QC工作流程-制程品质异常处理流程
品质异常处理流程

品质异常处理流程1.目的Purpose为规范公司制程品质异常处理流程,对制程中出现的品质异常及时处理,确保制程中的产品,品质得到有效控制,满足客户要求。
适用于制程品质异常处理3.定义Definitions3.1品质异常3.1.1IQC检验:超出允收水准,具体按照《进料检验作业规定》定义为准4.1.2巡检(单机台):外观单项不良:连续不良23pcs;尺寸单项不良:连续不良22pcs;功能单项不良:检验不良2Ipcs3.1.3全检:外观单项不良23%,尺寸单项不良21虬4.1.4抽检:违反3F(成型/适配/功能):检验不良21pcs.4.职责Responsibility4.1生产部4.1.1班组长:对不良品进行确认,对异常进行初步原因分析。
4.1.2课长:对生产管理人员作业层面等原因造成的异常,主导原因分析并推动改善。
5.2ME/生技:对非生产管理及作业层面的异常,主导原因分析并推动改善。
5.3品保单位4.3.1IPQC:对整个生产过程进行监控,将线上的异常向有关部门进行汇报,对改善行动进行跟踪,做好首件/巡检检查等。
4.3.2QE:对制程异常提出应急措施,并进行初步原因分析,跟进改善对策执行的有效性。
4.3.3SQE:对制程中确认的来料问题进行原因分析并推动供应商改善。
5.流程及说明ProcessFlowAndDescription5.1品质异常处理流程:6.2进料检验品质异常IQC进料检验发现的品质异常,依照《进料检验作业规定》处理。
6.3制程品质异常6.3.1作业员自检/互检发现之品质异常作业员依据作业指导书进行自检和互检,当发现品质异常时立即通知班组长进行确认处理。
6.3.2IPQC检验发现之制程异常6.3.2.1IPQC巡检发现品质异常时,通知生产单位确认并分析改善,将制程异常情况填写在《IPQC巡检记录表》和《IPQC尺寸检验记录表》中,初步统计不良数量,不良项目等信息,同时通知相关单位改善、处理。
[企业流程优化]制程品质异常处理流程
![[企业流程优化]制程品质异常处理流程](https://img.taocdn.com/s3/m/e280251fad02de80d5d8401f.png)
[企业流程优化]制程品质异常处理流程文件代码: 拟制:发布日期: 审核: 制程品质异常处理流程版本:B2 页次: 1/6 批准:文件修,制,订履历一览表版《管理文件审查单》 N0. 发布日期修,制,订说明拟制审核批准备注次编号1 B0 - -2 B1 061212002 优化流程:(更改格式,1 修改定义内容,2 简化活动框动作,3 修改生成记录表格。
3 B2 070518005 1 取消《品质异常报告单》~增加《品质异常处理单》并延用《品质异常报告单》的记录代码,2 取消《制程一览表》~增加《制程品质异常跟进表》并延用《制程一览表》的记录代码,3 更改部分职责.文件发放范围及份数,在“( )”中打“?”表示需分发的单位~在“[ ]”中填写该单位发放文件份数,: (?) 总裁办[ 1 ] ( ) 财务中心[ ] ( ) 管理者代表[ ] ( ) 人力资源中心[ ] (?) 研发项目中心[ 1 ] ( ) 蓝牙事业部[ ]( ) 营销中心[ ] ( ) 精密模具事业部[ ] (?) 品质中心[ 1 ] ( ) 精密塑胶事业部[ ] (?) 电池事业部,制造部,[ 1 ] ( ) 其他: [ ] ( ) 电池事业部,PMC,[ ]( ) 物流中心,采购,[ ]( ) 物流中心,仓库,[ ]( ) 信息中心[ ]文控员备注唯盖有红色的DCC正本受控章方为正式有效文件。
