灰铸铁件无热处理工艺探讨
灰铸铁缺陷及预防措施
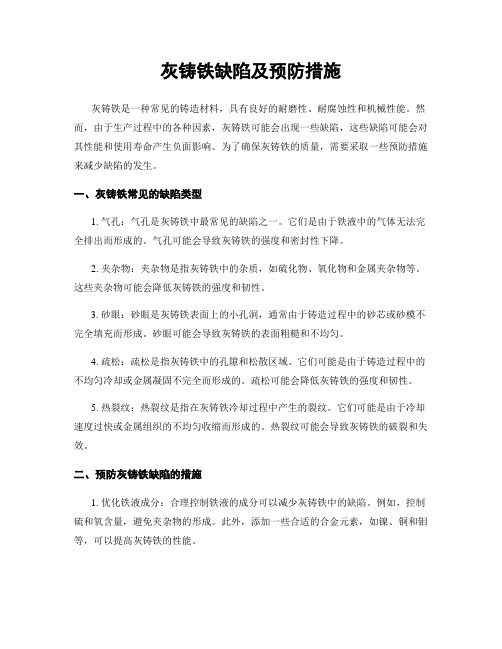
灰铸铁缺陷及预防措施灰铸铁是一种常见的铸造材料,具有良好的耐磨性、耐腐蚀性和机械性能。
然而,由于生产过程中的各种因素,灰铸铁可能会出现一些缺陷,这些缺陷可能会对其性能和使用寿命产生负面影响。
为了确保灰铸铁的质量,需要采取一些预防措施来减少缺陷的发生。
一、灰铸铁常见的缺陷类型1. 气孔:气孔是灰铸铁中最常见的缺陷之一。
它们是由于铁液中的气体无法完全排出而形成的。
气孔可能会导致灰铸铁的强度和密封性下降。
2. 夹杂物:夹杂物是指灰铸铁中的杂质,如硫化物、氧化物和金属夹杂物等。
这些夹杂物可能会降低灰铸铁的强度和韧性。
3. 砂眼:砂眼是灰铸铁表面上的小孔洞,通常由于铸造过程中的砂芯或砂模不完全填充而形成。
砂眼可能会导致灰铸铁的表面粗糙和不均匀。
4. 疏松:疏松是指灰铸铁中的孔隙和松散区域。
它们可能是由于铸造过程中的不均匀冷却或金属凝固不完全而形成的。
疏松可能会降低灰铸铁的强度和韧性。
5. 热裂纹:热裂纹是指在灰铸铁冷却过程中产生的裂纹。
它们可能是由于冷却速度过快或金属组织的不均匀收缩而形成的。
热裂纹可能会导致灰铸铁的破裂和失效。
二、预防灰铸铁缺陷的措施1. 优化铁液成分:合理控制铁液的成分可以减少灰铸铁中的缺陷。
例如,控制硫和氧含量,避免夹杂物的形成。
此外,添加一些合适的合金元素,如镍、铜和钼等,可以提高灰铸铁的性能。
2. 控制浇注温度和速度:合理控制浇注温度和速度可以减少气孔和疏松的形成。
温度过高或过低都会对灰铸铁的质量产生不利影响。
此外,控制浇注速度可以减少砂眼的发生。
3. 优化砂芯和砂模设计:合理设计砂芯和砂模可以减少砂眼和热裂纹的形成。
确保砂芯和砂模完全填充,并避免过度收缩和应力集中。
4. 控制冷却速度:合理控制灰铸铁的冷却速度可以减少热裂纹的形成。
可以采用适当的冷却介质和冷却时间来控制冷却速度。
5. 加强质量检测:对灰铸铁进行严格的质量检测可以及早发现和排除缺陷。
常用的检测方法包括金相显微镜检测、超声波检测和磁粉检测等。
铸铁热处理

1.炉冷至室温或600℃出炉空冷
1.出炉空冷至室温
2.冷却至720-760℃二阶段石墨化+炉
2.出炉空冷至600℃,再进炉,以速度
冷至室温,或炉冷至600℃出炉空冷 精选可编辑ppt 50-100℃/H;冷至300℃以下,出4炉空 冷
正火
铸铁正火的目的是为了提高铸件的硬度、耐磨性、或作为表面淬火的预备热处理, 改善基体组织.但是,灰铸铁无法通过热处理来改善力学性能,这是因为灰铸铁中 的石墨呈片状分布,破坏了铸铁基体组织的连续性,同时,石墨端部易引起应力集 中,致使灰铸铁热处理后基体组织的强度和塑性、韧性不能充分发挥作用
2.热处理不能改变石墨的形态和分布特性,而铸铁热处理的效果又与铸铁 基体中的石墨形态有密切关系.对于灰铁而言,热处理具有一点的局限性. 而球墨铸铁中的石磨成球状,对基体的削弱作用较小.因而,凡能改变金 属基体组织的各种热处理方法,对于球墨铸铁都是有效的
精选可编辑ppt
1
灰铸铁的热处理
退火
1.去应力退火:为消除铸件的残余应力,稳定几何尺寸,减小或消除加工 过后的畸变.通常普通灰铁件的去应力退火温度以550℃为宜.加热速度以 50℃/h.保温时间以25mm/h计算. 其冷却速度一定要慢,防止产生二次残 余内应力,冷却速度一般控制在20-40℃/h
精选可编辑ppt
6
加热温度对铸铁正火后硬度的影响
在正火温度范围内,加热温度愈高, 硬度也愈高. 正火后的冷却速度影响铁素体的析 出量,冷却速度愈大,铁素体的析 出量愈少,硬度愈高。因此,可采 用控制冷却速度的方法来达到调整 硬度.
精选可编辑ppt
7
球墨铸铁的热处理
球状石墨由于呈球形,故对集体的破坏割裂作用很小,引起应力集中的程度 也不大,基体的作用能较充分的发挥,所以可以通过热处理改变基体组织获 得所需性能
灰口铸铁补焊技术的探究综述
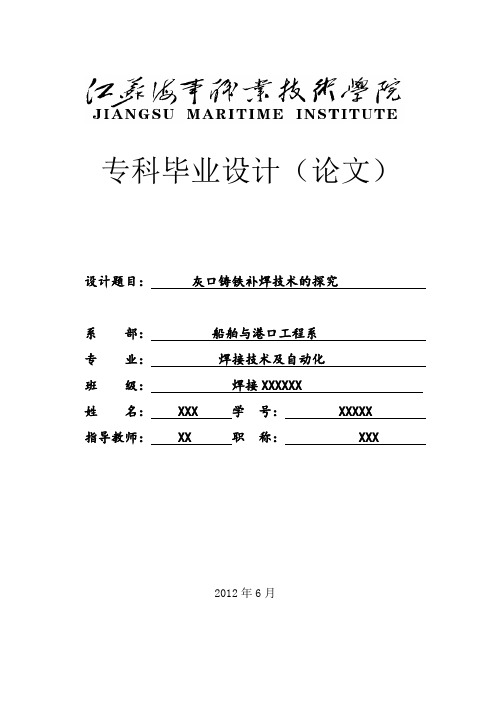
专科毕业设计(论文)设计题目:灰口铸铁补焊技术的探究系部:船舶与港口工程系专业:焊接技术及自动化班级:焊接XXXXXX 姓名: XXX 学号: XXXXX指导教师: XX 职称: XXX2012年6月目录目录 (I)摘要 (II)Abstract (III)1 引言 (1)2 铸铁的分类及其特点 (1)3 灰铸铁的焊接性 (3)3.1 焊接接头的白口及淬硬组织 (3)3.2 焊接接头裂纹 (5)4 灰铸铁的补焊接工艺 (8)4.1 同质焊缝的焊条电弧焊 (8)4.2 异质焊缝的电弧冷焊 (12)5 铸铁件补焊实例 (15)5.1 煤气发生炉的补焊 (15)5.2 机车摇臂补焊 (16)结论 (18)致谢 (19)参考文献 (20)摘要在工业生产中,由于铸铁的性能以及其生产成本低廉,因此在重型机械的零部件铸造中得到广泛的应用。
本文主要鉴于铸铁零部件在生产现场的使用过程中不可避免的会出现局部损坏或者断裂,考虑到经济效益,为节省更换零件的时间,只能采用补焊技术对损坏的铸铁零件进行修复,从而在分析灰口铸铁焊接性和特点的基础上,对灰口铸铁材料的补焊工艺和具体操作技术和方法给予较为详细的介绍,并且通过对某些铸铁工件的修补为实例,对焊工在对铸铁现场施焊技术的提高有非常大的参考价值。
关键词:铸铁零件;补焊工艺;修复。
AbstractIn industrial production, because of the performance and low production costs, the cast iron has been widely used in heavy machinery parts casting. This thesis is mainly in view of the inevitable partial damage or fracture that the cast iron parts will bring in the process of using in the production site. Considering the economic benefits, in order to save the time of replacement parts, we can only use welding technology to repair the damaged cast iron parts, which gives a more detailed introduction to the gray welding technology of cast iron materials and the operating techniques and methods on the basis of the analysis of gray cast iron welding properties and characteristics. Besides, taking the repair of some of the cast iron workpiece as examples provides valuable insight for welder to the improve the welding technology in cast iron field.Key words:Cast iron parts;Welding process;Repaired1 引言铸铁是碳当量大于2%的铁碳合金,工业铸铁的碳当量在2%~4%,铸铁中除了铁和碳以外,含有Si、Mn、P、S等元素,这些元素含量都比碳钢高,在某些特殊用途的合金铸铁中,根据需要还加入Cu、Mg、Ni、Mo、或者Al等合金元素。
