4冷挤压的特点 (3)1.4.1冷挤压特点 (3)1.4.2冷挤压的基本类型 (3)1.4.3冷挤压的优点 (4)1.4.4冷挤压缺点 (4)1.5冷挤压模具的构造及特点 (5)第2章齿轮轴成形工艺确定 (8)2.1齿轮轴的结构分析 (8)2.2冷挤压工艺的分析 (9)2.3冷挤压几种工艺组合形式 (9)2.4齿轮轴冷挤的理论基础 (10)2.5冷挤压工艺方案设计 (10)2.6齿轮轴冷挤压变形计算 (11)第3章齿轮轴的加工 (15)3.1基准的概念和分类 (15)3.2毛坯直径的计算及优化 (15)3.3各加工阶段的主要任务 (17)3.4加工顺序的安排 (18)3.5限制局部挤压镦粗办法 (18)3.6拟定加工工艺路线方案 (20)3.7冷挤压关键技术研究 (23)3.7.1 冷挤压前期出来 (23)3.7.2 冷挤压成形中的润滑 (23)第4章总结 (26)答谢词 (27)参考资料 (28)毕业设计(论文)报告纸┊ ┊ ┊ ┊ ┊ ┊ ┊ ┊ ┊ ┊ ┊ ┊ ┊ 装 ┊ ┊ ┊ ┊ ┊ 订 ┊ ┊ ┊ ┊ ┊ 线 ┊ ┊ ┊第1章 绪论1.1 毕业设计选题的背景及意义本课题是“齿轮挤压模具参数优化设计产业化推广”的一部分,过去采用切削加工方法得到,其生产工艺较复杂,成本较高,效率较低,质量也不易保证。
挤压成型模具设计手册

挤压成型模具设计手册一、模具设计基础模具设计是挤压成型工艺中的重要环节,它涉及到产品的形状、尺寸、精度和生产效率等方面。
在进行模具设计时,需要充分了解产品的用途和性能要求,同时考虑到生产条件和制造成本等因素。
二、材料选择与处理模具材料的选择和处理对于模具的寿命和性能至关重要。
常用的模具材料包括钢材、硬质合金、陶瓷等,具体选择应根据产品的要求和生产条件来确定。
材料处理包括热处理、表面处理等,可以提高材料的硬度、耐磨性和耐腐蚀性等性能。
三、模具结构设计模具结构设计是模具设计的核心,它决定了模具的功能和生产能力。
结构设计应充分考虑产品的形状、尺寸、精度和生产效率等因素,同时考虑到材料的流动和排溢等条件。
此外,结构设计还应考虑到维修和保养的方便性。
四、成型工艺优化挤压成型工艺是模具设计的重要环节之一,它涉及到材料的流动、温度和压力的控制等方面。
工艺优化可以提高生产效率、降低能耗和提高产品质量。
在进行工艺优化时,需要考虑多种因素,包括材料的性能、模具的结构和尺寸等。
五、温度控制系统温度是影响挤压成型工艺的重要因素之一,因此温度控制系统的设计也是模具设计的重要环节之一。
温度控制系统应能够精确控制模具的温度,并保持温度的稳定。
此外,温度控制系统的设计还应考虑到加热和冷却的速度和时间等因素。
六、模具强度与刚性模具的强度和刚性是影响模具寿命和产品质量的重要因素。
在进行模具设计时,应充分考虑模具的强度和刚性要求,并采取相应的措施来提高模具的强度和刚性。
例如,可以采用加强筋、增加厚度等方法来提高模具的强度和刚性。
七、润滑与保养润滑和保养是保持模具性能和延长模具寿命的重要措施。
在进行模具设计时,应充分考虑润滑和保养的要求,并采取相应的措施来实现润滑和保养的目的。
例如,可以采用润滑剂、密封圈等来润滑和保养模具。
挤压模具设计书说明书

挤压模具设计书说明书1. 引言本说明书旨在提供挤压模具设计的详细指导。
挤压模具是在挤压工艺中使用的一种关键工具,它对产品的质量和生产效率具有重要影响。
本说明书将涵盖挤压模具设计的基本概念、设计要点和步骤等内容,旨在帮助设计人员更好地理解和应用挤压模具设计相关知识。
2. 挤压模具设计概述挤压是一种通过挤压机将熔融的原料挤出成型的工艺。
挤压模具是挤压过程中起到塑料流动、形成和冷却等作用的工具。
挤压模具设计需要考虑多个因素,如材料选择、模具结构、模具加工工艺等。
3. 挤压模具设计步骤3.1. 产品分析在进行挤压模具设计之前,首先需要对待生产产品进行详细分析。
这包括产品的材料、形状、尺寸、表面要求等方面的分析。
通过产品分析,可以为模具设计提供基本的设计要求和指导。
3.2. 模具结构设计模具结构设计是挤压模具设计的核心部分。
在模具结构设计过程中,需要考虑到产品的形状和尺寸要求,确定模具的结构形式、模腔布置、模具开合方式等。
合理的模具结构设计能够有效提高产品的一致性和精度。
3.3. 材料选择挤压模具的材料选择对于模具寿命和产品质量具有重要影响。
常见的挤压模具材料包括合金钢、硬质合金等。
在选择材料时,需要综合考虑材料的硬度、强度、热导率等因素。
3.4. 模具加工工艺模具加工工艺是指模具从原料到成品的全过程。
挤压模具加工工艺包括切割、车削、铣削、磨削等。
在进行模具加工时,需要根据模具的具体要求选择合适的加工工艺,保证模具的加工精度和质量。
4. 挤压模具设计要点4.1. 模具结构要点•模具结构应满足产品的外观要求,确保产品的形状和尺寸精度。
•模具结构应具备良好的冷却系统,以提高模具的散热效果,避免产品变形和模具损坏。
•模具结构应具备合理的模腔设计,以确保塑料流动的均匀性和稳定性。
4.2. 模具材料要点•模具材料应具有高硬度和耐磨性,以提高模具的使用寿命。
