铝镁合金设计要点
运载装备轻量化用铝、镁合金高效设计制造关键技术与产业化应用

运载装备轻量化用铝、镁合金高效设计制造关键技术与产业化应用1.引言概述部分的内容可以写成以下样式:1.1 概述近年来,随着工业技术的不断发展和运输需求的不断增加,轻量化设计制造成为了装备制造行业的热点话题。
轻量化装备能够有效减轻运载装备的重量,提高装备的性能和效率,同时降低能源消耗,减少环境污染,因此备受各个行业的青睐。
在轻量化设计制造中,铝合金和镁合金作为重要的材料成为了研究的重点。
铝合金具有优异的力学性能和良好的加工性能,而镁合金则具有较低的密度和较高的强度。
因此,研究和发展铝、镁合金的高效设计制造关键技术对于实现装备的轻量化具有重要的意义。
本文旨在系统总结铝、镁合金在运载装备轻量化设计制造中的关键技术,并探讨其产业化应用情况,以期为相关领域的研究提供参考。
在接下来的章节中,我们将分别介绍铝合金轻量化设计制造技术和镁合金轻量化设计制造技术的研究进展和应用情况,并对其发展趋势进行展望。
通过本文的阅读,读者可以了解到铝、镁合金在轻量化设计制造领域的应用前景和挑战,并为相关产业的发展提供技术支持和指导,推动装备制造行业向着更加高效、环保的方向发展。
文章结构部分主要介绍文章的整体框架和组织结构,下面是1.2文章结构部分的一个示例内容:1.2 文章结构本文将按照以下结构进行组织和呈现:第一部分为引言,主要对本文的主题进行概述,介绍运载装备轻量化用铝、镁合金高效设计制造关键技术与产业化应用的背景和意义。
此外,我们还会介绍本文的目的和论述方法。
第二部分为正文,主要分为两个章节,分别介绍铝合金轻量化设计制造技术和镁合金轻量化设计制造技术。
对于每种合金材料,我们将详细探讨其在运载装备轻量化方面的关键技术,包括材料性能特点、设计原则、制造工艺等。
同时,我们还将介绍相关技术的研究现状和进展,并提供一些具体的案例分析以便读者更好地理解和应用这些技术。
第三部分为结论,主要对本文进行总结,并展望运载装备轻量化用铝、镁合金高效设计制造关键技术与产业化应用的发展前景。
镁铝合金外观件之设计规范
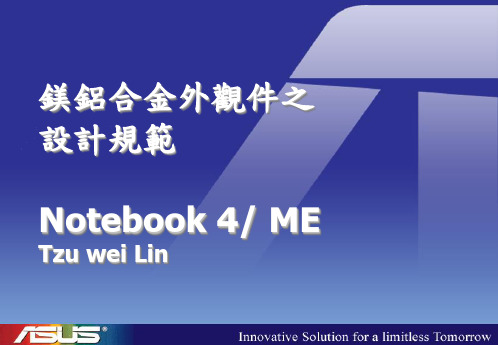
外觀
鎂鋁合金在噴漆,外觀修補痕跡,缺陷 等方面,均不同於一般塑膠及鈑金件, 宜另定新的外觀檢驗標準。
ห้องสมุดไป่ตู้
材料 1/2
一般使用的材料為AZ-91D,其成份及特性如下:
Magniesium Aluminum Zinc Manganese Iron Silicon Copper Nickel 90% 8.3~9.7% 0.35~1.0 % 0.15~0.5 % 0.005 % 0.10 % max 0.03 % max 0.002 % max
文字圖案: 成品文字圖案凹陷較不可行(除非線條寬度很大),以击起為可行 ,線條寬度b,線條高度h。 b≧0.5 mm h≦0.3 mm 但對表面烤漆件,為避免外觀不良無法處理,以印刷為宜。 考量模具壽命,不要設計公模斜梢之undercut,若無法避免,必須 以機械加工處理。 外滑塊可行,但拆模須延伸至Parting Line(隧道式滑塊不可行 )。 Rib 根部以R角與基材連接,可幫助充填及避免應力集中現象,一 般以R0.5~R2 為佳。Rib 寬度最小值小件如手機和PDA 應在0.6 mm 以上,大件如投影機和Notebook 應在0.8 mm以上,防止充填成形 不良。
Lead time
鎂鋁合金生產不同於一般流程,一般而 言,而壓鑄成品,設計階段約10~14 天(加工治具Ready 的狀況下),量產則 需2~3 週,必須對庫存做良好的控制, EC 亦需慎重。
修模
鎂鋁合金模具硬度較高,經焊補修模後 ,大大降低模具壽命(一般約10 萬模), 設計變更應儘量減少焊補部份。
5~10% 10~15% 10~20% 15~20% 10% 30~40%
鎂鋁合金件在開發過程的重點
設計 / 試模階段:
镁合金压铸产品设计要点

镁合金压铸产品设计要求1、尺寸公差要求
4、散热齿高度、厚度及拔模斜度等要求
此项指标与铝合金相比,同等尺寸下,高度可以稍高一点、厚度薄一些、拔模斜度稍小一点可行,若按原铝合金设计生产镁没有问题。
5、凸台/凹槽要求
这些没有特殊要求,主要根据产品结构而定,按铝合金设计可以再优化一点。
6、后面机加需留的余量
加工余量根据产品结构和精度要求而定,一般留0.5mm左右即可。
7、其他与铝合金压铸产品不同,设计上需要注意的地方
从制造工艺上来讲,铝合金生产时需用水来冷却,镁合金需加热,贵司产品结构设计考虑功能要求,有点问题我们可以从工艺上进行改良。
铝型材设计要点
