特采试制物料跟踪流程
物料特采程序(含表格)

物料特采程序(ISO9001-2015/IATF16949-2016)1.0目的规范物料特采流程,有效保证产品质量,促进供应商产品质量逐步提高,减少公司因物料特采带来的人工费用、物料损耗及可能的质量隐患。
2.0范围适用于公司物料特采的运作。
3.0职责3.1品质部负责特采物料挑选/加工标准的提供及全程跟踪。
3.2PMC部门根据生产排期、采购周期,提出特采申请。
3.3工程部负责特采物料的评估、确认(生产部负责加工能力的评估、确认)。
3.4生产部负责特采物料的加工/挑选及相应工时费用等数据的提供、反馈。
3.5采购部负责将工时费用反馈给供应商,向供应商退回不合格物料。
4.0定义物料特采是指对供应商(包括内部供应商)的不合格物料,因生产排期、紧急出货等原因需要进行让步接受,必要时加工、挑选使用的物料所进行特别采购行为。
5.0 运作流程图 形成记录《来料检查报告》《不合格物料处理单》正常情况下《不合格物料处理单》《不合格物料处理单》《不合格物料处理单》偏离标准太多无法接受或无能力加工时《不合格物料处理单》《特采物料加工/挑选时费用表》《特采物料加工/挑选时费用表》 《回仓单》 6.0作业流程6.1确认不合格物料正常情况下,IQC 对不合格物料填写《不合格物料处理单》经品管主管确认后,报PMC (在重新交货周期小于生产前周期时)呈决策者审批后,反馈和退货给供应商。
6.2特采申请6.2.1当PMC 根据生产排期,在重新交货周期大于生产前周期时,可在《不合格物料处理单》相关栏提出特采申请(这是唯一提出特采的条件)。
6.2.2PMC 督促采购部按交期交货,对供应商不依时交货或在生产上线后再交货的行为进行制约。
不合格物料 工程/品管评估确品管部开据处理报告 PMC 提出特采申请让步接收/使用 生产加工/挑选不合格退货/反馈不合格物料 退货供应商 决策者审批 生产部评估确认6.2.3PMC将特采申请反馈给工程部和品管部。
物料跟踪流程
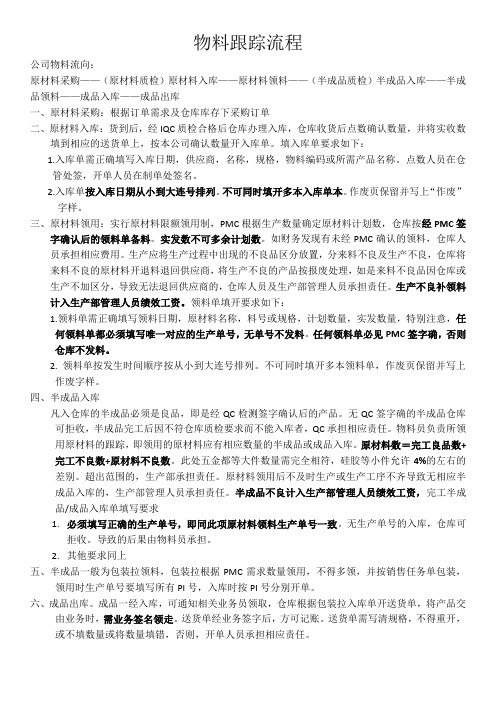
物料跟踪流程公司物料流向:原材料采购——(原材料质检)原材料入库——原材料领料——(半成品质检)半成品入库——半成品领料——成品入库——成品出库一、原材料采购:根据订单需求及仓库库存下采购订单二、原材料入库:货到后,经IQC质检合格后仓库办理入库,仓库收货后点数确认数量,并将实收数填到相应的送货单上,按本公司确认数量开入库单。
填入库单要求如下:1.入库单需正确填写入库日期,供应商,名称,规格,物料编码或所需产品名称。
点数人员在仓管处签,开单人员在制单处签名。
2.入库单按入库日期从小到大连号排列。
不可同时填开多本入库单本。
作废页保留并写上“作废”字样。
三、原材料领用:实行原材料限额领用制,PMC根据生产数量确定原材料计划数,仓库按经PMC签字确认后的领料单备料。
实发数不可多余计划数。
如财务发现有未经PMC确认的领料,仓库人员承担相应费用。
生产应将生产过程中出现的不良品区分放置,分来料不良及生产不良,仓库将来料不良的原材料开退料退回供应商,将生产不良的产品按报废处理,如是来料不良品因仓库或生产不加区分,导致无法退回供应商的,仓库人员及生产部管理人员承担责任。