文件代码: 拟制:发布日期: 审核: 制程品质异常处理流程版本:B2 页码:2/6 批准:1 目的 4.2 品质中心为规范本公司制程品质异常处理流程~对制程中的品质异常及时处理~确保制程中4.2.1 IPQC:对整个生产过程进行监控~将拉上的异常向有关部门进的产品品质得到有效控制~满足客户要求。
行汇报~对改善行动进行跟踪~做好首件检查等,4.2.2 QAE:对制程品质异常采取应急对策~对改善措施进行跟进。
2 适用范围适用于电池事业部所有制程品质异常处理。
制程检验作业流程及不合格品处理流程流程

制程检验作业流程流程图1.0目的为保证产品在生产制程中得到有效检验作业,控制制程品质,降低制程返工、报废,提升产品合格率,提高不良出来的时效性,特制定本作业流程。
2.0 范围适用于(备料车间、白身车间、油漆车间、包装车间)生产过程中的检验与控制及不良品处理。
3.0 职责3.1 PMC部:计划课负责生产指令的下达,参与生产异常处理;仓务课负责完成不良品的回仓分类保管、标识确认及不良品退料的督促工作。
3.2 各生产车间:负责制程产品材料确认,首件产品品质确认及生产过程中的自检、互检工作。
反馈、参与生产异常处理;3.3品管部:首件产品确认及生产过程中的巡检、完工后检验,反馈、主导或参与品质异常处理工作,并对数据记录保存、统计、分析、改善,持续改善;3.4 相关部门:主导或参与品质异常处理及异常分析工作。
4.0 作业程序4.1 PMC部下发《生产日计划》给各生产车间主管,各生产车间主管根据《生产日计划》,组织安排操作工做好生产前的准备工作;4.2 各车间组长、技术员准备工装夹具、测量量具、签样等,按样品或产品工程作业标准书等准备物料进行生产。
备料、白身、总装车间:工装夹具、测量量具、签样、作业指导书、图纸、模具等。
油漆车间:色板、签样、作业指导书、图纸等。
包装车间: 签样、作业指导书、图纸、产品包装示意图、模具等。
4.3组长、技术员对首件先自检,合格报制程检验员对首件进行检验,详细参考《首件检验控制卡》。
4.4制程检验员全检或按规定频次(正常情况下每天不少于6次)及工艺图纸等要求巡检各工序制程品质状况,巡检要有相关侧重点,填写巡检记录,若不符图纸和工艺要求,则知会操作员异常状况;当生产操作工自检发现不良现象时及时隔离和标识;当产生不良品超标时,发现人即时通知本组组长到现场确认,组长到现场确认后,按《生产异常提报控制卡》进行操作,必要时组长填写《品质异常报告和处理单》交责任单位处理(来料引起的不良交品管部处理;制程引起的不良交本部车间主管处理)。
驻外QC职责及流程

驻外QC职责及工作流程一、岗位职责:针对广州地区及附近地区的所有货品(主要针对牛仔裤、内衣、鞋子等)进行全检检验,根据公司发展和体系管理的需要以及本部门质量检验和检测工作计划和目标,保证检验结果的准确性和及时性,对产品异常情况即时处理,产品品质评估报表的作成。
二、工作流程:生产部跟单发周计划给质检部文员→质检部文员做计划安排(查货样提前一周给到质检部)→面料成衣测试员对大货查货样检测→合格后质检部文员提前三天通知驻外QC按标准对大货进行查货(不合格工厂返修直至合格才检品)→大货查验合格后通知工厂按良品实际数量发货→写好送货清单及评估报表及时传送公司(以邮件和传真形式及时发回公司)→质检部文员根据清单及日期及时告知生产跟单→生产跟单根据工厂发货日期密切关注送货周期→到仓后质检人员及时对广州过来货品进行抽检(牛仔裤)除外→合格的通知质检部文员做单入仓(不合格品通知生产跟单退工厂返修)三、主要职责及权限1.对广州周边地区的产品查验并及时做好产品检验结果记录2.对产品的质量判定以及不合格品处理,对查验后进仓货品的合格率负责3.对工厂不合格产品迅速做出判断及处理,对不能判定的提出意见或上报领导4.负责做好每月的工作总结四、日常工作1.严格依据本公司成品检验标准对产品进行检验2.