甲醇合成气压缩机操作规程
甲醇合成—甲醇合成操作
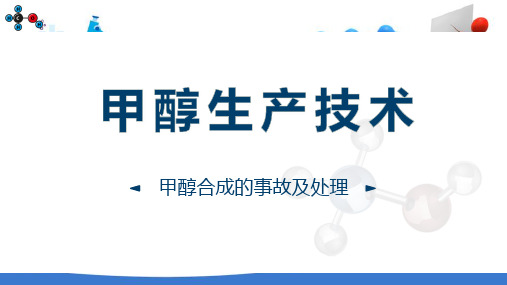
一、甲醇合成塔温度急剧上升
1.循环量突然减少; 2.汽包压力升高; 3.汽包连锁失灵出现事故; 4.气体成分突然发生变化,CO含量升高; 5.新鲜气量增加过快; 6.操作失误,调节幅度过大。
原因分析
一、甲醇合成塔温度急剧上升
处理方法:
1. 增加循环量; 2. 调节汽包压力使之恢复正常值,必要时可加大排污量或调整循环
三、日常停车安全操作规程
4.系统降压、降温必须按操作法规定的速率严格进行,防止串压、超温现象发生,并 做好记录工作。 5.机泵停车后按操作法做好备机状态的阀门确认工作,如需隔离,按隔离、排放操作 要求进行。 6.冬季停车后,要排尽蒸汽、冷却水等处积水,以防受冻。 7.发生爆炸、着火、大量泄漏等事故时,应首先切断气源,同时迅速通知其他岗位并 向车间及生产部报告。 8.更换触媒时必须先进行钝化,防止卸出地触媒燃烧造成人身伤害。
甲醇合成工段日常操作安全技术要求
一、甲醇气液分离器的作用
甲醇合成工段日常操作维护应严格按照 《甲醇合成岗位操作规程》进行操作,谨防 误操作引起事故。
一、日常运行安全操作规程
✓ 1.操作员必须遵守工艺纪律,不得擅自改变工艺指标,其修正或改变要以车间或 生产部印的书面通知为准。
✓ 2. 操作员必须严格执行“操作工的六严格”规定,不得擅自离开工作岗位。 ✓ 3.安全联锁不得随意拆卸和解除,声、光报警信号不能随意切断。 ✓ 4.现场检查时不准踩踏管道、阀门、电线、电缆架和仪表管线等设施,去危险地
✓ 11. 如发现甲醇或可燃性气体着火时,应视其部位迅速作出判断,边汇报边处理。
二、日常开车安全操作规程
1. 必须按操作规程和开车指令进行,对停车时动过的阀门要逐个确认, 水、电、汽、氮必须符合开车要求。 2. 检查阀门开闭状况及盲板抽加情况,保证装置流程畅通。 3. 开车工作按指令根据操作法逐步进行,不具备条件不赶进度,条件具 备不失时机。
合成气压缩机操作规程

合成气压缩机岗位操作规程1、岗位职责1.1在甲醇班长的领导下,直属中控室指挥,完成本岗位的生产任务。
1.2严格执行本岗位操作技术规程和安全规程,不违章,不违纪,确保人身、设备安全和产品质量稳定。
1.3负责对各工艺数据如实记录,并定时向生产调度室报告并服从调度室的指挥及安排。
1.4负责本岗位设备及所属管道阀门控制点、电气、仪表、安全防护设施等的管理。
1.5管好岗位所配工具、用具、防护器材、消防器材,通讯联络设施和照明。
1.6负责本岗位所管理设备的润滑、维护保养、环境卫生清洁,严防各种跑、冒、滴、漏事故的发生。
1.7发现生产异常或设备故障时应及时处理,并将发生的原因和处理经过及时向班长和生产调度室汇报,并如实记录。
1.8负责在《岗位操作记录报表》上填写各项工艺技术参数;在《生产作业交接班记录》中填写生产记录。
1.9按交接班制度认真做好交接班。
1.10服从班组和各部门分配工作,努力完成各项工作任务。
2、岗位工艺技术规定与操作指标(标准)2.12.2岗位任务2.2.1本岗位主要任务是:先将转化工序来的新鲜气压力2.0Mpa,温度40℃压缩至5.9Mpa,然后与来自合成系统的5.9MPa循环气一起在循环段中混合,再经循环段压缩至6.1MPa后去合成装置。
2.2.2联合压缩机工艺气流程叙述`来自转化工段的新鲜气,温度40℃,压力2.0MPa,进入合成气压缩机一段,压缩至约3.5MPa,气体温度升至108℃左右,经中间气体冷却器冷却至40℃,并经分离掉冷凝水后进入二段继续加压至5.9MPa与来自甲醇合成的循环气混合,压缩至6.1MPa。
压缩机出口合成气送至甲醇合成。
来自中压蒸汽管网的动力蒸汽,温度435℃,压力3.4MPa,经主汽阀、调节阀进入汽轮机,作功后排汽温度49℃,压力0.012MPa,进入凝汽器,经冷却水冷凝后,冷凝液用冷凝液泵(AB)打入二级射汽抽气器作为二级射汽抽气器和轴封冷却介质,最后送至合成除氧器。
甲醇合成操作规程

1、岗位的任务本工段是将压缩工段来的工艺气体,在一定的压力(5.3MPa)、温度(220~260℃)、触媒作用下合成粗甲醇,并利用其反应热副产3.9MPa中压蒸汽减压至1.3MPa送入管网。
同时将合成驰放气与膨胀气送往转化工段。
2、工艺过程概述2、1 甲醇合成原理:合成工艺气体中的CO、CO2分别与H2在铜基催化剂的作用下主要生成甲醇,同时还伴有许多副反应。
主反应:CO+2H2=CH3OH+QCO2+3H2= CH3OH+H2O+Q主要副反应:2CO+4H2=CH3OCH3+H2O4CO+8H2=C4H9OH+3H2OCO+3H2=CH4+H2O2CO+2H2=CH4+CO22、2 工艺流程经脱硫、转化制得总硫含量小于0.1ppm,(H2-CO2)/(CO+CO2)=2.72的合格新鲜合成气。
经合成气压缩机C3002的压缩段加压至5.3MPa与循环段加压至5.3MPa温度约为60℃的循环气混合,混合后的入塔气以每小时540000NM3的流量进入入塔气预热器E4001A.、B的壳程,被来自合成塔R4001A.、B反应后的出塔热气体加热到225℃后,进入合成塔R4001A.、B顶部。
R4001A.、B为立式绝热——管壳型反应器。
管内装有低压甲醇合成催化剂。
当合成气进入催化剂床层后,在5.30MPa,220~260℃下CO、CO2与H2反应生成甲醇和水,同时还有微量的其他有机杂质生成。
合成甲醇的两个反应都是强放热反应,反应释放出的热大部分由合成塔R4001A.、B壳程的沸腾水带走。
通过控制汽包压力来控制催化剂床层温度及合成塔出口温度。
从R4001A.、B出来的热反应气进入入塔气预热器E4001A.、B的管程与入塔合成气逆流换热,被冷却到90℃左右,此时有一部分甲醇被冷凝成液体。
该气液混合物再经水冷器E4002A、B进一步冷凝,冷却到≤40℃,再进入甲醇分离器V4002分离出粗甲醇。
分离出粗甲醇后的气体,压力约为 4.9MPa,温度约为40℃,返回C3002的循环段,经加压后循环使用。