生产不良补领料计入生产部管理人员绩效工资。
领料单填开要求如下:1.领料单需正确填写领料日期,原材料名称,料号或规格,计划数量,实发数量,特别注意,任何领料单都必须填写唯一对应的生产单号,无单号不发料。
任何领料单必见PMC签字确,否则仓库不发料。
2. 领料单按发生时间顺序按从小到大连号排列。
不可同时填开多本领料单,作废页保留并写上作废字样。
四、半成品入库凡入仓库的半成品必须是良品,即是经QC检测签字确认后的产品。
无QC签字确的半成品仓库可拒收,半成品完工后因不符仓库质检要求而不能入库者,QC承担相应责任。
物料员负责所领用原材料的跟踪,即领用的原材料应有相应数量的半成品或成品入库。
原材料数=完工良品数+完工不良数+原材料不良数。
此处五金都等大件数量需完全相符,硅胶等小件允许4%的左右的差别。
采购物料特采流程及流程图

物料特采流程1.0目的规范物料特采流程,有效保证产品质量,促进供应商产品质量逐步提高,减少公司因物料特采带来的人工费用、物料损耗及可能的质量隐患。
2.0范围适用于公司物料特采的运作。
3.0职责3.1品质部负责特采物料挑选/加工标准的提供及全程跟踪。
3.2PMC部门根据生产排期、采购周期,提出特采申请。
3.3工程部负责特采物料的评估、确认(生产部负责加工能力的评估、确认)。
3.4生产部负责特采物料的加工/挑选及相应工时费等数据的提供、反馈。
3.5采购部负责将工时费用反馈给供应商,向供应商退回不合格物料。
4.0定义物料特采是指对供应商(包括内部供应商)的不合格物料,因生产排期、紧急出货等原因需要进行让步接受,必要时加工,挑选使用物料所进行特别采购行为。
形成记录Array《来料检验报告》《不合格物料处理单》《不合格物料处理单》《不合格物料处理单》《不合格物料处理单》《不合格物料处理单》6.1确认不合格物料正常情况下,IQC对不合格物料填写《不合格物料处理单》经品质主管确认后,报PMC(在重新交货周期小于生产前周期)呈决策者审批后,反馈和退货给供应商。
6.2特采申请6.2.1当PMC根据生产排期,在重新交货周期大于生产周期时,可在《不合格物料处理单》相关栏提出特采申请(这是唯一提出特采的条件)。
6.2.2PMC督促采购部按交期交货,对供应商不依时交货或在生产上线后再交货的进行制约。
6.2.3PMC将特采申请反馈给工程部和品质部。
6.3特采物料评估与确认6.3.1品质部接到物料特采的申请后,组织技术人员、会同品管等相关人员进行评估。
工程部按照品质部检验结果和来料实物,评估特采对象对制造工艺、产品质量的影响,并作出是否可特采的决定,必要时可召开MRB会议评审决定。
6.3.2一般情况下物料特采的工程确认有PIE部负责,必要时由IQC 与开发部门联络共同确认,外观可以由品管部直接确认。
对PMC提出申请的特采物料,可有下列确认结果:①不可使用。
物料特采作业流程

财务部采购部质量管理部进料检验员
生产物料特采作业流程说明
序号
节点
责任人
相关说明
相关文件/记录
1
退货报告
C
IQC检验不合格,但急需上线的物料,
IQC提出特采申请
《退货报告》
2.