灰铸铁缺陷解决方法

在灰铸铁件生产中,常见的铸件缺陷有:气孔、成分与性能不合格、热裂与冷裂、缩孔与缩松、渣眼与铁豆、冷隔与浇不足、砂眼与夹砂、多肉与错辐、变形等。
通常,产生这些缺陷的原因不单是造型制芯问题,有时还有熔炼浇注、配砂质量、落砂清理等许多生产工序的问题,因此必须具体分析,以便采取相应的合理措施加以解决。
一、砂芯和砂型的刚性砂型浇注后,由于铁液的静压力或凝固而引起的膨胀力,常导致型壁移动和砂芯溃散,这就会使铸件产生内部缩孔和表面缩陷。
因此为使铸件尺寸稳定,要最大限度地使铸型紧实。
为了节约造型材料,造芯时广泛采用了空心砂芯,它比实体芯轻,故热容量小,凝固速度慢,这会导致砂型扩张或砂芯溃散。
此外,铁液可能通过芯头或砂芯上的裂纹而渗入其中空部分,这也会使铸件产生缺陷。
为了提高空心砂芯的刚性,可用湿型砂或水玻璃砂充填;也可将壳芯作成两半,其内部设置加强筋,造芯后粘合可得到坚硬的砂芯。
二、正确选择浇注温度1.浇注温度过低时可能形成的缺陷(1)硫化镒气孔此种气孔位于铸件表皮以下且多在上面,常在加工后显露出来,气孔直径约2~6mm°有时孔中含有少量熔渣,金相研究表明,此缺陷是由MnS偏析与熔渣混合而成,原因是浇注温度低,同时铁液中含Mn和S 量高。
(2)液体夹渣加工后铸件表皮之下会发现一个个单体的小孔,孔的直径一般为1~3mm o个别情况下只有1~2个小孔。
金相研究表明,这些小孔与少量的液体夹渣一起出现,但该处未发现S的偏析。
(3)砂芯气体引起的气孔气孔和多空性气孔常因砂芯排气不良而引起。
因为造芯时砂芯多在芯盒中硬化,这就常使砂芯排气孔数量不够。
为了形成排气孔,可在型芯硬化后补充钻孔。
浇注温度过低最常见的原因是浇注前,铁液在敞口的浇包中长时间运输和停留而散热。
用带有绝热材料的浇包盖,可以显著地减少热损失。
2.浇注温度过高浇注温度过高会引起砂型涨大,特别是具有复杂砂芯的铸件,当浇注温度21420C。
时废品增多,浇注温度为1460C。
一种灰铸铁HT250轴承套圈热处理工艺[发明专利]
![一种灰铸铁HT250轴承套圈热处理工艺[发明专利]](https://img.taocdn.com/s3/m/8862c16c302b3169a45177232f60ddccda38e6b9.png)
(10)申请公布号(43)申请公布日 (21)申请号 201510474415.7(22)申请日 2015.08.05C21D 9/40(2006.01)C21D 1/18(2006.01)C21D 5/00(2006.01)C22C 37/10(2006.01)(71)申请人人本集团有限公司地址325000 浙江省温州市高新技术产业开发区甬江路16号(72)发明人张志祥 郭长建(74)专利代理机构温州瓯越专利代理有限公司33211代理人陈加利(54)发明名称一种灰铸铁HT250轴承套圈热处理工艺(57)摘要本发明公开了一种灰铸铁HT250轴承套圈热处理工艺,其特征在于包括以下工序:(1)淬火:调整淬火温度到890℃~920℃,保温50~60min,然后油冷,油温设定为100±10℃,然后冷却至室温;(2)阶梯式回火,将灰铸铁HT250轴承套圈升温180±10℃,保温2~4h,然后再将灰铸铁HT250轴承套圈继续升温到300±10℃,保温2~4h,然后空冷至室温。
本发明的优点是显著改善热处理后硬度值均匀性,提高轴承套圈性能。
(51)Int.Cl.(19)中华人民共和国国家知识产权局(12)发明专利申请权利要求书1页 说明书2页 附图3页CN 105018711 A 2015.11.04C N 105018711A1.一种灰铸铁HT250轴承套圈热处理工艺,其特征在于包括以下工序:淬火:调整淬火温度到890℃~ 920℃,保温50min~60min,然后油冷,油温设定为90~120℃,然后冷却至室温;阶梯式回火,将灰铸铁HT250轴承套圈升温180±10℃,保温2~4h,然后再将灰铸铁HT250轴承套圈继续升温到300±10℃,保温2-4h,然后空冷至室温。
2.根据权利要求1所述的一种灰铸铁HT250轴承套圈热处理工艺,其特征在于:灰铸铁HT250轴承套圈包括以下组分,以质量百分比计:C 3.0~3.6%;Si 2.0~2.6%;Mn 0.6~1.0%;Cr 0.5~1.0%;P 0.1%以下;S 0.1%以下;余量为Fe。
金属材料与热处理 模块八 课题二 灰口铸铁
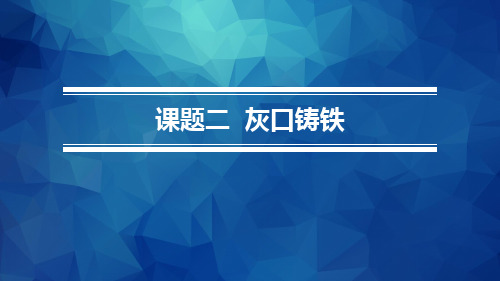
思与练习
1.灰铸铁与钢相比,其组织和性能有何特点?经过孕育处理后的灰铸铁性能有何 变化? 2.灰铸铁有哪些优越性? 3.生产中是采用什么方法来改善灰铸铁的力学性能的? 4.试分析制造齿轮箱所采用的材料和热处理方法 5.在机械加工车间加工一批灰铸铁件时,发现在铸件的薄壁处加工不动。试分析 其原因,并提出解决办法。 6.解释灰铸铁牌号HT250的含义。
HT200 或HT250这种灰铸铁材料强度较高,刚度很好,不易产生形变,这是 高精度机床最主要的性能要求;笨重的铸铁材料及其高含量的石墨可以起到减震 的作用。另外,超大尺寸和复杂外形的零件,选择灰铸铁制造,造价低,加工更 容易。由于床身尺寸大、形状复杂,在冷却过程中会产生较大的内应力。为防止 铸件变形或开裂,应采用去应力退火的热处理方法消除其内应力。
机车床床身
案例分析
•由于床身用于支撑机床上的全部零件,主要承受较大的压应力。 机床在工作时转速很高,产生震动,所以要求床身应具有足够的强 度、刚度(不易变形,提高加工精度)和良好的减震性。另外,床 身的尺寸较大,形状复杂,还要求加工容易,造价低等。选择什么 材料能满足其要求呢?
必备知识
灰铸铁通常是指断口呈灰色,其中的碳主要以片状石墨形式存在的铸铁。在 铸铁的总生产量中,灰铸铁件占80%以上。 一、灰口铸铁的成分和组织
因为化学成分将影响铸铁的石墨化程度,所以灰铸铁的成分应在一定的范围内, 一般为:WC为2.7%~3.6% 、WSi为1.0%~2.2%、 WS<0.15%、 Wp <0.3 %。其中碳、硅、锰是调节组织的元素,磷是控制使用的元素,硫是限制使用的 元素。
其组织是由钢的基体和在基体上分布的片状石墨组成。由于石墨化程度不同, 基体组织中的含碳量也不同;石墨化越充分,则基体中的含碳量也越低,这样便 形成了三种不同的基体组织的灰铸铁,即铁素体灰铸铁(F+片状G)、珠光 体—铁素体灰铸铁(P+F+片状G)和珠光体灰铸铁(P+片状G)。它们的 显微组织如图8—8所示。
灰铸铁件技术要求-
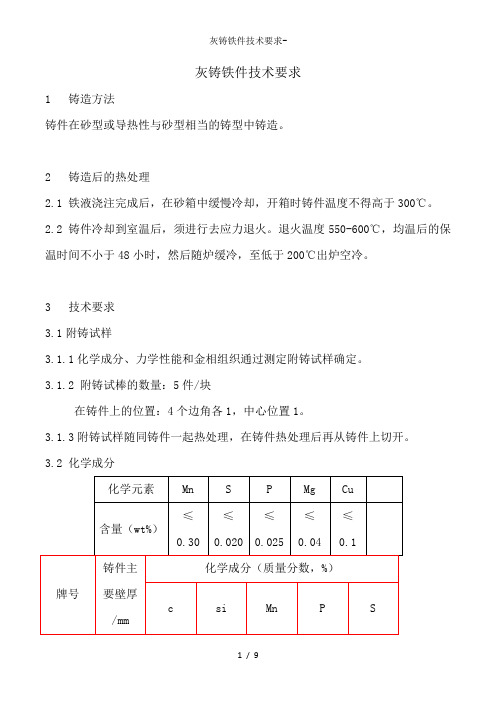
灰铸铁件技术要求1 铸造方法铸件在砂型或导热性与砂型相当的铸型中铸造。
2 铸造后的热处理2.1 铁液浇注完成后,在砂箱中缓慢冷却,开箱时铸件温度不得高于300℃。
2.2 铸件冷却到室温后,须进行去应力退火。
退火温度550-600℃,均温后的保温时间不小于48小时,然后随炉缓冷,至低于200℃出炉空冷。
3 技术要求3.1附铸试样3.1.1化学成分、力学性能和金相组织通过测定附铸试样确定。