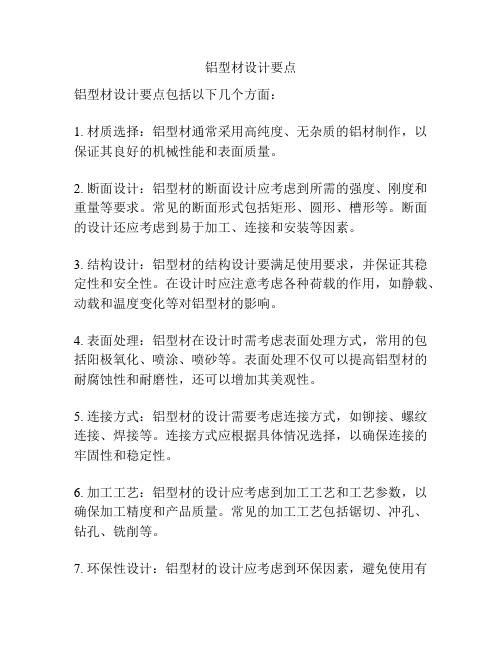
铝型材设计要点
铝型材设计要点包括以下几个方面:
1. 材质选择:铝型材通常采用高纯度、无杂质的铝材制作,以保证其良好的机械性能和表面质量。
2. 断面设计:铝型材的断面设计应考虑到所需的强度、刚度和重量等要求。
常见的断面形式包括矩形、圆形、槽形等。
断面的设计还应考虑到易于加工、连接和安装等因素。
3. 结构设计:铝型材的结构设计要满足使用要求,并保证其稳定性和安全性。
在设计时应注意考虑各种荷载的作用,如静载、动载和温度变化等对铝型材的影响。
4. 表面处理:铝型材在设计时需考虑表面处理方式,常用的包括阳极氧化、喷涂、喷砂等。
表面处理不仅可以提高铝型材的耐腐蚀性和耐磨性,还可以增加其美观性。
5. 连接方式:铝型材的设计需要考虑连接方式,如铆接、螺纹连接、焊接等。
连接方式应根据具体情况选择,以确保连接的牢固性和稳定性。
6. 加工工艺:铝型材的设计应考虑到加工工艺和工艺参数,以确保加工精度和产品质量。
常见的加工工艺包括锯切、冲孔、钻孔、铣削等。
7. 环保性设计:铝型材的设计应考虑到环保因素,避免使用有
害物质,如铅、汞等。
同时,设计还应考虑到铝型材的可回收性和可再利用性。
以上是铝型材设计的一些要点,设计过程中还需结合具体应用环境和要求进行综合考虑。
铝镁合金材料的特性分析及加工工艺研究

铝镁合金材料的特性分析及加工工艺研究铝镁合金是一种广泛应用于制造航空、汽车、电子和建筑等领域的高性能金属材料。
在铝镁合金中,铝是基体,镁是强化相,两者的共同作用使其拥有优异的机械性能、导电性能和抗腐蚀性能,并具有重量轻、强度高的优点。
本文将从铝镁合金材料的特性和加工工艺两方面进行探讨。
一、铝镁合金的特性1、机械性能铝镁合金的强度比普通铝合金高出很多,弹性模量也比较高。
这使得它可以满足在高温、高压等恶劣环境下所需的机械性能要求。
同时,它的韧性也比较好,不易出现脆性断裂。
2、导电性能铝镁合金具有很好的导电性能,可以广泛应用于电子工业。
在电子元器件的制造中,铝镁合金作为电路板的基底材料,能够有效提高电路板的导热性能和机械性能,从而提高整个电子设备的工作稳定性。
3、抗腐蚀性能铝镁合金的抗腐蚀性能也非常出色。
随着氧化膜的形成,其表面会形成一层坚固的氧化膜,具有很好的防腐蚀性能,可以在某些恶劣环境下长期使用。
4、重量轻相比于普通的钢材,铝镁合金的密度更小,重量更轻。
这使得使用铝镁合金可以有效降低产品的自重,节约能源,从而实现制造轻量化工业。
二、铝镁合金的加工工艺1、挤压加工挤压是铝镁合金加工中比较常用的一种工艺。
它可以有效地制造出长条状或复杂形状的产品。
在挤压过程中,铝镁合金经过高温加热,然后通过模具挤出成型。
挤压可以实现批量生产,并且生产的产品质量稳定,表面光滑,尺寸精度高。
2、铸造加工铸造是另一种常用的铝镁合金加工工艺。
它可以通过铸造模具,将铝镁合金熔融后倾入模具内进行凝固形成。
铸造加工具有生产效率高、成本低、适用于大件生产等特点,是制造大型零件或精密零件时常用的工艺。
3、冷变形加工冷变形加工是通过对铝镁合金进行冷加工,从而改善材料性能。
常见的冷变形加工工艺包括冷轧、冷拔和冷挤压。
由于冷变形加工可以改善铝镁合金的力学性能、表面结构和织构特性,因此在某些场合下,这可以是最好的选择。
以上几种铝镁合金加工工艺虽然各有优缺点,但在实际应用中,却是互相补充。
设计铝合金与镁合金铸件结构应注意的八个基本事项
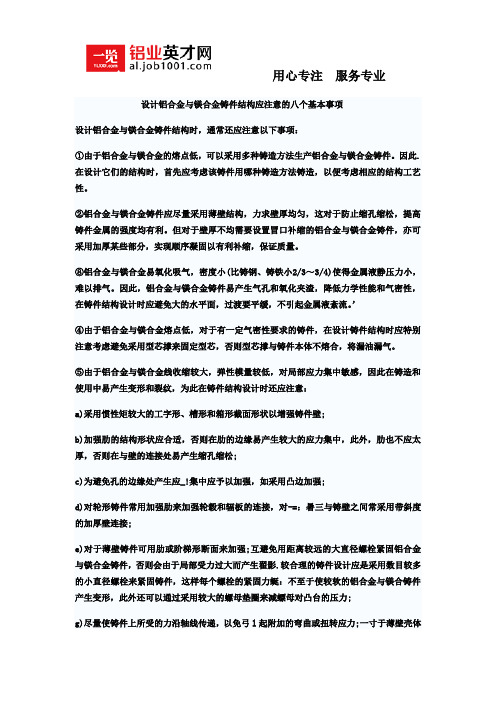
设计铝合金与镁合金铸件结构应注意的八个基本事项设计铝合金与镁合金铸件结构时,通常还应注意以下事项:①由于铝合金与镁合金的熔点低,可以采用多种铸造方法生产铝合金与镁合金铸件。
因此.在设计它们的结构时,首先应考虑该铸件用哪种铸造方法铸造,以便考虑相应的结构工艺性。
②铝合金与镁合金铸件应尽量采用薄壁结构,力求壁厚均匀,这对于防止缩孔缩松,提高铸件金属的强度均有利。
但对于壁厚不均需要设置冒口补缩的铝合金与镁合金铸件,亦可采用加厚某些部分,实现顺序凝固以有利补缩,保证质量。
⑧铝合金与镁合金易氧化吸气,密度小(比铸钢、铸铁小2/3~3/4)使得金属液静压力小,难以排气。
因此,铝合金与镁合金铸件易产生气孔和氧化夹渣,降低力学性能和气密性,在铸件结构设计时应避免大的水平面,过渡要平缓,不引起金属液紊流。
’④由于铝合金与镁合金熔点低,对于有一定气密性要求的铸件,在设计铸件结构时应特别注意考虑避免采用型芯撑来固定型芯,否则型芯撑与铸件本体不熔合,将漏油漏气。