提前做出准确查货计划,读懂查货样,对大货生产时出现的问题要有预见性3.规范、完整做好检验结果记录,并将检验报告及时提交部门负责人4.客观、公正地做出检验判定5.对不合格品及时作出处理并及时汇报主管6.及时向主管领导反映公司产品质量状况7.积极主动与跟单员做好配合,对大货有疑虑的及时回报相关部门确认五、产品检验后管理工作及工作要求1、制程控制管理要求1.1驻外QC对所在工厂生产的货品查验确认(必须是全尺寸及外观的检查)1.2按照公司的生产订单、检验标准书、生产注意事项、查货样等为标准对大货进行品质检验1.3驻外QC需每天将所管辖内的生产厂商之产品检查评估报表进行整理统计后以邮件形式发送部门负责人1.4每天及时将生产厂商在生产过程中所发现的品质异常记录,并每周以图片、文字方式以邮件形式发送部门负责人1.5每周对负责的各生产厂商之品质状况进行统计(如:品质异常统计、出货品质统计等),并将结果以邮件形式发送部门负责人1.6即时将公司所要求的品质目标传达到生产第一线,并每次查验时对工厂实施的状况跟踪与确认1.7定期对所负责之生产厂商整体稽核和考评。
QC工作流程(含各工序5个)

生产部门挑选/加工/翻修后的产品要 再次摆放在待检区内通知QC复查,直 至产品检验合格为止。
入库/转下工序
通过QC检验合格,产品标签上盖有QC 合格印章,或特采印章后产品才可入
库或转入下一部门生产。
编号
QC工作流程
生效日期 2020年11月10日
版本
1.0
制程品质异常处理流程
保密级别:C 级
第5页 共6页
生产上线
生产部根据PMC排产计划,领取合格物 料安排生产。
生产技术 部
调机或试组装 OK
技工/组长自检 NG
OK
NG
首件确认表 (不合格)
品管确认 OK
记录并签发 临时生产样板
员工操作前经生产技工/组长按图纸或 工艺要求调试机器、模具、夹具、试 装配,制作首件确认产品(有模号的 产品不同模号要各制作1件或多件)。
批量生产
生产部在接到QC的首件确认表和合格 的临时生产样板后,安排批量生产。
NG 生产组长
IPQC
员工自检 OK
QC巡检
NG
做巡检记录 不合格标识
OK
做巡检记录
生产组长 QC组长 不
合格处理
报 废
特 用采
使
挑 修选
翻
OK
入待检区
异常改善 效果确认
操作员在生产中每隔半小时或生产出 50--100PCS产品后要对照样板自检, 看产品的外观、形状是否出现变异后 有漏工序的现象。发现异常要及时通 知生产管理人员或QC确认处理。
现场做出改善措施后,QC要在1小时内 确认改善措施是否实施或改善的效 果,向上级(组长)汇报。
编号
QC工作流程
生效日期 2020年11月10日
制程品质异常管理程序(含表格)

制程品质异常管理程序(IATF16949-2016/ISO9001-2015)1.0目的为了快速对应生产过程中发生的品质异常并及时采取相应的纠正预防措施,特制定此规定。
2.0范围适用于生产过程中因设备、材料、工艺等发生异常时影响到产品质量的处理。
3.0定义3.1当生产过程的产品品质影响因素发生不符合常规变化,称之为品质异常。
异常的通常表现处理方式1 出现到目前为止,从未发生过的影响功能的或致命不良时 2S(立即反应、快速解决)2 工程直通不良率超过5%时3 同样的不良连续发生,且不良数达到5个4 按作业指导文件无法进行生产时5 设备、仪器不能正常工作而不能保证质量时6 材料发生变异时7 生产/储存环境发生变化可能导致产品质量无法保证时 8 品管巡检发现致命不良1件或以上时 9物料发生混乱时10 首检发现重大质量缺陷时3S11 工装夹具、辅料发生环境有害物质污染时,等等 12 制程直通不良率超15%时3.2异常发生处理的S.S.S 机制(3S 原则):异常快速反应处理机制,即异常发生时,需立即反应、马上停止、快速解决处理的机制。
