直插式元器件封装技术
单列直插式封装(SIP)
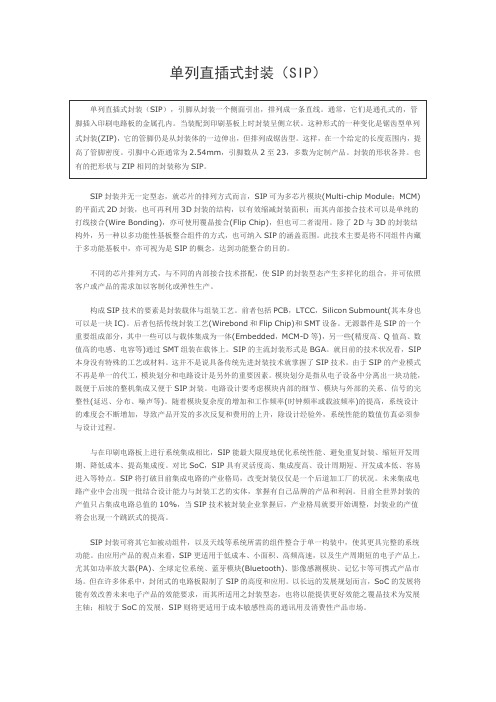
单列直插式封装(SIP)SIP封装并无一定型态,就芯片的排列方式而言,SIP可为多芯片模块(Multi-chip Module;MCM)的平面式2D封装,也可再利用3D封装的结构,以有效缩减封装面积;而其内部接合技术可以是单纯的打线接合(Wire Bonding),亦可使用覆晶接合(Flip Chip),但也可二者混用。
除了2D与3D的封装结构外,另一种以多功能性基板整合组件的方式,也可纳入SIP的涵盖范围。
此技术主要是将不同组件内藏于多功能基板中,亦可视为是SIP的概念,达到功能整合的目的。
不同的芯片排列方式,与不同的内部接合技术搭配,使SIP的封装型态产生多样化的组合,并可依照客户或产品的需求加以客制化或弹性生产。
构成SIP技术的要素是封装载体与组装工艺。
前者包括PCB,LTCC,Silicon Submount(其本身也可以是一块IC)。
后者包括传统封装工艺(Wirebond和Flip Chip)和SMT设备。
无源器件是SIP的一个重要组成部分,其中一些可以与载体集成为一体(Embedded,MCM-D等),另一些(精度高、Q值高、数值高的电感、电容等)通过SMT组装在载体上。
SIP的主流封装形式是BGA。
就目前的技术状况看,SIP 本身没有特殊的工艺或材料。
这并不是说具备传统先进封装技术就掌握了SIP技术。
由于SIP的产业模式不再是单一的代工,模块划分和电路设计是另外的重要因素。
模块划分是指从电子设备中分离出一块功能,既便于后续的整机集成又便于SIP封装。
电路设计要考虑模块内部的细节、模块与外部的关系、信号的完整性(延迟、分布、噪声等)。
随着模块复杂度的增加和工作频率(时钟频率或载波频率)的提高,系统设计的难度会不断增加,导致产品开发的多次反复和费用的上升,除设计经验外,系统性能的数值仿真必须参与设计过程。
与在印刷电路板上进行系统集成相比,SIP能最大限度地优化系统性能、避免重复封装、缩短开发周期、降低成本、提高集成度。
DIP双列直插式封装技术

DIP
DIP封装(Dual In-line Package),也叫双列直插式封装技术,双入线封装,DRAM的一种元件封装形式。
指采用双列直插形式封装的集成电路芯片,绝大多数中小规模集成电路均采用这种封装形式,其引脚数一般不超过100。
DIP 封装的CPU芯片有两排引脚,需要插入到具有DIP结构的芯片插座上。
当然,也可以直接插在有相同焊孔数和几何排列的电路板上进行焊接。
DIP封装的芯片在从芯片插座上插拔时应特别小心,以免损坏管脚。
DIP封装结构形式有:多层陶瓷双列直插式DIP,单层陶瓷双列直插式DIP,引线框架式DIP(含玻璃陶瓷封接式,塑料包封结构式,陶瓷低熔玻璃封装式)等。
DIP封装具有以下特点:
适合在PCB(印刷电路板)上穿孔焊接,操作方便。
芯片面积与封装面积之间的比值较大,故体积也较大。
最早的4004、8008、8086、8088等CPU都采用了DIP封装,通过其上的两排引脚可插到主板上的插槽或焊接在主板上。
在内存颗粒直接插在主板上的时代,DIP 封装形式曾经十分流行。
DIP 还有一种派生方式SDIP(Shrink DIP,紧缩双入线封装),它比DIP的针脚密度要高6六倍。
直插式电容封装及尺寸
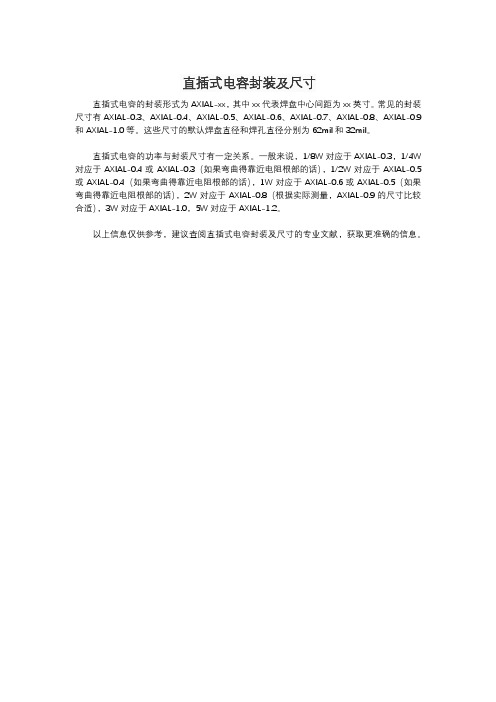
直插式电容封装及尺寸
直插式电容的封装形式为AXIAL-xx,其中xx代表焊盘中心间距为xx英寸。
常见的封装尺寸有AXIAL-0.3、AXIAL-0.4、AXIAL-0.5、AXIAL-0.6、AXIAL-0.7、AXIAL-0.8、AXIAL-0.9和AXIAL-1.0等。
这些尺寸的默认焊盘直径和焊孔直径分别为62mil和32mil。
直插式电容的功率与封装尺寸有一定关系。
一般来说,1/8W对应于AXIAL-0.3,1/4W 对应于AXIAL-0.4或AXIAL-0.3(如果弯曲得靠近电阻根部的话),1/2W对应于AXIAL-0.5或AXIAL-0.4(如果弯曲得靠近电阻根部的话),1W对应于AXIAL-0.6或AXIAL-0.5(如果弯曲得靠近电阻根部的话),2W对应于AXIAL-0.8(根据实际测量,AXIAL-0.9的尺寸比较合适),3W对应于AXIAL-1.0,5W对应于AXIAL-1.2。
以上信息仅供参考,建议查阅直插式电容封装及尺寸的专业文献,获取更准确的信息。
电子产品中的封装技术有哪些种类
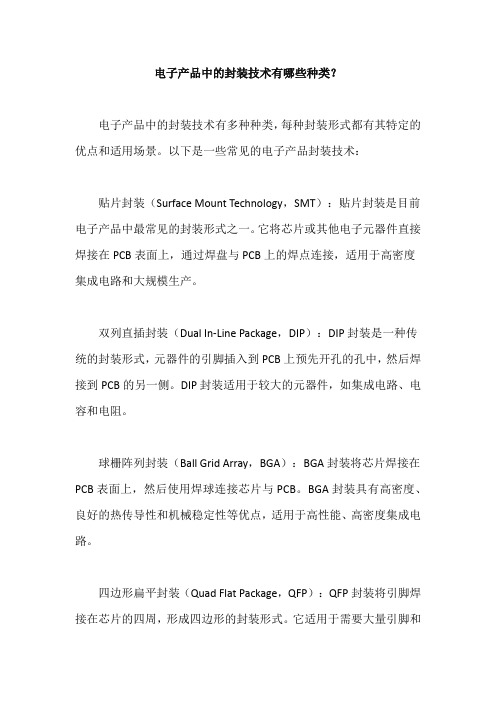
电子产品中的封装技术有哪些种类?电子产品中的封装技术有多种种类,每种封装形式都有其特定的优点和适用场景。