甲醇合成气压缩机操作规程
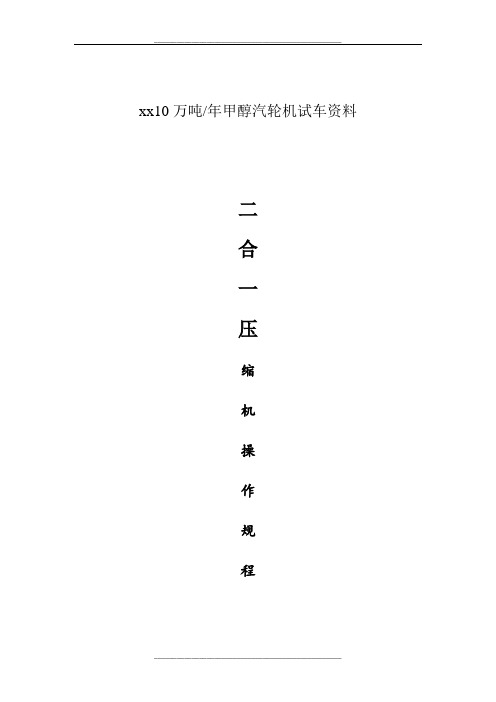
xx10万吨/年甲醇汽轮机试车资料二合一压缩机操作规程一、岗位的任务及意义合成气二合一压缩是将脱硫转化工段来的转化气经离心式压缩机的8级叶轮压缩后与来自合成的循环气共同经过第9级叶轮压缩,然后送入合成工序。
二、工艺过程概述2.1 工艺技术方案的选择压缩机的选择主要取决于装置的生产能力、气体的质量、气体的性质。
离心式压缩机适用于打气量大,压差小,气体质量好的气体场合,具有打气量大,维修少,无需看机,可用蒸汽透平驱动以提高能量转换,效率高等优点。
由转化来的转化气体压力1.6 MPa(G),甲醇合成需要的压力为5.3MPa(G),入塔气量要求大,压差小,因此选用一台离心式压缩机。
2.2 合成气压缩机流程2.2.1气体流程来自转化工序的合成新鲜气进入合成压缩机一、二段,压缩至4.8MPa(G),经冷却至40℃与来自甲醇合成的循环气(4.8MPa(G)、40℃),一起进入合成压缩机的三段,经过三段压缩至5.3MPa(G),然后送甲醇合成工序。
根据生产实际运行情况,在压缩机出口设有两个防喘振阀门。
新鲜气和合成循环气的气量通过这来两个防喘振进行调解,当压缩机运行工况进入喘振区时,阀门自动联锁开启,以防止压缩机喘振。
2.2.2 蒸汽和冷凝液流程合成气压缩机采用蒸汽透平驱动,中压蒸汽3.14—3.45MPa(A),进入蒸汽透平机,汽轮机出口减压至0.01MPa(A),经过凝汽器的全冷凝,冷凝液用冷凝液泵打入冷凝液管网。
2.2.3 润滑油流程从润滑油箱来的润滑油通过润滑油泵(主辅油泵)加压,经一次油压调解后,压力0.85MPa(G),进入油冷却器,油过滤器,二次油压调节,供油压力在0.3MPa (G),然后分二路分别进入汽轮机,压缩机。
回路经回路总管返回润滑油箱。
油冷却器,油过滤器均为一开一备,在不影响系统运行的情况下,进行切换、清洗。
本系统设有高位油箱一个,当两台油泵同时发生故障时,高位油箱的单向阀会自动打开,通过高位差流到各个润滑油点,使机组在惰走时间内能得到充分润滑。
合成气压缩机操作规程

合成气压缩机岗位操作法编制:校核:审核:审定:批准:2008年5月20日第一章岗位任务及流程说明1.岗位任务将净化过来的新鲜气及合成过来的闪蒸气通过高低压缸压缩进入合成系统,同时对合成系统过来的循环气经循环段补充压力后与新鲜气一起进入合成系统进行合成氨反应。
2 流程简述2.1工艺气系统液氮洗过来新鲜气与氨合成装置过来闪蒸气汇合,气量110001Nm3/h、压力5.1MPA(A)、温度29.9℃,进入压缩机一段进口。
经一段缸压缩后,压缩机出口气体压力9.3MPA(A)、温度112.9℃。
气体经过段间冷却器E33101冷却后温度降到40℃进入压缩机高压缸。
在高压缸内新鲜气与合成装置过来的循环气汇合进入压缩机循环段。
经压缩机循环段压缩后,压缩机最终出口气体气量390084 Nm3/h、压力14.6 MPA(A)、温度59℃进入氨合成装置。
2.2蒸汽系统来自管网的 3.9MPa(A)420℃的蒸汽经汽轮机主汽阀、蒸汽调节阀,进入汽轮机汽缸冲动转子做功后,进入表面冷凝器冷凝成液体,不凝气性体被抽气装置随同抽引蒸汽一起抽入抽汽冷凝器。
抽引蒸汽凝结成水返回表冷器,不凝性气体被排入大气中。
表面冷凝器内的蒸汽冷凝液降至凝汽器热井中,由凝结水泵P33102-1/ P33102-2送往锅炉房。
2.3油系统流程合成气压缩机设置有主、辅油泵,结构为螺杆式,均由电机带动。
由油箱出来的油经润滑油泵P33101-1/P33101-2加压后,经PCV33105控制泵出口压力,进入油冷器E33105-1/E33105-2 与油冷器管程内的循环水换热,冷却至45℃,进入油过滤器进行过滤,从过滤器出来的油分二路,一路经PCV33151减压,供给机组各轴承及润滑油高位槽,经其回油管到机组回油总管至油箱。
另一路作为汽轮机的调节油,供给调节系统的各部件,然后经其回油管到机组回油总管至油箱。
第二章设备说明合成气压缩机数据表低压缸数据汽轮机数据表合成气压缩机设备表第三章主要工艺指标一览表第四章联锁说明一、联锁紧停系统工艺描述合成气压缩机停车触发条件:E-33301出口温度过高(TSXH-33303和TSXH-33333) V-33302液位过高(LSXH-33315)E-33302出口温度过高(TSXH-33328和TSXH-33304) 锅炉E-33302液位过低(LSXL-33302)V-33301液位过高(LSXH-33310)冷冻压缩机停车合成手动停车来自装置前端的停车信号高压缸、低压缸、汽机轴位移高高润滑油压力PT33150~PT33152低低(三选二)控制油压力PS33152压力低低干气密封排气压力低低高压缸、低压缸、汽机轴振动高高高压缸、低压缸、汽机止推瓦、径向轴承温高高一段入口阀全关电子超速保护(三选二)现场、控制室紧急停车阀门动作:自动关闭压缩机出口和循环段进口大阀(XV-33307、XV-33308) 自动关闭一段进口阀(XV-33310)自动打开放空阀 (XV-33309、XV-33311)自动打开防喘振阀(FV33307、FV33314、FV33380)二、允许启动联锁说明主汽阀全关(ZS33151)油温正常一段防喘振阀全开、二段防喘振阀全开、循环段防喘振阀全开润滑油压正常控制油压正常循环段入口阀(XV-33308)全关循环段出口阀(XV-33307) 全关盘车电机托开以上条件满足现场、控制室允许启动灯亮第五章正常操作第一节原始开车或大修后的开车1、开车前的准备:1.1机械、电气、仪表检查确认。
20万吨焦炉气制甲醇操作规程
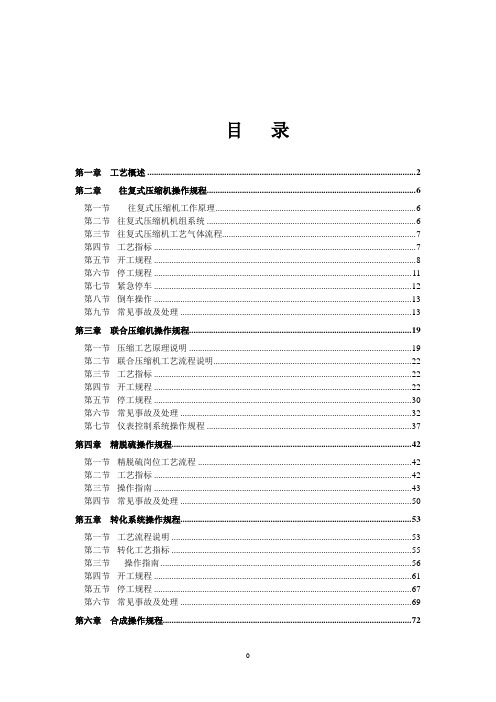
第六节
一、停车步骤
1)、接到调度停车通知后,注意检查各级压力,并做好停车准备工作,准备从高压端到低压端的顺序切气;
