制程异常报告书
三元材料指标产异常原因及措施

1、排除设备、操作手法的问题,并进 行复测,跟踪复测结果; 2、若复测结果仍不合格,及时通知技 术、品质等相关部门,决定如何处理 (返工/报废/让步接收);
1、出炉料残碱偏低,证明生料Li%低, 说明物料缺Li%,会降低材料的电性能及 充放电效率,影响电池性能; 2、物料残碱高,会增加物料制浆时粘 度,导致物料无法正常使用。
1、人员操作不熟练 2、检测设备未校准 3、物料存在问题 4、未按照作业指导书进行操作 5、环境影响 6、测试偏差
1、人员操作不熟练 2、检测设备未校准 3、物料存在问题 4、未按照作业指导书进行操作 5、环境影响 6、测试偏差
1、Ni:提高容量,过高与Li离子混排使循环下降; 2、Co:降低混排,稳定层状架构,降低阻抗,提高电导率。过 高,导致晶胞参数a和c减小且c/a增大,导致容量降低; 3、Mn:降低成本和改善材料的结构稳定性和安全性。过高,降 低材料克容量,并且容易产生尖晶石相而破坏材料的层状结构。
1、人员操作不熟练 2、检测设备未校准 3、物料存在问题 4、未按照作业指导书进行操作 5、测试偏差
1、人员操作不熟练 2、检测设备未校准 3、物料存在问题 4、未按照作业指导书进行操作 5、测试偏差
异常后果
措施
1、水分过高会导致前驱体中有效物质含量不足; 2、影响一次配料生料均匀性。
1、排除设备、操作手法、环境的问题, 并进行复测,跟踪复测结果; 2、若复测结果仍不合格,及时通知技 术、品质等相关部门,决定如何处理 (退换货/让步接收);
1、人员操作不熟练 2、检测设备未校准 3、物料存在问题 4、未按照作业指导书进行操作 5、环境影响 6、测试偏差
1、人员操作不熟练 2、检测设备未校准 3、物料存在问题 4、未按照作业指导书进行操作 5、环境影响 6、测试偏差
品质异常改善要求通知书

物料名称
规格/型号
品质异常问题来源
不良数量 不良率 异常描述:
总数量 发生日期
( )客户投诉( )制程检验( )出货检验 ( √ )可靠性试验( )其 他:
原因分析: 1.TFT卡座板 与按键板焊
提报:
改善处理 措施:
长期对策: 1.培训员工焊接技术;
作成:
责任单位 责任单位
改善回复:
生产/品质 部
作成:
不良物料处 置改:善完成日 期:
改善验证: 待验证 未改善原 因:
( )作已成: 改善
审核:
日期:
审核:
日期:
审核:
日期:
审(核: ) 未改善
日期:
下一份CAR No:
验证人/日期:
表单编号:
XXXX有限公司
品质异常改善要求书/通知书(CAR)
报告编号
发出部门
分 发 (√ )工程部( √ )品质部( )PMC部
责任部门 (用 表示)
(
协助部门 (用 表示)
(
)生产部( )销售部(
)研发部( √ )采购部 )其他:
回复要求 ( )要 ( )不要
生产部 特急 请于( )H内回复 急件 请于( )H内回复 普通 请于( )H内回复
品控报告(质量异常问题反馈单)管理规定
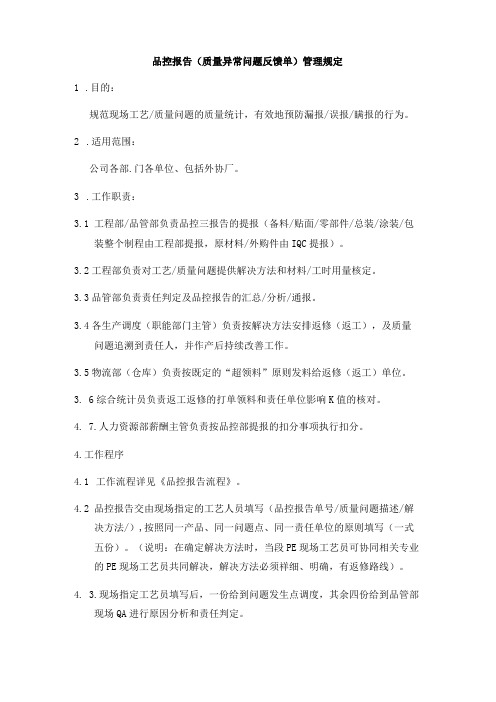
品控报告(质量异常问题反馈单)管理规定1.目的:规范现场工艺/质量问题的质量统计,有效地预防漏报/误报/瞒报的行为。
2.适用范围:公司各部.门各单位、包括外协厂。
3.工作职责:3.1工程部/品管部负责品控三报告的提报(备料/贴面/零部件/总装/涂装/包装整个制程由工程部提报,原材料/外购件由IQC提报)。
3.2工程部负责对工艺/质量问题提供解决方法和材料/工时用量核定。