以下是一些常见的电子产品封装技术:贴片封装(Surface Mount Technology,SMT):贴片封装是目前电子产品中最常见的封装形式之一。
它将芯片或其他电子元器件直接焊接在PCB表面上,通过焊盘与PCB上的焊点连接,适用于高密度集成电路和大规模生产。
双列直插封装(Dual In-Line Package,DIP):DIP封装是一种传统的封装形式,元器件的引脚插入到PCB上预先开孔的孔中,然后焊接到PCB的另一侧。
DIP封装适用于较大的元器件,如集成电路、电容和电阻。
球栅阵列封装(Ball Grid Array,BGA):BGA封装将芯片焊接在PCB表面上,然后使用焊球连接芯片与PCB。
BGA封装具有高密度、良好的热传导性和机械稳定性等优点,适用于高性能、高密度集成电路。
四边形扁平封装(Quad Flat Package,QFP):QFP封装将引脚焊接在芯片的四周,形成四边形的封装形式。
它适用于需要大量引脚和高性能的集成电路。
无尘球栅阵列封装(Flip Chip Ball Grid Array,FCBGA):FCBGA 封装是一种高性能封装形式,它将芯片翻转到PCB表面,然后使用焊球连接芯片与PCB。
FCBGA封装具有较高的密度、较低的电感和电阻,适用于高性能计算机芯片和图形处理器。
裸片封装(Chip-on-Board,COB):COB封装是一种将裸片直接粘贴到PCB表面上,并用线缆进行连接的封装形式。
COB封装适用于高密度、低成本和大规模生产的应用场景。
以上列举的封装形式只是电子产品中常见的几种,随着技术的不断发展和创新,还有其他更多种类的封装形式出现,以满足不同产品的需求和应用场景。
常见封装类型
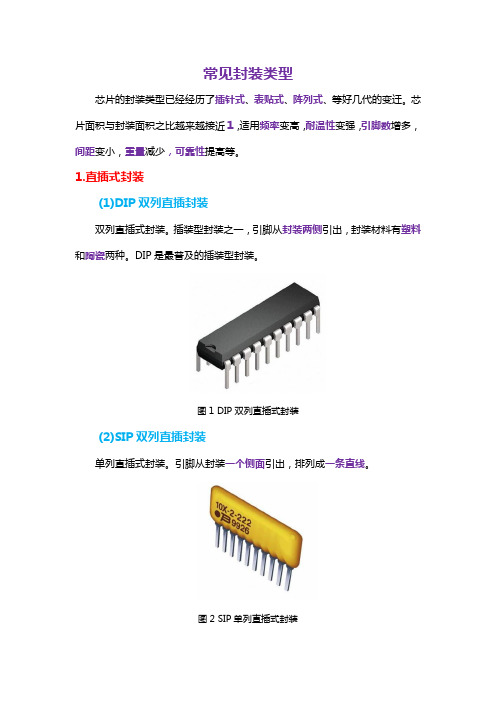
常见封装类型
芯片的封装类型已经经历了插针式、表贴式、阵列式、等好几代的变迁。
芯片面积与封装面积之比越来越接近1,适用频率变高,耐温性变强,引脚数增多,间距变小,重量减少,可靠性提高等。
1.直插式封装
(1)DIP双列直插封装
双列直插式封装。
插装型封装之一,引脚从封装两侧引出,封装材料有塑料和陶瓷两种。
DIP是最普及的插装型封装。
图1 DIP双列直插式封装
(2)SIP双列直插封装
单列直插式封装。
引脚从封装一个侧面引出,排列成一条直线。
图2 SIP单列直插式封装。
直插式红光LED的封装工艺简介

摘要本文以直插式红光 LED 的封装为例,通俗的描述了 LED 的封装工艺流程。
尤其对其中主要的固晶、焊线和灌胶工序分别从工序目的,重点及操作注意事项进行了表述。
由于 LED 芯片的两个电极很小,只有在显微镜下才能看见,因此在制作工艺上,除了要对 LED 芯片的两个电极进行焊接,从而引出正极、负极之外,同时还需要对 LED 芯片和两个电极进行保护。
LED 的封装的任务是将外引线连接到 LED 芯片的电极上,同时保护好 LED 芯片,不让其受到机械、热、潮湿及其它种种的外来冲击,并且起到提高光取出效率的作用。
LED 的封装形式多种多样,图 1 为直插式 LED 封装形式。
本文将以直插式红光 LED 为例介绍 LED 的封装流程。
直插式 LED封装又称Lamp-LED 封装,引脚式封装。
引脚式封装采用引线架作为各种封装外型,如直径为 5 mm 的圆柱型(简称Φ5)封装的引脚,图 2 为引脚式封装结构。
图 3 为红光 LED 的生产流程,依次是扩片、固晶、烘烤、焊线、灌胶、烘烤、一切、测试、二切和包装。
其中主要的工序是固晶、焊线、灌胶和测试。
扩片是对芯片的一个处理,为固晶做准备。
它是对黏结芯片的膜进行扩张,将排列紧密的 LED 晶片(间距约 0.1 mm)均匀分开,拉伸LED 芯片的间距(0.6 mm 左右)。
在扩片中要注意上升高度的控制以及割除多余蓝膜时不要把环内的蓝膜割破。
固晶是一个尤为重要的工序,它的目的是将芯片通过银胶或绝缘胶沾到支架上的杯中。
首先是点胶,即在 LED 支架的相应位置点上银胶或绝缘胶。
它的工艺难点在于点胶量的控制,其次是在胶体高度、点胶位置上的要求。
接着将晶片放置好调节芯片位置,通过界面看到芯片两极沿竖直方向,并通过手柄和键盘调节使界面上十字叉位于边缘,然后分别调节前后勾爪使之刚好抓住支架。
再通过调节两侧旋钮调节芯片使之位于杯中心,通过调节内置旋钮使银胶或绝缘胶均匀。
最后进料,点晶、固晶,没有问题就可以连续固晶。
直插式元器件的装配工艺

直插式元器件的装配工艺
直插式元器件的装配工艺如下:
1. 准备工具和材料。
需要准备直插式元器件、焊锡丝、焊接烙铁、夹子等工具和酒精、棉签等材料。
2. 准备PCB。
将PCB放在工作台上,清洗表面,检查是否存在短路、开路等问题。
3. 制定焊接计划。
根据PCB上元器件的位置和数量,制定焊接计划,确定哪些元器件先焊接。
4. 放置元器件。
