钢结构工艺(通用部分)
钢结构主要施工工艺流程

钢结构主要施工工艺流程如下:施工放线→基础混凝土内预埋螺栓→(钢结构加工制作)门式刚架吊装→吊车梁安装→钢梁安装→屋架、屋面板及屋檐板安装→墙面板安装→钢结构涂装。
一、施工放线(1)按照设计要求,根据图纸要求,配合土建单位将标高、轴线核实核准。
(2)施工前用经纬仪复核轴线,并用水准仪确定标高,并用墨线在不易损坏的固定物上作好记号,注明标高,并做好记录。
(3)在确定轴线和标高之后,即放好大样之后,再放小样,也就是确定每个钢柱在基础混凝土上的连接面边线及纵横十字轴线,即门式刚架的柱脚位置。
(4)在定位刚架时,要尽量避免刚架柱脚与螺栓的碰撞,以避免刚架柱底面的变形,从面减少与基础混凝土的接触面,以及螺栓的弯曲变形,造成螺栓纠直之后给螺栓带来的强度损耗。
二、基础混凝土内预埋螺栓(1)在基础混凝土浇捣之前,再仔细核对螺栓的大小、长度、标高及位置,并固定好预埋螺栓。
(2)在基础混凝土浇捣之前,黄油及塑料薄膜包住预埋螺栓的丝口部分,以避免混凝土浇捣时对螺栓丝口的污染。
/(3)在浇捣混凝土之时,派有经验的专人值班,做好混凝土浇捣时对预埋螺栓定位的影响。
以避免预埋累栓的位移及标高的改变。
(4)基础混凝土浇捣之后,及时清理预埋螺栓杆及丝口上的残留混凝土。
三、钢结构加工制作工艺过程:1.下料图单此工序为材料检验部分,其内容包括对工程所选用的型号、规格的确认以及材料的质量检查。
2.放样、号料①放样划线时,应清楚标明装配标记、螺孔标注、加强板的位置方向、倾斜标记及中心线、基准线和检验线,必要时制作样板。
②注意预留制作,安装时的焊接收缩余量;切割、刨边和铣加工余量;安装预留尺寸要求。
③划线前,材料的弯曲和变形应予以矫正。
3.下料:钢板下料采用数控多头切割机下料,但下料前应将切割表面的铁锈、污物清除干净,以保持切割件的干净和平整,切割后应清除溶渣和飞溅物,操作人员熟练掌握机械设备使用方法和操作规程调整设备最佳参数的最佳值。
4.组立、成型钢材在组立前应矫正其变形,并达到符合控制偏差范围内,接触毛面应无毛刺、污物和杂物,以保证构件的组装紧密结合,符合质量标准。
钢结构施工方案 (通用)

钢结构施工方案一、设计依据1、建设单位提供的并经过确认的功能布置图和平面资料图。
2、已有建筑结构图纸3、设计遵循的规范,规程及规定:3。
1《建筑结构荷载规范》(GB50009-2001)(2006年版)3。
2《建筑抗震设计规范》(GB50011-2010)3.3《钢结构设计规范》(GB50017—2003)3.4《冷弯薄壁型钢结构技术规范》(GB50018-2002)3。
5《门式钢架轻型房屋钢结构技术规程》(CECS102:2002)3。
6《钢结构工程施工质量验收规范》(GB50205—2001)3。
7《建筑钢结构焊接技术规程》(JGJ81—2002)3.8《涂装前钢材表面锈蚀等级和除锈等级》(GB/T8923)3。
9《钢结构高强螺栓连接的设计,施工及验收规程》(JGJ82-2011)3.10《钢结构防火涂料应用技术规程》(CECS24)3。
11《门式钢架轻型房屋钢结构(有吊车)》(04SG518-3)二、一般说明1、全部尺寸(除注明者外)均以毫米(mm)为单位,标高以米(m)为单位.2、未经技术鉴定或设计许可,不得改变结构的用途和使用环境。
3、本工程室内地面标高±0。
000,根据建筑总图确定(或由业主与施工单位现场定)。
4、本工程的建筑结构安全等级为二级。
耐火等级为二级。
5、本工程主体结构设计使用年限为50年.6、本工程抗震设防类别为丙类,抗震设防烈度为8度;设计基本加速度为0.2g;所在场地设计地震分组为第一组,场地类别为III类.7、本工程结构设计采用的计算程序:PKPM—STS,jccad,版本:2010年10月。
三、设计荷载(标准值)1、屋面恒荷载:0.30KN/㎡屋面活荷载:0。
50KN/㎡2、基本风压值为:0.45KN/㎡地面粗糙度为B类,钢架、檩条、墙梁及围护结构体型系数按(CECS102:2002)3、基本雪压值为:0。
40KN/㎡4、吊车荷载:Q=20T/5T,S=14.1米,A4—A5工作制桥式吊车(2台/跨)Q=10T,S=16。
钢结构工程施工工艺

钢结构工程施工工艺(一)、钢柱加工工艺1)空腹钢柱待钢焊接、矫正后, 定尺切头, 再焊接柱底板、顶板、筋板、墙皮支座。
2)格构式组合柱制作先定尺加工上下肢焊接钢, 下肢钢二次切头时要加焊接收缩余量、每米加1mm。
3)在刚性平台上搭设组装支架, 间隔约3m一个, 支架用水平仪测平, 调整好上下肢高差在组装支架上划出钢柱中线, 上、下肢边线, 再按图纸要求组装钢柱全部零件。
4)钢柱全部零件组装完毕, 要重点检查钢柱平整度、旁弯、肩梁和柱底板与柱轴线的垂直度、眼孔偏差。
柱下肢焊接时要采用对称焊接, 防止旁弯变形, 柱底板焊接要控制产生角变形。
5)柱间支撑为门式刚架。
三角形斜支撑桁架部分, 无法运输, 故此部分桁架弦杆、腹杆在工厂(或现场加工场地)加工后现场拼装成整体。
6)吊车梁加工工艺:吊车梁加工工序与焊接钢基本相同, 但在腹板下料时要注意起拱度的要求。
7)吊车梁腹板与翼板接头的焊接坡口, 采用刨边机加工。
8)装配定位前, 腹板坡口面及两侧50mm范围内的氧化物及铁锈用高速砂轮机除净, 翼板宽度方向的中心部位100mm范围内的氧化物铁锈进行彻底清理。
9)在专用台架上卧置组装成工字梁。