SOON:立即反应;STOP:马上停止;SOLVE:快速解决。
4.0职责4.1制造部负责异常问题的数据收集、汇总、报告、传达;4.2品管部负责对制程异常的监控,异常对策措施的实施跟进及验证;4.3出现严重品质不良时,制造部和品管部课长或以上领导有权立即停止生产;4.4品管部负责原材料(包括内制品)异常统筹处理以及主持召开会议;4.5工程部负责除原材料问题以外生产异常的统筹处理以及主持召开会议。
5.0作业程序6.7.责任部门主导对异常点进行原因分析,制定相应的改善对策方案,并进行水平展开,确保类似机种、类似问题能得到有效预防;6.8.《异常处理对策报告书》由责任部门负责整理、编制,并与对策会议结束后2小时内发行到所有的关联部门;责任部门6.9.各关联部门按异常对策报告的要求执行改善工作;6.10.如涉及到材料、工艺、业务流程等方面的变更,则需按《4M 变更管理规定》、《工程管理程序》、《文件管理程序》等文件的要求进行;6.11.如经分析,在线、在库或已发货的产品也存在同样的异常点(或有质量隐患),由品管部负责进行调查、处理。
品质异常处理流程
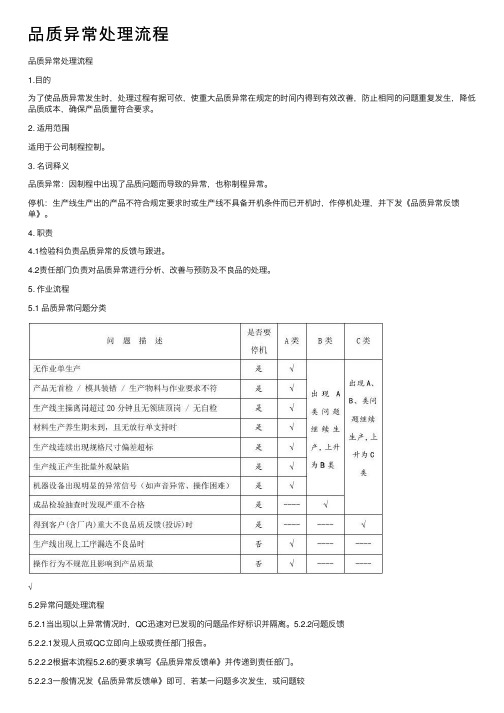
品质异常处理流程品质异常处理流程1.⽬的为了使品质异常发⽣时,处理过程有据可依,使重⼤品质异常在规定的时间内得到有效改善,防⽌相同的问题重复发⽣,降低品质成本,确保产品质量符合要求。
2. 适⽤范围适⽤于公司制程控制。
3. 名词释义品质异常:因制程中出现了品质问题⽽导致的异常,也称制程异常。
停机:⽣产线⽣产出的产品不符合规定要求时或⽣产线不具备开机条件⽽已开机时,作停机处理,并下发《品质异常反馈单》。
4. 职责4.1检验科负责品质异常的反馈与跟进。
4.2责任部门负责对品质异常进⾏分析、改善与预防及不良品的处理。
5. 作业流程5.1 品质异常问题分类√5.2异常问题处理流程5.2.1当出现以上异常情况时,QC迅速对已发现的问题品作好标识并隔离。
5.2.2问题反馈5.2.2.1发现⼈员或QC⽴即向上级或责任部门报告。
5.2.2.2根据本流程5.2.6的要求填写《品质异常反馈单》并传递到责任部门。
5.2.2.3⼀般情况发《品质异常反馈单》即可,若某⼀问题多次发⽣,或问题较严重,可能会导致批量不合格或客户重⼤投诉时。
检验科发出《纠正和预防措施处理单》,要求责任部门改善。
5.2.3异常问题处理5.2.3.1当缺陷不影响产品的性能(上表不需停机的问题),仅外观不良、⾮关键尺⼨超差时或问题未最终确认时,在得到检验科长级或⼚长同意后,不需要停机,可进⼀步确认或执⾏在线分选。
5.2.3.2当⽣产线出现异常时(上表中需停机的问题),相关⼈员参照本流程5.2.4的要求,暂停有问题的机器或⼯位的操作。
5.2.4停机的时机5.2.4.1 出现上表中需要停机时,QC直接下达停机指令,即上述表中所致A类问题,员⼯/主操/领班应主动停机。
5.2.4.2 出现需要停机时,QC直接下达停机指令,相关部门不执⾏的,QC领班跟进处理。
即上升为B类问题。
5.2.4.3 出现需要停机时,QC及QC领班先后要求停机,相关部门仍不执⾏的,及时反馈到检验科长,由检验科长跟进处理,即上述的C类问题。
IPQC(制程控制)工作流程与方法

IPQC(制程控制)工作流程与方法IPQC(InPut Process Quality Control)中文意思为制程控制,是指产品从物料投入生产到产品最终包装过程的品质控制。
由于IPQC采用的检验方式是在生产过程中的各工序之间巡回检查,所以又称为巡检。
IPQC一般采用的方式为抽检,检查内容一般分为对各工序的产品质量进行抽检、对各工序的操作人员的作业方式和方法进行检查、对控制计划中的内容进行点检。
