冷轧开题-11成型
薄板冷轧机轧钢的开题报告1
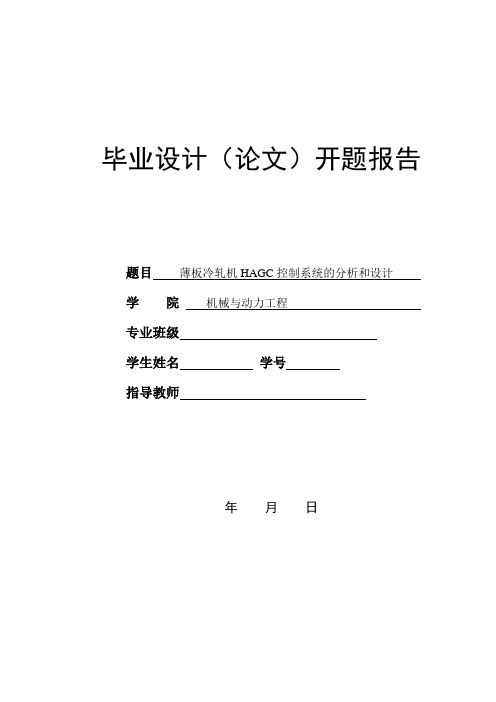
毕业设计(论文)开题报告题目薄板冷轧机HAGC控制系统的分析和设计学院机械与动力工程专业班级学生姓名学号指导教师年月日开题报告填写要求1.开题报告作为毕业设计(论文)答辩委员会对学生答辩资格审查的依据材料之一。
此报告应在指导教师指导下,由学生在毕业设计(论文)工作开始后2周内完成,经指导教师签署意见及系主任审查后生效。
2.开题报告内容必须用黑墨水笔工整书写或按教务处统一设计的电子文档标准格式(可从教务处网址上下载)打印,禁止打印在其它纸上后剪贴,完成后应及时交给指导教师签署意见。
3.学生查阅资料的参考文献理工类不得少于10篇,其它不少于12篇(不包括辞典、手册)。
4.“本课题的目的及意义,国内外研究现状分析”至少2000字,其余内容至少1000字。
毕业设计(论文)开题报告1.本课题的目的及意义,国内外研究现状分析一:冷轧板HAGC的目的和意义1什么是冷轧板HAGCHAGC 液压厚度自动控制系统,是根据设定厚度通过PLC程序模型计算给液压伺服系统相应的信号,以达到想要的厚度值。
响应速度快、控制精度高的优点,。
正在取代电动AGC成为当今新建轧机和欲改造轧机的首选技术,是生产厂家在未来激烈市场竞争中取得优势的重要保证。
2 研究冷轧板HAGC的意义和目的1)我国背景和现状钢铁行业“十二五”规划是指导钢铁行业未来五年发展的纲领性文件。
规划提出钢铁行业的主要发展目标、重点任务和措施;研究分析钢铁行业发展的突出瓶颈,提出突破上述瓶颈的对策建议;研究提出“十二五”期间及到2020年钢铁行业发展的总体思路、指导原则、战略选择和关键举措。
钢铁行业中的板带生产数量大、质量要求高、经济效益显著,因而各国都重视板带钢技术的提高,竞相把最先进的检测、控制技术用于板带轧制生产当中。
目前实际尺寸精度、组织性能都达到较高的水平。
而且随着连轧过程自动化技术的发展,对控制系统操作人员和工艺设计人员的要求也越来越苛刻。
特别是轧制速度普遍提高,基于实际运行或人的直觉来评价控制系统或控制器的优劣,已不可能保证获得较好的控制参数。
冷镦钢低温轧制的研究的开题报告

冷镦钢低温轧制的研究的开题报告一、选题背景冷轧钢材具有多种优点,例如表面光洁、尺寸精度高、机械性能良好等,得到了广泛应用。
但在低温环境下,冷轧钢材的韧性和抗裂性能下降较快,使得其在极端环境下的应用受到限制。
为了解决这个问题,冷镦钢低温轧制的研究得到了越来越广泛的关注。
低温轧制可以通过改变材料的微观组织和化学成分,提高其韧性和抗裂性能,从而适应低温环境下的应用需求。
二、选题意义随着科技的不断发展,低温环境下的应用需求越来越多,例如航空航天、核能、极寒地区等领域。