3.1.2 附铸试棒的数量:5件/块在铸件上的位置:4个边角各1,中心位置1。
3.1.3附铸试样随同铸件一起热处理,在铸件热处理后再从铸件上切开。
3.2 化学成分3.3 力学性能3.4 金相组织按GB/T7216-2009执行3.5 复验3.5.1 复验条件如果首次测试的结果不能满足材料的力学性能要求,允许进行重复试验。
3.5.2 试验的有效性如果不是由于铸件本身的质量问题,而是由于下列原因造成实验结果不符合要求时,则试验结果无效:a)试样在试验机上装卡不当或试验机操作不当。
b)试样表面有铸造缺陷或试样加工不当(如过渡圆角、表面粗糙度和尺寸不合要求等)。
c)拉伸试样在标距外断裂。
d)拉伸试样端口上存在明显的铸造缺陷。
在上述情况下,应在同一试块上重新取样或从同一批浇注的试块上重新取样再次试验。
3.5.3 铸件以去应力退火的状态交货。
如果力学性能不合格,允许供货方将铸件和代表该铸件的试块一起进行热处理,并再次提交验收。
为复验而进行的热处理次数不得超过两次。
3.5.4 复验的结果作为最终结果。
复验结果都达到要求,可判定该件铸件力学性能合格。
若复验结果仍达不到要求,则判断该件铸件力学性能不合格。
4 无损检测4.1顺序:目测、超声波探伤和加工表面的磁粉探伤。
4.2要进行试验的表面必须清洁无油、无油脂、无砂子或其他污物,表面粗糙度不大于Ra12.5,无影响试验或结果解释的异物存在。
4.3无损检测工作应由具备GB/T 9445规定的2级或以上资格的人员来完成。
jbt77111灰铸铁的热处理

J 36JB/T 7711-1995灰铸铁件热处理1995-06-20 发布1996-01-01 实施中华人民共和国机械工业部发布11 主题内容与适用范围本标准规定了灰铸铁件的热处理设备、工艺及质量检验方法。
本标准适用于灰铸铁件的退火、正火、回火及等温淬火热处理工艺。
2引用标准GB 230金属洛氏硬度试验方法GB 231金属布氏硬度试验方法GB 977灰铸铁机械性能试验方法GB 5614铸铁件热处理状态的名称、定义及代号GB 7216灰铸铁金相GB 7232金属热处理工艺术语GB 9439灰铸铁件GB 9452热处理炉有效加热区测定方法GB/T 6051球墨铸铁热处理工艺及质量检验JB/Z 234.9铸铁件热处理工艺规程3 热处理工艺的应用3. 1 高温石墨化退火用于基体组织中含有较多共晶渗碳体的铸件,以降低硬度,改善切削加工性。
3. 2 低温石墨化退火用于铸件硬度过高,基体组织中没有共晶渗碳体,要求具有高塑性和高韧性的铸件。
3. 3 去应力退火用于降低铸造、铸件焊接、机械加工等残余应力,保证铸件尺寸稳定。
3. 4 完全奥氏体化正火用于铁素体量过多、硬度较低的灰铸铁,提高铸件强度、硬度和耐磨性。
3. 5 部分奥氏体化正火用于基体组织相对均匀,且要求具有一定强度和韧性的铸件。
3. 6 完全奥氏体化淬火、回火用于采用不同回火温度的基体组织,提高铸件强度、硬度和耐磨性。
3. 7 完全奥氏体化等温淬火用于获得贝氏体基体组织,提高铸件综合性能。
3. 8 表面淬火用于提高铸件强度、表面强度和耐磨性。
3. 9 化学热处理用于获得铸件表面特殊物理、化学和力学性能。
4 热处理设备4. 1 加热设备4. 1. 1 采用燃气、燃油、燃煤与电阻加热炉。
根据铸件生产要求,也可采用无氧化加热设备、可控气氛加热炉与连续作业炉。
4. 1. 2 燃料加热炉的火焰不能直接接触铸件,可控气氛加热炉应能调节和控制炉内气氛。
连续作业炉应能调节输送速度,以使铸件在炉内保持必要的加热时间。
灰铸铁硬点、硬区

灰铸铁件的硬点、硬区缺陷分析
灰铸铁件出现硬点或硬区缺陷,在机械加工时会造成表面不平的现象,严重影响铸件加工的进程和表面质量。
需要将铸件从新进行退火热处理消除这种缺陷,这样做会影响铸件的机械性能,降低了强度,如果客户不能接受,则无法挽救只能报废。
对于灰铸铁件而言,当它的化学成分不适宜而铸造工艺上又有失误时,非常容易使铸件薄截面处、棱角、棱边出现硬点、硬区缺陷。
海钺铸造厂在灰铸铁的生产中进行了常识性改进,并且取得了一定的成效,主要做法是将铸件上薄截面竖立着放在上型中,并且远离浇注系统,铁液冲型时,流入此截面型腔中的是冷铁液,这样把三种不利因素即冷金属、薄截面、远离浇注系统都集中在此处,结果就极易使这种竖立着的薄面中或其棱角出现白口,造成硬点或硬区缺陷。
如果非得如此,则可以在这种金属液冲型时在死角的型腔上,设置溢流冒口,以排除冲型死角的冷铁液,加热此处的壁厚,有利于防止硬点和硬区的产生。
这种溢流冒口,也有利于防止薄截面中出现气孔。
铸造工艺设计时,使铁液从铸件薄截面处引入,将内浇道设置在此处,亦有利于防止灰铸铁件产生硬点或硬区。
非热处理灰铸铁活塞环的铸造技术
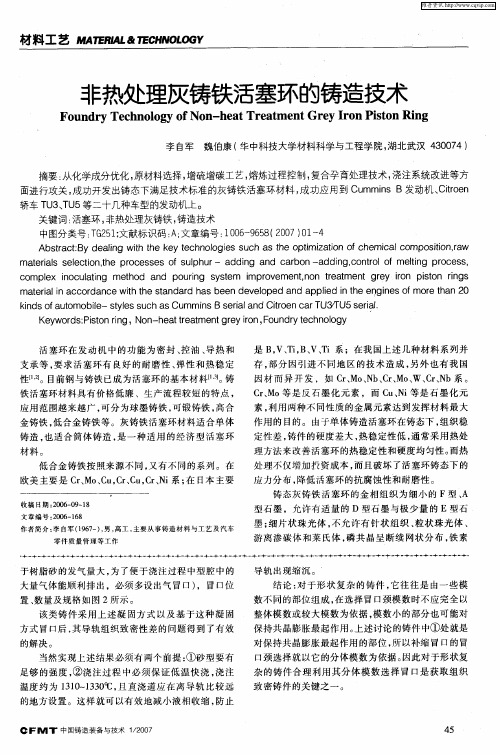
材料 。
低合金 铸铁 按照来 源不 同 , 又有不 同的 系列 。在
欧美 主要 是 C 、 、u C 、 u C 、 i ; 日本 主 要 rMo C , rC , rN 系 在
支 承等 , 要求 活 塞环 有 良好 的耐磨 性 、 性 和热 稳 定 弹 性【1 l 。目前钢 与铸铁 已成 为活 塞环 的基本 材料【1 铸 I 2 1。 . 3 铁 活塞环 材料具 有价格 低廉 、生 产流程 较短 的特点 , 应用 范 围越 来越 广 , 分为球 墨铸 铁 , 锻铸铁 , 可 可 高合
面进行攻关, 成功开发出铸态下满足技术标准的灰铸铁活塞环材料, 成功应 用到 C mmi u n B发动机、 i e s Ct n r o
轿车 T 3T 5 U 、U 等二十几种车型的发动机上。 关键词 : 活塞环 , 非热处理灰铸铁 , 铸造技术 中 图分 类号 :G 5 ; T 2 1文献标 识码 :; A 文章编 号 : 6 95 ( 0 7)1 4 1 0 ~ 68 20 0 — 0
活 塞环 在发 动 机 中 的功 能为 密封 、 控油 、 导热 和
是 B, T , V、i系 ;在我 国上 述几 种材料 系 列并 V、 i B、 T 存 , 分 因引进 不 同地 区 的技 术造 成 , 部 另外 也有 我 国
因材 而 异 开 发 ,如 C 、 、 b C 、 、 、 rN rMo N 、 rMo W C 、 b系 。
维普资讯
材 料工 艺 M TR L E H OO Y A EI &TC N L G A
国家标准《GBT_9439-2009_灰铸铁件》修订说明

20年来世界科学技术的发展及对于清洁生产的迫切化, 提高了对铸件的要求,促进了铸造技术(工艺、材质、 铸造方法、装备及控制等)及铸造工厂现代管理的快速 发展。
全面落实国家标准的维护和管理任务, 建立相应的管理机制,从根本上提高国 家标准的时效性。
2,中华人民共和国国家标准
GB/T 9439-XXXX 代替GB/T 9439-1988
灰铸铁件 grey iron castings
与ISO 185:2005相比的
Байду номын сангаас主要技术内容差异
——在结构上作了较大的编辑性修改; ——删除了ISO 185:2005中重复性的表注和部分技术要求,增加
楔压强度。
增加了两个牌号
HT225 HT275
灰铸铁的牌号和力学性能
灰铸铁单铸试棒的抗拉强度和硬度
抗拉强度与主要壁厚之间的关系
灰铸铁的硬度牌号
感谢全国铸造标准化技术委员会 全体委员的辛勤工作!