•模具材料应具有良好的热导率,以实现有效的模具冷却效果。
4.3. 模具加工工艺要点•模具加工工艺应具有高加工精度和稳定性,以确保模具的质量和精度。
冷挤压工艺和模具设计说明书模板

冷挤压工艺及模具设计
5.1.4 冷挤压变形程度
在冷挤压过程中,变形程度是决定使用设备压力大小及 影响模具寿命的主要因素之一,若要提高生产率,就必须增 大每次挤压的变形程度,以减少挤压次数。但变形程度越大, 其变形抗力也越大,就会降低模具的寿命,甚至引起凸模折 断或凹模开裂。因此对各种挤压材料,都应选择合适的变形 程度。
冷挤压工艺及模具设计
表5-1 碳素钢及低合金钢的许用变形程度
材料牌号 10 15 35 45 15Cr
34CrMo
反挤压εF 75~80 70~73 50 40 42~50 40~45
表5-2 有色金属冷挤压的许用变形程度
金属材料 铝
截面收缩率εF(%)
正挤压
95~99
防锈铝
反挤压
90~99
紫铜、黄铜、硬铝
单位挤压应力 /MPa
250~300 1500~2000
300~500 2000~2500
500~700 2500~3000
700~800 3000~3500
800~900 3500~4000
表5-4 冷挤压专用液压机主要技术规格
公称挤 活塞直 压力/kN 径/mm
10000
360
20000
500
30000
冷挤压工艺及模具设计
(4) 提高零件的精度,降低表面粗糙度
由于金属表面在高压、高温(挤压过程中产生的热量) 下受到模具光滑表面的熨平,因此,制件表面很光,表面强 度也大为提高。冷挤压零件的精度可达1T8~1T9级,有色金
属冷挤压零件的表面粗糙度可达Ra=1.6~0.4μm。有的冷挤
压件无需切削加工。
冷挤压工艺及模具设计
对于有些材料,为了确保冷挤压过程中的润滑层不被过 大的单位接触压力所破坏,毛坯要经过表面化学处理。例如 碳钢的磷酸盐处理(磷化)、奥氏体不锈钢的草酸盐处理、 铝合金的氧化、磷化或氟硅化处理、黄铜的钝化处理等。经 化学处理后的毛坯表面,覆盖一层很薄的多孔状结晶膜,它 能随毛坯一起变形而不剥离脱落,经润滑处理后在孔内吸附 的润滑剂可以保持挤压过程中润滑的连续性和有效的润滑效 果。
冷挤压工艺和模具设计说明书模板

冷挤压工艺及模具设计
5.2 冷挤压模具设计
5.2.1 冷挤压模的特点
由于冷挤压时,单位挤压力较大,因此冷挤压模具的强 度、刚度及耐用度等方面其要求都比一般冲模高,它与一般 普通冲模相比,主要有以下特点: 1.模具的工作部分与上、下底板之间一般都设有足够 的支承面与足够厚度的淬硬垫板,以承受很大的压力,减少 上、下底板上的单位压力。
冷挤压时,一次挤压加工所容许的变形程度,称为许用 变形程度。不同材料有不同的许用变形程度。在工艺上,每 道冷挤压工序的变形程度应尽量小于许用值,使模具承受的 单位挤压力不超过模具材料许用应力(目前一般模具材料的 许用应力为2500~3000N/mm2),确定许用变形程度数值是 冷挤压工艺计算的一个重要依据,因为冷挤压许用变形程度 的大小决定了制件所需的挤压次数。若计算出的冷挤压变形 程度超过许用值、则必须用多次挤压完成,以延长模具寿命, 避免损坏模具。
冷挤压工艺及模具设计
3.复合挤如图5-3所示,挤压时,金属流动方向相对于 凸模运动方向,一部分相同,另一部分相反,适用于各种复 杂形状制件的挤压;改变凹模孔口或凸、凹模之间缝隙的轮 廓形状,就可以挤出形状和尺寸不同的各种空心件和实心件。
图5-1 正挤压图
5-2 反挤压图
5-3 复合挤
冷挤压工艺及模具设计
程度。
冷挤压工艺及模具设计
4.1.4.1 变形程度的表示方法 变形程度是表示挤压时金属塑性变形量大小的指标,其 最常用的表示方法有两种:截面收缩率和挤压面积比。 (1) 截面收缩率 式中
挤压模具设计说明书

由于B0=1.4㎜.本设计△=0.1
故Tk=1.4+0.1=1.5㎜
7.模孔工作带长度hg的确定
由于本型材制品的对称性较好,外形相对较小,一般可取2~6㎜,生产实践中对铝合金常用6~15㎜
本设计取hg=6mm
8.模芯的设计
一般伸出下模工作带3-5mm,本设计取4mm,模腔外形按空心型材的空心部分确定。
序号
(mm)
(mm)
单重wd
填充系数K
填充后长度Le
压余厚hy
(mm)
切压余后的有效长度Ld
挤压比
λ
制品长
L制
(m)
成品数
nx6
(m)
成品重
W制(kg)
成材率
W制/Wd
(%)
1
Φ95
Φ90
270
4.64
1.114
242
20
222
54.65
13.512×6m3.89 Nhomakorabea83.84%
2
Φ95
Φ90
320
5.50
因为本设计采用孔道式分流组合模
故:取H上=48H下=40模垫厚10㎜
5.组合模相关参数的确定:
1).分流孔的个数取4个,形状为扇形
2).扇形面积的确定:
因为分流孔面积与制品断面积的比值∑F分/F型=K,K即为分流比,,一般K对于空心型材时,取K=10~30。本设计取K=10
分流孔的面积∑F分=K. F型=10×241=2410 mm2