因此,研究冷镦钢低温轧制的工艺和机理,有助于提高钢材的低温性能,拓展其在低温环境下的应用范围。
三、研究内容本研究将从以下三个方面进行探究:1.低温轧制对冷镦钢微观组织和物理性能的影响。
通过对不同温度、不同变形量的低温轧制试验,对冷镦钢的显微组织、晶格结构和力学性能等进行研究。
2.低温轧制工艺的优化。
结合实验结果,探究低温轧制的最佳工艺参数,包括轧制温度、变形量、冷却速率等,从而获得最佳的材料性能。
3.低温环境下的应用实践。
将优化后的低温轧制工艺应用到实际生产中,以验证其在低温环境下的性能表现。
四、研究方法本研究将采用以下方法:1.试验方法:通过对冷镦钢进行不同工艺条件下的低温轧制试验,获取样品的显微组织、晶格结构和力学性能等数据。
2.材料分析方法:采用扫描电镜(SEM)、透射电子显微镜(TEM)、X射线衍射(XRD)等分析方法,对样品的微观结构进行观察和分析。
3.数据处理及分析:对所得数据进行处理和分析,并通过统计学方法进行参数的拟合和预测。
五、预期成果本研究预计取得以下成果:1.深入理解低温轧制对冷镦钢的微观组织和物理性能的影响,确定最佳的低温轧制工艺参数。
2.通过优化低温轧制工艺,提高冷镦钢的低温韧性和抗裂性能。
3.将优化后的低温轧制工艺应用到实际生产中,为低温环境下的应用提供高性能的冷镦钢材料。
六、研究计划1.前期准备(1个月)文献搜集、基础实验准备、设备调试。
冷挤压成形技术

冷挤压成形技术冷挤压是精密塑性体积成形技术中的一个重要组成部分。
冷挤压是指在冷态下将金属毛坯放入模具模腔内,在强大的压力和一定的速度作用下,迫使金属从模腔中挤出,从而获得所需形状、尺寸以及具有一定力学性能的挤压件。
显然,冷挤压加工是靠模具来控制金属流动,靠金属体积的大量转移来成形零件的。
冷挤压技术是一种高精、高效、优质低耗的先进生产工艺技术,较多应用于中小型锻件规模化生产中。
与热锻、温锻工艺相比,可以节材30%~50%,节能40%~8 0%而且能够提高锻件质量,改善作业环境。
目前,冷挤压技术已在紧固件、机械、仪表、电器、轻工、宇航、船舶、军工等工业部门中得到较为广泛的应用,已成为金属塑性体积成形技术中不可缺少的重要加工手段之一。
二战后,冷挤压技术在国外工业发达国家的汽车、摩托车、家用电器等行业得到了广泛的发展应用,而新型挤压材料、模具新钢种和大吨位压力机的出现便拓展了其发展空间。
日本80年代自称,其轿车生产中以锻造工艺方法生产的零件,有30%~40%是采用冷挤压工艺生产的。
随着科技的进步和汽车、摩托车、家用电器等行业对产品技术要求的不断提高,冷挤压生产工艺技术己逐渐成为中小锻件精化生产的发展方向。
与其他加工工艺相比冷挤压有如下优点:1)节约原材料。
冷挤压是利用金属的塑性变形来制成所需形状的零件,因而能大量减少切削加工,提高材料利用率。
冷挤压的材料利用率一般可达到80%以上。