与GB/T 9439-1988相比 主要技术内容的修订
——增加了两个牌号; ——增加了拉伸试样规格; ——增加了取样批次的规定; ——增加了灰铸铁件壁厚和硬度的对应值; ——增加了硬度和抗拉强度的关系图; ——增加了壁厚和抗拉强度的关系图; ——删除原标准的附录D,增加新的附录D
经济全球化的发展使中国的铸造业已经进入国际竞争的 阶段,出现了“国际竞争国内化和国内竞争国际化”的状 况。中国的铸件已经销往世界上大多数制造业大国。因 此我们的国家标准也应该与相应的国际标准接轨。
铸件热处理工艺及作业指导书主
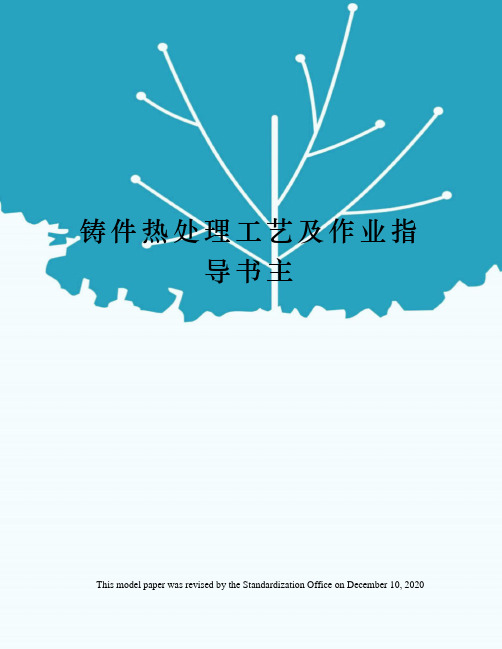
铸件热处理工艺及作业指导书主This model paper was revised by the Standardization Office on December 10, 2020前提:本作业指导书系建蓓铸造有限公司的核心工艺文件之一。
它针对公司产品实现的第三个特殊过程(见《公司质量手册》章节号之4.1.7)提出了系统完整的操作、控制规定,必须得到充分严格贯彻执行。
本作业指导书所取参数,主要源于化工出版社的《钢铁热处理实用技术》。
* 本作业指导书中打“*”并用楷体注明的文字,是警/提示内容,也可作为执行条款。
1.灰铸铁的退火、正火热处理工艺1.1消除内应力退火(人工时效)工艺灰铸铁消除内应力退火(人工时效)热处理工艺适用范围1.较薄、故冷却速度较快的灰铁件;2.形状复杂、截面变化较大的铸件;3.需进行机加工的大型铸件;4.经过少量焊修,因而局部积累些许焊应力的铸件。
* 加热温度越高,应力消除越快。
但温度过高,则易发生石墨化与珠光体球化而使性能降低,尤其是含Si量较高时;* 保温时间一般按炉内铸件平均壁厚的5min/mm计算。
形状复杂的铸件,要以75~100℃/h的速率缓慢加热;* 保温时间终了,以30~50℃/h的速率在炉内缓冷,冷却至150~200℃出炉冷却(空冷)。
1.2软化退火和正火工艺灰铸铁软化退火和正火热处理工艺适用范围3.正火工艺适用于对材质有硬度要求的铸件,退火工艺适用于对材质有韧性要求的铸件;4.经过较多焊修,因而积累较大焊应力的铸件。
* 保温时间一般按炉内铸件平均壁厚的5min/mm计算。
形状复杂的铸件,要以75~100℃/h的速率缓慢加热。
2.球墨铸铁的退火、正火(+回火)和调质热处理工艺高温退火当铸态组织为铁素体+珠光体+渗碳体+石墨时,必须采用高温退火工艺:适用范围1.获得铁素体球墨铸铁;2.分解渗碳体和珠光体,提高机械性能;3.改善加工性能,使工件容易加工且不易变形。
ht250灰铸铁热处理工艺
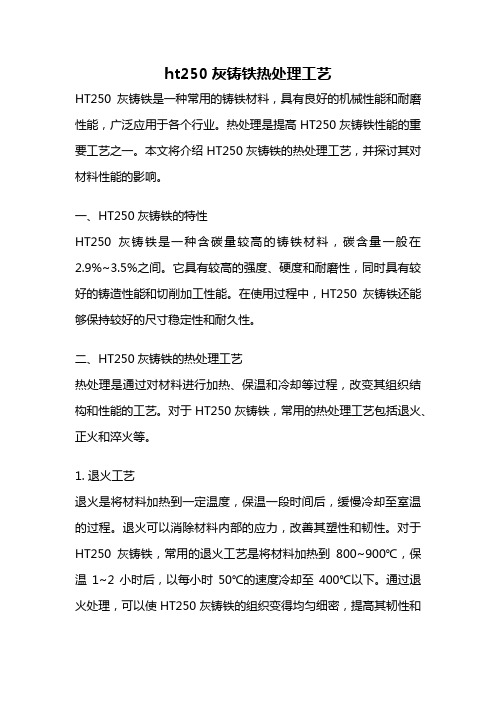
ht250灰铸铁热处理工艺HT250灰铸铁是一种常用的铸铁材料,具有良好的机械性能和耐磨性能,广泛应用于各个行业。
热处理是提高HT250灰铸铁性能的重要工艺之一。
本文将介绍HT250灰铸铁的热处理工艺,并探讨其对材料性能的影响。
一、HT250灰铸铁的特性HT250灰铸铁是一种含碳量较高的铸铁材料,碳含量一般在2.9%~3.5%之间。
它具有较高的强度、硬度和耐磨性,同时具有较好的铸造性能和切削加工性能。
在使用过程中,HT250灰铸铁还能够保持较好的尺寸稳定性和耐久性。
二、HT250灰铸铁的热处理工艺热处理是通过对材料进行加热、保温和冷却等过程,改变其组织结构和性能的工艺。
对于HT250灰铸铁,常用的热处理工艺包括退火、正火和淬火等。
1. 退火工艺退火是将材料加热到一定温度,保温一段时间后,缓慢冷却至室温的过程。
退火可以消除材料内部的应力,改善其塑性和韧性。
对于HT250灰铸铁,常用的退火工艺是将材料加热到800~900℃,保温1~2小时后,以每小时50℃的速度冷却至400℃以下。
通过退火处理,可以使HT250灰铸铁的组织变得均匀细密,提高其韧性和抗冲击性能。
2. 正火工艺正火是将材料加热到一定温度,保温一段时间后,通过适当速度的冷却使材料产生一定的组织转变。
对于HT250灰铸铁,常用的正火工艺是将材料加热到900~950℃,保温1~2小时后,以适当速度冷却至室温。
正火处理可以提高HT250灰铸铁的硬度和强度,但会降低其韧性。
3. 淬火工艺淬火是将材料加热到一定温度,保温一段时间后,迅速冷却至室温的过程。
对于HT250灰铸铁,常用的淬火工艺是将材料加热到900~950℃,保温1~2小时后,以水或油介质进行迅速冷却。
淬火处理可以使HT250灰铸铁产生马氏体组织,从而提高其硬度和强度,但会降低其韧性。
三、热处理对HT250灰铸铁性能的影响热处理可以改变HT250灰铸铁的组织结构,从而影响其性能。
退火处理可以使HT250灰铸铁的组织细化,提高其韧性和抗冲击性能;正火处理可以提高HT250灰铸铁的硬度和强度,但会降低其韧性;淬火处理可以进一步提高HT250灰铸铁的硬度和强度,但对韧性的影响更大。
灰铸铁件热处理

灰铸铁件热处理灰铸铁是一种常见的工业材料,在许多领域发挥着重要作用。
一些灰铸铁件需要进行热处理来改善其物理和机械性能。
本文将介绍灰铸铁件的热处理过程及其影响。
灰铸铁件的热处理包括两个主要步骤:加热和冷却。
在加热过程中,灰铸铁件被加热到一定温度,这个温度通常比室温高出很多,以使原始组织发生改变。
这个过程通常需要进行一定的保温时间,以确保灰铸铁件内部温度达到均衡。
接下来,灰铸铁件被迅速冷却,以保持新组织的形成。
热处理可以带来许多好处,包括:提高灰铸铁件的强度、硬度、耐磨性和抗腐蚀性能等。
热处理的效果与操作参数、炉子类型、冷却方式等因素有关。
选择不同的参数和方式可以使灰铸铁件获得不同的性能。
下面将分别介绍不同的热处理方式。
球化退火球化退火是一种常用的热处理方式,适用于铸件、锻件和冷作件等。
在这个过程中,灰铸铁件被加热到接近临界温度(通常为每种铸铁合金的不同温度)并保温一定时间,以使碳化物尽可能地溶解。
接下来迅速冷却灰铸铁件。
在这个过程中,碳元素从铁基体中扩散到碳化物中,使其形成球状颗粒,从而改善灰铸铁件的延展性和强度。
淬火淬火是一种灰铸铁件的热处理过程,通常在坚硬但脆性易碎的铸造物件上使用。
在淬火过程中,灰铸铁件被加热到很高的温度,超过各种铸件材料的固溶度,然后迅速冷却。
这使得灰铸铁件的碳化物成分处于超冷却状态并具有强度和硬度。
淬火灰铸铁件常常需要再进行回火工艺,以减少其脆性并提高其韧性。
回火热处理可以显著改善灰铸铁件的性能和质量。
不同的热处理方式可以使铸件和锻造物件获得不同的性能和应用范围。
在进行灰铸铁件热处理前,务必了解材料的物理和化学性质以选择合适的操作参数和方式。
灰铁、球铁热处理工艺指导书
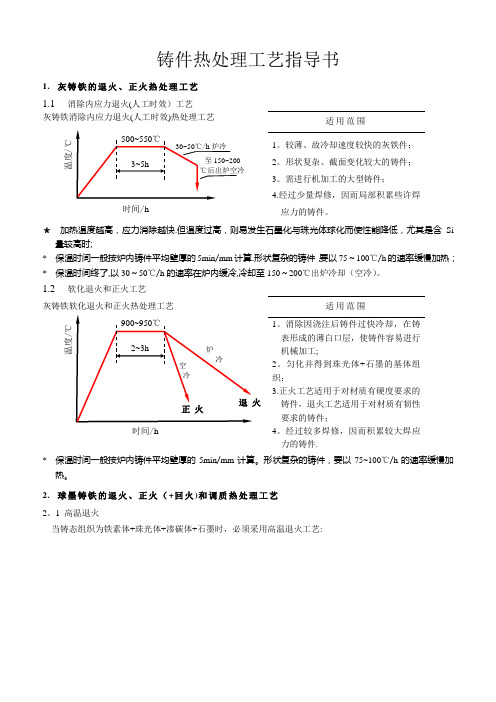
铸件热处理工艺指导书1.灰铸铁的退火、正火热处理工艺1.1消除内应力退火(人工时效)工艺灰铸铁消除内应力退火(人工时效)热处理工艺适用范围2。
形状复杂、截面变化较大的铸件;3。
需进行机加工的大型铸件;4.经过少量焊修,因而局部积累些许焊应力的铸件。
*加热温度越高,应力消除越快.但温度过高,则易发生石墨化与珠光体球化而使性能降低,尤其是含Si 量较高时;* 保温时间一般按炉内铸件平均壁厚的5min/mm计算.形状复杂的铸件,要以75~100℃/h的速率缓慢加热;* 保温时间终了,以30~50℃/h的速率在炉内缓冷,冷却至150~200℃出炉冷却(空冷)。
1.2软化退火和正火工艺灰铸铁软化退火和正火热处理工艺适用范围* 保温时间一般按炉内铸件平均壁厚的5min/mm计算。
形状复杂的铸件,要以75~100℃/h的速率缓慢加热。
2.球墨铸铁的退火、正火(+回火)和调质热处理工艺2。
1 高温退火当铸态组织为铁素体+珠光体+渗碳体+石墨时,必须采用高温退火工艺:适用范围1.获得铁素体球墨铸铁;2.分解渗碳体和珠光体,提高机械性能;3。
改善加工性能,使工件容易加工且不易变形。
*退火温度越高,渗碳体组织分解速度越快,白口现象越易消除。
但温度过高将使铸件机械性能反而变坏,发生变形和表面氧化失碳,故须严格控制温度上限.*保温时间也可按炉内铸件每15mm的有效厚度、需要保温1~2h计算,铸件白口深度大、渗碳体组织成分多时,应适当增加保温时间。
*形状复杂的铸件,要以75~100℃/h的速率缓慢加热。