3.3品管部负责责任判定及品控报告的汇总/分析/通报。
3.4各生产调度(职能部门主管)负责按解决方法安排返修(返工),及质量问题追溯到责任人,并作产后持续改善工作。
3.5物流部(仓库)负责按既定的“超领料”原则发料给返修(返工)单位。
3.6综合统计员负责返工返修的打单领料和责任单位影响K值的核对。
4.7.人力资源部薪酬主管负责按品控部提报的扣分事项执行扣分。
4.工作程序4.1工作流程详见《品控报告流程》。
4.2品控报告交由现场指定的工艺人员填写(品控报告单号/质量问题描述/解决方法/),按照同一产品、同一问题点、同一责任单位的原则填写(一式五份)。
(说明:在确定解决方法时,当段PE现场工艺员可协同相关专业的PE现场工艺员共同解决,解决方法必须祥细、明确,有返修路线)。
4. 3.现场指定工艺员填写后,一份给到问题发生点调度,其余四份给到品管部现场QA进行原因分析和责任判定。
4.4.责任判别定后,交质量统计员(1份,追溯责任人汇总/通报)、BOM/IE管理员(1份,材料/工时用量核定)、责任单位调度(2份,后续持续改善和责任人追溯)。
(说明:如果责任单位是公司职能部门,另外则相应的也要给到责任部门主管)4.5.BOM/IE管理员做最终用量核定后,交综合统计员进行打领料单。
4.6.质量统计员根据已收到的品控报告与综全统计员进行对单(主要检查此过程中有否漏单情况)。
然后依据上述已经发生的质量成本,分责任单位进行统计/汇总。
5.8各生产车间调度/职能部门主管接到品控报告后,2个工作日内追溯到责任人,并将追溯结果书面反馈给品管部质量统计员处汇总,责任单位依照后续改善方案对来批加以改善,此过程中如有对责任单位判别定有异疑,以“三级仲栽”方式进行(两个工作日内没有提出申诉的,视为认可此判定)。
制程品质异常管理程序(含表格)

制程品质异常管理程序(IATF16949-2016/ISO9001-2015)1.0目的为了快速对应生产过程中发生的品质异常并及时采取相应的纠正预防措施,特制定此规定。
2.0范围适用于生产过程中因设备、材料、工艺等发生异常时影响到产品质量的处理。
3.0定义3.1当生产过程的产品品质影响因素发生不符合常规变化,称之为品质异常。
异常的通常表现处理方式1 出现到目前为止,从未发生过的影响功能的或致命不良时 2S(立即反应、快速解决)2 工程直通不良率超过5%时3 同样的不良连续发生,且不良数达到5个4 按作业指导文件无法进行生产时5 设备、仪器不能正常工作而不能保证质量时6 材料发生变异时7 生产/储存环境发生变化可能导致产品质量无法保证时 8 品管巡检发现致命不良1件或以上时 9物料发生混乱时10 首检发现重大质量缺陷时3S11 工装夹具、辅料发生环境有害物质污染时,等等 12 制程直通不良率超15%时3.2异常发生处理的S.S.S 机制(3S 原则):异常快速反应处理机制,即异常发生时,需立即反应、马上停止、快速解决处理的机制。
SOON:立即反应;STOP:马上停止;SOLVE:快速解决。
4.0职责4.1制造部负责异常问题的数据收集、汇总、报告、传达;4.2品管部负责对制程异常的监控,异常对策措施的实施跟进及验证;4.3出现严重品质不良时,制造部和品管部课长或以上领导有权立即停止生产;4.4品管部负责原材料(包括内制品)异常统筹处理以及主持召开会议;4.5工程部负责除原材料问题以外生产异常的统筹处理以及主持召开会议。