确认
财务部采购部
通知财务部,同时交采购部进行确认,共同决定是否特采
3
特采
采购部品质部
无条件特采的情况下,仓库直接入库待
用
IQC/品质
有条件特采时,IQC须实施全检,偏差
《返修产品记录
工程师
接受或要求供应商进行返工处理
表》
4
统计
工时
品质部生产部
由品质部或生产部统计员统计工时,便于计算成本
《生产工时统计表》
5
重检
IQC
返工后产品,IQC须重新进行检验,合格则办理入库;不合格申请退货
6
计算费用
财务部
根据浪费工时数,计算费用,并按合同规定进行扣款处理
物料试产管理规范(含表格)
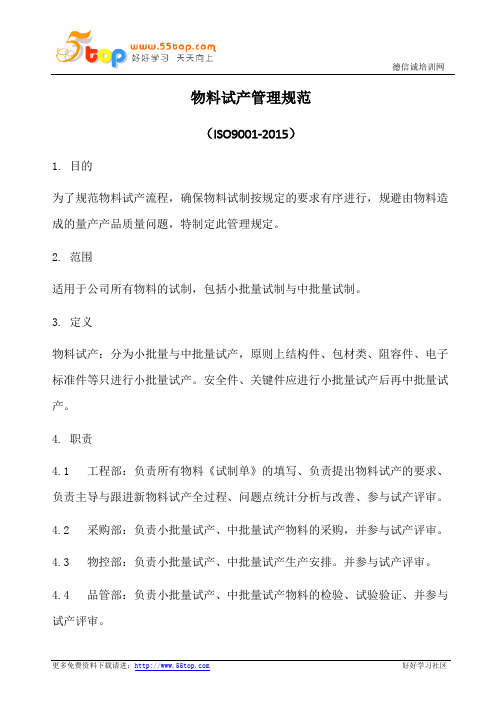
物料试产管理规范(ISO9001-2015)1. 目的为了规范物料试产流程,确保物料试制按规定的要求有序进行,规避由物料造成的量产产品质量问题,特制定此管理规定。
2. 范围适用于公司所有物料的试制,包括小批量试制与中批量试制。
3. 定义物料试产:分为小批量与中批量试产,原则上结构件、包材类、阻容件、电子标准件等只进行小批量试产。
安全件、关键件应进行小批量试产后再中批量试产。
4. 职责4.1 工程部:负责所有物料《试制单》的填写、负责提出物料试产的要求、负责主导与跟进新物料试产全过程、问题点统计分析与改善、参与试产评审。
4.2 采购部:负责小批量试产、中批量试产物料的采购,并参与试产评审。
4.3 物控部:负责小批量试产、中批量试产生产安排。
并参与试产评审。
4.4 品管部:负责小批量试产、中批量试产物料的检验、试验验证、并参与试产评审。
5. 作业内容5.1 新物料小批量试产5.1.1 工程部确定供应商所送样品为合格后,认为有必要进行小批量试产时,工程部负责开出试制单及相关试制条件及要求。
5.1.2 小批量试产物料到仓库后,IQC依据《来料检验规范》实施抽样检验判定、及不合格处理等。
5.1.3 物控部安排生产部进行试产。
5.1.4 生产部按照生产计划安排在要求机型上来试制,问题点记录在《试制单》上。
5.1.5 品质部对试产进行检验/试验验证,并做好检验/试验记录在《试制单》上。
5.1.6 工程部全程跟踪试产整个过程,对生产部提供技术支持,试产不良问题点进行原因分析。
5.1.7 针对试产问题点,由工程部进行汇总与统计,并进行分析与提出改善方案。
5.1.8 小批量试产后,由管理者代表裁决试产结论;若试产不通过时,决定是否继续小批量试产或者更换新供应商物料,并依5.1条款来执行。
品质部IQC 将试产结果扫描发放到相关部门。
5.2 物料中批量试产5.2.1物料小批量试产完成后,由采购部下中批量试产订单。
5.2.2中批量试产物料到仓库后,IQC依据《来料检验规范》实施抽样检验判定、及不合格处理等。
试产物料的跟踪流程
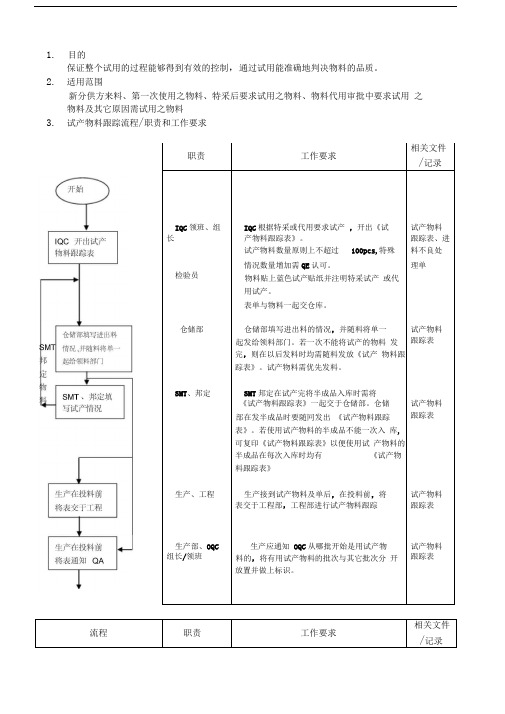
1.目的保证整个试用的过程能够得到有效的控制,通过试用能准确地判决物料的品质。
2.适用范围新分供方来料、第一次使用之物料、特采后要求试用之物料、物料代用审批中要求试用之物料及其它原因需试用之物料3.试产物料跟踪流程/职责和工作要求职责工作要求相关文件/记录IQC领班、组IQC根据特采或代用要求试产,开出《试试产物料长产物料跟踪表》。
跟踪表、进试产物料数量原则上不超过100pcs,特殊料不良处情况数量增加需QE认可。
理单检验员物料贴上蓝色试产贴纸并注明特采试产或代用试产。
表单与物料一起交仓库。
仓储部仓储部填写进出料的情况,并随料将单一试产物料起发给领料部门。
若一次不能将试产的物料发完,则在以后发料时均需随料发放《试产物料跟踪表》。
试产物料需优先发料。
跟踪表SMT、邦定SMT邦定在试产完将半成品入库时需将《试产物料跟踪表》一起交于仓储部。
仓储试产物料部在发半成品时要随冋发出《试产物料跟踪表》。
若使用试产物料的半成品不能一次入库,可复印《试产物料跟踪表》以便使用试产物料的半成品在每次入库时均有《试产物料跟踪表》跟踪表生产、工程生产接到试产物料及单后,在投料前,将试产物料表交于工程部,工程部进行试产物料跟踪跟踪表生产部、OQC生产应通知OQC从哪批开始是用试产物试产物料组长/领班料的,将有用试产物料的批次与其它批次分开放置并做上标识。
跟踪表流程职责工作要求相关文件/记录O QC在整机检查时,要针对该物料在整机情况,有目的地进行检验,产OQC检验员品QE确认并填写意见。
物料QE 物料QE根据各部的试产情况,最终判定试产合格与否IQC 试产结束后返单至IQC试产不合格退料,合格允收编制:审核:批准:。
试产物料的跟踪流程

试产物料的跟踪流程试产是产品开发流程中一个重要的环节,而物料准备是试产过程中必不可少的一环。