根据元器件的包装类型和名称,将元器件放置在PCB上。
5. 固定元器件。
使用夹子或手按将元器件固定在PCB上,确保元器件与PCB 贴合紧密。
6. 焊接元器件。
用焊接烙铁将焊锡丝加热,使其融化后覆盖在元器件的焊脚上,等待焊接完全后,用酒精和棉签清洗焊接部位。
7. 检查焊接质量。
检查焊接点是否充分焊接,是否存在短路、开路等问题。
8. 进行功能测试。
将已焊接的电路板连接上电源,进行功能测试,确保电路板能够正常工作。
9. 打标签和封装。
在PCB上打标签,包装并存储。
直插式LED封装工艺
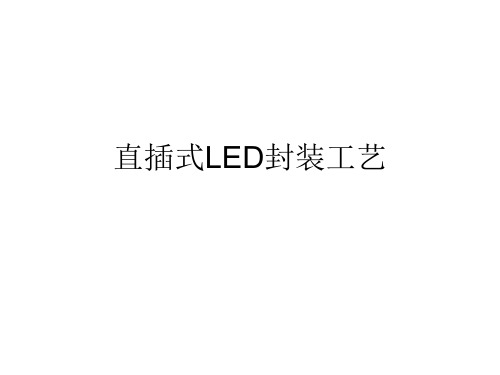
直插式LED
序号 1 2 3 4 5 6 7 8 9 10
设备名称 支架(4#) 脱模剂 模条 模条 银浆 环氧树脂 绝缘胶 金线 荧光粉(防潮) 普通LED芯片
型号/规格 长 Φ5 Φ3 50g/支 50g/支 小功率 大功率 红 黄 绿 普蓝 高亮
单价 26元/k 25元/瓶 6 元 /个 5 元 /个 22元/支 65元/kg 22元/支 1250元/卷 30瓶 20瓶 21元/K 21元/K 65元/K 75元/K 120元/K
直插式LED封装工艺 扩晶 封装工艺---扩晶 直插式 封装工艺
直插式LED封装工艺 扩晶 封装工艺---扩晶 直插式 封装工艺 • 一、目的:对黏结芯片的膜进行扩张,将 排列紧密的LED晶片均匀分Байду номын сангаас,拉伸LED 芯片的间距(约0.6mm) • 二、使用设备:工具-------扩晶机、子母环
1.开扩晶机电源开关。 2. 热板清温度调整至50-60℃,热机 十分钟; 3. 打开扩晶机上压架,在热板上放置 子母环内圈,圆角的一面朝上。 4. 将要扩晶之晶粒胶片放置热板上, 使晶粒位于热板中央,预热30秒之 后,扣紧上压架,晶粒在上,胶片 在下。 5. 拨动下顶开关,顶板顶上,晶粒胶 片开始扩张至定位。 6. 套上子母环,外环圆角的一面朝下。 按上压开关将外圈压紧,再按上压 开关,使上压座回到原位置。 7. 用小刀割除子母环外多余胶片,并 按下顶开关,使顶板回位。 8. 取出已扩好晶粒的子母环。
直插式LED封装工艺 灌胶 封装工艺---灌胶 直插式 封装工艺
一、目的:使灌胶工序受控,保证产品品质。 二、适用范围:灌胶工序 三、使用设备、工具——自动灌胶机/点胶机 四、相关文件:《生产工作》 五、作业规范 5.1先将配好经抽空的胶水从胶杯内壁缓缓倒入 针筒。防止气泡产生. • 5.2调好点胶机气压,时间等参数.选择灌胶用针 头 • 5.3控制出胶速度,出胶过快,透镜中的空气不易 排出 • • • • • •
SMT与DIP
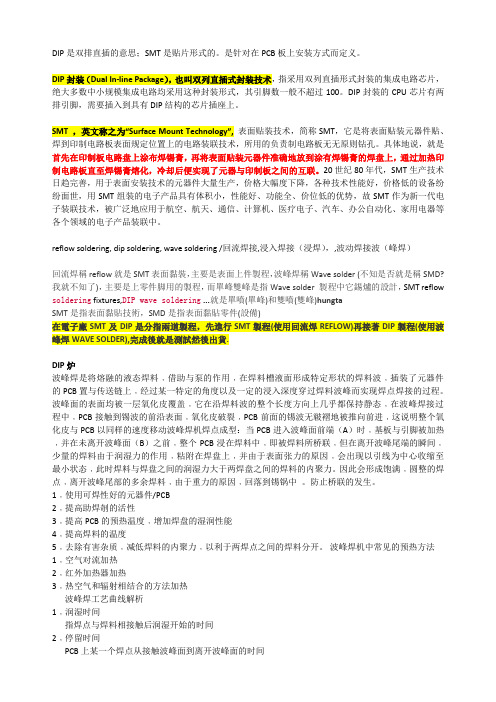
DIP是双排直插的意思;SMT是贴片形式的。
是针对在PCB板上安装方式而定义。
DIP封装(Dual In-line Package),也叫双列直插式封装技术,指采用双列直插形式封装的集成电路芯片,绝大多数中小规模集成电路均采用这种封装形式,其引脚数一般不超过100。
DIP封装的CPU芯片有两排引脚,需要插入到具有DIP结构的芯片插座上。
SMT ,英文称之为“Surface Mount Technology”,表面贴装技术,简称SMT,它是将表面贴装元器件贴、焊到印制电路板表面规定位置上的电路装联技术,所用的负责制电路板无无原则钻孔。
具体地说,就是首先在印制板电路盘上涂布焊锡膏,再将表面贴装元器件准确地放到涂有焊锡膏的焊盘上,通过加热印制电路板直至焊锡膏熔化,冷却后便实现了元器与印制板之间的互联。
20世纪80年代,SMT生产技术日趋完善,用于表面安装技术的元器件大量生产,价格大幅度下降,各种技术性能好,价格低的设备纷纷面世,用SMT组装的电子产品具有体积小,性能好、功能全、价位低的优势,故SMT作为新一代电子装联技术,被广泛地应用于航空、航天、通信、计算机、医疗电子、汽车、办公自动化、家用电器等各个领域的电子产品装联中。
reflow soldering, dip soldering, wave soldering /回流焊接,浸入焊接(浸焊),,波动焊接波(峰焊)回流焊稱reflow就是SMT表面黏裝,主要是表面上件製程,波峰焊稱Wave solder (不知是否就是稱SMD?我就不知了),主要是上零件脚用的製程,而單峰雙峰是指Wave solder 製程中它錫爐的設計,SMT reflow soldering fixtures,DIP wave soldering...就是單噴(單峰)和雙噴(雙峰)hungtaSMT是指表面黏貼技術,SMD是指表面黏貼零件(設備)在電子廠SMT及DIP是分指兩道製程,先進行SMT製程(使用回流焊REFLOW)再接著DIP製程(使用波峰焊WAVE SOLDER),完成後就是測試然後出貨.DIP炉波峰焊是将熔融的液态焊料﹐借助与泵的作用﹐在焊料槽液面形成特定形状的焊料波﹐插装了元器件的PCB置与传送链上﹐经过某一特定的角度以及一定的浸入深度穿过焊料波峰而实现焊点焊接的过程。