⑤由于铝合金与镁合金线收缩较大,弹性模量较低,对局部应力集中敏感,因此在铸造和使用中易产生变形和裂纹,为此在铸件结构设计时还应注意:a)采用惯性矩较大的工字形、槽形和箱形截面形状以增强铸件壁;b)加强肋的结构形状应合适,否则在肋的边缘易产生较大的应力集中,此外,肋也不应太厚,否则在与壁的连接处易产生缩孔缩松;c)为避免孔的边缘处产生应_!集中应予以加强,如采用凸边加强;d)对轮形铸件常用加强肋来加强轮毂和辐板的连接,对-=:暑三与铸壁之间常采用带斜度的加厚壁连接;e)对于薄壁铸件可用肋或阶梯形断面来加强;互避免用距离较远的大直径螺栓紧固铝合金与镁合金铸件,否则会由于局部受力过大而产生翟影.较合理的铸件设计应是采用数目较多的小直径螺栓来紧固铸件,这样每个螺栓的紧固力蜒:不至于使较软的铝合金与镁合铸件产生变形,此外还可以通过采用较大的螺母垫圈来减螵母对凸台的压力;g)尽量使铸件上所受的力沿轴线传递,以免弓l起附加的弯曲或扭转应力;一寸于薄壁壳体形的铝合金与镁合金铸件,不应具有突变的外形;i)由于铝合金与镁合金的弹r^竺囔量小易变形,因此对于有压配合关系的铝合金与镁合金铸件,在设计铸件结构时必须考虑,至j变形和多次拆装后产生的间隙,同理,铝合金与镁合金铸件上的螺纹孔应比铸铁件和铸钢件孵嗓纹孔适当加长,对于铝合金铸件取L(长度)脑(直径)一2,对于镁合金铸件取L/d:2.5。
铝镁合金管型母线结构

铝镁合金管型母线结构一、引言铝镁合金管型母线是一种电力传输和分配装置,广泛应用于电力系统中。
它由铝镁合金管和连接件组成,具有轻质、高强度、导电性好等特点,适用于高压、大电流的输电和配电场合。
本文将从材料特性、结构设计、应用领域等方面介绍铝镁合金管型母线的相关知识。
二、材料特性1. 铝镁合金管铝镁合金是一种由铝和镁组成的合金材料。
铝具有良好的导电性和导热性,而镁具有较低的密度和良好的机械性能。
铝镁合金管采用该材料制成,具有轻质、高强度、耐腐蚀等特点,适用于长距离输电和分配电流较大的场合。
2. 连接件连接件是将铝镁合金管连接成母线系统的重要组成部分。
常见的连接件有接头、接箍、接线夹等。
这些连接件采用高强度的材料制成,能够确保母线系统的稳定性和可靠性。
三、结构设计1. 母线管铝镁合金管型母线采用管状结构,能够有效降低电阻损耗和热损耗。
母线管的截面形状可以根据实际需求进行设计,常见的有圆形、方形和矩形等。
不同形状的母线管适用于不同的场合,可以满足不同的电流传输需求。
2. 连接方式铝镁合金管型母线的连接方式多样,常见的有焊接、螺栓连接和插接等。
这些连接方式具有连接牢固、电阻低、可靠性高等优点。
根据实际情况选择合适的连接方式,能够确保母线系统的稳定运行。
四、应用领域铝镁合金管型母线广泛应用于电力系统中的输电和配电场合。
具体应用领域包括:1. 高压输电线路铝镁合金管型母线适用于高压输电线路,能够承受较大的电流负荷,减少输电损耗,提高能源利用效率。
2. 变电站铝镁合金管型母线用于变电站的电流传输和分配,能够满足变电站对高强度、大电流的要求,确保电力系统的安全稳定运行。
3. 工业用电铝镁合金管型母线广泛应用于工业领域的电力供应系统,能够满足工业设备对大电流供电的需求,提高工业生产效率。
4. 建筑电力铝镁合金管型母线用于建筑领域的电力供应,能够满足建筑物对电力的稳定供应需求,确保建筑物内部各项设备的正常运行。
五、总结铝镁合金管型母线作为一种重要的电力传输和分配装置,具有轻质、高强度、导电性好等特点,广泛应用于电力系统中。
铝镁合金设计要点

镁压铸品尺寸公差 (2/9)
分模面公差: (ADCI-E2-65)(表3)
镁压铸品投影面积 320cm2以下 320cm2 ~650cm2 650cm2~1300cm2 1300cm2~2000cm2 公差量 (mm) ± 0.13 ± 0.20 ± 0.30 ± 0.40
浇,流道系统设计(8/10)
浇口与铸件接合之方式
端部充填:使熔汤容易往上充填,适用於深槽压铸件 使熔汤容易往上充填,
浇,流道系统设计(9/10)
浇口与铸件接合之方式
对合充填:适用於圆筒形压铸件
浇,流道系统设计(10/10)
浇口与铸件接合之方式
垫形充填:适用於平板压铸件及整缘容易要求铸件
模具分割面设定要因 (1/7)
圆角
当T1=最小壁厚时
当T型相交时,则R1=1~1.25 T1 型相交时, 当T2 > T1时,则R1=2/3( T1+T2) & R2=0~(R1+T2) 当十字或Y型相接时
当Θ=90°时,则 R1= T1 当Θ=45°时,则 R1= 0.7 T1 & R2= 1.5 T1 当Θ=30°时,则 R1= 0.5 T1 & R2= 2.5 T1
镁合金压铸件成品设计要点 (4/4)
拔模角(依ADAC建议)