2)提高劳动生产率。
用冷挤压工艺代替切削加工制造零件,能使生产率提高几倍、几十倍、甚至上百倍。
3)制件可以获得理想的表面粗糙度和尺寸精度。
零件的精度可达IT7~IT8级,表面粗糙度可达R0.2~R0.6。
因此,用冷挤压加工的零件一般很少再切削加工,只需在要求特别高之处进行精磨。
4)提高零件的力学性能。
冷挤压后金属的冷加工硬化,以及在零件内部形成合理的纤维流线分布,使零件的强度远高于原材料的强度。
此外,合理的冷挤压工艺可使零件表面形成压应力而提高疲劳强度。
冷轧工艺
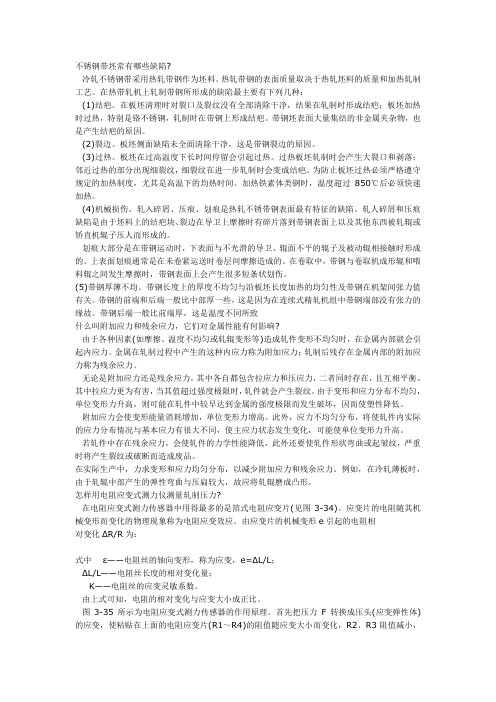
不锈钢带坯常有哪些缺陷?冷轧不锈钢带采用热轧带钢作为坯料。
热轧带钢的表面质量取决于热轧坯料的质量和加热轧制工艺。
在热带轧机上轧制带钢所形成的缺陷最主要有下列几种:(1)结疤。
在板坯清理时对裂口及裂纹没有全部清除干净,结果在轧制时形成结疤;板坯加热时过热,特别是铬不锈钢,轧制时在带钢上形成结疤。
带钢坯表面大量集结的非金属夹杂物,也是产生结疤的原因。
(2)裂边。
板坯侧面缺陷未全面清除干净,这是带钢裂边的原因。
(3)过热。
板坯在过高温度下长时间停留会引起过热。
过热板坯轧制时会产生大裂口和剥落;邻近过热的部分出现细裂纹,细裂纹在进一步轧制时会变成结疤。
为防止板坯过热必须严格遵守规定的加热制度,尤其是高温下的均热时间。
加热铁素体类钢时,温度超过850℃后必须快速加热。
(4)机械损伤。
轧入碎屑、压痕、划痕是热轧不锈带钢表面最有特征的缺陷。
轧人碎屑和压痕缺陷是由于坯料上的结疤块、裂边在导卫上摩擦时有碎片落到带钢表面上以及其他东西被轧辊或矫直机辊子压人而形成的。
划痕大部分是在带钢运动时,下表面与不光滑的导卫、辊面不平的辊子及被动辊相接触时形成的。
上表面划痕通常是在未卷紧运送时卷层间摩擦造成的。
在卷取中,带钢与卷取机成形辊和喂料辊之间发生摩擦时,带钢表面上会产生很多短条状划伤。
(5)带钢厚薄不均。
带钢长度上的厚度不均匀与沿板坯长度加热的均匀性及带钢在机架间张力值有关。
带钢的前端和后端一般比中部厚一些,这是因为在连续式精轧机组中带钢端部没有张力的缘故。
带钢后端一般比前端厚,这是温度不同所致什么叫附加应力和残余应力,它们对金属性能有何影响?由于各种因素(如摩擦、温度不均匀或轧辊变形等)造成轧件变形不均匀时,在金属内部就会引起内应力。
金属在轧制过程中产生的这种内应力称为附加应力;轧制后残存在金属内部的附加应力称为残余应力。
无论是附加应力还是残余应力,其中各自都包含拉应力和压应力,二者同时存在,且互相平衡。
其中拉应力更为有害,当其值超过强度极限时,轧件就会产生裂纹。
冷轧带钢起筋问题研究的开题报告

冷轧带钢起筋问题研究的开题报告
一、选题背景
冷轧带钢广泛应用于建筑、桥梁、汽车、机械等领域,其强度、硬度、延展性等性能