工字梁一律点焊定位, 点焊长度为100-200mm, 间距不大于400mm, 厚度均等于坡口深度二分之一。
10)根据吊车梁材质和结构要求, 气体保护焊打底选用镀铜焊丝, 焊丝的质量必须符合国际标准要求, 为防止因结构焊接应力大而引起焊接裂纹, 焊丝的碳含量应控制在0.08%以下。
2. 构件防腐(1)抛丸除锈:钢材(构件)的表面处理应按设计规定的施工方法施工, 并达到规定的除锈等级标准要求。
所有构件均采用抛丸除锈, 将表面油污、氧化层和铁锈以其它杂物清除干净, 达到标准要求。
构件表面的毛刺、电焊药皮、飞溅物、灰尘在除锈前应清除干净。
喷丸前应用砂轮打磨气割表面、火焰矫正部位的硬化层, 以使喷砂在这些部位能形成合适的表面粗糙度。
钢结构工程施工工艺

钢结构工程施工工艺一、预埋地脚螺栓(一)施工流程(二)地脚螺栓加工1、本工程地脚螺栓螺纹段全部采用车床加工,要求螺纹螺牙均匀、螺纹长度满足设计要求及规范要求。
2、地脚螺栓托板和加筋板采用人工电弧焊焊接,要求焊接焊缝均匀、满焊、不留气孔、无焊瘤,焊缝尺寸必须符合设计、符合规范要求。
3、螺栓加工完毕、进施工现场前必须由材料员和检验员进行100%自检,检查螺栓规格、尺寸、数量、螺纹段长度、总长度是否符合设计要求。
4、验收合格螺栓螺纹段及时涂防绣油,防止生绣;按规格堆放整齐,堆放过程中做好相应的保护措施,防止螺纹段磕碰造成不应有的损伤;并做好标识,使之醒目。
5、出厂前出具自检报告和出厂合格证。
(三)技术准备1、收集、准备相应的技术资料,如施工图纸,预埋规范等。
2、组织项目人员认真学习有关的规范、规程、规定,在施工的过程中做到有据可依。
3、施工前认真审阅施工图纸,在图纸会审的基础上争取将施工中可能碰到的问题在施工前解决,提前确定施工中存在的难点及需要重点注意的地方,做到目标明确,重点突出。
4、具体需要熟悉的有:螺栓规格、数量,轴距尺寸,每轴之间垮距尺寸,预埋种类等做到心中有数。
工作难点其注意的地方有:如何保证轴与轴之间平行,如何保证每轴距在规范要求内。
5、实行三级交底制:技术部对项目部有关此工程项目经理、技术人员进行方案交底;项目经理对工程部分包队长,班组长进行交底;分包队长对班组长,员工进行交底。
(四)钢制模板制作根据施工图纸对地脚螺栓做相应的钢制模板,其注意事项:1、钢制模板其目的是控制预埋尺寸精度,提高预埋速度。
2、模板采用4.5-6mm之间的钢板制作,板必须校平面度<1mm,若板厚度不够,则四周用Ø12mm钢筋焊接,加强模板钢性,图中虚线所示。
3、如上图所示模板孔尺寸ØD+2,D为螺栓圆钢直径,A、B中心尺寸要求<1mm,中心线用垂直钢尺靠住,水笔一次性划出中心线,中心线必须醒目。
钢结构各种焊接工艺大全(带图例)
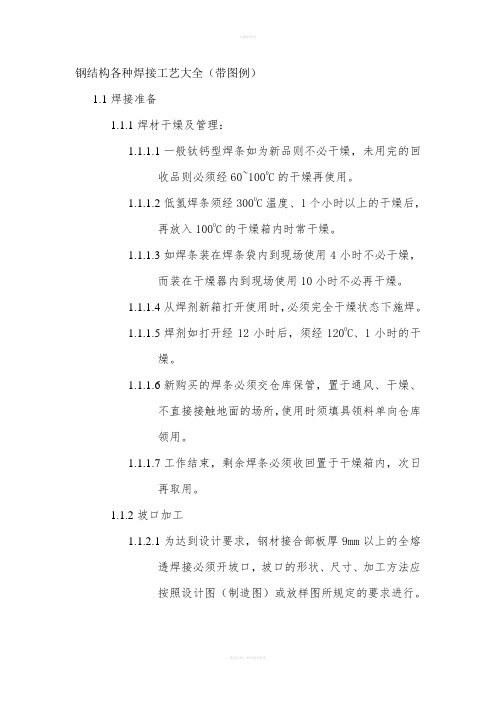
钢结构各种焊接工艺大全(带图例)1.1焊接准备1.1.1焊材干燥及管理:1.1.1.1一般钛钙型焊条如为新品则不必干燥,未用完的回收品则必须经60~1000C的干燥再使用。
1.1.1.2低氢焊条须经3000C温度、1个小时以上的干燥后,再放入1000C的干燥箱内时常干燥。
1.1.1.3如焊条装在焊条袋内到现场使用4小时不必干燥,而装在干燥器内到现场使用10小时不必再干燥。
1.1.1.4从焊剂新箱打开使用时,必须完全干燥状态下施焊。
1.1.1.5焊剂如打开经12小时后,须经1200C、1小时的干燥。
1.1.1.6新购买的焊条必须交仓库保管,置于通风、干燥、不直接接触地面的场所,使用时须填具领料单向仓库领用。
1.1.1.7工作结束,剩余焊条必须收回置于干燥箱内,次日再取用。
1.1.2坡口加工1.1.2.1为达到设计要求,钢材接合部板厚9mm以上的全熔透焊接必须开坡口,坡口的形状、尺寸、加工方法应按照设计图(制造图)或放样图所规定的要求进行。
1.1.2.2坡口表面要清理干净并作防锈处理或立即焊接。
1.1.2.3火焰开坡口若有伤痕,须用电焊修补后再用砂轮机磨平,并清理干净割渣和焊渣。
1.1.3焊接预热1.1.3.1在低温或母材为厚板时可进行焊接前加热,从而避免焊接部位因急冷而发生裂纹。
1.1.3.2预热温度控制如下:1.1.4焊接前检查1.1.4.1是否选择正确的焊接方法和焊接材料。
1.1.4.2坡口加工、构件组立是否达到规定的精度。
1.1.4.3焊接施工顺序是否正确。
1.1.4.4焊接面是否清洁。
1.1.4.5预热方案是否可行。
1.2焊接方法1.2.1手工电弧焊1.2.1.1焊条型号选择如下表:1.2.1.2焊条直径选择如下表:1.2.1.3电流选择如下表:1.2.2埋弧自动焊1.2.2.1钢板对接焊接参数表:1.2.2.2填角焊焊接参数表:1.2.3 CO2焊接电流参数表:1.3 焊接施工1.3.1 钢板对接1.3.1.1 下料:根据施工图要求把所要拼接的钢板放长30~50mm ,以补充焊缝收缩和边线的不整齐。
桥梁工程钢结构施工工艺(3篇)

第1篇随着我国基础设施建设的快速发展,桥梁工程作为交通运输的重要基础设施,其建设规模和水平不断提高。
钢结构因其具有自重轻、强度高、施工周期短、耐腐蚀等优点,在桥梁工程中得到广泛应用。
本文将简要介绍桥梁工程钢结构施工工艺。
一、施工准备1. 施工图纸:根据设计图纸,了解桥梁结构形式、尺寸、材料等,为施工提供依据。
2. 施工方案:根据施工图纸和现场实际情况,制定合理的施工方案,包括施工顺序、施工工艺、施工方法等。