一般拔模角 D = L / C ,θ = ( D / L ) / 0.01746 度 精级拔模角 D = 0.8( L / C ) , θ = (D / L) / 0.01746度
一般级拔模角所需C值 一般级拔模角所需 值 内表面(单边 单边)=7 内表面 单边 外表面(单边 单边)=14 外表面 单边 全部)=4.76 孔(全部 全部 精级拔模角所需C值 精级拔模角所需 值 内表面(单边 单边)=7.8 内表面 单边 外表面(单边 单边)=15.6 外表面 单边 全部)=5.3 孔(全部 全部
铝型材设计要点

铝型材设计要点1. 引言铝型材是一种广泛应用于建筑、工业和交通领域的重要材料。
其具有优异的性能,如轻质、高强度、耐腐蚀等,因此受到了广泛关注和应用。
在设计铝型材时,需要考虑多个因素,包括结构设计、制造工艺、表面处理等。
本文将介绍一些铝型材设计的要点,以帮助读者更好地理解和应用这一领域的知识。
2. 结构设计要点在进行铝型材的结构设计时,需要考虑以下几个方面:2.1 强度与刚度铝型材通常需要承受一定的载荷,在结构设计时需要确保其具有足够的强度和刚度。
这可以通过增加截面尺寸或改变截面形状来实现。
同时,还可以采用加强筋或腹板等方式来提高铝型材的承载能力。
2.2 连接方式在实际应用中,铝型材常常需要与其他部件进行连接。
因此,在结构设计时需要考虑连接方式。
常见的连接方式包括焊接、螺栓连接和槽口连接等。
选择合适的连接方式可以提高结构的稳定性和可靠性。
2.3 减震与防护铝型材在某些应用场景中需要具有减震和防护的功能。
例如,在交通工具中,铝型材可以用于制作车身结构,需要具有一定的减震能力以提高乘坐舒适度。
在建筑领域,铝型材也可以用于制作窗框等部件,需要具有一定的防护能力以抵御外部环境的影响。
3. 制造工艺要点在设计铝型材时,还需要考虑其制造工艺。
以下是一些制造工艺要点:3.1 挤压工艺挤压是制造铝型材最常用的工艺之一。
在挤压过程中,通过将铝料加热至可塑状态后,通过挤压机将其挤出所需形状的模具中。
在设计时需要考虑到挤压过程中可能出现的变形和缩孔等问题,并采取相应措施进行预防或修复。
3.2 热处理工艺为了改善铝型材的性能,常常需要进行热处理。
热处理可以通过调节铝型材的组织结构来改变其性能。
常见的热处理方法包括固溶处理、时效处理等。
在设计时需要考虑到热处理对铝型材形状和尺寸的影响,并进行相应的设计调整。
3.3 表面处理工艺铝型材在使用过程中需要具有一定的耐腐蚀性和装饰性。
为了实现这些要求,常常需要对铝型材进行表面处理。
镁铝合金表面处理工艺设计大全
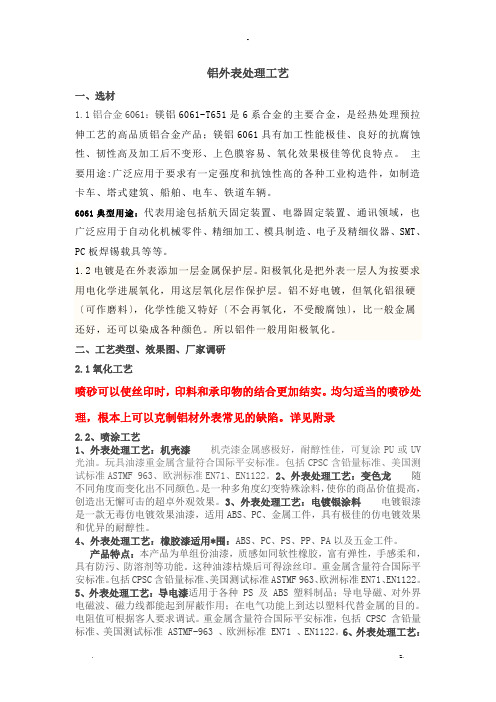
铝外表处理工艺一、选材1.1铝合金6061:镁铝6061-T651是6系合金的主要合金,是经热处理预拉伸工艺的高品质铝合金产品;镁铝6061具有加工性能极佳、良好的抗腐蚀性、韧性高及加工后不变形、上色膜容易、氧化效果极佳等优良特点。
主要用途:广泛应用于要求有一定强度和抗蚀性高的各种工业构造件,如制造卡车、塔式建筑、船舶、电车、铁道车辆。
6061典型用途:代表用途包括航天固定装置、电器固定装置、通讯领域,也广泛应用于自动化机械零件、精细加工、模具制造、电子及精细仪器、SMT、PC板焊锡载具等等。
1.2电镀是在外表添加一层金属保护层。
阳极氧化是把外表一层人为按要求用电化学进展氧化,用这层氧化层作保护层。
铝不好电镀,但氧化铝很硬〔可作磨料〕,化学性能又特好〔不会再氧化,不受酸腐蚀〕,比一般金属还好,还可以染成各种颜色。
所以铝件一般用阳极氧化。
二、工艺类型、效果图、厂家调研2.1氧化工艺喷砂可以使丝印时,印料和承印物的结合更加结实。
均匀适当的喷砂处理,根本上可以克制铝材外表常见的缺陷。
详见附录2.2、喷涂工艺1、外表处理工艺:机壳漆机壳漆金属感极好,耐醇性佳,可复涂PU或UV 光油。
玩具油漆重金属含量符合国际平安标准。
包括CPSC含铅量标准、美国测试标准ASTMF 963、欧洲标准EN71、EN1122。
2、外表处理工艺:变色龙随不同角度而变化出不同颜色。
是一种多角度幻变特殊涂料,使你的商品价值提高,创造出无懈可击的超卓外观效果。
3、外表处理工艺:电镀银涂料电镀银漆是一款无毒仿电镀效果油漆,适用ABS、PC、金属工件,具有极佳的仿电镀效果和优异的耐醇性。
4、外表处理工艺:橡胶漆适用*围:ABS、PC、PS、PP、PA以及五金工件。
产品特点:本产品为单组份油漆,质感如同软性橡胶,富有弹性,手感柔和,具有防污、防溶剂等功能。
这种油漆枯燥后可得涂丝印。
重金属含量符合国际平安标准。
包括CPSC含铅量标准、美国测试标准ASTMF 963、欧洲标准EN71、EN1122。