常见器件封装技术
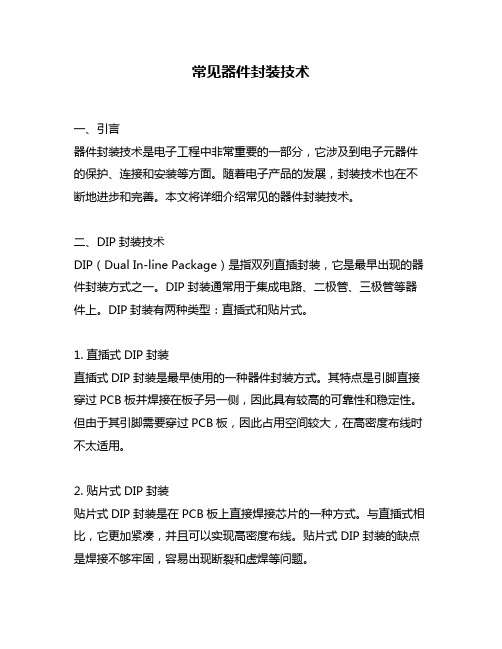
常见器件封装技术一、引言器件封装技术是电子工程中非常重要的一部分,它涉及到电子元器件的保护、连接和安装等方面。
随着电子产品的发展,封装技术也在不断地进步和完善。
本文将详细介绍常见的器件封装技术。
二、DIP封装技术DIP(Dual In-line Package)是指双列直插封装,它是最早出现的器件封装方式之一。
DIP封装通常用于集成电路、二极管、三极管等器件上。
DIP封装有两种类型:直插式和贴片式。
1. 直插式DIP封装直插式DIP封装是最早使用的一种器件封装方式。
其特点是引脚直接穿过PCB板并焊接在板子另一侧,因此具有较高的可靠性和稳定性。
但由于其引脚需要穿过PCB板,因此占用空间较大,在高密度布线时不太适用。
2. 贴片式DIP封装贴片式DIP封装是在PCB板上直接焊接芯片的一种方式。
与直插式相比,它更加紧凑,并且可以实现高密度布线。
贴片式DIP封装的缺点是焊接不够牢固,容易出现断裂和虚焊等问题。
三、SMT封装技术SMT(Surface Mount Technology)是表面贴装技术的缩写,它是一种将元器件直接贴在PCB板上的封装方式。
SMT封装技术已成为现代电子工业中最常用的封装方式之一。
1. SMD封装SMD(Surface Mount Device)是指表面贴装器件,它是一种小型化、轻量化、高可靠性和高集成度的元器件。
SMD封装有多种类型,包括芯片电阻、芯片电容、二极管、三极管等。
2. BGA封装BGA(Ball Grid Array)是一种球网格阵列封装方式,它将芯片与PCB板通过大量金属球连接在一起。
BGA封装具有较高的集成度和可靠性,在计算机CPU等高性能器件上广泛应用。
四、COB封装技术COB(Chip On Board)是指芯片直接粘贴在PCB板上并通过线或银浆连接到PCB板上的一种技术。
COB封装具有体积小、重量轻和可靠性高的特点,因此在手持设备、LED照明等领域得到广泛应用。
常用元器件封装大全
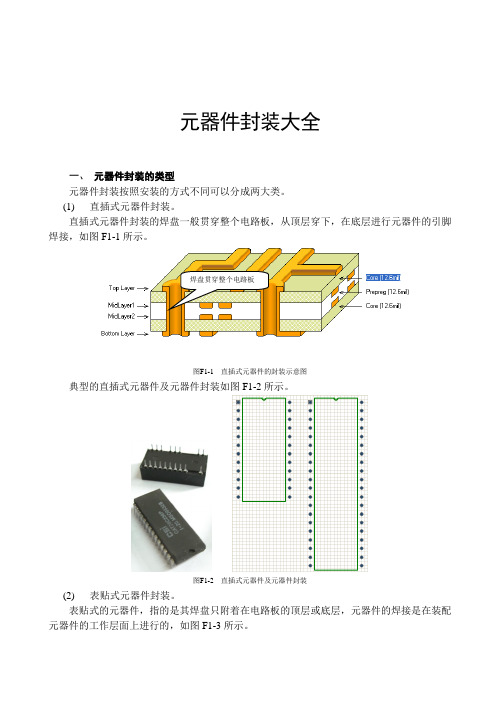
元器件封装大全一、元器件封装的类型元器件封装按照安装的方式不同可以分成两大类。
(1)直插式元器件封装。
直插式元器件封装的焊盘一般贯穿整个电路板,从顶层穿下,在底层进行元器件的引脚焊接,如图F1-1所示。
焊盘贯穿整个电路板图F1-1 直插式元器件的封装示意图典型的直插式元器件及元器件封装如图F1-2所示。
图F1-2 直插式元器件及元器件封装(2)表贴式元器件封装。
表贴式的元器件,指的是其焊盘只附着在电路板的顶层或底层,元器件的焊接是在装配元器件的工作层面上进行的,如图F1-3所示。
Protel 99 SE 基础教程2图F1-3 表贴式元器件的封装示意图典型的表贴式元器件及元器件封装如图F1-4所示。
图F1-4 表贴式元器件及元器件封装在PCB元器件库中,表贴式的元器件封装的引脚一般为红色,表示处在电路板的顶层(Top Layer)。
二、常用元器件的原理图符号和元器件封装在设计PCB的过程中,有些元器件是设计者经常用到的,比如电阻、电容以及三端稳压源等。
在Protel 99 SE中,同一种元器件虽然相同电气特性,但是由于应用的场合不同而导致元器件的封装存在一些差异。
前面的章节中已经讲过,电阻由于其负载功率和运用场合不同而导致其元器件的封装也多种多样,这种情况对于电容来说也同样存在。
因此,本节主要向读者介绍常用元器件的原理图符号和与之相对应的元器件封装,同时尽量给出一些元器件的实物图,使读者能够更快地了解并掌握这些常用元器件的原理图符号和元器件封装。
(1)电阻。
电阻器通常简称为电阻,它是一种应用十分广泛的电子元器件,其英文名字为“Resistor”,缩写为“Res”。
电阻的种类繁多,通常分为固定电阻、可变电阻和特种电阻3大类。
固定电阻可按电阻的材料、结构形状及用途等进行多种分类。
电阻的种类虽多,但常用的电阻类型主要为RT型碳膜电阻、RJ型金属膜电阻、RX型线绕电阻和片状电阻等。
固定电阻的原理图符号的常用名称是“RES1”和“RES2”,如图F1-5(a)所示。
元器件的封装技术解析封装对产品性能的影响
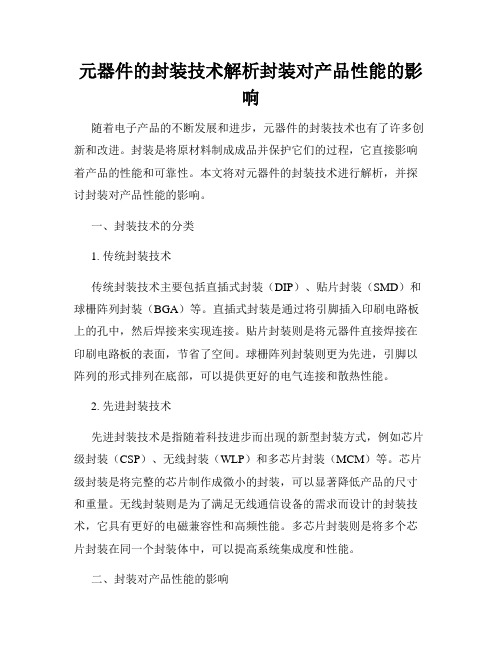
元器件的封装技术解析封装对产品性能的影响随着电子产品的不断发展和进步,元器件的封装技术也有了许多创新和改进。
封装是将原材料制成成品并保护它们的过程,它直接影响着产品的性能和可靠性。