保温终了,以60~80℃/h的速率在炉内缓冷,至600℃后出炉空冷。
2。
2 低温退火当铸态组织为铁素体+珠光体+石墨(没有渗碳体)时,只需采用低温退火工艺:球墨铸铁低温退火热处理工艺适用范围1。
获得铁素体球墨铸铁;2。
分解渗碳体和珠光体,提高机性能;3.改善加工性能。
*保温时间也可按炉内铸件每15mm的有效厚度、需要保温1~2h计算;* 形状复杂的铸件,要以75~100℃/h的速率缓慢加热.保温终了,以60~80℃/h的速率在炉内缓冷,至600℃后出炉空冷。
国家标准《灰铸铁件》解读

国家标准《灰铸铁件》解读?756?Ju1.2009V oI.58NO.7国家标准铸铁解读洪晓先,张寅(1.东风汽车有限公司工艺研究所,湖北十堰442001;2.沈阳铸造研究所,辽宁沈阳110022)1标准的历史概况及修订的必要性2新标准和旧标准主要内容的差异20世纪50年代,我国灰铸铁件生产是采用当时原苏联国家标准FOCT1412_48和经修订的FOCT1412—54铸铁标准.60年代初,我国制定了自己的灰铸铁件标准JB/T297一l962,其基本内容与FOCT14l2—54完全相同.1967年我国制定了灰铸铁件国家标准,即GB/T976—1967荻铸铁件分类及技术条f牛》,并于1968年1月试行.标准中按单铸试棒的抗弯,抗拉强度等级,将灰铸铁分为7级,牌号分别为HT10.26,HT15—33,HT20—40,HT25—47,HT30—54,HT35.61和HT40—68.该标准规定,灰铸铁的力学性能以qb30rnnl单铸试棒的抗拉强度和抗弯强度作为验收依据,以抗拉强度为主.由于抗弯强度试棒不需机加工,实际生产中通常是以抗弯强度作为验收依据,抗拉强度只是在抗弯强度不合格时才测定.GB/T976一l967一直沿用了近20年.到了80年代,改革开放政策促进铸造业有了较大发展,铸件出口也从无到有地发展起来,GB/T976—1967已不能满足生产与外贸的需要,1985年GB/T5675--1985铸铁分级》应运而生.GB/T5675--1985是等效采用国际标准ISO/DIS185(1983年草案)制定的,但这只是一个牌号分级标准,在技术条款方面仍沿用GB/T976一l967 的技术条款.为了方便使用,同时也考虑与球墨铸铁件,可锻铸铁件等国家标准在结构上一致,经国家技术监督局批准,决定编制铸铁件》国家标准.1988年6月25日经国家标准局批准发布了GB/T 9439—1988铸铁件》,1989年3月1Et实施,GB/T 9439---1988是等效采用国际标准ISO/DIS185—1983 铁件分和ISO/DP7191一l987《铸铁件交货通用技术条件》编制的,为推荐性国家标准.2001年11月,中国加人世界贸易组织,随之而来国家各项与经贸密切相关的基础标准需要与国际标准接轨.2005年国家标准化管理委员会对铸造国家标准清理评价,决定重新修订《灾铸铁件》国家标准.GB/T9439---2009等同采用国际标准ISO185:2005,并参考国外先进标准.为提高标准的市场适应性,新国家标准中增加了贸易性的内容,实现从产品型标准向贸易型标准的转变.新标准的主要内容与旧标准基本相近,但几乎在每个章节和条款上表述的方式都有所不同.新标准等同采用国际标准的同时,还保留,完善了旧标准中有利于标准可操作性,完整性的章节.新标准给出了更多的技术指标和数据,在取样要求,试验方法和检验规则等章节将各条款规定的更详细,更明确,在结构编排上也更趋合理.2.1适用范围新版标准规定了灰铸铁的术语和定义,灰铸铁牌号,技术要求,取样要求,试验方法,检验规则,以及铸件标识,包装和储运要求.标准所规定的范围阐述更为具体.2.2规范性引用文件在规范性引用文件中,引用的文件一律采用最新版的标准名称和编号,删除已作废的引用标准.新标准共引用了18项国家标准,全部为非注日期引用.比旧标准多引用的5项标准是:GB/T228金属材料室温拉伸试验方法GB/T4336碳素钢和中低合金钢火花源原子发射光谱分析方法(常规法)GB/T5611铸造术语GB/T8170数值修约规则GB/T11351铸件重量公差2.3术语和定义增加了术语和定义章节,对铸件主要壁厚定义为:指用以确定铸件材料力学性能的铸件断面厚度.2.4灰铸铁牌号在灰铸铁牌号一章中,等同采用了国际标准ISO 185:2005的牌号分级,增加了HT225和HT275两个新牌号,这是新,旧标准的最显着差别.2.5订货要求将旧标准放在资料性附录中的订货要求纳入正文,并作为独立章节.规定需方订货时最少应提供材料牌号和特殊需求,其他技术参数如需方不了解,供方可帮助确定,简化了需方的专业知识要求.这是产品型标准向贸易型标准转变的一个特征.2.6生产方法和化学成分(1)增加了生产方法和化学成分章节.铸造洪晓先等:国家标准《:扼铸铁解读(2)规定铸件的生产方法一般由供方自行决定,对特殊要求可双方商定.(3)规定如需方的技术条件中包含化学成分的验收要求时,按需方规定执行.化学成分按供需双方商定的频次和数量进行检测.体现了买方市场,满足用户需求的理念.(4)规定当需方对化学成分没有要求时,化学成分由供方自行确定,化学成分不作为铸件验收的依据. 但化学成分的选取必须保证铸件材料满足本标准所规定的力学性能和金相组织要求.2_7技术要求(1)力学性能试棒取自单铸试棒还是铸件本体,性能验收指标是抗拉强度还是硬度,均必须在订货协议或需方技术要求中明确规定.铸件的力学性能验收指标应在订货协议中明确规定.因铸件的形状,壁厚不同,力学性能验收指标应根据具体铸件确定.(2)除力学性能外,金相组织也是铸件验收的主要指标,比旧标准要求更严格.(3)新标准的表1将旧标准的三表合一,易于对照.(4)表1增加了HT225和HT275牌号铸件在不同壁厚时的最小抗拉强度值.(5)表1中,HT150的主要壁厚增加了两档.铸件本体预期抗拉强度略有调低.(6)将旧标准表2中的不同尺寸附铸试棒和附铸试块整合到一起,根据铸件壁厚选择30rnlTl或50mm附铸试棒,如选附铸试块也同样有Rl5和R25两种规格.铸件主要壁厚小于80mm的选用小规格试棒(块),801/11/1及以上壁厚选用大规格试样(块).(7)旧标准中铸件壁厚在40~80mm时,可选用qb30mm附铸试棒也可选用qb50mm附铸试棒,因此导致了同一牌号,同样壁厚范围,因采用附铸试样或附铸试块产生两个不同的最小抗拉强度值.新标准避免了这种情况,即壁厚大于80iYinl时,均采用大规格试棒或试块,而不同壁厚规定的最小抗拉强度值,基本上是采用旧标准的附铸试块强度值.因为附铸试块的抗拉强度略低于附铸试棒的抗拉强度,附铸试块的铸造也较为方便.(8)HT300牌号铸件在不同壁厚范围内,附铸试棒(块)的性能略有降低或提高.(9)新,旧标准对附铸试棒(块)最小抗拉强度规定的差异见表1.(10)新标准与国际标准ISO185:2005相比,在牌号HT150,HT200中缺少壁厚2.5~5inln档及对应的铸件本体预期抗拉强度,数据有待补充.因为随着直读光谱,孕育,保温浇注和整体组芯等新技术的应用,主要壁厚小于5Inl-n的铸件时常可见,尤其是小型发动机气缸体,最小壁厚通常仅为4innl左右.旧标准中HT100,HT150和HT200对应的最小壁厚为2.5~10mnl, 太宽泛,也不尽合理,在今后该标准修订时应予以补充. (11)铸件本体取样位置,试样尺寸和抗拉强度值可由供需双方商定,若需方有明确规定时,应符合需方图样及技术要求.若需方要求从铸件本体上取样,但未指定本体取样位置时,供方可根据铸件结构和受力状况,自行决定取样位置.(12)标准给出8种规格的本体试样加工尺寸(见表2),方便使用,符合用户对铸件本体质量要求不断提高的趋势.规定铸件本体抗拉强度的检测频次和数量,由供需双方商定.(13)将铸件硬度牌号规定,由旧标准的附录性文件改为纳入正文中,体现了实际生产中,用户对铸件本体硬度日益重视,同时也更易于通过铸件硬度对供方铸件的质量进行监测.新标准按不同壁厚对铸件本体硬度作了更详细的规定,见表3.将旧标准中的硬度牌号H145改为H155,使每个硬度牌号等级间的硬度差均为20HBW.(14)给出单铸试棒抗拉强度的同时还给出了单铸试棒的硬度值,见表4.(15)规定硬度检测应在铸造面1.5rnrn以下处测试, 因为铸件表面可能存在过冷组织,热处理贫碳和抛丸应力等影响材质的真实硬度.