得到广泛应用和认可。
然而,冷轧带钢在生产和使用过程中,常常出现起筋的问题,
严重影响了钢材性能,降低了其经济效益和使用寿命。
因此,研究冷轧带钢起筋问题,弥补目前研究中的空缺,具有重要的实际意义。
二、研究目的
本研究旨在通过对冷轧带钢起筋问题的研究,探究其形成机理和影响因素,以及相应
的改善方法,为钢材生产和使用提供理论依据和技术支持。
三、研究内容
1. 冷轧带钢起筋的物理、化学机理研究:通过对冷轧带钢材料的性能进行分析,探究
其在生产和使用过程中起筋的原因和机制。
2. 影响冷轧带钢起筋的因素分析:从原材料、化学成分、生产工艺、热处理等方面,
分析和探讨影响带钢起筋的因素及其作用机理。
3. 冷轧带钢起筋的预防和改善方法研究:通过现有的技术手段和方法,探讨预防和改
善冷轧带钢起筋问题的可行性和有效性。
四、研究方法
1. 系统调研:通过网上检索、文献资料查阅等方式,搜集目前国内外关于冷轧带钢起
筋方面的研究成果。
2. 实验研究:通过对不同类型、不同成分的冷轧带钢进行实验研究,探究其性能特点
和起筋问题的机理。
3. 数值模拟:通过数值分析软件,对带钢在张拉和热处理等过程中的应力和应变分析,研究其起筋问题。
五、预期成果
通过本研究,预计能够探讨冷轧带钢起筋问题的形成机理和影响因素,以及相应的预
防和改善方法,并对提高冷轧带钢的品质和使用寿命具有一定的理论和实践指导意义。
17 冷轧管材成形原理
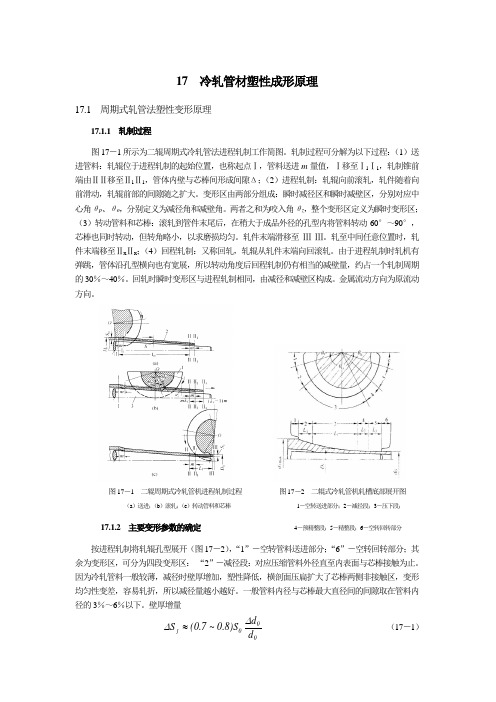
17 冷轧管材塑性成形原理17.1 周期式轧管法塑性变形原理17.1.1 轧制过程图17-1所示为二辊周期式冷轧管法进程轧制工作简图。
轧制过程可分解为以下过程:(1)送进管料:轧辊位于进程轧制的起始位置,也称起点Ⅰ,管料送进m 量值,Ⅰ移至Ⅰ1Ⅰ1,轧制锥前端由ⅡⅡ移至Ⅱ1Ⅱ1,管体内壁与芯棒间形成间隙Δ;(2)进程轧制:轧辊向前滚轧,轧件随着向前滑动,轧辊前部的间隙随之扩大。
变形区由两部分组成:瞬时减径区和瞬时减壁区,分别对应中心角θp 、θo ,分别定义为减径角和减壁角。
两者之和为咬入角θz ,整个变形区定义为瞬时变形区;(3)转动管料和芯棒:滚轧到管件末尾后,在稍大于成品外径的孔型内将管料转动60°~90°,芯棒也同时转动,但转角略小,以求磨损均匀。
轧件末端滑移至 Ⅲ Ⅲ。
轧至中间任意位置时,轧件末端移至Ⅱx Ⅱx ;(4)回程轧制:又称回轧,轧辊从轧件末端向回滚轧。
由于进程轧制时轧机有弹跳,管体沿孔型横向也有宽展,所以转动角度后回程轧制仍有相当的减壁量,约占一个轧制周期的30%~40%。
回轧时瞬时变形区与进程轧制相同,由减径和减壁区构成。
金属流动方向为原流动方向。