3. 施工材料:按照设计要求,准备足够的钢材、焊接材料、防腐材料等。
4. 施工设备:准备施工所需的吊装设备、焊接设备、切割设备、钻孔设备等。
二、施工工艺1. 钢结构预制:根据设计图纸,将钢材加工成梁、板、柱等构件,进行预拼装,确保构件尺寸和精度。
2. 钢结构运输:将预制好的构件运输至施工现场,注意保护构件,防止变形和损坏。
3. 钢结构安装:(1)基础施工:根据设计要求,完成基础施工,确保基础牢固、平整。
(2)支架安装:在基础上安装支架,确保支架稳定、可靠。
(3)构件安装:将预制好的构件按照设计要求,采用吊装设备进行安装,注意构件的定位和精度。
4. 钢结构焊接:采用焊接设备对构件进行焊接,确保焊接质量。
5. 钢结构防腐:对焊接好的钢结构进行防腐处理,防止腐蚀。
6. 钢结构涂装:在防腐处理后,对钢结构进行涂装,提高美观度和耐久性。
三、施工质量控制1. 材料质量:严格控制钢材、焊接材料、防腐材料等的质量,确保材料符合设计要求。
2. 施工工艺:严格按照施工方案和工艺进行施工,确保施工质量。
3. 施工检验:在施工过程中,对关键工序进行检验,确保施工质量。
4. 成品保护:在施工过程中,注意成品保护,防止损坏。
四、施工安全1. 安全培训:对施工人员进行安全培训,提高安全意识。
2. 安全防护:在施工过程中,采取必要的安全防护措施,确保施工安全。
3. 应急预案:制定应急预案,应对突发事件。
总之,桥梁工程钢结构施工工艺是一个复杂的过程,涉及多个环节。
钢结构施工方案(齐全通用)

欢迎共阅xxxxxx 工程钢 结 构 1234、钢结构生产制作 5、钢结构吊装 6、钢结构安装 7、辅钢结安装 8、钢结构涂装9、玻璃屋盖安装10、主要技术组织措施11、安全施工保证12、工期保证体系一、工程概况㎡,1233.13.2、建筑工程抗震设防类别标准GB50223-20083.3、建筑结构荷载规范GB50009-20123.4、建筑抗震设计规范GB50011-20103.5、钢结构设计规范GB50017-20033.6、建筑钢结构焊接技术规程JGJ81-2002,J218-20024、有关本工程技术洽商和图纸会审记录;三、材料选用1、本工程承力构件所采用的Q235B钢材的化学成份和力学性能应符合GB/T700及有关标准的要求;Q345B钢材的化学成份和力学性能应符合GB/T1591及有关标准的要求;除应具有抗拉强度、伸长率、屈服点和硫磷含1.11.21.32)为3级,4、锚栓采用符合现行国家标准《弹素结构钢》GB/T700-2006规定的Q235B 钢材制成。
《钢结构用高强度大六角头螺栓、大六角头螺母、垫圈与技术条件》(GB/T1228-1231)的规定。
5、零配件:5.1固定屋、墙面钢板自攻螺丝应经镀锌处理,螺丝之帽盖用尼龙头覆着,且钻尾能够自行钻孔固定在钢结构上。
5.2止水胶泥:应使用中性之止水胶泥(硅胶)。
5.3屋脊、墙角的固定件应加密,并加设固定压条。
四、钢结构生产制作1.2材料管理(1)材料进厂,按品名、规格、数量,会同供应人员清点入库。
并应认真核对镑码单、装箱单、运单、材质证明书及合格证等,并详细做好入库时的质量记录。
(2)对入库材料按其性能做到下垫、上盖、中通风,按规范进行堆放,材料员应随时检查落实情况。
2材平直,但由于薄型钢板易产生凹凸不平再加之剪切下料也易变形,焊接面型时必须进行矫正。
2.3放样号料:钢结构下料是第一道工序,该工程采取图纸下料法,直接按图纸所示的尺寸在钢材上按1:1的比例划线下料,允许偏差不超过1mm。
钢结构施工组织设计(通用版)

施工组织设计目录第一章指导思想及实施目标第二章编制目的与依据第三章工程概况及特点第四章主要施工部署第五章轻钢结构构件加工及技术措施第六章主要施工方法第七章工程拟投入的主要物资和施工机械设备情况、主要施工机械计划第八章劳动力安排计划第九章确保工程质量的技术组织措施第十章确保安全施工的技术组织措施第十一章确保文明施工的技术组织措施第十二章确保工期的技术组织措施第十三章施工总进度表和工期网络图第十四章施工总平面布置图及临时设施布置和临时用地表第十五章环境保护措施第十六章雨季、冬季施工措施第十七章服务承诺措施第十八章工程保修措施第一章指导思想及实施目标1.指导思想我公司针对本工程的指导思想是:为充分发挥企业优势,科学组织安装作业,我们将选派高素质的项目经理及工程技术管理人员。
按项目法施工管理,严格执行ISO9001质量保证体系,积极推广新技术、新工艺、新材料,精心组织,科学管理,优质高效地完成施工任务,创出省以至全国第一流水平的工程。
2.实施目标2.1工期目标根据建设单位要求总工期20天我公司确保按期完成整个施工任务。
2.2质量目标严格执行《建筑工程施工质量验收统一标准》GB50300-2001,确保一次交验达到优质。
争创优质样板工程。
2.3安全目标加强进场人员的安全思想教育,提高施工人员的安全意识,同时加大安全费用投入,杜绝死亡及重伤事故,月轻伤频率控制在1.5‰以下。
2.4文明施工目标严格按文明施工的各项规定执行,场内各种建筑材料堆码成行成垛,实行禁烟、无垃圾管理,保持场容、市容环境卫生,确保达到市级安全文明工地标准。
2.5环境保护目标在确保工程质量和工期的前提下,树立全员环保意识,采取有效措施,减少施工噪音和环境污染,自觉保护市政设施,最大限度减少对环境的污染。
2.6科技进步目标为实现上述质量、工期、安全文明施工等目标,充分发挥科技的作用,在施工中积极采用成熟的科技成果和现代化管理技术。