本文将对元器件的封装技术进行解析,并探讨封装对产品性能的影响。
一、封装技术的分类1. 传统封装技术传统封装技术主要包括直插式封装(DIP)、贴片封装(SMD)和球栅阵列封装(BGA)等。
直插式封装是通过将引脚插入印刷电路板上的孔中,然后焊接来实现连接。
贴片封装则是将元器件直接焊接在印刷电路板的表面,节省了空间。
球栅阵列封装则更为先进,引脚以阵列的形式排列在底部,可以提供更好的电气连接和散热性能。
2. 先进封装技术先进封装技术是指随着科技进步而出现的新型封装方式,例如芯片级封装(CSP)、无线封装(WLP)和多芯片封装(MCM)等。
芯片级封装是将完整的芯片制作成微小的封装,可以显著降低产品的尺寸和重量。
无线封装则是为了满足无线通信设备的需求而设计的封装技术,它具有更好的电磁兼容性和高频性能。
多芯片封装则是将多个芯片封装在同一个封装体中,可以提高系统集成度和性能。
二、封装对产品性能的影响1. 电气性能封装对于产品的电气性能起着至关重要的作用。
不同的封装技术会带来不同的信号传输性能和电气特性。
例如,传统的DIP封装由于引脚较长,会导致电阻和电感的增加,从而影响信号传输的速度和品质。
而先进的芯片级封装由于采用短引脚和微细线路,可以显著提高信号传输速度和品质。
2. 热管理性能封装对于产品的热管理性能同样具有重要的影响。
随着电子产品的迅速发展,元器件的功耗也越来越高,因此热管理成为一个重要的问题。
封装的散热设计直接影响着产品的温度分布和散热效果。
先进的封装技术通过采用导热材料和散热结构的优化,可以提高产品的散热性能,降低温度,从而提高产品的可靠性和寿命。
3. 尺寸和重量封装技术对于产品的尺寸和重量也有着直接的影响。
随着电子产品向迷你化和轻量化的发展,封装技术的创新变得更为重要。
常用电子元器件的封装形式
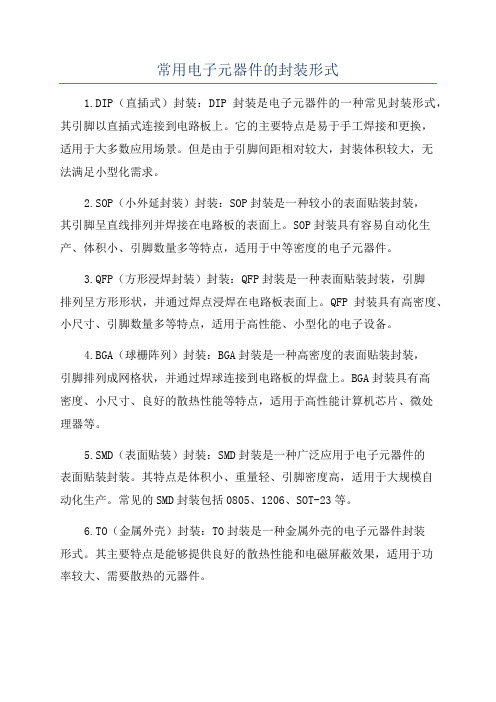
常用电子元器件的封装形式1.DIP(直插式)封装:DIP封装是电子元器件的一种常见封装形式,其引脚以直插式连接到电路板上。
它的主要特点是易于手工焊接和更换,适用于大多数应用场景。
但是由于引脚间距相对较大,封装体积较大,无法满足小型化需求。
2.SOP(小外延封装)封装:SOP封装是一种较小的表面贴装封装,其引脚呈直线排列并焊接在电路板的表面上。
SOP封装具有容易自动化生产、体积小、引脚数量多等特点,适用于中等密度的电子元器件。
3.QFP(方形浸焊封装)封装:QFP封装是一种表面贴装封装,引脚排列呈方形形状,并通过焊点浸焊在电路板表面上。
QFP封装具有高密度、小尺寸、引脚数量多等特点,适用于高性能、小型化的电子设备。
4.BGA(球栅阵列)封装:BGA封装是一种高密度的表面贴装封装,引脚排列成网格状,并通过焊球连接到电路板的焊盘上。
BGA封装具有高密度、小尺寸、良好的散热性能等特点,适用于高性能计算机芯片、微处理器等。
5.SMD(表面贴装)封装:SMD封装是一种广泛应用于电子元器件的表面贴装封装。
其特点是体积小、重量轻、引脚密度高,适用于大规模自动化生产。
常见的SMD封装包括0805、1206、SOT-23等。
6.TO(金属外壳)封装:TO封装是一种金属外壳的电子元器件封装形式。
其主要特点是能够提供良好的散热性能和电磁屏蔽效果,适用于功率较大、需要散热的元器件。
7.COB(芯片上下接插封装)封装:COB封装是一种将芯片直接粘贴到电路板上,并通过金线进行引脚连接的封装形式。
COB封装具有体积小、重量轻、引脚数量多等特点,适用于小型化、高集成度的电子设备。
8.QFN(无引脚封装)封装:QFN封装是一种无引脚的表面贴装封装,引脚位于封装的底部。
QFN封装具有体积小、引脚密度高、良好的散热性能等特点,适用于小型、高性能的电子产品。
9.LCC(陶瓷外壳)封装:LCC封装是一种使用陶瓷材料制成的封装形式,具有较高的耐高温性和良好的散热性能。
smt dip 工艺流程

smt dip 工艺流程SMT(Surface Mount Technology,表面贴装技术)DIP(DualIn-line Package,双列直插封装)是一种电子元器件封装技术,广泛应用于PCB(Printed Circuit Board,印刷电路板)的制造过程。
下面将介绍SMT DIP的工艺流程。
首先,制作PCB板。
制作PCB板是SMT DIP工艺的第一步。
首先,在一块底板上涂覆一层导电铜膜,然后利用光刻技术将电路图案的图层设计转移到铜膜上。
接下来,通过化学蚀刻去除未被光刻出的部分铜膜,然后用钻孔机将所需连接的电路孔钻出。
最后,通过喷锡或喷铝的方式涂覆一层保护层。
接下来,为了保证元器件与PCB的良好连接,需要将元器件进行预处理。
首先,通过焊膏印刷机在PCB上印刷上一层焊膏。
然后,将元器件按照电路图案的要求,精确地放置在相应位置上。