图17-1 二辊周期式冷轧管机进程轧制过程 图17-2 二辊式冷轧管机轧槽底部展开图 (a )送进;(b )滚轧;(c )转动管料和芯棒 1-空转送进部分;2-减径段;3-压下段;17.1.2 主要变形参数的确定 4-预精整段;5-精整段;6-空转回转部分 按进程轧制将轧辊孔型展开(图17-2),“1”-空转管料送进部分;“6”-空转回转部分;其余为变形区,可分为四段变形区: “2”-减径段:对应压缩管料外径直至内表面与芯棒接触为止。
因为冷轧管料一般较薄,减径时壁厚增加,塑性降低,横剖面压扁扩大了芯棒两侧非接触区,变形均匀性变差,容易轧折,所以减径量越小越好。
一般管料内径与芯棒最大直径间的间隙取在管料内径的3%~6%以下。
冷轧基础理论知识
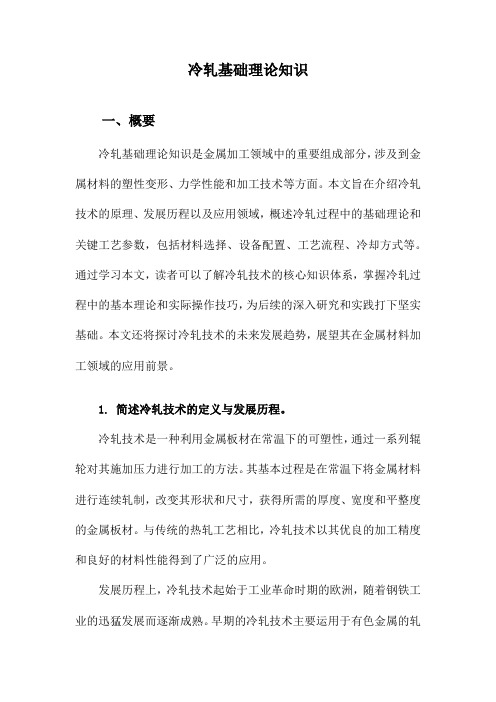
冷轧基础理论知识一、概要冷轧基础理论知识是金属加工领域中的重要组成部分,涉及到金属材料的塑性变形、力学性能和加工技术等方面。
本文旨在介绍冷轧技术的原理、发展历程以及应用领域,概述冷轧过程中的基础理论和关键工艺参数,包括材料选择、设备配置、工艺流程、冷却方式等。
通过学习本文,读者可以了解冷轧技术的核心知识体系,掌握冷轧过程中的基本理论和实际操作技巧,为后续的深入研究和实践打下坚实基础。
本文还将探讨冷轧技术的未来发展趋势,展望其在金属材料加工领域的应用前景。
1. 简述冷轧技术的定义与发展历程。
冷轧技术是一种利用金属板材在常温下的可塑性,通过一系列辊轮对其施加压力进行加工的方法。
其基本过程是在常温下将金属材料进行连续轧制,改变其形状和尺寸,获得所需的厚度、宽度和平整度的金属板材。
与传统的热轧工艺相比,冷轧技术以其优良的加工精度和良好的材料性能得到了广泛的应用。
发展历程上,冷轧技术起始于工业革命时期的欧洲,随着钢铁工业的迅猛发展而逐渐成熟。
早期的冷轧技术主要运用于有色金属的轧制,随着技术的进步,逐渐扩展到黑色金属的轧制领域。
随着材料科学和工艺技术的不断进步,冷轧技术也在不断地发展。
从简单的单机轧制到现代化的连续自动化生产线,从传统的模拟控制到数字化和智能化控制,冷轧技术已经成为现代制造业不可或缺的重要工艺手段。
其发展历程不仅体现了技术的进步,也反映了人类对材料性能的不断追求和探索。
2. 阐述冷轧技术在工业领域中的重要性。
冷轧技术在工业领域中的重要性不言而喻。
随着现代工业的发展,对于材料性能的要求越来越高,而冷轧技术作为一种先进的金属加工技术,能够满足这种高性能的需求。
冷轧过程通过控制金属的塑性变形和再结晶行为,可以显著提高金属的强度和硬度,同时保持良好的韧性和表面质量。
这使得冷轧材料在汽车、航空、建筑、电子等多个行业中得到广泛应用。
在汽车行业,冷轧技术用于生产高质量的钢板和带材,用于制造车身、发动机等关键部件。
开题报告-烟台无缝钢管生产线工程项目成本管理研究0111