5.0作业程序6.7.责任部门主导对异常点进行原因分析,制定相应的改善对策方案,并进行水平展开,确保类似机种、类似问题能得到有效预防;6.8.《异常处理对策报告书》由责任部门负责整理、编制,并与对策会议结束后2小时内发行到所有的关联部门;责任部门6.9.各关联部门按异常对策报告的要求执行改善工作;6.10.如涉及到材料、工艺、业务流程等方面的变更,则需按《4M 变更管理规定》、《工程管理程序》、《文件管理程序》等文件的要求进行;6.11.如经分析,在线、在库或已发货的产品也存在同样的异常点(或有质量隐患),由品管部负责进行调查、处理。
制程品质异常处理规定

1. 目的为规范本公司制程品质异常的处理流程,明确质量异常及时处理、报告内容的填写与发行,提高质量异常的处理时效,确保制程中的产品品质得到有效控制.2. 适用范围适用于公司内所有质量异常问题的提出、处理、执行、验证等.3. 定义3.1 一般异常的定义:3.1.1 产品在制程生产时一小时出现功能不良、尺寸不良、装配不良,不良率超过3%;3.1.2 产品在制程生产时一小时出现外观不良,生产300pcs及以上总不良率超过5%;300pcs以下总不良率超过7%3.1.3 产品在制程中出现安全性隐患;3.1.4 制程中出现物料来料不良超过5%(特采物料除外);3.1.5 工序漏做、做错或混料.3.2 严重异常的定义:3.2.1 制程同一时间段,不良超过10%且无有效改善措施,不良有明显上升趋势;3.2.2 产品出现有安全隐患且不能有效筛选;3.2.3 物料不良且无法加工或挑选使用;3.2. 4 重大质量问题(安全测试不通过、客户端有相关投诉且该产品在线生产且无明确的纠正预防措施)不能在产线得到相关的筛选.3.2.5 批量性不良(不良超过20%).4. 职责4.1 生产部: 负责制程异常的发现、反馈,不良品的区分、处理及制程失控造成的异常原因分析、纠正预防措施的制定和执行;4.2 研发部:4.2.1负责制程异常因工艺、作业标准、包装技术问题造成的不良的产品处理、原因分析及纠正预防措施的拟订和执行以及有效措施标准化文件的建立.4.2.3对生产员工操作进行指导,对异常原因进行分析,并对工艺问题进行改善.4.3 工程部4.3.1负责品质异常中牵涉到的设备异常的设备维修、原因分析、原因改善,以及相关措施的执行.4.4 品质部:4.4.1 IPQC:对整个生产过程进行监控,将车间发生的异常向有关部门进行汇报,对不良品进行标识和隔离,对改善行动进行跟踪、监督以及改善后数据的收集、反馈4.4.2 品质工程师:参与对异常进行分析,对最终执行的纠正预防措施进行跟踪、验证,并保证本管理办法有效执行4.4.3 品质文员:负责品质单的收集、分发、归类和存档以及通报4.5 PMC: 负责异常物料的退货、补发以及产品的入库处理4.6 财务部:负责异常工时的统计,异常财产损失的计算、通报以及相关部门的责任分摊5. 作业内容5.1 发现异常5.1.1 IPQC根据作业指导书的要求进行首件、巡检以及转序产品的抽检,当发现有品质异常时,初步统计不良数量、不良项目等信息.判定异常属于一般异常还是其他异常.5.1.2 当其他人员发现异常时,应立即通知组长和IPQC.5.2 判定异常5.2.1 IPQC对异常现象进行了解并统计后,应确认是否需要发出《品质异常处理单》.如果没有达到异常标准则只需反馈给操作员或组长进行改善,并填写《制程稽查记录表》同时跟进改善结果是否有效,如果达到异常标准3.1则开出《品质异常处理单》;如达到3.2时,除开出《品质异常处理单》外还要开出《品质异常事件单》.5.2.2 IPQC确认并发出《品质异常处理单》,并将异常单中得内容填写清楚,异常单必须具备以下几点:a) 产品批次、型号;b)发生异常的时间和地点;c)已生产数量;d)已发现(抽检)的不良数量;e)不良率;f)异常现象的详细描述;填写完成后交给生产组长或生产主管确认异常.