镁合金设计事项

鎂合金設計事項1.鎂合金設計壁厚一般要求0.6~1.0MM﹔在較小的局部區域可以做到0.4MM。
2.鎂合金模具一般在分模面采用搭接或對接等大澆口形式;沒有點澆、潛澆等小澆口形式。
3.鎂合金模具需在分模面布置澆口、溢料井(OVERFLOW)和排氣槽(VENT)等,因此在分模面位置需要約0.3~0.5MM的直邊。
如在此處不能滿足ID的要求,只能通過后加工來達到。
4.在止口位需倒圓角>=R0.1。
5.由於壓鑄的高速高壓,在產品上不建議有盲孔(模具上有懸置的細長型芯,在高壓下極易偏移、變形),因此在設計時應注意BOSS柱、螺絲柱的位置/大小的選擇,因為其上的BOSS孔/螺絲孔是通過后續機加工來實現的﹔如確有盲孔需求,建議孔徑>=1.5MM,孔深<=3.0MM,拔模角>=3.0度。
6.鎂合金模具一般不設置斜銷(頂)、行位,在產品上的倒扣、卡鉤等特征是通過后續機加工來完成的,因此在設計時需注意考慮對機加工時加工刀具空間和進/退刀位進行預留。
機加工時一般采用成形銑,其最小直徑ψ4(刀盤直徑)x ψ2MM(刀柄直徑)。
7.在壓鑄成型后,一般通過粗/精沖來去除毛邊、澆口、溢料井等余料,因此在產品設計時應考慮沖模設計的需求空間,在通孔的設計上一般要求:孔徑(最小邊長)>=0.80mm﹔孔邊距>=1.0MM(如在臺階邊,其邊距可最小為0MM ,但在墊料面必須要有空間供墊料)﹔孔間距>=1.0MM。
8.鎂合金強度好、硬度高,能承受較強的沖擊,但其彈性/塑性變形量小,容易引起脆裂,因此應特別注意加強筋的布置和對應力集中的改善,多加筋,多采用圓角,肉厚要均一。
9.應避免尖角尤其是外尖角(要求R0.3MM),因尖角處材料組織不致密,易磞缺,且應力高度集中。
10.鎂合金件的縮陷沒有塑件那麼明顯,Rib的尺寸可參考如下:11.平面度一般可達到0.2mm/40mm*90mm。
12.零件刻击字(模具凹字)以避免高速熔湯對模具的沖刷。
镁合金压铸成型设计要点

鎂合金壓鑄成型設計要點報告大綱l壓鑄機之選擇l熱室壓鑄機構造l鎂合金壓鑄件成品設計要點l壓鑄方案設計程序l壓鑄條件之決定(充填時間及澆口速度) l澆、流道系統設計l模具分割面設定要因l鎂壓鑄品尺寸公差壓鑄機之選擇(1/2) l選擇壓鑄機A: 成品投影面積(cm2)1.3A: 成品投影面積+流道&溢流井等鑄件投影面積(cm2) P: 鑄造壓力(Kg/cm2)熱室機鎂合金壓鑄壓力約為200~350 Kg/cm2鎖模力(噸) T=1.3AP/1000壓鑄機之選擇(2/2) l熱室壓鑄機之模具安裝關係規範u拉桿直徑(mm)u拉桿間隔(mm)u模具行程(mm)u模具高度(最大~最小) (mm)鎖模力u最大射出力(噸)u柱塞行程(mm)u柱塞直徑(Φmm)u可鑄重量(g)u鑄造壓力(Kg/cm2)u射出噴嘴位置(mm)u押出力(噸)u押出行程(mm)u噴嘴最大凸出量(Φmm)熱室壓鑄機構造l 壁厚須力求平均l 孔徑與深度關係鎂合金壓鑄件成品設計要點(1/4)最小孔徑d (mm)深度為孔徑d 的倍數經濟上合理孔徑技術上可能孔徑不通孔孔徑通孔孔徑l 肋與壁厚關係ðD ≦4~5t 在此比例下應不會產生縮水痕,但非必要還是以力求壁厚平均為佳。
2 1.5d> 5 d <5d> 5 d <55d 4d 10d 8d鎂合金壓鑄件成品設計要點(2/4)l圓角ð當T1=T2時;若R2=R1+T1則R1=T1 ,若R2=0則R1=1~1.25 T1鎂合金壓鑄件成品設計要點(3/4) l圓角ð當T1=最小壁厚時§當T型相交時,則R1=1~1.25 T1§當T2 > T1時,則R1=2/3( T1+T2) & R2=0~(R1+T2)§當十字或Y型相接時l當Θ=90°時,則R1= T1l當Θ=45°時,則R1= 0.7 T1 & R2= 1.5 T1l當Θ=30°時,則R1= 0.5 T1 & R2= 2.5 T1鎂合金壓鑄件成品設計要點(4/4))l拔模角(依ADAC建議壓鑄方案設計程序(1/2)l選擇壓鑄機l決定壓鑄條件ð決定充填時間ð澆口ð決定澆口速度ð模具分割面ð鑄口ð流道ð湯井ð排氣溝ð冷卻水孔ð押出銷Remark:鎂合金縮水率約為5~7/1000壓鑄方案設計程序(2/2)壓鑄條件之決定(1/2)l決定充填時間ð鑄件平均壁厚薄者宜短ð鑄件厚度不均形狀複雜者宜長ð鑄件表面光滑度好者宜短ð鑄件模具溫度低者宜短ð鑄件重量重者宜長(反之,輕者宜短) Remark:鎂合金壓鑄充填時間依平均厚度(mm)參考值如下表厚度(mm)充填時間(Second)2.00.0363.00.0553.50.07壓鑄條件之決定(2/2) l決定澆口速度ð鑄件平均壁厚薄者宜快ð鑄件厚度不均形狀複雜者宜快ð鑄件表面光滑度好者宜快ð鑄件充填長度長者宜快Remark:鎂合金壓鑄澆口速度40~75 