2)、减量:通知转化岗位准备减量,开一回一减量,当全开还需减量时,可开四回一进行大减量,减量的多少,应根据转化系统平稳状况,减到转化所需的压力时准备切气;
温度(供水/回水)
32/42℃
污垢系数
0.00034m2K/w
碳钢年腐蚀速度
<0.125mm/a
Cl-1
<100mg/L
SS
≤20 mg/L
PH值
6.5~9.5
浓缩倍数
K=3
4、生活用水和消防水
压力
0.5MPa(A)
温度
环境温度
5、精制脱盐水
压力
0.5MPa(A)
温度
≤40℃
电导率(25℃)
≤0.2us/cm
设计操作时间:8000小时/年
其工艺路线为:
1、脱油、粗脱硫、加氢串氧化锌干法脱硫
2、催化氧化
3、合成气及循环气联合压缩
4、低压法合成甲醇
5、粗甲醇3塔精馏
6、汽提法处理工艺冷凝液
二、主要工艺特点
1、采用2.3MPa(G)催化氧化制取甲醇合成气;
2、采用低压甲醇合成工艺以及副产中压蒸汽的管壳式等温甲醇合成塔,其能耗低,产品质量好,运行可靠,投资省;
7)、建立电机用油系统:由电工加入分析合格的润滑油进电机滑油系统,并保持油位2/3以上,最后检查是否有泄漏等情况,并处理至合格。
8)、建立注油系统:加入分析合格的润滑油进注油箱,保持油位1/2以上,然后用手盘动手柄数圈,无问题后开启注油器建立注油系统,并检查注油情况,如有泄漏、堵塞等现象,则停止注油,待处理合格后重新建立注油系统。
甲醇合成的工艺流程
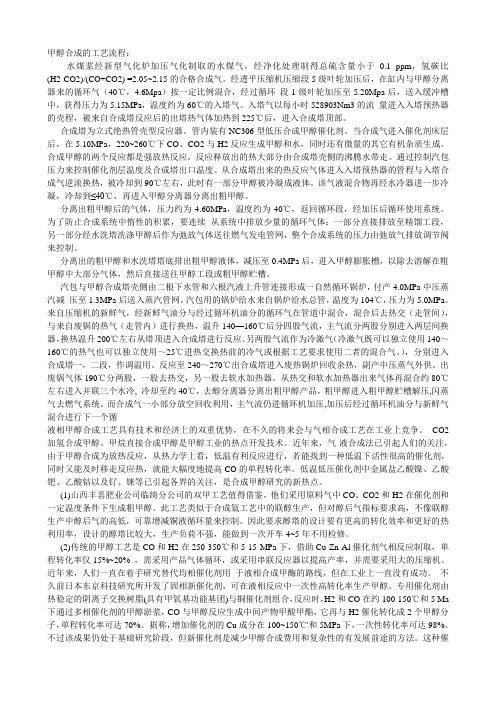
甲醇合成的工艺流程:水煤浆经新型气化炉加压气化制取的水煤气,经净化处理制得总硫含量小于0.1 ppm,氢碳比(H2-CO2)/(CO+CO2) =2.05~2.15的合格合成气。
经透平压缩机压缩段5级叶轮加压后,在缸内与甲醇分离器来的循环气(40℃,4.6Mpa)按一定比例混合,经过循环段1级叶轮加压至5.20Mpa后,送入缓冲槽中,获得压力为5.15MPa,温度约为60℃的入塔气。
入塔气以每小时528903Nm3的流量进入入塔预热器的壳程,被来自合成塔反应后的出塔热气体加热到225℃后,进入合成塔顶部。
合成塔为立式绝热管壳型反应器。
管内装有NC306型低压合成甲醇催化剂。
当合成气进入催化剂床层后,在5.10MPa,220~260℃下CO、CO2与H2反应生成甲醇和水,同时还有微量的其它有机杂质生成。
合成甲醇的两个反应都是强放热反应,反应释放出的热大部分由合成塔壳侧的沸腾水带走。
通过控制汽包压力来控制催化剂层温度及合成塔出口温度。
从合成塔出来的热反应气体进入入塔预热器的管程与入塔合成气逆流换热,被冷却到90℃左右,此时有一部分甲醇被冷凝成液体。
该气液混合物再经水冷器进一步冷凝,冷却到≤40℃,再进入甲醇分离器分离出粗甲醇。
分离出粗甲醇后的气体,压力约为4.60MPa,温度约为40℃,返回循环段,经加压后循环使用系统。
为了防止合成系统中惰性的积累,要连续从系统中排放少量的循环气体:一部分直接排放至精馏工段,另一部分经水洗塔洗涤甲醇后作为弛放气体送往燃气发电管网,整个合成系统的压力由弛放气排放调节阀来控制。
分离出的粗甲醇和水洗塔塔底排出粗甲醇液体,减压至0.4MPa后,进入甲醇膨胀槽,以除去溶解在粗甲醇中大部分气体,然后直接送往甲醇工段或粗甲醇贮槽。
汽包与甲醇合成塔壳侧由二根下水管和六根汽液上升管连接形成一自然循环锅炉,付产4.0MPa中压蒸汽减压至1.3MPa后送入蒸汽管网。
汽包用的锅炉给水来自锅炉给水总管,温度为104℃,压力为5.0MPa。
甲醇生产工艺操作规范
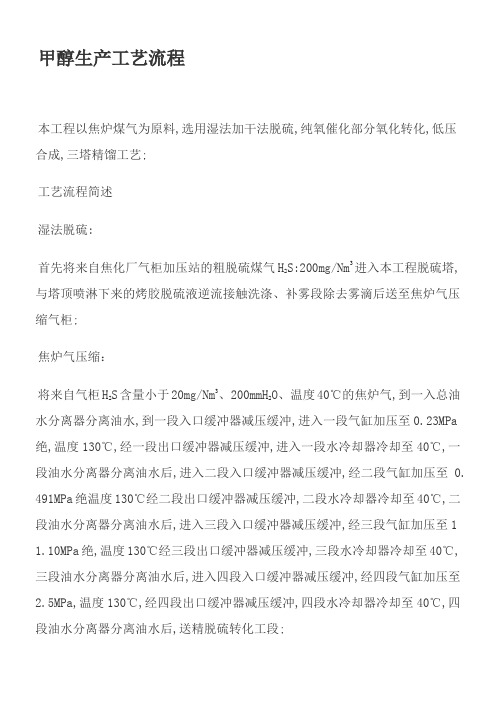
甲醇生产工艺流程本工程以焦炉煤气为原料,选用湿法加干法脱硫,纯氧催化部分氧化转化,低压合成,三塔精馏工艺;工艺流程简述湿法脱硫:首先将来自焦化厂气柜加压站的粗脱硫煤气H2S:200mg/Nm3进入本工程脱硫塔,与塔顶喷淋下来的烤胶脱硫液逆流接触洗涤、补雾段除去雾滴后送至焦炉气压缩气柜;焦炉气压缩:将来自气柜H2S含量小于20mg/Nm3、200mmH2O、温度40℃的焦炉气,到一入总油水分离器分离油水,到一段入口缓冲器减压缓冲,进入一段气缸加压至0.23MPa 绝,温度130℃,经一段出口缓冲器减压缓冲,进入一段水冷却器冷却至40℃,一段油水分离器分离油水后,进入二段入口缓冲器减压缓冲,经二段气缸加压至0. 491MPa绝温度130℃经二段出口缓冲器减压缓冲,二段水冷却器冷却至40℃,二段油水分离器分离油水后,进入三段入口缓冲器减压缓冲,经三段气缸加压至1 1.10MPa绝,温度130℃经三段出口缓冲器减压缓冲,三段水冷却器冷却至40℃,三段油水分离器分离油水后,进入四段入口缓冲器减压缓冲,经四段气缸加压至2.5MPa,温度130℃,经四段出口缓冲器减压缓冲,四段水冷却器冷却至40℃,四段油水分离器分离油水后,送精脱硫转化工段;转化:焦炉气来自压缩机的压力2.5MPa,温度40℃的焦炉气经过过滤器F61201A/B.过滤器分离掉油水与杂质;再经预脱硫槽脱除大部分无机硫后去转化工段焦炉气初预热器预热300℃、压力2.5MPa;回精脱硫的一级加氢转化器,气体中的有机硫在此进行加氢转化生成无机硫;不饱和烃生成饱和烃;加氢后的气体进入中温脱硫槽D61203ABC脱除绝大部分的无机硫;之后再经过二级加氢转化器D6 1205将残余的有机硫进行转化;最后经过中温氧化锌D61204AB把关;使出口焦炉气中总硫<0.1ppm后送至转化工序;精脱硫来的29196Nm3/h焦炉气总硫 0.1ppm和转化废热锅炉自产蒸气14.376t /h混合进入C60602焦炉气预热器〈壳程〉预热330℃,进入B60601预热炉预热至660℃,进入D60601转化炉混合室,与来自空分氧气5864m3/h,纯氧和经过B6 