(16)没有推荐采用易割片作敲落式铸件附铸硬度试块,这种方法在大量生产中不常用.2.8取样要求单铸试棒应在本批次铁液浇注后期浇注试棒,以保证试棒的代表性.2.9试验方法(1)样件,试生产铸件需提交全尺寸检测报告,检测数量由供需双方商定.量产供货的铸件应按批次提交关键尺寸(或重要尺寸)检测报告,检测频次和数量由供需双方商定.此规定的目的是保证铸件按生产流程的要求进行试制,试产和量产,以保证铸件品质的一致性,稳定性和可追溯性.(2)如供需双方同意,可选用等效的方法测定抗拉强度,布氏硬度,金相组织,如用测定楔压强度替代测定抗拉强度.楔压强度通常用于受铸件毛坯尺寸限制或已机加工后的铸件无法切取出本体抗拉试样的场合.2.10检验规则在取样批次的划分章节,.增加了2条新规定.(1)同一模具生产的同一炉铁液浇注的铸件构成一个取样批次.即铸件是以炉次为最大批次,条件是该炉次浇注的铸件应是采用同一型,芯模具,造型,?758?FOUNDRYV o1.58No.75lOlO2O2040HT2254080一一19O1708Ol50l55一一一l50300145一一一23020017015013510202040HT27540808015Ol50300205190l75250220190l75新版:表中斜体字数值表示指导值,其余抗拉强度值均为强制性值,铸件本体预期抗拉强度值不作为强制性值.旧版:1.壁厚150---300mm铸件的附铸试棒(块)最小抗拉强度没有规定指导值,均为强制性值.2.HT100牌号太低,没有实用价值,表中没有列出HT100牌号.3.HTI50,HT200,HT250牌号中没有5~10rnln和10---20nlnl档,以及对应的铸件本体预期抗拉强度.制芯工艺也是一样的.(2)在某一时间间隔内,如炉料,工艺条件或化学成分有变化时,在此期间连续熔化的铁液浇注的所有铸件,无论时间间隔有多短,都作为一个取样批次.强调无论是连续熔化还是间歇熔化,只要炉料,工艺条件或化学成分有变化,这个变化期间浇注的铸件都应该作为一个单独的批次.如感应炉熔化时,某包铁液加入了某种合金元素;同炉次铁液孕育剂,孕育方法的改变..浇注同样铸件但浇注工艺或浇注系统的改变等,都应该作为一个单独批次.铸造洪晓先等:国家标准锹铸铁牛》解读'759.注:1.在铸件应力最大处或铸件最重要工作部位或在能制取最大试样尺寸的部位取样.2.加工试样时应尽可能选取大尺寸加工试样.表3灰铸铁的硬度等级和铸件硬度表4单铸试棒的抗拉强度和硬度值规定供方应保存所有完整的试验和检查记录,留客户复查.需方没有特殊规定时,同一批次的拉伸试样和未做试验的试样应自填写试验报告之日起保存3个月以上.2.11附录为了方便设计者和用户,增加了"灰铸铁的力学性能和物理性能","灰铸铁件的抗拉强度,硬度和截面厚度的关系"以及"楔压强度"的附录.3标准的特点3.1由产品型标准向贸易型标准转变旧标准在内容和表述方式偏重于灰铸铁件自身的牌号等级规定,技术要求,试验方法和检验规则等,其考虑更多的是站在供方的角度指导制造商按国家标准的基本规定生产灰铸铁件.新标准虽然在主体内容上和旧标准相近,但是站在中间的立场,并以用户(需方)需求为上的理念来阐述标准的规定.3.1.1突出用户要求在很多情况下,用户对铸件的使用条件,工况和质量要求比铸件制造商更清楚,尽管用户可能对铸造工艺,材料技术本身不那么内行.反之铸件制造商虽然对铸件和铸件生产技术是内行,但其对该铸件的用途,使用工况并不一定了解.所以新标准给用户预留了更多的话语权.特别是在技术,质量要求方面,当用户有专门要求时,经供需双方协商同意,可按用户提出的要求验收.体现出在市场经济下,供方应不拘泥于标准的规定,尽可能满足客户需求,以需求拉动技术,质量提升的发展趋势.3.1.2强调供需双方协商准则标准只能做到确立规则,规定一般事件的处理方法,而实际生产,贸易中不同的情形和需求无法预知. 新标准几乎在所有重要条款中都规定了供需双方协商一致的原则,因为贸易本身就是不断洽谈协商,相互理解和妥协的过程.从某种意义上说,新标准是为供需双方协商提供了一个法定规则的平台.3.1_3重要环节和细节都列出了相应条款和具体要求铸造生产环节多,流程长,在签署订货协议中难免有漏项.新标准在主要技术,质量,检验等环节都给出了较为详细的条款,对供需双方都有提示或警示作用.?760?FOUNDRYdu1.2oo9VOI.58N0.73.2主要内容等同采用了国际标准的最新文本3.2.1与国际标准接轨与国际标准接轨是编制新标准的基本原则,为了更好地促进对外贸易和交流,国家标准应不低于国际标准已成为不言而喻的共识.新标准在主要技术内容方面等效采用了国际标准ISO185:2005((Greycast irons.Classification)),但在标准的编写结构上不完全对应.3.2.2表格合并与简化标准中规定的技术指标和技术参数多以表格的形式表述.与旧标准相比,新标准合并了一些相近内容的表格,还提供了更多的表格数据,在数据内容上更加完整.3.2-3新增加了两个灰铸铁牌号等同采用了国际标准的牌号分级.该标准的2005版,增加了HT225和HT275两个新牌号,这是新标准与旧标准的最显着差异.HT200.HT300牌号是用量最多,且随着牌号提高铸造性能恶化也较为显着的区域,为了充分挖掘灰铸铁材料的力学性能潜力,减缓铸造性能的恶化倾向,将牌号细分可为用户提供更多的选择,同时有利于物尽其用.铸造配料,熔化,炉前成分检测,孕育等新技术也为灰铸铁牌号的细分提供了技术保障.美国材料试验学会标准ASTMA48/A48M--2003 ((StandardSpecificationforGrayIronCastings))标准中,灰铸铁牌号按抗拉强度分级,从150至400,每增加25]VIVa 为一个牌号等级,分150,175,200,225,250,275,300,325,350,375和400共11个牌号.美国汽车工程师协会标准SAEJ431,将灰铸铁也分为8个等级.新标准中没有抗拉强度为375MPa和400MPa这2个级别的牌号,因为我国和许多工业国家一样,由于球墨铸铁,蠕墨铸铁的发展,实际上已很少生产这2种高强度的灰铸铁件了.对灰铸铁强度要求过高的并不总是有利的,因为它会恶化铸造性能,机加工性能和减震性.3.2.4将硬度牌号及验收指标纳入正文硬度牌号和抗拉强度牌号一样,也可以作为灰铁件的验收条件.以硬度牌号作为验收条件,一般是用于对切削性能或耐磨性能要求较高的灰铸铁件,且铸件主要壁厚小于80mill.3.2.5硬度牌号的分级硬度牌号分级的3位数字是表示各硬度牌号铸件在壁厚40mnl时所对应规定硬度的上限值,如硬度牌号H195,表示铸件壁厚40rnm部位,硬度的最大值不大于195HBW.3.2.6灰铸铁材料的性能指标附录中给出了不同牌号灰铸铁常用的力学,物理性能指标,抗拉强度和铸件壁厚的关系,以及楔压强度试验和换算方法,为标准使用者提供了方便.3.3保留,完善了旧国家标准中不可或缺的精华的部分对旧标准几十年实践证明不可或缺的部分予以保留,完善.如技术要求章节中的几何形状,尺寸,尺寸公差,加工余量,表面质量,铸造缺陷;检验规则章节中的检验权利,检验地点,取样批次的划分,试验数据保存,试样保存;铸件标识,包装,储运要求章节中的铸件标识和质量报告,表面防护,包装,储运要求等.上述条款强调了灰铸铁件作为商品的属性和商品交货时应符合的质量状态要求.这些内容国际标准ISO185: 2005((Greycastirons—Classification))均没涉及.3.4灰铸铁牌号单铸试棒的硬度值在3Omm单铸试棒上测试材质硬度是生产中常用的方法,但因单铸试棒硬度和铸件本体硬度有一定的差异,在供需双方没有事先商定的情况下,经常会因铸件硬度的定义发生争议.本标准既给出了单铸试棒的硬度范围也给出了铸件本体的硬度范围.4标准的应用铸铁件》是铸造标准中的基础性标准,应用面广,使用频率高,因此供需双方在应用新标准时应注意下列事项.4.1标准的适用范围新标准不适用于连铸型材,离心铸管,金属型铸造等非砂型灰铸铁件.4.2灰铸铁牌号的化学成分化学成分是保证力学性能的重要依据,因此在铸造企业自己的技术标准中通常都明确规定不同灰铸铁牌号的化学成分范围.