m/s (參考值)澆、流道系統設計(1/10)l一般通則ð澆口應在充填困難地方優先設置ð各澆口大小應依其主要充填區、鑄件體積比例分配設置ð各澆口設置應在最小阻抗位置ð分流道與主流道必須維持平衡及漸縮ð流道轉彎處應設凸出部以吸收雜質(如鑄液之前端固化物)ð流道轉彎及截面積避免突然改變(因尖角易造成亂流及捲入空氣)ð流道轉彎時,截面積應適度減小才不會捲入空氣ð流道轉彎截面積漸縮一般原則如下圖:澆、流道系統設計(2/10)澆、流道系統設計(3/10) l充填模式ð橫越式充填模式(常用於平板充填)ð漩渦式充填模式(常用於中間有孔鑄件充填) l決定充填模式的原則ð各個充填區域儘量能同時充填完畢ð非直接充填區域越小越好ð金屬流動路徑越短越好l 扇形澆口系統設計ð扇形澆口系統適用於澆口長度受限的鑄件ð扇形澆口其特性中央速度高,兩端速度較小ð扇形澆口兩端夾角應小於90°,如開的太大兩側並無熔澆、流道系統設計(4/10)湯射出ð扇形澆口其特性就是由較窄的流道轉變到較寬的澆口ð扇形澆口截面積由進口到出口其截面的寬與深建議比例如下:§流道面積:澆口面積= 1.5: 1§流道厚度:澆口厚度= 3: 1§扇形長度:澆口寬度= 1.34: 1澆、流道系統設計(5/10)l錐形流道系統設計ð錐形流道適用於澆口長度較長的鑄件其流道所佔體積較小ð錐形流道其特性是藉改變流道入口面積與澆口面積比,來控制流動角的大小ð錐形流道藉控制流動角的大小,便可控制充填模式l 澆口設計ð澆口面積計算公式V :壓鑄件體積(含溢流井體積)(cm 3) Vg:澆口速度(m/s) t:充填時間(s) 澆、流道系統設計(6/10)tVg Ag ×=VAg:澆口面積(mm 2)ð舉例說明:鑄件(含溢流井)重400g,平均壁厚1.4mm, V =400/1.8=222.22 cm 3(鎂鑄件比重為1.8) 假設Vg=55m/s, t=0.03 則Ag=222.22/(55*0.03)=134.68 mm 2,另澆口厚度不得超出鑄件厚度的一半,因而在此定為0.55mm ,故澆口寬度=134.68/0.55=245mm ,但澆口形狀計算值應為實際生產時的75~85% ,以利試鑄後之修正澆、流道系統設計(7/10) l澆口與鑄件接合之方式ð側向充填:使熔湯進入模穴時有特定角度澆、流道系統設計(8/10)l澆口與鑄件接合之方式ð端部充填:使熔湯容易往上充填,適用於深槽壓鑄件澆、流道系統設計(9/10) l澆口與鑄件接合之方式ð對合充填:適用於圓筒形壓鑄件澆、流道系統設計(10/10)l澆口與鑄件接合之方式ð墊形充填:適用於平板壓鑄件及整緣容易要求鑄件模具分割面設定要因(1/7)l熔液流動性l尺寸精度l模具構造模具分割面設定要因(2/7)l模具分割面選定原則ð無死角ð製品須卡在可動模ð符合壓鑄品的品質要求ð必須利於對熔液有流動影響的鑄口、流道、澆口與湯井等位置及面積設立ð壓鑄後半成品須無去邊、修飾、機械加工上的問題ð應利於模具製造加工及模具壽命ð應利於鑄造生產性模具分割面設定要因(3/7)l模具分割面的記號ð分割面以此記號表示,此記號表示模具打開方向,此方向側通常應在可動模。
铝材设计知识点总结

铝材设计知识点总结铝材是一种重要的工程材料,广泛应用于汽车、航空航天、建筑和电子等行业。
本文将对铝材设计中的关键知识点进行总结,包括铝材的特性、合金化设计、加工工艺和表面处理等方面。
一、铝材的特性铝材具有轻质、优良的导热和导电性能,以及良好的可塑性和耐腐蚀性。
同时,铝材还具备较高的强度和硬度。
诸多特性使得铝材成为设计中的理想选择。
1. 密度轻:铝材的密度为2.7g/cm³,仅为钢材的1/3,因此使用铝材可以减轻整体结构的重量,提高产品的性能。
2. 导热导电性好:铝材的导热率和导电率分别为235W/(m·K)和37 MS/m,远高于其他常见金属。
这使铝材在热交换和电子散热领域具备独特的优势。
3. 易塑性好:铝材具有良好的塑性,可通过挤压、拉伸和冲压等加工工艺成型复杂零件,适用于各种设计需求。
4. 耐腐蚀性强:铝材与氧气形成的氧化膜能够保护其本体不受腐蚀。
同时,铝材还可以通过防腐涂层进一步提高其耐腐蚀性。
5. 强度和硬度高:通过合金化和热处理等方式,铝材的强度和硬度可以显著提高,满足不同设计需求。
二、合金化设计通过向铝材中添加其他元素,可以形成各种铝合金,进一步拓展其性能范围。
1. 常见铝合金:常见的铝合金包括铝铜合金、铝锌合金、铝镁合金和铝硅合金等。
每种合金在强度、耐腐蚀性和可焊性等方面具有不同的特点,设计时需根据具体要求选择合适的铝合金。
2. 强化机制:减小晶粒尺寸、析出硬化相、固溶强化和变形强化是常见的铝合金强化机制。