在职攻读硕士学位研究生学位论文开题报告论文题目:烟台无缝钢管生产线工程项目成本管理研究姓名学号学部、院(系)学位类别专业领域研究方向指导教师开题时间一、立论依据:课题来源、选题依据和背景、课题研究目的、理论意义和实际应用价值1、课题来源本课题来源于“烟台无缝钢管生产线工程”的项目实践。
2、选题依据和背景钢管产业始于自行车制造业的兴起。
19 世纪初期石油的开发,两次世界大战期间舰船、锅炉、飞机的制造,第二次世界大战后火电锅炉的制造,化学工业的快速发展以及石油天然气的钻采和运输等,都有力地推动着钢管产业在品种、产量和质量上的发展。
钢管主要有无缝钢管和焊管两大类,无缝钢管以其优良的性能和高品质的精度成为衡量一个国家钢管技术发展水平的标志。
无缝钢管的生产分为热轧钢管和冷轧冷拔两大类。
由于基础理论技术的快速发展和能源环保等方面的要求,热轧钢管已成为当今无缝管生产的主流。
目前我国具备了设计生产制造 10~20 万吨/年无缝钢管生产机组的能力。
在这一进程中我国的无缝钢管生产设备制造企业在技术进步上成果明显。
值得注意的是,进入新世纪以后,一些由原国有大型企业技术人员自己组成的民营企业加入到了无缝钢管设备制造行业中来。
他们的进入,给这一行业带来了新的竞争,对该行业的科技进步和可持续发展起到了推动作用。
烟台宝钢钢管有限责任公司拟响应国家有关钢铁产业发展政策(鼓励发展石油开采用油井管、电站用高压锅炉管产品),在烟台市福山高新技术产业区投资建设钢管深加工项目。
本项目为高等级油(气)管及锅炉管生产线工程,采用宝钢分公司钢管厂及烟台鲁宝钢管有限责任公司生产的热轧管料进行深加工以提高产品附加值,提高企业经济效益。
因此,如何做好该工程项目的成本管理,并为今后我国类似工程提供借鉴与指导,是一项亟待研究解决的问题。
3、课题研究目的本课题拟通过相关文献资料的查阅、分析与研究,对工程项目成本管理的相关理论基础进行一定的归纳和总结,并结合烟台无缝钢管生产线工程项目的成本管理实例,从其市场分析、成本预算构成、成本控制方法及控制策略等方面进行综合分析与研究,并为今后我国类似工程提供借鉴与指导。
- 1、下载文档前请自行甄别文档内容的完整性,平台不提供额外的编辑、内容补充、找答案等附加服务。
- 2、"仅部分预览"的文档,不可在线预览部分如存在完整性等问题,可反馈申请退款(可完整预览的文档不适用该条件!)。
- 3、如文档侵犯您的权益,请联系客服反馈,我们会尽快为您处理(人工客服工作时间:9:00-18:30)。
1.4.轧制力、力矩计算;
1.5.凸度规程计算,轧制力挠曲计算,热膨胀计算,原始轧辊辊型设定,弯辊力计算;
1.6.酸洗工艺确定与质量标准;
1.7.平整机工艺制定,平直度、光洁度控制;