生产部门确认后,需要交给品质组长及以上进行审核.5.2.3 异常单会签完成后,IPQC组长将异常单交给文员进行编号登记.编号原则:QA+年份+月份+日+三位序列号.5.2.4 异常达到严重异常且暂时没有有效措施改善时,需要停机、停拉的,需各部门经理会签评审(夜班可根据情况电话通知,事后补签),经过副总经理批准.生产部立即将异常信息通知给PMC.5.3采取应急措施5.3.1 由生产组长主导对已生产的产品进行隔离、标识,待研发、品质现场工程师给出解决方案.5.3.2 IPQC将异常单交给研发部现场工程师,现场工程师接到异常单后,在现场对不良现象及不良率进行确认.必要时可向销售部了解交期,然后与生产主管、品质工程师共同分析确认,研发、品质现场工程师根据实际情况制定应急措施(严重异常时,可召集相关人员召开会议进行讨论).5.3.3 如应急措施需要返工,则由研发部现场工程师制定返工方案后,生产部按照公司《返工返修管理规定》进行返工.研发部现场工程师现场指导,IPQC对返工后的产品进行确认.5.3.4 研发、品质现场工程师提出临时解决方案一定对现场具有指导性、可行性等,不可用“加强”、“建议”等字眼. 提出临时处理措施时,应具备以下两点:a 对已经生产的产品给出处理措施,如:报废、返工、返修、挑选使用、区分下转等.b 对后续的生产过程给出纠正措施,提升产品合格率.5.3.5 研发部主管或经理负责对临时解决方案的可行性、合理性进行确认.5.4 临时处理措施验证5.4.1现场品质人员、以及现场负责人对于研发、品质现场工程师给出的临时处理措施的实施效果的可行性、合理性进行验证,确保临时处理措施可提升产品合格率或能准确区分、拦截不良品.5.4.2现场品质人员应对已生产产品的处理过程进行监督;对已按临时处理措施处理过的产品进行复检、标识和区分,并统计出准确数量记录在《品质异常处理单》上(含合格数量、不良数量或报废数量).5.4.3 对处理措施涉及到的报废、降级等方案,现场品质人员需复印异常单副本交于PMC和财务部,由PMC评估是否需要补料;由财务部统计异常损失(待追查到责任部门后,将异常损失转嫁到责任部门).5.5 原因分析5.5.1 研发、品质现场工程师对不良现象进行分析,并将分析结果记录在《品质异常处理单》中.必要时组织相关部门进行会议讨论或进行试验验证.5.5.2 研发、品质现场工程师找出异常造成的责任部门并记录在异常单中(异常责任部门明确到车间工序),异常单经部门负责人核准,核准后的异常单传递给责任部门.5.5.3 原因分析要合理、得体,不可用“估计”、“大概”、“可能是”等模棱两可的字眼.5.5.4 在涉及到物料问题时,要写清楚物料名称、物料编码、入库日期、入库状态;在涉及到文件问题时,要写清楚文件编码与版次,以便相关人员追溯、处理.5.5.5 品质工程师须对分析原因的符合性进行确认,并跟进确认库存物料、供应商处物料、在线产品、客户处产品的处理.5.5.6 责任部门收到异常单后,应立即对异常情况进行调查分析,并将分析结果记录在异常单中.如果对异常责任部门判定有异议时,需立即找到对应的现场工程师共同分析或进行试验验证,必要时可召集品质、研发以及总经理进行裁决,直到找到真因为止.5.5 纠正预防措施5.5.1 责任部门(工序)负责人将异常分析结果及改善对策填写在异常单后,经部门主管/经理审核.将异常单回复给品质工程师.