通过合理控制合金元素含量和热处理工艺,可以达到理想的强化效果。
三、加工工艺铝材的加工工艺对最终产品的质量和性能有着重要影响。
以下是常见的铝材加工工艺。
1. 挤压:挤压是将铝坯料置于挤压机内,通过挤出模具形成所需截面形状的加工方法。
挤压常用于制造铝型材,具有高效率、成本低、产品质量好等优点。
2. 拉伸:拉伸是将铝坯料置于拉伸机中,通过拉伸力使铝材在模具下拉伸成型。
镁合金压铸件设计要点(经典)

顶针
1.Boss上的顶针会影响组装; 顶针迹以击0,凹0.15为 2.顶针迹高度可能影响干涉. 基准。
往事如风
一.关于镁合金压铸件成品设计建议
汤痕 流痕,充填不良
Short shot 裂纹
裂纹
附圖(一) 往事如风
一.关于镁合金压铸件成品设计建议
冲模
孔部分先预设缺口 成形后形状 加工后形状
铣刀
以冲剪加工来通孔
E
C
E:非有效牙深長度
D尺寸 E尺寸(C+D)
絲攻直徑
螺距
C尺寸
M2 M2.5 M3
0.4 0.45 0.5
0.55 0.6 0.65
D
0.15~0.35
0.15~0.35 0.15~0.35
0.7~0.9 0.75~0.95 0.8~1.0
往事如风
七.几个制品设计的参考值(Mg)
Min0.3mm
课程:设计运用
镁合金压铸件成品设计要点
往事如风
镁合金压铸件成品设计要点
1.肉厚的均一性是必要的。 2.避免尖角。 3.注意拔模角度。 4.注意产品之公差标注。 5.太厚太薄皆不宜。 6.避免死角倒角(能少则少)。 7.考虑后加工的难易度。 8.尽量减少产品内空洞。 9.避免有半岛式的局部太弱的形状。 10.太长的成形孔,或太长的成形柱皆不宜。
拔模角
t
R
R
t2
t
附图(四) 往事如风
t1
t1
R
R
一.关于镁合金压铸件成品设计建议
部位 原因
因为易发生充填不良,组 织不致密,一踫就崩缺。 参考附图(五)。
建议
特别是外尖角,宜应避免。
尖角
镁铝合金结构设计

镁铝合金结构设计
镁铝合金结构设计是一项涉及材料科学、机械工程和产品设计等多个领域的复杂任务。
这种合金因其轻质、高强度和良好的耐腐蚀性而在航空、汽车、电子和许多其他行业中得到广泛应用。
在进行镁铝合金结构设计时,需要考虑以下几个关键因素。
首先,要深入了解镁铝合金的物理和化学性质。
这种合金具有较高的比强度和比刚度,这意味着在相同重量下,它可以提供更高的结构强度和刚度。
此外,镁铝合金还具有良好的电磁屏蔽性能和抗腐蚀性,这使得它在电子设备和汽车零件等领域具有广泛的应用前景。
其次,在结构设计中,要充分利用镁铝合金的这些优点。
例如,在航空航天领域,可以利用其轻质和高强度特性来减轻结构重量,提高燃油效率。
在汽车工业中,镁铝合金可以用于制造车身框架和零部件,以提高车辆的碰撞安全性和燃油经济性。
此外,还需要考虑镁铝合金的加工性能和成本。
虽然镁铝合金具有良好的可加工性,但在某些情况下,可能需要特殊的加工设备和工艺。
同时,镁铝合金的成本相对较高,这可能会限制其在某些低成本产品中的应用。
最后,在结构设计中,还需要考虑结构的整体稳定性和安全性。
这需要对结构进行详细的力学分析和模拟,以确保在各种工作条件下,结构都能够保持稳定和安全。
综上所述,镁铝合金结构设计是一项需要综合考虑材料性能、加工成本、结构稳定性和安全性等多个因素的复杂任务。
通过充分利用镁铝合金的优点,并克服其潜在的挑战,我们可以创造出更高效、更轻便、更安全的产品。
镁铝合金模板优化设计及施工质量控制

镁铝合金模板优化设计及施工质量控制摘要:在新一代的建筑模板系统中,镁铝合金模板是在常见的铝合金模板中加入镁的建筑模板系统。
本文就以国内铝模板的发展和目前应用的现状入手,着重分析镁铝合金模板的特点,并在此基础上重点介绍在高层建筑应用,探索施工技术的分析,并通过对质量管控的要求提出具体的解决办法。
关键词:高层建筑;镁铝合金模板;施工技术;技术研究一、镁铝合金模板的特点1.1镁铝合金模板的分类通过按照材料的划分方式来分辨镁铝合金模板,可以分为墙板、楼面板、梁侧板、C槽、转角C槽、支撑头等。
而镁铝板系统是相对而言造价比较低廉的,重量轻,就承载力而言,相对比较铝合金模板强度高、比较平整。
1.2镁铝合金模板的优点(1)模板系统组成合金模板体系由模板系统、支撑系统、紧固系统、附件系统组成。
模板系统构成混凝土结构施工所需的封闭面,保证混凝土浇灌时建筑结构成型;附件系统为模板的连接构件,使单件模板连接成系统,组成整体;支撑系统在混凝土结构施工过程中起支撑作用,保证楼面,梁底及悬挑结构的支撑稳固;紧固系统是保证模板成型的结构宽度尺寸,在浇筑混凝土过程中不产生变形,模板不出现涨模、爆模现象1.早拆技术、灵活快速施工合金模板的顶模和支撑系统实现一体化设计,将早拆技术融入了支撑系统,将大大提高模板周转率和施工效率,降低了材料成本和施工成本。