然后是回流焊接。
在回流焊炉中,将印刷有焊膏的PCB放入,然后加热到适当的温度。
在高温下,焊膏会熔化,将元器件与PCB连接起来。
经过冷却固化后,焊接完成。
接下来是清洗。
由于焊接过程中可能会产生焊剂和其他污染物,因此需要进行清洗。
这可以通过喷淋清洗机或浸泡在清洗溶液中来实现。
清洗后,使用热风干燥机对PCB进行干燥。
然后进行质量检测。
质量检测包括两个方面:外观检测和功能测试。
外观检测主要是检查PCB上的焊接点是否完好,是否有断路或短路等问题。
功能测试是通过给PCB输入特定的电信号,来测试PCB的各个功能是否正常工作。
最后是包装。
将通过质量检测的PCB进行组装,装入适当的包装盒中。
这样,SMT DIP的工艺流程就完成了。
综上所述,SMT DIP工艺流程包括制作PCB板、元器件预处理、回流焊接、清洗、质量检测和包装等步骤。
这一过程通过先进的技术保证了电子元器件与PCB板的精确连接,为电子产品的制造提供了关键支持。
元器件封装实物图.doc(实物图,DIP、PLCC、SOP、PQFP、SOJ、TQFP、TSSOP、BGA)

常见元器件封装实物图qqq芯片封装技术知多少前言我们经常听说某某芯片采用什么什么的封装方式,在我们的电脑中,存在着各种各样不同处理芯片,那么,它们又是是采用何种封装形式呢?并且这些封装形式又有什么样的技术特点以及优越性呢?那么就请看看下面的这篇文章,将为你介绍个中芯片封装形式的特点和优点。
一、DIP双列直插式封装DIP(DualIn-line Package)是指采用双列直插形式封装的集成电路芯片,绝大多数中小规模集成电路(IC)均采用这种封装形式,其引脚数一般不超过100个。
采用DIP封装的CPU芯片有两排引脚,需要插入到具有DIP结构的芯片插座上。
当然,也可以直接插在有相同焊孔数和几何排列的电路板上进行焊接。
DIP 封装的芯片在从芯片插座上插拔时应特别小心,以免损坏引脚。
DIP封装具有以下特点:1.适合在PCB(印刷电路板)上穿孔焊接,操作方便。
2.芯片面积与封装面积之间的比值较大,故体积也较大。
Intel系列CPU中8088就采用这种封装形式,缓存(Cache)和早期的内存芯片也是这种封装形式。
二、PQFP塑料方型扁平式封装和PFP塑料扁平组件式封装PQFP(Plastic Quad Flat Package)封装的芯片引脚之间距离很小,管脚很细,一般大规模或超大型集成电路都采用这种封装形式,其引脚数一般在100个以上。
用这种形式封装的芯片必须采用SMD(表面安装设备技术)将芯片与主板焊接起来。
采用SMD安装的芯片不必在主板上打孔,一般在主板表面上有设计好的相应管脚的焊点。
将芯片各脚对准相应的焊点,即可实现与主板的焊接。
用这种方法焊上去的芯片,如果不用专用工具是很难拆卸下来的。
PFP(Plastic Flat Package)方式封装的芯片与QFP方式基本相同。
唯一的区别是QFP一般为正方形,而PFP既可以是正方形,也可以是长方形。
QFP/PFP封装具有以下特点:1.适用于SMD表面安装技术在PCB电路板上安装布线。
插装元器件的封装技术

1958年发明了集成电路,它是完成一定功能的多个晶体管的集成。这 样,3-4个I/O引脚就不够用了,这时的全密封封装仍然采用TO的形式,只 是底座周围的I/O引线更多了。随着Ic集成度的提高,对I/O数要求越来越 高,于是开发出单列直插封装(SIP)、双列直插封装(D1P)、针栅阵列封装 和扁平外形封装等。
底座和盖板都是用加压陶瓷工艺制作,一般是黑色陶瓷,即把氧化铝粉末 润滑剂和粘接剂的混合物压制成所需要的形状,然后在空中烧结成瓷件, 把玻璃浆料印刷到底座和盖板上然后在空气中烧成.对陶瓷底座加热,使 玻璃熔化,将引线框架埋入玻璃中,粘接IC芯片,进行WB,把涂有低温 玻璃的盖板与装好IC芯片的底座组装在一起,在空气中使玻璃社会化,达 到密封.然后镀Ni-Au或Sn.
2、晶体管
各类晶体管的封装类型主要有玻封二极管和金属封装的三极管。普通管有3 根长引线,高频管或需要外壳接地的晶体管有4根长引线,晶体管的金属底座 与c极相通,而e、b两极则通过金属底座的开孔,用玻璃绝缘子隔离,金属帽 与金属底座的边缘进行密封焊接。这就构成了至今仍沿用的To型金属--玻璃绝 缘子全密封封装结构。
也大为降低。
金属外壳封装技术
可容许更高的功率密度,加上HIC能制作远小于PWB基板的线宽和间距, 因此,SMC/SMD和IC芯片的混合组装密度高,而多层布线内层还可以 埋置R、C和IC芯片,使电子产品更易于实现小型化和微型化,而且功率 更大,功能更强.
化学稳定性好,更抗外界环境的腐蚀等.
不足之处:制作工艺复杂,并难以制作平整的大基板,要使用现代化的贴 装设备,必须将小基板拼接成大基板后才行.此外,陶瓷或Si基板的成本 比PWB基板高.