为了确保试产过程的顺利进行,需要建立一套完善的物料跟踪流程。
本文将介绍试产物料跟踪流程的具体步骤及注意事项。
一、物料需求确认在试产前,需要进行物料需求确认,明确所需物料及数量。
通常可以通过以下途径获取物料需求信息:1. 产品设计部门提供的物料清单;2. 试产工程师根据产品的工艺流程及工作指导书确定所需物料;3. 研发部门提供的样品及样品测试报告。
二、物料采购与供应商选择在确定物料需求后,需要进行物料采购。
具体采购流程如下:1. 制定采购方案:根据物料需求与供应商信息,制定采购方案,包括采购数量、价格等;2. 筛选供应商:根据供应商的综合评估,选择符合要求的供应商,并与其达成合作意向;3. 签订采购合同:与供应商签订采购合同,明确双方的权利和义务;4. 物料采购:按照合同要求,采购所需物料;5. 物料入库:将采购的物料按照标准存放到仓库中。
三、物料领取与发放试产过程中,试产工程师需要按照实际需求领取物料,以确保试产工序的顺利进行。
物料领取与发放的具体步骤如下:1. 试产工程师填写物料领用申请单:包括领用物料的名称、规格、数量等信息;2. 申请单审批:相关部门对物料领用申请单进行审批,并确认申请单的真实性与合理性;3. 领料:经过审批的物料领用申请单交给仓库管理员,仓库管理员根据申请单领取相应的物料,并进行登记;4. 物料发放:试产工程师携带领取的物料进行试产,确保物料的正确使用。
四、物料消耗与追踪试产过程中,需要对物料的消耗情况进行追踪,以确保物料的合理利用。
具体步骤如下:1. 物料消耗记录:试产工程师在试产过程中需记录物料的消耗情况,包括数量、时间、位置等信息;2. 物料追踪:通过对物料消耗记录的统计与分析,追踪物料的使用情况,及时进行补充与调整;3. 物料报废处理:对于损坏、过期或其他不能继续使用的物料,需进行报废处理,并记录相关信息。
物料特采作业流程

物料特采作业流程一、物料特采作业流程步骤:1.需求确认:项目经理或相关部门通过需求确认,确定需要特别采购的物料的具体信息,包括物料名称、规格、数量等。
2.供应商选择:采购部门根据需求确认的信息,对市场上的供应商进行调研和评估,选出几家具备特采物料供应能力和实力的供应商。
3.技术评审:项目管理团队、采购部门和相关技术人员组成评审小组,对供应商的技术能力进行评审,确定是否符合项目需求。
4.商务谈判:采购部门与供应商进行商务谈判,包括物料价格、交货期、售后服务等方面的内容。
确保价格合理、交货期可行、服务到位。
5.合同签订:商务谈判达成一致后,采购部门与供应商签订正式合同,明确各项约定事项。
6.收货验收:物料到货后,采购部门组织相关人员进行收货验收,检查物料是否符合合同要求,数量是否正确,质量是否合格。
7.入库处理:验收合格的物料进行入库处理,库存管理部门负责对物料进行登记、整理和储存,确保物料的安全性和完整性。
8.付款处理:根据合同约定的付款方式和时间,财务部门进行付款处理,并及时与供应商沟通确认付款事宜。
9.跟踪反馈:采购部门对特采物料的使用情况进行跟踪和反馈,在项目执行过程中及时调整特采物料的采购计划,保证项目的正常进行。
二、物料特采作业流程责任人:1.项目经理:确认特采物料的需求,协调各个部门之间的沟通和合作,确保特采物料的及时交付和使用。
2.采购部门:负责对特采物料进行市场调研和供应商选择,与供应商进行商务谈判,签订合同,并组织物料的收货验收和入库处理。
3.技术人员:参与供应商的技术评审,对特采物料的技术能力进行评估,确保符合项目需求。
4.供应商:根据采购部门的需求,提供合格的特采物料,按时交货,并提供相关的售后服务。
5.财务部门:根据合同约定的付款方式和时间,进行付款处理,并与供应商确认付款事宜。
三、物料特采作业流程注意事项:1.需求确认时,应尽量明确和详细,确保采购部门了解项目的具体需求。
采购急料追踪流程

How totrace urgent parts
7-1、缺原材料。如果缺原材料,缺什么原材料,该原材 料哪家生产,他们的联系方式是什么?打电话给生产该原 材料供厂商,以便求正其真实性并依实际情况给以协助解 决 Lacking raw material, if the vendor is short of raw material, we must know short material item , which can be produced and the vendor’s telephone .so we could prove whether the vendor’s words ture or not and supply the constructive suggestion in time 7-2、供货商产能满载,无法安排上线。 The vendor’s capacity is too full to arrange for production. 7-3、模具、治具等设备坏掉,要告知我们其对策是什么? 多长时间可以恢复生产。 Such as tooling, functure are out of work ,we have to know their tactics and when they can be restored to formal/production.