1.8.辅助设备校核:圆盘切边剪选择,展进入了全新的阶段,为了使我国的经济建设更好更快的发展,冷轧产品有重要的作用。经济的快速发展,必然伴随着汽车、家电、建材、罐头盒及包装大量生产,而基础设施的建设,需要大量的不同种类的冷轧产品,因此,在以后很长的时间里,冷轧产品在国家经济建设与发展中占有相当重要的作用。
本次毕业设计课题主要是为实现高等院校培养高级应用型、技术型人才的目标所必须的实践性教学环节。通过毕业设计强化我们对基本知识和基本技能的理解和掌握,培养我们搜集资料和调查研究的能力,一定的方案比较、论证的能力,一定的理论分析与设计运算能力,进一步提高应用计算机绘图的能力以及编写编制能力。同时通过给轧钢厂车间设计,培养我们综合运用所学知识,使我们能比较熟练掌握车间设计的专项规划的编制过程。通过认真查阅与本设计相关的文献资料,做好设计前的各项准备工作;分阶段按时完成设计中的各项任务,配合指导老师检查,随时修正错误,改进方法,完成本次课题设计任务,可以与同学探讨,但不能简单套用他人成果。
2.2 机械除鳞
NID方法是日本石川岛播磨公司从1973年起着手研究的。此法是将铁砂送入高压水流通过扁缝式喷嘴, 使铁砂流布满带钢的横向表面, 但此工艺有使喷嘴磨损严重, 且不易调整浆液浓度的缺点。
新日铁八幡厂一号酸洗机组改造使用NID法, 使酸洗速度由180m/min提高到250m/min。用NID法取代酸槽及酸的回收系统,可以节约投资。
3.轧机方面的技术
3.1 HC 轧机
自1980年以来,世界上约有80%以上轧机为新建或改建的HC冷轧机。HC轧机的特点是可以使用平直工作辊;由于压下量的增大,相对地可以使用较厚的热轧料;可以缩小边部减薄的范围;板型控制能力大,可改善板形、产品平直度。
3.2 CVC(连续可变凸度)轧机
CVC技术是德国SMS公司开发出来的。CVC六辊轧机是在四辊轧机基础上开发出来的,中间辊为CVC轧辊,工作辊有立平稳定机构,特点是可用小直径工作辊、中间辊或支撑辊传动。工作辊的水平稳定机构优化了轧制工艺条件,中间辊设正负弯辊。这是一种能改善带钢平直度和横断面形状的技术,且易于应用,改造费用低CVC技术通过使用S型轧辊及轧辊轴向移动,使辊缝的形状与带钢的形状有效的配合,可以实现无级调节轧辊凸度,传统轧制需要准备几套不同凸度的轧辊。而CVC轧制只需一种辊型曲线的轧辊。CVC轧机与HC轧机相比不足之处是不能解决边部减薄问题,此外, HC轧机可用平辊,不需磨出凸度。
4.2 连续退火机组
20世纪70年代初期开始出现带有快速冷却系统的连续退火机组, 可以满足生产的连续化, 缩短生产周期, 提高产品质量, 减少劳动定额等诸因素的要求。
2、主要研究内容、应用价值和生产工艺
1.主要研究内容
1.1.所建厂产品范围,应用领域,产品特性,建厂经济依据;
1.2.典型产品总延伸率计算,道次选择,冷轧机布置选择比较;
1.7.深加工。
2.除鳞技术
2.1 酸洗