第二章编制目的与依据一、编制目的本施工组织设计编制的目的是为工程项目现场施工,提供较为完整的纲领性技术文件,用以指导工程施工与管理,确保优质、高效、安全、文明地完成该工程的建设任务。
桥梁钢结构工程通用工艺-高强螺栓作业指导书

桥梁钢结构工程通用工艺高强度螺栓作业指导书编制:审核:批准:版本:01一、技术标准《铁路钢桥高强度螺栓连接施工规定》(TBJ214-92)《钢结构用高强度大六角头螺栓、大六角螺母、垫圈技术条件》(GB/T1228-1231-2006)《公路桥涵施工技术规范》(JTG/T3650-2020)《钢结构高强度螺栓连接技术规程》(JGJ82-2011)《钢结构工程施工质量验收标准》(GB50205-2020)二、高强螺栓施拧2.1高强度螺栓连接副技术参数高强螺栓连接副应符合《钢结构用高强度大六角头螺栓、大六角螺母、垫圈技术条件»(GB/T1228~1231-2006)中所规定的技术条件。
摩擦面的表面抗滑移系数,出厂时不小于0.55,安装时不小于0.45。
高强度螺栓施拧采用扭矩法施工,分初拧、终拧两个步骤进行。
对于大型节点应分为初拧、复拧、终拧。
高强度螺栓初拧、终拧采用定扭矩扳手施拧,初拧、复拧扭矩等于终拧扭矩值的50%左右。
初拧或复拧后应对每个螺栓用颜色在螺母上标记,终拧后应对每个螺栓用另一种颜色在螺母上标记。
初拧、复拧、终拧宜在一天内完成。
2.2进场验收与保管高强度螺栓连接副应按批配套进场,须查验出厂质量保证书,并进行外观尺寸检查。
高强螺栓连接副应在同批内配套使用。
进场验收合格后,应按包装箱上注明的规格、批号分类存放和保管;室内存放,堆放时应有防止生锈、潮湿及沾染脏物等措施,并做好标识,在使用安装前严禁随意开箱。
高强度螺栓连接副在运输、保管过程中,应轻装、轻卸,防止损伤螺纹。
高强螺栓连接副的保管时间不应超过6个月,当保管时间超过6个月后使用时,必须按要求重新进行扭矩实验或紧固轴力实验,检验合格后,方可使用。
高强度螺栓、螺母和垫圈现场发放时,根据当天使用量进行登记发放,不得以长带短或者以短代长。
当天未使用的高强螺栓连接副应妥善保管,不得乱扔、乱放。
2.3现场工艺试验进场验收合格的高强度螺栓,应按生产厂提供的批号,并按每批不少于8套分批测定高强度螺栓扭距连接副的扭矩系数,该批扭矩系数平均值应在0.110-0.150范围内,其标准偏差应小于或等于0.010。
钢结构施工方案(齐全通用)

钢结构施工方案(齐全通用)1000字钢结构施工方案是指在建筑物和工程中采用钢材预制构件作为主要结构承载体的一种建筑施工方法。
以下是一般通用的钢结构施工方案:1. 施工前的准备在施工前,需要进行钢结构的设计、制造、运输及其安装的场地考察与规划等,确保有一个良好的施工现场。
2. 钢结构加工制造预制构件将根据设计方案加工制成,在工厂中完成。
3. 运输加工完成后,构件会被运输至施工现场。
运输需要选择专业的运输公司,并对于运输过程的安全进行规划、确认。
4. 施工现场的准备到达现场后,需要清除净化施工区域,妥善正确布置卸货区域、建筑设备以及材料和设备。
5. 钢结构的安装在进行安装前,需要进行工艺控制、安全操作、质量保证等准备工作。
详见如下:(1)搭设起吊设备,并进行检测;(2)钢结构构件卸货,并决定最后位置,并对其进行调整;(3)按照施工图纸进行结构安装,并严格按规范操作;(4)检查结构互锁、位置错位过大、单元变形以及表面损伤等情况;(5)进行焊接、切割等必要的工序,并保证工序安全;(6)对于明确标记的部分,进行密封,以减少灰尘和噪音等污染;(7)外部旋转结构和无依托结构进行临时支撑,并保证稳定;(8)结构竣工后进行检验,以查看与设计是否相符。
6.后续工作结构建成后,需要建立相关档案以便后续的监控。
此外,也应该对于施工人员进行教育,以致于在维护和保养时能够遵循规范操作。
综上所述,对于钢结构的施工,需要先进的技术和完备的施工方案,以保证施工出来的产品能够达到规定的标准。
还需要在施工过程中,对于施工安全、质量以及对环境的影响要进行控制和把控,才能够确保最终的质量和安全。
钢结构施工工艺
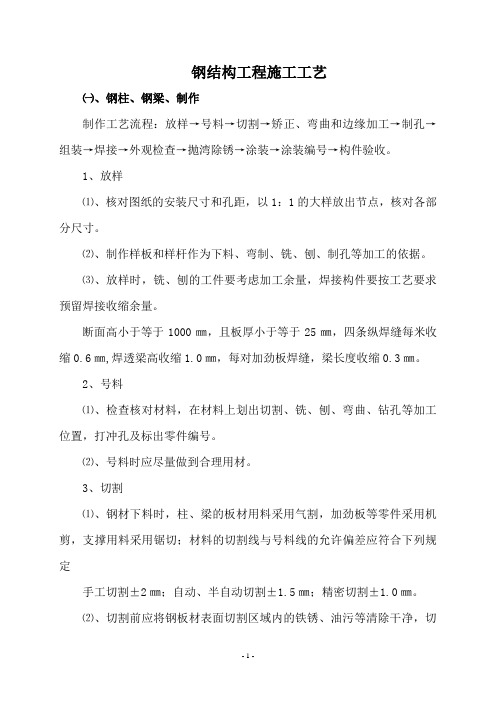
钢结构工程施工工艺㈠、钢柱、钢梁、制作制作工艺流程:放样→号料→切割→矫正、弯曲和边缘加工→制孔→组装→焊接→外观检查→抛湾除锈→涂装→涂装编号→构件验收。
1、放样⑴、核对图纸的安装尺寸和孔距,以1:1的大样放出节点,核对各部分尺寸。
⑵、制作样板和样杆作为下料、弯制、铣、刨、制孔等加工的依据。
⑶、放样时,铣、刨的工件要考虑加工余量,焊接构件要按工艺要求预留焊接收缩余量。
断面高小于等于1000㎜,且板厚小于等于25㎜,四条纵焊缝每米收缩0.6㎜,焊透梁高收缩1.0㎜,每对加劲板焊缝,梁长度收缩0.3㎜。
2、号料⑴、检查核对材料,在材料上划出切割、铣、刨、弯曲、钻孔等加工位置,打冲孔及标出零件编号。
⑵、号料时应尽量做到合理用材。
3、切割⑴、钢材下料时,柱、梁的板材用料采用气割,加劲板等零件采用机剪,支撑用料采用锯切;材料的切割线与号料线的允许偏差应符合下列规定手工切割±2㎜;自动、半自动切割±1.5㎜;精密切割±1.0㎜。
⑵、切割前应将钢板材表面切割区域内的铁锈、油污等清除干净,切割后,断面上不得有裂纹和大于1㎜的铁棱,•并应清除边缘上的熔瘤和飞溅物等。