插装元元器件的封装形式主要有PDIP、PGA和HIC用的金属插装外壳 封装。尽管至2002年插装元器件封装特别是PDIP的比例只占所有封装的 10%,但绝对数量仍有91亿块,插装元器件件与SMD在同一块PWB上然 要延用相当长的时间。近几年,PDIP的减少速度正在变慢,在各类大量民 用产品中,插装元器件仍具有强大的生命入。再就是HIC若干年来一直与 IC芯片保持10%的比例,今后一段时间内大体仍将保持这一比例。因此, 用于HIC的金属外壳封装仍将稳步地获得增长。
J型直插器件封装设计

J型直插器件封装设计
针对上述使用情景,J型直插器件封装设计在设计上往往比其他封装结构复杂得多,而且同规格的器件数量也更多,封装的器件体积也更小。
当封装较小的器件时,尤其是针对精密电子元件的J型直插器件封装设计,要求克服紧凑型件密度过密引起的电气接触和不稳定性等问题。
总之,J型直插器件封装设计具有灵活、可靠性好等特点,在集成电路及元器件封装设计中具有重要作用。
在设计及使用过程中,为保障J型直插器件封装的稳定可靠性,应当结合客户的工艺及技术要求合理把握宣传夹头的紧度与封装件的贴合特性,以此达到高质量的机动可靠性要求。
三引脚直插式封装意思

三引脚直插式封装意思《三引脚直插式封装的含义与相关》三引脚直插式封装,简单来说,就是一种电子元件的封装形式。
这种封装具有三个引脚,以直插的方式安装到电路板上。
可衍生注释:在电子电路中,引脚是电子元件与外部电路连接的接口。
三引脚直插式封装中的三个引脚各自有着不同的功能定义,这取决于所封装的具体电子元件,例如可能是电源引脚、接地引脚和信号引脚等。
就像一个小家庭有不同分工的成员一样,每个引脚在电路这个“大家庭”里都扮演着不可或缺的角色。
赏析:这种封装形式有它独特的优势。
从设计角度看,三引脚直插式封装结构简单明了,对于电路设计者来说就像是一把顺手的工具。
它在电路板上的布局比较规整,便于进行电路的规划和布线。
而且,这种封装形式的元件安装相对牢固,在一些对稳定性要求较高的电路中,就像可靠的基石一样。
从维修角度来看,由于引脚直观可见且数目较少,查找故障点或者更换元件都比较容易,仿佛是给维修人员开启了一扇方便之门。
运用片段:例子1:我最近在捣鼓一个小电路,那个三引脚直插式封装的元件可把我折腾坏了,不过也让我对它有了更深的理解。
你看啊,那三个引脚就像三条小尾巴,从元件身体里伸出来。
我在电路板上找对应的接口,就像给三个调皮的小孩找合适的座位一样。
我当时就想,这三引脚直插式封装的设计虽然简单,但真要把它用对地方还得费点心思呢。
我把电源引脚接到电源部分,接地引脚稳稳地连到地线上,信号引脚再连到对应的电路模块。
当整个电路开始工作的时候,我那个高兴劲儿啊,就像打了一场胜仗。
这小小的三引脚直插式封装元件,在整个电路里就像一颗关键的螺丝钉,别看它小,少了它还真不行。
我现在算是明白了,这东西就像隐藏在电路里的小精灵,虽然不起眼,但有着大大的能量。
例子2:我朋友小王是个电子迷,他整天就跟那些电子元件打交道。
有一次,他拿着一个三引脚直插式封装的芯片给我看。
他说:“你瞧,这东西可神奇了。
”我就纳闷了,这三个引脚有啥特别的呢?他笑着跟我解释,这就好比是一个有三个触角的小生物,每个触角都有特殊的使命。
- 1、下载文档前请自行甄别文档内容的完整性,平台不提供额外的编辑、内容补充、找答案等附加服务。
- 2、"仅部分预览"的文档,不可在线预览部分如存在完整性等问题,可反馈申请退款(可完整预览的文档不适用该条件!)。
- 3、如文档侵犯您的权益,请联系客服反馈,我们会尽快为您处理(人工客服工作时间:9:00-18:30)。
DIP封装的工艺流程
引线框贴装 芯片贴装 引线键合 密封
引脚成形 检漏
引脚电镀 标记
当粘贴压焊的芯片通过了目检测试后,接下来就 进行保护性封装结构;主要的封装方法有:陶瓷DIP 封装技术、多层CDIP封装技术和塑料DIP封装技术。
封装方法 密封型
•焊接 •焊接盖 •玻璃封装盖或顶部 陶瓷DIP封装技术和多层 CDIP封装技术
粘接剂的作用:在生瓷片制作过程中起粘接陶瓷 颗粒的作用;
溶剂的作用:一是在球磨过程中能使瓷粉均匀分
布;二是使生瓷片中的溶剂挥发后形成大量的微孔, 这种微孔能在以后的生瓷叠片层压过程中致使金属 线条的周围瓷片压缩而不损伤金属布线;
增塑剂的作用:能使生瓷片曾现“塑性”或柔性。
塑料DIP封装技术
因封装材质为塑料,所以用PDIP表示; 在PDIP封装中,因为IC芯片的I/O引脚数多, 再加上芯片也相对较大,这使得芯片与塑封 料的应力匹配更显重要。
目前,主要的印字手段有墨印法和激光印字法。墨 印法适用于所有的封装材料且附着性好,其工艺是先 用平版印字机印字,然后将字烘干。
激光印字特别适用于塑料封装体的印字方法,信息 被永久地刻入到封装体的表面,对深色材料的封装体 又能提供较好的对比度。另外,激光印字的速度快且 无污染,因为封装体表面不需要外来材料加工也不需 要烘干工序。缺点是一旦印错字或器件状况改变了就 很难改正。
为改善塑料封装环氧树脂的性能,还要添加一 定的填料。主要填料有:石英粉(二氧化硅)、二 氧化钛、氧化铝、氧化锌、无机盐或有机纤维等。
为使PDIP具有一定的颜色,还要添加一些调色 素,如黑色(碳黑)、红色(三氧化二铁)、白色 (二氧化钛)等。
为了塑封后易于脱膜,还要加入适量的脱膜剂。
塑料DIP封装全工艺过程:
5.1.2 分类及特点
根据封装接线端子的排布方式对其进行分类,可分 为引脚插入型和表面贴装型。
1、引脚插入型:
单列直插式封装(SIP) 双列直插式封装(DIP) Z型引脚直插式封装(ZIP) 收缩双列直插式封装(S-DIP) 窄型双列直插式封装(SK-DIP) 针栅阵列插入式封装(PGA)
2、表面贴装型:
5.清除塑料毛刺,还要对引线框架的引线连接处切筋,并打弯 成90度,就成为标准的PDIP;
6.对PDIP进行高温老化筛选,并达到充分固化,再经测试, 分选打印包装就可以成品出厂。
封装体印字
封装体加工完毕后,必须对其加注重要的识别信息, 封装体上典型的信息码有产品类别、器件规格、生产 日期、生产批号和产地。
非密封型 •树脂压模 •顶部滴胶封装 塑料DIP封装技术
CDIP封装工艺全过程
(1)底座和盖板的制作:粉末压制法工艺制作是用氧 化铝粉末、润滑剂和粘接剂的混合物压制成所需要的 形状,然后在空气中烧结成陶瓷件。
(2)具体封装工艺:
a. 芯片用Au浆料固定在陶瓷底座上; b. Al金属引线(Fe/Ni线)一端与芯片焊区键合连接,另 一端键合在引脚上; c. 在陶瓷盖板和底座上刷玻璃浆料,盖板盖在装好IC芯 片的底座组装件上;在空气中使玻璃溶化,使芯片密封在 陶瓷之中与外界隔离,玻璃即起到密封作用,还起到应力 缓和作用。 d. 经过玻璃过渡,使陶瓷与金属引线的热膨胀系数相匹 配。