目前,世界各国普遍采用浅槽盐酸酸洗代替老式的硫酸酸洗机组。主要原因为: ①盐酸比硫酸有更强的除鳞效果,盐酸酸洗机组前部不用破鳞装置,因而可以简化酸洗设备;②盐酸酸洗比硫酸酸洗更容易去除氧化铁皮,可以得到高质量的酸洗带钢;③浅槽酸洗槽进行排酸比较容易,如有断带发生,可以很快排出酸液,不易产生过酸洗;④盐酸再生系统回收效率高,可达99% ,大大地降低了酸的耗量,每生产1t 带钢仅耗酸3.5kg。
1.冷轧带钢技术的特点
1.1.大力开发高精度轧制技术。
1.2.以过程冶金理论为基础,以低合金钢为重点,提高产品的冶金质量,扩大品种。
1.3.提高连铸比,大力推广连铸连轧工艺及短流程技术。
1.4.轧制过程连续化的新进展——无头轧制技术。
1.5.采用柔性化的轧制技术。
1.6.轧制过程的自动控制和智能控制。
河北联合大学
本科生毕业设计开题报告
题目:年产230万吨2050冷轧板带车间设计
学院:冶金与能源学院
专业:材料成型及控制工程
班级:11成型(1)班
姓名:李宾宾
学号:201114660111
指导教师:董福涛
2015年03月20日
1、题目来源背景(现状、前景)
冷轧的生产方法较好的解决了钢板在热轧过程中温度和温度降不均匀,性能不一致的问题,保证良好的板型及表面光洁度。因此有了我们的设计题目“年产230万吨2050冷轧带钢车间设计”
4.退火工序的技术
4.1 全氢罩式退火炉
从20世纪70年代在欧洲出现并开始使用。由于在740℃时氢的热传导系数为氮的6.5倍,氢的动力粘度只有氮的50 ,因此,在强对流型的罩式退火炉中采用纯氢作保护气体,可以提高钢卷加热和冷却速度40%~50%。使用全氢罩式退火炉可得到优质表面的带钢,表面质量接近于连续退火可能达到的质量,总的能耗费用也减少30%。因此,在老厂改造时, 特别是炼钢、热轧等工艺条件没有重大改变的情况下, 在国外大部分选用全氢退火炉。
3.3 UPC(万能板形控制)轧机
UPC技术是由德国MDS公司开发的,与CVC 技术基本相似,也是一种能改善带钢平直度和横断面形状的技术,且易于应用,改造费用低。UPC技术通过使用雪茄形轧辊及轧辊轴向移动,使辊缝的形状与带钢的形状有效的配合,也可以实现无级调节轧辊凸度。
3.4 CR轧机
CR 轧机属日本三菱重工业公司开发的一种新型轧机, 具有压下量大及板型控制能力强的特点。如用于冷连轧第一架, 当轧制低碳钢时, 压下量可达60% , 也可以用于冷连轧末架, 使成品板形得到改善, 并能节约能耗。
APO除鳞机组,APO为铁粒磨料除鳞的缩写。原苏联与原西德共同开发研制出三套APO装置的连续式机组于1989年在切列波维茨车试车投产。被除鳞的钢板厚度为1.6~4mm ,宽为900~1550mm。除鳞的带钢运行速度为90 m/min, 年产量为50~60万t, 也可对6.5kg/mm2级的低合金钢进行除磷。