⑶、切割截面与钢材表面不垂直度应不大于钢板材厚度的10%,且不大于2㎜。
⑷、机械剪切的零件,其剪切线与号料线的允许偏差不得大于2.0㎜;断口处的截面上不得有裂纹和大于1.0㎜的缺棱,并应清除毛刺。
机械剪切的斜度不得大于2.0㎜。
4、矫正弯曲和边缘加工:⑴、普通碳素结构钢在高于-16摄氏度,可用冷矫正和冷弯曲。
⑵、矫正后的钢材表面不应有明显的凹面和损伤,表面划痕深度不能大于0.5㎜。
⑶、钢材矫正后的允许偏差应符合规范要求:①、钢板厚度小于或等于14㎜时,其允许偏差不大于或等于1.5㎜。
②、钢板厚度大于或等于14㎜时,其允许偏差不大于或等于1㎜。
⑷、普通碳素结构钢,允许加热矫正,其加热温度严禁超过正火温度。
⑸、边缘加工按需要可采用下列方法:①、刨边机加工;半自动、自动气割机坡扣加工;电弧气割。
(完整版)钢结构制作施工工艺手册
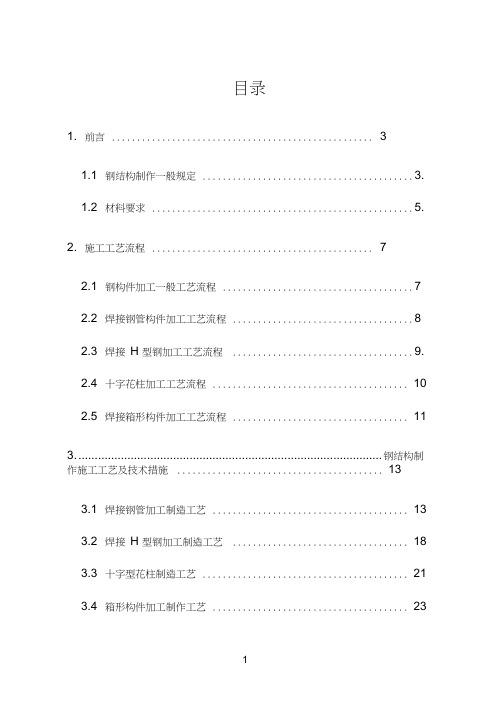
目录1. 前言 (3)1.1 钢结构制作一般规定.......................................... 3.1.2 材料要求.................................................... 5.2. 施工工艺流程 (7)2.1 钢构件加工一般工艺流程 (7)2.2 焊接钢管构件加工工艺流程 (8)2.3 焊接H 型钢加工工艺流程.................................... 9.2.4 十字花柱加工工艺流程 (10)2.5 焊接箱形构件加工工艺流程 (11)3. ............................................................................................. 钢结构制作施工工艺及技术措施.. (13)3.1 焊接钢管加工制造工艺 (13)3.2 焊接H 型钢加工制造工艺 (18)3.3 十字型花柱制造工艺 (21)3.4 箱形构件加工制作工艺 (23)3.5 钢结构构件制作技术措施 (26)4. 钢结构制作注意事项 (38)4.1 施工准备 (38)4.2 放样 (39)4.3 号料 (39)4.4 切割 (40)4.5 组装 (41)1. 前言技术部认真研究业主提供的施工技术文件(设计施工图、设计规范、技术要求等资料),并邀请设计院对工厂进行设计技术交底,经技术部门消化理解后,编制《制造工艺方案》《制造验收要求》、完成施工图转换、焊接工艺评定、火焰切割工艺评定、涂装工艺评定、工艺文件编制、工装设计和质量计划编制等技术准备工作。
1.1 钢结构制作一般规定1.1.1 钢结构的制作单位应根据已批准的技术设计文件编制施工详图,且经原设计单位批准。
当需要修改时,制作单位应向原设计单位申报,经同意并签署文件后方能生效。
1.1.2 钢结构在制作前,应根据设计文件和施工详图的要求编制制作工艺文件。
钢结构厂房施工工艺
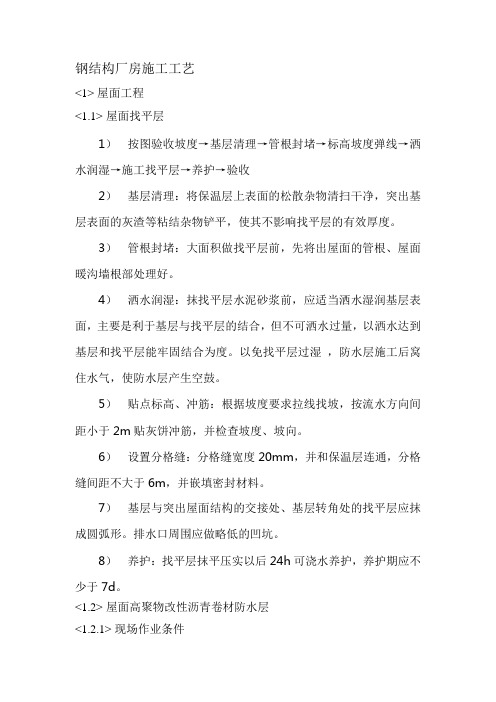
钢结构厂房施工工艺<1>屋面工程<1.1>屋面找平层1)按图验收坡度→基层清理→管根封堵→标高坡度弹线→洒水润湿→施工找平层→养护→验收2)基层清理:将保温层上表面的松散杂物清扫干净,突出基层表面的灰渣等粘结杂物铲平,使其不影响找平层的有效厚度。
3)管根封堵:大面积做找平层前,先将出屋面的管根、屋面暖沟墙根部处理好。
4)洒水润湿:抹找平层水泥砂浆前,应适当洒水湿润基层表面,主要是利于基层与找平层的结合,但不可洒水过量,以洒水达到基层和找平层能牢固结合为度。
以免找平层过湿,防水层施工后窝住水气,使防水层产生空鼓。
5)贴点标高、冲筋:根据坡度要求拉线找坡,按流水方向间距小于2m贴灰饼冲筋,并检查坡度、坡向。
6)设置分格缝:分格缝宽度20mm,并和保温层连通,分格缝间距不大于6m,并嵌填密封材料。
7)基层与突出屋面结构的交接处、基层转角处的找平层应抹成圆弧形。
排水口周围应做略低的凹坑。
8)养护:找平层抹平压实以后24h可浇水养护,养护期应不少于7d。
<1.2>屋面高聚物改性沥青卷材防水层<1.2.1>现场作业条件1)铺贴防水层的基层表面,应将尘土、杂物彻底清除干净。
2)基层坡度应符合设计要求,表面应顺平,阴阳角处应做成圆弧形,基层表面必须干燥,含水率应不大于9%。
3)卷材及配套材料必须验收合格,规格、技术性能必须符合设计要求及标准的规定。
存放易燃材料应避开火源。
<1.2.2>操作工艺1)清理基层→涂刷基层处理剂→铺贴卷材附层→铺贴卷材→热熔封边→蓄水试验→保护层2)清理基层:施工前将验收合格的基层表面尘土、杂物清理干净。
3)涂刷基层处理剂:高聚物改性沥青卷材施工,按产品说明书配套使用,基层处理剂是将氯丁橡胶沥青胶粘剂加入工业汽油稀释,搅拌均匀,用长把滚刷均匀涂刷于基层表面上,常温经过4h后,开始铺贴卷材。
4)附加层施工:一般用热熔法使用改性沥青卷材施工防水层,在女儿墙、水落口、管根、檐口、阴阳角等细部先做附加层,附加的范围应符合设计或规范要求。
钢结构工程施工工艺

XXXX钢结构加建工程施工方案一、技术准备1.根据工程特点,结合现场实际情况,绘出施工平面布置图2.认真审核、熟悉施工图纸,领会设计意图,做好图纸会审。
3.明确工程内容,分析工程特点,并由技术负责人组织编制切实可行的分部分项施工组织设计。
明确钢结构与常规土建以及钢结构与装饰工程的工作交接、互检、协调的具体内容与方法。