如异常单填写的改善措施无法有效解决问题,则直接退回给责任部门的主管/经理,由主管/经理监督或协助完成此异常单的回复.填写要求如下:A.责任部门对异常问题点提出纠正预防措施,须用简洁、明确、确定性的文件进行描述,多项措施应用项目符号标注,如:①、②….B.纠正预防措施应具备可行性、可测量性、权威性、有效性等,不可用“加强”、“建议”、“看情况”、“待确认(待验证)”等字眼.C.纠正预防措施如涉及到其他部门职责范围内,应提交相关责任部门填写预防方案;5.5.2 负责执行的职责部门必须明确纠正预防方案的完成时间,以保证此方案能够得到及时、有效的落实.5.5.3 现场研发部主管级以上人员负责对工程纠正与预防方案的可行性、合理性、有效性进行确认.并填写职责部门及具体完成日期.5.5.5 相关职责部门经理负责对本部门采取的纠正与预防方案的可行性、合理性、有效性进行确认.并确定部门纠正与预防措施的主责人.5.5.5 确认OK后的异常单,由部门文员将异常单给生产部统计异常损失的工时及物料.并将异常单复印分发给生产部、财务部、、PMC及相关责任部门.5.5.6 相关部门收到异常单后,应按照异常单的内容对改善行动进行执行,并将执行结果反馈给品质部.5.5.7 各部门在填写时须严格按以上职责与权限进行,并明确本身在此工作中的职能作用,避免越权,以避免造成异常单的层次不清与混乱及给处理者及执行者带来迷惑与误导.若有好的建议和其他意见,则以附件形式提出.5.5.8 改善措施一旦给出,相关职责部门须按照改善措施执行,如未执行改善措施,品质部有权要求停止生产,所造成异常损失由相关责任部门承担.5.6 效果确认5.6.1 IPQC在异常单原件上对改善后的效果进行跟踪,如改善OK,则可以关闭.如改善NG,则重新开出异常单.5.6.2 改善效果跟踪中,如发生的问题属于新发生的问题,则此份异常单也可关闭.如不良原因相同或由于改善措施引发的问题点,则改善措施无效.5.6.3 效果确认后,IPQC将填写完成的异常单给品质组长审核,品质工程师对已结案或完成改善的项目最终执行结果进行验证,,并对结批数据汇总进行汇报,必要时提供相应验证资料和异常单交给上级批准关闭项目.交由文员存档.5.6.4文员进行汇总各负责人跟进纠正预防措施执行情况,并抄送各部门负责人、副总;5.7 标准化如改善措施经最终判定合格有效,由研发部负责将改善措施增加(修改)到相关文件内,形成标准受控文件6. 相关文件《制程与出货检验作业规范》、《返工返修管理规定》7. 记录表单《品质异常处理单》、《制程稽查记录表》、《品质异常事件单》8. 附流程图。
制程检验作业指导书

制程检验作业指导书
1.目的
为了更好的控制生产的产品品质,并符合客户的要求。
2.范围
适用于本公司五金冲压件制造流程中的检测。
3.职责
生产部:负责各相关制程的自检、不良品的收集。
品质部:负责制程巡检、检验结果的记录、判定与标识。
4.工作内容
4.1 QC依据图纸、样品及相关检验标准每隔一小时对生产线上的正生产的产品进行检查。
拿取机台上正在生产的产品2PCS,对照
图纸及样品检查尺寸及外观,检查合格后将相关数据记录在《制程检验记录表》上。
4.2 检查到有产品不合格时,需通知操作员停机,并通知技术员调机,调机后的产品需品检确认合格后方可开机生产。
不合格品需
用不合格票标识并用黄色箱子隔离,同时需对上个时间段的产品进行检查,看有无同样的不良,如有需继续往上一个时间段追溯,直到无不良为止。
4.3 不能返修的不良品报废处理;可以返修的不良品通知相关责任部门及时处理,处理完后需品检确认OK后方可流入下工序。