而新,旧标准都没有对化学成分做出规定是因为:(1)化学元素之间有交互性和互补性,在某些元素增加的情况下,减少另外一些元素可得到同样的力学性能和硬度值范围.各铸造厂的情况和工艺方法差别很大,规定了成分就牺牲了灵活性,多样性,后果也不经济.(2)除化学成分外,还有很多其他因素对铸件的力学性能有重要影响,如微量元素,孕育,熔化过热,激冷倾向,替代元素,冷却方式,后续处理等.也就是说,即使化学成分合格或不合格,并不能完全主导铸件的力学性能和硬度.(3)中小冲天炉熔化和炉料比较复杂的情况下,难以做到对化学成分范围做比较准确的控制,铁液出炉后木已成舟,只能用综合调控手段来保证铸件力学性能.(4)对一个具体铸造企业,其条件和工艺已确定,经供需双方协商同意,可规定化学成分范围的要求.铸造洪晓先等:国家标准锹铸铁解读?761?对有特殊要求的铸件,甚至可将某些化学元素作为主要验收依据之一.(5)当需方没有提出化学成分范围要求时,铸件的化学成分由制造商自行决定,因为制造商比需方更清楚满足该牌号要求应选择的各化学元素范围,同时也有利于采用制造商的化学成分体系,检测验收体系, 实现规模化生产.(6)当需方提出具体的化学成分范围,经供需双方协商同意后,还应确认哪些元素属于强制性要求和强制性要求元素的波动范围以及超出范围时的处理办法等.4.3灰铸铁牌号灰铸铁牌号指30mm单铸试棒的最小抗拉强度,它只能间接反映铸件本体的力学性能.同样牌号的铸件,因形状,尺寸,壁厚不同,铸件本体性能力学性能和硬度会有不同.4.4HT_225和HT275~号特点提高灰铸铁牌号通常是用降低碳,硅含量或是添加合金元素来实现,而随着抗拉强度牌号的提高,灰铸铁的工艺性明显恶化,尤其是收缩倾向,白口倾向大和流动性差.新增加的2个牌号对工艺性较敏感的薄壁箱体件,薄壁小件,形状复杂件,盘类件等用途较大.4.5HT350以上牌号HT350以上牌号的铸造工艺性差,实际生产中已很少采用.对于更高强度牌号的要求,推荐采用蠕墨铸铁或球墨铸铁.虽然蠕墨铸铁和球墨铸铁各有自身特点,但除减震性外,其铸造工艺性,切削加工性和成本等都有较强的竞争力.建议在选用HT350牌号的同时应考虑对比选用蠕墨铸铁或球墨铸铁的可能性.4.6单铸试棒与本体试棒性能的差异铸造的特点是适于制造形状不规则,结构复杂的零件,因此壁厚差异较大会导致不同部位的冷速不同, 造成各部位力学性能和硬度有一定差异.单铸试棒只能代表该牌号材质特定壁厚的力学性能和硬度,铸件本体试样才能代表本体I生能.4.7附铸试棒(块)规格的选取以铸件主要壁厚80nlrn为界,壁厚小于80rnn'l时,选用小规格的附铸试棒(块),壁厚大于等于80mnl时,选用大规格试棒(块).4.8抗拉强度性能的差异(1)对于同档尺寸规格的单铸或附铸试棒,如加工成A型抗拉强度试样,其统计强度值要略高于B型试样. 因为A型试样标距内的平行段短,可能碰到组织不均匀影响的几率小,所以更能代表材质本身的真实抗拉强度.(2)对于同档尺寸规格的附铸试棒或附铸试块,附铸试棒的统计强度值要略高于附铸试块,因为附铸试棒的冷速要快一些,内部组织也致密一些.(3)附铸试棒(块)的性能还不能完全代表铸件本体性能,只是比单铸试棒性能的代表性更好一些,只有本体试样才能如实反映铸件本体性能.铸件本体性能可根据标准附录中给出的壁厚与抗拉强度,硬度的关系图估算.4.9铸件本体抗拉强度测定铸件本体抗拉强度时,抗拉强度试样的加工应尽可能选用尺寸较大的规格,大规格试样l:LsJ,规格试样的测试数据更稳定,准确.4.10抗拉强度的强制值和指导值灰铸铁各牌号等级规定的最小抗拉强度是强制性值,但对应于壁厚>150mm,≤300mi/l的铸件,新标准中给出的附铸试棒(块)抗拉强度值为指导值,在表中用斜体字表示.表中给出的铸件本体预期抗拉强度值也不是强制性值.4.11铸件的本体硬度范围可以小于新标准中规定的范围当供需方同意在铸件本体的指定部位测试硬度,则该指定部位硬度值的上,下限范围应不小于40HBW. 此条款一般用于大量生产的铸件.因为标准中给出的硬度值范围是泛指,所以对给定的铸件和硬度测试部位,经供需双方协商同意,可适当缩小硬度值范围.4.12硬度检验规则新标准取消了旧标准列在规范性附录中的硬度检验规则,因为影响硬度的因素较多,测试误差也较大,而且实际中容易测试多点,多部位的硬度值来综合判断铸件材质情况,不像抗拉强度,误差较小,也比较单一.但在实际应用中硬度检测规则和抗拉强度检测规则是一样的,即在事先规定的部位测试硬度,如该部位硬度合格则材质合格,若测试结果达不到要求,又不是试样制备或操作不当造成的,则可在硬度测定点附近再选定2处测定硬度,进行复验.如复验中,其中一处硬度不合格,则判该铸件材质不合格.铸件本体硬度的测试比例,检测频次,硬度合格率及抽取铸件的代表性等,由供需双方商定.4.13铸件本体硬度检测铸件本体硬度检测简单,方便,可以不损坏铸件,甚至可100%在线检测.对大批量生产的铸件,越来越多地用本体硬度来代替抗拉试棒检测,特别是汽车灰铸铁件.以检测本体硬度为主时,应在本企业生产条件下事先做出该铸件本体硬度和单铸试棒,本体试棒之间的函数关系,以此确定本体硬度的上,下限范围,并经需方同意及确定抽检比例后才可实施.大型铸件一般检测附铸试块的硬度.4.14灰铸铁的化学成分新标准和国际标准ISO185:2005都没有规定灰铸铁的化学成分,但化学成分的控制还是尽可能控制在较窄的范围.铸造熔化中炉料分选,分类,配比定量,?762?FoUNDRYJu1.2009VOI.58NO.7熔化参数稳定,过热,保温控制,炉前检验,调整等都是缩小化学成分范围的重要环节.与先进国家相比, 我国铸件化学成分波动范围较大,缩小成分波动范围是今后努力的方向.4.15灰铸铁件的金相组织(1)如果需方没有要求,则金相组织一般不作为验收项目.如果要求检测金相组织,则应规定铸件本体的检测部位.新标准虽然没有对灰铸铁件的金相组织要求和取样方法做详细的规定,实际中可参照铸件本体抗拉强度试样的作法进行.特别是铸件非正常损坏失效或铸件残体碎片,检测金相组织是判断铸件性能的一种常用方法.(2)影响灰铸铁力学性能的金相组织首先是石墨形态和石墨长度,其次是珠光体和铁素体比例.因为灰铸铁本身是脆性材料,所以少量碳化物和磷共晶对力学性能基本没有影响,一般要求总量≤3%,高牌号灰铸铁可以放宽到≤5%.共晶团数,珠光体片间距和石墨量等均不作为铸件的验收依据.4.16铸造残余应力灰铸铁件一般以铸态交货,不做消除残余应力处。
灰铸铁的热处理

(3)冷却速度一定成分的铸铁,石墨化程度取决于冷却速度。冷速越慢,越利于碳原子的扩散,促使石墨化进行。冷速越快,析出渗碳体的可能性就越大。这是由于渗碳体的WC(6.69%)比石墨(100%)更接近于合金的WC(2.5%~4.0%)
双重相图:实践证明,铸铁在冷却时,冷速越缓,析出石墨的可能性越大,用Fe-G相图说明;冷速赶快,则析出渗碳体的可能性越大,用Fe-Fe3C相图说明。为便于比较和应用,习惯上把这两个相图合画在一起,称之为铁-碳合金双相图。如图4-11所示。其中虚线表示稳定态(Fe-G)相图,实线表示亚稳定态(Fe-Fe3C)相图,虚线与实线重合的线用实线画出。石墨化以哪一种方式进行,主要取决于铸铁的成分与保温冷却条件。
正火后冷却速度影响铁素体的析出量,从而对硬度产生影响。冷速愈大,析出的铁素体数量愈少,硬度愈高。因此可采用控制冷却速度的方法)(空冷、风冷、雾冷),达到调整铸铁硬度的目的。
淬火与回火
1.淬火 铸铁淬火工艺是将铸件加热到Ac1上限+30~50℃的温度,一般取850~900℃,使组织转变成奥氏体,并在此温度下保温,以增加碳在奥氏体中的溶解度,然后进行淬火,通常采用油淬。
第三阶段石墨化在738℃(P'S'K'线),通过共析转变析出共析石墨。即
3.影响石墨化的主要因素
(1)化学成分按对石墨化的作用,可分为促进石墨化的元素(C、Si、Al、Cu、Ni、Co、P等)和阻碍石墨化的元素(Cr、W、Mo、V、Mn、S等)两大类。
灰铸铁件的缺陷分析和质量控制

也必然降低 了设备等级 , 使得设 备在 使用和控制工作 中存在着极 大 常排气截 面应为 内浇道总截面积 1 . 5 一 1 . 8 倍左右 。浇注 系统按半开 的隐 患 , 因此 来说 , 在 目前 的工业 生产 中尤其是运 用冲天炉 方式进 放半 封闭原则设 置为宜 , 且须具有一定 的拦渣功能 , 这样 铁液充 型 行铸造 , 而不是采用流水线生产方式 进行 铸造过程 中要做好灰铸铁 时比较平稳 , 不会冲击铸 型或产生飞溅 或卷人气体 。而浇注 系统 的 件的缺陷 以及质量控制就显得 至关 重要 。 截面大小 以 8 - 1 0 k g /s 的浇 注速度来计算较为适宜 。铁液的熔炼温