图7
依据经验a一般取2~5㎜,有的取8㎜.本设计取8㎜
图8
关于α的计算,由上图知
h=H/2+8=38.1/2+8=27.05㎜
毕业设计(论文)-冷挤压模具设计说明书

毕业设计(论文)-冷挤压模具设计说明书摘要阶梯形零件是多种复杂形状的组合,其成形工艺较难,在工艺设计和变形方案的制定上,有其独自的特点。
这类零件一般可采用板料多道拉深来成形。
但是对于本设计中的阶梯方铝罩零件来说,其内外都呈现阶梯状且形状不一致辞,并且由于中间过渡部分形状不规则,因此不可能用板材成形工艺成形,而只能采用挤压等其他方法成形。
对于复杂的阶梯形零件,一次挤压不容易达到预期成形效果。
因此,一般采用有预成形的多道次挤压工艺。
其中的关键是如何合理分配材料变形程度,控制材料流动,减少过度变形,从而得到合格的零件。
本文探讨了阶梯方铝罩挤压的可行性,通过对产品零件图的分析,制定了几种工艺方案并进行分析比较,在选择最优方案的同时也制定了工艺流程。
在此基础上详细地介绍了阶梯方铝罩挤压模具的设计过程。
采用冷挤压工艺加工后,提高了零件的精度和表面质量,改善了强度和韧性,减少了切削加工量,节约了原材料,提高了生产效率,也改善了零件的组织性能。
关键词:阶梯方铝罩,成形工艺,冷挤压,模具设计IABSTRACTMulti-step part is a combination, which is composed with various complicated shapes. Its forming craft is more difficult. So it has its own characteristic in the technological design and the distortion plan formulation. Generally, this kind of components can be formed with the technology of multi-drawing the sheet. However, the product in this paper is not so regular. Its shape has steps both in exterior andinterior and the shape is irregular. At the same time, the middle transition part is so complex that it is impossible to adopt the drawing technology to form. Therefore, we need to consider the cold extrusionand other way to get the shape. It is no easy to achieve the anticipated formed effect with only one extrusion, because the step-shape is so complex. It should use multi-extrusion craft with pre-form forging. So the key is how to distribute rationally the distortion degree, control material flow, reduce the excessive deformation and obtain the qualified components. The feasibility of extrusion forming of multi-step part was discussed in this article. With the analysis of several technological programs, the optimal plan was made and selected, the technological process was determined. Based on the pre-discussion, the extrusion die was design and the design process is presented detailedly. By using the cold extrusion craft process, the precision and the surface quality of the product is improved, the intensity and toughness is got better, the cutting process is reduced, the raw material is saved. Not only does it enhanced the production efficiency, but also improve the