How totrace urgent parts
5、供货商出货后,每隔半小时打电话给送货司机询问其 行程进度,一直跟踪到货物抵达我司。 After the track is shipped, we must make a telephone to the driver at an half hour so that we make sure when the track can arrive at the company. 6、物料运送之我司后,立即通知仓库,品管,告知该批 料为急料,请其快速做帐,检验,一直跟踪到良品入库。 When we receive the goods ,we will notice the warehouse keeper ,quality control department to deal with relative question at once . The buyer will make the goods go into good warehouse . 7、如果供货商不能按期交货,要问清楚不能按期交货之 详细原因。如: If the vendor can’t meet our schedule, we must understand which causes have bad effected on the delivery time.
仓库物料采购、跟进、保管、出入库流程

仓库物料采购、跟进、保管、出入库流程制度目的:为规范仓库物料管理,确保工作顺利开展。
使用范围:物料管理相关部门职责:仓管员负责物料的收货、入库、发货、退货处理、储存、防护工作;物近专员每季度给出库存处理方案(即消耗库存方案);各岗位人员需细心(严谨)、负责、诚实、团结互勉的工作态度和作风。
全文目录一、物料采购下单 (2)二、物料摆放 (3)1、分类 (3)2、标签 (3)三、物料出库 (3)四、物料跟进 (4)五、物料盘点 (4)六、出入登帐 (4)七、保管与出入库制度 (5)1、物料保管管理制度 (5)2、物料领发管理制度 (5)3、物料退库管理制度 (5)一、物料采购下单1、对接人:行政采购、供应商笔记本、奖牌、笔、服装、合同外壳2、流程及说明流程说明二、物料摆放1、分类①大仓库小件物品:办公用品、药品、会议活动物品、会议人员物料需求区分三区:常用区、会议区、会议人员需求区②办公室大件物品:易拉宝、背景、服装、存放物料准备物品2、标签每个货价标上物品名称及序号(为方便查找物料,注意物料明细表的序号以仓库摆放填写)三、物料出库1、流程及说明流程说明2、表格(出库单外地、本地)四、物料跟进1、流程及说明流程说明2、表格(出库单外地)五、物料盘点盘点时间:1、每月15、30日大盘点;2、会议结束2天内根据“出库单”领取的数量,清点“非易品”数量,确认数量同领取一致,如有出入,需查明原因补上;(领取人为第一责任人)盘点方式:①实物盘点②供应商、行政仓库核对库存数、实物六、出入登帐日常:物料一旦出入库当天需将数量登记帐本;结帐:每月15、30日结总帐注:通过每月15、30日结总帐特别关注需长周期制作的物料库存数是否能满足会议,做好及时补料的准备;七、保管与出入库制度1、物料保管管理制度1.1 物料入库后,需按不同类别、性能、特点和用途分类分区码放,做到"二齐、三清、四号定位";a)二齐:物资摆放整齐、库容干净整齐。
试制产品跟踪流程

6. 产品下线后,最后一道工序员工必须检验产品状态、标识等,隔离 存放,并挂上成品标识牌;
7. 班组长确认试制产品完工无误, 与其他班组接收人员对接后移交产 品。
相关考核:
2. 小班长负责试制产品的物料接收、出库工作,试制产品在其管辖的 线体内负责全程跟踪、隔离;
3. 操作人员负责按照试制工艺要求加工,对试制产品做标识,完工成 品必须隔离保存。
基本流程:
1. 班组长接收到通知单后,先与技术主管、试制相关人员对接信息; 其次与生产主管对接生产时间、避免影响正常生产,最后将全部信息传达给小班 长及员工;
2. 小班长与焊接线、物料部对接试制物料,接收前必须验证数量、状 态、标识等无误后方可接收;接收后按照生产时间安排人员加工;