0601上段预热至300℃3.5t/h自产蒸汽的进入转化炉上段,进行纯氧蒸汽部分氧化燃烧、,温度达950-1250℃左右,高温气体在经催化剂床层进行甲烷蒸汽转化,控制出口气体CH4≤0.6%;温度≤985℃,经C60601废热锅炉回收热量,每小时产生2.95MPa的蒸汽:约22.371t/h,供转化和外管网用,废热锅炉出口气体温度降至540℃,进入C60602焦炉气预热器〈管程〉与壳程气体换热后温度降至370℃,再经过C60603焦炉气初预热器〈壳程〉与〈管程〉焦炉气换热后出口温度280℃,经C60604锅炉给水预热器〈管程〉与来自锅炉的除氧水换热,出口温度降至161℃,经C60605脱盐水预热器〈管程〉与脱盐水站来的脱盐水〈壳程〉换热,出口温度降至113℃,经C60606采暖水预热器管程与采暖水管网来的采暖水〈壳程〉换热,温度降至90℃,经C60607水冷器〈管程〉与水〈壳程〉换热,出口温度降至40℃,经F60602气液分离器分离掉水分,出口温度约为40℃,经D60602常温氧化锌脱氯剂和氧化锌脱硫剂进一步脱氯、脱硫,再经过精密过滤器过滤气体后,去合成压缩机;合成:来自转化的新鲜原料气压力2.0Mpa,温度≤40℃进入二合一合成气压缩机组,经一段压缩后,与合成塔未反应的循环气压力5.4Mpa,温度≤40℃混合,再经过二段压缩压力5.9Mpa,温度≤73℃,出压缩机的混合气体去甲醇合成工段;来自合成气压缩630的合成气,温度73℃,压力5.9MPa,经气气换热器C40001B -A预热到225℃,进入甲醇合成塔D40001,在催化剂的作用下进行甲醇合成反应CO+2H2=CH3OH+Q、CO2+3H2=CH3OH+H2O+Q及副反应4CO+8H2=C4H9OH+3H2O等等;甲醇合成塔为管壳式反应器,管内填装触媒,反应管外为沸腾热水,利用反应热副产中压饱和蒸汽;合成塔出口气进气气换热器C40001A-B与合成塔入口气换热,把入口气加热到活性温度以上,同时合成塔出口气温度降至100℃,经水冷器C40002冷却到40℃后,进入水洗塔F40003进行气液分离并把反应气中未冷凝的甲醇洗出来;水洗塔为分离和洗醇一体的新型设备,在分离器的下部进行甲醇分离,上升的气体与塔顶喷淋下来的水逆流接触,气体中的甲醇溶解在水中,形成稀醇水落入分离器底部,与分离的粗甲醇一并进入过滤器,过滤出石蜡等固体杂质后送往精馏系统进行精馏;出水洗塔的气体大部分作为循环气去合成气压缩增压循环利用,提高气体的总转化率;一小部分作为弛放气,压力约5.4MPa g,经一次调节阀减压和二次调节阀减压后,送往转化装置、锅炉装置作燃料气;还有一小部分用于调整系统压力的放空气,送火炬燃烧;精馏:从合成工段来的粗甲醇,温度40℃,压力0.5MPag,通过粗甲醇缓冲槽F40501,流量为19043.231kg/h,经粗甲醇预热器C40510预热到65℃进入预精馏塔E405 01,调节粗甲醇缓冲槽液位的多余粗甲醇送入粗甲醇中间槽;当合成产量无法保证预塔进料时,启动粗甲醇泵补充进料;为中和预塔塔底的少量酸,用固体NaOH在配碱槽F40506配制5%碱液,流至碱液槽F40507,然后用碱液泵J40506A/B沿入口管线向预塔内加入碱液约25 kg/h,控制预塔的塔釜内液体PH=9~10范围内;从预塔E40501塔顶出来的气体温度75℃,压力0.05MPag,经预塔冷凝器IC405 02和预塔冷凝器IIC40503用循环水分级冷凝后,温度降到40℃,冷凝下来的甲醇溶液收集在预塔回流槽F40508内,通过预塔回流泵J40509A/B加压后,从预塔的塔顶进入到预塔内,预塔再沸器C40501的能力要满足一定的回流比;预塔再沸器的热源为低压蒸汽;预塔冷凝器IIC40503中不凝气、预塔E40501塔顶少量的排放气和各塔顶部气体管线上安全阀后的排放气体,均通入排放槽F40504,用软水吸收回收甲醇后高空排放;回收的甲醇液自流入地下槽F40505内,有液下泵打至粗甲醇中间槽继续精馏;从预塔塔底出来脱除轻组分后的预后甲醇,温度为85℃,压力为0.08MPa,用预后甲醇泵J40501A/B抽出,送入加压精馏塔E40502,加压精馏塔E40502的操作压力为0.7MPag,塔底有再沸器C40504加热,使塔底料液维持在135℃,压力0.7 MPa,从甲醇加压塔塔顶出口的甲醇蒸汽温度123℃,压力0.6MPa,在常压塔再沸器C40507中冷凝,释放的热用来加热常压塔E40503中的物料;常压塔再沸器出口的甲醇冷凝液进入加压塔回流槽F40502一部分由加压塔回流泵J40502A/B 在流量控制下送回加压塔顶回流;另一部分作为成品甲醇,成品甲醇首先经粗甲醇预热器C40510冷却,再经精甲醇冷却器C40505冷却到大约40℃,送往精甲醇中间槽F40510A/B;控制加压塔的液面使过剩的产物在135℃下进入常压塔E4 0503,常压塔E40503底部产物在107℃和0.08MPag压力条件下,由加压塔顶产物的冷凝热再沸;离开常压塔顶的蒸汽约65℃压力0.03MPa,在常压塔顶冷凝器C40506中冷却到40℃后送到常压塔回流槽F40503,在流量控制下,再用常压塔回流泵J40503A/B将回流液送回塔顶,其余部分作为精甲醇产品送入精甲醇中间槽F40510A/B;精甲醇中间槽的甲醇产品经分析合格后,通过精甲醇泵J40507 A/B送入到成品罐区;常压塔底的产物是水,含有微量的甲醇和高沸点杂醇;为防止高沸点的杂醇混入到精甲醇产品中,在常压塔E40503的上部和中下部有杂醇采出,温度约85℃,压力约0.035MPag,经杂醇冷却器C40509冷却到40℃,压力0.025MPa后,靠静压送到杂醇贮槽F40509,再通过杂醇泵J40510送到成品罐区贮存;从常压塔E40503底部排出的废水温度105-110℃,压力约0.08MPag,经残液泵送至残液冷却器冷却至40℃,分析甲醇含量≦0.2%时直接排入排水沟;甲醇含量≧0.2%时送至粗甲醇贮槽F40511;排放的污甲醇排到地下槽F40505,经地下槽液下泵J40505送到粗甲醇贮槽F40 511;开车时或事故状态下,经分析精甲醇中间槽F40510A/B内不合格的精甲醇由精甲醇槽底部与粗甲醇槽出口管道一并进入粗甲醇泵,向塔内进料;燃气锅炉:由焦化装置产生的合格焦炉煤气,通过煤气母管送入燃气锅炉进行燃烧,燃气锅炉所产生的热加热锅炉给水,使其便为中压蒸汽,锅炉蒸汽供应工艺转化、甲醇精馏等用户;。