1灰 铸 而 手 工 浇 注 时 末 箱 的 浇 注 温 度 应 控 制 在
灰铸铁是 目前铸铁技 术中较为常见的产品之一 , 其主要是指具 1 4 0 0  ̄ ( 2 左右( 视铸件大小与壁厚可适 当调整 ) 。 备 了片状 石墨 的铸铁 , 这种铸 铁主要成分是 铁 、 碳、 硅 等元 素 , 其中 3 . 2砂眼 也是 目前世界上发现的应用最早的铸铁技术和方法之一 , 这种铸铁 砂眼在 目前灰铸铁件 中也较为常见 , 其多 出现于器件 上型面之 的产量 占据了整个铸铁产 量的 8 0 %以上 。 中, 其 中也有一部分 出现去器件 的主体 构成部分 。就 目前灰铸铁件 灰铸铁是铁制品中最 为常见的一种 , 其力学性质与基本组织和 中常见的砂眼产生原因分析 , 其 主要是 由于铸铁浇筑系统设置不科 石墨存在着极为紧密的关 系。 抗 议者们说 , 灰铸铁中 , 片状 的石墨对 学 、 不合理 , 其次是 由于型砂 系统 的管理不够科学和完善造成 的。 其集体的切割十分严重 , 石 墨尖 角极容 易形成 一种应力集 中和分布 砂眼控制 密切 的关 系 , 使得 灰铸铁 的抗拉 强度 、 等级以及韧性 远远都低 于钢 a . 要有合理的浇注速度 。截面太小 , 则浇注速度太慢 , 铁液上升 结构 , 但是其抗 压强度却不弱 于钢结构 , 因此这种铸 铁器件 可以说 速度太慢 , 上型受铁液高温烘烤时 间长 , 容易使 型砂爆裂 , 严重时会 是力学性能最差的一 种铸铁器 件模 式 。一般来说 , 一个 良好的铸造 成片状脱落 。 浇注系统的 比例 , 应使铁液能平稳注人 , 不得形成紊流 性能和铸造器件的使 用情 况是 密不可分的 。在灰铸铁器件工作 中 , 或喷射 。b . 尽量使铁液 流经 的整个通 道在砂芯 内生 成 , 通 常坭 芯砂 其 良好 的减震性 、 耐磨性 以及切削加工性能成 为其 在 目前社会工业 ( 热法覆膜砂或冷芯砂) 较 之外模粘 土砂更耐 高温铁液冲刷 。而直浇 生产 中得 以广泛使用 的关键所在 。 道难 以避免设置在外模 的粘 土砂 砂型 中通过 , 这时可在直浇 口与横 2灰铸铁缺 陷存 在的原 因 浇V I 搭接 处设置过滤器 ( 最好是 泡沫陶瓷质) , 可以将铁液在 直浇道 随着我国国民经 济从计划 经济向市场经济的转变 , 解决 灰铸铁 内可能冲刷下来的散砂 和铁 液夹渣加 以过滤 , 从 而可减少砂眼和渣 器件铸造 的关 键技术既是 一种与生产 厂家经济效益 息息相关 的技 眼 。 术, 更是各生产企业和厂家竞争力 的体现 。这 就造 成这 种技术在交 3 . 3 夹渣 流与应用中受到一定 的限制与影 响。 关 于灰铸铁件存在缺陷 的主要 灰铸铁件也容易 出现夹 渣问题 , 如 氧化夹渣 以团絮状存 在于铸 原因主要有冷却速度 、 孕育处理 、 过热处理 以及炉料等 四个方面 。 件 内部断 口呈黄色或 灰白色 , 无光泽 ; 溶剂夹渣呈 暗褐 色点状 , 夹渣 2 . 1 关于冷却速度 的影响 ,铸铁是一种对冷却 速度 敏感 性很大 清除后呈 光滑表面 的孔洞 , 在 空气 中暴漏一段 时间后 , 有 时出现腐 的材料 , 同一铸件 的厚壁和薄 壁部分 , 内部和外表都 可能获得 相差 蚀特征 , 一般存在于铸件上部或浇 注死 角部 位。形成原因主要是 因 悬殊的组织 , 俗称为组织的不均匀性 。因为石 墨化 过程在很 大程度 为氧化夹 渣以团絮状存在 于铸 件 内部 断 V I 呈黄色 或灰 白色 ,无光 上取决于冷却速度。 泽 ,溶剂 夹渣呈 暗褐 色点状 , 夹渣清除后呈光 滑表面 的孔洞 , 在空 2 . 2关 于铁 液孕育处理的影响 , 孕育处理 就是在铁液进 入铸 件 气 中暴漏 一段时间后 , 有 时出现腐蚀特征 , 一般存 在于铸件 上部或 型腔前 , 把孕育剂 附加到铁液 中以改变铁液 的冶 金状态 , 从 而可改 浇注死角部位 。 善铸铁的显微组织和性能 。 夹渣控制 2 . 3关 于铁 液过热处 理的影 响 , 提 高铁液 过热温 度可 以 : ① 增 严格按精炼变质浇注工 艺操 作 , 浇注 时应使金属液流平稳 的注 加化合碳 含量和相应减少石 墨碳含量 , ②细化石 墨 , 并 使枝 晶石墨 入铸型 , 采用过滤技术 , 炉料应保持清洁 , 回炉料处理及使用量应严 的形成 , ③消除铸铁的“ 遗传性 ” , ④ 提高铸件断面上组织 的均匀性 , 格遵守工艺规章。 ⑤ 有利于铸件的补缩 。 同样 , 铁液保温也有铁液过热的类 似作用 。 3 . 4物理力学性能不合格等其他缺陷 2 . 4关 于炉料特性的影响 , 实际生产 中往 往发现改变金 属炉料 铸件强 度 , 硬度 , 伸长 率及耐热 , 耐蚀 , 耐 磨和 电性 能等不符 合 而化学成分似乎无变化的情况 下铸铁具有不同 的组织和性能 , 这说 技术条件 的规定 , 主要原 因是 因为合金成分不 合格 , 要想控制 铸铁 明原材料的性质直接影响着用 它熔炼 出来 的铸铁 的性质 。 件的物理力学性能 ,就要改 善金相不合格或热处理不合适等 因素 , 3灰铸铁件缺陷及控制措施 并根据需要调整合金成 分 , 热处理等。 3 . 1气孔 结束语 气孔是灰铸 铁件 中最 为常见的缺陷之一 , 其存 在与出现即容易 铸造是 目前社会 发展 的基 础 ,也是 制造装 备 的主要手段 和方 造成整个铸件成为废 品。 一般来 说 , 在灰铸铁件加工铸造 的过程 中 , 法 。 在 目前 的社会发展中铸造技术的高低和逐渐 品质 的优劣直接影 由于温度变化大 ,使得灰铸铁 器件的冷却系数和冷却速度加快 , 从 响着现代化工业发展以及装备技 术的性能 , 同时对于服役寿命 以及 而造成了灰铸铁器件中出现了相应的气孔现象 , 这 种现象产生的主 相关 的使用安全提出了新的要求 。 进人 2 1 世纪以来 , 我 国灰铸铁件 要原因在于器件内外部温 度相差悬殊而产生 了一定的不均匀性 。 究 产量 已居世界首位 , 若铸件存在缺 陷 , 即使没达到废 品的水平 , 也会 其产生的原因 , 主要是 由于设备在运行 的过程 中型腔排 气孔的应用 降低铸件的等级 , 故控制铸件缺陷有着重大的经济意义。
- 1、下载文档前请自行甄别文档内容的完整性,平台不提供额外的编辑、内容补充、找答案等附加服务。
- 2、"仅部分预览"的文档,不可在线预览部分如存在完整性等问题,可反馈申请退款(可完整预览的文档不适用该条件!)。
- 3、如文档侵犯您的权益,请联系客服反馈,我们会尽快为您处理(人工客服工作时间:9:00-18:30)。
灰铸铁件无热处理工艺探讨
1.问题的由来
常规厂家的灰铸铁件铸造后,均会对其进行去应力退火或高温退火热处理工序,特殊情况下对铸件进行表面硬化热处理。
对于汽车行业发动机缸体灰铸铁件的强度和性能均要求较高。
在保证铸件的强度和性能不降低的情况下,对灰铸铁件铸造后不热处理工艺进行探讨。
2.影响灰铸铁性能的因素
灰铁材质性能主要取决于化学成分及铸造过程中的冷却速度,同时,冶金因素也对灰铁性能有一定的影响,如原材料、炉料组成、熔化工艺操作、温度控制、炉前处理、浇筑温度等。
3.问题探讨
在产品确定灰铁材质各化学成分范围后,铸造厂家对化学成分调整的空间基本锁定,只可能对部分合金元素进行微调。
要达到灰铁件生产后不进行热处理,要满足两个条件:一是铸件生产完成后较低的应力甚至是完全消除应力。
二是保证铸件有良好的切削加工性能。
铸件内应力的产生,主要是因为铸件的厚度不均,冷却时的冷却速度不同,铸件收缩不一致产生内应力。
在铸造工艺上,合理控制铁水浇筑温度,采用同时凝固,浇筑完成后严格控制保温时间等,从而使生产出的铸件处于低内应力状态。
灰铸铁件本身具有良好的切削加工性能,在铸件的生产过程中,易因冷却速度不同在铸件的表层形成渗碳体组织,即白口倾向,使铸件的切削加工性能变差。
在铸件生产过程中合理使用孕育剂,消除或减轻白口倾向,并通过工艺避免出现过冷组织来保证铸件的切削加工性能。