对不良比例超过1%的产品需对责任部门开出《品质异常对策报告》。
5.1《制程检验记录表》5.2《品质异常对策报告》。
某公司生产制程异常处理及工时补贴管理规定

浙江********有限公司生产制程异常处理及工时补贴管理规定(试行)1.目的:为把生产制程中出现的异常状况迅速而有效地处理,健全各相关部门对生产异常处理的责任制度,规范工时补贴,特制定本规定。
2.适用范围:本规定适用于公司各车间生产制程中发生的影响生产正常进行的各类异常的管理。
3.定义:3.1 本规定所称的生产制程异常,是指造成生产车间停工或生产进度延迟的情形,由此造成的无效工时,亦可称为异常工时。
生产制程异常一般包括下列情形:(1)计划异常:因生产计划临时变更或安排错误/失误等导致的异常。
(2)物料异常:因物料供应不及时(断料)、物料品质不良等导致的异常。
(3)设备异常:因设备设施(含水、气、电)、工装不足或故障等原因而导致的异常。
(4)品质异常:因生产制程中出现了因来料、制程加工等品质问题而导致的异常。
(5)产品异常:因产品设计或其他工艺、技术问题而导致的异常。
(6)其它异常:因其它原因等导致的生产异常。
3.2 重大异常:品质部连续3批抽检不合格且同一故障、同一订单、同一班次,属性能不良的问题;生产发生批量质量异常,单项不良率超过10%,生产数量大于200PCS;其它异常(如工装设备故障、缺料等)造成生产制程停线在1小时以上的。
4.职责:4.1 工程部、研发部:按职责分工负责对技术、工艺与设备工装异常的分析、现场处理,临时改善对策的提供,改善过程跟进以及改善标准文件的制定;4.2 品质部:负责异常反馈、确认、分析、组织改善、原因分析讨论与对策汇总,改善措施的制订、改善对策的执行跟进,改善效果验证以及整个流程运作的监督跟进;4.3 各生产车间:负责异常的反馈、改善,异常对策的执行;4.4 物控部:负责生产异常的综合协调与跟进解决。
5.管理细则:5.1 生产制程异常管理的原则:5.1.1 生产制程异常发生时,一般先由车间/产线/班组自行处理,如果自行处理不了的,再申请外部支援。
5.1.2 对异常的反馈与处理坚持“谁发现、谁反馈”、“谁导致、谁负责”的原则。
生产异常管理培训教材
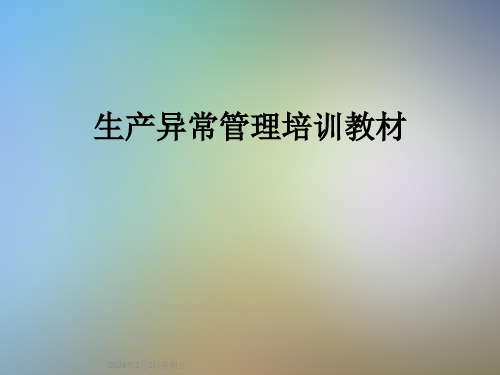
•2.异常处理与改善混为一谈 ;
将异常问题以改善的想法分析,但收集的 资料又不够,以致无法找到真正的异常原因。
3.异常反应单只由品管填发;
制程异常的发现,好象只是质量部门的责任, 而与制造现场等其他部门无关。
•4.未能掌握时效;
发生异常时须及时恢复正常。否则将造成
1、剔除:
(1) 剔除不必要的手工作业。 (2) 剔除不方便或不正常的动作。 (3) 剔除必须使用体力才能维持的姿势。 (4) 剔除必须使用体力的工作,用动力工具进行取代。 (5) 剔除危险的工作。 (6) 剔除所有不必要的闲置时间。
2、合并:
(1) 合并各种工具,使成为多用途。 (2) 合并可能的作业。
机遇性原因(Chance Cause)
机遇性原因又称不可控制原因,为生产过程中所产 生的变异。
此系由许多微小的不可控制因素所引起对产品品质影响不大; 例如,同种原料内的变化,机器轻微振动所引起的变化; 对工厂而言,这是一种正常的变动范围,其变化是不可避免的
; 在制程管制时,如希望予以减少或去除是非常不经济的,会增
4.Why (为何 ) 为什么是他做
? 为什么要做? 为什么在那里
做? 为什么那样做
?