甲醇合成操作规程
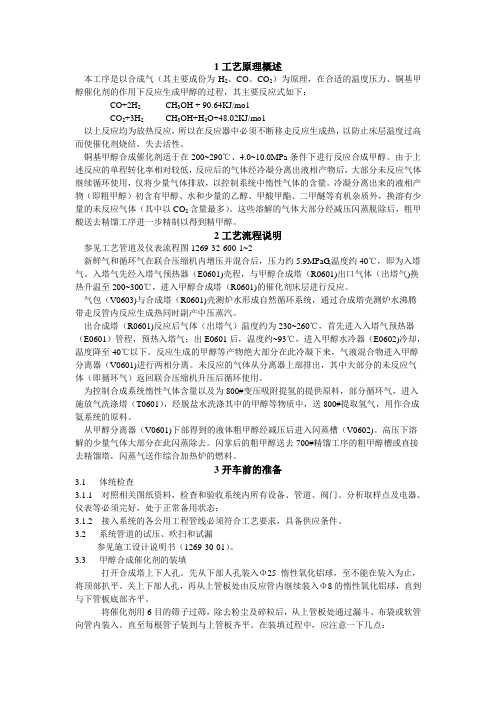
1工艺原理概述本工序是以合成气(其主要成份为H2、CO、CO2)为原理,在合适的温度压力、铜基甲醇催化剂的作用下反应生成甲醇的过程,其主要反应式如下:CO+2H2 CH3OH + 90.64KJ/mo1CO2+3H2CH3OH+H2O+48.02KJ/mo1以上反应均为放热反应,所以在反应器中必须不断移走反应生成热,以防止床层温度过高而使催化剂烧结,失去活性。
铜基甲醇合成催化剂适于在200~290℃、4.0~10.0MPa条件下进行反应合成甲醇。
由于上述反应的单程转化率相对较低,反应后的气体经冷凝分离出液相产物后,大部分未反应气体继续循环使用,仅将少量气体排放,以控制系统中惰性气体的含量。
冷凝分离出来的液相产物(即粗甲醇)初含有甲醇、水和少量的乙醇、甲酸甲酯、二甲醚等有机杂质外,换溶有少量的未反应气体(其中以CO2含量最多)。
这些溶解的气体大部分经减压闪蒸脱除后,粗甲酸送去精馏工序进一步精制以得到精甲醇。
2工艺流程说明参见工艺管道及仪表流程图1269-32-600-1~2新鲜气和循环气在联合压缩机内增压并混合后,压力约5.9MPaG,温度约40℃,即为入塔气。
入塔气先经入塔气预热器(E0601)壳程,与甲醇合成塔(R0601)出口气体(出塔气)换热升温至200~300℃,进入甲醇合成塔(R0601)的催化剂床层进行反应。
气包(V0603)与合成塔(R0601)壳测炉水形成自然循环系统,通过合成塔壳测炉水沸腾带走反管内反应生成热同时副产中压蒸汽。
出合成塔(R0601)反应后气体(出塔气)温度约为230~260℃,首先进入入塔气预热器(E0601)管程,预热入塔气;出E0601后,温度约~93℃,进入甲醇水冷器(E0602)冷却,温度降至40℃以下。
反应生成的甲醇等产物绝大部分在此冷凝下来,气液混合物进入甲醇分离器(V0601)进行两相分离。
未反应的气体从分离器上部排出,其中大部分的未反应气体(即循环气)返回联合压缩机升压后循环使用。
甲醇厂合成工序开车方案与操作规程

合成工序开车方案与操作规程编写:狄伟峰朱峻峰王芳审核:审定:批准:1、岗位任务本工序的任务是将压缩机岗位送来的工艺合成气,在一定温度(210~290℃)、一定压力(5.0~5.5Mpa)及触媒作用下,在甲醇合成塔内合成粗甲醇,并利用其反应热副产中压蒸汽,同时将粗甲醇送至精馏系统或粗甲醇贮槽,闪蒸汽送煤压机进口。
部分弛放气送往联合压缩机循环段循环利用,部分驰放气送焦炉或转化工序作燃料。
2、生产原理及流程叙述2.1甲醇合成原理甲醇合成是在一定温度、压力及铜基催化剂作用下,工艺气体中的CO、CO2与H2反应生产成甲醇,基本反应式为:主反应:CO+2H2=CH3OH+Q CO2+3H2=CH3OH+H2O+Q主要副反应:2CO+4H2=CH3OCH3+H2O+Q CO+3H2=CH4+H2O+Q4CO+8H2=C4H9OH+3H2O+Q CO2+H2=CO+H2O-QnCO+2nH2=(CH2)n+nH2O+Q甲醇主反应是可逆放热反应,反应时体积缩小,并且只有在催化剂存在的条件下,才能较快进行。
因此,甲醇合成反应必须在适当压力及温度下进行,合成气才能获得较高的转化率。
2.2工气流程叙述甲醇合成塔(R301)为管壳式反应器,管内装有铜触媒,反应管外为沸腾热水,利用反应热副产中压饱和蒸汽,合成塔出口温度是由汽包(F303)压力调节阀PRCA-305控制。
来自联合压缩机的合成气经入塔预热器(E301)与出合成塔(R301)的出塔气进行换热,入塔气被加热到200℃左右进入合成塔进行甲醇合成反应;出塔气被冷却至90℃,再经水冷器(E302)冷却到40℃,这时出塔气中绝大部分甲醇被冷凝下来,然后进入甲醇分离器(F301)进行气液分离。
甲醇分离器分离后的气体大部分作为循环气送至联合压缩机的循环段,加压后与联合压缩机新鲜段出来的合成气混合,再送到合成系统循环利用。
另一部分作为驰放气排出系统,这是由于新鲜中气中有氮气及甲烷等惰性气体存在,在甲醇合成过程中虽然不参与化学反应,也不会对催化剂造成太大的危害,但是随着合成反应的进行,系统内惰性气体含量会越来越多,为了避免惰性气体的积累必须将部分循环气体从合成回路中排出,以使合成回路中惰性气体含量保持在一定浓度范围,驰放气正常情况下作为燃料送至燃料气系统,事故情况下送至火炬。
甲醇合成操作法讲解

第十二部分甲醇合成操作法第一章概述第一节岗位任务1将合成气压缩机送来的合格合成气,经换热器提温后送入甲醇合成塔内,在适宜的压力、温度与催化剂的作用下合成甲醇。
2•利用废热锅炉回收出甲醇合成塔气体热量,副产0.5Mpa蒸汽。
3. 将分离器后的粗甲醇经降压闪蒸后送入粗甲醇中间槽或精馏系统。
第二节工艺原理甲醇合成是H2与CO CO在一定压力、温度及催化剂的条件下,按下述反应式进行的化学反应;一、主反应:C0+2年CHOH+90.56kj/molCO+3H = CH0H+H0+49.43kj/mol二、主要副反应:2CO+4涉CHOCH+HO4CO+8涉GF9OH+3HDCO+3涉CH+H2O2CO+2H=2H?O+2CO三、甲醇合成反应有如下特点:1放热反应:甲醇合成是可逆放热反应,反应过程中应采取必要的移热手段,使反应适应最佳温度曲线,达到较高的甲醇产量。
2、体积缩小反应:无论是CO与Hz合成甲醇还是CO与Hz合成甲醇,都是体积缩小反应,因此压力高有利于反应向生成甲醇的方向进行。
但是,压力提高将增加压缩机动力能耗,增加设备投资,且反应过程中的副产物将增加。
3、可逆反应:即CO CO与H合成甲醇的同时,甲醇也分解成CO CO与Hz,合成反应的转化率与反应压力、温度及(Hz- CO) / (C3 CQ)的比值有关,一般合成新鲜气的(Hz-CQ) / (CO^ CO) 控制在2.05〜2.15之间。