3. 员工必须按照班组长的安排和试制工艺要求加工,严禁私自更改工 艺参数、加工尺寸。
4. 试制加工过程出现不合格品、加工问题时,必须汇报给班组长,班 组长负责记录信息、隔离不合格件、处理问题等。
***系统有限公司
*** System Co.,Ltd.
关于新状态、试制产品的跟踪要求
目的:
为了较好的配合公司的产品试制工作、新产品的生产过程控制等;特在机 加工班组制定此要求,在本班组范围内全员必须执行试制产品所涉及的各项跟踪 要求。
相关人员:
对每次新产品试制的负责人员
职责要求:
1. 大班长负责接收各类技术通知单、试制通知单等,与试制项目的相 关人员对接生产要求,试制信息传递;反馈、处理试制过程中的问题等;
1. 产品试制过程中因大班长信息传达错误,加工过程产生的相关问题, 大班长负主要责任,由上级主管或部门对其考核。
物料采购及进仓的跟踪流程

物料采购及进仓的跟踪流程物料采购及进仓的跟踪流程物料采购及物料进仓跟踪是跟单员的工作之一,下面整理了关于物料采购及进仓的跟踪流程,希望对大家有所帮助!一、釆购跟单的基本要求:适当的交货时间,适当的交货质量,适当的交货地点,适当的交货数量及适当的交货价格。
(适时,适质,适地,适量,适价)二、物料采购跟单的原因:以下原因造成我们要对物料进行跟催:(1)供应商方面的'原因:由于供应商方而的原因造成交货不及时, 而使我们必须跟单的原因有:超过产能的接单和超过技术水准的接单。
制程管理不良,质量管理不充分而造成不良品的增多。
来自低工资的员工工作效率低,完不成。
等原因。
(2)企业方面的原因:供应商的选定有误,对他的产能和技术调查不足。
所要求的品质没说清楚。
价格的决定很勉强。
进度的掌握和督促不力。
下订单到过远的地方。
(3)沟通方面的原因:信息交换不及时。
三、物料采购跟单流程:(1)制作订购单跟单员接到所需部门的请购单,要制成订购单传给供应商。
制订购单时注意:审查请购单。
熟悉订购的物料,价格确认,确认质量标准。
确认物料需求量,制定订单说明书,发出订购单。
(制作采购单P。
26),将要采购的物料名称,规格型号,数量,价格。
交期等要求表达清楚。
采购单经审核无误后发给供应商,并要求供应商签字回传。
(2)订单跟踪对长期合作的,信誉好的供应商可以不进行跟踪。
跟踪加工工艺,跟踪原材料,跟踪加工过程,跟踪组装总测,跟踪包装入库。
(3)物料检验确定检验日期,通知检验人员,进行物料检验,处理检验问题(4)物料进仓协调送货,协调接受,通知送货,物料入库, 处理接受问题四、物料釆购跟单的方法策略:催单的目的是使供应商在必要的时候送达所采购的物料,使企业的经营成本降低。
催单的方法:(1)按订单跟催。
按订单预定的进料日期提前一定时间进行跟催。
联单法:将订购单按日期顺序排列好,提前一定时间进行跟催。
统计法:将订购单统计成报表,提前一定时间进行跟催。
特采原材料标识和追溯程序(含表格)
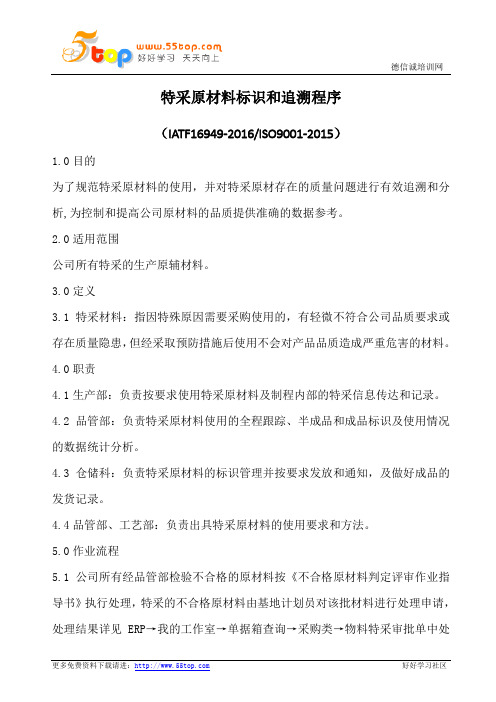
特采原材料标识和追溯程序(IATF16949-2016/ISO9001-2015)1.0目的为了规范特采原材料的使用,并对特采原材存在的质量问题进行有效追溯和分析,为控制和提高公司原材料的品质提供准确的数据参考。
2.0适用范围公司所有特采的生产原辅材料。
3.0定义3.1特采材料:指因特殊原因需要采购使用的,有轻微不符合公司品质要求或存在质量隐患,但经采取预防措施后使用不会对产品品质造成严重危害的材料。
4.0职责4.1生产部:负责按要求使用特采原材料及制程内部的特采信息传达和记录。
4.2品管部:负责特采原材料使用的全程跟踪、半成品和成品标识及使用情况的数据统计分析。