4.对施工班组进行有针对性的技术交底。
5.根据工程实际情况划分施工区域,并以此为依据确定劳动力及材料需用量。
制定流水作业图,具体细化到每道工序在每层、每个流水段的作业部位及作业时间。
6.根据施工图提出半成品等材料加工计划。
提早落实各种材料的货源,并根据工程进度计划确定进场日期。
同时要做好各种材料进场的复试工作和样本、样品的报验工作。
7.根据工程的需要培训操作工人。
特殊工种操作人员必须持证上岗。
8.对照施工图查验现场实际情况,提前将无法按照设计意图施工的部分整理出来,提前与设计人员协商施工方法。
二、物资准备工作根据施工预算和施工进度的安排,组织货源,确定加工地点和供应方式,签订物资供货合同。
根据各种物资的需要量计划和合同,拟定运输计划和运输方案。
按照施工平面图的要求,组织物资按计划时间进场,在指定地点,按规定方式进行储存和保管。
钢材应附有质量证明书,其质量标准应符合现行标准的各种技术条件并应符合设计图纸的标,不得使用无质量证明的钢材。
三、施工准备工作1、设计阶级:(1)根据建设单位意图,了解其总体设想,并根据郑州市陇海路支行装饰及加建工程施工图进行施工。
(2)积极参与图纸会审,及时提出问题请求答复,并积极向建设单位及设计单位推荐优秀建筑节点图集。
2、原材料供应阶段:(1)根据经建设单位审核的施工图纸要求积极采购原材料,所有原材料的供应必须符合ISO9001质量标准要求。
(2)原材料采购过程中,如某些材料市场未能采购到,应积极同业主联系,在业主签字认可的情况下遵循等强度代换原则方可使用。
钢结构下料通用工艺

钢结构下料通用工艺1、主体内容与适用范围1.1 主体内容:钢材划线、下料及切割的有关技术要求。
1.2适用范围:板材、型材和管材的划线、下料及切割。
2、编制依据JGJ81-2002《钢结构焊接技术规程》JGJ99-98 《高层民用建筑钢结构技术规程》3、操作前的准备3.1 操作人员应熟悉图样、技术要求及工艺文件的内容,并熟悉所用的设备、工具的使用性能,严格遵守安全操作规程和设备维护保养规则。
数控切割应预先输入图形或编制程序。
气割及设备操作人员须考试合格后上岗。
3.2 操作人员应按有关文件的规定,认真做好现场管理工作。
对工件和工具应备有相应的工位器具,整齐地放置在指定地点,防止碰损、锈蚀。
3.3 操作前,操作人员应准备好作业必备的工具、量具,并仔细检查、调试所用的设备、仪表、量检具、模具、刀具,使其处于良好的状态。
使用的仪表、量检具应在有效检定期内。
4、划线4.1 一般规定4.1.1 钢材存在影响划线的弯曲、凹凸不平时,应先进行矫正。
4.1.2 划线前,钢材表面必须清理干净,去除油污、锈蚀等,发现钢材有裂纹、严重锈蚀等缺陷,应经检查部门做出处理后,方可划线。
4.1.3 自行制作的划线样板、样杆,应得到检验部门的确认。
4.2 划线的技术要求4.2.1 应按设计图样、工艺文件在钢材上以1:1实样进行划线,根据不同的下料方法,划线时应留出适当的切割余量。
4.2.2 断面不规则的板材、型材及管材等材料划线时,必须将不规则部分让出。
应注意个别件对材料轧制纹络的要求。
第 1 页共 7 页4.2.3 用石笔所划出的线条及粉线所弹出的线条必须清晰。
4.2.4 划线时,应首先划基准线,而后再划其它线;对于对称的工件,一般应先划中心线,以此为基准在划圆弧,最后在划各直线。
划线时可用样冲打小眼让圆规定脚。
4.2.5 需要剪切的工件,划线时应考虑剪切线是否合理,避免发生不适于操作的情况。
4.2.6 在带有毛边的钢板上下料线时,要根据钢板毛边的实际情况,去除不符合钢板质量要求的部分,并在此基础上再向内让出10mm划出下料线。
钢结构施工工艺流程(完整版)

钢结构施工工艺流程(完整版)一:钢结构施工工艺流程(完整版)1. 前期准备1.1 调查阶段1.1.1 场地调查1.1.2 地质勘查1.1.3 设计要求评估1.1.4 方案确定1.2 施工准备1.2.1 材料准备1.2.2 设备准备1.2.3 人员组织1.2.4 施工计划制定2. 地基处理2.1 土地平整2.2 地基处理方案选择2.2.1 地基强化2.2.2 地基加固2.2.3 地基处理资料2.3 地基施工2.3.1 挖土施工2.3.2 固定地基处理材料2.3.3 地基处理验收3. 钢结构安装3.1 钢结构材料验收3.1.1 钢材验收3.1.2 连接件验收3.2 钢结构预制3.2.1 钢构件预制3.2.2 衔接件制造3.2.3 钢结构成品保护3.3 钢结构组装3.3.1 设备、工具准备 3.3.2 搭设起重设备 3.3.3 钢结构吊装3.3.4 钢结构定位3.3.5 钢结构连接3.4 焊接工艺3.4.1 焊接材料选择 3.4.2 焊接设备准备 3.4.3 焊接方法3.5 钢结构防腐3.5.1 防腐材料选择 3.5.2 防腐工艺流程3.5.3 防腐验收4. 装饰装修4.1 防火涂料施工4.2 玻璃幕墙安装4.3 室内装修4.3.1 空调安装4.3.2 墙面装修4.3.3 地面装修4.3.4 电气线路布置5. 竣工验收5.1 安全检查5.2 施工质量检查5.3 设备调试5.4 相关手续办理附件:1. 钢结构施工图纸2. 设计方案文件3. 钢材、连接件材质检测报告4. 地基处理验收报告5. 焊接工艺规程法律名词及注释:1. 土地平整:将工地土地表面进行整平处理,提供施工基础。
2. 地基强化:使用某种方法对地基进行强化,提高地基承载力。