4、催化反应:甲醇反应在催化剂存在条件下才能较快的进行,没有催化剂存在时,即使在较高的温度和压力条件下,反应仍极慢的进行,低压法甲醇合成催化剂最佳使用温度范围为210〜270°C;5、循环反应:反应生成的甲醇与未反应的f、N2 CO CO等气体必须得到及时分离,降低反应生成物的浓度,以利提高合成反应的平衡浓度,甲醇分离后的一部分气体经循环机进行循环,为防止循环气中N2.CH4等惰性气累积和有效气组分降低,分离后的一部分排出甲醇合成装置。
二合一合成气压缩机操作

二合一二合一合成气压缩机操作发布日期:2011-1-1 实施日期:2011-1-10甲醇车间二合一二合一合成气压缩机操作手册编制:校核:审核:审定:批准:目录二合一合成气压缩机岗位操作法1 主题内容与适应范围 (1)2 压缩机岗位的任务 (1)3 工艺原理 (1)3.1汽轮机的工作原理: (1)3.2离心压缩机的工作原理 (1)4 流程简述 (2)4.1工艺气系统 (2)4.2蒸汽系统 (2)4.3油系统流程 (2)4.4分子筛系统流程 (3)5 设备说明 (3)5.1机组性能表 (3)5.2主要工艺指标一览表 (4)5.3设备一览表 (6)5.4仪表调节阀 (10)5.5仪表显示报警联锁一览表 (10)6 原始开车 (19)7 机组的热态启动 (28)8 机组正常停车 (39)9 机组紧急停车 (40)10 手动停车 (41)11 机组事故处理 (42)12 合成压缩的其它操作 (47)13.巡回检查及设备维护保养 (51)13.1压缩机 (51)13.2汽轮机 (52)13.3油系统 (52)13.4冷凝液系统 (53)14 岗位安全注意事项及冬季防冻 (54)14.1岗位安全注意事项 (54)14.2冬季防冻 (54)二合一合成气压缩机岗位操作法1 主题内容与适应范围本操作法规定了甲醇车间二合一合成气压缩机岗位的任务、工艺流程、主要设备的结构与性能、工艺操作指标、压缩机的正常操作、压缩机的正常开车、正常停车、紧急停车、压缩机的相关操作、事故原因及处理等有关事项。
本操作法适用于甲醇车间合成IV二合一合成气压缩机岗位的工艺操作。
2 压缩机岗位的任务将净化工段甲烷化来的40℃、3.05MPa的精制气和氢氨回收工序来的40℃、3.5MP氢气,进入一段加压至7.1MPa(A)温度为153℃后送往分子筛系统,经分子筛吸附净化的合成气温度5℃压力6.9MPa(A)进入二合一合成气压缩高压缸与氨合成工序来的循环气混合加压到15.45MPa,温度为72.6℃送至合成氨装置。
甲醇合成操作规程

合成部分第一节岗位的任务和管辖范围合成岗位的主要任务而言之有两个:一、是合成粗甲醇。
二、是回收反应热副产蒸汽。
净化工序送来的新鲜气,经联合压缩机压缩段压缩后和合成回路来的循环气混合,经循环段压缩后导入合成系统,在适当的压力、温度条件下,通过甲醇催化剂的作用使一定量的一氧化碳、二氧化碳和氢合成粗甲醇,分离后的气再循环使用,反应器管间的锅炉给水被反应热加热产生蒸汽送入汽包,通过压力(用于控制合成塔炉温)调节后送入蒸汽管网。
合成岗位的管辖范围包括:甲醇合成塔、塔前预热器、甲醇分离器,冷却器、合成汽包、洗醇塔、汽包上水泵、洗醇泵、软水槽,及以上设备所附属的设备管道、阀门、仪表、液位计等。
主要设备一览表第三节生产原理及工艺流程一、生产原理主反应:CO+2H2=CH3OH+QCO2+3H2=CH3OH+H2O+Q副反应:2CO+4H2=CH3OCH3+H2O+QCO+3H2=CH4+H2O+Q4CO+8H2=C4H9OH+3H2O+QCO2+H2=CO+H2O-QnCO+2nH2=(CH2)n+NH2O+Q甲醇主反应是可逆放热反应,反应时体积缩小,并且只有在催化剂存在的条件下,才能较快进行,所以反应在较高压力和适当的反应温度下进行,一氧化碳、二氧化碳才能获得较高转化率。
二、工艺流程说明来自净化温度为40度,压力为3—3.3MPa的新鲜气进入合成塔联合压缩机压缩段升压至 6.48MPa,经冷却分离水后与合成回来的循环气混合,进入循环段压缩至6.8MPa(温度48度)后送入合成系统.出循环段的合成气先经中间换热器管间.被管内反应气加热至220~225度由合成塔顶部斜向45度进入合成塔反应管顶端,沿轴向进入反应管.反应管内装有铜基催化剂,在催化剂的作用下合成甲醇.并伴有微量的副反应.反应后反应器底部出来的含甲醇7.0%温度为225度气体,进入中间换热器管内,与管间的气体换热后被降至97度;在此,有少量的甲醇气体冷凝;然后进入甲醇分离器分离甲醇,从分离器顶部出来的气体从洗醇塔中部进入,和从洗醇塔上部来的稀醇水在填料层逆流接触,气体中少量的甲醇被吸收.吸收少量甲醇的稀醇水减压后进入稀醇水槽,由洗醇水泵打入洗醇塔内,循环吸收.当甲醇浓度达到8~10%后,由洗醇塔后调节阀直接排入精馏工段.从洗醇塔顶部出来的气体,绝大部分是未反应的合成气及惰性气体.为防止惰性气体在系统中的累积,必须将一部分气体排出.排出后的循环气,进入联合压缩机的循环段,继续进行循环.驰放气送到总厂压缩三段出口回收利用.从甲醇分离器底部排出的甲醇,送入闪蒸槽.在此减压至0.3~0.4MPa并闪蒸出大部分溶解气体.闪蒸气送入总厂.闪蒸槽出来的粗甲醇送往粗甲醇计量槽或精馏生产.甲醇合成塔管间环隙通过汽包给水泵不断的打入锅炉给水.反应器与汽包通过上升管及下降管相连接,形成一个独立的蒸汽发生系统.汽包蒸汽出口管线压力控制阀,通过保持蒸汽压力来控制催化剂床层温度的恒定.合成塔还装有一个开车用的蒸汽加热系统,由一个蒸汽喷射器及循环水管组成.开工用饱和蒸汽通过针形阀冷凝.产生动力以推动反应器管间的锅炉水不断地循环,加热管内催化剂以达到活性温度.第四节工艺指标一、压力及压差(MPa)1.补气压力3~3.32.合成系统入口压力6.83.系统压差小于0.34.合成塔压差小于0.15.升降压速率小于0.4MPa6.放醇压力小于0.5MPa7.闪蒸槽压力小于0.4MPa8.汽包给水压力~5.69.汽包蒸汽压力2.4~4.010.开工蒸汽压力1.3(低压),4.0~4.5(中压)11.洗醇泵出口压力6.612.洗醇泵油压0.25~0.3二、温度1.