organization of component.Keywords: multi-step part,forming technique,cold extrusion,die designII目录第1章冷挤压技术的介绍 .............................................11.1冷挤压工艺的实质 .................................................11.2冷挤压工艺的优点 .................................................11.3冷挤压工艺的缺点 .................................................21.4冷挤压工艺的应用范围 .............................................31.5冷挤压工艺的的发展方向 ...........................................3 第2章工艺分析及制定 ...............................................42.1产品零件的分析 ...................................................42.2工艺方案的分析 ...................................................5 第3章毛坯制备及处理 ..............................................113.1冷挤压件毛坯的制备 ..............................................113.2冷挤压件材料的软化热处理 ........................................133.3冷挤压件的表面处理与润滑 ........................................14 第4章冷挤压力 .....................................................164.1影响冷挤压压力的主要因素 ........................................164.2变形程度 ........................................................164.3冷挤压力的计算 ..................................................17 第5章冷挤压设备的选择 ............................................185.1冷挤压设备的基本要求 ............................................185.2冷挤压设备的选择 ................................................18 第6章冷挤压模具设计 ..............................................206.1冷挤压模具特点 ..................................................206.2冷挤压模架设计 ..................................................206.3凸、凹模设计 ....................................................216.3.1反挤压凸模的设计 (21)6.3.2反挤压凹模的设计 (23)6.3.3反挤压凸、凹模制造公差 (25)第7章模具结构部件设计 (26)7.1上模具部分结构设计 ..............................................267.2卸件装置设计 ....................................................27III7.3下模具部分结构设计 ..............................................297.4模具结构和工作原理 ..............................................307.5成形模具三维图 ................................ 错误~未定义书签。
挤压模具设计说明书资料

二.总设计过程概论1.挤压工艺流程:铸锭加热→挤压→切压余→淬火→冷却→切头尾→切定尺→时效→表面处理→包装→出厂2.挤压工艺条件1)铸锭的加热温度6063铝的最高允许加热温度为550℃,下限温度为320℃,为了保证制品的组织,性能,挤压时锭坯的加热温度不宜过高,应尽量降低挤压温度2)挤压筒的加热温度模具的成分多为合金钢,由于导热性差,为避免产生热应力,挤压前挤压筒要预热,为保证挤压制品的质量,并且具有良好的挤压效应,挤压筒温度可取400℃~450℃。