3. 地基加固:使用某种方法对地基进行加固,增加地基稳定性和抗震性能。
4. 施工计划制定:制定详细的施工进度计划,明确施工工作时间和工序。
5. 防腐材料选择:选择符合相关标准和要求的防腐材料。
全套钢结构企业的钢结构制造通用工艺规程(原材料,焊接,螺栓)
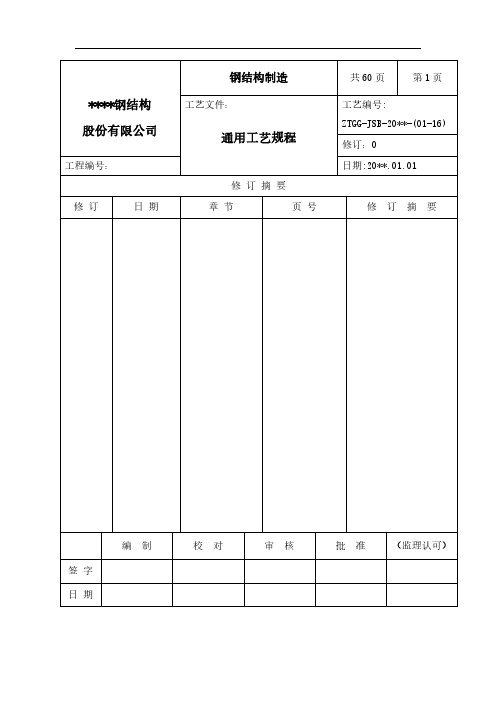
6 钢板辊平预处理工艺规程 7 零件下料加工工艺规程 8 火焰切割工艺评定试验工艺规程 9 火焰切割缺陷修补工艺规程 10 精密切割工艺规程 11 螺栓孔制作工艺规程 12 焊工资格考试大纲 13 焊接工艺规程 14 焊缝返修工艺规程 15 火焰矫正工艺规程 16 高强度螺栓抗滑移系数试验工艺规程
文件编号 ZTGG—JSB—20**—01 ZTGG—JSB—20**—02 ZTGG—JSB—20**—03 ZTGG—JSB—20**—04 ZTGG—JSB—20**—05 ZTGG—JSB—20**—06 ZTGG—JSB—20**—07 ZTGG—JSB—20**—08 ZTGG—JSB—20**—09 ZTGG—JSB—20**—10 ZTGG—JSB—20**—11 ZTGG—JSB—20**—12 ZTGG—JSB—20**—13 ZTGG—JSB—20**—14 ZTGG—JSB—20**—15 ZTGG—JSB—20**—16
****钢结构股份有限公司
钢结构制造通用工艺规程
5. 理化检验
图 4.7 检验工艺流程
5.1. 化学分析
表 5.1-1 钢材化学成份复验
序号
钢材牌号
检验项目
1
碳 素 结 构 钢
Q235A Q235B Q235C Q235D
C、Si、Mn、P、S
Q345qC
2
桥 梁 用 结 构 钢
Q345qD Q345qE Q370qC Q370qD Q370qE Q420qC Q420qD
钢结构制造通用工艺规程
表 4.5 钢板取样规定和检验项目
序号 名称 牌号
执行标准
抽检比例
检验项目 取样方法
备注
Q345qC
- 1、下载文档前请自行甄别文档内容的完整性,平台不提供额外的编辑、内容补充、找答案等附加服务。
- 2、"仅部分预览"的文档,不可在线预览部分如存在完整性等问题,可反馈申请退款(可完整预览的文档不适用该条件!)。
- 3、如文档侵犯您的权益,请联系客服反馈,我们会尽快为您处理(人工客服工作时间:9:00-18:30)。
钢结构制造工艺(通用部分)
一、钢材
1.1、购钢材必须确认具有资质的供应商及生产厂,购入时应附有生产钢厂的材质质量证明书,
出厂合格证书。
1.2、钢材进入制造工厂后,并按标准进行抽查复验,同一厂家、同一材质、同一出厂状态抽验一组试件,钢材的化学成份及机械性能应符合标准,做好复验检查记录。
1.3、制造使用的钢材,在材质或规格方面,如有意外变化,对原设计需做任何改变时,不允
许自行更换,必须由设计单位确认方可变更。
1.4、当钢材表面有锈蚀、麻点或划痕等缺陷时,其深度0.3~1mm时可磨修匀顺;如钢材
有层状裂纹深度超过1mm且不超过5mm,碳弧气刨清除缺陷,两端必须按要求各延伸50mm并有1:5的斜坡,将焊处异物清除,再填焊,焊后磨修匀顺。
1.5、原材料进厂后的堆放应整齐,避免潮湿,腐蚀,实行专料专用,按保存规定涂刷
标记。
二、制造工艺
1、施工人员应有专业操作证书、並持证上岗;
2、施工人员首先必须熟悉图纸,掌握各另部件的部位,了解每项部位所起的用途,
方可进行施工;
3、施工人员首先必须熟悉各项施工工序,及按施工工艺,严格按施工工艺进行操作;
4、各部门所使用的计量工具,应是经过计量机构鉴定合格的方可使用;
2.1结构件
2.1.1、凡参加本项目施工的主要操作人员,必须具有中级以上技术水平,必须熟悉施工工艺,
施工工序;
2.1.2、结构件的下料、加工、组拼、焊接,应严格按施工图和施工工艺规则执行;
2.1.3、领用的材料应为进厂后按规定经过复验合格的材料;
2.1.4、焊接组拼工作必须在专用平台或胎架内进行,并应在平台或胎架上设置组拼定位板,以
保证另部件的位置。
组拼合格后应在规定部位打上编号标记;
2.1.5、凡需焊接、对接部位的位制必须打磨,无锈及氧化铁皮,露出金属光泽,并不得超过
24小时,否则应重新打磨;
2.1.6、焊缝坡口应符合GB985和GB986的规定;
2.1.7、受拉区的翼板,腹板的对接焊缝应进行无损探伤,射线探伤时应不低于GB3323中规
定的Ⅱ级,超声探伤时应不低于GB11345-89中规定的Ⅰ级。
重要角焊缝应不低于GB11345-89中规定的Ⅱ级。
2.1.8、所有须焊接的杆件下料时应留有焊缝收缩余量
2.1.9、所有钢材焊前必须调平、调直;
2.2、各部件制造允许偏差:
2.2.2、箱梁腹板的局部平面度,以2m平尺测量,在受压区以内小于3mm, 其他区域不
大于5mm。
2.2.3、箱梁上翼板水平偏斜≤B/600(B为翼缘宽)。
2.2.4、箱梁腹板的垂直偏斜≤H/1000(H为梁高)。
2.2.5、除上述要求外,应符合TB10212-98 《铁路钢桥制造规范》
2.3、焊缝质量要求
2.3.1、焊缝外观质量
2.3.2、对接焊缝、角焊缝超声波探伤范围及质量等级GB/T3323-87要求
2.3.3 、对接焊缝X射线探伤范围及质量等级
2.3.4、焊接:
1)CO2气体保护焊或手工电弧焊可用于所有焊缝的焊接,及定位焊;