2.What(何事 ) 要做什么? 已经做了什么? 应该完成什么? 还该完成什么?
5WIH审核
5.When(何时 ) 什么时候做? 什么时候完成的? 该在什么时候完成的? 为什么在那个时候做?
预防措施 消除「异常真因」, 使不重复发生「治本」。
应急措施的具体作法
明确发生异常时的群体。 将异常现象迅速通知有关单位,并要求其参与
处理。 对过程采取处置措施,使异常现象暂时控制而
- 1、下载文档前请自行甄别文档内容的完整性,平台不提供额外的编辑、内容补充、找答案等附加服务。
- 2、"仅部分预览"的文档,不可在线预览部分如存在完整性等问题,可反馈申请退款(可完整预览的文档不适用该条件!)。
- 3、如文档侵犯您的权益,请联系客服反馈,我们会尽快为您处理(人工客服工作时间:9:00-18:30)。
应急处置 紧 急 处 理 承办 时间 确认 原因调查 原 因 调 查 时间 调查 月 日 月 日
确认
再发防止 再 发 防 止 对 策 承办 时间 月 日
确认
确 批 时间 调 查 人 批示人
认 月 日
示
四 E05 不良品报废申请书
项次 1 2 3 4 5 6 7 8 9 10 11 12 13 品名/型号 数量
四 E03 成品入库单 入库部门 项次 制单号 1 2 3 4 5 6 7 8 9 10 11 12 13 14 15 16 17 18 19 合计 入库日期 数 量
No. 日期:品名箱 数备注
仓库: 四 E04 制程异常报告书
工程名 异 常 状 况 作业员 说明: 品质特性 检 验 员
入库者: No. 日期:
四 E01 委外加工单
No. 日期:
厂商 委制编号 品 名
厂商 编号 数 量 需求日期
地址 电话 单 价 金 额 备 注
合
计
品质要求
提 供
1.图纸 2.模、夹具 3.材料明细
说明:1.委外加工单视同协力厂的订单; 2.应注明品质要求; 3.协力厂签认回联。
四 E02 外厂加工入库验收单 No. 日期:
No. 申请日期:
报废原因 备注
14 15 16
17 18 合计
核准:
主管:
申请:
四 E06 品质月报
部门: 项 次 1 2 3 4 5 6 7 8 9 10 11 12 13 14 15 16 17 18 19 20 合 计 合计占有率 % 100% % % % % % % % % % 月 份: 制表日期: 品名/型号 生产数 不良数 不良率% 不 良 项 目 别
制单号
承制厂商 品 名 编 号 交 货 数 量 点收人 送货日期 箱 数
实 际 点 收 数 量 品质验收 验收方式 项 次 1 2 3 4 5 6 7 综合判定 备注: 主 管 检验项目
日
期
全检 规格值
抽检 实测值
免检 判定
允收 品
特采 管 检 验 员
选别
拒收 仓 主 管 库 经 办
说明:1.仓库收货后即进行数量点收; 2.品检品质判定后再交回仓库处理。