1IPQC目的产品实现的过程是一个复杂的人机交互的系统,由不同的工序构成, 在这个过程中,既有物流,又有信息流,要想使输出满足客户要求,就必须做到如下几个方面:1.保证输入质量2.机器设备稳定,有充分的能力,人员严格按标准作业3.与产品质量密切相关的各关键参数(CTQ)处于稳定受控状态4.信息准确,完整,及时,能发挥指导作用5.有效的工序监控机制,能及时发现过程的异常6.向前反馈机制使过程能及时对异常进行修正7.向后反馈机制能有效防止不良流失8.产品初末件审核,提供班次质量保证9.工序接口顺畅,防止资源浪费以上各方面的执行有赖于IPQC的持续努力,而正是有了以上的支持,过程才是真正意义上的,保证输出质量的过程,所以IPQC的工作,实现了流程向过程的过渡,使输出不再是输入的简单相加,而是数量和质量上增值。
2IPQC工作流程简单的说:工作内容包括首件检查、各类变更文件的跟踪。
4M1E的巡查。
发现异常的提出、跟踪与验证。
详细的说:过程检验(IPQC,in process quality contrl)目的是为了防止出现大批不合格品,避免不合格品流入下道工序去继续进行加工。
因此,过程检验不仅要检验产品,还要检定影响产品质量的主要工序要素(如 4MIE)。
实际上,在正常生产成熟产品的过程中,任何质量问题都可以归结为4M1E中的一个或多个要素出现变异导致,因此,过程检验可起到两种作用:1. 根据检测结果对产品做出判走,即产品质量是否符合规格和标准的要求;2. 根据检测结果对工序做出判定,即过程各个要素是否处于正常的稳定状态,从而决定工序是否应该继续进行生产。
- 1、下载文档前请自行甄别文档内容的完整性,平台不提供额外的编辑、内容补充、找答案等附加服务。
- 2、"仅部分预览"的文档,不可在线预览部分如存在完整性等问题,可反馈申请退款(可完整预览的文档不适用该条件!)。
- 3、如文档侵犯您的权益,请联系客服反馈,我们会尽快为您处理(人工客服工作时间:9:00-18:30)。
PE要现场跟进改善措施实施的效果,QC要在1小时后再次复查异常产品的改善情况。
改善合格
改善不合格异常问题改善合格,QC要记录在相关报告上,改善不合格,要及时通知生产课或生产技术课再分析处理。
记录结案修订标准
生产技术课确认
严重异常
此异常处理流程只针对生产过程中QC 在巡检(抽查)中发现的品质异常后的处理方法。
轻微异常本部门可以改善的异常生产技术课
确认第4页 共6页
1.1
生产部可针对异常分析,是本部门原因可以改善的及时安排处理,还是其它因素本部门无法控制改善,回复给QC或QC组长。
生产部门无法解决的异常,要及时通知到生产技术课去协助生产改善,此时生产技术课应及时分析、处理。
本部门无法改善的异常
生产主导改善
轻微的异常QC告诉员工和生产组长要求改善。
如果严重异常不但要告诉员工、组长,还要通知到生产主管要求改善。
生产员工与组长改善异常要分情况,属员工操作不当或不良缺陷轻微,比例不大为轻微品质异常。
非人为因素或不良缺陷严重、比例很大、产品尺寸功能不良为严重品质异常。
QC巡检中发现品质异常
QC工作流程
制程品质异常处理流程
生效日期改善方案实施
汇报高层管理改善合格PE要对工艺、检验标准做的修改。
多次改善无效果,QC开不合格处理报告向公司高层提出协助处理。
无论是生产部/技术部PE都要对异常及时进行分析处理,制定出解决方案,时间要求在接到异常改善通知后1小时内,不超出2小时就有改善方案。
改善方案
版本
改善效果验证
对制定出的改善措施生产部要及时安排实施,并跟进可行性,有问题及时反映出来。
(不能再按之前方式生产)
2020年4月17日编号WI-PG-011制程巡检IPQC将检验异常信息如实填入制程异常处理报告,并附上不良样品。
制程异常处理报告。