合成塔热点温度初期230正负5度,中期235~260度,末期265正负5度.2.水冷器温度小于40度3.水冷前温度~90度,汽包给水温度~120度4.汽包蒸汽出口温度220~260度5.合成塔催化剂升降温速率:210度前小于40℃/H6.合成塔出口温度200~220度7.进中间换热器前温度~48度三、液位1.醇分液位1/3~1/22.汽包液位40%~70%3.闪蒸槽液位1/2~2/34.洗醇塔液位1/3~1/25.稀醇槽液位1/2~2/3四、成分1.补气:(H2-CO2)/(CO+CO2)=2.12.入塔气: (H2-CO2)/(CO+CO2)=4.323.循环气中惰性气含量:开车初期10~15%末期15~20%4.新鲜气CO=25%正负3 CO2=5正负2%5.合成塔入口气CO=9正负2%,CO2=7正负2%6.合成汽包脱盐水电导率小于150第五节正常开、停车步骤一、原始开车1.开车前的准备1)消防器材、防护用品、仪器、工具、备品备件以及开车人员配备落实。
- 1、下载文档前请自行甄别文档内容的完整性,平台不提供额外的编辑、内容补充、找答案等附加服务。
- 2、"仅部分预览"的文档,不可在线预览部分如存在完整性等问题,可反馈申请退款(可完整预览的文档不适用该条件!)。
- 3、如文档侵犯您的权益,请联系客服反馈,我们会尽快为您处理(人工客服工作时间:9:00-18:30)。
xx10万吨/年甲醇汽轮机试车资料二合一压缩机操作规程一、岗位的任务及意义合成气二合一压缩是将脱硫转化工段来的转化气经离心式压缩机的8级叶轮压缩后与来自合成的循环气共同经过第9级叶轮压缩,然后送入合成工序。
二、工艺过程概述2.1 工艺技术方案的选择压缩机的选择主要取决于装置的生产能力、气体的质量、气体的性质。
离心式压缩机适用于打气量大,压差小,气体质量好的气体场合,具有打气量大,维修少,无需看机,可用蒸汽透平驱动以提高能量转换,效率高等优点。
由转化来的转化气体压力1.6 MPa(G),甲醇合成需要的压力为5.3MPa(G),入塔气量要求大,压差小,因此选用一台离心式压缩机。
2.2 合成气压缩机流程2.2.1气体流程来自转化工序的合成新鲜气进入合成压缩机一、二段,压缩至4.8MPa(G),经冷却至40℃与来自甲醇合成的循环气(4.8MPa(G)、40℃),一起进入合成压缩机的三段,经过三段压缩至5.3MPa(G),然后送甲醇合成工序。
根据生产实际运行情况,在压缩机出口设有两个防喘振阀门。
新鲜气和合成循环气的气量通过这来两个防喘振进行调解,当压缩机运行工况进入喘振区时,阀门自动联锁开启,以防止压缩机喘振。
2.2.2 蒸汽和冷凝液流程合成气压缩机采用蒸汽透平驱动,中压蒸汽3.14—3.45MPa(A),进入蒸汽透平机,汽轮机出口减压至0.01MPa(A),经过凝汽器的全冷凝,冷凝液用冷凝液泵打入冷凝液管网。
2.2.3 润滑油流程从润滑油箱来的润滑油通过润滑油泵(主辅油泵)加压,经一次油压调解后,压力0.85MPa(G),进入油冷却器,油过滤器,二次油压调节,供油压力在0.3MPa (G),然后分二路分别进入汽轮机,压缩机。
回路经回路总管返回润滑油箱。
油冷却器,油过滤器均为一开一备,在不影响系统运行的情况下,进行切换、清洗。
本系统设有高位油箱一个,当两台油泵同时发生故障时,高位油箱的单向阀会自动打开,通过高位差流到各个润滑油点,使机组在惰走时间能得到充分润滑。
三、汽轮机概述本汽轮机采用xx集团从德国西门子引进的积木块反动式汽轮机技术设计,生产制造。
汽轮机为凝汽式,型号NK25/28/25。
汽轮机为单侧进汽,采用向上进汽和向下排气的结构,汽轮机带有保湿材料和罩套。
汽轮机上装有疏水阀,所有的疏水口都最后集中到疏水膨胀箱。
汽轮机带有表面式冷凝器和液位自动调节装置,并配有两极射气抽气装置以保障冷凝器能正常工作。
3.1 规格介绍N ——常压进汽K ——冷凝式25 ——进气缸半径单位cm28 ——转子末根部直径单位cm25 ——气缸延长段长度单位cm3.2 主要零件介绍3.2.1 气缸前缸为铸钢体,排气缸为灰铸铁,二者通过垂直中分面相接,整个气缸有水平中分面,上下缸用法兰面和螺钉连接。
3.2.2 轴承汽轮机径向轴承采用滑动轴承,其孔是二油叶型式,能保持转子运行稳定,轴承工作面上浇有巴氏合金。
汽轮机止推轴承装在前轴承座,它除起到转子轴向定位的作用外,同时也承受经平衡活塞平衡后所剩余的轴向推力,其形式为弧段式(米契尔式),两边对称可承受两个方向的推力,瓦块上浇有巴氏合金。
3.2.3 汽轮机转子转子为整个锻钢结构,调节级是冲动式叶片,中间转鼓级为反动式直叶片,末级为纽叶片,均为不调频叶片。
叶片叶根型线部分及围带三者由整块材料铣成,纽叶片因在叶片顶部叶距大,叶形薄,不宜用围带而采用拉筋结构。
转鼓级叶根为倒T形,再经过加工而成,叶根为钩形。
3.2.4 汽轮机汽封在导叶和动叶的围带上,铣出有径面高低的台阶,这些台阶和导叶持环上及转子上的汽封片一起组成有效的级间迷宫式汽封。
转子和气缸间需要密封的地方,装有汽封体,汽封体固定在气缸上,允许热膨胀,对冷凝式汽轮机组,在启动时,为了保持必要的真空,需向汽封送入蒸汽。
3.2.5 调节系统新蒸汽速阀位于气缸前部,新蒸汽通过其进入蒸汽室。
当机组正常运行时,速关阀中的油压克服弹簧力顶开阀门,出现故障时,油路中压力下降,阀门就立即快速关闭。
调节气阀用来调节进气量,而进气量决定着汽轮机的转速和功率,调节气阀是用油压操纵的,各个阀碟挂在横梁上,横梁通过两根拉杆和一套杠杆机构被装在进气室前的油动机所带动。
所有控制调节系统的信号变换机构都集中装在前轴承座旁边。
汽轮机调速器采用Woodward505调速器。
四、合成气压缩机操作规程该压缩机是为xx公司年产10万吨甲醇装置合成气压缩机。
压缩机与原动机由膜片联轴器联接,压缩机与汽轮机安装在底座上,整个机组采用润滑联合油站供油,压缩机的轴端密封采用鼎铭公司的干气密封,原动机采用汽轮机集团的冷凝汽轮机。