4.3仓储科:负责特采原材料的标识管理并按要求发放和通知,及做好成品的发货记录。
4.4品管部、工艺部:负责出具特采原材料的使用要求和方法。
5.0作业流程5.1公司所有经品管部检验不合格的原材料按《不合格原材料判定评审作业指导书》执行处理,特采的不合格原材料由基地计划员对该批材料进行处理申请,处理结果详见ERP→我的工作室→单据箱查询→采购类→物料特采审批单中处理结果。
5.2仓库依据《物料特采审批单》的结果对不合格物料作好特采、退货标识并定点摆放,特采标识单上须注明该批材料的特采编号及特采原因,以便追溯。
5.3仓库在发放特采原材料时必须在物料上贴上特采单或在生产部领用单上注明该批材料的特采编号并在首次发放时知会品管部跟踪,避免生产线混用。
5.4生产部领料员领用原材料时,要求必须将所领用的材料作好标识,并将特采材料分开存放。
车间人员严格按照标识单来使用材料并作好记录,并且每次领用到车间后通知生产班组和IPQC进行使用跟踪指导,并在领用单上签字确认。
5.5生产部在使用特采原材料时,须严格按照品管部和工艺部提出的使用要求进行生产,并要求分开使用及在生产各工序物料使用记录上注明特采编号,生产的半成品、成品需与其它全合格材料的产品分开码放标识,禁止出现合格与特采材料混用和产品码放混乱导致无法追溯的现象。
特采物料的使用流程

特采物料的使用流程1. 特采物料的定义特采物料是指在正常的物料采购流程之外进行的物料采购活动,通常是由于紧急需求、特殊规格或其他特殊原因导致的物料采购。
2. 特采物料的使用流程步骤一:提出特采申请1.确定特采物料的具体需求和目的。
2.在采购部门或相关部门内部填写特采申请表,并注明特采物料名称、规格、数量、用途等信息。
3.将特采申请表提交给审批人员进行审批。
步骤二:审批特采申请1.审批人员对特采申请进行评估,并根据特采物料的紧急程度和重要性进行优先级排序。
2.审批人员将特采申请表交给负责特采物料采购的部门或人员。
步骤三:寻找供应商1.负责特采物料采购的部门或人员根据特采申请表上的物料需求信息,寻找适合的供应商。
2.与供应商沟通,获取特采物料的报价和交货时间等信息。
3.对供应商进行评估,选择最合适的供应商进行物料采购。
步骤四:签订采购合同1.在选择好供应商后,采购部门或相关部门与供应商签订采购合同。
2.采购合同中应明确特采物料的名称、规格、数量、价格、交货时间等重要信息,并约定双方的权益和责任。
步骤五:物料采购与交付1.物料采购部门或相关部门按照合同约定的时间和数量要求与供应商进行物料的采购。
2.物料采购完成后,采购部门或相关部门应进行验收,确保所收到的物料与采购合同中的要求一致。
3.物料验收合格后,将物料交付给使用部门或相关部门。
步骤六:特采物料的使用1.使用部门或相关部门根据特采物料的要求和用途,合理使用特采物料。
2.使用部门或相关部门应及时向采购部门反馈特采物料的使用情况,以便采购部门进行后续跟踪和管理。
3. 特采物料使用注意事项•特采物料的使用应遵守公司的相关规定和流程。
•特采物料的使用应合理,避免浪费和过度使用。
•特采物料的使用过程中如有问题或质量异常,应及时向采购部门报告并要求供应商解决。
特采物料的使用流程是一项复杂但必要的工作,通过合理的流程和严格的执行,可以确保特采物料的采购和使用符合需求和规范,最大程度地满足特殊情况下的物料需求。
- 1、下载文档前请自行甄别文档内容的完整性,平台不提供额外的编辑、内容补充、找答案等附加服务。
- 2、"仅部分预览"的文档,不可在线预览部分如存在完整性等问题,可反馈申请退款(可完整预览的文档不适用该条件!)。