3)挤压温度热挤压时,加热温度一般是合金熔点绝对温度的0.75~0.95倍,本设计挤压温度为450℃~500℃,挤压过程中温度控制在450℃左右4)挤压速度考虑金属与合金的可挤压性,制品质量要求及设备的能力限制,本设计的挤压速度取0.7~0.8m/s5)工模具的润滑因本设计采用热挤压,故不采用润滑6)模具模具应具有足够的耐高温疲劳强度和硬度,较高的耐回火性及耐热性,足够的韧性,低的膨胀系数和良好的导热性,可加工性,及经济性,本设计采用4Cr5MoSiV1作为模具的材料,热处理的硬度为HRC45~507)切压余根据所选的设备:500T,切压余厚为20mm;800T,切压余厚为25mm8)淬火本工艺过程中,制品挤出后可通过设置风扇对制品进行吹风来达到风淬的目的9)冷却直接露置在空气中冷却,达到自然时效的目的10)切头尾本工艺过程统一去头尾各300mm三.实心型材模设计1.所要设计的实心型材制品本制品的形状和尺寸如下图1牌号XC111(L 型)制品的截面积F 制=116.42mm模孔外接圆直径D 外=46.28mm 现有设备(如下表):设备吨位500T800T 1630T 挤压筒直径0D Φ95 Φ125 Φ187 挤压截面积0F 70851226627451锭坯尺寸ddD L Φ90x270/320Φ120X400/450Φ178X540/600/660冷床长26m 32m 44m 填充系数 1.114 1.085 1.104 压余厚20 25 30 最大挤压比97.4 8273.6加工范围最大外接圆直径Φ65 Φ95 Φ147挤一根最小制品断面积F 制min72 150 3722.选坯和选设备根据加工范围要求(F 制≥F 制min,及D 外≤D 外max )只有500T 的可用,按成才率最高的原则,进一步优化,计算列表序号0D d D (mm ) dL (mm ) 单重wd 填充系数K 填充后长度Le 压余厚hy (mm) 切压余后的有效长度Ld挤压比λ制品长L 制(m) 成品数nx6 (m) 成品重W 制(kg)成材率W 制/Wd (%)1 Φ95 Φ90 270 4.64 1.114 242 20 222 54.65 13.51 2×6m 3.8983.84%2 Φ95 Φ90 320 5.50 1.114 287 20 267 54.65 16.25 2×6m 3.8970.73%最后选择成才率最高的83.84%对应的方案 1 即:500T 的挤压机设备锭坯尺寸为:dd D L =Φ90X270mm λ=54.653.挤压力的计算根据经验系数公式:211.7750.8bD PDd, D 为挤压筒内径,d 为制品等面积直径,b为某温度下坯料的抗拉强度,450℃下6063的b≈12MPa带入数据求得:29511.7750.89512253.812.2PTF <额定吨位500T ,设备选择符合要求,即理论技术可行4.实心型材模具体结构设计模组的结构如下图图21.模子2.模垫3.前环4.后环5.保护垫板6.前机架7.模座8.模套9.剪刀 10.挤压筒模组的结构:对于不同吨位的挤压机,下图中的主要结构尺寸都是配套设置的,可以从有关资料中查得。
齿轮轴冷挤压模具设计说明书

目录前言 (1)1 冷挤压基础知识 (2)1.1 冷挤压的实质及方法分类 (2)1.2 冷挤压工艺的优缺点及应用范围 (2)1.2.1 冷挤压的特点 (2)1.2.2 冷挤压的优点 (3)1.2.3 冷挤压的缺点 (4)1.2.4 冷挤压工艺的应用范围 (4)1.3 冷挤压技术现状及发展方向 (5)1.3.1 冷挤压技术的现状 (5)1.3.2 冷挤压技术发展方向 (6)1.4 冷挤压模具设计基础知识 (6)1.4.1 冷挤压模具的构造及特点 (6)1.4.2 模具设计基本要求 (7)1.4.3 模具设计的一般程序 (7)1.5 本文研究的主要内容 (8)2 冷挤压件图的设计及毛坯准备 (10)2.1 冷挤压件图的设计 (10)2.2 毛坯的制备及处理 (12)2.2.1 坯料形状和尺寸确定 (12)2.2.2 坯料的软化处理 (12)2.2.3 坯料表面处理及润滑 (13)2.3 冷挤压工艺方案设计 (14)2.4 冷挤压模具材料 (15)3 挤压力的估算及挤压设备的选择 (16)3.1 影响单位挤压力的主要因素 (16)3.2 冷挤压力的估算及压力机选择 (18)4 模具结构设计 (19)4.1 凹模设计 (19)4.1.1 凹模的结构形状设计 (20)4.1.2 凹模各部分尺寸的设计计算 (20)4.2 上模部分结构设计 (23)4.3 导向装置 (24)4.4 卸料装置 (25)4.5 凹模压板紧固螺钉计算 (26)4.6 模具总体结构 (26)5凸、凹模失效形式及分析 (28)5.1凸模失效形式及分析 (28)5.1.1 凸模失效原因 (28)5.1.2 凸模失效形式 (28)5.2凹模失效形式及分析 (31)5.3齿轮部分冷挤压的相关问题 (32)6 技术经济分析 (34)7 结论 (36)致谢 (37)参考文献 (38)附录A (39)附录B译文 (40)附录C外文资料 (51)前言随着家用电器产量的迅速猛增,对锻压行业的工艺技术水平提出了更高的要求,突出的问题就是以少无切屑毛坯为核心的合理选择变形方式,提高材料利用率和制件尺寸精度、减少机械加工工时、降低能耗、提高生产率。