4.1 离心压缩机型号的意义3BCL459压缩机为叶轮顺排布置、机壳垂直剖分结构,叶轮名义直径为φ450mm/φ438mm,合成气体依次进入八级叶轮进行压缩与循环气混合经一级叶轮压缩至出口状态。
有中间气体冷却器。
3 ——合成段与压缩段叶轮背靠背布置B ——机壳为垂直剖分结构CL ——无叶扩压器45 ——首级叶轮名义直径450mm9 ——共9级叶轮4.2 离心压缩机定子及其组成3BCL459型压缩机是一种多级高压离心压缩机,机壳为垂直剖分式。
压缩机主要由定子(机壳、隔板、密封、端盖) 、转子(主轴、叶轮、隔套、平衡盘、推力盘、联轴器等)及支撑轴承、推力轴承、轴端密封等组成。
4.2.1机壳3BCL459型压缩机的机壳,根据压力和介质的需要,采用锻钢材料制成.机壳在两端垂直剖分,用螺栓将两侧的端盖和机壳紧固在一起。
为了具有良好的密封性,机壳端面要精加工,端面上铣密封槽,密封槽安装“O”型胶圈和加强环,具有良好的密封性。
在机壳端面的上半部,每侧有两个装导杆的螺孔,每个导杆上安装有导向套环,在装拆端盖时起导向作用。
保证在装卸端盖时不致碰坏机壳的密封和转子,这四个导杆还兼做固紧机壳和端盖的螺栓之用。
在机壳筒体的两侧伸出四个支腿,将压缩机支在底座上。
在机壳的两个支腿上,有横向键槽,是为压缩机轴向定位之用,对于3BCL459型压缩机,在机壳下部外侧有两个立键,用于机器的横向定位。
这些键能防止机壳位移,保持机器的良好对中,并能适应因温度变化而引起机壳热膨胀变形。
轴承箱和端盖连成一体,这种结构可增加机壳的刚性。
密封室装干气密封。
轴承压盖是可拆卸的,在检查轴承时,只要拆掉轴承压盖即可,不必拆卸压缩机机壳。
这种压缩机的进、出气管焊接在机壳上。
它们的方向为垂直向上。
机壳的底部有三个排污孔,用于排出压缩机运转时产生的冷凝液。
4.2.2 隔板3BCL459型压缩机隔板由ZG230-450材料制造。
隔板的作用是把压缩机每一级隔开,将各级叶轮分隔成连续性流道,隔板相邻的面构成扩压器通道,来自叶轮的气体通过扩压器把一部分动能转换为压力能。
隔板的侧是迥流室。
气体通过迥流室返回到下一级叶轮的入口。
迥流室侧有一组导流叶片,可使气体均匀地进到下一级叶轮入口。
隔板从水平中分面分为上、下两半。
隔板和隔板之间靠止口配合径向定位,各级隔板靠隔板束把合螺栓依次紧密地连在一起。
隔板和机壳间的定位:径向靠进口和末级隔板的外径定位;轴向靠进口隔板、端盖及机壳的止口定位。
出口隔板靠止口和螺栓把合固定在端盖上。
4.2.3 级间密封3BCL459型压缩机级间密封采用迷宫密封,在压缩机各级叶轮进口圈外缘和隔板轴孔处,都装有迷宫密封,以减少各级气体回流。
迷宫密封是采用锻铝制成,用这种较软的材料主要是为了避免损坏轴套和叶轮。
为避免由于热膨胀而使密封变形,发生抱轴事故,一般将密封体做成带有L 形卡台。
密封齿为梳齿状,密封体外环上半用沉头螺钉固定在上半隔板上,但不固定死。
外环下半自由装在下隔板上。
4.2.4 平衡盘密封压缩机平衡盘上装有迷宫密封,这是为了尽量减少平衡盘两边的气体泄漏。
对3BCL459型压缩机,其作用是减少末级出口和压缩机平衡气腔间的气体泄漏。
结构与级间密封类似。
4.3 转子及其组成压缩机的转子包括主轴、叶轮、轴套、轴螺母、隔套、平衡盘和推力盘等。
4.3.1主轴压缩机的主轴的主要作用是传递功率,主轴应有一定的刚度和强度。
4.3.2叶轮叶轮采用闭式、后弯型叶轮。
叶轮与轴之间有过盈,热装在轴上。
叶轮上的叶片铣在轮盘上,再把轮盖焊到叶片上。
对较窄的叶轮,焊条伸到弯曲的叶片和轮盖相接处有困难,叶片可铣在轮盖上。
把叶片焊到平坦的轮盘上比较容易。
对更窄的叶轮,则采用开槽焊接。
根据API617的规定,叶轮做超速试验。
4.3.3 隔套隔套热装在轴上,它们把叶轮固定在适当的位置上,而且能保护没装叶轮部分的轴,使轴避免与气体相接触。
且起导流作用。
4.3.4 轴螺母轴螺母主要是起轴向固定作用。
如轴向固定叶轮,轴端密封等等。
4.3.5 平衡盘由于在叶轮的轮盖和轮盘上有气体产生的压差,所以压缩机转子受到朝向叶轮入口端的轴向推力的作用。
这种推力一般是由平衡盘来抵消的。
对于3BCL459压缩机平衡盘装在最后一级叶轮相邻的轴端上。
在设计时使残余的推力作用在止推轴承上,这就保证了转子在轴向不会有大的串动。
4.3.6 推力盘叶轮一开始旋转,就受到指向吸入侧的力,这主要是因为轮盖和轮盘上作用的压力不同造成推力不等的原因。
作用在叶轮上的轴向推力,将轴和叶轮沿轴向推移。
一般压缩机的总推力指向压缩机进口,为了平衡这一推力,安装了平衡盘和推力轴承,盘采用锻钢制造而成。
4.4支撑轴承3BCL459由油站供油强制润滑,卸压缩机壳体。
热量。
承体的上方有防转销钉。
4.5推力轴承止推轴承采用金斯伯雷型止推轴承。
止推轴承的作用是承受压缩机没有完全抵消的残余的轴向推力,以及承受膜片联轴器产生的轴向推力。
根据需要止推轴承装在支撑轴承外侧的轴承箱。
金斯伯雷止推轴承也是双面止推的,轴承体水平剖分为上、下两半,有两组止推元件,每组一般有6块止推块(特殊系列要多一些),置于旋转时推力盘两侧。
推力瓦块工作表面浇铸一层巴氏合金,等距离的装到固定环的槽,推力瓦块能绕其支点倾斜,使推力瓦块均匀的承受挠曲旋转轴上变化的轴向推力。
这种轴承一般情况下,装有油控制环,其作用是当轴在高速旋转时,可减少润滑油紊乱的搅动,使轴承损失功率减少。
止推轴承的轴向位置,由调整垫调整,调整垫的厚度在装配时配加工。
4.6 轴端密封轴端密封根据用户的要求选用干气密封。
干气密封是用于离心压缩机的一种新型密封。
干气密封可节省运行成本,排除了不定期的维修,避免了产品的污染(气体被油污染、或者油被气体污染)。
因为没有密封油系统,因此减少了总重量,节省了占地空间。
同时停车时不需要放空,运行时耗功极小,但价格较高。
干气密封实质上是一对机械密封,它是流体通过动环和静环的径向接合面上的唯一通路实现密封。
密封表面被研磨得非常光滑,转动的硬质合金环在其旋转的平面上加工出一系列螺旋槽。
随着旋转,流体被泵入螺旋槽的根部,在此环形面形成密封的屏障,此密封屏障阻止流动,并增高压力。