2)埋孤自动焊可用于钢板全熔透对接、盖板与腹板的T型、工型或箱型杆件,中长直线主角焊位的焊接;
3)CO2气体保护焊丝:H08Mn2Si,φ1.2mm;
用于Q345B钢与Q345B钢、Q345B钢与其它钢、Q235钢与中碳钢的焊接;
4)E5015,φ4.0mm~φ5.0mm手工电弧焊焊条、
用于Q345B钢与Q345B钢、Q345Bc钢与其它钢、Q235钢与中碳钢的焊接;
5)E4303,φ4.0mm~φ5.0mm手工电弧焊焊条
用于Q235钢与Q235钢之间的焊接;
6) H08MnA,φ5mm埋孤自动焊丝、HJ431 φ1.0~φ3.0mm焊剂
用于Q345B钢与Q345B钢之间的焊接;
2.4、下料:
2.4.1、特殊板料应根据实际来料规格,编排下料图
2.4.2、周边及剖口不进行机加工的零件,放出0.5‰焊接收缩余量用精密切割的方法完成;
2.4.3周边及剖口须进行机加工的零件,放出加工余量、及0.5‰焊接收缩余量,用精密切割的
方法法或其它下料方法完成;
2.4.4、因供料原因或变截面的原因,均允许采用对接接长、接宽,但要求在同一组件、或同一
部件中,相邻对接接头应错位,其错开位最小距离应大于200mm,且距水平或垂直筋板距离应大于100mm,长度接头最小应大于1000mm;
2.4.5、凡须焊接的腹板、各箱梁中间的定位隔板、均必须用机加工的方法完成,对角线<0.5mm;
2.4.6、须焊接部位须打磨除锈,露出金属原有光泽,且不得超过24小时;
2.5、主梁的制造;
2.5.1、原材料进厂经复检后,上平板机进行平整;
2.5.2、各板下料质量按下表进行:
2.5.2.1、主梁的内腹板、外腹板、根据排料图下料;
2.5.2.2、腹板按排料图及拼接图,宽进行对接下料,下料必须留有对接、焊接收缩余量,拼接
按排料图所示,拼接必须错开相邻盖板对接焊缝200mm隔扳100mm,对接头大于1000mm;
2.5.2.3、对接后将各板调平、划切割边线,起拱点是靠腹板间断折线来完成;
2.5.2.4、内腹板、外腹板均为对称配对成形;
2.5.2.5、上盖板、下盖板均为对称配对成形;
2.6、主梁拼装
2.6.1、按试拼要求将试拼所须构件,按拼装顺序编号、进场、组拼;
2.6.2、预铺设起拱施工平台,按设计图要求设置最高起拱,设置支撑点,并用水平仪操起拱支
点;
2.6.3、将各隔板按图横向定位、纵筋板、内腹板、外腹板纵向定位并施焊固定;
2.6.4、将上盖板按图定位,并施焊固定;
2.6.5、经检测后方可全部焊接;
2.6.6、用已钻好连接孔的拼接板,将节段1、节段3内外腹板及上盖板用磁铁钻套钻各连接孔,
并用各1/3冲钉定位及螺栓固定;
2.6.7、用起吊支撑的方法,在主梁32700支撑位,将主梁撑起
2.6.8、按图划直线开梳形梁方孔,注意各孔孔距土1.0、孔与主梁中心线的垂直度;
2.6.9、将主梁翻身下盖扳向上,调好两边主梁平行度;
2.6.10、定位纵移孔扳,保证主梁两边纵移孔扳长方孔在同一截面上,再定位焊接并钻连接孔;
2.6.11定位纵移轨道扳,保证主梁两边轨道扳平行度,及单片主梁轨道扳宽度及直线度,再定
位焊接,保证轨道板平面度。
2.7、导(桁)梁的制造
2.7.1、加工各上下弦杆的腹板,与盖板的双面焊接面;
2.7.2、加工各连接板,与上下弦杆的双面剖焊口;
2.7.3、将各连接板的孔划线及镗好连接孔;
2.7.4、须焊接部位须打磨除锈,露出金属原有光泽,且不得超过24小时;
2.7.5、各板完工后经检测无误方可待下步拼装用。
2.7.6、拼装
2.7.5.1、按工艺图所示,制作组拼胎模,在拼装胎模上按图将导梁上下弦杆进行组拼成H型;
2.7.5.2、将H型进行调平调直,并探伤检测;
2.7.5.3、将各槽钢对扣施焊,并检测;若设计图采用间断焊接时,间断间隔按焊接规范执行。
2.7.6、导(桁)梁的组拼
2.7.6.1、首先进行前导梁单片组拼,在拼装平台上按导梁图将两下弦用平联并成一体,并焊为
一体;
2.7.6.2、用拼接板将各竖斜杆与上下弦杆点焊定位,按图焊各部角焊;
2.7.6.3、注意控制下弦杆的外宽;
2.7.6.4、将第一节和第二节导梁上下弦划孔的加工线;
2.7.6.5、按第一节和第二节导梁上下弦孔线,校正加工;
2.7.6.7、用工艺销轴将各连接板和三节导梁定位;
2.7.6.8、经检测无误方可将各连接板施焊;
2.8、梳形梁的制造
2.8.1、将不等边角钢125X80修边为125X76及倒焊接剖口,将角钢内筋板与角钢配做,对称
定位并焊接;
2.8.2、各槽钢对扣定位焊接;
2.8.3、在拼装平台上,首先将各腹板与盖板组拼成单H体,并施焊;
2.8.4、将已拼的H体调整平直;
2.8.5、将焊接好筋板的不等边角钢125X76,在H体梁外侧上下分别,对称定位焊接,并调整
平直;
2.8.6、制作控制梳形粱宽度及直线度垂直度的拼装胎模;
2.8.7、将对称工体梁在拼装胎模内定位,用平联及钭撑连接定位焊接,并调平直;
2.8.8、用孔群组整体模板钻各联接孔孔群;
2.8.9、将拼装好的梳形粱划线切法兰端头,保证端头垂直度及平面度;
2.8.10、将己钻好孔的法兰板,两两对称中心用定位销、及上下左右各一个冲钉(φ31-0.2)定位,
并将梳形粱端部倒焊接剖口;
2.8.10、将法兰两边配对的梳形粱划中心定位线,保证同一直线及对角线,再焊接。
三、组装
3.1、在主梁拼装的场地进行;
3.2、将导粱在主梁前端起翘50mm定位,并焊接;。