施工现场每栋楼各采用一套模板主系统,三套楼板底支撑,三套梁底支撑,就可实现3天一层的施工速度。
主模板在该层混凝土强度达到要求后,拆除并传送至上层。
1.工厂化施工更快捷精确实现工厂化施工,在工程准备阶段,铝模厂家根据施工图进行了深化设计及厂内试拼装后运往工地,将所有可能出现的问题均提前解决在工厂里,从而大大提高了施工速度和精度。
二、高层建筑镁铝合金模板施工技术2.1镁铝合金模板的安装1、前期准备工作(1)技术、生产人员熟悉图纸,认真学习掌握施工图的内容、要求和特点,同时针对有关施工技术和图纸存在的疑点作好记录,通过会审,对图纸中存在的问题,与设计、甲方、监理共同协商解决,取得一致意见后,办理图纸会审记录,作为施工图的变更依据和施工操作依据,并由厂家进行深化设计拼装图。
铝镁合金外壳压铸工艺

铝镁合金外壳压铸工艺铝镁合金外壳压铸工艺引言:铝镁合金外壳是一种常见的金属外壳结构,具有轻质、高强度和优良的导热性能等特点。
铝镁合金外壳的制造工艺至关重要,其中压铸工艺是一种常用的方法。
本文将深入探讨铝镁合金外壳压铸工艺的各个方面,包括材料选择、模具设计、工艺参数和质量控制等,并分享对这一工艺的观点和理解。
一、材料选择1.1 铝镁合金的特点铝镁合金是一种由铝和镁组成的合金材料,具有轻质、高强度和优良的耐腐蚀性能。
其低密度使得铝镁合金外壳重量轻,适用于需要降低整体重量的应用场合。
同时,铝镁合金还具有良好的导热性能,能够有效地散热,提高设备的工作效率。
1.2 材料选择的考虑因素在选择铝镁合金材料时,需考虑以下因素:- 强度要求:根据外壳所需承受的力学载荷和环境条件,选择适当的铝镁合金牌号,以满足强度要求。
- 耐腐蚀性能:根据外壳使用环境和工作条件,选择具有良好耐腐蚀性能的铝镁合金。
- 可加工性:考虑到后续的压铸加工工艺,选择可加工性良好的铝镁合金。
二、模具设计2.1 模具类型在铝镁合金外壳压铸工艺中,常用的模具类型包括冷室压铸模具和热室压铸模具。
冷室压铸模具适用于铝镁合金外壳的生产,具有较高的生产效率和较低的能耗;而热室压铸模具适用于高硬度、高熔点的铝镁合金。
2.2 模具结构设计模具结构设计对于外壳质量和工艺效率至关重要。
在外壳的设计中,需考虑以下因素:- 浇注系统:合理设计浇注系统,确保熔融金属均匀填充模具腔体,避免气孔和缺陷的产生。
- 温度控制:通过合理设计冷却系统和温度控制装置,控制铝镁合金的冷却速度,防止过热或过快冷却引起的变形和质量问题。
- 模具材料选择:选择具有较高耐磨性和耐腐蚀性的模具材料,以延长模具使用寿命。
三、工艺参数3.1 注射压力和速度在铝镁合金外壳压铸工艺中,注射压力和速度对产品的质量具有重要影响。
适当的注射压力和速度可以保证铝镁合金在模具中充分充填,避免孔洞和冷隔等缺陷的产生。
- 1、下载文档前请自行甄别文档内容的完整性,平台不提供额外的编辑、内容补充、找答案等附加服务。
- 2、"仅部分预览"的文档,不可在线预览部分如存在完整性等问题,可反馈申请退款(可完整预览的文档不适用该条件!)。
- 3、如文档侵犯您的权益,请联系客服反馈,我们会尽快为您处理(人工客服工作时间:9:00-18:30)。
熱室壓鑄機構造
在此比例下應不會產生縮水痕,但非必
⇨拔模角(依ADAC 建議)
⇨一般拔模角, 度精級拔模角, C L D /=01746.0/)/(L D =θ)/(8.0C L D =01746.0/)/(L D =θ
●
扇形澆口系統設計
⇨扇形澆口系統適用於澆口長度受限的鑄件⇨扇形澆口其特性中央速度高,兩端速度較小
⇨扇形澆口兩端夾角應小於90°,如開的太大兩側並無熔湯射出
⇨扇形澆口其特性就是由較窄的流道轉變到較寬的澆口⇨扇形澆口截面積由進口到出口其截面的寬與深建議比例如下:
▪流道面積:澆口面積= 1.5: 1▪流道厚度:澆口厚度= 3: 1▪扇形長度:澆口寬度= 1.34: 1
澆、流道系統設計(4/10)
錐形流道藉控制流動角的大小,便可控制充填模式
端部充填:使熔湯容易往上充填,適用於深槽壓鑄件對合充填:適用於圓筒形壓鑄件墊形充填:適用於平板壓鑄件及整緣容易要求鑄件
動模,而使壓鑄件開模時附著於可動模。
及排氣溝順利排出使熔液的流動性較佳。
B部份仍會發生龜裂及熔損等現象。
表3)
之公差,追加垂直於分模面
4)
之公差追加於表4之公差
450cm2, A為20mm則
其公差值應為±0.10,活動
⇨超過75mm每25mm追加公差……………0.04mm ⇨超過75mm每25mm追加公差……………0.075mm。