- 3、如文档侵犯您的权益,请联系客服反馈,我们会尽快为您处理(人工客服工作时间:9:00-18:30)。
特采/试制物料跟踪流程
1.目的:
为规范公司特采以及小批试制物料的跟踪方式,使得特采/小批试制物料的数量、位置、状态、使用性能以及最终评价结果等信息流畅,相关的记录准确完善,制定此流程。
2.定义:
2.1特采:是指物料等不符合品质规格,但为了使生产不陷于停顿或遭受更大的经济损失,在影响
品质不大的范围内,限定条件(数量、期限)而进行的允收。
2.2小批试制:本流程中的小批试制主要是指原材料经过小批量生产加工,成为半成品的过程。
3.职责
3.1品保部负责判定物料质量状态并做相应标识,跟踪上线物料的使用特性,反馈验证结果并对物
料做出最终评价;
3.2生管部负责组织物料评审,安排特采/小批试制物料的生产计划,在领料单上备注特采信息;
3.3技术/研发部负责提供特采物料返工或特殊使用方案,明确特采或小批试制物料的跟踪项,并
提供特采或小批试制物料使用产生的不合格品的处理意见。
3.4制造部负责按照生产计划和技术方案进行生产,并隔离特采/小批试制物料与普通物料。
4.内容
4.1品保部IQC根据《报检单》的物料进行检验,并开具《来料检验报告》;
4.2生管部计划员负责组织对《来料检验报告》中不合格的物料进行评审,并填写《物料/产品评
审报告》,并将物料评审结果发给总经办、生管部、技术部、品保部、信息部、采购部等部门和相关负责人。
4.3品保部IQC负责根据评审结果,对仓库的物料做相应标识(特采、选别、退货等)。
标识工作
应在评审结果公布后的24小时之内完成。
4.4研发/技术部相关负责人在评审结果公布后24小时内,填写《特采/小批物料试制报告》,说明
跟踪项目,提供特采/小批试制物料的特殊使用方案,并将报告通过公司邮箱发给生管部。
4.5生管部计划员收到《特采/小批物料试制报告》后,根据人员、工装、设备等情况安排特采/小
批试制物料的生产计划。
原则上计划中给出的上线时间,应在评审报告公布后一周之内。
计划员填写《特采/小批物料试制报告》中生产订单、生产日期、工作中心、生产批号、生产数量等信息后,将该报告通过公司邮箱发给生管部仓库主管、制作部相关产线主管和品保部IPQC
主管。
在《生产计划单》备注栏注明“使用特采物料,物料名称:xxxxxxxx,物料规格:xxxxxxxx,供应商:xxxxxxxx,批号:xxxxxxx”,并发放给生管仓库、制造部、品保部等部门。
4.6部门主管对《特采/小批物料试制报告》的处理。
4.6.1制造部主管收到《特采/小批物料试制报告》后,及时打印纸质版交给产线班长,并交代生
产过程中的注意事项,准备该特采/小批试制物料的生产条件。
4.6.2品保部主管收到电子版《特采/小批物料试制报告》后,必须在特采/小批物料生产前一天将
其打印并交给IPQC,同时交代跟踪事项。
4.6.3仓库主管接到《特采/小批物料试制报告》后负责对配料员进行提醒。
4.7产线班长、配料员、IPQC执行程序
4.7.1制造部产线班长根据该特采/小批试制物料的《生产计划单》打印领料单,并注明物料信息。
4.7.2生管部配料员根据领料单上信息发放特采/小批试制物料。
4.7.3产线班长负责组织操作者按照技术/研发部给出的特采物料使用方案进行生产。
4.7.4品保部IPQC依照《特采/小批物料试制报告》,对技术/研发部给出的跟踪项进行跟踪,并填
写其中的质量状态项。
4.8特采/小批物料试制结束后,品保IPQC主管根据小批产品填写《物料/产品评审报告》中的跟
踪验证项,交品保部经理,决定特采/小批物料的最终处理意见。
5.相关记录
5.1《来料检验报告》
5.2《物料/产品评审报告》
5.3《特采/小批物料试制报告》。