齿轮轴——课程设计说明书

机械制造工艺学课程设计设计说明书设计“齿轮轴”零件的机械加工工艺规程起止日期: 2011 年 12 月 19 日至 2011 年 12 月 25 日学生姓名班级学号成绩指导教师(签字)机械工程学院(部)2011年12月19日《机械制造工艺学》课程设计任务书2011—2012学年第一学期机械工程学院机械工程及其自动化专业班课程名称:机械制造工艺学课程设计设计题目:设计“齿轮轴”零件的机械加工工艺规程完成期限:自2011年 12 月 19 日至2011年 12月 25日共1周一、课程概述课程名称:机械制造工艺学课程设计总学时数:一周课程类别: 必修专业课授课专业:机械设计制造与自动化专业先修课程:机械制图、机械设计、互换性与技术测量、机械制造工艺学等二、本课程的目的和任务本课程设计是学生在学完机械制造工艺学课程、进行了生产实习之后的一个综合性和实践性很强的教学环节,学生通过课程设计,能综合运用所学基本理论以及在生产实习中学到的实践知识进行工艺及结构设计的基本训练,掌握机械制造过程中的加工方法、加工装备等基本知识,提高学生分析和解决实际工程问题的能力,为后续课程的学习及今后从事科学研究、工程技术工作打下较坚实的基础。
三、课程设计的基本内容(一)对零件(中等复杂程度)进行工艺分析,画零件图。
(二)选择毛坯的制造方式。
(三)制订零件的机械加工工艺规程1.选择加工方案,制订工艺路线;2.选择定位基准;3.选择各工序所用的机床设备和工艺装备(刀具、夹具、量具等);4.确定加工余量及工序间尺寸和公差;5.确定切削用量(四)填写工艺文件1.填写机械加工工艺卡片;2.填写机械加工工序卡片。
(五)编写设计说明书。
四、课程设计的基本要求(一)通过本课程设计,应使学生在以下几方面得到锻炼:1.能运用机械制造工艺学课程中的基本理论和生产实习中学到的实践知识,正确地解决一个零件在加工中的定位、夹紧以及工艺路线安排、工艺尺寸确定等问题,保证零件的加工质量。
齿轮轴设计说明书
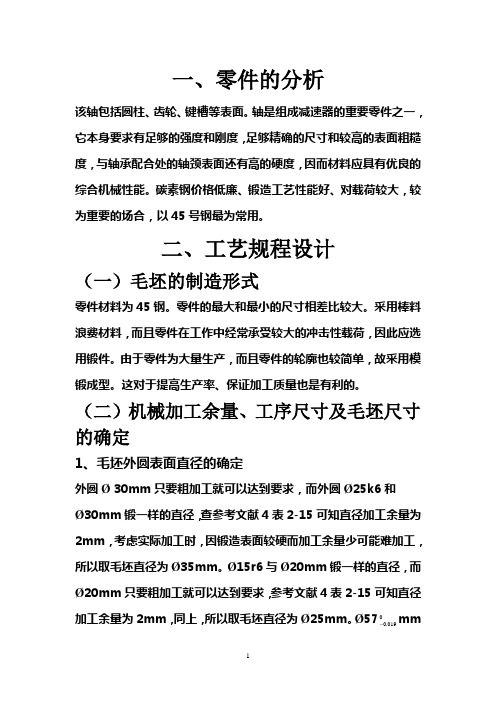
一、零件的分析该轴包括圆柱、齿轮、键槽等表面。
轴是组成减速器的重要零件之一,它本身要求有足够的强度和刚度,足够精确的尺寸和较高的表面粗糙度,与轴承配合处的轴颈表面还有高的硬度,因而材料应具有优良的综合机械性能。
碳素钢价格低廉、锻造工艺性能好、对载荷较大,较为重要的场合,以45号钢最为常用。
二、工艺规程设计(一)毛坯的制造形式零件材料为45钢。
零件的最大和最小的尺寸相差比较大。
采用棒料浪费材料,而且零件在工作中经常承受较大的冲击性载荷,因此应选用锻件。
由于零件为大量生产,而且零件的轮廓也较简单,故采用模锻成型。
这对于提高生产率、保证加工质量也是有利的。
(二)机械加工余量、工序尺寸及毛坯尺寸的确定1、毛坯外圆表面直径的确定外圆Ø 30mm只要粗加工就可以达到要求,而外圆Ø25k6和Ø30mm 锻一样的直径,查参考文献4表2-15可知直径加工余量为2mm,考虑实际加工时,因锻造表面较硬而加工余量少可能难加工,所以取毛坯直径为Ø35mm。
Ø15r6与Ø20mm锻一样的直径,而Ø20mm只要粗加工就可以达到要求,参考文献4表2-15可知直径加工余量为2mm,mm要经过粗加工和精加工,同上,所以取毛坯直径为Ø25mm。
Ø570019.0参考文献4表2-15可知直径加工余量为2mm+1.5mm=3.5mm,考虑实际加工时,因锻造表面较硬而加工余量少可能难加工,所以取毛坯直径为Ø65mm。
长度方向的余量查参考文献2,其余量值规定2.0-2.5mm,取2.0mm。
2、加工余量产品毛坯图:(三)选择定位基准1)精基准的选择由零件的工艺分析可以知道,此零件的设计基准是Ø25k6mm和Ø15r6mm的轴线,根据基准重合选择,应选择设计基准为精基准,即以Ø25k6mm和Ø15r6mm的轴线为精基准,由于多数工序的定位基准都是中心孔,符合基准统一原则,且能保证工件定位准确,装夹方便,夹具结构简单。
- 1、下载文档前请自行甄别文档内容的完整性,平台不提供额外的编辑、内容补充、找答案等附加服务。
- 2、"仅部分预览"的文档,不可在线预览部分如存在完整性等问题,可反馈申请退款(可完整预览的文档不适用该条件!)。
- 3、如文档侵犯您的权益,请联系客服反馈,我们会尽快为您处理(人工客服工作时间:9:00-18:30)。