这时,各类晶体管的封装类型主要有玻璃封装的 二极管和金属封装的三极管。普通管封装有3根长引 线,高频管或需要外壳接地的晶体管封装有4根长引 线;
晶体管的金属底座与c极相通,而e、b两极则通过 金属底座的开孔,用玻璃绝缘子隔离,金属帽与金属 底座的边缘进行密封焊接,这就构成了至今仍沿用的 TO型封装——圆柱形外壳封装。当时用晶体管组装的 典型电子整机首推黑白电视机。
5.2 插装技术
5.2.1 TO型封装
TO金属封装工艺: 1. 将芯片固定在外壳底座的中心,常常采用Au-Sb 合金共熔法或导电胶粘接固化法使晶体管的接地极与底 座间形成良好的欧姆接触(多引脚的TO型结构还可以封 装IC芯片,对于IC芯片,还可以采用环氧树脂粘接固化 法); 2. 在芯片的焊接区与接线柱间用Au丝或AI丝连接起 来;接着将焊好的内引线的底座移至干燥箱中操作,并 通以惰性气体或N2保护芯片; 3. 将管帽套在底座上,利用电阻熔焊法或环形平行 缝焊法将管帽与底座边缘焊牢,并达到密封要求。 TO金属封装是使用最早,应用最为广泛的全密封晶 体管封装结构。
从上述可以看出,晶体管和电子管有一个基本的 共同点:管脚带有引线,适合进行插装,只是晶体管 引脚插装后仍需焊接方能达到可靠连接,而电子管插 脚坚硬,只需与插座紧密接触就能达到可靠连接。
目前,各类插装元器件封装的引脚间距多为 2.54mm。DIP封装已形成4-64个引脚的系列化产品; PGA封装能适应LSI芯片封装的要求,I/O数可达数百 个。
ቤተ መጻሕፍቲ ባይዱ
塑料SIP(PSIP)封装实物图
5.2.3 DIP双列直插式封装
上 世 纪 70 年 代 , 芯 片 封 装 基 本 都 采 用 DIP(Dual ln-line Package)封装,此封装形式在当时具有适合 PCB穿孔安装,布线和操作较为方便等特点。
DIP是指采用双列直插形式封装的集成电路芯片。 目前,绝大多数中小规模集成电路均采用这种封装形 式,其引脚数一般为4-64个,多的也不超过100个;产 品呈系列化,标准化,品种规格齐全,至今仍然大量沿 用。
2.在-65~150℃的环境使用温度范围内能正常工作, 要求玻璃化温度大于150℃。
3.树脂的吸水性要小,并与引线的粘接性能良好,防 止湿气沿树脂—引线界面侵入内部。
4.要有良好的物理性能和化学性能。 5.要有良好的绝缘性能。 6.固化时间短。 7.Na含量低。 8.辐射性杂质含量低。
能连续注塑的热固性环氧系材料正具备这些良 好的特性,已成为国际上通用的材料。近年来,在 提高耐湿性、热导率、降低应力等方面有了明显的 进步。
PSDIP
DIP封装结构具有以下特点:
1.适合PCB的穿孔安装; 2.与TO型封装相比,易于PCB布线; 3.操作方便。
因此,Intel系列CPU中8088就采用这种封装形 式;缓存(Cache)和早期的内存芯片也是采用DIP封 装 ; Intel 公 司 的 CPU 如 8086 、 80286 都 采 用 PDIP 封 装。
1. 塑料封装的引线框架需局部镀Ag的C194铜合金或42号铁 镍合金;
2.将IC芯片用粘接剂粘接在引线框架的中心芯片区,用WB连 接IC芯片的各焊区与局部电镀Ag的引线框架各焊区;
3.将载有IC芯片的引线框架置于塑封模具的下模中,再盖上 上模;
4.将预热过环氧坯料放入树脂腔中,置于注塑机上,加热上下 模具达到150~180℃,这时环氧坯料已经软化熔融并具有一 定的流动性,注塑机对各个活塞加压,熔融的环氧树脂就通 过 注 塑 流 道 挤 流 到 各 个 IC 芯 片 所 在 的 空 腔 中 , 保 温 加 压 约 2~3min即可脱模已成形的塑封件;
5.1 插装器件概述及分类特点 5.1.1 概述 5.1.2 分类及特点
5.2 插装技术 5.2.1 TO型 5.2.2 SIP单列直插式封装 5.2.3 DIP双列直插式封装 5.2.4 PGA针栅阵列插入式封装
5.1 插装器件概述及分类特点
5.1.1 概述
随着晶体管的出现及其质量的稳步提高,特别是 硅平面晶体管的日趋成熟;20世纪50年代末,晶体管 代替电子管已成为席卷全球之势。
电子管封装结构示意图
电子管插装结构示意图
晶体管封装结构示意图
由于晶体管的体积和重量均为电子管的数十分之 一,安装基板可省去笨重的插座,也不需用金属基板 支撑各种元器件了,选用单面酚醛环氧纸质覆铜板 (有机基板)就可胜任,而且这种基板制作工艺简单, 成本低廉,易打孔。
由于晶体管体积小、电压低、耗电省,所以在覆 铜板上刻蚀成所需的电路图形后,元器件穿过通孔焊 接在铜焊区上即可。这样,既提高了生产效率和产量, 又提高了焊接的一致性,从而提高了焊点的质量和电 子产品的可靠性。
外部打磨
塑料封装器件会经过一道额外的工序,称为外 部打磨。
先将基板上的I/O引脚引向一边,用镀Ni、Ag或 Pb-Sn的“卡式”引线卡在基板一边的 I/O焊区上; 接着在卡式引线的I/O焊区上涂上焊膏;然后成批 在再流焊炉中进行再流焊。
通常,它的引线的间距有2.54mm与2.27mm之分。
SIP的插座占的基板面积小,插取自如,SIP的 工艺简便易行,很适于多品种、小批量的HIC及PWB 基板封装,还便于逐个引线的更换和返修。下图为 塑料SIP的结构示意图:
采 用 DIP 封 装 的 CPU 芯 片 有 两 排 引 脚 , 引 脚 间 距 有 2.54mm和1.78mm两种,一般需要插入到具有DIP结构 的芯片插座上使用。当然,也可以直接插在有相同焊 孔数和几何排列的电路板上进行焊接。
PDIP
DIP
PCDIP
FDIP
DIP-tab 部分DIP封装芯片照片
TO8
TO5 TO3
晶体管封装结构示意图
TO塑料封装工艺: 1. 将I/O引线冲制成引线框架,在芯片焊区将芯 片固定,将芯片的各焊区用WB焊到其他引线键合区; 2.按塑封件的大小制成一定规格的塑封模具,模 具有数十个甚至数百个相同尺寸的空腔,每个空腔体 间有细通道相连; 3.将焊接好内引线的引线框架放到模具的各个腔 体中,塑封时,先将塑封料加热至150~180℃,待其 充分软化融融后,再加压将塑封料压到各个腔体中, 略待几分钟固化后,就完成了注塑封装工作; 4.开模,整修塑封毛刺,再切断各引线框架不必 要的连接部分,就成为单独的TO塑封件了; 5.最后切筋,打弯,成形和镀锡。
TO型塑料封装图片
工艺中如何控制好模塑时的压力,粘度,并保持 塑封时的流道及腔体设计之间的综合平衡,是优化模 塑器件的关键。
该封装简便易行,适用于大批量生产,因此成本 低廉。