目录前言 (1)1冷挤压基础知识 (2)1.1冷挤压的实质及方法分类 (2)1.2冷挤压工艺的优缺点及应用范围 (2)1.2.1冷挤压的特点 (2)122冷挤压的优点 (3)1.2.3冷挤压的缺点 (4)1.2.4冷挤压工艺的应用范围 (4)1.3冷挤压技术现状及发展方向 (5)1.3.1冷挤压技术的现状 (5)1.3.2冷挤压技术发展方向 (6)1.4冷挤压模具设计基础知识 (6)1.4.1冷挤压模具的构造及特点 (6)1.4.2模具设计基本要求 (7)1.4.3 模具设计的一般程序 (7)1.5 本文研究的主要内容 (8)2冷挤压件图的设计及毛坯准备 (10)2.1冷挤压件图的设计 (10)2.2毛坯的制备及处理 (12)2.2.1坯料形状和尺寸确定 (12)222坯料的软化处理 (12)223 坯料表面处理及润滑 (13)2.3冷挤压工艺方案设计 (14)2.4冷挤压模具材料 (15)3挤压力的估算及挤压设备的选择 (16)3.1影响单位挤压力的主要因素 (16)3.2冷挤压力的估算及压力机选择 (18)4模具结构设计 (19)4.1凹模设计 (19)4.1.1凹模的结构形状设计 (20)4.1.2凹模各部分尺寸的设计计算 (20)4.2上模部分结构设计 (23)4.3导向装置 (24)4.4卸料装置 (25)4.5凹模压板紧固螺钉计算 (26)4.6模具总体结构 (26)5凸、凹模失效形式及分析 (28)5.1凸模失效形式及分析 (28)5.1.1凸模失效原因 (28)5.1.2 凸模失效形式 (28)5.2凹模失效形式及分析 (31)5.3 齿轮部分冷挤压的相关问题 (32)6 技术经济分析 (34)7 结论 (36)致谢 (37)参考文献 (38)附录A (39)附录B 译文 (40)附录C 外文资料 (51)、八、,刖言随着家用电器产量的迅速猛增,对锻压行业的工艺技术水平提出了更高的要求,突出的问题就是以少无切屑毛坯为核心的合理选择变形方式,提高材料利用率和制件尺寸精度、减少机械加工工时、降低能耗、提高生产率。
为此,必需逐步研制和推广应用一项先进的金属塑性成形技术一一冷挤压工艺。
对于汽车齿轮轴零件,过去一直采用切削加工方法得到,其生产工艺较为复杂,成本较高,效率较低,质量也不易保证。
当采用冷挤压成形工艺后,该件制造工艺简单,生产效率能提高20倍以上,并且实现了少废料加工,节约了原材料,制件质量也得到了明显改进。
1冷挤压基础知识1.1冷挤压的实质及方法分类冷挤压的加工方法是利用金属材料塑性变形的原理,在室温的条件下,将冷态的金属毛坯放入装在压力机上的模具型腔内,在强大的压力和一定的温度作用下,迫使金属毛坯产生塑性流动,通过凸模与凹模的间隙或凹模出口,挤出空心或断面比毛坯断面要小的实心零件,可以获得所需一定形状及尺寸,还具有较高力学性能挤压件的工艺技术⑴。
冷挤压是无切屑、少切屑零件加工工艺之一,所以是近代金属塑性加工中一种先进的加工方法。
冷挤压成型加工是靠模具来控制金属流动,靠软化金属体积的大量转移来成形所需的零件。
由此可知,冷挤压工艺的成功与失败与模具结构设计,模具材料以及金属毛坯的软化处理等密切相关。
冷挤压加工的成形速度范围很广,所用的设备可以在专用的冷挤压压力机上进行,也可在一般的机械压力机(如冲床)或在液压机、摩擦压力机以及高速锤上进行。
冷挤压工艺可按金属流动方向,金属流动速度以及变形温度等进行分类⑴:1)按金属流动方向分类与凸模运动方向之间的相互关系,冷挤压方法分为正挤压、反挤压、复合挤压、减径挤压、径向挤压、斜向挤压、镦挤法。
2)按金属坯料充填模具型腔的流动速度有一般速度、低速及高速挤压之分。
3)按变形温度状态分,有冷挤压(室温挤压)、温挤压(半热挤压)、热挤压及等温挤压。
1.2冷挤压工艺的优缺点及应用范围1.2.1冷挤压的特点冷挤压技术是一种高精、高效、优质低耗的先进生产工艺技术,比较多的应用于中小型锻件规模化生产中。
与常规模锻工艺技术相比,可以节材30%~50%,节能40%~80%,而且能够提高锻件质量和改善作业环境。
二战后,冷挤压技术在国外工业发达国家的汽车、摩托车、家用电器等行业得到了广泛的发展应用,而新型挤压材料、模具新钢种和大吨位压力机的出现,更拓展了其发展空间。
日本80年代自称,其轿车生产中以锻造工艺方法生产的零件,有30%~40%是采用冷锻工艺生产的,近年来生产的新型轿车则每车平均使用42kg的冷锻件。
美国等国家的轿车生产中,每车平均使用40kg的冷锻件。
随着科技的进步和汽车、摩托车、家用电器等行业对产品技术要求的不断提高,冷锻生产工艺技术已逐渐成为中小锻件精化生产的发展方向⑵。
1.2.2冷挤压的优点近年来,在机械制造工艺方面广泛采用冷挤压先进技术,取得了显著的成效。
目前,随着计算机、快速造型及数字化等现代科学的迅速发展及应用,使冷挤压工艺进一步得到开拓及采用。
与其他制造方法相比,冷挤压工艺已成为金属塑性变形中最先进工艺之一,在技术上和经济上它都有很多的显著优点。
1)显著降低原材料的消耗冷挤压是一种金属塑性成形加工方法。
它在不破坏金属的前提下使金属体积作出塑性转移,达到少无切屑而使金属成形,制得所需的形状及尺寸零件。
这样就避免了在切削加工时而形成的大量金属废屑,大大节约了各种有色金属及钢铁原材料。
2)提高劳动生产率冷挤压零件是在压力机上进行的,操作方便,容易掌握,生产率很高。
3)可形成复杂形状的零件在压力机的往复直线动作下完成复杂的加工工序,并可以制成形状复杂的零件。
4)提高零件的力学性能在冷挤压过程中,金属材料处于三向不等的压应力作用下。
挤压变形后,金属材料的晶粒组织更加致密,金属流线不被切断,成为沿着挤压件轮廓连续分布的金属流线。
同时,挤压利用了金属材料冷变形的加工硬化特性,使冷挤压件的强度大为提高,从而提供了用低强度钢代替高强度钢的可能性。
5)可获得较高尺寸精度及较小表面粗糙度值的零件经冷挤压成形零件的表面质量是十分良好的。
在冷挤压过程中,金属表面在高压下受到模具光滑表面的熨平,因此零件的表面粗糙度值很小,表面强度也大为提高。
冷挤压零件的精度可达IT7~IT8级,表面粗糙度可达Ra0.2~1.d3]。
因此,用冷挤压加工的零件一般很少再切削加工,只需在要求特别高之处进行精磨。
冷挤压工艺可以获得理想的制件表面粗糙度与尺寸精度,有些零件经挤压后可以不再进行切削加工,从而为采用冷挤压加工代替某些零件的锻造、铸造与切削加工开辟了一条广阔的道路。
6)减少工序,缩短生产周期冷挤压工艺是在闭式模具型腔中进行金属塑性变形,所得的挤压件是没有飞边的,故不再需要切边(或冲孔)后续工序,从而缩短了生产周期。
7)减少设备投资与模锻工艺相比,因冷挤压不产生飞边,故可以省去切边模及切边压力机,明显地减少了设备投资。
另外,冷挤压生产加工,可在专用的冷挤压压力机上,也可以在通用液压机上进行,还可以在非专门为冷挤压而设计的普通压力机上进行,如通用冲床或摩擦压力机。
8)降低零件的生产成本由于冷挤压可以大大节约原材料和加工工时,因此必然可降低零件的制造成本。
123冷挤压的缺点在长期的生产实践中,与其他制造工艺相比,冷挤压虽然表现出很多优点,但往往还存在一定的问题⑴。
1)变形抗力高冷挤压时,被挤压材料的变形抗力较高,其中最有实用意义的是钢的冷挤压,其变形抗力高达2000MPa以上。
这样的超高压力,对模具材质、结构以及加工制造等提出了更高的要求。
2)模具寿命短由于冷挤压模具承受着很大的单位挤压力作用,最高可打3000MPa,模具易磨损、易破坏;虽然在模具材料和模具结构等方面采用了很多有效的措施,但与冲压模具相比,其使用寿命还是不高的。
3)对毛坯的要求较高冷挤压加工时对毛坯的要求比其他金属塑性成形加工工艺都高,否则,会使模具受到损坏。
对于冷挤压毛坯,除了要求毛坯具有准确的几何形状和较高的尺寸精度外,还要求在冷挤压变形之前对毛坯进行一定的软化退火处理及表面润滑处理。
4)对冷挤压设备要求较高当实施冷挤压工艺过程时,除了要求冷挤压设备应有较大的强度以外,还要求有较好的刚度。
此外,还要求设备具有良好的精度并具有可靠的保险装置。
1.2.4冷挤压工艺的应用范围通过上述分析可见,冷挤压加工方法是一种“优质、高产、低消耗、低成本”的先进工艺,在技术上和经济上都有很高的应用价值。
目前,冷挤压技术已经在我国汽车、摩托车、仪表、电信器材、轻工、建筑、宇航、船舶、军工及五金等工业部门中获得了广泛的应用,已成为金属塑性成形技术中不可缺少的重要加工手段之一。
冷挤压作为一种少无切屑的新工艺,已经成为世界先进制造技术中及具特色的一个门类。
冷挤压加工的缺点和优点相比是次要的,是相对于当前技术条件而言的,随着科学技术的迅速发展,模具钢新材料的研究及开发,模具结构设计的合理化,缺点问题会被解决,优越性将会得到充分发挥。
在21世纪,这种先进的金属塑性成形加工工艺将会起到更大的作用,在各个行业中得到越来越广泛的应用。
1.3冷挤压技术现状及发展方向1.3.1冷挤压技术的现状冷挤压加工的发展在初期是极其缓慢的,长期以来一直局限于铅和锡等几种较软的金属材料。
18世纪末,法国人首先成功地冷挤压出铅棒。
直到19世纪末20世纪初,才开始应用于锌、锡、纯铜、无氧铜及黄铜等,如冷挤压生产锡制牙膏管。
英国于1886年开始运用于冷挤压加工,某一工厂先从加工软金属开始,后来逐步实现冷挤压比较坚硬的有色金属,如锌、铝、铜及其合金。
1903年美国运用冷挤压制成薄壁黄铜管。
随后,又采用预制成杯形坯料,然后再用正挤压的方法,成功地制成深孔杯形件。
第一次世界大战期间,美国军火商采用这种挤压方法大批量生产黄铜弹壳。
第一次世界大战后,德国用冷挤压方法可成批生产纯铝和纯锌电容器外壳等各种有色金属器件。
至于钢的冷挤压,美国曾企图通过冷挤压法生产刚质弹壳,经过较长时间的研制,但是最终还是未获成功。
这是因为在黑色金属冷挤压时需要很大的压力,而在当时的工业条件下还不能找到能承受较大压力下的模具材料,也没有找到良好的润滑剂以及大吨位的冷挤压压力机。
直到20世纪40年代,冷挤压钢零件的新工艺才开始在德国首先得到应用。
钢的冷挤压正式用于国民经济中的各行各业始于1947年。
美国于1949年发表了关于各种钢材冷挤压前后力学性能的实验结果。
德国于1950年发表了关于黑色金属的冷挤压试验报告,得出了一些基本工艺的技术数据,并在1953年公布了关于钢的冷挤压压力和挤压功的实验结果。
日本于1957年引进专用冷挤压压力机以后,在钟表等精密仪器工业中开始应用冷挤压加工。
由于这种技术的经济效益极其显著,不久,便在大批量生产的汽车、电器及纺织等工业部门中得到了广泛的应用。